ДИПЛОМНА РОБОТА
"Друга фаза композитів на основі міді, що виготовлені методом осадження у вакуумі"
Вступ
Важливою задачею сучасної науки матеріалознавства є створення матеріалів з високим комплексом механічних та фізичних властивостей. Це обумовлено постійно зростаючими вимогами до конструкційних матеріалів. Значне підвищення цих вимог обумовлено прагненням до різкої зміни характеристик енергетичних, транспортних та інших установок – підвищення КПД, потужності, строку служби та зниження габаритних розмірів. Відомим методом рішення цієї задачі є розробка та створення композиційних матеріалів. Однім із класів композиційних матеріалів є дисперсно-зміцнені композити.
Дисперсно-зміцнені композиційні матеріали на основі міді дістали широкого використання в таких галузях як електротехніка, мікроелектроніка та ядерна техніка. Відомо, що рівень фізико-механічних властивостей дисперсно-зміцнених композиційних бінарних систем (наприклад, Cu–Mo, Cu–W, Cu–Ta, Cu-Co, Cu-Fe) залежить від ступеня дисперсності структурних елементів та вмісту зміцнюючої фази. За умови, що частки зміцнюючої фази не перерізаються дислокаціями, характеристики міцності визначає не розмір самих часток, а відстань між ними, також важливі рівномірність розподілення та характер зв’язку частка-матриця.
Зменшення розміру та забезпечення відсутності сегрегацій зміцнюючих часток дозволить знизити вміст другої фази, без зниження характеристик міцності та підвищити електропровідність композиційних матеріалів, що припускає велику економічну користь. Це неможливо без глибокого знання структури композита та її змін під впливом технологічних чинників. Для вивчення структури композитів зміцнених нанорозмірними частками другої фази та з розміром зерна матриці менше 0,5 мкм доцільно використання методу електронної мікроскопії, це дуже інформативний метод.Метод дозволяє наглядно представити структуру, що вивчається та співпоставити її з дифракційною картиною. Такі дослідження та застосування їх результатів при виробництві композитів та деталей з них викликають велику цікавість.
1. Аналітичний огляд джерел інформації
1.1
Переваги дисперсно-зміцнених композиційних матеріалів над традиційними сплавами
Інтенсивний розвиток найважливіших галузей техніки подає все більш високі вимоги до конструкційних матеріалів. Значне підвищення цих вимог обумовлено прагненням до різкої зміни параметрів (підвищення КПД, міцності, термічної стабільності та зниження габаритних розмірів) енергетичних, транспортних та інших установок.
Основними шляхами підвищення міцності металів [1], є: механічне деформування на холоду (нагартовування); сплавлення з компонентами, що входять до твердого розчину на базі ґратки основного металу; виготовлення високодисперсної суміші фаз шляхом загартування сплаву на пересичений твердий розчин з послідуючим зміцнювальним відпуском чи старінням; додавання до розчину компонентів, що утворюють вже у процесі кристалізації нову, більш тверду фазу у вигляді сітки по границям зерен основної фази.
Додаткове зміцнення у кожному з вказаних випадків (за винятком ливарних сплавів, які не підлягають деформуванню) може бути досягнуто використанням термомеханічної обробки, що формує стійку субструктуру[2].
Одночасна дія всіх вказаних чинників зміцнення виконується при температурах, що не перевищують (0,3–0,4) Тпл
.Саме на цій основі отримані в наш час сталі з міцністю до 300–350 кгс/мм2
.
При підвищенні температури до (0,5–0,6) Тпл
різко слабшає зміцнююча дія від утворення твердих розчинів. Зміцнення за рахунок дисперсних виділень зберігається до (0,6–0,7) Тпл.
, і тільки додаткове ускладнення складу і будови виділяючихся фаз та легування твердого розчину матриці дозволяє інколи підняти робочу температуру сплавів до (0,7–0,8) Тпл
. Складне легування повинно забезпечувати підвищення стабільності твердого матричного розчину та зміцнюючих фаз за рахунок уповільнення дифузійних процесів, які можуть порушити тонку гетерофазну структуру сплаву.
Успіхи у комплексному легуванні разом з оптимальною термічною обробкою дозволили, наприклад, підвищити рівень робочих температур нікелевих сплавів до 1000−1050 °С. Додаткове підвищення робочих температур (до 1100 °С для нікелевих сплавів) досягається удосконаленням технології (наприклад, направленою кристалізацією).
Разом з тим резерви подальшого підвищення жароміцності шляхом додаткового легування на сьогоднішній день вичерпуються. Тим паче, введення більшої кількості легуючих елементів викликає негативні наслідки: знижується температура солідусу сплавів, утворюються скопління крихких фаз, що призводять до зниження опору руйнуванню, внаслідок погіршення характеристик пластичності багато жароміцних сплавів стають нетехнологічними.
Усунення різниці між вимогами сучасної техніки до конструкційних матеріалів досягається шляхом утворення і використання композиційних матеріалів.
За механізмом зміцнення композиційні матеріали можна розділити на дві групи. Основою зміцнення матеріалів першої групи є принцип армування металевої матриці високоміцними несучими елементами. Цей принцип був раніше реалізований у неметалевих конструкційних матеріалах – залізобетонні, склопластиках і т. п. Рівень міцності (та жароміцності) матеріалів цієї групи залежить в основному від властивостей самих елементів, що армують, а роль матриці зводиться головним чином до перерозподілу напружень між елементами, що армують.
В композиційних матеріалах другої групи, до яких відносять і дисперсно-зміцнені матеріали, головна роль в зміцненні належить структурним чинникам. Матриця в цих сплавах є основним елементом, що несе навантаження, роль фази, що зміцнює зведена в основному до полегшення формування дислокаційної субструктури в процесах виготовлення сплавів, головним чином під час деформації та термічної обробки, і до стабілізації цієї субструктури в умовах експлуатації [3].
Дисперсно-зміцнені сплави принципово не відрізняються за механізмом зміцнення від класичних старіючих сплавів. Основна різниця між ними полягає в тому, що якщо в старіючих сплавах фазові співвідношення визначаються фізико-хімічними процесами розпаду пересичених твердих розчинів, то в дисперсно-зміцнених сплавах фазові співвідношення задаються штучно в процесі виготовлення.
Активний вплив на морфологію, дисперсність та характер розподілу фази, що зміцнює дозволяє отримати дисперсно-зміцнених сплавах сполуку властивостей, яка недосяжна в звичайних сплавах. Використання у якості фаз, що зміцнюють стабільних тугоплавких сполучень, що не взаємодіють активно з матричним металом і не розчиняються в ньому аж до температури його плавлення, забезпечує можливість збереження мікрогетерогенної будови та дислокаційної субструктури, що формується у процесі деформації і термічної обробки, до передплавильних температур. Це дозволяє зберегти тривалу роботоздатність матеріалів до (0,9–0,95) Тпл
.
Ефективність зміцнюючої дії часток другої фази, стабільних у контакті з металевою матрицею, визначається геометричними чинниками структури. З аналізу великої кількості експериментальних даних та теоретичних зображень [4] випливає, що максимальний ефект досягається під час виконання наступних умов:
1. Розмір часток, що зміцнюють не повинен перевищувати 0,01–0,05 мкм. Частки великих розмірів при високих температурах стають неефективними, хоча при помірних та низьких температурах ще можуть задавати зміцнюючий вплив.
2. Середня відстань між частками, що зміцнюють повинна бути не більш ніж 0,1–0,5 мкм при рівномірному їх розподілі в матриці.
Зазначені геометричні чинники визначають необхідний об’ємний вміст часток, що зміцнюють в сплаві адже для рівномірного розподілення в об’ємі сферичних включень виконується співвідношення:
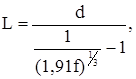
де L – відстань між центрами часток;
d – діаметр часток;
f – об’ємна доля часток.
Розрахунок показує, що ефективне зміцнення забезпечується при вмісті фази, що зміцнює не вище 5–10℅ (об’ємн.), в той час як в сучасних жароміцних старіючих сплавах об’ємний вміст зміцнюючих виділень досягає 60℅.
Вміст фази, що зміцнює принципово відрізняє дисперсно-зміцнені сплави від керметів. Якщо в перших невелика кількість твердих тугоплавких часток зміцнює метал, то в останніх, навпаки, невелика кількість металу, що вводиться служить для пластифікуючої зв’язки твердої та тугоплавкої кераміки.
Утворення в сплаві рівномірної дисперсії стабільних аж до температури її плавлення ультра дисперсних часток, що не взаємодіють з матрицею можливо тільки штучним шляхом в наслідок використання специфічних технологічних прийомів виготовлення сплавів. При цьому активний вплив на структуру сплаву дозволяє в широких межах регулювати фізико-механічні властивості при незмінному хімічному складі.
Невеликий об’ємний вміст фаз, що зміцнюють сприяє, з одного боку, збереженню в дисперснозміцених сплавах високої пластичності, що характерна чистим металам та твердим розчинам, а з іншого боку, ця обставина ускладнює поєднування високої жароміцності з високими характеристиками міцності при низьких та помірних температурах. Звідси випливає, що метод дисперсного зміцнення в першу чергу є ефективним способом підвищення високотемпературної міцності та жароміцності, причому при таких температурах, коли інші методи, наприклад старіння, стають неефективними.
Якщо схематично зобразити зміну міцності відносно температури (рис. 1.1), то для чистих металів характерно достатньо монотонне знеміцнювання з більш інтенсивним падінням міцності при рекристалізації – (0,3–0,4) Тпл
. Для дисперснозміцнених сплавів характерна схожа залежність міцності від температури, але відношення міцності сплаву до міцності матричного металу постійно збільшується з підвищенням температури. Наприклад, якщо при температурах до (0,3–0,4) Тпл
це відношення звичайно не перевищує 2–3, то з приближенням до температури плавлення воно досягає 10–20. в старіючих сплавах високий рівень міцності зберігається до 0,7–0,8 температури плавлення основного металу, тобто до початку інтенсивної коагуляції і розчинення виділень, що зміцнюють. Подальше міцність старіючих сплавів падає настільки інтенсивно, що з приближенням до температури плавлення стає навіть нижче міцності чистих металів внаслідок зниження температури плавлення при легуванні.
Оцінюючи експлуатаційні властивості дисперсно-зміцнених сплавів потрібно мати на увазі характерну для них дуже високу стабільність характеристик міцності у часі.
У ряді випадків метод дисперсного зміцнення виявляється незамінним при утворенні матеріалів, що експлуатуються при помірних і навіть низьких температурах, але повинні, поряд з підвищеною міцністю та низькою швидкістю повзучості, мати певний комплекс фізичних властивостей. Сюди відносяться, наприклад, сплави для електротехніки на основі міді і срібла, в яких вимагається збереження високої електропровідності, цирконієві сплави для атомної енергетики з високою прозорістю для нейтронів та ін. Деякі дисперснозміцнені сплави вийшли за межі лабораторних розроблень, їх виготовляють в промислових масштабах та успішно використовують в конструкціях.
