Основные методы умягчения воды
Содержание
Теоретические основы умягчения воды, классификация методов
Термический метод умягчения воды
Реагентные методы умягчения воды
Технологические схемы и конструктивные элементы установок реагентного умягчения воды
Термохимический метод умягчения воды
Умягчение воды диализом
Магнитная обработка воды
Литература
Теоретические основы умягчения воды, классификация методов
Под умягчением воды подразумевается процесс удаления из нее катионов жесткости, т.е. кальция и магния.
В соответствии с ГОСТ 2874-82 "Вода питьевая" жесткость воды не должна превышать 7 мг-экв/л. Отдельные виды производств к технологической воде предъявляют требования глубокого ее умягчения, т.е. до 0,05.0,01 мг-экв/л. Обычно используемые водоисточники имеют жесткость, отвечающую нормам хозяйственно-питьевых вод, и в умягчении не нуждаются. Умягчение воды производят в основном при ее подготовке для технических целей. Так, жесткость воды для питания барабанных котлов не должна превышать 0,005 мг-экв/л. Умягчение воды осуществляют методами: термическим, основанным на нагревании воды, ее дистилляции или вымораживании; реагентными, при которых находящиеся в воде ионы
Ca
(
II
) и
Mg
(
II
) связывают различными реагентами в практически нерастворимые соединения; ионного обмена, основанного на фильтровании умягчаемой воды через специальные материалы, обменивающие входящие в их состав ионы
Na
(
I) или Н (1) на ионы Са (II) и
Mg
(
II
), содержащиеся в воде диализа; комбинированным, представляющим собой различные сочетания перечисленных методов.
Выбор метода умягчения воды определяется ее качеством, необходимой глубиной умягчения и технико-экономическими соображениями. В соответствии с рекомендациями СНиПа при умягчении подземных вод следует применять ионообменные методы; при умягчении поверхностных вод, когда одновременно требуется и осветление воды, - известковый или известково-содовый метод, а при глубоком умягчении воды - последующее катионирование.
Основные характеристики и условия применения методов умягчения воды приведены в табл. 20.1.
умягчение вода диализ термический
Для получения воды для хозяйственно-питьевых нужд обычно умягчают лишь ее некоторую часть с последующим смешением с исходной водой, при этом количество умягчаемой воды Qy
определяют по формуле
(20.1)
где Жо. и
. - общая жесткость исходной воды, мг-экв/л; Ж0. с
. - общая жесткость воды, поступающей в сеть, мг-экв/л; Ж0.
у. -
жесткость умягченной воды, мг-экв/л.
Методы умягчення воды
Показатель |
термический |
реагентный |
ионообменный |
диализа |
Характеристика процесса |
Воду нагревают до температуры выше 100°С, при этом удаляется карбонатная и некарбонатная жесткости (в виде карбоната кальция, гидрокси-. да магния и гипса) |
В воду добавляют известь, устраняющую карбонатную и магниевую жесткость, а также соду, устраняющую некарбонат - иую жесткость |
Умягчаемая вода пропускается через катионито - вые фильтры |
Исходная вода фильтруется через полупроницаемую мембрану |
Назначение метода |
Устранение карбонатной жесткости из воды, употребляемой для питания котлов низкого н среднего давления |
Неглубокое умягчение при одновременном осветлении воды от взвешенных веществ |
Глубокое умягчение воды, содержащей незначительное количество взвешенных веществ |
Глубокое умягчение воды |
Расход воды на собственные нужды |
- |
Не более 10% |
До 30% и более пропорционально жесткости исходной воды |
10 |
Условия эффективного применения: мутность исходной воды, мг/л |
До 50 |
До 500 |
Не более 8 |
До 2,0 |
Жесткость воды, мг-экв/л |
Карбонатная жесткость с преобладанием Са (НС03) 2, некарбонатная жесткость в виде гипса |
5.30 |
Не выше 15 |
До 10,0 |
Остаточная жесткость воды, мг-экв/л |
Карбонатная жесткость до 0,035, CaS04 до 0,70 |
До 0,70 |
0,03.0,05 прн одноступенчатом и до 0,01 при двухступенчатом ка - тионировании |
0,01 и ниже |
Температура воды,°С |
До 270 |
До 90 |
До 30 (глауконит), до 60 (сульфоугли) |
До 60 |
Термический метод умягчения воды целесообразно применять при использовании карбонатных вод, идущих на питание котлов низкого давления, а также в сочетании с реагентными методами умягчения воды. Он основан на смещении углекислотного равновесия при ее нагревании в сторону образования карбоната кальция, что описывается реакцией
Са (НС03
) 2
- > СаСО3
+ С02
+ Н2
0.
Равновесие смещается за счет понижения растворимости оксида углерода (IV), вызываемого повышением температуры и давления. Кипячением можно полностью удалить оксид углерода (IV) и тем самым значительно снизить карбонатную кальциевую жесткость. Однако, полностью устранить указанную жесткость не удается, поскольку карбонат кальция хотя и незначительно (13 мг/л при температуре 18°С), но все же растворим в воде.
При наличии в воде гидрокарбоната магния процесс его осаждения происходит следующим образом: вначале образуется сравнительно хорошо растворимый (110 мг/л при температуре 18° С) карбонат магния
Mg (НСО3
) → MgC03
+ С02
+ Н2
0,
который при продолжительном кипячении гидролизуется, в результате чего выпадает осадок малорастворимого (8,4 мг/л). гидроксида магния
MgC03
+H2
0 → Mg (0H) 2
+C02
.
Следовательно, при кипячении воды жесткость, обусловливаемая гидрокарбонатами кальция и магния, снижается. При кипячении воды снижается также жесткость, определяемая сульфатом кальция, растворимость которого падает до 0,65 г/л.
