Министерство образования российской федерации Санкт-Петербургский институт Московского государственного университета печати. Факультет Полиграфических технологий и оборудования. Специальность 261202. Форма обучения интегрированная. Кафедра технологии полиграфического производства
Курсовая работа
Тема работы: "Металлизированные краски и их основные особенности"
Студент Никифорова М.А. гр. ВТ- 4.2
Руководитель
канд. хим. наук, доцент Груздева И.Г.
2008 год
Реферат
Записка 32 с., 6 рис., 3 табл., 8 источников.
Металлизированные краски, металлизированные пигменты, офсетная печать, связующее, растворитель, абсорбция, эмульгирование.
Объектом исследования являются металлизированные краски.
Цель работы заключается в исследовании основных особенностей и проблем печати металлизированными красками.
В процессе работы были подробно рассмотрены состав и разновидности металлизированных красок, их основные свойства и особенности печати. Отдельная глава посвящена проблемам, возникающим при печати данными красками и способам их устранения.
Результаты исследования металлизированных красок выявили преимущества и недостатки их основных свойств и печатных характеристик.
Содержание
Реферат
Введение
1. Состав и разновидности металлизированных красок
2. Особенности печати металлизированными красками
3. Проблемы, возникающие при печати металлизированными красками
Заключение
Список использованных источников
Приложение
Введение
флексографический печать металлизированный краска анилокс
Эффект металлического блеска применяется при оформлении самой разнообразной печатной продукции. Металлизированные элементы бросаются в глаза, привлекая внимание к оттиску. Наиболее дешевым способом нанесения металлизированных покрытий является печать металлизированными красками.
Металлизированные краски обеспечивают отличный эстетический результат. Они способны придать обыкновенному печатному оттиску волнующий блеск благородного металла.
Непревзойденное по красоте чистое самородное золото — первый из открытых человеком металлов. Его применяли для украшения — в том числе и рукописей. В особенно роскошных рукописях названия разделов, инициалы, начальные буквы прописывали золотом. Известны рукописные книги, полностью написанные золотом или серебром по белому или окрашенному в пурпурный цвет пергамену. Кстати, красная краска — киноварь — тоже имела в своем составе серебристый металл — ртуть.
Для защиты печатной продукции от подделки используются краски со специальными свойствами.
В настоящее время все большее применение находят покрытия с различными оптическими эффектами, в которых при покраске используются блестящие металлизированные пигменты. Согласно DIN 55944 краска со специальным оптическим эффектом называется – металлик.
Пигменты с эффектом металлик представляют собой частицы алюминия пластинчатой формы, реже – меди, цинка, латуни или бронзы. Краска металлик появилась в середине восемнадцатого века, как альтернатива золочению или серебрению очень тонкими микропластинками драгоценных металлов. В середине девятнадцатого века металлизированные частицы начали производить в промышленных масштабах, но, по-прежнему, использовались для отделки произведений искусства и архитектуры. Лишь во второй половине двадцатого века металлизированные пасты получили повсеместное распространение: мебель, интерьер, автомобили и пр.
В данной работе рассмотрены возможные проблемы, возникающие при работе с металлизированными красками, и способы их устранения.
1. Состав и разновидности металлизированных красок
Настоящего золота или серебра в современных металлических печатных красках, конечно же, нет. Но они очень удачно имитируют благородные металлы, так как на треть состоят из металлических пигментов серебристого или золотистого цвета. Серебристый оттенок обеспечивает алюминиевая пудра, а золотистый — бронзовая, полученная из сплава меди и цинка. Строго говоря, бронзой называются сплавы меди с оловом, алюминием, свинцом или хромом. Сплав меди с никелем — это мельхиор, а с цинком — латунь. Тем не менее, пудра из сплава меди и цинка почему-то называется не латунной, а бронзовой, — видимо, по инерции: первые порошки для "бронзирования" производились из оловянистой меди, то есть из истинной бронзы. И возникло такое производство еще в 18-м веке, однако бронзовые печатные краски появились только в конце 19-го столетия. Оттенок "самоварного золота" зависит от соотношения двух металлов: чем больше в сплаве розовато-красной меди, тем более красноватый получается оттенок. Если меди 80% — цвет пигмента желтоватый, если 70% — уже зеленоватый (cм. таблица 1).
Таблица 1. Оттенки золотисто-бронзовых красок
Наименование |
Цвет |
Медь |
Цинк |
Reichgold/Richgold |
Зеленоватый |
70% |
30% |
Reichbleichgold/Richpalegold |
Желтоватый |
80% |
20% |
Bleichgold/Palegold |
Красноватый |
90% |
10% |
Получение металлизированных пигментов состоит из целого ряда производственных этапов. Сначала алюминиевые электроды распыляют в электрическом поле при температуре чуть выше температуры плавления алюминия при высоком давлении и получают гранулы размером от нескольких до сотни микрон. Далее полученные гранулы перемалывают в шаровых мельницах в присутствии органических кислот, как смазочного материала, чтобы избежать холодного спаивания металлических частиц. После перемалывания частицы алюминия не только меняют свой размер, но и приобретает пластинчатую форму. Следующий этап – просеивание, удаляются агломераты и выделяются фракции металлика с максимально узким распределением по размеру. На заключительной стадии производства металликов частицы проходят поверхностную обработку для придания специфических оптических свойств.
Металлики делятся на два типа: всплывающие и невсплывающие, что характеризует степень смачиваемости пигментов в краске. Всплывающие пигменты из-за высокого поверхностного натяжения не смачиваются и всплывают на поверхность мокрой пленки при нанесении на изделие и ориентируются параллельно подложке.
Невсплывающие, напротив, полностью смачиваются связующим и равномерно распределяются по всей толщине лакокрасочного покрытия. Металлики всплывающего типа дают ровный серебристый блеск, так называемый хром-эффект или эффект хромирования.
Краска металлик характеризуется двумя основными параметрами: блеском (metallicbrilliance) и искрением (sparkle-effect). Первый описывает уровень отражения, другими словами, чем выше доля отраженного света по отношению к рассеянному или поглощенному, тем большим блеском характеризуется эффект металлика. На практике чем более совершенна поверхность металлизированного пигмента (отсутствие дефектов), чем выше отношение площади к периметру отдельного пигмента (в идеале – круглый диск) и чем уже распределение по размеру частиц, тем выше показатель брилеанса. Очень мелкие пигменты с нерегулярной формой и широким распределением по размерам дают просто серый цвет мало напоминающий серебристый металлик. Искрение наблюдается, когда можно увидеть отражение от отдельных частиц металлизированного пигмента. Для этого эффекта важен размер частиц, он должен быть от 25 микрон и более. Также большую роль играет идеальность формы, распределение по размеру и ориентация металлика в пленке краски.
При использовании в краске металлик только алюминиевого металлизированного пигмента получается серебристый металлик. Для придания, какого либо цвета краске, например синий металлик, зеленый металлик или серый металлик в краску вводят высокодисперсные колеровочные пигментные пасты. Таким же способом можно при покраске получить золотой или бронзовый металлик, соответственно. Использование напрямую медных, бронзовых или латунных пигментов ограничено из-за слабой их светостойкости и атмосферостойкости.
