Содержание
|
Введение |
5 |
1.Техническое задание |
6 |
2.Техническое предложение |
6 |
2.1 Назначение узлов и проектируемого привода в целом |
7 |
2.2 Выбор компоновки привода |
7 |
2.3 Кинематический расчет |
8 |
2.3.1 Выбор электродвигателя |
8 |
2.3.2 Определение общего передаточного числа привода |
11 |
2.3.3 Вычисление частот вращения валов редуктора |
13 |
2.4 Силовой расчет |
13 |
2.4.1 Вычисление вращающих моментов на валах редуктора |
13 |
2.5 Выбор твердости, термической обработки и материала колес |
15 |
2.6 Допускаемые контактные напряжения |
15 |
2.7 Допускаемые напряжения изгиба |
21 |
2.8 Расчет цилиндрических зубчатых передач |
23 |
2.8.1 Межосевое расстояние |
24 |
2.8.2 Предварительные основные размеры колеса |
26 |
2.8.3 Модуль передачи |
27 |
2.8.4 Суммарное число зубьев и угол наклона |
28 |
2.8.5 Число зубьев шестерни и колеса |
29 |
2.8.6 Фактическое передаточное число |
30 |
2.8.7 Диаметры колес |
30 |
2.8.8 Размеры заготовок |
32 |
2.8.9 Проверка зубьев колес по контактным напряжениям |
33 |
2.8.10. Силы в зацеплении |
34 |
2.8.11 Проверка зубьев колес по напряжениям изгиба |
35 |
2.8.12 Проверочный расчет на прочность зубьев при действии пиковой нагрузки |
36 |
3. Эскизный проект |
40 |
3.1 Определение диаметров валов и предварительный выбор подшипников |
40 |
3.2 Эскизная компоновка редуктора |
44 |
4. Расчет валов привода на прочность |
45 |
5. Расчет подшипников для валов привода
6. Определение размеров элементов корпуса, крышек и др. деталей
|
62
67
|
7. Расчет посадок с натягом
8. Расчет цепной передачи
|
69
74
|
9. Расчет предохранительной муфты
10. Расчет исполнительного механизма
11. Проверочный расчет шпоночных соединений
Библиографический список
|
82
89
|
Приложения |
93 |
Введение
Машиностроению принадлежит ведущая роль среди других отраслей экономики, так как основные производственные процессы выполняют машины. Технический уровень многих отраслей определяет уровень развития машиностроения.
Развитие машиностроения возможно только при широком внедрении специализации, механизации и автоматизации, использовании принципов взаимозаменяемости, унификации и стандартизации сборочных единиц и деталей машин, внедрении прогрессивных технологий.
Машины прочно вошли в жизнь общества. В настоящее время трудно найти предмет или продукт потребления, который был бы изготовлен или доставлен к месту потребления без помощи машин. Без машин невозможно было бы современное развитие наук, медицины, искусства, требующих совершенных инструментов и материалов, не могли бы удовлетворяться потребности населения в предметах широкого потребления.
В свою очередь создание мощных, высокопроизводительных, технологичных и экономичных машин невозможно без постоянного их конструктивного совершенствования, использования новых, более прочных и износостойких материалов, различных способов их упрочнения и коррозионной защиты, совершенствования форм деталей.
Основными задачами конструкторов-машиностроителей являются повышение качественных и эксплуатационных показателей, сокращение времени разработки и внедрения новых машин, повышение их надежности и долговечности.
1.Техническое задание
Разработать привод транспортера роликового со следующими характеристиками:
1) тяговое усилие ;
2) скорость ролика ;
3) кратность пускового момента ;
4) тип предохранительной муфты − фрикционная конусная;
5) график нагрузки −III;
6) срок службы: ; ;
7) среда − влажная;
8) требования к приводу − минимальная длина.
9) параметры рабочего органа – диаметр ролика 350 мм, длина – 400 мм.
2.Техническое предложение
Транспортеры классифицируют в зависимости от:
1) направления перемещения объектов: горизонтальные, вертикальные, наклонные;
2) типа груза: насыпные и штучные;
3) выполняемых функций: транспортировочные и сборочные;
4) размещения самого транспортера или деталей: напольные и подвесные;
5) тягового органа: ленточные, цепные, роликовые, канатные, без тягового органа (гравитационные, инерционные, винтовые);
6) грузонесущей конструкции (с тяговым органом): ленточный, пластинчатый, роликовый, люлечный, скребковый, ковшовый.
2.1 Назначение узлов и проектируемого привода в целом
Электродвигатель – устройство, преобразующее электрическую энергию в механическую, создавая вращающий момент.
Муфта упругая служит для соединения вала электродвигателя с быстроходным валом редуктора, также для снижения динамической (ударной) нагрузки и предотвращения опасных колебаний.
Редуктор предназначается для понижения угловой скорости и повышения крутящего момента.
Муфта предохранительная служит для передачи крутящего момента, ограничивает передаваемый момент и предохраняет узлы привода от поломок при перегрузках, превышающих расчётные.
Исполнительным механизмом является приводной ролик.
2.2 Выбор компоновки привода
Целью разработки технического предложения является определение кинематической схемы будущего привода, соответствующего техническому заданию.
Зная параметры выходного звена привода, и учитывая требования, предъявляемые к нему, рассчитаем предварительные размеры возможных компоновок привода при помощи ЭВМ. Для составления компоновок использовали: цилиндрический развернутый редуктор; цилиндрический соосный вертикальный однопоточный (2-х ст.) редуктор; планетарный редуктор; коническо-цилиндрический редуктор. Полученные результаты включают в себя: габаритные размеры основных узлов привода, кинематические характеристики и подбор электродвигателя (приложения 1- 4).
Проанализировав полученные схемы компоновок с учетом требования по минимальной длине привода, примем для дальнейшего расчета компоновку, состоящую из электродвигателя 1, упругой муфты 2, цилиндрического развернутого редуктора 3, цепной передачи 4, предохранительной муфты 5, встроенной в ролик, и исполнительного механизма 6 в виде ролика.
                  Полученные при расчете на ЭВМ кинематические характеристики примем за исходные данные для дальнейшего расчета привода.
Рисунок 1 – Кинематическая схема привода
2.3 Кинематический расчет [1]
2.3.1 Выбор электродвигателя
Расчёт приводной установки начинают с выбора электродвигателя и определения общего передаточного числа привода.
Для выбора электродвигателя определяют требуемую его мощность и частоту вращения.
Требуемая мощность электродвигателя:
, |
(1) |
где: – мощность на выходе (потребляемая);
– общий КПД привода.
Мощность на выходе (потребляемая):
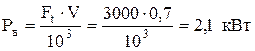
|
(2)
|
Общий КПД привода:
, |
(3)
|
где: – КПД зубчатой передачи; ;
– КПД цепной передачи; ;
– КПД муфты; ;
– КПД опор; .
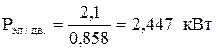
Выполним проверку электродвигателя на запуск.
Среднеквадратическая мощность:
,
где: – угловая скорость ролика;
– среднеквадратический момент.
Угловая скорость ролика:

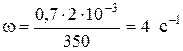
|
(4)
(5)
|
Среднеквадратический момент:
(6)


