Министерство образования и науки Украины
Севастопольский национальный технический университет
Кафедра Океанотехники и кораблестроения
Курсовой проект
по дисциплине«Технология строительства судов и плавучих сооружений»
на тему «Разработка технологии изготовления секции левого борта»
Выполнил:
ст. гр. К-42д
Енокян М.А.
Проверил:
Жибоедов В.В.
Севастополь
2010
СОДЕРЖАНИЕ
Введение ………………………………………………………………………. 3
1 Характеристика сборочно-сварочного цеха. ……………………...…..….. 4
2 Краткое описание заданной секции …………………………………….... 11
3 Разработка технологических маршрутов изготовления деталей корпуса 12
4 Расчет трудоемкости изготовления деталей …………………………....... 14
5 Описание и характеристика технологической линии изготовления сек-
ции ……………………………………………………………………………... 16
6 Разработка технологии изготовления секции на линии. Контроль ка-
чества и проверочные работы. ………………………………………………. 21
6.1 Разработка технологии изготовления секции на линии «ESAB»….. 21
6.2 Контроль качества сварных соединений………………………...…… 25
6.3 Проверочные работы. ……………………………………………..…... 27
7 Расчет трудоемкости изготовления плоской секции ………………….… 29
7.1 Расчет трудоёмкости изготовления секции при существующей ме-
ханизированной линии. ………………………………………………………. 29
7.1.1 Сборка полотна……………………………………….…………… 29
7.1.2 Сварка полотна………………………………...…………….……. 29
7.1.3 Разметка……………………………………………….…….…….. 29
7.1.4 Установка набора главного направления ……………….…......... 29
7.1.5 Приварка набора главного направления в зависимости от
типа сварки и расположения швов………………………….………...... 29
7.1.6 Установка перекрестного набора…………………………............ 29
7.1.7 Сварка перекрестного набора……………………………….......... 29
7.1.8 Установка и приварка насыщения: …………………..………….. 30
7.2 Трудоёмкость изготовления секции на механизированной линии......... 30
8 Размерный анализ секции ………….………………………………............ 32
9 Условия и метод постройки судна..……………………………..………… 38
9.1 Условия постройки судна………………………………….…..…….... 38
9.2 Описание спуска судна…………………….…………….…..….…….. 38
9.3 Метод постройки судна………………………………..….…..………. 39
9.3.1 Изготовления деталей…………….……………………………..... 42
9.3.2 Изготовления секции…………….………………………..…….... 42
9.4 Технология сборки блоков…………….…………………………...…. 43
9.5 Технология постройки судна……………………….…….…..……..... 43
Заключение ……………..………………………………………………….….. 45
Библиографический список…………….……………………………..…....… 46
ВВЕДЕНИЕ
Основной задачей судостроения является рост производительности труда и подъем эффективности производства. Решение этой задачи возможно лишь на основе внедрения более прогрессивного оборудования и новых форм организации труда.
В решении этой задачи главное место занимает технология судостроения. Эта наука, изучающая сущность производственных процессов постройки судов, взаимную связь этих процессов и закономерности их развития.
Производственный процесс – это совокупность всех действий, направленных на превращение материалов и полуфабрикатов в законченную продукцию – предмет производства. Производственный процесс постройки судна включает получение и обработку материалов для корпуса и оборудования, сборку и сварку частей корпуса и целого корпуса, изготовление и монтаж различных устройств, систем, аппаратов и приборов, отделку помещений, наладку различных технических средств испытания и сдачу заказчику судна.
В ходе каждого производственного процесса объекты труда заготавливают, транспортируют, складируют, обрабатывают различным способом, собирают, подвергают контролю и т.д. пока не будет создано изделие. Часть производственного процесса, связанная с изменением и последующим определением состояния предмета производства, называется технологическим процессом.
В данной курсовой работе будет разработана технология изготовления плоскостной секции переборки сухогруза.
1 Сборочно-сварочный цех
В состав сборочно-сварочного цеха обычно входят следующие подразделения: склад готовых деталей корпуса; участки сборки и сварки узлов и секций; участок грунтовки секций; склад готовых секций; кладовые и вспомогательные службы цеха.
Склад готовых деталей предназначается для хранения и комплектации деталей корпуса, поступающих в контейнерах или пачками из корпусообрабатывающего цеха.
Склад рассчитывают на одновременное хранение готовых деталей в объеме 0,5—0,6 месячного их расхода сборочно-сварочным цехом для заводов I, Пи III классов и 0,2—0,35 —для заводов IV и V классов.
Детали хранят на складе в контейнерах различных типоразмеров, а крупные листы и профили — пачками. Для уменьшения площади склада крупные контейнеры устанавливают друг на друга, а для укладки небольших контейнеров предусматриваются стеллажи.
Склад обслуживается мостовыми кранами грузоподъемностью 20—30 т, если он расположен в закрытом помещении. При расположении склада на открытой площадке его обслуживают козловыми кранами.
Площадь склада определяется из расчета удельной нагрузки на 1 м2
, составляющей 0,4—0,6 т для заводов I, II и III классов и 0,1—0,3 т для заводов IV и V классов.
Участки сборки, и сварки узлов и секций являются основными производственными подразделениями и снабжены технологическим и подъемно-транспортным оборудованием и оснасткой.
В целях механизации и автоматизации производственных процессов в современных сборочно-сварочных цехах стремятся использовать специализированные линии и участки. На неспециализированных участках изготовляют менее распространенные секции, а также нетиповую продукцию.
По общности выполняемых операций, составу оборудования и средств механизации специализированные линии и участки могут быть сгруппированы следующим образом (рис. 1.1):
1 Линия сборки и сварки балок (преимущественно узлов таврового сечения), состоящая из двух позиций: автоматическая сборка и сварка тавровых балок на различных станках и отдельная позиция их правки с использованием профилегибочного станка.
2 Поточная линия сборки и сварки полотнищ, имеющая от двух до шести позиций в зависимости от принятой тexнoлогии сборки и сварки. Передвижение полотнищ по позициям производится по роликовым опорам.
3 Линия сборки и сварки плоскостных секций, состоящая из нескольких позиций. Эта линия может быть объединена с изготовлением полотнищ или же возможна подача на первую позицию готового сваренного полотнища. Далее оно перемещается по остальным позициям.
4 Поточные линии сборки и сварки палубных и бортовых секций с небольшой погибью, оборудованные рамами постелей со съемными лекалами и погрузчиками для установки и прижатия набора. Рамы передвигаются по эстакаде высотой около 2 м над сборочной площадкой.
5 Участки сборки и сварки крупных полуобъемных и объемных секций (днищевых, бортовых и других, имеющих большую погибь), а также секции оконечностей. Участки оборудованы стационарными постелями и портальными агрегатами, передвигающимися по рельсам над постелями или стендами.
6 Участки сборки и сварки объемных узлов небольшой протяженности, а также бракет, коротких тавров и прочих, узлов корпуса. На них предусматривают постоянные рабочие места, оснащенные универсальными стендами и кондукторами, способствующими механизации сборочных операций, а также позиционерами для выполнения сварки в удобном положении.
Все технологическое оборудование сборочно-сварочного цеха разделяется на две основные категории: специализированное и универсальное. Первое предназначается только для конкретных узлов или секций. Универсальное оборудование может быть использовано для изготовления разнообразных видов узлов и секций.
На неспециализированных участках цеха для проведения сборочно-сварочных работ используются универсальные сборочные площадки и плиты, представляющие собой ровную горизонтальную поверхность, которая по действующим нормам не должна иметь местных отклонений от плоскости более ±3 мм при проверке линейной длиной 3 м. Наиболее широкое применение нашли плиты, сверенные из листовой и профильной стали. На ряде заводов предусмотрены площадки для сборки и сварки в виде сплошного железобетонного пола с вмонтированными балками вровень с поверхностью пола на расстоянии 1,0—1,5 м друг от друга.

Рисунок 1.1. Схема сварочно-сборочного цеха судостроительного предприятия II класса.
I – механизированная линия сборки и сварки тавровых балок; II – стенды для сборки узлов набора и фундаментов; III – поточно-позиционная линия сборки и сварки лёгких выгородок; IV – поточно-позиционная линия сборки и сварки полотнищ; VI – стенд для сборки и сварки люковых закрытий; VII – линии сборки и сварки палубных секций; VIII – стенды для сборки и сварки надстроек и рубок; IX – поточно-позиционная линия сборки и сварки плоскостных секции; X – линия сборки и сварки бортовых секций; XI – участок сборки и сварки объемных сеций.
1 – рольганг; 2 – велосипедный кран грузоподъёмностью 10 т; 3 – станок для сварки тавровых балок; 4 – рольганг-накопитель; 5 – пресс типа «Бульдозер» для правки балок; 6 – портальный агрегат для сварки листов; 7 – мостовой кран грузоподъёмностью до 30 т; 8 – портальный агрегат для приварки набора; 9 – самоходная тележка; 10 – набороукладчик; 11 – мостовой кран грузоподъёмностью 50 т.
При изготовлении объемных узлов иногда находят применение позиционеры для закрепления и поворота изделий при сварке. Они могут быть отнесены к универсальному оборудованию.
На линиях и участках, специализированных по видам продукции, применяется:
для сборки и сварки плоских полотнищ:
1) листоукладчик самоходный портального типа;
2) стенд электромагнитный для прихватки кромок листов полотнищ под сварку;
3) порталы сварочные самоходные для сварки полотнищ;
4) стенд электромагнитный с флюсомедной подкладкой (в случае использования процесса односторонней сварки с обратным формированием);
5) устройство для кантовки полотнищ;
для сборки и сварки плоскостных секций, состоящих из полотнищ и балок набора, если этот участок отделен от линии полотнищ:
1) агрегат для установки и прижатия набора к полотнищу;
2) агрегат для приварки набора;
для сборки и сварки полуобъемных и объемных секций, ограниченных плоскими и криволинейными поверхностями:
1) универсальные механизированные постели или переналаживаемые с флюсовыми лотками;
2) портальные агрегаты разного назначения, например, в листоукладчиках — траверсы с вакуумными или электромагнитными присосами для подъема и укладки листов; в прижимных агрегатах — гидравлические устройства, прижимающие набор к листам; в сварочных порталах — навесные сварочные головки для сварки стыковых или угловых швов, в том числе и крестообразных соединений набора в вертикальном положении; в погрузчиках — траверсы с гидравлическими захватами для подъема и наведения на место балок набора или других узлов;
3) устройства для прижима полотнища к набору снизу;
4) стрелы с контейнерами, содержащими сварочное оборудование для приварки перекрестного набора;
5) устройства для транспортировки секций по позициям.
