СОДЕРЖАНИЕ
ВВЕДЕНИЕ
1 ОСНОВНЫЕ ПРОЕКТНЫЕ РЕШЕНИЯ И УСЛОВИЯ РЕКОНСТРУКЦИИ
1.1 Физико-географические характеристики района строительства
1.1.1 Климат
1.1.2 Рельеф. Растительность и почвы
1.1.3 Инженерно-геологические условия
1.1.4 Местные и привозные дорожно-строительные материалы
1.2 Экономическая и транспортная характеристика
1.3 Основные технологические нормативы и показатели дороги
2 СТРОИТЕЛЬНЫЕ РЕШЕНИЯ
2.1 Подготовка территории строительства
2.1.1 Отвод и рекультивация земель
2.2 Малые искусственные сооружения
2.3 Пересечения и примыкания
2.4 Земляное полотно
2.5 Дорожная одежда
2.6 Расчет объемов дорожной одежды
2.7 Обстановка дороги
3 ПРОЕКТ ПРОИЗВОДСТВА РАБОТ И ОРГАНИЗАЦИЯ СТРОИТЕЛЬСТВА
3.1 Основы организации строительства
3.2 Подготовительные работы
3.2.1 Восстановление и закрепление трассы на местности
3.2.2 Расчистка полосы отвода
3.3 Проект производства работ по строительству малых искусственных сооружений
3.3.1 Подготовительные работы
3.3.2 Устройство котлована
3.3.3 Устройство фундаментов
3.3.4 Монтаж звеньев и оголовков
3.3.5 Устройство гидроизоляции
3.3.6 Засыпка трубы
3.3.7 Укрепительные и отделочные работы
3.4 Проект производства работ по возведению земляного полотна
3.4.1 Возведение насыпи с разработкой грунта экскаваторами и транспортировкой а/самосвалами
3.4.1.1 Область применения
3.4.1.2 Указания по технике безопасности
3.4.1.3 Указания по организации труда
3.4.2 Технологическая карта устройства уширения земляного полотна
3.4.2.1 Область применения
3.4.2.2 Организация и технология производства работ
3.4.2.3 Технико-экономические показатели
3.4.2.4 Материально-технические ресурсы
3.4.2.5 Техника безопасности
3.4.3 Технологическая карта на устройство выемки глубиной до 5 м экскаватором
3.4.3.1 Область применения
3.4.3.2 Организация и технология производства работ
3.4.3.3 Технико-экономические показатели
3.4.3.4 Материально-технические ресурсы
3.4.3.5 Техника безопасности
3.5 Проект производства работ по строительству дорожной одежды
3.5.1 Технологическая карта на устройство двухслойного основания
3.5.1.1 Область применения
3.5.1.2 Указания по технологии производственного процесса
3.5.1.3 Устройство нижнего слоя основания
3.5.1.4 Устройство верхнего слоя основания
3.5.1.5 Технический контроль при строительстве оснований
3.5.1.6 Технико-экономические показатели
3.5.1.7 Материально-технические ресурсы
3.5.2 Технологическая карта на устройство асфальтобетонного покрытия
3.5.2.1 Область применения
3.5.2.2 Указания по технологии производственного процесса
3.5.2.3 Подготовка основания
3.5.2.4 Устройство асфальтобетонного покрытия
3.5.2.5 Установка копирных струн
3.5.2.6 Подготовка асфальтоукладчика к работе
3.5.2.7 Правила управления асфальтоукладчиком
3.5.2.8 Укладка асфальтобетонной смеси
3.5.2.9 Уплотнение асфальтобетонной смеси
3.5.2.10 Начальное укатывание
3.5.2.11 Промежуточная укатка
3.5.2.12 Технико-экономические показатели
3.5.2.13 Материально-технические ресурсы
3.5.2.14 Контроль качества
4 ОРГАНИЗАЦИЯ РАБОТ В ДОРОЖНО-СТРОИТЕЛЬНОМ ОТРЯДЕ
4.1 Составление линейного календарного графика реконструкции
4.2 Численный состав дорожно-строительного отряда
5 ТЕХНИКО-ЭКОНОМИЧЕСКИЕ ПОКАЗАТЕЛИ ОРГАНИЗАЦИИ РЕКОНСТРУКЦИИ И СМЕТНО-ФИНАНСОВЫЕ РАСЧЕТЫ
6 ДЕТАЛЬ ПРОЕКТА. ОБНОВЛЕНИЕ АСФАЛЬТОБЕТОННЫХ ПОКРЫТИЙ
6.1 Способы обновления асфальтобетонных покрытий
6.2 Требования к материалам
6.2.1 Асфальтобетоны
6.2.2 Влажные органоминеральные смеси (ВОМС)
6.2.3 Асфальтогранулобетоны
6.3 Конструирование и расчет дорожной одежды
6.4 Подбор состава асфальтогранулобетона
6.4.1 Отбор пробы
6.4.2 Выбор типа АГБ
6.4.3 Приготовление смесей
6.4.4 Изготовление образцов и подготовка их к испытанию
6.4.5 Подбор состава АГБ
6.5 Технологические схемы производства работ
6.6 Фрезерование
7 ОХРАНА ОКРУЖАЮЩЕЙ СРЕДЫ
7.1 Оценка природных условий
7.2 Воздействие на животный и растительный мир
7.3 Мониторинг в процессе эксплуатации автомобильной дороги
СПИСОК ИСПОЛЬЗОВАННЫХ ИСТОЧНИКОВ
ВВЕДЕНИЕ
Для перспективного развития автомобильно-дорожного транспорта требуется постоянное совершенствование направления в области проектирования, строительства и эксплуатации дорог.
Прогресс в строительстве автомобильных дорог связан с рядом крупных проблем: всестороннее исследование и изучение грунтов, законов воднотеплового режима земляного полотна, способ его регулирования; совершенствования расчета дорожных одежд и способов комплексного конструирования земляного полотна, широкое изучение минеральных материалов и подробное исследование органических вяжущих; исследование технологии строительства асфальтобетонных покрытий; разработка научных основ дорожного машиностроения в области создания машинороботов и др.
С вводом в 2003 году закона Российской Федерации №110 Ф3 изменились источники формирования доходов в территориальный дорожный фонд. Основным источником формирования собственных доходов территориального дорожного фонда являлся транспортный налог, акцизы на нефтепродукты, земельный налог.
В связи с принятием Земельного кодекса в 2001 году не определен порядок представления земельных участков для строительства, реконструкции автодорог, мостовых переходов. Из-за несогласованности Министерств Российской Федерации (Министерство природных ресурсов РФ и Министерство имущества РФ) не определен порядок предварительного согласования земельных участков – стадия проектно-изыскательских работ. Согласно постановления Правительства РФ №278, от 29.04.02 года были значительно повышены базовые размеры платы за перевод лесных земель в нелесные и за изъятие земель лесного фонда.
Сохранялся высокий уровень задолженности в территориальный дорожный фонд – 246 млн.рублей, составляющий практически третью часть бюджета ТДФ.
Ненадежность новых финансовых источников и отсутствие ритмичного ежемесячного поступления доходов осложнили расчеты с подрядчиками и оказали негативное воздействие на их финансовое состояние (сокращение объемов работ, сокращение численности дорожных организаций, потеря квалифицированных рабочих.).
Одной из проблем содержания автомобильных дорог, является недостаточная оснащенность подрядных организаций соответствующей дорожно-строительной техникой и, прежде всего на зимнее содержание.
Необходимо создать условия для формирования требуемого объема территориального дорожного фонда, позволяющие осуществлять стабильное финансирование дорожных работ по содержанию и нормативному ремонту существующей сети, реконструкции и строительству автодорог и мостов с максимальным использованием имеющихся дорожных и мостовых предприятий республики.
В сентябре текущего года были организованны и проведены в соответствующих структурных подразделениях Федерального дорожного агентства рассмотрение предложений федеральных управлений автомобильных дорог, управлений автомобильных магистралей, межрегиональных дирекций по дорожному строительству, дирекций по строительству и реконструкции автомобильных дорог, функциональных центров и дирекций по проектировкам программы дорожных работ, выполняемых за счет средств федерального бюджета, и смет доходов и расходов по бюджетным средствам на 2006 год и среднесрочный период до 2008 года.
Настоящий регламент разработан в целях обеспечения качественного и своевременного формирования проекта программы дорожных работ на среднесрочный период 2006 - 2008 годы, а также обеспечения реализации подпрограммы «Автомобильные дороги» федеральной целевой программы «Модернизация транспортной системы России (2002-2010 годы)».
В целях реализации подпрограммы «Автомобильные дороги» федеральной целевой программы «Модернизация транспортной системы России (2002 – 2010 гг)» и принятой Правительством Республики Карелия программы развития и совершенствования сети автомобильных дорог Республики Карелии
В настоящее время реализуется территориальная целевая программа «Региональная Программа развития и совершенствования сети автомобильных дорог Республики Карелия до 2010 года с прогнозом на 20-летний период», часть средств, из которых инвестируется из федерального бюджета.
Республика Карелия имеет выгодное расположение в плане транзитного сообщения с развитыми областями Северо-запада и Финляндией, членом ЕЭС, а также морскими портами Балтийского и Баренцева морей. Создание межрегиональных транспортных коридоров имеет важное экономическое значение для Северо-запада России. Ведущими отраслями промышленности данного региона являются: лесная, деревообрабатывающая, металлообрабатывающая, нефтяная и газовая. Вся северо-западная экономическая территория развивается как сырьевой и энергетический источник европейской части России.
Дорожный Комитет совместно с правительством Республики Карелия принимает активное участие в разработке и внедрении международного проекта «Коридор» в области развития автодорожных путей сообщения.
Как основное направление в 9-м транспортном коридоре «Урал – С.Петербург с выходом к государственной границе России с Финляндией» первоочередным включен южный вариант по территории Республики Карелия с прохождением трассы «Пудож – Петрозаводск _ Пряжа – Леметти _ Сортавала _ Лахденпохья – Приозерск с выходом к госгранице в Вяртсиля и Сювяоро».
В настоящее время проводится работа по следующим направлениям межрегиональных транспортных связей:
·Мурманская область – Республика Карелия – Вологодская область
·Мурманская область – Республика Карелия – Архангельская область
·Мурманская область – Республика Карелия – Ленинградская область
·через Сортавалу в Приозерск
·через Ошту в Вытегру
·через Ревсельгу в Подпорожье.
Основными выходами к государственной границе с перспективным развитием пограничным пунктов пропуска определены следующие:
·г. Петрозаводск – а/д «Пряжа – Леметти», а/д «Олонец – Сортавала», а/д «С.Петербург – Сортавала» - выход к упрощенному пункту пропуска Сювяоро Лахденпохского района и международному пункту пропуска Вяртсиля г.Сортавала;
·а/д «Кочкома – Тикша – Ледмозеро – Костомукша – Госграница» - выход к международному пункту пропуска Люття г.Костомукша;
·а/д «Кемь – Лонка» - выход к упрощенному пункту пропуска Лонка Калевальского района;
·а/д «Лоухи – Суоперя» - выход к упрощенному пункту пропуска Суоперя Лоухского района.
