Министерство образования Российской Федерации
НИЖЕГОРОДСКИЙ ГОСУДАРСТВЕННЫЙ ТЕХНИЧЕСКИЙ УНИВЕРСИТЕТ
Кафедра «Металловедение, термическая и пластическая обработка металлов»
Курсовой проект
По дисциплине «Оборудование и проектирование термических цехов»
Тема: "Технический проект участка термической обработки шевера"
Выполнил:
студент группы 23МВ
Розенберг Я.Д.
Проверил:
Сорокина Светлана Александровна
Нижний Новгород
2007
Содержание
Введение
1 Годовая программа участка
2 Технические требования к изделию
3 Обоснование выбора марки материала
4 Разработка технологического процесса термической обработки на проектируемом участке
4.1 Обоснование температур нагрева под операции термообработки
4.2 Расчет времени нагрева
4.3 Обоснование выбора способа охлаждения при закалке и отпуске
5 Выбор источника нагрева
6 Сменность работы участка и определение потребности в рабочей силе
7. Выбор и расчет оборудования участка
7.1. Основное оборудование
7.2. Дополнительное и вспомогательное оборудование
Площадь и планировка участка. Краткие сведения о здании цеха
9. Технические расчеты
9.1 Расчет расхода топлива
9.2 Расчет расхода воды, масла, солей и других материалов
9.3 Расчет освещения участка
9.4 Расчет вентиляции и отопления участка
9.5 Расчет расхода солей
Введение
Целью курсового проекта является реализация теоретических знаний, полученных при изучении дисциплин «Основы низко- и высокоэнергетических технологий» и «Оборудование и проектирование термических цехов», приобретение навыков по проектировании термических участков и отделений термической обработки металлоизделий.
Проектируемый участок предназначен для термической обработки шевинговального инструмента (шевер). В данном проекте рассмотрена термическая обработка шевера выполненного из стали Р18, предназначенного для шевингования (отделочной обработки) незакалённых зубьев зубчатых колёс срезанием тонкой стружки. Целью термической обработки является получение необходимых физических характеристик детали.
1
. Годовая программа участка
Годовая программа участка представлена в таблице 1, брак - 3%. Объемы годной продукции составляют 76339,3 кг.
С учетом брака она составляет:
(кг)
Таблица 1 - Производственная программа термического участка на 2007 год
Наименование детали |
Объем ТО, кг |
Масса деталей подвергаемых ТО по операциям, кг |
Промежуточные операции |
Закалка + отпуск |
Мойка |
Шевер |
78700,32 |
78700,32 |
78700,32 |
2. Технические требования
Шеверы должны изготовляться ив соответствии с требованиями ГОСТ 8570 по рабочим чертежам, утвержденным в соответствующем порядке.
Шеверы должны изготавливаться из быстрорежущей стали по ГОСТ 19265-73. допускается изготовление шеверов из других марок быстрорежущей стали, обеспечивающих стойкость шеверов в соответствии с требованиями вышеуказанного стандарта.
Твёрдость шевера HRC 62…65.
На всех поверхностях шевера не должно быть трещин, забоин, выкрошенных мест, заусенцев и следов от коррозии.
Контроль параметров шевера должен производиться средствами контроля:
А) Твёрдость режущей части шевера проверяется по ГОСТ 9013-59 твердомером Роквелла или Винкерса по ГОСТ 23667-79.
Б) Параметры шероховатости поверхности шевера контролируют путем сравнения с образцовыми инструментами, поверхности которых имеют предельные значения параметров шероховатости при помощи лупы ЛП1–4х по ГОСТ 25706-83
В) Внешний вид шевера проверяется осмотром.
3. Обоснование выбора марки материала
Марка стали Р18 по ГОСТ 8570-80. Сталь Р18 относится к быстрорежущим сталям нормальной теплостойкости. Быстрорежущие стали наиболее характерны для режущих инструментов. Они сочетают высокую теплостойкость (500-650°С) в зависимости от состава и обработки) с высокими твердостью (до HRC 68-70), износостойкостью при повышенных температурах и повышенным сопротивлением пластической деформации. Быстрорежущие стали позволяют повысить скорость резания в 2 - 4 раза по сравнению со скоростями, применяемыми при обработке инструментами из углеродистых и легированных инструментальных сталей. Быстрорежущие стали широко применяют для режущих инструментов, работающих в условиях значительного нагружения и нагрева рабочих кромок. Инструмент из быстрорежущих сталей обладает достаточно высокой стабильностью свойств, что особо важно в условиях гибкого автоматизированного производства. Большое количество избыточной карбидной фазы делает сталь Р18 более мелкозернистой, менее чувствительной к перегреву при закалке, более износостойкой.