На рис. 1 показан термоумягчитель конструкции Копьева, отличающийся относительной простотой устройства и надежностью работы. Предварительно подогретая в аппарате обрабатываемая вода поступает через эжектор на розетку пленочного подогревателя и разбрызгивается над вертикально размещенными трубами, и по ним стекает вниз навстречу горячему пару. Затем совместно с продувочной водой от котлов она по центрально подающей трубе через дырчатое днище поступает в осветлитель со взвешенным осадком.
Выделяющиеся при этом из воды углекислота и кислород вместе с избытком пара сбрасываются в атмосферу. Образующиеся в процессе нагревания воды соли кальция и магния задерживаются во взвешенном слое. Пройдя через взвешенный слой, умягченная вода поступает в сборник и отводится за пределы аппарата.
Время пребывания воды в термоумягчителе составляет 30.45 мин, скорость ее восходящего движения во взвешенном слое 7.10 м/ч, а в отверстиях ложного дна 0,1.0,25 м/с.
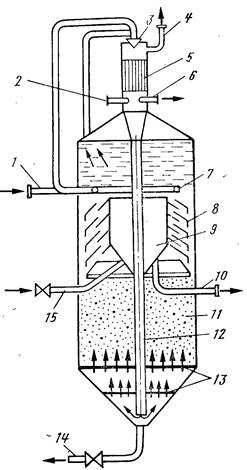
Рис. 1. Термоумягчитель конструкции Копьева.
15
- сброс дренажной воды; 12
- центральная подающая труба; 13
- ложные перфорированные днища; 11 - взвешенный слой; 14
- сброс шлама; 9 -
сборник умягченной воды; 1, 10
- подача исходной и отвод умягченной воды; 2
- продувка котлов; 3 - эжектор; 4
- выпар; 5 -
пленочный подогреватель; 6 - сброс пара; 7
- кольцевой перфорированный трубопровод отвода воды к эжектору; 8 - наклонные сепарирующие перегородки
Умягчение воды реагентными методами основано на обработке ее реагентами, образующими с кальцием и магнием малорастворимые соединения: Mg (OH) 2
, СаС03
, Са3
(Р04
) 2
, Mg3
(P04
) 2
и другие с последующим их отделением в осветлителях, тонкослойных отстойниках и осветлительных фильтрах. В качестве реагентов используют известь, кальцинированную соду, гидроксиды натрия и бария и другие вещества.
Умягчение воды известкованием
применяют при ее высокой карбонатной и низкой некарботаной жесткости, а также в случае, когда не требуется удалять из воды соли некарбонатной жесткости. В качестве реагента используют известь, которую вводят в виде раствора или суспензии (молока) в предварительно подогретую обрабатываемую воду. Растворяясь, известь обогащает воду ионами ОН - и Са2+
, что приводит к связыванию растворенного в воде свободного оксида углерода (IV) с образованием карбонатных ионов и переходу гидрокарбонатных ионов в карбонатные:
С02
+ 20Н -
→ СО3
+ Н2
0,НСО3
-
+ ОН -
→ СО3
-
+ Н2
О.
Повышение в обрабатываемой воде концентрации ионов С03
2 -
и присутствие в ней ионов Са2+
с учетом введенных с известью приводит к повышению произведения растворимости и осаждению малорастворимого карбоната кальция:
Са2+
+ С03
-
→ СаС03
.
При избытке извести в осадок выпадает и гидроксид магния
Mg2+
+ 20Н -
→ Mg (ОН) 2
Для ускорения удаления дисперсных и коллоидных примесей и снижения щелочности воды одновременно с известкованием применяют коагуляцию этих примесей сульфатом железа (II) т.е. FeS04
*7 Н2
0. Остаточная жесткость умягченной воды при декарбонизации может быть получена на 0,4.0,8 мг-экв/л больше некарбонатной жесткости, а щелочность 0,8.1,2 мг-экв/л. Доза извести определяется соотношением концентрации в воде ионов кальция и карбонатной жесткости: а) при соотношении [Са2+
] /20<Жк
,
(20.2б)
б) при соотношении [Са2+
] /20 > Жк
,
(20.3)
где [СО2
] - концентрация в воде свободного оксида углерода (IV), мг/л; [Са2+
] - концентрация ионов кальция, мг/л; Жк
- карбонатная жесткость воды, мг-экв/л; Дк
- доза коагулянта (FeS04
или FeCl3
в пересчете на безводные продукты), мг/л; ек
- эквивалентная масса активного вещества коагулянта, мг/мг-экв (для FeS04
е
к
= 76, для FeCl3
ек
= 54); 0,5 и 0,3 - избыток извести для обеспечения большей полноты реакции, мг-экв/л.
Выражение Дк
/ек
берут со знаком минус, если коагулянт вводится раньше извести, и со знаком плюс, если совместно или после.
При отсутствии экспериментальных данных дозу коагулянта находят из выражения
Дк
= 3 (С) 1/3
, (20.4)
где С - количество взвеси, образующейся при умягчении воды (в пересчете на сухое вещество), мг/л.
В свою очередь, С определяют, используя зависимость

где Ми
- содержание взвешенных веществ в исходной воде, мг/л; m
- содержание СаО в товарной извести, %.
Известково-содовый метод умягчения воды
описывается следующими основными реакциями:
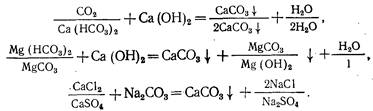
По этому методу остаточная жесткость может быть доведена до 0,5.1, а щелочность с 7 до 0,8.1,2 мг-экв/л.
Дозы извести Ди
и соды Дс
(в пересчете на Na2
C03
), мг/л, определяют по формулам
(20.6)
(20.7)
где [Mg2+
] - содержание в воде магния, мг/л; Жн. к. -
некарбонатная жесткость воды, мг-экв/л.
