РОСЖЕЛДОР
Государственное образовательное учреждение высшего профессионального образования
Дипломный проект
по специальности "Подъемно-транспортные, строительные, дорожные машины и оборудование"
Тема: Модернизация пневмоочистительной машины ПОМ-4
2008
Содержание
Введение
1. Аналитический обзор
2. Техническое предложение
3. Расчет мультипликатора
3.1 Исходные данные
3.2 Кинематический расчет мультипликатора
3.3 Расчет передачи
3.4 Расчет валов
3.5 Выбор посадок
3.6 Конструирование валов
3.7 Конструирование колес
3.8 Конструирование элементов корпуса
3.9 Уплотнения
3.10 Смазка
3.11 Порядок сборки мультипликатора
3.12 Проектирование муфты
4. Проектирование оборудования охлаждения
4.1 Выбор оборудования охлаждения
4.2 Проектирование рамы вентиляторов охлаждения
5. Расчет экономической эффективности модернизации ПОМ-4
Заключение
Список использованных источников
Приложение
Введение
На железной дороге в ее современном виде организация работ поставлена на высокий уровень, но есть сферы (такие как стихийные явления, аварийные ситуации и т.д.) спрогнозировать которые очень сложно, но предусмотреть возможности наибыстрейшего разрешения необходимо.
В нашей климатической зоне одной из актуальнейших проблем железной дороги всегда являлись снегопады, приводящие к задержке, а иногда и к полной остановке движения поездов. Целью этого проекта является улучшение положения как раз в этом направлении. Кроме того целью проекта является уменьшение финансовых затрат на уборку снега.
1. Аналитический обзор
В практике зимней очистки железных и автомобильных дорог нашли широкое применение технические средства, основанные на механическом взаимодействии рабочих органов со снегом и льдом. Это машины с рабочими органами плужного (ножевого), роторного и щеточного типов.
В лабораториях различных стран исследуются такие нетрадиционные методы, как использование водяных струй (непрерывных и ударных), ультразвука, транспортно-очистительных средств на воздушной подушке, источников света высокой интенсивности и др. [1…4].
В настоящее время на уровень практического и достаточно широкого применения вышел метод выдувания снега с пути.
За последние двадцать лет создано большое количество различных машин данного класса, существенно облегчающих работу служб по уборке снега на станциях.
В 1986 году ВНИИЖТом на базе ПМГ был создан снегоочиститель МОС-1, представленный на рисунке 1.1. Эта машина с февраля 1986 года успешно эксплуатируется на Московско-Рижской дистанции пути Московской дороги.
Она представляет собой самоходный двухосный экипаж, на раме которого расположены силовая установка 5, состоящая из дизель-генератора АД-200 ТСП и кабины управления 6. На передней консоли рамы смонтированы рабочие органы, состоящие из двух вентиляторов высокого давления 3, подающих на путь холодный воздух по трубопроводам через воздухопроводящие сопла 1, и камера сгорания 4 с форсункой и системой подачи топлива и воздуха. Камера сгорания с расходом горючего 120-150 кг/ч, генерирует две мощные струи горячих газов. Этими струями снег и лед удаляется и труднодоступных мест стрелочных переводов. Горячие газы поступают по трубопроводам через газоподводящие сопла 2, размещенные позади воздухоподводящих. Для вписывания машины в транспортном положении в габарит подвижного состава каждый трубопровод выполнен из двух частей. Одна часть присоединена к вентилятору или к камере сгорания, а другая к соплам с возможностью поворота относительно оси. Для облегчения подъема патрубков с соплами на оси закреплены противовесы. Приводится машина в транспортное или рабочее положения электромеханическим приводом с цепной передачей.
При очистке пути в шпальных ящиках образуется талая вода. Для ее удаления под кабиной управления установлен третий вентилятор 7 с воздухоподводящими соплами 8. Мощность каждого вентилятора, установленного на машине – 45 кВт.
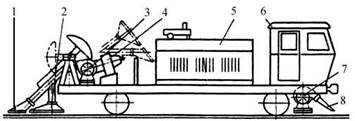
1, 8 – воздухоподводящие сопла; 2 – газоподводящее сопло; 3, 7 - вентиляторы; 4 – камера сгорания; 5 – силовая установка; 6 – кабина управления
Рисунок 1.1 – Машина для очистки стрелочных переводов от снега МОС-1
Приводится машина в движение двумя тяговыми двигателями ДК-116А постоянного тока, образующими два колесно-моторных блока. Рабочими органами управляют с пульта.
Машина работает следующим образом: при подходе к стрелочному переводу подвижные патрубки из транспортного положения приводятся в рабочее. Включаются вентиляторы и при необходимости – камера сгорания. Струи холодного воздуха сдувают со стрелочного перевода основную массу снега. В желобах может остаться увлажненный снег. Он удаляется струями горячих газов. Продолжительность очистки одного перевода 1-2 мин. Если высота снежного покрова 20 см над головкой рельса и более и плотность снега доходит до 0,2 г/см3
, продолжительность очистки удваивается. Скорость движения машины в зависимости от толщины и плотности снега составляет от 0,5 до 2 м/мин. Особенно эффективна машина во время снегопадов и метелей [5].
Опытные дорожные ремонтно-механические мастерские службы пути Южно-Уральской дороги изготовили опытный образец снегоочистителя "Ветерок" ВС-1 [6]. Испытания показали высокую эффективность его в работе. Снегоочиститель представлен на рисунке 1.2.
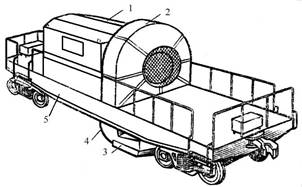
1 – привод вентилятора; 2 – вентилятор; 3 – плужный отражатель; 4 – сопло-диффузор; 5 – четырехосная платформа
Рисунок 1.2 – Вентиляторный снегоочиститель "Ветерок"
На четырехосной платформе 5 устанавливается вентилятор 2 (ВДН-17-1000 или ВДН-18-1000). К улитке вентилятора, выход которой направлен вертикально вниз, постоянно закреплен сопло-диффузор 4. Его выходное отверстие направлено под углом 45° к пути и развернуто в плане относительно продольной оси колеи на 25°. Сопло-диффузор соединен общим кожухом с отражателем плужным 3, рабочая плоскость которого установлена под углом 65° относительно продольной оси пути, что позволяет выбрасывать снег на обочину при помощи воздуха подаваемого с рабочего органа на высокой скорости и под высоким давлением. Привод вентилятора 1 смонтирован под капотом через упругую втулочно-пальцевую муфту от электродвигателя П 112 (180 кВт, 440 В, 1500 об/мин, с независимым возбуждением отрегулированным на 220-340 В) [3].
На Апатитской дистанции Октябрьской дороги в 1988 г. был изготовлен вентиляторный снегоочиститель "Тайфун-Д" [7], представленный на рисунке 1.3. В качестве привода вентилятора 1 (ДН-17Н) был принят автономный дизель 3 (1Д-12), всё это было установлено в четырехосном крытом вагоне. Привод от дизеля был осуществлен с помощью муфты сцепления от дрезины ДГКу
, карданный вал 2 был укорочен. Для очистки плотного и обледенелого снега на перегонах и станционных путях в голове "Тайфуна-Д" был установлен рыхлитель 5. Управление вентилятором осуществлялось из кабины 4. При небольшой собственной массе 28 т снегоочиститель передвигался любым локомотивом или дрезиной ДГКу
. "Тайфун-Д" с направленным соплом 6 применялся для очистки переводов от рыхлого снега, съездов и вставок между стрелочными переводами, закрестовинных кривых.
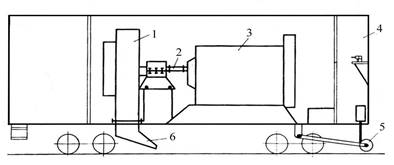
1 – вентилятор; 2 – укороченный карданный вал; 3 – дизель; 4 – кабина управления; 5 – рыхлитель; 6 – сопло.
Рисунок 1.3 – Снегоочиститель "Тайфун-Д"
Дзержинской дистанцией пути Горьковской дороги в 1988 г. был изготовлен вентиляторный снегоочиститель для очистки стрелочных переводов и станционных путей от снега, а летом – от засорителей [8]. Он смонтирован на двухосной платформе УП-2 (рисунок 1.4) и оснащен двумя вентиляторами 1 (ВДН-11.1) с электродвигателями 2 (4АМ200), питаемыми током от дизель-генератора 6 (АД-200-Тсп). Также на платформе размещены: пульт управления 4, электрический щит переключения питания 5 (от дизель-генератора, электровоза или ПМГ). Воздух поступает через сопла 3. Размещение оборудования на платформе представлено на рисунке 7. Передвигает машину дрезина ДГКу
, а обслуживает один механик. Рабочая скорость снегоочистителя 3-4 км/ч, время очистки одного стрелочного перевода 1-2 мин., производительность до 17 м3
/мин при толщине наста 0,3 м и ширине 2,7 м [5].
