Министерство сельского хозяйства Российской Федерации
ФГОУ ВПО «Чувашская государственная сельскохозяйственная академия»
Кафедра «Эксплуатация автомобильного транспорта»
КОНТРОЛЬНАЯ РАБОТА
Транспортное обеспечение в агропромышленном комплексе
Выполнила студентка I
курса
экономического отделения
заочного факультета
Иванова Оксана Владимировна
(Ф.И.О. студента)
2010 год
Содержание
1. Общее устройство и принципы работы тормозного механизма
2. Расчет производительности КамАЗа 55111
3. Расчет потребности транспортных средств на уборке кукурузы
4. Перевозка грузов цистернами
5. Перечень средств механизации погрузочно-разгрузочных и транспортных работ в СХК «Атлашевский» Чебоксарского района ЧР
1.
Общее устройство и принципы работы тормозного механизма
Задан узел автомобиля-тормозной механизм.
Тормозная система (рис. 1) предназначена для уменьшения скорости движения и остановки автомобиля (рабочая тормозная система). Она также позволяет удерживать автомобиль от самопроизвольного движения во время стоянки (стояночная тормозная система).
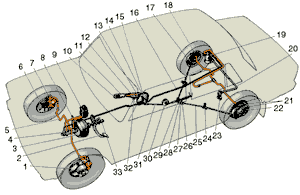
Рис. 1. Общая схема тормозной системы:
1 - передний тормоз; 2 - педаль тормоза; 3 - вакуумный усилитель; 4 - главный цилиндр гидропривода тормозов; 5 - трубопровод контура привода передних тормозов; 6 - защитный кожух переднего тормоза; 7 - суппорт переднего тормоза; 8 - вакуумный трубопровод; 9 - бачок главного цилиндра; 10 - кнопка рычага привода стояночного тормоза; 11 - рычаг привода стояночного тормоза; 12 - тяга защелки рычага; 13 - защелка рычага; 14 - кронштейн рычага привода стояночного тормоза; 15 - возвратный рычаг; 16 - трубопровод контура привода задних тормозов; 17 - фланец наконечника оболочки троса; 18 - задний тормоз; 19 - регулятор давления задних тормозов; 20 - рычаг привода регулятора давления; 21 - колодки заднего тормоза; 22 - рычаг ручного привода колодок; 23 - тяга рычага привода регулятора давления; 24 - кронштейн крепления наконечника оболочки троса; 25 - задний трос; 26 - контргайка; 27 - регулировочная гайка; 28 - втулка; 29 - направляющая заднего троса; 30 - направляющий ролик; 31 - передний трос; 32 - упор выключателя контрольной лампы стояночного тормоза; 33 - выключатель стоп-сигнала.
транспортное средство сельское хозяйство
Рабочая тормозная система приводится в действие нажатием на педаль тормоза, которая располагается в салоне автомобиля. Усилие ноги водителя передается на тормозные механизмы всех четырех колес. Стояночная тормозная система нужна не только на стоянке, она также необходима для предотвращения скатывания автомобиля назад при старте на подъем. С помощью рычага стояночного тормоза, который располагается между передних сидений автомобиля, водитель рукой может управлять тормозными механизмами задних колес. Рабочая тормозная система состоит из:
- тормозного привода;
- тормозных механизмов колес.
Привод тормозов служит для передачи усилия ноги водителя от педали тормоза к исполнительным тормозным механизмам колес автомобиля. На современных легковых автомобилях применяется гидравлический привод тормозов, в котором используется специальная тормозная жидкость.
