Министерство общего образования РФ
КАЗАНСКИЙ ГОСУДАРСТВЕННЫЙ ТЕХНОЛОГИЧЕСКИЙ
УНИВЕРСИТЕТ
НИЖНЕКАМСКИЙ ХИМИКО-ТЕХНОЛОГИЧЕСКИЙ
ИНСТИТУТ
Кафедра химической
технологии
Группа
Курсовой проект
Тема:
Получение этилбензола методом алкилирования бензола этиленом
Студентка:
Руководитель
(_________)
Студент
ка
(_________)
г. Нижнекамск
ВВЕДЕНИЕ
Темой данного курсового проекта является получение этилбензола методом алкилирования бензола этиленом.
Наиболее распространенным процессом нефтехимического синтеза является каталитическое алкилирование бензола олефинами, что определяется высоким спросом на алкилароматические углеводороды – сырьё в производстве синтетических каучуков, пластических масс, синтетических волокон и др.
Алкилированием называют процессы введения алкильных групп в мо- лекулы органических и некоторых неорганических веществ. Эти реакции имеют большое практическое значение для синтеза алкилароматических соединений, изо-алканов, аминов, меркаптанов и сульфидов и др.
Реакция алкилирования бензола алкилхлоридами в присутствии безводного хлорида алюминия впервые была осуществлена в 1877 г. Ш. Фриделем и Дж. Крафтсом. В 1878 г. ученик Фриделя Бальсон получил этилбензол алкилированием бензола этиленом в присутствии ALCL3
.
Со времени открытия реакции алкилирования было разработано много различных методов замещения водородных атомов бензола и других ароматических углеводородов на алкильные радикалы. Для этого применяли различные агенты алкилирования и катализаторы 48,49.
Скорость алкилирования ароматических углеводородов в несколько сот раз выше, чем парафинов, поэтому алкильная группа практически всегда направляется не в боковую цепь, а в ядро.
Для алкилирования ароматических углеводородов олефинами применяются многочисленные катализаторы, имеющие характер сильных кислот, в частности серная кислота (85-95%-ная), фосфорная и пирофосфорная кислоты, безводный фтористый водород, синтетические и природные
алюмосиликаты, иониты, гетерополикислоты. Кислоты в жидком виде проявляют каталитическую активность в реакциях алкилирования при невысоких температурах (5-100°С); кислоты на твердых носителях, например фосфорная кислота на кизельгуре, действуют при 200-300°С; алюмосиликаты активны при 300-400 и 500°С и давлении 20-40 кгс/см² (1,96-3,92 МН/м²).
Актуальность данной темы является, что в дальнейшем из этилбензола получают стирол, методом дегидрирования этилбензола.
1. ТЕОРЕТИЧЕСКАЯ ЧАСТЬ
2.1 Теоретические основы принятого метода производства.
Алкилирование бензола этиленом.
Промышленные процессы алкилирования бензола этиленом различаются в зависимости от применяемого катализатора. Ряд катализаторов опробован в опытно-промышленном масштабе.
В 1943 г.фирмой «Copers» осуществлено алкилирование бензола этиленом на алюмосиликатном катализаторе в жидкой фазе при 310°С и 63 кгс/см² (6,17 МН/м²) при мольном отношении этилен:бензол 1:4.
Широкое распространение приобрёл процесс алкилирования бензола этиленом на хлористом алюминии при атмосферном или несколько повышенном давлении и температуре 80-100°С.
Конкурирует с этим методом алкилирование на твердом фосфорнокислотном катализаторе, однако на этом катализаторе может быть получен только изопропилбензол. Алкилирование же бензола этиленом практически на нём не проводится.
Большую группу катализаторов алкилирования составляют апротонные кислоты (кислоты Льюиса) – галогениды некоторых металлов. Они обычно проявляют каталитическую активность в присутствии промоторов, с которыми образуют продукты, имеющие характер сильных протонных кислот. Из катализаторов этого типа могут применяться хлористый алюминий, бромистый алюминий, трёххлористое железо, хлористый цинк, трёххлористый и четырёххлористый титан. Промышленное применение имеет только хлористый алюминий.
