Курсовой проект
на тему:
«Привод конвейера»
Харьков 2010
1. Кинематический расчет привода
1.1 Определение параметров исполнительного органа
Подбор ленты для транспортёра.
F=F1
-F2
,
где F– сила тяги перемещения грузов;
n=10…13 – коэффициент запаса.
SH= 2Р – усилие в набегающей части
[F]=100 м/Н – допускаемое разрывное усилие.
[1]
=350 мм – ширина барабана;
i– число прокладок ленты;
Принимаем i=2.
Из справочника выбираем ленту: Лента 2Т-300–2-ТК-100–8–2-Т-1 ГОСТ 20–85. Тип 1, шириной 300 мм, с 2 прокладками из ткани ТК-100, с рабочей обкладкой толщиной 8 мм и нерабочей 2 мм из резины класса Т.
1.2 Подбор электродвигателя
От характеристик выбранного двигателя (мощность, частота вращения) во многом зависит конструкция всего механизма в целом.
,
где V – скорость транспортирования грузов;
D – диаметр барабана;
Потребная мощность на барабане:
,
Где F – сила тяги для перемещения грузов.
Вычислим общий КПД механизма :

где – для конвейера;
- для компенсирующей муфты;
– КПД упругой муфты,
– для тихоходной ступени;
– КПД подшипников.
– КПД зубчатого зацепления;
Потребная мощность двигателя:
.
Подберем асинхронный двигатель с короткозамкнутым ротором и стандартным значением мощности .
Определим необходимое передаточное отношение редуктора, в зависимости от стандартных значений частоты вращения вала двигателя по формуле:
.
Выберем двигатель 4АС80В2У3 ГОСТ 15150–69 (2,5 кВт, частота вращения-2745, КПД 76%). Трехфазный асинхронный двигатель, четырехполюсный. Климатического исполнения «У», категории 3.
Пересчитаем потребное значение передаточного отношения редуктора:
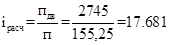
Разделим наше передаточное отношение по ступеням и определим его значения на валах. Результату расчетов:

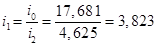
=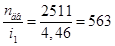   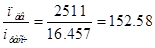
Зная частоты вращения валов и предаваемую мощность, определим вращающие моменты на валах:



Результаты расчета зубчатой передачи сведены в таблицы.
Исходные данные
|
Наименование параметра
|
Обозначение
|
Быстроходная ступень
|
Тихоходная ступень
|
Мощность, кВт |
P
|
2,3 |
2,1 |
Передаточное число |
U
|
3,85 |
4,57 |
Частота вращения, мин-1
|
n
|
2745 |
713 |
Срок службы, ч |
Lh
|
20
000
|
Режим работы |
постоянный
|
Тмах
/Тном
|
2
|
Угол зацепления, град |
0
|
Степень точности |
8
-B
|
Заготовка |
Шестерня |
поковка
|
Колесо |
поковка
|
Марка стали |
Шестерня |
30ХГСА
|
Колесо |
Термообработка |
Шестерня |
Закалка ТВЧ
|
Колесо |
Твердость рабочей поверхности зубьев, HRC |
Шестерня |
HB
|
55
|
55
|
Колесо |
60
|
60
|
Смещение |
Шестерня |
x
|
0
|
Колесо |
Количество зубьев |
Шестерня |
Z
|
26
|
23
|
Колесо |
100
|
105
|
Определение допускаемых контактных напряжений
|
Наименование параметра
|
Обозначение
|
Формула
|
Значения для ступени
|
Быстроходная ступень
|
Тихоходная ступень
|
Количество нагружений за один оборот |
с
|
Ш |
1 |
1 |
К |
1 |
1 |
Количество циклов нагружения с учётом режима работы, млн. |
Nk
|
Nk=60∙c∙n∙Lh
|
Ш |
3.29e9 |
0,856e9 |
К |
0,856е9 |
184,5е6 |
Базовое число циклов, млн. |
NHB
|
NHB
=30∙(
HB
)2.4
|
Ш |
358,6е3 |
358,6е3 |
К |
555е3 |
555,5е3 |
Показатель степени |
m
|
т. к.