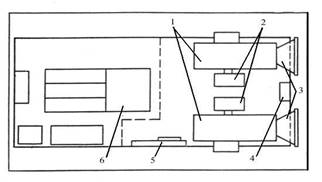
1 – вентиляторы; 2 – электродвигатели; 3 – сопла; 4 – пульт управления; 5 – электрический щит; 6 дизель-генератор
Рисунок 1.4 – Размещение оборудования на вентиляторном снегоочистителе
На Карагандинском металлургическом комбинате в 1989 г. был изготовлен вентиляторный снегоочиститель "Ветерок" на базе дрезины АГМу
[9], представленный на рисунке 1.5. На платформе смонтирована дизель-генераторная установка ДГ-200 (дизель УД12, генератор мощностью 200 кВт). Электростанция питает и вентиляторы, и привод машины. Снегоочиститель в транспортном положении развивает скорость до 40 км/ч – в этом случае включается электродвигатель мощностью 75-100 кВт, рабочая же скорость до 5 км/ч – для привода взят электродвигатель МТВ-211 мощностью 14 кВт. Муфта переключается пневмоцилиндром, заимствованным с машины ШПМ-02. Рабочий орган состоит из восьми вентиляторов СВМ-6М (шахтные вентиляторы). Вентиляторы спарены по два в четыре ряда. Рама, на которой смонтированы вентиляторы, и рама платформы связаны между собой шарнирно, поэтому при работе с помощью пневмоцилиндра можно менять угол атаки воздушного потока от 20° до 45°. При максимальном угле атаки очищают слежавшийся снег на стрелочных переводах. Если же снег рыхлый, то угол атаки уменьшают до 20-30°. Производительность машины до 305 м3
/мин [6].
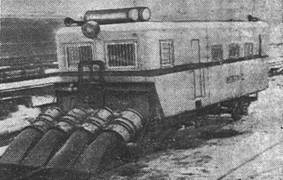
Рисунок 1.5 - Вентиляторный снегоочиститель "Ветерок" на базе АГМу
Путевой дорожной мастерской в Гулбене Прибалтийской дороги в 1990 г. была создана снегоочистительная машина СОМ-1 [10], изготовленная на базе платформы УП-2 и предназначена для очистки от снега путей, стрелочных переводов. Принципиальная схема СОМ-1 представлена на рисунке 1.6. Проведенные испытания дали неплохие результаты.
Машина состоит из дизель-генераторной установки, расположенной в капоте 2, куда возможен свободный доступ для обслуживания и ремонта, и вентиляционной установки с очень простым устройством для приведения в транспортное и рабочее положение. Направляющий кожух сопл 4 может поворачиваться в плане на угол, кратный 28°, что обеспечивает выброс снега в любую сторону. Производительность машины 3-5 км/ч. Радиальный вентилятор 3 (В-Ц6-28-6,31) совмещен с электродвигателем 5. Один вентилятор – правого, другой – левого вращения. Вентиляторы расположены таким образом, что выходной патрубок направлен под углом 110° к горизонтали. Снег сдувается при движении в одном направлении. Управление вентилятором осуществляется из кабины 1. Для работы с очистителем СОМ-1 можно использовать дрезину или любую другую самоходную единицу.
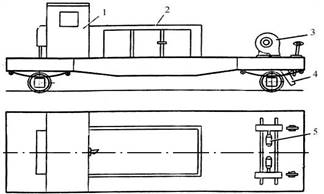
1 – кабина управления; 2 – капот; 3 – радиальный вентилятор;
4 – направляющий раструб; 5 – электродвигатель
Рисунок 1.6 – Принципиальная схема вентиляторного снегоочистителя СОМ-1
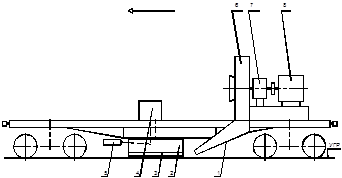
1 – направляющий аппарат; 2 – щит отбойный; 3 – фартук; 4 – ручная стопорная лебедка; 5 – пневмоцилиндр; 6 – вентилятор; 7 – подшипниковая опора рабочего колеса вентилятора; 8 – электродвигатель
Рисунок 1.7 – Схема путевой очистительная машины типа ПОМ с одновентиляторной пневмоустановкой (ППСМ-П)
На Зап.-Сиб. ж.д. с начала 80-х годов широкое применение получили машины типа ПОМ. На машинах первых выпусков устанавливался один вентилятор, направленность снеговоздушного потока не обеспечивалась. На последних моделях одновентиляторных машин для задания фиксированного направления потока предусматривался отбойный щит (рисунок 1.7).
Главным недостатком этих машин является то, что из-за недостаточной мощности воздушной струи, создаваемой одним вентилятором, не обеспечивалась достаточная производительность на уплотненном снеге. Для устранения этого недостатка машины ПОМ стали выпускаться с двумя вентиляторами и двумя направляющими аппаратами (рисунок 1.8).
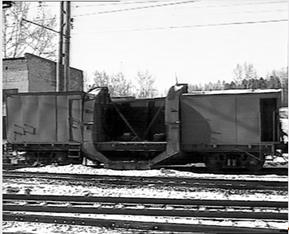
Рисунок 1.8 – Путевая очистительная машины типа ПОМ с двухвентиляторной пневмоустановкой
Машины оснащаются вентиляторами высокого давления (ВДН-17, ВДН-18, ВМ-18А и т.д.). В качестве привода вентиляторов на машинах используются двигатели постоянного тока (тяговые двигатели локомотивов) мощностью до 400 и более кВт, что значительно упрощает комплектацию машины и схему ее электропитания: от сети при тяге электровозом, от дополнительного тепловоза при тяге тепловозом. К выходному окну улитки вентилятора присоединен насадок – сопло, направляющий подаваемый вентилятором воздух в путь. Насадок установлен таким образом, что поток воздуха направляется под углом 30° к вертикальной плоскости и под таким же углом развернут к оси пути.
Снегоочистители типа ПОМ обладают наиболее мощными воздуходувными установками, но даже их пневмоустановки не справляются с уплотненным настом. Для повышения их эффективности в последние годы для привода каждого вентилятора устанавливают по два двигателя, но и это в полной мере не решает проблему.
Установка двух двигателей в одну линию значительно снижает надежность привода из-за невозможности обеспечить равенства их параметров.
Повышение мощности воздушного потока, формируемого пневмоустановками, нуждается в четком обосновании, возможном только на базе научных исследований. Это позволит исключить необоснованные затраты мощности и, соответственно, необоснованное усложнение и удорожание машин.
Существенным недостатком также является тот факт, что тяговые двигатели развивают скорость 930 об/мин, а номинальной скоростью вращения используемых вентиляторов является 1500 об/мин. Усилиями специалистов СГУПС был спроектирован мультипликатор с передаточным числом u=1,62 для машины ПОМ-4, позволяющий выводить вентилятор на номинальный режим.
2. Техническое предложение
В процессе эксплуатации машины ПОМ-4 последней модернизации выявлены следующие недостатки:
· перегрев двигателя рабочего органа - несмотря на требование производителя двигателей о принудительном охлаждении двигателя ТЛ-2К (а именно такие двигатели ставят на машины ПОМ-4 для привода рабочего органа), используется пассивное охлаждение. В процессе работы двигатель включают на 20-30 минут, затем в паузе производят пассивное охлаждение при выключенном двигателе. Тем не менее электродвигатели, выработавшие свой ресурс еще в электровозе, часто возгораются из-за межвиткового замыкания вследствие перегрева; рекомендация: перед установкой таких двигателей необходим капитальный ремонт - это значительно снизит риск выхода из строя двигателя рабочего органа;
· нагрев мультипликатора;
· частота вращения у различных двигателей ТЛ-2К под нагрузкой разная, в пределах 800…1200 об/мин, что при наличии мультипликатора с постоянным передаточным числом может существенно отличаться от расчетных 1480 об/мин у вентилятора.
Необходима дальнейшая модернизация данной машины. Целью данного проекта является проектирование системы охлаждения для двигателя и мультипликатора и приведение частоты вращения вентилятора в соответствие с действительной частотой вращения двигателя путем применения нескольких вариантов мультипликатора с разными передаточными числами.
3. Расчет мультипликатора
3.1 Исходные данные
Расчетная мощность P= 400 кВт.
Расчетные частоты вращения электродвигателя, n2
= 1230, 1050, 930, 820, об/мин.
Расчетная частота вращения вентилятора n1
= 1480 об/мин.
В качестве примера рассмотрен расчет при n2
= 930 об/мин
3.2 Кинематический расчет мультипликатора
Передаточное число
u= n1
/n2
=1480/930 = 1,59. (3.1)
Крутящие моменты на валах Т, Н×м:
T= 9550P/n, (3.2)
где Р – расчетная мощность, Р = 400 кВт; n – частота вращения вала, n2
= 930 об/мин.
Тихоходный вал [15]: Т2
= 9550×400/930 = 4108 Н×м.
Быстроходный вал:
T1
=9550Ph/n1
, (3.3)
где h- КПД зубчатой передачи, h= 0,96 [10].
T1
=9550×400×0.96/1480=2478 Н×м.