О механизме реакций алкилирования бензола и его гомологов олефинами придерживаются следующих общих представлений.
Алкилирование в присутствии хлористого алюминия трактуется по механиз-
му кислотного катализа. В этом случае в системе должен присутство-
вать промотор, роль которого играет хлористый водород. Последний может
образоваться в присутствии воды:
ALCL3
+ Н2
О → ALOCL + 2HCL
Далее предполагается образование сильной алюминийхлористоводородной кислоты ALCL3
+ HCL → H – CL ∙ ALCL3
которая затем взаимодействует с олефином с образованием поляризованного комплекса:
CH3
CH=CH2
+ H – CL ∙ ALCL3
↔ CH3
– CH – CH3
∙ CL ∙ ALCL3
Дальнейшее присоединение к ароматическому ядру проходит по меха низму, аналогичному рассмотренному выше:
HCL(CH3
)2
∙CL∙ALCL3
+CH3
–CH–CH3
∙CL∙ALCL3
→HCH(CH3
)2
+ CH(CH3
)2
+ CL ∙ ALCL3
+ HCL + ALCL3
В присутствии хлористого алюминия легко протекает деалкилирование, что указывает на обратимость реакции алкилирования. Реакции деалкилирования пользуются для превращения полиалкилбензолов в моноалкил-
бензол.
Термодинамика реакции алкилирования.
На основе физико-химических
констант углеводородов и их термодинамических функций – энтальпии ΔН и
энтропии ΔS можно найти константы равновесия и рассчитать равновесные
выходы алкилпроизводных при алкилировании бензола олефинами в зависи-
мости от температуры и давления.
Равновесный выход этилбензола возрастает с увеличением мольного
избытка бензола и с повышением давления при данной температуре.
С6
H6
+ C2
H4
↔ C6
H5
C2
H5
При алкилировании бензола этиленом при температуре ниже 250-300°С
достигается практически полное превращение бензола в этилбензол. При 450
-500°С для увеличения глубины превращения требуется повышение давления до 10-20 кгс/см² (0,98-1,96 МН/м²).
Реакция алкилирования бензола этиленом является последовательной обратимой реакцией первого порядка. С углублением процесса наряду с моноалкилбензолом образуются также полиалкилбензолы
C6
H6
+ Cn
H2n
↔ C6
H5
Cn
H2n+1
C6
H5
Cn
H2
n
+1
+ Cn
H2
n
↔ C6
H4
(Cn
H2
n
+1
)2
которые являются нежелательными побочными продуктами. Поэтому состав реакционной смеси алкилатов чаще определяется кинетическими факторами, чем термодинамическим равновесием.
Так, деалкилирование термодинамически возможно с большой глубиной при 50-100°С. И действительно, в присутствии хлористого алюминия оно проходит хорошо, так как с этим катализатором процесс алкилирования является обратимым. Однако при тех же температурах в присутствии кислот деалкилирование вовсе не происходит. М.А. Далиным экспериментально изучен состав продуктов алкилирования бензола этиленом в присутствии хлористого алюминия.
Состав реакционной смеси определяется соотношением бензола и этилена и не зависит от того, каким образом получен алкилат: прямым алкилированием или деалкилированием полиалкилбензола. Однако этот вывод справедлив только при применении в качестве катализатора хлористого алюминия.
Процесс алкилирования проводится в алкилаторе – реакционной колонне, эмалированной или футерованной графитовой плиткой для защиты от коррозии. Три секции колонны имеют рубашки для охлаждения, однако основное количество тепла отводится испарением некоторой части бензола. Алкилирование ведется в присутствии жидкого катализаторного комплекса, состоящего из хлористого алюминия (10-12%), бензола (50-60%) и полиалкилбензолов (25-30%). Для образования хлористого водорода, который является промотором реакции, в каталитический комплекс добавляют 2% воды от
массы хлористого алюминия, а также дихлорэтан или хлористый этил, при расщеплении которых образуется хлористый водород.