При известково-содовом методе умягчения воды образующиеся карбонат кальция и гидроксид магния могут пересыщать растворы и долго оставаться в коллоидно-дисперсном состоянии. Их переход в грубодисперсный шлам длителен, особенно при низких температурах и наличии в воде органических примесей, которые действуют как защитные коллоиды. При большом их количестве жесткость воды при реагентном умягчении воды может снижаться всего на 15.20%. В подобных случаях перед умягчением или в процессе его из воды удаляют органические примеси окислителями и коагулянтами. При известково-содовом методе часто процесс проводят в две стадии. Первоначально из воды удаляют органические примеси и значительную часть карбонатной жесткости,
используя соли алюминия или железа с известью, проводя процесс при оптимальных условиях коагуляции. После этого вводят соду и остальную часть извести и доумягчают воду.
При удалении органических примесей одновременно с умягчением воды в качестве коагулянтов применяют только соли железа, поскольку при высоком значении рН воды, необходимом для удаления магниевой жесткости, соли алюминия не образуют сорбционно-активного гидроксида. Дозу коагулянта при отсутствии экспериментальных данных рассчитывают по формуле (20.4). Количество взвеси определяют по формуле
(20.8)
где Жо
- общая жесткость воды, мг-экв/л.
Более глубокое умягчение воды может быть достигнуто ее подогревом, добавлением избытка реагента-осадителя и созданием контакта умягчаемой воды с ранее образовавшимися осадками. При подогреве воды уменьшается растворимость СаСО3
и Mg (OH) 2
и более полно протекают реакции умягчения.
Из графика (рис. 2, а) видно, что остаточная жесткость, близкая к теоретически возможной, может быть получена только при значительном подогреве воды. Значительный эффект умягчения наблюдается при 35.40°С, дальнейший подогрев менее эффективен. Глубокое умягчение ведут при температуре выше 100° С. Большой избыток реагента-осадителя при декарбонизации добавлять не рекомендуется, так как возрастает остаточная жесткость из-за непрореагировавшей извести или при наличии в воде магниевой некарбонатной жесткости вследствие ее перехода в кальциевую жесткость:
MgS04
+ Са (ОН) 2
= Mg (ОН) 2
+ CaS04
Поэтому рекомендуется принимать избыток извести не более 0,5 мг-экв/л. Зависимость остаточной жесткости воды от дозы извести приведена на рис. 2, б.
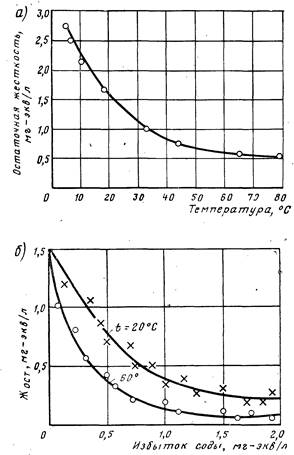
Рис. 2. Влияние температуры (а) и дозы извести (б) на глубину умягчения воды известково-содовым и известковым методом
При известково-содовом методе также не рекомендуется применять большие избытки извести, однако, в данном случае они не вызывают увеличения остаточной жесткости, поскольку снимаются содой
Са (0H) 2
+ Na2
C03
= CaC03
+2NaOH,
но избыток извести приводит к нерациональному перерасходованию соды, повышению стоимости умягчения воды и увеличению гидратной щелочности. Поэтому избыток соды принимают около 1 мг-экв/л. Жесткость воды в результате контакта с ранее выпавшим осадком понижается на 0,3.0,5 мг-экв/л п сравнению с процессом без контакта с осадком.
Контроль процесса умягчения воды следует осуществлять коррекцией рН умягченной воды. Когда это невозможно, его контролируют по значению гидратной щелочности, которую при декарбонизации поддерживают в пределах 0,1.0,2 мг-экв/л, при известково-содовом умягчении - 0,3.0,5 мг-экв/л.
При содово-натриевом методе умягчения воды ее обрабатывают содой и гидроксидом натрия:
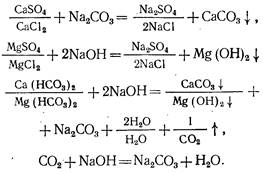
Ввиду того, что сода образуется при реакции гидроксида натрия с гидрокарбонатом, необходимая для добавки в воду доза ее значительно уменьшается. При высокой концентрации гидрокарбонатов в воде и низкой некарбонатной жесткости избыток соды может оставаться в умягченной воде. Поэтому этот метод применяют лишь с учетом соотношения между карбонатной и некарбонатной жесткостью.
Содово-натриевый метод
обычно применяют для умягчения воды, карбонатная жесткость которой немного больше некарбонатной. Если карбонатная жесткость приблизительно равна некарбонатной, соду можно совсем не добавлять, поскольку необходимое ее количество для умягчения такой воды образуется в результате взаимодействия гидрокарбонатов с едким натром. Доза кальцинированной соды увеличивается по мере повышения некарбонатной жесткости воды.
Содорегенеративный метод, основанный на возобновлении соды в процессе умягчения, применяют при подготовке воды, для питания паровых котлов низкого давления
Са (НС03
) 2
+ Na2
C03
= СаС03
+ 2NaHC03
.
Гидрокарбонат натрия, попадая в котел с умягченной водой, разлагается под влиянием высокой температуры
2NаHC03
= Na2
C03
+ Н2
0 + С02
.
Образующаяся при этом сода вместе с избыточной, введенной вначале в водоумягчитель, тут же в котле гидролизует с образованием гидроксида натрия и оксида углерода (IV), который с продувочной водой поступает в водоумягчитель, где используется для удаления из умягчаемой воды гидрокарбонатов кальция и магния. Недостаток этого метода состоит в том, что образование значительного количества СО2
в процессе умягчения вызывает коррозию металла и повышение сухого остатка в котловой воде.