3.3 Расчет передачи
двигатель мультипликатор вал муфта вентилятор
Выбор материала
Для уменьшения габаритов мультипликатора по высоте приняты зубчатые колеса большой ширины, при этом использование высокотвердых материалов нецелесообразно так как по концам зубьев наблюдается высокая концентрация нагрузки. Основными критериями работоспособности и расчета зубчатых передач является контактная и изгибная прочность. Этим условиям отвечают углеродистые и легированные стали.
Принята для обоих колес сталь 45 улучшенная со следующими характеристиками [15]:
- твердость НВ=235-262;
- предел прочности σв
=780 МПа;
- предел текучести sт
=540 МПа.
Допускаемые напряжения.
Контактные напряжения
, (3.4)
где - предел длительной выносливости [15]; SH
- коэффициент безопасности, SH
=1,1 [15].
=2 +70=2×0,5(235+262)+70=567 МПа. (3.5)
=567/1,1=515 МПа.
Изгибные напряжения
. (3.6)
Предел длительной выносливости при нереверсивной работе [15]:
=1,8 =1,8×0,5(235+262)=447 МПа. (3.7)
При коэффициенте безопасности =1,75 [15] допускаемое напряжение изгиба:
=447/1,75=256 МПа.
Межосевое расстояние.
Межосевое расстояние из расчета на контактную выносливость [1]:
aw
=(u+1) , (3.8)
где - коэффициент распределения нагрузки; при 7 степени точности и скорости =15 м/с =1,09 [15];
- коэффициент ширины колеса; для шевронных колес =0,8 [1];
- коэффициент концентрации нагрузки; для симметричного расположения колес (схема 7) =1,23 [15];
- коэффициент динамической нагрузки; =1,08 [15].
По исходным данным межосевое расстояние aw
, другие геометрические параметры, силы в зацеплении, проверки по контактным и изгибным напряжениям рассчитаны в программе DМ-21 в системе BASIC. Распечатки компьютерных данных приведены в приложении А.
Геометрические параметры. Модуль зацепления
m=(0,01…0,2)aw
. (3.9)
Ширина колес
b= aw
.
(3.10)
Суммарное число зубьев при угле наклона колес с раздвоенной ступенью b=35°:
zS
=2 aw
cosb/m, (3.11)
Число зубьев шестерни
z1
=zS
/(u+1). (3.12)
Число зубьев колес
z2
= zS
-z1
, (3.13)
Уточненный угол наклона
b=arcos(mzS
/2aw
), (3.14)
Делительные диаметры
d=mz
/cosb. (3.15)
Диаметры вершин
da
=m(z/ cosb+2). (3.16)
Диаметры впадин
df
= m(z/ cosb-2,5). (3.17)
Окружная скорость колес.
u=pd1
n1
/60000. (3.18)
Рабочее контактное напряжение.
. (3.19)
Силы в зацеплении.
Окружная сила, действующая на полушеврон:
Ft
=T2
/d2
. (3.20)
Радиальная сила:
Fr
=Ft
tga/cosb, (3.21)
где a- угол профиля; a=20°[15].
Осевая сила:
Fa
=Ft
tgb. (3.22)
Проверка по изгибным напряжениям.
Эквивалентные числа зубьев
zn
=z/cos3
b. (3.23)
Коэффициент формы зуба Yf
из таблицы 4.13 [15].
Коэффициент наклона зубьев
Yb
=1-b/140. (3.24)
Рабочие изгибные напряжения:
=YF
Yb
Ft
KF
a
KF
b
KF
n
/mb. (3.25)
Таблица параметров.
Основные геометрические и силовые параметры всех четырех вариантов зацепления сведены в таблицу 3.1.
Таблица 3.1 - Основные геометрические и силовые параметры
Параметры |
МП-250-1,2 |
МП-250-1,4 |
МП-250-1,6 |
МП-250-1,8 |
Частота вращения двигателя, об./мин |
n2
=1230 |
n2
=1050 |
n2
=930 |
n2
=820 |
Передаточные числа |
1,20 |
1,41 |
1,59 |
1,80 |
Крутящий момент на тихоходном валу, Н·м |
3106 |
3638 |
4108 |
4659 |
Крутящий момент на быстроходном валу, Н·м |
2478 |
2478 |
2478 |
2478 |
Межосевое расстояние, мм |
250 |
250 |
250 |
250 |
Модуль зацепления, мм |
4 |
4 |
4 |
4 |
Число зубьев шестерни |
46 |
43 |
39 |
36 |
Число зубьев колеса |
56 |
59 |
63 |
66 |
Угол наклона β |
35º 18’ 8" |
Ширина венца шестерни, мм |
200 |
200 |
200 |
200 |
Ширина венца колеса, мм |
200 |
200 |
200 |
200 |
Окружная скорость, м/с |
17,5 |
16,3 |
14,8 |
13,7 |
Окружное усилие, кН |
22,6 |
25,2 |
26,6 |
28,8 |
Радиальное усилие, кН |
10,1 |
11,2 |
11,9 |
12,8 |
Осевое усилие, кН |
0 |
0 |
0 |
0 |
Примечания.
1. По сравнению с компьютерными распечатками увеличена ширина венцов полушевронов с 70 до 100 мм. Это привело к уменьшению рабочих напряжений. Недогрузка по контактным напряжениям составляет 19 %, по изгибным напряжениям - 76 %.
2. В одновременном зацеплении находятся 4-5 пар зубьев, что свидетельствует о высокой плавности работы зацепления.
Вывод. Контактная и изгибная прочность достаточна, так как напряжения ниже допускаемых.
3.4 Расчет валов
Исходные данные.
Момент на быстроходном валу Т1
= 2478 Н·м.
Момент на тихоходном валу принят максимальный из четырех значений при u=1,8 Т2
= 4659 Н·м.
Расчет тихоходного вала.
Диаметр опасного сечения из расчета на кручение [15]:
, (3.26)
где - допускаемое касательное напряжение; =15 МПа [15].
=114,5 мм.
Принято d=115 мм. Диаметры шеек под подшипники d1
=95 мм. Выходной конец - конический с наибольшим диаметром d2
=90 мм и конусностью 1:10 (рисунок 3.1).
Эскизная компоновка для определения расстояний между линиями действия всех сил и реакций опор.
Они зависят от некоторых конструктивных элементов.
Суммарная длина ступиц колес lст
S
=2(b+20)=2(100+20)=240 мм.
Толщина стенки корпуса мультипликатора [15]
d=1,2 9,91 мм. (3.27)
Принято d=12 мм.
Расстояние от торцов колес до внутренних стенок D=10 мм, расстояние от стенки корпуса до торцов подшипников D2
=7 мм. Приняты роликоподшипники 2219 с В=32 мм без буртов на наружных кольцах. Компоновка выполнена в компьютерном варианте. Расстояния от середин венцов колес до середин подшипников l1
=87 мм. Расстояние между серединами колес l2
=140 мм. Расстояние от середины подшипника до середины консоли с полумуфтой l3
=140 мм. Вследствие несоосности соединяемых валов на их консольные участки действует дополнительная сила Fм
. Сила от несоосности муфты [9]
FМ
=0,5Fсм
=0,5×2T2
/Dо
, (3.28)
где Dо
- диаметр отверстий под пальцы МУВП, Dо
=280 мм [10].
FМ
=4659×103
/280=14640 Н=14,6 кН.
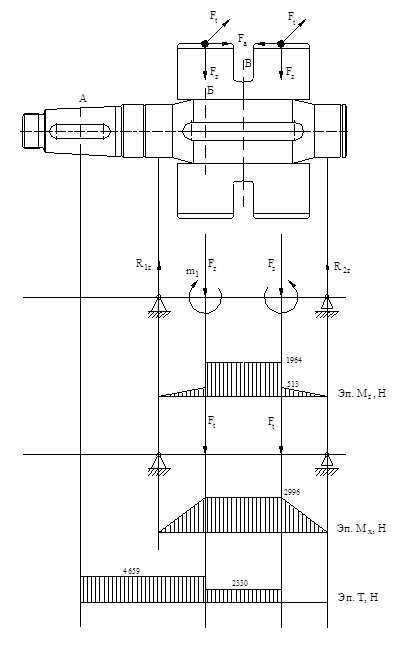
Рисунок 3.1 – Расчетные схемы тихоходного вала
Сосредоточенные моменты от осевой силы
m2
=Fa
d2
/2=9,4×308,822=1451 Н×м.
Расчетные схемы в направлениях Х и Z представлены на рисунке 3.1.
Реакции опор в направлении Z (вертикальном).
Sm1
=О; R2
z
×(2l1
+l2
)+m2
-Fr
(l1
+l2
)-m2
- Fr
l1
=0, откуда
R2
z
= кН. (3.30)
Так как схема симметрична (рисунок 3.1), R1
z
= R2
z
=5,9 кН.
Изгибающие моменты в направлении Z.
M3
= R1
z
l1
=5,9×87=513 Н×м (3.31)
=M3
+m2
=513+1451=1964 Н×м.
Аналогично M4
=513 Н×м, =1964 Н×м. Эпюра момента Мz
представлена на рисунке 3.1.
Реакции опор в направлении Х (горизонтальном).
Расчетная схема на рисунке 3.1.
