Реферат
амоній
сульфат абсорбер
Пояснювальна записка до дипломного проекту:137 с., 9рис.,21 табл., 37 літературних джерел.
Об’єкт дослідження – відділення уловлювання аміаку.
Мета роботи – проектреконструкції сульфатно-піридинового відділення з метою впровадження безсатураторного способу уловлювання амоніаку, спеціальна частина– абсорбер для уловлювання аміаку.
У загальній частині проекту вибрано та обґрунтованонеобхідність реконструкції відділення,описано асортимент продукції та вимоги до неї, подано характеристику сировинних матеріалів, описано фізико-хімічні основи уловлюванняаміаку.
У технологічній частиніподано структурно-технологічну схему виробництва та описано технологічний процес, розраховано матеріальнийта тепловийбалансивиробництва, наведено розрахунок основного технологічного обладнання.
У спеціальній частині описана конструкція та принцип діїосновних апаратів, якіпропонуються до впровадження вреконструюємому відділенні; зроблено їхконструктивний розрахунок.
У проекті розроблено заходи з охорони праці та з автоматизації виробничих процесів.
В організаційно-економічній частині проекту розраховано основні техніко-економічні показники реконструюємого відділення.
РЕКОНСТРУКЦІЯ, КОКСОВИЙ ГАЗ, АМІАК,СУЛЬФАТ АМОНІЮ, КРИСТАЛИ, СХЕМА ТЕХНОЛОГІЧНА, АБСОРБЕР, ВИПАРНИК
Зміст
Вступ
1. Аналітичний огляд методів виробництва
1.1 Сатураторний метод
1.2 Безсатураторний метод
1.3 Уловлювання аміаку водою
1.4 Отримання безводного аміаку
1.5 Очищення коксового газу круговим фосфатним способом зі знищенням аміаку
2. Фізико-хімічні основи виробництва
2.1 Заходи проти злежування
3. Характеристика сировини, напівпродуктів і готової продукції
3.1 Характеристика сировини
3.2 Характеристика продуктів
4. Вибір, обґрунтування і опис технологічної схеми
5.Матеріальний та тепловий баланси виробництва
5.1.1 Кількість розчину, що перетікає з абсорберу другого ступеня в абсорбер першого ступеня
5.1.2 Кількість розчину, що виводиться з першого ступеня абсорберу у випарник
5.2 Матеріальний та тепловий баланси абсорбера першого ступеня
5.3 Матеріальний та тепловий баланси збірника першого ступеня
5.3.1 Матеріальний розрахунок
5.3.2 Тепловий баланс збірника першого ступеня
5.4 Матеріальний та тепловий баланси абсорберу другого ступеня
5.5 Матеріальний та тепловий баланси збірника другого ступеня
5.5.1 Матеріальний розрахунок
5.5.2 Тепловий баланс збірника другого ступеня
5.6 Розрахунок випарника
5.6.1 Матеріальний розрахунок
5.6.2 Тепловий розрахунок випарника
6.Технологічні розрахунки
6.1 Визначення розмірів абсорберів першого та другого ступенів
6.2 Визначення поверхні теплопередачі випарника
7. Механічні розрахунки
7.1 Товщина обичайки
7.2 Днище
7.3 Штуцери
7.4 Розрахунок опори
Список літератури
Вступ
Аміак утворюється в процесі коксування з азоту і водню кам'яного вугілля. Велика частка азоту вугілля (до 60%) залишається в коксі у вигляді термічно стійких азотистих поєднань, а остання частка видаляється з вугілля разом з леткими продуктами коксування - газом, смолою і надсмольною водою.
Утворення аміаку при коксуванні вугілля починається при температурі біля 600°С, а максимальний вихід його досягається при температурах 800-900°С.
По даним [1] вихід аміаку від сухої шихти для донецького вугілля варіюється в межах 0,25-0,30%, а для кузнецьких може досягати 0,45 %.
Вміст аміаку в газі для різного вугілля [1] може варіюватися в межах 5,5 - 12,5 г/м3
(0 °С).
Вилучення аміаку з коксового газу - обов'язкова технологічна операція при підготовці газу до його подальшого використання. Норми допустимого вмісту аміаку в газі: не більше 0,03 г/м3
[2], тобто повнота витягання аміаку з газу повинна складати 99,7 – 99,8 % мас. Такі серйозні вимоги визначаються чисто технологічними причинами [3]:
- необхідність видалення компонента, який призводить до корозії газопроводів та обладнання;
- для попередження виникнення відкладань в газопровідних комунікаціях і регулючих пристроях коксових батарей;
- для нормальної експлуатації бензольно-скруберних відділень і цехів сіркоочистки;
- аміак з ціаністим воднем, що знаходиться в газі, різко посилює корозію устаткування, утворюючи добре розчинне комплексне з'єднання –
гексацианферрат – (NH4
)4
[FeCN6
];
- аміак, що залишається в газі, при спалюванні перетворюється переважно на токсичні і корозійно-небезпечні оксиди азоту;
- аміак стабілізує емульсії води і олії при уловлюванні бензольних вуглеводнів.
У результаті уловлювання аміаку сірчаною кислотою утворюється сульфат амонію.
Сульфат амонію виробляється на коксохімічних заводах у великих кількостях. На 1 т сухої шихти виробництво сульфату амонію (сухого) складає 11,0-11,5 кг.
Сульфат амонію являється дуже ефективним азотним добривом. Особливістю цього вигляду добрива є ті, що він дозволяє підпитувати ґрунт не лише азотом, але і сіркою. Остання входить до складу білків і амінокислот рослин і тому разом з азотом є одним з важливих елементів живлення сільськогосподарських культур. По мірі важливості для рослин сірку можна поставити на третє місце після азоту і фосфору. Продукт володіє важливою для життєдіяльності рослин властивістю. Він переводить фосфор, що знаходиться в ґрунті з нерозчинної форми в розчинну і тим самим підсилює процес поглинання рослиною цієї речовини. Це дозволяє понизити кількість фосфорних добрив, що вносяться до ґрунту.
Не дивлячись на те, що продукт найширше використовується в сільському господарстві, він також застосовується і в інших галузях. Наприклад, у біохімії переосадження сульфатом амонію є загальним методом очищення білків. Використовується в технології хлорування води з амонізацією, вводиться в оброблювану воду за декілька секунд до хлору, з хлором утворює хлораміни - зв'язуючи вільний хлор, завдяки чому значно скорочується утворення хлорорганіки шкідливої для організму людини, скорочується витрата хлору, зменшується корозія трубопроводів. В харчовій промисловості його використовують як харчову добавку Е517 (речовини проти злежування). В промисловості сульфат амонію використовують як сировину при виробництві акумуляторів, у виробництві віскозного волокна і як основу при виробництві вогнезахисних просочень для дерева.
Так як сатураторний метод не дає можливості регулювати розмір отримуваних кристалів, то пропонується для впровадження безсатураторний метод отримання сульфату амонію на ПАТ ЕВРАЗ «Днепродзержинский КХЗ», у якому на стадії абсорбції отримують ненасичений розчин солі, що піддається вакууму, - випарці в умовах інтенсивної циркуляції , що забезпечує незначне пересичення і керований ріст кристалів.[3]
1 Аналітичний огляд методів виробництва
Залежно від схеми охолодження прямого коксового газу і уловлювання з нього аміаку розрізняють три способи отримання сульфату амонію : непрямий, прямий та напівпрямий.[4]
При непрямому способі частина аміаку (20-30% від загальних ресурсів) уловлюєтьсяз коксового газу конденсатом, що утворюється при охолодженні газу в первинних холодильниках до 25-35°С, а інша частина (80-70%) оборотною водою при промиванні газу в аміачних скруберах. Надсмольна вода(газовий конденсат) і слабка аміачна вода із скруберів переробляються потім в аміачних колонах з отриманням парогазової суміші, що складається з пари води, аміаку, вуглекислоти, сірководню, ціаністого водню та інших компонентів. Ця суміш спрямовується в сатуратор, де аміак зв'язується з сірчаною кислотою з утворенням насиченого розчину сульфату амонію і кристалів солі, які виводяться з дна апарату з частиною розчину на центрифугу, а після промивання і сушки передаються на склад.
Непрямий спосіб отримання сульфату амонію має велику гнучкість процесу, що дозволяє виробляти залежно від умов ринку, що міняються, сульфат амонію або концентровану аміачну воду, або одночасно обидва продукти в одному цеху. Важливою перевагою цього способу є також виробнича надійність оскільки різні відділення цеху слабо пов'язані між собою і тому виробничі порушення в аміачному або сульфатному відділеннях можуть бути усунені без зупинки інших відділень при подачі отримуваної в скруберах аміачної води на склад. Крім того непрямий спосіб дозволяє виробляти сірчану кислоту та піридинові основи з парогазової суміші, що виходить з сатуратора за порівняно простою технологією.
Разом з цими перевагами непрямий спосіб має ряд серйозних недоліків:
- великі капіталовкладення;
- значні експлуатаційні витрати, пов'язані з переробкою великого об'єму аміачної води;
- велика кількість стічних вод (близько 250 м3
на 1000 т коксуємого вугілля);
- значні втрати аміаку зі зворотним газом.
Із-за цих недоліків непрямий спосіб виробництва сульфату амонію нині не знаходить застосування. Проте у поєднанні з аміачним очищенням коксового газу від сірководню він може виявитися перспективним.
Прямий метод полягає в тому, що весь аміак, що утворюється при коксуванні, уловлюється з коксового газу сірчаною кислотою до охолодження в первинних холодильниках. З газозбірника гарячий коксовий газ поступає в електрофільтр для очищення від туманоподібної смоли, а потім в сатуратор, де аміак зв'язується сірчаною кислотою з утворенням насиченого розчину і кристалів сульфату амонію.
Відмінною особливістю цього методу є те, що при охолодженні коксового газу після сатуратора в первинних холодильниках конденсат (надсмольна вода), що утворюється, не містить аміаку та амонійних солей і тому відпадає необхідність його переробки в аміачній колоні. Відсутність аміачного відділення дозволяє понизити витрату пари, вартість устаткування і займану виробничу площу, а також скоротити до мінімуму об'єм стічних вод (близько 50 м3
на 1000 т коксуємого вугілля).
Проте широкого поширення цей метод не отримав із-за істотних недоліків:
- наявність великого числа апаратів, працюючих під розрідженням, що підвищує вірогідність підсосу повітря і утворення вибухонебезпечної суміші збільшує витрату електроенергії на транспортування газу;
- інтенсивної корозії устаткування, обумовленій наявністю в газі хлористого водню і хлористого амонію;
- труднощів очищення газу від смоли при високій температурі та утворення в сатураторі великої кількості кислої смолки;
- великого об'єму апаратури із-за високої температури і влаговмісту газу;
- неможливості уловлювання в сатураторі легких піридинових основ із-за високої температури розчину і відсутності аміачної пари для його нейтралізації в піридиновій установці.
Найбільше поширення на заводах отримав напівпрямий метод виробництва сульфату амонію, що має переваги, а частково і недоліками непрямого і прямого способів. По цьому методу коксовий газ після газозбірника охолоджується в первинних холодильниках до 25-35°С, внаслідок чого водяні пари конденсуються практично повністю, а газовий конденсат (надсмольна вода), що утворюється розчиняє до 20-30% аміаку, що міститься в прямому газі. Охолоджений газ подається нагнітачами в абсорбер, де інший аміак поглинається сірчаною кислотою з утворенням сульфату амонію.
Отримувані при переробці надмірної надсмольної води аміачні пари подаються частково в абсорбер разом з коксовим газом, а частково в нейтралізатор піридинової установки, де аміак також зв'язується сірчаною кислотою. Таким чином увесь аміак прямого коксового газу зрештою переробляється в сульфат амонію.
Недоліками напівпрямого способу виробництва сульфату амонію є необхідність переробки надмірної надсмольної води в аміачних колонах, що вимагає значної витрати пари і лугу, а також утворення значного об'єму стічних вод що вимагають складного очищення.
Залежно від апаратурного оформлення процесів поглинання аміаку сірчаною кислотою і кристалізації сульфату амонію розрізняють два різновиди напівпрямого способу, що отримав найбільше поширення в промисловості - сатураторний і безсатураторний. Слід відзначити, що в літературі немає єдиного тлумачення цих термінів і вони не відображають особливостей апаратурного оформлення процесів.
По термінології, прийнятій в коксохімічній промисловості, сатураторним називається процес, при якому поглинання аміаку з коксового газу сірчаною кислотою і утворення кристалів сульфату амонію здійснюються в одному апараті барботажного типу що називається сатуратором. При безсатураторному способі поглинання аміаку сірчаною кислотою відбувається у форсуночному скрубері (чи насадному), який може зрошуватися як пересиченим, таким, що містить кристали сульфату амонію розчином, так і ненасиченим розчином. У першому випадку кристалізація сульфату амонію відбувається одночасно з поглинанням аміаку в скрубері, а в другому утворення пересиченого розчину і кристалів сульфату амонію здійснюється при випарюванні розчину в спеціальному апараті - кристалізаторі.
Перевагами безсатураторних процесів є менший гідравлічний опір форсуночних абсорберів і можливість проведення окремих стадій процесу (абсорбція аміаку, кристалізації сульфату амонію та ін.) за найбільш сприятливих умов.
1.1 Сатураторний метод
Технологічна схема отримання сульфату амонію по сатураторному методу[5]зображена на Рисунку 1.1.
Коксовий газ, охолоджений в первинних газових холодильниках і очищений від туманоподібної смоли в електрофільтрах подається нагнітачем в паровий підігрівач 1 сульфатного відділення. В підігрівачі газ підігрівається до 65-70°С та поступає в сатуратор 2 по центральній газопідводящій трубі, яка закінчується газорозподільним зонтом, який знаходиться в матковому розчині ванні сатуратора

1 - паровий підігрівач; 2 - сатуратор; 3 - кислотна ловушка; 4, 10, 12 -насоси; 5 - кристалоприймач; 6 - кастрюля зворотніх токів маткового розчину; 7 -центрифуга; 8 - циркуляційна кастрюля; 9 - збірник маткового розчину; 11 - напірний бак з сірчаною кислотою;13-транспортер; 14-сушка.
Рисунок 1.1 Технологічна схема отримання сульфату амонію по сатураторному методу
Сірчана кислота з концентрацією 92-94% безперервно надходить до сатуратора з напірного бака 11 по спеціальній трубі. Коксовий газ, який пройшов крізь шар маткового розчину і звільнився від аміаку і піридинових основ, крізь газовий патрубок направляється в кислотну ловушку 3, в якій із газу уловлюються краплі маткового розчину.
Після кислотної ловушки коксовий газ направляється в кінцеві газові холодильники для охолодження його до 25-30°С для уловлювання бензольних вуглеводнів в скруберах.
Кристали сульфату амонію разом з деякою кількістю маткового розчину насосом 4 подаються в кристалоприймач 5 для відстоювання кристалів сульфату амонію. Крізь штуцер матковий розчин відстояний від кристалів сульфату амонію безперервно стікає в каструлю зворотніх токів 6 і з неї в сатуратор.
З нижньої частини кристалоприймача 5 суміш кристалів сульфату амонію з матковим розчином самотіком поступає в центрифугу безперервної дії 7, де кристали відділяються від маткового розчину і промиваються горячою водою (78-80°С). Відфугований сульфат амонію з центрифуги подається транспортером 13 на сушку 14, а потім на склад. Розчин після центрифуги крізь каструлю зворотніх токів повертається в сатуратор.
Рівень маткового розчину в сатураторі підтримується постійним за допомогою спеціального бічного штуцера, через який надлишок маткового розчину відводиться в циркуляційну каструлю 8, яка являється одночасно гідравлічним затвором, що робить неможливим вихід газу з сатуратора разом з розчином.
При виникненні в ванні сатуратора надлишку маткового розчину останній з циркуляційної каструлі самотіком перетікає в збірник 9, звідки по потребі насосом 10 повертається в сатуратор.
1.2 Безсатураторний метод
Подальше вдосконалення методів отримання сульфату амонію на коксохімічних заводах привело до появи бессатураторного процесу уловлювання аміаку з коксового газу в насадних або безнасадних (форсуночних) абсорберах.
Безсатураторний процес отримання сульфату амонію може здійснюватися по двох принципово різним схемам: уловлювання аміаку пересиченим розчином, що містить кристали, і ненасиченим розчином з подальшим отриманням в окремому апараті кристалів солі сульфату амонію шляхом упарювання частини розчину[5].
На вітчизняних коксохімічних заводах частіше застосовується друга схема у якій передбачається установка двоступінчатого абсорбера для здійснення роздільного уловлювання з газу аміаку і піридинових основ і кристалізація сульфату амонію, що утворився, в окремому апараті - випарнику (під вакуумом).
Ця схема має ряд переваг: абсорбери зрошуються ненасиченим розчином, що усуває їх засолення; при кристалізації солі в окремому апараті можна отримати кристали практично будь-якого розміру, процес легко керований; процес кристалізації можна здійснювати періодично і насичений розчин може складуватися. При цьому не порушується робота уловлюючої установки.
Здійснення процесу уловлювання аміаку, піридинових основ і кристалізація солі сульфату амонію в окремих апаратах, дозволяють підтримувати для кожного з них найбільш доцільний режим. Це забезпечує достатню повноту уловлювання аміаку піридинових основ з газу і отримання великокристалічної солі.
Таким чином, отримання сульфату амонію по безсатураторному методу здійснюється в двох установках - абсорбційній і випарно-кристалізаційній.
Розглянемо технологічну схему отримання сульфату амонію без сатураторним методом[6]. (рисунок 1.2).
Коксовий газ, що містить аміак і піридинові основи, поступає в абсорбер 1, що є полим апаратом із форсуночним зрошенням, що складається з двох ступенів, - нижнього та верхнього, розділених між собою горизонтальною тарілкою.
У нижньому ступені 2 абсорберу циркулює розчин, що містить близько 40% сульфату амонію і 1-1,5% вільної сірчаної кислоти. У верхньому ступені 3 абсорберу циркулює розчин що містить від 20 до 30% сульфату амонію і 10-12% вільної сірчаної кислоти.
Після проходження нижнього і верхнього ступенів абсорбера коксовий газ проходить кислотну ловушку 4, що призначена для видалення бризок маткового розчину.
Кожен ступінь абсорбера має свою самостійну систему зрошування.

