Содержание
1. Исследование влияния смещений в кинематической цепи рулевого привода на работу и момент сил трения
2. Расчёт пути трения и скорости относительного скольжения элементов шарниров рулевых тяг
3. Исследование зависимости изменения схождения управляемых колёс от упругости, зазоров в сопряжениях и усилия в рулевом приводе
4. Силовой способ оценки характеристик и состояния рулевого привода
5. Теоретическое обоснование критериев оценки эксплуатационного состояния рулевого привода и шарниров рулевых тяг
5.1 Обоснование критерия качества рулевого привода
5.2 Обоснование критериев оценки эксплуатационного состояния шарниров рулевых тяг с осевой пружиной
Библиографический список
1. Исследование влияния смещений в кинематической цепи рулевого привода на работу и момент сил трения
Выходной характеристикой рабочих процессов в рулевом приводе автомобилей можно считать величину изменения угла схождения управляемых колёс и соотношения их углов поворота. Обе величины в процессе эксплуатации изменяются в зависимости от ряда конструктивных и эксплуатационных факторов.
Рабочие процессы в РП, имеющем звенья, сопряжённые силовым замыканием с упругой связью [3], сопровождаются непрерывными относительными смещениями элементов, которые происходят под действием переменных по величине и направлению поперечных, касательных и вертикальных сил, создающих поворачивающие моменты относительно оси поворотной стойки передней подвески.
В зависимости от соотношения суммарных моментов, действующих на каждое управляемое колесо, в рулевом приводе автомобилей с рулевой трапецией, расположенной сзади передней оси, возникает растяжение, причём начальное схождение увеличивается или сжатие - уменьшается.
Таким образом, характеристикой рабочих процессов в РП является работа, затраченная на преодоление сил трения в подвижных сопряжениях РП и выборку смещений в его кинематической цепи. При этом, полезной работой считается израсходованная на обеспечение курсовой устойчивости, т.е. на гашение колебаний управляемых колес, вызванных стохастическими нагрузками.
Эту работу в основном производят обратимые смещения, обусловленные упругостью РП, она выполняется без участия водителя в режимах движения по траектории, близкой к прямолинейной, когда выполняется большая часть транспортной работы.
Часть же работы, затраченной водителем на обеспечение заданной траектории движения, расходуется на преодоление необратимых смещений, вызванных зазорами в подвижных сопряжениях рулевого привода.
Эта работа затрачивается непроизводительно, уменьшает силовое передаточное число РУ, вызывает увеличение утомляемости водителя и интенсивности износа шарниров рулевых тяг, резко снижает заданный при проектировании автомобиля уровень эксплуатационных свойств.
В процессе движения автомобиля работа сил, прилагаемых к рулевому колесу для поддержания заданной траектории движения, затрачивается на изменение кинетической энергии поворота рулевого вала и связанных с ним деталей, а также поворота управляемых колёс. При этом преодолеваются активные силы, вызванные влиянием микропрофиля дорожного полотна, момент сопротивления управляемых колёс повороту, вызванный стабилизирующим моментом, и силы трения в подвижных сопряжениях рулевого привода, которые могут быть приведены к поворотному рычагу цапфы и выражены моментом трения.
Аналитическое выражение связи перечисленных сил, моментов и углов поворота следует из теоремы об изменении кинетической энергии системы рулевого управления и может быть представлено в виде равенства работ - затраченной на рулевом колесе и полученной на управляемых колёсах:
 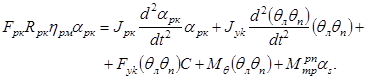 |
(1) |
Примем допущения:
и ,
т.к. в 10 в рассматриваемых режимах движения.
Угол поворота управляемого колеса с учётом угла поворота рулевой сошки на величину смещений в кинематической цепи РП равен:
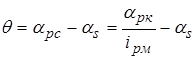 |
(2) |
Тогда выражение (1) принимает вид:
 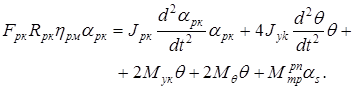 |
(3) |
При установившемся движении рулевого колеса равенство работ, совершённых в рулевом приводе на рулевой сошке и управляемых колёсах учётом момента сил трения в подвижных сопряжениях РП имеет вид:
 . |
(4) |
Отсюда получаем зависимости влияния величины смещений в РП на:
а) угол поворота управляемого колеса:
; |
(5) |
б) момент сил трения в подвижных сопряжениях рулевого привода:
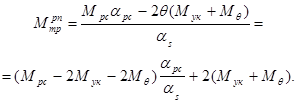 |
(6) |
Из выражения (5) следует, что с увеличением смещений в РП, являющихся основным параметром технического состояния рулевого привода, уменьшается угловое передаточное число рулевого управления, т.е. уменьшается угол поворота управляемых колёс на единицу поворота рулевого колеса. Из выражения (6) следует, что при этом также уменьшается и момент сил трения в подвижных сопряжениях РП, что порождает ударный характер нагружения и прогрессивное увеличение смещений в РП.