Частота вращения приводного вала ролика:
, |
(7) |
где Dр
– диаметр приводного ролика.
Требуемая частота вращения вала электродвигателя:
, |
(8) |
где: uц
– передаточное отношение цепной передачи;
uт
– передаточное отношение тихоходной ступени редуктора;
uб
– передаточное отношение быстроходной ступени редуктора.
2.3.2 Определение общего передаточного числа привода
|
(9) |
Из расчета на ЭВМ принимаем uц
=2,499 и uред
=29,85.
передаточное число тихоходной ступени:
 |
(10) |
 |
Передаточное отношение быстроходной ступени:

(11)
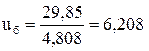
Требуемую частоту вращения вала электродвигателя вычисляем, подставляя в формулу (8) среднее значение передаточных чисел из рекомендуемого диапазона.
Выбираем электродвигатель АИС80В2, Р = 2,2 кВт, n = 2850 мин-1
.
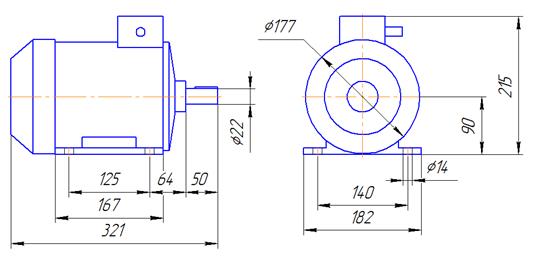
Рисунок 2 – Эскиз электродвигателя
2.3.3 Вычисление частот вращения валов редуктора
Частота вращения вала колеса тихоходной ступени:
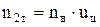 |
(12) |
Частота вращения вала шестерни тихоходной ступени:
 |
(13) |
Частота вращения вала шестерни быстроходной ступени:
|
(14) |
2.4 Силовой расчет [1]
2.4.1 Вычисление вращающих моментов на валах редуктора
Вращающий момент на приводном валу ролика:
|
(15) |
Момент на валу колеса тихоходной ступени редуктора:
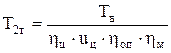 |
(16) |
 |
Вращающий момент на валу шестерни тихоходной ступени:
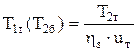 |
(17) |
Вращающий момент на валу шестерни быстроходной ступени:
|
(18) |
2.5 Выбор твердости, термической обработки и материала колес [1]
В зависимости от вида изделия, условий его эксплуатации и требований к габаритным размерам выбирают необходимую твердость колес и материал для их изготовления. Для силовых передач чаще всего применяют стали. Передачи со стальными зубчатыми колесами имеют минимальную массу и габариты, тем меньшие, чем выше твердость рабочих поверхностей зубьев, которая в свою очередь зависит от марки стали и варианта термической обработки.
Принимаем передачи редуктора косозубыми.
Выбранные твердости, термическая обработка и материала колес представлены в таблице 1.
Таблица 1 – Выбранные материалы
Ступень |
Марка стали |
Твердость зубьев |
,
МПа
|
Термо-обработка |
в сердцевине |
на поверхности |
1-ая (б/ход.) |
колесо |
40Х |
235-262НВ |
235-262НВ |
640 |
Улучшение |
шестерня |
40Х |
269-302НВ |
269-302НB |
750 |
Улучшение |
2-ая (т/ход.) |
колесо |
40ХН |
235-262HB |
235-262HB |
630 |
Улучшение |
шестерня |
40ХН |
269-302HB |
269-302HB |
750 |
Улучшение |
2.6 Допускаемые контактные напряжения [1]
Определяют по общей зависимости, учитывая влияние на контактную прочность долговечности, шероховатости сопрягаемых поверхностей зубьев и окружной скорости.
, |
(19) |
где ZN
– коэффициент долговечности;
ZR
– коэффициент учитывающий шероховатость; ZR
=1;
Zv
– коэффициент учитывающий влияние угловой скорости; Zv
=1;
Sн
– коэффициент запаса прочности; Sн
=1,1.
предел контактной выносливости вычисляют по эмпирическим формулам в зависимости от материала и способа термической обработки
зубчатого колеса и средней твердости (НВср
или HRCэ ср
) :
|
(20) |
1-ая ступень:
для шестерни:
для колеса:
2-ая ступень:
для шестерни:
для колеса:
Коэффициент долговечности:
при условии , |
(21) |
где NHG
– число циклов, соответствующее перелому кривой усталости, определяют по средней твердости поверхностей зубьев:
 |
(22)
|
1-ая ступень:
для шестерни:
для колеса:

2-ая ступень:
для шестерни:
для колеса:

ресурс передачи в числах циклов перемены напряжений при частоте вращения n, об/мин и времени работы Lh
, час:
, |
(23) |
где n3
– число вхождений в зацепление зуба рассчитываемого колеса за один его оборот; n3
= 1.
, |
(24) |
где – количество лет; ;
– количество смен; ;
– количество часов в смену. .
Тихоходный вал:
Промежуточный вал:
Быстроходный вал:
Для длительно работающих быстроходных передач Nk
³NHG
и, следовательно, ZN
=1, что и учитывает первый знак неравенства в формуле (21). Второй знак неравенства ограничивает допускаемые напряжения по условию предотвращения пластической деформации или хрупкого разрушения поверхностного слоя: ZNmax
=2,6 для материалов с однородной структурой (улучшенных, объемно закаленных).
Эквивалентное число циклов:
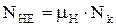 |
(25) |
где – коэффициент эквивалентности; .
Тихоходный вал:
Промежуточный вал:
Быстроходный вал:
Коэффициент долговечности шестерни быстроходной ступени:
Аналогично выполняем расчеты для других ступеней и результаты расчета сводим в таблице 2.
Таблица 2 – Коэффициенты долговечности
Коэффициенты долговечности |
шестерни быстроходной ступени |
0,606 |
колеса быстроходной ступени |
0,757 |
шестерни тихоходной ступени |
0,822 |
колеса тихоходной ступени |
0,983 |
По условию принимаем ZN
= 1.
Подставив все найденные значения в формулу (19) получим:
Допускаемые контактные напряжения шестерни быстроходной ступени:
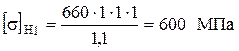
Аналогично выполняем расчеты для других ступеней и результаты расчета сводим в таблице 3.
Таблица 3 – Допускаемые контактные напряжения
допускаемые контактные напряжения |
, МПа |
шестерни быстроходной ступени |
600 |
колеса быстроходной ступени |
500 |
шестерни тихоходной ступени |
600 |
колеса тихоходной ступени |
500 |
В связи расположения линии контакта под углом к полюсной линии допускаемые напряжения можно повысить до значения:
, |
(26) |
где .
Условие выполняется.
|
2.7 Допускаемые напряжения изгиба [1]
Определяют по общей зависимости, учитывая влияние на сопротивление усталости при изгибе долговечности, шероховатости
поверхности, и реверса нагрузки:
, |
(27) |
где:  – предел выносливости;
– коэффициент долговечности;
– коэффициент учитывающий влияние шероховатости; = 1,1;
– коэффициент учитывающий влияние двухстороннего приложения нагрузки (реверса); = 0,65;
– коэффициент запаса прочности; = 1,7.
Предел выносливости для колеса:
 |
(28) |
Предел выносливости для шестерни:
при условии , |
(29) |
Коэффициент долговечности:
где: – число циклов соответствующее перелому кривой усталости; ;
– эквивалентное число циклов.
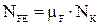 |
(30) |
где – коэффициент эквивалентности.
Для улучшенных зубчатых колес , .
эквивалентное число циклов для шестерни быстроходной ступени:
Аналогично выполняем расчеты для других ступеней, и результаты расчета сводим в таблице 4.
Таблица 4 – эквивалентное число циклов
эквивалентное число циклов |
 |
шестерни быстроходной ступени |
8,536∙108
|
колеса быстроходной ступени |
1,375∙108
|
шестерни тихоходной ступени |
1,375∙108
|
колеса тихоходной ступени |
2,86∙107
|
Коэффициент долговечности шестерни быстроходной ступени:
Аналогично выполняем расчеты для других ступеней и результаты расчета сводим в таблице 5.
Таблица 5 – Коэффициент долговечности
Коэффициент долговечности |
 |
шестерни быстроходной ступени |
0,409 |
колеса быстроходной ступени |
0,555 |
шестерни тихоходной ступени |
0,555 |
колеса тихоходной ступени |
0,72 |
По условию принимаем = 1.
Допускаемые напряжения изгиба для шестерни быстроходной ступени:
Аналогично выполняем расчеты для других ступеней и результаты расчета сводим в таблице 6.
Таблица 6 – Допускаемые напряжения изгиба
Допускаемые напряжения изгиба |
, МПа |
шестерни быстроходной ступени |
217,13 |
колеса быстроходной ступени |
176,65 |
шестерни тихоходной ступени |
217,13 |
колеса тихоходной ступени |
176,65 |
Принимаем наименьшее из допускаемых напряжений .
2.8 Расчет цилиндрических зубчатых передач [1]
Расчет приведем для первой (быстроходной) ступени.
2.8.1 Межосевое расстояние
Предварительный расчет межосевого расстояния:
(31)
Окружную скорость вычисляют по формуле:
(32)