Главной задачей Дорожного Комитета является сохранение существующей дорожной сети общего пользования, улучшение ее состояния и повышение безопасности движения.
Основная деятельность по содержанию, ремонту и строительству (за счет федерального бюджета) выполняется в соответствии с территориальной целевой программой.
1 ОСНОВНЫЕ ПРОЕКТНЫЕ РЕШЕНИЯ И УСЛОВИЯ РЕКОНСТРУКЦИИ
1.1 Физико-географические характеристики района
Рабочий проект на реконструкцию автомобильной дороги «Вологда – Кириллов – Пудож – Медвежьегорск» км 533 – км 544 разработан ООО «Трансстройпроект» на основании задания, выданного и утвержденного Госкомитетом по строительству, эксплуатации и содержанию автомобильных дорог. Исходными данными послужили материалы полевых изысканий и данные о состоянии существующей дороги.
Проектируемый участок дороги является частью дороги территориального значения «Вологда – Кириллов – Пудож – Медвежьегорск». По техническим показателям плана проектируемый участок дороги соответствует III категории, по нормативам продольного и поперечного профилей, конструкции дорожной одежды существующая дорога относится к IV категории.
В связи с тем, что по природоохранным причинам запрещен молевой сплав леса по реке Водла и Онежскому озеру, практически весь объем расчетной лесосеки 1200000 м3
перевозится автомобильным транспортом из Пудожского района в сторону г. Петрозаводска. Реконструкция участка вызвана возросшей интенсивность движения и неудовлетворительным состоянием дороги. Земляное полотно состоит в основном из невысоких насыпей, обочины просели, откосы размыты. При прохождении по заболоченным участкам существующая дорога имеет просадки земляного полотна. Дорожная одежда на всем протяжении находится в неудовлетворительном состоянии, износ составляет 60-70 %, наблюдаются продольные и поперечные трещины, просадки, выбоины, волны, ямочность, разрушение кромок, что вызывает снижение нормативной скорости движения автотранспорта на 50 %.
Искусственные сооружения представлены: круглыми ж/бетонными трубами диаметром 0,5 м – 1 шт., 1,0 м – 8 шт., 1,5 м – 1шт., прямоугольной ж/б трубой 1,5х2,0 м и двумя мостами, через реку Филиппа Г-8+2х1,5 длиной 58 м, через реку Тамбица Г-8+2х1,5 длиной 24 м. Состояние круглых ж/б труб удовлетворительное, звенья и оголовки в хорошем состоянии, требуется омоноличивание стыков звеньев труб и оголовков, прочистка на входах и выходах от наносов грунта. Прямоугольная ж/б труба на ПК 100+60 находится в удовлетворительном состоянии: незначительное смещение звеньев труб, разрушен правый открылок оголовка на выходе, вход завален грунтом. Труба требует ремонта: восстановление откосных крыльев, омоноличивание стыков и очистка лотков от грунта и грязи.
Существующие железобетонные мосты через р. Филиппа и р. Тамбица подлежат реконструкции в связи несоответствия габаритов, как для дороги III категории. Существующий железобетонный мост через р. Филиппа, длиной 58 метров, габарит моста Г-8+2х1,0 м.; железобетонный мост через р. Тамбица, длиной 36,1 метров, габарит моста Г-8+2х1,0 м. Пролетное строение у мостов состоит из железобетонных балок.
Дефекты существующих мостов:
·Отсутствие водоотводных трубок на пролетном строении;
·Нет силового ограждения на подходах;
·В местах сопряжения а/дороги с мостом просадки;
·Конуса деформированы, оползли, укрепления отсутствуют и заросли травой и кустарником;
·Проезжая часть из а/б покрытия имеет продольные и поперечные трещины, выбоины, ямочность;
·Железобетонные конструкции моста находятся в удовлетворительном состоянии, частично разрушен защитный слой бетона на балках и в местах омоноличивания стыка или балок, оголена арматура, разрушены деформационные швы.
Существующая автодорога пересекает в начале трассы воздушную линию связи 12 проводов, ВЛС 22 провода и 2 провода, ЛЭП-10 кВ. На всем протяжении участка реконструкции справа проходит воздушная линия связи 2 провода, на ПК 115+87 существующую дорогу пересекает ЛЭП-110 кВ. При расширении и поднятии земляного полотна требуется переустройство коммуникаций.
Существующая полоса отвода заросла лесом и кустарником, видимость в плане и продольном профиле ограничена и не соответствует требованиям III технической категории согласно СНиП 2.05.02-85.
По населенным пунктам проектируемый участок не проходит, на ПК 1+60 имеется пересечение влево в п. Пяльма, вправо к складам, ПК 37+50 в лес. Существующие съезды: ПК 0+80, ПК 20+91, ПК 26+50, ПК 47+92, ПК 85+30, ПК 93+55 и ПК 101+95. Автобусные остановки расположены на ПК 3+70 и ПК 4+20 и обслуживают пассажиров из п. Пяльма и п. Тамбица.
1.1.1 Климат
По дорожно-климатическому районированию территория района проложения трассы реконструкции автомобильной дороги относится ко II дорожно-климатической зоне и характеризуется умеренным климатом с продолжительной зимой, прохладным летом, высокой влажностью воздуха, небольшой амплитудой температур.
Средняя годовая температура воздуха +1,50
С, годовое количество осадков – 681 мм, средняя высота снежного покрова – 650 мм, глубина промерзания для суглинистых грунтов – 149 см, для супесчаных грунтов – 181 см.
1.1.2 Рельеф. Растительность и почвы
Участок реконструируемой автодороги расположен в Пудожском и Медвежьегорском районах на землях Пяльмского лесхоза (ПК 0+00 – ПК 61+50) и на землях Медвежьегорского лесхоза (ПК 61+50 – ПК 119+47).
Особенности рельефа района работ обусловлены прохождением проектируемого участка вдоль восточного берега Онежского озера, что предопределяет общий уклон местности и направлении стока.
Для района в целом характерна значительная расчлененность рельефа и большое разнообразие его форм. Ведущими рельефообразующими процессами явились резко дифференцированные тектонические движения и многократные оледенения. Неровности микрорельефа, в основном, обязаны своим происхождением аккумулятивной деятельности ледника и его потоков, создавших формы (Камы, озы, долины стока ледниковых вод), наложенные на разбитый тектоническими разломами, коренной рельеф.
Для района работ характерно наличие озер, болот и небольших по протяженности рек, принадлежащих к бассейну Онежского озера.
Трасса дороги проложена в пределах сравнительно равнинной местности, осложненной невысокими холмами и грядами ледникового происхождения и заболоченными понижениями. Природный рельеф частично спланирован при строительстве автодороги. Тип местности по степени увлажнения – I и II, из за необеспеченного стока наблюдаются заболоченные участки.
Район строительства дороги расположен в зоне тайги, лес преобладает смешанный (ель, сосна, береза, осина). Заболоченные участки покрыты порослями мелкой сосны, ели, а также кустарником. Почвы по трассе представлены подзолами торфяно-глеевыми иллювиально-гумусовыми толщиной от 0,15 м до 0,3-0,4 м на заболоченных участках.
1.1.3 Инженерно-геологические условия
В геологическом строении на исследованном участке реконструируемой автомобильной дороги принимают участие верхнечетвертичные и современные отложения. Распространение встречных разновидностей грунтов приведены на продольном профиле, составленном по оси трассы, и на поперечных профилях трассы автодороги.
Современные отложения представлены насыпными грунтами и торфом. Насыпные грунты проходят по всей длине проектируемого участка, так как трасса максимально совмещена с существующей дорогой. Они представлены песками средней крупности и песками крупными с включениями гравия и валунов до 10 %. Мощность слоя насыпи достигает 5,5 м. Группа разработки грунта по СНиП VI-2-82, т.1.1 от ПК 0+00 до ПК 75+00 – 10б, от ПК 119+47 – 27а.
1.1.4 Местные и привозные дорожно-строительные материалы
Для устройства нижнего слоя основания (на съездах) и укрепления обочин применяется щебеночно-песчаная смесь карьера «Голодай-Гора», состоящая из 70% щебня фракции 20-40 мм и 30% отсевов.
Для основания применяется щебень карьера «Голодай-Гора». Характеристика щебня:
- марка щебня по прочности – 1400
- марка щебня по износу – И-1
- по лещадности – 38,4%
- по морозостойкости – Мрз-50
- механическая прочность в сухом состоянии – 2100-2700 кг/см2
- водопоглощение – 0,24%
- фракции: 20-40 мм и 5-20 мм.
Для усовершенствованного покрытия применяются горячая плотная мелкозернистая смесь типа Б II марки, приготовляемая на АБЗ «Медвежьегорск». Щебень на устройство основания, укрепления обочин с карьера «Голодай-Гора» доставляется ввозным путем с причала «Уя» на причал «Пергуба» Медвежьегорского района и далее автотранспортом на месте работ.
Железобетонные изделия для водопропускных труб предусмотрено доставлять с завода ЖБИ г. Вологда железнодорожным транспортом до ст. Медвежья Гора, далее автотранспортом на место работ.
1.2 Экономическая и транспортная характеристика
Экономика района представлена преимущественно лесозаготовительными и деревообрабатывающими отраслями промышленности. Это обстоятельство обуславливает перевозку лесных грузов тяжелыми автопоездами грузоподъемностью более 20 т. В перспективе ожидается увеличение грузопотока в связи с открытием транспортного коридора «Восток-Запад». Следует иметь в виду, что за последнее время прослеживается устойчивая тенденция увеличения интенсивности движения транспортных средств с осевой нагрузкой 130 кН и более.
По данным Дорожного Комитета Республики Карелия средний годовой рост интенсивности движения таких транспортных средств превышает 10 %.
Динамика роста грузооборота, грузонапряженности и интенсивности движения представлены в таблице 1.1.
Таблица 1.1 Сводная ведомость грузооборота, грузонапряженности и интенсивности движения по реконструируемому участку автодороги Вологда-Кириллов-Пудож-Медвежьегорск.
Наименование перегонов и перспективные сроки |
Грузооборот мин.тн.км |
Интенсивность движения авт/сут с грузоподъемностью транспортных средств |
Интенсив-ность движения авт/сут |
Лег-ковые |
Авто-бусы |
До 2 т |
2-5 тн |
5-12 тн |
12-20 тн |
>20 тн |
1986 год |
2,0 |
55 |
15 |
35 |
193 |
42 |
24 |
3 |
367 |
1990 год |
2,2 |
58 |
20 |
37 |
203 |
44 |
25 |
3 |
390 |
2004 год |
3,2 |
118 |
42 |
69 |
206 |
86 |
60 |
9 |
590 |
2010 год |
3,4 |
203 |
63 |
78 |
152 |
117 |
74 |
13 |
700 |
2015 год |
4,7 |
312 |
88 |
99 |
152 |
149 |
99 |
19 |
918 |
Анализ таблицы 1.1 показывает, что средний рост интенсивности движения составляет 5,1 %. Рост интенсивности движения автомобилей грузоподъемностью более 20 тн составляет 8 %. Средняя грузоподъемность автомобилей – 7,7 %.