Как известно, краски — это не только пигмент. Это дисперсии пигментов в связующем — в воде или пленкообразователях. К примеру, для масляных красок пленкообразователями выступают масла (высыхающие и олифы), для эмалевых — лаки, для клеевых — крахмал или казеин, силикатных — жидкое стекло, эмульсионных — водные дисперсии синтетических полимеров. Теперь производители металлизированных красок чаще всего поставляют их уже готовыми, а в прежние времена такие краски поставлялись на полиграфические предприятия только в виде двухкомпонентной системы, состоящей из пигментной пасты и связующего. Процесс приготовления красок при помощи дрели с насадкой-смесителем требовал большой аккуратности и ловкости. Нужно было получить однородную массу с гладкой поверхностью, но при чересчур старательном размешивании хрупкие металлические чешуйки повреждались и уже не давали нужного блеска. Каждая частица металлического пигмента, или шлифа, — это не комок, а неправильной формы плоский листик, чешуйка, пластинка тонко расплющенного металла. За счет наложения этих частиц при печати друг на друга и обеспечивается требуемый металлический эффект.
Для разных способов печати применяется пигмент из того же самого металлического сырья, но с частицами разного размера. Для офсетной и высокой печати нужны чешуйки толщиной около 0,1 микрона и диаметром 3,5 микрона. А для глубокой и флексографической печати частицы шлифа с такой же толщиной имеют диаметр от 8 до 9 микрон. Казалось бы, самый простой способ усилить блеск — это применить пигмент с увеличенными частицами. Но для хороших кроющих свойств в краске нужно поддерживать достаточно высокое содержание пигмента, а увеличение размеров металлических частиц ведет к ослаблению действия связующих веществ и оседанию, выпадению бронзовых или алюминиевых пигментов в осадок. Срок хранения готовой краски резко сокращается. При глубокой печати наличие в краске частичек размером свыше 10 микрон ведет к образованию на оттиске поглощения и других дефектов — в основном, из-за нежелательного накапливания краски позади ракеля. Такие наслоения краски время от времени "выскакивают" из-под ножа, заметно ухудшая качество готовой продукции. Отсюда следует, что в металлических печатных красках нельзя использовать частицы произвольного размера, а при комбинировании надо придерживаться определенного баланса.
Сухой металлический порошок превращается в пригодную для печатных процессов краску благодаря связующим, обволакивающим и несущим каждую частицу пигмента. Предварительно порошок слегка увлажняют для облегчения последующего смешивания. Естественно, состав связующих у красок, предназначенных для разных способов печати, разный. В состав фирнисов (приготовленных связующих) для офсетных красок входят твердые смолы (модифицированная канифоль и/или углеводородная смола), алкидная смола на растительной основе, минерально-масляный разбавитель, растительные масла, структурообразователи. Связующие для красок, используемых в глубокой печати, включают в себя производные целлюлозы (нитроцеллюлоза, этилцеллюлоза, целлюлозаацетатбутират и целлюлозаацетопропинат), полиамидные смолы, сополимеры винила и другие смолы.
Всего в производстве красок применяются не менее тысячи наименований компонентов связующих. Понятно, что количество возможных комбинаций бесконечно. Вот почему разработано столько серий красок, различных по своим свойствам, хотя пигментов для металлизированных красок изначально только два. Меняется состав, меняются пропорции компонентов, меняются свойства продукции. Естественно, прежде всего, при создании композиции краски учитывается метод печати. Так, краски для высокой и офсетной печати должны быть гораздо более вязкими, чем краски для глубокой и флексографской печати. И тут решающее значение приобретает выбор растворителя и определение его пропорции.
В офсетных машинах красочный аппарат состоит из множества валиков, и краска довольно долго находится в машине. Если бы она содержала легколетучие растворители, то успевала бы, высыхая, много раз изменить свои свойства за время печатания, чего не должно быть ни в коем случае. Поэтому в офсетных красках используются малолетучие разбавители с очень высокой (до 300 градусов и выше) температурой кипения — минеральные масла (см. таблица 2).
Таблица 2. Диапазон кипения разбавителей для офсетных красок (в градусах Цельсия)
Для красок хит-сет |
240-290 |
Для красок листовой офсетной печати |
280-310 |
Для красок колд-сет |
280-370 |
Количество разбавителя в пастообразных офсетных красках обычно не превышает 30%. А вот в составе жидких красок для глубокой и флексопечати очень много — более 65% — растворителя. В идеале он должен иметь минимум цвета, запаха и токсичности, а также испаряться без остатка. Растворители для жидких красок кипят при низких (до 100 градусов) и средних (до 150 градусов) температурах. Только диацетоновый спирт, который уже не используется в производстве красок, относился к высококипящим (точка кипения 166 градусов Цельсия).
Говорить что-либо конкретное о химическом составе красок и, особенно о новых рецептурах и технологиях не принято, так как производители держат эти сведения в секрете друг от друга.
В производстве красок для глубокой печати в качестве растворителей до недавних пор применяли толуол (бесцветная горючая жидкость, добываемая из каменноугольной смолы и продуктов нефтепереработки) и другие вредные с точки зрения экологии ароматические углеводороды. Понадобилось найти им приемлемую замену. При создании металлизированных красок нужно учитывать, что металлические пигменты лучше всего взаимодействуют с неполярными растворителями, имеющими высокое поверхностное натяжение. Использовать в этом случае низкомолекулярные спирты нежелательно. На одной из стадий производства металлической краски к пигменту добавляется смазочный материал на основе концентрированной жирной кислоты, чтобы придать поверхности металла гидрофобные и олеофобные свойства. Но низкомолекулярные спирты разрушают получившуюся на поверхности металла защитную пленку. Удовлетворительный результат дает изопропиловый ацетат, который является хорошим растворителем для типичных связующих, применяемых в металлизированных красках, и оставляет после себя меньше следов, что особенно важно для кондитерской и табачной упаковки. Изопропилацетат - легколетучий растворитель,- может в небольших количествах использоваться также и в офсетных металлизированных красках.
Применение вместо толуола сложных эфиров сказывается на смачивающей способности растворителя. Одним из важных преимуществ толуола была способность прекрасно смачивать цилиндр в точке контакта с ракельным ножом в ходе печатания тиража, улучшать скольжение и качество работы ракеля, что положительно сказывалось на качестве готовой продукции. С эфирными растворителями степень смачивания снизилась, и это нужно как-то компенсировать. В отсутствие ароматических углеводородов наиболее эффективный способ повысить смачивающую способность — это использовать пластификаторы — субстанции с низкой летучестью, которые улучшают пластические качества смол и одновременно могут действовать как смачивающие вещества в рецептуре металлизированных красок. /1/
При взгляде на химическую формулу типичных смол или канифолей, которые используются в промышленности, видно, что это высокомолекулярные соединения, в которых молекулы связаны между собой только в одном продольном направлении. Химические связи эффективно действуют только по длине полимерных цепочек, а между отдельными цепочками они очень слабые — скорее, физической, чем химической природы, а значит, пригодны для модификации пластификаторами. Степень пластификации зависит от молекулярной структуры полимера и самого пластификатора, а также от силы притяжения между полимерными цепями. Пластификаторы также способствуют испарению летучих веществ растворителя в определенных канифолях. Целлюлозные эфиры имеют свойство соединяться с некоторым количеством растворителя, но в присутствии пластификатора растворитель испаряется лучше и полнее, содержание остаточного растворителя в высохшей красочной пленке минимально.