Для выделения этилбензола из алкилата отгоняют при атмосферном давлении бензол (одновременно с бензолом удаляются следы воды). От кубовой жидкости при пониженном давлении (200 мм рт.ст., 0,026 МН/м²) отгоняется широкая фракция – смесь этилбензола и полиалкилбензолов. В следующей колонне при остаточном давлении 50 мм рт.ст. (0,0065 МН/м²) полиалкилбензолы отделяются от смол. Широкую фракцию разгоняют в вакуумной колонне при остаточном давлении 420-450 мм рт.ст. (0,054-0,058 МН/м²). Товарный этилбензол перегоняется в пределах 135,5-136,2°С.
Для получения этилбензола используется этан – этиленовая фракция пиролиза, содержащая 60-70% этилена.
Бензол для алкилирования должен содержать не более 0,003-0,006% воды, в то время как товарный бензол содержит 0,06-0,08% воды. Обезвоживание бензола проводится методом азеотропной дистилляции. Содержание серы в бензоле не должно превышать 0,1%. Повышенное содержание серы вызывает увеличение расхода хлористого алюминия и ухудшает качество готовой продукции.
1.2. Характеристика сырья и получаемого продукта.
Наименование сырья, материалов,
реагентов,
катализаторов.
полуфабрикатов,
изготовляемой
продукции.
|
Номер государст-
венного или
отраслевого
стандарта,
технических
условий
стандарта
предприятия.
|
Показатели качества, обязательные для проверки.
|
Норма (по
ГОСТу,
ОСТу,стан-
дарту предпри-
ятия)
|
Назна-чение,
область применения.
|
1
|
2
|
3
|
4
|
5
|
1.ЭТИЛБЕНЗОЛ
|
С6
H5
C2
H5
бесцветная прозрачная жидкость. Основные показатели свойств этилбензола:
Молекулярная масса=106,17
Плотность, г/см³ = 0,86705 Температура,°С Кипения= 176,1
Плавления=-25,4 Вспышки= 20
Самовоспламенения= 431.
Теплота, кДж/моль
Плавления=9,95
Испарения=33,85 Теплоёмкость, Дж/моль ∙ К=106,4
Теплота сгорания, ккал/моль=1089,4
Растворимость в воде, г/100мл=0,014
|
В промышленности используют в основном как сырье для синтеза стирола, как добавка к моторному топливу, в качестве разбавителя и растворителя. С6
H5
C2
H5
Большую часть этилбензола получают алкилированием бензола этиленом и значительно меньшее его количество выделяют сверхчеткой ректификацией из продуктов риформинга прямогонного бензина. Основные показатели свойств этилбензола: Этилбензол раздражает кожу, оказывает
судорожное действие. ПДК в атмосферном воздухе составляет 0,02 мг/м³, в водоёмах хозяйственно-
бытового пользования – 0,01 мг/л. КПВ 0,9-3,9% по объёму. Объём мирового
производства около 17 млн. т в год (1987). Объём производства в России 0,8
млн. т в год (1990).
|
2.ЭТИЛЕН
|
(этен)
H2
C=CH2
. Бесцветный газ со слабым запахом. Этилен растворяется в воде 0,256 см³/см³ (при 0 °С), растворяется в спиртах и эфирах.
Этилен обладает свойствами фитогормонов – замедляет рост, ускоряет старение клеток, созревание и опадение плодов. Он взрывоопасен, КПВ 3-34% (по объёму), ПДК в атмосферном воздухе 3 мг/м³, в воздухе рабочей зоны 100 мг/м³. Мировое производство 50 млн. т в год (1988).
|
В больших количествах (20%) содержится в газах нефтепереработки; входит в состав коксового газа. Один из основных продуктов нефтехимической промышленности: применяется для синтеза винилхлорида, этиленоксида, этилового спирта, полиэтилена и др. Этилен получается при переработке нефти и природного газа. Выде-
ленная этиленовая фракция содержит 90-95% этилена с примесью пропилена, метана, этана. Применяется как сырьё в производстве полиэтилена, окиси этилена, этилового спирта, этаноламина, поливинилхлорида, в хирургии – для наркоза.
|
 |
3.БЕНЗОЛ
|
C6
H6
. Бесцветная жидкость со своеобразным нерезким запа
хом. С воздухом образует взрывоопасные смеси, хорошо смешивается с эфирами, бензином и другими органическими растворителями. Растворимость в воде 1,79 г/л (при 25 °С). Токсичен, опасен для окружающей среды, огнеопасен. Бензол – ароматический углеводород.
