Министерство образования и науки Российской Федерации
Сибирская государственная автомобильно-дорожная академия
Кафедра Автоматизация производственных процессов и электротехника
Расчетно-пояснительная записка к курсовой работе по дисциплине “Технические измерения и приборы”
Тема работы:
«Разработка автоматизированных систем контроля технологического процесса на современных кирпичных заводах»
Омск 2008
Введение
В данной курсовой работе необходимо разработать автоматизированную систему контроля технологического процесса на современных кирпичных заводах.
Несмотря на утвердившееся направление бесщитового распределенного управления, существенно ограничивающее применение традиционных вторичных приборов (мостов, потенциометров, дифференциально-трансформаторных приборов), последние находят применение. Следует отметить, что измерительные схемы потенциометров и мостов используются для измерения различных физических величин (кроме температуры), которые с помощью соответствующих первичных измерительных преобразователей могут быть преобразованы в электрические напряжения или сопротивления. Так, например, они могут быть использованы для измерения влажности с помощью двух резистивных датчиков температуры, измерения давления с помощью тензометрических и пьезоэлектрических преобразователей и в других случаях.
На кирпичном заводе применяется технология пластического формирования, по которой изготавливают кирпичи и камни согласно ГОСТ 530-95.
В качестве АСР я решил выбрать систему регулирования температуры в туннельной печи, в зоне обжига керамического кирпича. На рисунке 1 представлена функциональная схема контура управления температурой в ТОУ,
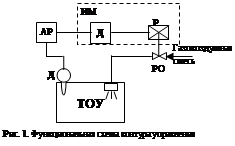
где: ТОУ – технологический объект управления;
АР - автоматический регулятор;
ИМ - исполнительный механизм - включает в себя двигатель (Д) и редуктор (Р);
РО - регулирующий орган – заслонка клапана;
Д - датчик.
Работа такой системы заключается в том, что регулирование температуры осуществляется путем изменения подачи газо-воздушной смеси. Если в печи изменилась температура, то датчик фиксирует это и подает сигнал автоматическому регулятору, который в свою очередь вырабатывает сигнал управления и посылает его на исполнительный механизм. Двигатель начинает вращаться в сторону соответствующую закрытию или открытию клапана (в зависимости от роста или уменьшения температуры в ТОУ), который через редуктор связан с выходным валом двигателя. Изменение положения заслонки приводит к соответствующему изменению расхода газо-воздушной смеси, а следовательно и к изменению температуры в ТОУ.
Автоматическое регулирование температуры в печи очень важно для получения высококачественного кирпича, т.к. в настоящее время является одним из самых распространенных строительных материалов в мире. Из кирпича возводятся не только жилые здания, но и производственные помещения, и его качество определяет длительность эксплуатации и надежность этих построек.
Производство кирпича включает в себя несколько этапов:
- Разработка карьера,
- Первичная переработка массы,
- Накопление и хранение глиняной шихты,
- Вторичная переработка шихты ,
- Формирование и транспортировка кирпича-сырца,
- Сушка кирпича-сырца,
- Садка высушенного кирпича-сырца на обжиговые вагонетки,
- Обжиг кирпича,
- Разгрузка готовой продукции.
В технологии керамического кирпича обжиг является завершающей и наиболее ответственной стадией его изготовления. Процесс обжига керамического кирпича заключается в высокотемпературной обработке сформованного и высушенного кирпича-сырца при заданных температурах в определенной газовой среде. Под влиянием теплового воздействия в керамических массах происходит ряд физико-химических процессов, в результате которых формуются наиболее важные свойства и структура керамического кирпича, определяющие его техническую ценность - прочность, плотность, морозостойкость и др.
Продолжительность обжига и последующего охлаждения, температурные условия и характер газовой среды находится в зависимости от физико-химических свойств сырья и от процессов, протекающих в кирпиче.
Процесс обжига делится на несколько периодов: подогрев до 200°С, досушка - удаление физической воды из глины, дальнейший нагрев до 700°С "на дыму" и удаление химически связанной воды из глины, "взвар" ~ до температуры обжига 900~1100°С - созревание черепа, охлаждение "закал" - медленное до 500°С и быстрое от 500 до 50°С обожженного кирпича.
Для производства кирпича используется туннельная печь. В зоне обжига печи, в своде, вмонтированы горелки. Имеются также дополнительные сводные отверстия, позволяющие перемешать зону обжига по длине печи. Установка для подачи газообразного топлива состоит из 7 групп газовых горелок принудительного смешивания по 14 горелок в каждой группе. На участке расположения горелок установлен датчик температуры (термопара) в рабочем канале печи. Для подачи воздуха к горелкам на своде печи установлено 7 вентиляторов системы «вулкан» с воздуховодами и арматурой. Для горения используется воздух из цеха, но возможно использование горячего воздуха из меж сводного пространства (температура не выше 150-160С).
Описание технологического процесса и технологического производства
Разработка карьера
Добыча глинистого сырья начинается с вскрышных работ, которые производятся бульдозером Д 3-27С. Размер отвала: высота – 1200 мм., длина – 3000 мм. Вскрытие должно опережать работы по добыче сырья.
Разработка и погрузка глины производится одноковшовыми экскаваторами ЭО-1252 и ЭО-5111. разрабатывают сырье на глубине 5-6,8 м. Перед загрузкой в автомашину глина предварительно разрыхляется и усредняется экскаватором.
В зимний период производится разогрев глины путем сжигания бурого угля слоем 20-40 см. Более подробно технологический процесс разработки сырья описан в «Паспорте карьера», разработанном «Уралгеолстроем» в 1991 году.
Первичная переработка массы.
Глинистое сырье, доставляемое из карьера автомашиной КАМАЗ-5511 в приемное отделение, поступает в бункер рыхлителя СМ-1031 М или в глинозапасник емкостью 200 м.куб. Глинорыхлитель производит первичное дробление сырья и подачу его на ленточный питатель КМ-21. Питатель осуществляет подачу и дозировку сырья (поднятием или опусканием шибера). Регулировку подачи производят при изменении карьерной влажности глинистого сырья, в период межсезонья, при изменении физико-механических показателей глины.
С ленточного питателя сырье ленточным конвейером попадает в глиномешалку СМК-126. над конвейером установлен электромагнитный железоотделитель для удаления металлических предметов из глины.
Поступившее в глиномешалку сырье усредняется, увлажняется до 20%. Масса глины, заполняющая корпус смесителя, должна закрывать валы, но не более чем на 1/3 высоты лопастей, находящихся в верхнем положении. Зазор между кожухом смесителя и лопастями должен быть не более 10 мм.
Из глиномешалки масса ленточным конвейером подается в бегуны КМ-25. На бегунах мокрого помола измельчают и перемешивают глиняную массу. Степень увлажнения массы в бегунах определяется визуально. Нормально увлажненная глина (20-22%) хорошо обрабатывается и не прилипает к каткам и скребкам. Переувлажненная глина прилипает к каткам, замазывает отверстия в шнеках и стенках чаши. Недостаточно увлажненная глина состоит из неслипшихся между собой кусков, рассыпающихся при разминании руками. На бегунах куски глины под тяжестью катков раздавливаются, а за счет усилий сдвига, образуемого при вращении катков, разрываются и истираются. Обработка массы на бегунах мокрого помола повышает ее связность и однородность. Прочность сырца приготовленного из обработанной на бегунах массы, повышается и, вследствие этого, увеличивается прочность готовых изделий.
Обслуживание бегунов в процессе работы заключается в непрерывном наблюдении за подачей глиняной массы, степенью ее увлажнения и качеством обработки, толщиной материала под катками (допускается слой 25 мм.), а также за состоянием скребков. Увлажнение осуществляется по имеющемуся на бегунах водопроводу.
После обработки на бегунах глиняная масса ленточным конвейером пересыпается на вальцы грубого помола МГФ-1000, рабочий зазор между валками 5-7 мм. Вальцы грубого помола предназначены для дальнейшего измельчения глиняной массы путем раздавливания материала и его истирания за счет различной частоты вращения валиков, вращающихся навстречу один другому.