Эти причины вызывают увеличение суммарного угла поворота рулевого колеса для поддержания заданной траектории движения на единицу пути, часть которого служит для компенсации люфтов в рулевом управлении. В этом случае уравнение работ, затраченных в рулевом приводе только на преодоление сил трения в подвижных сопряжениях и компенсацию смещений в них, с учётом (3), принимает вид:
Отсюда путём интегрирования при известных начальных условиях можно получить выражение зависимости угла поворота УК от смещений в кинематической цепи рулевого привода автомобиля.
Шарниры рулевых тяг, учитывая их количество, являются основными элементами, формирующими смещения в кинематической цепи рулевого привода автомобилей. Это определяет необходимость анализа работ сил трения в них, которые можно определить как разность работ, совершаемой рулевой сошкой и полученной на поворотных рычагах цапф.
При этом элементарная работа определяется:
а) рулевой сошки: (8)
б) поворотного рычага: (9)
Для определения этих работ необходимо представить моменты на рулевой сошке и поворотном рычаге функциями их углов поворота. С этой целью введём коэффициент пропорциональности нарастания момента относительно угла поворота (то же - усилия в РП относительно смещения в нём), физический смысл которого следует из диаграммы (рис.1) равен:
 . |
(10) |
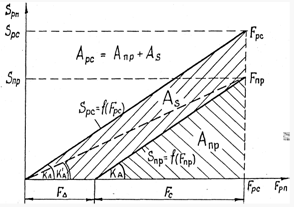
Рис.1. Диаграмма работ: затраченной на рулевой сошке на преодоление необратимых смещений в РП и полученной на поворотном рычаге.
Тогда работа, затраченная на рулевой сошке и полученная на поворотном рычаге цапфы, будет равна, соответственно:
, |
(11) |
. |
(12) |
Работа сил трения для обеих половин рулевого привода равна:
. |
(13) |
Учитывая, что угол поворота рулевой сошки можно выразить:
. |
(14) |
Выражение (13) может быть приведено к виду:
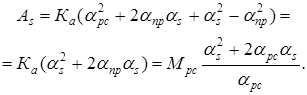 |
(15) |
Исходя из физических процессов, протекающих в рулевом приводе, разделим всю область смещений в РП и соответствующих им усилий на четыре диапазона согласно диаграмме (рис.2). В первом диапазоне преобладают предварительные смещения, вызванные силами вязкого трения в подвижных сопряжениях РП. Их величина незначительна (до 0,15 мм), они полностью выбираются при усилии 10 Н.
Во втором диапазоне преобладают необратимые смещения, вызванные наличием зазоров в сопряжениях носящие износный характер. Их величина не превышает 1,5-2 мм для технически исправных автомобилей при усилии 30-50 даН, после снятия которого они не компенсируются.
В третьем диапазоне имеют место обратимые смещения, вызванные упругостью элементов РП. Они достигают 8-10 мм при средне эксплуатационных нагрузках в РП не выше 300 даН, после снятия которых они компенсируются. В четвертом диапазоне имеют место только остаточные смещения, вызванные пластическим деформированием деталей и являющиеся критерием прочностных свойств.
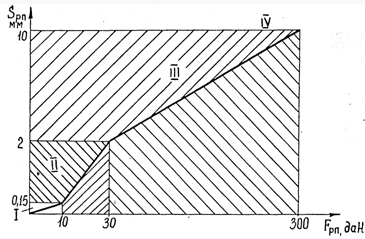
Рис.2. Диаграмма диапазонов усилий и смещений в кинематической цепи РП, вытекающая из физических процессов в рулевом приводе
Таким образом, при условии, что поворот рулевой сошки происходит в пределах смещений в кинематической цепи РП, учитывая принятые ранее допущения, работа, затраченная на преодоление моментов трения в подвижных сопряжениях, зазоров и упругости РП, равна:
, |
(16) |
Или
. |
(17) |
Тогда момент сил трения в сопряжениях рулевого привода равен:
. |
(18) |
Поэтому для рассматриваемого случая поворота рулевой сошки на величину смещений в РП, работа сил трения может быть определена:
, |
(19) |
что представляет удобство для экспериментальных исследований, в условиях которых коэффициент Ка
равен критерию качества РП.
2. Расчёт пути трения и скорости относительного скольжения элементов шарниров рулевых тяг
В настоящее время проблема надежности узлов и систем автомобиля очень актуальна. Надежность рулевого привода является одной из составляющих надежности автомобиля в целом.
Шарнирные соединения рулевых тяг автомобилей являются основным элементами, регламентирующими надёжность рулевого привода [2]. Рабочие процессы в них характеризуются значительным количеством циклов относительного скольжения элементов шарнира. При этом особую важность приобретает фактор, учитывающий переход трения покоя в трение скольжения, когда преодолеваются "точки покоя". Последнее обстоятельство является причиной увеличения интенсивности изнашивания шарнира, несмотря на некоторое её ослабление из-за нестационарности процесса нагружения рулевого привода.
