ПРОЦЕСС
КАЛАНДРОВАНИ
Я
Каландрованием называется процесс формования, при котором разогретую резиновую смесь пропускают в зазоре между горизонтальными валками, вращающимися навстречу друг другу, при этом образуется бесконечная лента определенной ширины и толщины.
При каландровании полимерный материал проходит через зазор только один раз. Поэтому для получения листа с гладкой поверхностью очень часто используют трех- или четырехвалковые каландры, имеющие соответственно два или три зазора. На каландрах можно получать листы с точностью по толщине до ±0,02 мм. Ширина листа определяется рабочей длиной валка. При каландровании проводятся различные технологические операции:
- формование резиновой смеси и получение гладких или продольных листов;
- дублирование листов;
- обкладка и промазка текстиля резиновой смесью.
Под действием упругих сил деформируемого материала, проходящего через зазор, между валками каландра возникают распорные усилия, величина которых зависит от зазора между валками, вязкоупругих свойств смеси, скорости обработки и других факторов.
Рабочие скорости на каландре зависят от вида технологической операции и могут достигать 90 м/мин.
Мощность электродвигателей каландра зависит в основном от числа валков, длины рабочей поверхности и скорости каландрования.
Классификация каландров
В зависимости от выполняемых процессов каландры подразделяют на:
листовальные — для изготовления резиновых смесей в виде гладких листов;
профильные — для выпуска резиновых смесей с более сложным профилем сечения или с нанесением на лист рисунка (подошвенный и др.);
обкладочные — для наложения резиновой смеси тонким слоем на ткань при одинаковых окружных скоростях валков в выпускающем зазоре;
промазочные — для втирания резиновой смеси в нити ткани и переплетения между ними;
универсальные, снабженные механизмами для изменения угловой скорости валков.
Определяющими параметрами каландров, применяемых в резиновой промышленности, являются число валков, диаметр и длина их рабочей части, а также расположение валков. Все каландры подразделяют по числу валков на трех-, четырех - и пятивалковые. Валки каландров обычно изготавливают из чугуна. Материал валка должен обладать высокой плотностью, однородностью структуры, не иметь пор и раковин, быть износоустойчивым. Рабочая (внешняя) поверхность валков должна обладать высокой твердостью. Однако при очень высокой твердости рабочих поверхностей валки становятся хрупкими и чувствительными к резким изменениям температуры. Поэтому для предотвращения поломки прогревать и особенно охлаждать валки следует с большой осторожностью (равномерно, без резких скачков температуры). Толщина стенок валка должна быть одинакова по всей его длине, так как при этом валки прогреваются и охлаждаются более равномерно.
Для точного соблюдения заданного калибра (толщина каландруемого материала) валки должны иметь минимальный «прогиб», возникающий под действием распорных усилий в зазоре между валками. Прогиб валков вызывает изменение калибра по длине их рабочей поверхности; при этом в средней части каландруемый материал утолщается на 0,1—0,2 мм (рис.1, а, б).
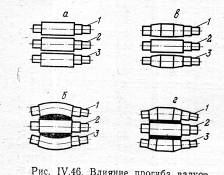
Рис.1. Влияние прогиба валков на толщину каландрованной заготовки при действии распорных усилий на цилиндрические валки (а, б) и валки, имеющие стандартную бомбировку (в, г): 1, 2, 3 – соответственно верхний, средний и нижний валки.
При изменении распорных усилий изменяется и максимальная стрела прогиба. Прогиб валков при возникновении между ними распорных усилии устранить нельзя, но можно частично компенсировать бомбировкой валков (приданием особой, бочкообразной формы их рабочим поверхностям). Если верхний и нижний валки сделать выпуклыми, то изменение калибра будет менее заметно. Для того чтобы упростить изготовление валков, позволить использование их для различных процессов формования, применяют так называемую стандартную бомбировку (рис.1 ,в). Верхний 1 и нижний 3 валки обрабатывают с обоих концов слегка на конус, оставляя среднюю часть этих валков и средний приводной валок 2 цилиндрическими; разность диаметров конусной части валков 0,2—0,4 мм. Возможно и равномерное увеличение диаметра валков от краев к центру. При прогибе верхнего и нижнего валков под действием распорных усилий зазоры между валками в значительной степени выравниваются по длине образующей валка (рис.1, г); при этом калибр каландруемого материала становится более равномерным по всей его ширине.