Основные показатели свойств бензола:
Молекулярная масса=78,12
Плотность, г/см³=0,879
Температура, °С:
Кипения=80,1
Плавления=5,4
Вспышки=-11
Самовоспламенения=562
Теплота, кДж/моль:
Плавления=9,95
Испарения=33,85
Теплоёмкость, Дж/моль ∙ К=81,6
Бензол смешивается во всех отношениях с неполярными растворителями: углеводородами, скипидаром, эфирами, растворяет жиры, каучук, смолы (гудрон). Даёт с водой азеотропную смесь с температурой кипения 69,25 °С, образует двойные и тройные азеотропные смеси со многими соединениями.
|
Встречается в составе некоторых
нефтей, моторных топлив, бензинов. Широко применяется в промышленности, является исходным сырьём для производства лекарств, различных пластмасс, синтетической резины, красителей. Бензол входит в состав сырой нефти, но в промышленных масштабах по большей части синтезируется из других её компонентов. Применяется также для получения этилбензола, фенола, нитробензола, хлорбензола, как растворитель.
В зависимости от технологии производства получают различные марки бензола. Бензол нефтяной получают в процессе каталитического риформинга бензиновых фракций, каталитического гидродеалкилирования толуола и ксилола, а также при пиролизе нефтяного сырья.
|
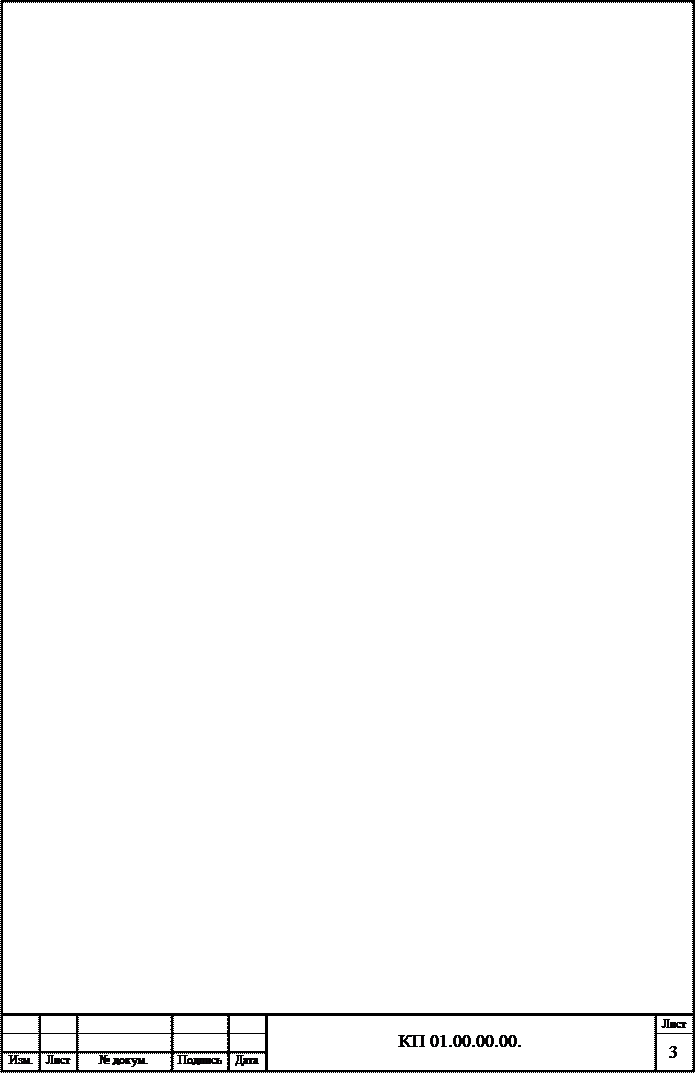 |
2.3. Описание технологической схемы.