1.2 Дисперсно-зміцнені матеріали на основі міді
1.2.1 Властивості та використання мідних дисперсно-зміцнених матеріалів
Під час опису властивостей дисперсно-зміцнених матеріалів головна увага приділяється найбільш важливим експлуатаційним характеристикам, таким як межа міцності, показники пластичності, опір повзучості, тривала міцність, жаростійкість. При оцінюванні досягнутого рівня властивостей у різноманітних системах виникають труднощі співпоставлення, оскільки навіть стосовно до тих самих сплавів у різних роботах використані суттєво різні схеми отримання порошків та напівфабрикатів. Разом з тим по мірі удосконалення техніки отримання напівфабрикатів та оптимізації параметрів деформування та термічної обробки властивості майже всіх дисперснозміцнених сплавів будуть підвищуватися. Найбільш перспективними матеріалами в цьому відношенні є конденсовані дисперснозміцнені системи метал-метал з компонентами, що взаємно не розчиняються, які за можливістю зберігати задані властивості після впливу високих температур можуть перевершувати композиції метал-окисел. Новим технологічним прийомом синтезування композиційних матеріалів є метод вакуумної конденсації, який володіє рядом переваг перед порошковою металургією та внутрішнім окисленням. Здатність будь-яких речовин утворювати однорідну суміш у паровому стані та специфічні умови над швидкої заготовки, що реалізуються при конденсації цього пару на холодній підложці у вакуумі дозволяють отримувати матеріали, які неможливо отримати іншими методами. Характерною відмінністю конденсованих плівкових композитів є виключно висока неровноважність їх структури, яка зумовлює їх високі властивості міцності.
Найбільш цінними технічними властивостями міді, що визначають основні галузі її застосування, є високі електропровідність та теплопровідність. При звичайних методах легування вимоги підвищення жароміцності і збереження високої електропровідності вступають у супереч. Наслідком цього є те, що леговані сплави з електропровідністю не нижче 0,8 від електропровідності чистої міді характеризуються максимальним значенням відношення міцності сплаву до міцності матричного металу при температурах 0,5–0,6 Тпл
. При більш високих температурах це відношення падає занадто різко, що вже біля 700 °С (≈0,7 Тпл
) леговані сплави не мають переваг міцності відносно чистої міді.
Для дисперснозміцненої міді коефіцієнт зміцнення з підвищенням температури невпинно зростає, що забезпечує високу жароміцність при температурах 0,9–0,95 Тпл
.
Як видно з рисунку 1, переваги дисперсно-зміцнених матеріалів перед звичайними виявляються вже при температурах вище 0,5Тпл
(400 °С) и з підвищенням температури виявляються більш виразно.
Завдяки занадто малій розчинності кисню (менш 0,001% (за масою) при 800 °С) та низькій термодинамічній стабільності власних окислів мідь ефективно зміцнюється тугоплавкими окислами, що не взаємодіють з нею аж до температури плавлення. Найбільш високі значення жароміцності отримані при введені окислів алюмінію, берилію та торію. Для введення зміцнюючих окислів використовують методи внутрішнього окислення, хімічного осадження та відновлення у розчинах, які дають майже однакові результати. З підвищенням об’ємного вмісту зміцнюючої фази (при збереженні середнього розміру часток) міцність дисперснозміцненої міді підвищується, але для збереження високої електропровідності та хорошої пластичної у промислових жароміцних сплавах об’ємний вміст окислів не перевищує 1,5–2%. При такому вмісті зміцднюючої фази міцність при кімнатній температурі складає 380–450 МПа (в залежності від способу приготування порошків та режимів обробки напівфабрикатів) підчас подовжування 15–20%. Високий запас пластичності дозволяє методами холодного деформування отримувати прутки, листи, фольгу та проволоку малих перетинів.
Дослідження температурної залежності електропровідності міді, яка була зміцнена двоокисом торію і отримана з порошків, що виготовлені хімічним відновленням у розчинах, показало, що при кімнатній температурі вона складає біля 85% від електропровідності чистої міді, але з підвищенням температури ця різниця зменшується та при 800 °С значення електропровідності майже співпадають. У промислових марках, що зміцнені окислами берилію чи алюмінію та отримані з використанням методу хімічного осадження, електропровідність змінюється в межах 0,8–0,9 від електропровідності безкисневої провідникової міді.
Висока жароміцність дисперснозміцненої міді може бути вигідно використана при виготовлені обмоток роторів двигунів, що працюють при підвищених температурах, трубчатих теплообмінників, деталей електровакуумних приладів, контактів.
Широке використання дисперснозміцнена мідь знайшла у зварювальній техніці при виготовлені електродів для стикового та роликового зварювання. Робоча частина мідних електродів зварювальних машин у процесі експлуатації може нагріватися до 600–800 °С, внаслідок чого відбувається швидкий спад твердості і міцності, який призводить до погіршення стабільності та якості зварювання.
Результати досліджень механічних властивостей дисперсно-зміцнених композицій та аналіз механізмів їх зміцнення свідчить про те, що рівень їхніх характеристик міцності визначається складом та структурними параметрами матриці та фаз, що зміцнюють [5]. Специфіка структури вакуумних конденсатів міститься у високій дисперсності її елементів, сильній неровноважності та складному внутрішньому напруженому стані.
Високі властивості міцності дисперсно-зміцнених матеріалів обумовлені наявністю в об’ємі матриці некогерентних високодисперсних часток другої фази, які в значно більшому ступені, ніж субграниці та границі зерен чинять опір руху дислокацій під час деформування. Частки другої фази впливають також і на структуру матриці, знижують розмір зерна та переборюють у значному ступіні процеси рекристалізації.
1.2.2 Вплив дисперсних некогерентних часток двофазних сплавів на рекристалізацію
Відомо, що дисперсні тверді некогерентні частки можуть уповільнювати рекристалізацію металу.
Рекристалізація уповільнюється за двома причинами: по-перше, частки другої фази можуть обумовити стабільність дислокаційної структури; по-друге, вони можуть чинити опір перебудові дислокацій та ґратки, заважаючи утворенню границь зерен та їх міграції.
Підвищений опір рекристалізації полікристалічних матеріалів повинен проявлятися внаслідок стопорного ефекту виділень, що зупиняють дислокації, а не зумовлюватися границями зерен чи дислокаційними субграницями. Цей ефект можна розділити на дві категорії: зерно граничний та субграничний.
Ефективне подавлення рекристалізації відбувається у гетерофазних матеріалах, у яких відстань між частками менш ніж 10-3
мм. Так, наприклад, при відстані між частками, що становить декілька десятків нанометрів, рекристалізація може не відбуватися навіть при температурах відпалу, які приближуються до температури плавлення матеріалу матриці. Це відноситься в першу чергу до конденсованих дисперсно-зміцнених композицій, що мають дуже дисперсні, близько розташовані одна до одної зміцнюючі частки.
1.2.3 Методи виготовлення дисперсно
-
зміцнених композиційних матеріалів
1) Порошковий метод виготовлення дисперсно-зміцнених композиційних матеріалів (ДКМ). Виготовлюють суміші порошків матричного матеріалу та зміцнюючої фази. Зазвичай це суміші порошків металів з порошками оксидів, боридів, карбідів, потім пресування, спікання та термічна обробка. Недоліками цього методу є те, що цією технологією складно отримувати зміцнюючі частки розміром менш ніж 1000Å; під час спікання відбувається коагуляція часток та в результаті цього ДКМ поступається старіючим сплавам при помірних температурах.
2) Метод внутрішнього окислення. Технологія полягає в тому, що спочатку отримають сплав матричного матеріалу, легований метал, потім цей сплав нагрівають та витримують у атмосфері кисню, при цьому відбувається дифузія атомів кисню у глибину металу та їх взаємодія з легуючими елементами. Внаслідок цього в об’ємі матриці формуються частки зміцнюючої фази. Недоліками цього методу є обмежений вибір систем а також те, що по глибині металу частки мають не однаковий розмір, головним чином через те, що тривалість процесу для об’ємів, що знаходяться на поверхні та в середині зразка різна. У зв’язку з цим методом внутрішнього окислення отримують або тонкі фольги, або дифузійні шари.
3) Метод композиційних електрохімічних покриттів. Технологія полягає в тому, щоб до електроліту додавати високодисперсні порошки зміцнюючих часток (окисли, бориди, карбіди), потім відбувається процес отримання покриттів (електроліз). Частки порошку, які находяться в електроліті поглинаються фронтами кристалізації, тобто відбувається «замурування» їх в об’ємі. Недоліками цієї технології є отримання тільки тонких шарів, які насичуються Н2
та іншими елементами, що ходять до складу електроліту, а також цим методом неможливо отримати високодисперсні частки.
4) Метод кристалізації з парової фази у вакуумі. Кристалізація з парової фази має необмежені можливості вибору складових компонентів, дозволяє отримувати матеріали з рівномірним розподіленням часток другої фази по об’єму матриці та відкриває великі перспективи у рішенні проблеми диспергування зміцнюючих часток.
У якості зміцнюючої фази у конденсованих композиціях найбільше розповсюдження отримали окисли, а також карбіди, бориди, нітриди та метали, що мають обмежену розчинність в матриці або зовсім її не мають.
Технологія полягає в тому, що відбувається одночасне осадження матричного металу та матеріалу зміцнюючої фази. Під час конденсації на поверхні деталі чи підложці відбувається формування сплаву чи двофазної системи. Регулюючи технологічні параметри: температуру підложки, швидкість конденсації компонентів, ступінь вакууму можна отримати широкий діапазон структурних станів [7]. Таким чином можна отримувати будь-який ступінь дисперсності часток зміцнюючої фази, а також можна отримувати сплави таких металів, які не мають взаємної розчинності у рівноважних умовах. Якщо такі сплави піддати старінню шляхом термічної обробки, то в результаті незворотного розпаду пересичених розчинів формується композиційна структура, а матеріали, що отримані таким методом мають такі ж переваги як ДКМ та як старіючі сплави.
Недоліки цього методу: ДКМ отримують у вигляді фольги чи покриття на деталях; висока вартість методу; залежність структурних параметрів від багатьох факторів.
1.3 Вибір метода дослідження структури
Атестація структури, що містить нанорозмірні частки, судячи з літературних даних [13], є необхідною, але важкою задачею. Най частіше для вирішення таких задач використовують: рентгенівський та електронно мікроскопічний методи.
Рентгенівський метод
Дозволяє одержати усередненні данні які характеризують деякий об’єм речовини (наприклад, розмір областей когерентного розсіювання).
Для цього методу існують фізичні обмеження, пов’язані з тим, що при збільшенні дисперсності структури (часток, зерен) смуги поширюються та перекривають одна іншу, цей ефект спостерігається при зменшенні розміру нижче 1000Å. Така структура отримала назву рентген-аморфної.
Метод електронної мікроскопії
Метод дозволяє наглядно представити структуру, що вивчається та співпоставити її з дифракційною картиною. При цьому методі також спостерігається поширення смуг, але при цьому за рахунок того, що розмір хвилі на один або два порядки менший (0,1–0,01Å) ніж у рентгенівському методі то цей ефект спостерігається при дисперсності структури нижче 100Å. В той же час для електронограм характерна низька точність у визначенні положення смуг. Також, якщо зйомки при рентгеноструктурному аналізі потребують кількох годин, то при зйомці електронограм витримка складає декілька секунд.
З огляду на вище наведене, для вивчення нанорозмірних часток другої фази в дисперсно-зміцнених композитах з розміром зерна матриці менше 0,5 мкм доцільно використовувати метод електронної мікроскопії.
1.3.1 Просвічуюча електронна мікроскопія
В основі методу просвічуючої електронної мікроскопії (ПЕМ) лежить вплив на об'єкт дослідження електронного променя. При реалізації методу беруть участь електрони, що пройшли через об'єкт і електрони, що дифрагували відповідно до умови Брегга. [8]
Застосування методу просвічуючої електронної мікроскопії вплинуло на формування сучасних представлень про механізми фазових перетворень, про будівлю границь зерен і міжфазних поверхонь, про процеси пластичної деформації, полігонізації, рекристалізації, радіаційних ушкодженнях і про багатьох інших процесах і явищах, що складають основу сучасного матеріалознавства.