Для автомобилей с независимой передней подвеской нагружение рулевых шарниров определяется тремя факторами: рулевыми воздействиями водителя, колебаниями колёс относительно оси поворотной стойки и колебаниями подвески. При этом скорость движения способствует увеличению интенсивности возбуждений и при возрастании становится фактором, определяющим частоту и амплитуду колебаний колёс.
Из практики технической эксплуатации автомобилей известно, что наибольший износ имеют шарнирные соединения рычагов поворотных цапф и боковых рулевых тяг (крайние рулевые шарниры). Основная причина в том, что эти шарниры соединяют без упругих элементов неподрессоренную массу колёсного узла передней подвески и подрессоренную массу кузова. Это определяет интенсивные динамические нагрузки на элементы шарнира, частично воспринимаемые его пружиной.
Анализируя пространственное скольжение элементов рулевых шарниров, следует отметить, что характеристикой рабочих процессов являются путь трения и скорость относительного скольжения. Используя методику Фоллерта Людера для шарниров автомобилей МАЗ, и рассмотрев дополнительно процесс относительного перемещения элементов шарнира от колебаний подвески для исследуемых моделей, определим суммарный путь трения, отнесённый к площади трения с диаметром, равным диаметру шарового пальца, на 1000 км пробега для автомобилей ВАЗ.
Путь трения в случае имитации процесса основных угловых перемещений управляемых колёс случайной последовательностью, имеющей место от рулевых воздействий водителя, может быть определён:
, |
(20) |
где - среднестатистический угол поворота шарового пальца, град;
d -
диаметр шарового пальца, мм.
Путь трения в случае имитации процесса основных угловых перемещений управляемых колёс гармоническим процессом, имеющем место при колебаниях управляемых колёс относительно оси поворотной стойки и при колебаниях передней подвески, может быть определён :
, |
(21) |
где n
- число колебаний на 1 км пути;
- угол размаха, град.
Так, относительная величина пути трения при движении на булыжном шоссе со скоростью 8,4 м/с определена следующим образом:
а) от рулевых воздействий водителя:
;
б) от колебаний колес относительно оси поворотной стоки:
;
в) от колебаний передней подвески:
.
Результаты расчёта сведены в таблице 1. Исходные данные взяты из работы Гольда Б.В. [3], получены экспериментально.
Характеристикой рабочих процессов в рулевом шарнире является также, скорость относительного скольжения его элементов. Известно [6], что главными механизмами нарушения работоспособности рулевых шарниров являются окислительное, абразивное изнашивание и усталостное выкрашивание поверхностей трения. Кинематической характеристикой этих механизмов является средняя скорость скольжения шарового пальца в наконечнике рулевой тяги:
. |
(22) |
Таблица 1 Результаты расчёта относительных величин пути трения и скорости скольжения элементов шарниров рулевых тяг автомобилей ВАЗ-2105
Характер нагружения рулевых шарниров |
Скорость движения, м/с |
Тип дорожного покрытия |
Исходные данные для расчета |
Относительная величина пути трения, м/1000 km |
Относительная скорость скольжения, мм/с |
Рулевое
воздействие водителя
|
8,4 |
асфальтобетон |
nk
=18,4,8
=8°20
|
13,26 |
1,45 |
(30) |
булыжное шоссе |
nk
=18,11,5
=8°20
|
31,77 |
3,46 |
16,8 |
асфальтобетон |
nk
=5,4,8
=2°20
|
0,92 |
0,12 |
(60) |
булыжное шоссе |
nk
=5,11,5
=2°20
|
2,21 |
0,29 |
Колебания колёс
вокруг оси поворотной стойки
|
8,4 |
асфальтобетон |
fk
=4, 1/c
=0,1°
|
36,84 |
57,84 |
(30) |
булыжное шоссе |
fk
=12, 1/c
=0,1°
|
110,52 |
173,52 |
16,8 |
асфальтобетон |
fk
= 2,5 1/c
=0,15°
|
17,23 |
27,11 |
(60) |
булыжное шоссе |
fk
=8, 1/c
=0,15°
|
55,14 |
86,76 |
Колебания передней подвески |
8,4 |
асфальтобетон |
fk
=3, 1/c
= 2,8°
|
386,04 |
1214,64 |
(30) |
булыжное шоссе |
fk
=8, 1/c
= 2,8°
|
1031,59 |
3239,03 |
16,8 |
асфальтобетон |
fk
= 1,6 1/c
fk
=3, 1/c
= 2,8° = 3,6°
|
102,95 |
416,45 |
(60) |
булыжное
шоссе
|
fk
=3,5 1/c
= 3,6°
|
225,20 |
910,98 |
Максимальная скорость относительного перемещения трущихся деталей зависит от параметров и кинематики рулевого привода и может быть определена по рекомендации Фоллерта Людера:
, |
(23) |
где - угловая скорость вращения шарового пальца;
- максимальная амплитуда отклонения.
Результаты расчёта относительной скорости скольжения шарового пальца в наконечнике для рассматриваемых условий приведены в таблице 1.