Накопление и хранение глиняной шихты
От вальцов глина наклонным конвейером ЛТГС -650 подается на конвейер ЛТГС -700, оборудованный передвижным плужковым срабатывалетем. Плужковым срабатывалетем подготовленная шихта перемещается на один из двух расстилочных мостов, перемещающихся вдоль шихтозапасника. Расстилочный мост представляет собой два конвейера: один неподвижный, принимающий шихту с конвейера, другой подвижный (челнок), равномерно распределяющий шихту в шихтозапаснике в бурт правильной конусообразной формы емкостью до 250 м.куб.
Поступившая в шихтозапасник шихта вылеживается в течении 7 суток, усредняется по влажности (20-22%). Шихтозапасник размечен на 20 позиций для лучшего учета и контроля высыпаемых и выбираемых буртов сырья.
Вылежавшееся сырье отбирается из шихтозапасника с помощью многоковшовых экскаваторов БМК-11-25/40, установленных на самоходных мостах. Во время работы экскаватор, стрела которого имеет наклон до 45 градусов, передвигается с одной стороны на другую по всей ширине шихтозапасника с последовательным углублением стрелы.
Ковшами экскаватор снимает слой шихты определенной толщины – 40-50 мм по всей длине бурта. Затем стрела углубляется на 40-50 мм. и операция повторяется. При помощи ленточного конвейера многоковшового экскаватора шихта подается на ленточный конвейер ЛТГС-800, над которым установлен электромагнитный железоотделитель.
Шихта с ЛТГС-800 при помощи плужковых сбрасывателей пересыпается в один из двух питателей КМ-22 формовочного отделения.
Вторичная переработка шихты.
Ящичным питателем КМ-22 производится дозирование сырья и равномерная передача его на ленточный конвейер. Дозирование осуществляется шибером, изменяющим сечение выходного пласта глины от 20 см до 60 см по высоте.
Над конвейером установлен электромагнитный железоотделитель. С конвейера шихта направляется на вальцы тонкого помола МГФ-36. При работе вальцов материал поступает на валок с меньшей частотой вращения, затягивается в зазор между вращающимися валками и раздавливается. Вальцы эффективно работают при соблюдении соотношения между размерами кусков материала и зазором между валками не более 4:1. При большем зазоре обработка глины значительно ухудшается.
После обработки на вальцах глиняная масса ленточным конвейером подается в Фильтр-смеситель ГДФ-302, зазор между внутренней поверхностью и лопатками которого должно быть не более 8 мм. В фильтр-смесителе масса доувлажняется до формовочной влажности (22%), перемешивается и обрабатывается на фильтрующих решетах.
Регулировка подаваемой для увлажнения воды осуществляется вручную.
Переработанная масса поступает в глиномешалку пресса.
Формование и транспортировка кирпича-сырца.
Глиномешалка принимает глину, дополнительно дробит ее, смешивает и транспортирует в вакуум-камеру пресса ПВШ-500. Зазор между шнеком и рубашкой пресса должен быть не более 5 мм., температура бруса 25-30С, влажность бруса 21-22%, разрежение в вакуум-камере 680-700 мм.рт.ст.(0,91-0,94 кг/см. кв.). Вакуумирование создается вакуум насосом ПВД-13. Из глиняной массы, поступившей в вакуум-камеру предварительно удаляется воздух с помощью вакуума, при этом масса приобретает высокую связанность и плотность. Увеличивается сопротивление разрыву глиняного бруса, он приобретает резиноподобное состояние. Из вакуум-камеры при помощи питательного устройства глина подается к приемным шнекам, которые перемещают глину вдоль цилиндра к переходной головке. Переходная головка служит для уплотнения глиняной массы и передачи ее к мундштуку. Из мундштука глина с определенным давлением выходит в виде сплошной и профилированной ленты размерами по сечению: 269-131. Замена мундштука производится периодически по мере износа (размер более 269-131 и уменьшение пустотности 21%). На выходящий из мундштука глиняный брус валиками может наноситься рифление и маркировка завода, а также штамп работающей смены. Далее брус через ролики поступает на многострунный резательный автомат МРА-10000, предназначенный для одновременного резания глиняного бруса на 14 равных частей. Автомат состоит их основных механизмов: однострунный резательный станок, роликовый транспортер, входящая лента, исходящая лента, основная рама, лента для удаления отходов. Отходы вновь возвращаются в фильтр-смеситель, а отрезанные кирпичи-сырцы подаются на реечный автомат, который разнеживает и устанавливает их на пару реек по 14 штук. Далее реечный автомат переводит пару реек с сырцом в приемный автомат. Последний принимает поданные рейки с сырцом, юстирует их и направляет на стеллаж-элеватор кирпича-сырца.
Приемный автомат состоит из: рольганга, запускного механизма, механизма юстирования.
Стеллаж-элеватор принимает и группирует кирпич в определенном порядке. Емкость стеллажа 400 камней или 700 кирпичей. После заполнения стеллажей кирпич-сырец подъемной 10-полочной тележкой снимается с элеватора, тележка устанавливается на лафет, лафет перемещается вдоль сушильных камер по рельсовым путям. С лафета тележка перемещается по рельсовым путям сушильной камеры.
Сушка кирпича-сырца
Для сушки кирпича-сырца предусмотрены камерные сушила с поперечным движением теплоносителя. Сушила имеют 13 камер, разделенных на 2 части: в первой части с 1 по 6 камеры, во второй с 7 по 13 камеру. По схеме теплоснабжения все камеры разбиты на 3 блока. Блок сушки обслуживается группой, состоящей их 2-х теплогенераторов ГГ-100, смесительной камеры, подающего вентилятора С-112 и распределительного воздуховода, связанного с клапанами для подачи теплоносителя в каждую камеру.
Глубина камеры 18,5 м.
Высота 3,13 м.
Ширина 16 м.
Объем 1345 м3
Каждая камера оборудована дверью, поднимающейся вверх при помощи электро-тельфера. Внутри камеры установлено 6 параллельных рельсовых путей, вдоль которых смонтированы металлические 10-полочные стеллажи для укладки на них пары реек с кирпичом-сырцом. Верхняя часть камеры перекрыта «ложным» потолком из асбоцементных листов. В результате, между сводом и «ложным» потолком образуется полость для циркуляции теплоносителя. На внутренней стороне боковых стен установлены направляющие аппараты, служащие для рассеивания потока теплоносителя по всему сечению камеры. В средней стенке встроено 36 осевых вентиляторов С-72, которым осуществляется циркуляция внутри камеры.
В центральной (подовой) части каждой половины камеры предусмотрены каналы для удаления влажного отработанного воздуха в атмосферу.
Горячий воздух в камеру поступает из зоны охлаждения печи и от теплогенераторов ГГ-100, топливом для которых служит природный газ. Теплогенератор забирает воздух из помещения цеха через теплообменник, нагревая до 120 С, и отдает нагретый воздух в смесительную камеру; в смесительной камере нагретый воздух смешивается с воздухом печи и подающим вентилятором С-112, направляется к сушильным камерам.
Перед тем, как начать загрузку в камеры, необходимо выполнить следующие технологические операции: очистить камеру от оставшегося брака; шибера подачи и отбора тепла должны быть закрыты и проверена их работоспособность; произвести орошение камеры водой до относительной влажности около 95%; температура камеры во время загрузки должна быть ниже на 4-6 С, чем температура сформованного бруса; это достигается путем работы шиберов отбора и подачи тепла.
После замера влажности, температуры в камере и бруса и в случае соблюдения технологических требований разрешается загрузка камеры.
В теплое время года загрузка камеры производится следующим образом: в первую очередь загружают дальний от осевых вентиляторов путь. В холодное время камеру загружают срезе по трем путям, ставя поочередно на каждый по одной тележке для более длительного сохранения тепла в сырце.
После загрузки одной половины камеры двери ее закрывают и продолжают загрузку другой половины. По окончании, когда поставлены все тележки (66 штук) закрывают вторые двери, камера устанавливается на режим сушки.
Режим сушки существует: летний и зимний, ручной и автоматический.
Летний режим примерно с 15 мая, зимний с 10 октября.