На всех участках цеха для выполнения прихватки, ручной и полуавтоматической сварки расположены источники их питания — сварочные генераторы и трансформаторы. Их обычно устанавливают группами на специальных площадках между колоннами цеха. Имеются также переносные аппараты для автоматической сварки в среде углекислого газа и под флюсом с источниками питания, а также комплексные посты для полуавтоматической сварки в среде углекислого газа, смонтированные на тележках или в переносных контейнерах. Они подаются краном к местам наибольшего сосредоточения сварочных работ.
Для питания постов углекислым газом в цехе имеется централизованный трубопровод, для выполнения тепловой резки (обрезка припусков, вырезка отверстий и др.) — ацетиленовый и кислородный трубопроводы с распределительными устройствами. Зачистка кромок шлифовальными машинками, вырубка сварных швов и выполнение других пневматических работ обеспечиваются трубопроводом сжатого воздуха давлением 0,4—0,5 МПа (4 — 5 кгс/см2) с распределительными устройствами.
Участок грунтовки секций предназначен для предохранения секций от коррозии в период их хранения на складе и при постройке судна на построечном месте.
Исходя из условий противопожарной безопасности участок грунтовки секций обычно располагают в отдельно стоящем здании и реже — в пристройке к сборочно-сварочному цеху. Секции подаются на участок безрельсовым транспортом или на железнодорожных платформах, оборудованных опорными балками. На платформе производится очистка и грунтовка секций. Участок оборудуется передвижными люльками-манипуляторами для доступа ко всем поверхностям секций.
Все электрооборудование участка (включая мостовые краны) выполняется во взрывобезопасном исполнении. Для сушки окрашенных секций установлены вентиляторы с калориферами и переносными шлангами большого диаметра. Участок должен быть оборудован системой автоматического пожаротушения и общеобменной приточно-вытяжной вентиляцией.
Склад готовых секций обычно расположен на открытой площадке и обслуживается мостовыми или козловыми кранами, грузоподъемность которых определяется в зависимости от максимальной массы хранимых секций.
Склад рассчитывается на одновременное хранение секций в пределах 0,25—0,60 заданного ритма при секционной постройке и в пределах заданного ритма при постройке блоками. Под ритмом подразумевается количество выпускаемых поточно-позиционным методом судов (изделий) за определенный промежуток времени (ГОСТ 3-1109—73).
Для расчета полезной площади склада удельную нагрузку на 1 м2
принимают в пределах 4—6 кН (0,4—0,6 тс). Отношение полезной площади к общей составляет 0,4—0,5.
Количество оборудования, рабочих мест и работающих в цехе рассчитывают исходя из годовой программы цеха. По программе определяется годовой выпуск узлов и секций в тоннах, включающий массу металла корпуса и деталей и узлов насыщения.
Примерное распределение трудоемкости сборки и сварки узлов и секций корпусов средних транспортных судов по операциям (%) показано ниже:
Разметка, сборка, правка и проверка........................................ 43,0—45,0
Ручная сварка и прихватка………………...…………………. 12,0—14,0
Полуавтоматическая сварка:
под слоем флюса……………………...………………. 3,0—4,0
в среде углекислого газа…………...……………........ 17,0—19.0
Автоматическая сварка……………….………………………. 6,0—8,0
Зачистка и рубка пневматическим инструментом…….......... 7,0—9,0
Газовая резка……………………………...………………........ 3,0—4,0
Воздушно-дуговая строжка…...…………...…………………. 1,0—1,5
Контроль, испытания и сдача……….……...……………...…. 1,5—2,0
Для расчетов затрат электроэнергии и расхода сварочных материалов общую трудоемкость сварки и прихватки принимают равной 12—14%.
Действительный годовой фонд времени при двухсменной работе принимают: электросварочного и газорезательного оборудования 3900 ч; сборочного оборудования (постелей, стендов, сборочных плит и прочего) — 4075 ч.
Сборочно-сварочные цехи оборудуют электрическими мостовыми кранами грузоподъемностью от 20 до 200 т. Необходимое количество мостовых кранов в сборочно-сварочных цехах — один кран на 60—80 м длины пролета. Более точно количество кранов можно определить согласно выражению
Скорость подъема груза и передвижение тележки и моста определяют согласно технической характеристике крана.
Для определения времени на «участие» крана при установке и монтаже конструкции используют средние величины хронометражных наблюдений за выполнением этих операций.
Коэффициент использования крана по времени принимается равным 0,7 для крюкового крана и 0,8—0,95 — для электромагнитного крана.
Средняя продолжительность циклов работы мостовых кранов в сборочно-сварочныхцехах приведена в таблице 1.1.
Таблица 1.1 Средняя продолжительность циклов работы кранов при подъёме секций и установке узлов и деталей в сборочно-сварочных цехах
Масса единицы груза, т |
Продолжительность цикла, ч |
Обработка груза |
Установка и монтаж |
Всего |
До 5 |
0,15 |
0,3 |
0,45 |
6 - 15 |
0,17 |
1,2 |
1,37 |
16 - 30 |
0,18 |
1,8 |
1,98 |
31 - 50 |
0,25 |
2,0 |
2,25 |
51 - 75 |
0,50 |
- |
0,50 |
76 - 120 |
0,80 |
- |
0,80 |
121 - 150 |
1,00 |
- |
1,00 |
Расчет площади и планировка цеха. Сборочно-сварочные цехи располагаются в зданиях, имеющих от двух до шести пролетов.
Длину цеха выбирают в зависимости от длины поточных линий и принимают кратной 12 м. Характеристики сборочно-сварочных цехов приведены в табл. 1.2.
Таблица 1.2 Характеристика сборочно-сварочных цехов заводов различных классов
Характеристики |
Класс завода |
I |
II |
III |
IV |
V |
Ширина пролётов, м |
48 |
48 |
36 |
30 |
30 |
Шаг колонн в пролётов (до отметки подкрановых рельсов), м |
24; 36 |
24; 36 |
24 |
12 |
12 |
Грузоподъёмность мостовых кранов, т |
22,5 |
22,5 |
16,0 |
12,65 |
11,45 |
 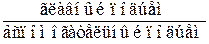 |
 |
 |
 |
 |
 |
Площадь сборочно-сварочного цеха в первом приближении может быть определена по годовому выпуску с 1 м2
площади цеха (т/м2
).
Более точный расчет площади цеха получают по чертежу его планировки исходя из количества оборудования и рабочих мест, полученных расчетом, как об этом говорилось в гл. 3. Так же, как и для корпусообрабатывающего цеха, определяют абсолютные и относительные показатели спроектированного сборочно-сварочного цеха:
годовой выпуск продукции с 1 м2
площади цеха (без служебно-бытовых помещений), который составляет 4,0—1,6 т/м2
;
годовой выпуск продукции на одного списочного рабочего (суммарное количество производственных и вспомогательных рабочих). Он колеблется от 30 до 165 т/чел.;
трудоемкость в чел-ч, приходящуюся на 1 т годового выпуска продукции. Она составляет 8,5—46,0 чел-ч/т.
Первые цифры относятся к заводам I класса, вторые — V класса.
2 КРАТКОЕ ОПИСАНИЕ ЗАДАННОЙ СЕКЦИИ
Название секции: левый борт в районе 167..178 шпангоутов.
Габариты секции: ширина и длина соответственно 9980х7920.
Секция имеет поперечную систему набора. Балки главного направления – полособульб 18б (L=9980, 8шт.).
Высота большей части балок главного направления t= 180 мм.
Меньший размер в плане В = 9500 мм.

Поскольку секция состоит из плоского полотнища, в котором высота большей части балок набора составляет 2,3% меньшего размера в плане В и имеет 2 балки перекрёстного направления, классифицируем её как плоскостную с набором одного направления.
Конструкция секции позволяет при оптимальных затратах труда, средств, материалов и времени изготовить её на механизированной поточной линии ESAB.
3 РАЗРАБОТКА ТЕХНОЛОГИЧЕСКИХ МАРШРУТОВ ИЗГОТОВЛЕНИЯ ДЕТАЛЕЙ СЕКЦИИ
Деталь 1 – лист
S
18.
Класс 1 – крупногабаритные детали с прямолинейными кромками.
Группа 1.3 – плоские детали без вырезов и с разделкой кромок.
0.5– 1.1 – 2.1 – 3.4 – 4.4 – 4.6 – 5.1 – 6.1 – 7.1 – 1001 – 1002
0.5– составление программ для тепловой вырезки корпусных деталей;
1.1 – предварительная правка листов в исходном состоянии в листоправильных машинах;
2.1 – дробометная очистка листовой стали;
3.4 – грунтовка в специальных агрегатах;
4.4 – разметка на машинах с программным управлением;
4.6 – маркировка на машинах с программным управлением;
5.1 – газовая резка листовой стали на машинах с программным управлением;
6.1 – разделка кромок в процессе резки на машинах с программным управлением;
7.1 – правка деталей после вырезки в листоправильных вальцах;
1001 – сортировка и комплектация корпусных деталей;
1002 – цеховая транспортировка.
Деталь 4 –
ребро жесткости Р18б
Класс 5 – детали из профильного проката.
Группа 5.1 – прямые без вырезов и разделки кромок.
Технологический маршрут изготовления:
0.1 – 101 – 201 – 304 – 404 – 503 – 604 – 701 – 1001 – 1002
0.1 – определение контуров и размера детали по рабочим чертежам;
101 – правка профильного проката на роликовых машинах;
201 – дробеметная очистка профильного проката;
304 – грунтовка профильного проката в специальных установках;
404 – разметка по эскизам;
503 – резка профильного проката газовая ручная;
604 – зачистка кромок от грата;
701 – правка деталей из профильного проката на горизонтально-гибочном прессе;
1001 – сортировка и комплектация корпусных деталей;
1002 – цеховая транспортировка.