Nk
>
NHB
|
Ш |
20 |
20 |
К |
20 |
20 |
Коэффициент долговечности |
ZN
|
ZN
=
|
Ш |
1,578 |
1,476 |
К |
1,444 |
1,338 |
Коэффициент запаса прочности |
SH
|
для зубчатых колес с поверхностным упрочнением зубьев
|
Ш |
1.2 |
1.2 |
К |
1.2 |
1.2 |
Предел контактной выносливости, МПа |
у
Hlim
|
у
Hlim
=17
HRC
+200
|
Ш |
1135 |
1135 |
К |
1380 |
1380 |
Допускаемое контактное напряжение, МПа |
[
у
]H
|
|
Ш |
718 |
768 |
К |
938 |
1013 |
Принятое |
718
|
768
|
Определение делительного диаметра и модуля
|
Наименование параметра
|
Обозначение
|
Формула (источник)
|
Быстроходная ступень
|
Тихоходная ступень
|
Коэффициент, учитывающий неравномерность распределения нагрузки по длине контактных линий |
KHв
|
ГОСТ 21354–87
|
1,36
|
1,07
|
Вспомогательный коэффициент |
Kd
|
Для прямозубых передач
Kd
=770
|
770
|
Относительная ширина венца |
Ш
bd
|
Для проектировочного расчета
|
0,6
|
Крутящий момент на шестерне, Hм |
T
|
|
8
|
28,2
|
Расчетный делительный диаметр, мм |
dW
|
|
30,6
|
55,8
|
Модуль, мм |
Расчетный |
m
|
|
1,18
|
2
|
Принятый |
m
|
ГОСТ 9563–60
|
2
|
1,5
|
Делительный диаметр, мм |
Шестерня |
dW
|
|
46,97
|
34,5
|
Колесо |
180,64
|
157,5
|
Межосевое расстояние, мм |
aW
|
|
-
|
96
|
Ширина венца, мм |
Расчетная |
bW
|
|
5,9
|
27,5
|
Принятая |
20
|
20
|
Определение допускаемых напряжений
для расчета на максимальные нагрузки и на изгиб
|
Наименование параметра
|
Обозначение
|
Формула
|
Значения для ступени
|
Быстроходная ступень
|
Тихоходная ступень
|
Количество циклов нагружения. |
Nk
|
Nk=60∙c∙n∙Lh
|
Ш
К
|
3.29e9 |
0,856e9 |
0,856e9 |
184,52е6 |
Базовое число циклов. |
NFв
|
Для обоих колес:
|
Ш
К
|
4e6 |
4e6 |
Показатель степени |
m
|
Для данного вида термообработки
|
Ш
К
|
9 |
9 |
Коэффициент долговечности |
YN
|
|
Ш |
1 |
1 |
К |
1 |
1 |
Коэффициент, учитывающий размеры колеса |
Yx
|
|
Ш |
1.04 |
1.05 |
К |
1.02 |
1.03 |
Коэффициент, учитывающий способ получения заготовки |
Yk
|
Так как колеса и шестерни получаем штамповкой, то:
|
Ш
К
|
1 |
1 |
Коэффициент запаса прочности |
SF
|
По табл.
2.4
[6]
|
Ш
К
|
1.7 |
1.7 |
Предел выносливости при изгибе, МПа |
уFlim
0
|
По табл.
2.4
[6]
|
Ш
К
|
580 |
580 |
Допускаемое напряжение при изгибе, МПа |
[
уF
]
|
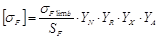 |
Ш |
356 |
356,8 |
К |
349,7 |
351,5 |
Допускаемое контактное напряжение, МПа |
[
у
]H
|
|
Ш |
718 |
768 |
К |
938 |
1013 |
Предел выносливости при изгибе, МПа |
уFlim
max
|
По табл.