После загрузки камеры устанавливается «выдержка». На этом этапе в камере находится один и тот же объем воздуха, температура которого 20-30С (зимой ниже). Происходит медленное усреднение воздуха и сырца, затем включаются осевые вентиляторы с реверсом: 8 минут вращаются в одну сторону, 5 минут стоят, 8 минут вращаются в другую сторону. Поток воздуха проходит то с одной стороны через зазоры между уложенным сырцом, то с другой, проходя через «ложный» потолок. После того, как циркулирующий внутри сушилки воздух увлажняется, подается небольшое количество теплоносителя путем открывания шибера подачи тепла. Под влиянием избыточного давления, обязательного для нормальной работы камеры, и естественной тяги, отработанный теплоноситель (насыщенный влагой) выдавливается в подовый канал и удаляется через трубу в атмосферу. Благодаря избыточному статическому давлению, равному 5 мм. рт. ст., а также работе осевых вентиляторов, перепады температуры внутри камеры очень малы (2-3С).
Оператор сушильных камер постоянно контролирует работу камер по приборам. Каждые 3 часа показания приборов записываются в журнал. В случае скачкообразного изменения относительной влажности необходимо проверить правильность работы приборов. В случае резкого подъема температуры в камере необходимо снизить давление подаваемого теплоносителя открываем шибера на смесительной камере для добавления холодного воздуха.
Приборы автоматического регулирования режима установлены на 7-13 сушильные камеры. Автоматический режим сушки производится на заданной программе с использованием ЭВМ. Программа летнего и зимнего режимов в автоматическом режиме приведена в Приложении Г.
После окончания цикла сушки высушенный кирпич не должен простаивать более одних суток. В противном случае происходят структурные разрушения керамического камня, снижается механическая прочность.
Таблица 1. Основные технологические параметры сушки.
№ п/п
|
Наименование параметра
|
Единица измерения
|
Величина
|
1
2
3
4
5
6
7
8
9
10
|
Влажность сырца, загружаемого в сушилку
Полный цикл сушки
Остаточная влажность изделия
Температура сырца, поступающего в сушилку
Температура теплоносителя в начале периода
Температура теплоносителя в конце периода
Влажность теплоносителя в сушилке в начале периода
Температура воздуха в распределительном воздуховоде
Теоретическое количество воздуха для сушилки, на один блок
Рабочее давление теплоносителя
|
%
час.
%
С
С
С
%
С
тыс.м.куб/ч
кгс/см.кв.
|
22
120
2-3
30-40
30-40
50-60
90-95
95-120
115
1,0
|
Таблица 2. Основная технологическая характеристика сушилки
№ п/п
|
Наименование показателей
|
размерность
|
величина
|
1
2
3
4
5
6
7
8
|
Число камер
Размер сушильных реек
Полезные размеры камеры:
Глубина
Ширина
Высота
Количество полок на каждые путь
Количество полок по высоте
Количество путей в камере
Количество полок на каждую камеру
Количество кирпича усл. в каждой камере
|
шт
мм
м
м
м
шт
шт
шт
шт
шт
|
13
1590-55-55
18,5
15
3,13
1100
10
6
6600
46200
|
Таблица 3. Перечень оборудования сушильных камер.
№ п/п
|
Наименование
|
Единица измерения
|
Количество
|
Производительность
|
1
2
3
4
5
6
7
|
Осевые вентиляторы С-72
Направляющие аппараты
Двери гильотинного типа
Напольные решетки каналов отбора
Генератор горячего воздуха ГГ-100
Центральный вентилятор С-112
Металлические стеллажи
|
шт
-
шт
шт
шт
шт
-
|
468
-
26
78
7
3
-
|
6000 м.куб/ч
-
-
-
-
150000 м.куб/ч
-
|
Садка высушенного кирпича на обжиговые вагонетки.
Высушенный кирпич из сушильной камеры 10-полочной тележкой и лафетом перемещается и устанавливается на стеллаж-элеватор автомата-садчика.
Автомат-садчик производит укладку высушенного кирпича на обжиговые вагонетки. Установка вагонеток и размещение стопок посаженного кирпича производится в строгом соответствии с расположением горелок туннельной печи. Раскладка кирпича на вагонетки осуществляется при помощи программного устройства (программатора).
На вагонке размещено 6 стопок по 784 кирпича (364 камня), всего 4704 кирпича (2184 камня).
Стеллаж-элеватор предназначен для приема сухого кирпича с передаточной тележки и передачи его на приемный транспортер. Приемный транспортер служит для подачи реек с кирпичом с определенным промежутком времени и шагом на промежуточный элеватор. На раме приемного транспортера установлено юстирующее устройство, которое юстирует кирпич и рейки перед установкой на элеватор. Промежуточный элеватор предназначен для приема пары реек с кирпичом и подъема их на определенную высоту. Далее рейки с кирпичом устанавливаются и группируются на группирующем транспортере. Затем при помощи перебрасывающего устройства кирпич снимается с реек, а рейки продолжают движение до транспортера, отделяющего освободившиеся рейки, к подавательному устройству и размещает их в снимающем элеваторе. Рейки снимающим элеватором подаются на собирающий транспортер, который подает рейки в накопитель для создания запаса. Накопитель отдает накопленные рейки в реечный автомат.
Перебрасывающим устройством кирпич устанавливается на группирующем столе. Перебрасывающее устройство представляет собой одиночный грейферный захват, управляемый при помощи гидроцилиндров. Группирующий стол малый
предназначен для приема кирпичей с перебрасывающего устройства и подачи их на программный стол.
Программный стол выравнивает кирпич, компонует по заданной программе и передает на группирующий стол большой
.
Группирующий стол большой
принимает кирпич с программного стола и подает на тройной грейферный захват, назначение которого в снятии рядов кирпича и укладке на печные вагонетки в определенном порядке.
Печные вагонетки подаются под садчик-автомат с определенным шагом при помощи толкательного устройства.
Загруженные вагонетки транспортируют тележкой маневрового устройства. Вагонетка перемещается к концу маневрового пути и вкатывается на электролафет КМ-10В. Имеется 2 маневровых пути от садчика-автомата №1 и №2. Путь №1 68 м., и путь №2 120 м. Далее гидротолкателем печи вагонетка снимается с электролафета и перемещается в печь.
Оборудование садчика-автомата.
1) стеллаж-элеватор; 2) приемный транспортер; 3) устройство юстировочное; 4) элеватор промежуточный; 5) транспортер группирующий; 6) одиночный захват; 7) транспортер рейки; 8) устройство подавательное (рольганг); 9) элеватор понижающий; 10) транспортер собирающий; 11) накопитель для реек; 12) стол группирующий малый; 13) стол группирующий большой; 14) стол программный; 15) тройной захват; 16) устройство толкательное.
Обжиг кирпича.
Обжиг кирпича производится в туннельной печи с плоским сводом и верхним расположением горелок.
Таблица 4. Техническая характеристика туннельной печи.
№ п/п
|
Наименование показателей
|
Размерность
|
Величина
|
1
|
2
|
3
|
4
|
1
2
3
4
5
6
7
8
9
10
11
12
13
14
15
16
17
|
Номинальная проектная производительность
Суточная производительность
Часовая производительность
Длина обжигового канала
Ширина обжигового канала
Минимальный срок обжига
Длина технологических зон:
Подготовки
Обжига
Охлаждения
Количество вагонеток, пропускаемых печью:
В час
В сутки
Количество вагонеток в печи
Годовой фонд рабочего времени
Интервал проталкивания вагонеток
Габаритные размеры вагонеток:
Ширина
Длина
Высота (с садкой)
Количество пакетов на вагонетке
Емкость 1 пакета
Емкость 1 вагонетки
Единовременная емкость печи
Рабочее давление газа
|
млн.шт.усл.кирп.
млн.шт.усл.кирп.
млн.шт.усл.кирп.
м
м
ч.
м
м
м
шт
шт
шт
ч.
мин.
м
м
м
шт
шт.усл.кирп.
шт.усл.кирп.
шт.усл.кирп.
кгс/см.кв.
|
30,0
92720
3863
125,0
3,5
58
47(18 вагон)
39(15 вагон)
39(15 вагон)
0,8
20
48
8760
72
3,58
2,6
1,6
6
784
4704
222528
0,5
|
Имеется две туннельные печи.
В качестве топлива используется природный газ (метан).
Основной особенностью печи является перекрытие обжигового канала плоским подвесным сводом, выполненным из жароупорного бетона с вмонтированными питателями для подачи топлива в специальные вводные отверстия, расположенные по верху всей зоны обжига.
Введение вагонеток в форкамеру и перемещение их в печи производится при помощи гидротолкателя. Скорость продвижения вагонеток 0,94 м/мин. В начале печи и в фокамере установлены ворота гильотинного типа.