Среднегодовая суточная интенсивность движения – 918 авт/сут. Учитывая среднегодовой прирост интенсивности движения 12 %, и расчетный срок эксплуатации 16 лет, приведенная интенсивность движения определяется равной 222,7 ед/сутки.
С учетом перспективы изменения состава движения и концу межремонтного срока доля тяжелых автомобилей (грузоподъемностью 20 тн и более) систематически обращающихся по дороге, составляет 13 %. Поэтому согласно ОДН 218-046 расчетный тип автомобиля – грузовой – А2
.
1.3 Основные технологические нормативы и показатели дороги
Согласно заданию, а также учитывая перспективную интенсивность движения, проект реконструкции участка дороги разработан по нормативам III категории.
Основные параметры, принятые при проектировании:
- расчетная скорость 100 км/час
- наименьший радиус кривой в плане 600 м
- наибольший продольный уклон 50 0
/00
- наименьшие радиусы вертикальных кривых: выпуклой - 12700 м
вогнутой - 3000 м
- наименьшее расстояние видимости встречного автомобиля -350 м
- то же, для остановки 200 м
- ширина земляного полотна 12 м
- ширина проезжей части 7 м
- ширина укрепительных работ 0,5х2
- тип покрытия усовершенствованный капитальный
- искусственные сооружения под нагрузку А-11 и НК-80
- протяжение участка 11,947 км
2 СТРОИТЕЛЬНЫЕ РЕШЕНИЯ
2.1 Подготовка территории строительства
В подготовительный период производится рубка и корчевка леса и кустарника, перенос коммуникаций. Проект переустройства коммуникаций выполнен на основании технических условий и данных полевых изысканий.
2.1.1 Отвод и рекультивация земель
Трасса реконструируемой дороги проложена согласно акта выбора земельных участков. При выборе направления проложения трассы дороги учитывалось максимальное сохранение хозяйственных земель и использование существующего земляного полотна дороги, максимальное сохранение окружающей среды, снижение транспортных расходов, улучшение социально-бытовых и производственных условий близлежащих населенных пунктов и др. условий.
В процессе реконструкции автомобильной дороги требуется отвод земель, как в постоянное, так и во временное пользование (аренду).
Исходя из проложения дороги и запроектированного продольного профиля, а также ширины земляного полотна, элементов обустройства дороги, искусственных сооружений, водоотводных устройств, обеспечения боковой видимости на пересечениях и примыканиях, с учетом уже существующей полосы отвода Дорожного Комитета. Вновь отводятся в постоянное пользование земля общей площадью 10,7 га, занимаются земли Гослесфонда (Медвежьегорский и Пяльмский лесхозы). Существующий отвод (земли Дорожного Комитета) составляет 33,56 га.
Временный отвод (аренда) составляет 7,78 га и необходим для переноса воздушной линии связи, для складирования торфа, грунта и захоронения порубочных остатков. По окончанию строительных работ земли, занимаемые во временное пользование (аренду) подлежат рекультивации с возвратом их в лесное хозяйство.
2.2 Малые искусственные сооружения
Искусственные сооружения в проекте представлены существующими ж/б трубами – 10 шт. и двумя железобетонными мостами, которые отражены в «Ведомости проектируемых искусственных сооружений» (табл.2.1).
Таблица 2.1 Ведомость проектируемых искусственных сооружений
Местоположение |
Наименование водотока |
Расчетный расход, м/сек |
Тип и отверстие сооружения |
Гидравлический режим |
Глубина подпертой воды, |
Количество звеньев |
Длина трубы или моста |
Примечание |
КМ |
ПК |
2 |
11+58 |
перепуск |
б/р |
ж/б труба Д-1,5 |
б/н |
0,4 |
11 |
20,77 |
Удл. влево на 8,77 м |
3 |
21+20 – 21+80 |
р. Филиппа |
Мост Г-8+2* 1,5 |
б/н |
- |
- |
80,0 |
5 |
47+38 |
перепуск |
б/р |
ж/б труба Д-1,0 |
б/н |
0,1 |
12 |
24,54 |
Удл. влево на 8,77 м, вправо 5,77 м |
6 |
52+64 |
перепуск |
б/р |
ж/б труба Д-1,0 |
б/н |
0,1 |
12 |
22,53 |
Удл. влево на 8,80 м, вправо 1,73 |
7 |
67+05 |
перепуск |
б/р |
ж/б труба Д-1,0 |
б/н |
0,2 |
12 |
23,53 |
Удл. влево на 4,76 м, вправо 6,77 м |
8 |
73+54 |
перепуск |
б/р |
ж/б труба Д-1,0 |
б/н |
0,1 |
13 |
25,56 |
Удл. влево на 7,79 м, вправо 5,77 м |
8 |
76+75 |
перепуск |
б/р |
ж/б труба Д-1,0 |
б/н |
0,1 |
11 |
20,80 |
Удл. влево на 5,77 м, вправо 3,03 м |
9 |
81+38 |
перепуск |
б/р |
ж/б труба Д-1,0 |
б/н |
0,3 |
13 |
22,79 |
Удл. влево на 7,79 м |
9 |
89+41 – 89+78 |
р. Тамбица |
мост Г-8+2* 1,5 |
б/н |
- |
- |
37,0 |
11 |
100+60 |
ручей |
0,7 |
ж/б труба Д-1,5*2,0 |
б/н |
0,5 |
26 |
38,60 |
Ремонт |
11 |
103+14 |
перепуск |
б/р |
ж/б труба Д-1,0 |
б/н |
0,3 |
19 |
29,0 |
Ремонт |
11 |
108+80 |
перепуск |
б/р |
ж/б труба Д-1,0 |
б/н |
0,3 |
16 |
28,79 |
Удл. влево на 4,03 м, вправо 4,76 м |
ИТОГО |
12 штук |
145 |
373,91 |
В связи с тем, что существующие водопропускные трубы находятся в хорошем состоянии, в местах поднятия земляного полотна проектом предусмотрено их удлинение. Всего удлиняется ж/б труб диаметром 1.0 м – 7 шт. на 75,54 пм, диаметром 1.5 м – 1 шт. на 8,77 пм. Железобетонная прямоугольная труба отверстием 1,5х2,0 м на ПК 100+60 находится в хорошем состоянии, удлинению не подлежит, проектом предусмотрено выполнение ремонтных работ.
Существующие железобетонные мосты через р. Филиппа и р. Тамбица реконструируются.
2.3 Пересечения и примыкания
Проектом предусмотрено устройство 7 примыканий и одного пересечений.
На ПК 1+20 трасса пересекает узкоколейную железную дорогу Пяльмского леспромхоза, проектом предусмотрена разборка существующего переезда с деревянным настилом и устройство нового переезда с железобетонным настилом. Работы по устройству переезда должны быть выполнены в соответствии с «Инструкцией по эксплуатации железнодорожных переездов» 1997 г., изданной Министерством путей сообщения Российской Федерации.
2.4 Земляное полотно
Проектная линия продольного профиля запроектирована с учетом геологических, гидрологических условий и рельефа местности, рекомендаций РН, СНиП 2.05.02-85.
Руководящая отметка насыпи назначена исходя из условий снегозаносимости и минимального возвышения поверхности покрытия над поверхностью земли на участках с необеспеченным стоком и составляет 1,3 м.
Элементы продольного профиля запроектированы под расчетную скорость 100 км/час, максимальный продольный уклон, примененный при проектировании, составляет 24,42 0
/00
, минимальные радиусы вертикальных кривых: выпуклой – 12800 м, вогнутой – 3700 м.
Наименьшее расстояние видимости встречного автомобиля, исходя из расчетных скоростей, составляет не менее 350 метров.
Ширина земляного полотна принята 12 м, разработано 5 типов конструкции поперечного профиля земляного полотна с привязкой к местным условиям и учитывая требования ТП 503-0-48.87, РН и СНиП 2.05.02-85.
В связи с увеличением платы за перевод лесных земель в нелесные и за изъятие земель лесного фонда на основании Постановления Правительства РФ №278 более чем в 100 раз согласно СНиП 2.05.02-85 п. 4.21 и п. 1.9 крутизна откосов насыпей до 2 метров принята 1:3, при высоте более 2 м – 1:1,5, что влечет за собой экономию строительных материалов, уменьшение объемов земляных работ, а также уменьшает объемы по переустройству коммуникаций.
Для возведения насыпи используются грунты карьеров «Челмужи» и «69 квартал». Карьер «Челмужи» расположен на км 552+200 автомобильной дороги «Вологда-Кириллов-Пудож-Медвежьегорск», влево до 100 м. Полезный слой представлен песками средними (группа грунта по трудности разработки – I, объемный вес – 1,6 т/м3
), согласно СНиП 2.05.02-85 пригодными для возведения насыпи. Остаточные запасы грунта в карьере составляют 130 тыс. м3
. Карьер разрабатывается по лицензии ПТЗ 00326 ТЭ со сроком действия до 31 декабря 2007 года. По окончании строительных работ карьер подлежит рекультивации.
Карьер «69 квартал» расположен на км 533+200 а/д «Вологда-Кириллов-Пудож-Медвежьегорск», в 1,8 км в северо-восточном направлении по грунтовой дороге в сторону поселка Тамбичозеро, полезный слой представлен песками средними с содержанием гравия и гальки 10-15 %, валунов 5-10 %, пригодными для возведения всех слоев насыпи и замены грунта, коэффициент фильтрации составляет более 1 м/сут., группа грунта по трудности разработки – I, объемный вес 1,70 т/м3
. Запасы песчаного материала составляют 55 тыс. м3
. Транспортировка грунта на трассу осуществляется автосамосвалами по существующей дороге. Рабочий проект на разработку и рекультивацию карьера выполнен отделом инженерных изысканий ЗАО ПИ «Карелпроект».
На участках совмещения с существующей дорогой при прохождении через заболоченные места выторфовку производят на полную глубину под уширяемую часть земляного полотна. Отсыпка насыпи до минерального дна производятся дренирующим грунтом.
Коэффициент уплотнения грунта принят 0,98 при коэффициенте относительного уплотнения 1,08.
Откосы земляного полотна укрепляются засевом трав с плакировкой.
Объемы земляных работ подсчитаны по поперечникам с учетом поправок на дорожную одежду, устройство виражей, замену грунта после выторфовки, снятие растительного слоя, отсыпку берм под знаки, потери грунта при транспортировании.