Бариевый метод умягчения воды
применяют в сочетании с другими методами. Вначале вводят барий содержащие реагенты в воду (Ва (ОН) 2
, ВаСО3
, ВаА12
04
) для устранения сульфатной жесткости, затем после осветления воды ее обрабатывают известью и содой для доумягчения. Химизм процесса описывается реакциями:
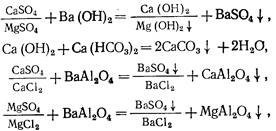

Из-за высокой стоимости реагентов бариевый метод применяют очень редко. Для подготовки питьевой воды из-за токсичности бариевых реагентов он непригоден. Образующийся сульфат бария осаждается очень медленно, поэтому необходимы отстойники или осветлители больших размеров. Для ввода ВаС03 следует использовать флокуляторы с механическими мешалками, поскольку ВаСО3
образует тяжелую, быстро осаждающуюся суспензию.
Необходимые дозы бариевых солей, мг/л, можно найти, пользуясь выражениями: гидроксида бария (продукт 100% -ной активности) Дб
=1,8 (SO4
2-
), алюмината бария Дб
=128Ж0
; углекислого бария Дв
= 2,07γ (S04
2-
);
Углекислый барий применяют с известью. Путем воздействия углекислоты на карбонат бария получают бикарбонат бария, который и дозируют в умягчаемую воду. При этом дозу углекислоты, мг/л, определяют из выражения: Дуг.
= 0,46 (SO4
2-
); где (S04
2-
) - содержание сульфатов в умягчаемой воде, мг/л; γ=1,15.1,20 - коэффициент, учитывающий потери углекислого бария.
Оксалатный метод умягчения воды
основан на применении оксалата натрия и на малой растворимости в воде образующегося оксалата кальция (6,8 мг/л при 18° С)

Метод отличается простотой технологического и аппаратурного оформления, однако, из-за высокой стоимости реагента его применяют для умягчения небольших количеств воды.
Фосфатирование применяют для доумягчения воды.
После реагентного умягчения известково-содовым методом неизбежно наличие остаточной жесткости (около 2 мг-экв/л), которую фосфатным доумягчением можно снизить до 0,02-0,03 мг-экв/л. Такая глубокая доочистка позволяет в некоторых случаях не прибегать к катионитовому водоумягчению.
Фосфатированием достигается также большая стабильность воды, снижение ее коррозионного действия на металлические трубопроводы и предупреждаются отложения карбонатов на внутренней поверхности стенок труб.
В качестве фосфатных реагентов используют гексаметафос - фат, триполифосфат (ортофосфат) натрия и др.
Фосфатный метод умягчения воды при использовании три - натрийфосфата является наиболее эффективным реагентным методом. Химизм процесса умягчения воды тринатрийфосфатом описывается реакциями

Как видно из приведенных реакций, сущность метода заключается в образовании кальциевых и магниевых солей фосфорной кислоты, которые обладают малой растворимостью в воде и поэтому достаточно полно выпадают в осадок.
Фосфатное умягчение обычно осуществляют при подогреве воды до 105.150° С, достигая ее умягчения до 0,02.0,03 мг-экв/л. Из-за высокой стоимости тринатрийфосфата фосфатный метод обычно используется для доумягчения воды, предварительно умягченной известью и содой. Доза безводного тринатрийфосфата (Дф
; мг/л) для доумягчения может быть определена из выражения
ДФ
=54,67 (ЖОСТ
+ 0,18),
где Жост
- остаточная жесткость умягченной воды перед фосфатным доумягчением, мг-экв/л.
Образующиеся при фосфатном умягчении осадки Са3
(Р04
) 2
и Mg3
(P04
) 2
хорошо адсорбируют из умягченной воды органические коллоиды и кремниевую кислоту, что позволяет выявить целесообразность применения этого метода для подготовки питательной воды для котлов среднего и высокого давления (58,8.98,0 МПа).
Раствор для дозирования гексаметафосфата или ортофосфата натрия с концентрацией 0,5-3% приготовляют в баках, количество которых должно быть не менее двух. Внутренние поверхности стенок и дна баков должны быть покрыты коррозионноустойчивым материалом. Время приготовления 3% -ного раствора составляет 3 ч при обязательном перемешивании мешалочным или барботажным (с помощью сжатого воздуха) способом.
В технологии реагентного умягчения воды используют аппаратуру для приготовления и дозирования реагентов, смесители, тонкослойные отстойники или осветлители, фильтры и установки для стабилизационной обработки воды. Схема напорной водоумягчительной установки представлена на рис. 3
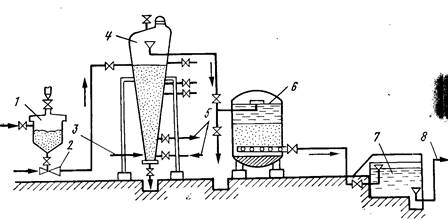
Рис. 3. Водоумягчительная установка с вихревым реактором.
1 - бункер с контактной массой; 2 -
эжектор; 3, 8
- подача исходной и отвод умягченной воды; 4
- вихревой реактор; 5
- ввод реагентов; 6
- скорый осветлительный фильтр; 9 -
сброс контактной массы; 7 - резервуар умягченной воды
В этой установке отсутствует камера хлопьеобразования, поскольку хлопья осадка карбоната кальция формируются в контактной массе. При необходимости воду перед реакторами осветляют.