Удаление дымовых газов из печи производится дымососом С-111. Дымосос отбирает дымовые газы через 10 отверстий, расположенных в начале печного канала (1-5 позиций) на уровне пода. Отверстия объединены в центральный коллектор металлическим каналом. Отработанные газы по дымовой трубе выбрасываются в атмосферу. Температура отходящих дымовых газов 60С. Отверстия в каналах имеют клапаны для ручной регулировки. На всасывающем фланце дымового вентилятора установлен клапан для общей регулировки разряжения внутри печи так, чтобы оно перед первой группой горелок (19 порция) составляло 5-7 кгс/м.кв. (5-7 мм.в.ст.)
Для охлаждения ходовой части обжиговых вагонеток и обслуживания по всей длине печи выполнен подвагонеточный канал. Температура в подвагонеточном канале не должна превышать 50С.
В зоне предварительного нагрева печи установлено три пары вентиляторов рециркуляции дымовых газов для создания равномерной температурной среды по сечению канала печи. Дымовые газы из участков с более низкой температурой засасываются через отверстия на уровне пода и направляются через отверстия в потолке вертикально вниз на участки с более высокой температурой в пространство между пакетами с продукцией.
Температура в зоне подготовки, где установлены вентиляторы рециркуляции не превышает 350С. Каждая цепь рециркуляции снабжена задвижками забора холодного воздуха из цеха, которые позволяют производить регулировку температуры.
На первой позиции установлен вентилятор низкотемпературной рециркуляции (противодавления), отбирающий часть дымовых газов, приходящих на дымосос и подающий их в канал печи противопотоком по отношению к основному газовому потоку на 2,3 и 4 позициях.
В зоне обжига печи, в своде, вмонтированы горелки. Имеются также дополнительные сводные отверстия, позволяющие перемешать зону обжига по длине печи. Установка для подачи газообразного топлива состоит из 7 групп газовых горелок принудительного смешивания по 14 горелок в каждой группе. На каждой группе горелок установлен датчик температуры (термопара) в рабочем канале печи. Для подачи воздуха к горелкам на своде печи установлено 7 вентиляторов системы «вулкан» с воздуховодами и арматурой. Для горения используется воздух из цеха, но возможно использование горячего воздуха из межсводного пространства (температура не выше 150-160С).
Вентиляционная система рекуперативного воздуха состоит из вентилятора ВНСН-16,5, всасывающего воздуховода, который отбирает воздух из пяти точек зоны охлаждения и из двух точек межсводного пространства. Каждый всасывающий насос снабжен шибером ручной настройки по количеству засасываемого воздуха. После вентилятора смонтирован воздуховод для отвода горячего воздуха к смесительным камерам генераторных групп. Температура рекуперативного воздуха 180-250 С.
В зоне охлаждения печи установлены две пары вентиляторов рециркуляции. Они служат для более полного и равномерного охлаждения обожженной продукции. Воздух из участка с более низкой температурой засасывается через отверстия на уровне пода канал и через отверстия в своде печи поступает вертикально вниз на участки с более высокой температурой в пространство между пакетами с продукцией.
Вентиляционная система для охлаждения продукции состоит из 2-х вентиляторов ВСН-8, связанных с воздуховодом, подающим воздух через свод и стены на 47-ю позицию. Воздух забирается из цеха или аварийного канала в зоне охлаждения (или из обоих мест одновременно). Регулировка количества засасываемого воздуха производится с таким расчетом, чтобы температура выходящей продукции из печи не превышала 50С.
Во время работы печи контролируется температура по всей длине рабочего канала (позиции 5,10,15,19-30,34,42), температура в межсводном пространстве, температура в подвагонеточном канале.
По длине печи с кирпичом происходят следующие процессы:
Зона подготовки (позиции 1-18) – подсушка сырца и нагрев его до температуры 500-540С.
Зона обжига (позиции 18-33) – обжиг кирпича при температуре 900-980С.
Зона закалки и охлаждения (позиции 33-48) – закалка и охлаждение обожженной продукции до 50С.
Регулирование температуры воздуха в вагонеточном канале осуществляется с помощью вентиляторов Ц-4-70 №8, установленными снаружи цеха по 1 штуке на печь. Вентиляторы подают холодный воздух в шахту, соединенную с печью подземным каналом.
Для предупреждения выхода из строя плит подвесного потолка и металлических балок на печи установлены пары вентиляторов:
Таблица 5.
Зона установки
|
Марка вентилятора
|
Производительность тыс.м.куб./час
|
Зона установки (позиция 15)
Зона обжига (позиция 21)
Зона охлаждения (позиция 45)
|
Ц 4-7 №8 (15,5 кВт)
Ц 4-7 №5 (1,5 кВт)
Ц 4-7 №6,3 (5,5 кВт)
|
20,0
8,0
10,0
|
Вентиляционное оборудование установлено на виброоснованиях.
Обожженная продукция, выходящая из печи, выставляется лафетом КМ-10 и толкателем на запасной путь и разгружается козловым краном ККТ-5 грузоподъемностью 5 тонн. Пролет крана 16 метров, высота подъема 7,1 м. Пакеты с помощью контейнера выставляются на площадку, где производится разбраковка и укладка на поддоны.
Разгрузка готовой продукции.
На площадке готовой продукции ведется контроль службой ОТК. Из нескольких мест выбираются образцы, по результатам испытаний которых определяется приемка партии. Партией считается количество выпускаемого кирпича за сутки. На каждую партию выписывается паспорт установленного образца, содержащий:
наименование предприятия;
дату выпуска паспорта;
дату выпуска изделий;
количество изделий в партии;
вид изделий;
марку;
водопоглощение;
предел прочности при сжатии и изгибе;
морозостойкость;
удельную эффективность естественных радионуклидов;
теплопроводность изделий;
массу изделий;
подпись лаборанта-контролера и печать.
Таблица 6. Краткая характеристика технологического оборудования
№ п/п
|
Наименование оборудования
|
Тип (марка)
|
Кол-во
|
Техническая
Характеристика
|
1
|
2
|
3
|
4
|
5
|
1
2
3
4
5
6
7
8
9
10
11
12
13
14
15
16
17
18
19
20
21
|
Бульдозер
Одноковшовый экскаватор
Грузовой автомобиль
Рыхлитель
Питатель ленточный
Конвейер ленточный
Глиномешалка
Бегуны
Конвейер ленточный
Конвейер ленточный
Вальцы грубого помола
Конвейер ленточный
Конвейер ленточный
Расстилочный мост
Многоковшовый экскаватор
Конвейер ленточный
Питатель ящичный
Конвейер ленточный
Вальцы тонкого помола
Фильтр-смеситель
Пресс шнековый
|
Т-130 (ДЗ-27С)
ЭО-1252
ЭО-5111
Камаз 5511
СМ-1031М
КМ-21
СМК-126
КМ-25
МГФ-1000
ЛТГС-650
ЛТГС-700
БМК- 11-25/40
ЛТГС-800
КМ-22
МГФ-36
ГДФ-302
ПВШ-500
|
2
1
1
2
2
2
4
2
2
2
2
1
2
2
1
2
4
2
2
2
|
Мощность двигателя
240 л.с.
Мощность двигателя
240 л.с., произв.80м.куб/ч
объем ковша 1,5 м.куб.
мощность двигателя 160 л.с., произв.60м.куб/ч
объем ковша 1,25 м.куб.
Мощность двигателя 270 л.с., емкость кузова
14т.
Производительность 35 м.куб/час, нагрузка 30 м.куб/час (85%), мощность э/двигателя 11 кВт, 1000 об/мин.
Производительность 35 м.куб/час, нагрузка 25 м.куб/час (71%), мощность э/двигателя 7,5 кВт, 1500 об/мин.
Производительность 35 м.куб/час, нагрузка 25 м.куб/час (71%), мощность э/двигателя 5 кВт, 1500 об/мин.
Производительность 35 м.куб/час, нагрузка 25 м.куб/час (71%), мощность э/двигателя 40 кВт, 1500 об/мин.
Производительность 30-40 м.куб/час, нагрузка 25 м.куб/час (70%), мощность э/двигателя 55 кВт, 1500 об/мин.