В Приложении А представлена технологическая схема производства этилбензола. Процесс алкилирования бензола этиленом проводится в алкилаторе поз. Р-1 в среде этилхлорида при температуре 125-135C и давлении 0,26-0,4 МПа. В алкилатор подаются: осушенная бензольная шихта, каталитический комплекс, фракция полиалкилбензолов, этилен, рециркулирующий каталитический комплекс, возвратный бензол.
Реакция алкилирования идет с выделением теплоты, избыточное количество которой снимается рециркулирующим каталитическим комплексом и испаряющимся бензолом. Бензол из верхней части алкилатора в смеси с абгазом направляется в конденсатор поз. Т-1, охлаждаемый водой. Несконденсировавшиеся газы из конденсатора поз. Т-1 направляются в конденсатор поз. Т-2, охлаждаемый охлажденной водой t=0°C. Отдувки после конденсатора поз. Т-2 поступают на дальнейшее улавливание паров бензола. Бензольный конденсат из конденсаторов поз. Т-1 и Т-2 самотеком сливается в низ алкилатора поз. Р-1. Из алкилатора поз. Р-1 реакционная масса через теплообменник поз. Т-3, где охлаждается водой до 40—60 °С, направляется в отстойник поз. Е-1 для отделения от циркулирующего каталитического комплекса. Отстоявшийся каталитический комплекс с низа отстойника поз. Е-1 забирается насосом поз. Н-1 и возвращается в алкилатор поз. Р-1. Для поддержания активности катализатора в линию рециркулирующего комплекса подается этилхлорид. В случае снижения активности катализатора предусмотрен вывод, отработанного каталитического комплекса на разложение. Реакционная масса из отстойника поз. Е-1 собирается в емкость поз. Е-2, откуда за счет давления в системе алкилирования поступает в смеситель поз. Е-3 на смешение с Кислой водой, циркулирующей в системе разложения:
отстойник поз. Е-4—насос, поз. Н-2—смеситель, поз. Е-3. Соотношение циркулирующей воды, подаваемой в смеситель, и реакционной массы составляет l/2 : 1. Во да в систему разложения подается из сборника поз. Е-5 насосом поз. Н-3. Реакционная масса отстаивается от воды в отстойнике поз. Е-4; нижний водный слой насосом поз. Н-2 направляется в смеситель; а верхний слой — реакционная масса — самотеком стекает в промывную колонну поз. К-1 на вторичную промывку водой, подаваемой насосом поз. Н-4 из промывной колонны поз. К-2. Из промывной колонны поз. К-1 реакционная масса самотеком поступает в сборник поз. Е-6, откуда насосом поз. Н-5 откачивается на нейтрализацию в смеситель поз. Е-7.
Нижний водный слой из промывной колонны поз. К-1 самотеком сливается в емкость поз. Е-5 и насосом поз. Н-3 подается в смеситель поз. Е-3. Нейтрализация реакционной массы в смесителе поз. Е-7 проводится 2—10%-ным раствором едкого натра. Соотношение реакционной массы и циркулирующего раствора едкого натра 1:1.Отделение реакционной массы от раствора щелочи происходит в отстойнике поз. Е-8, откуда реакционная масса самотеком поступает в колонну поз. К-2 на отмывку от щелочи водным конденсатом. Нижний слой — химически загрязненная вода — из колонны сливается в емкость поз. Е-9 и насосом поз. Н-4 откачивается на промывку реакционной массы в колонну поз. К-1. Реакционная масса из верхней части колонны самотеком поступает в отстойник поз. Е-10, затем собирается в промежуточную емкость поз. Е-11 и откачивается насосом поз. Н-7 на склад.
Технологическая схема алкилирования бензола этиленом на хлористом алюминии, пригодная также и для алкилирования бензола пропиленом.