Назначаем степень точности зубчатой передачи 8.
Межосевое расстояние вычисляем по формуле:
,
(33)
где: Ка
– коэффициент для косозубых колес; Ка
= 410;
yba
– коэффициент ширины;
– коэффициент нагрузки в расчетах на контактную прочность.
Из расчета на ЭВМ – ψbd
= 1,129.
, |
(34) |
, |
(35)
|
где: KH
n
– коэффициент учитывающий внутреннюю динамику нагружения; KH
n
=1,06;
KH
b
– коэффициент учитывающий неравномерность распределения нагрузки по длине контактной линии;
KHa
– коэффициент учитывающий распределение нагрузки между зубьями.
, |
(36) |
где: – коэффициент учитывающий неравномерность распределения нагрузки в начальный период работы; =1,18;
– коэффициент учитывающий приработку зубьев; 0,28.
 |
, |
(37) |
где – начальное значение распределения нагрузки между зубьями.
при условии ,
|
где: A= 0,25 – для зубчатых колес твердостью Н1
и Н2
£ 350НВ;
nст
= 8 – степень точности.

, принимаем
Из стандартного ряда примем aw
= 80 мм.
2.8.2 Предварительные основные размеры колеса
делительный диаметр колеса быстроходной ступени:
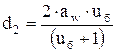
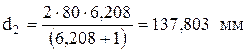
|
(38) |
ширина колеса быстроходной ступени:
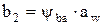 |
(39) |
Принимаем b2
= 25 мм.
2.8.3 Модуль передачи
модуль быстроходной ступени:
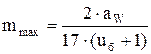
|
(40)
|

,
где: Km
– для косозубых передач; Km
= 2,8∙103.
KF
– коэффициент нагрузки при расчете по напряжениям изгиба:
|
(41)
|
, (42)
где KFv
– коэффициент учитывающий внутреннюю динамику нагружения; KFv
= 1,12;
KFβ
– коэффициент учитывающий неравномерность распределения нагрузки по длине контактной линии;
KFα
– коэффициент учитывающий распределение нагрузки между зубьями; KFα
= 1,6.
(43)

(44)

Принимаем меньшее значение, согласуя его со стандартным, m= 1 мм.
2.8.4 Суммарное число зубьев и угол наклона
Минимальный угол наклона зубьев косозубых колес:
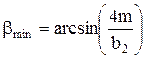 |
(45) |
Суммарное число зубьев:
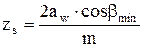 |
(46) |
Полученные значения zs
округляем в меньшую сторону до целого числа и определяют действительные значения угла b:
Принимаем zs
= 157.
Для косозубых колес .
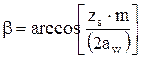 |
(47) |
2.8.5 Число зубьев шестерни и колеса
Число зубьев шестерни:
 |
(48) |
Значение z1
округляют в ближайшую сторону до целого числа z1
= 22.
Для косозубых колес:
(49)


22 ³ 16,06
Число зубьев колеса:
 |
(50) |
2.8.6 Фактическое передаточное число
Фактические значения передаточных чисел не должны отличатся от номинальных более чем на 4%.
 |
(51) |
Условие выполняется.
2.8.7 Диаметры колес
Делительный диаметр шестерни:
 |
(52) |
Делительный диаметр колеса:
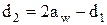 |
(53) |
Диаметр вершины шестерни:
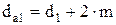 |
(54) |
Диаметр вершины колеса:
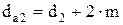 |
(55) |
Диаметр впадин шестерни:
 |
(56) |
Диаметр впадин колеса:
 |
(57) |
2.8.8 Размеры заготовок
Чтобы получить при термической обработки принятые для расчета механические характеристики материала колес, требуется, чтобы размеры Dзаг
, Sзаг
заготовок колес не превышали предельно допустимых значений Dпр
, Sпр
.
или |
Шестерни:
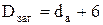 |
(58) |
мм, мм, условие выполняется.
Колеса:

мм, мм, условие выполняется.
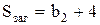 |
(59) |
, мм, условие выполняется.
так как неравенства выполняются, оставляем материал деталей и способ термической обработки.
2.8.9 Проверка зубьев колес по контактным напряжениям
Расчетное значение контактного напряжения:
, |
(60) |
где Zs
=8400 МПа1/2
для косозубых передач.
 |
(61) |
Так как расчетное напряжение sН
меньше [s]Н
в пределах 15-20%, то ранее принятые параметры передачи принимают за окончательные.
2.8.10 Силы в зацеплении
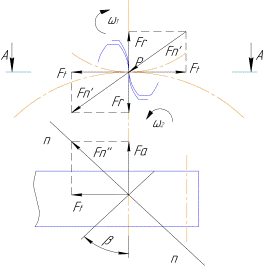
Рисунок 3 – Схема сил в зацеплении
окружная:
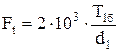 |
(62) |
радиальная:
 |
(63) |
осевая:
 |
(64) |
2.8.11 Проверка зубьев колес по напряжениям изгиба
Расчетное напряжение изгиба в зубьях колеса:
, |
(65) |
где: – коэффициент нагрузки при расчете по напряжениям изгиба; ;
UFS
2
– коэффициент учитывающий форму зуба колеса; UFS
2
= 3,59;
– коэффициента, учитывающего угол наклона зуба;
Ue
– коэффициент, учитывающий перекрытие зубьев; Ue
= 0,65 .
Значение коэффициента Ub
, учитывающего угол наклона зуба в
косозубой передачи, вычисляют по формуле:
(66)
122,27 < 176,65 условие выполнено.
Расчетное напряжение изгиба в зубьях шестерни:
, |
(67) |
где UFS
1
– коэффициент учитывающий форму зуба колеса; UFS
1
= 3,91.
133,17 < 217,13 условие выполнено.
2.8.12 Проверочный расчет на прочность зубьев при действии пиковой нагрузки
Целью расчета является предотвращение остаточных деформаций или хрупкого разрушения поверхностного слоя или самих зубьев при действии пикового момента Tпик
. Действие пиковых нагрузок оценивают коэффициентом перегрузки Кпер
=2,2. Если пиковый момент не задан, то его значение находят с учетом спецификации работы машины по пусковому моменту электродвигателя.
(68)