Необходимо отметить, что при компенсации прогиба валков путем их бомбировки не учитывают изменение распорного усилия в процессе каландрования, что затрудняет получение листов, равномерных по толщине. Для получения каландрованных листов, более равномерных по толщине, применяют способ компенсации прогиба валков перекрещиванием их главных осей. Величина перекрещивания может изменяться в зависимости от распорного усилия.
Более точное регулирование толщины каландрованного листа по ширине достигается компенсацией прогиба валков путем их изгиба в направлении, обратном прогибу. Такой эффект возможен при дополнительной установке второго подшипника с каждой стороны на шейке вала. Противодействующий прогибу валка изгибающий момент получается за счет усилия на подшипник, создаваемого гидравлическим цилиндром.
Иногда для каландров с большой длиной валков, работающих при высоких скоростях, с целью обеспечения высокой точности калибра полотна применяют совместно все три метода компенсации прогиба валков.
Калибр каландруемого материала изменяют при помощи механизма регулирования зазора. На каландрах современных конструкций регулирование зазора производят от электропривода; грубое регулирование зазора осуществляют механизмом с меньшим передаточным числом, изменяющим расстояние между валками со скоростью 10 мм/мин; более точное регулирование обеспечивается механизмом с большим передаточным числом со скоростью 0,5— 1,0 мм/мин.
Толщину выпускаемого с каландра материала контролируют стоматическими регистрирующими приборами (механические, пневматические, магнитоиндуктивные приборы с использованием радиоактивных изотопов), которые устанавливают обычно на приемном транспортере или на валке каландра.
В настоящее время применяют приборы, одновременно производящие контроль толщины листов и регулирование зазоров между валками (рис. 2).
При профилировании на каландрах и червячных машинах толщину заготовок контролируют с помощью весов непрерывного действия, установленных на приемном конвейере агрегата. Для получения каландруемого материала высокого качества очень важно обеспечить плавность хода каландра; поэтому приводные и передаточные шестерни привода изготовляют с шевронными или с косыми зубцами. Каландр в движение приводят от индивидуальных электродвигателей (электродвигатели постоянного тока или коллекторные электродвигатели переменного тока), допускающих регулирование частоты вращения в широких пределах. Механические нагрузки на валки при работе каландров более равномерны и не имеют больших пиков, как при работе вальцов. Это объясняется тем, что питание каландра производится непрерывно и равномерно резиновой смесью, предварительно разогретой на вальцах.
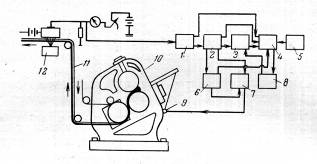
Рис. 2. Система автоматического регулирования зазора между валками каландра: 1 — самопишущий прибор с передающим потенциометром;2 — блок установки порога регулирования; 3 — блок накопления информации; 4 — блок определения продолжительности исправления зазора; 5 —блок максимальной продолжительности исправления зазора; 6 — блок введения поправок на люфты; 7 — блок управления приводом исполнительного механизма; 8 — блок установки интервалов регулирования по времени; 9 — исполнительный механизм; 10 — каландр; 11 — обрезиненный корд; 12 - лучевой толщиномер.
При каландровании очень важно поддерживать температурный режим валков и обрабатываемого материала. Температуру поверхности валков регулируют подачей внутрь валков охлаждающей воды или пара под давлением 0,3—0,4 МПа. В современных конструкциях каландров применяют валки, вода или пар, в которые подается по каналам, расположенным по окружности вблизи от рабочих поверхностей. При таком устройстве валков появляется возможность более точно и быстро регулировать температуру их рабочей поверхности.
Пуск каландра в работу производится обычно в следующем порядке: сначала пускают каландр вхолостую, затем между валками устанавливают зазор (не менее 1 мм) и, медленно открывая паровые вентили, подают в них пар. При быстрой подаче пара, особенно в неподвижные (невращающиеся) валки, наблюдаются местные термические деформации и разрушение валков, что может привести к аварии.