Ширина ленты 1600 мм., производительность 55 м.куб/час, нагрузка 25 м.куб/час (45%), мощность э/двигателя 5 кВт, 1500 об/мин.
Ширина ленты 650 мм., производительность 40 м.куб/час, нагрузка 25 м.куб/час (62%), э/двигатель 5 кВт, 1500 об/мин.
30м.куб/час, нагруз.м.куб/час (83%), э/двигатель 75 кВт, 1000 об/мин, диам. волков 1000 мм., ширина 800 мм., рабочий зазор между валками 5-7 мм
производительность 30 м.куб/час, нагрузка 25 м.куб/час (83%), э/двигатель 5,5 кВт, 1500 об/мин.
производительность 30 м.куб/час, нагрузка 25 м.куб/час (83%), э/двигатель 5,5 кВт, 1500 об/мин.
Производительность 40 м.куб/час, скорость передвижения моста 0,12 м/с, скорость движения человека 8 м./мин.
Производительность 35 м.куб/час, угол наклона стрелы до 45 град.
Производительность 35 м.куб/час, нагрузка 20 м.куб/час (57%), э/двигатель 7,5 кВт, 1500 об/мин.
производительность 25 м.куб/час, нагрузка 20 м.куб/час (81%), э/двигатель 7,5 кВт, 1500 об/мин., скорость ленты 0,95 м/мин
производительность 30 м.куб/час, нагрузка 20 м.куб/час (66%), э/двигатель 5,5 кВт, 1500 об/мин.
производительность 36 м.куб/час, нагрузка 20 м.куб/час (55%), э/двигатель 75,45 кВт, частота вращ. валков 320/280 об/мин., диам. валков 1000, зазор между валками 2-4 мм.
производительность 30 м.куб/час, нагрузка 20 м.куб/час (66%), э/двигатель 93 кВт, 1500 об/мин., частота вращения лопаток 24 об/мин
производительность 10000 шт.усл.кирп./час, нагрузка 7600(83%), суммарная мощность э/двигателей 177 кВт, 1500 об/мин., диам. шнеков 500 мм., разряжение в камере 680-700 мм.рт.ст(0,91-0,94 кг/см.кв.)
|
Спецификация средств измерения
Изобразим функциональную схему автоматической системы регулирования:
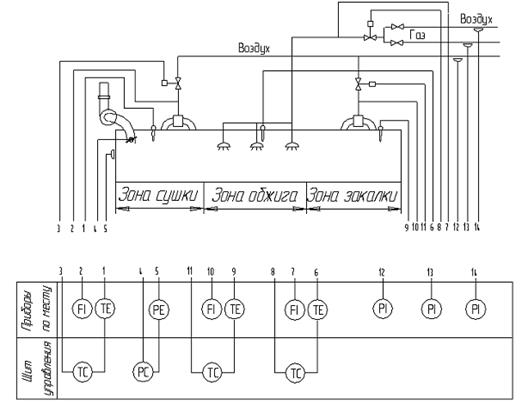
Рис.2 функциональная схема АСР.
Обозначение приборов:
FI – прибор, показывающий расход,
PI – прибор, показывающий давление,
TE – датчик температуры,
PE – датчик давления,
TC – регулятор температуры.
PC - регулятор давления.
Проведем анализ динамических характеристик АСР с типовым регулятором. Для избежания расчетов характеристик по сложным алгоритмам предлагается использовать пакет программ Matlab 6.5, и его приложение Simulink, которое позволяет эмулировать работу АСР. Первоначально определим структурную схему АСР и передаточные функции всех элементов. Все системы автоматического регулирования могут быть разделены на два звена: обобщенный объект регулирования и автоматический регулятор. Обобщенным объектом регулирования в дальнейшем будем называть сложное динамическое звено, которое включает: собственно объект регулирования (процесс), измерительные приборы и регулирующий орган. При этом передаточные функции составляющих обобщенного объекта отдельно не рассматриваются. Это касается и элемента сравнения и исполнительного устройства, входящие в состав пропорционального регулятора. При этом функциональная схема АСР и ее структурная схема представляются так, как показано соответственно на рис. 3 и 4.
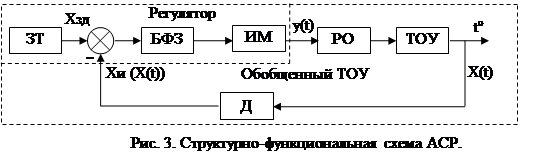
На рис.3. изображены: ЗТ- задатчик температуры,
БФЗ – блок формирования закона регулирования,
ИМ – исполнительный механизм,
РО – регулирующий орган,
ТОУ – технологический объект управления,
Д – датчик.
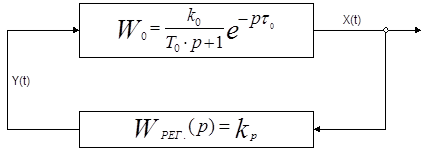
Рис. 4. Структурная схема АСР.
W0
(p) – передаточная функция обобщенного объекта. Так как по заданию объект является апериодическим звеном первого порядка с запаздыванием, то его передаточная функция записывается в виде:
, или 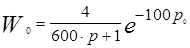
где k0
– коэффициент передачи объекта; Т0
– постоянная времени объекта; τ0
- запаздывание объекта; Х(t) – регулируемый параметр, температура; Y(t) – управляющее воздействие.
Wрег
(р) = kp
– передаточная функция пропорционального регулятора; kp
– коэффициент передачи регулятора.
В результате использования программы Matlab получили график переходного процесса (рис. 5). Из графика видно что:
Таблица 7.
Характеристики
|
полученные значения
|
Требуемые значения
|
Перерегулирование, º
|
4,16
|
≤ 10
|
Время переходного процесса, с
|
315
|
≤ 3200
|
Установившееся значение (Статическая ошибка, º)
|
1 (0)
|
1 (≤ 320)
|
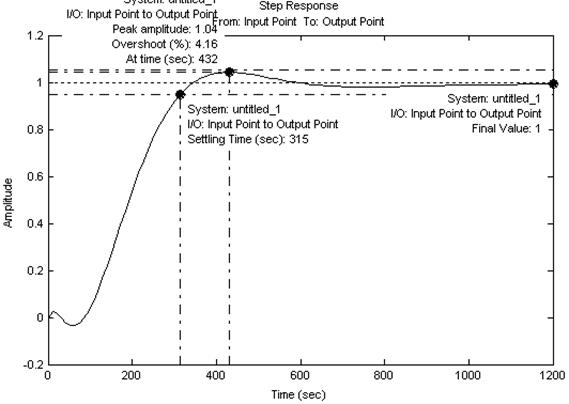
Рис.5. Характеристика переходного процесса.
В качестве автоматического регулятора предлагаю использовать микропроцессорный измеритель-регулятор ТРМ1Б-Н.ТП. И класс точности 0,5. Т.е. одноканальный измеритель-регулятор типа ТРМ1 в корпусе настенного крепления с размерами 130х105х65 мм, предназначенный для работы с термоэлектрическими преобразователями (термопарами), имеющий на выходе для управления исполнительными механизмами цифро-аналоговый преобразователь “параметр-ток” 4..20мА, класс точности которого 0.5, диапазон напряжений питания 85…250 В постоянного или переменного тока.
Микропроцессорный программируемый измеритель-регулятор типа ТРМ1 совместно с входным датчиком (термопарой) предназначен для контроля и управления различными технологическими производственными процессами и позволяет осуществлять следующие функции:
- измерение температуры с помощью стандартных датчиков.
- регулирование измеряемой величины.
- формирования выходного тока 4..20 мА для регистрации или управления ИМ по П-закону.
- отображения текущего измерения на встроенном светодиодном цифровом индикаторе.
Таблица 8.
Технические характеристики и условия эксплуатации
.
Условия окружающей среды
|
Температура воздуха , окружающего прибор
|
+5..50ºС
|
Атмосферное давление
|
86,,107 кПа
|
Относительная влажность воздуха (+35ºС)
|
30..80%
|
Питание
|
Напряжение питания
|
85..250 В постоянного или переменного тока
|
Потребляемая мощность, не более
|
6 ВА
|
Входы
|
Тип датчика
|
Диапазон измерения, ºС
|
Разрешающая способность
|
TXK(L)
|
-50..+750
|
0,1
|
TXA(K)
|
-50..+1300
|
1
|
THH(N)
|
-50..+1300
|
1
|
TЖK(J)
|
-50..+900
|
1
|
Параметры встроенных выходных устройств
|
Диапазон сопротивлений нагрузки для ЦАП “параметр-ток” 4..20мА
|
200..800 Ом
|
Диапазон напряжения питания для ЦАП “параметр-ток” 4..20мА
|
24..30 постоянного тока
|
Устройство и работа прибора.