При визначенні параметрів просторової структури по електронно-мікроскопічним знімкам виникає ряд труднощів, які обумовлені наступними причинами: електронно-мікроскопічний знімок є пласким відображенням об’єму, тому в випадку однакової швидкості розчину матриці та частки на знімку присутні зображення як часток, так і їх розрізів верхньою та нижньою поверхнею зразка. Коли матеріал часток розчиняється швидше, ніж матеріал матриці, тоді на верхній та нижній поверхні будуть присутні тільки сліди часток, розрізнити які дуже складно. В тому випадку, коли частки не розчиняються в електроліті, їх зображення на знімку будуть в натуральний розмір. Окрім того, на знімку можливе багатократне накладання зображень часток, а визначити густину накладання часто неможливо. Але для малих концентрацій накладання чи зовсім відсутнє, чи цим ефектом можна зневажити.
1.3.2 Будова, збільшення і розрізнення просвічуючого електронного мікроскопа
Основою ПЕМ є джерело електронів − електронна гармата, розташована у вакуумній камері з вакуумом 10-4
…10-7
Па. Електронна гармата виконує функцію освітлювальної системи. Першою лінзою, у яку попадають електрони є конденсорна лінза. Конденсор фокусує на зразку зменшене зображення джерела електронів, що може бути перетворене в крапку ~ 2 мкм. Це забезпечує гарне висвітлення досліджуваної ділянки об'єкта.
Перше зображення об'єкта (досліджуваного зразка) формується в площині зображення об'єктивної лінзи. Надалі це зображення збільшується ще два рази – у проміжній і проекційній лінзі. Проекційна лінза формує кінцеве зображення об'єкта на флуоресціюючому екрані мікроскопа.
Проходячи через об'єкт, розташований поблизу апертурної діафрагми об'єктивної лінзи, електрони взаємодіють з атомами об'єкта і відхиляються від первісного напрямку, тобто розсіюються. Електрони, розсіяні на кут більше апертурного кута об'єктивної лінзи, обумовленого діаметром апертурної діафрагми, поглинаються в товщі матеріалу цієї діафрагми і надалі у формуванні зображення на екрані мікроскопа участі не приймають. Це дозволяє одержувати різке, контрастне зображення об'єкта [11].
Фокусування зображення здійснюється шляхом зміни фокусної відстані об'єктивної лінзи. Зміна фокусної відстані здійснюється зміною сили струму в обмотці лінзи.
У площині зображення об'єктивної лінзи розташовується рухлива селекторна (мікродифракційна) діафрагма. За допомогою цієї діафрагми можна одержати мікродифракційні картини від ділянок, виділених нею.
Для проведення металознавчих і метало-фізичних досліджень звичайно використовують мікроскопи з прискорюючою напругою 100…200 кВ. У залежності від типу об'єкта (щільності матеріалу) такі мікроскопи дозволяють переглядати об'єкти товщиною ~ 0,1…0,2 мкм.
Збільшення, забезпечуване просвічуючим електронним мікроскопом знаходиться у діапазоні ~ 200…400000 разів.
Теоретична розрізнююча здатність будь-якого оптичного приладу має величину порядку довжини хвилі випромінювання, що використовується для висвітлення об'єкта. Для 100 кВ електронного мікроскопа довжина хвилі електронів складає 0,037 Å. Однак, через наявність дефектів електронної оптики (хроматичної і сферичної аберації, астигматизму) реальна здатність електронних мікроскопів, що дозволяє, на 2…3 порядки гірше теоретичної. Проте, просвічуюча електронна мікроскопія дає можливість одержати зображення з високим розрізненням, аж до атомного (~ 0,1 нм).
1.3.3 Контраст і формування зображення
У формуванні зображення беруть участь тільки ті електрони, що попадають в отвір апертурної діафрагми. Якщо в результаті розсіювання частина електронів відхилилася на великі кути і не потрапила в отвір апертурної діафрагми, то інтенсивність електронного пучка, що бере участь у формуванні зображення, слабшає. Таким чином, зображення відповідної ділянки на екрані мікроскопа буде більш темним.
При дослідженні більш товстих і більш щільних об'єктів у більшому ступені виявляється розсіювання електронів, отже, через отвір апертурної діафрагми проходить менша кількість електронів. Це означає, що зображення товстих об'єктів буде більш темнішим, ніж тонких.
Якщо об'єкт має кристалічну структуру, то крім дифузійного розсіювання на контраст зображення буде впливати ще і дифракційне розсіювання. У загальному випадку кути дифракції перевищують апертурний кут об'єктива, тому у світлопольному зображенні за інших рівних умов кристалічні ділянки здаються більш темними, ніж аморфні.
Якщо об'єкт має полікристалічну структуру, то в залежності від орієнтації об'єкта стосовно електронного пучка яскравість зображення окремих ділянок (зерен) може сильно відрізнятися.
Умови відображення електронів можуть змінитися через вигини фольги чи локальних порушень кристалічної ґратки біля дефектів, наприклад біля дислокацій.
Дифракційним контрастом зображення можна керувати за допомогою контрольованого нахилу об'єкта навколо будь-якої заданої осі.
Контраст зображення можна поліпшити шляхом зменшення апертури об'єктивної лінзи. Теоретично це повинно приводити до втрати розрізнюючої здатності мікроскопа. До поліпшення контрасту також приводить зниження прискорюючої напруги.
Контраст на включеннях другої фази може мати або абсорбційну, або дифракційну природу. Абсорбційний контраст – частки другої фази можуть бути як з важчих так і з легших чим матриця атомів, та виглядати, відповідно, або світліше, або темніше від матриці. Однак в більшості случаїв контраст на частках другої фази має дифракційну природу.
Виділяють такі типи дифракційного контрасту:
А) Контраст на викривленях в матриці коло виділень:
1) деформаційний контраст виникає як що кристалічна решітка частки ізоморфна решітці матриці та має трохи інший період ґратки, а матриця коло включення пружно-здеформована.
Б) Контраст на виділеннях другої фази:
1) контраст за рахунок різниці структурних чинників матриці і виділень;
2) контраст на зображенні поверхні з’єднання фаз;
3) орієнтаційний контраст, спостерігається коли частки орієнтовані відносно матриці.
Так на тип контрасту, що спостерігається на електронно-мікроскопічних знімках, впливає цілий ряд чинників, тому аналіз електронно-мікроскопічних знімків досить кропіткий процес.
1.3.4 Розсіювання електронів речовиною. Утворення дифракційної картини в електронному мікроскопі
Щораз, коли на екрані електронного мікроскопа виникає зображення об'єкта, у задній фокальній площині об'єктива виникає дифракційна картина.
Якщо досліджується полікристалічний зразок, на електронограмі спостерігаються рефлекси, що мають форму концентричних окружностей.
У випадку дослідження монокристалічного зразка електронограмма виглядає у виді сукупності регулярно розташованих плям. Ці дифракційні максимуми виникають на тлі дифузійного розсіювання поблизу центральної плями. Орієнтація серій площин ґратки з міжплощинною відстанню d, при якій буде відбуватися дифракція електронів з утворенням дискретних рефлексів у вигляді плям чи кілець, визначається відомим законом Брегга [10].
λ = 2dhkl
sіnΘ,
де λ – довжина хвилі падаючих електронів (залежить від прискорюючої напруги; чим більше напруга, тим менше довжина хвилі);
Θ – кут між напрямком електронного променя й атомною площиною;
dhkl
- відстань між окремими площинами даної серії площин.
Дискретні дифракційні плями чи кільця утворяться тільки в тому випадку, якщо падаючі електрони розсіюються атомними площинами, розташованими стосовно падаючого променю під кутом Θ, що задовольняє закону Брегга.
Якщо при проходженні променів закон Брегга не виконується, то розсіяні електронні хвилі при взаємодії будуть послабляти один одного а, на електронограмі навколо центральної плями з'явиться тільки тло слабкого дифузійного розсіювання. Але в дійсності серед численних систем площин у кристалі завжди знайдеться кілька площин, розташованих під кутом Брегга стосовно падаючого променю. Отже, у електронограмі від кристалічного об'єкта завжди будуть матися дискретні рефлекси. На основі яких і проводиться фазовий аналіз. На точність проведення фазового аналізу будуть впливати багато чинників. При цьому може відбуватися накладення рефлексів матриці і другої фази, що найбільш вірогідно при когерентному зв’язку часток та матриці та (чи) високій дисперсності другої фази. Також на електронограмах можуть утворюватися сателіти, тяжі та ін., що ускладнює аналіз, є також вірогідність одержання зображення не придатного для репродукції.
2. Вибір напрямку дослідження
Дисперсно-зміцнені композиційні матеріали на основі міді дістали широкого використання в таких галузях як електротехніка, мікроелектроніка та ядерна техніка. Відомо, що рівень фізико-механічних властивостей дисперсно-зміцнених композиційних бінарних систем Cu–Mo, Cu–W, Cu–Ta, Cu-Co, Cu-Fe залежить від ступеня дисперсності структурних елементів та вмісту зміцнюючої фази, а стабільність властивостей обумовлена стабільністю структури. За умови, що частки зміцнюючої фази не перерізаються дислокаціями, характеристики міцності визначає не розмір самих часток, а відстань між ними, також важливі рівномірність розподілення та характер зв’язку частка-матриця. Всі ці характеристики мікроструктури можна змінювати, змінюючи технологію виготовлення та послідуючу термічну обробку для утворення оптимальної мікроструктури та надання матеріалу заданих властивостей, необхідно також дослідження її термодинамічної стабільності. Це можливо лише при певному контролі структури та детальному знанню її змін під впливом технологічних чинників.
Метою даної роботи є покращення характеристик дисперсно-зміцнених композитів на основі міді, шляхом встановлення впливу термічної обробки на морфологію нанорозмірних часток зміцнюючої фази.
Для досягнення мети вирішувалися наступні задачі:
1) Визначення особливостей часток другої фази дисперсно-зміцнених композитів бінарних систем Cu–Mo, Cu–W, Cu–Ta, Cu-Co, Cu-Fe в вихідному стані;
2) Дослідження впливу відпалу на другу фазу композитів.
3.
Теоретичні та експерементальні дослідження
3.1 Матеріал дослідження
Матеріалом дослідження є композити на основі міді, що виготовлені методом осадження у вакуумі, другою фазою яких є частки кобальту, заліза, молібдену, вольфраму, танталу.
Зразки у вигляді плівок Cu-Co, Cu-Fe, Cu-W, Cu-Ta, Cu-Mo були виготовлені методом електронно-променевого випаровування компонентів з роздільних джерел у вакуумі, ступінь якого коливається у межах 10-4
– 10-5
мм. рт. ст. Осадження плівок проводилося на ситалову підложку, яка підігрівалась до температури 500 °С зі швидкістю 9–15 мкм/хв. Отримані плівки мали товщину 5–25 мкм при вмісті зміцніючої фази 0,1–5%
3.2 Підготовка зразків для дослідження методом просвічуючої електронної мікроскопії
Для електронно-мікроскопічних досліджень виколювали зразки діаметром 3 мм, а потім стоншували методом струменевої електролітичної поліровки. Склад електроліту: ортофосфорна кислота густиною 1,55 г./см3
. Режим стоншення U=14–15 В, І=17 мА.
3.3 Методика дослідження зразків методом просвічуючої електронної мікроскопії
Електронно-мікроскопічні дослідження проводили на електронному мікроскопі ПЕМ-100. При цьому зі зразків були зроблені знімки, які були початковим матеріалом для отримання даних про розмір та форму часток.
Розмір часток вимірювали за допомогою вимірювального мікроскопу МІМ-2 в різних напрямках на багатьох знімках а площу за допомогою програми обробки зображень на базі пакету MATLAB. Отримані дані використовували для побудови гістограм їх розмірів. Гістограми будували в координатах відносний розмір часток-кількість часток даного розміру в відсотках.