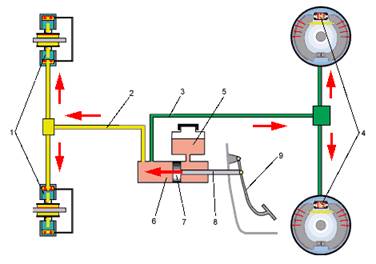
Рис. 2. Схема гидропривода тормозов:
1 - тормозные цилиндры передних колес; 2 - трубопровод передних тормозов; 3 - трубопровод задних тормозов; 4 - тормозные цилиндры задних колес; 5 - бачок главного тормозного цилиндра; 6 - главный тормозной цилиндр; 7 - поршень главного тормозного цилиндра; 8 - шток; 9 - педаль тормоза
Привод тормозов гидравлический (рис. 2) состоит из:
- педали тормоза;
- главного тормозного цилиндра;
- рабочих тормозных цилиндров;
- тормозных трубок;
- вакуумного усилителя.
Когда нога водителя нажимает на педаль тормоза, то ее усилие, через шток передается на поршень главного тормозного цилиндра. Давление жидкости, на которую давит поршень, от главного цилиндра по трубкам передается ко всем колесным тормозным цилиндрам, заставляя выдвигаться их поршни. Ну, а они, в свою очередь, передают усилие на тормозные колодки, которые и выполняют основную работу тормозной системы.
Современный гидропривод тормозов состоит из двух независимых контуров, связывающих между собой пару колес. При отказе одного из контуров, срабатывает второй, что обеспечивает, хотя и не очень эффективное, но все-таки торможение автомобиля.
К примеру, на автомобиле «Жигули» ВАЗ 2105, один контур объединяет тормозные механизмы передних колес, а другой – задних. На автомобиле «Жигули» ВАЗ 2109, между собой связаны: переднее левое колесо с задним правым, и переднее правое с задним левым.
Для уменьшения усилия при нажатии на педаль тормоза и более эффективной работы системы, применяется вакуумный усилитель. Усилитель явно облегчает работу водителя, так как использование педали тормоза при движении в городской цикле носит постоянный характер и довольно быстро утомляет.
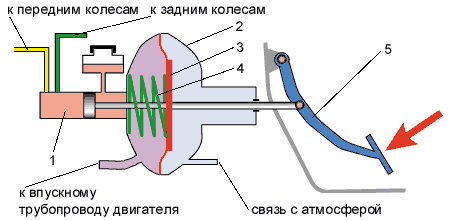
Рис. 3. Схема вакуумного усилителя:
1 - главный тормозной цилиндр; 2 - корпус вакуумного усилителя; 3 - диафрагма; 4 - пружина; 5 - педаль тормоза.
Вакуумный усилитель (рис. 3) конструктивно связан с главным тормозным цилиндром. Основным элементом усилителя является камера, разделенная резиновой перегородкой (диафрагмой) на два объема. Один объем связан с впускным трубопроводом двигателя, где создается разряжение около 0,8 кг/см2, а другой с атмосферой (1 кг/см2). Из-за перепада давлений в 0,2 кг/см2, благодаря большой площади диафрагмы, «помогающее» усилие при работе с педалью тормоза может достигать 30 - 40 кг и больше. Это значительно облегчает работу водителя при торможениях и позволяет сохранить его работоспособность длительное время. Тормозной механизм предназначен для уменьшения скорости вращения колеса, за счет сил трения возникающих между накладками тормозных колодок и тормозным барабаном или диском. Тормозные механизмы делятся на барабанные и дисковые. На отечественных автомобилях барабанные тормозные механизмы применяются на задних колесах, а дисковые на передних. Хотя в зависимости от модели автомобиля могут применяться только барабанные или только дисковые тормоза на всех четырех колесах.
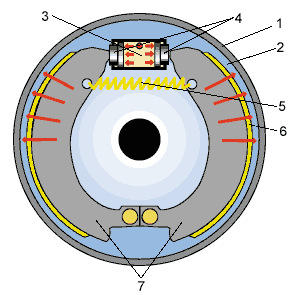
Рис. 4. Схема работы барабанного тормозного механизма:
1 - тормозной барабан; 2 - тормозной щит; 3 - рабочий тормозной цилиндр; 4 - поршни рабочего тормозного цилиндра; 5 - стяжная пружина; 6 - фрикционные накладки; 7 - тормозные колодки.