Ввиду высокого содержания вольфрама сталь Р18 целесообразно
использовать только для изготовления инструментов высокой точности, когда стали других марок нецелесообразно применять из-за прижогов режущей части при шлифовании и заточке.
Химический состав стали Р18:
Хим. Эл-т |
C |
Si |
Mn |
Ni |
S,P |
Cr |
Mo |
W |
V |
Co |
Содержание |
0.73-0.78 |
До 0,5 |
До 0,5 |
До 0,5 |
До 0,03 |
3,8-4,4 |
До 1 |
17-18,5 |
1-1,4 |
До 0,5 |
Физические свойства стали Р18:
σв
= 840 МПа
σт
= 510 МПа
ψ = 10 %
КСU = 190 кДж/м2
ρ = 8800 кг/м3
Т, ْ
˚С |
Модуль упругости Е, 10-5
МПа |
Коэф-т теплопроводности λ, Вт/м·град |
20 |
2,28 |
100 |
2,23 |
26 |
200 |
2,19 |
27 |
300 |
2,10 |
28 |
400 |
2,01 |
29 |
500 |
1,92 |
28 |
600 |
1,81 |
27 |
700 |
27 |
4. Разработка технологического процесса термической обработки на проектируемом участке
Требуемые свойства изделия обеспечиваются путём закалки в соляной ванне и трёхкратного отпуска.
Закалка в полуавтомате:
Первый подогрев в газовом тигле до 600 ˚С
Второй подогрев в соляной ванне до 960 ˚С. Состав раствора: BaCl2
– 96%, MgF2
– 4% - раскислитель.
Окончательный подогрев в соляной ванне того же состава.
Соляные ванны должны быть очищены от осадков и тщательно раскисленны.
Охлаждение производить в селитровом приспособлении при t=280˚С.
Состав раствора: KNO3
– 50%, NaNO2
-50%.
Время выдержки равно времени окончательного нагрева.
Отпуск:
Нагрев в селитровой ванне (KNO3
– 100%) до t = 565 ˚С и выдержка 1 час 30 минут.
Отпуск трехкратный.
Охлаждение на отпуске до температуры цеха.
Очистка:
Промыть в моечной машине при t = 80 – 90˚С в 5% растворе NaNO2
до удаления соли, после чего прочистить зубья капроновой щеткой.
4.1 Обоснование температур под операции термообработки
Для предупреждения образования трещин и повышенных термических напряжений нагрев под закалку ведут с одним или двумя подогревами. Первый подогрев при 400-600 °С, второй при 800-950 °С. Время выдержки при подогреве обычно берут удвоенным по сравнению с выдержкой при окончательном нагреве. Выдержку при окончательном нагреве выбирают из расчета 10-15 с на 1 мм диаметра (толщины) для инструмента диаметром 5-30 мм.
Для стали Р18 основным является карбид М6С (Fe3W3C). Для получения высоких теплостойкости и твердости достаточно большая доля распадающегося карбида должна быть переведена при закалке в твердый раствор (аустенит, мартенсит), что насыщает его углеродом, вольфрамом, молибденом, ванадием, хромом.
Последующий отпуск при температурах 550-570 °C повышает твердость до максимальных значений вследствие выделения дисперсных, карбидов и распада остаточного аустенита.
Переохлажденный аустенит быстрорежущих сталей устойчив, вследствие чего они могут охлаждаться в любой среде - воздухе, масле, горячих средах при 500-560 °С. Будем охлаждать изделие на воздухе. Отпуск быстрорежущих сталей выполняется при температурах 550-570 °С, 2-3 раза по 1 ч. Быстрорежущие стали с большой устойчивостью остаточного аустенита требуют трех- и даже четырехкратного отпуска. Будем выполнять трехкратный отпуск при температуре 565 °С с выдержкой 1ч 30 мин. При отпуске происходит выделение упрочняющих карбидов и распад остаточного аустенита. В результате быстрорежущая сталь получает высокую твердость, прочность и теплостойкость. При закалке в аустените растворяется весь хром, 8% W, 1% V и 0,4-0,5% C. После закалки в структуре кроме мартенсита и первичных карбидов содержится 30-40% остаточного аустенита. Остаточный аустенит превращают в мартенсит при отпуске. Аустенит, обедняясь углеродом и легирующими элементами, становится менее устойчивым и при охлаждении ниже точки MН испытывает мартенситное превращение. Однократного отпуска недостаточно для превращения всего остаточного аустенита, поэтому применяют многократный отпуск.