Проектом предусмотрено рыхление существующих откосов и устройство уступов.
Местоположение и объемы работ по отсыпке берм под знаки и нарезке уступов отражены в отдельной ведомости.
Общий объем оплачиваемых земработ составляет 207378 м3
или 17358 м3
на 1 км дороги.
Распределение объемов работ по видам разработки и транспортировки приведено на графиках попикетного распределения земляных масс и в покилометровой ведомости объемов земляных работ.
2.5 Дорожная одежда
Согласно заданию на проектирование в проекте принят усовершенствованный капитальный тип покрытия, дорожная одежда рассчитана на перспективный период 16 лет.
Расчет прочности дорожной одежды произведен под осевую нагрузку автомобилей группы А, приведенная интенсивность движения – 222,7 ед/сутки.
Конструкция дорожной одежды рассчитана согласно «Проектированию нежестких дорожных одежд» ОДН 218.046-01.
Вычисляем суммарное расчетное количество приложений расчетной нагрузки за срок службы:
Для расчета по допускаемому упругому прогибу и условию сдвигоустойчивости:
ΣNр
=0,7Nр
(Кс
/q(Тсл-1)
)Трдг
Кn
(2.1)
Где
Кс
- коэффициент суммирования (табл. П.6.5)
Nр
- приведенная интенсивность на последний год срока службы, авт/сутки
Трдг
- расчетное число расчетных дней в году, соответствующих определенному состоянию деформируемости конструкции
Кn
– коэффициент, учитывающий вероятность отклонения суммарного движения от среднего ожидаемого
ΣNр
=0,7.
222,7(15/1,0414
)145.
1,38=27046 авт.
Исходя из наличия дорожно-строительных материалов в проекте разработана следующая конструкция дорожной одежды
(тип I), которая устраивается на всем реконструируемом участке дороги.
Таблица 2.2 Расчетные параметры дорожной одежды
№ п/п |
Материал слоя |
Высота слоя, см |
Е, по упругому прогиб |
Е, по сдвигу |
Расчет на растяжение при изгибе |
Источники обоснования |
Е, Мпа |
Rо
, Мпа |
a |
m |
1 |
А/б плотный БНД 90/130 |
5 |
2400 |
1200 |
3600 |
9,50 |
5,4 |
5,0 |
Пр.3 |
2 |
А/б пористый БНД 90/130 |
6 |
1400 |
800 |
2200 |
7,80 |
6,3 |
4,0 |
Пр.3 |
3 |
Щебень фракцированный заклинкой из изверж.пород основания |
30 |
250 |
250 |
250 |
Пр.3 |
4 |
Песок крупный гравелистый |
25 |
130 |
130 |
130 |
Пр.3 |
5 |
Песок мелкий |
100 |
100 |
100 |
Пр.2 |
Расчет по допускаемому упругому прогибу.
Рисунок 2.1 Схема конструкции дорожной одежды.
Расчет ведем послойно, начиная с подстилающего слоя по номограмме рис.3.1:
1) Ен
/Ев
=Егр
/Епс
=100/130=0,769
По приложению 1 табл.П.1.1 p=0,6 МПа, D=37 см
hв
/D=hщеб1
/D=25/37=0,68
Епс
общ
/Епс
=0,86
Епс
общ
=0,86.
130=112 МПа
2) Епс
общ
/Ещеб
=112/250=0,448
hщеб
/D=30/37=0,81
Ещеб
общ
/Ещеб
=0,69
Ещеб
общ
=0,69.
250=173 МПа
3) Ещеб
общ
/Еаб1
=173/1400=0,124
hаб1
/D=6/37=0,16
Еаб1
общ
/Еаб1
=0,152
Еаб1
общ
=0,152.
1400=213 МПа
4) Еаб1
общ
/Еаб2
=213/2400=0,09
hаб2
/D=5/37=0,14
Еобщ
/Еаб2
=0,10
Еобщ
=0,10.
2400=242 МПа
Определяем требуемый модуль упругости:
Етр
=98,65[lg(ΣNp
)-3,55] (2.2)
Етр
=98,65[(lg27046)-3,55]=87 МПа
Определяем коэффициент прочности по упругому прогибу:
Кпр
=Еобщ
/Етр
(2.3)
Ктр
=242/87=2,78
Требуемый минимальный коэффициент прочности для расчета по допускаемому упругому прогибу – 1,20.
Следовательно, выбранная конструкция удовлетворяет условию прочности по допускаемому упругому прогибу.
Рассчитываем конструкцию по условию сдвигоустойчивости в грунте.
Действующие в грунте активные напряжения сдвига вычисляем по формуле:
Т=τн
р (2.4)
Для определения τн
предварительно назначенную дорожную конструкцию приводим к двухслойной расчетной модели.
В качестве нижнего слоя модели принимаем грунт (песок мелкий) со следующими характеристиками: Ен
=100 МПа (табл.П.2.5), φ=140
и с=0,004 МПа (табл.П.2.4).
Модуль упругости верхнего слоя модели вычисляем по формуле:
Ев
=Σn
i=1
Еi
hi
/Σhi
(2.5)
Где
n – число слоев дорожной одежды;
Еi
– модуль упругости i-го слоя;
hi
– толщина i-го слоя.
Значения модулей упругости материалов, содержащих органическое вяжущее, назначаем по табл.П.3.2 при расчетной температуре +200
С.
Ев
=[(1200.
5)+(800.
6)+(250.
30)+(130.
25)]/66=327 МПа
По отношениям Ев
/Ен
=327/100=3,27 и hв
/D=66/37=1,78 и при φ=260
с помощью номограммы находим удельное активное напряжение сдвига:
τн
=0,025 МПа
Таким образом:
Т=0,025.
0,6=0,015 МПа.
Предельное активное напряжение сдвига в грунте рабочего слоя определяем по формуле:
Тпр
=сN
*кσ
+0,1γср
zоп
tgφвт
(2.6)
Где:
сN
– сцепление в грунте земляного полотна, МПа, принимаемое с учетом повторности нагрузки (табл.П.2.6 или П.2.8);
кσ
– коэффициент, учитывающий особенности работы конструкции на границе песчаного слоя с нижним слоем несущего основания;
zоп
– глубина расположения поверхности слоя, проверяемого на сдвигоустойчивость, от верха конструкции, см;
γср
– средневзвешенный удельный вес конструктивных слоев, расположенных выше проверяемого слоя, кг/см3
;
φвт
– расчетная величина угла внутреннего трения материала проверяемого слоя при статическом действии нагрузки (табл.П.2.4);
0,1 – коэффициент для перевода в МПа.
Тпр
=0,006.
3+0,1.
0,002.
66.
tg140
=0,021 МПа
Определяем коэффициент прочности по сдвигоустойчивости:
Кпр
=0,021/0,015=1,4 , что больше Ктр
пр
=1,00
Рассчитываем конструкцию на сопротивление монолитных слоев усталостному разрушению от растяжении при изгибе.
Приводим конструкцию к двухслойной модели, где нижний слой модели – часть конструкции, расположенная ниже пакета асфальтобетонных слоев, т.е. щебеночное основание и грунт рабочего слоя.
Ен
=173 МПа;
К верхнему слою относят все асфальтобетонные слои.
Модуль упругости верхнего слоя устанавливают по формуле:
Ев
=Σn
i=1
Ei
hi
/ Σn
i=1
hi
(2.7)
Где:
Еi
– модуль i-го слоя;
hi
– толщина i-го слоя.
Ев
=3600.
5+2200.
6/11=2836 МПа
По отношениям hв
/D=11/37=0,30 и Ев
/Ен
=2836/173=16,4 по номограмме находим определяем σр
`=2,3 МПа.
Расчетное растягивающее напряжение вычисляем по формуле:
σр
= σр
`ркв
(2.8)
σр
=2,3.
0,6.
0,85=1,17 МПа
Вычисляем предельное растягивающее напряжение по формуле:
RN
=Ro
k1
k2
(1-VR
t) (2.9)
Где:
R0
– нормативное значение предельного сопротивления растяжению (прочность) при изгибе при расчетной низкой весенней температуре при однократном приложении нагрузки, принимаемое по табличным данным (табл.П.3.1);
k1
– коэффициент, учитывающий снижение прочности вследствие усталостных явлений при многократном приложении нагрузки;
k2
– коэффициент, учитывающий снижение прочности во времени от воздействия погодно-климатических факторов (табл.3.6);
VR
– коэффициент вариации прочности на растяжение (приложение 4);
t – коэффициент нормативного отклонения (приложение 4).
R0
=7,80 МПа – для нижнего слоя асфальтобетонного пакета.
k1
=а/m
ÖSNр
(2.10)
Где
m – показатель степени, учитывающий свойства монолитного слоя (табл.П.3.1) – 4,0
а – коэффициент, учитывающий различие в реальном и лабораторном режимах растяжения повторной нагрузкой, а так же вероятность совпадения во времени расчетной температуры покрытия и расчетного состояния рабочего слоя по влажности (табл.П.3.1) – 6,3
k1
=6,3/4
Ö27046=0,491
t=1,39; k2
=0,80
Отсюда
RN
=7,8.
0,491.
0,8(1-0,1.
1,39)=2,64 МПа
Находим коэффициент прочности
Кпр
= RN
/sr
=2,64/2,19=1,21, что больше чем Кпр
тр
=1,00
Вывод: Выбранная конструкция удовлетворяет критериям прочности.
Проверка на морозоустойчивость.
1. По приложению 5 табл.5.1 назначаем для каждого слоя коэффициент теплопроводности.
Таблица 2.3 Коэффициенты теплопроводности дорожной одежды.
Материал |
Толщина слоя hод
, м |
Коэффициент теплопроводности lод
|
Плотный а/б |
0,05 |
1,40 |
Пористый а/б |
0,06 |
1,25 |
Щебень фракцированный |
0,30 |
1,86 |
Песок гравелистый |
0,25 |
Талый – 1,74
Мерзлый – 2,32
|
2. Определяем глубину промерзания по карте (рис.4.4), для Карелии – 1,4 м, и по формуле:
Zпр
=Zпр
ср
1,38 (2.11)
Zпр
=1,4.
1,38=1,93»2 м
Для глубины промерзания 2 м по номограмме (рис.4.3) находим величину пучения для кривой (песок мелкий – II группа, слабопучинистая) – lп(ср)
=1 см.
3. Далее находим поправочные коэффициенты
Уровень грунтовых вод от поверхности, - 0,8 м
Кугв
=0,7 (рис.4.1)
Кнагр
=0,81 (рис.4.2)
Квл
=1,0 (табл.4.6)
Кгр
=1,0 (табл.4.5)
Кпл
=1,0 (табл.4.4) при Купл
=1,01-0,98
Тогда
lпуч
=lпуч(ср)
Кугв
Кнагр
Квл
Кгр
Кпл
(2.12)
lпуч
=1.
0,7.
0,81.