Продолжительность разогревания валков и расход пара зависят от размера и числа валков.
Все каландры снабжены электродинамическими или электромагнитными механизмами аварийного останова валков, которые обеспечивают пробег валков после отключения не более 0,25 оборота.
Вспомогательные приспособления
Большую роль при работе на каландре играют различные вспомогательные устройства и приспособления (транспортеры для подачи резиновой смеси в каландр, приспособления для дублирования слоев резины и их накатки, ножи для обрезания кромок и разрезания заготовок на полосы). От них часто зависит не только скорость процесса, но и качество изготовляемого полуфабриката.
Профильные каландры (протекторные, подошвенные и др.) снабжают съемными профильными валками или «скорлупами», ножами для обрезания кромок, приемными роликовыми усадочными и весовыми транспортерами для контроля равномерности калибра выпускаемой продукции, охладительными ваннами.
Резиновые смеси и прорезиненные ткани после обработки на каландре закатывают в валики с прокладочной тканью или без прокладки.
Из каландра резиновая смесь выходит с температурой, близкой к температуре валков, поэтому перед закаткой ее охлаждают для предотвращения подвулканизации, а также деформации и слипания. Охлаждение необходимо проводить для резиновых смесей, содержащих ускорители вулканизации, а также при высоких скоростях каландрования.
Закаточные приспособления устанавливают непосредственно на станине каландра, если резиновые смеси в дальнейшем дублируют, или после вспомогательных приспособлений — транспортера (рис. 3), скорость которого можно регулировать в зависимости от свойств каландруемого материала: его усадки, когезионной прочности, клейкости и других факторов.
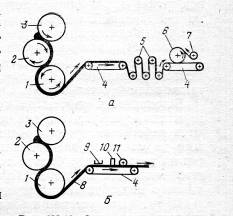
Рис. 3
. Системы приема резиновой смеси с каландра на транспортер: с охлаждением на барабанах и закаткой в ролик с прокладочным холстом (а) и с опудриванием резиновой смеси (б): 1,2,3 — валки трехвалкового каландра; 4 — транспортеры; 5 — охлаждающие барабаны;6 — ролик для закатки резиновой смеси с прокладочным холстом; — ролик с прокладочным холстом; — каландрованная резиновая смесь; — качающееся сито; 10— рейка, обитая тканью; 11 — щетка.
Как правило, каландрованные листы и прорезиненные ткани после выхода с каландра охлаждают на транспортере или пропускают через охлаждающие барабаны или ванны с антиадгезивами. В некоторых случаях, когда необходимо полностью снять все напряжения, возникающие в материале (каландровый эффект), каландрованные резиновые смеси пропускают через нагретые барабаны, плиты или камеры-туннели.
Для обеспечения равномерной усадки и устранения ориентационного эффекта каландрованные листы, предназначенные для изготовления мячей, баллонов, спринцовок и других изделий, дополнительно обогревают.
Каландрованную резиновую смесь и прорезиненные ткани накатывают на полые валики из жести, алюминия или дерева. В центре валика имеется квадратное отверстие, куда вставляется металлическая штанга, являющаяся осью валика. Так как при накатке листов резиновой смеси и тканей диаметр валика постепенно увеличивается, накаточные приспособления снабжают фрикционами — устройствами, позволяющими сохранить постоянную окружную скорость накатки.
Если необходимо, чтобы поверхность резиновых листов была совершенно гладкой (например, для передов галош, резиновых нитей, некоторых хирургических и технических изделий), каландрованную резиновую смесь накатывают на валки без ткани. Чтобы избежать слипания резиновых листов при накатке, по выходе из каландра их опудривают тальком, мелом, стеаратом цинка, реже крахмалом. Во избежание комкования мел и тальк для опудривания хорошо просушивают и просеивают. Во всех случаях, когда каландрованный лист предназначается для изготовления деталей, подлежащих склеиванию, для опудривания следует применять мел, так как он менее глубоко проникает в резиновую смесь и легче удаляется с ее поверхности; лучше применять стеарат цинка. Обычно достаточно опудрить одну сторону листа резиновой смеси.