Мерой эффективности пластифицирующих компонентов является "glasstransitiontemperature" — Tg. Упрощенно эту величину можно представить как температуру стеклования.
Большая часть пластификаторов, базирующихся на дифенилфосфате или глицерилтриацетате, хорошо зарекомендовала себя в большинстве красочных систем. Тем не менее, использовать их надо с осторожностью, так как они могут портить упаковку и понижать прочность красочного слоя.
Казалось бы, выбор смол диктуется выбором растворителей, которые можно применять для металлизированных красок. Поэтому в поисках безвредных технологий пытались обратиться к совершенно новым смолам и растворителям для создания безуглеводородных металлизированных красок. На практике обнаружилось, что многие из уже известных смол, применявшихся ранее в системах на базе толуола, вполне пригодны в сочетании со сложноэфирными и подобными им растворителями. Идеальными оказались низкокислотные акрилы и целлюлозные эфиры, образующие растворы с низкой вязкостью и едкостью (высокая едкость может неблагоприятно повлиять на металлические частицы и вызвать нежелательные химические реакции, поэтому лучше всего подходят для металлических красок смолы с кислотными номерами менее 10).
Чем лучше растворимость и восстановимость смол, тем лучше стойкость и стабильность краски при печати, меньше накопление краски позади ракельного ножа и тем реже появляются полошение и тенение. При создании рецептур красок было бы гораздо проще иметь дело с одной группой смол и одной группой растворителей, однако обычно приходится модифицировать металлизированные краски дополнительными смолами, улучшающими стойкость к истиранию, блеск и другие полезные качества. Но это опять-таки должны быть низкокислотные смолы с хорошей растворимостью.
Изменения в технологии изготовления и применения металлизированных красок были вызваны возросшими требованиями заказчиков и законодателей. Пришлось искать новые красочные рецептуры на основе растворителей и одновременно разрабатывать металлизированные краски на водной основе. В узкорулонной флексографской печати уже сегодня широко применяются водорастворимые металлизированные краски, так как в этом секторе традиционно работают с красками на водной основе и здесь приняты собственные стандарты.
Строго говоря, вода тоже является растворителем, только неорганическим, и относится к очень труднолетучим: число испарения воды — 90, то есть она испаряется в 90 раз медленнее, чем эфир. Кроме того, вода по сравнению с другими растворителями имеет более сильное поверхностное натяжение. Но ведь искусственные смолы, которые применяются в качестве связующего, не растворяются в воде! Чтобы сделать их водоразбавляемыми, смолы эмульгируют в воде подобно дисперсии или нейтрализуют аммиаком или органическими аминами (омыливание). Понятно, что водорастворимые краски сохнут медленнее, чем обычные, и ускорить этот процесс можно повышением температуры, дополнительной вентиляцией, снижением скорости печати и уменьшением высоты стопы. При глубокой печати глубину травления печатного цилиндра также необходимо уменьшить.
Водорастворимые краски сильнее подвержены пенообразованию, чем обычные. К тому же их труднее смывать. Из-за своего химического состава водорастворимые краски и лаки хорошо закрепляются. Поэтому валики и цилиндры должны двигаться до самого завершения работы, а после прогона тиража необходимо все части машины, контактирующие с краской, незамедлительно промыть водой или смесью воды и этанола. Засохшую краску можно удалить с помощью смеси: вода, этанол, аммиак или амин и любое чистящее средство. Этилацетат также хорошо очистит засохшие цилиндры. Краски, содержащие воду, ни в коем случае нельзя оставлять на морозе.
В отличие от грунтовых золотых красок или офсетных бронзовых красок, которые закрепляются в результате окислительной полимеризации, краски по композиции связующего аналогичные дисперсионным лакам не имеют характерного запаха и подходят для печати на упаковках пищевых продуктов и сигарет. По качеству передачи металлического блеска и степени глянца оттиски, полученные с использованием данных красок, которые можно наносить через модифицированную лаковую башню офсетной печатной машины, намного превосходят достигаемый сегодня результат офсетной печати. Эти краски поставляются, как в однокомпонентном, так и в двухкомпонентном виде.
Интересно, что для достижения различных золотых оттенков в этих красках применяются наряду с металлическими интенсивные цветные пигменты с высокой степенью прозрачности. Вводить красочные подцветки можно самостоятельно, используя специальную серию концентрированных красочных паст.
Преимущества становятся очевидными при сравнении данного способа с бронзированием. Для грунтования золотой краской и бронзирования требуются дополнительные рабочие операции и площади для промежуточного хранения оттисков между операциями. К тому же процесс этот трудоемкий и вредный ввиду образования пыли от металлического пигмента.
Таким образом, от состава напрямую зависят печатные свойства металлизированных красок. В следующей главе будут подробно рассмотрены особенности печати данными красками.
2. Особенности печати металлизированными красками
Ведущие производства металлизированных пигментов постоянно работают над внедрением новых технологий, что приводит к появлению металликов с улучшенными показателями по химической, температурной и механической устойчивости. Применяются технологии покрытия частиц оксидами или атомарными металлами (технология PVD – PhysicalVapourDeposition), что значительно повышает зеркальность поверхности, повышая показатели блеска, иногда придает дополнительный цвет. Например эффект двух тонов – так называемый frost-effect, при котором краска металлик меняет цвет от синего до зеленого в зависимости от угла зрения.
В настоящее время все металлизированные краски подходят для печати растрированных изображений. Следует помнить, что при более грубом растре (меньшей линатуре изображения) краскоперенос будет выше, что позволит усилить металлический эффект. Для улучшения условий закрепления металлизированной краски и повышения ее блеска при многокрасочной печати "по сырому" желательно, чтобы она наносилась непосредственно на бумагу, а не на нанесенную в предыдущих секциях краску (если эта краска не является специальным грунтом). Это следует учесть на допечатной стадии при подготовке макета продукции.
Для инструментального контроля качества печати металлизированными красками рекомендуется применять спектрофотометры со сферической геометрией или с помощью денситометров с геометрией 450
. Измерения выполняются через поляризационный фильтр и соответствующий зональный светофильтр. При денситометрическом контроле оттисков золотой краской следует использовать зональный светофильтр для желтой краски, а при измерении оптической плотности серебряной краски — светофильтр для черной краски.
В процессе печати металлизированными красками, изготавливаемыми по специальной рецептуре, на быстроходных печатных машинах происходит ориентирование пигмента параллельно движению машины, видимость краев пигментов существенно снижается, происходит рассеивание света от пигмента при одновременном отражении от его поверхности. При этом ориентирование частиц и эффект отражения в значительной степени определяются качеством запечатываемого материала. Но в целом достижимый с этими пигментами блеск изображения на оттиске сравним с блеском металлизированных бумаг или пленок и вполне их заменяют.