Критические точки;
Ас1
=820˚С Ас3
=860˚С
Аr1
=725˚С Аr3
=770˚С
4.2 Расчёт времени нагрева
Схема термической обработки изделия:
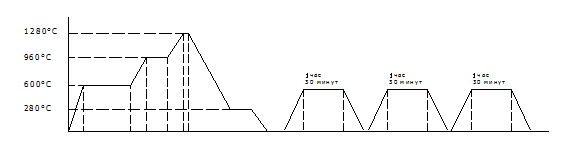
Время нагрева будем рассчитывать по формуле:
τобщ
= τс.п.
+ τи.в.
, где
τс.п.
- время сквозного прогрева,
τи.в.
- время изотермической выдержки,
τс.п.
= К1
·(V/F)·KP
·KK
(ч)
τи.в.
= 0.08·W + 0.2·V+0.15·Mo(мин)
W,V,Mo – количество процентов вольфрама, ванадия и молибдена соответственно.
К1
– коэффициент, зависящий от марки, состава и температуры среды.
Дла стали Р18 при температуре закалки 1280˚С:
К1
= 4,4 мин/см = 7,3 ч/м
V/F – соотношение объёма к поверхности простого тела, схожего с нашим изделием.
Для короткого полого цилиндра:
V/F=(D-d)·l/(4l-2(D-d))
D=0.185 м
d =0.063 м
l = 0.020 м
V/F = 0,00753 м
KP
– критерий формы:
KP
= 1+0,2·(D-d)/l
KP
= 1,0327
KK
– коэффициент конфигурации:
KK
=1
τс.п.
= 0,057 ч = 3,42 мин
τи.в.
= 0.08·18,5 + 0.2·1,4+0.15·(%Мо) = 1,7 мин
τоб
= 10,26 +6,84+1,7+10,26=29,06 мин
4.3 Обоснование выбора способа охлаждения при закалке и отпуске
Охлаждение при закалке следует проводить в селитровом приспособлении или в масле, так как при медленном охлаждении (на воздухе) могут выделиться карбиды, что ухудшит режущие свойства изделия. Выбор селитрового приспособления продиктован большей технологичностью и безопасностью. Масло – огнеопасно (температура вспышки колеблется от 150 до 320˚С). Масло необходимо менять по истечению срока службы. Кроме того масло пригорает к поверхности изделия и образует пригар, что требует лишних затрат на очистку детали. Расплав же солей не обладает выше указанными недостатками. Температура расплава 280˚С обеспечивает замедленное охлаждение, что исключает возникновение термических напряжений и, как следствие коробление изделия.
5. Выбор источника нагрева
Учитывая марку стали(быстрорежущая), технологические требования и экономический фактор производства, для термической обработки изделия целесообразно использовать последовательность из четырёх соляных ванн типа СВС.
В соответствие с годовой ь из четырёх соляных ванн типа СВС изделия.______________________________________________________программой, габаритами и технологией обработки были выбраны следующие установки:
Операция |
Тип оборудования |
Количество единиц оборудования, шт |
Первый подогрев до 600 |
соляная электропечь-ванна СВС4,8,4/6,5 |
1 |
Второй подогрев до 960 |
соляная электропечь-ванна СВС2,3/13 |
1 |
Окончательный подогрев до 1260-1280 |
соляная электропечь-ванна СВС2,3/13 |
1 |
Охлаждение после закалки |
соляная электропечь-ванна СВС4,8,4/6,5 |
1 |
Отпуск |
соляная электропечь-ванна СВС4,8,4/6,5 |
1 |
Конструкция соляных ванн :
Электрованны представляют собой футерованную камеру, заполненную расплавленной солью, в которую опущены металлические электроды, и состоят из кожуха, футеровки, электродной группы, выемных устройств и нагревателя. Кожух круглый, сварной из листового проката.
Футеровка состоит из огнеупорного тигля, сложенного из высокоглиноземистых блоков, утрамбованной засыпки из высокоглиноземистого мертеля, слоя секторных кирпичей из легковесного шамота, теплоизоляции из легковесного шамота и пенодиатомита.