Для предотвращения остаточных деформаций или хрупкого
разрушения поверхностного слоя контактное напряжение sHmax
не должно превышать допускаемое напряжение [s]Hmax
.
, |
(69) |
где – контактное напряжение.
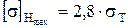 |
(70) |
где – предел текучести; .
774,81 < 1792 условие выполнено.
Для предотвращения остаточных деформаций и хрупкого разрушения зубьев напряжение σFmax
изгиба при действии пикового момента не должен превышать допускаемое [σ]Fmax
.
 |
(71) |
Для шестерни:
Для колеса:
Допускаемое напряжение вычисляют в зависимости от вида термической обработки:
, |
(72) |
где: σFlim
– предел выносливости при изгибе;
YNmax
– максимально возможное значение коэффициента долговечности;
kst
– коэффициент влияния частоты приложения пиковой нагрузки;
Sst
– коэффициент запаса прочности.
Для шестерни:
σFlim
=516,25 МПа; YNmax
=4; kst
=1; Sst
=1,75.
292,98 < 1180 условие выполнено.
Для колеса:
σFlim
=420 МПа; YNmax
=4; kst
=1,3; Sst
=1,75.
268 < 960 условие выполнено.
Аналогично выполняем расчет цилиндрической зубчатой передачи для второй ступени и результаты сводим в таблице 7.
Таблица 7 – Результаты расчета второй ступени
Межосевое расстояние, мм |
125 |
ширина колеса тихоходной ступени, мм |
40 |
Модуль передачи, мм |
2,5 |
Суммарное число зубьев |
96 |
угол наклона зубьев |
16,26 |
Число зубьев шестерни |
17 |
Число зубьев колеса |
79 |
Фактическое передаточное число |
4,647 |
Делительный диаметр шестерни, мм |
44,27 |
Делительный диаметр колеса, мм |
205,73 |
Диаметр вершины шестерни, мм |
49,27 |
Диаметр вершины колеса, мм |
210,73 |
Диаметр впадин шестерни, мм |
38,02 |
Диаметр впадин колеса, мм |
199,48 |
Размеры заготовок, мм |
шестерни |
56 |
колеса |
217 |
Расчетное значение контактного напряжения, МПа |
506,67 |
Допустимое значение контактного напряжения, МПа |
552,27 |
Силы в зацеплении, Н |
окружная |
2208 |
радиальная |
837,1 |
осевая |
644 |
Расчетное напряжение изгиба в зубьях колеса, МПа |
75,92 |
Расчетное напряжение изгиба в зубьях шестерни, МПа |
86,28 |
Допустимое значение напряжения изгиба в зубьях колеса, МПа |
176,65 |
Допустимое значение напряжения изгиба в зубьях шестерни, МПа |
217,13 |
Максимальное контактное напряжение, МПа |
751,51 |
Максимальное напряжение изгиба, МПа |
шестерни |
189,81 |
колеса |
167,01 |
допускаемое контактное напряжение, МПа |
1764 |
допускаемое напряжение изгиба, МПа |
шестерни |
1180 |
колеса |
960 |
3. Эскизный проект [1]
3.1 Определение диаметров валов и предварительный выбор подшипников
Предварительные значения диаметров различных участков стальных валов редуктора.
Для быстроходного входного вала (рис. 4)
 |
(73) |
мм
|
Т.к. быстроходный вал приводится во вращение валом электродвигателя через стандартную муфту, то диаметр выходного конца этого вала согласовываем с диаметром вала электродвигателя: .
Принимаем d = 18 мм ( ).
где tкон
– высота заплечика; tкон
= 1,5.
Назначаем подшипник радиальный шариковый однорядный серии 205
ГОСТ 8338-75.
Принимаем dn
= 25 мм – диаметр посадочного отверстия подшипника.
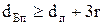 |
(75) |
где r=1,5– фаска подшипника.
dБ
n
= 25+3∙1,5 = 29,5 мм
|
Принимаем dБ
n
= 30 мм – диаметр буртика подшипника.
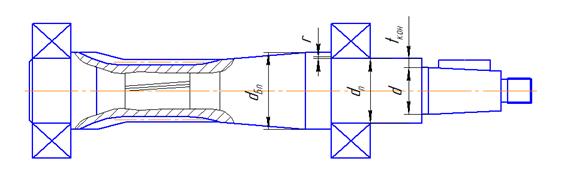
Рисунок 4 – Быстроходный вал
для промежуточного вала (рис.5)
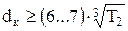 |
(76) |
мм |
Для унификации конструкции редуктора примем подшипники для промежуточного вала такие же, что и для быстроходного и проведем расчет диаметров оставшихся участков относительно диаметров под подшипники.
Принимаем dK
= 32 мм – диаметр посадочного отверстия зубчатого колеса.
, |
(77) |
где f= 1 – фаска колеса.
мм
|
Принимаем dБк
= 38 мм – диаметр буртика зубчатого колеса.
dБ
n
= 25 + 3∙1,5 = 29,5 мм
Принимаем dБ
n
=30 мм – диаметр буртика подшипника.
|
Рисунок 5 – Промежуточный вал
для тихоходного вала (рис. 6)
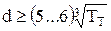 |
(78) |
мм
|
Принимаем d = 36 мм.
Назначаем подшипник радиальный шариковый однорядный серии 208
ГОСТ 8338 - 75.
Принимаем dn
= 40 мм.
Принимаем dБп
= 48 мм – диаметр буртика подшипника.
мм
Примем dБк
= 53 мм – диаметр посадочного отверстия зубчатого колеса.
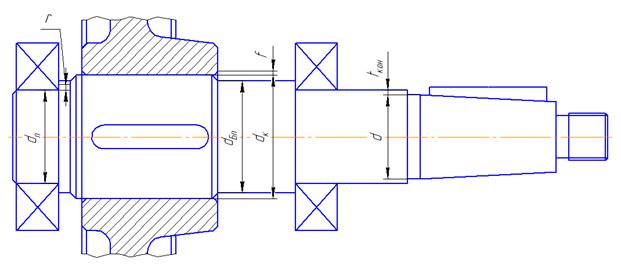
Рисунок 6 – Тихоходный вал
3.2 Эскизная компоновка редуктора
Определяем расстояния между деталями передач.
Чтобы поверхности вращающихся колес не задевали за внутренние поверхности стенок корпуса, между ними оставляют зазор а.
, |
(79) |
где L – расстояние между внешними поверхностями деталей передач; L = 450,9 мм.
мм |
Принимаем а = 10 мм.
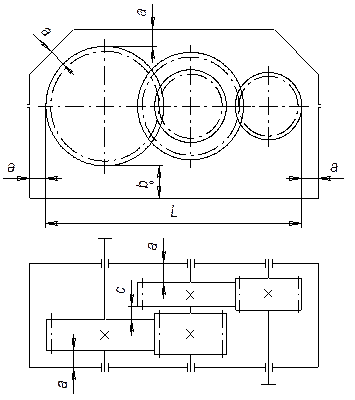
Рисунок 7 – Компоновка
4. Расчет валов привода на прочность [1]
4.1 Быстроходный вал.
Силы, действующие на вал.
Ft
2
= 716,6 Н
Fr
2
= 265,8 Н
Fa
2
= 140,8 Н
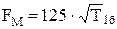 |
(82) |
H |
1) 
 |
H |
2) 
H |
3) 
Н |
4) 
Н |
5) 
Н |
Строим эпюры моментов:
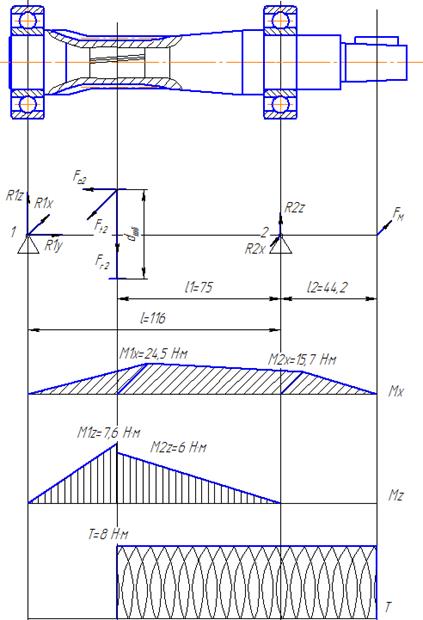
Рисунок 7 – Эпюры моментов
Расчет на статическую прочность.
Расчет для шестерни.
Нормальные напряжения:
, |
(83) |
где: Мmax
– суммарный изгибающий момент;
W – момент сопротивления сечения вала при расчете на изгиб;
Fmax
– осевая сила;
A – площадь поперечного сечения.
Касательные напряжения:
, |
(84) |
где: MК
max
– крутящий момент;
WК
– момент сопротивления сечения вала при расчете на кручение.
, |
(85) |
где Кпер
– коэффициент перегрузки; Кпер
= 2,2.
Н∙м |
Площадь поперечного сечения:
, |
(87) |
где: = 0,97;
d0
– диаметр центрального отверстия;
d – делительный диаметр.
мм2
|
,
|
(88) |
где J – момент инерции.
,
|
(89) |
где = 0,97;
мм4
|
мм3
|
WК
= 2∙W |
(90)
|
WК
= 2∙985,4 = 1971 мм3
|
Н∙м |
 |
(91) |
МПа |
МПа |
Определяем частные коэффициенты запаса прочности:
 |
(92) |
 |
(93) |
Общий коэффициент запаса:
, |
(94) |
где .
Расчет на сопротивление усталости.
Находим коэффициент запаса S.
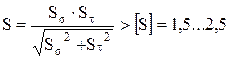 |
(95) |
, |
(96) |
где и – амплитуды напряжений цикла.
, |
(97) |
где М – результирующий изгибающий момент.
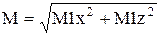 |
(98) |
Н∙м |
Нормальные напряжения в опасном сечении:
МПа |
(99) |
 |
(100) |
где – коэффициент снижения предела выносливости.
МПа |
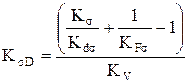 |
(101) |
где: – эффективный коэффициент концентрации напряжений; ;
– коэффициент влияния абсолютных размеров поперечного сечения; ;
– коэффициент влияния шероховатости; ;
– коэффициент влияния поверхностного упрочнения; ;
МПа |
