1 ЗАГАЛЬНА ЧАСТИНА
1.1 Аналіз господарської діяльності ДП «Красноградський Лісгосп»
Красноградський лісгосп організований у 1959 році, як лісова меліоративна станція на базі Водолазького і Красноградського лісівництва Харківського лісгоспу. В 1961 році 12 жовтня Красноградська лісова меліоративна станція була реорганізована в Красноградський лісгосп в складі трьох лісництв: Старовірівського, Красноградського, Зачепілівського. На базі прийнятих від колгоспів земель Сахновщинського району організувалася Сахновщинська виробнича дільниця. У 1970 році на базі урочищ Ордовське, Козачя балка, Власівське, Грачово Старовірівського лісництва і за рахунок прийнятих земель Красноградського району було створено Кегичівське спец лісництво.
Початок вивчення лісового фонду, який належить лісгоспу, відноситься до 1927 року. Останнє лісовпорядкування проводилось 1 1990 році.
Лісгосп знаходиться у південно-західній частині Харківської області на території Красноградського, Нововодолазького, Зачепілівського, Кегичівсбкого, Сахновщинського і Первомайського районів, загальна площа його становить 14634 га, у тому числі 11987 га покрито лісом. Територія Красноградського лісгоспу розташована у басейні річок Орілі та Бересової. В адміністративно-господарському відношенні лісгосп має 5 лісництв: Наталинське з загальною площею 5527га, Старовірівське – 3217га, Зачепілівське – 3119га, Кегичівське – 977га, Сахновщинське – 1463гектари і деревообробний цех.
У перший час щорічно лісгосп проводить посадку лісових культур на площі 100-150 гектарів. Основні дерево утворюючі породи: сосна звичайна, дуб звичайний, ясен, клен.
У 2007 році планується створити лісових культур в держлісфонді на площі 100 гектарів, та на землях, непридатних до сільгоспвикористання, на площі 65 гектарів. Зазвичай – це схили та яруги, що схильні до водної та вітрової ерозії.
Для збереження пам’яток природи законами України на території лісгоспу охороняються дуб звичайний, якому вже понад 250 років та осика, віком понад 120 років, більше 3м в обхваті, висотою 30м. в Зачипилівському лісництві в 1975 році було проведено щеплення кедру на сосну звичайну. На даний час цей досвід знаходиться під наглядом лісгоспу.
Щорічно в лісгоспі проводиться посадка ялинкових плантацій сосни звичайної та сосни кримської на площі 2-3 гектарів з метою збереження молодників.
1.1.1
Відомості про деревообробний цех Наталинського лісівництва та його діяльність
Цех переробки деревини призначений для переробки деревини, одержаної від рубок головного та проміжного використання. Об’єм переробки складає 600м3 за рік.
Випускається наступна продукція:
- розпилювання колод на пиломатеріали не обрізні та обрізні;
- переробка технологічної сировини м’яких та хвойних порід на різноманітні заготовки;
- виготовлення черенків;
Кількість робочих днів за рік 253, двох змінний робочий тиждень з 2-ма вихідними днями, тривалість зміни – 8 годин.
Кількість працівників в цеху – 12 чоловік, у більш мночисленну зміну – 6 чоловік.
1.1.2 Технологічна схема і організація виробництва деревообробного цеху з переробки деревини
Лісоматеріали круглі листяних та хвойних порід підвозять до цеху переробки деревини і розвантажують козловим краном на площадку. Підсортоване за породами та діаметром сировина козловим краном подається на прийомні естакади стрічкового розпилювання. З прийомної естакади круглий ліс накатується на стрічковий конвеєр, яким колоди подаються до стрічково-пилкових установок РИТМ -1.
1.
2 Характеристика стрічкопилкового обладнання
1.2.1 Особливості пиляння деревини стрічковими пилками
Пиляння стрічковими пилками відбувається при прямолінійному русі нескінченної пилкової стрічки і подачі розпилюваного матеріалу (рис. 1.2) [1]. На одній (або двох) крайках пилки нарізані зубці. Існують столярні, ділильні і колодорозпилювальні стрічкопилкові верстати, на яких столярними, ділильними і пилками для розпилювання колод і брусів здійснюється випилювання криволінійних профілів, ділення товстих пиломатеріалів на тонкі і розпилювання колод і брусів [2].
Швидкість різання (швидкість руку пилки) при пилянні деревини стрічковими пилками, м/с визначається за формулою
, (1.1)
де D- діаметр шківа стрічкопилкового верстата, мм
n - частота обертання шківа, хв-1;
z- кількість зубів, які приймають участь в різанні за 1 оберт шківа;
t - крок зубів,мм.
Швидкість подачі, м/хв, визначається за формулою
, (1.2)
де Sz - подача на зуб, мм
При пилянні стрічковими пилками Vs/Vr=const, і відносні траєкторії зубів в деревині є прямими лініями, паралельними вектору-швидкості
, (1.3)
Дереворізальні пилки повинні витримувати високі напруження. Зуби врізаються в деревину з великою швидкістю і піддаються ударному навантаженню. Кожен день полотно піддається сотням тисяч згинів при проходженні по пилкових шківах. При випилюванні воно, нагрівається, головним чином в крайці зубів. Це створює теплові напруження, які повинні сприйматись іншою частиною пилки, але полотно при цьому не повинно втрачати своєї площинності. Зуби повинні витримувати плющення або розведєння, без утворення дефектів, і мати високу стійкість до затуплення. Полотно повинно зберігати :розведення і правку, незважаючи на високу температуру і різницю температур. Ділильні стрічкові пилки випускаються згідно з ГОСТом 6532-77, а пилки для розпилювання колод і брусів - згідно з ГОСТом І0670-77. Вони відрізняються між собою розмірами і профілем зубів Основні типи профілів показані на рис. 1.3, а розміри зубів стрічкових пилок наведені в таблиці 1.2. [3].