3.4 Методика аналізу електронограм
Метод
постійної приладу
Згідно з тим, що кут Θ достатньо невеликий, то sinΘ дорівнює Θ, тому рівняння Вульфа-Брега λ=2dsinΘ може бути переписано у вигляді λ=d2 Θ, де d– міжплощинна відстань, що відповідає плямі, для якої визначаються індекси. Вважаючи, що 2Θ=tg2Θ= r/L отримаємо
Lλ=dr, де (3.1)
L – довжина приладу,
r – відстань від центру електронограми до індицируємої плями.
Lλ – постійна приладу, що визначається вимірюванням відстані r на електронограмі речовини з точно відомими параметрами ґратки.
Визначення індексів плям на електронограмі за допомогою методу постійної приладу полягає у вимірюванні величини r для кожного рефлексу, розрахунку міжплощинної відстані d з рівняння (3.1) і співпоставленні її з міжплощинними відстанями, що зведені в таблицях довідника стандартних параметрів ґратки для досліджуємого металу. Індекси площини, міжплощинна відстань якої dнайближче підходить до експериментально визначеної, попередньо приписують плямі, що досліджується.
Метод відношень
Попередньо знайдені індекси повинні перевірятися порівнянням виміренних значень r з відомою міжплощинною відстанню d. Згідно з рівнянням (3.1) r~(1/d). Відповідно, відношення значень rдля будь-яких двох плям буде дорівнювати

Якщо це співвідношення зберігається для кожної пари плям, то тоді попередньо встановлені індекси повинні відповідати міжплощинним відстаням, що визначаються.
3.5 Розрахунок розміру часток по електронно-мікроскопічним знімкам
Проводили розрахунок двома методами.
Метод січних
(визначення умовного розміру часток) полягає в тому, що на зображенні проводиться визначене число ліній у різних напрямках. Потім підраховується кількість перетинів границь часток кожною лінією. Після чого сумується кількість перетинань границь по всіх частках для всіх ліній.
Умовний розмір часток при цьому визначали по формулі:
dусл
=∑L/K·∑n, (2.1)
де К – збільшення;
∑L – сумарна довжина сiчних ліній;
∑n – сумарна кількість пересічень ліній.
Другий метод складається з визначення загального числа кулястих мікрочастинок в обсязі сплаву методом площин.
Метод площин.
Для одержання надійного результату необхідно щоб загальне число обмірюваних площин мікрочастинок склало приблизно 150–200.
При цьому в ряді полів зору (чи на мікрофотографії) вимірюються площини досить великої кількості мікрочастинок. Вимірювання площин та аналіз розмірних характеристик структури проводилися за допомогою програми на базі пакету MATLAB у інтерактивному режимі, також розраховувався еквівалентний діаметр часток.
4.
Структура бінарних дисперсно-зміцнених композитів на основі міді вакуумного походження у вихідному стані
Відомо [15], що при конденсації двох або багатокомпонентного пару, наприклад, типу метал-окисел чи метал-метал з мало чи зовсім нерозчинними у рівноважних умовах компонентами формуються пересичені розчини, гетерофазні конденсати з різним розміром структурних елементів. У зв’язку з тим, що морфологія другої фази дуже впливає на фізико-механічні властивості конденсатів, в роботі проведено порівняльне вивчення морфологічних особливостей часток другої фази в конденсатах бінарних систем на основі міді.
Головне призначення технологічного процесу виготовлення дисперсно-зміцнених композитів сплавів, що розглядаються – утворення гетерофазної високодисперсної, аж до нанорівня, структури. Нанозерна з нанодисперсними, рівномірно розташованими виділеннями зміцнюючої фази всередині пересиченого твердого розчину.
Механічні та електрофізичні властивості дисперсно-зміцнених композитів залежать від вмісту зміцнюючої фази та дисперсності структурних складників. Тому особлива увага приділяється тим композитам, у яких досягнута дисперсність нанорівня. Це дисперсно-зміцнені композити на основі систем: Cu-Mo, Cu-W, Cu-Ta, в яких другий компонент не розчиняється в матриці у рівноважних умовах. Для порівняння досліджувалися дисперсно-зміцнені композити на основі систем Cu-Co, Cu-Fe, що одержані в однакових умовах, другий компонент яких має незначну розчинність в матриці.
Структура дисперсно-зміцнених композитів у вихідному стані (рис. 4.1– рис. 4.5) представляє собою двофазну систему або однофазну, при низькому вмісті другого компоненту. Матриця в цих системах, згідно даних по періоду ґратки, є пересиченим твердим розчином легуючих елементів в міді, друга фаза, наявність якої підтверджують дані електронографічного аналізу (рис. 4.1 – рис. 4.5) – нанорозмірні частки Ta, Mo, W, Co та Fe Середній розмір зміцнюючих часток композитів, що одержані в однакових умовах зведені у таблиці 4.1.
Таблиця 4.1-Розмір часток у дисперсно-зміцнених композитах вакуумного походження
Система |
Нерозчинні компоненти |
Обмежено розчинні компоненти |
Cu-Ta |
Cu-W |
Cu-Mo |
Cu-Co |
Cu-Fe |
Dч
, нм |
14 |
8 |
5 |
12 |
34 |
Як видно у системах з нерозчинними компонентами дисперсність часток вища. Крім того вид контрасту на електронно-мікроскопічних знімках системи Cu-Co є характерним (деформаційний контраст), це говорить про когерентний зв’язок частка-матриця. Такий тип контрасту спостерігається також в системі Cu-Co металургійного походження. Відсутність такого контрасту в системі Cu-Fe скоріш за все обумовлена незначною різницею атомних діаметрів міді та заліза та відповідно низьким рівнем напружень у матриці. Виділення Ta, Mo, Wне мають яскраво виражених границь, до них скоріш за все можна застосувати термін гетерогенна зона, що зустрічається в літературі. Контраст на знімках цих систем, скоріш за все, обумовлений різною здатністю атомів до розсіювання. Виходячи з типу контрасту та значної різниці атомних діаметрів компонентів можна припустити некогерентний зв’язок частка-матриця.
Виявлено, що у вихідному конденсованому стані структура фольг Cu-Mo, Cu-W, Cu-Та, Cu-Co, Cu-Fe є двофазною.
Метод спільного осадження у вакуумі нерозчинних компонентів, що випарені з різних джерел, дозволяє отримати гетерофазну нанодисперсну структуру. Застосування у якості другого компоненту Ta, Mo, W, які не розчиняються у міді, дозволяє збільшити дисперсність виділень.
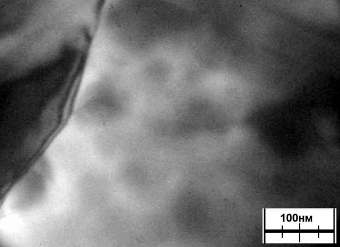 |
а |
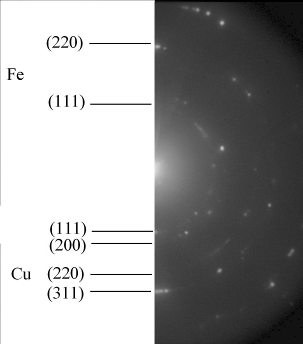 |
б |
а – світле поле; б – дифракція |
Рисунок 4.1 – Електронно-мікроскопічне зображення (а) та дифракція (б) композиту Cu-Feв вихідному стані |
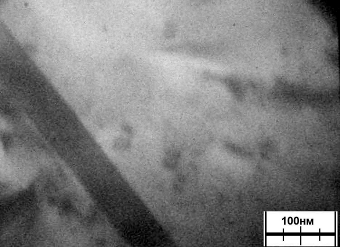 |
а |
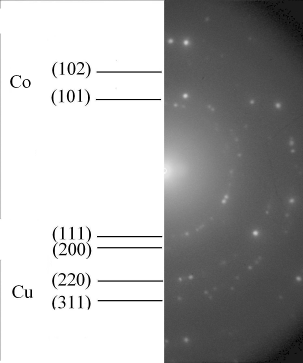 |
б |
а – світле поле; б – дифракція |
Рисунок 4.2– Електронно-мікроскопічне зображення (а) та дифракція (б) композиту Cu-Coв вихідному стані |
 |
а |
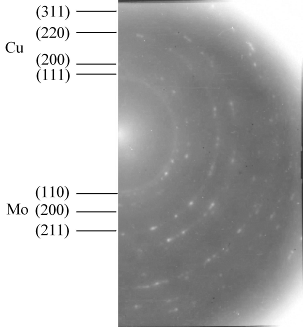 |
б |
а – світле поле |
б – дифракція |
Рисунок 4.3– Електронно-мікроскопічне зображення (а) та дифракція (б) композиту Cu-Moв вихідному стані |
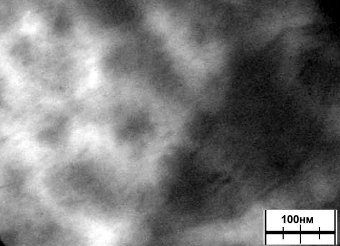 |
а |
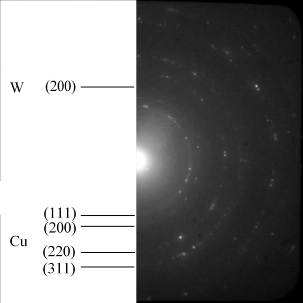 |
б |
а – світле поле |
б – дифракція |
Рисунок 4.4– Електронно-мікроскопічне зображення (а) та дифракція (б) композиту Cu-Wв вихідному стані |
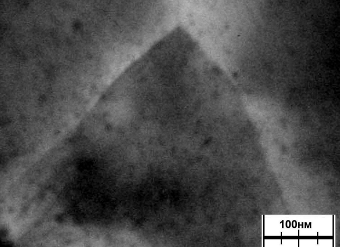 |
а |
 |
б |
а – світле поле |
б – дифракція |
Рисунок 4.5– Електронно-мікроскопічне зображення (а) та дифракція (б) композиту Cu-Taв вихідному стані |
4.1 Стабільність виділень другої фази в бінарних дисперсно-зміцнених композитах вакуумного походження
Вивчення впливу відпалу є дуже важливим з кількох причин. Так основа необхідної жароміцності дисперсно-зміцнених композитів − збереження дисперсності гетерофазної структури. Як відомо, «огрубіння» структури (процеси коагуляції, сегрегації) має дифузійну природу. Процеси дифузії прискорюються при підвищенні температури, і дослідження впливу відпалів при підвищених температурах на структуру дисперсно-зміцнених композитів дозволяють прогнозувати їх поведінку при температурі експлуатації. До того ж відпал є важливою технологічною операцією термічної обробки.
Відпал проводили вар’юючи температуру в інтервалі 500 – 900 о
С та час в інтервалі від 30 хв. до 3 год. На електронно-мікроскопічних знімках вимірювався розмір часток, у випадку їх округлої форми приймали діаметр частки, а якщо форма часток інакша, розраховували за площею, яку займає частка, її еквівалентний діаметр. На основі отриманих даних будувались гістограми розподілення, перевірялась статистична гіпотеза відповідності нормальному розподіленню, згідно чого експериментальні дані і апроксимувались.
На рисунках 4.6– рис. 4.10 приведена структура дисперсно-зміцнених композитів після відпалу. Під його впливом в усіх досліджених системах змінюеться густина часток на одиниці площи. Крім того в частках другої фази системи Cu-Fe при температурі 800 о
С протікає поліморфне перетворення зі зміною контрасту (рис. 4.6) та характеру зв’язка з матрицею. З теорії відомо, що навіть при частковій втраті когерентності в кілька разів зростає модуль зміцнення. Це явище може бути використане в на практиці.