2.4
[6]
|
Ш
К
|
2250 |
2250 |
Коэффициент запаса прочности |
SFmax
|
ГОСТ 21354–87
|
Ш
К
|
2 |
1.7 |
Допускаемое напряжение при изгибе, МПа |
[уF
]max
|
|
Ш |
1174 |
1384 |
К |
1153 |
1364 |
Проверочный расчет на контактную выносливость
|
Наименование параметра
|
Обозначение
|
Формула (источник)
|
Быстроходная ступень
|
Тихоходная ступень
|
Коэффициент, учитывающий форму сопряженных поверхностей зубьев в полюсе зацепления |
|
для эвольвентного зацепления
|
2.5 |
Коэффициент, учитывающий механические свойства материалов сопряженных колёс, МПа-0,5
|
|
для сталей
|
190 |
Коэффициент торцового перекрытия |
|
|
2,036 |
2,05 |
Окружная скорость, м/с |
V
|
|
6,75 |
1,29 |
Коэффициент, учитывающий вид передачи и модификацию профиля |
|
без модификации
ГОСТ 21354–87
|
0.14 |
Коэффициент, учитывающий разность шагов зацепления колёс |
g0
|
для модуля до m=4
ГОСТ 21354–87
|
4.7 |
Удельная окружная динамическая сила, Н/мм |
WHV
|
|
42,81 |
4,63 |
Окружная сила, Н |
Ft
|
|
341 |
1634 |
Коэффициент, учитывающий внутренюю динамическую нагрузку |
KHV
|
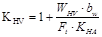 |
3,51 |
1.06 |
Относительная ширина венца |
Ш
bd
|
 |
0,43 |
0.6 |
Коэффициент, учитывающий неравномерность распределения нагрузки по длине контактных линий |
KHв
|
ГОСТ 21354–87
|
1.36 |
1.07 |
Коэффициент нагрузки |
K
Н
|
|
4,78 |
1.13 |
Действующее контактное напряжение, МПа |
|
|
686 |
748 |
Сравнение с допускаемым, % |
|

|
-4,4 |
-2,5 |
Определение действующих напряжений для расчета на изгиб
|
Наименование параметра
|
Обозначение
|
Формула
|
Значения для ступени
|
Быстроходная ступень
|
Тихоходная ступень
|
Коэффициент, учитывающий форму зуба и концентрацию напряжений |
YFS
|
|
Ш |
4,75 |
4,04 |
К |
4,2 |
3.6 |
Коэффициент, учитывающий неравномерность распределения нагрузки по длине контактных линий |
KFв
|
|
3,61 |
1.06 |
Коэффициент, учитывающий внутреннюю динамическую нагрузку |
KFV
|
|
3,61 |
1,06 |
Коэффициент нагрузки |
KF
|
|
13,03 |
1.12 |
Действующее изгибное напряжение, МПа |
[
уF
]
|
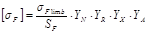 |
Ш |
247 |
248 |
К |
218 |
220 |
Сравнение с допускаемым |
|

|
Ш |
-30,6 |
-30,6 |
К |
-37,6 |
-37,3 |
Определяющим является расчет на контактную прочность зубьев. При расчете на контактную прочность недогрузка составляет -4,4% и -2,5% для быстроходной и тихоходной ступени соответственно. При расчете на изгибные и максимальные напряжения недогрузка колес более 30%. Определение геометрических и других параметров колеса и шестерн
и.
Значения линейных размеров в миллиметрах
Название |
Формула |
Быстроходная ступень |
Тихоходная ступень |
Делительный диаметр шестерни |
 |
47 |
34,5 |
Делительный диаметр колеса |
 |
180 |
157,5 |
Диаметр вершин шестерни |
 |
56 |
37,5 |
Диаметр вершин колеса |
 |
201 |
160,5 |
Диаметр впадин шестерни |
 |
48 |
30,75 |
Диаметр впадин колеса |
 |
198 |
153,75 |
4. Проектирование валов
Определим диаметры валов из расчета только на кручение по следующей формуле:
,
где
– момент сопротивления круглого сечения при кручении.
Значение условного допускаемого напряжения выбирают из диапазона 
· быстроходный: примем ;
· на промежуточном: примем ;
· на тихоходном: примем .
После определения минимальных значений диаметров валов нам необходимо спроектировать вал с расчетом на свободную установку зубчатого колеса (шестерни), подшипников и уплотнений, а так же точной фиксации всех элементов в осевом направлении на нем. Для этого сделаем вал со ступенчатым изменением диаметров по длине.
В первом приближении выберем подшипники, подходящие по диаметру вала:
· на быстроходный вал подшипники легкой серии;
· на промежуточный – легкой;
· на выходной – средней.
При дальнейших расчетах нагрузки, действующей на них, будем подбирать наиболее оптимальные подшипники, удовлетворяющие всем условиям.
Так как в конструкции редуктора используются прямозубые передачи, то основными нагрузками, действующими на подшипники, будут радиальные силы и окружные силы, а осевые силы будут незначительными. Поэтому выберем шариковые радиальные однорядные подшипники:
В конструкции имеются и конические передачи, в которых имеют местоосевые силы,поэтому на быстроходный и промежуточный валы устанавливаем шариковые радиально – упорные подшипники.
