Министерство образования и науки Украины
Национальный горный университет
Кафедра обогащенияполезных ископаемых
Индивидуальное задание
по дисциплине
«Гравитационные методы обогащения полезных ископаемых»
на тему;
Расчет теоретического баланса продуктов
обогащения угля
Выполнила:
ст. гр. ГТЗ-07
Мироненко Анна
Проверила:
Машкова Т.Ю.
Днепропетровск
2008
Содержание
Введение
1.Сырьевая база
2.Обработка исходных данных
2.1Обработка результатов ситового анализа углей шахт
2.2Выбор машинных классов
2.3Обработка результатов фракционного анализа углей шахт
3.Теоретический баланс продуктов обогащения
Список литературы
Введение
уголь обогащение шихта
Уголь является одним из основных источников тепловой и электрической энергии, а также технологическим сырьем для восстановительных процессов в черной и цветной металлургии, при химической обработке и производстве искусственных абразивных материалов.
Уголь занимает и будет занимать большой удельный вес в топливном балансе страны.
Угли отличаются большим разнообразием, обусловленным составом и свойствами исходного растительного материала, условиями и степенью изменений.
В зависимости от назначения все угли подразделяются на:
- энергетические угли;
- коксующиеся (технологические) угли.
Основными требованиями, предъявляемыми к концентратам коксующихся углей, являются:
- зольность ≤ 8,5%;
- содержание влаги – 12% в летнее время и 9% в зимнее время;
- содержание серы – 1,4-1,6%.
Основными требованиями, предъявляемыми к концентратам энергетических углей, являются:
- зольность ≤ 35%;
- содержание влаги – 16% в летнее время и 9% в зимнее время;
- предельное содержание минеральных примесей – 2,5%.
Детальное изучение вышеперечисленных параметров и свойств углей является определяющим при выборе схем и методов обогащения углей и направлений рационального использования продуктов обогащения.
1
.
Сырьевая база
Таблица 1
Результаты ситового анализа угля шахт №1 и №2
Класс
крупности, мм
|
Шахта №1 |
Шахта №2 |
Выход γ, % |
Зольность Аd, % |
Выход γ, % |
Зольность Аd, % |
1 |
2 |
3 |
4 |
5 |
-100+50 |
22,80 |
41,90 |
20,00 |
25,7 |
-50+13 |
10,30 |
25,59 |
8,50 |
18,9 |
-13+6 |
21,00 |
21,36 |
6,30 |
16,9 |
-6+3 |
24,50 |
19,94 |
37,00 |
15,9 |
-3+0,5 |
11,60 |
18,25 |
17,80 |
13,1 |
-0,5+0 |
9,80 |
24,20 |
10,40 |
14,2 |
Итого: |
100,00 |
26,05 |
100,00 |
17,5 |
Таблица 2
Результаты фракционного анализа угля шахты №1
Плотность
фракций, г/см3
|
-100+50 |
-50+13 |
-13+6 |
-6+0,5 |
γк, % |
Аd, % |
γк, % |
Аd, % |
γк, % |
Аd, % |
γк, % |
Аd, % |
1 |
2 |
3 |
4 |
5 |
6 |
7 |
8 |
9 |
<1,3 |
21,60 |
4,10 |
48,90 |
3,60 |
45,00 |
5,90 |
56,00 |
5,10 |
1,3-1,4 |
12,10 |
9,40 |
12,10 |
4,00 |
21,40 |
7,20 |
14,00 |
6,10 |
1,4-1,5 |
7,30 |
17,70 |
5,00 |
22,10 |
9,60 |
18,00 |
6,30 |
19,20 |
1,5-1,6 |
3,90 |
26,50 |
2,50 |
35,20 |
2,50 |
28,30 |
3,50 |
28,20 |
1,6-1,8 |
6,10 |
27,60 |
2,50 |
42,50 |
3,60 |
35,10 |
2,80 |
39,30 |
>1,8 |
49,00 |
73,20 |
29,0 |
70,00 |
17,90 |
75,20 |
17,40 |
71,20 |
Итого: |
100,0 |
41,90 |
100,0 |
25,59 |
100,0 |
21,36 |
100,0 |
19,40 |
Таблица 3
Результаты фракционного анализа угля шахты №2
Плотность
фракций, г/см3
|
-100+50 |
-50+13 |
-13+6 |
-6+0,5 |
γк, % |
Аd, % |
γк, % |
Аd, % |
γк, % |
Аd, % |
γк, % |
Аd, % |
1 |
2 |
3 |
4 |
5 |
6 |
7 |
8 |
9 |
<1,3 |
33,30 |
3,30 |
72,70 |
5,60 |
73,00 |
5,80 |
77,10 |
3,00 |
1,3-1,4 |
15,30 |
7,70 |
3,90 |
8,00 |
5,40 |
7,40 |
5,40 |
7,20 |
1,4-1,5 |
17,20 |
23,90 |
3,90 |
21,00 |
2,70 |
19,00 |
2,10 |
19,90 |
1,5-1,6 |
3,80 |
27,60 |
1,90 |
28,20 |
2,70 |
23,70 |
1,20 |
25,40 |
1,6-1,8 |
4,80 |
38,60 |
1,90 |
35,90 |
2,70 |
40,10 |
1,20 |
38,20 |
>1,8 |
25,60 |
64,00 |
15,70 |
79,30 |
13,50 |
74,20 |
13,00 |
85,30 |
Итого: |
100,00 |
25,67 |
100,00 |
18,87 |
100,00 |
16,89 |
100,00 |
14,97 |
Таблица 4
Результаты дробной флотации угля класса 0-0,5 мм
Время флотации, мин |
γк, % |
Аd, % |
1 |
55,9 |
4,0 |
2 |
20,0 |
10,0 |
3 |
8,6 |
19,6 |
4 |
2,0 |
37,1 |
5 |
2,9 |
49,5 |
6 |
10,6 |
78,1 |
Итого: |
100,0 |
16,4 |
Процент участия в шихте шахты №1 –53%, шахты №2 –47
%.
2
.
Обработка исходных данных
Перед обработкой исходных данных произведена проверка таблиц ситового и фракционного анализов углей шахт: зольность соответствующих классов ситового и фракционного анализов одинакова, итоговые данные таблиц проверены.
Обработка результатов ситового и фракционного анализов углей шахт сводится к получению ситового и фракционного состава принятых машинных классов и построению кривых обогатимости по этим данным.
2.1 Обработка результатов ситового анализа углей шахт
Обработка результатов ситового анализов углей шахт сводится к получению ситового состава шихты (табл.5) и ситового состава машинных классов (табл.6).
Составляем таблицу ситового состава шихты (табл.5).
Графы 2, 4, 5 и 7 заполняем из таблицы 1. Данные граф 3 и 6 подсчитываем по формуле:
,
где γш – выход данного класса ситового анализа шахты к шихте, %;
γ – выход данного класса, %;
η – участие шахты в шихте, доли ед.