Барабанный тормозной механизм (рис. 4) состоит из:
- тормозного щита;
- тормозного цилиндра;
- двух тормозных колодок;
- стяжных пружин;
- тормозного барабана.
Тормозной щит жестко крепится на балке заднего моста автомобиля, а на щите, в свою очередь, закреплен рабочий тормозной цилиндр. При нажатии на педаль тормоза поршни в цилиндре расходятся и начинают давить на верхние концы тормозных колодок. Колодки в форме полуколец прижимаются своими накладками к внутренней поверхности круглого тормозного барабана, который при движении автомобиля вращается вместе с закрепленным на нем колесом. Торможение колеса происходит за счет сил трения, возникающих между накладками колодок и барабаном. Когда же воздействие на педаль тормоза прекращается, стяжные пружины оттягивают колодки на исходные позиции.
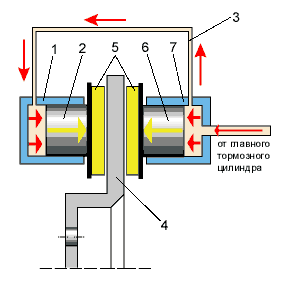
Рис. 5. Схема работы дискового тормозного механизма:
1 - наружный рабочий цилиндр (левого) тормоза; 2 - поршень; 3 - соединительная трубка; 4 - тормозной диск переднего (левого) колеса; 5 - тормозные колодки с фрикционными накладками; 6 - поршень; 7 - внутренний рабочий цилиндр переднего (левого) тормоза.
Дисковый тормозной механизм (рис.5) состоит из:
- суппорта;
- одного или двух тормозных цилиндров;
- двух тормозных колодок;
- тормозного диска.
Суппорт закреплен на поворотном кулаке переднего колеса автомобиля. В нем находятся два тормозных цилиндра и две тормозные колодки. Колодки с обеих сторон «обнимают» тормозной диск, который вращается вместе с закрепленным на нем колесом. При нажатии на педаль тормоза поршни начинают выходить из цилиндров и прижимают тормозные колодки к диску. После того, как водитель отпустит педаль, колодки и поршни возвращаются в исходное положение за счет легкого «биения» диска. Дисковые тормоза очень эффективны и просты в обслуживании. Даже дилетанту замена тормозных колодок в этих механизмах доставляет мало хлопот. Стояночный тормоз (рис. 1) приводится в действие поднятием рычага стояночного тормоза (в обиходе – «ручника») в верхнее положение. При этом натягиваются два металлических троса, последний из которых заставляет тормозные колодки задних колес прижаться к барабанам. И как следствие этого, автомобиль удерживается на месте в неподвижном состоянии. В поднятом состоянии, рычаг стояночного тормоза автоматически фиксируется защелкой. Это необходимо для того, чтобы не произошло самопроизвольное выключение тормоза и бесконтрольное движение автомобиля в отсутствии водителя.
2.
Расчет производительности КамАЗа 55111
Технические характеристики КамАЗа 55111:
Тип грузовика Самосвал
Колесная формула автомобиля 6x4
Снаряженная масса автомобиля, кг 9150
Грузоподъемность автомобиля, кг 13000
Полная масса грузовика, кг 22300
Полная масса буксируемого прицепа, кг 12800
Полная масса автопоезда, кг 35100
Объем кузова, м3
6,6
Размер шин 10.00R20
Ошиновка задних колес Двухскатная
Максимальная скорость, км/час 90
Максимальный преодолеваемый подъем, ° 25 (18)
Радиус поворота автомобиля, м 9
Высота грузовика, мм 2765
Длина автомобиля, мм 6700
Ширина автомашины, мм 2500
Передний свес, мм 1320
Внутренние размеры (объем) платформы, м3
6.6
Колея передних колес, мм 2043
Колея задних колес, мм 1890
Двигатель (модель, мошность) КАМАЗ 740.31 240 л.с
Расход топлива а/м КАМАЗ, л/100 км. 28
Коробка передач (модель) 152
Вместимость топливного бака, л. 250
Рассчитаем производительность КамАЗа 55111 при перевозке силосной массы в одном направлении на расстояние 20 км. Время пребывания в наряде 7 часов.