6. Выбор муфт
Муфты подбираются по диаметру вала и расчетному значению вращающего момента, который для каждого типа муфт определяется по определенной формуле.
.
Выбираем упругую муфту с торообразной оболочкой Муфта 8–1–38–1-У2 ГОСТ 20884–82, так как она имеет более простую конструкцию и малую стоимость, а также содержит небольшое количество деталей, что снижает вероятность выхода ее из строя. [3]
Расчетное значение вращающего момента
.
Выбираем компенсирующую упругую втулочно-пальцевую муфту, так как она имеет допускаемое радиальное смещение. Муфта 250–32–58-У3 ГОСТ 21424–75. [3]
Подшипник – это техническое устройство, являющееся частью опоры, которое поддерживает вал, ось или иную конструкцию, фиксирует положение в пространстве, обеспечивает вращение, качание или линейное перемещение (для линейных подшипников) с наименьшим сопротивлением, воспринимает и передаёт нагрузку на другие части конструкции.
Стандартные подшипники выбираем по динамической грузоподъемности. Она определяется следующим образом:
;
где
– расчетный ресурс;
– для шариковых подшипников;
– коэффициент надежности, – для надежности 0.9;
– коэффициент, учитывающий качество материала подшипников, смазочный материал и условия эксплуатации, - для обычных условий эксплуатации;
– эквивалентная нагрузка для радиальных подшипников,
– радиальная нагрузка,
– коэффициент вращения, – при вращении внутреннего кольца,
– коэффициент безопасности, учитывающий характер нагрузки;
– температурный коэффициент (при ).
В расчете участвует сила , которую создает муфта, зависит от типа муфты. Необходимо приложить ее в месте, где она может иметь наибольшее влияние. Точка приложения – середина шпонки.
Расчетной схемой для вала, опирающегося на подшипники, является балка на двух опорах. Из действующих сил (нормальные и силы трения) рассматривают только нормальные силы. Это связано с тем, что коэффициент трения в зубчатом зацеплении очень мал благодаря отполированным поверхностям зубьев и хорошей смазки.
Быстроходный вал
Схема
|
|
Вал
|
Разм
|
Формула
|
Результат
|
a
|
мм
|
Размеры взяты с компоновочного чертежа редуктора
|
34,99
|
b
|
80
|
c=d
|
24,74
|
Ft
|
Н
|
|
340,643
|
Fr
|
|
119,99
|
F
а
|
|
31,21
|
RAB
|
|
-27,945
|
RA
Г
|
|
105,319
|
RBB
|
|
147,935
|
RB
Г
|
|
-445,979
|
R
э
|
|
458,246
|
P
|
|
595,72
|
L
|
|
2851,589
|
Cp
|
|
9548,1
|
№ подш-ка
|
36205
|
С
p(
Н
)
|
9100
|
Промежуточный вал
Схема |
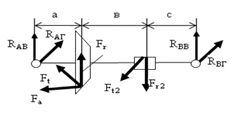 |
a |
мм |
Размеры взяты с компоновочного чертежа редуктора
|
23,53
|
b |
46,45
|
с |
22,97
|
Ft1/Ft2 |
Н |
|
340,643/1,635
|
Fr1/Fr2 |
|
31,21/0,6
|
RAB
|
Н |
|
93,434
|
RАГ
|
|
-254,006
|
RВ
B
|
|
-124,489
|
RВГ
|
|
-85,0017
|
RA
|
|
267,852
|
P |
|
348,2071
|
L |
|
3602,308
|
CP
|
Н |
|
5581,03
|
№
Подшипника
|
36203К6
|
CP
, (Н) |
5750
|
Тихоходный вал
Шпонка – деталь, предназначенная для передачи крутящего момента между валом и установленной на нем детали (зубчатое колесо, полумуфта).
Основным расчетом для шпонок является расчет на смятие в предположении равномерного распределения давления по поверхности контакта боковых граней шпонки. Высота (h) и ширина (b) подобраны таким образом, чтобы при расчете на смятие шпонку не нужно было бы рассчитывать на срез (ГОСТ 23360–78)
, откуда расчетная длина шпонки равна
, где
Т – вращающий момент на валу;
– допускаемое напряжение смятия;
- предел текучести материала шпонки.