Три электрода массивного сечения свободно опущены в углы шестигранного огнеупорного тигля. Каждый электрод выполнен из двух частей – электродержателя и рабочей части, которая является сменным элементом. Для подсоединения токоподводящих шин к электродержателям приварены контактные пластины.
Удаление паров солей с зеркала электрованны производится вытяжным устройством, подсоединенным к цеховой вытяжной вентиляционной системе. Для повышения безопасности обслуживания и эффективности вытяжного устройства над зеркалом электрованны рекомендуется устанавливать защитный колпак (в комплект поставки не входит) с проемом для обслуживания.
Выемной нагреватель предназначен для пуска электрованны. Термообрабатываемые изделия опускаются в расплав на специальных подвесках.
Для измерения, записи и регулирования температуры расплава служит электронный потенциометр, датчиком которого является термопара.
В электрованнах имеется ручное или автоматическое управление подачей напряжения на электроды.
В автоматическом режиме при температуре расплава ниже заданной включается промежуточное реле приставки позиционного регулирования, которое дает команду на включение контактора, подающего напряжение на электроды.
При достижении заданной температуры расплава промежуточное реле отключается, отключая при этом контактор.
Условия эксплуатации:
Высота не более 1000 м над уровнем моря;
Окружающая среда невзрывоопасная, не содержащая агрессивных газов и паров в концентрациях, разрушающих металл и изоляцию, ненасыщенная водяными парами и токопроводящей пылью.
Электрованны выпускаются по ТУ 16-681.110 – 85.
Технические характеристики оборудования:
Соляная электропечь-ванна СВС4,8,4/6,5:
Наименование параметра |
Норма параметра |
Установленная мощность, кВт |
110 |
Номинальная температура в рабочем пространстве, 0
С |
650 |
Номинальное напряжение питающей сети, В |
380 |
Частота электрического тока, Гц |
50 |
Число фаз, шт. |
3 |
Напряжение на электродах, В |
8-80 |
Размеры рабочего пространства, мм, не менее: – ширина – длина – высота |
400
800
400
|
Теплоноситель |
хлористые соли |
Электроды: сталь |
15Х25Т |
Соляная электропечь-ванна СВС2,3/13:
Наименование параметра |
Норма параметра |
Установленная мощность, кВ*А |
100 |
Номинальная температура, °С |
1300 |
Напряжение питающей сети, В |
380/220 |
Частота, Гц |
50 |
Число фаз |
3 |
Напряжение на электродах, В:
пусковое
рабочее
холостого хода
|
31,8
23; 27,7
18,4
|
Напряжение на выемном нагревателе, В |
18,4 |
Производительность, кг/ч |
360 |
Объём расплавляемой соли, макс., л |
70 |
Мощность холостого хода, кВт |
60 |
Размеры рабочего пространства (по садке), мм:
диаметр
глубина
|
200
300
|
Удельный расход электроэнергии, кВт*ч/кг |
0,24 |
Масса футеровки, т |
1,14 |
Масса электрованны (без соли), т |
3,1 |
6. Сменность работы участка и определение потребности в рабочей силе
В условиях серийного производства учитывая особенности технологического процесса и выбранного оборудования, целесообразно выбрать односменный режим для участка термообработки. Продолжительность смены составляет 8 часов.
Определение численности работающих
1) Основные рабочие
На термическом участке основными рабочими являются термисты. Различают явочное и списочное число основных производственных рабочих.
Явочное - это такое количество рабочих, которое необходимо для работы участка. Явочное число основных производственных рабочих рассчитывается по нормам обслуживания, по следующей формуле:
Ря
=М*а/Н0
,
где М - количество единиц оборудования;
а - число смен;
Н0
- норма обслуживания, т.е. число агрегатов, обслуживаемое одним рабочим.
Явочное количество рабочих:
Наименование оборудования |
Количество
единиц оборудования
|
Норма обслуживания (агр/чел) |
Численность рабочих, чел |
Кол-во смен |
Явочное число рабочих |
СВС2,3/13; СВС4,8,4/6,5 |
6 |
3 |
2 |
1 |
2 |
Итого |
2 |
2 |
На основе явочного числа рабочих (Ря
) определяется их списочная численность Рс
по формуле:
Рс
=Ря
*Фн/Фд, где
Фн
- номинальный фонд времени работы рабочих, час;
Фд
- действительный фонд времени работы рабочих, час.
