Зміст
Вихідні дані
Вступ
1.Енергосиловий та кінематичний розрахунок
1.1 Визначення потрібної потужності привода
1.2 Вибір електродвигуна
1.3 Кінематичний та силовий розрахунок привода
2. Розрахунок клинопасової передачі
3. Розрахунок черв’ячної передачі
3.1 Вибір матеріалу
3.2 Допустимі напруження
3.3 Проектний розрахунок
3.4 Перевірний розрахунок
4. Проектування валів
4.1 Розрахунок валів з умови кручення
4.2 Вибір типа та схеми розташування підшипників
4.3 Ескізна компоновка редуктора
4.4 Вибір матеріалу валів
4.5 Розрахунок валів на статичну міцність та опір втомі тарозрахунок підшипників на витривалість
5. Розрахунок з’єднань
5.1 Шпонкові з’єднання
5.2 З’єднання з натягом
6. Тепловий розрахунок редуктора
7. Остаточна компоновка редуктора
8. Пристрої для натягу пасу передач та рама привода
Література
Вихідні дані
Завдання ДМ 4.2-3
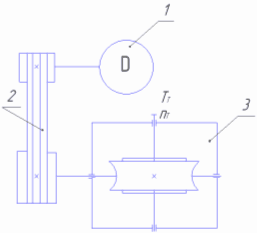
Склад привода: 1 – електродвигун; 2 – клинопасова передача; 3 – редуктор черв’ячний
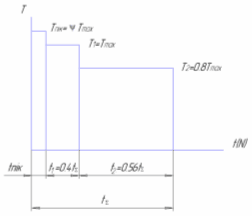
Обертовий момент Тт
=255Нм
Частота обертання nт
=75 хв-1
Термін використання L=6років
Коефіцієнти використання – річний Кр=0,55, добовий Кд=0,75, перевантаження ψ=1,8
Вступ
Значення машин для людського суспільства надзвичайно велике. Машини максимально підвищують продуктивність праці, сприяють поліпшенню якості продукції, що виготовляється, і зниженню її собівартості. У сучасній промисловості машинобудуванню належить провідна роль, оскільки на базі машинобудування розвивається решта всіх галузей промисловості, будівництва і сільського господарства. Рівень виробництва машин, ступінь їх технічної досконалості - основні показники розвитку всіх галузей народного господарства, основа технічного прогресу держави і добробуту суспільства.
Всяка машина складається з деталей. Деталь - виріб, виготовлений з однорідного по найменуванню і марці матеріалу без застосування складальних операцій (вал, гайка, кришка і т.п.). Комплекс спільно працюючих деталей, об'єднаних загальним призначенням і по конструкції тих, що є відособлену одиницю, називається складальною одиницею (муфта, редуктор, рама). Складальні одиниці і деталі, у свою чергу, утворюють комплекси (намотувальний пристрій, транспортер, робоча кліть). Деталі, складальні одиниці і комплекси утворюють готові вироби, що підлягають виготовленню (прокатний стан, продольно-строгальний верстат).
При конструюванні і виготовленні нових машин економічні показники повинні завжди стояти на одному з перших місць. Вартість машини, визначувана витратами на матеріали, виготовлення і збірку, повинна бути мінімальною. Габарити і маса машини в значній мірі визначаються її кінематичною схемою і компоновкою складників. Компоновка деталей і вузлів повинна бути такій. щоб можливо більш повно використовувався робочий простір несучих деталей (рам, станин, корпусів).
Величезне значення для здешевлення машин при одночасному підвищенні якості має стандартизація. Широке впровадження взаємозамінних деталей машин значно полегшує збірку машин і дозволяє використовувати для їх виготовлення більш передові методи масового і потокового виробництва, що дозволяє отримати великий економічний ефект.
Автоматизація роботи машини не тільки сприяє підвищенню продуктивності, поліпшенню якості роботи, але і до мінімуму знижує вплив людського чинника.
1. Енергосиловий та кінематичний розрахунок
1.1 Визначення потрібної потужності привода
При довгостроковому постійному або незначному змінному навантаженні, яке притаманне компресорам, конвеєрам, транспортерам та іншим механізмам, розрахункова потужність електродвигуна Р'д
(кВт) привода визначається через потужність на вихідному валу привода Рт
(кВт), яка може бути задана або визначена по тяговому зусиллю F (Н), коловій швидкості стрічки V (м/с), або обертовому моменту Тт
(Нм), кутовійшвидкості вала ωт
хв-1
.
(1.1)
де