1. Определим массу груза в кузове по формуле:
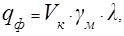
где - вместимость кузова по технической характеристике, м3
;
- объемная масса груза, т/м3
;
- коэффициент использования объема кузова, для силоса насыпью-1,1.
= 6,6 * 0,8 * 1,1 = 5,808
2. Рассчитаем время ездки автомобиля:
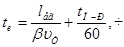
где - расстояние перевозки, км;
- коэффициент использования пробега; в случае перевозки груза в одном направлении - =0,5; в случае перевозки груза в двух направлениях - =1,0;
- техническая скорость автомобиля, км/ч;
- время простоя автомобиля под погрузкой-разгрузкой, мин;
= , мин.
где - норма времени простоя при погрузке-разгрузке, мин/т.
=(2,6+4)*5,808=38,33 мин
te
=
20 / 0,5 *90 + 38,33 / 60 = 1,1 ч
3. Количество ездок автомобиля за время пребывания в наряде вычислим по выражению:

Расчетное значение = 7 / 1, 1 = 6
4. Уточним время пребывания автомобиля в наряде:
, ч
где - уточненное время пребывания в наряде, ч;
- принятое количество ездок.
= 6 * 1,1 = 6,6 ч
5. Вычислим производительность автомобиля в т/ч по формуле:
т/ч
где - номинальная грузоподъемность, т;
- коэффициент статического использования грузоподъемности,
= / = 5,808 / 13 = 0,45
т/ч
6. Производительность автомобиля в т. км/ч вычисляют по формуле:
, т·км/ч
где - коэффициент динамического использования грузоподъемности; при перевозке одного груза, одним автомобилем =
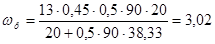
Вывод.
При перевозке силосной массы на расстояние в 20 км автомобиль-самосвал КамАЗ 55111 за время пребывания в наряде выполняет 6 рейсов, при этом время пребывания в наряде уменьшается на 0,4 часа по сравнению с заданным. Производительность за один час составляет 0,15 т, выполняется за час 3,02 ткм/ч. Следует отметить, что при номинальной грузоподъемности 13 т автомобиль загружен лишь на 5,8 т (45%), что не эффективно. Поэтому необходимо дополнительно нарастить борта автомобиля.
3.
Расчет потребности транспортных средств на уборке кукурузы
Задано: убираемая культура – кукуруза на силос, урожайность – 30 т/га, марка и количество уборочных агрегатов – кормоуборочный комбайн Е281 «MARAL» -1шт, транспортное средство – КамАЗ 55102, расстояние перевозки – 8 км.
1. Краткая техническая характеристика кормоуборочного комбайна Е-281 "MARAL": пропускная способность на уборке кукурузы - 21,8 кг/c; ширина захвата жатки для уборки кукурузы – 2,87 м, рабочая скорость – 6,1 км/ч.
2. Транспортное средство для транспортировки измельченной кукурузы - КамАЗ 55102 – 3 единицы. КАМАЗ-55102 – это сельскохозяйственный самосвал, имеющий возможность боковой разгрузки. Его грузоподъемность составляет 7000 кг. Снаряженная масса автомобиля составляет 8 630 кг, а полная его масса - 15 630 кг. Оснащаются представители этой модели двигателем КАМАЗ 740.11 (240), мощность которого 176 кВт (240 л. с.). Объем кузова с основными бортами – 7,9 куб. м., с надставными бортами – 15,8 куб. м.