Функциональная схема прибора приведена на рис.6. прибор имеет вход для подключения первичных преобразователей (датчиков), блок обработки данных, состоящего из измерителя физических величин, цифрового фильтра и логического устройства (ЛУ). ЛУ в соответствии с запрограммированными пользователями функциональными параметрами формирует сигналы управления выходным устройством, которое в зависимости от модификации прибора может быть дискретного или аналогового типа.
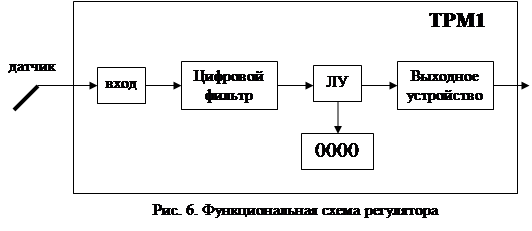
В качестве датчика я выбираю термопару ТХА (хромель-алюмель) с НСХ ХА (К) с диапазоном измерения -50 .. 1300 ºС и разрешающей способностью 1. Диапазон измерения этой термопары вполне обеспечивает диапазон температур в печи по технологическим требованиям процесса обжига кирпича (900-1100ºС), а также ненамного превышает ее верхний предел.
Термопара (термоэлектрический преобразователь) состоит из двух соединенных на одном из концов проводников, изготовленных из металлов, обладающих разными термоэлектрическими свойствами.
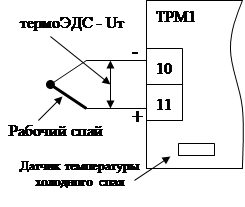 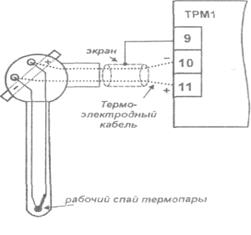
Рис. 7 Термопара.
Соединенные концы, называемые рабочим спаем, опускают в измеряемую среду, а свободные концы (холодный спай) термопары подключают к входу ТРМ. Если температуры рабочего и холодного спаев различны, то термопара вырабатывает термоЭДС, которая и подается на измеритель.
Поскольку термоЭДС зависит от разности температур двух спаев термопары, то для получения корректных показаний необходимо знать температуру "холодного" спая (ее свободных концов), чтобы скомпенсировать ее в дальнейших вычислениях.
В приборах модификаций ТРМ1Х-Х.ТП.Х, ТРМ1Х-Х.ТПП.Х предусмотрена схема автоматической компенсации температуры свободных концов термопары. Датчиком температуры "холодного" спая служит полупроводниковый диод, установленный рядом с присоединительным клеммником.
Подключение термопар к прибору должно производиться с помощью специальных компенсационных (термоэлектродных) проводов, изготовленных из тех же самых материалов, что и термопара (см. рис. 4). Допускается также использовать провода из металлов с термоэлектрическими характеристиками, которые в диапазоне температур 0...100°С аналогичны характеристикам материалов электродов термопары. При соединении компенсационных проводов с термопарой и прибором необходимо соблюдать полярность. При нарушении указанных условий могут иметь место значительные погрешности при измерении.
Преобразование сигнала, полученного с датчика, в текущее цифровое значение измеряемой величины (температуры, давления, расхода и т.д.) производится в измерителе. Поскольку большинство датчиков температуры имеют нелинейную зависимость выходного сигнала от температуры, в измерителях заложены таблицы коррекции показаний для всех типов датчиков, которые могут быть подключены к прибору. При работе с датчиками, формирующими на выходе унифицированный сигнал тока или напряжения, предусматривается произвольное масштабирование шкалы измерения. Для этого в соответствующих функциональных параметрах устанавливаются нижняя и верхняя границы диапазона отображения, а также положение десятичной точки.
Для улучшения эксплуатационных качеств в блоке обработки входных сигналов введен цифровой фильтр, позволяющий уменьшить влияние случайных помех на измерение контролируемых величин. Работа фильтра описывается двумя параметрами, задаваемыми при программировании (b0-2 и b0-3).
При низком уровне помех или при работе с быстроменяющимися процессами рекомендуется увеличить значение параметра или отключить действие полосы фильтра, установив в параметре b0-2 значение 00. В случае работы в условиях сильных помех для устранения их влияния на работу прибора необходимо уменьшить значение параметра. При этом возможно ухудшение быстродействия прибора из-за повторных измерений.
Глубина фильтра (b0-3) - позволяет добиться более плавного изменения показаний прибора. В этом параметре задается количество последних N измерений, из значений которых прибор вычисляет среднее арифметическое. Полученная величина поступает на вход ЛУ. При значении параметра равном 1 фильтр выключен. Уменьшение значения N приводит к более быстрой реакции прибора на скачкообразные изменения контролируемой величины, но снижает помехозащищенность измерительного тракта. Увеличение значения N приводит к улучшению помехозащищенности, но вместе с этим повышает инерционность прибора.
Логическое устройство работает в режиме П-регулятора. ЛУ сравнивает текущее значение измеряемой величины с заданной установкой "Т" и выдает на выход сигнал 4...20 мА, пропорциональный величине отклонения. Зона пропорциональности при этом задается параметром ∆. Ток 4...20 мА формируется в соответствии с установленной в параметре А1 -1 характеристикой регулятора либо по прямо-пропорциональному (нагреватель) либо обратно пропорциональному (охладитель) закону регулирования.
Аналоговый выход представляет собой формирователь токовой петли 4-20 мА на активной нагрузке 200...800 Ом (см. рис. 8). Аналоговый выход имеет гальваническую развязку от схемы прибора. Для работы аналогового выхода используется внешний источник питания 27В±10% постоянного тока.
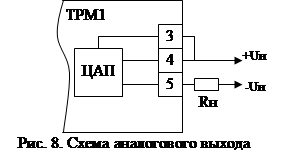 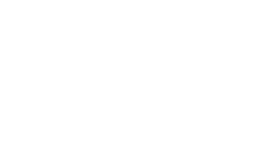
В качестве ИМ применяется регулирующее устройство РУ 16 (рисунок 9), которое состоит из регулирующего органа 1 (клапан), редуктора 2 и моторно-исполнительного механизма 3.
Моторно-исполнительный механизм, это электродвигатель модели ДСРК-30-01, реверсивный с пристроенным к нему редуктором. Такие двигатели используются в качестве комплектующих изделий в приборах и средствах промышленной автоматики, бытовых приборах для противопожарных и вентиляционных клапанов систем вентиляций зданий и др. двигатель работает от однофазной сети напряжением 220В и частотой 50 Гц. Режим работы – продолжительный. Климатическое исполнение – УХЛ4, с верхним предельным значением температуры окружающего воздуха 60ºС. Технические характеристики:
частота вращения – 0,5 мин-1
,
номинальный вращающий момент – 30(300) Нм (кгс*см),
характеристика вращения - ≤92º,
время одного цикла – 2,5 мин,
масса - ≤ 1.2 кг,
потребляемая мощность – 50 Вт.
С помощью редуктора угловое перемещение выходного вала преобразуется в линейное перемещение запорного штока клапана (происходит открытие или закрытие клапана).
Исполнение клапана – коррозионностойкое из стали Х18Н12МЗТЛ с плунжером, обеспечивающим линейную внутреннюю характеристику. Клапан нормально работает при перепаде давлений на них до 5 кГ/см2
, температуре окружающей среды от -30 до +50ºС и относительной влажности до 98%.
Регулирующий клапан с моторно-исполнительным механизмом на РУ 16 устанавливают на трубопроводах для агрессивных жидких и газообразных сред при температуре до 160ºС. Предназначены они для регулирования различных параметров технологических процессов. Клапаны устанавливаются на трубопроводах в вертикальном положении, электроприводом вверх.
Таблица 9.
Основные габаритные и присоединительные размеры (в мм.).