Деталь 12– кница
S
12
Класс 3 - Мелкая деталь с прямолинейными кромками
Группа 3.5 – С отогнутыми фланцами без вырезов и разделки кромок
Технологический маршрут изготовления:
0.5 – 1.1 – 2.1 – 3.4 – 4.4 – 4.6 – 5.1 – 6.9 – 7.3 – 8.4 – 3.4 – 1001 – 1002
0.5 – составление программ для тепловой вырезки корпусных деталей;
1.1 – предварительная правка листов в исходном состоянии в листоправильных валковых машинах;
2.1 – дробемётная очистка листовой стали;
3.4 – грунтовка в специальных агрегатах;
4.4 – разметка на машинах с программным управлением;
4.6 – маркировка на машинах с программным управлением;
5.1 – газовая резка листовой стали на машинах с программным управлением;
6.9 – зачистка кромок от грата;
7.3 – правка деталей после вырезки на прессе;
8.4 – отгибка фланцев на прессе;
3.4 – грунтовка в специальных агрегатах;
1001 – сортировка и комплектация корпусных деталей;
1002 – цеховая транспортировка.
Деталь 14 – кница
S
9
Класс 3 – мелкие с прямолинейными кромками.
Группа 31 – плоские без вырезов и разделок кромок.
Технологический маршрут изготовления:
0.5 – 1.1 – 2.1 – 3.4 – 4.4 – 4.6 – 5.1 – 6.9 – 7.3 – 3.4 – 1001 – 1002
0.5 – составление программ для тепловой вырезки корпусных деталей;
1.1 – предварительная правка листов в исходном состоянии в листопровильных валковых машинах;
2.1 – дробемётная очистка листовой стали;
3.4 – грунтовка в специальных агрегатах;
4.4 – разметка на машинах с программным управлением;
4.6 – маркировка на машинах с программным управлением;
5.1 – резка листовой стали на машинах с программным управлением;
6.9 – зачистка кромок от грата;
7.3 – правка деталей после вырезки на прессе;
3.4 – грунтовка в специальных агрегатах;
1001 – сортировка и комплектация корпусных деталей;
1002 – цеховая транспортировка.
4 РАСЧЕТ ТРУДОЕМКОСТИ ИЗГОТОВЛЕНИЯ ДЕТАЛЕЙ СЕКЦИИ
Деталь 1
ЛистS=18 мм, длина 9980 мм, ширина 1980 мм.
Предварительная правка листов в исходном состоянии в листоправильных валковых машинах.
Диаметр валков 240 мм при расстоянии между центрами крайних валков 500 мм и скорости вращения 6 м/мин.
Тн
=Тшк
·N/n- норма времени.
Штучно-калькуляционное время определяем по формуле:
Тшк
=(0,49·L+0,02)·(0,017В+0,064)·(1,8-0,1s)
Тшк
=4,91·0,098·1,7=0,34
Тн
=0,34·1/1=0,34 ч.
Разметка детали.
Тн
=Тшк
·N
Тшк
=0,0194+0,0623·L+0,1134·B-0,0017·L2
-0,0313B2
+0,0144·L·B
Тшк
=1,43
Тн
=1,43·1=1,43 ч.
Тепловая резка.
Тн
=Тшк
·L
Тшк
=0,04
Тн
=0,04·9,98=0,39 ч.
Деталь 4
РЖ P18б
, длина 6500 мм, ширина 42 мм.
Предварительная правка листов в исходном состоянии в листоправильных валковых машинах.
Диаметр валков 240 мм при расстоянии между центрами крайних валков 500 мм и скорости вращения 6 м/мин.
Тн
=Тшк
·N/n- норма времени.
Штучно-калькуляционное время определяем по формуле:
Тшк
=(0.49·L+0.02)·(0.017В+0.064)·(1.8-0.1s)
Тшк
=4,91·0,081·1,7=0,02
Тн
=0.02·16/1=0,46 ч.
Разметка детали.
Тн
=Тшк
·N
Тшк
=0,0194+0,0623·L+0.1134·B-0.0017·L2
-0.0313B2
+0.0144·L·B
Тшк
=0,043
Тн
=0,043·16=0,69 ч.
Тепловая резка.
Тн
=Тшк
·L
Тшк
=0,04
Тн
=0,04·0,25=0,01 ч.
Деталь 12
Кница S=12 мм, длина 600 мм, ширина 600 мм
Вырезаем из листа 6000x1600 мм.
Предварительная правка листов в исходном состоянии в листоправильных валковых машинах.
Норму времени рассчитываем по формуле:
Тн
=Тшк
·N/n
Штучно-калькуляционное время определяем по формуле:
Тшк
=(0.49·L+0.02)·(0.017В+0.064)·(1.8-0.1s)
Тшк
=0,39
Тн
=0,39·1/1=0,39 ч.
Разметка детали.
Тн
=Тшк
·N
Тшк
=0,04·1,25=0,05
Тн
=0.05·1=0.05 ч.
Тепловая резка.
Тн
=Тшк
·L
Тшк
=0,037
Тн
=0,037*0,16=0,005 ч.
Деталь 14
Кница S=9 мм, длина 350 мм, ширина 350 мм
Вырезаем из листа 6000x1600 мм.
Предварительная правка листов в исходном состоянии в листоправильных валковых машинах.
Норму времени рассчитываем по формуле:
Тн
=Тшк
·N/n
Штучно-калькуляционное время определяем по формуле:
Тшк
=(0.49·L+0.02)·(0.017В+0.064)·(1.8-0.1s)
Тшк
=0,32
Тн
=0,32·1/1=0,32 ч.
Разметка детали.
Тн
=Тшк
·N
Тшк
=0,04·1,25=0,05
Тн
=0,05·1=0.05 ч.
Тепловая резка.
Тн
=Тшк
*L
Тшк
=0,037
Тн
=0,037*0,160=0,005 ч.
Вывод:
Произведен расчет трудоемкости некоторых технологических процессов изготовления деталей. В результате расчета было получено время нужное для изготовления деталей.
5 Описание и характеристики технологической линии изготовления секции
На рис. 5.1 показана схема весьма распространенной МПЛ, установленной шведской фирмой ESAB на многих заводах в разных странах. Производительность линии при работе 12 человек — четыре секции в смену размером 12 X 12 м при толщине листов 20 мм и 14 ребрах жесткости. Линия длиной около 110 м может иметь от шести до восьми позиций. Элементы секции последовательно перемещаются с позиции на позицию по сигналу с пульта управления. Перемещение осуществляется по выдвижным роликам с помощью тянущей боковой тележки. Ролики утоплены в стендах линий, на которых лежит секция. Они могут быть подняты одновременно в пределах данной позиции при необходимости переместить секцию.
На позициях выполняются следующие этапы технологического процесса:
Нулевая позиция. Хранение подготовленных пачек листов.
Позиция I. Раскладка листов с помощью портального» Листоукладчика с магнитными присосами и ручная прихватка их по стыкам.
Позиция II. Сварка листов встык под флюсом или односторонняя с обратным формированием или двусторонняя на флюсовом желобе, при которой после сварки необходима последующая перекантовка полотнища для подварки обратной стороны. Сварочные головки расположены на порталах, которые устанавливаются над осью шва.
Позиция III. Перекантовка полотнища, если на позиции II не применялась сварка с обратным формированием шва. Если же такая сварка применялась, эта позиция отсутствует. Для) перекантовки установлен специальный мостовой кран с автоматическими захватами.
Позиция IV. Снабжена поворотным устройством, разворачивающим секцию на 90° для установки на последующих позициях балок набора поперек сваренных пазов секции. На этой же позиции можно осуществлять воздушно-дуговую строжку корня шва (если сварка выполнялась без обратного формирования). Разметка мест установки балок набора выполняется по световой линии, направленной специальным проектором, или с помощью лазера.
Позиция V (соединенная с боковым накопителем балок набора). На этой позиции устанавливаются и привариваются балки набора (ребра жесткости). Балки хранятся в накопителе; и с помощью цепного транспортера подаются по одной к устанавливающему устройству. Устройство захватывает балку, перемещает ее вдоль оси, опускает на размеченную линию и плотно прижимает к полотнищу. Установленная балка приваривается тремя сварочными головками, расположенными в ряд на портале. По окончании сварки балки захваты освобождаются, полотнище перемещается на определенный шаг для установки следующей балки, и операция повторяется. Таким образом, происходит постепенное наращивание секции.
Позиция VI. Установка и сварка перекрестных связей; операции выполняются вручную с применением сварочных полуавтоматов.
Позиция VII. Установка насыщения, проведение контрольных операций (просвечивание, обмер и т. д.), а также исправление дефектов сварки.

Рис. 5.1. Схема линии для изготовления плоских секций.
1 — листоукладчик с магнитными присосами; 2 — продольные толкачи для листов; 3 — поперечные толкачи; 4 — захваты тянущих тележек; 5 — автомат для сварки пазов; 6 — мостовой кран для перекантовки полотнищ; 7 — выдвижной поворотный круг; 8 — портальная газорезательная машина; 9 — резаки машины; 10 — агрегат для установки, прижима и приварки балок набора; 11— цепной транспортер для балок; 12 —транспортеры для поперечного перемещения балок; 13 — перегрузчик для укладки балок набора на транспортер; 14 — приготовленная пачка балок набора.
Техническая характеристика линии сборки и сварки плоских секций
Габаритные размеры собираемых секций, м:
длина........................................................................................................... 3,5-10,0
ширина........................................................................................................ 3,5-10,0
высота, не более ................................................................................................ 1,2
толщина листов полотна, мм.......................................................................... 6-24
Масса (максимальная), т.................................................................................... 25
Набор главного направления:
полособульб по ГОСТ 5353-83.................................................... С № 8 по № 24
полособульб по ГОСТ 9235-76............................................ С №824 по №24712
тавр, мм.................................................................................................. - 
длина, м...................................................................................................... 3,0-10,0
масса (максимальная), т.................................................................................... 1,8
Набор перекрестного направления:
полособульб по ГОСТ 5353-83...................................................... С №9 по №24
полособульб по ГОСТ 9235-76.......................................... С № 824 по № 24712
высота шельфа, мм......................................................................................... 1200
высота листа, мм...................................................................................... 160-600
длина (максимальная), мм........................................................................... 10000
масса (максимальная), кг............................................................................... 2000
Габаритные размеры линии, м:
длина................................................................................................................. 93,0
ширина.............................................................................................................. 20,0
высота в исходном положении......................................................................... 8,5
высота в рабочем положении......................................................................... 13,5
производственная площадь, м²...................................................................... 1860
Масса оборудования, т..................................................................................... 295
Шаг установки набора главного направления
при механизированной установке (шпация), м..........От 0,35 до 0,75 через 0,05
В состав позиции IV входят устройство ориентации полотна; агрегат подачи набора; агрегат установки и приварки набора, оснащенный устройством для обратного выгиба полотна с целью предотвращения остаточных угловых деформаций полотна, и кассеты для продольного набора. Кроме того, в состав позиции входят пульты и шкафы для электро-, пневмо- и гидроуправления работой оборудования.