Рисунок 1.1 - Профілі зубів стрічкових пилок:
t- крок зуба, мм; h -висота зуба, мм; l
- довжина задньої крайки, мм;
а- відстань бід вершини зуба до центра радіуса закруглення впадини, мм; g - передній кут зуба, град; b - кут загострення зуба, град.
Таблиця 1.1. - Розміри зубів стрічкових пилок
Пилки |
Тип профілю зубів |
Крок зубів t., мм |
Висота зубів h, мм |
Радіус западин r,мм |
Передній кут g,град |
Задній кут a,град |
Кут загострення b,град |
Стрічкові для розпилювання:
Деревини (ділильні ГОСТ 6532-77) |
І |
30 |
10 |
5 |
20 |
30 |
50 |
50 |
13 |
5 |
30 |
25 |
45 |
ІІ |
50 |
13 |
6 |
25 |
30 |
45 |
колод та брусів (ГОСТ 10670-77) |
ІІ |
50 |
16,7 |
20,8 |
25 |
12 |
53 |
60 |
20,0 |
25,0 |
При виборі параметрів пилок, користуються наступними рекомендаціями [4]:
1) товщина пилки повинна задовольняти залежності
, (1.4)
де D - діаметр шківів, мм
2) довжина пилки визначається за формулою
, (1.5)
де, Амах - мінімальна і максимальна, відстань між осями шківів верстата, мм.
3) профіль зубів ділильних стрічкових пилок вибирається залежно від фізико-механічних властивостей деревини. Для розпилювання деревини твердих порід необхідно застосовувати зуби профілю І, а для м'яких порід - профілю II(див. рис. 1.1).
4) крок зубів вибирається з умов забезпечення достатньої ємкості і міжзубих западин і заданої шорсткості отримуваних матеріалів
, (1.6)
де hmax - максимальна висота пропилу, мм.
5) подача на зуб Sz приймається за допустимою шорсткістю поверхні матеріалів (табл. 1.2).
Таблиця 1.2. - Допустима за шорсткістю поверхні пиломатеріалів подача на зуб, мм
Висота нерівностей
Rzmax, не більше
|
Мяка деревина літом |
Деревина твердих порід або мерзла |
1600 |
2, 00 |
2, 50 |
800 |
1, 50 |
2, 00 |
500 |
1, 00 |
1, 20 |
320 |
0, 60 |
0, 75 |
200 |
0, 30 |
0, 40 |
100 |
0, 15 |
0, 20 |
Важливий параметр зубів пилки - розвід зубів на сторону. При малій величині розводу відбувається затискання пилки в пропилі. При великій - ростуть втрати деревини в стружку і витрати електроенергії. Величина розводу зубів залежить від гідротермічного стану деревини, висоти пропилу, точності підготовки пилки рекомендовані величини розводу зубів пилок на сторону наведені нижче.
Породи деревини: І ІІ
хвойні 0,60…0,75 0,55…0,65
твердолистяні 0,50…0,60 0,40…0,55
листяні та модрина 0,70…0,80 0,60…0,70
Примітка. І - значення вологості деревини > 30%; II - < 30% або для мерзлої деревини.
В правильно підготовлених зубів лінійні і кутові параметри повинні відповідати стандартним.
1.2.2 Класифікація і технічні дані
Стрічкопилкові верстати класифікуються за наступними ознаками:
1) 3а призначенням: столярні, ділильні, колодорозпилювальні;
2) за розміщенням стрічкової пилки: вертикальні, горизонтальні нахилені;
3) за видом різання: з торцевим, поздовжнім, з поперечним різанням;
4) за конструкцією механізму різання; без шківів, з одним шківом, з двома шківами, з трьома шківами, з кількістю шківів більше трьох;
5) за видом механізму подачі: з ручною, вальцєвою, гусеничною, з подачею кареткою, з подачею візком;
6) за кількістю пилок: одно пилкові, багато пилкові.
7) за кількістю різальних крайок на пилці: з одною, з двома різальними крайками;
8) за комбінуванням з іншими пилковими вузлами: з кругло пилковими вузлами, з фрезерними вузлами.
Схеми найбільш поширених типів стрічкопилкових верстатів наведено рис. 1.2. Ділильні стрічкопилкові верстати призначені для розпилювання товстих дошок і горбилів на більш тонкі. Потреба народного господарства б тонких пиломатеріалах значна і становить близько 15…20% від загальної кількості пиломатеріалів. Випилювання тонких пиломатеріалів на лісопильних рамах має технічні трудності і стримує збільшення продуктивності верстата. Застосування ділильних стрічкопилкових верстатів дозволяє більш раціонально використовувати горбилі, отримувані на лісопильних рамах. Відрізки дощок, відкалібровані по товщині на ділильному верстаті, знаходять широке застосування в клеєних конструкціях, підвищуючи раціональне використання деревини [3].
Колодорозпилювальні стрічкопилкові верстати призначені для поздовжнього розпилювання крупномірної фаутної деревини хвойних порід і розкрою деревини цінних твердих листяних порід.
Горизонтальні стрічкопилкові верстати можуть застосовуватись для розпилювання колод і горбилів. Вісь робочої ділянки стрічкової пилки перпендикулярна вертикальній осі верстата. Колодорозпилювальні стрічкопилкові верстати (рис. 1.2 в) суттєво відрізняються від горизонтальних стрічкопилкових верстатів для розпилювання горбилів. Колодорозпилювальні горизонтальні верстати застосовуються для розпилювання колод великого діаметра, які на вертикальних стрічкопилкових верстатах у складене через малу відстань між стрічковою пилкою і колоною і через складність закріплення колоди на візку.

Рисунок 1.2 - Типи стрічкопилкових верстатів;
а - ділильний: 1 гусениця механізму подачі, 2 - вальці. 3 - гідроциліндр;
б - колодорозпилювальний вертикальний: 1, 4 - пилкові шківи, 2 плита. 3 - стояк станини, 5 - стояк, візка, 6 - рельси;
в - колодорозпилювальний горизонтальний; г - здвоєний стрічкопилковий.
Горизонтальні стрічкопилкові верстати для розпилювання горбилів призначені в основному для ділення по товщині крупник горбилів, оскільки дрібні і середні горбилі простіше розпиляти на вертикальних стрічкопилкових верстатах. Розпилювання крупних горбилів на горизонтальних стрічкопилкових верстатах зручне, оскільки при пилянні горбиль лежить на пласті, займаючи стійке положення. Крім того, спрощується його повернення для повторного розпилювання.
0днопилкові стрічкопилкові верстати при розпилюванні колод малого і середнього діаметрів менш ефективні, ніж лісопильні рами оскільки пиляння здійснюється одною пилкою і 2/3 часу витрачається на допоміжні операції. Ефективнішим є застосування здвоєних і зчетверених стрічкопилкових верстатів прохідного типу, призначений для заміни лісопильних рам першого ряду. Такі верстати мають переваги, характерні як для лісопильних рам (прохідний метод пиляння без повернення розпилюваного матеріалу одночасно декількома пилками), так і стрічкопилковим верстатам (високі швидкості подачі, висока якість за шорсткістю пиломатеріалів, малі втрати деревини в тирсу).
Технічні характеристики стрічкопилкових верстатів наведено в таблиці 1.3. [7].
Таблиця 1.3. - Технічна характеристика стрічкопилкових верстатів
Показники
|
ЛБ240
|
ЛБ150-І
|
ЛДІ 25-1
|
Діаметр шківів, мм |
2400 |
1 500 |
1250 |
Ширина шківів, мм |
290 |
200 |
150 |
Найбільша висота пропилу, мм |
1100 |
900 |
63О |
Товщина пилки, мм |
1,6...2.4 |
1,2...1.6 |
1,0...1,2 |
Швидкість різання, м/с |
50 |
45 |
40 |
Швидкість подачі найбільша, м/хв |
20 |
125 |
5...45 |
Габаритні розміри, мм: |
Висота |
4500 |
4750 |
3700 |
Ширина |
8750 |
7600 |
3100 |
довжина (з рейковим шляхом) |
36000 |
27800 |
5000 |
Маса верстата, кг |
34670 |
29700 |
4900 |
Стрічкопилкові верстати мають наступні переваги: ширину пропилу, низьку шорсткість поверхні пиломатеріалів, відсутність великий сил інерції у вузлах верстата, можливість індивідуального розпилювання з урахуванням особливостей деревини, не потрібно ретельного сортування колод перед розпилюванням. Ці переваги стрічкопилкових верстатів привертають все більшу увагу споживачів, оскільки дозволяють зменшити розхід деревини в стружку, спростити підготовку сировини до розпилювання, автоматизувати лісопильне виробництво.
Застосування на підприємствах стрічкопилкових верстатів зменшує втрати стружку у порівнянні із застосуванням лісопильних рам в 1,5...2 рази, у порівнянні із застосуванням круглопилкових верстатів в 2 З рази. Крім того значно розширює діапазон розмірів оброблюваних матеріалів.
Разом з цим стрічкопилкові верстати мають низьку точність пиляння при великих швидкостях подачі, малу надійність стрічковий пилок, великі габарити, необхідна висока кваліфікація робітників, які підготовлюють пилки і обслуговують верстат. При створенні багато пилкових верстатів ці недоліки набувають те більше значення. В міру усунення вищезгаданих недоліків сфера застосувань стрічкопилкових верстатів може розширюватися [2].
1.2.3 Обладнання із застосуванням вузьких стрічкових пилок
Протягом останнього десятиліття в Україні дедалі більше знаходить застосування стрічкова, технологія розпилювання круглого лісу за допомогою вузьких стрічкових пилок. При цьому застосовуються стрічкопилкові верстати нового взірця (з горизонтальним розміщенням пилки) [1].
Різальним інструментом на них машинах використовуються вузькі і стрічкові пилки шириною до 40 мм і товщиною 0,9...1,1мм. На вітчизняних деревообробних підприємствах застосовують, як правило, імпортні пилки, профіль зубчастого вінця яких зображено на рис 1.5.