SМ1
=0; -FM
l3
+R2
x
(2l1
+l2
)-Ft
(l1
+l2
)-Ft
l1
=0,
кН. (3.32)
S Х=0; -2Ft
+R2
x
R1
x
-FM
=0.
R1x
=2Ft
+FM
-R2x
=2×13,3+14,6-19,8=21,4 кН. (3.33)
Изгибающие моменты в направлении Х:
M3
=R1
X
l1
=21,4×87=1862 Н×м. (3.34)
M4
=R1
X
(l1
+l2
)-Ft
l2
=21,4(87+140)-13,3×140=2996 Н×м.
M2
=-FM
l3
=-14,6×140=-2044 Н×м.
Эпюра моментов Мх
на рисунке 3.1.
Диаметр опасного сечения.
Опасное сечение - Б. Суммарный изгибающий момент:
Н×м.
Н×м.
Приведенные моменты
Н×м. (3.35)
Н×м.
Эпюра крутящих моментов на рисунке 3.1.
Диаметр вала под колесом:
, (3.36)
где - допускаемое напряжение на изгиб при знакопеременной нагрузке; принято =50 МПа [6].
мм.
Принято d1
=115 мм из соображений повышенной прочности и высокой жесткости ответственной детали.
Диаметры шеек подшипников d1
=95 мм, наибольший диаметр выходного конца 90 мм при конусности 1:10.
Подбор подшипников качения.
Тихоходный вал принят плавающим на роликоподшипниках без буртов на наружных кольцах.
Радиальные нагрузки на подшипники
кН. (3.37)
кН.
Частота вращения вала n2
=930 об/мин.
Диаметры шеек d2
=95 мм.
Расчет проведен для опоры 1. Приведенная нагрузка
, (3.38)
где kd
- коэффициент нагрузки; принято kd
=1,3 [15].
P=22,2×1,3=28,86 кН.
Сп
=22,86×(60×930×5000/106
)3/10
=149,37 кН. (3.39)
Принят подшипник 2219 со следующими характеристиками: d´D´B=95´170´34; С=165 кН [10].
Фактический ресурс
Lh
=106
(C/P)3.33
/60n=106
(195/28,86)3,33
/60×930=5954 ч. (3.40)
Ресурс подшипников приемлем.
Подбор шпонок.
Под обоими колесами принята общая призматическая шпонка b´h´l=25´14´210. Рабочее напряжение смятия на боковых поверхностях шпонки и ступицы
, (3.41)
где - расчетная длина шпонки; t2
- глубина паза ступицы, t2
=5,4 мм [15].
= =210-25=185 мм. (3.42)
МПа.
Допускаемое напряжение смятия [15]:
, (3.43)
где - предел текучести; для стали 45 =590 МПа [10].
МПа.
Прочность достаточна.
На коническом выходном конце средний диаметр
мм. Принята шпонка 25´14´110. Глубины пазов t1
=9 мм, t2
=5,4 мм [15]. Рабочее напряжение смятия:
МПа.
Прочность достаточна.
Расчет прессового соединения.
Исходные данные.
Момент на одном полушевроне Т=4659/2=2330 Н×м.
Осевая сила Fa
=9,4 кН.
Номинальный диаметр d=115 мм.
Диаметр ступицы d2
=180 мм.
Рабочая длина ступицы lст
=90 мм.
Коэффициент трения f=0,08 [7].
Расчетный натяг
, (3.44)
где К - коэффициент запаса по сцеплению, принят К=2,5 [7]; E1
=E2
-модуль упругости стали, Е=2,15×105
МПа; С1
и С2
- коэффициенты, получаемые из решения задачи Лямэ.
, (3.45)
где - коэффициенты Пуассона, для стали m=0,3; d1
- внутренний диаметр вала, d1
=0.
. (3.46)
; .
Величина расчетного натяга
мкм.
Поправка на шабровку при напрессовке
, (3.47)
где и - максимальные вычеты микронеровностей, принято =6,3 мкм, =10 мкм.
мкм.
Технологический натяг.
NT
=48+20=68 мм.
Принята посадка Æ=115 H7/t6=Æ=115 c натягами Nmin
=69 мкм и Nmax
=126 мкм.
Расчет вероятностных натягов. Средний натяг
Nm
=0,5(Nmin
+Nmax
)=0,5(69+126)=97,5 мкм. (3.48)
SA
=(Es
-Ei
)/6=TD/6=35/6=5,83 мкм. (3.49)
SB
=(es
-ei
)/6=Td/6=(126-104)/6=3,67 мкм.
Среднее квадратическое отклонение табличного натяга
SN
= мкм. (3.50)
Минимальный вероятностный натяг
Npmin
=Nm
-Up
SN
, (3.51)
где Up
- квантиль нормального распределения.
При надежности P=0,999 Up
=3,09 [6] и Npmin
=97,5-3,09×6,89=76 мкм.
При надежности P=0,99 Up
=2,33 [6] и Npmin
=81 мкм.
Посадка принята верно.
Уточненный расчет.
Расчетными приняты сечения А, Б и В. Крутящий момент Т=2330 Н×м.
Изгибающий момент М=3582 Н×м.
Осевая сила Fa
=9,4 кН.
Концентратор напряжения - шпоночная канавка.
Коэффициенты запаса по нормальным и касательным напряжениям
; , (3.52)
где и - пределы выносливости, для стали 45 =250 МПа, =150 МПа [15]; и - эффективные коэффициенты концентрации напряжений, =1,46, =1,54 [15]; и - масштабные коэффициенты, =0,7, =0,59 [15]; и - коэффициенты, =0,05, =0 [15]; - амплитудное напряжение цикла; для симметричного цикла = .
Момент сопротивления:
(3.53)
МПа;
- среднее напряжение цикла:
МПа. (3.54)
- амплитудное напряжение цикла; при нереверсивной работе:
. (3.55)
Полярный момент сопротивления:
мм3
. (3.56)
МПа.
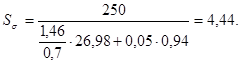
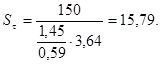
Общий коэффициент запаса:
. (3.57)
Рекомендуемый коэффициент запаса [S]=2,5…3,5 [15]. Прочность достаточна.
Сечение Б - слева от середины венца.
Крутящий момент Т=4956 Н×м.
Изгибающий момент М=3040 Н×м.
Осевая сила Fa
=0 кН.
Амплитудные напряжения цикла:
МПа.
МПа.
Среднее напряжение цикла =0,94 МПа.
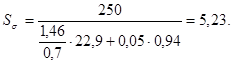
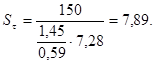
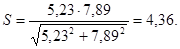
Прочность достаточна.
Крутящий момент Т=4108 Н×м. Напряжения цикла
.
Полярный момент инерции при среднем диаметре d2ср
=83,5 мм:
мм2
.
МПа.
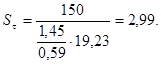
Прочность достаточна. Расчет быстроходного вала. Вал фиксированный. Диаметр опасного сечения:
мм.
Принято d=95 мм. Диаметры шеек под подшипники d1
=80 мм. Выходной конец - конический с наибольшим диаметром d2
=71 мм.
Сила от несоосности муфты:
Fм
=0,5×2×Т1
/Do
=0,5×2×2478×103
/280=8850 Н.
Сосредоточенные моменты m1
=Fa
d1
/2=9,4×191,18/2=8995 Н×м.
Расчетные схемы в направлениях осей Х и Z представлены на рисунке 3.2. Реакции опор в направлении Z (рисунок 3.1): R1
z
= R2
z
=Fr
=5,9 кН.
Изгибающие моменты в направлении моментов Мz
(эпюра на рисунке 3.2).
M3
= R1
z
l1
=5,9×87=513 Н×м.
=M3
+m1
=513+899=1412 Н×м.
M4
= 513 Н×м;
=1412 Н×м.
Реакции опор в направлении Х (схема на рисунке 3.2).
кН.
R1х
=2×13,3+8,85-17,24=18,21 кН.
Изгибающие моменты в направлении Х (эпюра на рисунке 3.2)
M3
=18,21×87=1584 Н×м.
M4
=18,21(87+140)-13,3×140=2272 Н×м.
Mr
=8,85×140=1239 Н×м.
Диаметр опасного сечения. Опасное сечение Б. Суммарный изгибающий момент слева и справа от сечения
Н×м.
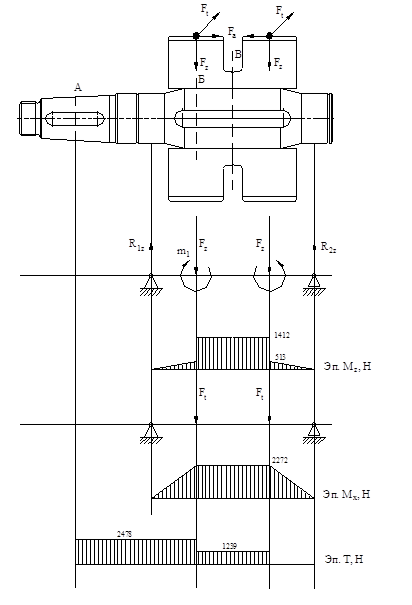
Рисунок 3.2 – Расчетные схемы быстроходного вала
Н×м.