При печати тиражей больше 5 тыс. оттисков рекомендуется применять прошедшие термообработку офсетные монометаллические пластины, так как абразивные металлические частицы пигмента ускоряют изнашивание печатной формы и снижают ее тиражеустойчивость. В процессе очистки печатных форм необходимо следить, чтобы средство, содержащее кислоту, не попадало в увлажняющий раствор, и тщательно промывать пластины водой.
При выборе металлизированной краски необходимо учитывать следующие факторы:
· тип запечатываемого материала;
· скорость печати;
· тип послепечатной обработки оттисков.
Идеальным запечатываемым материалом при использовании металлизированных красок является гладкая мелованная бумага с низкой абсорбцией масел. Гладкая поверхность бумаги и слабое впитывание связующего увеличивают глянец оттиска, усиливают эффект металлического блеска и обеспечивают хорошую стойкость оттиска к истиранию. При работе с бумагами без покрытия достичь высоких результатов можно за счет нанесения грунтового слоя — лака или краски. Для грунтовки следует использовать ахроматические краски (белую или черную) или краски, цвет которых близок к цвету металлических пигментов (желтая и оранжевая краски — под золото; синяя — под серебро).
Тиражную печать на невпитывающих материалах (пластиках, металлизированных и синтетических бумагах, металлизированном картоне) рекомендуется выполнять только после проведения предварительных тестов на адгезию краски к материалу.
Для печати на высоких скоростях (более 10 тыс. отт./ч) предпочтительно использовать краски с особо мелкими пигментами. При лакировании или ламинировании оттисков следует выбирать металлизированные краски, совместимые с лаками и клеями для ламинирования.
Металлизированные краски, как правило, имеют хорошую стойкость к спиртам и низкую стойкость к щелочам. Светостойкость золотых красок составляет около 3-4 единиц, серебряных — до 7 единиц по шкале Blue Wool (ISO 2835-1974).
При печати металлизированные краски на масляной основе не требуют применения специальных офсетных полотен и специальных покрытий валиков красочного аппарата. Для изготовления печатных форм рекомендуется использовать высококачественные пластины; при печати больших тиражей формы следует подвергать термообработке (обжигу).
Кислотность увлажняющего раствора должна быть равной примерно 5,5 единицам pH при минимальном уровне электропроводности. Содержание спирта в увлажнении рекомендуется минимизировать, чтобы ограничить эмульгирование краски и предотвратить окисление металлических пигментов. Многие современные офсетные металлизированные краски, в частности краски на растительных маслах, позволяют качественно печатать вообще без добавления спирта в увлажняющий раствор.
Настройку подачи краски и увлажнения в секциях, печатающих металлизированными красками, рекомендуется начинать только после того, как будет установлен оптимальный водно-красочный баланс и достигнуты нормированные величины оптических плотностей на оттисках во всех других красочных секциях. При настройке секций печати металлизированными красками следует установить минимально необходимую (только чтобы не было тенения) подачу увлажнения, после чего постепенно увеличивать подачу краски, пока не будет достигнута требуемая величина оптической плотности плашки на отпечатке. В процессе печати следует поддерживать минимальную подачу увлажнения и контролировать величину оптической плотности.
Минимизация подачи увлажнения способствует более быстрому высыханию оттисков и получению наилучшего эффекта металлического блеска. При повышенном эмульгировании краски оттиски будут медленно сохнуть, и выглядеть тусклыми, а в худшем случае возможно появление дефекта меления (осыпания краски).
В машинах для двусторонней печати с устройством переворота листа металлизированные краски целесообразно наносить только после того, как лист прошел устройство переворота.
При печати на невпитывающих материалах обязательной является сушка оттисков ИК-излучением, а также нанесение противоотмарочного порошка или лакирование. Для минимизации риска отмарывания и растискивания также следует контролировать количество наносимой краски и высоту стопы в приемном устройстве (не более 500 листов). /2/
При необходимости свойства красок могут корректироваться путем введения специальных добавок:
· регуляторов вязкости;
· регуляторов липкости;
· добавок для повышения прочности красочного слоя к истиранию;
· добавок для снижения способности красок к эмульгированию.
Для коррекции вязкости в краску добавляют прозрачное связующее. Следует учитывать, что слишком высокая вязкость краски может привести к ухудшению краскопереноса. Кроме того, введение связующего снижает концентрацию пигмента, уменьшая красящую силу и укрывистость краски. Слишком низкая вязкость ведет к повышенной склонности краски к эмульгированию с увлажняющим раствором. Необходимость в снижении липкости краски возникает при печати на бумагах и картонах с низкой прочностью поверхностного слоя. Чтобы избежать выщипывания волокон, в краску добавляют специальный гель или рафинированное соевое масло.
Для повышения прочности красочного слоя к истиранию в состав краски могут вводиться синтетические (например, полиэтиленовые) воски. В исходном составе красок содержание таких добавок минимизировано с целью достижения максимальной гладкости поверхности и наилучшего глянца. Добавление восков целесообразно при печати на материалах с неровной абразивной поверхностью, например на матовых бумагах. Стойкость оттисков к истиранию может быть также улучшена путем добавки в краску веществ, повышающих твердость красочного слоя, например тунгового масла.
Эффективными способами повышения глянца этикеток и упаковок, а также защиты печатного изображения от механических повреждений, выцветания и воздействия химических веществ являются лакирование и ламинирование прозрачными пленками, однако при нарушении технологии лакирования или при неправильном его подборе металлический блеск краски уменьшается.
Технологичность металлизированной краски с точки зрения последующей отделки оттиска зависит от степени адгезии лака или клея для ламинирования к сырой (при отделке в линию) или подсохшей/сухой (при отделке отдельным прогоном) красочной пленке. Необходимым условием прочной приклейки пленки также является прочное соединение слоя металлических пигментов с запечатываемым материалом, поэтому для ламинирования лучше всего подходят оттиски на мелованных слабовпитывающих бумагах.
Большинство масляных металлизированных красок могут лакироваться в линию масляными и водными лаками и масляными лаками. Однако надо иметь в виду, что металлические краски "не любят", когда поверх них наносят дополнительные покрытия, особенно УФ-лаки. При необходимости нанесения УФ-лаков и для ламинирования рекомендуется использовать краски, специально разработанные для последующей отделки. В любом случае перед печатью тиража следует выполнить тестирование совместимости краски и лака или клея. В сложных случаях может понадобиться нанесение праймера.
При разработке дизайна печатной продукции, подлежащей ламинированию, следует минимизировать количество металлизированных элементов, расположенных на линии обреза (высечки), поскольку такие элементы увеличивают риск отслаивания пленки.
При лакировании масляным лаком время между прогонами рекомендуется минимизировать.
Металлизированные краски на водной основе для нанесения в анилоксовых лакировальных секциях создаются на базе водных красок для флексографской печати. Основным достоинством нанесения металлизированных красок в лакировальных секциях является возможность формирования более толстых слоев краски, чем в офсетных секциях.