РТ
=1,047·10-4
·255·75=2,0 кВт
η– загальний ККД привода
(1.2)
де η1
, η2
– ККД окремих передач привода
ηп
, ηпк
– ККД відповідно пасової передачі та підшипників кочення однієї пари
k – число валів або пар підшипників
η1
=0,95; η2
=0,8; ηп
=0,98; ηпк
=0,99; k=3
η=0,95·0,8·0,98·0,993
=0,72
кВт
1.2 Вибір електродвигуна
Для привода конвеєра і інших механізмів широко використовують асинхронні коротко замкнуті електродвигуни серії 4А виконання М1081, М1081 по ГОСТ 19523-81 потужністю від 0,55 до 30кВт та синхронними частотами обертання ротора nд
с
від 750 до 3000 хв-1
перенавантаження дорівнює:
(1.3)
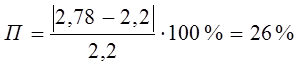
що перевищує 12% які допустимі при змінному навантаженні привода. Тому вибираємо двигун з потужністю Рд
=3кВт
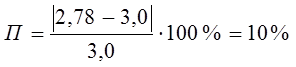
При сталій потужності двигуна із збільшенням частоти обертання його розміри, маса та вартість зменшуються, а ККД зростає. Однак із збільшенням частоти обертання, робочий ресурс двигуна зменшується, а передаточне число привода, його маса, габаритні розміри і вартість зростають. Для приводів загального призначення, якщо немає спеціальних вказівок, перевагу слід віддати двигунам з частотою обертання 1500 та 1000хв-1
.
Вибираємо nс
д
=1000хв-1
, це двигун 1М1081 4А112М6У3, потужністю Рд
=3кВт з частотою обертання nд
= 950хв-1
, коефіцієнтом пускового та максимального перенавантаження ψпуск
=2,0; ψmax
=2,2(ГОСТ 19523-81)
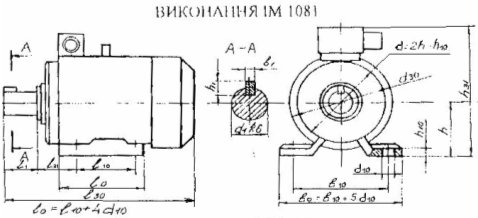
Мал. 1.1. Ескіз електродвигуна
d30
=260мм
l1
=80мм
l30
=452мм
d1
=32мм
b1
=10мм
h1
=8мм
l10
=140мм
l31
=70мм
d10
=12мм
b10
=190мм
h=112мм
h10
=12мм
h31
=310 мм
1.3Кінематичний та силовий розрахунок привода
Розрахункове загальне передаточне число привода U' визначаємо із співвідношення частот обертання вала двигуна nд
та вихідного вала привода nд
:
(1.4)
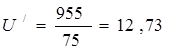
Виходячи із розрахункового значення загального передаточного числа U'=U'п
·U'р
визначимо попереднє передаточне число редуктора:
(1.5)
Вибираємо передаточне число клинопасової передачі по ГОСТ 17383-73 Uп
=2
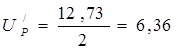
Узгодимо передаточне число редуктора з нормальним рядом чисел по ГОСТ 2144-76: Up
=6,36
Загальне передаточне число привода
UП
=U/Up
=12,73/6,3=2,0
U=UП
· UТ
=6,3·2,0=12,6
Відхилення передаточного числа не повинно перевищувати 4%
(1.6)

Визначимо частоти обертання валів привода, потужностей та обертових моментів, що передаються валами
а) Вал електродвигуна – вал ведучого шківа пасової передачі:
Навантаження розрахункове
Потужність РД
=2,78
Частота обертання nс
д
=1000хв-1
Обертовий момент Тд
(1.7)

б) Вхідний вал редуктора – вал веденого шківа пасової передачі – вал черв’яка редуктора:
Рш
=Р'д
·ηп
·ηпк
=2,78·0,95·0,99=2,61 кВт
(1.8)
хв-1
Тш
=Тд
·Uп
· ηп
·ηпк
=27,8·2,0·0,95·0,99=52,3 Н·м
в) Тихохідний вал редуктора – вал черв’ячної шестерні:
Рт
=Рш
·η1
·ηпк
=2,61·0,95·0,99=2,45 кВт
(1.9)
хв-1
Тт
=Тш
·Uш
· η1
·ηпк
=52,3·6,3·0,95·0,99=310 Нм
Ресурс роботи привода
t∑
=L·365·k·24·kc
(1.10)
t∑
=8·365·0,55·24·0,75=28908 годин
Таблиця 1.1 Розрахункові дані параметрів привода.
Номер вала |
Частота обертання, хв-1
|
Потужність,кВТ |
Обертовий момент, Н·м |
Передаточне число |
D |
nа
д
=955 |
Рд
′=2,78 |
Тд
=27,8 |
Uп
=2,0 |
Ш |
nш
=477,5 |
Рш
=2,61 |
Тш
=52,3 |
Т |
nт
=75,8 |
Рт
=2,0 |
Тт
=310 |
Uт
=6,3 |
2. Розрахунок клинопасової передачі
Вибираємо переріз пасу А, тому мінімальний діаметр ведучого шківа dmin
=90мм. Для підвищення довговічності пасу діаметр ведучого шківа приймаємо D1
=112мм.
Розрахуємо розрахунковий діаметр веденого шківа
D'2
=D1
·U=112·2=224мм (2.1)
Зі стандартного ряду вибираємо D2
=224мм
Розрахуємо колову швидкість паса
(2.2)
м/с
Шківи виготовляємо з чавуну СЧ15 т.к. колова швидкість V<30м/с
Розрахуємо орієнтовану міжосьову відстані. Двигун встановлюємо на полозки, тому
а=1,5(D1
+D2
)=1,5(112+224)=504мм
Знайдемо потрібну довжину пасу
(2.3)
мм
Приймаємо стандартну довжину пасу Lp
=1600мм
Розрахуємо дійсну міжосьову відстань, яка відповідає прийнятій стандартній довжині пасу:
(2.4)
де Δ1
=0,5π(D1
+D2
)=0,5·3,14(112+224)=527
та Δ2
=0,25(D2
-D1
)2
=0,25(224-112)2
=3136
тому
мм
Для регулювання міжосьовий відстані застосовуємо установку двигуна з ведучим шківом на полозках враховуючи що:
для установки та зміни пасів повинна бути передбачена можливість зменшення міжосьової відстані на 2% від довжини пасу, тобто 20мм;
для компенсації відхилень від номіналу довжин пасів і його витяжки за час експлуатації повинна бути передбачена можливість збільшення ад на 6% від довжини пасу.
Визначимо кут обхвату на ведучому шківі
(2,5)