3. Определим продолжительность оборота транспортного средства. Для этого вычислим продолжительность ездки с грузом и без груза:
tг
= (lег
× 60 ) : nг
, tбг
= (lбг
× 60 ) : nбг
, мин
где lег
= lбг
- расстояние перевозки;
nг
- скорость движения с грузом, учитывая класс груза (силос – II класс), группу дорог (II группа - стерня после уборки бобовых культур) и грузоподъемность прицепа (7 т), скорость 75 км/ч;
nбг
- скорость движения транспортного средства без груза, в нашем примере составит 80 км/ч.
Тогда tг
= (8 х 60) : 75 = 6,4 мин; tбг
= (8 х 60) : 80 = 6,0 мин.
При уборке кукурузы в данном примере используется прямое комбайнирование. Поэтому заполнение кузова рассчитывается исходя из его вместимости и рабочей скорости комбайна.
Продолжительность разгрузки кузова транспортного средства определим по формуле:
tр.к.
= gм
×t'п-р
+ tвзв
,
где t'п-р
- норма времени простоя при разгрузке, определяется, учитывая класс груза, способ погрузки и разгрузки, а также грузоподъемность прицепа. В нашем примере - класс груза – II, способ погрузки-разгрузки -–механизированный, грузоподъемность – 7 т. t'п-р
= 1,8 мин/т;
tвзв
- продолжительность взвешивания, 1,5 мин.
Тогда: tр.к.
= (0,8 х 1,8) + 1,5 = 3 мин.
Отсюда продолжительность оборота транспортного средства составит:
tоб
= tг
+ tбг
+ tз.к.
+ tр.к.
= 6,4 + 6,0 + 3 = 15,4 мин.
4. Продолжительность заполнения кузова автомобиля найдем по формуле:
tз.б.
= (Кв
×Vб
×gм
× 600) : ( Hо
× Вр
×nр
) , мин
где Кв
- коэффициент, учитывающий потери времени на повороты, 1,1;
Но
-урожайность основной продукции, 30 т/га;
Нп
– урожайность побочной продукции, 3 т/га;
Вр
- Ширина захвата комбайна, принимаем по пункту 1, Вр
= 2,87 м;
nр
- рабочая скорость комбайна, км/ч :
nр
= (36 qд
) : [(Но
+ Нп
)] Вр
= (36 х 21,8) : [(30 + 3)] х 2,87 = 8,3 км/ч <21,5 км/ч,
где qд
- допустимая пропускная способность комбайна, по характеристике комбайна – 21,8 кг/с
21,5 км/ч – допустимая рабочая скорость комбайна.
Значит, комбайн Е 281 в заданных условиях может передвигаться по полю с рабочей скоростью до 8,3 км/ч, однако с учетом того, что при таком комбайнировании существует необходимость постоянного присутствия автомобиля рядом с комбайном, рабочую скорость установим равной 7,2 км/ч. Продолжительность заполнения кузова КамАЗа 55102 с надставными бортами при прямом комбайнировании кукурузы составит:
tз.б
= (Кв
×Vб
×gм
×600):(Hо
×Вр
×nр
)=(1,1* 15,8 * 0,8 * 600) : (30 * 2,87 * 7,2) = 13,5 мин.
5. Потребное количество транспортных средств для обслуживания заданного количества комбайнов.
В нашем примере определим потребное количество транспортных средств КамАЗа 55102 для перевозки зерна от одного комбайна, убирающего кукурузу, по формуле:
nт
= (tоб
×К) : [(tз.б
. + tр.б.
) nб
] = 15,4 : 13,5 = 1,1;
где К – заданное количество комбайнов, К = 1 единица.
Окончательно принимаем количество транспортных средств nт
= 2 единицы, т.к. первый необходим для ездки под силосопроводом комбайна во время уборки культуры, второй - для транспортировки силосной массы.
4.
Перевозка грузов цистернами
Еще в самом начале своей истории, сразу после освоения массового выпуска универсальных грузовых автомобилей, потребовалось решение ряда вопросов, связанных с перевозкой отдельных видов грузов, сыпучих, скоропортящихся и наливных. Это послужило толчком для разработки и начала выпуска, на базе грузовиков общего назначения, специально приспособленных для этих целей машин, соответственно самосвалов, изотермических фургонов и цистерн.