Для изготовления печатных форм рекомендуется использовать фотополимерные пластины с металлической основой в сочетании с компрессионными декельными материалами. Предпочтительно применение закрытого (камер-ракельного) красочного аппарата с перистальтическим насосом для подачи краски в красочный ящик. Анилоксовый вал должен иметь линиатуру 100-220 лин/см. Применение более краскоемких анилоксовых валов, как правило, приводит к проблемам с отмарыванием.
Очистка красочного аппарата и офсетного полотна может выполняться с применением обычных чистящих средств для масляных офсетных красок. Очистка лакировальной секции выполняется с помощью стандартных средств, предназначенных для водных лаков. При наружном применении краски с металлизированными пигментами, следует дополнительно проводить покраску защитным прозрачным лаком, чтобы избежать нежелательных побочных реакций частиц алюминия с кислыми или щелочными солями, что приводит к возникновению на покрытии пятен серого цвета и исчезновению металлического цвета. Дополнительно качественный глянцевый полиуретановый лак усиливает оптический эффект цвета металлик, из-за дополнительного преломления света на поверхности лака. При всех способах печати при работе с металлическими красками надо принимать во внимание температуру и влажность воздуха в печатном цехе.
Обычно в летние месяцы гораздо больше неприятностей, чем зимой: из-за повышенной температуры растворители улетучиваются быстрее (см. таблица 3), и краска покрывается пленкой.
Таблица 3 - Летучесть некоторых растворителей для флексографской и глубокой печати
Растворитель |
Точка кипения |
Число испарения |
Этанол |
78 |
8,3 |
Метилэтилкетон |
80 |
2,6 |
Изопропанол |
82 |
1,0 |
Изопропилацетат |
88 |
4,0 |
Этоксипропанол |
134 |
33,0 |
Этилацетат |
77 |
2,9 |
Вода |
100 |
ок.90,0 |
Чтобы свести испарение до минимума, требуется поддерживать в цехе постоянную температуру и плотно закрывать емкости с краской. Если краски мало и ее не перемешивать, пленка обязательно появится.
Говоря о поведении металлизированных красок при печати, нужно иметь в виду, что на разных печатных машинах будут получены разные результаты. Для большинства машин вязкость металлизированных красок должна строго выдерживаться.
Таким образом, внимательно контролируя подачу краски на печатную секцию, можно уменьшить число дефектов печати по вине краски благодаря сокращению разбрызгивания и в некоторой степени тенения. На меньших машинах реже возникают проблемы с тенением, но в процессе высыхания чаще происходит расщепление краски.
В следующей главе будет рассмотрены возможные дефекты печати, возникающие по вине краски, и способы их устранения.
3. Проблемы, возникающие при работе с металлизированными красками
Сегодня без металлизированных красок невозможно представить себе процесс изготовления значительной доли этикеточно-упаковочной продукции. Различные оттенки "золота", а также серебряный цвет востребованы таким количеством производителей товаров, что простое перечисление займет слишком много времени. Однако при печати металлизированными красками офсетным способом (рис. 1) необходимо знать и учитывать целый ряд особенностей, связанных собственно со свойствами красок, с взаимодействием краски с увлажняющим раствором и бумагой, с влиянием окружающей среды (температура и влажность в помещении) и с некоторыми другими факторами.
Как указывалось ранее, в настоящее время металлизированные краски производятся, в основном, в однокомпонентном варианте, т.е., готовые к использованию. Теперь нет необходимости в предварительном смешивании пигментной составляющей со связующим компонентом, что в недалеком прошлом являлось "суровой необходимостью"— ингредиенты производились и поставлялись отдельно. Вместе с циклом составления красок непосредственно в типографии, что требовало наличия специального оборудования, трудозатрат, квалификации персонала, исключены и неизбежные погрешности в результате — в конечной формуле краски.
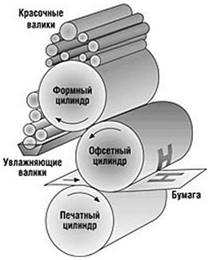
Рисунок 1. Схема офсетной печати
Одной из основных проблем при работе с металлизированными красками является потеря пигментом блеска, предотвратить которую помогут следующие шаги:
· Тщательный контроль подачи увлажняющего раствора. Подача увлажнения должна быть минимальной, иначе краски потеряют блеск из-за окисления металлических пигментов в воде. Для того чтобы свести к минимуму подачу воды, уменьшить эмульгирование краски и ускорить ее закрепление на оттиске, в увлажняющий раствор рекомендуется вводить изопропиловый спирт. Однако его концентрация не должна превышать 10%, так как большее количество спирта может привести к тенению (то есть к передаче краски пробельными элементами формы), к растворению защитной оболочки вокруг металлического пигмента и в результате вызвать потускнение краски.
· Отказаться от кислых добавок в увлажняющий раствор и использовать специально предназначенные для металлизированных красок добавки.
· Использовать качественные высокоглянцевые мелованные бумаги c низким показателем адсорбции жира. Ровная гладкая поверхность увеличивает металлический эффект и отражение, низкая жироадсорбция обеспечит хороший глянец и гладкость поверхности оттиска.
· При работе с немелованными бумагами возникает опасность впитывания в нее большей части связующего, в результате чего оттиски будут иметь очень низкую прочность на истирание (возможно осыпание металлического порошка). Поэтому бумагу с высокой впитывающей способностью рекомендуется предварительно запечатывать олифой или лаком.
· Показатель кислотности рН бумаги должен быть не ниже 7. Определить уровень кислотности бумаги поможет карманный рН-метр, работающий по принципу обесцвечивания бумаги, которое сигнализирует о степени кислотно-щелочной реакции. В ходе теста необходимо провести ручкой по бумаге и сравнить цвет оставшегося следа со шкалой, нанесенной на ручке.
· Количество краски, помещаемой в красочный ящик, следует минимизировать. Влага и кислород негативно воздействуют на краску – они вызывают коррозию и окисление пигмента. Поэтому при длительном пребывании в красочном ящике из-за изменений, происходящих с пигментом, краски теряют блеск. Следует помнить, что "металлики" относятся к категории непрозрачных красок, поэтому оптимально начинать подачу краски с небольшого количества, затем можно постепенно увеличивать объем подаваемой краски до уровня, позволяющего покрыть площадь запечатки. Затем подача понемногу увеличивается до уровня достижения желаемого блеска, и параллельно регулируется подача увлажнения во избежание явления тенения на пробельных элементах формы. Установленный таким путем водно-красочный баланс необходимо контролировать в течение всего тиража.
· Усиления металлического эффекта позволит добиться предварительное запечатывание поверхности полутоном желтого цвета – для золота и голубого – для серебра.
· Не рекомендуется использовать добавки, ускоряющие высыхание, — они провоцируют окисление и снижают глянец оттисков. Ускорить закрепление красок и сохранить металлический блеск поможет применение ИК- сушки.