Для опудривания лист с каландра подают на отборочный транспортер, где на него через качающееся сито наносят опудривающий материал, излишек которого снимают рейкой, установленной под углом 45° к направлению движения транспортера, и обитой мягкой тканью. Полное удаление избытка опудривающего материала производится круглой щеткой, очищающей мел в сторону, противоположную движению резины.
Опудривающий прибор заключен в кожух, соединенный с вытяжной вентиляцией. Для опудривания листов резины применяют также водные суспензии мела или стеарата цинка.
Безопасность работы на каландре гарантируется аварийным тормозным устройством, для чего с каждой стороны каландра имеются небольшие тросы, соединенные с выключателем, действующим на механизм электродинамического торможения. При нажатии на трос каландр быстро останавливается.Приводные шестерни и все вращающиеся детали должны иметь предохранительные кожухи.
Питание каландров
Каландрование резиновой смеси возможно, когда она достаточно пластична и подогрета; для этого перед каландрованием ее обрабатывают на подогревательных вальцах. Во избежание поломки вальцов жесткие смеси предварительно пропускают без разогрева через рифленые вальцы и только затем подают на гладкие. С подогревательных вальцов резиновую смесь направляют на питательные вальцы и далее в виде ленты или небольших рулонов (при ручном питании) подают на каландр.
Для получения каландрованных заготовок, равномерных по толщине, необходимо, чтобы пластичность и температура поступающей в каландр резиновой смеси были постоянны, а подача равномерной. Наилучшим способом питания является автоматическая непрерывная загрузка каландра резиновой смесью. Для этого на конце переднего валка питательных вальцов устанавливают нож, срезающий полосу резиновой смеси, которую затем транспортером подают в каландр. Ширина срезаемой ленты зависит от скорости каландра и толщины каландруемого материала. В рабочей зоне между валками, куда загружают резиновую смесь, устанавливают ограничительные передвижные стрелки из достаточно мягкого материала, не оставляющего следов на валке, довольно прочного, трудно истираемого, а также легко очищающегося от резиновой смеси (дерево, алюминий, сплав алюминия и кремния и др.). Чтобы избежать попадания резиновой смеси между валками и станиной каландра, ширина каландрованных листов должна быть на 6—10 см меньше длины валков. Кроме того, в процессе каландрования от листа с краев срезают кромки шириной 4—10 см, толщина которых отличается от установленного калибра каландрованного листа. Для получения каландрованной резиновой смеси в виде узких полос устанавливают несколько спиральных ножей, устроенных аналогично ножам для обрезания кромок. Нарезанные полосы наматывают на валки, расположенные поочередно спереди и сзади каландра.
Листование и объемное профилирование
резиновых смесей
В процессе листования разогретая резиновая смесь формуется в тонкие листы при прокатывании ее через валки каландра, при этом листы каландрованного материала должны быть одинаковой толщины по всей площади листа, а в некоторых случаях обладать гладкой поверхностью (иногда до блеска). При определении допусков по толщине учитывают техническое назначение каландруемой смеси и исходят из экономических соображений.
Отклонение толщины каландрованного листа от величины зазора обусловлено эластическим восстановлением резиновой смеси, которое, в свою очередь, зависит от состава смеси, вязкости и природы полимера, температуры валков каландра и смеси, а также скорости каландрования. Очень важно правильно регулировать температуру валков каландра.
Адгезия к металлу натурального и изопренового каучуков увеличивается с повышением температуры, причем каландруемые смеси на их основе легче переходят на более нагретый валок. Для большинства других синтетических каучуков адгезия к металлу увеличивается при понижении температуры, и каландруемые смеси на их основе легче переходят на более холодный валок. Выбор температуры каландрования зависит от состава резиновой смеси и ее когезионных свойств. При высокой температуре прочность каландрованного листа может стать настолько малой, что его невозможно будет принять на транспортер. Температурный режим каландрования для резиновых смесей разных типов определяется опытным путем. Обычно каландрование производят в интервале температур 60—110 °С.