1-абсорбер;2-нижній ступень;3-верхній ступень;4-кислотна ловушка;
5,7,12-збірники;6,8,13,15,25-насоси;9,10-напірні баки;11-смоловідділювач;14-випарник;16-ценрифуга;17,18-ежектори;19-циркуляуційна труба;20-сушка; 21, 22-конденсатори; 23-збірник чистого конденсату; 24-збірник брудного конденсату.
Рисунок 1.2 Схема безсатураторного методу отримання сульфату амонію.
Так, з нижнього ступеня абсорбера розчин через гідрозатвір поступає в циркуляційний збірник слабкого розчину 5, звідки насосом 6 подається на зрошування цього ж ступеня. Розчин же з верхнього ступеня абсорбера поступає в циркуляційний збірник міцного розчину 7, звідки насосом 8 подається на зрошування верхнього ступеня абсорбера.
Подача розчину як в нижній, так і у верхній ступені абсорбера робиться на двох рівнях.
Сірчана кислота і вода, необхідні для поповнення циркулюючих розчинів, подаються з напірних баків 9 і 10 в циркуляційні збірники першого і другого ступенів 5 і 7.
Частина маткового розчину з нижнього ступеня абсорбера безперервно відводиться в смоловідділювач 11, а. звідти у збірник 12, з якого насосом 13 подається вниз конічної частини трубчастого випарника 14.
У смоловідділювачі виділяється велика частина смоли яка випливає на поверхню розчину і безперервно видаляється скребковим транспортером. Це забезпечує мінімальне попадання смолянистих речовин у збірник 12 і, отже, запобігає забрудненню сульфату амонію.
У випарнику 14 відбувається випарювання води з розчину і кристалізація сульфату амонію. Завдяки вакууму (тиск дорівнює 75 мм рт. ст.), що створюється двоступінчатим паровим ежектором, температура кипіння розчину дорівнює 50-60° С. Випарник обігрівається парою низького тиску, близько 2 кгс/см2
. У випарнику є внутрішня циркуляційна труба 19 більшого діаметру, ніж трубки, внаслідок чого створюється термічна циркуляція розчину усередині апарату, яка сприяє росту кристалів.
Пульпа, що утворюється в нижній частині випарника, є сумішшю кристалів сульфату амонію (приблизно 50-60% від маси пульпи) і насиченого маткового розчину, відкачується відцентровим насосом 15 в центрифугу безперервної дії 16. Матковий розчин після центрифуги повертається в циркуляційний збірник 5 нижнього ступеня абсорбера. Туди ж поступає промивна вода з центрифуги.
Вологий сульфат амонію з центрифуги поступає в сушарну установку 20 і далі на розфасовку.
Вакуум у випарнику створюється за допомогою парових ежекторів 17, 18, в які подається пара високого тиску. Між випарником і першим ступенем ежектора 17 встановлений поверхневий трубчастий конденсатор 21, охолоджуваний водою. Між ступенями ежектора є також конденсатор 22, охолоджуваний водою.
Конденсат гріючої пари, що утворюється у випарнику, поступає у збірник конденсату 23, а конденсати, що утворюються в конденсаторах 21 і 22 поступають у збірник брудного конденсату 24. З цих збірників конденсати передаються насосом 25 в напірний бак 10 і, отже йдуть на поповнення циклів або використовуються для інших цілей.
У верхньому ступені абсорбера, окрім доуловлювання аміаку, відбувається також уловлювання піридинових основ. Уловлювання піридинових основ здійснюється більше концентрованим розчином сірчаної кислоти (10-12%) що містить меншу кількість сульфату амонію (20-30%), чим забезпечується висока міра уловлювання піридинових основ з газу і велика концентрація їх в розчині.
Для виведення поглинених піридинових основ частина маткового розчину з верхнього ступеня абсорбера безперервно відводиться в піридинову установку.
Після вилучення піридину розчин з нейтралізатора піридинової установки поступає в розкислювач куди подається також сірчана кислота, тут доводиться її вміст до 4-5%, внаслідок чого осідає шлам, який відділяється в шламовому відстійнику. Після шламового відстійника розчин поступає у збірник циркуляції міцного розчину 7.
Таким чином, в циркуляційний збірник нижнього ступеня абсорбції поступають: розчин з нижнього ступеня абсорбера, вода для поповнення циклу з напірного баку 10, сірчана кислота з напірного баку 9, матковий розчин з центрифуги, а також надмірний розчин з циклу циркуляції верхнього ступеня абсорбера, зі збірника 7; у циркуляційний збірник верхнього ступеня абсорбера поступають: розчин з верхнього ступеня абсорбера, вода для поповнення циклу з напірного баку 10, сірчана кислота з напірного баку 9, матковий розчин з ловушки 4, знепіридинений розчин з піридинової установки.
Аміачні пари з дефлегматора аміачно-вапняної колони, як і при сатураторному методі отримання сульфату амонію, поступають в абсорбер і в піридинову установку.
1.3 Уловлювання аміаку водою
Основні реакції при уловлюванні аміаку водою - це реакції утворення в розчині гідроксиду амонію, гідрокарбонату, гідросульфіду і ціаніду амонію на стадії абсорбції. Частково відбувається фізична абсорбція молекулярного аміаку і цианістого водню, добре розчинних у воді. Виділення аміаку з розчину на стадії регенерації здійснюється десорбцією - аналогічно очищенню надлишкової надсмольної води в аміачних колонах. При цьому леткий аміак і кислі домішки з води практично повністю відганяються і переходять в пароаміачну суміш. У сучасних процесах цю суміш направляють або на очищення від кислих домішок (Н2
S, НСN), а далі аміак спалюється в суміші з водяними парами, або на каталітичне розкладання аміаку і цианістого водню у відновній середі. У варіанті із спалюванням аміаку витягненні з газу сірководень, діоксид вуглецю і цианістий водень повертаються в прямий коксовий газ. При каталітичному руйнуванні аміаку в прямий коксовий газ повертаються заздалегідь охолоджені гази з каталітичного реактора, що містять водень, сірководень, діоксид вуглецю і частково непрореагваний аміак.
Перевагою технології уловлювання аміаку слід вважати поєднання процесів абсорбції аміаку з кінцевим охолоджуванням газу і відсутність хімічних реагентів. Газ з абсорбера аміаку при 30°С поступає в абсорбер бензольних вуглеводнів. Вживані в цій технології процеси - безперервні, здійснюються в герметичній апаратурі; відсутнє забруднення атмосфери шкідливими викидами; застосовується АСУТП з дистанційним контролем оператором з диспетчерського пункту.
В той же час технологія має і недоліки, які неможливо усунути:
1. Повне очищення газу від аміаку досягається при температурі абсорбенту 30°С , що вимагає підвищення ступеня очищення газу від нафталіну при первинному охолоджуванні газу (залишковий вміст нафталіну в газі 0,8 г/м ). У сучасних схемах цього типу з цієї причини газ охолоджують в холодильниках з горизонтальними трубами до зниженої температури (20 °С). Використовують холодильні машини для подачі в нижню секцію газових холодильників води при температурі 18 °С .
2. Обов'язкове практично повне очищення газу перед аміачним абсорбером від смоли (концентрація в очищеному газі 20 мг/м3
).
З. Вода є неселективним абсорбентом аміаку і володіє невисокою аміакоємністю. Для підвищення аміакоємкості за рахунок хімічних реакцій - утворення з'єднань аміаку з кислими газами використовують абсорбери з більшою поверхнею насадки і максимальним часом контакту фаз. При цьому разом з аміаком абсорбується до 30-40% сірководню і цианістого водню від ресурсів в коксовому газі.
4. При невисокій аміакоємкості розчину в циклі кругового очищення газу («абсорбер — десорбер - теплообмінники - абсорбер») обробляється великий об'єм абсорбенту (100 м3
на 100 тис. м3
газу в годину). Наслідок цього великі поверхні холодильників і теплообмінників води, дорогі десорбери, велика витрата пари на відгін аміаку і кислих газів з абсорбенту і так далі.
5. Абсорбент і пароаміачна суміш, що містять сірководень, діоксид вуглецю і ціаністий водень, вьісококорозіонноактивні при підвищеній температурі. Тому апаратуру регенерації аміачної води виготовляють з високолегированої сталі або титану. Сталева апаратура швидко виходить з роботи унаслідок корозії.
6. Навіть за умови ефективного очищення коксового газу від смоли спостерігаються відкладення в теплообмінній апаратурі вузла регенерації розчину. Великий об'єм абсорбенту і летючість домішок, що містяться в ньому, не дозволяють використовувати поширені способи очищення розчину від суспензій (смоли, вугільний пил).
7. Переробка пароаміачних сумішей, забруднених сірководнем і цианістим воднем, в цьому процесі ускладнена. При спалюванні аміаку пароаміачна суміш заздалегідь очищується від кислих домішок. При каталітичному руйнуванні аміаку утворюється низькокалорійний газ (до 500 ккал/м3
), що містить водень, аміак, сірководень, цианістий водень, оксид вуглецю в об'ємі 8% від коксового газу, який при його поверненні в прямий газ до первинних газових холодильників збільшує навантаження на апаратуру по всіх відділеннях обробки коксового газу. Каталітичний реактор вимагає складної системи автоматичного регулювання і блокування.
Комплексно автоматизована технологія очищення коксового газу від аміаку водою у поєднанні з круговим аміачним очищенням газу від сірководню каталітичним розкладанням аміаку і цианістого водню і отриманням сірки по методу Клауса один з широко поширених сучасних способів комплексного очищення коксового газу з підвищеним вмістом сірководню.
На деяких заводах для уловлювання аміаку з коксового газу використовують холодну воду. На рисунку 1.3 показана схема уловлювання аміаку з охолодженням газу перед скрубером в трубчастому газовому холодильнику .
Охолоджений в холодильнику 1 коксовий газ поступає в послідовно включені аміачні скрубери 3, де промивається водою з аміачної колони. З першого по ходу газу скрубера вода спрямовується на дистиляцію.

1-холодильник;2-збірник конденсату;3-скрубери;4-насоси.
Рисунок 1.3 Схема уловлювання аміаку водою у скруберах[7]
В результаті проведення дистиляції в якості продукту виходить концентрована аміачна вода. Після виділення аміаку і охолодження вода повертається на останній по ходу газу скрубер (круговий процес).
Вміст аміаку в газі після скруберів не повинен перевищувати 0,03 г/м3
. Витрата води на уловлювання аміаку складає 0,6-0,7 л/м3
газу. Поверхня насадки аміачних скруберів складає 0,7- 1 м2
на 1 м3
/ч газу.[7]
Одночасно з аміаком з газу уловлюються двоокис вуглецю, сірководень і цианістий водень, що розчиняються у воді і взаємодіють з аміаком. Вміст аміаку та інших компонентів у воді залежить від їх вмісту в газі, температури уловлювання величини поверхні і тривалості контакту газу з водою.
Зазвичай в скруберній воді міститься 10-20 г/л аміаку, 8-10 г/л двоокису вуглецю, 2-4 г/л сірководню, близько 1 г/л цианістого водню, близько 1 г/л фенолів. Частина аміаку знаходиться в скруберній воді у вигляді солей, що розкладаються при кип'яченні, (NH4
)2
СO3
, (NН4
)2
S, NH4
CNі частина аміаку - у вигляді з'єднань NH4
Cl, NH4
CNS, (NH4)2
SO4
, (NH4)2
SO3
, (NH4)2
S2
O3
та ін. [7]
Температура газу до кінцевого холодильника і точка роси залежать від температури газу після первинного охолодження і міри стискування газу в нагнітачі. Нормальна температура газу перед кінцевим холодильником не повинна перевищувати 65°С, а точка роси має бути не вище 35°С. Температура газу після кінцевого холодильника залежить від температури охолоджувальної води і не повинна перевищувати 28°С. Більш глибше охолодження газу сприяє інтенсивному поглинанню аміаку і, отже збільшенню його концентрації в скруберній воді. Це дозволяє понизити витрату пари на відгін аміаку .
Температура води, що поступає на поглинання аміаку з газу, не повинна перевищувати 25° С. При абсорбції малою кількістю води з тим, щоб отримати високі концентрації аміаку в скруберній воді, істотну роль грає відведення тепла, що виділяється при поглинанні аміаку.
На рисунку 1.4 приведений один з варіантів схеми процесу очищення коксового газу від аміаку водою з отриманням концентрованої аміачної води[1].
У скрубері 1 здійснюється промивка коксового газу холодною водою (питома витрата 0,6-0,7 л/м3
газу) внаслідок чого газ очищається, а вода поглинає аміак (і частково кислі гази) і виводиться у збірник 1а, куди також поступає надмірна вода процесу коксування.
Скруберна вода зі збірника 1а насосом 2 подається в напірний бак 3, звідки основний її потік (близько 90%) поступає на другу або третю тарілку дисоціатора 5 (заздалегідь підігріваючись в теплообміннику 4 до температури 50-60 °С), а інша (близько 10%) - безпосередньо на його верхню тарілку.