На рисунках 4.11 – 4.13 наведені гістограми розподілення часток за розмірами після різних режимів відпалу, також показані характеристики розподілення: середній діаметр та дисперсія. Прийнято вважати, що кожній температурі та тривалості відпалу відповідає певний розмір часток. Проте, дані електронної мікроскопії вказують, що спостерігається полідисперсна система часток. Можливо ця невідповідність між теоретичною оцінкою механічних властивостей, наприклад по Оровану, та експериментальних даних пов’язана з цим спрощенням. Також з отриманих даних видно, що характер розподілення часток за розмірами залежить від температури та часу витримки при відпалі (рис. 4.11–4.13). Зі збільшенням часу витримки чи температури відпалу кількість дрібних часток зменшується, максимуми на кривих знижуються, а дисперсія збільшується, хоча для системи Cu-Ta спостерігається її зниження (рис. 4.13).
Розглядаючи отримані експериментальні дані можна відмітити, що зміна розміру часток у всіх системах протікає певним чином у наступній послідовності, найбільш наглядно це виражено в системах Cu-Mo, Cu-Co:
1. Спочатку спостерігається зниження середнього розміру часток (рис. 4.11, 4.12 (б)) відносно вихідного стану. Це можна пояснити, наприклад, зміною характеру контрасту на частках у випадку первинних та відпалених зразків або, що вірогідніше, розпадом пересиченого твердого розчину з утворенням більш дисперсних часток. Проте встановлення причин цього явища потребує подальших досліджень.
2. Потім спостерігається монотонне підвищення середнього діаметру часток з одночасним підвищенням дисперсії, що пояснюється подальшим розпадом пересиченого твердого розчину та коагуляцією часток (рис. 4.11, 4.12 (в, г) та рис. 4.13 (в)).
Характерно те, що у поведінці системи з найбільшою невідповідністю атомних розмірів розчинника та розчинного є деякі особливості (рис. 4.13):
1. Деградація другої фази відбувається значно повільніше у порівнянні з іншими системами.
2. Відзначається деяке зниження дисперсії розміру часток у порівнянні з вихідним станом.
Відпал повинен впливати і на зеренну структуру композитів. На рис. 4.14 наведена зеренна структура дисперсно-зміцених композитів у вихідному стані та після високотемпературного відпалу.
Видно, що темп зміни зерневої структури, перш за все величини зерна, для різних систем відрізняється. Найбільш сильно зернева структура змінюється в системі Cu-Co, в системі Cu-Та зміни спостерігаються лише у вигляді границь зерен. Тож зміни у зернистій структурі матриці корелюють із змінами на рівні часток, хоча значно запізнюються у відношенні до них.
Встановлено, що деградація структури у вивчених системах відбувається у певній послідовності, але швидкість процесу залежить від розчинності другого компоненту в матриці та від його атомного радіусу.
Зміни у зернистій структурі матриці корелюють із зміною морфології часток, хоча значно запізнюються у відношенні до них. Найбільшою структурною стабільністю володіють композити на основі системи Cu-Ta.
 |
а
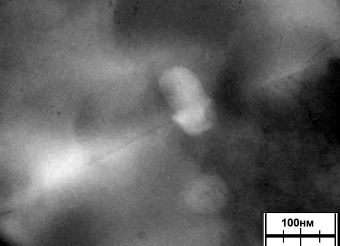
б
|
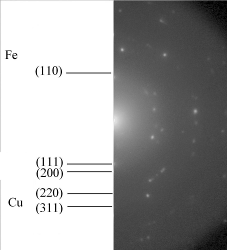
в
|
а – світле поле, відпал (600 о
С, 1 час); б – світле поле, відпал (800 о
С, 1 час); в – дифракція, відпал (800 о
С, 1 час)
Рисунок 4.6 – Структура композиту Cu-Feпісля відпалу
|
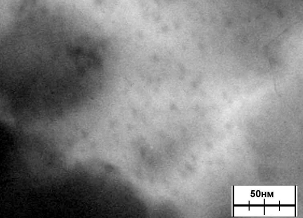 |
Рисунок 4.9 – Структура композиту Cu-W після відпалу при температурі 800о
С, 1 година |
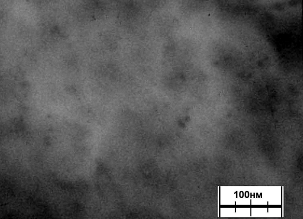 |
Рисунок 4.10 – Структура композиту Cu-Ta після відпалу при температурі 900о
С, 1 година |
а – вихідний стан; б – відпал (800 о
С, 1 час); в – відпал (900 о
С, 1 час)
Рисунок 4.13 – Гістограма розподілення часток другої фази композиту Cu-Ta в вихідному стані та після відпалу
5. Економічне обгрунтування і оцінка дипломної роботи
5.1 Обґрунтування дослідження
Дана робота є частиною дослідження, яке проводиться у рамках держбюджетної теми М 2016 та виконується кафедрою «МіТОМ» НТУ «ХПІ». Був складений кошторис витрат на проведення науково-дослідницької роботи. При складанні кошторису враховувалося, що для виконання даного дослідження необхідно 4 місяці повноцінної роботи дослідників і керівників дослідження.
Плановий кошторис витрат на проведення дипломної науково – дослідницької роботи включає статті:
1) заробітна плата;
2) відрахування у фонд соціального страхування;
3) витрати на матеріали;
4) витрати на електрику;
5) амортизаційні відрахування;
6) витрати на господарчий інвентар;
7) витрати на воду.
Дипломна науково-дослідницька робота «Друга фаза композитів на основі міді, що виготовлені методом осадження у вакуумі» проведена на кафедрі «Металознавство і термічна обробка металів» Національного технічного університету «Харківський політехнічний інститут».
Об'єктами дослідження були конденсовані плівки Cu-W, Cu-Ta, Cu-Mo.
5.2 Розрахунок заробітної плати
Заробітна плата – це частина національного доходу, що виділяється для особистого споживання працюючих відповідно до якості і кількості їхньої праці. [16]
Чисельність співробітників для проведення НДР установлюється згідно зі штатним розкладом.
Основний фонд заробітної плати всіх, хто приймає участь у проведенні НДР, наведений у табл. 5.1.
Таблиця 5.1 – Витрати по заробітній платі
Склад
виконавців
|
Кількість
працівників
|
Оклад
на місяць, грн
|
Кількість
місяців
роботи
|
Сума, грн |
Керівник НДР |
1 |
844 |
4 місяця |
3376 |
Виконавець |
1 |
175 |
4 місяця |
700 |
Разом |
4076 |
Основний фонд заробітньої плати визначається за формулою (5.1):
де Р – кількість людин даної посади;
М – оклад на місяць;
Ч – кількість місяців роботи.
5.3 Розрахунок додаткової заробітної плати
дисперсний мікроскопічний композит вакуумний
Додаткова заробітна плата складає 40% від основної, и визначається за формулою (5.2):
Здод
= 0,4∙4076=1630,4 грн. |
(5.2) |
5.4 Розрахунок відрахувань у фонд соціального страхування
Відрахування у фонд соціального страхування складають 37% від основної та додаткової заробітної плати, і визначаються за формулою (5.3):
Всоц стр
= 0,37∙(Зосн
+Здод
) |
(5.3) |
Всоц стр
= 0,37 (4076+1630,4)=2111,4 грн.
Сумарна заробітна плата визначається за формулою 5.4:
Зсум
=Зосн
+Здод
+Всоц стр
|
(5.4) |
Зсум
=4076+1630,4+2111,4=7817,8 грн.
5.5 Розрахунок витрат на матеріали
Витрати на матеріали, що використовуються при виконанні дипломної роботи наведені в табл. 5.2
Таблиця 5.2 – Витрати на матеріали
Найменування
матеріалу
|
Одиниця
виміру
|
Кількість |
Ціна за
одиницю, грн.
|
Сума, грн. |
Папір
для креслення
|
лист |
5 |
1 |
5 |
Папір |
пачка |
1 |
15 |
15 |
Олівець |
шт. |
1 |
0,5 |
0,5 |
Лінійка |
шт. |
1 |
0,5 |
0,5 |
Маркер |
шт. |
1 |
4 |
4 |
Фотоплівка |
шт. |
1 |
10 |
10 |
Друк фотографій |
шт. |
70 |
1 |
70 |
Гумка |
шт. |
1 |
0,5 |
0,5 |
Електроліт |
л. |
0,2 |
50 |
10 |
ФольгаCu-W, Cu-Ta, Cu-Mo |
грам |
1,5 |
80 |
120 |
Всього |
235,5 |
5.6 Розрахунок витрат на електроенергію
Витрати на електроенергію, що споживає обладнання, визначаються за формулою (5.5):
де М–потужність обладнання;
Тр
–час роботи;
К–коефіцієнт використання, (0,9);
Ц–ціна 1 кВт.
У відповідності з переліком обладнання, що використане в роботі, складена табл. 5.3.
Таблиця 5.3 – Обладнання що використовується
Найменування
обладнання
|
Потужність,
кВт
|
Час роботи, г |
Витрати електроенергії |
Мікроскоп металографічний МИМ-8 |
0,2 |
5 |
1 |
Прилад для вимірювання
мікротвердості ПМТ-3
|
0,2 |
5 |
1 |
Електронний мікроскоп |
1 |
25 |
25 |
Установка для стоншення зразків |
1 |
10 |
10 |
Комп’ютер |
1 |
150 |
150 |
Разом |
187 |
Таким чином, при ціні за 1 кВт·г електроенергії, що дорівнює 0,35 грн, загальна вартість електроенергії складає:
Взаг обл
= 187·0,9·0,35=58,9 грн.
Витрати на електроенергію для освітлення визначаються за формулою (5.6):
Восв
= ∑S∙Q∙T∙Cосв
∙K/ 1000, |
(5.6) |
де ∑S – освітлювана площа, 32 м2
;
Q – питома витрата електроенергії, 15 Вт/ м2
;
К – коефіцієнт, що враховує одночасне горіння ламп, 0,8;
Т – години горіння, 160 г.;
Сосв
– вартість 1 кВт·г, 0,35
Восв
= 32∙15∙0,35∙0,8∙160/1000 = 21,5 грн.
Загальні витрати на електроенергію визначаються за формулою (5.7):
Взаг
= Взаг обл
+ Восв
. |
(5.7) |
Взаг
=58,9+21,5=80,4 грн.
5.7 Розрахунок амортизаційних відрахувань
Амортизацією називають процес відшкодування зносу основних фондів. [17].
Амортизаційні відрахування – грошове вираження амортизації для одиниці устаткування в даній роботі визначаються за формулою (5.8):
Аобл
= |
(5.8) |
де Оц
– оптова ціна за одиницю обладнання;
На
– норма амортизації;
Т – термін використання обладнання, міс;
В табл. 5.4 наведена вартість обладнання, що використане
Таблиця 5.4 – Вартість обладнання
Найменування
обладнання
|
Одиниці
виміру
|
Кількість |
Вартість
Одиниці
|
Норма
амортизації
|
Строк використання, міс |
Сума
амортизації
|
Приміщення |
м2
|
32 |
400 |
10% |
4 |
13,33 |
Мікроскоп металографічний МИМ-8 |
шт. |
1 |
3000 |
15% |
0,008 |
0,3 |
Електронний мікроскоп ПЕМ100 |
шт. |
1 |
50000 |
15% |
0,04 |
25 |
Прибор для вимірюваннямікротвердості ПМТ-3 |
шт. |
1 |
5000 |
15% |
0,008 |
0,5 |
Установка для стоншення зразків |
шт. |
1 |
5000 |
15% |
0,015 |
0,95 |
Комп’ютер |
шт. |
1 |
3000 |
15% |
0,23 |
8,65 |
Разом |
48,73 |
Аобл.