Состав позиции V: стенд с регулируемыми опорными роликами; кассеты для поперечного набора; агрегат полукозлового типа марки МСН-10, служащий для подачи, установки и разворота на 270° балок набора и их прижима к полотну; пульты и шкафы электро-, пневмо- и гидроуправления работой оборудования этой позиции.
Позиция VI включает шесть поворотных стрел, несущих на себе сварочное оборудование для полуавтоматической сварки перекрестного набора в среде двуокиси углерода.
Позиция VII содержит кантователь, подъемные балки с опорными роликами, гидроподъемники, а также пульты и шкафы электро-, гидро- и пневмоуправления работой оборудования.
Позиция VIII состоит из двух поворотных стрел марки ПСО-5, конструкция которых аналогична стрелам, расположенным на позиции VI.
Транспортная система линии представляет собой восемь тележек, обслуживающих попарно две смежные позиции. Они перемещаются по специальному транспортному каналу (на схеме не показан). Секции перемещаются на протяжении всей площади линии по неподвижным вращающимся опорным роликам.
При проектировании агрегатов механизированной поточной линии и их изготовлении с целью повышения эксплуатационной надежности всего комплекса линии и ритмичности ее работы необходимо обращать внимание на следующие моменты (выявленные в процессе годичной эксплуатации линии):
· соблюдение требуемой точности изготовления гидроцилиндров подъема роликов, установленных на флюсомедных балках, и класса чистоты рабочих поверхностей цилиндров. Нарушение этих требований приводит к нарушению плотности гидросистемы и утечке масла;
· обязательная термообработка сварных металлоконструкций перед механической обработкой их сварных поверхностей. Отказ от термообработки вызывает значительные деформации конструкций после механической обработки и изменение их основных размеров;
· отсутствие гарантии безотказной работы шарового поворотного устройства траверсы листоукладчика. Вследствие этого при раскладке листов взамен листоукладчика используют цеховой мостовой кран, нарушая ритм производства на линии и в цехе;
· недостаточная надежность системы ориентирующего устройства, состоящего из боковых захватов и упорных роликов. При работе с листами больших толщин, предусмотренных проектом линии, захваты из-за недостаточной жесткости теряют свою форму и не обеспечивают подачу листов больших толщин;
· недостаточная величина подъема роликов на позиции сборки полотен, что приводит к зацеплению кромок тонколистовых полотен за опорные брусья флюсомедного устройства при подаче их шлепперным транспортным механизмом;
· установка настила на поверхность стенда, где расположены опорные ролики. Наиболее целесообразным является зашивка стенда металлическим настилом на высоте 10-15 мм ниже опорных поверхностей роликов, в районах их расположения оставляются вырезы;
· наличие блокировки в электросхеме сборочного стенда, предупреждающей включение электропривода шлепперного устройства при включенных электромагнитах сборочной балки. В случае отсутствия блокировки может произойти поломка шлепперного устройства или электромагнитов сборочного стенда. В шлепперном устройстве следует предусмотреть тормозную систему, обеспечивающую точную остановку полотна при его перемещении;
· обеспечение в составе линии средств механизации для зачистки стыкуемых кромок набора под сварку. Ручная зачистка снижает общий уровень механизации работ на линии;
· исключение не надежности эксплуатации устройства для подачи полотна на величину шпации при механизированной безразметочной установке набора главного направления. Применение в противном случае ручной разметки мест установки набора нарушает ритм производства на линии;
· невозможность механизированной установки и прижатия набора главного направления полособульбового профиля высотой 50 мм и более с помощью агрегата АПН-10 принятой конструкции;
· сложность обслуживания транспортных тележек, размещенных в глубоком и узком транспортном канале, затрудняющем доступ к ним для осмотра и устранения неисправностей.
Низкая технологичность корпусных конструкций, не приспособленных для их механизированного изготовления на поточных линиях с определенным технологическим оснащением, отсутствие налаженной комплектации деталей, подаваемых на поточную линию, также нарушают ритмичность работы линии и снижают ее эффективность.
6 РАЗРАБОТКА ТЕХНОЛОГИИ ИЗГОТОВЛЕНИЯ СЕКЦИИ НА СТЕНДЕ
КОНТРОЛЬ КАЧЕСТВА И ПРОВЕРОЧНЫЕ РАБОТЫ
6.1 Разработка технологии изготовления секции на линии «ESAB»

Рисунок 6.1 – Схема секции левого борта
I – Изготовление полотна
Шифр
|
Расшифровка |
109
|
Сборка полотнища на линии ЭСАБ:
1) подать листы листоукладчиком на магнитную балку;
2) сориентировать листы с осью магнитной балки;
3) выровнять магнитами кромки по толщине;
4) закрепить листы на прихватках;
5) переместить полотнище на ширину листа;
6) аналогично состыковать остальные листы полотнища.
|
17
|
Установка выводных планок:
1) установить и приварить по концам стыковых швов, подлежащих сварке автоматом или полуавтоматом под флюсом, выводные планки размером 100X100 мм, толщиной, одинаковой со свариваемыми конструкциями;
2) при наличии технологического припуска не менее 50 мм установку планок можно не производить
|
7
|
Сдача конструкции под сварку:
1) проверить правильность сборки согласно чертежам и плазовым данным;
2) проверить правильность подготовки кромок под сварку;
3) проверить чистоту кромок. В случае их загрязнения очистить в соответствии с ОСТ5.9092—81
|
111
|
Кантование кантующим устройством |
151
|
Подварка швов:
1) подготовить сварные швы корпусных конструкций и насыщения для подварки;
2) подварить сварные швы в последовательности, аналогичной сварке основного шва
|
10
|
Контроль сварных швов:
1) осуществить контроль сварных швов в соответствии ОСТ5.1093—78 и схемой контроля сварных швов;
2) исправить дефекты сварных швов в соответствии с ОСТ5.1078—76
|
152
|
3амеры секции или узла согласно ОСТ5.9324—79 |
153
|
Сдача секции или узла на комплектность и качество |
156
|
Маркирование. Выполнить маркирование секции или узла с лицевой и внутренней стороны белой краской. Маркировку обрести краской |
II. Изготовление секции
Предварительно изготовляемые узлы:
1) полотнище настила;
2) рамный набор.
Последовательность выполнения работ:
Шифр работ |
Наименование и содержание работы |
35 |
Разметка полотнища. Провести разметку полотнища согласно ОСТ 5.9324-79. Линии разметки накернить. |
112 |
Разворот полотнища на 90° устройством линии. |
113 |
Установка и приварка набора главного направления к полотнищу на механизированных линиях:
1) подать полотнище к агрегату автоматической приварки набора, провести ориентацию полотнища относительно оси агрегата;
2) создать упругий выгиб полотнища включением электромагнитов с выдвижением стоек балки выгиба;
3) передать с помощью устройства первую балку набора главного направления в систему установки набора агрегата;
4) установить первую балку набора на полотнище с помощью системы установки набора агрегата, ориентируя торец балки набора по линии разметки;
5) подвести один сварочный автомат агрегата к началу балки набора, второй автомат к середине балки, приварить балки набора к полотнищу одновременно с двух сторон двумя автоматами
6) переместить полотнище на шаг под установку слудующего ребра;
7) аналогично установить остальные рёбра набора;
8) зачистить сварные швы от шлака;
9) передать полотнище с установленным набором на очередную позицию линии.
|
115 |
Установка перекрёстного набора агрегатом. Захватить агрегатом из кассеты балку перекрёстного направления или высокого набора, навести на линию разметки, прижать и закрепить к полотнищу прихватками. |
64 |
Установка деталей россыпи. Установить детали россыпи согласно чертежам и прикрепить прихватками. |
7 |
Сдача конструкции под сварку:
1) проверить правильность сборки согласно чертежам и плазовым данным;
2) проверить правильность подготовки кромок под сварку;
проверить чистоту кромок. В случае их загрязнения очистить в соответствии с ОСТ5.9092 – 81.
|
114 |
Сварка набора полуавтоматами, размещёнными на сварочных стрелах:
1) сварить набор. Сварку выполнить от середины секции к краям, сначала набора между собой, затем с полотнищем;
2) переместить секцию на следующую позицию.
|
142 |
Установка и приварка доизоляционного насыщения:
1) разместить места установки насыщения;
2) сделать вырезы, зачистить кромки;
3) установить насыщение согласно чертежу;
4) сдать установку насыщения под сварку;
5) приварить насыщение полуавтоматом в двуокиси углерода или вручную, выполняя сварку симметрично относительно продольной и поперечной осей секции.
|
144 |
Установка и приварка обухов для кантования и транспортирования:
1) установить обухи в соответствии со схемой кантовки и транспортирования секции, сдать под сварку;
2) раскрепить при необходимости секцию временными рёбрами жесткости;
3) приварить обухи;
4) приварить набор корпусной конструкции в районе обухов в объёме, предусмотренном схемой кантования и транспортирования секции.
|
10 |
Контроль сварных шов:
1) осуществить контроль сварных швов в соответствии с ОСТ5.1093-78 и схемой контроля сварных швов;
2) исправить дефекты сварных швов в соответствии с ОСТ5.1078-76.
|
111 |
Кантование кантующим устройством |
143 |
Установка и приварка доизоляционного насыщения после кантования секции. Выполнить с обратной стороны секции установку и приварку корпусного насыщения аналогично работе 142. |
151 |
Подварка швов:
1) подготовить сварные швы корпусных конструкции и насыщения для подварки;
2) подварить сварные швы в последовательности, аналогичной сварке основного шва.