1-скрубер;1а-збірник;1б,16-приколонки;2,8-насоси;3-напірний бак;4-теплообмінник;5-дисоціатор;6,13-колони;7-яма;9-градирня;10-дефлегматор; 11-конденсатор;12-мірник;14-воронка;15-змішувач.
Рисунок 1.4 Схема процесу очищення коксового газу від аміаку водою з отриманням концентрованої аміачної води
У нижню частину дисоціатора 5 підводиться пара для підігрівання скруберної води, що стікає по тарілках, до температури 95 - 98°С, внаслідок чого відбувається виділення з води в парову фазу кислих газів, які разом з аміаком спрямовуються у верхню частину дисоціатора 5. Внаслідок того, що верхня тарілка дисоціатора 5 живиться холодною скруберною водою, а нижні тарілки - водою при температурі 50-60°С, відбувається охолодження і часткова конденсація парової фази, що піднімається, яка на виході з дисоціатора 5 має температуру близько 45°С.
Завдяки такому режиму роботи істотно знижується концентрація аміаку в парах, що покидають дисоціатор 5, оскільки розчинність аміаку у воді при знижених температурах значно перевищує розчинність кислих газів. Така попередня обробка скруберної води дозволяє виділити з неї до 80% діоксиду вуглецю і до 50 % сірководню, тобто відповідно понизити їх вміст в отримуваному на стадії регенерації поглинача товарному продукті.
Пари після дисоціатора 5 додатково очищаються від аміаку в промивачі 17 і спрямовуються в газопровід (чи можуть бути безпосередньо використані для отримання сірчаної кислоти), а гаряча скруберна вода спрямовується на парову регенерацію в колону 6. За відсутності необхідності виділення кислих газів (допускається їх присутність в отримуваній концентрованій аміачній воді) скруберна вода після теплообмінника 4 може подаватися безпосередньо в колону 6, минувши дисоціатор.
У вичерпній частині колони 6 із скруберної води аміак і залишкова кількість кислих газів десорбують в парову фазу. Регенерована скруберна вода при температурі дещо більше 100°С виводиться з колони 6 і спрямовується в теплообмінник 4 (для теплообміну з вихідною скруберною водою), а потім до ями 7, звідки насосом 8 подається в градирню 9 (де охолоджується до 25 - 30 °С) і насосом 19 - на зрошування скрубера 1.
Наявність дефлегматора 10, а також зміцнюючої частини в колоні 6 сприяє збільшенню концентрації аміаку в паровій фазі, що поступає в конденсатор 11, за рахунок часткової конденсації водяної пари (при температурі 89-92 °С) і повернення того, що утворюється в дефлегматорі 10 аміаковмісного конденсату на верхню тарілку колони 6 у вигляді флегми.
Повна конденсація концентрованої аміачної пари в трубчастому конденсаторі 11 забезпечує отримання товарного продукту, що виводиться через оглядовий ліхтар в мірник 12 при температурі не більше 30°С.
Для запобігання накопиченню пов'язаних солей аміаку в оборотній скруберній воді частина її подається на живильну тарілку колони 13, працюючу аналогічно колоні 6 з тією лише різницею, що після десорбції літкого аміаку, що стікає з вичерпної частини колони 13 вода змішується з розчином лужного реагенту (сода, вапно, луг), що подається з воронки 14. Після хімічної взаємодії і розкладання пов'язаних солей в змішувачі 15 вода з низу колони 13 спрямовується на верхню тарілку приколонку 1 б, де в результаті подачі гострої пари десорбує аміак, що вивільнився хімічним шляхом, який разом з водяними парами поступає в середню частину колони 13. З нижньої частини приколонку 16 стічна вода поступає у відстійник 18, а її надлишок виводиться з технологічного циклу. При необхідності розкладанню пов'язаних солей може передувати процес знефенолення води, що поступає з вичерпної частини колони 13.
Для отримання концентрованої аміачної води з меншим вмістом сірководню і діоксиду вуглецю використовують спеціальні прийоми, зокрема процес дисоціації здійснюють під тиском або використовують вапно при паровій регенерації скруберної води (для зв'язування кислих газів в початковій воді і уловлювання їх з аміачної пари). Такі прийоми можуть забезпечити зниження вмісту сірководню в продукті до 0,005 % і менше.
1.4 Отримання безводного аміаку
Отримання безводного (рідкого) аміаку здійснюється шляхом ректифікації під тиском чистої (що не містить кислих газів) концентрованої аміачної води,яка отримується при витяганні аміаку з коксового газу круговим фосфатним методом. Принципова технологічна схема цього процесу приведена на рисунку 1.5 [1]. Абсорбція аміаку з газу здійснюється при температурі 40 - 50°С поглинальним розчином моноамонійфосфату, що містить 330-380 г/л NH4
H2
PO4
і 8 - 12 г/л (NH4
)2
HPO4
в двоступінчатому абсорбері 1. Перший (по ходу газу) ступінь абсорбера 1, розташований нижче розділяючої перегородки 3, працює в режимі форсуночного зрошування, яке забезпечується циркуляційним насосом 2, а друга (вище за перегородку 3) – у

1-абсорбер;2,5,11,21-насоси;3-перегородка;4-смоловідділювач;6-теплообмінник;7-підігравач;8-регенатор;9-конденсатор;10-збірник;12-колона ректифікації; 13-дефлегматор; 14-холодильник; 15,20-збірники; 16-підігрівач; 17-евапаратор; 18-пароінжекторна установка; 19-холодильник.
Рисунок 1.5 Схема уловлювання аміаку з коксового газу круговим фосфатним методом.
барботажному режимі й оснащена пакетом тарілок спеціальної конструкції . Такі умови витягання аміаку обмежують розчинення кислих газів у поглиначі і забезпечують нормативні вимоги до очищення коксового газу.
У другому (барботажному) ступеню абсорбера 1 поглинальний розчин містить переважно однозаміщену форму фосфату амонію і характеризується вищою кислотністю (рН 5,2 - 5,6), що сприяє повнішому витяганню аміаку.
У першому (форсуночному) ступеню в результаті витягання аміаку і взаємодії його з моноамонійфосфатом (МАФ) зростає вміст діамонійфосфату (ДАФ) до величини близько 230-250 г/л, при цьому рН розчину зростає до 5,8 - 6,5. Насичений розчин фосфатів амонію виводиться з першого ступеня абсорбера 1 на регенерацію при питомій витраті 30-35 м3
/т витягуваного аміаку. Цей розчин містить смолянисті та інші зважені домішки, вимиті з газу у зв'язку з чим він передусім {піддається тривалому відстою в смоловідділювачі 4, потім насосом 5 подається, в тарілчастий регенератор 8, працюючий під надмірним тиском близько 0,35 МПа. При цьому розчин ДАФ підігрівається в парорідинному теплообміннику 6, а потім в паровому підігрівачі 7 до температури близько 180 °С. У регенераторі 8 під впливом температури відбувається гідроліз діамонійфосфату з виділенням молекулярного аміаку, який десорбує в парову фазу і відноситься висхідним потоком водяної пари у верхню частину регенератору 8, де на верхніх тарілках здійснюється їх промивання розчином лугу для доочистки від кислих газів (на рисунку 1.5 не показано). Пароаміачна суміш охолоджується спочатку в теплообміннику 6, а потім в конденсаторі 9, де утворюється концентрована аміачна вода, що направляється у збірник 10.
Концентрована аміачна вода, що практично не містить кислі гази подається насосом 11 через паровий підігрівач в колону ректифікації 12, працюючу під тиском 1,5 - 2,0 МПа (відповідна температура кипіння води близько 200°С). Колона 12 в нижній частині обладнана виносним циркуляційним підігрівачем 16, за допомогою якого в ній підтримується відповідний тиск і створюється висхідний потік парогазової фази. У вичерпній частині колони 12 відбувається десорбція аміаку з аміачного розчину, що поступає, а у верхній зміцнюючій частині - концентрація аміачної пари. Конденсація водяної пари в дефлегматорі 13 забезпечує живлення зміцнюючої частини колони 12 висококонцентрованою (по аміаку) рідкою фазою і отримання практично безводної парової фази, що конденсується під тиском у холодильнику 14 з утворенням рідкого аміаку, що поступає в спеціальний збірник 15.
Збіднена аміачна вода з низу колони 12 поступає в нижню частину регенераційної колони 8, звідки разом з регенерованим розчином МАФ виводиться в евапоратор 17, працюючий під вакуумом близько 400 мм рт. ст., де відбувається часткове випарне охолодження розчину і додаткова десорбція аміаку водяними парами, що утворилися.
Після евапоратора 17 регенерований розчин МАФ остаточно охолоджується в холодильнику 19 і поступає у збірник 20, звідки насосом 21 знову подається в абсорбер 1. Температура цього розчину встановлюється з урахуванням температури і відносного вологовмісту газу, що поступає в абсорбер 1, і є одним з чинників забезпечення водного балансу установки, що впливає на міру упарювання оборотного поглинального розчину коксовим газом. Кондиційність оборотного розчину по розчинених домішках забезпечується шляхом виводу з циклу відповідної його кількості зі збірника 20.
Вакуум в евапораторі 17 забезпечується за рахунок пароежекторної установки 18, призначеною як для евакуації аміаковмісної парогазової суміші з евапоратору 17, так і для створення висхідного потоку парової фази-носія в регенераційній колоні 8.
Приведений вище процес забезпечує отримання рідкого продукту, що містить 99,99 % аміаку і не більше 0,003 % діоксиду вуглецю, який може бути використаний як в якості сировини при виробництві органічних і неорганічних азотвмісних речовин, так і в якості висококонцентрованого азотного добрива. Для зберігання і транспортування цього продукту застосовується спеціальне устаткування і транспортні засоби.
1.5 Очищення коксового газу круговим фосфатним способом зі знищенням аміаку
Технологія очищення газу круговим фосфатним способом із знищенням аміаку, упроваджена у ВАТ «Кокс» в 2000 р. по раніше виконаних розробках Вухіна й Уральського політехнічного інституту, всесторонньо досліджена і удосконалена в період більш ніж трилітній експлуатації промислової установки великої одиничної продуктивності (до 120 тис. м3
/ч газу, що очищається.
Нові технічні рішення, захищені патентами і «ноу-хау», вигідно відрізняють технологічний процес від способу ФОСАМ. Фактично утворений новий, найбільш економічний спосіб очистки коксового газу, що відповідає перспективним вимогам за умовами праці, екологічною і промисловою безпеки:
1) абсорбціяаміакуздійснюєтьсяселективнов тарільчастофорсуночному апараті до залишкового вмісту аміаку в газі 0,03 г/м3
; з газу абсорбується 0,7% сірководню і 3,5% цианістого водню (від ресурсів в газі); абсорбер одиничною потужністю 100 тис. м3
/ч має мінімальні розміри: діаметр 3600 мм, висота 23 м, гідравлічний опір 450 мм вод. ст.;
2) регенерацію розчину діамонійфосфату здійснюють в колоні мінімальних розмірів (діаметр 1800 мм, висота 14 м) завдяки оптимізації режиму барботування на тарілках апарату;
3) розчин перед регенерацією очищують від зважених забруднень ефективним способом, що забезпечує тривалу експлуатацію устаткування без очищення від відкладень; застосовують високоефективний і надійний спосіб охолоджування регенерованого розчину; в процесі освоєння технології встановлено, що прийнята конструкція абсорбера забезпечує повне уловлювання аміаку при подачі регенерованого розчину в нього при температурі 70°С;
4) в період трьохлітньої експлуатації в промислових умовах були проведені випробування добавок ортофосфорної кислоти трьох сортів на поновлення втрат розчину ортофосфатів амонію; обрані доступні сорти очищених кислот з гарантованим їх отриманням з підприємств-постачальників;
5) пароаміачна суміш після регенератора мінімально забруднена сірководнем (0,08-0,02 г/кг), що не вимагає очищення від кислих домішок перед реактором знищення аміаку спалюванням;
6) створений агрегат спалювання аміаку в горизонтальному циклонному реакторі з незалежними топками спалювання коксового газу і висококонцентрованої пароаміачної суміші; конструкція реактора дозволяє отримати продукти горіння з мінімальним вмістом оксидів азоту і при охолодженні цих газів забезпечити максимальну паропотужність котла-утилізатора;
7) технологія керується АСУТП, управління відбувається з диспетчерського пункту двома операторами .
Технологічна схема процесу очищення коксового газу круговим фосфатним способом із знищенням аміаку зображена на рисунку 1.6[3].
Коксовий газ, охолоджений в холодильниках з горизонтальними трубами, очищений від нафталіну і аерозолів смоли в скрубері Вентурі і нагнітачах, подають при 55-60 °С у абсорбер 1. В якому розчином моноамонійфосфату (МАФ) з газу уловлюється аміак. Далі газ поступає в бензольно-скруберне відділення, де охолоджується при закритому циклі кінцевого холодильника. Сирий бензол уловлюється кам'яновугільним поглинальним маслом в скруберах з плоскопаралельною насадкою.
Очищений газ подають споживачам на спалювання в котлах ГРЕС, котельні заводу і опалювальні системі коксових батарей.
Розчин ортофосфатів амонію (переважно діамонійфосфату - ДАФ) після абсорбера 1 насосом подають у відстійники 2, де він очищується від уловлених з газу домішок смоли. Розчин, що відстоявся, насосом подається через теплообмінники 3 в регенератор 4, в якому з розчину паром