Рисунок 1.3 - Профілі вузьких стрічкових пилок
На відміну від вертикальним стрічковопилкових верстатів горизонтальні верстати дозволяють більш зручно, симетрично закріплювати колоду і дають кращу видимість пласті, що відкривається після кожного проходу. Колода, закріплюється нерухомо на напрямних верстата, різання відбувається за рахунок переміщення по напрямний супорта. В горизонтальних стрічкопилкових верстатах кожного різу установка колоди не міняється, а опускається пилковий супорт по колонах станини на товщину дошки. Крім цього, горизонтальні стрічкопилкові верстати дозволяють випилювати і дошки маленької товщини.
В таблиці 1.4 наведено перелік деяких стрічковіпилкових верстатів, що використовуються на українському ринку [5,6,7]
Таблиця1.4.- Стрічковіпилкові машини, що використовуються на українському ринку
Вуд
Майзер США
|
Борд
Мастер Канада
|
СерраФРГ |
Кали-нівка UA |
Прімекс UA |
Ромни UA |
Бевер-1 UA |
Діам. колоди, мм |
900 |
760 |
900 |
760 |
820 |
900 |
900 |
Довж. колоди, мм |
6500 |
6500 |
6500 |
6000 |
6000 |
6000 |
7300 |
Управління |
ручне |
ручне |
Ел.мех |
ручне |
ручне |
Ел.мех |
Ручне |
Потужність, кВт |
11 |
7,5 |
14 |
7,5 |
9 |
н/д |
11 |
Продуктивність, м3/зміну |
6 |
6 |
12 |
3 |
4 |
н/д |
8 |
Ціна базової моделі, тис. USD |
9 |
12 |
50 |
6,5 |
5 |
18 |
12 |
Гарантія |
- |
- |
- |
- |
- |
- |
1 рік |
Досвід використання описаного вище обладнання на лісопильних підприємствах виявив наступні переваги такої технології порівняно із традиційними рамними кривошипними багато пилковими машинами, круглопилковими верстатами та стрічковими верстатами з широкими пилками:
1. Індивідуальний підхід до випилювання кожної дошки, і разом з тим можливість попередньої оцінки її якості і кращого використання властивостей деревини;
2. Можливість розпилювання колод значних діаметрів, які перевищують розміром нормальні просвіти лісопильних рам (деякі із стрічкових лісопильних машин дають можливість розпиляти колоду діаметром 1 метр і більше).
3. Відсутність необхідності попереднього сортування колод як за якістю, так і за розмірами, оскільки індивідуальне розпилювання дає можливість враховувати і те і інше в самому процесі пиляння.
4. За рахунок малої товщини стрічкової пилки (від 0.9 до 1,2мм) товщина пропилу не перевищує 2 мм, що дає значну економію сировини (вихід необрізаного пиломатеріалу в середньому становить 86%, рамні машини - до 65%).
5. Стрічкові машини дозволяють отримати дошку будь-якої товщини від 2 мм.
6. Пиломатеріали, виготовлені на стрічкових машинах, відповідають світовим стандартам щодо рівномірної товщини (різниця в товщині дошки не перевищує 1 мм на всій довжині), а. в розрізі якщо виготовлено брус чи обрізну дошку – мають вид правильного паралелепіпеда, поверхня чиста і під час подальшої обробки знімається мінімальна, стружка.
7. Стрічкові машини мобільні, не потребують фундаменту, і їх може бути встановлено практично в будь-якому місці, а в разі необхідності швидко демонтовано, перевезено і змонтовано на новій виробничій ділянці.
До певної міри недоліком стрічкових лісопильних машин порівняно із рамними є менша продуктивність (від 3 до 10 м3 пиломатеріалів за 8 годин роботи), але більша продуктивність рамних лісопилок в цьому контексті не може розглядатися як перевага - підходячи із точки зору сучасних економічних та екологічних вимог, можна стверджувати, що рамні лісопилки є на порядок "продуктивнішим" у справі переробки круглого лісу на тирсу.
Із наведеного вище випливає, що порівняно із традиційними рамними лісопилками технологія розпилювання колод вузькими стрічковими пилками дозволяє отримати на кожні 4…5м3 круглої сировини додатково 1м3 високоякісного пиломатеріалу. В масштабах країни це означає значну економію такої дефіцитної і довго відтворюваної сировини, як ліс.
Екологічні вигоди (економія сировини і зменшення відходів) в даному випадку ідуть поруч з економічними.
Очевидно, що застосування стрічкової технології для виготовлення обрізної дошки, меблевої заготовки, вагонки, паркету та ін. може дати ніяк не менший, а значно більший економічний ефект, особливо для цінних порід дерева.
2 АНАЛІЗ ТА КЛАСИФІКАЦІЯ ДЕБАРКЕРІВ
В сучасному деревообробному виробництві існує велика кількість засобів боротьби з брудом на колодах. До одного з них відноситься механізм попереднього очищення кори – дебаркер. Дебаркери класифікуються по способу приводу (підводу ріжучого інструменту) та характеристикою ріжучого інструменту [8].
По способу підводу дебаркери бувають гідравлічні та механічні. Гідравлічні дебаркери відрізняється своєю високою вартістю як самого пристрою та його обслуговування, тому застосовувати його доцільніше на більш крупних та розвинутих деревообробних підприємствах. Приклад гідравлічного дебаркеру наведено на рисунку 1.4
 
Рисунок 2.1 – Гідравлічний дебаркер
До більш простих та практичних відносять ся механічні дебаркери. Принцип роботи такий же як у гідравлічних, але матеріальні витрати на обслуговування набагато менші.Приклад механічного дебаркеру наведено на рисунку 1.5