а) Рс
=2*1984/1706,24=3 чел.
Списочную численность основных рабочих принимаем 3 человека.
2) Вспомогательные рабочие
Вспомогательные рабочие выполняют вспомогательные операции по обслуживанию основного технологического процесса.
Рабочие, занятые ремонтом и обслуживанием оборудования:
электрик по ремонту и обслуживанию оборудования - 1 чел.;
слесарь по ремонту оборудования - 1 чел.;
уборщик - 1 чел;
контролёр ОТК - 1 чел.
Численность уборщиков определяется исходя из нормы обслуживания 650 м2
на одного человека в смену. При общей площади 140 м2
для обслуживания участка требуется 1 уборщика в смену.
Таким образом, общая численность вспомогательных рабочих равна 4 человек.
3) Руководители
Число руководителей определяется с учетом схемы управления участка. Управление осуществляется старшим мастером, ему подчиняется 1 сменный мастер. Кроме того, на участке закреплен 1 контролер ОТК на смену.
Расчет представлен в таблице 5.
4) Специалисты
За участком закреплен инженер - технолог 2-ой категории.
5) Служащие
На термическом участке служащие, кроме уборщика, не предусматриваются, т.к. они числятся не в штате участка, а в штате цеха.
Состав рабочих термического участка с указанием их квалификационного разряда приведен в таблице:
Состав рабочих и служащих термического участка:
Наименование специальности |
Всего, чел. |
В том числе по разрядам |
Средний разряд |
I |
II |
III |
IV |
V |
VI |
1 Основные рабочие: |
- термист |
2 |
1 |
5,0 |
2 Вспомогательные рабочие: |
- слесарь по ремонту и обслуживанию оборудования |
1 |
1 |
4 |
- электрик по ремонту и обслуживанию оборудования |
1 |
1 |
5,0 |
- контролер ОТК |
1 |
1 |
4,0 |
3 Служащие |
- уборщик |
1 |
Итого |
6 |
Таким образом, численность работающих на термическом участке составляет 5 человек.
Таблица 9. Расчет численности руководителей и специалистов
Категория работающих |
Количество человек |
Руководители: |
Старший мастер |
1 |
Сменный мастер |
1 |
Итого |
2 |
Специалисты: |
Инженер-технолог 2 категории |
1 |
Итого |
1 |
Всего |
3 |
7. Выбор и расчет оборудования участка
Для осуществления операции термической обработки (ступенчатый нагрев и охлаждение в селитре) в соответствии с принятыми технологическими процессами в пункте 5 выбрана соляная электропечь-ванна СВС4,8,4/6,5 в количестве 3 штук и соляная электропечь-ванна СВС2,3/13 в количестве 2 штук. По технологии после термической обработки необходима мойка изделий . Для мойки применяется моечная машина KMPV-100S.
7.1 Основное оборудование
Для квалифицированного выбора основного оборудования требуется определить: - тип производства – серийное. Следовательно необходимо и достаточно оборудования с средней загрузкой;
данная марка материала склонна к короблению, что накладывает ограничения на достижимую скорость нагрева;
загрузка – выгрузка производится партиями в закрепленные в специальных оборудованиях.
рабочие температуры нагрева не превышают номинальной температуры выбранных печей; - тип нагрева – объемный;
Для выбранного оборудования приводятся данные технического паспорта (габариты, потребляемая мощность, производительность, масса, размеры рабочего пространства и проч.) в пункте 5 данного проекта.