1-абсорбер аміаку; 2-відстійник розчину ДАФ; 3-теплообмінник; 4-регеніратор; 5-випарювач; 6-промзбірник розчину МАФ; 7-холодильник; 8-резервуар розчину МАФ; 9-промзбірник розчину ДАФ; 10-промзбірник смоли; 11-кондесатор; 12-промзбірник водяного аміаку; 13-десорбер; 14-пічь-реактор; 15-котел-утилізатор; 16-димовідсмоктувач; 17-димар; А-прямий коксовий газ; Б-зворотній коксовий газ; В-смола у відділення конденсації; Г-вода у збірник води після аміачних колон; Д-пар; Е-димові гази.
Рисунок 1.6 Технологічна схема відділення очистки коксового газу зі знищенням аміаку
десорбується аміак. Регенератор має випарник 5. У випарник і куб регенератора подають перегріту пару. Співвідношення витрати "гострої" і "глухої" пари регулюється - для підтримки постійної концентрації розчину ортофосфатів в абсорбційно- десорбційному циклі. Регенерований розчин МАФ з молярним співвідношенням аміаку до фосфорної кислоти 1,25-1,28 з регенератора поступає в теплообмінники З, нагріває розчин ДАФ, охолоджується до 80-90 °С і скидається в промзбірник розчину МАФ 6. Звідси розчин насосом прокачується через холодильники 7 і після охолоджування до 40-45 °С поступає в резервуар 8,з якого надлишок розчина крізь перелив перетікає в промзбірник 6. З резервуару 8 розчин ДАФ насосом подається на верхню тарілку абсорбера 1.
Розчин з нижньої тарілки стікає в шар циркулюючого розчину нижньої порожнистої секції абсорбера із зрошуванням форсунки. З абсорбера через гідрозатвір він перетікає в промзбірник 9, з якого насосом подасться на циркуляцію через форсунки нижньої секції абсорбера. У промзбірник автоматично підтримується постійний рівень відкачуванням надлишку розчину ДАФ з нагнітальної лінії циркуляційного насоса в перший по ходу розчину відстійник 2. Після відстою від домішок смоли і вугільних часток розчин ДАФ подається насосом в теплообмінники 3, а потім при 110-120 °С поступає на верхню тарілку регенератора 4. Смола періодично по графіку виводиться з поверхні відстійників в промзбірник 10, з якого у міру накопичення відкачується в механізованих освітлювачів відділення конденсації.
Пароаміачна суміш (ПАС) з регенератора, що містить 15-20% аміаку, ділиться на два рівні потоки; 50% ПАС проходить через конденсатори 11. Концентрована аміачна вода з конденсаторів стікає в промзбірник 12, з якого насосом подається на верхню тарілку десорбера 13 установок спалювання аміаку. Друга половина ПАС вводиться в середню частину міжтарільчастого простору десорбера 13. У куб десорбера подають "гостру" пару. Воду з десорбера з вмістом леткого аміаку 0,1—0,15 г/дм3
передають в збірник води після аміачної колони.
ПАС з десорбера поступає в пічь-реактор термічного руйнування і спалювання аміаку 14. У верхній частині печі-реактора розміщені пальники для спалювання коксового газу. Коксовий газ спалюється при змішуванні з повітрям і при температурі 1450 °С; продукти горіння у вихровому потоці поступають в зону подачі пароаміачної суміші. При нагріві останньої продуктами горіння коксового газу до температури 800-1000°С аміак в основному термічно руйнується - виходять азот і водень. Частка аміаку і водень при подачі повітря в зону нижче за введення ПАС спалюють при температурі на виході з печі 1150°С. Продукти горіння після реактора проходять через котел-утилізатор 15, охолоджуються до 140-160 °С і димовідсмоктувачем 16 подаються в димар 17.
У котлі-утилізаторі отримують перегріту пару середнього тиску (12-14 атм). Велика частка пари використовується в технології очищення газу від аміаку; невеликий надлишок передають на завод. У експлуатаційному режимі відділення очищення газу від аміаку працює без зовнішнього пароспоживання. Для умов планової або аварійної зупинки вузла знищення аміаку передбачена можливість конденсації всього об'єму пароаміачної суміші в конденсаторах 11 і передача концентрованої аміачної води в накопичувальний резервуар, розрахований на декілька діб роботи без установки спалювання. Для цих умов передбачено резервне постачання парою відділення очищення газу від мережі заводу. Резервні піч-реактор і котел-утилізатор проектом не передбачені. Відділення очищення газу зі знищенням аміаку працює в автоматичному режимі. Система АСУТП розроблена фахівцями заводу. Управління агрегатами очищення газу і знищення аміаку здійснюється з пульта двома операторами в зміну .
2 Фізико-хімічні основи виробництва
Отримання сульфату амонію засноване на поглинанні аміаку з коксового газу розчином сірчаної кислоти і протіканні реакції нейтралізації [4].
2NH3
+H2
SO4
→(NH4
)2
SO4
+q(2.1)
Процес нейтралізації сірчаної кислоти аміаком протікає в дві стадії:
-утворення кислої солі - бісульфату амонію
H2
SO4
+NH3
→NH4
HSO4
; (2.2)
-перетворення кислої солі на середню у міру перенасичення розчину аміаком
NH4
HSO4
+NH3
→(NH4
)2
SO4
(2.3)
Ці реакції протікають з виділенням тепла, кількість якого залежить від умов ведення процесу. При взаємодії чистого аміаку і насиченого розчину сульфату амонію що містить 7-8% вільної кислоти, тепловий ефект сумарної реакції складає при 47,5°С 815 кДж/кг сульфату амонію, а при 66,3°С 1855 кДж/кг При поглинанні аміаку з коксового газу тепловий ефект процесу значно менший оскільки частина аміаку знаходиться у вигляді летких з'єднань з сірководнем, вуглекислотою і іншими кислими газами, на розкладання яких витрачається тепло. Для практичних розрахунків можна приймати тепловий ефект сумарної реакції рівним 1180 кДж/кг сульфату амонію.
Співвідношення між сульфатом та бісульфатом в розчині визначається кислотністю останнього. При низькій кислотності (1-2%) в розчині переважає сульфат, який випадає з пересиченого розчину у вигляді кристалів. При підвищенні кислотності розчину до 34% середня сіль переходить практично повністю в кислу, яка має кращу розчинність у воді і в кислих розчинах. При 60°С розчинність сульфату амонію у воді складає 46,6%, при підвищенні кислотності до 19% вона практично не міняється, а потім поступово росте і при кислотності 34% досягає максимуму (близько 52%) після чого починає знижуватися.
Утворення кристалів сульфату амонію відбувається при пересиченні маткового розчину за рахунок безперервного процесу поглинання аміаку сірчаною кислотою або в результаті упарювання розчину. Кристалізація розпочинається з утворення центрів кристалізації - зародків кристалів. Для отримання великих кристалів необхідно забезпечити умови для їх росту, інтенсивність якого залежить від швидкості дифузії сульфату амонію з розчину до граней кристалів швидкості переходу молекул солі з рідкої фази в тверду і швидкості відведення прихованої теплоти кристалізації від поверхні кристалів в розчин. При інтенсивному перемішуванні розчинів процеси дифузії сульфату амонію з розчину до граней кристалів і відведення тепла кристалізації настільки інтенсифікуються, що практично не роблять впливу на процес кристалізації. При цьому швидкість переходу речовини з рідкої фази в тверду пропорційна другому ступеню різниці концентрації пересиченого і насиченого розчинів
(2.4)
Коефіцієнт швидкості кристалізації К залежить в сильній мірі від умов кристалізації. Експериментально встановлено, що основними чинниками, що роблять вплив на ріст кристалів, являються інтенсивність перемішування температура і кислотність маткового розчину, а також концентрація різних домішок в нім.
Шляхом перемішування розчинів можна прискорити ріст дрібних кристалів, затримати утворення нових зародків або розчинити центри кристалізації, що вже утворилися. Для отримання великих кристалів необхідно підтримувати їх тривалий час в зваженому стані в пересиченому розчині, що може бути забезпечено за наявності висхідного потоку розчину в кристалізаторі. При такому русі розчину створюються сприятливіші умови для росту великих кристалів, оскільки вони мають більшу енергію кристалізації і розташовані в нижній частині кристалізатора, куди підводиться свіжий пересичений розчин.
Дрібніші кристали і зародки в таких умовах поступово розчиняються, оскільки вони мають більшу розчинність і знаходяться у верхній частині кристалізатора, де міра пересичення маткового розчину незначна. Коли розмір кристалів досягає певної величини, вони осідають на дно кристалізатора і виводяться в якості продукту.
Утворенню великих кристалів сприяють нижча температура і кислотність маткового розчину. У виробничих умовах розчин постійно контактує з холодними стінками апаратів й трубопроводів, внаслідок чого він стає пересиченим і в цих зонах утворюються нові зародки кристалів. При накопиченні їх в системі не можуть бути отримані великі кристали через нестачу пересиченого розчину. Чим вище температура маткового розчину, тим значніше вплив місцевих переохолоджень розчину, тим більше зміст дрібних фракцій в отримуваному продукті.
Для отримання великокристалічного продукту процес кристалізації повинен проводитися при можливо низькій температурі, а апарати і трубопроводи мають бути теплоізольовані.
Підвищення кислотності розчину призводить до збільшення змісту бісульфату амонію зростанню в'язкості і щільності розчину, припиненню росту кристалів. Бісульфат піридину, що утворюється при цьому, також перешкоджає росту кристалів і сприяє збільшенню тієї солі, що злежується при зберіганні.
Найбільш великі кристали виходять при кислотності розчину 1-2%. Проте, якщо кристалізація сульфату амонію робиться в апараті для поглинання аміаку сірчаною кислотою при такій кислотності відбувається інтенсивне відкладення кристалів на стінках апарату і в трубопроводах, порушується нормальна робота установки. З цієї причини в таких установках підтримується кислотність маткового розчину на рівні 4-5%. При цьому дуже важливо підтримувати однакову кислотність в усьому об'ємі розчину і виключати утворення нейтральних зон, в яких виходить сіра або чорна сіль (перепал).
Істотний вплив на ріст кристалів і їх форму роблять різні домішки в матковому розчині. При змісті більше 1 г з'єднань окисного (трьохвалентного) заліза в 1 кг розчину збільшується зміст дрібних фракцій в продукті. Наявність в розчині хрому, алюмінію, кадмію сприяє утворенню голчастих кристалів, які при зберіганні легко ламаються, утворюючи пил, і схильні до злежування. Наявність в розчині цианідів і хлоридів також перешкоджає росту кристалів.
Негативна дія названих домішок може бути обмежена при введенні в розчин щавлевої кислоти, сульфату магнію і щавлевокислого кальцію, сечовини, з'єднань закисного (двовалентного) заліза, марганцю, кобальту.
Домішки в матковому розчині не лише перешкоджають росту кристалів, але і надають їм різне забарвлення. Сірий колір сульфату амонію обумовлений наявністю смолянистих речовин, сірчистих з'єднань заліза, міді, свинцю. Жовте забарвлення дають з'єднання миш'яку. Роданисті з'єднання у присутності слідів заліза дають червоне або рожеве забарвлення. Блакитний колір надає сульфату берлінська лазур. Крім того, цианісті з'єднання утворюють із залізом комплексні з'єднання, які в суміші з іншими речовинами надають сульфату колірні відтінки від зелено-жовтого до фіолетового.
Для отримання сульфату амонію білого кольору необхідно робити попереднє очищення коксового газу від смолянистих речовин цианістого водню і сірководню, застосовувати чисту сірчану кислоту та апаратуру з корозійностійких матеріалів.
2.1 Заходи проти злежування
Важливим показником якості сульфату амонію є розсипчастість. Для підвищення цього показнику у сульфат амонію вносять добавки.
На коксохімічних підприємствах, які випускають мілкокристалічний сульфат амонію, у якості антизлежувальної добавки впродовж останніх років використовували сульфазол. За ці роки виявлені негативні властивості сульфазолу. Тому були запропоновані у промисловості інші антизлежувальні добавки порошкоподібного типу, наприклад шлаки, сульфат монометиламіну, залізовмісні добавки. Однак, цим добавкам, як і сульфазолу, властиві такі недоліки, як дефіцитність чи відсутність промислового виробництва, наявність технологічних утруднень, що пов’язані з їх внесенням, екологічні, що виникають при їх застосуванні.[8]
Політехнічним інститутом Томська спільно з Кемеровським коксохімічним заводом розроблена і освоєна нова антизлежувальна добавка до сульфату амонію - НМ. Добавка НМ недефіцитна, вдесятеро дешевше сульфанолу, нетоксична, не є поверхнево-активною речовиною, тому відпадає необхідність перевірки її дії на рослинні та тваринні організми, що зазвичай виникає при пропозиції нових кондиціонуючих добавок для мінеральних добрив. Добавка НМ легко розчиняється у воді і не викликає спінювання технологічних розчинів, її склад: суміш аміачної селітри і карбаміду в співвідношенні 1:1 (масові долі); концентрація речовин в розчині 30%. [8]
Введення в сульфат амонію гігроскопічної добавки НМ може викликати різке зниження гігроскопічної точки продукту, аж до величини критичної відносної вологості, рівної 20% при 25°С. Сульфат амонію з добавкою НМ в умовах змінної відносної вологості повітря поводитиметься абсолютно інакше, ніж продукт без добавки. Такий продукт не зможе висохнути повністю, а тому не злежиться. Між кристалами речовини завжди присутня рідка фаза. При 35°С значення критичної відносної вологості для сульфату амонію з добавкою НМ знижується до 8%, означає і в умовах сухого жаркого клімату добавка НМ забезпечуватиме отримання розсипчастого продукта. Якщо вміст добавки НМ в сульфаті амонію складає 0,1-0,3%, то перевищення меж норм вологи по ГОСТ 9097-82 в продукті не спостерігається. Застосування добавки дозволяє отримати 100 % розсипчастість сульфату амонію.
Значне зниження злежуваності досягається при обробці сульфату амонію 10 % розчином хлорного заліза. При витраті хлорного заліза 0,05-0,1 % сіль практично не злежується, але при цьому відбувається підвищення кислотності сульфату амонію на 70-80%.[9]
На Ждановському коксохімічному заводі у якості антизлежувальної добавки випробовували мартенівський тонкоподрібнений шлак (як найбільш доступний і дешевий).[10]
Для обробки сульфату амонію шлаком в цеху уловлювання встановили дозатор, схема якого приводиться на рисунку 2.1.