Рисунок 2.2 – Механічний дебаркер
В якості ріжучого інструменту механізму підрізання кори застосовують циркулярні пилки. Дискові пилки з напайками та окорочні фрези. Інструмент вбираються в залежності від виду оброблюваної деревини. Найбільш оброблюваної на підприємстві.
Принци роботи дебаркеру полягає в наступному: на початку розпилювання пилка (фреза) підводиться до колоди і притискається до нього пружиною. В процесі роботи обмежуючий кожух приладу ковзає по колоді, описуючи його профіль, а пилка робить попередній підріз кори в місці входу стрічкової пилки в колоду [9].
Ця операція захищає стрічкову пилку від передчасного виходу із строю внаслідок попадання в пропил піску та бруду, які знаходяться в корі дерева.
В залежності від інструменту, який застосовується, змінюються характеристики дебаркера в цілому. Наприклад окорочна фреза може очищати колоду від кори на глибину 15мм, тоді як циркулярна пилка здібна заглибитися лише на 7мм.
2.1 Обґрунтування необхідності використання дебаркеру
Лісопереробні цехи представляють собою доволі складну та різноманітну за складом виробничу систему, на основі якої лежать технологічні процеси різних видів обробки лісу. Чимале значення при поточному виробництві має рівень механізації операцій обробки лісоматеріалів, що в свою чергу впливає на продуктивність виробництва в цілому.
Для лісопереробних цехів характерна різноманітність розмірів та якості сировини, яка частіше потребує індивідуального підходу до обробки. Часто для первинної обробки подають колоди прямо з лісу, не очищуючи їх від кори, піску та інших домішок. Це призводить до ускладнень в процесі розпилювання, затуплення ріжучого інструменту, а як наслідок зайві витрати на обслуговування обладнання, зниження якості обробки та рівня виробництва в цілому. Верстати та механізми, які використовуються в лісопереробних цехах, повинні мати універсальність та легко перенастроюватися на обробку іншої сировини. Все це створює немалі труднощі при механізації виробничих процесів.
В деревообробному цеху, на ділянці подачі круглого лісу до стрічкопилкового верстата РИТМ-1 існує проблема «брудних колод», тобто грязь та пісок у місці входу пилки. Перед розпилюванням колоди кору необхідно очистити від піску и грязіПилки затуплюються при пилянні брудних колод - іноді достатньо пропилити усього лише 15-20 см. і зрозуміти, що при розпилюванні неочищених колод стрічкова пилка верстату дуже швидко затупляється, має погану якість пропилу. Вирішенням цієї проблеми є застосування дебаркеру, або як його ще називають механізм підрізання кори. Підрізний вузол автоматично чистить кору від грязі з торця колоди, від якого починається розпил.Застосування дебаркера значно підвищує стійкість стрічкових пил та час роботи між переточками збільшуючи строк служби пильної стрічки на 20-25% і, відповідно економить витрати на її обслуговування. До того ж, скорочення перерв у роботі підвищує продуктивність.
3 КОНСТРУКТИВНА ЧАСТИНА
3.1 Вихідні дані для визначення робочих параметрів дебаркеру
Пристрої очищення колод від піску та бруду – дебаркери, відрізняються більшою розмаїтістю за принципом дії, характеру руху робочих органів і конструктивному виконанню. Зустрічаються дебаркери механічні (з механічним способом підведення) та гідравлічні. В якості ріжучого інструменту застосовують як окорочні фрези так і циркулярні (дискові) пилки.
При розрахунку робочих параметрів дебаркеру мається на увазі розрахунок його режимів різання, пов’язаних з режимами роботи всього стрічкопилкового верстата. Вихідними даними для визначення робочих режимів пристрою очищення колод є параметри ріжучого інструменту, його зносостійкість, потужність двигуна пристрою. Все це в сукупності вплине на режими роботи, продуктивність верстата та підприємства в цілому
3.2 Розрахунки режимів роботи верстата
Привід механізму різання здійснюється безпосередньо від асинхронного електродвигуна типу 4АМ13256УЗ потужністю 5,5 кВт та номінальною частотою обертання 930 хв-1.
Пиляння кріпиться на шківах діаметром 450 мм. За. Формулою (1.1) швидкість різання становитиме [10]:
, м/с
м/с,
де D- діаметр пильного шківа, мм;
n- частота обертання пильних шківів, хв-1.
Розраховуємо швидкість подачі
, м/хв. (3.1)
м/хв;
Відстань між траєкторіями руху зубів по векторі подачі розуміється як подача на зуб.
, мм. (3.2)
мм.
де U- швидкість подачі, м/хв; U
=6,55 м/хв
t- крок зуба, мм. t =12 мм.
Зусилля різання розраховують по об'ємній формулі
, H, (3.3)
198,5 H;
де K
-питома робота різання, Дж/см3, по обчисленнях приймаємо К=164;
b
- ширина пропила, b
=1,4мм;
H
- висота пропила, H
=50мм;
U
- швидкість подачі, U
=6,55м/хв
V
- швидкість різання, V
=23м/с
Питома робота різання розраховується по залежності:
по обчисленнях приймаємо 164.
, (3.4)
Дж/см3
де: K - питома робота різання (Дж/см3) залежно від подачі на зуб U . К=164
апопр- поправочний коэф. аu=1,55; аw=0,9; азат=1,6; аd=1,65
(3.5)
3,68
Ширина пропила визначається по формулі
, (3.6)
мм
де: S=0,001
Dш- товщина стрічки, мм;
Dш- діаметр пильного шківа, мм;
S/- розширення стрічки на сторону, мм.
Потужність привода механізму різання розраховується по формулі
, квт; (3.7)
кВт
де: Nрез
-мощность затрачувана на різання, квт;
- КПД механізму різання КПД = для клиноремінної hр
=0,96; підшипників кочення hпк
=0,99. Приймається КПД електродвигуна hэд
=0,96; КПД пильної стрічки hл=0,95
h=hэдhрh2пкhл= 0,9 0,96 0,992 0,95=0,8
Визначимо значення сил різання.
Дотична сила різання
Н, (3.8)
Нормальна, сила різання
Fy = m × Fz = 0,25 ×239,1 = 59,8 H, (3.9)
де m - перехідний множник, m = 0,25 (з справ очних даних).
3.3 Розрахунок робочих параметрів дебаркеру
стрічкова пилка дебаркер деревина
Даний дебаркер має дискову пилку з пластинами з твердого сплаву діаметром 200мм, кількістю зубів 32, шириною пропилу 4мм і глибиною 7мм. В даному випадку глибина може змінюватися в залежності від виду оброблюваного матеріалу і товщини його кори [11]. Пристрої приводиться в дію від електродвигун потужністю 0,55 кВт з частотою обертання 3000об/хв. Даний розрахунок проводимо для колоди діаметром 40см, середньою довжиною 4м, об’єм якої становить 0,5 м3.. Розпилюємо колоду на 12 дошок товщиною 25мм.
Розрахунок швидкості різання дебаркера проводимо аналогічно верстата за формулою 3.1
м/с
Знаходимо значення подачі на зуб за формулою 3.2
мм
Де 6,55м/хв. швидкість подачі пильного механізму верстату. Так як дебаркер встановлюється саме на цей механізм, то й подається з такою ж самою швидкістю.
Визначаємо значення кута контакту [12]:
(3.10)
або
(3.11)
де t
– глибина пропилу, мм

Визначаємо довжину дуги різання:
(3.12)
мм
Знаходимо середню товщину стружки:
(3.13)
де Н=
t
– H висота пропилу, а в нашому випадку глибина, мм.
мм
В залежності від товщини стружки та дуги контакту встановлюємо, що допустима кількість заточок даного інструменту становить приблизно 20, а це оптимальний варіант для даного виду обробки.
Розрахуємо можливу швидкість подачі для дебаркеру при даних його режимах роботи в залежності від кроку зуба пилки:
(3.14)
деtZ
– крок зуба пилки, мм
(3.15)
м/хв.
Одержана швидкість подачі дебаркера майже співпадає зі швидкістю подачі верстата, отже розрахунок режимів різання дебаркеру проведені вірно.
Наступник кроком розрахунків роботи пристрою очищення колод є визначення зусилля різання.
(3.16)
де К
– питома робота різання, Дж/см3.
З довідкових даний та з урахування поправочного коефіцієнту питому роботу різання приймаємо рівною 110 Дж/см3;
b
– з параметрів ріжучого інструменту ширина пропилу складає 4мм:
Н
– глибина пропилу є рівною 7мм;
U
– швидкість подачі, м/хв. В усіх розрахунках приймає швидкість подачі верстата 6,55м/хв.;
V
– швидкість різання дебаркера, м/с
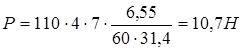
Визначаємо потужність приводу механізму різання дебаркеру:
  