Ду
|
D
|
D1
|
D2
|
D3
|
D4
|
f1
|
f2
|
H
|
H1
|
l
|
L
|
d
|
b
|
h
|
G,кг
|
50
|
160
|
125
|
102
|
72
|
88
|
3
|
4
|
570
|
141
|
298
|
230
|
4 отв. п/б М16
|
16
|
25
|
37
|
Рис.9. регулирующий клапан на РУ 16 с моторно-исполнительным механизмом
Последовательность расчета электрических исполнительных устройств.
Расчет производится с учетом следующих основных требований:
а) напряжение UН
и номинальный ток IН
аппаратуры должны соответствовать напряжению и длительному току;
б) аппаратура управления должна без повреждений включать и отключать пусковой ток электродвигателей: Iпуск
= (7…9)Iн
; Iоткл.
≥ Iпуск
;
в) аппаратура защиты по своей отключающей способности должна соответствовать токам короткого замыкания в начале защищаемого участка: Iоткл.
≥ Iк.з.
.
Расчет и выбор элементов в автоматических системах регулирования электроприводами по техническим данным регулируемого двигателя осуществляется следующим образом.
Напряжение усилителя мощности, питающего двигатель, Uу.м.
=1,05Uн.дв.
.
Ток усилителя мощности, с учетом динамических режимов в процессе регулирования Iу.м.
= (1,15…1,25)Iн.дв.
, где Uн.дв.
, Iн.дв.
– соответственно номинальные значения напряжения и тока регулируемого двигателя.
По номинальной частоте вращения двигателя выбирается тахогенератор: nн.тг.
≥ nн.дв.
; ωн.тп.
= π∙nн.тг.
/30 ≥ ωн.дв.
= πnн.дв.
/30, где nн.тг.
– номинальная частота вращения тахогенератора.
Выбор реле.
Промышленностью выпускается большое количество различных типов и серий реле, выбор которых производится в соответствии с техническими данными реле, электрическими режимами работы и условиями их эксплуатации. Тип реле выбирают в зависимости от рода тока, напряжения питания, значения коммутируемых токов и напряжений в выходной цепи, времени срабатывания и отпускания, числа контактов, массы и габаритов. Особое внимание обращается на соответствие номинальных данных обмоток реле и контактов режимам их работы в различных устройствах автоматики [23].
При коммутации активных и активно – индуктивных нагрузок следует учитывать возникновение искрового разряда при размыкании цепи и в необходимых случаях применять устройства искрогашения.
Рубильники, пакетные выключатели, тумблеры выбирают:
а) по номинальному напряжению сети Uн
≥ Uн.с.
, где Uн.с.
– номинальное напряжение сети;
б) по длительному расчетному току Iн
> Iдлит.
; Iоткл.
≥ Iдлит.
; Iдлит
=
где Iдлит.
= длительный расчетный ток цепи; – суммарный номинальный ток всех n – потребителей.
Кроме того, указанная аппаратура должна без повреждений включать и отключать пусковые токи потребителей, которые превышают номинальные токи в несколько раз. Магнитный пускатель выбирают в зависимости от мощности электродвигателя и номинального напряжения сети.
Номинальные данные магнитного пускателя должны быть
Uн.
≥ Uн.с.
; Iн.
≥ Iн.дв.
.
Магнитные пускатели должны без повреждений включать и отключать пусковой ток двигателя.
Тепловые реле магнитных пускателей выбирают по номинальному току двигателя или длительному расчетному току
Iн.т.
> Iн.дв.
; Iн.т.
> Iдлит.
, где Iн.т.
– номинальный ток теплового элемента.
Автоматические выключатели выбирают по номинальным напряжениям и току
Uн.а.
≥ Uн.с.
; Iн.а.
≥ Iдлит.
, где Uн.а.
, Iн.а.
– номинальное напряжение и ток автомата.
Предохранители используют для защиты источников питания от перегрузок и коротких замыканий в силовых цепях и цепях управления, для защиты и сигнализации. Различают предохранители с большой тепловой инерцией – свинцовые токопроводящие проводники и с малой тепловой инерцией – медные проводники. В системах автоматики наиболее распространены медные предохранители.
В цепях управления и сигнализации плавкие предохранители выбираются по соотношению: где наибольший суммарный ток, потребляемый катушками реле и контакторов, сигнальными лампами при их одновременной работе; наибольший суммарный ток, потребляемый катушками аппаратов, включаемых одновременно.
Расчет источников питания.
Для электропитания задатчиков, регуляторов, различных электронных и электромагнитных устройств автоматики используются источники питания постоянного тока. Общая структурная схема (рис. 4.1.) источника питания постоянного тока включает в себя: трансформатор (Тр), выпрямитель (В), фильтр (Ф), стабилизатор (Ст).

Рис. 10. Общая структура источника питания.
Исходными данными для расчета трансформаторов являются: тип и материал магнитопровода, амплитуда переменной составляющей индукции Вm = 0,5…1,5 Тл и частота перемагничивания f; наибольшее действующее значение напряжения E1
≈ U1
; наибольшее действующее значение тока первичной обмотки I1
= Iн
U2/(U1
·η), где η = 0,84…0,96 – КПД трансформатора. Цель расчета – определение типоразмера магнитопровода, чисел витков обмоток, коэффициент трансформации и сечения проводов.
Электрические исполнительные двигатели.
Необходимость преобразования переменного тока в постоянный удорожает и усложняет конструкцию электроприводов постоянного тока. Они менее надежны в эксплуатации, чем бесколлекторные машины переменного тока.
Двухфазные асинхронные двигатели.
В маломощных следящих системах и исполнительных механизмах преимущественно применяют двухфазные двигатели с короткозамкнутым ротором. Они обладают небольшим моментом трения. Мощность усилителей, необходимая для управления этими двигателями, меньше мощности самих двигателей, так как часть мощности двигатель получает непосредственно от источника переменного тока с напряжением U ~.
К недостаткам двухфазных двигателей по сравнению с двигателями постоянного тока относят больший удельный объем на единицу мощности и малый КПД. Однако простота их конструкции обеспечивает высокую надежность в эксплуатации.
Асинхронные двигатели мощностью до 600 Вт чаще всего питаются от однофазной сети с фазосдвигающим конденсатором. При включении трехфазного двигателя в однофазную сеть возможны различные схемы включения.
Трехфазные асинхронные двигатели.
Исполнительные двигатели переменного тока мощностью свыше 500 Вт, как правило, трехфазные и питаются от трехфазной сети через управляющие устройства. Энергетические и регулировочные свойства асинхронных двигателей определяются электромагнитным вращающим моментом и статическими характеристиками.
Исполнительные двигатели как объекты автоматического управления.
Автоматические системы с исполнительными электрическими двигателями, как правило, рассчитывают на основе упрощенных передаточных функций, которые определяют из интегро-дифференциальных уравнений, описывающих поведение исполнительных двигателей в переходных процессах. Однако они дают возможность анализировать устойчивость и динамические характеристики систем электроавтоматики с исполнительными двигателями в линейном приближении при малых отклонениях координат относительно установившихся значений.
Основными показателями исполнительных механизмов с постоянной скоростью перемещения исполнительного органа, которые необходимо учитывать при их выборе, являются:
а) максимальное среднесуточное число включение в 1ч.;
б) момент на валу исполнительного двигателя;
в) мощность электродвигателя;
г) оптимальное передаточное отношение редуктора;
д) скорость перемещения регулирующего органа.
Регулирующие органы.
В качестве регулирующих органов используются различные заслонки, задвижки, клапаны, краны, ножи тарельчатых питателей и т. п.
В конечном счете, регулирующий орган меняет проходное сечение (отверстие) или сопротивление на пути следования вещества или энергии в объект управления. К основным характеристикам регулирующих органов относятся – перемещающее усилие, диапазон регулирования, расходная характеристика.
Расходной характеристикой
называется зависимость между изменением положения регулирующего органа в процентах и расходом подаваемого в объект вещества. Расход вещества, однако, зависит не только от положения регулирующего органа, но и от свойств подаваемого вещества, его плотности, вязкости, от условий работы регулирующего органа, в том числе напора, сопротивления среды, перепада давления на регулирующем органе.
Расходные характеристики могут быть линейными и нелинейными. Наиболее предпочтительна линейная зависимость между расходом, подаваемого в объект компонента, и положением регулирующего органа.