В этих условиях особую важность приобретает оптимальная жёсткость осевой пружины рулевого шарнира, которая должна превышать инерционные усилия, возникающие от массы рулевых тяг при движении с колебаниями.
3. Исследование зависимости изменения схождения управляемых колёс от упругости, зазоров в сопряжениях и усилия в рулевом приводе
Изменение схождения управляемых колёс происходит под действием среднеэксплуатационных нагрузок с интенсивностью, которая зависит от его первоначальной величины. Оно вызвано смещениями в кинематической цепи рулевого привода, которые формируются за счёт упругости деталей и подвижных сопряжении РП с одной стороны и зазорами, вызванными износом и деформацией элементов подвижных сопряжении, а также ослаблением креплений и потерей прочности деталей РП с другой. Изменение величины первоначального схождения колёс проявляется взаимными относительными смещениями звеньев кинематической цепи рулевого привода, которые могут быть приведены к приращению расстояния между дисками управляемых колёс. Процесс формирования смещений в РП рассмотрим в виде схемы, где изображена плоская модель рулевого привода автомобилей рассматриваемого класса. Исследуем вначале этот процесс при допущении, что в рулевом приводе действует усилие 30 даН, достаточное для выбора зазоров и начала деформации РП. При этом, изменение схождения происходит только под действием упругости и зазоров, остальные факторы можно считать постоянными. Тогда, согласно обозначениям (рис. 3) схождение, измеренное как разность расстояний между заокраинами дисков управляемых колёс впереди и сзади передней оси на высоте центров колёс, равно:
 |
(24) |
Угол схождение управляемых колес можно выразить:
 |
(25) |
где Срп
-
суммарная упругость элементов рулевого привода, мм/даН; D
рп
-
суммарная величина зазоров в сопряжениях РП, приходящаяся на единицу приложенного усилия при замере, мм/даН. - коэффициент приведения к высоте центров колёс, учитывающий измерение смещений на высоте РП. ВАЗ, АЗЛК - =1,25, ГАЗ- = 1,30; -
коэффициент пропорциональности между величинами схождения, измеренными по разности расстояний и углу поворота управляемых колёс.
ВАЗ (АЗЛК) - = I4·I0-4
рад = 0,08° = 4,8 мин; ГАЗ - =
13,2 I0-4
рад = 0,075° == 4,5 мин.
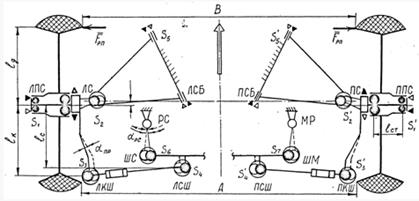

Рис. 3 Схема формирования смещений в кинематической цепи рулевого привода автомобилей с независимой передней подвеской с обозначением подвижных сопряжении и зазоров в них.
Коэффициент показывает, что смещение в РП на I мм соответствует углу поворота одного управляемого колеса для моделей ВАЗ на 9,6 мин (0,16°) при условии, что второе колесо неподвижно. Величины обоих коэффициентов зависят от углов установки управляемых колёс, конструктивных особенностей рулевого привода и передней подвески, шин и давления воздуха в них.
В дальнейшем исследовании будет использована величина схождения, измеренная по разности расстояний между дисками колёс на высоте рулевого привода (представляет удобство для экспериментальных исследований), т.к. она изменяется на двойную величину смещений в РП:
Знак и величина второго слагаемого зависимостей (24) - (27) определяется величиной и направлением усилия в рулевом приводе, которое вызвано действием моментов на управляемых колёсах и может быть приведено к усилию, приложенному к дискам управляемых колёс в месте измерения величины схождения (рис.3). Подвижные сопряжения рулевого привода находятся на разном расстоянии от заокраин дисков управляемых колёс, между которыми измеряется схождение, поэтому смещения в них должны быть приведены к радиусу диска колеса. Методика приведения и ранжирование коэффициентов изложена автором
 |
(29) |
где, согласно обозначениям на схеме рулевого привода (рис. ):
 |
Процесс изменения схождения управляемых колёс по зависимости (29) моделировался на ЭВМ "НАИРИ-2" путём перебора задаваемых значений упругости и зазоров в отдельных сопряжениях РП, допустимые величины которых взяты из инструктивных материалов автомобильных заводов, а также работ и приведены в таблице 2. Моделирование показало, что суммарное действие допустимых величин перечисленных параметров при усилии в РП до 50 даН может вызвать смещение в кинематической цепи рулевого привода до 10,68 мм, т.е. изменить схождение на величину, в 3-5 раз большую начального значения, и вызвать поворот управляемых колёс до 150·10-4
рад (0,85°) каждое. Однако линейный характер зависимости (29) вносит существенную погрешность в оценку влияния зазоров в сопряжениях, упругости и усилия в РП на изменение схождения и поворот управляемого колеса. Поэтому, на основании анализа физической сущности процесса формирования смещений в РП и результатов экспериментальных исследований достаточно представительной выборки (105 автомобилей) путём совместного моделирования процесса изменения схождения и его влияние на изменение эксплуатационных свойств автомобилей было подобрано аппроксимированное выражение зависимости изменения схождения, т.е. смещений в РП от перечисленных факторов с допустимой погрешностью.