де:Nрез
- потужність затрачувана на різання, кВт;
кВт
- КПД механізму різання Приймається КПД електродвигуна hэд
=0,96 [14];
кВт
З розрахунку бачимо, що потужність різання знаходиться в допустимих межах по відношенню до потужності двигуна дебаркеру.
Визначаємо значення сил різання. Дотична сила різання [13]:
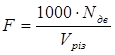
Н
Нормальна сила різання:
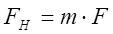
Н
4 ОХОРОНА ПРАЦІ ТА НАВКОЛИШНЬОГО СЕРЕДОВИЩА
4.1 Обґрунтування конструкції горизонтального стрічкопилкового верстата з позиції безпеки праці, ергономіки та екології
Станина верстата зварена із профільних металевих конструкцій. Зварні шви зачищені з допомогою ручних шліфувальних інструментів для забезпечення естетичного вигляду і виключення травмування рук робітників. Всі кромки закруглені [15].
З точки зору сучасної технічної естетики радіуси закруглень загального контуру станини закруглено радіусом R = 150 мм.
Зовнішні частини станини пофарбовані в світло-зелений колір, який діє заспокійливо на робітника, і компенсує шум та вібрацію, які виникають при експлуатації обладнання.
Привод механізмів подачі і настроювання здійснюється мотор-редукторами. З точки зору техніки безпеки таке виконання найбільш безпечне для робітників, так як немає передавальних механізмів, а також муфт, які можуть травмувати робітника. Тип двигуна полезахисний, фланцевий достатньо для надійної його експлуатації в умовах деревообробного цеху []
Органи пуску і керування верстата виконані згідно вимог ГОСТ вимикач, розмішений на передній панелі верстата, а також кнопки включєння-виключення приводу подаю чого візка.
Згідно з ГОСТ 27472-87 діаметр основної кнопки кнопочної станції становить 25 мм [16]. Кнопка вимикача розмішена на 30 мм нижче вмикача, має червоний колір. Довжина робочого ходу - 5 мм.
Крім органів керування на верстаті застосовується і органи настроювання переміщень. Це настроювальний механізм вузла різання, який складається із гвинтового механізму і маховичка.
Враховуючи те, що робота з маховиком проводиться робітником, який знаходиться в стоячому положенні, діаметр маховичка, згідно ҐОСТ 27472-87 становить 200 мм, ширина ободу - 15 мм. Для виключення можливості самовільного ходу гвинтової передачі між ступицею маховика, і стойкою рами встановлена пружина [16].
4.1.1 Механізм різання і подачі
На базовому горизонтальному стрічкопилковому верстаті огородження закриває обидва шківа і неробочу частину стрічкової пилки. Колоди, які проходять розпилювання на верстаті надійно закріплюються гвинтовими затискачами. Вони розміщені в зоні, де виключено попадання на них ріжучого інструмента [17].
Для точного налагодження верстата і забезпечення зручних умов роботи огородження виконані сітчастими або решітчастими.
Виконується блокування огородження за допомогою кінцевих вимикачів таким чином, що при знятті огородження розмикається контакт вимикача, який включений в систему електроживлення двигуна.
4.1.2 Енергонебезпека та електрозахист
На верстаті встановлено асинхронний електродвигун з короткозамкнутим ротором в пилезахисному виконанні.
Ланцюг електросхеми живиться безпосередньо віл сітки напругою 220/380В.
Від перевантаження двигун захищений тепловим реле, а для захисту від струмів короткого замикання - запобіжниками ПР, встановленими в електрокарі.
Ввід силових дротів в шафу управління виконується знизу і здійснюється дротом марки ПГВ перерізом 2,5 мм2 чорного кольору, заземлення тим же дротом зелено-жовтого кольору.
Всі огородження мають електричне блокування за допомогою кінцевих вимикачів, електричні контакти яких при відкриванні огороджень розмикають ланцюг живлення силового електродвигуна [17].
Заземлення приєднується до верстата за допомогою металевої стрічки. Опір розтікаючого струму заземлювачів повинен бути менший або рівний 4 Ом.
4.1.3 Пожежна і вибухова небезпека
Для додержання пожежної і вибухової небезпеки в першу чергу налагоджено надійне видалення відходів, які отримуються при обробці деревини на верстаті. Розрахунок пристроїв, які видаляють відходи забезпечує їх видалення навіть при найбільш можливо великих розмірах частинок.
Під'єднання вентиляційних пристроїв здійснюється зі сторони, куди направлений потік пилу і стружки.
Періодично треба здійснювати перевірку вентиляційних труб для попередження накопичення там дрібного пилу, який може привести до вибухових ситуацій [18].
Робоче місце повинно бути підтримуване в чистоті і не загромаджене заготовками і виробами, для складування яких відводяться спеціальні місця (ССБГ ГОСТ 12.3.042) [19].
4.1.4 Ступінь освітлення робочої зони
При розробці місцевого освітлення користуємось таблицями розподілу освітленості в перпендикулярних площинах осей світильника. Для місцевого освітлення верстата вибираємо світильник СМО-2, і встановлюємо його на шарнірному кронштейні так, щоб світильник знаходився на відстані 0,3 м від зони, що освітлюється. Потужність лампи освітлення вибираємо за таблицею 6. При точності виконання робіт від 1 до 5 мм, освітленість приймаємо Емін=150 лк згідно з СНІП II-4-79 [20]. За таблицею 6 при освітленості 150 лк і напрузі в мережі 24 В вибираємо електролампу потужністю 25 Вт.
Для перевірки правильності підбору лампи розраховуємо її середню освітленість робочої поверхні
, (4.1)
де nпр – кількість освітлюваних приладів, nпр = 1;
Fл – світловий потік вибраної електролампи (Fл = 1050 лк);
ηу- коефіцієнт корисної дії освітлювальної установки, ηу =0,3;
S - площа освітленості, м2, S = 2,4 м2;
к - коефіцієнт запасу, к = 1,2.
Есер = 262 лк.
Есер = 262 лк > Емін = 150 лк.
Отже, світильник вибраний правильно і він задовольняє умови освітлення верстата лампою потужністю 25 Вт.
4.1.5 Захист від шуму і вібрації
Рівень шуму та вібрації значною мірою залежить від якості виготовлення пилкових шківів. Конструкція шківів забезпечує радіальне биття 0,05 мм на радіусі 4 см.
Рівень шуму на верстаті забезпечений високою точністю виготовлення обертових деталей і відповідними огородженнями і становить 80...85 дБ(А) на холостому ході і 85...96 дБ(А) при різанні [21].
Основним елементом огородження, який безпосередньо захищає робітника на робочому місці є передня панель, яка закриває робочу зону.
Рівень звукового тиску L в октавних смугам частот на робочому ходу і допустимі рівні звукового тиску Lд стрічкопилкового верстата за ГОСТом 12.1.003-76.
Таблиця 4.1. - Рівень звукового тиску
Рівень тиску |
63 |
125 |
250 |
500 |
1000 |
2000 |
4000 |
8000 |
L
Lд
|
84,6
99
|
85,9
92
|
97,7
86
|
93,8
83
|
88,1
80
|
85,1
78
|
80,1
76
|
73,7
74
|
Необхідне зниження шуму:
Lн = L – Lд, (4.2)
Таблиця 4.2. - Необхідне зниження шуму
Октавна смуга |
63 |
125 |
250 |
500 |
1000 |
2000 |
4000 |
8000 |
Lн, дБ |
-14,4 |
-6,1 |
8,7 |
10,8 |
8,1 |
7,1 |
4,1 |
-0,3 |
Необхідна звукоізолююча здатність огородження;
, (4.3)
де Sn - площа зовнішньої поверхні огородження. Sn = 1 м2;
Sз - загальна площа з врахуванням поролонових внутрішніх накладок;
Sз = 1 + 0.02*0.9 + 0,02*0,3 + 0,02*0,6 + 0,02*0,4 + 0,02*0,38 + 0,02*0,7 + +0,02*0,8 = 1,12 м2
Для октанової смуги 63:

Подальший розрахунок зводимо в таблицю.
Таблиця 4.3. - Звукоізолююча здатність огородження
Октавна смуга |
63 |
125 |
250 |
500 |
1000 |
2000 |
4000 |
8000 |
Rн |
-13 |
-5,7 |
9,1 |
11,2 |
8,5 |
7,5 |
4,5 |
0,1 |
Таблиця 4.4. - Звукоізолююча здатність стінок панелі із алюмінію і його сплавів
Октавна смуга |
125 |
250 |
500 |
1000 |
2000 |
4000 |
8000 |
Rт, Дб |
20,5 |
17 |
22 |
28 |
32 |
30 |
20 |
З врахуванням звукоізолюючого матеріалу загальна, звукопоглинаюча здатність
, (4.4)
Звукопоглинаючу здатність пінопласту зводимо в таблицю.
Таблиця 4.5. - Звукопоглинаюча здатність пінопласту
Октавна смуга |
125 |
250 |
500 |
1000 |
2000 |
4000 |
8000 |
Rn, Дб |
1 |
2 |
4 |
6 |
7 |
8 |
9 |
Дані розрахунку за формулою 4.4 зводимо в таблицю.
Таблиця 4.6. - Загальна, звукопоглинаюча здатність
Октавна смуга |
125 |
250 |
500 |
1000 |
2000 |
4000 |
8000 |
Rз, Дб |
21,5 |
19 |
26 |
34 |
39 |
44 |
31 |
Вираховуємо звукопоглинаючу здатність з врахуванням конструкції огородження:
, (4.5)
де Rф - поправка на вплив форми звукоізолюючої панелі; Rф = 3 Дб;
Rконст - поправка на вплив виду конструкції панелі, Rконст = 1Д6.
Результати розрахунків за формулою 4.5 зводимо в таблицю.
Таблиця 4.7. - Звукопоглинаюча здатність з конструкції огородження:
Октавна смуга |
125 |
250 |
500 |
1000 |
2000 |
4000 |
8000 |
Rог, Дб |
17,5 |
15 |
22 |
30 |
35 |
40 |
27 |
Порівнюючи Rн і Rог видно, що Rог > Rн, отже панель забезпечує необхідну звукоізоляцію.
Вібрація верстата в основному спричиняється роботою електродвигуна і пилкових шківів.
Найкращий шлях зменшення вібрації - точне виготовлення обертових деталей верстата і виконання технічних умов [22].
Для забезпечення зменшення вібрації в спроектованому верстаті виконано:
-правильно підібрані підшипники;
-передбачено балансування пильник шківів;
-передбачено надійне кріплення всіх елементів конструкції з застосуванням пружних і прогумованих шайб;
- рекомендовані параметри різання які забезпечують мінімальну вібрацію.
4.2 Вибір індивідуальних засобів захисту
При роботі на стрічкопилковому верстаті робітник знаходиться в зоні підвищеного рівня шуму. Цей шум при роботі знаходиться вище санітарних норм і зменшити його технічними засобами на верстаті можна тільки частково.
Отже, необхідно застосовувати індивідуальні засоби захисту.
Індивідуальними засобами захисту від шуму є вкладиші (ГОСТ 12.4.051-87). Для захисту від середньо часткового шуму з рівнем до 100 Дб необхідно застосовувати вкладиші типу «Беруши» із матеріалу ФПП-Ш (ТУ6-162402-80) [23].
5 ЕКОНОМІЧНА ЧАСТІНА
5.1 Обґрунтування економічної ефективності
Лісопереробні цехи представляють собою доволі складну та різноманітну за складом виробничу систему, на основі якої лежать технологічні процеси різних видів обробки лісу Основою сучасного масового виробництва, до якого відносяться лісопереробні цехи, є поточне виробництво. Чимале значення при поточному виробництві має рівень механізації оперцій обробки лісоматеріалів, що в свою чергу впливає на продуктивність виробництва в цілому.
Для лісопереробних цехів характерна велика різноманітність розмірів та якості сировини, яка частіше потребує індивідуального підходу до обробки. Часто для первинної обробки подають колоди прямо з лісу, не очищуючи їх від кори, піску та інших домішок. Це призводить до ускладнень в процесі розпилювання, затуплення ріжучого інструменту, а як наслідок зайві витрати на обслуговування обладнання, зниження якості обробки та рівня виробництва в цілому. Верстати та механізми, які використовуються в лісопереробних цехах, повинні мати універсальність та легко перенастроюватися на обробку або транспортування іншої сировини. Все це створює немалі труднощі при механізації виробничих процесів.
В деревообробному цеху (на базі Красноградського лісгоспу), на ділянці обробки круглого лісу існує проблема «забруднених колод», тобто грязь та пісок у місці входу пилки. Рішення проблеми може бути використання нового сучасного деревообробного обладнання удосконаленого різноманітними допоміжними операціями. Однак не кожне підприємство спроможне піти на заміну старого обладнання. Тому досить актуальним та менш витратним є рішення удосконалення конструкцій обладнання.в даному проекті пропонується застосування на стрічко пилковому верстаті дебаркеру, або як його ще називають механізм підрізання кори. Підрізний вузол автоматично чистить кору від грязі з торця колоди, від якого починається розпил.
Застосування дебаркера значно підвищує стійкість стрічкових пил та час роботи між переточками збільшуючи строк служби пильної стрічки на 20-25%. і, відповідно економить витрати на її обслуговування. До того ж, скорочення перерв у роботі підвищує продуктивність.
5.2 Розрахунок продуктивності верстата
Визначаємопродуктивністьверстату базового варіанту та з застосуванням приладу очищення колод за формулою[24]:
(5.1)
де Т - тривалість зміни, хв;
Кд - коефіцієнт використання робочого дня;
Км - коефіцієнт використання машинного часу;
q– об’єм колоди, м3;
tц - тривалість циклу, хв.
(5.2)
де tУ - тривалість установлення колоди, 1,5хв;
L - довжина, колоди, 4м;
m - число різів на одну колоду 11
VР.Х. - швидкість робочого ходу, 6,55 м/хв
VХ.Х. - швидкість холостого ходу, 10 м/хв;
tрозв - тривалість розвантаження дошки, 0,2, хв;
tн - час налагодження верстата на товщину дошки, 0,083 хв;
tпeр - час на переорієнтацію колоди, 1 хв.
Тривалість циклу: tц=22,1хв
Продуктивність верстата залежить від розмірів розпилюваної колоди та кількості дощок, які необхідно випиляти. Даний розрахунок проводимо для колоди діаметром 40 см довжиною 4 м, об’єм якої становить q = 0,5 м3. Розпилюємо колоду на 12 дощок товщиною 25 мм.
Розрахунок проводимо для базового варіанту.
Знайдемо коефіцієнт використання робочого часу обладнання, так як застосування дебаркеру збільшує ресурс стрічкових пилок, відповідно зменшує кількість замін інструменту у зміну, а значить і час роботи обладнання збільшується [27]:
(5.3)
Топ.ч. - час оперативної роботи обладнання.
Для базового варіанту Топ.ч складється:
Топ.ч=Тзм- (Тп.з+Тобс.+Твідп.+Тв.п) (5.4)
Тзм – тривалість зміни – 480хв;
Тпз – час на підготовчі та заключні роботи – 10хв;
Твідп. – час на відпочинок – 30хв;
Тв.п. – час на власні потреби – 10хв;
Тобс. – час на обслуговування верстату, заміну пилок і т.п.
В базовому варіанті заміна стрічкової пилки проводиться 3 рази, тобто кожні 3 години . На кожну заміну інструменту витрачається 20хв. Таким чином за зміну 60хв тратиться на обслуговування обладнання.
Тоді для базового варіанту:
Топ.=480- (10+60+30+10)=370 хв
При застосуванні механізму підрізання кори ресурс стручкової пилки збільшується на 25%. Таким чином пилка до переточки буде працювати не 3 години, а 4год 15 хв (180хв +45 хв=225хв=4год15хв) , а отже і заміна інструменту буда проводитися 1раз за зміну (20хв). Тоді:
Топ=480-(10+20+30+10)=410 хв
Так як на обслуговування дебаркеру також витрачається час, то проводимо розрахунок і для обслуговування круглої пилки, виходячи з умов, що до переточування вона може пропилити 6км пиломатеріалу (зі швидкістю подачі 6,55м/хв.), тобто 15 годин, що це в середньому складає 1 переточку в 2 робочі зміни На переналадку інструменту витрачається 10хв. Тоді Топ для модернізованого варіанту складає:
Топ =480-(10+10+20+30+10)=400хв
Визначаємо коефіцієнт робочого часу верстату для базового варіанту:
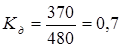
Для модернізованого варіанту:
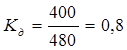
Визначаємо продуктивність верстату за базовим варіантом:
 м3/зм
Годинна продуктивність верстата становить Пгод = 6,8:8=0,85 м3/год.
Річна продуктивність складе Прічне = 6,8·256=1740,8 м3/рік.
Визначаємо продуктивність верстату за модернізованим варіантом:
м3/зм
Годинна продуктивність верстата становить Пгод = 7,8:8=0,97 м3/год.
Річна продуктивність складе Прічне = 7,8·256=2022,3 м3/рік.
Таким чином
(5.5)