· Для получения максимального металлического эффекта не рекомендуется применение лакирования (любое лаковое покрытие вызовет снижение металлического блеска). Этот оптический феномен возникает при покрытии металлизированной краски любыми лаками; светорассеяние увеличивается, а отражательная способность и металлический эффект снижаются.
Основными причинами возникновения дефектов при печати являются:
· эмульгирование краски с увлажняющим раствором,
· абразивность пигмента,
· повышенная кислотность увлажняющего раствора,
· избыток увлажняющего раствора,
· впитывающая способность запечатываемого материала,
· вязкость и липкость краски,
· дефекты печатной формы.
Так как металлизированные краски в своем составе имеют мельчайшие частицы металла, при печати этими красками офсетным способом могут возникнуть некоторые проблемы. Далее будут рассмотрены возможные дефекты и способы их устранения.
Эффект "апельсиновой корки" на плашках или пятнистость плашек, отпечатанных металлизированными красками, часто является следствием слишком сильного эмульгирования краски с увлажняющим раствором. Для его устранения следует уменьшить подачу увлажняющего раствора до минимально необходимой величины. Также рекомендуется проверить величину подачи краски, которая не должна быть слишком высокой, и проконтролировать качество печатной формы. Возможной причиной пятнистости плашек может быть неравномерная впитывающая способность бумаги и быстрый износ печатной формы.
Металлизированные пигменты абразивны, а потому пониженная тиражестойкость печатных форм — нормальное явление. Тем не менее если износ формы происходит слишком быстро, то следует проверить давление между формой и накатными валиками, а также между формным цилиндром и офсетной покрышкой. Снижение тиражестойкости качественно изготовленной формы также может быть обусловлено слишком высокой кислотностью увлажняющего раствора.
Выщипывание - отрыв в процессе печатания волокон или частиц от поверхностного слоя бумаги (рис. 2).
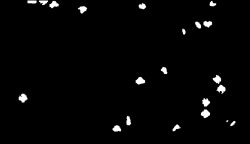
Рисунок 2 - Микрофотография черной плашки со следами выщипывания
Легкая форма этой неприятности - выщипывание отдельных волокон бумаги, которые постепенно накапливаются на красочных валиках, а также появляются в виде белесого осадка в лотке увлажняющего аппарата. В конечном счете, это приводит к потере вязкости краски и нарушению режима увлажнения. Сильнее всего это проявляется на плохих, рыхлых бумагах. Единственный выход - приостановить печать, смыть краску и закатать свежую. При смывке зачастую краска уходит, а волокна остаются на валиках в виде пуха. Иногда его после высыхания можно просто сдуть, но чаще требуется протереть валики вручную. Ипользовать для этого лучше не смывку, а спирт или увлажнение. Увлажнение в лотке лучше менять почаще.
В тяжелой форме выщипывание проявляется в выдирании больших клоков бумаги, которые остаются на офсетном полотне и попадают в красочный аппарат. Машину надо обязательно остановить и удалить большие куски вручную; затем смыть и очистить резину и, при необходимости, красочный аппарат. Если бумагу "размолотило" в валиках, стоит после смывки снять все снимающиеся валики и очистить их вручную, иначе остатки ворса еще долго будут портить плашки. Лучше всего валики очищаются от волокон под струей теплой воды - достаточно просто протереть их ладонью.
Выдирание бумаги обычно бывает при следующих условиях: тонкая или непрочная бумага, вязкая или быстросохнущая краска, плашки на изображении. Можно преодолеть это затруднение, добавив в краску какую-либо присадку, уменьшающую ее липкость. Полезно также уменьшить до давление минимального, обеспечивающего приемлемое качество печати.
Когда краска накапливается на валиках красочного аппарата, форме или офсетном полотне, но плохо переносится на запечатываемый материал, рекомендуется в первую очередь проверить баланс подачи краски и увлажнения. Если выявлено сильное эмульгирование краски - дефект, состоящий в образовании эмульсии печатной краски с водой вследствие попадания в краску увлажняющего раствора, что приводит к возникновению полос и разводов на оттиске, снижает его интенсивность и вызывает несовмещение красок и пр., следует очистить красочный аппарат и заново настроить водно-красочный баланс при минимально необходимой подаче увлажнения. Если краска имеет повышенную склонность к эмульгированию, в нее надо ввести соответствующую корректирующую добавку. Другими причинами дефекта могут быть слишком высокая вязкость краски и загрязнение офсетного полотна в результате растворения покрытия бумаги. В последнем случае следует сократить подачу увлажняющего раствора до минимально необходимой величины и уменьшить скорость печати.
Марашки - дефект печати, при котором посторонние частицы, попадая на печатную форму или на офсетную резинотканевую пластину, создают на оттиске лишние визуально заметные элементы, снижающие качество оттиска (рис. 3).

Рисунок 3 - Марашка на оттиске
Основными источниками марашек являются частицы засохшей краски из-за плохой смывки красочного аппарата, частицы бумаги от некачественно подрезанных листов или частицы поверхностного слоя бумаги, если последний имеет низкую прочность.
В дополнение к обычным источникам марашек существует множество необычных, и для того, чтобы разобраться в них иногда требуется тщательный и длительный поиск. Ключом к разгадке причин этого дефекта может явиться сам вид марашки. Марашки с плотными , темными центрами вызываются воспринимающей краску грязью. Полые марашки (без видимого центра) порождаются воспринимающей воду грязью, а марашки с хлопьевидным центром – тем и другим видом грязи.
Избежать появления данного дефекта поможет содержание в чистоте пресса и территории вокруг него, а также понижение липкости краски.
Медленное высыхание краски на оттисках может быть обусловлено слишком толстым красочным слоем, если в процессе печатания были значительно изменены свойства краски, а так же если бумага имеет очень низкую кислотность.
Меление - дефект, выражающийся в отделении или стирании под действием легкого трения слоя печатной краски после высыхания оттиска вследствие ряда причин: высокой впитывающей способности бумаги, излишне жидкой и быстровпитывающейся краски, повышенной кислотности увлажняющего раствора, его чрезмерной подачи.
Решить проблему поможет применение грунтовки. Другие возможные причины меления: сильное эмульгирование краски с увлажняющим раствором, большая толщина красочного слоя, высокая влажность запечатываемого материала (неакклиматизированный материал).
Низкий глянец красочного слоя. Глянец - оптическое свойство гладкой поверхности оттиска, направленно отражать свет, падающий на нее. Зависит от качества (оптических параметров) запечатываемой поверхности, способа печати, свойств печатных красок, фактуры печатной бумаги. Уровень глянца обусловлен в основном степенью ровности красочного слоя на оттиске. Возможными причинами низкого глянца являются микронеровности поверхности запечатываемого материала, высокая впитывающая способность запечатываемого материала, а также избыточный или недостаточный перенос краски. Также негативно влияет на степень глянца сильное эмульгирование краски с увлажняющим раствором.
Оголение раскатных валиков красочного аппарата свидетельствует о дестабилизации подачи краски. Причинами этого явления может быть загрязнение (плохая очистка) поверхности раскатных валиков, слишком высокая кислотность увлажняющего раствора или недостаточная величина подачи краски дукторным цилиндром.