Оптимальным сооружением для умягчения воды известковым или известково-содовым методами является вихревой реактор (спирактор напорный или открытый) (
рис. 20.4). Реактор предоставляет собой железобетонный или стальной корпус, суженный книзу (угол конусности 5.20°) и наполненный примерно до половины высоты контактной массой. Скорость движения воды в нижней узкой части вихревого реактора равна 0,8.1 м/с; скорость восходящего потока в верхней части на уровне водоотводящих устройств - 4.6 мм/с. В качестве контактной массы применяют песок или мраморную крошку с размером зерен 0,2.0,3 мм из расчета 10 кг на 1 м3 объема реактора. При винтовом восходящем потоке воды контактная масса взвешивается, песчинки сталкиваются друг с другом и на их поверхности интенсивно кристаллизируется СаСО3
; постепенно песчинки превращаются в шарики правильной формы. Гидравлическое сопротивление контактной массы составляет 0,3 м на 1 м высоты. Когда диаметр шариков увеличивается до 1,5.2 мм, крупную наиболее тяжелую контактную массу выпускают из нижней части реактора и догружают свежую. Вихревые реакторы не задерживают осадка гидроксида магния, поэтому их следует применять совместно с установленными за ними фильтрами только в тех случаях, когда количество образующегося осадка гидроксида магния соответствует грязеемкости фильтров.
При грязеемкости песчаных фильтров, равной 1.1,5 кг/м3
, и фильтроцикле 8 ч допустимое количество гидроксида магния составляет 25.35 г/м3
(содержание магния в исходной воде не должно превышать 10.15 г/м3
). Возможно применение вихревых реакторов и при большем содержании гидроксида магния, но при этом после них необходимо устанавливать осветлители для выделения гидроксида магния.
Расход свежей контактной массы, добавляемой с помощью эжектора, определяют по формуле G
=
0,045QЖ, гдеG
- количество добавляемой контактной массы, кг/сут; Ж
- удаляемая в реакторе жесткость воды, мг-экв/л; Q - производительность установки, м3
/ч.
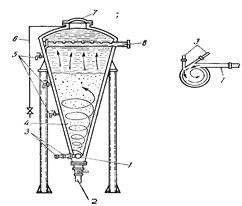
Рис. 4. Вихревой реактор.
1,8
- подача исходной и отвод умягченной воды: 5
- пробоотборники; 4 -
контактная масса; 6
- сброс воздуха; 7
- люк для загрузки контактной массы; 3 - ввод реагентов; 2
- удаление отработавшей контактной массы
В технологических схемах реагентного умягчения воды с осветлителями вместо вихревых реакторов применяют вертикальные смесители (рис. 5). В осветлителях следует поддерживать постоянную температуру, не допуская колебаний более 1°С, в течение часа, поскольку возникают конвекционные токи, взмучивание осадка и его вынос.
Подобную технологию применяют для умягчения мутных вод, содержащих большое количество солей магния. В этом случае смесители загружают контактной массой. При использовании осветлителей конструкции Е.Ф. Кургаева, смесители и камеры хлопьеобразования не предусматривают, поскольку смешение реагентов с водой и формирование хлопьев осадка происходят в самих осветлителях.
Значительная высота при небольшом объеме осадкоуплотнителей позволяет применять их для умягчения воды без подогрева, а также при обескремнивании воды каустическим магнезитом. Распределение исходной воды соплами обусловливает ее вращательное движение в нижней части аппарата, что повышает устойчивость взвешенного слоя при колебаниях температуры и подачи воды. Смешанная с реагентами вода проходит горизонтальную и вертикальную смесительные перегородки и поступает в зону сорбционной сепарации и регулирования структуры осадка, что достигается изменением условий отбора осадка по высоте взвешенного слоя, создавая предпосылки для получения его оптимальной структуры, улучшающей эффект умягчения и осветления воды. Проектируют осветлители так же, как и для обычного осветления воды.
При расходах умягчаемой воды до 1000 м3
/сут может быть применена водоочистная установка типа "Струя". Обрабатываемая вода с добавленными к ней реагентами поступает в тонкослойный отстойник, затем на фильтр.
В Институте горного дела Сибирского отделения РАН разработана безреагентная электрохимическая технология умягчения воды. Используя явление подщелачивания у анода и подкисления у катода при пропускании постоянного электрического тока через водную систему, можно представить реакцию разряда воды следующим уравнением:
2Н2
0 + 2е1
→ 20Н -
+ Н2,
где е1
- знак, указывающий на способность солей жесткости диссоциировать на катионы Ca (II) и Mg (II).
В результате протекания этой реакции концентрация гидроксильных ионов возрастает, что вызывает связывание ионов Mg (II) и Ca (II) в нерастворимые соединения. Из анодной камеры диафрагменного (диафрагма из ткани типа бельтинг) электролизера эти ионы переходят в катодную за счет разности потенциалов между электродами и наличия электрического поля между ними.
На рис. 6 показана технологическая схема установки для умягчения воды электрохимическим способом.
Производственная установка была смонтирована в районной котельной, испытания которой длились около двух месяцев. Режим электрохимической обработки оказался устойчивым, осадка в катодных камерах не наблюдалось.
Напряжение на подводящих шинах составляло 16 В, суммарный ток 1600 А. Общая производительность установки - 5 м3/ч, скорость движения воды в анодных камерах 0,31 н-0,42 м/мин, в зазоре между диафрагмой и катодом 0,12-0,18 м/мин.