1-бункер; 2-шнек; 3-клапан; 4-труба; 5-сітка; 6-електродвигун; 7-сушка
Русинок 2.1 Схема дозатора
Шлак засипають в бункер 1, у верхній частині якого знаходиться металева сітка 5 для відділення крупних шматочків. При видачі солі з сушарки автоматично включається шнек 2і відкривається клапан 3, шлак подається через розподільні отвори в трубі 4на сульфат амонію. Попередні випробування по подачі мартенівського шлаку перед сушаркою 7 показали неефективність цього способу, оскільки спостерігалися сильне пиління та значні втрати шлаку з викидами з сушарки (6 - електродвигун).
Кількість доданого шлаку складала 0,1-0,5%. Введення шлаку в кількості, що перевищує 0,5%, впливає на вміст азоту в добриві, яке не має бути менше 21%.
Ступінь злежування оцінювали наступним способом: закладали оброблені шлакому проби сульфату амонію в мішках, а також з сіллю без добавки шлаку на шестимісячне зберігання в штабелях. Після закінчення зазначеного терміну вміст мішків аналізували на розсипчастість по ГОСТ 21560.5-82. Вміст шлаку в обробленому сульфаті амонію визначали по кількості фосфору, який є одним з компонентів мартенівського шлаку.
Аналіз результатів промислового випробування показав, що в процесі шестимісячного зберігання початковий сульфат амонію без добавки шлаку злежувався до моноліту, розсипчастість коливалася в межах 28,8-70,1. В той же час сіль з добавкою мартенівського шлаку вільно висипалася з мішків. Це можна пояснити тим, що тонкоподрібнений шлак роз'єднує поверхню сульфату амонію, а основні оксиди, що входять до складу шлаку нейтралізують надмірну сірчану кислоту, яка сприяє злежуванню готового продукту. Одночасно мікроелементи, що входять до складу шлаку, самі є мікродобривами.
Таким чином, вміст добавки повинен складати 0,3-0,5%. При цьому якість сульфату амонію повністю відповідає вимогам стандарту, а розсипчастість складає 98,7-99,8%.[10]
У лабораторних умовах випробували наступні тверді добавки: золу ТЕЦ Ясиновського коксохімічного заводу,феросплавний пил,шлам газоочистки, шлакову муку конвертерного цеху і подрібнений гранульований шлак доменного цеху, а також подрібнений силікатний пісок.
З рідких добавок випробовували відходи власного виробництва: регенерований розчин ділянко сірко очистки, лужні води цехів ректифікації і смоло переробного. Витрата добавки у всіх випадках складала 0,5 %(масові долі) на суху речовину. Після обробки сульфат висушували до первинної вологи.
Результати наведені у таблиці 2.1
Таблиця 2.1 Результати випробувань
Добавка
|
Зусилля руйнування брикету |
Візуальна характеристика брикету
|
Тверді |
– |
88,2 |
Твердий |
Зола ТЕЦ |
19,6 |
Розсипається при легкому натисканні |
Гранульований шлак |
58,8 |
Зберігає форму, краї осипаються |
Силікатний пісок |
39,2 |
Теж саме |
Феросплавний пил |
0 |
Не утворюється |
Шлам газоочистки |
0 |
Теж саме |
Шламова мука |
0 |
—»— |
Рідкі |
Регенерований розчин |
0 |
—»— |
Лужні відходи: |
ректифікації |
0 |
—»— |
Смолопереробного цеху |
49,0 |
Зберігає форму, краї осипаються |
Хорошою розсипчастістю володіє сульфат після обробки металургійним пилом і регенерованим розчином сіркоочистки. Відмічено, що після зберігання сульфату з добавкою регенерованого розчину він набуває слабо-рожеве фарбування. З металургійних пилів кращий феросплавний, оскільки він не змінює колір сульфату. Навіть повністю висушений сульфат злежується, а оброблений добавками зберігає сипучість протягом року. [8]
Таким чином, ефективними антизлежувальними добавками можуть бути відхід коксохімічного виробництва-відпрацьований розчин сіркоочистки і деякий металургійний пил.
3. Характеристика сировини, напівпродуктів і готової продукції
3.1
Характеристика сировини
Основною сировиною цеху уловлювання є коксовий газ, продукт коксування кам'яновугільної шихти в камерах коксових батарей.
Склад прямого (сирого) коксового газу того, що виходить з камер коксових печей, його вихід і густина змінюються впродовж періоду коксування[1].
У газозбірнику відбувається усереднювання суміші газів і пари що виділяються в різні години коксування з різних камер, що складають коксову батарею.
Вихід і склад коксового газу залежить від технологічного режиму процесу коксування і якості вугільної шихти, що переробляється. При незмінному режимі коксування і постійному складі шихти вихід і склад коксового газу на конкретному коксохімічному підприємстві залишаються практично постійними.
Вихід окремих компонентів газу і хімічних продуктів коксування в масових відсотках від сухої шихти :
Метан 5,5 - 6,5
Ненасичені вуглеводні 1,2 - 1,25
Оксид вуглецю 2,6 - 2,8
Ароматичні вуглеводні 1,0 - 1,02
Азот 2,1-2,4
Аміак 0,3 - 0,47
Водень 1,5-1,7
Кам'яновугільна смола 3-4
Діоксид вуглецю 1,2 - 1,3
Прямий коксовий газ переробляється в хімічних цехах коксохімічного підприємства. Процес переробки зводиться до охолодження коксового газу і виділення з нього кам'яновугільної смоли, витяганню аміаку, нафталіну піридинових основ, ароматичних вуглеводнів, сірководню і ряду інших продуктів.
Відповідно до ТУ У 40.2-05393085-001-2003 якість коксового газу повинна відповідати наступним вимогам [11](таблиця 3.1):
Таблиця 3.1 Газ коксовий неочищений. Технічні умови
Найменування показника
|
Норма для марок |
Марка А |
Марка Б |
1.Масова концентрація нафталіну, г/м3
, не більше |
0,3 |
0,85 |
2.Масова концентрація сірководню, г/м3
, не більше |
5 |
3.Нижча питома теплота згорання 1м3
газу при 20°С і тиску 101325 Па, кДж/м3
не більше |
16380
|
Ще однією необхідною сировиною цеху уловлювання є сірчана кислота. У хімічно чистому сульфаті амонію аміак складає 25,76%, останні 74,24% припадають на частку сірчаної кислоти. На ПАТ ЕВРАЗ «Дніпродзержинський КХЗ» для виробництва сульфату амонію використовується сірчана кислота наступних видів: контактна технічна, контактна покращена. Сірчана кислота H2
SO4
сильна двоосновна, така, що відповідає вищому ступеню окислення сірки (+6). За звичайних умов концентрована сірчана кислота важка масляниста рідина без кольору і запаху[5].
Для виробництва сульфату амонію вищого і першого сортів використовується контактна сірчана кислота покращена концентрації 92,0–94,0% з вмістом заліза не більше 0,006%оксидів азоту 0,00005% і миш'яку 0,00008 %; для виробництва сульфату амонію другого сорту використовується контактна технічна кислота концентрації 92,0%, що містить 0,02% заліза. За фізико-хімічними показниками сірчана кислота повинна відповідати нормам, вказаним в таблиці 3.2 [12]. (ГОСТ 2184-77).
Таблиця 3.2 Показники якості сірчаної кислоти
Найменування показника
|
Норма |
Покращена
|
Технічна |
1-й сорт |
2-й сорт |
1.Масова доля моногідрату (H2
SO4
), % |
92,5-94,0 |
Не менше 92,5 |
2. Масова частка заліза (Fe), % не більше |
0,006
|
0,02
|
0,1
|
3. Масова частка залишку після прокалювання, % не більше |
0,02
|
0,05
|
Не нормується |
4.масова частка окислів азоту (N2
O3
), % не більше |
0,00005
|
Не нормується
|
5. Масова частка миш’яку(As), %не більше |
0,00008
|
6. Масова частка хлористих з’єднань (Cl), %не більше |
0,0001
|
7. Масова частка свинцю (Pb), %не більше |
0,001
|
8. Прозорість |
Прозора без розбавлення |
9. Колір, см3
розчину порівняння, не більше |
1
|
6
|
—
|
3.2 Характеристика продуктів
Коксовий газ, що пройшов конденсаційну і уловлюючу апаратуру хімічних цехів (зворотній), має наступний склад [1] (таблиця. 3.3):
Таблиця 3.3 Склад зворотнього коксового газу
Компонент
|
Вміст, %(об’єм.)
|
Середній склад, %(об’єм.)
|
Водень |
54,3–60,4 |
57,35 |
Метан |
23,7–27 |
25,35 |
Ненасичені вуглеводні |
1,9–3,8 |
2,85 |
Оксид вуглецю |
5,5–7,77 |
6,64 |
Азот |
2,9–5,5 |
4,2 |
Діоксид вуглецю |
2,05–3,5 |
2,78 |
Кисень |
0,6–1,0 |
0,8 |
Коксовий газ, що пройшов очищення від смоли, аміаку, бензольних вуглеводнів та нафталіну (марки А) використовується для обігріву коксових печей, а також теплосиловим цехом та на інші енергетичні потреби [11].
Середня густина зворотного коксового газу при 0°С дорівнює 0,44 кг/м3
, при 20°С - 0,41 кг/м3
. Нижча теплота згорання сухого газу – 16380 кДж/м3
(3909 ккал/м3
).
Сульфат амонію представляє собою білі прозорі кристали форми подовженого ромба величиною від сотих і десятих частин міліметра до 6-8 мм і більше. Густина кристалічного сульфату амонію при 20 °С складає 1,768 г/см3
. Насипна маса залежно від великості кристалів і вмісту вологи коливається в межах 780-830 кг/м3
. Сульфат амонію добре розчиняється у воді. З підвищенням температури розчинність його у воді збільшується. Хімічно чистий сульфат амонію містить 21,237 % N2
або 25,76 % NН3
.[5]
За фізико-хімічними показниками сульфат амонію повинен відповідати нормам, вказаним в таблиці 3.4(ТУ У 322-00190443067-97)[13]
Таблиця 3.4 Показники якості сульфату амонію
Найменування показників
|
Сорт |
Вищий |
1 Сорт |
1. Зовнішній вигляд
|
Білі або слабо забарвлені кристали |
Не нормується |
2. Масова частка азоту у перерахунку на суху речовину, %, не менше |
21,0
|
21,0
|
3. Масова частка води, %, не більше |
0,2 |
0,3 |
4. Масова частка вільної сірчаної кислоти, %, не більше |
0,03 |
0,05 |
5. Масова частка нерозничного у водізалишку, % ,не більше |
0,02 |
0,05 |
6. Розсипчастість, % |
100 |
100 |
Важливим показником якості сульфату амонію є розмір кристалів. Дрібнокристалічна структура солі з сильно розвиненою поверхнею є причиною підвищеного вмісту в ній вологи і сірчаної кислоти, що призводить до злежування при зберіганні і зрощення її в агломерати. Великокристалічна сіль менш схильна до злежування і рівномірно розподіляється в ґрунті при використанні її в якості добрива [5].
Сульфат амонію виробляється на коксохімічних заводах у великих кількостях. На 1 т сухої шихти виробництво сульфату амонію (сухого) складає 11,0-11,5 кг.
Сульфат амонію є одним з найбільш ефективних азотних добрив. Особливістю цього вигляду добрива є ті, що він дозволяє підпитувати ґрунт не лише азотом, але і сіркою. Остання входить до складу білків і амінокислот рослин і тому разом з азотом є одним з важливих елементів живлення сільськогосподарських культур. По мірі важливості для рослин сірку можна поставити на третє місце після азоту і фосфору. Продукт володіє важливою для життєдіяльності рослин властивістю. Він переводить фосфор, що знаходиться в ґрунті з нерозчинної форми в розчинну і тим самим підсилює процес поглинання рослиною цієї речовини. Це дозволяє понизити кількість фосфорних добрив, що вносяться до ґрунту.
Не дивлячись на те, що продукт найширше використовується в сільському господарстві, він також застосовується і в інших областях. Наприклад, в біохімії з його допомогою отримують білки. В харчовій промисловості його використовують як харчову добавку Е517 (речовини проти злежування). В промисловості сульфат амонію використовують як сировину при виробництві акумуляторів і як основу при виробництві вогнезахисних просочень для дерева.
Побічним продуктом уловлювання аміаку є смолка кисла сульфатного відділення,яка утворюється у сатураторі чи абсорбері внаслідок полімеризації смолистих полімерних сполук, нафталіну, сульфату амонію, сірчаної кислоти.
За хімічними показниками смолка кисла сульфатного відділення повинна відповідати вимозі ТУ У 23.1-0539085-002-2004, по вмісту вільної сірчаної кислоти не вище 3,5% [14]
Передається по мірі накопичення у вуглепідготовчий цех для додавання у шихту.
4. Вибір, обгрунтування і опис технологічної схеми
Одним з найважливіших показників якості сульфату амонію, що визначає ефективність його застосування, являється гранулометричний склад. Великокристалічна сіль, що має меншу питому поверхню граней, сорбує менше вологи, сірчаної кислоти і інших домішок, проявляє меншу схильність до злежування, легше вноситься в грунт, діє ефективніше на розвиток рослин.
Показники роботи без сатураторних установок у порівнянні з сатураторними :[15]
1) більш високий ступінь вилучення аміаку та піридинових основ з коксового газу;
2) поліпшений гранулометричний склад солі. Вміст фракцій >0,25 мм у сульфаті, отриманому на без сатураторній установці, складає 60-70 %, на сатураторній-13-25 %;
3) зниження гідравлічного опору газових апаратів, а отже, і витрати електроенергії на транспортування коксового газу через уловлюючу апаратуру.
Більш висока собівартість сульфату амонію, який отримується на без сатураторній установці (на 7-8 % вище, чим при його отримуванні в сатураторах) компенсується кращою якістю отримуваного продукту.
Для впровадження на ПАО ЕВРАЗ «Днепродзержинський КХЗ»пропонується наступна технологічна схема, що наведена на рисунку 4.1.
Коксовий газ 1, що містить аміак , поступає в паровий підігрівач Пр, де нагрівається до температури 65-70°С, потім направляється в абсорбер А, що є полим апаратом із форсуночним зрошенням, що складається з двох ступенів, - нижнього та верхнього, розділених між собою горизонтальною тарілкою.

Рисунок 4.1 Технологічна схема одержання сульфату амонію по без- сатураторному методу.
У нижньому ступеню абсорберу циркулює розчин 2, що містить близько 40% сульфату амонію і 1-1,5% вільної сірчаної кислоти. У верхньому ступеню абсорберу циркулює розчин 2.1 що містить від 20 до 30% сульфату амонію і 10-12% вільної сірчаної кислоти.
Після проходження нижнього і верхнього ступенів абсорбера коксовий газ проходить кислотну ловушку Л, що призначена для видалення бризок маткового розчину.
Кожен ступінь абсорбера має свою самостійну систему зрошування.
Так, з нижнього ступеня абсорбера розчин через гідрозатвір поступає в циркуляційний збірник слабкого розчину Зб1, звідки насосом Н6 подається на зрошування цього ж ступеня. Розчин же з верхнього ступеня абсорбера поступає в циркуляційний збірник міцного розчину Зб2, звідки насосом Н5 подається на зрошування верхнього ступеня абсорбера.
Подача розчину як в нижній, так і у верхній ступені абсорбера робиться на двох рівнях.
Сірчана кислота 3 і вода 4, необхідні для поповнення циркулюючих розчинів, подаються з напірних баків Нб в циркуляційні збірники першого і другого ступенів Зб1 і Зб2.
Частина маткового розчину з нижнього ступеня абсорбера безперервно відводиться в смоловідділювач Св, а звідти у збірник Зб3, з якого насосом Н4 подається вниз конічної частини трубчастого випарника В.
У смоловідділювачі виділяється велика частина смоли яка випливає на поверхню розчину і безперервно видаляється скребковим транспортером у смоляний ящик Зб4. Це забезпечує мінімальне попадання смолянистих речовин у збірник Зб3 і, отже, запобігає забрудненню сульфату амонію.
У випарнику В відбувається випарювання води з розчину і кристалізація сульфату амонію. Завдяки вакууму (тиск дорівнює 75 мм рт. ст.), що створюється двоступінчатим паровим ежектором, температура кипіння розчину дорівнює 50-60° С. Випарник обігрівається парою низького тиску 9.1, близько 2 кгс/см2
. У випарнику є внутрішня циркуляційна труба більшого діаметру, ніж трубки, внаслідок чого створюється термічна циркуляція розчину усередині апарату, яка сприяє росту кристалів.
Пульпа 6, що утворюється в нижній частині випарника, є сумішшю кристалів сульфату амонію (приблизно 50-60% від маси пульпи) і насиченого маткового розчину, подається в центрифугу безперервної дії Ц. Матковий розчин після центрифуги повертається в циркуляційний збірник Зб1 нижнього ступеня абсорбера. Туди ж поступає промивна вода з центрифуги.
Вологий сульфат амонію 8 з центрифуги поступає в сушарну установку С і далі в яму на склад.
Вакуум у випарнику створюється за допомогою парових ежекторів Пе1, Пе2, в які подається пара високого тиску 9. Між випарником і першим ступенем ежектора Пе1 встановлений поверхневий трубчастий конденсатор Пк, охолоджуваний водою . Між ступенями ежектора є також конденсатор П, охолоджуваний водою.
Конденсат гріючої пари 10, що утворюється у випарнику, поступає у збірник конденсату , а конденсати, що утворюються в конденсаторах Пк і П поступають у збірник брудного конденсату Зб5. З цього збірника конденсат передається на поповнення циклів або може використовуватися для інших цілей.
Таким чином, в циркуляційний збірник нижнього ступеня абсорбції Зб 1 поступають: розчин з нижнього ступеня абсорбера, вода для поповнення циклу, сірчана кислота з напірного баку Нб, матковий розчин з центрифуги Ц, а також надмірний розчин з циклу циркуляції верхнього ступеня абсорбера, зі збірника Зб2; у циркуляційний збірник верхнього ступеня абсорбера поступають: розчин з верхнього ступеня абсорбера, вода для поповнення циклу, сірчана кислота з напірного баку Нб, матковий розчин з ловушки Л .
В умовах постійної економічної нестабільності у світі попит на кокс Дніпродзержинського КХЗ також являється нестабільним. У періоди зниження попиту на кокс завод вимушений для зниження виробництва збільшувати періоди коксування , що негативно впливає на якість хімічних продуктів коксування. Це в свою чергу негативно впливає на роботу сульфатного відділення. Разом з порушенням технологічного режиму сульфатного відділення постійно порушується робота піридинового відділення, в результаті чого піридинові основи не отримуються. Одночасно з тим, при виведенні піридинового відділення на режим, порушується робота сатуратора.
Виробництво піридинових основ зв’язано з витратами сірчаної кислоти, енергетичними витратами, витратами на ремонт устаткування. А при низькому виробництві коксу кількість піридинових основ, які знаходяться в коксовому газі невелика.
Враховуючи все вище сказане керівництво Дніпродзержинського КХЗ прийшло до висновку ,що виробництво піридинових основ економічно недоцільно. Тому на ПАО ЕВРАЗ «Днепродзержинський КХЗ»піридинові основи не виробляються.
5. Матер
іальний та тепловий баланси виробництва
5.1 Матеріальний розрахунок безсатураторного методу отримання сульфату амонію
Вихідні дані:
Склад прямого коксового газу:
Водяні пари 30,0 г/м3
Бензольні вуглеводні 36,0 г/м3
Аміак 7,0 г/м3
Сірководень 16,0 г/м3
Піридинові основи 0,4 г/м3
Склад сухого коксового газу:
H2
–60,0%
CO – 7,0%
CO2
–2,7 %
Cn
Hm
– 2,3 %
N2
–4,0%
O2
–1,0%
CH4
– 22,0%
Вміст аміаку у очищеному коксовому газі – 0,03 г/м3
Проектна потужність заводу по газу – 52000 м3
/год
Перераховую кількість компонентів, які містяться у 52000 м3
/год коксового газу за формулою:
Gкомп.
= ,(5.1)
де Vк.г.
- кількість коксового газу - 52000 м3
/год
gкомп.
- кількість компоненту г, у 1 м3
Gв.п.
= 52000×30/1000=1560 кг/год.
Gб.в.
= 52000×36/1000=1872 кг/год.
Gам.
= 52000×7/1000=365 кг/год.
Gс
=52000×16/1000=832 кг/год.
Gп.о.
= 52000×0,4/1000=20,8 кг/год.
Об’єм складових коксового газу розраховую за формулою:
Vi
=Gi
×22,4/M(5.2)
де Gi
-кількість компонента
Mi
-молекулярна масса компонента
Vв
= Gв
×22,4/Мв
=1560×22,4/18=1941,3м3
/год
Vб
= Gб
×22,4/Мб
=1872×22,4/83=505,2м3
/год
Vс
= Gс
×22,4/Мс
= 832×22,4/34=548,1м3
/год
Vа
= Gа
×22,4/Ма
=365×22,4/17=480,9м3
/год
Vп
= Gп
×22,4/Мп
=20,8×22,4/80=6м3
/год
Об’єм сухого коксового газу розраховую за формулою:
(5.3)
де Vк.г.
- об’єм коксового газу, м3
/год,
- сума кількості компонентів коксового газу.
Vс.г.
= 52000-(1941,3+505,2+548,1+480,9+6)=48518,5 м3
/год.
Gс.г.
= ρс.г
×Vс.г.
(5.4)
де ρс.г.
– густина сухого коксового газу кг/м3
,ρс.г
=0,401 кг/м3
[1]
Vс.г.
– об’єм сухого коксового газу м3
/год.
Gс.г.
=0,401×48518,5=19456 кг/год
У абсорбер надходить наступна кількість коксового газу з нагнітача (табл.5.1).
Таблиця 5.1 Склад коксового газу, що входить до абсорбера
Компоненти |
кг/год |
м3
/год |
Сухий коксовий газ, Gг
|
19456,0 |
48518,5 |
Водяні пари, Gв
|
1560,0 |
1941,3 |
Бензольні вуглеводні, Gб
|
1872,0 |
505,2 |
Сірководень, Gс
|
832,0 |
548,1 |
Аміак, Gа
|
365,0 |
480,9 |
Піридинові основи, Gп
|
20,8 |
6,0 |
Всього |
24105,8 |
52000,0 |
Кількість сірчаної кислоти, яка необхідна для нейтралізації 365 кг/год аміаку розраховуємо за рівнянням хімічної реакції, на основі закону еквівалентів:
2NН3
+ Н2
SO4
= (NН4
)2
SO4
(5.5)
За умовою νNH
3
=mNH
3
/MNH
3
=365000/17=21470,6 моль/год
де mNH
3
- маса аміаку, що поступає в абсорбер з газом 365кг/год=365000 г/год;
MNH
3
-молекулярна масса аміаку 17 г/моль
Відповідно до рівняння реакції 1 моль Н2
SO4
реагує з 2 моль NН3
, а з 21470,6 моль/годNН3
реагують 10735,3 моль Н2
SO4
або 10735,3×98=1052059,4 г/год=1052,1 кг/год
Кількість 92,5 %-ої кислоти:
GH
2
SO
4
=1052,1 /0,925=1137,4 кг/год.
Кількість поглинутого аміаку на першому ступеню абсорберу можна визначити виходячи з умови рівняння поверхні контакту чи об’ємів обох ступенів абсорберів та коефіцієнтів абсорбції, що приводить до рівняння:
(5.6)
де а1
, а2
,та а3
– вміст аміаку у газі до першої,до другої та після другої ступені абсорберу.
Величина а1
дорівнює 7 г/м3
Величину a3
приймаюзгідно ПТЕ0,03 г/м3
. [2]
Тоді
 =
Таким чином, на першому ступені абсорберу поглинається аміаку