Знайдемо число пробігів пасу
(2.6)
де =20с-1
– допустиме число пробігів пасу
- умова виконується.
Розрахуймо допустиму потужність при заданих умовах роботи передачі для одного клинового пасу
(2.7)
де Р0
– допустима потужність для одного паса певного перерізу у дослідних умовах (D1
=D2
;α1
=α2
=180°, базова довжина пасу L0
та спокійне навантаження)
Обираємо Р0
=1,15 (при типі пасу А, базовій довжині пасу L0
=1700мм, діаметрі шківа D1
=112мм )
Cα
– коефіцієнт, що враховує вплив кута обхвату на тягову здатність;
Са
=1-0,003(180°
-а1
)
Са
=1-0,003(180°
-168°
)=0,964
СL
– коефіцієнт, що враховує вплив довжини пасу на довговічність;
(2.8)
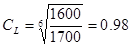
ΔPзг
– поправка, що враховує зменшений вплив напружень згину пасу на веденому шківі на довговічність із збільшенням передаточного числа
(2.9)
де ΔТЗГ
– поправка до моменту на ведучому шківі, який може передати пас за рахунок зниження напружень згину на веденому шківі в залежності від передаточного числа.
ΔТЗГ
=1,1
∆Рзг
=10-4
·1,1·477,5=0,052
Cр – коефіцієнт режиму роботи Ср=0,8
кВт
Визначаємо необхідне число клинових пасів
(2.10)
де Р1
– потужність на ведучому шківі
Сz
– коефіцієнт числа пасів у комплекті Сz
=0,95
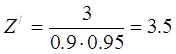
Приймаємо Z=4шт.
Визначаємо навантаження на вал:
(2.11)
де F0
– сила попереднього натягу паса з урахуванням додаткового натягу паса від відцентрових сил
(2.12)
де qm
– маса 1м довжини паса qm
=0,105кг/м (переріз А)

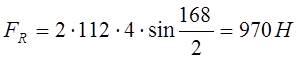
Розрахуємо колову силу
(2.13)
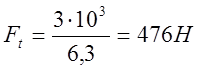
Перевіримо міцність пасу за умовою:

де σmax
– максимальне напруження пасу
[σ]р
=10МПа – допустиме напруження пасу
(2.14)
де σр
– напруження розтягу (з урахуванням напружень від дії відцентрових сил)
σЗГ1
– напруження згину
(2.15)
де А – площа перерізу пасу А=81мм2
МПа
(2.16)
де ЕЗГ
=100МПа – модуль пружності матеріалу пасу при згинанні
у0
=2,8мм (для перерізу А)
МПа

Розрахуємо ресурс передачі
(2.17)
де σlim
=9…10МПа – обмежена границя витривалості пасу при базі випробувань N0
=107
циклів навантажень
m=8 – показник ступеня кривої втоми
СЗГ
– коефіцієнт, що враховує різний ступінь впливу напружень згину у пасі на ведучому та веденому шківах
(2.18)
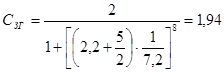
Zш
=2 – число шківів в передачі;
[th
]=1000год. – мінімальний ресурс передачі.
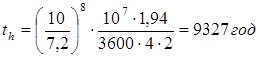
3. Розрахунок черв’ячної передачі
3.1 Вибір матеріалу
Черв’яки виробляють зі сталей, які дозволяють отримати після термообробки велику міцність (Н ≥ 45HRC) робочих поверхонь витків, наприклад, сталь 45, 40Х, 40ХН, 12Х2Н4А та інші.Черв’ячні колеса виготовляють із бронзи і чавунів. Матеріал черв’ячного колеса назначаємо в залежності від швидкості ковзання.Швидкість ковзання.
,м/с(3.1)
де n1
– частота обертання черв’яка, об/хв.;Т2Н
– обертовий момент, Н·м.
n1
= 477,5 об/хв., Т2Н
= 310 Н·м.
м/с
Так как 5 > > 1м/с – матеріал черв’ячного колеса безоловяніста бронза (Бр. АЖ 9-4)
σ =400 МПа,
σТ
= 200 МПа.
3.2 Допустимі напруження
Допустимі напруження для сірого чавуна
(3.2)
МПа

Допустимі напруження при згині для колеса


3.3 Проектний розрахунок
Розраховуємо міжосьову відстань за формулою:
,мм (3.3)
де q– коефіцієнт діаметру черв’яка, приймаємо q=10 ;
Z2
– число зубів черв’ячного колеса.
При ≤ 3 м/с =1,0
Відносно "U" призначаємо z1
так, щоб витримати z1
=1, 2, 4; 28 ≤ z2
≤ 63 ( 80 ); U=12,6 (вихідні дані).
Принимаем U=12,5; z1
=4
Розраховуємо число зубів черв’ячного колеса за формулою:
z2
=U · z1
(3.4)
z2
=12.5 · 4 = 50
28<50<63 – умова виконується.
мм
Узгоджуємо по ГОСТ 2144-76
Приймаємо = 50 мм.
Розраховуємо модуль за формулою:
,мм (3.5)
мм
Розраховуємо коефіцієнт діаметру черв’яка за формулою:
(3.6)
= 10,6
12,5 > 10,6 – умова виконується.
Підбираємо m і q по таблиці2.3 за умовою-1 ≤ X≤ 1, де
(3.7)

-1 < 0,95 < 1 – умова виконується.
Приймаємо m = 2,5 мм; q =10.
При х > 0
(3.8)

(3.9)

Розраховуємо начальний діаметр черв’яка за формулою:
(3.10)
мм
мм
Розраховуємо ділильний діаметр черв’ячного колеса за формулою:
d2
=m · z2
,мм(3.11)
d2
= 2,5 · 50 = 125 мм.
Розраховуємо діаметр впадини черв’яка за формулою:
, мм(3.12)
мм
Розраховуємо діаметр впадини черв’ячного колеса за формулою:
,мм(3.13)
мм
Розраховуємо діаметр вершини витків черв’яка за формулою:
, мм(3,14)
мм
Розраховуємо діаметр вершини витків черв’ячного колеса за формулою:
, мм(3.15)

Розраховуємо найбільший діаметр черв’ячного колеса за формулою:
, мм(3.16)

Розраховуємо довжину нарізаної частини черв’яка :
При z1
=4;
, мм(3.17)
мм
(3.18)