Материалом шпонок назначим Сталь 45 ГОСТ 1050–88. МПа.
Сопрягаемый элемент
|
d
, мм
|
Стандартные
bxh
|
Длина, мм
|
Обозначение
|
Стандартная (диапазон)
|
Расчетная
|
Принятая
|
Упругая полумуфта
|
2
2
|
5х5
|
10–56
|
5,3
|
10
|
Шпонка
5х5х10
ГОСТ 23360–78
|
Колесо быстроходной ступени
|
20
|
6х6
|
14–70
|
14
|
14
|
Шпонка 6
x
6
x
14
ГОСТ 23360–78
|
Колесо тихоходной ступени
|
44
|
12х8
|
28–140
|
17,6
|
28
|
Шпонка
12х8х28
ГОСТ 23360–78
|
Компенсирующая полумуфта
|
32
|
10х8
|
22–110
|
22
|
Шпонка
10х8х22
ГОСТ 23360–78
|
9. Проверочный расчет валов
Условие статической прочности выглядит так:
,
где
– запас статической прочности;
– предел текучести материала.
Для проверочного расчета валов составим расчетную схему. Вал представим как балку на двух опорах. Построим эпюры изгибающих и крутящих моментов.
Опасным является сечение вала рядом с опорой В-галтель. Величины реакций опор нам известны из проверочного расчета подшипников. Выполним проверку вала на прочность в этом сечении.
Мг
, Нмм
|
|
3621,384
|
МВ
,
Нмм
|
|
7200,27
|
,
Нмм
|
|
7447,501
|
|
2
|
d,
мм
|
40
|
,
МПа
|
|
28,856
|
,
МПа
|
30
ХГСА
|
600
|
S
|
|
4,9
>1,5
условие прочности удовлетворяется
|
Расчет на сопротивление усталости проводят в форме проверки коэффициента запаса прочности по усталости.
При совместном действии изгиба и кручения запас усталостной прочности определяется по формуле
, где
– коэффициент запаса по нормальным напряжениям;
– коэффициент запаса по касательным напряжениям;
– предел выносливости материала при изгибе;
– предел выносливости материала при кручении;
– коэффициенты чувствительности к асимметрии цикла напряжений; – амплитудные напряжения;
– средние значения напряжений.
Напряжения кручения изменяются пропорционально изменению нагрузки. В большинстве случаев трудно установить действительный цикл нагрузки машины в условиях эксплуатации, тогда расчет выполняют условно по номинальной нагрузке, а цикл напряжений принимают симметричным для напряжений изгиба и отнулевым для напряжений кручения.
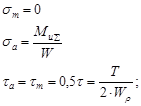
– суммарные коэффициенты, учитывающие влияние всех факторов на сопротивление усталости при изгибе и кручении – коэффициенты перехода от пределов выносливости образца к пределу выносливости детали;
– коэффициент абсолютных размеров поперечного сечения;
– коэффициент влияния шероховатости поверхности;
– коэффициент влияния упрочнения, вводимый для валов с поверхностным упрочнением;
– эффективные коэффициенты концентрации напряжений.
Механические характеристики стали 30ХГСА: твердость НВ не менее 240;
МПа, Мпа, Мпа, Мпа;
, .
Проведем расчет вала на усталостную прочность. Коэффициенты в формулах выбираются в зависимости от концентратора напряжений.
Место расположения |
шпонка |
, Мпа |
из справочника |
550 |
, Мпа |
из справочника |
320 |
, Мпа |
 |
16,108 |
, Мпа |
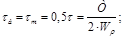 |
16,544 |
 |
0,7 |
 |
1 |
 |
2 |
 |
2,3 |
 |
2,15 |
 |
 |
1,643 |
 |
 |
1,536 |
 |
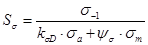 |
12,091 |
 |
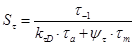 |
7,622 |
 |
 |
6>1.5
Условие прочности удовлетворяется
|
10. Расчет и конструирование элементов корпусных деталей и крышек подшипников
электродвигатель вал передача подшипник
Корпусные детали предназначаются для обеспечения правильного взаимного расположения сопряженных деталей редуктора, восприятия нагрузок, действующих в редукторе, защиты рабочих поверхностей зубчатых колес и подшипников от инородных частиц окружающей среды, защиты от выброса масла в окружающую среду при работе редуктора, отвода теплоты, а также для размещения масляной ванны.