=48,75 грн
Таким чином, амортизаційні відрахування на виробничі приміщення та технологічне обладнання приймаємо 48,75 грн за 4 місяця.
5.8 Розрахунок витрат на господарський інвентар
Амортизаційні відрахування на господарський інвентар за 4 місяці роботи визначаються за формулою (5.9):
Вгос інв
=Цод
∙На
∙М/12, |
(5.9) |
де Цод.
– ціна інвентарю;
На
– норма амортизації;
М – місяці роботи.
Кошторис витрат на господарський інвентар наведений у табл. 5.5
Таблиця 5.5 – Витрати на господарчий інвентар
Найменування інвентарю |
Кількість одиниць |
Вартість одиниці, грн. |
Норма амортизації, % |
Амортизаційні відрахування, грн. |
Стіл |
1 |
150 |
40 |
20 |
Стілець |
1 |
60 |
40 |
8 |
Шафа |
1 |
320 |
40 |
42,66 |
Всього |
70,66 |
Таким чином амортизаційні відрахування на господарський інвентар приймаємо 70,66 грн за 4 місяця
5.9 Розрахунок витрат на опалення
Вартість 1м2
опалювальної площі за один рік складає 15 грн. Площа лабораторії складає 32 м2
.
За один рік вартість опалення складає:
32∙15=480 грн.
За чотири місяці роботи вартість опалення:
5.10
Розрахунок витрат на воду
Витрати установки на воду визначаються за формулою (5.10):
де Тв
– дійсний фонд часу роботи установки, г;
Цв
– вартість води, 0,95 грн.;
П – норма витрати води, м3
.
Вв уст
=35∙0,95∙0,063=2,1 грн.
Витрати працівників на воду визначаються за формулою (5.11):
Вв прац
=n·Цв
· N ·П, |
(5.11) |
де n – кількість працівників;
Цв
– вартість води, 0,95 грн.;
N – кількість місяців роботи;
П – норма витрати води на одного працівника за місяць, м3
.
Вв прац
=2∙0,95∙4·1,25=9,5 грн.
Сумарні витрати на воду визначаються за формулою (5.12):
Вв сум
=Вв уст
+ Вв прац.
|
(5.12) |
Вв сум
=2,1+9,5=11,6 грн.
Кошторис витрат на проведення дипломної роботи наведений у табл. 6.6.
Таблиця 5.6 – Кошторис витрат на проведення дипломної роботи
Витрати |
Сума, грн |
Основна заробітна плата |
4076 |
Додаткова заробітна плата |
1630,4 |
Відрахування соціальні витрати |
2111,4 |
Витрати на матеріали |
235,5 |
Витрати на електроенергію |
80,4 |
Амортизаційні відрахування |
48,75 |
Витрати на господарчий інвентар |
70,66 |
Витрати на опалення |
160 |
Витрати на воду |
11,6 |
Всього |
8424,71 |
Загальні витрати на дипломну роботу визначаються за формулою (5.13):
де 1,2 – коефіцієнт, що враховує планові накопичення.
ЗНДР
=8424,71·1,2=10109,65 грн.
Загальні передвиробничі витрати залежать від пайової участі організацій у розробці [20]. У середньому частка пошукових і прикладних досліджень складає 40% і визначається за формулою (5.14):
Кпередвироб
= , |
(5.14) |
де охоплює Зпроек
+Зісп
+Зост
Кпередвироб
=10109,65/0,4=25274,13 грн.
5.11 Розрахунок економічного потенціалу НДР
Економічний потенціал визначається за формулою (5.15):
де Кпідп
– укрупнений норматив загальних трудових витрат;
t – тривалість даного дослідження, рік;
р – чисельність дослідників, що працюють над даною темою.
Ент
= 75230,2·0,33 2·=49651,93 гр.
За умови наявності одного споживача даної НДР.
5.12 Види ефективності НДР у вищих навчальних закладах
Ефективність НДР у вищих навчальних закладах проявляється у взаємозв’язку і взаємодії декількох середовищ:
– навчального процесу;
– процесу проведення НДР;
– процесу створення й експлуатації нової техніки.
Тому оцінку ефективності варто здійснювати за наступними напрямками:
– загальнонаукова;
– навчально-дослідницька;
– економічна.
Загальнонаукова ефективність характеризується показниками, що відбивають взаємовідношення НДР вищого навчального закладу з наукою, вона характеризує рівень приросту нової науково-технічної інформації, що отримана в результаті проведення наукових досліджень і призначеної для подальшого розвитку науки [18].
Навчально-дослідницька ефективність обумовлена співвідношенням НДР з навчальним процесом. Вона характеризує ступінь впливу наукових досліджень на удосконалення навчального процесу: кваліфікацію професорсько-викладацького складу, методику й організацію процесу навчання, якість підготовки фахівця.
Економічна ефективність наукових досліджень проводиться у відповідності з «Методическими указаниями по комплексной оценке эффективности мероприятий, направленных на ускорение научно-технического прогресса (1987 г.)».
Загальнонаукова й навчально-дослідницька ефективність взаємозалежні і можуть бути виражені в бальній оцінці, тому їх можна об’єднати в єдиний показник – інтегральний з урахуванням високих коефіцієнтів.
5.13 Навчально-дослідницька ефективність
5.13.1 Розрахунок показника навчально-дослідницької діяльності
Показник навчально-дослідницької діяльності К1
визначається як сума приватних показників К1j
, що характеризують різні ознаки навчально-дослідницької ефективності вузівських НДР і приведених до однієї розмірності за допомогою коефіцієнтів ознак Y1j
за формулою (5.16):
де К1j
–приватний показник Y-тої ознаки навчально-дослідницької ефективності НДР;
Y1j
– ваговий коефіцієнт j-тої ознаки навчальної ефективності НДР;
j-кількість приватних показників навчально-дослідницької ефективності НДР, j = 1, 2, m.
Приватні показники навчально-дослідницької ефективності НДР визначаються на основі бальної оцінки [19].
5.13.2 Розрахунок показника рівня відповідності НДР
Показник рівня відповідності НДР визначається за формулою (5.17):
Таблиця 5.7
Рівень відповідності |
Бал τ1k
|
Цілком відповідає |
1,0 |
Значною мірою відповідає |
0,5 |
До деякої міри відповідає |
0,2 |
Цілком не відповідає |
0,0 |
К1.1
= 1,0.
5.13.3 Розрахунок показника ступеня участі викладачів в НДР
Показник ступеня участі викладачів в НДР визначається за формулою (5.18):
К1.2
=
, |
(5.18) |
де Qп
– кількість викладачів, що беруть участь у виконанні даної теми, люд; Qп
= 1;
Qз
– загальна кількість виконавців даної теми, люд; Qз
= 1;
К1.2
= = 1.
5.13.4 Розрахунок показника ступеня участі студентів в НДР
Показник ступеня участі студентів в НДР визначається за формулою (5.19):
К1.3
=
, |
(5.19) |
де Qг
– кількість студентів, що беруть участь у виконанні даної теми, люд; Qг
= 1.
К1.3
= 1.
5.13.5 Розрахунок показника рівня використання результатів НДР у курсових і дипломних проектах
Показник рівня використання результатів НДР у курсових і дипломних проектах визначається за формулою (5.20):
К1.4
= , |
(5.20) |
де Qk
– кількість курсових проектів, що виконані з використанням результатів даної НДР;
Qу
– кількість дипломних робіт, що виконані з використанням результатів даної НДР;
К1.4
=2+0,4+1 =3,4.
5.14 Наукова ефективність
5.14.1 Розрахунок показника загальнонаукової ефективності НДР
Показник загальнонаукової ефективності НДР визначається за формулою (5.21):
де К2j
– приватний показник j-тої ознаки загальнонаукової ефективності НДР;
Y2j
– ваговий коефіцієнт j-тої ознаки загальнонаукової ефективності НДР;
5.14.2 Розрахунок показника рівня важливості НДР
Показник рівня важливості НДР визначається за формулою (5.22):
Таблиця 5.8-Рівень важливості дослідження
Рівень ознаки |
Визначення рівня |
Бал τ1k
|
Світовий |
Робота, результати якої можуть бути використані в дослідженнях інших стран за даною проблемою |
1,0 |
Вітчизняний |
Робота, результати якої можуть бути використані в деяких галузях народного господарства |
0,7 |
Галузевий |
Робота, результати якої можуть бути використані тільки в масштабах конкретної галузі |
0,4 |
Внутрішньо-інститутський |
Робота, результати якої можуть бути використані тільки в масштабах конкретної організації |
0,2 |
К2.1
= 1.
5.14.3 Розрахунок показника рівня новизни НДР
Показник рівня новизни НДР визначається за формулою (5.23):
Таблиця 5.9-Рівень новизни НДР
Рівень ознаки |
Визначення рівня |
Бал τ2k
|
Принципово нова |
Робота не нова за постановкою задачі але заснована на застосуванні оригінальних методів дослідження |
1,0 |
Відносно нова |
Робота, що має елементи новизни в постановці задачі і методах дослідження |
0,6 |
Традиційна |
Робота виконана за традиційною методикою |
0,2 |
К2.2
= 1.
5.14.4 Розрахунок показника рівня публікацій загальнонаукового значення за результатами НДР
Показник рівня публікацій загальнонаукового значення за результатами НДР визначається за формулою (5.24):
К2.3
= , |
(5.24) |
де Q3k
– кількість публікацій загальнонаукового значення К-того виду за результатами НДР, Q3k
= 1;
τ3k
– бал К-того виду публікацій; (табл. 5.10);
Таблиця 5.10-Бал К-того виду публікацій
Вид публікацій |
Кількість Q3k
|
Кількість τ3k
|
Q3k
τ3k
|
Книга, монографія |
1 |
1,0 |
1 |
Стаття в центральних виданнях |
1 |
0,5 |
0,5 |
Стаття у виданнях організації |
1 |
0,2 |
0,2 |
К2.3
= 1
5.15 Розрахунок інтегрального показника
Таблиця 5.11
№
з/с
|
Найменування |
Позначення |
Значення
К1j
|
Значення
Y1j
|
Сума |
Показники навчальної ефективності |
1 |
Показник рівня відповідності НДР |
К1.1
|
1,0 |
0,15 |
0,15 |
2 |
Показник ступеня участі викладачів в НДР |
К1.2
|
1,0 |
0,1 |
0,1 |
3. |
Участь студентів в НДР |
К1.3
|
1,0 |
0,15 |
0,15 |
4. |
Використання результатів НДР у курсових і дипломних проектах |
К1.4
|
4,4 |
0,1 |
0,44 |
Всього |
0,84 |
Показники наукової ефективності |
1. |
Важливість НДР |
К2.1
|
1 |
0,2 |
0,2 |
2. |
Новизна НДР |
К2.2
|
1 |
0,15 |
0,15 |
3. |
Публікації загальнонаукового значення |
К2.3
|
1 |
0,25 |
0,25 |
Всього |
0,6 |
В моїй роботі отримані такі значення коефіцієнтів: К1
= 0,84; К2
= 0,6; що свідчить про достатній рівень даної роботи.
5.16 Мережні методи планування і керування
При плануванні і проведенні науково-дослідних робіт доцільно використовувати мережні методи планування [21].
Планування припускає побудову мережної моделі – комплексу взаємозалежних робіт, що визначає послідовність і терміни виконання окремих робіт для того, щоб весь комплекс робіт був виконаний з мінімальними витратами.