Если простым сочленением ИМ с РО не удается добиться линейности, то используются нелинейные связи (сочленения) с помощью профилированных кулачков и тяг для придания характеристики желательной формы.
Наиболее простым видом РО являются регулирующие краны, используемые при управлении расходом потоков воды, а также вязких и агрессивных жидкостей.
Последовательность расчета гидравлических исполнительных устройств.
Исходными данными для расчета являются:
а) заданная полезная нагрузка Т на штоке поршня при рабочем ходе (вправо); при холостом ходе нагрузка отсутствует;
б) заданная скорость рабочего хода поршня Vп
.
Порядок расчета.
1. Определяем рабочее давление привода из нормализованного ряда давлений (ГОСТ 356-59) Р, руководствуясь технологическими условиями, конструктивными особенностями машины, наличием гидроаппаратуры.
2. Рассчитываем диаметр цилиндра Д0
из условия:
пологая, что до 20% (0,2) мощности насосной станции расходуется на преодоление сопротивлений в гидравлических магистралях и управляющей аппаратуры привода, на трение в исполнительном механизме и уплотнениях штока и поршня гидроцилиндра:

3. Выбор основных параметров гидроцилиндров, в том числе диаметров поршней и штоков, регламентируется ГОСТ 6340-64. Поэтому полученный диаметр Д0
следует округлить до ближайшего стандартного значения (округление проводится, как правило, в сторону увеличения) .
Диаметр штока dш
определяется обычно из условия:
.
Полученный dш
также округляют до ближайшего большого по ГОСТ 6540-64 dш
.
Рис. 4.2. Структурная схема гидропривода: 1) Насос; 2) Предохранительный клапан;
3) Фильтр; 4) Золотник; 5)обратный клапан; 6) Дроссель; 7) Цилиндр.
4. Определение рационального диаметра трубопроводов гидропривода d проводится после подсчета расхода Qмасла
, необходимого для обеспечения заданной скорости поршня цилиндров диаметром :
.
5. Рекомендуемая скорость течения жидкости в трубопроводах при рабочих давлениях от 25 • 105
Н/м2
до 100 • 105
Н/м2
составляет 3 – 6 м/сек, возрастая с увеличением давления. Принимая эту скорость в приводе машины Vр
, определяем внутренний диаметр трубопровода из равенства:
, откуда .
6. Полученный диаметр также округляют до ближайшего большого по ГОСТ 355-67 d*
.
7. По полученным ориентировочным расчетам для монтажа системы выбирают по ГОСТ 8734-58 трубы определенного материала, внешнего диаметра и толщины стенки, рассчитанные на эксплуатацию при выбранном рабочем давлении Р или ниже.
8. При выборе аппаратуры руководствуются допустимым давлением Р и расходом Q, которые рекомендует завод – изготовитель для каждого аппарата. Выбирают наименования и типоразмеры насоса, предохранительного клапана, фильтра, золотника, дросселя и обратного клапана.
9. В ответственных случаях после ориентировочного расчета необходимо провести поверочные расчет привода с целью определения всех потерь и произвести корректировку параметров, которые были получены при ориентировочном расчете.
Последовательность расчета пневматических исполнительных устройств.
Расчет параметров и подбор аппаратуры пневмопривода (рис. 4.3.) производится из следующих заданных условий:
а) полезная нагрузка Т на штоке поршня при рабочем ходе (вправо); при холостом ходе нагрузка отсутствует;
б) установившаяся скорость движения поршня Vп
.
Порядок расчета.
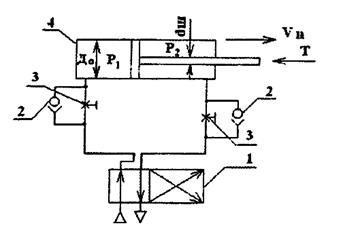
Рис. 11. Структурная схема пневмопривода: 1) Золотник; 2) Обратные клапаны; 3) Дроссели; 4) Пневмоцилиндр.
1. Диаметр цилиндра Д0
рассчитывается из условия: , откуда , где Р1
и Р2
– абсолютные давления соответственно в левой и правой полостях цилиндра, Д0
– диаметр цилиндра; k – коэффициент, учитывающий потери на трение в цилиндре.
Площадь штока в виду ее незначительной величины по сравнению с площадью поршня не учитывается при расчете пневмопривода.
Давление Р1
при достаточно больших проходных сечениях трубопровода можно считать равным давлению Рс
воздуха в сети.
Абсолютное давление в выходной полости цилиндра рекомендуется не менее 2 • 105
Н/м2
. Если к равномерности скорости движения поршня (особенно при меняющейся во время движения нагрузки Т) предъявляются повышенные требования или выхлопная магистраль имеет большое сопротивление, оно должно быть увеличено.
Значение коэффициента k колеблется в пределах 1,15 ÷ 1.3 в зависимости от нагрузки, возрастая с ее уменьшением.
2. Выбор основных параметров пневмоприводов, в том числе диаметров поршней и штоков, регламентируется ГОСТ 6540-64. Поэтому полученный диаметр Д0
, следует округлить до ближайшего большого стандартного значения .
3. Диаметр штока dш
выбирают обычно из условия:
.
Полученный диаметр dш
округляют до ближайшего большего по
ГОСТ 6540-64 .
4. Рекомендуемая скорость движения воздуха в трубопроводах пневматических приводов линейно зависит от давления. При Р = 1 • 105
Н/м2
она не должна превышать 40м/сек. При Р = 10 • 105
Н/м2
– ее рекомендуемая величина - не более 16 м/сек. Значение допустимой скорости Vдоп.
при промежуточных значениях легко найти с помощью интерполяции. Имея это ввиду, из условия можно найти внутренний диаметр d подводящий к цилиндру воздух трубопровода: .
Полученный диаметр трубопровода округляют до ближайшего большего значения по ГОСТ 35567 и получают d*
.
5. Подбор аппаратуры осуществляется по давлению и расходу аналогично подбору аппаратуры в гидроприводе.
Заключение
На кирпичном заводе применяется технология пластического формирования, по которой изготавливают кирпичи и камни согласно ГОСТ 530-95.
В качестве АСР я выбрал систему регулирования температуры в туннельной печи, в зоне обжига керамического кирпича. В результате проделанной работы я выбрал конкретные технические средства автоматизации, привел последовательности расчета электрических, гидравлических и пневматических исполнительных устройств. Усвоил принципы расчета автоматизированной системы управления.
Таким образом, представил автоматизированную систему контроля технологического процесса на современных кирпичных заводах.
Библиографический список
1 С.Ж. Сайбулатов. “Производство керамического кирпича”. Москва. Стройиздат 1989.
2 В.С. Щербаков, А.А. Руппель, В.А.Глушец “Основы моделирования систем автоматического регулирования и электротехнических систем в среде MATLAB и Simulink”. Учебное пособие. Омск. 2003.
3 Коновалов Л.И., Петелин Д.П. Элементы и системы электроавтоматики. М., 1980. – 216 с.
4 Лапшенков Г.И., Полоцкий Л.М. Автоматизация производственных процессов в химической промышленности. Технические средства и лабораторные работы. Изд. 3-е, перераб. и доп. М.: Химия, 1988. 288 с.
5 Приборы и средства автоматизации. Каталог 1.1 Приборы для измерения и регулирования температуры. Часть I-II. АО (“Информприбор”). Москва 1991.
6 Приборы и средства автоматизации. Каталог 2. Регулирующая и исполнительная техника. 2.1. Первичные и регулирующие устройства Часть II. АО (“Информприбор”). Москва. 1991
7 Приборы и средства автоматизации. Каталог 1. Устройства для контроля и регулирования технологических параметров. Приборы для измерения и регулирования уровня жидких и сыпучих сред. АО (“Информприбор”) Москва. 1991.
8 Приборы и средства автоматизации. Каталог 4. Приборы для нефтяной и газовой промышленности. Приборы регулирующие, пневматические. АО (“Информприбор”). Москва. 1991.
9 Приборы и средства автоматизации. Номенклатурный перечень серийно выпускаемых приборов и средства автоматизации .АО (“Информприбор”). Москва. 1991.
10 Приборы и средства автоматизации. Каталог 2. Регулирующая и исполнительная техника. Исполнительные механизмы и устройства. АО (“Информприбор”). Москва. 1991.
|