Перетискивание (то же, что и отмарывание) - процесс переноса печатной краски с одного листа на другой в незапланированных местах под весом стопы. Этот дефект является следствием плохого закрепления краски или при некачественной краске, слишком большого веса (высоты) стопы на приемке или недостаточной подачи противоотмарочного порошка. К тому же чем выше уровень статического заряда на поверхности листов, тем больше вероятность перетискивания. /3/
Адгезия - слипание поверхностей твердых тел и жидких веществ при их контакте. В полиграфии большое значение имеет адгезия печатной краски к печатной форме и к бумаге, к свежему слою краски на многокрасочном оттиске при многокрасочной печати и пр. Адгезию краски к субстракту часто определяют с помощью простых качественных тестов,таких как испытание на сморщивание, скребок ногтем, отрыв скотч-ленты и сгибание металлической пластинки.
Для достижения хорошей адгезии краски к нанесенным в предшествующих секциях сырым красочным слоям и предотвращения обратного краскопереноса нужно следить за тем, чтобы вязкость наносимой краски не превышала вязкости ранее нанесенных красок.
Причинами плохой адгезии лака к краске — осыпания лака после высыхания — может быть меление краски или хрупкость лаковой пленки. Во втором случае решением проблемы может быть использование лака, создающего на оттиске гибкую эластичную пленку.
Повышенное растискивание - эффект расплывания точки при нанесении ее на бумагу в печатной машине, связано с характером взаимодействия "краска-бумага", а также с силой прижатия печатного цилиндра к бумаге. В результате необходимо учитывать, что точки при печати больше, чем они выглядели на цветоделенной пленке или пластине. В современных системах печати учет растаскивания может производиться в программах растрирования.
При появлении дефекта следует проверить величину давления между формным и офсетным цилиндрами и между формным цилиндром и накатными валиками, т.к. при переходе краски с формы на резину и с нее на бумагу площадь растровой точки увеличивается (рис 4), а также проконтролировать величину подачи краски (она не должна быть слишком высокой), вязкость краски и баланс краски и увлажнения. Еще одной причиной повышенного растискивания может быть ошибка при допечатной подготовке макета. Дефект, заключающийся в увеличении размеров печатных штриховых и растровых элементов на оттиске в процессе печатания, что приводит к градационным и цветовым искажениям репродукции.
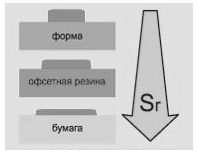
Рисунок 4 - Увеличение площади растровой точки
От чего же зависит растискивание?
1. Печатная основа. Растискивание почти напрямую зависит от диффузионных и оптических свойств основы. В большинстве случаев печатная основа - это бумага. Именно она является причиной оптического растискивания - увеличения оптической плотности растровых полей в результате рассеивания света в материале основы.
2. Краска, ее физико-механические и оптические свойства.
3. Давление между механическими парами в процессе печати (дробление).
4. Правильность передачи листов в процессе печати на многокрасочных листовых печатных машинах (двоение).
5. Различие линейных скоростей офсетных цилиндров для рулонных машин и разница диаметров офсетных цилиндров по сравнению с диаметрами печатных цилиндров для листовых машин (проскальзывание, дробление).
6. Размер и форма печатного элемента, а точнее - его периметр. Круглая точка имеет наименьшее растискивание при прочих равных условиях (рис. 5). Чем больше периметр печатного элемента, тем больше величина растискивания Z.
Поскольку величина растискивания зависит от периметра точки, то чем сложнее форма точки, тем больше ее растискивание. Минимальное растискивание - у круглой растровой точки.
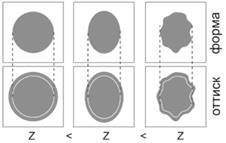
Рисунок 5. Изменение значения растискивания при изменении формы растровой точки
В производственных условиях измеряют растискивание в двух опорных точках: 40% или 50% и 75% или 80%. Растискивание 50% растрового элемента нормируется не только в типографии, есть госстандарт ОСТ 29.66-90 (еще с советских времен) и современный европейский ISO 12647–2. В стандартах даны рекомендованные зональные значения растискивания и величины отклонения от рекомендованного значения 50% растровых точек для различных типов бумаг и печатных машин.
В европейском стандарте кроме рекомендованных величин растискивания введено понятие "разброса полутона", или "растискивание в полутонах". Это разница между максимальной и минимальной величинами отклонения растискивания красок от рекомендованного. /4/
Пыление краски - дефект, состоящий в образовании красочного тумана при раскате печатной краски и появляться при избыточной подаче краски. При сухом воздухе и высокой температуре краски этот эффект возрастает. Обычно дефект наблюдается при печатании на рулонных машинах.
Краска, нанесенная на одну сторону оттиска, может обусловливать неравномерное высыхание второй стороны и, как следствие, неравномерность глянца. В этом случае нужно либо увеличить время или интенсивность сушки первой стороны, либо покрывать вторую сторону водным лаком.
Смазывание (скольжение) является следствием неверного подбора толщины формной пластины и/или декеля, слабого натяжения офсетного полотна или слишком высокого давления между формным и офсетным цилиндрами.
Стекление - дефект, заключающийся в образовании прочной, ровной, блестящей пленки на поверхности высохшей печатной краски на оттиске. При многокрасочной печати стекленение красок является серьезной помехой, так как последующие краски не ложатся на предыдущие при печати "по сухому". Можно избежать этого дефекта, если добавить в предыдущую краску небольшое количество воска (предварительно растворенного в скипидаре) или вазелина. Не рекомендуется вводить в краски, которые наносятся первыми, ускорители высыхания. Следует печатать красками с возможно минимальной толщиной и интервалы между листопрогонами не должны превышать 24 часов, чтобы краска не успела высохнуть до образования твердой пленки.
Тенение - дефект, состоящий в переходе мельчайших частиц печатной краски на пробельные элементы печатной формы, а затем – на оттиск, связанный с печатной формой и с рН (кислотностью) увлажняющего раствора. Для устранения тенения проводят дополнительную гидрофилизацию пробельных элементов печатной формы. /3/
Полошение - дефект оттиска, заключающийся в образовании заметных полос в направлении движения бумаги в печатной машине. Полошение может возникнуть из-за деформации ракеля, попадания твердых частиц на форму (в глубокой печати), из-за плохой регулировки печатного и красочного аппаратов, а также из-за износа или повреждения красочных валиков, цилиндров или зубчатых передач печатной машины. Наиболее заметны полосы на "тяжелых" плашках и сетках. Причем даже не при стопроцентной плашке, а при 75–80% растра. В этом случае малейшие колебания давления на красочных валиках или цилиндрах машины вызывают изменение растискивания, и пробельные элементы между растровыми точками то "раскрываются", то исчезают вовсе, и мы видим, что цвет неоднороден.
Чтобы избежать эффекта полошения можно подготовить макет таким образом, чтобы полосы были предусмотрены в самом сюжете изображения, и чтобы они совпадали с теми, которые возникают на оттиске из-за несовершенства технологии.