7.2 Расчет количества оборудования
На проектируемом участке для ТО шеверов используется оборудование, приведенное в таблице
Наименование оборудование |
Количество единиц |
Коэффициент загрузки, % |
Мощность нагревателей, кВт |
По расчету |
принято |
СВС4,8,4/6,5 |
0,69 |
1 |
69 |
110 |
СВС2,3/13 |
0,69 |
1 |
69 |
100 |
KMPV-100S |
0,69 |
1 |
69 |
5 |
1. Определение задолженности СВС4,8,4/6,5 и СВС2,3/13
З = Nг/Пр
|
З - задолженность оборудования, ч |
Nг - годовая программа выпуска, шт или кг |
Пр - часовая производительность единицы оборудования, шт/ч или кг/ч |
З, ч |
Nг, кг |
Пр, кг/ч |
1311,7 |
78700 |
360 |
Расчетное количество оборудования Ср = З/Фд |
Ср = 0,12 |
Принятое количество оборудования Спр = 1 |
Коэффициент загрузки Кз = Ср/Спр |
Кз =0,12 |
2. Определение задолженности KMPV-100S
З = Nг/Пр
|
З - задолженность оборудования, ч |
Nг - годовая программа выпуска, шт или кг |
Пр - часовая производительность единицы оборудования, шт/ч или кг/ч |
З, ч |
Nг, кг |
Пр, кг/ч |
1311,7 |
78700 |
60 |
Расчетное количество оборудования Ср = З/Фд |
Ср = 0,69 |
Принятое количество оборудования Спр = 1 |
Коэффициент загрузки Кз = Ср/Спр |
Кз =0,69 |
Оборудование |
Выпол-няемая опера-ция |
Наимено-вание детали |
Годовая програм-ма, кг |
Произ-ть обор-я, кг/ч |
Задолжен-ность оборудо-вания, ч |
Фонд времени работы обору-дования, ч |
Количество печей |
Коэф-фициент загрузки, % |
Рас-четное |
При-нятое |
СВС4,8,4/6,5 |
1-й подогр |
шевер |
78700 |
60 |
1311,7 |
1861,5 |
0,12 |
1 |
69 |
СВС2,3/13 |
2-й подогр |
шевер |
78700 |
60 |
1311,7 |
1861,5 |
0,12 |
1 |
69 |
СВС2,3/13 |
оконч. нагрев |
шевер |
78700 |
60 |
1311,7 |
1861,5 |
0,12 |
1 |
69 |
СВС4,8,4/6,5 |
охл-е |
шевер |
78700 |
60 |
1311,7 |
1861,5 |
0,12 |
1 |
69 |
СВС4,8,4/6,5 |
отпуск |
шевер |
78700 |
60 |
1311,7 |
1861,5 |
0,12 |
1 |
69 |
KMPV-100S |
мойка |
шевер |
78700 |
60 |
1311,7 |
1861,5 |
0,69 |
1 |
69 |
8.Площадь и планировка участка
Преимущество принятого расположение оборудования в рациональном компактном размещении всего необходимого на принятой площади.
Для выбранного оборудования по нормативным документам необходимо 220 м2
.
Объем участка: , где
- длина, ширина, высота участка
18 м, 12 м, м
Vуч
=18·12·8,4=403,2 м3
9.Технические расчеты
9.1 Расход энергии на технологические нужды определяется из соотношения
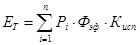
Рi - мощность печей и силовых энергопотребителей
Р |
Фэф |
Кисп |
Eт |
530 |
1861,5 |
0,12 |
118391 |
Р |
Фэф |
Кисп |
Eт |
20 |
1861,5 |
0,7 |
26061 |
Расход электроэнергии на освещение определяется по формуле:
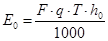
F - освещаемая площадь, кв.м
Т - число часов горения в году, здесь - для 2-сменной работы
F |
q |
T |
hо |
Eо |
216 |
11 |
1725 |
0,8 |
3278,9 |
Общее количество потребления энергии за год: 147730,9 кВт*ч/год
9.2 Расчет расхода воды
Расход воды в моечных машинах составляет 20-30 % от веса промываемых изделий:
Норма расхода воды в смену на человека: 75 л
Рс, л |
Кол-во рабочих в смену |
300 |
4 |
Расход воды на бытовые нужды за год: Рг = Рс*а*с
Робщ, л = 157675
Робщ, м^3= 157,675
9.3 Определение необходимости в отоплении
Тепловыделение от электропечей (ккал/ч):
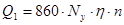
Ny=90
η=0,45
n=3
Q1
= 104490
Тепловыделение от работы двигателей (ккал/ч):

Тепловыделение от нагретого металла (ккал/ч):

А |
Сср |
tн |
tохл |
Q3 |
1014,8 |
0,139 |
280 |
20 |
36673 |
Количество тепла, вносимое солнечной энергией (ккал/ч):

Fокон |
q |
μ |
Q4
|
21,6 |
70 |
1,45 |
2192,4 |
Fокон - площадь окон, м2
q - тепло солнечной радиации
μ - к-т, учитывающий вид застекления
Тепловыделения от рабочих (ккал/ч):

150- количество выделяемого тепла одним человеком за 1 час, ккал/ч
Суммарное тепловыделение на участке (ккал/ч):
Qизб = Q1+Q2+Q3+Q4+Q5
Qизб = 163455,4 ккал
Система отопления должна компенсировать потери теплоты через строительные ограждения, а также обеспечивать нагрев проникающего в помещение холодного воздуха, поступающих материалов и транспорта
Теплопотери через окна (ккал/ч):
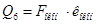
Fокон |
Кокон |
Q6, ккал/ч |
21,6 |
5,1 |
110,16 |
Кокон - к-т теплопотерь через окна
Кокон =5,1 для одинарного остекления
Теплопотери через стены (ккал/ч):

Fст |
Кст |
Q7 |
191,52 |
1,32 |
252,8 |
Теплопотери через перекрытия (ккал/ч):

Общие потери тепла (ккал/ч):
Qп |
Q6-8 |
к-т |
667 |
633 |
1,0526 |
Т.к. по сравнению с количеством избыточного тепла общие теплопотери малы, то отопления не требуется.