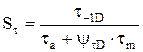 |
(102) |
где: – коэффициент чувствительности к асимметрии цикла;
– среднее напряжение цикла.
Касательные напряжения в опасном сечении:
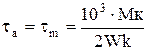 |
(103) |
МПа |
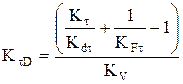 |
(104) |
, , , .
МПа |
 |
(105) |
МПа |
, |
(106) |
где – коэффициент чувствительности материала к асимметрии цикла напряжений; =0,1.
Общий коэффициент запаса:
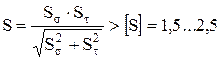 |
(107) |
4.2 Промежуточный вал.
Силы, действующие на вал.
шестерня |
колесо |
Ft
1
= 2208 Н
Fr
1
= 837,1 Н
Fa
1
= 644 Н
|
Ft
2
= 716,6 Н
Fr
2
= 265,8 Н
Fa
2
= 140,8 Н
|
1) 
2) 
H |
3) 
Н |
4) 
Н |
5) 
Н |
Строим эпюры моментов:
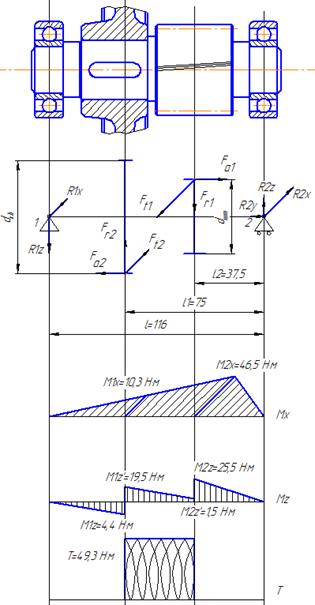
Рисунок 8 – Эпюры моментов
Расчет на статическую прочность.
Аналогично выполняем расчет на статическую прочность и результаты сводим в таблице 8.
Таблица 8 – Результаты расчета
Нормальные напряжения, МПа |
22,1 |
Касательные напряжения, МПа |
7,3 |
суммарный изгибающий момент, Н∙м |
116,7 |
момент сопротивления сечения вала при расчете на изгиб |
7348 |
осевая сила(max), Н |
1417 |
площадь поперечного сечения, мм2
|
1478 |
крутящий момент, Н∙м |
107,5 |
момент сопрот. сечения вала при расчете на кручение, Н |
14695 |
момент инерции, мм4
|
181014 |
коэффициенты запаса прочности |
по нормальным напряжениям |
44,5 |
по касательным напряжениям |
61,5 |
Общий коэффициент запаса |
36,1 |
Допустимое значение коэффициента запаса |
[1,3 … 2] |
Расчет на сопротивление усталости.
Аналогично выполняем расчет на сопротивление усталости и результаты сводим в таблице 9.
Таблица 9 – Результаты расчета
Нормальные напряжения в опасном сечении, МПа |
6,3 |
Касательные напряжения в опасном сечении, МПа |
1,7 |
Результирующий изгибающий момент, Н∙м |
46,6 |
Предел выносливости вала при изгибе, МПа |
203,1 |
Предел выносливости вала при кручении, МПа |
110,7 |
коэффициенты запаса прочности |
по нормальным напряжениям |
32 |
по касательным напряжениям |
63,5 |
Общий коэффициент запаса |
28,6 |
Допустимое значение коэффициента запаса |
[1,5 … 2,5] |
4.3 Тихоходный вал.
Силы, действующие на вал.
Ft
= 2208 Н
Fr
= 837,1 Н
Fa
= 644 Н
Fc
= 2834 Н
1) 
 |
H |
2) 
H |
3) 
Н |
4) 
 |
H |
5) 
Н |
Строим эпюры моментов:
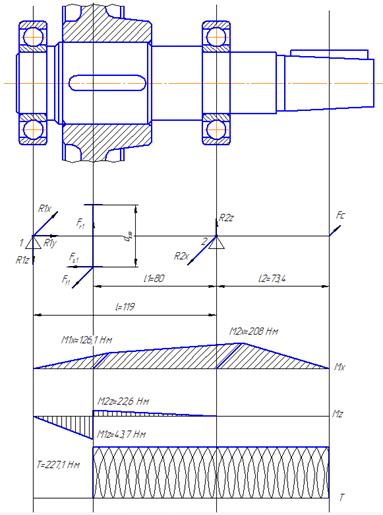
Рисунок 9 – Эпюры моментов
Расчет на статическую прочность.
D = 40 мм – посадочный диаметр подшипника.
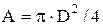 |
(108) |
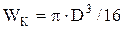 |
(110) |
мм3
|
Дальнейший расчет выполняем аналогично выше приведенному и результаты сводим в таблице 10.
Таблица 10 – Результаты расчета
Нормальные напряжения, МПа |
74 |
Касательные напряжения, МПа |
40,3 |
суммарный изгибающий момент, Н∙м |
457,6 |
осевая сила(max), Н |
1417 |
крутящий момент, Н∙м |
506,6 |
коэффициенты запаса прочности |
по нормальным напряжениям |
8,8 |
по касательным напряжениям |
9,7 |
Общий коэффициент запаса |
6,5 |
Допустимое значение коэффициента запаса |
[1,3 … 2] |
Расчет на сопротивление усталости.
Аналогично выполняем расчет на сопротивление усталости и результаты сводим в таблице 11.
Таблица 11 – Результаты расчета
Нормальные напряжения в опасном сечении, МПа |
33,1 |
Касательные напряжения в опасном сечении, МПа |
1,9 |
Результирующий изгибающий момент, Н∙м |
208 |
Предел выносливости вала при изгибе, МПа |
88,4 |
Предел выносливости вала при кручении, МПа |
83,2 |
коэффициенты запаса прочности |
по нормальным напряжениям |
2,7 |
по касательным напряжениям |
41,3 |
Общий коэффициент запаса |
2,7 |
Допустимое значение коэффициента запаса |
[1,5 … 2,5] |
5. Расчет подшипников качения на заданный ресурс [1]
5.1 Быстроходный вал.
Исходные данные для расчета:
частота вращения вала n1б
=2850 мин-1
;
требуемый ресурс при вероятности безотказной работы 90%: L=16640 ч;
диаметр посадочной поверхности вала мм;
Режим нагрузки III: .
Силы действуют в опорах:
(111)
Н
|
 |
(112) |
Н
Н
|
Определяем эквивалентные нагрузки:
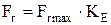 |
(113) |
Н |
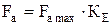 |
(114) |
Н |
Предварительно выбираем шариковый радиальный подшипник легкой серии 205. Схема установки подшипников – враспор.
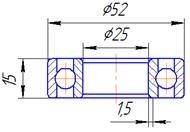
Рисунок 10 – Шариковый радиальный однорядный подшипник
Н – динамическая грузоподъемность; Н – статическая.
Расчёт производим для 1 опоры как наиболее нагруженной.
X=0,56; Y=2,41; e = 0,18.
> 0,18 |
Принимаем: X=0,56; Y=2,41.
Эквивалентная динамическая нагрузка:
, |
(115) |
где: – коэффициент безопасности; ;
– коэффициент температуры; .
Н |
Расчётный ресурс:
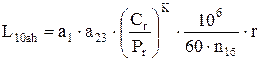 |
(116) |
; ; .
ч
|
Расчетный ресурс больше требуемого, то предварительно назначенный подшипник №205 пригоден.
5.2 Промежуточный вал.
Исходные данные для расчета:
частота вращения вала n1Т
=459,1 мин-1
;
требуемый ресурс при вероятности безотказной работы 90%: L=16640 ч;
диаметр посадочной поверхности вала мм;
Режим нагрузки III: .
Аналогично проведем расчет на заданный ресурс и результаты сведем в таблице 10.
Таблица 10 - Результаты расчета
, Н |
272,6 |
, Н |
1501 |
, Н |
503,2 |
, Н |
840,8 |
, Н |
281,8 |
Подшипники легкой серии № = 208 |
, Н |
14000 |
, Н |
6950 |
 |
0,56 |
X |
0,56 |
Y |
1,8 |
e |
0,25 |
> e |
0,34 |
, Н |
1369 |
, ч |
27183 |
Расчетный ресурс больше требуемого, то предварительно назначенный подшипник №205 пригоден.
5.3 Тихоходный вал.
Исходные данные для расчета:
частота вращения вала n2Т
=95,5 мин-1
;
требуемый ресурс при вероятности безотказной работы 90%: L=16640 ч;
диаметр посадочной поверхности вала мм;
Режим нагрузки III: .
Аналогично проведем расчет на заданный ресурс и результаты сведем в таблице 11.
Таблица 11 - Результаты расчета
, Н |
3480 |
, Н |
3869 |
, Н |
644 |
, Н |
2167 |
, Н |
360,6 |
Подшипники легкой серии № = 208 |
, Н |
32000 |
, Н |
17800 |
 |
0,27 |
X |
1 |
Y |
0 |
e |
0,21 |
 e |
0,17 |
, Н |
3034 |
, ч |
143409 |
Расчетный ресурс больше требуемого, то предварительно назначенный подшипник №208 пригоден.
6. Определение размеров элементов корпуса, крышек и др. деталей [1]
Корпус редуктора служит для размещения и координации деталей передачи, защиты их от загрязнения, организации системы смазки, а также восприятия сил, возникающих в зацеплении редукторной пары, подшипниках, открытой передачи. Наиболее распространенный способ изготовления корпусов – литье из серого чугуна.
Толщина стенки корпуса:
(117)