Таблица 2 Исходные данные для моделирования величины изменения схождения
№ п/п |
Наименованиепараметра |
Обозна-чение |
Среднее значение |
Интервал варирования |
Шаг варирования |
I. |
Зазоры в подшипниках ступиц передних колёс |
S1
|
0,05 , мм |
0 - 0,1 |
0,025 |
2. |
Зазоры в шарнирах поворотной стойки |
S2
|
0,25 , мм |
0 – 0,5 |
0,05 |
Зазоры в крайних рулевых шарнирах |
S3
|
0,15 , мм |
0 – 0,3 |
0,05 |
4. |
Зазоры в средних рулевых шарнирах |
S4
|
0,10 , мм |
0 - 0,3 |
0,05 |
5. |
Зазоры в шарнирах рулевой сошки и
маятникового рычага
|
S6
, S7
|
0,15 , мм |
0 - 0,3 |
0,05 |
6. |
Упругость рулевойсошки |
Сpc
|
0,0085  |
0,005-0,010 |
0,0005 |
7. |
Упругость средней-рулевой тяги |
Сcт
|
0,0042  |
0,002-0,006 |
0,0005 |
8. |
Упругость поворотных рычагов цапфы |
Спp
|
0,0083  |
0,005-0,010 |
0,0005 |
9. |
Упругость боковыхрулевых тяг |
Сбт
|
0,0047  |
0,002-0,006 |
0,0005 |
 |
(30) |
 |
(31) |
При этом принято допущение, что усилие в РП сжимает рулевую трапецию, т.е. уменьшает начальное схождение (имеет место в большинстве режимов движения). Разделение диапазона усилий в РП до и более 30 даН вызвано наличием двух экстремумов этой зависимости с учётом результатов дорожных и стендовых испытаний автомобиля ВАЗ. Однако при моделировании достигнуто удовлетворительное совмещение этих зависимостей, позволяющее описать процесс в диапазоне усилий до 150 даН.
В результате моделирования процесса изменения схождения управляемых колёс по зависимостям (30, 31) получены номограммы (рис.4) зависимостей изменения схождения от усилия в рулевом приводе, упругости и уровня его технического состояния, удобные для практического применения при регулировке и оптимизации характеристик и состояния РП и ПМ.
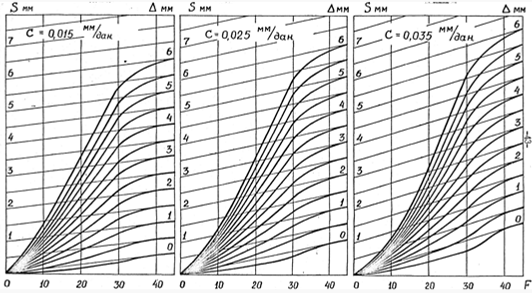
4. Силовой способ оценки характеристик и состояния рулевого привода
ГОСТ 25478-82 указывает на необходимость введения инструментальных методов контроля рулевого привода и его шарнирных сочленений. Однако, кроме суммарного люфта рулевого колеса, общепризнанный критерий оценки эксплуатационного состояния рулевого привода отсутствует.
Существующие способы испытания рулевого управления автомобилей заключаются в приложении усилия к поворотным площадкам или непосредственно к шине. При этом величина измеряемого параметра (суммарного люфта) выражается косвенно, путём измерения углов поворота площадок (или боковых сил). Существующие методы оценки эксплуатационного состояния РП не обладают требуемой достоверностью из-за невозможности раздельного определения величин упругости и зазоров в подвижных сопряжениях, которые оказывают не однозначное влияние на эксплуатационные свойства автомобилей.
В этой связи для решения задач диссертационной работы разработан силовой способ испытания рулевых механизмов автомобилей, заключающийся в установке управляемых колёс на поворотные площадки и приложении усилия, нагружающего рулевой привод, и измерении возникающей деформации.
При этом, с целью повышения достоверности результатов испытания, усилия прикладывают непосредственно к дискам колёс, одинаковые по величине и противоположно направленные, измеряют приращение расстояния между дисками колёс и по величине и характеру изменения отношения этого приращения к нагружающему усилию производят оценку эксплуатационного состояния рулевого привода.
Под эксплуатационным состоянием РП понимается совокупность характеристик - упругость, момент сил трения, кинематика РП и технического состояния - величина износов и деформаций сопряжений, ослабление креплений и изменение прочностных свойств деталей, дефекты сборки. Предложенный параметр назван критерием качества РП - S
F
и является интегральным (комплексным) показателем характеристик и состояния рулевого привода автомобилей.
Способ испытания рулевого привода автомобилей осуществляется следующим образом. Автомобиль устанавливается управляемыми колёсами на поворотные площадки, задние колёса фиксируются колодками. Затем между дисками управляемых колёс впереди передней оси в горизонтальной плоскости на высоте рулевого привода устанавливается пневмоцилиндр, создающий одинаковые по величине, противоположно направленные усилия.