Перевозка грузов цистернами, история которых началась в середине 30-х годов прошлого века, позволяет решать транспортные задачи по перемещению, в основном, наливных грузов. Однако при кажущейся простоте, перевозка грузов цистернами, на самом деле, имеет ряд тонкостей и нюансов. Дело в том, что для каждого из наливных грузов, даже однотипных, требуются отдельные, специально для них модифицированные цистерны. Например, сырую нефть и бензин, или другие продукты переработки нефти, перевозить в одинаковых цистернах нельзя. Не говоря уже о молоке, или, скажем, о живой рыбе, так как перевозка и этого груза, осуществляется именно в цистернах. Перевозка грузов цистернами, осуществляется, в подавляющем большинстве, цистернами с типичными характеристиками. Можно указать основные из них:
• емкость от 15 до 40 тыс. л;
• длина от 13,7 до 16,1 м;
• масса в пределах 4,5-6 т;
• от 1 до 5 отсеков в цистерне;
• рабочее давление до 25 кг/см. куб;
• цистерны оснащаются пневматической или рессорной подвеской, в зависимости от типа груза.
• для загрузки автоцистерн применяются два способа: верхний (через заливную горловину) и нижний (через специальный фланец). Разгрузка выполняется нижним методом.
В зависимости от перевозимых грузов
цистерны могут быть разделены на две группы:
- общего назначения – для перевозки широкой номенклатуры нефтепродуктов;
- специальные – для перевозки отдельных видов грузов.
Цистерны общего назначения
, в свою очередь могут подразделяться на:
- цистерны для перевозки светлых (бензин, лигроин и т.п.);
- тёмных (нефть, минеральные масла и т.п.) нефтепродуктов.
Повышенная огнеопасность светлых нефтепродуктов при ненадёжной герметичности нижних сливных приборов обусловила оборудование цистерн для их перевозки устройствами верхнего слива (через колпак). Цистерны для тёмных нефтепродуктов оборудовались нижними сливными приборами.
Такое разделение парка цистерн общего назначения уменьшает трудоёмкость и продолжительность операций по очистке внутренних поверхностей котлов перед наливом грузов, отличающихся от ранее перевозимых. Однако из-за этого разделения повышается порожний пробег цистерн, увеличивается простой под накоплением на сортировочных станциях порожних цистерн и осложняется регулировка парка цистерн.
В связи с созданием нижнего сливного прибора, обеспечивающего надёжную герметичность затворов, все цистерны общего назначения железных дорог СНГ имеют такие приборы.
Специальные цистерны
разделяются на цистерны для перевозки:
- вязких грузов;
- пищевых продуктов (молоко, патока, спирт, вина);
- кислот (азотная, соляная, серная и др.);
- сжиженных газов (пропан, аммиак, и др.);
- затвердевающих (пек, капролактан и др.);
- некоторых других грузов.
Специфические особенности различных кислот, газов и тому подобных грузов обуславливают соответствующие видоизменения внутри перечисленных подгрупп. Поскольку специальные цистерны строят в сравнительно небольшом количестве и обычно на тех заводах, что и цистерны общего назначения, они для удобства эксплуатации, ремонта и постройки имеют унифицированные с цистернами общего назначения рамы, узлы крепления котла, ходовые части и многие другие элементы.
На железных дорогах СНГ массу жидкого груза, перевозимого в цистерне, определяют не взвешиванием, как в других типах вагонов, а замерно-калибровачным способом. Для этого измеряют высоту наполнения котла, учитывают плотность груза, а затем посредством специальных таблиц калибровки, в которых приведена ёмкость котла в зависимости от уровня его налива, подсчитывают массу груза. Ликвидация операций взвешивания ускоряет оборот цистерн и снижает себестоимость перевозок.
Для возможности применения замерно-калибровочного способа цистерны различаются калибровочным типом, который обозначен металлическими цифрами, приваренными к котлу на обеих сторонах его цилиндрической части.