Залишається аміаку в коксовому газі :

Надходитьаміаку на другу ступінь 365-340 =25 кг/год та поглинається аміаку на другій ступені 25-1,6=23,4 кг/год.
Для поглинання 340 кг/год аміаку на першому ступеню абсорберу необхідно витратити сірчаної кислоти у моногідраті [6]:
(5.7)
де - кількість аміаку, яка поглинається на першому ступеню абсорберу
- молекулярна маса сірчаної кислоти
- молекулярна маса аміаку.
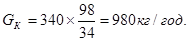
При цьому утворюється сульфату амонію 340+980=1320 кг/год.
На другому ступеню поглинається аміаку 23,4 кг/год, витрачається сірчаної кислоти :
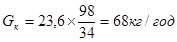
та утворюється сульфату амонію 23,6+68=91,6 кг/год.
Таким чином, накопичується сульфату амонію у матковому розчині на другому ступені абсорберу 91,6 кг/год.
Загальна кількість сульфату амонію, яка утворюється 1320+91,6=1411,6 кг/год, а з вологістю 2% .
5.1.1 Кількість розчину, що перетікає з абсорберу другого ступеня в абсорбер першого ступеня
Ця кількість повинна бути такою, щоб вивести у перший ступінь абсорберу сульфат амонію у кількості, що утворюється на другому ступені абсорбції.
Кількість сульфату амонію, що утворюється на другому ступені, як вказано вище, дорівнює 91,6 кг/год.
Так як розчин, що перетікає, містить 28% (NH4
)2
SO4
[6], то кількість цього розчину буде дорівнювати:
Gр
= чи за об’ємом Vр
= .
Таким чином, розчин, що перетікає містить, кг/год:
Сульфату амонію …327×0,28=91,6
Сірчаної кислоти…. 327×0,12=39,2
Води за різницею ……..……..196,2
Всього …………….327,0
5.1.2 Кількість розчину, що виводиться з першого ступеня абсорберу у випарник
Кількість розчину, що виводиться у випарник, має бути таким, щоб після випару води і виділення всього сульфату амонію, що виробляється, залишився насичений розчин сульфату амонію визначеної концентрації. [6]
Кількість розчину, що виводиться з першого ступеня абсорбера у випарник, визначаю таким чином.
Позначаю кількість цього розчину через Gі вміст в ньому сульфату амонію 40% та Н2
SO4
1%. Тоді в ньому міститься сульфату амонію 0,4Gкг/год.
Після випару Wкг/год води у випарнику в центрифугу входить пульпа в кількості (G– W) кг/год, в якій знаходиться 0,4Gкг/год сульфату амонію.
Після видалення вологого сульфату амонію в центрифузі у кількості 1411,6/0,98 = 1440,4 кг/год (де 0,98 - вміст сухого сульфату амонію) залишиться маткового розчину (G- W– 1440,4), з них сульфату амонію (0,4G– 1411,6).
Оскільки вміст сульфату амонію в матковому розчині після центрифуги дорівнює 47%, тому можна скласти рівняння:
(5.8)
Кількість води, що видаляється у випарнику, можна визначити по наступній формулі [6] :
(5.9)
де С0
- вміст (NН4
)2
SO4
у сульфаті амонію, що виробляється, С0
= 98%;
С1
- те ж, в пульпі після випарника; приймаємо, що пульпа містить 50% по масі солі, що викристалізувалася, а насичений матковий розчин містить 47% сульфату амонію; тоді С1
= 50 + 0,5×47 = 73,5%;
С2
- те ж, в матковому розчині після центрифуги, С2
= 47%;
С3
- те ж, в розчині, що виводиться з першого ступеня абсорбції у випарник, С3
= 40%;
Gс
- кількість вологого сульфату амонію, кг/ч, що виробляється.
Тоді
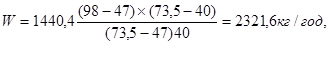
Підставляючи W, отримав з рівняння 5.8
0,4×G– 1411,6=0,47×(G- 2321,6 – 1404,4).
0,47×G-0,4×G+1411,6 – 1091,2 – 677=0
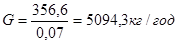
чи при густині розчину 1,24 кг/л об’єм розчину дорівнює:

Таким чином, у розчині,який спрямовується у випарник, міститься, кг/год:
Сульфату амонію ………...0,4×5094,3=2037,7
Сірчаної кислота …………..0,01×5094,3=50,9
Води за різницею…………….………….3005,7
Всього …………………5094,3.
З цієї кількості розчину, спрямованого у випарник, після випару води у кількості 2321,6 кг/год і відділення вологого сульфату амонію в центрифузі у кількості 1440,4 кг/год (з них сухого 1411,6 кг/год і волога 28,8 кг/год) залишиться маткового розчину 5094,3 – 2321,6 – 1440,4 =1332,3 кг/год.
Після додавання промивної води у кількості 95 кг/год повертається маткового розчину у збірник першого ступеня абсорбції 1332,3 + 95 = 1427,3 кг/год.
Склад цього розчину та кількість наступні
Сульфату амонію …………….…2037,7– 1411,6=626,1
Сірчаної кислоти ………………………….…………50,9
Води за різницею…..3005,7 – 2321,6 – 28,8 + 95=750,3
Всього ……………….………………...1427,3
5.2 Матеріальний та тепловий баланси абсорбера першого ступеня
Прихід. 1. Коксовий газ.
Склад та кількість коксового газу, який надходить із нагнітача у абсорбер першого ступеня наведено у таблиці 5.1.
2. В абсорбер поступає циркулюючий розчин зі збірника першого ступеня абсорбера. Позначимо цю кількість через G1
.
Таким чином, загальний прихід рівний:
24105,8+ G1
кг/год. (5.10)
Витрата.1. Коксовий газ.
З тих, що були в коксовому газі 365 кг/год аміаку поглинається 340 кг/год і залишається в газі 25 кг/год.
Кількість водяної пари, що виходить з газом з першого ступеня абсорбції, можна визначити виходячи з того, що за рахунок тепла нейтралізації відбувається нагрів газу до 58°С, тобто до температури розчину, що поступає, і випар відповідної кількості води. Позначаю цю кількість через GВ
:
, (5.11)
де Q1
- тепло, що вноситься коксовим газом, ккал/год;
Q2
- тепло реакції нейтралізації, ккал/год;
Q3
-тепло, що уноситься сухим коксовим газом, ккал/год;
t- температура газу на виході з абсорберу, t=58°C.
Кількість тепла розраховую за формулою:
Q=G×c×t, (5.12)
де G- кількість речовини кг/год;
c- теплоємність речовини кДж/кг×град;
t- температура речовини °С.
Тепло, що вноситься коксовим газомпри 50°С:
а) тепло, що вноситься сухим коксовим газом:
q1
= 19456×2,933×50=2853222,4кДж/год
де 2,933- теплоємність коксового газу, кДж/(кг×град) [6];
б) тепло, що вноситься парами води:
q2
=1560×(2493+1,84×50)=4032600кДж/год;
де 1,84кДж/(кг×град)теплоємність води [6];
в)тепло,що вноситься бензольними вуглеводнями:
q3
=1872×1,03×50=96408 кДж/год;
де 1,03кДж/(кг×град)теплоємність бензольних вуглеводнів [6];
г)тепло, що вноситься сірководнем:
q4
=832×0,997×50=41475,2 кДж/год;
де 0,997кДж/(кг×град)теплоємність сірководню [6];
д)тепло, що вноситься аміаком:
q5
=365×2,11×50=38507,5 кДж/год;
де 2,11кДж/(кг×град)теплоємність аміаку [6];
є) тепло, що вноситься піридиновими основами:
q6
=20,8×1,03×50=1071,2кДж/год;
де 1,03кДж/(кг×град)теплоємність піридинових основ.
Всього вноситься газом:
Q1
=q1
+q2
+qЗ
+q4
+q5
+q6
=2853222,4+4032600+96408+41475,2+38507,5+1071,2= 7063284,3 кДж/год.
Тепло реакції нейтралізації аміаку:
(5.13)
де GК
- кількість сірчаної кислоти кг/год;
MК
– молекулярна маса сірчаної кислоти
iн
– тепло нейтралізації, кДж/кг сірчаної кислоти, iн
=195673 [6].
.
Тепло циркулюючого розчину:
Q3
=G1
×2,933×58 кДж/год.
Тепло, що уноситься сухим коксовим газом при температурі 58°С:
Q4
=(25×2,11+832×0,997+20,8×1,03+1872×1,03+19456×2,933)×58=
3473984,6 кДж/год.
Тоді
.
Об’єм цих парів:
Vв
= Gв
×22,4/Мв
=2188,7×22,4/18=2723,7 м3
/год
Таким чином, загальна кількість газів, що виходять з першого ступеня абсорберу у другу, дорівнює:
кг/год м3
/год
Сухий коксовий газ ……………....…19456,0 48518,5
Бензольні вуглеводні……………..…..1872,0 505,2
Аміак……………………….……....….....25,0 32,9
Сірководень………………………....….832,0 548,1
Піридинові основи………………………20,8 6,0
Водяні пари……….……….…….……2188,7 2723,7
Всього….…….……..24394,5 52334,4
2.Циркулюючий розчин.
Кількість циркулюючого розчину, що виходить з першого ступеня абсорберу, позначимо G2
, кг/год. Тоді спільна витрата дорівнює:
24394,5+G2
. (5.14)
Прирівнюючи прихід та витрату, отримаємо:
24105,8+ G1
=24394,5+ G2
, (5.15)
чи G1
= G2
+288,7.
Друге рівняння для визначення G1
і G2
отримаємо виходячи зі значень концентрацій сірчаної кислоти на вході та виході з першого ступеня абсорбції та кількості сірчаної кислоти, що витрачається, на першому ступені. Приймаємо концентрацію розчину, що надходить 1,6% і 1% розчину, що виходить, отримаємо рівняння:
, (5.16)
де Gк
- кількість кислоти, що витрачається в першому ступені абсорбера, кг/год.
Для зв'язування в першому ступені абсорбера 340 кг/год аміаку необхідно витратити сірчаної кислоти 980 кг/год.
Тому Gк
= 980 кг/год.
Таким чином, 1,6×G1
=G2
+98000.
Отримав систему рівнянь:
(5.17)
У результаті вирішення двох рівнянь отримав G1
=162852,2 кг/год та G2
=162563,5 кг/год.
Об’єм розчину, що поступає при густині 1,24 кг/л буде дорівнювати
Vр
= .
Матеріальний баланс першого ступеня абсорбції (табл.5.2), кг/год:
Таблиця 5.2 Матеріальний баланс першого ступеня абсорбції
Прихід |
Витрата |
Коксовий газ |
24105,8 |
Коксовий газ |
24394,5 |
Циркулюючий розчин |
162852,2 |
Циркулюючий розчин |
162563,5 |
Всього |
186958,0 |
Всього |
186958,0 |
Тепло циркулюючого розчину, що входить в абсорбер:
Q3
=162852,2 ×2,933×58=27703439,2 кДж/год.
Тепло, що уноситься коксовим газом при температурі 58°С:
Q5
=3473984,6+(2493+1,84×58)×2188,7=9163991,8 кДж/год.
Тепло циркулюючого розчину, що виходить з абсорбера:
Q6
=162563,5×2,933×t=476798,7×tкДж/год.
Тепловий баланс першого ступеня абсорбції наведено у таблиці 5.3, кДж/год:
Таблиця 5.3 Тепловий баланс першого ступеня абсорбції
Прихід |
Витрата |
Тепло коксового газу |
7063284,3 |
Тепло коксового газу |
9163991,8 |
Тепло нейтралізації |
2100689,4 |
Втрати тепла зовні (за практичними даними) |
167600,0 |
Тепло циркулюючого розчину |
27703439,2 |
Тепло циркулюючого розчину |
476798,7×t |
Всього |
36867412,9 |
Всього |
9331591,8+
+476798,7×t
|
Прирівнюючи прихід та витрату тепла, отримав температуру розчину, який виходить з першого ступеня абсорберу, що дорівнює 57,8°C, тобто приблизно таку ж, як і поступаючого.
5.3 Матеріальний та тепловий баланси збірника першого ступеня
5.3.1 Матеріальний розрахунок
Прихід. У збірник абсорбера першого ступеня поступають: циркулюючий розчин з абсорбера, матковий розчин з центрифуги, переток з другого ступеня абсорбера, сірчана кислота, вода для поповнення циклу.
Визначимо кількість цих потоків :
1. Кількість розчину, що поступає з першого ступеня абсорбера, дорівнює:
G1
=162563,5 – 5094,3=157469,2 кг/год
2.Кількість маткового розчину, що поступає з центрифуги, дорівнює:
1427,3 кг/год.
3. Кількість розчину, що поступає з другого ступеня абсорбера (переток), дорівнює 327 кг/год.
4.Кількість кислоти, що поступає, позначимо х1
.
5.Кількість води для поповнення циклу позначимо у1
.
Загальний прихід дорівнює 159223,5 + х1
+ у1
.
Витрата. Кількість розчину, що виводиться зі збірника в циркуляцію, дорівнює 162852,2 кг/год.
Прирівнюючи прихід і витрату, отримаємо:
х1
+ у1
=3628,7
Для визначення х1
і у1
складаю баланс моногідрату сірчаної кислоти.
Прихід:
З кислотою при концентрації, рівною 92,5%.......0,925× х1
з матковим розчином з центрифуги . . ……………..…50,9
У перетоку з 2-го абсорбера ………………………..…39,2
Всього………….……0,925× х1
+90,1
Витрата:
У розчині, що йде у випарник………………….……50,9
На реакцію з NH3
у першому ступеню ……………980,0
Всього…………...1030,9
Прирівнюючи прихід і витрату, отримаємо 0,925× х1
+90,1=1030,9.
Звідси кількість розчину кислоти х1
= 1017,1 кг/год, з них: моногідрату 1017,1×0,925= 940,8 і води 76,3 кг/год.
Кількість води, необхідної для поповнення циклу :
y1
=3628,7 – 1017,1=2611,6кг/год.
5.3.2 Тепловий баланс збірника першого ступеня
Прихід. 1. Тепло, внесене циркулюючим розчином:
Q1
=157469,2×2,933×57,8=26695344,1кДж/год.
2. Тепло, внесене матковим розчином при 50°С:
Q2
=1427,3×2,68×50=191258,2кДж/год,
де 2,68 - теплоємність маткового розчину, кДж/(кг×град).[6]
3. Тепло, внесене перетоком розчину з другого ступеня абсорбера :
Q3
=327×3,31×50=54118,5 кДж/год
де 3,31 - теплоємність цього розчину, кДж/(кг×град).[6]
4.Тепло, внесене кислотою:
Q4
=1017,1×1,55×20=31530,1 кДж/год,
де 1,55 - теплоємність сірчаної кислоти, кДж/(кг×град). [6]
5.Тепло, внесене водою поповнення :
Q5
=2611,6×4,19×20=218852,1кДж/год,
де 4,19 - теплоємність води, кДж/(кг×град).
6.Тепло розбавлення сірчаної кислоти від 92,5 до 1,6%:
кДж/кмоль Н2
SO4
[6]стор 105
де n1
- відношення числа молей води до числамолей кислоти у 1,6%-ій сірчаній кислоті;
n2
- те ж саме, у92,5 %-вій сірчаній кислоті.
(5.18)
де С1
– кількість відсотків води у розчині, С1
=98,4;
С2
– кількість відсотків кислоти у розчині, С2
=1,6;
МК
– молекулярна маса сірчаної кислоти Мк
=98;
МВ
– молекулярна маса води МВ
=18;
;
;(6.19)
де 7,5- кількість відсотків води у розчині;
92,5- кількість відсотків кислоти у розчині;
Тоді:(6.20)
=59723 кДж/моль Н2
SО4
тана940,8 кг/годмоногідрату
Q6
= .
Загальний прихід тепла
Qприх
= Q1
+Q2
+Q3
+Q4
+Q5
+Q6
=26695344,1+191258,2+54118,5+31530,1+
+218852,1+573340,8=27764443,8 кДж/год.
Витрата.1.Тепло, що втрачається зовні (згідно практичних даних):
Q7
=167600 кДж/год.
2.Тепло, що уноситься циркулюючим розчином:
Q8
=162852,2×2,933×tДж/год.
Всього, витрата тепла : 167600+477645,5×t.
Прирівнюючи прихід та витрату
27764443,8 =167600+477645,5×t,
звідси температура розчину, яка встановилася t=58°С.
5.4 Матеріальний та тепловий баланси абсорберу другого ступеня
Прихід. 1. У абсорбер другого ступеня надходить коксовий газ з абсорбера першого ступеня у наступній кількості
кг/год м3
/год
Сухий коксовий газ ……………......19456,0 48518,5
Бензольні вуглеводні……………..….1872,0 505,2
Аміак……………………….……....….....25,0 32,9
Сірководень………………………........832,0 548,1
Піридинові основи……………….……..20,8 6,0
Водяні пари……….……….………….2188,7 2723,7
Всього….…………...24394,5 52334,4
2. Розчин, що циркулює зі збірника другого ступеня. Позначимо цю кількість через G3
. Тоді загальний прихід дорівнює 24394,5+G3
.
Витрата. 1. Коксовий газ.
З тих 25 кг/год аміаку, що були в коксовому газі, поглинається 23,4 кг/год і залишається в газі 1,6 кг/год.
Кількість водяної пари, що виходить з газом з другого ступеня абсорбції Gв
визначаємо виходячи з того, що за рахунок тепла нейтралізації та охолодження газу від температури 58°С до 52°С відбувається випаровування води.
Величина Gв
може бути визначена за рівнянням 5.11
Тепло, що вноситься коксовим газом:
Q1
=9163991,8 кДж/год.
Тепло реакції нейтралізації складає:
Q2
= ,
де 195673-тепло реакції нейтралізації, кДж/кмоль Н2
SO4
.
Тепло, що уноситься сухим коксовим газом:
Q3
=(19456×2,933+1872×1,03+832×0,997+1,6×2,13)×52=3110927кДж/год
Тоді
,
Таким чином, загальна кількість газів, що виходять з другого ступеня абсорбції, дорівнює:
кг/год м3
/год
Сухий коксовий газ …………….......19456,0 48518,5
Бензольні вуглеводні……………..…..1872,0 505,2
Аміак……………………….……......….....1,6 2,1
Сірководень………………………....….832,0 548,1
Піридинові основи………………..….….20,8 6,0
Водяні пари……….……….…….........2377,5 2958,7
Всього….…….……...24559,9 52538,6
2. Циркулюючий розчин
Кількість циркулюючого розчину, що виходить з другого ступеня абсорбера, позначимо G4
кг/год.
Тоді загальна витрата дорівнює 24559,9+ G4
Прирівнюючи прихід і витрату, отримаємо
24394,5+G3
= 24559,9+ G4
чи
G3
= G4
+165,4.
Кількість розчину, що поступає на другий ступінь абсорбера, приймаємо за об'ємом рівним кількості розчину, що поступає на перший ступінь абсорбції, що забезпечує однакову щільність зрошування.
Оскільки об'єм розчину, що поступає на другий ступінь, рівний 131,3 м3
/год, то маса розчину при щільності 1,2 кг/л буде дорівнювати:
G3
= 131,3×1200=157560 кг/год.
Тоді
G4
=157560 - 165,4=157394,6 кг/год.
Матеріальний баланс другого ступеня абсорберу заносимо у таблицю 5.4 , кг/год:
Таблиця 5.4 Матеріальний баланс другого ступеня абсорберу
Прихід |
Витрата |
Коксовий газ |
24394,5 |
Коксовий газ |
24559,9 |
Циркулюючий розчин |
157560,0 |
Циркулюючий розчин |
157394,6 |
Всього |
181954,5 |
Всього |
181954,5 |
Тепло, що уноситься коксовим газом при температурі 52°С:
Q5
=3110927+(2493+1,84×52)×2377,5 =9291761,3кДж/год.
Тепло циркулюючого розчину:
Q6
=157394,6×2,933×t=461638,4×tкДж/год.
Тепловий баланс другого ступеня абсорберу наведено у таблиці 5.5.
Таблиця 5.5 Тепловий баланс другого ступеня абсорберу
Прихід |
Витрата |
Тепло коксового газу |
9163991,8 |
Тепло коксового газу |
9291761,3 |
Тепло нейтралізації |
101630,2 |
Втрати тепла зовні |
125700 |
Тепло циркулюючого розчину |
24030421 |
Тепло циркулюючого розчину |
157394,6×2,933×t=
461638,4×t
|
Всього |
33296043 |
Всього |
9417461,3+461638,4×t |
Прирівнюючи прихід та витрату тепла, отримаємо температуру розчину, який виходить з другого ступеня абсорберу у циркуляцію t=51,7°C
5.5 Матеріальний та тепловий баланси збірника другого ступеня
5.5.1 Матеріальний розрахунок
Прихід. У збірник абсорбера другого ступеня поступають: циркулюючий розчин з абсорбера, сірчана кислота, вода для поповнення циклу.
Визначимо кількість цих потоків :
1. Кількість кислоти, що поступає, позначимо х2
.
2. Кількість розчину, що поступає з абсорберу, дорівнює:
G2
=157394,6 –327=157067,6кг/год.
3. Кількість води для поповнення циклу позначимо у2
.
Загальний прихід дорівнює 157067,6+ х2
+ у2
.
Витрата. Кількість розчину, що виводиться зі збірника в циркуляцію, дорівнює 157560 кг/год.
Прирівнюючи прихід і витрату, отримав:
x2
+ у2
=492,4.
Для визначення х2
і у2
складаю баланс моногідрату сірчаної кислоти.
Прихід:
З кислотою при концентрації, рівною 92,5%.......0,925× х2
Витрата:
Переток розчину на перший ступінь………….………39,2
На реакцію з NH3
у другому ступені ………………....67,4
Всього……..…….....106,6
Прирівнюючи прихід і витрату, отримаємо 0,925× х2
=106,6
Звідси кількість розчину кислоти х2
= 115,2 кг/год, з них: моногідрату 115,2×0,925= 106,6 і води 8,6 кг/год.
Тоді, кількість води, необхідної для поповнення циклу :
y2
=492,4 – 115,2=377,2кг/год.
5.5.2 Тепловий баланс збірника другого ступеня
Прихід. 1. Тепло, внесене циркулюючим розчином:
Q1
=157067,6×3,31×52=27034475,3 кДж/год.
2. Тепло, що вноситься кислотою:
Q2
=115,2×1,55×20=3571,2кДж/год ,
де 1,55 - теплоємність сірчаної кислоти, кДж/(кг×град), 20-температура кислоти °С.
3. Тепло, внесене водою поповнення :
Q3
=377,2×4,19×20=31609,4 кДж/год,
де 4,19 - теплоємність води, кДж/(кг×град).
4. Тепло розбавлення сірчаної кислоти від 92,5 до 12%:
кДж/кмоль
де
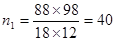
де 88 - кількість відсотків води у розчині;
12 - кількість відсотків кислоти у розчині;
98 - молекулярна маса сірчаної кислоти;
18 - молекулярна маса води;
тана106,6 кг/годмоногідрату
Q4
= .
Загальний прихід тепла
Qприх
=Q1
+Q2
+Q3
+Q4
=27034475,3+3571,2+31609,4+61896,7=27131552,6 кДж/год.
Витрата.1.Тепло, що втрачається зовні (згідно практичних даних):
Q5
=125700кДж/год.
2.Тепло, що уноситься циркулюючим розчином:
Q8
=157560×3,31×t=521523,6×tДж/год.
Всього, витрата тепла : 125700+521523,6×t.
Прирівнюючи прихід та витрату
27131552,6=125700+521523,6×t,
звідси температура розчину, яка встановилася t=52°С.
Баланс кислоти та води поповнення наведено у таблиці 5.6
Таблиця 5.6 Баланс кислоти та води
Компоненти |
Збірник 1 |
Збірник 2 |
Всього |
Разом |
Н2
SО4
|
H2
O |
Н2
SО4
|
H2
O |
Н2
SО4
|
H2
O |
Розчин кислоти |
940,8 |
76,3 |
106,6 |
8,6 |
1047,4 |
84,9 |
1132,3 |
Вода поповнення циклу |
—
|
2611,6
|
—
|
377,2
|
—
|
2988,8
|
2988,8
|
Всього |
940,8 |
2687,9 |
106,6 |
385,8 |
1047,4 |
3073,7 |
4121,1 |
Матеріальний баланс сульфатної установки наведено у таблиці 5.7, кг/год:
Таблиця 5.7 Матеріальний баланс сульфатної установки, кг/год
Прихід |
Витрата |
Коксовий газ:
Сухий коксовий газ
Водяні пари
Бензольні вуглеводні
Сірководень
Аміак
Піридинові основи
|
24105,8
19456
1560
1872
832
365
20,8
|
Коксовий газ:
Сухий коксовий газ
Водяні пари
Бензольні вуглеводні
Сірководень
Аміак
Піридинові основи
|
24559,5
19456
2377,5
1872
832
1,6
20,8
|
Сірчана кислота |
1132,3 |
Сульфат амонію
|
1440,4
|
Промивна вода |
95 |
Вода для поповнення циклу |
2988,8
|
Випаровується води у випарнику |
2321,6 |
Всього |
28321,9 |
Всього |
28321,9 |
5.6 Розрахунок випарника
5.6.1 Матеріальний розрахунок
У випарник поступає розчин з першого ступеня абсорберу наступного складу:
кг/год %
Сульфату амонію………….2037,7 40
Сірчаної кислоти…………......50,9 1
Води………………………...3005,7 59
Всього……5094,3 100
У випарнику випаровується вода у кількості 2321,6 кг/год. Тому з випарника виходить пульпа наступного складу :
кг/год %
Сульфату амонію………….2037,7 73,4
Сірчаної кислоти…………......50,9 1,8
Води……………………….....684,1 24,8
Всього.........2772,7 100
При відділенні кристалів сульфату амонію у кількості 1440,4 кг/год після центрифуги залишиться маткового розчину 2772,7 – 1440,4=1331,8 кг/год.
Склад цього розчину: кг/год %
Сульфату амонію ……..2037,7 – 1411,6=626,1 47,0
Сірчаної кислоти…………...………............50,9 3,8
Води…………………...........684,1 – 28,8=655,3 49,2
Всього……...............1332,3 100
5.6.2 Тепловий розрахунок випарника
Прихід. 1. Тепло, що вноситься розчином при температурі 57,8°С :
Q1
=5094,3×2,933×57,8=863623,4 кДж/год.
2. Тепло кристалізації сульфату амонію
Q2
= ,
де 10894- тепло кристалізації , кДж/моль (NH4
)2
SO4
.[6]
3. Тепло гріючої пари Q3
.
Всього прихід: Qприх.
=980123,2+ Q3
.
Витрата. 1. Тепло, що уноситься пульпою з випарника:
Q4
=(1332,3×2,68+1440,4×1,42)×58=325724,1кДж/год.
2. тепло, що уноситься парами води з випарника :
Q5
=2321,6×4,19×2576,9=25066805,1 кДж/год,
де 2576,9- ентальпія пари,кДж/кг, при тиску у апараті, рівному
760-685=75 мм рт. ст.
3. Тепло концентрування сірчаної кислоти незначне (від 1% до 3,8%), тому ним нехтуємо.
4. Тепло, що втрачається зовні:
Q6
=125700 кДж/год.
Загальна витрата тепла Qвитр.
=25518229,2 кДж/год.
Прирівнюючи прихід та витрату, отримаємо тепло гріючої пари :
980123,2+ Q3
=25518229,2
Q3
=24538106 кДж/год.
Приймаючи пару тиском 1,75 кг/см2
з температурою 115°С та теплотою конденсації 2220,7 кДж/кг, отримаємо витрату пари :

6. Технологічні розрахунки
6.1 Визначення розмірів абсорберів першого та другого ступенів
Кількість газу, який поступає в абсорбер наведено у таблиці 5.1
Об’єм коксового газу визначаю за формулою [6]:
Vк.г
= (6.1)
де G– кількість коксового газу, кг/год;
t– температура коксового газу після нагнітача, приймаю t=50°С;
p– атмосферний тиск, мм рт.ст.;
P– тиск газу перед абсорбером P=960 мм рт.ст.;
Vк.г
=
Приймаємо швидкість газу в абсорбері 4 м/с [6]. Тоді потрібний переріз абсорберу:
, (6.2)
де Vк.г.
-об’єм газу, м3
/год
ν- швидкість газу, м/с;
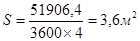
та діаметр абсорберу
D= , (6.3)
де S- переріз абсорберу,м2
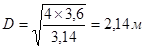
Приймаємо D=2,5 м.
Тоді переріз буде дорівнювати
S=πR2
S=3,14×1,252
=4,9 м2
.
Об’єм абсорберу визначаємо з умов абсорбції аміаку за рівнянням [6] :
, (6.4)
де Vк.г.
- об’єм газу, який поступає, Vк.г.
=51609,4 м3
/год;
К - коефіцієнт абсорбції аміаку сірчаною кислотою у розпилюючих апаратах, за практичними даними К=5000 год-1
;
a1
і а2
- вміст аміаку у газі, що входить та виходить, г/м3
.
Об’єм абсорберу першого ступеня буде дорівнювати:
,
Тоді потрібна висота робочої частини абсорберу першого ступеня [6]
, (6.5)
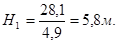
Розміри робочої частини абсорберу другого ступеня абсорбції залишаються такими ж, як і першого ступеня, так як 
де a3
- вміст аміаку в газі, що виходить з другого ступеня абсорбції.
H2
= 5,8 м.
Загальна висота абсорберу
H= H1
+ H2
+ H3
+ H4
де H3
– висота від робочої частини абсорберу до кришки абсорберу, приймаємо =1,25м;
H4
– висота простору від нижньої робочої частини до днища, приймаємо =1,25 м.
H=5,8+5,8+1,25+1,25=14,1 м.
6.2 Визначення поверхні теплопередачі випарника
Поверхню теплопередачі випарника визначаємо за формулою:
, (6.6)
де Q- кількість тепла, що передається ,
Q=Q3
– Q6
Q3
=24538106 кДж/год- тепло граючої пари;
Q6
=125700 втрати тепла зовні.
Q=24538106 - 125700= 24412406 кДж/год;
Δtср
- різниця температур у теплопередачі між парою та розчином, Δtср
=115-58=57°С;
К- коефіцієнт теплопередачі визначаємо за формулою [6]
(6.7)
α1
- коефіцієнт тепловіддачі пари, α1
=41900 кДж/(м2
×год×°С);[6]
δ1
/λ1
- термічний опір стінок трубок; цією величиною нехтуємо;
δ2
/λ2
- термічний опір забруднень, приймаємо рівним 4,773×10-4
м2
×год×°С/кДж;
α2
- коефіцієнт тепловіддачі від стінки до киплячого розчину визначаємо за наближеною формулою :[6]
,(6.8)
тут q- тепловий потік; q=KΔtср
.
Задаємося q=62000 кДж/(м2
×год), [6] тоді
,
і