Процесс алкилирования проводится в алкилаторе – реакционной колонне эмалированной или футерованной графитовой плиткой для защиты от коррозии. Три секции колонны имеют рубашки для охлаждения, однако основное количество тепла отводится испарением некоторой части бензола. Алкилирование ведется в присутствии жидкого катализаторного комплекса, состоящего из хлористого алюминия (10 – 12 %), бензола (50 – 60 %) и
полиалкилбензолов (25 – 30 %). Для образования хлористого водорода, который является промотором реакции, в каталитический комплекс добавляют 2 % воды от массы хлористого алюминия, а также дихлорэтан или хлористый этил, при расщеплении которых образуется хлористый водород.
1.5. Описание устройств и принцип действия основного аппарата.
Алкилирование производится в реакторе колонного типа без механического перемешивания при давлении, близком к атмосферному (Приложение Б). Реактор состоит из четырёх царг, эмалированных или футерованных керамическими либо графитовыми плитками. Для лучшего контактирования внутри реактора имеется насадка. Высота реактора 12 м, диаметр 1,4 м. Каждая царга снабжена рубашкой для отвода тепла при нормальном режиме работы реактора (она же используется для разогрева при пуске реактора). Реактор доверху заполнен смесью бензола и катализатора. В нижнюю часть реактора непрерывно подают осушенный бензол, каталитический комплекс и газообразный этилен. Жидкие продукты реакции алкилирования непрерывно отбирают на высоте примерно 8 м от основания реактора, а сверху реактора отводится паро-газовая смесь, состоящая из непрореагировавших газов и паров бензола. Температура в нижней части реактора равна 100°С, в верхней – составляет 90 - 95°С. Катализаторный комплекс приготовляют в аппарате, откуда суспензия катализатора непрерывно подаётся в реактор алкилирования.
Алкилатор для получения этилбензола в жидкой фазе представляет собой стальную колонку, выложенную внутри кислотоупорной футеровкой поз. 4
или покрытую кислотоупорной эмалью для защиты стенок от корродирующего действия соляной кислоты. Аппарат имеет четыре царги поз.1,
соединенные фланцами поз. 2.
Три царги снабжены рубашками поз. 3
для охлаждения водой (для отвода тепла при реакции алкилирования). Реактор во время работы заполнен реакционной жидкостью, высота столба которой составляет 10 м
.
Над уровнем жидкости иногда располагают два змеевика, в которых циркулирует вода, для дополнительного охлаждения.
Работа алкилатора непрерывна: в нижнюю часть его все время подаются бензол, этилен и каталитический комплекс; смесь реагирующих веществ и катализатора поднимается в верхнюю часть аппарата и отсюда перетекает в отстойник. Пары, выходящие из верхней части алкилатора (состоящие в основном из бензола), конденсируются и снова возвращаются в алкилатор в виде жидкости.
За один проход этилен реагирует почти полностью, а бензол только на 50—55%; следовательно, выход этилбензола за один проход составляет около 50% от теоретического; остальной этилен теряется на образование ди- и полиэтилбензола.
Давление в алкилаторе во время работы составляет 0,5 ат
(избыточное), температура 95—100°С.
Алкилирование бензола этиленом можно вести и в газовой фазе, над твердым катализатором, но этот метод еще мало применяется в промышленности.
Выход этилбензола составляет 90 – 95 % в расчёте на бензол и 93 % в расчёте на этилен. Расход на 1 т этилбензола составляет: этилена 0,297 т,
бензола 0,770 т, хлористого алюминия 12 – 15 кг.
2. ВЫВОДЫ ПО ПРОЕКТУ.
Наиболее дешёвый этилбензол получают выделением его из ксилольной фракции продуктов риформинга или пиролиза, где он содержится в количестве 10-15 %. Но основным способом получения этилбензола остаётся способ каталитического алкилирования бензола.