В зависимости от вида несущих элементов
цистерны разделяют на конструкции, у которых все основные действующие на вагон нагрузки воспринимаются рамой кузова, и конструкции, у которых эти нагрузки воспринимаются котлом, - безрамные цистерны.
Кроме того, цистерны подобно другим типам вагонов различаются по осности, грузоподъёмности, объёму котла, устройству, материалу и способу изготовления котла и другим признакам.
Технические требования к цистернам регламентированы ГОСТ 10674-75.
Примером специализированной цистерны является автоцистерна БЦМ-139 (молоковоз) вместимостью 16000 л. (4 отсека по 4000 л.), которая предназначена для перевозки пищевых жидкостей.
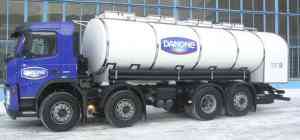
Рис. 6. Автоцистерна БЦМ-139 (молоковоз).
В технологическом шкафу в задней части цистерны БЦМ-139 установлены насос, счетчик, пеноотделитель, автономный отопитель, сливные трубопроводы с запорной арматурой, блок пневмоуправления донными клапанами. Теплоизоляция технологического шкафа минеральной ватой толщиной 50-70 мм. Обогрев технологического шкафа осуществляется автономным отопителем. Топливный бак отопителя вынесен за пределы технологического шкафа. Производительность – 30000 л/час.
Контрольно-измерительная аппаратура молоковоза БЦМ-139 выполняет следующие функции:
- автоматическое отключение насоса при заполнении отсека;
- блокировка молочного насоса при превышении верхней границы температуры молока;
- возможность передачи результатов измерений через спутник в формате GPS;
- измерение количества полученного молока с выводом результата на дисплее бортового компьютера;
- измерение средней температуры молока;
- печать результатов измерения;
- промывка сосуда собственным или посторонним насосом;
- регистрация в памяти результатов измерений;
- суммирование количества собранного молока.
5.
Перечень средств механизации погрузочно-разгрузочных и транспортных работ в СХК «Атлашевский» Чебоксарского района ЧР
В СХК «Атлашевский» Чебоксарского района ЧР для погрузочно-разгрузочных и транспортных работ применяет следующую технику:
- трактор КамАЗ ХТХ-215и трактор КамАЗ ХТХ-85- многофункциональные тракторы, которые пригодны и для полевых работ;
- РТМ-160 – вывозит навоз с МТФ;
- МТЗ-82 и Т-16 – применяются для раздачи кормов;
- МТЗ-80 – занимается погрузкой и перевозкой кормов;
- Т-160К – выполняет бульдозерные работы, перевозит разные грузы;
- МТЗ 1221 – вывозит мусор и навоз;
- ГАЗ-53, КамАЗы 55102 – занимаются транспортировкой всех видов грузов;
- ГАЗ САЗ-3307 – заправщик дизельным топливом;
- ГАЗ САЗ-3307 – выкачивает воду и навозную жижу.
Машинно-тракторный парк СХК «Атлашевский» оснащен всеми необходимыми средствами техники. Ежегодно происходит его обновление новой техникой, в среднем на 2 единицы.
Список использованной литературы
1. Учебник по устройству автомобиля: Учебник /В.А. Молоков, С.Ф. Зеленин.- М.: "РусьАвтокнига", 2000г. – 80с.;
2. Организация автомобильных перевозок: Учебник / Афанасьев Л.Л., Цукерберг М.С. - М.: Транспорт,1982u/ - 202c/;
3. Грузовые автомобильные перевозки: Учебник / Лейдерман С.Р. - М.: Транспорт,1970 – 152c.;
4. Использование транспорта в сельском хозяйстве: Учебник / Миронюк С.К. – М.: Колос, 1982. – 287с.;
5. Транспортные и погрузочно-разгрузочные средства: учебник для вузов. Под ред. С.А. Ширяева. – М.: Горячая линия – Телеком, 2007. – 848с.
|