(3.19)
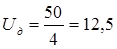
(3.20)
UГОСТ
=12,5

0 < 4% - умова виконується.
Розраховуємо коефіцієнт корисної дії передачі:
(3.21)
де кут тертя, вибираємо з табл. 2.4
Таблица 3.1 – Кут тертя між стальним черв’яком і венцем колеса
Vs
, м/с |
 |
Vs
, м/с |
 |
0,5 |
3°10' - 3°40' |
3 |
1°30' - 2°00' |
1,0 |
2°30' - 3°10' |
4 |
1°20' - 1°40' |
1,5 |
2°20' - 2°50' |
7 |
1°00' - 1°30' |
2,0 |
2°00' - 2°30' |
10 |
0°55' - 1°20' |
2,5 |
1°40' - 2°20' |
15 |
0°50' - 1°10' |
Приймаємо =3°20'

Розраховуємо колову швидкість черв’яка за формулою:
(3.22)
м/с
(3.23)

Визначаємо швидкість ковзання за формулою:
(3.24)
=0,95
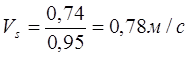
σ =280МПа
Розраховуємо колову, радіальну і осьову сили в зачепленні:
(3.25)
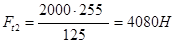
(3.26)

(3.27)

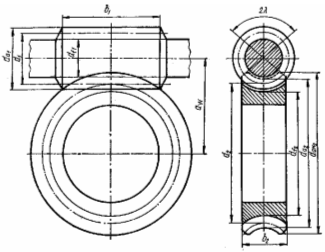
Мал. 3.1. Схема зачеплення черв’ячної передачі
3.4 Перевірний розрахунок
Розраховуємо дійсне контактне напруження за формулою:
(3.28)

254 МПа < 400 МПа – умова виконується.
Розраховуємо максимальне дійсне контактне напруження за формулою:
(3.29)
Т2Н
max
= Тт
/ 0,8 =310 / 0,8 = 387,5 Н·м

284 МПа < 400 МПа – умова виконується.
Розраховуємо дійсне напруження згину за формулою:
(3.30)
YFN
– вибираємо з таблиці 3.1 в залежності від
(3.31)
(3.32)

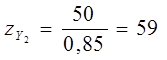
ПриймаємоYFN
=1,4

29,6 МПа < 400 МПа – умова виконується.
Розраховуємо максимальне дійсне напруження згину за формулою:
(3.33)

37 МПа < 400 МПа – умова виконується.
4.Проектування валів
4.1Розрахунок валів з умови кручення
Розрахунок виконується за умов:
- міцність на кручення
; (4.1)
- зниженого умовного допустимого напруження кручення в межах пропорційно відносної навантаженості вала
- забезпечення осьової фіксації деталей, що розміщуються на валу.
Швидкохідний вал
Діаметр консольної ділянки
(4.2)
де Тш
– момент на швидкохідному валу редуктора
мм.
Округляємо до d=17мм.
Діаметр вала під підшипник
(4.3)
де t=2мм – розмір висоти бурта.
dП
=17+2·2=21мм
Приймаємо dп
=20мм.
Діаметр бурта під підшипник
(4.4)
де r=1,6мм – радіус галтельного переходу
dбп
=20+3,2·1,6=25,12 мм
Приймаємо dбп
=25мм.
Так як діаметр вершин зубців черв’яка dа1
=34,75 мм, менше за 2dбп
, то черв’як виконуємо сумісно з валом.
Тихохідний вал
Діаметр консольної ділянки
(4.5)
де Тт
– момент на тихохідному валу редуктора

Округляємо до d=40мм.
Діаметр вала під підшипник
(4.6)
де t=1,7мм – розмір висоти бурта
dП
=40+2·1,7=43,4 мм
Приймаємо dп
=45мм.
Діаметр бурта під підшипник
(4.7)
де r=3мм – радіус галтельного переходу
dбп
=45+3,2·3=53,6 мм
Приймаємо dбп
=55мм.
Діаметр вала під колесо
(4.8)
Приймаємо dк
=55мм.
Діаметр бурта під колесо
(4.9)
де f=1,6мм – розмір факи
dбк
=55+3·1,6=59,8 мм
Приймаємо dбп
=60мм.
4.2 Вибір типа та схеми розташування підшипників
В опорах валів встановлюємо роликові радіально-упорні конічні однорядні підшипники. На швидкохідному валу встановлюємо підшипники середньої серії за схемою "у розпір. На тихохідному валу встановлюємо підшипники легкої серії за схемою "у розпір".
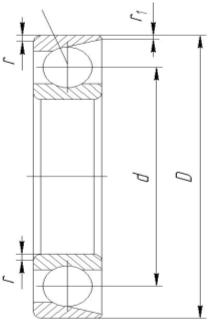
Мал. 4.1. Ескіз підшипників кочення
Таблиця 4.1.Вибір підшипників
Вал |
№ |
D |
d |
B |
r |
r1
|
Сr
|
Со
r
|
Швидкохідний |
46304 |
52 |
20 |
19 |
2 |
1,0 |
14,0 |
9,17 |
Тихохідний |
36209 |
85 |
45 |
19 |
2,0 |
1,0 |
32,3 |
25,6 |
4.3 Ескізна компоновка редуктора
Відстань між колесом і внутрішньою поверхнею корпуса редуктора