|
10 |
Контроль сварных шов:
1) осуществить контроль сварных швов в соответствии с ОСТ5.1093-78 и схемой контроля сварных швов;
2) исправить дефекты сварных швов в соответствии с ОСТ5.1078-76.
|
111 |
Кантование кантующим устройством |
149 |
Снятие секции или узла с оснастки. Снять секцию или узел краном, подать на сборочный стенд или площадку для сдачи и доделки, установить секцию или узел на опоры. |
147 |
Контуровка:
1) проверить габаритные размеры секции или узла;
2) удалить припуски по кромкам секции газовой резкой, разделать кромки под сварку согласно чертежу, зачистить кромки.
|
148 |
Нанесение контрольных линий. Нанести контрольные линии согласно ОСТ 5.9324 – 79, накернить их, отметить краской. |
152 |
Замеры секции или узла согласно ОСТ 5.9324-79. |
153 |
Сдача секции или узла на комплексность и качество. |
154 |
Испытание на непроницаемость сварных швов. В соответствии с ОСТ 5.1180-87 испытать керосином сварные швы непроницаемых конструкции. |
156 |
Маркирование. Выполнить маркирование секции или узла с лицевой и внутренней стороны белой краской. Марки обвести краской. |
155 |
Грунтовка секции:
1) провести грунтовку секции согласно ведомости грунтовки и ОСТ 5.9566 – 83 монтажные кромки шириной 50 – 75 мм не грунтовать;
2) восстановить контрольные линии, нанесенные на секции, отметить их белой краской.
|
6.2 Контроль качества сварных соединений
Качество сварных швов регламентируется стандартами и техническими условиям на сварные соединения. Отклонения от требуемых норм считаются дефектами.
Дефекты уменьшают прочность и плотность твои и могут принести к разрушению сварных соединений. В зависимости от месторасположения дефекты разделяют на наружные и внутренние.
Наружными дефектами
считают дефекты формы шва: неравномерность сечения по длине, отклонения размеров катетов, вогнутость корня, смещение, непровары, наплывы, подрезы, прожоги, поры на поверхности, трещины.
К внутренним дефектам
относят пористость, неметаллические включения, несплавления, непровары, внутренние трещины (рис. 6.2).
Основными причинами образования дефектов являются нарушения технологии сборки и сварки, применение несоответствующих сварочных материалов, неправильный выбор режимов сварки, низкая квалификация сварщика. Причинами возникновения дефектов могут быть также влияние неучтенных факторов на физико-химические процессы при остывании и кристаллизации шва.
Оценка качества сварных швов производится по трехбалльной системе: высшее качество — балл 3, хорошее качество — балл 2, швы с баллом 1 подлежат исправлению.
Контроль качества сварных соединений заключается в выявлении факторов, которые могут привести к образованию дефектов (предупреждающий контроль), и контроле продукции с целью обнаружения дефектов. К предупреждающему контролю относят контроль основного металла, электродов, проволоки, флюсов, контроль применяемого оборудования и проверку квалификации сварщиков.
Одним из весьма распространенных способов контроля является внешний осмотр. Внешним осмотром проверяют подготовку под сварку, правильность сборки, наличие и расположение прихваток, качество разделки, величину зазоров.
После сварки внешним осмотром выявляют наружные дефекты. Для этого сварной шов очищают от остатков шлака, окалины, брызг и других загрязнений. При внешнем осмотре швы замеряют измерительным инструментом и специальными шаблонами. При этом проверяют ширину и высоту усиления в стыковых швах, величину катетов в угловых швах.
Наружные дефекты, невидимые при внешнем осмотре (микротрещины, поры), могут быть обнаружены посредством проведения капиллярной дефектоскопии — смачивания швов специальными растворами с последующего воздействия на деталь ультрафиолетовыми лучами. Сквозные трещины, неплотности, свищи выявляют с помощью различных методов проверки швов на плотность: гидравлическим давлением, наливом и поливом воды или керосина на мел. Плотность сварных швов проверяется при гидравлических и пневматических испытаниях корпуса на непроницаемость.

Рисунок 6.2 Виды внутренних дефектом сварных швов: а— поры и свищи;
б — шлаковые включения; в — несплавление; г —непровар; д— трещины
Внутренние дефекты обнаруживают с помощью различных физических методов контроля: радиационного контроля, акустического контроля (ультразвукового метода), электромагнитной дефектоскопии.
Для данной секции применяем контроль сварных швов: ультразвуковой контроль и радиационный контроль.
Радиационный контроль заключается в изображении на фотопленке внутренней структуры сварного шва, просвечиваемого ионизирующим излучением. Из способов радиационного контроля в судостроении наиболее распространены рентгеновский контроль и контроль гамма-лучами.
Радиационный контроль основан на различном поглощении ионизирующих лучей металлом и неметаллическими включениями. При этом более плотные металлические включения на снимке выглядят более светлыми пятнами и точками. Так же и шов на снимке получается более светлым, чем околошовная зона, поскольку он имеет большую толщину, чем сваренный металл. Дефекты шва (трещины, норы) поглощают лучи в меньшей степени, чем металл. Поэтому на светлом фоне шва они выделяются темными пятнами, точками, полосами.
Ультразвуковой контроль основан на способности ультразвуковых колебаний проникать в толщину металла и отражаться от неметаллических включений и дефектов, которые имеют иное, чем металл, акустическое сопротивление. От границ трещин и пор отражается до 90 % энергии ультразвуковых колебаний. Дефектоскопы, работающие по эхо-методу, оснащены осциллографами, на экране которых по отраженному сигналу определяют характер дефекта. Кроме того, эти дефектоскопы снабжены электронными глубиномерами, с помощью которых определяют место дефекта.
6.3 Проверочные работы
К проверочным относятся специфические для судостроения работы, заключающиеся в разметке базовых, осевых, эксплуатационных, контрольных линий и в проверке размеров, формы и пространственного положения отдельных частей и всего корпуса судна в процессе изготовления и монтажа. Проверочные работы проводят также с технологической оснасткой для изготовления корпусных конструкций и для формирования корпуса на построечном месте.
Проверочные операции выполняются в ходе сборочных работ, а также и после окончания сборки для контроля положения конструкций, находящихся на построечном месте. Дело в том, что вследствие просадки под действием силы тяжести, от укорочения сварных швов, а также от смены наружной температуры положение некоторых частей корпуса может изменяться. Проверщики должны регулярно контролировать это положение и принимать необходимые меры и по его корректировке. По существующим нормам проверку положения корпуса на стапеле, а именно координат килевой линии и отсутствие крена, производят один раз каждые 7—10 дней и записывают в журнале.
Проверку производят также перед сваркой фундаментов под главные механизмы и валопровод, перед испытанием корпуса наливом и перед монтажом ответственных механизмов и устройств;
Проверка стапеля и всех устанавливаемых конструкций, как правило, производится с помощью оптических приборов — теодолитов или специально разработанных для судостроения стапельных визиров. Оптические приборы начинают применять.
Применяемый для проверки теодолит типа Т-5 (и более точный Т-2) представляет собой переносной геодезический прибор (массой около 5 кг), укрепляемый на штативе. Прибор состоит из измерительной трубы (с увеличением в 27 раз) с пределами визирования от 2 м, закрепленной на горизонтальной оси.
Труба с осью закреплены в корпусе, вращающемся на вертикальной оси, что позволяет производить отсчеты в горизонтальной плоскости. На основании прибора имеется уровень, с помощью которого можно располагать прибор строго по горизонту.
Для возможности работы в активном режиме такие приборы имеют или обычный световой источник, или лазер (источник концентрированного светового луча). С их помощью на проверяемый объект можно спроецировать световую точку, и по ее положению судить о расхождениях при установке объекта.
1. Проверка длины и ширины после окончания сварочных работ не менее в 3-х точках, совпадающих со средней и крайними балками набора и монтажными кромками.
2. Проверка диагонали.
3. Проверка изгиба секции (после сварки по крайним балкам набора вдоль и поперек секции).
4. Проверка положения контрольных линий.
5. Проверка бухтиноватости обшивки на участках между набором.
Проверочные работы производить инструментом:
Метр складной металлический ТУ 105-093-007-77 и ТУ 206-УССР-49-77.
Рулетка измерительная металлическая ГОСТ 7502-80.
Карандаш маркировочный типа КМ ОСТ 5.9716-78.
Отвесы стальные строительные ГОСТ 7948-80.
Трубка шлангового уровня типа ТШУ ОСТ 5.9716-78.
Чертилки проволочные ГОСТ 24.473-80.
Бухтиномеры типа БМ ОСТ 5.
7 РАСЧЕТ ТРУДОЕМКОСТИ ИЗГОТОВЛЕНИЯ ПЛОСКОЙ СЕКЦИИ
7.1 Расчет трудоёмкости изготовления секции при существующей механизированной линии.
7.1.1 Сборка полотна
Тн
= L1
× (K1
+ K2
),
где: K1
= 0,33 ч - время сборки на один погонный метр;
K2
= 0,18 ч - коэффициент при стыковании, обжатии кромок без набора;
L1
= 30 м - длина стыкующихся кромок;
Тн
= 30×(0,33+0,18) = 15,3 часов
7.1.2 Сварка полотна
Тн
= L2
× К3
где: К3
= 0,094 ч - сварка полотна;
L2
= 30 м - длина шва стыкующихся кромок;
Тн
= 30 × 0,094 = 2,82 часов.
7.1.3 Разметка
Разметка составляет 20% от трудоемкости сборки полотна
Тн
=3,06 часов.