1,0.
1,0.
1,0=0,57 см
Согласно табл.4.3,
l
доп
=4 см, что больше полученного нами, следовательно, данная конструкция дорожной одежды не требует дополнительного морозозащитного слоя.
Анализ выполненных расчетов позволяет сделать вывод, что принятая конструкция дорожной одежды имеет запасы прочности, сопротивлению сдвигу и сопротивлению растяжению при изгибе.
В качестве альтернативного варианта разработана следующая конструкция дорожной одежды.
Она также будет устраиваться на всем протяжении участка дороги.
Таблица 2.4 Расчетные параметры дорожной одежды
№ п/п |
Материал слоя |
Высота слоя, см |
Е, по упругому прогиб |
Е, по сдвигу |
Расчет на растяжение при изгибе |
Источники обоснования |
Е, Мпа |
Rо
, Мпа |
a |
m |
1 |
А/б плотный БНД 90/130 |
12 |
2400 |
1200 |
3600 |
9,50 |
5,4 |
5,0 |
Пр.3 |
2 |
Черный щебень, уложенный по способу заклинки |
15 |
600 |
600 |
600 |
Пр.3 |
3 |
Щебеночная/гра-вийная смесь с максимальным размером зерен С5
-40 мм (ГОСТ 25607) |
25 |
260 |
260 |
260 |
Пр.3 |
4 |
Песок мелкий |
100 |
100 |
100 |
Пр.2 |
Расчет по допускаемому упругому прогибу.
Рисунок 2.2 Схема конструкции дорожной одежды.
Расчет ведем послойно, начиная с подстилающего слоя по номограмме рис.3.1:
2) Епс
общ
/Ещгс
=100/260=0,385
hщгс
/D=25/37=0,68
Ещгс
общ
/Ещеб
=0,57
Ещгс
общ
=0,57.
260=148 Мпа
3) Ещгс
общ
/Ечщ
=148/600=0,247
hчщ
/D=15/37=0,41
Ечщ
общ
/Ечщ
=0,38
Ечщ
общ
=0,38.
600=228 Мпа
4) Ечщ
общ
/Еаб
=228/2400=0,095
hаб
/D=12/37=0,32
Еобщ
/Еаб
=0,17
Еобщ
=0,16.
2400=408 Мпа
Определяем требуемый модуль упругости:
Етр
=98,65[(lg27046)-3,55]=87 Мпа
Определяем коэффициент прочности по упругому прогибу:
Ктр
=408/87=4,69
Требуемый минимальный коэффициент прочности для расчета по допускаемому упругому прогибу – 1,20.
Следовательно, выбранная конструкция удовлетворяет условию прочности по допускаемому упругому прогибу.
Рассчитываем конструкцию по условию сдвигоустойчивости в грунте.
Действующие в грунте активные напряжения сдвига вычисляем по формуле 2.4.
Для определения τн
предварительно назначенную дорожную конструкцию приводим к двухслойной расчетной модели.
В качестве нижнего слоя модели принимаем грунт (песок мелкий) со следующими характеристиками: Ен
=100 Мпа (табл.П.2.5), φ=140
и с=0,004 Мпа (табл.П.2.4).
Модуль упругости верхнего слоя модели вычисляем по формуле 2.5.
Значения модулей упругости материалов, содержащих органическое вяжущее, назначаем по табл.П.3.2 при расчетной температуре +200
С.
Ев
=[(1200.
12)+(600.
15)+(260.
25)]/52=575 Мпа
По отношениям Ев
/Ен
=575/100=5,75 и hв
/D=52/37=1,405 и при φ=260
с помощью номограммы находим удельное активное напряжение сдвига:
τн
=0,024 Мпа
Таким образом:
Т=0,024.
0,6=0,0144 Мпа.
Предельное активное напряжение сдвига в грунте рабочего слоя определяем по формуле 2.6.
Тпр
=0,006.
3+0,1.
0,002.
52.
tg140
=0,021 Мпа
Определяем коэффициент прочности по сдвигоустойчивости:
Кпр
=0,021/0,0144=1,46 , что больше Ктр
пр
=1,00
Рассчитываем конструкцию на сопротивление монолитных слоев усталостному разрушению от растяжении при изгибе.
Приводим конструкцию к двухслойной модели, где нижний слой модели – часть конструкции, расположенная ниже пакета асфальтобетонных слоя, т.е. щебеночное основание и грунт рабочего слоя.
Ен
=228 Мпа;
К верхнему слою относят все асфальтобетонные слои.
Модуль упругости верхнего слоя устанавливают по формуле 2.7.
Ев
=3600.
12/12=3600 Мпа
По отношениям hв
/D=12/37=0,32 и Ев
/Ен
=3600/228=15,8 по номограмме находим определяем σр
`=2,25 Мпа.
Расчетное растягивающее напряжение вычисляем по формуле 2.8.
σр
=2,25.
0,6.
0,85=1,15 Мпа
Вычисляем предельное растягивающее напряжение по формуле 2.9.
R0
=9,50 Мпа – для слоя асфальтобетонного пакета.
k1
=5,4/5
Ö27046=0,701
t =1,39; k2
=0,90
Отсюда
RN
=9,50.
0,701.
0,90(1-0,10.
1,39)=5,16 Мпа
Находим коэффициент прочности
Кпр
= RN
/sr
=5,16/1,15=4,49, что больше чем Кпр
тр
=1,00
Вывод: Выбранная конструкция удовлетворяет критериям прочности.
Проверка на морозоустойчивость.
1. По приложению 5 табл.5.1 назначаем для каждого слоя коэффициент теплопроводности.
Таблица 2.5 Коэффициенты теплопроводности дорожной одежды.
Материал |
Толщина слоя hод
, м |
Коэффициент теплопроводности lод
|
Плотный а/б |
0,12 |
1,40 |
Черный щебень уложенный по способу заклинки |
0,15 |
0,52 |
Щебеночная/гравийная смесь |
0,25 |
2,10 |
2. Определяем глубину промерзания по карте (рис.4.4), для Карелии – 1,4 м, и по формуле 2.11.
Zпр
=1,4.
1,38=1,93»2 м
Для глубины промерзания 2 м по номограмме (рис.4.3) находим величину пучения для кривой (песок мелкий – II группа, слабопучинистая) – lп(ср)
=1 см.
3. Далее находим поправочные коэффициенты
Уровень грунтовых вод от поверхности, - 0,8 м
Кугв
=0,7 (рис.4.1)
Кнагр
=0,81 (рис.4.2)
Квл
=1,0 (табл.4.6)
Кгр
=1,0 (табл.4.5)
Кпл
=1,0 (табл.4.4) при Купл
=1,01-0,98
Тогда
lпуч
=1.
0,7.
0,81.
1,0.
1,0.
1,0=0,57 см
Согласно табл.4.3,
l
доп
=4 см, что больше полученного нами, следовательно, данная конструкция дорожной одежды не требует дополнительного морозозащитного слоя.
Анализ выполненных расчетов позволяет сделать вывод, что альтернативный вариант дорожной одежды имеет более высокие прочностные характеристики и меньшую трудоемкость.
Выбираем в качестве базового - альтернативный вариант.
2.6 Расчет объемов дорожной одежды
Для определения объема каждого слоя дорожной одежды составим поперечный профиль, показанный на рисунках 2.3 и 2.4.
1 вариант дорожной одежды.
  |
 |
 |
  |
    |
 |
  |
 |
  |
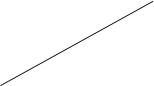 |
 |
  |
 |
 |
   |
  |
 |
  |
 |
Плотный асфальтобетон тип Б 1 марки ГОСТ 9128-97 – 0,05 м |
Пористый асфальтобетон 1 марки ГОСТ 9128-97 - 0,06 м |
Щебень фракцированный устр. По способу заклинки ГОСТ 8736-93-0,12 м |
Щебень фракцированный устр. По способу заклинки ГОСТ 8736-93-0,18 м |
Подстилающий слой – песок ГОСТ 8736-93 - 0,25 м |
Рисунок 2.3 Поперечный профиль дорожной одежды (1 вариант)
Определяем объем асфальтобетона.
Площадь а/б покрытия (нижний слой) Sпокр.н.сл.
=99670 м2
, высота слоя Hпокр.н.сл.
=0,06 м, Vпокр.н.сл.
=99670.
0,06=5980 м3
.
Объемный вес γаб
=2,3 т/м3
, отсюда Vаб
=5980.
2,3=13755 тн, а с учетом уширений Sпокр.н.сл.
=101849 м2
, отсюда 101849/99670=1,022, тогда Vаб.н.сл.
=13755.
1,022=14058 тн
Площадь а/б покрытия (верхний слой) Sпокр.вер.сл.
=100446 м2
, высота слоя Нпокр.вер.сл.
=0,05 м, Vпокр.вер.сл.
=100446.
0,05=5022 м3
.
Vаб
=5022.
2,3=11551 тн, с учетом уширений и примыканий Sпокр.вер.сл.
общ.
=108027 м2
, отсюда 108027/100446=1,075, тогда Vаб.вер.сл.
=11551.
1,075=12417 тн.
Определяем объем обочин.
Hбр
=h-С(iо
-iп
)=0,11-1,5(0,04-0,02)=0,08 м;
Sоб
=С([h+hбр
]/2)+mhбр
2
=1,5([0,11+0,08]/2)+3.
0,082
=0,162 м2
;
2Sоб
=2.
0,162=0,323 м2
, отсюда Vоб
=0,323.
11947=3859 м3
.
Определяем объем щебеночного основания.
Vос
=(Вос
hос
+mhос
2
)L, отсюда Вос
=Ваб
+2mhаб
=8+2.
3.
0,11=8,66 м;
Vос
=(8,66.
0,30+3.
0,302
)11947=34264 м3
.
Определяем объем подстилающего слоя.
Vпс
=(Впс
hпс
+mhпс
2
)L, отсюда Впс
=Вос
+2mhос
=8,66+2.
3.
0,30=10,46 м;
Vпс
=(10,46.
0,25+3.
0,252
)11947=33481 м3
2 вариант дорожной одежды.
   |
 |
 |
 |
 |
   |
  |
  |
  |
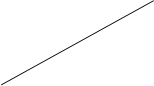 |
  |
 |
 |
  |
    |
 |
 |
 |
 |
Плотный асфальтобетон тип Б 2 марки ГОСТ 9128-97 – 0,12 м |
Черный щебень уложенный по способу заклинки ГОСТ 30491-97 – 0,15 м |
Щебеночная/гравийная смесь С-40 мм ГОСТ 25607 - 0,25 м |
Рисунок 2.4 Поперечный профиль дорожной одежды (2 вариант)
Определяем объем асфальтобетона.
Sаб
=100446 м2
; Наб
=0,12 м; Vаб
=100446.
0,12=12053,5 м3
Vаб
=12053,5.
2,3=27723 тн, с учетом уширений и примыканий Vаб
=27723.