Приведенные моменты:
Н·м.
Н·м.
Эпюра крутящих моментов на рисунке 3.2.
Диаметр вала из расчета на сложное сопротивление:
мм.
Оставлено ранее принятое =95 мм, 1
=80 мм и 2
=71 мм.
Подбор подшипников качения
Приняты роликоподшипники с тремя буртами на кольцах, расчетная схема на рисунке 5.4, е. Радиальные нагрузки:
кН.
кН.
Расчет проведен по опоре 2. Приведенная нагрузка:
Р1
=19,14·1,3=24,88 кН.
Динамическая грузоподъемность:
С=24,88·(60·1480·5·103
/106
)1/3,33
=154,9 кН.
Принимаем подшипники 42516 со следующими характеристиками d´D´B=80´140´33 с динамической грузоподъемностью С=147 кН. Фактический ресурс:
(3.58)
Результат приемлем.
Подбор шпонок. Под колесами принята шпонка 25´14´220 [15]. Глубина пазов t1
=9 мм, t2
=5,4 мм. Рабочая длина шпонки lp
=180 мм, рабочее напряжение смятия
=(2·2478·103
)/(95·180·5,4)=53,67 МПа.
Прочность достаточна.
На коническом выходном конце средний диаметр d1ср
=(71+60)/2=65,5 мм. Принята шпонка20´12´90. Глубины пазов t1
=7,5; t2
=4,9 [15]. Рабочее напряжение смятия
=(2·2478·103
)/(65,5·70·4,9)=221 МПа.
Прочность достаточна.
Расчет прессового соединения
Исходные данные.
Момент на одном полушевроне T=2478/2=1239 Н×м.
Осевая сила Fa
=0 кН.
Номинальный диаметр d=95 мм,
диаметр ступицы d2
=150 мм,
рабочая длина l=180·2=90 мм,
коэффициент трения f=0,08.
Расчетный натяг
мм.
C1
=952
/952
-0,3=0,7; C2
=((1502
+952
)/(1502
-952
))+0,3=2,64.
Технологический натяг
NT
=29+1,2(6,3+10)=49 мкм.
Принята посадка Æ95 Н7/t6=Æ95 [10] с натягами Nmin
=56 мкм и Nmax
=113 мкм.
Вероятностные натяги Np
min
=65 мкм при P=0,999 и Np
min
=68 мкм при P=0,99. Посадка выбрана верно.
Уточненный расчет. Расчетные сечения 4', 4 и 5 на рисунке 3.1.
Сечение 4' - посередине венца колеса со стороны пролета.
Крутящий момент T=1239 Н×м.
Изгибающий момент M=2675 Н×м.
Осевая сила Fa
=0 кН.
Момент сопротивления:
мм3
.
Амплитудное напряжение:
МПа.
Среднее напряжение цикла:
МПа.
Полярный момент сопротивления:
мм3
.
Напряжения цикла:
МПа.
Запас прочности по нормальным напряжениям:
.
Запас прочности по касательным напряжениям:
.
Общий коэффициент запаса:
.
Прочность достаточна.
Сечение 4 - справа от середины венца, со стороны подшипника. Крутящий момент T=2478 Н×м, изгибающий момент M=2329 Н×м, осевая сила Fa
=9,4 кН, диаметр d=95 мм, W=75414 мм3
. Амплитудное напряжение:sa
=2329×103
/75414=30,88 МПа.Среднее напряжение цикла =1,37 МПа. Коэффициент запаса по нормальным напряжениям:
.
Напряжение цикла:
МПа.
Запас по касательным напряжениям:
.
Полный коэффициент запаса:
.
Прочность достаточна.
В сечении 5 - шпоночная канавка. Средний диаметр конического участка d1
c
р
=65,5 мм. Полярный момент сопротивления
мм3
.
Напряжения цикла:
МПа.
Коэффициент запаса:
.
Прочность достаточна.
3.5 Выбор посадок
Подшипниковые посадки выбраны из [15]. Принят нормальный класс точности - по ГОСТ 520-71. Посадка наружного кольца в корпусе принята в системе вала: для быстроходного вала Æ140 Н7/l0, для тихоходного вала Æ170 Н7/l0. Это обеспечивает небольшой зазор, позволяющий кольцу при работе проворачиваться относительно своего посадочного места и более равномерный износ беговых дорожек. Это также упрощает сборку мультипликатора, так как посадку с зазором легче осуществлять в разъемах корпусов.
Посадка внутреннего кольца подшипника на вал принята по системе отверстия. Так как поле допуска на диаметр отверстия внутреннего кольца подшипника расположено в "минус" от номинального размера, то переходная посадка вала обеспечивает гарантированный натяг, предотвращающий проворачивание внутреннего кольца и ослабление натяга в соединении. Приняты сопряжения: для внутреннего кольца быстроходного вала Æ80 L0/n6, тихоходного вала -Æ95 L0/n6.
Крышку подшипников ставят с зазором: Æ140 Н7/d11 и Æ170 Н7/d11- для глухих крышек (без отверстия) и Æ140 Н7/h8 и Æ170 Н7/h8- для сквозных крышек для повышения долговечности манжетных уплотнений.
Шпоночные посадки приняты по [10]. Для нормального соединения предельные отклонения пазов валов приняты N9, пазов ступиц -Js
9. Предельные отклонения шпонок по ширине b-h9, по высоте h-h9, по длине -h14.
3.6 Конструирование валов
Валы спроектированы ступенчатые цилиндрические с коническими выходными концами и резьбовыми участками для закрепления полумуфт по ГОСТ 12081-72 [3]. Для конических хвостовиков приняты высокие призматические шпонки по ГОСТ 10748-79. Под гайки подготовлены шайбы стопорные с носком по ГОСТ 13465-77 [3].
На подступичной части основную нагрузку (восприятие крутящего момента Т и осевой силы Fa
) несет посадка с гарантированным натягом H7/t6 (шпонка поставлена как страховочный элемент) с минимальным вероятностным натягом Np
min
=65 мкм при вероятности P=0,999. Это должно обеспечить надежность прессового соединения.Для снижения концентрации напряжений у краев колес переход от подступичного участка к шейке подшипника выполнен коническим, таким образом, что часть ступицы колеса имеет участок, не сопрягаемый с валом, что существенно снижает концентрацию напряжения за счет повышения податливости крайних участков отверстий в колесах. Для облегчения прессовой посадки конический переходной участок продлен за скругление шпонки на 4-5 мм.Между ступицей колеса и подшипником поставлена фасонная распорная втулка, которая является упором для подшипника. Внутреннее кольцо роликоподшипника фиксируется от осевых перемещений на валу плоским прижимным упорным эксцентрическим кольцом по ГОСТ 13942-86. Между подшипником и пружинным кольцом поставлено компенсаторное кольцо калибровочной толщины. Натяг в соединениях колес с валами, подшипников с валами и упорные пружинные кольца надежно фиксируют детали на валах.
3.7 Конструкция колес
Каждое колесо составлено из двух полушевронов с противоположным направлением косых зубьев. При небольшой разности диаметров валов и колес принята цилиндрическая конструкция с односторонней ступицей. Колеса собираются ступицами друг к другу для возможности снятия полушевронов съемником либо под прессом.
Для работы мультипликатора весьма важным является правильная сборка полушевронов на валу, когда зубья на торцах колес расположены по образующей цилиндра (параллельной осям валов). Для этого после изготовления полушевронов их необходимо расположить плоскими торцми друг к другу, совместив зубья по торцам, скрепить оба полушеврона, и шпоночный глаз долбить в отверстиях обоих полушевронов заодно.
Для снижения концентрации нагрузки по краям полушевронов предусмотрены фаски на зубьях m=4 мм.
3.8 Конструирование элементов корпуса
Принята толщина стенки корпуса d=12 мм, корпус сварной. Материал корпуса сталь 20. Принята вертикальная конструкция мультипликатора с двумя разъемами по валам. Корпусные конструкции: крышка, средний корпус и нижний корпус. Диаметры стяжных болтов
мм. (3.57)
Приняты болты М20. Толщина фланцев болтов h2
=1,2; dc
=1,2×20=25 мм.
Диаметр фундаментальных болтов
dф
=1,25; мм.
Приняты болты М30.
Толщина ребер жестокости h3
=8 мм.
Диаметр винтов, крепящих подшипники М10, количество винтов z=6, толщина фланцев h4
=10 мм, толщина стенки h5
=7 мм [3].
Основной материал заготовок - листовой прокат. Для подшипниковых узлов приняты бруски, к которым привариваются фланцы и стенки корпуса. В брусках сверлятся и растачиваются отверстия под подшипники, затем они разрезаются и привариваются к другим корпусным деталям.
Перед сборкой элементов корпуса фланцы механически обрабатывают (фрезеруют и шлифуют). Чистовая расточка отверстий под подшипники выполняется после скрепления болтами элементов корпусов. Предварительно отверстия под болты центрируют двумя цилиндрическими штифтами, либо калибровочными чистыми болтами.
В корпусе мультипликатора предусмотрены захваты для транспортирования всего мультипликатора либо его корпусов с собранными деталями. Нижняя часть корпуса выполнена расширенной (тангенциальной) для увеличения объемов заливаемого масла до 32 л и повышения устойчивости мультипликатора.