Етапи планування мережної моделі містить у собі наступні операції:
1) виявлення й опис усіх робіт, необхідних для виконання дипломної роботи;
2) установлення взаємозв’язку і послідовності виконання робіт;
3) індексація робіт;
4) визначення тривалості кожної роботи.
Отримані дані, що є вхідними параметрами мережного графіка, наведені у табл. 5.12.
Мережний графік, побудований на основі вхідних характеристик мовою робіт, наведений на рис. 5.1
5.17 Мережне планування. Розрахунок параметрів мережного графіку
До розрахункових параметрів мережного графіка відносяться:
1) тривалість критичного шляху;
2) ранній початок j-тої роботи;
3) раннє закінчення j-тої роботи;
4) пізній початок j-тої роботи;
5) пізнє закінчення j-тої роботи;
6) повний резерв мережного графіка;
7) вільний резерв робіт.
Критичний шлях Ткр
. дорівнює сумі робіт з максимальною тривалістю від початку науково-дослідної роботи до її закінчення.
Ткр
= 121 дн.
Ранній початок j-тої роботи визначається за формулою (5.25):
Рj
п
= max·(Рi
п
+ di
), |
(5.25) |
де і – індекс попередньої роботи;
j – індекс наступної роботи;
Рі
п
– ранній початок попередньої роботи;
dі
– тривалість попередньої роботи.
Раннє закінчення j-тої роботи визначається за формулою (5.26):
Рj
з
= Рj
п
+ dj
. |
(5.26) |
Пізній початок j-тої роботи визначається за формулою (5.27):
П j
п
= Ткр
– Рj
з
, |
(5.27) |
де Ткр
– тривалість критичного шляху;
Рj
з
– раннє закінчення j-тої роботи у зворотному порядку, для його визначення використовують регресивний графік.
Пізнє закінчення j-тої роботи визначається за формулою (5.28):
П j
з
=П j
п
+ dj
, |
(5.28) |
Повний резерв мережного графіку – це резерви часу робіт, що не лежать на критичному шляху і отже, мають раннє і пізніше початок. Повний резерв j-тої роботи визначається за формулою (5.29):
Ri
п
= Пi
п
– Рi
з
. |
(5.29) |
Вільний резерв мережного графіку – це резерв часу робіт, що можуть бути закінчені за раннім терміном, а наступна за ним робота може бути почата за раннім терміном. Вільний резерв j-тої роботи визначається за формулою (5.30):
Рi
в
= Рi
п
– (Рi
з
+ ti
). |
(5.30) |
Результати розрахунку параметрів мережного графіку зведені в табл. 5.12.
6. Охорона праці і навколишнього середовища
6.1 Загальні питання охорони праці і навколишнього середовища
Розглядаючи питання охорони праці, треба мати на увазі всі моменти процесу праці і його стадії, тобто зародження наукового задуму, дослідницько-експериментальної роботи, проектування, виготовлення, реконструкція, експлуатація. Такий підхід до охорони праці забезпечує безпеку виробничого процесу, як при створенні продукції, так і при подальшому її використанні.
Щоб забезпечити безпеку роботи, збереження здоров’я і працездатності людини необхідно керуватися спеціально розробленими нормами і актами соціально-економічних, організаційних і гігієнічних заходів. Технічний процес металургії змінює умови, характер і зміст праці. Спорудження нових цехів, агрегатів і устаткування великої потужності, перехід на інтенсивні методи ведення технологічних процесів ускладнює взаємовідносини в системі «людина – машина», виникає ряд задач, пов’язаних із забезпеченням здоров’я і безпечних умов праці.
Основною задачею охорони праці є зменшення вірогідності захворювань або ураження робітників з одночасним забезпеченням комфорту при максимальній продуктивності праці. Охорона праці базується на принципах пріоритету життя і здоров’я працівників відповідно до результатів виробничої діяльності на підприємстві, тому одним з особливо важливих заходів є розробка нових методів і засобів боротьби з небезпечними і шкідливими чинниками, такими як шум, висока напруга, електричний струм, вібрація, шкідливі речовини.
Охорона праці встановлена і регламентується Конституцією України (28.06.96), Кодексом законів про працю України (1991), законом України «Про охорону праці» (21.11.2002) [20].
Захист навколишнього середовища в наш час розглядають як комплекс заходів, які здатні забезпечити єдність екологічної політики – економічного і соціального розвитку народного господарства зокрема. Охорона навколишнього середовища – це комплекс заходів, які націлені на раціональну взаємодію між діяльністю людини і охороною природи, забезпечуючи збереження і відновлення природних ресурсів, попереджуючих прямий і непрямий вплив результатів діяльності людини на природу.
На Україні прийнятий ряд законів про охорону навколишнього середовища, [21] сформована система по захисту природи і раціональному використанню природних ресурсів, що передбачає систему стандартів охорони праці.
Темою дипломної науково-дослідницької роботи є «Друга фаза композитів на основі міді, що отримані методом осадження у вакуумі».Дана робота проведена в металографічній лабораторії кафедри «Металознавство і термічна обробка металів» НТУ «ХПІ».
При виконанні науково-дослідницької роботи застосовувалось таке обладнання: мікротвердомір ПМТ-3, прилад для стоншення зразків ПТФ-2, мікроскоп електронний, мікроскоп МІМ-7.
Питання охорони праці і навколишнього середовища розглянуті для забезпечення здорових і безпечних умов праці дослідника на робочому місті.
6.2 Виробнича санітарія
З урахуванням вимог ГОСТ 12.0.003–74* [22] в приміщенні лабораторії при виконанні науково-дослідницької роботи можливі небезпечні і шкідливі виробничі чинники, наведені в таблиці 6.1.
Таблиця 6.1 –
Перелік небезпечних і шкідливих виробничих чинників в приміщенні лабораторії
Небезпечні і
шкідливі виробничі чинники
|
Джерела
виникнення
|
Нормований параметр |
Характер дії |
Заходи для забезпечення нормованих параметрів не вище допустимих |
1. Електричний струм |
Лабораторне устаткування що живиться від мережі |
U, В; I, А |
Електричні травми, електричні удари |
Конструктивні: ізоляція, огорожа; Схемно-конструктивні:
занулення, захисне заземлення
|
2.Неякісне освітлення в лабораторії |
Прибори для освітлення |
Еmin
, лк;
КПО, %
|
Органи зору |
Застосуван-ня більш раціональ-них систем освітлення |
3.Шкідливі речовини |
Протравлен-ня шліфів, шліфувальні станки |
ГДК, мг/м³ |
Захворювання легень, опік |
Приточно–витяжна вентиляція, герметизація |
При виконанні науково-дослідницької роботи не вимагається постійної фізичної напруги або підняття і перенесення важких речей, тому робота дослідника відноситься до легких фізичних робіт категорії 1б. Енерговитрати організму (витрати енергії при виконанні роботи) – (121 – 150 ккал/г): (140–174 Вт).
Згідно вимогам ГОСТ 12.1.005–88 [23] в приміщенні металографічної лабораторії передбачені допустимі параметри мікроклімату, наведені в таблиці 6.2. з урахуванням періоду року і категорії робіт по фізичній тяжкості.
Дані метеорологічні умови досягнуті за допомогою природної і штучної вентиляції (приточно-витяжна), в холодний період року опалювання, згідно СНиП 2.04.05–91 [24] опалювання здійснено від тепломережі.
Таблиця 6.2 – Допустимі норми температури, відносної вологості, швидкості руху повітря у виробничому приміщенні лабораторії
Період року |
Категорії робіт |
Температура, ºC |
Відносна вологість, %,
не більше
|
Швидкість руху повітря, м/с,
не більше
|
Холодний |
Легка – 1б |
20–24 |
75 |
0,2 |
Теплий |
Легка – 1б |
21–28 |
60 (при 27 ºC) |
0,1 – 0,3 |
В процесі експерименту можливе виділення шкідливих речовин у вигляді парів і аерозолів, що утворюються при отриманні і дослідженні зразків. Перелік шкідливих речовин і їх гранично-допустимі концентрації (ГДК) згідно вимогам ГОСТ 12.1.005–88 [23] наведені в таблиці 6.3.
Таблиця 6.3 – ГДК шкідливих речовин в повітрі робочої зони лабораторії
Шкідливі речовини |
ГДК, мг/м³ |
Клас безпеки |
Ортофосфорна кислота |
5 |
ІІІ |
Забезпечення ГДК в приміщенні лабораторії досягнуто використанням приточно-витяжної вентиляції згідно з СНиП 2.04.05–91 [24].
В лабораторії передбачено природне і штучне освітлення. Природне освітлення приміщення – бічне одностороннє. Якнайменший розмір об’єкту розрізнення від 0,5 до 1 мм, тому зорові роботи, що виконуються на робочому місці відносяться до IV розряду, під розряду «в» згідно СНиП II-4–79 [25].
Природне освітлення характеризується коефіцієнтом природної освітленості – КПО (еІІІ
), %.Нормативне значення КПО для IV – «в» розряду зорових робіт згідно СНиП II-4–79 [25] складає е
III
= 1,5%. Оскільки дипломна робота виконана на Україні (м. Харків – IV-й світловий пояс), тому що нормативне значення КПО визначено по формулі:
e
IV
= е
III
·m
·c
(6.1)
де еIII
– значення КПО світлового клімату для третього поясу, дорівнює 1,5%;
m
– коефіцієнт світлового клімату, дорівнює 0,9;
c
– коефіцієнт сонячності клімату, дорівнює 0,85;
е
IV
= 1,5·0,9·0,85 = 1,15%
Реалізація КПО в лабораторії досягнута шляхом розрахунку площі світлових отворів у стадії проектування будівлі в цілому.
Штучне освітлення в приміщенні – комбіноване і загальне рівномірне. Нормованою величиною штучного освітлення є мінімальне значення освітленості (Еmin
, лк). Згідно СНиП II-4–79 [19] для IV – «в» розряду зорових робіт середній точності, контраст об’єкту розрізнення з фоном – середній, характеристика фону – середній; нормативне значення мінімальної освітленості складає 200 лк при загальному і 400 лк при комбінованому освітленні.
Реалізація мінімальної освітленості в лабораторії досягнута використанням в якості джерела світла люмінесцентних ламп ЛБ80–4 та володіючих великою світловіддачею і спектром світла, близьким до природного освітлення.
Розрахунок штучного освітлення у приміщенні лабораторії.
Штучне освітлення в лабораторії–загальне рівномірне. Для даного розряду зорових робіт, виконуваних в лабораторії відповідає контраст об'єкта розрізнення–середній, фон–середній. Нормованою величиною штучного освітлення є мінімальна освітленість, що для проектованої ділянки становить Е
min
=200 лк [25].
Вибір джерел світла залежить від наступних факторів: будівельні параметри, архітектурно-планувальні рішення, стан повітря, дизайн.
Лампи накалювання – малоекономічні, мають світловіддачу до 26 лм / Вт і термін служби до 100 годин, але при роботі спотворюють спектр, нагріваються.
Люмінесцентні лампи мають світловіддачу 75 лм / Вт і термін служби 1000 г. також характеризуються гарною передачею кольору, але разом з тим вони дорогі, вимагають спеціального обслуговування, мають складну систему пуску, шумлять і іноді мерехтять. Важко утилізуються.
У приміщеннях з висотою стелі 7 м і вище застосовуються лампи типу ДРЛ. Тому що вони могутніші й мають світловіддачу до 90 лм / Вт.
Висота лабораторії 4 м тому вибираємо люмінесцентні лампи типу ЛБ80–4.