1,075=29802 тн.
Определяем объем обочин.
Hбр
=h-С(iо
-iп
)=0,12-1,5(0,04-0,02)=0,09 м
Sоб
=С([h+hбр
]/2)+mhбр
2
=1,5([0,12+0,09]/2)+3.
0,092
=0,167 м2
2Sоб
=2.
0,167=0,334 м2
, отсюда Vоб
=0,334.
11947=3985 м3
.
Определяем объем основания из черного щебня.
Vчщ
=(Вчщ
hчщ
+mhчщ
2
)L, отсюда Вчщ
=Ваб
+2mhаб
=8+2.
3.
0,10=8,6 м;
Vчщ
=(8,6.
0,15+3.
0,152
)11947=16218 м3
.
Определяем объем ЩГС.
Vщгс
=(Вщгс
hщгс
+mhщгс
2
)L, отсюда Вщгс
=Вчщ
+2mhчщ
=8,6+2.
3.
0,15=9,5 м;
Vщгс
=(9,5.
0,25+3.
0,252
)11947=30614 м3
.
2.7 Обстановка дороги
Для обеспечения безопасности движения и ориентации водителей предусмотрена расстановка дорожных знаков, ограждающих устройств, направляющих сигнальных тумб и нанесение горизонтальной и вертикальной разметочной линии.
Дорожные знаки приняты в соответствии с требованиями ГОСТ 10807-78* и ГОСТ 23457-86, металлическое ограждение барьерного типа по ГОСТ 26804-86.
Подробные данные по обустройству дороги приведены на графике обустройства.
3 ПРОЕКТ ПРОИЗВОДСТВА РАБОТ И ОРГАНИЗАЦИЯ СТРОИТЕЛЬСТВА
Основой для составления проекта производства работ (далее ППР) является проект организации строительства (далее ПОС). При составлении ППР основные данные по срокам строительства, потребность в рабочих, дорожно-строительной технике и требуемым материалам, а также сметной стоимости взяты из ПОС.
При разработке ППР придерживаются основных нормативов СНиП 3.01.01-85 «Организация строительного производства» и СНиП 4.02.01-85 «Инструкция о составе, порядке разработки, согласования и утверждения проектно-сметной документации на строительство предприятий, зданий и сооружений».
Основная цель ППР – ввод в действие реконструируемого участка с высшим качеством, в установленные сроки, с получением экономии отпущенных на реконструкцию и получаемых по договору средств.
Для достижения поставленной цели необходимо:
1. Использовать новейшие достижения в области дорожного строительства;
2. Широкое использование поточной организации строительства, как дающей высокий экономический эффект по сравнению с другими (непоточными) методами.
3. Производство работ в две или три смены или вахтовым методом, с максимальным и равномерным использованием всех имеющихся на стройке ресурсов и рабочего персонала;
4. Детальное изучение условий производства дорожно-строительных работ с целью изыскания резервов снижения трудоемкости и стоимости строительства.
Эффективность выполнения работ зависит от фактора времени. Временной фактор, как правило, нормирован. Соблюдение нормативов времени позволят обоснованно определить сроки ввода в действие реконструируемого участка, повысить реальность составления планов капитальных вложений в производство строительно-монтажных работ, планов материально-технического снабжения, проектов организации строительства и производства работ.
Нормы продолжительности строительства назначаем согласно СНиП 1.04.03-85. Продолжительность вахтового цикла две недели, а смены 10 часов.
3.1 Основы организации строительства
Основной прогрессивный метод организации строительства – поточный, т.е. метод непрерывного и равномерного производства. При реконструкции поточный метод предусматривает выполнение всех строительных работ комплексно-механизированными подразделениями (отрядами); обеспечение их необходимыми материалами, изделиями, полуфабрикатами; передвижение специализированных подразделений непрерывно друг за другом по трассе реконструируемой дороги с установленной средней скоростью потока.
Учитывая природные условия, объемы работ и практический опыт строительства (реконструкции) подобных сооружений, работы предлагаются вести следующими специализированными потоками (отрядами):
·Отряд №1 (звено №1) по устройству малых искусственных сооружений, автопавильонов и обустройству автомобильной дороги.
·Отряд №2 (звено №2 - №4) по возведению земляного полотна. Работы ведутся поточным методом одновременно двумя захватками длиной 300 м. В состав звеньев №2 и №3 входят: бульдозер, легкий, тяжелый катки, ПМ-130. Экскаваторное звено №4 с автотранспортом.
·Отряд №3 (звено №5, №6) по устройству щебеночного основания. Звено №5 по устройству нижнего слоя основания. Звено №6 по устройству верхнего слоя основания.
·Отряд №4 (звено №7) по устройству асфальтобетонного покрытия.
Минимальные составы характеристики и особенности работы этих отрядов приведены в соответствующих технологических картах и схемах. Отряд №1 после строительства искусственных сооружений выполняет укрепительные работы (укрепление откосов земляного полотна, кюветов).
Порядок работ принят с учетом производительности специализированных отрядов, технологической последовательности и сроков выполнения работ.
В целях равномерной загрузки а/транспорта в течение года предусмотрена вывозка щебня для устройства щебеночного основания со складированием его в притрассовые конуса. Последующая вывозка его из конусов на трассу производится а/транспортом с загрузкой экскаватором CATERPILLAR на среднее расстояние до 5 км, что позволяет уменьшить потребность в а/транспорте в летне-осенний строительный период.
Все виды выемок, а также грунтовые карьеры должны быть защищены от доступа поверхностных вод. Водоотвод поверхностных вод следует осуществлять до начала основных работ с помощью постоянных или временных устройств.
Во время возведения земляного полотна необходимо следить за обеспечением водоотвода и не допускать застоя поверхностной воды, как на земляном полотне, так и в водоотводных сооружениях.
3.2 Подготовительные работы
Земельные участки, отведенные в период реконструкции для притрассовых карьеров, временных инженерных сооружений, после окончания реконструкции подлежат возврату землепользователям в состоянии, пригодном для последующих нужд пользователя.
Дорожная полоса является промышленной строительной площадкой. Ширина постоянного и временного отвода оговорена нормами отвода в зависимости от категории дороги.
При индивидуальном проектировании ширина дорожной полосы определяется расчетом.
Состав подготовительных работ:
·Восстановление и закрепление трассы на местности;
·Расчистка полосы отвода;
·Производство разбивочных работ;
·Удаление растительного слоя почво-грунта и обваловывание его за пределы дорожной полосы;
·Устройство осушительных и водоотводных канав;
·Перенос коммуникаций.
3.2.1 Восстановление и закрепление трассы на местности.
В процессе рубки деревьев, трелевки и расчистки кустарника, ось трассы, закрепленная в процессе изыскательских работ, как правило, нарушена. Поэтому её необходимо восстановить и закрепить. С этой целью необходимо восстановить и вынести за пределы полосы отвода:
·Начало и конец прямых участков дороги;
·Вершины углов поворотов и створных точек;
·Высотные положения точек (закрепляются реперами);
·Пикетаж (характерные плюсовые точки);
·Начало и конец переходных и круговых кривых.
По ходу выполнения данных работ возможно закрепление на местности дополнительных земельных участков (резервы, карьеры и т.д.).
Все планово-высотные, геодезические разбивочные работы должны соответствовать действующим нормативным положениям (СНиП 3.01.03-84), а техническая документация передается подрядчику не позднее, чем за десять дней до начала строительно-монтажных работ.
3.2.2 Расчистка полосы отвода.
При проведении расчистки необходимо обозначить границы полосы вырубаемого леса, определенной ПОС, границы расчищаемых участков, зоны отвалов растительного почво-грунта. Сваленные деревья и деревья с корнями разделывают на месте и вывозят с дорожной полосы. Вершины и сучья сжигают. Недопустимо создавать при расчистке вдоль дороги с обеих сторон валы из растительного грунта, пней, сучьев и т.п., являющихся препятствием для строительных работ.
Прорубку просеки выполняют лесозаготовительной бригадой.
Метода расчистки площадей от кустарника и способы производства работ принимают в зависимости от конструкции и возможностей корчевателя-собирателя и густоты кустарника. При выполнении этих работ желательно применять специализированные агрегаты с активными рабочими органами.
В соответствии со СНиП 3.06.03-85, отходы из кустарников, мелколесья и корней должны быть сожжены до начала земляных работ.
3.3 Проект производства работ по строительству малых искусственных сооружений.
В проекте предусмотрено сооружение водопропускных труб в условиях опережения отсыпки земляного полотна и после его отсыпки, когда трубы возводят в разрывах насыпей.
3.3.1 Подготовительные работы.
В состав подготовительных работ входят:
- планировка строительной площадки;
- отвод существующего русла; разбивка оси трубы, контуров котлована и русла;
- разбивка контура фундамента;
- доставка оборудования и элементов временных инвентарных обустройств;
- монтаж на объекте строительства;
- завоз материалов и сборных элементов;
- разгрузка их на строительной площадке.
Для установления проектного положения трубы теодолитом восстанавливают, ось трассы и стальной лентой дважды измеряют расстояние от ближайшего пикета до продольной оси трубы. В полученной точке закладывают деревянный столб на уровне с землей и в него точно по оси трассы забивают гвоздь, фиксирующий центр оси трубы. После этого устанавливают теодолит и переносят в натуру угол между осями трубы и трассы дороги.
Продольную ось трубы закрепляют двумя .контрольными знаками ( по два столба на каждую сторону), устанавливаемыми не ближе 3 м от грани котлована. Эти знаки связывают между собой нивелированием и передают на них отметки от ранее установленных ближайших реперов. Одновременно дают отметки лотков входного и выходного оголовков. От продольной оси трубы разбивают очертание котлована и по контуру забивают колья. Точность разбивки ±5 см.
Завоз оборудования, материалов и сборных элементов трубы осуществляется транспортной колонной. Сборные элементы трубы (блоки) доставляют автомобилями. Блоки разгружают автомобильным краном грузоподъемностью 12 т н.. Укладывают блоки в местах, указанных на стройплощадке. Звенья труб, имеющие строительные петли, на месте выгрузки у объекта могут располагаться в вертикальном или в горизонтальном положении. В последнем случае должен быть обеспечен свободный доступ ко всем стрелочным петлям.
3.3.2 Устройство котлована.
Котлован разрабатывают экскаватором САТЕRPILLAR в предельно сжатые сроки, без нарушения несущей способности грунта основания.
Котлованы в нескальных связных грунтах необходимо разрабатывать ниже проектной отметки на 0,1-0,2 м окончательная планировка и зачистка дна котлована, а при необходимости также и уплотнение грунта основания должны производиться непосредственно ручными инструментами перед кладкой фундамента. Фундаменты устанавливаются на подушку из ПГЩС. Верх слоя ПГЩС должен располагаться не выше проектной отметки заложения фундамента.