7.1.4 Установка набора главного направления
Время установки набора профиля на полотнище с выставленным набором:
Тн
= L3
×K4
,
где: L3
= 7920×4+6500×8 = 83680 мм = 83,68м - длина набора главного направления;
К4
= 0,56 ч - время установки набора;
Тн
= 83,68 × 0,56 = 46,86 часов;
7.1.5 Приварка набора главного направления в зависимости от типа сварки и расположения швов
Тн
= L4
×K5
×n,
где:
n - двусторонний шов;
K5
= 0,096 ч - сварка главного набора;
L4
= 83,68 м – длина шва;
Тн
= 83,68 ×0,096 × 2 = 16,07 часов;
7.1.6 Установка перекрестного набора
Тн
= L6
×K6
где: К6
= 0,56 ч – время установки набора;
L6
= 19,96 м – длина перекрестного набора;
Тн
= 0,56 × 19,96 = 11,18 часов;
7.1.7 Сварка перекрестного набора
Тн
=L7
× K7
× n
где: L7
= 19,96 м - длина шва перекрестного набора;
К7
= 0,096 ч - сварка перекрестного набора;
n - двусторонний шов;
Тн
= 19,96 × 0,096 × 2 = 3,83 часов;
7.1.8
Установка и приварка насыщения,
укрупнение, проверочные работы, сдача секции
Тн
= 10 % от сборки полотна
Тн
= 1,53 часов.
7.2 Трудоёмкость изготовления секции на механизированной линии.
В этом пункте производится пересчёт трудоёмкости изготовления секции со стенда на механизированную линию, используя коэффициенты корректировки трудоёмкости. Коэффициенты корректировки трудоёмкости по операциям полностью или частично определяются путём сопоставления норм трудоёмкости с расчётами, определёнными исходя из объёмов работ и характеристик оборудования. Коэффициенты трудоёмкости приняты:
К1
= 0,57 - сборка полотна. За счёт оборудования позиции перегружателем для подачи и ориентирования листов полотна и стенда, обеспечивающих механизированное обжатие кромок.
К2
=0,55 – сварка полотна. За счёт оборудования позиции сварочные стендом, обеспечивающее обжатие свариваемых кромок и одностороннюю автоматическую сварку стыков и пазов полотнища. С образованием форм шва.
К3
=0,80 – за счёт создания специальных линий, либо улучшения организации труда.
К4
=0,49 – установка и приварка набора главного направления. За счет оборудования позиции агрегатом, обеспечивающим механическую установку, обжатие и автоматическая приварка набора одновременно с 2х сторон (АПН16).
К5
=0,70 – установка перекрёстного набора за счёт применения агрегата для подачи, установки и механизации обжатия набора.
К6
=0,80 – сварка перекрёстного набора. За счёт применения стрел для подачи сварочных автоматов к местам сварки, улучшение организации труда.
К7
=0,90 - за счёт создания специальных линий, либо улучшения организации труда.
Расчёт представлен в таблице 7.1
Таблица 7.1 - Технологическая трудоемкость
№ |
Наименование операции |
Трудоемкость,
часы
|
Коэффициент механизации |
Трудоемкость на механиз. линии
(3)×(4)
нормо-час
|
Трудоемкость на сварочном стенде (5)/1,1
человеко-час
|
1 |
2 |
3 |
4 |
5 |
6 |
1 |
Сборка полотна |
15,3 |
0,57 |
8,72 |
7,93 |
2 |
Сварка полотна |
2,82 |
0,55 |
1,55 |
1,41 |
3 |
Разметка |
3,06 |
0,80 |
2,45 |
2,23 |
4 |
Установка и сварка набора главного направления |
62,93 |
0,49 |
30,84 |
28,03 |
5 |
Установка перекрестного набора |
11,18 |
0,70 |
7,83 |
7,12 |
6 |
Сварка перекрестного набора |
3,83 |
0,80 |
3,06 |
2,79 |
7 |
Установка и приварка насыщения, укрупнение, проверка, сдача |
1,53 |
0,90 |
1,38 |
1,25 |
8 |
Итого |
100,65 |
4,81 |
55,82 |
50,75 |
Вывод:
После проведения расчета трудоемкости изготовления плоской секции получены данные каждого этапа изготовления секции, результаты которого занесены в таблицу. На сборочном сварочном стенде трудоемкость изготовления составила 50,75 часов, а на механизированной линии 55,82 нормо-часов.
8 РАЗМЕРНЫЙ АНАЛИЗ СЕКЦИИ
Размерным анализом постройки (формирование корпуса судна) называется расчётное определение требуемой точности элементов конструкции.
Размерной цепью называется совокупность размеров, образующих замкнутый контур и непосредственно участвующих в решении поставленной задачи.
В цепи различают два вида звеньев:
1) составляющие, которые получились непосредственно при изготовлении детали;
2) замыкающие, которые получились последние при обработке детали (по детализации цепи) и при сборке узла (в сборочной цепи), и величины которых зависят от величины всех остальных звеньев.
Составляющие звенья по-разному влияют на замыкающее звено. Если при увеличении составляющего звена замыкающее звено увеличивается, то такое звено называется увеличивающим. Если при увеличении составляющего звена замыкающее звено уменьшается, то такое звено – уменьшающееся.
Расчёт размерных цепей сводится к решению задач, называемых прямой и обратной. В прямой задаче на основании заданных требований к величине замыкающего звена рассчитываются все данные составляющие звеньев (отклонения и допуски).
В обратной задаче расчёт предельных отклонений и допусков на замыкающее звено по заданным отклонениям и допускам всех составляющих звеньев.
8.1 Цели размерного анализа являются
8.1.1 определение количественной взаимосвязи между точностью изготовлением секции и точностью построения корпуса судна;
8.1.2 назначение обоснования технологических допусков на форму и размеры секции и их установка на стапеле;
8.1.3 определение монтажных соединений корпуса, которые целесообразно предварительно контуровать по данным с плаза или чертежа и собирать на стапеле без монтажных припусков;
8.1.4 определение монтажных соединений корпуса, по которым следует оставлять монтажные припуски, удаляемые до установки секции на стапель по замерам с места;
8.1.5 определение монтажных соединений корпуса, по которым следует оставлять монтажные припуски, удаляемые после установки секции на стапель по замерам с места;
8.1.6 расчёт величины монтажных припусков;
8.1.7 уточнить номинальность размеров корпусных конструкций с учётом случайных и системных погрешностей при изготовлении и установке;
8.1.8 анализ конструкционно-технологических факторов с точки зрения их влияния на точность изготовления и установки корпусных конструкций.
Последовательность выполнения размерного анализа:
подготовка исходных данных;
· выявление требований к точности размеров и форме корпуса судна, фиксирование этих требований в виде замыкающих звеньев размерной цепи;
· выявить составляющие звеньев, составить эскизы размерной цепи;
· составить уравнения размерной цепи;
· назначение дополнительных отклонений замыкающих звеньев;
· назначение дополнительных отклонений составляющих звеньев;
· определение половины поля рассеивания размеров замыкающих звеньев;
· сравнение полученных расчётных значений половины поля рассеивания размеров замыкающих звеньев с дополнительными отклонениями;
· выполнить способность обеспечения требований точности составляющих звеньев;
· выбор способа обеспечения требований точности замыкающего звена;
· определение объёма подготовки по стыку монтажных соединений;
· назначение номинальных размеров составляющих звеньев и замыкающего звена;
· уточнение номинальных размеров составляющих звеньев и замыкающего звена;
· оформление результата анализа в табличной форме.
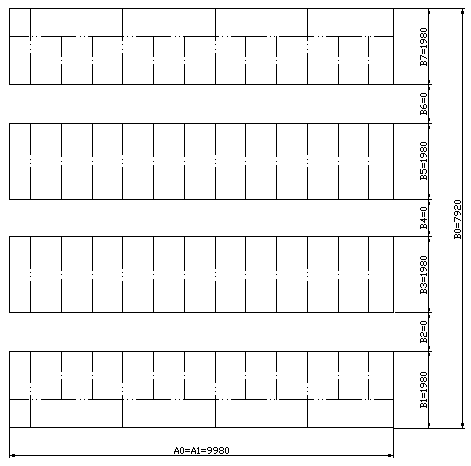
Рисунок 8.1.1 - Расчётная схема размерного анализа секции
Расчет погонной энергии сварки.
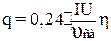



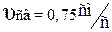

Таблица 8.1 - Исходные данные.