Корпус редуктора состоит из собственно корпуса и крышки, которые отливаются из чугуна. Основными элементами корпуса являются его стенки, лапы, фланец корпуса, прилегающая к фланцу крышка и гнезда для подшипников с ребрами жесткости. В нижней части корпуса имеется резьба для маслоспускной пробки. Предусмотрен также прилив для маслоуказателя.
Для транспортировки корпусных деталей и редуктора в сборе его крышка снабжена подъемными ушами.
Габаритные размеры корпусных деталей выясняются при компоновке редуктора, они в основном определяются типом, размерами и относительным расположением деталей передачи.
Максимальный крутящий момент:

Элемент
|
Формула
|
Значение
|
Толщина стенки корпуса
|
|
Расч.
|
3,77 |
Прин.
|
6 |
Толщина стенки крышки
|
|
Расч.
|
3,4 |
Прин.
|
6 |
Толщина ребра
|
|
Расч.
|
4.8 |
Прин.
|
5 |
Диаметр фундаментных болтов
|
|
Расч.
|
8 |
Прин.
|
12 |
Диаметр фланцевых болтов
|
|
Расч.
|
6,35 |
Прин.
|
10 |
Толщина фундаментных лап
|
|
Расч.
|
18 |
Прин.
|
18 |
Толщина фланца
|
|
Расч.
|
15 |
Прин.
|
15 |
Толщина подъемных ушей
|
|
Расч.
|
10 |
Прин.
|
10 |
Ширина фланца
|
|
Расч.
|
32,4 |
Прин.
|
33 |
Смазочные материалы применяют с целью уменьшения интенсивности изнашивания, снижения сил трения, отвода от трущихся поверхностей теплоты и продуктов изнашивания, а также для предохранения деталей от коррозии. Снижение сил трения благодаря смазке обеспечивает повышение КПД машины. Кроме того, стабильность коэффициента трения и демпфирующие свойства слоя смазочного материала между взаимодействующими поверхностями способствуют снижению динамических нагрузок, увеличению плавности и точности работы машины.
Применим комбинированный способ смазки. Зубчатые колеса погружаются в масло, залитое в нижнюю часть корпуса (картер). А смазка подшипников качения осуществляется маслом, которое разбрызгивается зубчатой передачей. По времени – это непрерывное смазывание.
Емкость ванны для масла такова, при которой на каждый киловатт передаваемой мощности приходится 0,5 л масла. Таким образом, в картер необходимо залить масло в количестве 0,5∙5=1,25 л.
Экономичность и долговечность машины в большой степени зависят от правильности выбора смазочного материала. Поэтому масло следует выбрать исходя из рекомендации справочников
Из рекомендуемого выбираем масло РП-150. Ту38–01451–79.
Но для надёжного смазывания масла наливаем так, чтобы зубчатое колесо окуналось в него на всю ширину венца. Кол-во масла контролируем при помощи щупа.
Исполнительным органом привода конвейера для транспортирования грузов является барабан. Барабан служит для придания движения транспортировочной ленте.
Ширина барабана равна 350 мм, диаметр барабана D=160 мм. (по усл.)
Вал барабана нагружен таким же крутящим моментом, как и выходной вал редуктора. Поэтому при приближенном расчете получим то же среднее значение диаметра. Принимаем: диаметр входного конца вала (по муфте) 60 мм; диаметр в месте посадки подшипников 70 мм. Длины участков определяем в процессе конструирования.
Приводной вал имеет большую длину и подвержен значительным прогибам под действием внешних нагрузок, поэтому подшипники должны допускать значительные перекосы. В связи с этим выбираем радиальные двухрядные сферические шарикоподшипники.
Необходимо определить динамическую грузоподъемность, чтобы подобрать из стандартных соответствующий подшипник.
Для определения нагрузок, действующих на опоры, вал на подшипниках заменяем балкой на опорах.
Рассмотрим расчетную схему приводного вала.
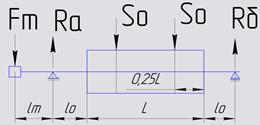
Усилие S0
=Р/2=*1500/2=750 Н.
Усилие от муфты Fм
=114,29 Н.
Определим реакцию в опоре В.

Аналогично определяем реакцию Rа=877,5
Динамическая грузоподъемность подшипника
, где
– коэффициент, вводимый при необходимости повышения надежности – для надежности 0.9,
– коэффициент, учитывающий качество материала подшипников, смазочный материал и условия эксплуатации – для обычных условий работы,
Динамическая грузоподъемность.