Грунт из котлована следует удалять в отвал на такое расстояние, чтобы на всех этапах производства не возникало опасение обрушивания стенок котлована, препятствий для передвижения строительных машин или других затруднений.
Отрытый котлован должен быть немедленно освидетельствован и принят комиссией с участием представителя заказчика. Приемка котлована должна быть оформлена актом.
3.3.3 Устройство фундаментов.
Фундаменты следует устраивать немедленно после приемки основания комиссией иподписания акта, разрешающего приступить к укладке фундамента.
Уклон основания под блочный фундамент должен соответствовать проектному уклону трубы с учетом строительного подъёма.Монтаж блочных фундаментов рекомендуется начинать со стороны выходного оголовка. Блоки фундамента укладываются автомобильным краном грузоподъемностью 12 тонн.При монтаже оголовка с блочными железобетонными фундаментами вначале следуетукладывать блоки фундаментов под выходной и входной оголовки до уровня подошвыфундамента. Скосы в котловане, устраиваемые в месте сопряжения более глубокой части котлована подфундаменты оголовков с подошвой котлована под тело трубы, должны быть заполненыпесчано-гравийным грунтом. Грунты следует укладывать горизонтальными слоями толщиной15 см и тщательно уплотнять.
Последующие ряды блоков укладывают в фундаменты оголовков и звеньев трубы вследующем порядке: сначала ряд блоков в фундамент одного из оголовков, затем ряд блоковво всех секциях фундамента под звеньями и далее — в фундамент другого оголовка трубы.
Вертикальные швы между блоками заливают цементным раствором (через плоскую воронку) и уплотняют раствор плоской металлической шуровкой. Наружные стороны вертикальных швов при этом должны быть законопачены паклей или бумагой от мешков из-под цемента или заделаны раствором.
При укладке блоков фундамента следует применять цементный раствор марки не ниже 150. Водоцементное отношение в цементном растворе допускается не выше 0,60. Цементный раствор для горизонтальных швов сопряжения блоков должен иметь осадку конуса 6—8 см, а для вертикальных швов 11—13 с м. Большие величины осадки конуса принимаются при работах в жаркую погоду.
3.3.4 Монтаж звеньев и оголовков.
Монтаж звеньев и оголовков трубы производится автомобильным краном грузоподъемностью 12 тонн сразу после устройства фундаментов. В первую очередь, как правило, должны монтироваться блоки выходного оголовка трубы. Затем приступают к монтажу звеньев трубы (см. рис). Звенья трубы укладывают от выходного (смонтированного) оголовка к входному. При наличии смонтированных обоих оголовков направление укладки звеньев может быть любым.
При установке цилиндрических звеньев на сборные лекальные блоки звенья устанавливают на деревянных (не удаляемых) клиньях, обеспечивая при этом по возможности проектную величину зазора укладки цементного раствора.
Раствор сначала укладывают с одной стороны звена, добиваясь, чтобы он при уплотнении проник под нижнюю образующую звена и вышел на другую сторону. С противоположной стороны звена следует восполнять недостающее количество раствора в зазоре, обеспечивая при этом плотное заполнение и выравнивание шва.
Швы между звеньями после окончания монтажа должны быть снаружи и изнутри плотно законопачены жгутами из пакли, пропитанной битумом. Жгуты поставленные с внутренней стороны, должны быть утоплены внутрь швов на 2—3 см от поверхности звеньев.
По окончании монтажа трубы производится засыпка пазух котлована местными однородными грунтами слоями толщиной 15 см с тщательным послойным уплотнением ручными электрическими или механическими трамбовками. Одновременно устраивается, также с уплотнением, гравийно-песчаная подготовка (толщиной 30 см) под лотки оголовков.
После засыпки пазух котлована приступают к устройству лотков из монолитного бетона марки 150 в пределах оголовков.
3.3.5 Устройство гидроизоляции.
Работы по гидроизоляции выполняются обязательно в сухую погоду с обеспечением условий для высококачественного выполнения гидроизоляционных работ.
Гидроизоляция может быть применена двух типов: оклеенная и обмазочная. Для труб из звеньев заводского изготовления допускается применение обмазочной гидроизоляции при условии:
а)использования плотного бетона водопроницаемостью не ниже W-6 по ГОСТ 24547-81;
б)удовлетворительных результатов испытания звеньев труб на водонепроницаемость на заводе-изготовителе;
в)наличия технического паспорта наготовленных звеньевс результатом испытания бетона и звеньев на водопроницаемость.
Обмазочная гидроизоляция состоит из двух слоев горячей или холодной битумной мастикипо битумной грунтовке.
Швы в стыках звеньев конопатятся с обеих сторон паклей, пропитанной битумом. Снаружной стороны трубы поверх пакли наносят слой горячей битумной мастики и поверх еенаклеивают слой гидроизоляции шириной 25 см, покрытый горячей битумной мастикой. Свнутренней стороны на глубину 3 см шов заделывают цементным раствором.
3.3.6 Засыпка трубы.
При постройке труб с опережением отсыпки земляного полотна на данном участке трассы полную засыпку звеньев трубы следует производить после готовности всего сооружения (на основании акта приемки трубы).
При постройке труб одновременно с отсыпкой земляного полотна или после окончания отсыпки его на данном участке трассы размеры оставляемых в этом случае разрывов в насыпи должны назначаться с учетом способа отсыпки грунта, планирующих и уплотняющих средств. Расстояние между торцовым откосом насыпи и трубой должно быть с каждой стороны не менее 4 м, а общая длина разрыва — не менее 10м.
Возведение насыпи над трубами включает три основных стадии, от которых зависят условия работы сооружения совместно с грунтом:
а) первая стадия — заполнение грунтом пазух между стенками котлована и фундамента.(до уровня верха фундамента) ;
б)вторая стадия — засыпка трубы на высоту звена плюс 2 м (или до проектной отметки земляного полотна при низких насыпях, когда высота засыпки менее- 2
м;
в)третья стадия—возведение насыпи над трубой до проектной отметки.
В данном случае труба засыпается до проектной отметки (вторая стадия работы) строительной организацией, строящей трубу.
Грунт отсыпается одновременно с обеих сторон трубы горизонтальными слоями толщиной 15 см с тщательным уплотнением, каждого слоя для создания плотного грунтового ядра вокруг звеньев. Для засыпки труб применяют грунты с карьера «69 Квартал».
Плотность грунтов в призмах и над трубами должна быть не менее значений приведенных в табл. 29, п, 9.11., СНиП 3.06.04-91.
Уплотнение грунта производится с помощью виброплиты DYNAPAK.
Запрещается уплотнять грунт тяжелыми трамбовочными машинами ударного действия: над трубой — при высоте засыпки менее 2 м и по сторонам от трубы—на расстоянии от боковых стенок трубы менее 3 м (в пределах выше указанной толщины, засыпки). Особое внимание следует обращать на качество уплотнения грунта в труднодоступных местах — в нижних четвертях звеньев труб. Не следует допускать переуплотнения грунта непосредственно над звеньями труб особенно в средней части сооружения (во избежание перегрузки конструкции), а также превышения засыпки звеньев с одной стороны по отношению к другой более чем на высоту 20 см.
Минимальная высота засыпки над трубой, допускающая проезд над ней тяжелых подвижных нагрузок (автомобилей-самосвалов, скреперов, катков), должна быть не менее величин, приведенных в рабочих чертежах труб.
При проектной высоте засыпки над трубой более 1,0 м каждый слой грунта по обеим сторонам трубы в пределах высоты звена плюс 1 м следует отсыпать на всю ширину насыпи. Автомобили-самосвалы, бульдозеры и другие тяжелые машины должны при этом перемещаться по обеим сторонам сооружения без переезда над трубой, как правило, до тех пор, пока высота уплотненной засыпки над звеньями не достигнет 1 м.
Рисунок 3.1 Постройка трубы в провале насыпи.

Рисунок 3.2 Схемы уплотнения грунтового ядра:
а) – при постройке трубы «с опережением» (до отсыпки насыпи);
б) – при постройке трубы в провале насыпи;
1 – грунтовое ядро (слои не более 15-20 см); 2 – основание насыпи; 3 – пазуха котлована (слои не более 15 см).
3.3.7 Укрепительные и отделочные работы.
Откосы насыпи у оголовков и русло на подходе и выходе из трубы укрепляют от размыва мощением камня высотой слоя 0,16 м. на подстилающем слое из щебня высотой слоя 0,10 м.
Укрепительные работы, как правило, следует выполнять при положительных температурах воздуха.
Размеры указывают в каждом конкретном случае в рабочих чертежах. Камень для мощения заготавливают из слабовыветривающихся твердых скальных пород с объемным весом не менее 2тм3
.
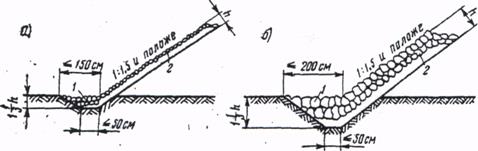
Рисунок 3.3 Мощение откосов:
а
— одиночное; б
— двойное;
1
— упор; 2
— подстилающий слой толщиной 10 см
Мощение должно выполняться обязательно на спланированных и тщательно уплотненных откосах горизонтальными рядами до упора снизу вверх. Камни укладывают, подбирая их по размерам с тщательной расщебенкой и уплотнением.
Откосы подводящего и отводящего русел должны быть сопряжены с выходными и входными оголовками труб и при необходимости дополнительно спланированы и зачищены. Строительный мусор и забракованные элементы должны быть удалены от сооружения.
Швы между блоками оголовков по видимым поверхностям должны быть" расшиты цементным раствором. При необходимости перед расшивкой швов в них втрамбовывают полусухой цементный раствор, кроме того, перед расшивкой швы необходимо тщательно промыть водой.
Расшитые швы должны быть ровными, без трещин и иметь хорошее сцепление раствора с блоками.
Швы между звеньями, законопаченные паклей и осмотренные представителем заказчика, должны быть с внутренней стороны звеньев расшиты цементным раствором.
Оштукатуривать наружные поверхности элементов труб и швов запрещается.
3.4 Проект производства работ по возведению земляного полотна.
3.4.1 Возведение насыпи с разработкой грунта экскаваторами и транспортировкой, а/самосвалами.
3.4.1.1.Область применения.
Технологическая карта разработана на основе методов научной организациитруда и предназначена для использования при разработке проекта производства работ на объекте: «Реконструкция участка автомобильной дороги Вологда-Кириллов-Пудож-Медвежьегорск км 533 - км 544».
Для возведения насыпи должны быть выполнены все предшествующие работы, согласно "Инструкции по сооружению земляного полотна автомобильных дорог", в том числе восстановление и закрепление трассы дороги, расчистка полосы отвода, разбивка земляного полотна и грунтового карьера. Устройство временных землевозных дорог для транспортирования грунта .
2.Указания по технологии производственного процесса.