3.9 Уплотнения
Уплотняющие устройства предназначены для предотвращения утечки масла из внутренней полости мультипликатора и попадания грязевых частиц внутрь корпуса. Приняты манжетные уплотнения, которые используют при окружной скорости J<20 м/с [1].
Для быстроходного вала принята манжета 1.1-80´105-1 по ГОСТ 8752-79, для тихоходного вала - 1.1-95´130-1. Поверхность вала под уплотнением должна быть закаленной до твердости HRС 40, параметр шероховатости Ra
=0,32 мкм. Допуск вала под уплотнение должен соответствовать h11. Параметр шероховатости отверстия Ra
=2,5 мкм. Для извлечения манжет в крошках предусмотрены по 2 отверстия [1].
Запрессовать манжету в посадочное отверстие следует с помощью специальной оправы равномерным нажатием по всей торцовой поверхности [3].
3.10 Смазка
Принята картерная смазка. При скорости J<5 м/с реализуется кинематическая вязкость =22 мм2
/с [4]. Минимальная вязкость обосновывается также низкими рабочими температурами в зимнее время работы ПСМ-П. По аналогии с локомотивами (электровоз ВЛ10) принята осерненная смазка З (зимняя). Глубина погружения тихоходного колеса - на 0,25 r2
=0,25×0,5×308,8»40 мм. Объем масла 32 л.
В подшипниках качения небольшие силы трения скольжения возникают между роликами и сепараторами, роликами и упорами колец. При высокой окружной скорости колес масло будет разбрызгиваться, попадать на стенки корпуса и в подшипники. Внутри корпуса также образуется масляный туман.
3.11 Порядок сборки мультипликатора
1. Поставить шпонки на подступичные части и хвостовики валов.
2. Впрессовать вал в один полушеврон с контролем длины запрессовки.
3. Напрессовать второй полушеврон до соприкасания с первым.
4. Установить дистанционные втулки с обоих сторон колес.
5. Нагреть в масле и надеть на шейки валов роликоподшипники: на тихоходном валу внутренне кольцо, на быстроходном валу - внутренне кольцо с роликовой обоймой. Собрать остальные детали.
6. Запрессовать манжету в сквозную крышку подшипника.
7. Установить крышку подшипника на валу.
8. Впрессовать валы в полумуфты: быстроходный вал - в пальцевую полумуфту, тихоходный вал - в ступочную полумуфту.
9. Закрепить и застопорить полумуфты гайками и шайбами с лапками.
10.Собрать нижние корпуса: установить тихоходный вал в сборе в нижний корпус. Покрыть плоскости разъема пастой "Герметик". Установить средний корпус, двумя цилиндрическими штифтами отцентрировать отверстия под болты и посадочные места подшипников, стянуть корпуса болтами с пружинными шайбами, провернуть вал.
11.Привинтить крышки подшипников, поставив под них набор регулировочных прокладок. Застопорить головки винтов проволокой попарно, для чего предварительно просверлить отверстия в головках.
12.Собрать крышку со средним корпусом: установить быстроходный вал в сборе, покрыть плоскости разъема пастой "Герметик", установить крышку корпуса, два цилиндрических штифта, стянуть крышку и средний корпус болтами с пружинными шайбами, провернуть вал.
13.Установить крышку люка с прокладкой и закрепить винтами.
14.Ввинтить контрольные пробки и пробку маслосливного отверстия с прокладками.
3.12 Проектирование муфты
Исходные данные.
Для снижения динамических нагрузок, устранения возможности резонансных разрушений и компенсирования несоосности принята муфта упругая втулочно-пальцевая (МУВП). Допускаемые смещения: осевое Dа
=3 мм [4], радиальное Dz
=0,3…0,6 мм [2], угловое Dα
=1°[2]. Упругий элемент кольца тангенциального сечения или гофрированные резиновые втулки. Для обоих валов приняты одинаковые муфты, так как диаметры сопряженных с мультипликатором диаметры валов тягового электродвигателя и вентилятора приблизительно одинаковы. Расчетный момент Т2
=4107 Н×м.
Основные размеры.
Муфта спроектирована специальной, так как выходной конец тягового электродвигателя не соответствует размерам стандартной муфты. Многие размеры приняты из ГОСТ 2229-55 для муфт МУВП.
D=400 мм - диаметр муфт;
Dо
=300 мм - диаметр расположения осей пальцев;
dст
=220 мм - диаметр ступицы;
l1
=57 мм - толщина фланца пальцевой полумуфты;
l2
=90 мм - толщина фланца втулочной полумуфты;
lст1
=140 мм - длина пальцевой полумуфты;
lст2
=170 мм - длина втулочной полумуфты;
Δ=5 мм - зазор между полумуфтами;
dп
=38 мм - диаметр пальца;
М30- резьба хвостовика пальца;
dв
=70 мм - диаметр резиновой втулки;
dо
=72 мм - диаметр отверстия под втулки;
lв
=72 мм - длина втулки;
z=10 - число пальцев.
Число пальцев определено из условия
Zdo
£ 2,8Dо
, откуда
Z=2,8 Dо
/dп
=2,8×300/72=11,7. (3.58)
Расчет на смятие.
Упругие элементы специальной муфты проверяют на смятие в предположении равномерного распределения нагрузки между пальцами. Рабочее напряжение смятия
Мпа. (3.59)
Прочность достаточна, так как допускаемое напряжение
[sсм
]=2МПа [4].
Расчет на изгиб.
Пальцы муфты изготавливают из стали 45 и рассчитывают на изгиб [4]:
МПа (3.60)
В формуле (3.3) d1
- толщина кольца на пальце; d1
=10 мм.
Допускаемое напряжение материала пальцев
[sи
]=0,4sТ
, (3.61)
где sТ
- предел текучести; sТ
=280 МПа.
[sи
]=0,4×280=112 МПа.
Прочность пальцев достаточна.
4. Проектирование оборудования охлаждения
4.1 Выбор оборудования охлаждения
Обоснование применения принудительного охлаждения.
Совершенно очевидна необходимость применения принудительного охлаждения для двигателя ТЛ-2К. Требования по эксплуатации двигателя и технические характеристики [20]: "…при напряжении на выводах 1500 В и количестве воздуха, прогоняемого для охлаждения машины, 95 м3
/мин тяговые электродвигатели ТЛ-2К1 имеют следующие основные данные для длительной работы: мощность 560 кВт, ток 400 А, частота вращения якоря 820 об/мин, КПД 93,6%, максимальная частота вращения якоря 1690 об/мин, вес электродвигателя без шестерен 5000 кгс".
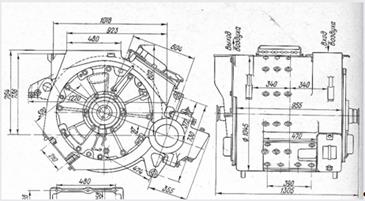
Рисунок 4.1 – Основные размеры и схема охлаждения двигателя ТЛ-2К
В стесненном рабочем пространстве машины ПОМ-4 для охлаждения двигателя ТЛ-2К выбран радиальный вентилятор 2D08 немецкой фирмы "ELEKTROR" (компания "ELEKTROR" основанная в 1923г - один из ведущих немецких производителей промышленных радиальных вентиляторов), который полностью обеспечит принудительное воздушное охлаждение двигателя рабочего органа.
Таблица 4.1 – Основные технические характеристики вентилятора 2D08
Обозначение |
2D 08 |
Цена без опоры, руб. |
85655 |
Производительность м3
/мин |
95 |
Напряжение, В |
380 Δ |
Частота, Гц |
50 |
Сила тока, А |
10 |
Потребляемая мощность, кВт |
5 |
Частота вращения рабочего колеса, об/мин |
2910 |
Емкость конденсатора, мкФ/В |
52 |
Масса, кг |
- |
Вентиляторы этой серии изготавливаются на основе алюминия, что выгодно выделяет их из числа прочих вентиляторов по таким характеристикам как масса и стойкость к коррозии. Лопасти крыльчатки выполнены из стойкой к коррозии нержавеющей стали, кроме того, двигатели этих вентиляторов не нуждаются в дополнительном охлаждении – они охлаждаются воздухом, проходящим через них. Для крепления на фланцах предусмотрены отверстия.
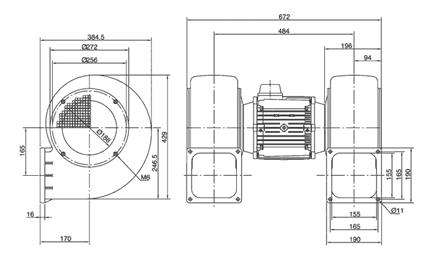
Рисунок 4.1 – Вентилятор 2D08
Для охлаждения мультипликатора выбран вентилятор 2D05 с характеристиками приведенными в таблице 4.2.