Принимаем .
Толщину наружных ребер жесткости принимаем 6 мм.
Назначаем крепление крышки редуктора к корпусу болтами.
Диаметр болтов:

(118)

Принимаем диаметр болтов .
Конструирование крышек подшипников.
Используем закладные крышки. Назначаем материал крышек – СЧ15.
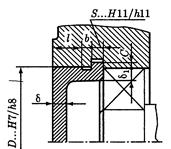
Рисунок 11 – Крышка подшипника
1. Быстроходный вал.
D = 52 мм – диаметр наружного кольца подшипника.
– толщина стенки.
мм |
(119) |
мм |
(120) |
2. Промежуточный вал.
D = 52 мм.
мм.
мм |
мм |
3. Тихоходный вал.
D = 80 мм.
мм |
мм.
мм |
7. Расчет посадок с натягом [1]
Тихоходный вал.
Т2Т
= 230,266 Н∙м
Колесо: сталь 40ХН
Вал: сталь 45
d = 53 мм – диаметр посадки
d1
= 0 – диаметр отверстия вала
d2
= 85 мм – диаметр ступицы колеса
мм – длина сопряжения
1. Среднее контактное давление
, |
(122) |
где К = 4,5 – коэффициент запаса сцепления;
f = 0,14 – сборка нагревом.
МПа |
2. Деформация деталей.
, |
(123) |
где С1
, С2
– коэффициенты жесткости.
0,7 |
(124) |
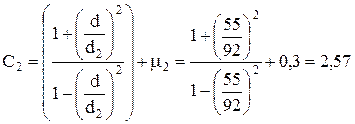 |
(125) |
мкм |
3. Поправка на обмятие микронеровностей.
мкм |
(126) |
4. Минимальный натяг.
мкм |
5. Максимальный натяг.
 |
(127) |
где [δmax
] – максимальная деформация.
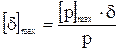 |
(128) |
где рmax
– максимальное давление.
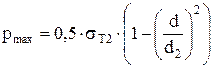 |
(129) |
МПа |
мкм |
мкм |
Выбираем посадку:
У которой: Nmin
= 55 мкм.
Nmax
= 119 мкм.
Температура нагрева вала:
(130) где: – зазор; ;
– средняя объемная температура; .