Рис. 5. Установка нзвестково-содового умягчения воды.1,8
- подача исходной и отвод умягченной воды; 2 - эжектор; 3
- бункер с контактной массой; 5 ввод реагентов; 6
- осветлитель со слоем взвешенного осадка; 7 - осветлительный скорый фильтр; 4 - вихревой реактор
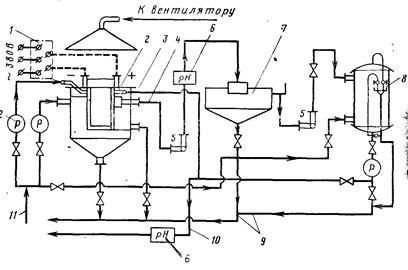
Рис. 6. Схема установки электрохимического умягчения воды I - выпрямитель ВАКГ-3200-18; 2
- диафрагменный электролизер; 3, 4 -
аналит и каталит; 5
- насос; 6
- рН-метр; 7 - осветлитель со слоем взвешенного осадка; 8 -
осветлительный скорый фильтр; 9
- сброс в канализацию; 10, 11 -
отвод умягченной и подача исходной воды; 12
- расходомер; 13
- вытяжной зонт
Установлено, что из воды с Жо
= 14,5-16,7 мг-экв/л получают анолит с жесткостью 1,1 - 1,5 мг-экв/л при рН = 2,5-3 и католит с жесткостью 0,6-1 мг-экв/л при рН=10,5-11. После смешения отфильтрованных анолита и католита показатели умягченной воды были следующими: общая жесткость Жо
составляла 0,8-1,2 мг-экв/л, рН = 8-8,5. Затраты электроэнергии составили 3,8 кВт*ч/м3
.
Химическим, рентгеноструктурным, ИК-спектроскопическим и спектральным анализами установлено, что в осадке преимущественно содержатся CaC03
, Mg (OH) 2
и частично Fe2
03
*Н2
0. Это свидетельствует о том, что связывание ионов Mg (II) происходит за счет гидроксил-ионов при разряде молекул воды на катоде.
Электрохимическая обработка воды перед подачей на катионитовые фильтры позволяет значительно (в 15-20 раз) увеличить их рабочий цикл.
Термохимическое умягчение применяют исключительно при подготовке воды для паровых котлов,
так как в этом случае наиболее рационально используется теплота, затраченная на подогрев воды. Этим методом умягчение воды производят обычно' при температуре воды выше 100°С. Более интенсивному умягчению воды при ее подогреве способствует образование тяжелых и крупных хлопьев осадка, быстрейшее его осаждение вследствие снижения вязкости воды при нагревании, сокращается также расход извести, так как свободный оксид углерода (IV) удаляется при подогреве до введения реагентов. Термохимический метод применяют с добавлением коагулянта и без него, поскольку большая плотность осадка исключает необходимость в его утяжелении при осаждении. Помимо коагулянта используют известь и соду с добавкой фосфатов и реже гидроксид натрия и соду. Применение гидроксида натрия вместо извести несколько упрощает технологию приготовления и дозирования реагента, однако экономически такая замена не оправдана в связи с его высокой стоимостью.
Для обеспечения удаления некарбонатной жесткости воды соду добавляют с избытком. На рис. 7 показано влияние избытка соды на остаточную кальциевую и общую жесткость воды при ее термохимическом умягчении. Как видно из графиков, при избытке соды 0,8 мг-экв/л кальциевая жесткость может быть снижена до 0,2, а общая - до 0,23 мг/экв-л. При дальнейшем Добавлении соды жесткость еще более понижается. Остаточное содержание магния в воде может быть снижено до 0,05.0,1 мг-экв/л при избытке извести (гидратной щелочности) 0,1 мг-экв/л. На рис. 20.8 показана установка термохимического умягчения воды.
Известково-доломитовый метод
используют для одновременного умягчения и обескремнивания воды при температуре 120° С. Этим методом умягчения щелочность воды, обработанной известью или известью и содой (без избытка), может быть снижена до 0,3 мг-экв/л при остаточной концентрации кальция 1,5 мг-экв/л и до 0,5 мг-экв/л при остаточной концентрации кальция 0,4 мг-экв/л. Исходная вода обрабатывается известково-доломитовым молоком и осветляется в напорном осветлителе. Затем она проходит через напорные антрацитовые и Na-катионитовые фильтры первой и второй ступеней.
В осветлителях высоту зоны осветления принимают равной 1,5 м, скорость восходящего потока при известковании - не более 2 мм/с. Время пребывания воды в осветлителе от 0,75 до 1,5 ч в зависимости от вида удаляемого загрязнения. Коагулянт соли железа (III) рекомендуется добавлять в количестве 0,4 мг-экв/л.
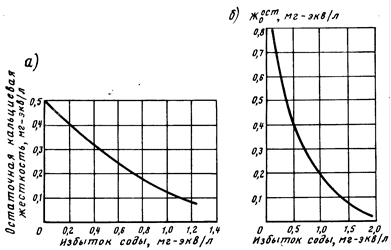
Рис. 7. Влияние избытка соды на остаточную кальциевую (а) и общую (б)
жесткость воды при ее термохимическом умягчении

Рис. 8. Установка известково-содового умягчения воды с фосфатным доумягчением: 1
- сброс шлама из накопителя 2,3
- сборник умягченной воды; 4
- ввод извести и соды; 5, 11
- подача исходной и отвод умягченной воды; 6
- ввод пара; 7, 8
- термореактор первой и второй ступени; 9
- ввод тринатрийфосфата; 10
- осветлительный скорый фильтр
Метод высокотемпературного умягчения воды
применяют практически для полного ее умягчения. Установки термохимического умягчения воды обычно более компактны. Они состоят из дозаторов реагентов, подогревателей тонкослойных отстойников или осветлителей и фильтров. Дозы извести Ди
и соды Дс
, мг/л, при термохимическом умягчении воды

где Си
и Сс -
соответственно содержание СаО и Na2
C03
в техническом продукте, %.