В ресивере создаётся постоянное давление в 0,5 МПа, откуда с помощью редуктора в пневмоцилиндр плавно подаётся воздух, обеспечивая равномерное приращение величины усилия. Одновременно и непрерывно с созданием усилий между внутренними сторонами дисков управляемых колёс измеряется приращение расстояния между ними. Оценка эксплуатационного состояния РП производится по величине и характеру изменения отношения приращения расстояния между дисками к приращению усилия между ними при установке управляемых колёс в ряд угловых положений в обе стороны
Таким образом, реализация силового способа позволяет повысить достоверность и точность оценки эксплуатационного состояния рулевого привода, исключив влияние дисперсии упругих свойств шин и деформации деталей РУ не связанных с РП [140]. Это позволяет добиться стабильности результатов измерения и осуществить комплексное исследование влияния характеристик и состояния рулевого привода на эксплуатационные свойства автомобилей. Экспериментальное оборудование позволило получить непрерывную графическую запись зависимости изменения критерия качества РП, пример которой для автомобиля с аварийным техническим состоянием РП приведен на рисунке 5. Здесь показана тарировочная характеристика устройства - 1, зависимости изменения смещений в РП от величины прикладываемого усилия на прямом - 2 и обратном - 3 ходе штока силового пневмоцилиндра. Заштрихованные площади могут быть пересчитаны в работу упругих деформаций и зазоров в сочленениях РП.
На рисунке 6 показана зависимость изменения смещении в кинематической цепи РП от усилия в нём, пересчитанная с учётом масштабных коэффициентов и тарировочной характеристики в декартову систему координат с непосредственной графической зависимости, полученной автомобиля, эксплуатационное состояние которого соответствовало нормативным требованиям (пробег 2тыс.км), на который были установлены крайние рулевые шарниры с зазорами 0,170-0,175 мм.
Из рисунка 6 следует возможность раздельного определения зазоров и деформаций в подвижных спряжениях РП. Так, люфту соответствует наибольшее и скачкообразное смещение на единицу создаваемого усилия, что характеризуется углом наклона зависимости - при усилии 16-18 даН.
Упругая деформация элементов подвижных сопряжении (не деталей, для деформации которых необходимо гораздо большее усилие) характеризуется плавным и стабильным смещением на единицу силы и меньшим углом - . Преодоление вязкого трения характеризуется наименьшим углом - (рис.6).
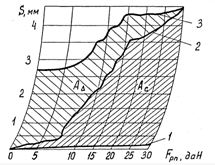
Рис.5. Графическая зависимость изменения критерия качества РП, полученная экспериментально: I - тарировочная характеристика устройства, 2 и 3 - зависимости на прямом и обратном ходе
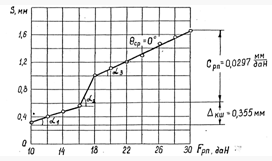
Рис. 6. Зависимость изменения критерия качества РП, пересчитанная в декартову систему координат для модели "Москвич – 2140"
Кинематика рулевого привода оценивается в условиях силового нагружения по соотношению углов поворота управляемых колёс при установке их в заданное угловое положение в обе стороны на один и тот же угол путём сравнения приращения расстояний между ними с расстоянием между дисками управляемых колёс в положении прямолинейного движения.
Поворот управляемых колёс осуществляется как рулевым колесом, так и приложением усилий к управляемым колёсам, причём в определённых режимах испытания это позволит увеличить объём информации, т.к. подвижные сопряжения реагируют на усилие поочерёдно, в соответствии с коэффициентами приведения смещений к радиусу диска колеса [4]. При правильной кинематике РП гистограмма (рис.7) будет симметричной.
Характер износа, т.е. геометрию износа подвижных сопряжений можно оценить по величине приращения расстояния между 'дисками (а не по абсолютной величине расстояния) после создания усилия между ними также при установке колёс в ряд угловых положений. Так, из диаграммы (рис.8) следует неравномерность износа подвижных сопряжении и эксплуатация автомобиля с уводом вправо от заданной траектории движения.
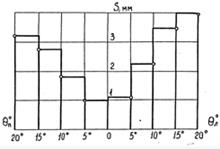
Рис.7. Гистограмма абсолютных величин смещений в кинематической цепи рулевого привода, полученных при установке управляемых колёс в ряд фиксированных положений в обе стороны
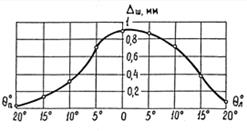
Рис. 8. Диаграмма величин зазоров (люфт) в шарнирных сопряжениях рулевой трапеции, полученная при установке управляемых колёс в ряд фиксированных положений в обе стороны
5. Теоретическое обоснование критериев оценки эксплуатационного состояния рулевого привода и шарниров рулевых тяг
5.1 Обоснование критерия качества рулевого привода
Критерий качества РП - SF
является интегральным (комплексным) параметром оценки упругости, момента сил трения, кинематики и уровня технического состояния рулевого привода. Его величина за отдельный промежуток времени равна отношению приращения расстояния между дисками управляемых колёс к величине приращения плавно нарастающего усилия, создаваемого между ними. Критерий качества РП отвечает требованиям, предъявляемым к диагностическому параметру, т.е. обладает чувствительностью, стабильностью, однозначностью, высокой информативностью, доступностью и низкой трудоёмкостью измерения. Он позволяет оценить качество и оптимизировать параметры рулевого привода и углов установки колёс на всех стадиях проектирования, производства и эксплуатации автомобилей.