Відстань між маточиною колеса і внутрішньою поверхнею корпуса приймаємо g=8мм
Відстань між опорами черв’яка приймаємо
l1
=da
м
2
=137мм
Довжина консольної ділянки швидкохідного вала по ГОСТ 12081-72 приймаємоl=36мм
Довжина консольної ділянки тихохідного вала по ГОСТ 12081-72 приймаємо l=82мм
Довжина маточини черв’ячного колеса
lм
=1,2dк2
=1,2·55=66мм
приймаємо lм
=70мм
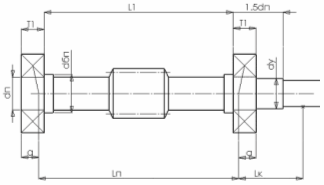
Мал. 4.2. Ескізна компоновка швидкохідного валу
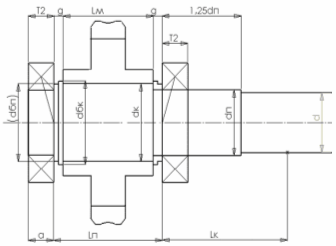
Мал. 4.3. Ескізна компоновка тихохідного валу
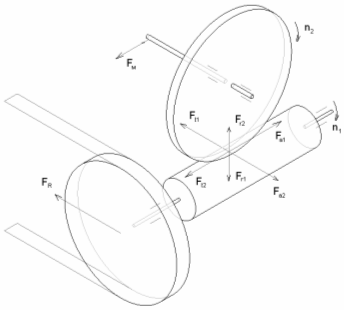
Мал. 4.4. Схема сил у зачепленнях
4.4 Вибір матеріалу валів
Швидкохідний вал виконаний заодно ціле з черв’яком.
Матеріал виготовлення: сталь 40Х ГОСТ 4543-71 з послідуючою термообробкою – поліпшення (НВ270…320) та гартування СВЧ до отримання твердості HRC 48…53. В цьому випадку σт
=750МПа;
σв
=900МПа; τт
=450МПа; σ-1
=410МПа; τ-1
=240МПа; ψτ
=0,10
Тихохідний вал виготовляємо зі сталі 40Х ГОСТ 4543-71 з послідуючим поліпшенням до отримання твердості НВ270…320. В цьому випадку σт
=750МПа; σв
=900МПа; τт
=450МПа; σ-1
=410МПа; τ-1
=240МПа; ψτ
=0,10
4.5 Розрахунок валів на статичну міцність та опір втомі та розрахунок підшипників на витривалість
Розрахунок на статичну міцність
Швидкохідний вал
Реакції опор
В вертикальній площині
∑М3
=0
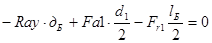

∑М1
=0
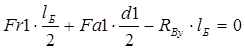

Перевірка
∑У=0
RB
У
-Fr1-Raу=0
874,87-138,72-(-512,32)=0
MX1
=0

MX3
=0

Реакції опор
В горізонтальній площині
∑М3
=0
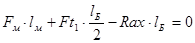

∑М1
=0

RBX
=[-Ft
1
·(lБ
/2)+FМ
·(lМ
+lБ
)]/ lБ
RBX
=[-4080·134/2+970·(41,3+134)]/134=-771,189
Перевірка
∑Х=0
RА
X
- RBX
- Ft
1
+ FМ
=2338,84-(-771,189)+970-4080=0
Будуємо епюру згинаючих моментів
МУ1
=0
МУ2
=- RА
X
(lБ
/2)=-2338,84·134/2=-156700
МУ3
= - FМ
·l=-4080·175,279=-170021
Будуємо епюру згинаючих моментів
МК
=( Ft
1
·d1
)/2=4080·29,8/2=60690
Сумарні опорні реакції


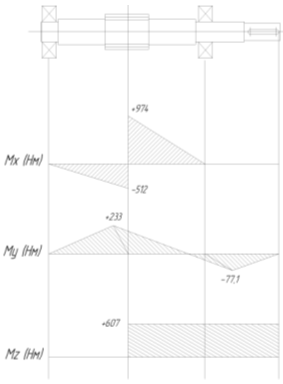
Подбіраємо підшипник по перший опорі.
Підшипник шариковий радіально-упорний 46304.
d=20мм, D=52мм, В=15мм, r=2,0 r1
=1,0, Cr
=14, Cor
=9,17
Визначаємо еквівалентне навантаження.
Рэ
=(XVFr
1
+YFa
)·Кб
·Кт
(4.10)
де- Fr
1
=816; Fa
= 3400; V=1; Кб
=1; Кт
=1.
Відношення - величина соответствует е=0,68
Відношення >е; Х=0,41; Y=0,87
Рэ
=(0,41·1·816+0,87·3400)·1·1=2958Н
Розрахункова довговічність, млн.об
(4.11)
, млн.об
Розрахункова довговічність, ч
(4.12)
, ч
Тихохідний вал.
Вертикальна площа
∑М4
=0

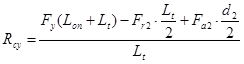

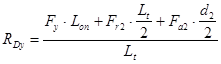

Перевірка
∑У=0
Fу
-Rc
у
- Fr2
- FD
2
=0
1996,1-4390,33-1387+3781,44=0
Будуємо епюру.
Мх2
= Fу
·Lon
Мх2
=1996·175,28=349858
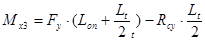

Мх4
=0

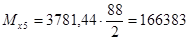
Горизонтальна площа
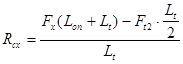

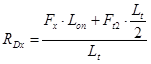

Fх
-Rc
х
- Ft
2
+ FDx
=0
3457,3-4756,79-4080+5379,44=0
Строємо епюру
Му2
= - Fx
∙ lоп
Му2
= - 3457 ∙ 175,88 = - 293873
Му3
= - Fx
∙ (lоп
+ ) + Rсх