Процент риска |
32 |
Коэффициент риска |
1 |
Кол-во составляющих звеньев |
1 |
7 |
Обозначения звеньев |
A0
|
A1
|
B0
|
B1
|
B2
|
B3
|
B4
|
B5
|
B6
|
B7
|
Наименование звена |
Длина секции |
Лист |
Ширина секции |
Лист |
Зазор |
Лист |
Зазор |
Лист |
Зазор |
Лист |
Относит. СКВО |
– |
0,111 |
– |
0,111 |
0,167 |
0,111 |
0,167 |
0,111 |
0,167 |
0,111 |
Номинальный размер звена |
9980 |
9980 |
7920 |
1980 |
0 |
1980 |
0 |
1980 |
0 |
1980 |
Допуск на размер |
2 |
2 |
2 |
2 |
3 |
2 |
3 |
2 |
3 |
2 |
Предельное отклонение |
верхнее |
+1 |
+1 |
+1 |
+1 |
+1 |
+1 |
+1 |
+1 |
+1 |
+1 |
нижнее |
-2 |
-1 |
-2 |
-1 |
-2 |
-1 |
-2 |
-1 |
-2 |
-1 |
Кол-во попереч. РЖ |
12 |
12 |
2 |
1 |
– |
– |
– |
– |
– |
1 |
Укороче-ние сварного. шва |
– |
– |
– |
– |
1,38 |
1,38 |
1,38 |
1,38 |
1,38 |
– |
Укороче-ние секции от приварки РЖ |
0,05 |
0,05 |
0,05 |
0,05 |
– |
– |
– |
– |
– |
0,05 |
ТАБЛИЦА 8.2
РАСЧЕТ СОСТАВЛЯЮЩИХ ЗВЕНЬЕВПО ДЛИНЕ СЕКЦИИ 0 ┌────────┬─────────┬─────────┬───────────────┬─────────┬─────────┐
│НОМЕР │НОМИНАЛ. │ДОПУСК НА│ПРЕД.ОТКЛОН.,ММ│СЕРЕДИНА │ОТНОСИТ. │
│ЗВЕНА │РАЗМЕР,ММ│РАЗМЕР,ММ│ВЕРХНЕЕ│НИЖНЕЕ │ПОЛЯ.ДОП │ СКВО │
├────────┼─────────┼─────────┼───────┼───────┼─────────┼─────────┤
│ 1 │ 2 │ 3 │ 4 │ 5 │ 6 │ 7 │
├────────┼─────────┼─────────┼───────┼───────┼─────────┼─────────┤
│ A 0 │ 9980.0 │ 3.00 │ 1.00│ -2.00│ 1.50 │ 0.0000 │
│ A 1 │ 9980.0 │ 2.00 │ 1.00│ -1.00│ 1.00 │ 0.1110 │
└────────┴─────────┴─────────┴───────┴───────┴─────────┴─────────┘
ПРОДОЛЖЕНИЕ ТАБЛИЦЫ 8.2
┌───────┬───────┬───────────────────────┬───────┬──────────┬──────┐
│НОМЕР │КОЛИЧ │ПОПЕРЕЧ.СВАР.УКОРОЧЕНИЯ│СВАРОЧ.│ПОПЕРЕЧНОЕ│РАЗМЕР│
│ │ПОПЕР │ОТ ОДНОГО ПО│ОТ ПРОДОЛ.│ЗАЗОР │УКОРОЧЕНИЕ│ЗВЕНА │
│ЗВЕНА │ РЖ │ПЕРЕЧН.РЖ,ММ│ РЖ,ММ │ ММ. │СВАРН.ШВА │ ММ. │
├───────┼───────┼────────────┼──────────┼───────┼──────────┼──────┤
│ 8 │ 9 │ 10 │ 11 │ 12 │ 13 │ 14 │
├───────┼───────┼────────────┼──────────┼───────┼──────────┼──────┤
│ A 0 │ 12 │ 0.05 │ 0.00 │ 0 │ 0.00 │9980.0│
│ A 1 │ 12 │ 0.05 │ 0.00 │ 0 │ 0.00 │9980.5│
└───────┴───────┴────────────┴──────────┴───────┴──────────┴──────┘
ЗАДАННЫЙ ДОПУСК ЗАМЫКАЮЩЕГО ЗВЕНА....: 3
РАСЧЕТНЫЙ ДОПУСК ЗАМЫКАЮЩЕГО ЗВЕНА...: 0.666
ПРОЦЕНТ РИСКА........................: 32
КОЭФФИЦИЕНТ РИСКА....................: 1
УРАВНЕНИЕ РАЗМЕРНОЙ ЦЕПИ:
A0=+A 1
ТАБЛИЦА 8.3
РАСЧЕТ СОСТАВЛЯЮЩИХ ЗВЕНЬЕВПО ШИРИНЕ СЕКЦИИ 0
┌────────┬─────────┬─────────┬───────────────┬─────────┬─────────┐
│НОМЕР │НОМИНАЛ. │ДОПУСК НА│ПРЕД.ОТКЛОН.,ММ│СЕРЕДИНА │ОТНОСИТ. │
│ЗВЕНА │РАЗМЕР,ММ│РАЗМЕР,ММ│ВЕРХНЕЕ│НИЖНЕЕ │ПОЛЯ.ДОП │ СКВО │
├────────┼─────────┼─────────┼───────┼───────┼─────────┼─────────┤
│ 1 │ 2 │ 3 │ 4 │ 5 │ 6 │ 7 │
├────────┼─────────┼─────────┼───────┼───────┼─────────┼─────────┤
│ A 0 │ 7920.0 │ 2.00 │ 1.00│ -2.00│ 1.00 │ 0.0000 │
│ A 1 │ 1980.0 │ 2.00 │ 1.00│ -1.00│ 1.00 │ 0.1110 │
│ A 2 │ 0.0 │ 3.00 │ 1.00│ -2.00│ 1.50 │ 0.1670 │
│ A 3 │ 1980.0 │ 2.00 │ 1.00│ -1.00│ 1.00 │ 0.1110 │
│ A 4 │ 0.0 │ 3.00 │ 1.00│ -2.00│ 1.50 │ 0.1670 │
│ A 5 │ 1980.0 │ 2.00 │ 1.00│ -1.00│ 1.00 │ 0.1110 │
│ A 6 │ 0.0 │ 3.00 │ 1.00│ -2.00│ 1.50 │ 0.1670 │
│ A 7 │ 1980.0 │ 2.00 │ 1.00│ -1.00│ 1.00 │ 0.1110 │
└────────┴─────────┴─────────┴───────┴───────┴─────────┴─────────┘
УРАВНЕНИЕ РАЗМЕРНОЙ ЦЕПИ: A0=+A 1 +A 2 +A 3 +A 4 +A 5 +A 6 +A 7
ПРОДОЛЖЕНИЕ ТАБЛИЦЫ 8.3
┌───────┬───────┬───────────────────────┬───────┬──────────┬──────┐
│НОМЕР │КОЛИЧ │ПОПЕРЕЧ.СВАР.УКОРОЧЕНИЯ│СВАРОЧ.│ПОПЕРЕЧНОЕ│РАЗМЕР│
│ │ПОПЕР │ОТ ОДНОГО ПО│ОТ ПРОДОЛ.│ЗАЗОР │УКОРОЧЕНИЕ│ЗВЕНА │
│ЗВЕНА │ РЖ │ПЕРЕЧН.РЖ,ММ│ РЖ,ММ │ ММ. │СВАРН.ШВА │ ММ. │
├───────┼───────┼────────────┼──────────┼───────┼──────────┼──────┤
│ 8 │ 9 │ 10 │ 11 │ 12 │ 13 │ 14 │
├───────┼───────┼────────────┼──────────┼───────┼──────────┼──────┤
│ A 0 │ 0 │ 0.00 │ 0.00 │ 0 │ 0.00 │7920.0│
│ A 1 │ 1 │ 0.05 │ 0.00 │ 0 │ 0.00 │1980.1│
│ A 2 │ 0 │ 0.00 │ 0.00 │ 0 │ 0.00 │ 0.0│
│ A 3 │ 0 │ 0.00 │ 0.00 │ 0 │ 1.38 │1981.4│
│ A 4 │ 0 │ 0.00 │ 0.00 │ 0 │ 0.00 │ 0.0│
│ A 5 │ 0 │ 0.00 │ 0.00 │ 0 │ 1.38 │1981.4│
│ A 6 │ 0 │ 0.00 │ 0.00 │ 0 │ 0.00 │ 0.0│
│ A 7 │ 1 │ 0.05 │ 0.00 │ 0 │ 0.00 │1980.1│
└───────┴───────┴────────────┴──────────┴───────┴──────────┴──────┘
ЗАДАННЫЙ ДОПУСК ЗАМЫКАЮЩЕГО ЗВЕНА....: 2
РАСЧЕТНЫЙ ДОПУСК ЗАМЫКАЮЩЕГО ЗВЕНА...: 2.51
ПРОЦЕНТ РИСКА........................: 32
КОЭФФИЦИЕНТ РИСКА....................: 1
УРАВНЕНИЕ РАЗМЕРНОЙ ЦЕПИ:
A0=+A 1 +A 2 +A 3 +A 4 +A 5 +А 6 +А 7 +А 8 +А 9
9 УСЛОВИЯ И МЕТОД ПОСТРОЙКИ СУДНА. СУХОЙ ДОК.
9.1 Условия постройки судна
Выбранное судно строится в сухом доке блочным методом.
места. Оборудование в эти блоки заводится с торцов, так как через палубные вырезы погрузка часто невозможна. Применение этого метода постройки позволяет сократить продолжительность работ на стапеле, перенести их в более удобные цеховые условия, расширит фронт работ, так как блоки можно изготовлять параллельно.
Для стыкования корпуса на построечном месте весьма важно обеспечить плавность обводов в районе монтажного стыка. Поэтому при изготовлении каждого блока вводится специальная операция – контроль формы по стыкуемой кромке. При правильной форме обеих кромок на стыке между двумя блоками не получится уступов, завалов или разностесненности.
9.2 Описание спуска судна на воду.
Док заполняется водой самотеком через клинкеты батопорта (затвора). Всплывшее судно выводится из дока буксирами.
При необходимости судно удифферентовывают на ровный киль приемом водяного балласта в носовые отсеки.

9.3 Методы постройки судна
Формирование корпуса на построечном месте начинается с установки блоков, поверки положения и сварки этих конструкций; затем устанавливают фундаменты, надстройки, испытывают корпус на непроницаемость и герметичность и осуществляют спуск судна. Постройка судна выполняется на одной позиции (без перемещения судна).
Характеристика сухого дока и оборудования:
Сухой док представляет собой вырытую в грунте ниже уровня акватории забетонированную камеру, отделенную от акватории протапливаемым батопортом или откидывающимся на горизонтальных осях затвором. Осушается док насосами.
Построечные места оборудуются:
— опорными устройствами для опирания судов в процессе постройки;
— подъемно-транспортными средствами — кранами для выполнения подъемно-транспортных операций;
— лесами - наружными и внутренними для производства работ на высоте;
— системами энергоснабжения для подачи на строящееся судно электроэнергии, сжатого воздуха, кислорода и ацетилена, углекислого газа, воды и пара.
Построечные места обеспечиваются различными источниками энергии для выполнения работ, в том числе:
а) электроэнергией — переменным током напряжением 380 В для питания электродвигателей крапов и сварочных постов; напряжением 127 и 220 В для общего постоянного освещения и для питания электродвигателей вентиляторов, отсасывающих вредный воздух при сварочных, очистных, малярных и других работах; напряжением 36, 24, 12 и 6 В — для переносных ламп. Ток подается от трансформаторных подстанций на силовые щиты построечного места. Для питания кранов ток подводится по гибким кабелям, уложенным в троллейных каналах вдоль рельсового пути;
б) сжатым воздухом давлением 0,5—0,6 МПа (5 — 6 кгс/см2
) для работы пневматического инструмента и краскораспылителей. Воздух подается по постоянным магистральным трубопроводам от компрессорной станции через влагомаслоотделители — отстойники на разделительные коробки, к которым приворачивают гибкие переносные шланги, соединенные с инструментом;
в) кислородом и ацетиленом для газовой резки и строжки и для нагрева корпусных конструкций при их правке. Кислород и ацетилен подают по постоянным проложенным трубопроводам, либо доставляют в баллонах к местам выполнения работ;
г) углекислым газом и аргоном для ручной, полуавтоматической и автоматической сварки. Газ подается тоже по трубопроводам или в баллонах;
д) паром для отопления судовых помещений в холодное время года;
е) водой для гидравлических испытаний отсеков, "противопожарных целей и других нужд.