Получение каландрованных листов с гладкой поверхностью и без воздушных включений (пузырей) возможно только для сравнительно небольших толщин резиновых смесей; при низких скоростях каландрования. Даже при каландровании на самых точных каландрах, доброкачественную резиновую смесь можно получить лишь при калибре листа не менее 0,15 мм и не более 1,2 мм. Эти пределы зависят от свойств резиновых смесей, в особенности от содержания в них каучука. С увеличением содержания каучука в смесях более резко проявляются их упругие свойства, в результате затрудняется возможность получения гладких листов без включений воздуха.
Особенности, характерные для листования, наблюдаются и при объемном профилировании резиновых смесей, которое проводится на профильных каландрах, имеющих один валок (последний) с профильным рисунком. Для профилирования обычно используют очень пластичные резиновые смеси с малой усадкой.
Каландровый эффект
каландрование валка резиновая
При каландровании резиновых смесей и многих каучукоподобных материалов наблюдается явление ориентационного или каландрового эффекта. Отличительным признаком резин, обладающих каландровым эффектом, является различие их механических свойств в направлении каландрования перпендикулярно валкам и в перпендикулярном к нему направлении (параллельно валкам). При этом прочность при растяжении листа резиновой смеси в первом направлении выше, чем во втором, относительное же удлинение, наоборот, меньше в направлении каландрования.
Каландровый эффект зависит от температуры каландрования, скорости валков, а также от свойств резиновой смеси. С повышением температуры каландрования каландровый эффект уменьшается.
При нагревании резиновой смеси при условии, что данная смесь обладает каландровым эффектом, наблюдается сжатие листа в направлении каландрования, при этом ширина его и толщина увеличиваются. Так, круг, вырубленный из листа резиновой смеси, имеющей каландровый эффект, довольно быстро превращается в эллипс, малая ось которого совпадает с направлением каландрования. Это можно объяснить наличием остаточных напряжений в направлении каландрования и снижением напряжений в поперечном направлении. При уменьшении толщины резиновой смеси каландровый эффект возрастает.
Появление каландрового эффекта в резиновых смесях обусловлено ориентацией молекулярных цепей полимера вдоль направления каландрования вследствие направленной деформации. Для каучуков с разветвленной структурой и небольшой молекулярной массой каландровый эффект незначителен. Для снятия каландрового эффекта смеси обычно нагревают. Однако для резиновых смесей, содержащих анизотропные наполнители, частицы которых имеют пластинчатое или игольчатое строение, каландровый эффект не может быть устранен нагреванием смеси. Такой вид каландрового эффекта называется зернистым эффектом; особо резко он проявляется в резиновых смесях, наполненных тальком, природным баритом, каолином. Для получения особо жесткой резины, плохо растягивающейся в одном направлении, специально применяют анизотропные наполнители.
Обкладка тканей резиновой смесью на каландрах
Для обкладки ткани резиновой смесью применяют каландры, валки которых вращаются с одинаковой частотой. Обкладку тканей с одной стороны можно производить за один пропуск на трехвалковом каландре, с двух сторон за один пропуск — на четырехвалковом каландре или за два пропуска — на трехвалковом.
Обкладка ткани резиновой смесью происходит следующим образом. Сначала через калибровочный зазор между валками пропускают бесформенную резиновую смесь. Далее полученный тонкий лист ее определенной толщины направляют в прессующий зазор между валками, куда также подают ткань.
Качество дублирования двух разнородных материалов зависит от равномерности нанесения резиновой смеси на ткань и главным образом от прочности их сцепления, толщины резинового листа и прессующего усилия.
С увеличением прессующего усилия до определенного значения увеличивается глубина проникновения резиновой смеси в ткань. При оптимальном значении прессующих усилий происходит максимальное заполнение полотна смесью, после которого, несмотря на увеличение прессующих усилий, происходит уменьшение прочности связи. Это объясняется снижением поступления резиновой смеси в полотно, так как с увеличением прессующих усилий уменьшается прессовочный зазор, а следовательно, и его пропускная способность. При этом не прошедшая через прессовочный зазор резиновая смесь собирается перед зазором, что приводит к разрушению ткани. Качество обрезинивания зависит в основном от пластоэластических свойств смеси, температуры и скорости каландрования, влажности, структуры и химической природы волокон ткани. Для улучшения прочности связи с резиной ткани на основе искусственных и синтетических волокон предварительно обрабатывают адгезивами. Перед обкладкой ткань нагревают, при этом влажность ее не должна превышать 2%. Резиновая смесь должна иметь низкую вязкость для лучшего проникновения ее в ткань, хорошую адгезию к ткани и плохую — к материалу валков каландра.