Му3
= - 3457∙ (175,88 + ) + 4756,72 = - 236696
Му4
= 0
Строємо епюру крутних моментів
Мк
= Мr
= 
Мк
= Мr
= = 255000
Визначаємо реакціі
Rc
= 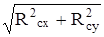
Rc
= = 6473.18
RD
= 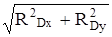
RD
= = 6575,658
Сумарні згинальні моменти
М2
= 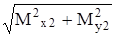
М3
= 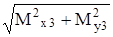
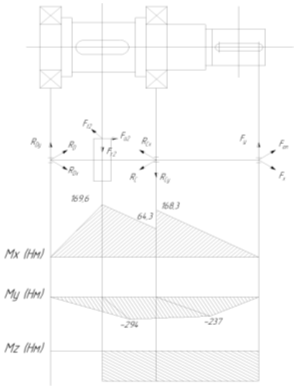
Вибираємо підшипник – радіально упорний по ГОСТ 831-75 легкоі серіі 36209. d = 45мм D = 85 мм B = 19 мм α = 12° Cr
= 32,3 Co
= 25,6
Відношення = = 0,059
Відношення = = 0,248 < l тому X = 1 Y = 0
Рэ
= Rd
∙ V ∙ Кб
∙ Кт
= 6575,685 ∙ 1 ∙ 1 ∙ 1 = 6575,685
Розрахунок довговічності, мм
L = ( )3
= = 137 мм
Розрахунок довговічності в годинах
Lh
= = = 30000 год.
Для зубчастих редукторів приймаємо ресурс роботи підшипників від 30 тис (такий ресурс самого редуктора) до 10 тис ( такова допустима довговічность підшипника).
Перевірка міцності шпонкових з’єднань.
В редукторі застосовуємо шпонки призматичні з округленими торцями. Розміри перерізу шпонок і пазів; довжина шпонок по СТ СЭВ 189-75.
Матеріал шпонок: Сталь 45 нормалізована.
Напругу змиття і умову міцності визначаємо по формулі:
(4.13)
Призначаємо напругу змиття:
при стальній ступиці [σ] = 110 – 190 Н/мм2
при чавунній ступиці [σ] = 50 – 70 Н/мм2
Вал черв’яка:
Діаметр Ø 17 мм b×h = 5×5; Глибина паза t1
= 3; Довжина l = 20 мм; Момент Тзг
= 52,3 Н·м
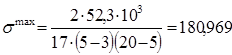 < 190 [σ]
Вал відомий.
З двох шпонок – під шестерню та на вихідному валу, найбільш напружена шпонка на вихідному валу (менший діаметр вала, тому й менші розміри поперечного перерізу шпонки).
Діаметр вала d = 40 мм; b×h = 17×8; Глибина паза t1
= 5; Довжина l1
= 45 мм; Момент Тзг
=255 Н·м
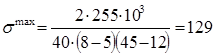 < 190 [σ]
Розрахунок валів
Швидкохідний вал
Розміри поперечних перерізів ,прийнятих при конструюванні, значно перевищують ті, могли бути одержані при розрахунку на кручення.
Перевірка стріли прогину
Приведений момент інерції в поперечному перерізі черв’яка
Јпр
= (4.14)
Јпр
= 1827,1мм4
стріли прогину
ƒ = (4.15)
ƒ = 0,021
припустимий прогин
[ƒ] = (0,005… 0,01) m
[ƒ] = (0,013…0,025)
Вал під шестерню
Матеріал –сталь 45, термообробка – улучення. При діаметру заготовки до 100 мм середне значення σв
= 780н/мм2
Границя витривалості при симетричному циклі вигіну
σ-1
= 0,43·σв
(4.16)
σ-1
= 0,43·780=335н/мм2
Границя витривалості дотичним напруженням при симетричному циклі
=0,58· σ-1
(4.17)
τ-1
=0,58·335=193 н/мм2
Переріз А-А
Концентрацію напружень викликає шпоночка канавка.
Кσ
= 1,75
К τ
= 1,6
ε σ
≈ετ
=0,63
ψσ
=0,15
ψ τ
= 0,1
Крутний момент Мкр = 255 Нм
Згинальний момент в горизонтальної площини
М2 = 3393,35Нмм
В горизонтальної площини
М = 245280 Н мм
Суммарний крутний момент
М= (4.18)
М = = 245303,75 Нмм
Момент скручувальний
d= 55
b×h = 16 × 10 t1
=6 l1
=60
Wк нетто
= (4.19)
Wк нетто
= 32608,5
Wнетто
= (4.20)
W нетто
= 16282,783
Амплітуда і середня напруга цикла дотичним напруженням визначаємо по формулі:
τ-υ
= τ-
m
= (4.21)
τ-υ
= τ-
m
= 3,91н/мм2
Амплітуда нормальних напруг вигіну
σ-υ
= (4.22)
σ-υ
=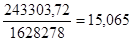
Коефіцієнт запаса міцності по нормальним напруженням
nσ-1
= (4.23)
nσ-1
=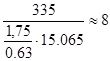
Коефіцієнт запаса дотичним напруженням
n = (4.24)
n = 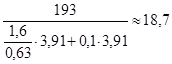
Результуючий коефіцієнт запаса міцності для перерізу А-А
n= (4.25)
n=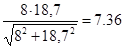
Переріз К – К .
Концентрація напруги обумовлена посадкою підшипника з гарантованим натягом.
 Ψσ
= 0,15 Ψτ
= 0,1
Згинальний момент М2
= 339335 Н·м
Момент опору
W = (4.26)
W = = 12265,625
Амплітуда нормального напруження