Выход классов шихты (графа 8) определяем суммированием выходов к шихте соответствующих классов крупности шахты №1 и №2:

Зольность классов шихты (графа 9) определяем как средневзвешенную зольность соответствующих классов:

Общую зольность шихты определяем как средневзвешенную зольность всех классов шихты:
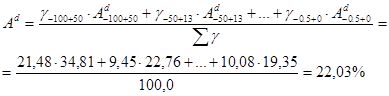
Таблица 5
Ситовый состав шихты
Класс
крупности,
мм
|
Шахта №1 – 88% |
Шахта №2 – 12% |
Шихта |
γ, % |
γ’ш , % |
Аd, % |
γ, % |
γ"ш, % |
Аd, % |
γ, % |
Аd, % |
1 |
2 |
3 |
4 |
5 |
6 |
7 |
8 |
9 |
-100+50 |
22,80 |
12,08 |
41,90 |
20,00 |
9,4 |
25,7 |
21,48 |
34,81 |
-50+13 |
10,30 |
5,46 |
25,59 |
8,50 |
3,99 |
18,9 |
9,45 |
22,76 |
-13+6 |
21,00 |
11,13 |
21,36 |
6,30 |
2,96 |
16,9 |
14,09 |
20,42 |
-6+3 |
24,50 |
12,39 |
19,94 |
37,00 |
17,39 |
15,9 |
30,38 |
17,63 |
-3+0,5 |
11,60 |
6,15 |
18,25 |
17,80 |
8,37 |
13,1 |
14,52 |
15,28 |
-0,5+0 |
9,80 |
5,19 |
24,20 |
10,40 |
4,89 |
14,2 |
10,08 |
19,35 |
Итого: |
100,00 |
53,0 |
26,05 |
100,00 |
47,0 |
17,5 |
100,00 |
22,03 |
2.2 Выбор машинных классов
Выбор машинных классов и шкалы грохочения производят в зависимости от принятого процесса обогащения, нагрузки на обогатительные машины, ГОСТа на сортовое топливо и других факторов.
При обогащении коксующихся углей рекомендуется принимать два машинных класса:
- крупный +10 (13) -75 (100) мм,
- мелкий -10 (13) +0,5 мм.
При обогащении энергетических углей в отсадочных машинах принимают те же машинные классы, что и для коксующихся углей (для антрацитов принимают 6-250 мм).
При отсутствии в таблицах результатов ситового анализа необходимых размеров машинных классов производят построение кривых ситового анализа и по ним определяют выход и зольность нужного класса.
В данной работе принимаем к расчету два машинных класса: крупный -13+100 мм и мелкий -13+0,5 мм.
Выход крупного машинного класса определяем по формуле:
,
где γ-100+50 и γ-50+13 – выхода классов шихты (графа 8 табл.5).
Зольность крупного машинного класса определяем по формуле:

Выход мелкого машинного класса определяем суммированием выходов классов -13+6, -6+3, -3+0,5 мм шихты, а зольность мелкого машинного класса – как средневзвешенную зольность перечисленных выше классов шихты.
Выход и зольность класса 0-0,5 мм переносим из табл.5.
Таблица 6
Ситовый состав машинных классов
Класс крупности, мм |
Продукт |
γ, % |
Аd, % |
13-100 |
Необогащенный уголь |
30,93 |
31,13 |
0,5-13 |
Необогащенный уголь |
58,99 |
17,72 |
0-0,5 |
Шлам |
10,08 |
19,35 |
Итого: |
100,00 |
22,03 |
2.3 Обработка результатов фракционного анализа углей шахт
Обработка фракционного анализа углей шахт сводится к получению фракционного состава шихты и фракционного состава машинных классов.
Обработку осуществляем в следующем порядке:
1. Составляем таблицы результатов фракционного анализа для каждой шахты с подсчетом выхода каждой фракции к шихте (табл.7, 8).
Выход к шихте определенной фракции шахты рассчитываем с учетом выхода класса, к которому принадлежит эта фракция, и процента участия шахты в шихте.
Так, выход к шихте фракции <1,3 г/см3 класса -100+50 мм шахты №1 составляет:
,
где 21,6% - выход фракции <1,3 г/см3 класса -100+50 мм (графа 2 табл.2);
12,08% - выход к шихте класса -100+50 мм (графа 3 табл.5);
100 – коэффициент, который переводит выход класса из % в доли ед.
Аналогично определяем выход к шихте других фракций того же класса.
Для расчета выхода к шихте фракций других классов значения соответствующих выходов берем из табл.2 (графы 4. 6, 8) и табл.5 (графа 3).
Для класса -6+0,5 мм из табл.2, 5 берем суммарные выхода классов -6+3 и -3+0,5 мм.
Аналогично определяем выхода к шихте фракций всех классов крупности шахты №2 (табл.3, 5).
Зольности фракций оставляем без изменений и переносим из табл.2, 3.
Таблица 7
Результаты фракционного анализа шахты №1 с выходом к шихте фракций
Плотность
фракций, г/см3
|
-100+50 |
-50+13 |
-13+6 |
-6+0,5 |
γк, % |
γш,
%
|
Аd, % |
γк, % |
γш,
%
|
Аd, % |
γк, % |
γш,
%
|
Аd, % |
γк, % |
γш,
%
|
Аd, % |
1 |
2 |
3 |
4 |
5 |
6 |
7 |
8 |
9 |
10 |
11 |
12 |
13 |
<1,3 |
21,6 |
2,61 |
4,1 |
48,9 |
2,67 |
3,6 |
45,0 |
5,01 |
5,9 |
56,0 |
10,72 |
5,1 |
1,3-1,4 |
12,1 |
1,46 |
9,4 |
12,1 |
0,66 |
4,0 |
21,4 |
2,38 |
7,2 |
14,0 |
2,68 |
6,1 |
1,4-1,5 |
7,3 |
0,88 |
17,7 |
5,0 |
0,27 |
22,1 |
9,6 |
1,07 |
18,0 |
6,3 |
1,2 |
19,2 |
1,5-1,6 |
3,9 |
0,47 |
26,5 |
2,5 |
0,14 |
35,2 |
2,5 |
0,28 |
28,3 |
3,5 |
0,67 |
28,2 |
1,6-1,8 |
6,1 |
0,74 |
27,6 |
2,5 |
0,14 |
42,5 |
3,6 |
0,4 |
35,1 |
2,8 |
0,54 |
39,3 |
>1,8 |
49,0 |
5,92 |
73,2 |
29,0 |
1,58 |
70,0 |
17,9 |
1,99 |
75,2 |
17,4 |
3,33 |
71,2 |
Итого: |
100 |
12,08 |
41,9 |
100 |
5,46 |
25,59 |
100 |
11,13 |
21,36 |
100 |
19,14 |
19,4 |
Таблица 8
Результаты фракционного анализа шахты №2 с выходом к шихте фракций
Плотность
фракций, г/см3
|
-100+50 |
-50+13 |
-13+6 |
-6+0,5 |
γк, % |
γш,
%
|
Аd, % |
γк, % |
γш,
%
|
Аd, % |
γк, % |
γш,
%
|
Аd, % |
γк, % |
γш,
%
|
Аd, % |
1 |
2 |
3 |
4 |
5 |
6 |
7 |
8 |
9 |
10 |
11 |
12 |
13 |
<1,3 |
33,3 |
3,13 |
3,3 |
72,7 |
2,9 |
5,6 |
73,0 |
2,16 |
5,8 |
77,1 |
19,86 |
3,0 |
1,3-1,4 |
15,3 |
1,44 |
7,7 |
3,9 |
0,15 |
8,0 |
5,4 |
0,16 |
7,4 |
5,4 |
1,39 |
7,2 |
1,4-1,5 |
17,2 |
1,62 |
23,9 |
3,9 |
0,15 |
21,0 |
2,7 |
0,08 |
19,0 |
2,1 |
0,54 |
19,9 |
1,5-1,6 |
3,8 |
0,36 |
27,6 |
1,9 |
0,08 |
28,2 |
2,7 |
0,08 |
23,7 |
1,2 |
0,31 |
25,4 |
1,6-1,8 |
4,8 |
0,45 |
38,6 |
1,9 |
0,08 |
35,9 |
2,7 |
0,08 |
40,1 |
1,2 |
0,31 |
38,2 |
>1,8 |
25,6 |
2,4 |
64,0 |
15,7 |
0,63 |
79,3 |
13,5 |
0,4 |
74,2 |
13,0 |
3,35 |
85,3 |
Итого: |
100 |
9,4 |
25,67 |
100 |
3,99 |
18,87 |
100 |
2,96 |
16,89 |
100 |
25,76 |
14,97 |
2. Составляем таблицу фракционного состава шихты (табл.9).
Для этого суммируем выхода к шихте соответствующих фракций и определяем их средневзвешенную зольность.
Графы 3, 6, 9 и 12 табл.9 заполняем, суммируя соответствующие графы табл.7, 8.
Например, суммарный выход к шихте фракции <1,3 г/см3 класса -100+50 мм составит:

Суммарную зольность этой фракции определяем как средневзвешенную:

Суммарную зольность класса -100+50 мм определяем как средневзвешенную для всех фракций этого класса:

Выход к классу фракции <1,3 г/см3 класса -100+50 мм определяем делением выхода каждой фракции к шихте на суммарный выход всех фракций к шихте данного класса.
Например, выход к классу фракции <1,3 г/см3 класса -100+50 мм составит:
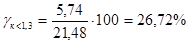
Аналогично определяем выхода других фракций и других классов.
Таблица 9
Фракционный состав шихты
Плотность
фракций, г/см3
|
-100+50 |
-50+13 |
-13+6 |
-6+0,5 |
γк, % |
γш,
%
|
Аd, % |
γк, % |
γш,
%
|
Аd, % |
γк, % |
γш,
%
|
Аd, % |
γк, % |
γш,
%
|
Аd, % |
1 |
2 |
3 |
4 |
5 |
6 |
7 |
8 |
9 |
10 |
11 |
12 |
13 |
<1,3 |
26,72 |
5,74 |
3,66 |
58,94 |
5,57 |
4,64 |
5,89 |
7,17 |
5,87 |
68,11 |
30,58 |
3,74 |
1,3-1,4 |
13,5 |
2,9 |
8,56 |
8,57 |
0,81 |
4,74 |
18,03 |
2,54 |
7,21 |
9,06 |
4,07 |
6,48 |
1,4-1,5 |
11,64 |
2,5 |
21,72 |
4,44 |
0,42 |
21,71 |
8,16 |
1,15 |
18,07 |
3,88 |
1,74 |
19,42 |
1,5-1,6 |
3,86 |
0,83 |
26,98 |
2,33 |
0,22 |
32,65 |
2,55 |
0,36 |
27,3 |
2,18 |
0,98 |
27,35 |
1,6-1,8 |
5,54 |
1,19 |
31,76 |
2,33 |
0,22 |
40,1 |
3,41 |
0,48 |
35,95 |
1,89 |
0,85 |
38,95 |
>1,8 |
38,74 |
8,32 |
70,60 |
23,39 |
2,21 |
72,52 |
16,96 |
2,39 |
75,08 |
14,88 |
6,68 |
78,37 |
Итого: |
100 |
21,48 |
34,81 |
100 |
9,45 |
22,76 |
100 |
14,09 |
20,42 |
100 |
44,9 |
16,88 |
3. Составляем таблицу фракционного состава машинных классов и суммарного класса 0,5-100 мм (табл.10).
Выход к шихте фракций крупного машинного класса 13-100 мм (графа 3 табл.10) определяем суммированием выходов к шихте фракций классов -100+50 и -50+13 мм (графы 3, 6 табл.9).
Например, выход к шихте фракции <1,3 г/см3 крупного машинного класса составит:

Зольность данной фракции определяем как средневзвешенную:

Аналогично определяем выхода и зольности других фракций и классов.
Выход фракций суммарного класса 0,5-100 мм определяем суммированием выходов фракций крупного и мелкого машинных классов, а зольность – как средневзвешенную.
Выход к шихте фракции <1,3 г/см3 суммарного машинного класса составит:

Зольность данной фракции составит:

Выход фракций к классу рассчитываем аналогично табл.9.
Таблица 10
Фракционный состав машинных классов и
суммарного класса 0,5-100 мм
Плотность
фракций, г/см3
|
-100+13 |
-13+0,5 |
-100+0,5 |
γк, % |
γш,
%
|
Аd, % |
γк, % |
γш,
%
|
Аd, % |
γк, % |
γш,
%
|
Аd, % |
1 |
2 |
3 |
4 |
5 |
6 |
7 |
8 |
9 |
10 |
<1,3 |
36,57 |
11,31 |
4,14 |
63,99 |
37,75 |
4,14 |
54,55 |
49,06 |
4,14 |
1,3-1,4 |
11,99 |
3,71 |
7,73 |
11,21 |
6,61 |
6,76 |
11,48 |
10,32 |
7,11 |
1,4-1,5 |
9,44 |
2,92 |
21,72 |
4,9 |
2,89 |
18,88 |
6,46 |
5,81 |
20,31 |
1,5-1,6 |
3,39 |
1,05 |
28,17 |
2,27 |
1,34 |
27,34 |
2,66 |
2,39 |
27,7 |
1,6-1,8 |
4,56 |
1,41 |
33,06 |
2,25 |
1,33 |
37,87 |
3,05 |
2,74 |
35,39 |
>1,8 |
34,05 |
10,53 |
71,0 |
15,38 |
9,07 |
77,5 |
21,8 |
19,6 |
74,01 |
Итого: |
100 |
30,93 |
31,13 |
100 |
58,99 |
17,72 |
100 |
89,92 |
22,33 |
4.Составляем таблицы суммарных выходов всплывших и потонувших фракций, для крупного, мелкого и суммарного машинных классов (табл. 11, 12, 13).
Графы 2 и 3 табл.11, 12, 13 заполняем по данным табл.10 (выхода к классу и зольности фракций). Графа 4 – произведение выхода фракции на зольность фракции.
Выход всплывших фракций (графа 5) определяем последовательным суммированием выходов всех фракций (графа 2) сверху вниз.
Например, выхода всплывших фракций крупного машинного класса составят:


и т.д.
Суммарную зольность всплывших фракций определяем следующим образом:


и т.д.
Таким образом, графу 6 заполняем последовательным суммированием сверху вниз данных графы 4 и делением на соответствующее значение графы 5.
Выход потонувших фракций (графа 7) определяем последовательным суммированием выходов всех фракций (графа 2) снизу вверх.
Суммарную зольность потонувших фракций (графа 8) определяем последовательным суммированием снизу вверх данных графы 4 и делением на соответствующее значение графы 7.
Аналогично заполняем табл.12, 13.
Таблица 11
Суммарные показатели фракционного состава крупного машинного класса
Плотность
фракций,
г/см3
|
Выход
γк, %
|
Зольность
Аd, %
|
Суммарно |
всплывшие фр. |
потонувшие фр. |
γ, % |
Аd, % |
γ, % |
Аd, % |
1 |
2 |
3 |
5 |
6 |
7 |
8 |
<1,3 |
36,57 |
4,14 |
36,57 |
4,14 |
100 |
31,13 |
1,3-1,4 |
11,99 |
7,73 |
48,56 |
5,03 |
63,43 |
46,69 |
1,4-1,5 |
9,44 |
21,72 |
58,0 |
7,74 |
51,44 |
55,77 |
1,5-1,6 |
3,39 |
28,17 |
61,39 |
8,87 |
42,0 |
63,42 |
1,6-1,8 |
4,56 |
33,06 |
65,95 |
10,54 |
38,61 |
66,52 |
>1,8 |
34,05 |
71,0 |
100 |
31,13 |
34,05 |
71,0 |
Итого: |
100 |
31,13 |
— |
— |
— |
— |
Таблица 12
Суммарные показатели фракционного состава мелкого машинного класса
Плотность
фракций,
г/см3
|
Выход
γк, %
|
Зольность
Аd, %
|
Суммарно |
всплывшие фр. |
потонувшие фр. |
γ, % |
Аd, % |
γ, % |
Аd, % |
1 |
2 |
3 |
5 |
6 |
7 |
8 |
<1,3 |
63,99 |
4,14 |
63,99 |
4,14 |
100 |
17,72 |
1,3-1,4 |
11,21 |
6,76 |
75,2 |
4,53 |
36,01 |
41,86 |
1,4-1,5 |
4,9 |
18,88 |
80,1 |
5,41 |
24,8 |
57,73 |
1,5-1,6 |
2,27 |
27,34 |
82,37 |
6,01 |
19,9 |
67,3 |
1,6-1,8 |
2,25 |
37,87 |
84,62 |
6,86 |
17,63 |
72,44 |
>1,8 |
15,38 |
77,5 |
100 |
17,72 |
15,38 |
77,5 |
Итого: |
100 |
17,72 |
— |
— |
— |
— |
Таблица 13
Суммарные показатели фракционного состава суммарного машинного класса
Плотность
фракций,
г/см3
|
Выход
γк, %
|
Зольность
Аd, %
|
Суммарно |
всплывшие фр. |
потонувшие фр. |
γ, % |
Аd, % |
γ, % |
Аd, % |
1 |
2 |
3 |
5 |
6 |
7 |
8 |
<1,3 |
54,55 |
4,14 |
54,55 |
4,14 |
100 |
22,33 |
1,3-1,4 |
11,48 |
7,11 |
66,03 |
4,66 |
45,45 |
44,18 |
1,4-1,5 |
6,46 |
20,31 |
72,49 |
6,05 |
33,97 |
56,7 |
1,5-1,6 |
2,66 |
27,7 |
75,15 |
6,82 |
27,51 |
65,25 |
1,6-1,8 |
3,05 |
35,39 |
78,2 |
7,93 |
24,85 |
69,27 |
>1,8 |
21,8 |
74,01 |
100 |
22,33 |
21,8 |
74,01 |
Итого: |
100 |
22,33 |
— |
— |
— |
— |
5.Составляем таблицу результатов дробной флотации угля класса 0-0,5 мм (табл. 15).
Производим корректировку результатов дробной флотации угла класса 0-0,5 мм (табл.14). Выход продуктов за первую и шестую минуты обозначим соответственно через x и y; выход и зольность продуктов берем из табл.4; зольность в строке «Итого» берем из табл.6. Составляем уравнения баланса:

,
откуда получаем x=51,89%, y=14,61 %.
Таблица 14
Результаты дробной флотации угля класса 0-0,5 мм после корректировки
Время флотации, мин |
γк, % |
Аd, % |
1 |
51,89 |
4,0 |
2 |
20,0 |
10,0 |
3 |
8,6 |
19,6 |
4 |
2,0 |
37,1 |
5 |
2,9 |
49,5 |
6 |
14,61 |
78,1 |
Итого: |
100,0 |
19,35 |
Суммарные показатели результатов дробной флотации угля определяем аналогично суммарным показателям фракционного состава машинных классов.
Таблица 15
Результаты дробной флотации угля класса 0-0,5 мм
Время флотации,
мин.
|
Выход
γк, %
|
Зольность
Аd, %
|
Суммарно |
концентрат |
хвосты |
γ, % |
Аd, % |
γ, % |
Аd, % |
1 |
2 |
3 |
5 |
6 |
7 |
8 |
1 |
51,89 |
4,0 |
51,89 |
4,0 |
100 |
19,35 |
2 |
20,0 |
10,0 |
71,89 |
5,67 |
48,11 |
35,9 |
3 |
8,6 |
19,6 |
80,49 |
7,16 |
28,11 |
54,33 |
4 |
2,0 |
37,1 |
82,49 |
7,88 |
19,51 |
69,65 |
5 |
2,9 |
49,5 |
85,39 |
9,3 |
17,51 |
73,36 |
6 |
14,61 |
78,1 |
100 |
19,35 |
14,61 |
78,1 |
Итого: |
100 |
19,35 |
— |
— |
— |
— |
6. Строим кривые обогатимости машинных классов и суммарного класса по данным табл.11, 12, 13 (рис. 1, 2, 3) и кривые флотируемости угля класса 0-0,5 мм по данным табл.14 (рис.4).
Кривые обогатимости строим следующим образом.
Квадрат длиной стороны 200 мм разбиваем тонкой сеткой на квадратики 10 10 мм. На оси ординат (левая вертикальная сторона) откладываем в масштабе через каждые 5% (сверху вниз) выхода фракций, которые всплыли, а на оси абсцисс (слева направо) через каждые 5% - зольности фракций. На правой вертикальной шкале квадрата в таком же масштабе откладываем суммарный выход утонувших фракций через каждые 5% (снизу вверх). На верхней стороне квадрата через каждые 100 кг/м3 откладываем плотности фракций (справа налево).
Кривую элементарных фракций λ = γ(Ad) строим по данным граф 5 и 3, для чего проводим линии суммарных выходов всплывших фракций, на которых откладываем последовательно зольность фракций и поднимаем перпендикуляры в пределах каждой фракции таким образом, чтобы каждая из них представляла собой прямоугольник высотой выхода данной фракции, и шириной зольности данной фракции. Через середины проведенных перпендикуляров проводим сглаженную кривую λ так, чтобы площади отсекаемых треугольников в пределах каждой фракции были равновеликими.
Кривую концентрации β = γ(Аd) строим по данным граф 5 и 6, для чего на линиях суммарных выходов откладываем суммарные зольности всплывших фракций, и полученные точки соединяем плавной кривой как обычный график.
Кривую отходов θ = γ(Аd) cтроим по данным граф 7 и 8. Выход берем на правой вертикальной шкале. Выхода потонувших фракций – дополнение к выходам всплывших фракций, и поэтому тоже лежат на линиях суммарных выходов. Зольности откладываем на нижней горизонтальной шкале. Полученные точки тоже соединяем плавной линией.
Кривую плотности δ = γ(ρ) строим по данным граф 1 и 5. Если плотность фракции <1,3 г/см3, то она всплывет при плотности разделения 1,3 г/см3, тогда, именно эту плотность и берем для построения кривой обогатимости. Фракция, суммирующая две фракции: <1,3 г/см3 и 1,3 – 1,4 г/см3 всплывет при плотности разделения 1,4 г/см3, то есть на первую линию суммарного выхода опускаем точку с плотностью 1,3, на вторую – с 1,4 и т.д. В разделении нет плотности 1,7, поэтому после 1,6 следующую точку строим по плотности 1,8. Полученные точки соединяем плавной кривой.
Начало кривых λ и β откладываем с зольностью 2-3%, взяв данную зольность как минимальную для отдельных кусков угля. Окончание кривых λ и θ откладываем на зольности 90-95% (данная зольность – максимальная зольность отдельных кусков породы).
3. Теоретический баланс продуктов обогащения
Теоретический баланс продуктов обогащения предназначен для определения теоретически возможных показателей обогащения и составляет основу для расчета качественно-количественной схемы обогащения.
Теоретический баланс продуктов обогащения составляем аналитическим способом по таблицам ситового и фракционного состава машинных классов шихты при заданной плотности разделения, или графическим – по кривым обогатимости машинных классов при заданной общей зольности концентрата и зольности породы отдельных машинных классов.
При графическом способе составления теоретического баланса для получения оптимальных показателей используем теорему максимального выхода концентрата (теорема Рейнгардта), который формулируется следующим образом: «Если при раздельном обогащении нескольких видов угля необходимо получить суммарный концентрат с заданным средним содержанием золы, то максимальный суммарный выход концентрата с общей заданной зольностью будет получен при одинаковой средней зольности элементарных слоев разделения». То есть задаемся нужной зольностью концентрата суммарного класса, поднимаемся по кривой β и проектируем горизонталь на кривую λ кривых обогатимости суммарного класса. Из кривой λ, опускаясь на шкалу зольности, определяем зольность элементарной фракции, по которой выполняется разделение. Взяв ту же зольность элементарной фракции для крупного и мелкого класса, определяем зольность концентрата соответствующих классов, выполняя построения в обратном порядке.
Теорема максимального выхода для определения выхода породы не используется. Зольность породы принимается из расчета отвального содержания в ней горючей массы (зольность >75%).
1. Задаемся средней зольностью суммарного концентрата Аdк = 8,0%.
На оси абсцисс кривых обогатимости суммарного класса 0,5-100 мм (рис.3) откладываем в масштабе зольность концентрата 8,0% и проводим линию, параллельную оси ординат до пересечения с кривой β. Через точку пересечения проводим демаркационную линию. Отрезок этой линии от оси ординат до кривой λ ab будет равен зольности элементарного слоя разделения.
2. Составляем теоретический баланс продуктов обогащения класса 13-100 мм.
На оси абсцисс кривых обогатимости класса 13-100 мм (рис.1) откладываем отрезок ab и проводим линию, параллельную оси ординат, до пересечения с кривой λ. Через точку пересечения проводим демаркационную линию и находим выход и зольность концентрата: γк=68,0% и Аdк=11,5%.
Зольность породы Аdп находим из уравнения:

Выход продуктов обогащения к шихте определяем обычным способом:
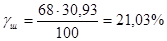
Данные строки «Итого» берем из табл.6. Полученные данные заносим в табл.16.
Таблица 16
Теоретический баланс продуктов обогащения класса 13-100 мм
Продукт |
Выход, % |
Зольность
Аd, %
|
γ |
γш |
Концентрат |
68,0 |
21,03 |
11,5 |
Порода |
32,0 |
9,9 |
72,85 |
Итого: |
100,0 |
30,93 |
31,13 |
3. Теоретический баланс продуктов обогащения класса 0,5-13 мм (табл.17) составляем по кривым обогатимости (рис.2) аналогично теоретическому балансу класса 13-100 мм.
Таблица 17
Теоретический баланс продуктов обогащения класса 0,5-13 мм
Продукт |
Выход, % |
Зольность
Аd, %
|
γ |
γш |
Концентрат |
84,5 |
49,85 |
6,5 |
Порода |
15,5 |
9,14 |
78,89 |
Итого: |
100,0 |
58,99 |
17,72 |
4. Составляем теоретический баланс продуктов флотации (табл.18).
Задаемся зольностью флотационного концентрата Аdк = 8,0 % и по кривым флотируемости угля класса 0-0,5 мм (рис.4) находим выход концентрата γк=83,0% и флотационных хвостов γх=17,0%.
Зольность флотационных отходов находим из уравнения баланса:

Таблица 18
Теоретический баланс продуктов флотации класса 0-0,5 мм
Продукт |
Выход, % |
Зольность
Аd, %
|
γ |
γш |
Концентрат |
83,0 |
8,37 |
8,0 |
Хвосты |
17,0 |
1,71 |
74,76 |
Итого: |
100,0 |
10,08 |
19,35 |
5. На основании табл.16, 17 и 18 составляем общую таблицу теоретического баланса продуктов обогащения (табл. 19).
Таблица 19
Теоретический баланс продуктов обогащения
Продукт |
Выход, % |
Зольность, % |
Концентрат класса, мм: |
13-100 |
21,03 |
11,5 |
0,5-13 |
49,85 |
6,5 |
0-0,5 |
8,37 |
8,0 |
Итого концентрата: |
79,25 |
7,98 |
Порода класса, мм: |
13-100 |
9,9 |
72,85 |
0,5-13 |
9,14 |
78,89 |
0-0,5 |
1,71 |
74,76 |
Итого отходов: |
20,75 |
75,67 |
Всего: |
100 |
22,03 |
Проверяем правильность составления всего теоретического баланса:

- зольность шихты.
Список литературы
1.Артюшин С.П. Проектирование углеобогатительных фабрик. Изд. 2-е. перераб. и доп. М., «Недра», 1974. 200 с.
2.Артюшин С.П. Обогащение углей. Учебник для вузов. М., «Недра», 1973.
3.Бедрань Н.Г. Обогащение углей. – М., «Недра»,1988, 206 с.
|