Качество обкладки зависит также от диаметра, бомбировки, обработки поверхности валков, и других факторов.
Обкладку тканей, используемых в очень больших количествах (шинного корда), проводят на сложных каландровых линиях со скоростью до 90 м/мин.
Широко применяют каландровые линии с двумя трехвалковыми каландрами или с одним четырехвалковым каландром. Эти каландры обеспечивают точность калибра ±0,2 мм.
Каландровые линии состоят из агрегатов: пропитки корда с вытяжкой и последующей сушкой, термообработки с зонами вытяжки и нормализации, обрезинивания корда на каландрах с предварительной его сушкой и последующим охлаждением. Каждый из трех агрегатов может работать самостоятельно, так как они снабжены раскаточными устройствами, стыковочным прессом, компенсаторами и закаточными устройствами. В процессе обработки корд вытягивается, поэтому все агрегаты оборудованы специальными механизмами для его натяжения. Температура в сушильной камере составляет 150—170 °С, в камере термообработки и нормализации она достигает230°С. Стыковочный пресс создает давление до7,0МПа при 260 °С.
При работе на агрегатах необходимо строго контролировать температуру, натяжение корда и другие параметры технологического процесса.
В случае окисления и преждевременного структурирования адгезива при последующей обкладке корда резиновой смесью не обеспечивается высокая прочность связи между резиной и кордом, ухудшаются прочностные свойства изделий, а также сокращается срок их службы.
В процессе обкладки непрерывно контролируют методом взвешивания толщину полученных листов.
При накладке резиновой смеси на уточный корд ширина ткани сокращается на 5—8% вследствие уплотнения нитей. Поэтому предельное отклонение массы, а следовательно, и толщины прорезиненных тканей от номинального значения должно быть не более 3%.Точность калибра прорезиненной ткани зависит от температурного режима, однородности смеси по пластичности, равномерности питания каландра и, наконец, от однородности самой ткани.
При использовании четырехвалковых каландров взамен двух трехвалковых в линиях для обкладки тканей резиновой смесью снижаются капитальные затраты и эксплуатационные расходы в результате сокращения необходимых производственных площадей и числа обслуживающего персонала. Однако линии с двумя трехвалковыми каландрами более надежны в работе и позволяют получить обрезиненный корд высокого качества, благодаря тому, что толщину обкладки можно контролировать после каждого трехвалкового каландра. Точность обкладки на двух трехвалковых каландрах выше, чем на четырехвалковом, так как прессующие и распорные усилия, действующие на валки трехвалкового каландра, более равномерно распределяются по образующей валка. У трехвалкового каландра только два валка (верхний и средний) подвергаются действию распорных усилий; прессующим усилиям подвергаются средний и нижний валки. У четырехвалкового каландра все валки подвергаются действию распорных усилий, средние валки дополнительно испытывают действие еще и прессующих усилий, что приводит к более сильному прогибу валков, который трудно компенсировать. Поэтому при обрезинивании на четырехвалковом каландре наблюдаются значительные отклонения толщины и массы резиновой смеси по ширине обрезиненной ткани. Прочность связи резины с тканью по ширине обрезиненного полотна равномерна и выше на двух трехвалковых каландрах, чем на одном четырехвалковом. Внешний вид трехвалкового каландра показан на рис.4.

Рис. 4
. Трехвалковый каландр с треугольным расположением валков: 1 –станина; 2 – валки; 3 – механизмы регулирования зазоров между валками; 4 – прессующие валки.
Сдваивание (дублирование) каландрованных листов
Для получения листов большой толщины листы каландрованной резиновой смеси сдваивают (дублируют), т. е. склеивают их по два, по три и более.