Некоторые цвета на офсетной печатной машине очень трудно напечатать без полошения. А некоторые - легко. Объясняется это особенностями человеческого зрения. На самом деле, полосы есть всегда. Но, к примеру, на оранжевой или, тем более, желтой поверхности они заметны гораздо меньше, чем на темно-зеленой или темно-синей. /5/
Эмульгирование краски - дефект, состоящий в образовании эмульсии печатной краски с водой вследствие попадания в краску увлажняющего раствора; приводит к возникновению полос и разводов на оттиске, снижает его интенсивность, вызывает несовмещение красок и пр.
Эмульгирование зависит от множества факторов. Три основных: бумага, увлажняющий раствор, краска. Химический состав краски определяет, насколько она подходит к конкретному увлажняющему раствору и какова стабильность эмульсии. Как бы там ни было, условия (температура, управление технологическим процессом, регенерация увлажняющего раствора) могут выйти из-под контроля, и увлажняющий раствор перестанет восприниматься формой, что потребует дополнительной подачи воды и приведёт к изменению баланса.
Как же решить проблему эмульгирования? Универсальных рекомендаций по балансу краска/вода нет. Считается, что краскоперенос приближается к оптимальному при минимальном уровне увлажняющего раствора и краски, дающем удовлетворительную плотность оттиска и поддерживающем корректный тоновый баланс. Впрочем, это не означает, что при колебаниях уровня эмульгирования увлажняющего раствора не будет удовлетворительной печати (рис. 6).
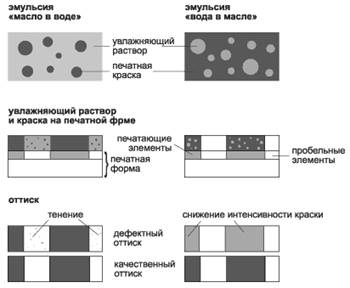
Рисунок 6. Взаимодействие увлажняющего раствора с краской и влияние эмульгирования на качество оттиска
Корректировать ситуацию допустимо и в процессе печати, добавляя воду или краску, но, хотя многочисленные попытки могут завершиться успехом, истинная проблема останется нерешённой.
Образование эмульсии офсетной краски с увлажняющим раствором обязательно, но необходимо контролировать уровень эмульгирования. У каждой краски есть рекомендованные параметры для оптимальной печати: эмульсия краска/вода не должна утратить рабочие характеристики собственно краски — липкость, вязкость, краскоперенос.
При нарушении баланса краска/вода сокращается способность краски к расщеплению, нарушается процесс переноса жидкости. Эмульсия становится нестабильной, краска скапливается и эмульгирует, красочная плёнка больше не переносится на валики и печатные формы. Единственное средство избавиться от перенасыщения краски водой — удалить краску из машины, смыть красочный аппарат, заложить свежую краску, начать восстановление баланса краска/вода заново, с минимальными начальными параметрами.
С большим количеством воды и краски можно добиться приемлемого результата на начальных этапах, но постепенно возникнут проблемы. Опытный печатник распознает перенасыщенную водой краску и в случае необходимости выровняет баланс.
Причин и следствий эмульгирования множество, но гораздо важнее понять, как избежать нарушения баланса краска/вода или выровнять нарушенный баланс. К сожалению, однозначного ответа на этот вопрос нет. Можно вносить корректировки, заменять увлажняющий раствор на имеющий меньшее химическое сродство с краской, в конце концов, поменять краску. Ниже приведены проблемы, вызываемые эмульгированием.
Нарушение баланса краска/вода с тенденцией к эмульгированию чревато следующими осложнениями:
· скопление краски на накатном валике увлажняющего аппарата;
· полошение на красочном валике;
· скапливание краски на валиках;
· чрезмерное растискивание;
· марашки на плашках;
· проблемы с треппингом в многокрасочной печати;
· потеря деталей в тенях изображений;
· отклонения цвета;
· пониженная оптическая плотность оттисков;
· сужение цветового охвата;
· медленное высыхание краски;
· осыпание пигмента с оттиска. /6/
Заключение
На основе использования закономерностей отражения и рассеивания в зависимости от структуры применяемых пигментов были созданы металлические пигменты на основе алюминия, которые обеспечивают получение в красочном слое на оттиске специфический блеск. В них оптимально скомбинированы блеск, кроющая способность и технические свойства использования. Эти пигменты изготавливаются на базе способа PVD, что переводится как "физическое термовакуумное напыление", которое обычно используется при металлизации пленок.
Благодаря этому трудоемкому способу достигается получение исключительно высокой гладкости поверхности при очень тонких частичках. Частички пигмента в 5-10 раз тоньше, чем у обычных пигментов.
Распространение красок на основе металлических пигментов привело к созданию различных их видов специального назначения. Например, известны краски с термохромными эффектами, которые будучи нанесенными на этикетки бутылок, сигнализируют о температуре напитка, одновременно обеспечивая отличный дизайнерский эффект. Здесь широкое поле деятельности оформителя, который может получить различные художественные эффекты сочетанием различных красок. Имеются и зональные термохромные краски, по цвету которых можно определить температуры не в одной, а в нескольких температурных зонах. Таким образом, металлизированные краски находят в полиграфии все более широкое распространение.
В данной работе были рассмотрены состав и основные свойства металлизированных красок, а также преимущества и недостатки их печатных характеристик.
Список использованных источников
1. Емельянова Т. "Металлические краски: бледно- богатое золото красок"/ Полиграфист и Издатель. – 2002. - № 7.
2. Марогулова Н., Рамонов Д. "Краски для офсетной печати. Состав, ассортимент, свойства"/ Мир Этикетки. – 2007. - № 4; 2003. - №1.
3. Нельсон Р. "Что полиграфист должен знать о красках". – М., 2005. – 328 с.
4. Шарифуллин М., Савастоно Д. "Расходные материалы для офсетной печати"/ Publish. – 1999. - № 7; 2008. - № 1.
5. Захаржевский Ю. "Еще раз о полошении на оттисках и как с ним бороться"/ Формат. – 2007. - №8.
6. Рамонов Д./ КомпьюАрт. – 2007. - № 11; 2006. - № 12.
7. Марогулова Н., Стефанов С., справочник "Расходные материалы для офсетной печати". – М., 2002. – 240 с.
8. Материалы с сайта http://www.newsprint.ru/
9. DIN 55944
10. ISO 2835-1974
11. ISO 12647-2
12. OCT 29.66-90
Приложение
1. Все упомянутые выше проблемы можно избежать, если использовать лакирующиеся краски с низким содержанием летучих органических соединений.
2. Такого рода проблемы обычно не возникают при применении лаков на масляной основе.
3. Предварительное запечатывание основной краской поможет улучшить адгезию.
Так как металлизированные краски изначально обладают низкой липкостью и вязкостью, что обеспечивает максимальный перенос металлических пигментных частиц и обладают отличными раскатно - накатными свойствами, прекрасно полимеризуются на всех типах подложек, включая слабо впитывающие и не впитывающие материалы, то при печати ими следует строго контролировать подачу краски и увлажнения.
|