(Н).
Выбираем радиальный двухрядный сферический подшипник средней серии, имеющий обозначение №53507 ГОСТ 24696–81 (Рис. 15) и следующие данные:
· динамическая грузоподъемность ;
· внутренний диаметр ;
· наружный диаметр ;
· ширина ;
Фиксация вала осуществляется двумя сферическими двухрядными подшипниками. Выбираем из стандартных корпуса типа ШМ 140 ГОСТ 13218.1–80 и крышки торцовые ГОСТ 18512–73 [1]
Одну из опор выполняем фиксирующей (после полумуфты), а вторую – плавающей. Плавающая опора компенсирует погрешности изготовления и температурные деформации.
Расстояние между опорами 455 мм.
Установочная рама предназначена для объединения механизмов привода в установку, монтируемую на фундаменте.
Конструкция установочной плиты разрабатывается на основе эскизной компоновки.
Сначала вычерчиваем контур электродвигателя, затем в соединении с валом электродвигателя муфту, контур редуктора. В результате выясняем разность высот центров осей электродвигателя и редуктора и расстояние между болтами их крепления к плите.
Места под крепеж необходимо фрезеровать. Крепление сборочных единиц выполняют болтами. Крепление рамы к фундаменту выполним фундаментными Г-образными болтами.
В данной курсовой работе был спроектирован конвейер для транспортировки грузов. Особенного расчета потребовал редуктор.
Прочность конструкции обеспечивается применением разнообразных сталей и чугунов. Ответственные детали рассчитаны с учетом множества факторов влияющих на работу этих деталей. Конструирование производилось из условия минимума массы. Максимально использовались стандартные детали и узлы: подшипники, корпуса, торцевые крышки, крепежные изделия; что позволяет существенно снизить стоимость агрегата и обеспечить высокую точность в соединениях. Поверхности зубчатых колес имеют высокое качество поверхности и подвергаются смазке картерным способом. Для обеспечения герметичности стыки уплотняются герметиком, в местах выхода и входа валов применяются манжеты. Редуктор имеет проушины для транспортировки. На крышке расположено смотровое окно для проведения осмотра состояния зубчатых колес, подшипников и валов.
К недостаткам редуктора можно отнести высокий уровень шума, так как зубчатые колеса быстроходной ступени имеют малую жесткость в виду больших радиальных габаритов и малой ширины. Поэтому может возникать шум высокой частоты. Этот недостаток можно устранить дополнительной шумоизоляцией стыков, либо накрыть редуктор шумопоглощающим кожухом.
Для привода конвейера был спроектирован барабан и подшипниковые узлы. Барабан состоит из оболочки и торцевых крышек, которые свариваются между собой и привариваются к валу. Подшипники рассчитаны на заданный ресурс и имеют возможность компенсации угловых смещений вала, что положительно при наличии перегрузок, позволяет устанавливать привод на раму с меньшими требованиями по точности.
Данный конвейер можно применять в цехах при серийном, массовом производствах в целях увеличения продуктивности труда путем уменьшения времени переходов при транспортировочных операциях.
1. Анурьев В.И. Справочник конструктора-машиностроителя. В 3-х т. – М.: Машиностроение, 1979.
2. И.П. Копылов и др. Справочник по электрическим машинам. Том I М. Энергоатомиздат, 1988 – 456 с.
3. А.Е. Шейнблит. Курсовое проектирование деталей машин. М.: «Высшая школа», 1991.432 с.
4. Назин В.И. Проектирование подшипников и валов. Учебное пособие. – Х.: «ХАИ», 2004. – 220 с.
5. Кузьминов Ф.Ф., Пшеничных С.И. Подбор муфт. Конструкция, основы расчета. Учеб. пособие по курсовому и дипломному проектированию. – Х.: «ХАИ», 2006. – 103 с.
6. Курсовое проектирование деталей машин. Под общей редакцией В.Н. Кудрявцева. Учеб. пособие для машиностроит. специал. вузов. – Л.: Машиностроение, 1984. – 400 с.
7. Иванов В.Н. и Иванов М.Н. Детали машин. Курсовое проектирование. Учеб. пособие для машиностроит. вузов. – М.: «Высшая школа», 1975. – 551 с.
|