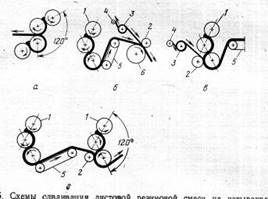
Рис. 5
. Схемы сдваивания листовой резиновой смеси на четырехвалковом каландре (а); на трехвалковом каландре с применением специального дублирующего барабана (б) или с помощью сдваивающих валков (в) на спаренных трехвалковых каландрах (г): 1 — каландр; 2— сдваивающий валик; 3 — ролик с резиновой смесью в прокладочном холсте; 4 — ролик с прокладочным холстом; 5 — транспортер; 6 — дублирующий барабан.
Дублирование обычно проводят на четырехвалковых каландрах (рис. 5, а), на трехвалковых каландрах со специальным дублирующим барабаном (рис. 5, б) или сдваивающим валиком, установленным на каландре (рис. 5,б), а также на спаренных трехвалковых каландрах (рис. 5,г).
Дублирующий барабан предназначен для обработки сравнительно жестких подошвенных резиновых смесей, эбонитовых пластин и т. п. Его изготавливают литым или полым и с достаточно хорошо полированной поверхностью. Для поддержания требуемых пластичности и клейкости резиновой смеси дублирующий барабан обогревают паром.
Сдваивающий валик на каландре применяют довольно часто. Он предназначен для сдваивания листа готовой каландрованной резиновой смеси, находящегося обычно на замкнутом транспортере, с листом, выходящим с каландра. Применение спаренных каландров (рис. 5, г) экономически целесообразно при массовом производстве однотипных дублированных резиновых смесей. При этом способе сдваивания резиновая смесь, выходящая из первого кадандра, находится под некоторым натяжением и несколько вытягивается. Поэтому ход первого каландра должен быть несколько замедлен по сравнению с ходом второго каландра; в противном случае на обрабатываемой резиновой смеси получаются складки.
Пути повышения качества каландрованных заготовок
Дефекты при каландровании обусловлены нарушениями температурного режима каландра, неравномерными подачей и подогревом резиновой смеси, а также непостоянной ее пластичностью. Наиболее характерными видами брака при листовании являются: негладкая поверхность, воздушные включения (пузыри), рисунок в виде «елки» на поверхности резины. В тех случаях, когда резины предназначаются для изделий, вулканизуемых неформовым методом, вредным является каландровый эффект. В таких резинах и после вулканизации сохраняется анизотропность, вследствие чего они легко раздираются.
При нарушении температурного режима возможны следующие виды брака: вследствие недостаточного разогрева резиновой смеси или валков каландра — негладкая поверхность, рисунок в виде «елки»; в результате перегрева последнего валка — воздушные включения, а предпоследнего валка — пузыри с отростками «слезки». Число воздушных включений может возрасти, если отрезаемые при каландровании кромки будут возвращаться непосредственно на каландр. Поэтому желательно пропускать кромки сначала через подогревательные вальцы, а затем равномерными порциями добавлять ко вновь приготовляемой резиновой смеси.
Улучшить качество каландрованных заготовок, уменьшить число пузырей, увеличить толщину каландрованных листов без дублирования и повысить производительность процесса можно, применяя специальные клиновые устройства, устанавливаемые в зазоре валков и увеличивающие интенсивность механической обработки резиновой смеси.
Прокладочные ткани и другие материалы
Для предохранения невулканизованных каландрованных листов или полотен прорезиненных тканей от слипания применяют прокладочные ткани, в которые их закатывают по выходу с каландра.
Чтобы уменьшить прилипание смесей, отличающихся большой липкостью к ткани, и предотвратить появление на каландрованных листах отпечатка переплетения основы и утка, прокладочные ткани пропитывают различными составами. Благодаря такой обработке увеличивается срок службы и прочность прокладок, облегчается процесс закатки и раскатки тканей при каландровании, раскрое и сборке, что вполне окупает стоимость их дополнительной обработки.
Для увеличения срока службы прокладочных тканей их следует периодически чистить щетками и пылесосами с целью удаления опудривающих материалов следов серы, накапливающейся в ткани в результате ее миграции из резиновых смесей, а также других загрязнений. Кроме того, прокладочные ткани проглаживают.
В качестве прокладочного материала можно использовать различные полимерные пленки (например, полиэтиленовые). Они в меньшей степени загрязняются, чем ткани, и не оставляют отпечатков на поверхности каландрованных листов.
|