Таблица 4.2 - Основные технические характеристики вентилятора 2D05
Обозначение |
2D 05 |
Цена без опоры, руб. |
26714 |
Производительность, м3
/мин |
21 |
Напряжение, В |
220/380 |
Частота, Гц |
50 |
Сила тока, А |
1,91/1,1 |
Потребляемая мощность, кВт |
0,35 |
Частота вращения рабочего колеса, об/мин |
2770 |
Емкость конденсатора, мкФ/В |
8,4 |
Масса, кг |
- |
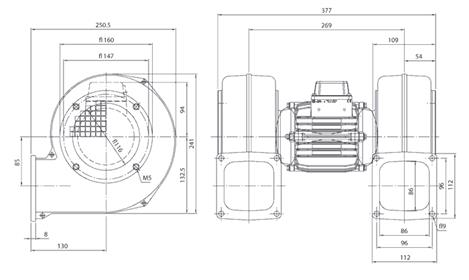
Рисунок 4.2 – Вентилятор 2D05
В качестве воздуховода между вентилятором 2D08 и двигателем ТЛ-2К спроектирован коллектор, объединяющий два потока воздуха и направляющий воздух непосредственно во входное отверстие двигателя рабочего органа. Воздух, произведя теплообмен, покидает двигатель из выходного отверстия с другой стороны.
Для подвода воздуха от вентилятора 2D05 к нижней части мультипликатора с находящимися на ней теплообменными ребрами используется воздуховод.
Расчет и выбор воздуховода [21].
Скорость выхода воздуха из вентилятора 2D05 Vв
, м/с:
(4.1)
где L – расход воздуха за минуту, L = 10,5 м3
/мин (половина общей производительности вентилятора на каждый воздуховод); А – площадь сечения выходного отверстия вентилятора, А = 86х86 мм.
.
Принят воздуховод круглого сечения с внутренним диаметром 100 мм, толщиной 0,55 мм и погонной массой 1,36 кг на один метр.
Проектирование коллектора.
Коллектор проектируется с переменным сечением, сварной из двух деталей, изготавливаемых из стального листа толщиной 5 мм. Материал - сталь 3. Предусмотрены фланцы для крепления к раме вентиляторов охлаждения и двигателю рабочего органа. Таким образом, коллектор является не только воздуховодом от радиального вентилятора 2D08 к двигателю рабочего органа, но и элементом крепежа, усиливающим раму вентиляторов охлаждения.
4.2 Проектирование рамы вентиляторов охлаждения
Опорная рама охлаждающих вентиляторов сварена из равнополочного уголка с шириной полки 80 мм и толщиной 8 мм и стальной плиты толщиной 10 мм. К раме двигателя крепится шестнадцатью болтами за подпятники, приваренные к уголкам-стойкам. В плите вырезаются два квадратных отверстия размерами 155х155 мм для вентилятора охлаждения двигателя и два отверстия 86х86 мм для вентилятора охлаждения мультипликатора. Все четыре отверстия сверху обрамлены квадратными присоединительными платиками шириной 20 мм и толщиной 5 мм, а снизу два квадратных платика для отверстий под воздуховоды охлаждения мультипликатора и один прямоугольный для присоединения коллектора. Все платики привариваются угловыми швами с катетом 5 мм к стальной плите и обрабатываются по классу шероховатости до Ra 10. Рама укреплена укосинами.
5.Расчет экономической эффективностимодернизации Пом-4
Основным обобщающим показателем, определяющим эффективность модернизированной техники, является экономический эффект, в котором находят отражение все показатели, характеризующие модернизацию.
Годовой экономический эффект от применения модернизированной ПОМ-4 рассчитывается как абсолютная величина между затратами машины до модернизации и после модернизации:
, (5.1)
где - годовые затраты на эксплуатацию машины до модернизации, руб; - годовые затраты на эксплуатацию модернизированной машины, руб.
Годовая выручка от использования машины , руб [16]:
, (5.2)
где - годовая производительность устройства, ;
Часовая выработка машины составляет 1600 м3
/час. До модернизации машина не могла выполнять работу целый день в связи с перегревом двигателя, к тому же работа по уборке снега требуется не каждый день, поэтому объем работы за рассматриваемый период времени составляет: 787,2×1600=1259520 м3
. После модернизации машины двигатели не перегреваются и она может выполнять работы в соответствии с установленным графиком работ. Объем работ машины после модернизации – 1574,4×1600=2519040 м3
.
Цена единицы продукции , . =10 
тыс. руб.
тыс. руб.
Количество машино-часов работы устройства ( ), .
, (5.3)
где Д – количество рабочих дней машины в году (машина работает 6 месяцев в году); - время смены, ч, =8 ч; - количество смен, =2; - коэффициент, учитывающий время простоя, =0,8 [16].
Машина работает 6 месяцев в году – с октября по март включительно. Расчет производится за октябрь, ноябрь, декабрь 2007 года и январь, февраль, март 2008 года. Количество календарных дней – 183. Количество праздничных и выходных дней – 60. Количество рабочих дней машины в году Д:
Д = 365/2 – åП, (5.4)
где åП – количество выходных и праздничных дней в период работы машины (åП=60 дней).
Д = 183 – 60=123 дня.
Работы выполняется в две смены, то есть 16 часов в день. Количество рабочих часов за полгода работы составляет: 16×123=1968 часов.
Количество машино-часов работы устройства , :
 .
 .
Эксплуатационные затраты по использованию устройства складываются из затрат на заработную плату машиниста тепловоза, двух ремонтников, затрат на материалы, на замену вышедших из строя деталей, электроэнергию и т.п.
Заработная плата машиниста , тыс. руб.:
, (5.5)
где - оклад машиниста, =15000); - районный коэффициент ( =20 %);
- коэффициент, учитывающий начисления на заработную плату ( =26,2%); - коэффициент премирования ( =25 %).
тыс. руб.
В обоих рассматриваемых вариантах затраты на заработную плату машиниста одинаковы. Заработная плата рассчитывает за период работы машины.
Затраты на ремонт :
, (5.6)
где - заработная плата ремонтнику, тыс. руб.; - затраты на ремонтные материалы, тыс. руб.
Заработная плата ремонтнику :
, (5.7)
где - оклад ремонтника, руб.( =10,0 тыс. руб.); - затраты времени на выполнение ремонта за рассматриваемый период, руб.
Ремонтные работы выполняются силами двух ремонтников. За рассматриваемый период каждый из ремонтников работает в общей сложности 15 дней:
тыс. руб.
Затраты на материалы составляют 50 тыс. руб. за весь рассматриваемый период (6 месяцев), при этом в базовом варианте добавляются расходы на замену электродвигателя стоимостью 2500 тыс. руб. Затраты на ремонт составляют:
=50+2500=2550 тыс. руб.
=50 тыс. руб.
Годовая сумма амортизационных отчислений составляет , тыс. руб.:
, (5.8)
где - норма амортизации, % ( =15%); К – стоимость устройства, руб.
тыс. руб.
тыс. руб.
Расходы электроэнергии на работу электродвигателей , [16]:
, (5.9)
где - суммарная мощность электродвигателей, кВт, =800 кВт,
=811 кВт; - стоимость единицы электроэнергии, , =0,98 ; К – время работы машины.
тыс. руб.
тыс. руб.
Для обоих вариантов расход электроэнергии на работу электродвигателей одинаков.
Итоговая величина эксплуатационных расходов составляет:
Э0
=158,8+2550+1500+617,16=4825,96 тыс. руб.
Э1
=158,8+50+1537,5+1251,3=2817,6 тыс. руб.
Выполненные расчеты сводим в таблицу 5.1.
Таблица 5.1 - Расчет эффективности модернизации ПОМ-4
Наименование показателя |
До модернизации |
После модернизации |
Производительность ПОМ-4, м3
/час |
1600,00 |
Объем работ, м3
|
12595200,00 |
2519040,00 |
Количество машино-часов работы ПОМ-4,  |
787,20 |
1574,40 |
Годовая выручка от использования ПОМ-4, тыс. руб. |
12595,20 |
25190,40 |
Капитальные затраты, тыс. руб. |
10 000,00 |
250,00 |
Эксплуатационные расходы, в т.ч. |
4825,96 |
2817,60 |
- заработная плата машиниста, тыс. руб. |
158,80 |
158,80 |
- затраты на ремонт, тыс. руб. |
2550,00 |
50,00 |
- амортизация, тыс. руб. |
1500,00 |
1537,50 |
- электроэнергия, тыс. руб. |
617,16 |
1251,30 |
4. ИТОГО затрат, тыс. руб. |
14825,96 |
3067,6 |
Годовая экономия затрат от внедрения модернизации на ПОМ-4 составляет: Эг
=14825,96-3067,6= 11758,36 тыс. руб.
Показатель экономической эффективности :
. (5.10)
. (5.11)
где - нормативный показатель экономической эффективности ( =0,15).
.
.
Срок окупаемости , лет:
 . (5.12)
года.
Условие выполнено, следовательно, внедрение модернизации для ПОМ-4 с экономической точки зрения выгодно.