σ = σmax
= = = 27,67
σм
= 0
Полярний момент опору
Wp
= 2 · W(4.27)
Wp
= 2 · 12265,625 = 24531,25
Амплітуда і середня напруга цикла :
(4.28)
= 6,916
Коефіцієнти запасу міцності при нормальному напруженні
nσ
= (4.29)
nσ
= = 3,027
Коефіцієнти запасу прочності при касательних напруженнях:
nτ
= (4.30)
nτ
= = 9,622
Підсумковий коефіцієнт запасу міцності для перерізу К – К :
nτ
= (4.31)
nτ
= = 2,888
Переріз Л – Л
Концентрація напруги обумовлена переходом від Ø 50 до Ø 40:
При = = 1,25 и = = 0,063
Коефіцієнти концентрації напруження
Кσ
= 1,75; Кτ
= 1,6
εσ
= ετ
= 0,85
Внутрішні силові фактори:
Осьовий момент опору перерізу
W = (4.32)
W = = 6280
Амплітуда нормального напруження
συ
= = 54,034 
Полярний момент опору
Wp
= 2 · 6280 = 12560
Амплітуда і середня напруга цикла :
= 13,509
Коефіцієнти запасу міцності для перерізу Л – Л:
nσ
= = 3,011
nτ
= = 7,207
Підсумковий коефіцієнт запасу міцності для перерізу Л – Л :
nτ
= = 2,77
Переріз Б – Б:
Концентрація обумовлена приналежністю шпоночної канавки :
Кσ
= 1,75; Кτ
= 1,7
εσ
= ετ
= 0,85
F = (4.33)
При Fx
= 3457; Fy
= 1996,1
F = = 3976,98 Н
Згинальний момент при Х = 25:
МБ-Б
= F · х (4.34)
МБ-Б
= 3976,98 · 25 = 99427,382 Н·мм
Момент опору перерізу приb×h = 12×8; t1
= 5; l = 45 мм:
W = (4.35)
W = = 6253,75
Амплітуда нормальних напружень згину:
συ
= (4.36)
συ
= = 15,898 
Момент опору крученню нетто:
WК нетто
= = 12533,75
Амплітуда і середня напруга цикла :
= 10,173
Коефіцієнти запасу міцності для перерізу Б – Б:
nσ
= =10,235
nτ
= = 9,57
Підсумковий коефіцієнт запасу міцності для перерізу Б – Б :
nτ
= = 6,99
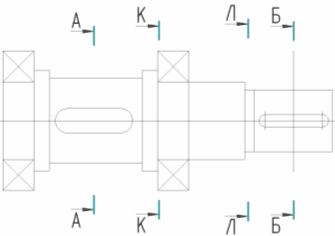
5. Розрахунок з’єднань
5.1 Шпонкові з’єднання
З’єднання на швидкохідному валу (вал – шків пасової передачі)
Назначаємоматеріал шпонки: Сталь 6 ГОСТ 380-94
По ГОСТ 23360-78 встановлюєморозмірипризматичної шпонки із закругленими краями: b´h=5х5.
Розрахункова довжина шпонки
(5.1)
де: h – висота шпонки
t1 – глибина шпонкового пазу
σсм
– допустиме напруження зминання, для чавунної маточини
σсм
=80 МПа
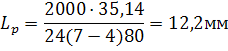
Приймаємо довжину L=Lp+b=12,2+5=17,2мм, зі стандартного ряду L=18мм
Посадка шпонки:на валу: h9, до шківа:JS9
З’єднання на тихохідному валу(вал – черв’ячне колесо)
Назначаємоматеріал шпонки: Сталь 6 ГОСТ 380-94
По ГОСТ 23360-78 встановлюєморозмірипризматичної шпонки із закругленими краями: b´h=16х10.
Розрахункова довжина шпонки
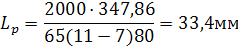
Приймаємо довжину L=Lp+b=33,4+16=49,4мм, зі стандартного ряду L=50мм
Посадка шпонки:
на валу: h9, до шківа: JS9
З’єднання на тихохідному валу(консольна ділянка)
Назначаємоматеріал шпонки: Сталь 6 ГОСТ 380-94
По ГОСТ 23360-78 встановлюєморозмірипризматичної шпонки із закругленими краями: b´h=12х8.
Розрахункова довжина шпонки
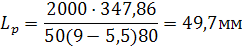
Приймаємо довжину L=Lp+b=49,7+12=61,7мм, зі стандартного ряду L=63мм
5.2 З’єднання з натягом
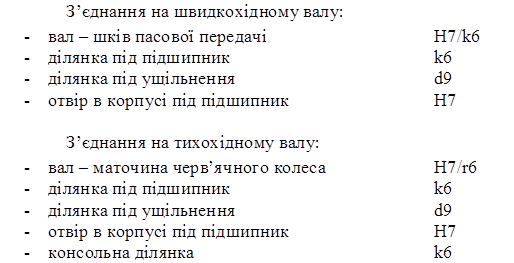
6. Тепловий розрахунок редуктора
При роботі редуктора втрата потужності, за рахунок тертя в зачепленні та підшипниках, перемішуванням та розбризкуванням масла, приводять до нагрівання деталей редуктора та масла. При нагріванні в'язкість масла різко падає, що приводить до порушення режиму змащення. Нормальна робота редуктора буде забезпечена, якщо температура масла не перевісить допустиму.
При сталому режимі роботи редуктора усе тепло віддається через стінки повітрю що його оточує. Умова роботи редуктора без перегріву:
(6.1)
де tм – температура масла
tп
=20°С – температура повітря
kt
=17Вт/(м2
·°С) коефіцієнт теплопередачі
F=0,6 – коефіцієнт сталості роботи
А=0,421м2
- площа тепловіддающої поверхні корпуса редуктора
[Δt] =120°С – для масла авіаційного