Несмотря на наличие многотоннажных производств алкилбензолов, существует ряд нерешённых проблем, снижающих эффективность и технико-экономические показатели процессов алкилирования. Можно отметить следующие недостатки:
- Отсутствие стабильных, высокоактивных катализаторов алкилирования бензола олефинами; нашедшие же широкое применение катализаторы – хлорид алюминия, серная кислота и др.вызывают коррозию аппаратуры, не регенерируются;
- Протекание вторичных реакций, снижающих селективность производства алкилбензолов, что требует дополнительных затрат на очистку получаемых продуктов;
- Образование большого количества сточных вод и отходов производств при существующих технологических схемах алкилирования;
- Недостаточные единичные мощности производства.
Таким образом, вследствие большой ценности этилбензола, в настоящее время спрос на него очень велик, при этом его себестоимость сравнительно невысока. Сырьевая база для получения этилбензола также широка: бензол и этилен в больших количествах получаются при крекинге и пиролизе нефтяных фракций.
3. СТАНДАРТИЗАЦИЯ
В курсовом проекте были применены следующие ГОСТы:
ГОСТ 2.105 – 95 Общие требования к текстовым документам.
ГОСТ 7.32 – 81 Общие требования и правила оформления курсовых и дипломных работ.
ГОСТ 2.109 – 73 Основные требования чертежа.
ГОСТ 2.104 – 68 Основные надписи на чертежах.
ГОСТ 2.108 – 68 Спецификации.
ГОСТ 2.701 – 84 Схемы, виды, типы, общие требования.
ГОСТ 2.702 – 75 Правила выполнения схем различных видов.
ГОСТ 2.721 – 74 Обозначения условные и графические в схемах.
ГОСТ 21.108 – 78 Условное и графическое изображение на чертежах.
ГОСТ 7.1 – 84 Правила оформления списка литературы.
4. СПИСОК ИСПОЛЬЗУЕМОЙ ЛИТЕРАТУРЫ.
1. Травень В.Ф. Органическая химия: в 2 т: учеб.для вузов / В.Ф. Травень. – М.: НКЦ Академкнига, 2005. – 727 с.: ил. – Библиогр.: с. 704 – 708.
2. Эпштейн Д.А. Общая химическая технология: учеб.для ПТУ / Д.А. Эпштейн. – М.: Химия, - 1979. – 312 с.: ил.
3. Литвин О.Б. Основы технологии синтеза каучуков. / О.Б. Литвин. – М.: Химия, 1972. – 528 с.: ил.
4. Ахметов Н.С. Общая и неорганическая химия: учеб.для вузов – 4-е изд., испр. / Н.С. Ахметов. – М.: Высшая школа, изд. центр Академия, 2001. – 743 с.: ил.
5. Юкельсон И.И. Технология основного органического синтеза. / И.И. Юкельсон. – М.: Химия, -1968. – 820 с.: ил.
6. Паушкин Я.М., Адельсон С.В., Вишнякова Т.П. Технология нефтехимического синтеза: часть 1: Углеводородное сырьё и продукты его окисления. / Я.М. Паушкин, С.В. Адельсон, Т.П. Вишнякова. – М.: Химия, -1973. – 448 с.: ил.
7. Лебедев Н.Н. Химия и технология основного органического и нефтехимического синтеза: учеб.для вузов – 4-е изд., перераб. и доп. / Н.Н. Лебедев. – М.: Химия, -1988. – 592 с.: ил.
8. Платэ Н.А., Сливинский Е.В. Основы химии и технологии мономеров: учеб.пособие. / Н.А.Платэ, Е.В.Сливинский. – М.: МАИК Наука / Интерпериодика, -2002. – 696 с.: ил.
СОДЕРЖАНИЕ.
Введение…………………………………………………………………………3
2.Технологическая часть……………………………………………………….
2.1. Теоретические основы принятого метода производства………….5
2.2. Характеристика сырья и получаемого продукта…………………..9
2.3. Описание технологической схемы…………………………………12
2.4. Материальный расчёт производства……………………………….15
2.5. Описание устройства и принцип действия основного аппарата….20
3. Выводы по проекту………………………………………………………….22
4. Стандартизация………………………………………………………..........24
5. Список используемой литературы…………………………………………25
6. Спецификация………………………………………………………………26
7. Приложение А………………………………………………………………27
8. Приложение Б………………………………………………………………28
|