Кабели и трубопроводы прокладывают вдоль всего построечного места с обеих сторон судна, а посты для подключения к магистралям энергосистем оборудуют на колоннах лесов и площадках построечного
Опорные устройства построечных мест, когда судно строится на одной позиции без перемещения, состоят из кильблоков, клеток, подстав и упоров, а на наклонном продольном стапеле, кроме того, из строительных стрел, препятствующих смещению судна. Кильблоки должны воспринимать вес всего судна. Кильблоки типа показанного на рис. 9.2 а, состоят из стальных сварных тумб, поверх которых находится сосновая прокладка, деревянные клинья и сосновая подушка. Применяются также кильблоки с быстро-разборным элементом (рис. 9.2, б), состоящим из двух стальных клиновых призм, соединенных между собой тягой из стальных угольников.

Рисунок 9.2 Типы кильблоков: а
– из металлических тумб; б
– быстроразборный.
1
– сосновая прокладка; 2
– сосновая подушка; 3
– деревянные клинья; 4
– стальные сварные тумбы; 5
– клиновая призма; 6
– тяга; 7
– стальной клин; 8
– стопорная планка.
Тяга стопорится самотормозящимся стальным клином. Для отдачи кильблока клин выбивают. На наклонном продольном стапеле могут также применяться кильблоки, у которых основным элементом является гидравлический домкрат. В цилиндр домкрата подается масло под высоким давлением с помощью гибкого шланга, подключенного к общей системе стапельного гидропривода. Эта система, состоящая из насосной станции и трубопроводов, позволяет осуществлять дистанционный контроль давления на каждом кильблоке, его просадки и управлять высотой кильблока, не прибегая к ручной подклинке. Кильблоки с гидравлическими домкратами позволяют легко пересадить судно па спусковое устройство путем стравливания масла из цилиндров.
Простейшие кильблоки представляют собой просто набор коротких сосновых брусьев с клиньями. Встречаются и железобетонные кильблоки, и состав которых входят сосновая прокладка, клинья и сосновая подушка. Высоту кильблока в ходе постройки регулируют подклинкой, относящейся к тяжелым ручным операциям.
Кильблоки располагаются в диаметральной плоскости судна под флорами и поперечными переборками.
Клетки обеспечивают устойчивость судна на построечном месте и разносят сосредоточенные нагрузки от массы сосредоточенных грузов, например, главных механизмов или воды (при испытаниях отсеков водой) на большую площадь. Клетки состоят из тех же элементов, что и кильблоки, но отличаются от них большими размерами в плане. Клетки располагают, как правило, под поперечными переборками.
Подставы и упоры также разносят вес судна на большую площадь основания построечного места и, кроме того, они используются для выравнивания днищевых секций в процессе установки последних. Стальные подставы представляют собой трубчатый винтовой домкрат или имеют телескопическую конструкцию, а упоры просто сосновые брусья, поставленные стоймя.
К подъемно – транспортным средствам на построечных местах относятся различные краны, в том числе козловые, мостовые, башенные и портальные.
При постройке судна на наклонном стапеле применяются башенные и портальные краны.
Башенные краны, грузоподъемность которых от 20 до 250 т, имеют неповоротную вертикальную башню и консольную поворотную стрелу, по которой перемещается грузовая тележка.
Портальные краны имеют прямые или шарнирно-сочлененные стрелы. Их основание имеет вид портала, откуда и пошло название. Грузоподъемностью таких кранов на построечных местах составляет от 20 до 100 т.
Захват и подъем секций и блоков осуществляются стальными канатами, которые при помощи скоб прикрепляют крымам, приваренным к секциям и блокам. После установки секции и блоков на построечное место рымы срезают тепловой резкой.
На построечных местах применяют наружные, а в отсеках судна внутренние леса. Конструкции лесов весьма разнообразны.
В состав наружных сплошных лесов входят металлические стойки (чаще всего трубчатые), щитовые деревянные пастилы, леера, переносные башни с трапами и поярусными площадками и переходные мостики между ними. Для крупных судов в состав лесов входят грузовые и пассажирские электрические лифты. Применяются сплошные облегченные стоечные трубчатые леса быстроразборной конструкции.
Традиционные сплошные наружные леса иногда заменяют подвесными люльками пли передвижными самоходными или несамоходными многоярусными лесами-башнями, устанавливаемыми только в районе выполнения работ. Передвижные леса передвигаются на рельсах или на пневматическом ходу. Некоторые имеют телескопически выдвигаемую платформу, исключающую необходимость в ярусах.
Состав внутренних лесов определяется в основном высотой отсеков и развитостью их люковых проемов. В отсеках высотой до 3,5 м устанавливают деревянные щиты на металлических козлах или одиночные складные столы. В отсеках высотой более 3,5 м, но менее 8 м с люковыми проемами, комингсы которых отстоят от борта или переборки на расстояниях до 4,5 м, приходится возводить трубчатые леса со щитовым настилом. Для выполнения небольшого объема работ ограничиваются передвижной площадкой, поднимаемой лебедкой.
В отсеках высотой более 8 м применяют леса на кронштейнах, навешиваемых ярусами на переборки и борта на приварных зацепах или винтовых струбцинах. На кронштейнах укладывают щитовой настил.
9.3.1 Изготовление деталей
Количество деталей в корпусе весьма велико и измеряется десятками тысяч. Все детали корпуса могут быть разделены на небольшое число групп, каждой из которых соответствует определённый технологический маршрут изготовления. Основой такого деления является: материал корпуса, технологическая последовательность операций и применяемое оборудование. При изготовлении стальные детали корпуса проходят предварительные и основные операции обработки.
К предварительным операциям относятся: правка; очистка от окалин и ржавчины; нанесение антикоррозионного покрытия.
Основными операциями являются: разметка и маркирование деталей; резка механическая или тепловая; правка вторичная; гибка. Кроме того для отдельных деталей применяется разделка кромок и снятие ласок, сверление отверстий, их зенковка. Заканчивается техпроцесс сортировкой и комплектацией.
Детали были изготовлены в сборочно-сварочном цеху. Технологический процесс изготовления и обработки изложен в пункте 3.
9.3.2 Изготовления секции
Плоскостные секции наиболее распространены. На современных заводах производство их организуется на механизированных поточных линиях, первые позиции которых предназначены для сборки и сварки полотнищ. На сваренное полотнище на последующих позициях устанавливаются элементы набора, привариваются детали насыщения и т.д.
Секция была выполнена на технологической линии "Янтарь". Технический процесс её изготовления изложен в пункте 6.
9.4 Технология сборки блоков.
При формировании блока соблюдается такая последовательность работ:
9.4.1 устанавливают и проверяют днищевые секции, подгоняют стыки между ними, секции раскрепляют растяжками за опорные тележки или стапель-кондуктор, если блок собирается в нём;
9.4.2 сваривают монтажные стыки между днищевыми секциями;
9.4.3 устанавливают поперечные переборки;
9.4.4 устанавливают и закрепляют на прихватках после проверки бортовые секции;
9.4.5 устанавливают при необходимости монтажные рамы на концах блока
9.4.6 устанавливают палубные секции;
9.4.7 после проверки положения всех собранных секций сваривают пазы между днищевыми, бортовыми и палубными секциями, а затем приваривают к ним поперечные переборки;
9.4.8 устанавливают внутренние конструкции в блоке;
9.4.9 контролируют сварные швы, а затем испытывают блок на непроницаемость.
9.5 Технология постройки судна из блоков.
Процесс сборки состоит из: установки закладного блока машинного отделения на опорные устройства стапеля, проверки закладного блока по длине, полушироте, высоте и, полушироте, высоте и на крен, подачи и установки смежных блоков на расстоянии от закладного на 50-150 мм, причерчивания и подрезки кромок, сближения смежных блоков с закладным, окончательной проверки положения блоков подгонки кромок и прихватки, сварки изнутри и снаружи листов обшивки и палубы, сварки набора блоков между собой и приварки его к обшивке, подачи и установки носового и кормового блоков, разметки мест установки машинного капа и блока надстройки, установки блока надстройки и капа, проверки положения блока надстройки, причерчивание монтажных нижних кромок и выгородок блока на высоту 150-200 мм от палубы и обрезки припусков, подгонки соединений, поджима и сборки на электроприхватки, сварки соединений капа и надстройки с палубой, установки блока рулевой рубки, проверки положения, подгонки кромок и сборки на прихватки, сварки монтажных соединений блока рулевой рубки, испытания корпуса и надстроек на водонепроницаемость и устранения обнаруженных дефектов.
Закладные блоки изготовляются в чистый размер без припусков, остальные блоки – с припуском по кромкам. При выполнении сварочных работ вначале заваривают оставленные в блоках участки пазов обшивки, затем – монтажные стыки наружной обшивки и палубы в направлении от ДП к бортам и к нейтральной оси поперечно сечения корпуса.
ЗАКЛЮЧЕНИЕ
В данном курсовом проекте была разработана технология изготовления бортовой секции сухогрузного судна.
В процессе выполнения проекта разработала технологические маршруты изготовления деталей секции, рассчитала трудоемкость их изготовления. Далее была разработана технологическая линия изготовления секции и рассчитана трудоемкость этого процесса. По заданию секцию проектируется на линии ESAB. Также был произведен размерный анализ секции и были рассчитаны предельные допуски для секции.
На основании этих данных были разработаны условия и метод постройки судна.
В графическую часть проекта входят чертеж секции (общий и все необходимые сечения), а также эскизы заданных деталей секции.
Библиографический список
1. Мацкевич В.Д. Основы технологии судостроения. Издательство «Судостроение» 1980г.
2. Голота Г.Ф. Техническое нормирование судо-корпусных и судо-монтажных работ Издательство «Судостроение» 1967г.
3. Галкин В.А. Справочник технолога- судосборщика. Издательство «Судостроение» 1985г.
4. ОСТ5.9912 – 88 Корпуса стальных надводных судов. Типовые технологические процессы изготовления узлов и секций.
5. Рабочий альбом типовых конструкций. Типовые корпусные конструкции из стали для надводных кораблей и секций. Часть 1. Узлы и элементы.
|