Температура нагрева должна быть такой, чтобы не происходило структурных изменений в материале. Для стали [t] = 260…2700
С.
Расчет на прочность соединения.
Предел текучести: Сталь 40ХН = 750 МПа
Сталь 45 = 650 МПа
Для колеса:
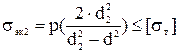 |
(131) |
МПа |
для вала:
 |
(132) |
МПа
|
Промежуточный вал.
Выбираем посадку с натягом.
Т1Т
= 48,875 Н∙м
Колесо: сталь 40ХН
Вал: сталь 45
d = 32 мм – диаметр посадки
d1
= 0 – диаметр отв. вала
d2
= 58 мм – диаметр ступицы колеса
мм – длина сопряжения
Расчет посадки с натягом проведем аналогично, и результаты сведем в таблице 12.
Таблица 12 – Результаты расчета
Среднее контактное давление, МПа |
27,1 |
Деформация деталей, мкм |
11,9 |
коэффициенты жесткости |
С1
|
0,7 |
С2
|
2,18 |
Поправка на обмятие микронеровностей |
13,2 |
максимальное давление, МПа |
260,9 |
максимальная деформация, мкм |
114,3 |
Минимальный натяг, мкм |
25,1 |
Максимальный натяг, мкм |
127,5 |
Эквивалентные напряжения колеса, МПа |
77,9 |
Эквивалентные напряжения вала, МПа |
54,2 |
Выбираем посадку:
У которой: Nmin
= 64 мкм.
Nmax
= 119 мкм.
Температура нагрева вала t = 197°C.
8. Расчет цепной передачи [2]
Исходные данные:
передаточное число ;
мощность на выходе ;
частота вращения .
Число зубьев ведущей звездочки:
(133)

Принимаем .
Число зубьев ведомой звездочки:
(134)
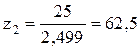
Принимаем .
Фактическое передаточное число:
(135)
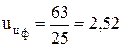
Отклонение , такое отклонение допускается.
Определение расчетной мощности.
(136)
где: – коэффициент эксплуатации;l
– коэффициент числа зубьев; ;
– коэффициент частоты вращения; ;
– коэффициент рядности; .
(137)
где: – коэффициент динамической нагрузки; ;
– коэффициент межосевого расстояния; ;
– коэффициент наклона передачи к горизонту; ;
– коэффициент способа регулировки натяжения цепи; ;
– коэффициент смазки или загрязнения передачи; ;
– коэффициент режима; .


Назначаем приводную роликовую однорядную цепь с шагом рц
= 19,05 мм.
Определяем окружную скорость по формуле:
(138)
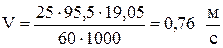
Назначаем густую внутришарнирную смазку.
Число звеньев цепи или длину цепи в шагах определяем по формуле:
, (139)
где: – межосевое расстояние.
По соображениям долговечности цепи на практике рекомендуют принимать
(140)


Расчетное межосевое расстояние:
(141)

Передача работает лучше при небольшом провисании холостой ветви цепи. Поэтому расчетное межосевое расстояние рекомендуют уменьшать примерно на (0,002…0,004)a. ( )
Принимаем a = 568 мм.
Диаметр звездочек определяется по формуле:
(142)
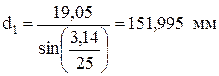
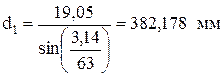
Определяем окружную силу:
(143)
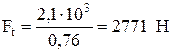
Натяжение от центробежных сил:
, (144)
где q – масса единицы длины цепи; q = 1,9 кг/м.

Сила предварительного натяжения от массы цепи:
, (145)
где: а – длина свободной ветви цепи, приближенно равная межосевому расстоянию;
g – ускорение силы тяжести; g = 9,81 м/с2
;
Kf
– коэффициент провисания; Kf
= 6.

Оценим возможность резонансных колебаний цепи по формуле при :
(146)

Резонанса нет.
Натяжение ведущей ветви цепи:
, (147)
где – натяжение ведомой ветви цепи.
Натяжение ведомой ветви равно большому из натяжений Fo
и Fv
. (F2
= Fo
= 63 Н).

9. Расчет предохранительной муфты [8]
Фрикционная двухконусная муфта.
Материал трущихся поверхностей: ферродо по стали.
Коэффициент трения f = 0,3
Допускаемое давление [p] = 0,3 МПа.
Номинальный момент Т = 540,91 Н∙м.
Коэффициент запаса .
Угол .
Средний диаметр поверхности трения:
, |
(148) |
где .

Ширина поверхности трения:
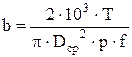 |
(149) |
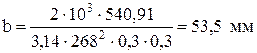
Окружная сила в зоне контакта:
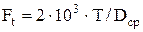

|
(150) |
Осевая сила развиваемая пружиной:
Н |
(151) |
Предельное значение осевой силы:
Н |
(152) |
где Tпред
– предельный вращающий момент.
Н∙м |
(153) |
Нормальная предельная сила:
Н |
(154) |
Среднее давление на поверхности соприкосновения:
МПа |
(155) |
Расчет пружины [9].
При проектировочном расчете диаметр проволоки, из которой свита пружина, определяют по формуле:
, (156)
где: k – поправочный коэффициент, учитывающий влияние кривизны витков; k = 1,37;
с – индекс пружины; с = 4;
[τ] – допускаемое напряжение; τ = 1350 МПа (сталь 60С2А).
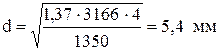
После определения диаметра по формуле окончательное значение dвыбирают по ГОСТу для пружинной проволоки.
Принимаем d = 6 мм.
Условие прочности для пружин из проволоки круглого сечения имеет вид:
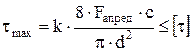

Осевое упругое сжатие пружины из проволоки круглого сечения определяют по формуле:
, (157)
где: D0
– средний диаметр витков пружины; ;
n – число рабочих витков пружины; n = 2;
G – модуль сдвига; G = 8∙104
МПа.
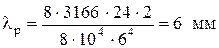
10. Расчет исполнительного механизма
10.1 Конструирование вала исполнительного механизма
Определяем диаметр вала под ведомую звездочку по формуле:
, (158)
где [τ]к
– допускаемое напряжение на кручение; [τ]к
= 20 МПа.

Принимаем d1
= 50 мм.
где tкон
– высота заплечика; tкон
= 2,3.
dn
= 50 + 2∙2,3 = 54,6 мм
|
Принимаем dn
= 55 мм – диаметр посадочного отверстия подшипника.
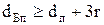 |
(160) |
где r= 2,5– фаска подшипника.
Принимаем dБ
n
= 62 мм – диаметр буртика подшипника.