Диализ - метод разделения растворенных веществ, значительно отличающихся молекулярными массами. Он основан на разных скоростях диффузии этих веществ через полупроницаемую мембрану, разделяющую концентрированный и разбавленный растворы. Под действием градиента концентрации (по закону действующих масс) растворенные вещества с различными скоростями диффундируют через мембрану в сторону разбавленного раствора. Растворитель (вода) диффундирует в обратном направлении, снижая скорость переноса растворенных веществ. Диализ осуществляют в мембранных аппаратах с нитро - и ацетатцеллюлозными пленочными мембранами. Эффективность полупроницаемой мембраны для умягчения воды определяется высокими значениями селективности и водопроницаемости, которые она должна сохранять в течение продолжительного времени работы. Селективность мембраны можно выразить следующим образом:
(Жи
- Жу
) /Жи
(20.11)
где Жв
- концентрация исходного раствора (жесткость); Жи -
жесткость умягченной воды.
На практике часто используют коэффициент снижения соле - содержания Си
/Собр
. Он наиболее полно отражает изменения в работе мембраны, связанные с ее изготовлением или с воздействием внешних факторов.
Существует несколько гипотетических моделей действия полупроницаемых мембран.
Гипотеза гиперфильтрации
предполагает существование в полупроницаемой мембране пор, пропускающих при диализе ас - социанты молекул воды и гидратированные ионы солей. Основой теоретических разработок явилось положение о том, что через полупроницаемую мембрану вода и растворенные в ней соли проникают с помощью диффузии и потоков через поры.
Сорбционная модель
проницаемости основана на предпосылке, согласно которой на поверхности мембраны и в ее порах
адсорбируется слой связанной воды, обладающей пониженной растворяющей способностью. Мембраны будут полупроницаемы, если они, хотя бы в поверхностном слое имеют поры, не превышающие по размеру удвоенной толщины слоя связанной жидкости.
Диффузионная модель
исходит из предположения, что компоненты системы растворяются в материале мембраны и диффундируют через нее. Селективность мембраны объясняется различием в коэффициентах диффузии и растворимости компонентов системы в ее материале.
Электростатическая теория
заключается в следующем. При движении исходной воды в камере с одной стороны селективной (катионитовой) мембраны, а рассола с другой, ионы натрия в случае, когда рассол приготовлен из раствора поваренной соли, мигрируют в мембрану и далее в исходную воду, а ионы кальция в противоположном направлении, т.е. из жесткой воды в рассол. Таким образом, происходит удаление ионов кальция из исходной воды и замена их неосадкообразующими ионами натрия. Одновременно в камерах происходят побочные процессы, сопутствующие основному процессу диализа: осмотические переносы воды, перенос одноименных ионов, диффузия электролита. Эти процессы зависят от качества мембраны.
Уравнение обмена между ионами [Ca2+
], содержащимися в исходной воде, и ионами [Na+
] в мембране имеет вид

где х, х
- прочие ионы, содержащиеся в растворе и в мембране.
Константа равновесия
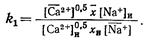
Уравнение обмена написано только для иона кальция, но> фактически необходимо учитывать сумму ионов кальция и магния. Равновесие между рассолом и мембраной имеет вид:
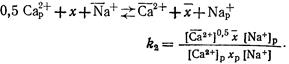
Если k1+ k2
, то
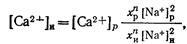
где n - показатель степени, зависящий от того, какие ионы входят в состав раствора.
Из последнего выражения можно заключить, что, если равновесии отношение ионов натрия в рассоле и жесткой исходной воде равно, например, 10, то жесткость в исходной воде будет примерно в 100 раз меньше, чем в рассоле. Площадь, м2
, поверхности мембраны

где М - количество вещества, прошедшее через мембрану; ΔСср
- движущая сила процесса, т е. разность концентраций вещества по обе стороны мембраны; Кд
- коэффициент массопередачи, определяемый обычно экспериментально или приближенно из выражения

β1
и β2
- соответствующие коэффициенты скорости переноса вещества в концентрированном растворе к мембране и от нее в разбавленном; б - толщина мембраны; D
- коэффициент диффузии растворенного вещества.
Жесткость умягченной воды после диализа:

где Сд
и Ср
- концентрации солей в начале аппарата соответственно в диализате и в рассоле, мг-экв/л; и
Qp
-
производительность аппарата соответственно по диализату и рассолу, м3
/ч; Жд
и Жр
- жесткость диализата и рассола в начале аппарата, мг-экв/л; а - константа, определяемая свойствами мембран и растворов;; L
- длина пути раствора в диализатной и рассольной камерах аппарата, м; υд
- скорость движения диализата в камере, м/с.
Экспериментальная проверка уравнения (20.13) на катионитовых мембранах МКК показала хорошую сходимость результатов. Анализ формулы (20.13) показывает, что уменьшение скорости движения диализата в камерах аппарата увеличивает эффект умягчения, снижение жесткости умягченной воды прямо пропорционально концентрации рассола.
В последнее время в отечественной и зарубежной практике для борьбы с накипеобразованием и инкрустацией успешно применяют магнитную обработку воды. Механизм воздействия магнитного поля на воду
и ее примеси окончательно не выяснен, имеется ряд гипотез, которые Е.Ф. Тебенихиным классифицированы на три группы: первая, объединяющая большинство гипотез, связывает действие магнитного поля на ионы солей, растворенных в воде. Под влиянием магнитного поля
происходят поляризация и деформация ионов, сопровождающиеся уменьшением их гидратации, повышающей вероятность их сближения, и в конечном итоге образование
центров кристаллизации; вторая предполагает действие магнитного поля на коллоидные примеси воды; третья группа объединяет представления о возможном влиянии магнитного поля на структуру воды. Это
влияние, с одной стороны, может вызвать изменения в агрегации молекул воды, с другой - нарушить ориентацию ядерных спинов водорода в ее молекулах.