9.4 Расчет вентиляции
Требуемое количество приточного воздуха, м3
/ч:

Српр |
Tпр |
Tвыт |
Qизб |
Lпр |
5,4431 |
20 |
24,40 |
205983 |
8600,7 |
Српр = 1,3 кДж/м3
К (5,4431 ккал/м3
К) - объемная удельная теплоемкость воздуха
Тпр - температура приточного воздуха
Твыт - температура удаляемого воздуха
Твыд = Тпр+0,5(Н-2)
Н - высота цеха, м = 8,4
Кратность воздухообмена(ч-1
):

К |
Lпр |
Vуч |
5,0588 |
8600 |
1700 |
Vуч - объем участка, м3
Средняя кратность обмена в ТЦ =5...10. При большем К необходимо применение аэрации.
9.5 Расчет расхода солей
наим-е соли |
процентное соотношение в печи |
расход за плановый период, кг |
расход соли в сутки, кг |
Фд, ч |
1 |
BaCl2 |
0,96 |
548,52 |
0,3 |
1905 |
MgF |
0,04 |
22,855 |
2 |
BaCl2 |
0,96 |
548,52 |
MgF |
0,04 |
22,855 |
3 |
BaCl2 |
0,96 |
548,52 |
MgF |
0,04 |
22,855 |
4 |
KNO3 |
0,5 |
285,69 |
NaNO2 |
0,5 |
285,69 |
5 |
KNO3 |
1 |
571,38 |
итого BaCl2 |
1645,6 |
итого MgF |
68,566 |
итого KNO3 |
857,07 |
итого NaNO2 |
285,69 |
2 Определение задолженности KMPV-100S
З = Nг/Пр
|
З - задолженность оборудования, ч |
Nг - годовая программа выпуска, шт или кг |
Пр - часовая производительность единицы оборудования, шт/ч или кг/ч |
З, ч |
Nг, кг |
Пр, кг/ч |
1311,7 |
78700 |
60 |
Расчетное количество оборудования Ср = З/Фд |
Ср = 0,69 |
Принятое количество оборудования Спр = 1 |
Коэффициент загрузки Кз = Ср/Спр |
Кз =0,69 |
Оборудование |
Выпол-няемая опера-ция |
Наимено-вание детали |
Годовая програм-ма, кг |
Произ-ть обор-я, кг/ч |
Задолжен-ность оборудо-вания, ч |
Фонд времени работы обору-дования, ч |
Количество печей |
Коэф-фициент загрузки, % |
Рас-четное |
При-нятое |
СВС4,8,4/6,5 |
1-й подогр |
шевер |
78700 |
60 |
1311,7 |
1861,5 |
0,69 |
1 |
69 |
СВС2,3/13 |
2-й подогр |
шевер |
78700 |
60 |
1311,7 |
1861,5 |
0,69 |
1 |
69 |
СВС2,3/13 |
оконч. нагрев |
шевер |
78700 |
60 |
1311,7 |
1861,5 |
0,69 |
1 |
69 |
СВС4,8,4/6,5 |
охл-е |
шевер |
78700 |
60 |
1311,7 |
1861,5 |
0,69 |
1 |
69 |
СВС4,8,4/6,5 |
отпуск |
шевер |
78700 |
60 |
1311,7 |
1861,5 |
0,69 |
1 |
69 |
KMPV-100S |
мойка |
шевер |
78700 |
60 |
1311,7 |
1861,5 |
0,69 |
1 |
69 |
|