Фл
= 4960 лм
Робимо розрахунок числа світильників у приміщенні лабораторії із формулою 5.2
, |
(5.2) |
де Еmin
– задана мінімальна (нормована) освітленість, лк. Еmin
= 200 лк;
k – коефіцієнт запасу, приймаємо 1,6, тому що запиленість значно нижче 1 мг/м3,
відсутність пар кислот і лугів;
S – освітлювана площа, м2
, S=8·4=32 м2
;
z – коефіцієнт мінімальної освітленості, характеризує нерівноваженість освітленості і є функцією багатьох змінних, але найбільшою мірою залежить від відношення відстані між світильниками до розрахункової висоти (L/h),
Для люмінесцентних ламп приймаємо z = 1,1;
n – число ламп у світильнику, n = 2 шт.
η – коефіцієнт використання світлового потоку в частках одиниці.
Для визначення η знаходимо індекс приміщення й попереднього коефіцієнта відбиття поверхні приміщення: стелі ρп
= 70%, стін ρс
= 50%, підлоги ρр
= 30% для даного виду приміщення.
Індекс приміщення
де A, B, h – довжина, ширина, і розрахункова висота (висота підвісу світильника над робочою поверхнею) приміщення, м.
де H – геометрична висота приміщення, м;
hсв
– звис світильника (довжина штанги або шнура, на яких він висить), м; hc
в
=0,2…0,8 м, прийнято hсв
=0,4;
hрп
– висота робочої поверхні від рівня підлоги, м; hрп
=0,8…1,0 м, прийнято hрп
=0,8 м.
h=4–0,4–0,8=2,8,
i=8·4/2,8 (8+4)=0,95
Тоді коефіцієнт використання світлового потоку для люмінесцентних ламп беремо 37%
Визначаємо кількість світильників за формулою 5.5
, |
(5.5) |
N=200·1,6·32·1,1/ 4960·2·0,37=3,1 св.
Прийнято 3 світильника.
Розрахунок штучного освітлення призведений методом коефіцієнта використання світлового потоку. Визначена кількість світильників та потужність ламп, що необхідні для забезпечення нормованої освітленості у приміщенні лабораторії.
6.3 Міри безпеки
Все технологічне устаткування, що використовується в ході проведення дипломної науково-дослідницької роботи, живиться від електричної мережі. Особливу увагу приділено питанням електробезпеки.
Приміщення лабораторії по небезпеці ураження людей електричним струмом відповідно до вимог ПУЭ-87 [26], відноситься до класу приміщень з підвищеною небезпекою, оскільки в приміщенні є можливість одночасного дотику людини до металевих будівель (труби водопроводу), що мають з’єднання з землею з одного боку, і металевому корпусу електроустаткування – з іншого.
Устаткування застосоване для досліджень, має живлення низько- і високовольтне. Клас встановленого устаткування в лабораторії засобом захисту від ураження електричним струмом згідно ГОСТ 12.2.007–75* [27]:
1 – для низьковольтної сторони і 01 – для високовольтної.
Технічне устаткування живиться від трифазної чотирьох дротяної мережі змінного струму з напругою 380/220 В з промисловою частотою 50 Гц з глухо заземленою нейтраллю. Таким чином, низьковольтна частина установки занулена, а високовольтна заземлена по ГОСТ 12.1.030–81* [28].
Конструктивними заходами електробезпеки служить ізоляція токоведучих частин і використання кожухів на електроустаткуванні для захисту від випадкового дотику до токоведучих елементів установок, застосування закритих конструкцій, вимикачів і перемикачів, рубильників з приводом важеля згідно ГОСТ 12.1.019–79* [29].
6.4 Пожежна безпека
Причини пожеж технічного характеру, які можуть виникнути в приміщенні термічної лабораторії:
· спалах легкозаймистих і горючих рідин;
· порушення технологічного процесу;
· несправність електроустаткування (коротке замикання, перевантаження і великі перехідні опори);
· недотримання графіка планового ремонту;
· ремонт устаткування на ходу.
Приміщення лабораторії, де проведена дипломна науково-дослідницька робота, згідно НАПБ Б.07.005–86 (ОНТП 24–86) [30] по пожежній і вибухопожежній небезпеці відноситься до категорії В-пожежонебезпечна, оскільки в лабораторії знаходяться тверді речовини і матеріали, що згорають. Необхідний ступінь вогнестійкості будівлі, в якій знаходиться приміщення термічної лабораторії ІІ, згідно ДНБ В.1.1–7–2002 [31].
Відповідно до вимог ГОСТ 12.1.004–91* [32] пожежна безпека в лабораторії забезпечена системою запобігання пожежі (СЗП), системою протипожежного захисту (СПЗ) і організаційними заходами. В якості СЗП передбачено:
– робота на справних установках;
– можливе вживання негорючих матеріалів, речовин;
– вживання захисних кожухів для запобігання займанняелектроустаткування.
Джерела забруднення води, повітря, землі відсутні, тому що названі речовини не перевищують нормативних значень.
Дотримання вищевказаних нормативних параметрів небезпечних і шкідливих виробничих факторів дозволяє забезпечити безпечні умови роботи дослідника на робочому місці.
6.5 Захист навколишнього середовища
При проведенні дипломної науково-дослідницької роботи шкідливої дії на оточуюче середовище не виявилено, оскільки в процесі експериментів не відбувався викид шкідливих речовин в атмосферу ГОСТ 17.2.3.02 – 78 [33]. Енергетичного забруднення навколишнього середовища не відбувалося.
Відповідно до вимог ГОСТ 17.2.3.02–78 [33] вода, що використовується для охолодження, прямує в каналізацію, а звідти – на міські очисні споруди. Забруднення води в процесі експерименту не відбувалося [34].
Висновки
1. Виявлено, що у вихідному конденсованому стані структура фольг Cu-Mo, Cu-W, Cu-Та, Cu-Co, Cu-Fe є двофазною.
2. Метод спільного осадження у вакуумі нерозчинних компонентів, що випарені з різних джерел, дозволяє отримати гетерофазну нанодисперсну структуру. Застосування у якості другого компоненту Ta, Mo, W, які не розчиняються у міді, дозволяє збільшити дисперсність виділень.
3. Встановлено, що деградація структури у вивчених системах відбувається у певній послідовності, але швидкість процесу залежить від розчинності другого компоненту в матриці та від його атомного радіусу.
4. Зміни у зернистій структурі матриці корелюють із зміною морфології часток, хоча значно запізнюються у відношенні до них. Найбільшою структурною стабільністю володіють композити на основі системи Cu-Ta.
Список джерел інформації
1. Бочвар А.А. Металловедение. Изд. 5-е М., Металлургиздат, 1956 г.
2. Бернштейн М.Л. Термомеханическая обработка металлов и сплавов. М., «Металлургия», 1968. Т. I.
3. Электронно-микроскопические исследования структуры жаропрочных сплавов и сталей. Сб. сталей под ред. С.Т. Кишкина. М., «Металлургия», 1969
4. Захаров М.В., Захаров А.М. Жаропрочные сплавы. М., «Металлургия», 1972.
5. Котрелл А.Х. Дислокации и пластическое течение в кристаллах. Пер. с англ. М.: Металлургиздат, 1958.
6. Мартин Дж., Доэрти Р. Стабильность микроструктуры металлических систем. Англия, 1976. Пер. с англ. − М.: Атомиздат, 1978.
7. Микромеханизмы дисперсионного твердения сплавов. Дж. Мартин: Пер. с англ. – М.: Металлургия, 1983.
8. Дисперсноупрочненные материалы. Портной К.И., Бабич Б.Н. Серия «Успехи современного металловедения». М., Металлургия, 1974
9. Горелик С.С. Рекристаллизация металлов и сплавов, М.: Металлургия, 1978
10.Уманский Я.С., Скаков Ю.А., Иванов А.Н., Расторгуев Л.Н. Кристалло-
графия, рентгенография и электронная микроскопия. – М: Металлургия, 1982.
11. Пилянкевич А.Н. Практика электронной микроскопии.-М.: Машгиз,1961.
12. Фрактография и атлас фрактограмм. Справочник/ Под ред. Дж. Феллоуза.-М.: Металлургия, 1982.
13. Практические методы в электронной микроскопии/ Под ред. ОдриМ. Глоэра. – Л.: Машиностроение, 1980.
14. Томас Г., Гориндж М.Дж. Просвечивающая электронная микроскопия.-М.: Наука, 1983.
15. Металловедение и термическая обработка стали. В 3-х т./ Под ред. Бернштейна М.Л., Рахштадта А.Г. – Т.1. Методы испытаний и исследования. – В 2-х кн.Кн. 1. – М.: Металлургия, 1991.
16. Экономика предприятия II, под ред. Горфинкеля В., Купринова Е.М. – Юнити, 1996.
17. Организация и планирование производственных предприятий. Под ред. Войталовского В.М. и др. СПБ ХЭФ, 1996.
18. Яковлев А.И. Социально – экономическая эффективность нововведений в условиях рынка, Киев, Украина.1995.
19. Покропивний С.Ф. и др. Экономика предприятия, учебник в двух томах, Киев, «Хвиле – Прес», 1995.
20. Збірник законів«Охорона праці». Київ: 2003. -120 с.
21. Никитин Д.П., Новиков Ю.В. Окружающая среда и человек: учеб. пособие для студентов вузов. – М.: Высш.шк., 1980. –424 с.
22. ГОСТ 12.0.003–74*. ССБТ. Опасные и вредные производственные факторы. Классификация – Введ. 01.01.76. Изменен 1978.
23. ГОСТ 12.1.005–88. ССБТ. Общие санитарно – гигиенические требования к воздуху рабочей зоны. – Введ. 01.01.89.
24. СНиП 2.04.05–91. Строительные нормы и правила. Отопление. Вентиляция и кондиционирование воздуха. – М.:Стройиздат, 1987. – 110 с.
25. СНиП II-4–79. Строительные нормы и правила. Естественное и искусственное освещение. Нормы проектирования. – М.: Стройиздат, 1980. – 48 с
26. ПУЭ-87. Правила устройства электроустановок. – М.: Энергоатомиздат, 1988. – 648 с.
27. ГОСТ 12.2.007–75*. ССБТ. Изделия электротехнические. Общие требования безопасности. – Введ. 01.01.78. Изменен в 1988 г.
28. ГОСТ 12.1.030–81*. ССБТ. Электробезопасность. Защитное заземление. Зануление. – Введ. 01.07.82. Изменен в 1987 г.
29. ГОСТ 12.1.019–79*. ССБТ. Электробезопасность. Общие требования и номенклатура видов защиты. – Введ. 01.07.80. Изменен в 1986.
30. НАПБ Б.07.005–86 (ОНТП 24–86). Нормативний акт пожежної небезпеки. Визначення категорій будівель і споруд по вибухопожежної і пожежній безпеці. – М.: 1991.
31. ДНБ В.1.1–7–2002. Державні будівельні норми. Захист від пожежі. Пожежна безпека об’єктів будівництва. – К.: 2003. – 41 с.
32. ГОСТ 12.1.004–91*. ССБТ. Пожарная безопасность. Общие требования. – Введ. 01.07.92.
33. ГОСТ 17.2.3.02–78. ССОП. Охрана природы. Атмосфера. Правила установления допустимых выбросов вредных веществ промышленных предприятий. – Введ. 01.01.80.
34. Правила охраны поверхностных вод от загрязнения сточными водами. – М: Изд-во Минздрава СССР, 1975.
35. Закон Украины «О гражданской обороне Украины». – Введ. 01.04.91.
36. Атаманюк В.Г. и др. Гражданская оборона. – М.: Высшая школа, 1986.
37. Депутат О.П., Ковалєнко І. В., Мужик І. С. Цивільна оборона. Навчальний посібник / За ред. полковника Франчука В.С. – Львів, Афіша, 2000 – 336 с.
|