Рисунок 12 – Вал исполнительного механизма
10.2 Расчет вала исполнительного механизма на прочность
Определяем реакции в опорах.
Ft
= 3000 Н
Fс
= 63 Н
1) 
 |
H |
2) 
H |
3) 
Н |
4) 
Н |
Строим эпюры моментов:
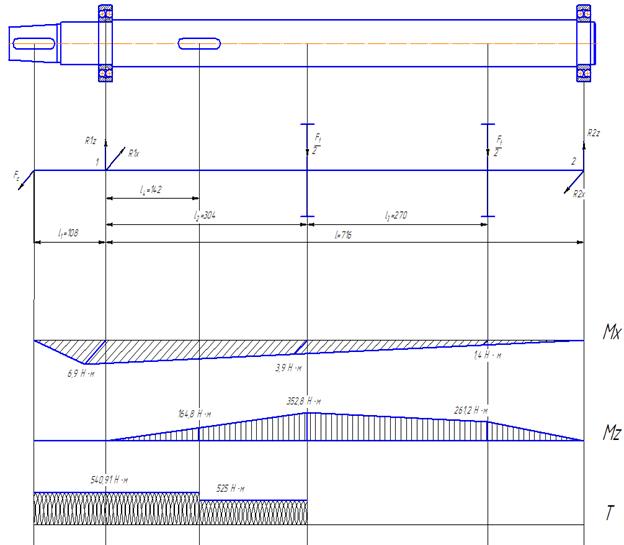
Рисунок 13 – Эпюры моментов
Расчет на статическую прочность.
Расчет на статическую прочность производим аналогично вышеприведенным расчетам валов редуктора и результаты сводим в таблицу 13.
Таблица 13 – Результаты расчета
Нормальные напряжения, МПа |
6,8 |
Касательные напряжения, МПа |
5,1 |
суммарный изгибающий момент, Н∙м |
776,4 |
крутящий момент, Н∙м |
1155 |
коэффициенты запаса прочности |
по нормальным напряжениям |
79,4 |
по касательным напряжениям |
76,8 |
Общий коэффициент запаса |
55,2 |
Допустимое значение коэффициента запаса |
[1,3 … 2] |
Расчет на сопротивление усталости.
Аналогично выполняем расчет на сопротивление усталости и результаты сводим в таблице 14.
Таблица 14 – Результаты расчета
Нормальные напряжения в опасном сечении, МПа |
3,1 |
Касательные напряжения в опасном сечении, МПа |
0,1 |
Результирующий изгибающий момент, Н∙м |
352,9 |
Предел выносливости вала при изгибе, МПа |
88,4 |
Предел выносливости вала при кручении, МПа |
83,2 |
коэффициенты запаса прочности |
по нормальным напряжениям |
23,8 |
по касательным напряжениям |
74,7 |
Общий коэффициент запаса |
23,7 |
Допустимое значение коэффициента запаса |
[1,5 … 2,5] |
10.3 Расчет подшипников вала исполнительного механизма
Предварительно выбираем шарикоподшипник радиальный сферический двухрядный легкой серии 1211. Схема установки подшипников с двумя фиксирующими опорами.
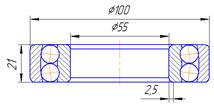
Рисунок 14 – Шариковый сферический двухрядный подшипник
Исходные данные для расчета:
частота вращения вала nв
= 38,2 мин-1
;
требуемый ресурс при вероятности безотказной работы 90%: L = 16640 ч;
диаметр посадочной поверхности вала мм;
Режим нагрузки III: .
Для этого подшипника (из табл.24.12 стр.460 [1]) выписываем:
; ; e = 0,2, Х = 1.
Силы действуют в опорах:
(161)
Н
|
 |
(162) |
Н
Определяем эквивалентные нагрузки:
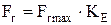 |
(163) |
Н |
Осевые составляющие от радиальных нагрузок равны нулю.
Осевые силы, нагружающие подшипники:
Т.к. Fa
= 0 , то Fa
1
= Fa
2
=0
Эквивалентная динамическая нагрузка:
, |
(164) |
где: – коэффициент безопасности; ;
– коэффициент температуры; .
Н |
Расчётный ресурс:
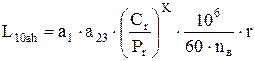 |
(165) |
; ; .
ч |
Расчетный ресурс больше требуемого, то предварительно назначенный подшипник №1211 пригоден.
11. Проверочный расчет шпоночных соединений
Призматические шпонки, применяемые в проектируемом приводе,
проверяют на смятие. Проверке подлежат шпонка вала электродвигателя;
шпонка быстроходного вала – под упругой муфтой; шпонки тихоходного вала – под ведущей звездочкой и под зубчатым колесом, шпонка на промежуточном валу – под зубчатым колесом, шпонки на валу исполнительного механизма – под ведомой звездочкой и муфтой, встроенной в ролик.
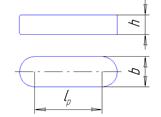
Рисунок 15 – Эскиз шпонки
Условие прочности:
, (166)
где: h– высота шпонки;
lp
– рабочая длина шпонки; ;
d – диаметр соединения;
[σ]см
– допускаемое напряжение на смятие; [σ]см
= 100-150 МПа.
Для вала электродвигателя
Шпонка 6 х 6 х 36 по ГОСТ 23360-78.
Tэ/дв
= 8,2 Н∙м; d = 22 мм; h = 6 мм; b = 6 мм; l= 36 мм;


Для быстроходного вала
Шпонка 6 х 6 х 36 по ГОСТ 23360-78.
Tэ/дв
= 8,033 Н∙м; d = 18 мм; h = 4 мм; b = 4 мм; l= 20 мм;


Для промежуточного вала редуктора
Шпонка 8 х 7 х 28 ГОСТ 23360-78.
T1
T
= 48,875 Н∙м; d = 32 мм; h = 7 мм; b = 8 мм; l= 28 мм;


Для тихоходного вала редуктора
Шпонка 6 х 6 х 50 ГОСТ 23360-78.
Соединение зубчатого колеса с тихоходным валом.
T2
T
= 230,266 Н∙м; d = 53 мм; h = 6 мм; b = 6 мм; l= 50 мм;


Соединение ведущей звездочки с тихоходным валом.
T2
T
= 230,266 Н∙м; d = 36 мм; h = 6 мм; b = 6 мм; l= 50 мм;


Для вала исполнительного механизма
Шпонка 14 х 9 х 63 ГОСТ 23360-78.
Соединение ведомой звездочки с валом исполнительного механизма.
T = 540,91 Н∙м; d = 50 мм; h = 14 мм; b = 9 мм; l= 63 мм;


Соединение муфты, встроенной в ролик, с валом исполнительного механизма.
T = 540,91 Н∙м; d = 62 мм; h = 14 мм; b = 9 мм; l= 63 мм;


Библиографический список:
1. Дунаев П.Ф., Леликов О.П. Конструирование узлов и деталей машин: Учеб. пособие для машиностр. спец. вузов. – 8-е изд., перераб. и доп. – М.: Высш. шк., 2004. 496с.
2. Иванов М.Н. Детали машин: Учебник для машиностр. спец. вузов. – М.: Высш. шк., 1984.
3. Детали машин и прикладная механика: Учебное пособие к курсовому проекту/Составители: О.В. Калинин, Р.И. Зайнетдинов, Д.Б. Лопатин. – Челябинск: ЮУрГУ, 1999.
4. Решетов Д.Н. Детали машин: Учебник для студентов машиностр. спец. вузов. – М.: Машиностроение, 1974.
5. Цехнович Л.И., Петриченко И.П. Атлас конструкций редукторов. – Киев: Висш. школа, 1979.
6. Двигатели асинхронные единой серии АИ мощностью 0,06…400 кВт. - Владомир: Тестэк, 1995.
7. Справочник конструктора – машиностроителя/под ред. В.И. Анурьева. – М: Машиностроение, 1982. – Т.2.
8. Справочник по муфтам/ Под ред. В.С. Полякова. 2-е изд., испр. и доп.—Л.: Машиностроение, Ленингр. отделение, 1979.—344 с., ил.
9. Расчеты деталей машин: Справ. пособие/ А.В. Кузьмин, И.М. Чернин, Б.С. Козинцов. – 3-е изд., перераб. и доп.– Мн.: Выш.шк., 1986.– 400 с.
|