7. Остаточна компоновка редуктора
Використовуючи креслення ескізної компоновки валів конструктивно оформлюємо інші деталі редуктора – черв’ячний вал, черв’ячне колесо, корпус, підшипникові вузли тощо.
Змазка зачеплення та підшипників – розбризкуванням рідкого масла, залитого до корпусу до рівня центра нижнього ролика підшипника. На валу черв’яка встановлюємо крильчатки; при роботі редуктора вони будуть розбризкувати масло та закидати його на колесо та в підшипники.
Відстань між крильчаткою та внутрішньою поверхнею корпуса

Ущільнення валів забезпечуємо резиновими манжетами. Для обох валів використовуємо манжети І типу ГОСТ 8752-79:
dxDxH
х40х8
х70х10
В нижній частині корпуса викреслюємо пробку для спуску масла та масловказівник.
Для редукторів товщину стінки розраховуємо за формулою

мм
Обираємо δ=6мм.
Корпус робимо нероз’ємним (aw
<150мм) с двома вікнами на бокових стінках, через яки при зборці вводять до корпусу комплект вала з черв’ячним колесом. Для зручності складання діаметр отвору вікна робимо більшим за діаметр шестерні.
D=dam
2
+2·c=137,25+2·5=147,25 мм
Приймаємо D=150мм
Посадка бокових кришок перехідна та приєднується до корпусу гвинтами d=8мм. Відстань між гвинтами

Діаметр кришки Dк
=D+(4…4,5)d=150+4·8=182мм.
Діаметр приливу Dф
=Dк
+4…6мм=182+4=186мм.
Щоб кришка була достатньо жорсткою її виконуємо досить високою =0,1·182=18мм з шістьма ребрами.
Для контролю зачеплення та заливу масла на горі робимо люк з вмонтованою віддушиною.
Для швидкохідного вала використовуємо накладні кришки.
Посадка бокових кришок перехідна 25 та приєднується до корпусу чотирма гвинтами М8.
Діаметр кришки Dк
=D+(4…4,5)d=25+4·8=57мм.
Діаметр приливу Dф
=Dк
+4…6мм=57+5=62мм
8. Пристрої для натягу пасу передач та рама привода
Для регулювання натягу пасів клино-пасової передачі привода використовують пристрій натягу, який забезпечує зміну міжосьової відстані в межах аф
, де λ – довжина пасу.
Натяг пасів регулюється зміною положення двигуна відносно редуктора та іноді за допомогою натяжного ролика.
Двигун переміщується на полозках або на обертовій плиті.
Розміри полозків вибирають з урахуванням розмірів болтів закріплення електродвигуна привода.
Рама привода виготовляється литою або зварною із швелерів.
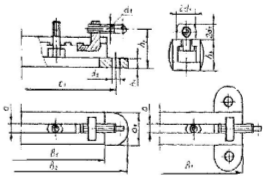
Рисунок 8.1 – Ескіз полозків для регулювання міжосьової відстані пасової передачі
Таблиця 8.1 – Основні розміри полозків пристрою натягу.
Типполозків |
Маса комплекта |
Болти |
а |
а1
|
b1
|
b2
|
c1
|
d1
|
d2
|
h1
|
h2
|
h3
|
C-4 |
18 |
45 |
430 |
510 |
470 |
М12 |
14 |
18 |
55 |
45 |
5,3 |
М12х40 |
Швелер та косі шайби під болти вибираємо виходячи із розрахункової ширини полки.
В = 2,2 d10
+ r + R + S,
де d10
– діаметр отвору для болта кріплення редуктора до рами;
r, R, S – розміри швелера приймаємо відповідно (3,5,8).
В = 2,2 · 12 + 3 + 5 + 8 = 42,4 мм.
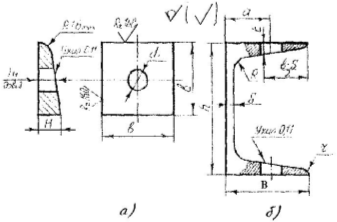
Рисунок 8.2 – Деталі конструкції рами привода: а) коса шайба; б) швелер.
Таблиця 8.2 – Основні розміри косої шайби та швелера
Діаметр болта мм |
Розміри косої шайби, мм |
№ швелера |
Розміри швелера з нахилом ГОСТ 8240-72, мм |
d1
|
H1
|
H |
b |
h |
B |
S |
t |
R |
r |
a |
12 |
13-0,43
|
5 |
5 |
25 |
10 |
100 |
50 |
4,8 |
7,5 |
7 |
3 |
30 |
Література
1. Методичні вказівки до виконання курсового проекту з дисципліни "Деталі машин" для студентів заочної, дистанційної та денної форм навчання/ Укл.: Е. Т. Білий, О. П. Ляшенко – Запоріжжя: ЗДТУ, 2000 – 85 с.
2. Методичні вказівки до розрахунку та проектування пасової передачі з дисципліни "Деталі машин" для студентів заочної, дистанційної та денної форм навчання/ Укл.: Вільчек О. І. , Глушко В. І., Камель Г. І – 2-е вид. перероб. і доп. – Запоріжжя: ЗДТУ, 2003 – 18 с.
3. Методические указания по расчету червячных передач редукторов общего назначения по дисциплине "Детали машин и ПТМ" для студентов специальностей 0502. 0503. 0504 всех форм обучения/ Сост. А. И. Вильчек, В. Г. Суворов, - Запорожье: ЗМИ, 1988. – 12 с.
4. Шейнблит А. Е. Курсовое проектирование деталей машин: Учеб. Пособие для техникумов. – М.: Высш. шк., 1991. – 432 с., ил.
5. Орлов П. И. Основы конструирования: Справочно-методическое пособие. В 2-х кн. Кн. 2. Под ред. П. Н. Учаева. – 3-е изд., исправл. – М.: Машиностроение, 1988. – 544 с., ил.
6. Курсовое проектирование деталей машин: Учеб. Пособие для техникумов/С. А. Чернавский, К. Н. Боков и др. – М.: Машиностроение, 1979, - 351 с., ил.
7. Конструкция и расчет зубчатых редукторов. Справочное пособие. Кудрявцев В. Н., Державец Ю.А., Глухарев Е. Г.Л., "Машиностроение". 1971 г. 328 стр. Табл. 107. 274. Библ. 144 назв.
8. Зубчатые и червячные передачи. Голованов Н. Ф., Гинзбур Е. Г., Фирун Н. Б., 1967г., 516 стр.
9. Гжиров Р. И. Краткий справочник конструктора: Справочник – Л.: Машиностроение, Ленингр. отд-ние, 1983. – 464 с., ил.
|