Обработка воды в магнитном поле распространена для борьбы с накипеобразованием.
Сущность метода состоит в том, что при пересечении водой магнитных силовых линий накипеобразователи выделяются не на поверхности нагрева, а в массе воды. Образующиеся рыхлые осадки (шлам) удаляют при продувке. Метод эффективен при обработке вод кальциево-карбонатного класса, которые составляют около 80% вод всех водоемов нашей страны и охватывают примерно 85% ее территории.
Обработка воды магнитным полем получила широкое применение для борьбы с накипеобразованием в конденсаторах паровых турбин, в парогенераторах низкого давления и малой производительности, в тепловых сетях и сетях горячего водоснабжения и различных теплообменных аппаратах, где применение других методов обработки воды экономически нецелесообразно. В сравнении с умягчением воды основными преимуществами ее магнитной обработки являются простота, дешевизна, безопасность и почти полное отсутствие эксплуатационных расходов.
Магнитная обработка природных вод (как пресных, так и минерализованных) приводит к уменьшению интенсивности образования накипи на поверхностях нагрева только при условии перенасыщенности их как карбонатом, так и сульфатом кальция в момент воздействия магнитного поля и при условии, что концентрация свободного оксида углерода (IV) меньше его равновесной концентрации. Противонакипный эффект Э обусловливает присутствие в воде оксидов железа и других примесей:

где mн
и mм
- масса накипи, образовавшейся на поверхности нагрева при кипячении в одинаковых условиях одного и того же количества воды, соответственно необработанной и обработанной магнитным полем, г.
Противонакипный эффект зависит от состава воды, напряженности магнитного поля, скорости движения воды и продолжительности ее пребывания в магнитном поле и от других факторов. На практике применяют магнитные аппараты с постоянными стальными или феррито-бариевыми магнитами и электромагнитами (рис. 9). Аппараты с постоянными магнитами конструктивно проще и не требуют питания от электросети. В аппаратах с электромагнитом на сердечник (керн) наматываются катушки проволоки, создающие магнитное поле.
Магнитный аппарат монтируется к трубопроводам в вертикальном или горизонтальном положении с помощью переходных муфт. Скорость движения воды в зазоре не должна превышать 1 м/с. Процесс работы аппаратов может сопровождаться загрязнением проходного зазора механическими главным образом ферромагнитными примесями. Поэтому аппараты с постоянными магнитами необходимо периодически разбирать и чистить. Оксиды железа из аппаратов с электромагнитными удаляют, отключив их от сети.
Результаты исследований МГСУ (Г.И. Николадзе, В.Б. Викулина) показали, что для воды с карбонатной жесткостью 6.7 мкг-экв/л, окисляемостью 5,6 мг02/л и солесодержанием 385.420 мг/л, оптимальная напряженность магнитного поля составляла (10.12,8) * 194
А/м, что соответствует силе тока 7.8 А.
Схема установки для магнитной обработки добавочной питательной воды отопительных паровых котлов приведена на рис. 20.10.
В последнее время получили распространение аппараты с внешними намагничивающими катушками. Для омагничивания больших масс воды созданы аппараты с послойной ее обработкой.
Помимо предотвращения накипеобразования магнитная обработка,
по данным П.П. Строкача, может применяться для интенсификации процесса коагуляции и кристаллизации, ускорения растворения реагентов, повышения эффективности использования ионообменных смол, улучшения бактерицидного действия дезинфектантов.
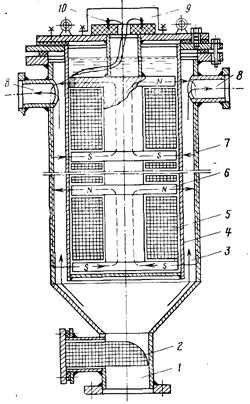
Рис. 9. Электромагнитный аппарат для противонакипной обработки воды СКВ ВТИ: 1,8
- подача исходной и отвод омагниченной воды; 2
- сетка; 3 - рабочий зазор для прохода омагничиваемой воды; 4 -
кожух; 5 - намагничивающая катушка; 6 -
сердечник; 7
- корпус; 9 -
крышка; 10
– клеммы
При проектировании магнитных аппаратов для обработки воды задаются такие данные: тип аппарата, его производительность, индукция магнитного поля в рабочем зазоре или соответствующая ей напряженность магнитного поля, скорость воды в рабочем зазоре, время прохождения водой активной зоны аппарата, род и его напряжение для электромагнитного аппарата или магнитный сплав и размеры магнита для аппаратов с постоянными магнитами.
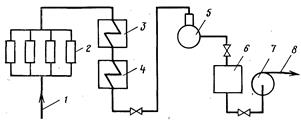
Рис. 10. Схема размещения магнитной установки для обработки котловой воды без предварительной очистки.
1,8 -
исходная и подпиточная вода; 2
- электромагнитные аппараты; 3, 4
- подогреватели I и II ступени; 5
- деаэратор; 6
- промежуточный бак; 7 - подпиточный насос
1. Алексеев Л.С., Гладков В.А. Улучшение качества мягких вод. М.,
2. Стройиздат, 1994 г.
3. Алферова Л.А., Нечаев А.П. Замкнутые системы водного хозяйства промышленных предприятий, комплексов и районов. М., 1984.
4. Аюкаев Р.И., Мельцер В.З. Производство и применение фильтрующих материалов для очистки воды.Л., 1985.
5. Вейцер Ю.М., Мииц Д.М. Высокомолекулярные флокулянты в процессах очистки воды. М., 1984.
6. Егоров А.И. Гидравлика напорных трубчатых систем в водопроводных очистных сооружениях. М., 1984.
7. Журба М.Г. Очистки воды на зернистых фильтрах. Львов, 1980.
|