Критерий качества РП может быть представлен пределом отношения приращения смещения в рулевом приводе, т.е. изменения схождения управляемых колёс, к величине приращения усилия в нём, при стремлении последнего к нулю, т.е. производной от функции :
. |
(32) |
Производную (32) следует рассматривать как частную производную функции ряда переменных ,
одной из переменных - усилию в рулевом приводе автомобиля:
. |
(33) |
Усилие в рулевом приводе, являющееся основной характеристикой рабочих процессов, в момент измерения критерия качества РП можно считать единственной переменной величиной, рассматривая остальные факторы постоянными, в пределах допустимой погрешности.
Выражая производную (32) через дифференциалы переменных и учитывая, что критерий качества РП является производной сложной функции, т.е. равен произведению производных по времени от функции и аргумента, получим:
. |
(34) |
Таким образом, полный дифференциал функции
имеет вид:
. |
(35) |
Если задать функцию в параметрическом виде, то имеем:
 . |
(36) |
Причём, первую функцию (36) можно определить, задавая плавным приращением усилие в рулевом приводе в процессе испытания, однако исключить промежуточный параметр t
аналитически невозможно, т.к. на смещение влияет ещё и ряд других факторов.
Учитывая цель, поставленную в работе, а также то, что рабочие процессы рулевого привода характеризуются в первую очередь смещениями в его кинематической цепи, происходящими только под действием усилий, и удобство экспериментального получения графической записи этой зависимости, обратимся к геометрическому смыслу производной. Тогда критерий качества РП может быть представлен тангенсом угла между касательной к кривой функции в данной её точке (т.е. для данного дискретного значения силы в рулевом приводе) и осью ОF
:
. |
(37) |
Причём, при построении графической зависимости смещения от усилия в РП в декартовой системе координат необходимо соблюдение равных (пропорциональных) масштабов осей для сравниваемых случаев.
Геометрическая интерпретация критерия качества РП следует из рисунков 5 и 6.
Критерий качества обладает разрешающей способностью для раздельного определения величин смещения, вызванных действием различных факторов, при обеспечении заданной погрешности измерения. Разработанная методика измерения позволяет оценить характеристики и состояние отдельных групп подвижных сопряжений, т.е. поэлементную оценку эксплуатационного состояния сопряжении рулевого привода, т.к. последние реагируют на усилие между дисками колёс не одновременно, а в соответствии с коэффициентами приведения смещений согласно принципу "виртуальных перемещений" аналитической механики.
При этом, поворот рулевого колеса на угол 35-40° ориентирует относительное расположение элементов подвижных сопряжении определённым образом, что следует из рисунка Так, уравнение (29) составлено для случая, когда после предварительной деформации рулевого привода (создания равного по величине, но приложенного сзади передней оси усилия) усилие прикладывается впереди передней оси к дискам.
Однако, после поворота рулевого колеса на указанный угол сопряжения рулевого привода деформированы усилием со стороны рулевой сошки. После поворота рулевого колеса, усилие, приложенное также между дисками управляемых колёс впереди передней оси, выбирает зазоры в определённых группах подвижных сопряжении РП (рис. 3). В этом случае, зависимость изменения схождения на величину смещений (29) приобретает вид, соответственно для поворота рулевого колеса:
влево  |
(38.1) |
вправо  |
(38.2) |
Равенство этих смещений является критерием правильности кинематики рулевого привода и оказывает положительное влияние на эксплуатационные свойства в режимах криволинейного движения.
В дальнейшем исследовании будет использована средняя величина смещений в кинематической цепи РП в случае неустановившегося движения по криволинейной траектории:
. |
(39) |
5.2 Обоснование критериев оценки эксплуатационного состояния шарниров рулевых тяг с осевой пружиной
Кинематическая цепь рулевого привода включает на менее четырёх шарнирных соединений, которые предназначены для подвижного соединения рулевых тяг при условии их перемещения в пространстве по сложным траекториям. В настоящее время имеется более 20 конструктивных вариантов и типоразмеров шаровых шарниров рулевых тяг отечественных автомобилей с нагрузкой на ось до 10 тонн [3, 4].
Рулевые шарниры рассматриваемых моделей легковых автомобилей различны по конструкции. Так, шаровый палец шарнира "ГАЗ-24" сопрягается с металлическим вкладышем, запрессованным в наконечник, а площадь контакта - наименьшая из всех конструкций; рулевой шарнир АЗЛК имеет два вкладыша, а ВАЗ - один, разрезной, причём поверхность контакта с шаровым пальцем наибольшая из всех конструкций.