Заключение
В заключении можно отметить, что достигнуты все цели, поставленные в проекте. При том, что часовая производительность по уборке снега не изменялась мы видим, что производительность за год увеличится практически вдвое, теперь не нужно будет после непродолжительной работы останавливать машину для охлаждения двигателя рабочего органа, машина может беспрепятственно работать много часов подряд, не задерживая движения поездов, кроме того существенно уменьшатся затраты на эксплуатацию машины ПОМ-4, что связано прежде всего с тем, что перестанут гореть двигатели ТЛ-2К. Так же можно отметить, что проектирование универсального мультипликатора с несколькими расчитанными передачами позволит существенно уменьшить диапазон частот вращения рабочего органа, что приведет к увеличению мощности воздушного потока в случае, когда двигатель не способен набать расчетную частоту вращения, и не будет заставлять рабочий орган вращаться намного быстрее наминальной частоты если скорость вращения двигателя намного быстрее расчетной частоты вращения, что может привести к поломке вследствие значительного увеличения нагрузки
Список использованных источников
1 Белоусов И. А. Вентиляторный снегоочиститель // Путь и путевое хозяйство. - 1988. - №6. - С. 6.
2 Бурдаков Ю.И., Зарницин Э.Г., Кеммер А.С. Проектирование установок пневмотранспорта. Ч1, Ч2. - Барнаул, 1982. - 43 с.
3 Войтковский К.Ф. Механические свойства снега. -М., 1977. - 126 с.
4 Гирин С. А. Снегоочиститель "Тайфун-Д".// Путь и путевое хозяйство. - 1988. - № 11. - С. 16.
5 Глотов В.А., Якимович А.Н. Моделирование рабочего прцесса аэродинамического снегоочистителя для станций // Сб. докл. регион. научно-практ. конф. "Вузы Сибири и Дальнего Востока Транссибу". - СГУПС, Новосибирск, 2002. - С56-61.
6 Детали машин. Под ред. О. А. Ряковского. - М., 2002. - 554 с.
7 Дунаев П. Ф., Леликов О. П. Конструирование узлов и деталей машин. - М., 2000. - 447 с.
8 Ермилов А. Льдоуборочная машина: ультразвуковой вариант // Изобретатель и рационализатор. - М., 1985. - С.14-15.
9 Иванов М. Н. Детали машин. - М., 1991. - 383 с.
10 Курмаз Л. В., Скобейда А. Т. Детали машин, проектирование. - Минск, 2001. - 290 с.
11 Куценко Г. П. Вентиляторный снегоочиститель на АГМу
.// Путь и путевое хозяйство. - 1989. - №11. - С. 30.
12 Моут Т.В., Саундерс Р.Л. Отделение льда от поверхности с помощью источников света высокой интенсивности // Путь и путевое хозяйство. - 1989. - №11. -С. 206-209.
13 Нещадин В. П., Карпов Н. А., Копчугов В. А. Машина сдувает снег с пути. // Путь и путевое хозяйство. - 1988. - №3. - С. 19.
14 Поляков В.В., Скворцов Л.С. Насосы и вентиляторы. - М., 1990. - 336 с.
15 Проектирование механических передач / С. А. Чернавский и др. - М., 1984. - 560 с.
16 Ринджер Т.Р. Исследования, касающиеся удаления льда и снега с транспортных средств // Борьба со снегом и гололедом на транспорте. Материалы 2-го международного симпозиума. - М., 1986. - С. 25-29.
17 Роберт Р.Блекберн, Эндрю Д. Ст. Джон Физические альтернативы использования химикатов против обледенения проезжей части дорог. - М., 1986. - С.114-129.
18 Свинтицкий Л. И. Вентиляторный снегоочиститель.// Путь и путевое хозяйство. - 1990. - №2. - С. 24.
19 Ясюченя В. В. Вентиляторный снегоочиститель "Ветерок".// Путь и путевое хозяйство. -1988. - №12. - С. 6.
20 Чиракадзе Г. И., Кикнадзе О. А. "Электровоз ВЛ 11. Руководство по эксплуатации". М., Транспорт, 1983 г., 464 с.
21 "Справочник по теплоснабжению и вентиляции". Щекин Р. В. и др. Книга 2-я, Киев, "Будiвельник", 1976 г., стр. 352.
Приложение А
Результаты расчетов ЭВМ
Для передаточного числа u = 1,2

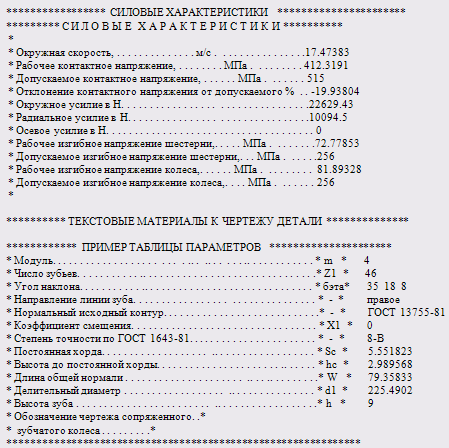
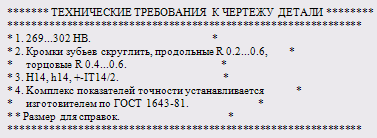
Для передаточного числа u = 1,4
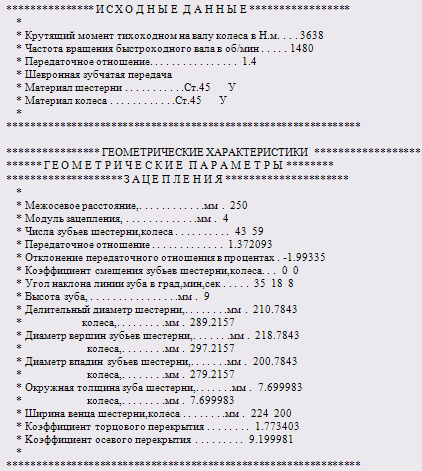
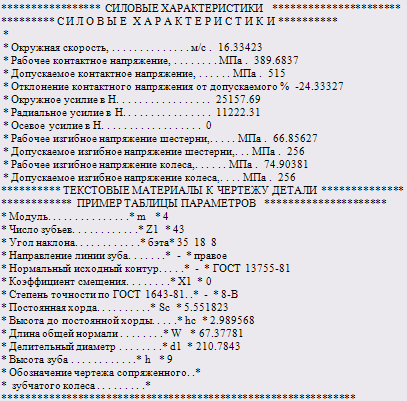
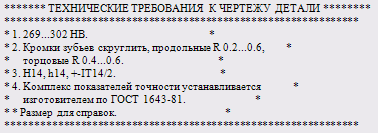
Для передаточного числа u = 1,6
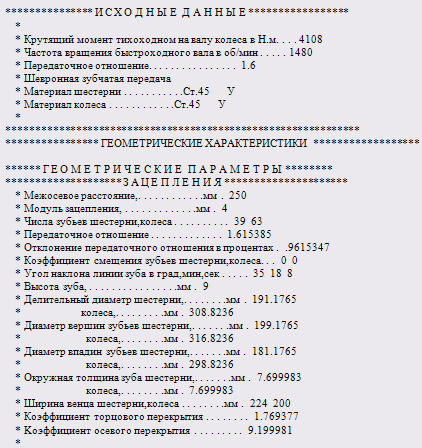
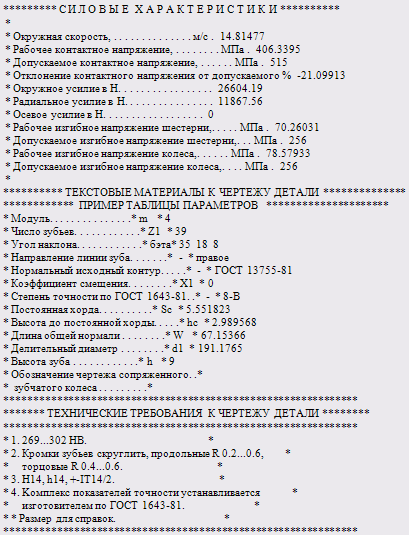
Для передаточного числа u = 1,8
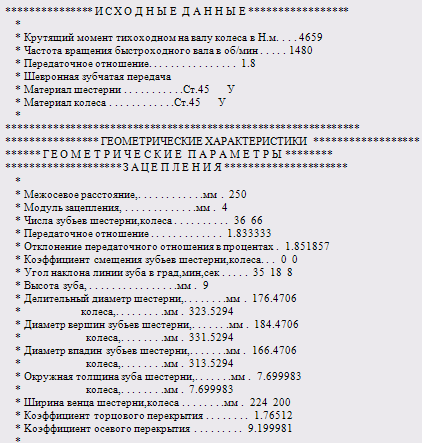
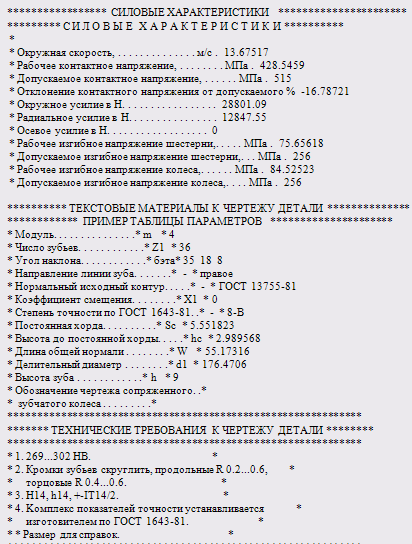
|