Перевіряємо значення q:
q=KΔtср
=1085,2×57=62000 кДж/(м2
×год),
тобто α2
та К розраховані правильно.
Необхідна поверхня теплопередачі
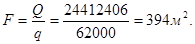
Приймаємо трубки діаметром 57/ 4 мм та довжиною 2,5м.
Тоді необхідна кількість трубок
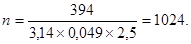
Приймаємо 1027 трубок, що розміщені на 18 шестикутниках.
Тоді діаметр трубчатки буде дорівнювати:
D=2×(xt+t′), (6.9)
де x- число шестикутників x=18;
t- шаг розміщення трубок, t=1,4 d=1,4×0,057=0,08 м;
t′- відстань від кожуху, t′=0,06 м.
Тоді
D=2×(18×0,08+0,06)=3 м.
Асорбер.
При безсатураторному методі отримання сульфату амонію очищення газу від аміаку здійснюють в двоступінчатому абсорбері зрошувального типу.
Корпус апарату складається з циліндричної обичайки 4, конічного днища 5 і кришки 1. Внутрішній простір апарату розділений на дві секції за допомогою кільцевої перегородки з обичайкою 10, у верхній частині якої змонтована (суворо горизонтально) ковпачкова барботажна тарілка з кільцевим переливанням на рівні кромок обичайки 10. Штуцери 3, а також встановлені над ними ковпаки 11 мають трапецеїдальну форму і на тарілці розташовані радіально.
Усередині обичайки 10 встановлений краплевідбійник 9, виконаний із зігнутих смуг листового матеріалу. Верхня і нижня секції абсорбера обладнані індивідуальними системами зрошування і виконують функції першого і другого ступеня абсорбції аміаку. Нижня секція (перший ступінь) обладнана двома ярусами форсунок 8 по шість штук в кожному. Верхня секція (другий ступінь) має один ярус форсунок 12, крім того, уздовж осі апарату розташована форсунка 13 з крупнокаплевим зрошуванням призначена також для зменшення бризкоуносу газовим потоком. Верхня секція обладнана люками 2.
Коксовий газ поступає в нижню секцію апарату через патрубок 7, промивається кислим розчином циркуляційного циклу першого ступеня абсорбції за допомогою форсунок 8, потім звільняється від бризок розчину в краплевідбійнику 9 і поступає в штуцери 3 ковпачкової тарілки, яка заповнена рідиною до рівня кромок обичайки 10. При цьому в нижній секції абсорбера з газу витягається близько 95 % аміаку, що міститься в ньому.
Циркулюючий розчин кислотністю близько 1 % після контакту з газом поступає в конічне днище 5 і виводиться через патрубок 6.
Вхід газу у верхню секцію абсорбера здійснюється в режимі барботажу завдяки наявності занурених в рідину ковпаків 11. Далі газ піддається повторному контакту з рідкою фазою в режимі зрошування за допомогою форсунок 12 і 13. В процесі рециркуляції в контурі зрошувальної системи другого ступеня розчину кислотністю 10-12% з газу витягаються залишки аміаку і легкі піридинові основи. Очищений коксовий газ виводиться з абсорбера через патрубок 14, а розчин накопичується в кільцевому проміжку між стінками абсорбера і обичайки 10 і виводиться через патрубок 15.
Випарник
Отримання кристалічного сульфату амонію шляхом переробки ненасиченого маточного розчину, що виводиться з першого ступеня аміачного абсорбера, здійснюється у випарному кристалізаторі .
Корпус апарату має циліндричну форму. Порожниста частина його складається з секцій 3 і 4 різнихдіаметрів, причому секція 3 частково заповнюється розчином, рівень якого візуально контролюється за допомогою оглядових вікон 10. Секція 3 стикується за допомогою фланцевого з'єднання з верхніми трубними гратами нагрівача 1, в центральній частині якого розташована циркуляційна труба 2, а в периферійній частині - вертикальна трубчатка. Верхня частина нагрівача 1 обладнана кільцевим колектором з патрубком 7 для подачі гріючої пари, а в нижній частині встановлений патрубок 9 для виведення конденсату. Нижні трубні грати нагрівача 1 за допомогою фланцевого з'єднання стикується з конічним днищем, у якомує
люк - лаз, патрубок 5 для подачі живлячого розчину і труба 6для виведення готової суспензії.
Секція 4 забезпечена системою краплевідбіюу вигляді похило встановлених полиць і патрубком 8 для виведення вторинної пари.
В процесі роботи у випарному кристалізаторі підтримується постійний рівень розчину шляхом регулювання витрати живлячого розчину на вході в патрубок 5. У зоні конічного днища апарату живлячийрозчин змішується з, циркулюючим розчином, що поступає з труби 2.
Циркулюючий розчин містить кристалічну фазу і на виході з труби 2 має залишкове пересичення, яке знижується або повністю знімається в результаті змішення з живлячим розчином. Після змішення розчин поступає в трубчатку нагрівача 1.
В результаті конденсації пари в міжтрубному просторі нагрівача 1 розчин, що знаходиться в трубчатці, отримує відповідну кількість тепла. Залежно від висоти рівня розчину над верхніми трубними гратами, який визначає величину гідростатичного тиску рідини у верхній частині трубчатки, отримуване розчином тепло витрачається в певному співвідношенні на підвищення його температури або на випар водибезпосередньо у трубчатці. Ця обставина визначає два можливі режими роботи нагрівача 1: при збільшеному рівні розчину в апараті в трубчатці переважає режим конвективного підігрівання розчину з подальшим його кипінням поза трубчаткою у міру підйому розчину і зниження гідростатичного тиску; при мінімальному рівні розчину відносно верхніх трубних грат процес теплопередачі супроводжується кипінням розчину безпосередньо в трубчатці.
У другому випадку можливий форсований режим роботи апарату при високих теплових навантаженнях, оскільки кипіння розчину в трубчатці істотно інтенсифікує тепловіддачу. Проте при такому режимі зростає вірогідність пристінкового солеутворення в трубчатці, а також надмірного зародкоутворення при підвищеному пересиченні розчину. Оптимальний режим роботи нагрівача 1 припускає забезпечення таких умов випарної кристалізації , які гарантують отримання великокристалічного продукту при безперервній роботі апарату між його промиваннями впродовж 3 діб.
Кипіння розчину в периферійній частині перерізу апарату супроводжується його пересиченням і створює низхідний потік в трубі 2 і висхідний в трубчатці нагрівача 1, тобто циркуляцію суспензії кристалів по замкнутому контуру. Багатократне проходження кристалів через зону утворення пересичення (зону кипіння) забезпечує їх ріст і накопичення маси твердої фази в циркуляційному контурі. Безперервне виведення суспензії з постійною об'ємною швидкістю по трубі 6 забезпечує постійність маси твердої фази у випарному кристалізаторі на оптимальному рівні.
Парова фаза, що утворилася в процесі кипіння розчину проходить крапле відбійну секцію 4, де звільняється від бризок розчину, що виносяться, і виводиться через патрубок 8 на конденсацію. Для зниження температури кипіння розчину у випарному кристалізаторі підтримується відповідний вакуум.
7. Механічні розрахунки
7.1
То
в
щина
обичайки
Товщина обичайки визначається за формулою [16]
(7.1)
деp- тиск у апараті, н/м2
D- діаметр апарату, м
[s] = 137МН/м2
–напряження, що допускається[16 c394];
j = 0,8 – коэффициент ослаблення з-за зварного шву[16];
Ск
= 0,001 м – поправка на коррозию[16].
Приймаю S=0,008 м.
7.2 Днище
Товщина конічного днища розраховується за формулою [16]
(7.2)
деp- тиск у апараті, н/м2
;
D- діаметр апарату, м;
s = 137МН/м2
–напряження, що допускається[16 c394];
j = 0,8 – коэффициент ослаблення з-за зварного шву;
Ск
= 0,001 м – поправка на коррозию;
α=60° кут при вершині
Приймаю Sд
=0,007 м.
Обираю днище по ГОСТ 12621– 78[17], товщина стінки Sд
=0,007 м
Маса днища mд
= 133,5 кг.
Об’єм днища Vд
= 0,18 м3
.
7.3 Штуцери
Діаметр штуцерів розраховується заформулою:
, (7.3)
деG - масова витрата речовини в секунду, м3
/год;
ρ -густина речовини,кг/м3
;
υ- швидкість руху речовини в штуцері, м/с.
Приймаємо швидкість рідини в штуцері υ = 1 м/с, а для газуυ = 25 м/с, тоді:
діаметр штуцеру для входу і виходу газу
;
приймаємо 1000 мм,
діаметр штуцеру для входу і виходу циркулюючого маткового розчину
,
приймаємо 250 мм.
Всі штуцера забезпечуються плоскими приварними фланцями по ГОСТ 12820-80 [18], параметри яких наведено у таблиці 7.3.1 та на рисунку 7.3.1:
Таблиця 7.3.1 Параметри фланців
Dу
|
dн |
dв |
b |
маса, кг |
250 |
273 |
273 |
18 |
6,95 |
1000 |
1020 |
1020 |
25 |
52,58 |

Рисунок 7.1 Фланець
7.4 Розрахунок опори
Апарати вертикального типу із співвідношенням Н/D > 5, розміщувані на відкритих майданчиках, оснащують так званими юбочними циліндричними опорами.
Орієнтовна маса апарату.
Маса обичайки
, (7.4)
де Dн
=2,516 м - зовнішній діаметр колони;
Dвн
= 2,5 м - внутрішній діаметр колони;
Ноб
= 19,2 м - висота циліндричної частини колони;
ρ = 7900 кг/м3
– густина стали
mоб
= 0,785(2,5162
-2,52
)×19,2×7900 = 9556 кг
Загальна маса колони. Приймаємо, що маса допоміжних пристроїв (штуцерів, вимірювальних приладів, люків і так далі) складає 10% від основної маси колони, тоді
mк
= mоб
+ mд
= 1,1(9556+133,5 кг) = 10658,5 кг
Максимальна вага колони:
mmax
= mк
+ mф
= 10658,5 +20000 =30658,5 кг = 0,307 МН
Приймаємо внутрішній діаметр опорного кільця D1
= 2,44 м, зовнішній діаметр опорного кільця D2
= 2,64 м.
Площа опорного кільця:

Питоме навантаження опори на фундамент
σ = Q/A = 0,307/0,8 = 0,38 МПа < [σ] = 15 МПа - для бетонного фундаменту.
Список літератури
1. Ковалев, Е.Т. Справочниккоксохимика. В 6 т. Т 3. Улавливание и переработка химических продуктов коксования / Евгений Ковалев.- Харьков: Издательский Дом «ИНЖЭК», 2009. – 432 с.
2. Белицкий, А.Н. Правила технической эксплуатации коксохимических предприятий / А.Н. Белицкий [и др.]– М.: Металлургия, 1985.- 248 с.
3. Кауфман, А.А. Технология коксохимического производства : учебное пособие / А.А. Кауфман, Г.Д. Хармалпович - Екатеринбург: ВУХИН-НКА, 2005.- 288 с.
4. Гребенюк, А.Ф. Улавливание химических продуктов коксования : учебное пособие. В 2ч. Ч 1. / А.Ф. Гребенюк [и др.].- Донецк: «Восточный издательский дом», 2002. – 228 с.
5.Лейбович, Р.Е. Технология коксохимического производства : ученик для техникумов / Р.Е. Лейбович [и др.] : М. : Металлургия , 1982.- 360 с.
6. Коробчанский, И.Е. Расчеты аппаратуры для улавливания химических продуктов коксования / И.Е. Коробчанский, М.Д. Кузнецов : Изд-во «Металлургия», 1972. – 296 с.
7. Шелков, А.К. Справочниккоксохимика. В 6 т. Т 3. Улавливание и переработка химических продуктов коксования / А.К. Шелков – М.: Издательство «Металлургия» 1966. – 394 с.
8. Кокс и химия : научно-технический и производственный журнал. Влияние добавок на расыпчатость сульфата аммония / М.: «Металлургия». – 1988, сентябрь - № 9.
9. Кокс и химия : научно-технический и производственный журнал. Возможность повышения рассыпчатости сульфата аммония / М.: «Металлургия». – 1987, август - № 8.
10. Кокс и химия : научно-технический и производственный журнал. Улучшение качества сульфата аммония / М.: «Металлургия». – 1988, май - №5.
11. ТУ У 40.2-05393085-001-2003. Газ коксовый неочищенный. Технические условия с зим 1,2. – Введ. 2009-09-21
12. ГОСТ 2184-77 . Кислота серная техническая. Технические требования. – Введ.1978-07-01. – М.: ИПК Изд-во стандартов, 2003. – 21 с.
13. ТУ У 24.1-00190443-067:2007 Амония сульфат коксохимического производства. Технические условия. – Введ.2008-01-01.
14. ТУ У 23.1-05393085-002-2004 Смолка кислая сульфатного отделения. Технические условия с зим. 1. –Введ. 2004-05-14.
15. Башлай, З.И. Оборудование цехов улавливания и переработки продуктов коксования : Справочник / З.И. Башлай [и др.]– М.:Металлургия , 1992. – 256 с.
16. Борисов, Г.С. Основные процессы и аппараты химической технологии: Пособие по проектированию / Г.С. Борисов [и др.] - М.: Химия,1991. -496 с.
17. Михалев, М.Ф. Расчет и конструирование машин и аппаратов химических производств : Примеры и задачи / М.Ф. Михалев – Ленинград «Машиностроение», 1984. – 150 с.
18. ГОСТ 12621-78. Днища конические неотбортованные. Основные размеры. – Введ. 1979-01-01. – М.: Комитет стандартизации и метрологии СССР, 1978. – 3 с.
19.ГОСТ 12820-80. Фланцы стальные плоские приварные. Конструкция и размеры. – Введ. 1983-01-01.– М.: ИПК Изд-во стандартов, 2003. – 40 с.
20.СанПиН 2.2.1/2.1.1.1200-03.Санитарно-защитные зоны и санитарная классификация предприятий, сооружений и иных объектов. 2004. – 48с.
21. СНиП II-89-80. Генеральные планы промышленных предприятий.– Введ.1982-01-01. Госстрой СССР. – ЦНИИпромзданий.
22. СНиП 2.05.02-85.Автомобильные дороги.- Введ.1987-01-01. Госстрой СССР.
23. ГОСТ 12.1.005-88. ССБТ. Общие санитарно-гигиенические требования к воздуху рабочей зоны. – Введ. 1989-01-01.– М.: ИПК Изд-во стандартов, 1998. – 50 с.
24. ГОСТ 12.1.007-76. Вредные вещества. Классификация и общие требования. – Введ. 1977-01-01.– М.: ИПК Изд-во стандартов, 2007. – 7 с.
25. ГОСТ 12.0.003-74. Опасные и вредные производственные факторы. – Введ. 1976-01-01.– М.: ИПК Изд-во стандартов, 1999. – 3 с.
26. Макаров, Г.В.Охрана труда в химической промышленности/ Г.В. Макаров [и др.]– М.: Химия, 1989. – 496 с.
27. СНиП 11-4-79. Естественное и искусственное освещение.Госстрой СССР – М.: Стройиздат. 1980. – 48 с .
28. ГОСТ 12.1.001-91. Пожарная безопасность. Общие требования.– Введ. 1992-07-01.– М.: Стандартинформ, 2006. – 68 с.
29.РД 34.21.122-87Инструкция по проектированию и устройству молниезащиты зданий и сооружений. Введ. 1988-07-01.– Государственный научно-исследовательский энергетический институт им. Г М. Кржижановского Минэнерго СССР.
30. СНиП 2.04.02-84. Водоснабжение. Наружные сети и сооружения.- Введ.2000-04-01.СоюзводоканалНИИпроект.
31. Правила устройства электроустановок (ПУЭ-2009) Украина. Х.: Изд-во «Форт», 2009. – 726 с.
32.ДНАОП 0.00-1.32-01Правила устройства электроустановок.Электрооборудование специальных установок. Киев 2001.
33. Бабіченко, В. І. промислові засоби автоматизації. Ч. 1. Вимірювальні пристрої / В.І. Бабіченко [и др.] :Навч.посібник. – Харків:НТУ «ХПІ», 2001 р. – 470 с.
34. Тематический каталог. Метран. Датчики давления. – 2009. – 312с.
35. Тематический каталог. Метран. Уровнемеры. – 2009. – 187с.
36. Методичні вказівки до виконання розділу АСК ТП дипломного проекту для студентів V–VIкурсів спеціальностей7.091600Технологія жирів та жирозамінників. 7.051401Біотехнологія. 7.091700Харчові добавки та компоненти / Укл.: О. Ф. Шуть, О. Ю. Олійник, Н. С. Петрова. – Дніпропетровськ: УДХТУ, 2010. – 28 с.
37. Методичні вказівки до виконання організаційно-економічної частини дипломного проекту студентів V–VIкурсів та курсової роботи з курсу «Економіка хімічної промисловості» для студентів IVкурсу спеціальності 7.091604 (ХТП) / Укл. І.В. Багрова, Т.С. Яровенко. – Дніпропетровськ ДВНЗ УДХТУ, 2008. – 26 с.
|