5.3 Розрахунок капітальних вкладень
Капітальні вкладення на проектування та виготовлення дебаркеру визначаємо за формулою[26]:
Кн = Кт + Кб + Км +
Кп+ О(5.6)
де Кт - вкладення, щоскладаються з вартості матеріалів, транспортних витрат, монтажнихвитрат;
Кб - затрати на будівельні роботи;
Км - затрати на модернізацію;
Кп - затрати на проектні роботи, Кп = 500,0 грн.;
0 - сума оборотних засобів.
Враховуючи відсутність будівельних робіт, витрат на модернізацію формула набуде вигляду:
Кн = Кт + Кп. (5.7)
Вартість матеріалів для виготовлення механізму підрізання кори визначаємо за формулою:
Ц = (М · 3 + Д) · П, (5.8)
де М - маса пристрою, без комплектуючих;
З - собівартість 1 кг маси механізму різання верстата;
Д - вартість комплектуючих;
П - коефіцієнт рентабельності галузі, П = 1,1.
Таблиця 5.1. – Перелік комплектуючих дебаркеру
Назва комплектуючих |
Вартість, грн |
Електродвигун 0,55кВт |
280 |
Пилка дискова, D=200мм |
260 |
Сталь листова 1м2 |
160 |
Круг металевий |
15 |
Куток сталевий 30 для рамки |
10 |
Пружина |
15 |
Витрати на виготовлення |
300 |
Усього |
1040 |
Визначаємо вартість пристроюпідрізання кори:
Ц = (4824 +1040) · 1,1 = 6450,4 грн.
Витрати на транспортування і монтаж приймаємо 12% від ціни за обладнання
Втр.м = 6450,4 · 0,12 =774 грн.
Тоді, вкладення, щоскладаються з вартості матеріалів, транспортних витрат, монтажнихвитрат:
КТ=6450,4 +774=7224,4 грн.
Отже, нові капітальні вкладення дорівнюють
Кн= 7224,4 + 500,0 = 7724,4 грн.
5.4 Розрахунок заробітної плати
Для роботи в умовах підприємства необхідно оператор керування верстатом IV розряду та двох робітників ІІ розряду. Оплата здійснюється за виконану роботу з розрахунку по трудовитратах: 1 люд/год - 4 грн. для оператора і 2,6 грн. для робітників.
Визначаємо основну і додаткову зарплату робітників. Годинна тарифна ставка на підприємстві 1,2 грн.
Ефективний фонд робочого часу робітника в рік становить 2188,0 годин
Основна заробітна плата [27]:
(5.9)
Зоп=
2188·4=8755 грн.
Зроб=
2188·2,6=5688 грн.
Зо=
8755+5688=20131 грн.
Відрахування на соціальне страхування складає 47,5%

5.5 Визначення вартості електроенергії
Вартість електроенергії, грн. [27]:
(5.10)
де М - встановлена потужність, в даному випадку вона складається з потужності верстата та потужності завантажую чого пристрою, М=10 кВт;
Кс. - коефіцієнт попиту, Кс=0,8
То - річний ефективний фонд робочого часу обладнання;
Цел - ціна 1 кВт/год електроенергії, грн;, ЦЄл = 0,48 грн/кВтг.
- коефіцієнт корисної дії електрообладнання, ц = 0,9.
Річний фонд часу То = 2188 год.
Вартість електроенергії: базового варіанту:

Проектного варіанту:

5.6 Визначення амортизаційних відрахувань
Амортизаційні відрахування складають 15,0% від ціни верстата.
Ціна базового верстата 30000 грн.
Ціна проектного устаткування 34400 грн.
Амортизаційні відрахування базового варіанту:

Проектного варіанту:

5.7 Розрахунок витрат на утримання і ремонт верстатів
Витрати на утримання і ремонт складають 15% від капіталі вкладень завантажую чого пристрою[27]:

5.8 Розрахунок вартості інструменту
Вартість інструменту знаходимо виходячи з річної потреби в інструменті [28].
На підприємстві маємо 8 годинний робочий день, 5 днів у тиждень. Знаходимо кількість годин роботи верстату в тиждень (враховуючи коефіцієнт трудовитрат 0,85) та в рік:
8·5·0,85=34 год (за тиждень);
34·48 = 1632 год (за рік)
Визначимо кількість замін інструменту за рік для базового варіанту:
1632:3 = 544 замін
За технічними характеристиками стрічкових пилок кількість можливих переточок складає 15, тоді 544:15=36 пилок за рік, а враховуючи запас 36·1,1=39 пилок. Таким чином річна потреба в інструменту на рік складає 39 пило по 2000грн кожна.
Витрати на інструмент:
36·2200=79200грн
Проводимо розрахунок витрат на заточку стрічкових пилок.
Стрічкова пилка довжиною 4м та кроком зуба 22м, кількість зубів пилки складає 4000:22=182 зуби. Вартість заточки одного зуба складає 0,2 грн, тоді:
182·0,2=36 грн
За рік вартість переточок 39 пилок складе:
36·544=19584грн;
Визначимо кількість замін інструменту за рік для модернізованого варіанту. Так як застосування дебаркеру збільшує ресурс пилок на 25%, то при його застосуванні річна потреба в інструменті складе 39·75%=29 пилок по 2000грн кожна:
29·2200=63800грн
Витрат на заточку стрічкових пилок складуть:
36·29·15=15660грн
Визначимо витрати на обслуговування дебаркеру. Умови роботи такі ж як і для стрічкових пил 1632 години на рік, але розрахунок проводимо для 14 годин роботи до переточки (для кратності з умовою заміни інструменту кожні 2 зміни):
1632:14 = 116 замін за рік
З технічних характеристик дискової пилки з твердими напайками маємо,що кількість допустимих переточок складає 20, тоді річна потреба пилок складає:
116:20=5,8=6 пилок
Вартість однієї дискової пилки для даного механізму 200грн - 6·200=1200грн.
Вартість заточки одного зуба дискової пилки складає 0,4грн, кількість зубів 32. тому:
116·32·0,4=1484грн
Таким чином вартість інструменту для модернізованого варіанту складає:
63800+1200=65000грн
В результаті розрахунків виходить:
Різниці базового та модернізованого варіантів складає:
-з точки зору перезаточки
Езат.=Езат б.-Е зат м (5.11)
Езат= 19584-(15660+1484)=2440грн
-з точки зору витрат на річну потребу інструменту
Еінст=79200-65000=14200грн
Таким чином з розрахунків видно, що загальна економія при застосуванні дебаркера тільки на інструменті та його обслуговуванні за рік складе:
14200+2440=16640грн
Собівартість за статтями затрат зводимо в таблицю 5.2.
Таблиця 5.2. - Собівартість по статтях витрат
Статті витрат |
Базовий варіант, грн |
Проектний варіант, грн |
1. Річні витрати на інструмент
2. Витрати на обслуговування інструменту
3. Заробітна плата
4. Вартість електроенергії
5. амортизаційні відрахування
6. Відрахування на утримання і ремонт
Всього
|
79200
19584
20131
9335,5
4500
-
132750,5
|
65360
17144
20131
9848,9
5160
813
118456,9
|
5.9 Розрахунок економічної ефективності
Основними показниками для визначення економічної ефективної проекту є умовно-річна економія, яка визначається за формулою[28]:
(5.12)
де С1, і С2 - собівартість базового і проектного варіантів:
(5.13)
(5.14)
де ВБ, ВМ – загальні витрати по стаття базового та модернізованого варіантів;
ПБ, ПМ – продуктивність базового та модернізованого варіантів за рік;
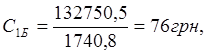
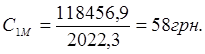

Таким чином умовна річна економія при застосуванні дебаркеру складає 36401,4 грн.
Визначаємо строк окупності устаткування за формулою:
(5.15)
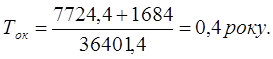
З розрахунку бачимо, що застосований пристрій для очищення колод окипиться майже за два місяці.
Виконуємо оцінку доцільності запровадженого проекту, визначаючи рентабельність вказаних капітальних вкладень:
(5.16)
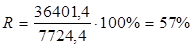
Річний економічний ефект
Ееф = Еур – Ен · Кзаг, (5.17)
де Ен = 0,15 - нормативний коефіцієнт економічної ефективності.