Кроме того, шарниры рулевого привода одной модели также могут иметь конструктивные отличия. Так, шаровый палец маятникового рычага модели 2140 имеет не сферическую, а овальную форму и между вкладышами установлена дополнительная пластмассовая втулка для предотвращения проворачивания средней рулевой тяги вокруг её продольной оси.
Согласно классификации Лысова М.И. [6], рулевые шарниры легковых автомобилей имеют простую кинематику, т.е. перемещения шарового пальца относительно головки шарнира происходят за счёт скольжения его сферической поверхности относительно поверхности вкладышей во всех направлениях. Все они имеют одинаковый способ устранения зазоров, возникающих при износе - автоматические, с пружиной осевого действия.
При анализе рабочих процессов в рулевых шарнирах определялись удельные давления из условия нагружения рулевого привода усилием 30 даН и отсутствии зазоров в них, которые составили, соответственно: ГАЗ-24 - 0,476 МПа, АЗЛК – 0,264 МПа и ВАЗ - 0,186 МПа, что позволило обосновать диапазоны усилий при оценке эксплуатационного состояния.
Из анализа конструкций шарнирных соединений рулевых тяг следует, что их эксплуатационное состояние характеризуется критериями:
- F
пр
- осевое усилие при перемещении шарового пальца и преодолении усилия сжатия пружины шарнира и сопротивления перемещению вкладыша в наконечнике тяги (корпусе);
- M
шп
- момент сопротивления шарового пальца повороту;
- Км
-
коэффициент стабильности момента сопротивления шарового пальца повороту при его установке в ряд угловых положений;
- S
а
-
обратимое и необратимое относительное смещение шарового пальца в осевом направлении;
- S
r
-
обратимое и необратимое относительное смещение шарового пальца в радиальном направлении.
Кроме момента сопротивления повороту и коэффициента его стабильности остальные критерии эксплуатационного состояния рулевых шарниров доступны для измерения непосредственно на автомобиле.
Осевое усилие перемещения шарового пальца и момент сопротивления его повороту характеризуют конструктивные факторы, определяющие эксплуатационное состояние рулевых шарниров. Относительные смещения элементов шарнира в осевом и радиальном направлении характеризуют эксплуатационные факторы и техническое состояние рулевого шарнира.
Из практики технической эксплуатации автомобилей [2, 6] известно, что отказ рулевых шарниров наступает в большинстве случаев из-за потери жёсткости пружины шарнира. После чего наблюдается резкое нарастание интенсивности износа сопряжения. Поэтому, величину момента сопротивления повороту и осевое усилие пружины следует считать основными критериями эксплуатационного состояния шарниров.
Таким образом, рассмотренные критерии оценки эксплуатационного состояния рулевого привода и его элементов отражают рабочие процессы в них и позволяют выполнить комплексное исследование влияния характеристик и состояния рулевого привода на эксплуатационные свойства.
шарнир рулевой привод трение скольжение
Библиографический список
1. Власов B.M. Организация технического контроля и диагностики в региональных автотранспортных системах. - Автомобильный и городской транспорт. (Итоги науки и техники. ВИНИТИ). - М.: 2006. - №11. - С. 1-66.
2. Волошин Г.Я. Анализ дорожно-транспортных происшествий / Г.Я. Волошин, В. П. Мартынов, А. Г. Романов. – М.: Транспорт, 2007. – 240 с.
3. Герами В.Д. Концепция формирования системы городского пассажирского общественного транспорта / В.Д. Герами // Автотранспортное предприятие. – 2008. - №5. - С. 8.
4. Говорущенко Н.Я. Диагностика технического состояния автомобилей / Н.Я. Говорущенко. - М.: Транспорт, 2010. – С. 54.
5. Гольд Б.В. Прочность и долговечность автомобиля / Б.В. Гольд. - М.: Машиностроение, 2008. – С. -328.
6. Денисов А.С. Основы формирования эксплуатационно-ремонтного цикла автомобилей / А.С. Денисов. – Саратов: Сарат. гос. техн. ун-т, 2009. – 352 с.
7. Дмитриев С.Н. Дорожно-патрульная служба: Пособие для сотрудников ГИБДД / С.Н. Дмитриев. – М.: Спарк, 2010. – 656 с.
8. Иванов В.Н. Пассивная безопасность автомобиля / В.Н. Иванов, В.А. Лялин. – М.: Транспорт, 2009. – 304 с., ил., табл.
9. Иларионов В.А. Стабилизация управляемых колес автомобиля / В.А. Иларионов. – М.: Транспорт, 2006. – 167 с.
10. Келдыш М.В. Шимми переднего колеса трехколесного шасси. - М: Бюро новой техники НКАП, 2008. – С. 1-32.
11. Клинковштейн Г.И. Организация работы службы безопасности движения на автомобильном транспорте: Учеб. пособие / Г.И. Клинковштейн, М.А. Луковецкий. – М.: МАДИ, 2010. – 73 с.
|