Ріст продуктивності праці.
Ріст продуктивності праці визначаємо ва формулою:
(5.18)
де ПП1, ПП2 - продуктивності модернізованого і базового варіантів

Основні техніко-економічні показники зводимо до таблиці 5.3.
Таблиця 5.3. - Основні техніко-економічні показники
Показники |
Одиниця виміру |
База |
Проект |
1. Річна продуктивність верстата |
м3/рік |
1740,8 |
2022,3 |
2. Додаткові капітальні вкладення |
грн. |
- |
7724,4 |
3. Умовно-річна економія |
грн. |
- |
36401,4 |
4. Собівартість обробки 1м3 лісоматеріалу |
грн |
76 |
58 |
5. Собівартість по статтях затрат |
грн |
132750,5 |
118456,9 |
6.Термін окупності загальних капітальних вкладень |
роки |
0,4 |
7. Рентабельність впровадження проекту |
% |
- |
57 |
8 Ріст продуктивності праці |
% |
- |
16,2 |
9. Річний економічний ефект |
грн |
- |
35242,8 |
Оцінка економічної ефективності проекту та висновок
Розрахунок техніко-економічних показників показав доцільні вигідність даного проекту.
При загальній сумі додаткових капітальних вкладень – 7724,4 грн. і умовно-річній економії 36401,4 грн. проект окупиться за 0,4 року. Обчислене значення рівня рентабельності задовольняє умові R≥0,15, що вказує на доцільне запровадження пристрою для очищення колод від бруду та піску. Сума річного економічного ефекту складає 35242,8 грн, а продуктивність праці виросте на 16,2%.
Таким чином, можна зробити висновок, що проект економічно оправданий.
ВИСНОВОК
Виконана модернізація дільниці по обробці круглої деревини на стрічкопилковому верстаті, визначається простотою конструкції дебаркеру, який не вимагає вартісних комплектуючих виробів.
Модернізація може бути виконана в умов ремонтно-механічних майстерень.
Обслуговування може здійснюватись робітником 2 розряду, а ремонт проводитись ремонтниками ремонтної служби цеху.
В проекті передбачені засоби по зменшенню шуму, вібрації та очищенню робочої дільниці від стружки, що дозволяє безпечно працювати на верстаті.
Впровадження дебаркеру дозволить значно зменшити річні витрати на інструмент і збільшити продуктивність верстату, а тим самим і продуктивність всього цеху.
СПИСОК ВИКОРИСТАНИХ ДЖЕРЕЛ
1. Прокофьєв Г.Ф. Интенсификация пиления древесины рамными и ленточными пилами. - М.: Лєсн. пром-сть, 1990. - 240 с.
2. Манжос Ф.М. Дереворежущие станки. - М.: Лесн. пром-сть, 1974. 453 с.
3. Амалицкий В.В. Станки и инструменты лесопильного и деревообрабатывающего производства. - М.: Лесн. пром-сть, 1985. - 288 с.
4. Настенко А.А. Подготовка ленточных пил. - М.: Лесн. пром-сть, 1989. - 152 с.
5. Проспект СП "РОЙЄК-ЛЬВІВ" (Польща).
6. Проспект Р. Р. WIREX (Польща).
7. Проспект НВО БЕВЕР (Україна).
8. Лившиц Н.В., Меньшиков Б.Е. Механизация околостаночных операций в лесоперерабатывающих цехах.- М.: Лесная промышленность, 1975 – 176с.
9. Проспект фірми WOODMIZER (США).
10. Баракинов В.И., Жаринов А.В., Юдина Н.Д. Прогрессивные режущие инструменты и режимы резания металлов: Справочник..- М.: Машиностроение. 1990. - 400 с.
11. Шостак В.В., Савчук Я.І. Методичні вказівки до виконання проекту з дисципліни «Теорія і конструювання деревообробного обладнання». - Львів: Редакційно видавничий центр УкрДЛТУ. 2004.-44с.
12. Пижурин А.А. оптимальные режимы пиления дисковыми пилами.-М.: Лесн. пром-сть, 1988.-48с.
13. Ординарцев И.А. Справочник инструментальщика. - Л.: Машиностроение. Ленинград. отделение. 1987. - 846 с.
14. Скороходов А.Е., Законников В.П., Пикнис А.Б. Общетехнический справочник. – М.: Машиностроение, 1990.- 496с.
15. Апостолюк С.О.,Джиги рей В.С., Книш Ю.В. Охорона праці в лісопильно-деревообробному виробництві. Навч.пос. -Київ: Основа, 2003. – 288с.
16. ГОСТ 27472-87 Средства автотранспортные специализированные. Охрана труда, эргономика. Требования.- М.: Изд. станд., 1987.-16с.
17. Симсон И.И. Техника безопасности при механической обработке древесины. - Л.: Машиностроение, 1977. - 188 с.
18. СНип II-33-87. Отопление, вентиляция и кондиционирование воздуха. -М.: Изд. станд., 1987.-16с.
19. ГОСТ 12.3.042-88. ССБТ. Деревообрабатывающее производство. Общие требования безопасности.- М.: Изд. станд., 1988.-16с.
20. СНиП II-4-80. Строительные нормы и правила. Естественное и искусственное освещение.- М.: Изд. станд., 1980.-17с.
21. ГОСТ 12.1.003-83. ССБТ. Шум. Общие требования безопасности.- М.: Изд. станд., 1988.-16с.
22. ГОСТ 12.1.012-78. ССБТ. Вибрация. Общие требования безопасности.- М.: Изд. станд., 1988.-16с.
23. ГОСТ 12.4.051-87. Средства индивидуальной защиты. Общие требования безопасности.- М.: Изд. станд., 1988.-17с.
24. Справочник экономиста деревообрабатывающей промышленности / В.С. Рыбалко, В.Г. Морозов и др. – М.: 1974. - 438 с.
25. Саклаков В.Д., Сергеев М.П. Технико-экономическое обоснование выбора средств механизации. – М.: Колос, 1973. – 200 с.
26. Воронин И.В., Васильев П.В., Судачков Е.Я. Экономика лесного хозяйства СССР. – М.: Лесная промышленность, 1978. – 264 с.
27. Петров А.П., Бельдиева А.А., Дикарева О.А., Климонтова Л.Я. Экономика лесного хозяйства. – М.: ВНИИЛМ, 2002. – 304 с.
28. Никифоров А.Ф. Основы определения экономической эффективности новой техники и технологии по обработке древесины. – Л.: ВЗЛИ, 1963. – 98 с.
29. Марочник сталей и сплавов / В.Г. Сорокин, А. В. Волосникова, С.А. Вяткин и др.; Под общ. ред. В.Г. Сорокина. - М.: Машиностроение, 1989. - 640с.
30. Гузенков П.Г. Детали машин. - М.: Высш. школа, 1982. - 351 с.
31. Данилевский В.В. Справочник молодого машиностроителя. - М.: Высш. школа. 1973 - 698 с.
|