При возведении насыпи с разработкой грунта экскаватором с транспортировкой автомобилями-самосвалами (рис.3.4) выполняются следующие работы:
а)подготовка и зачистка забоя; (карьер «Челмужский" карьер "69 квартал")
б)разработка грунта экскаватором в карьере с погрузкой его в а/самосвалы, перевозкой и выгрузкой в насыпь
в)послойное разравнивание грунта в теле насыпи
г)послойное уплотнение грунта
Разработка грунта экскаватором ведется комплексными механизированными бригадами. В комплект машин комплексной бригады: экскаваторы, а/самосвалы, бульдозеры, катки.
Разработка грунта экскаватором и
Разработка грунта в карьере ведется до отметки позволяющей обеспечить нормальный набор грунта ковшом экскаватора. Ширина проходок должна быть обеспечена с таким расчетом, чтобы экск. мог работать при средней величине углов поворота 70-90
Наибольшую допустимую высоту забоя в связанных и плотных грунтах принимать равной наибольшей высоте резания экскаватора. Наибольшая высота забоя в пределах 8-9м. При разработке грунта продольной проходкой расстояние от оси пути экск. до стенки забоя должна быть равна 5-6м; до места погрузки грунта -3,6м. Экскавацию грунта вести с наименьшими затратами времени на выполнение рабочего цикла.
Транспортировка грунта из карьера в насыпь производят а/самосвалами МАЗ-503,КРАЗ, КАМАЗ. Количество транспортных средств определяется плановым заданием для каждого конкретного случая. В каждый а/самосвал КРАЗ 256-Б загружается 6 м3
грунта. Затем грунт транспортируется до места производства работ, и выгружают через каждые 5м вдоль насыпи и через каждые 3м по ширине насыпи, начиная с ее краев (рис.2). Грунт разравнивают слоями толщиной 0,35-0,40 за 1-2 прохода бульдозера по одному следу. Работу выполнять на II скорости с перекрытием предыдущего слоя на 0,5-0,8м. После разравнивания грунта производят сначала предварительную планировку слоя 1-2 прохода бульдозера по одному следу, а затем окончательную с приданием ровности слоя поперечного уклона, согласно типового поперечника на данном участке.
Уплотнение грунта.
Уплотнение грунта послойно. Согласно акта пробного уплотнения число проходов уплотняющих машин по одному следу 18, достигнутое уплотнение 0,98. Первые проходы начинают на расстоянии 2-3 метров от бровки насыпи во избежание обрушения откоса, следующими проходами смещаясь за каждый проход 1/3 ширины катка. Уплотнение грунта продолжают с перемещением от края насыпи к ее оси. Степень уплотнения грунта проверяется лабораторией.
3.4.1.2 Указания по технике безопасности.
При производстве работ на экскаваторе необходимо соблюдать следующие правила техники безопасности.
Экскаваторы во время работы должны устанавливаться на спланированной площадке. При работе экскаватора рабочим запрещается находится под его ковшом или стрелой со стороны забоя. Посторонним лицам запрещается находиться на расстоянии менее 5м от радиуса действия экскаватора. Во время перерывов в работе ковш следует опустить на землю. Очищать ковш можно, только опустив его на грунт. При погрузке грунта ковш экскаватора не должен перемещаться над кабинами автомобилей. Водитель автомобиля во время погрузки должен находится в кабине. Запрещается изменять вылет стрелы при заполненном ковше, регулировать тормоза при поднятом ковше. Поворот ковша для выгрузки и передвижку экскаватора с опорожненным ковшом следует начинать только после выхода ковша из грунта, тормозить в конце поворота с заполненным ковшом плавно, без резких толчков, при подъеме ковша не допускать упора блока ковша о блок стрелы при опускании ковша не сообщать рукояти напорного движения, не допускать ударов о раму, гусеницу или грунт. Следить за правильной навивкой канатов на барабаны лебедок. Запрещается направлять канаты руками.
При работе бульдозера необходимо соблюдать следующие правила. Сбрасывая грунт под откос отвалом бульдозера, не выдвигать отвал за бровку откоса насыпи. Не поворачивать бульдозер с загруженным или заглубленным отвалом. Во время случайных остановок бульдозера отвал должен быть опущен на землю.
3.4.1.3 Указания по организации труда.
Работу по возведению насыпи из грунта, разрабатываемого экскаваторами с подвозкой автомобилями-самосвалами и отсыпкой его в тело насыпи, выполняет комплексная бригада. Для выполнения работ по отсыпке насыпи высотой до 1 м, участок длиной 400 м делят на две равные захватки. Работу организуют так.чтобы отсыпка и разравнивание грунта велось на одной захватке, а уплотнение на другой.
Состав бригады:
Машинист экскаватора 6 разр.
Помощники машинистов 6 разр
Водители автомобилей -самосвалов Машинист бульдозера 6 разр
Машинист катка 6 разр
|
-2
-2
по расчету
-1
-1
Таблица 3.1 Карта технологии операционного контроля
Контролируемые параметры |
Предельные отклонения |
1)Высотные отметки продольного профиля |
Не более 10%определений от проектных-100 мм 90% +/- 50мм |
2)Ширина земляного полотна между бровкой и осью 3)Поперечные уклоны 4)Коэффициент уплотнения
Не более 10%определений от проектных+/20 см
90%*+/-10см
Не более 10%определений до20%;остальные10%
+0.04
Основные операции .подлежащие контролю |
Разравнивание и планировка |
Факт, плотность грунта |
Состав контроля |
Высотные отметки прод.проф. ширина зем. полотна крутизна откосов |
Метод и средства контроля |
Инструментальный нивелир, стальная мерная лента |
Метод режущего кольца, прибор типа ПРП-2 |
Режим и объем контроля |
Промеры через 50м;продольное нивелирование и промеры через каждые 100м;ширину зем. полотна и крутизну откосов проверяют не менее чем в трех местах на 1 км дороги |
Не менее трех образцов на каждые два пикета |
Лицо контролирующее операцию |
Мастер |
Лаборант" |
Лицо, ответственное за организацию и осуществление контроля |
Прораб |
Где регистрируются результаты контроля |
Журнал производства работ |
Журнал контроля за уплотнением насыпи |

Рисунок 3.4 Схема возведения насыпи с разработкой грунта экскаваторами Э-1252Б и перемещением автомобилями-самосвалами:
1-экскаватор Э-1252Б; 2-автомобиль-самосвал; 3-бульдозер Д-493А; 4-прицепной каток.
3.4.2 Технологическая карта устройства уширения земляного полотна.
3.4.2.1 Область применения.
Технологическая карта разработана на устройство уширения земполотна существующей автомобильной дороги в соответствии с проектом. В качестве ведущего механизма используется бульдозер Т-170.
В состав работ входят:
- снятие растительного слоя грунта;
- устройство основания земполотна;
- нарезка уступов;
- послойная отсыпка земполотна с послойным уплотнением;
- планировка верха земляного полотна и откосов;
- нарезка кюветов.
3.4.2.2 Организация и технология производства работ
До начала производства работ по устройству уширения земполотна необходимо:
- восстановить трассу дороги;
- выполнить детальную разбивку земполотна;
- очистить территорию в пределах полосы отвода от леса, пней, кустарников и валунов; выполнить перенос инженерных коммуникаций;
- выполнить временный водоотвод (при необходимости).
Устройство уширения земполотна ведется поэтапно справа и слева от оси дороги, не создавая помех для движения транспортных средств по противоположной полосе дороги. Работы на каждом этапе выполняются поточным методом на трех захватках обшей протяженностью 300-600 м.
На первой захватке
выполняются следующие работы:
- срезка растительного слоя грунта бульдозером;
- уборка камней размером более 2/3 толщины отсыпаемого слоя экскаватором САТЕRPILLАР, (HITACHI) с погрузкой в автосамосвалы;
- - выравнивание основания уширения земполотна, нарезка уступов высотой 1-1,5 м и шириной 1,5-2 м при высоте насыпи более 2 м бульдозером Т-170;
- уплотнение основания земполотна катком DYNAPAC СС-222 7,5 т; .рыхление откосов старой насыпи.
Толщина срезаемого слоя назначается проектом. В карте принята толщина слоя 15 см. Грунт срезают бульдозером Т-170 (или экскаватором САТЕRPILLAR, (HITACHI), перемещают к границе полосы отвода или вывозят в отведенные для этого места для складирования и обваловывают. В дальнейшем его используют для укрепления откосов.
Перекрытие следов от предыдущих проходов бульдозера и срезке грунта должно составлять 0,25-0,3 м.
На второй захватке
выполняются следующие технологические операции:
- разравнивание грунта на насыпи слоями по 0,3 м бульдозером Т-17О;
- уплотнение слоя грунта самоходным катком DYNAPAK СС-422 10 т.
Отсыпка земполотна ведется от краев к середине насыпи. Песчаный грунт доставляется автомобилями-самосвалами грузоподъёмностью до 13т.
Самосвалы для выгрузки разворачиваются на существующей насыпи и подаются к месту выгрузки грунта по оборудованному съезду задним ходом. При малых объемах отсыпки возможно выгрузку грунта вести с обочины существующей дороги. При этом тщательно обеспечивать безопасность движения транспортных средств.
Перемещение и разравнивание грунта на насыпи выполняют челночными проходами бульдозера Т-170 на второй рабочей скорости.
Каждый слой следует разравнивать, соблюдая проектный продольный и поперечный .уклоны.
Возвращение бульдозера к началу захватки осуществляется задним ходом с опущенным отвалом, которым бульдозер частично уплотняет грунт.
В целях надлежащего уплотнения грунта в краевых частях насыпи ширина отсыпки должна быть больше проектного очертания насыпи на 0,3-0,5 м с каждой стороны. Излишек грунта убирается на завершающем этапе возведения насыпи при планировке.
Уплотнение следует выполнять при оптимальной влажности грунта. Перед началом работы производитель работ совместно с лаборантом устанавливает рациональный режим работы уплотняющих средств пробным уплотнением.
В карте предусмотрено уплотнение грунта выполнять катком DYNAPAC СС-422 за десять проходов по одному следу по челночной схеме.
Первый проход выполняют на расстоянии не менее 2 м от бровки насыпи, после чего, смещая каток при каждом последующем проходе .на 1/3 ширины следа в сторону бровки, прикатывают края насыпи. Затем уплотнение продолжают челночными проходами с перемещением полос уплотнения от краев насыпи к её середине с перекрытием следов на 1/3.
Каждый последующий проход по одному и тому же следу начинают после перекрытия предыдущими проходами всей ширины земляного полотна.
Первый и последний проходы катка на полосе укатки выполняют на малой скорости (2-2,5 км/ч), промежуточные - на скорости 8-10 км/ч.
Отсыпку каждого следующего слоя можно производить только после разравнивания и уплотнения предыдущего с соблюдением продольного и поперечного уклонов.
На третьей захватке
выполняются такие технологические операции:
- срезка грунта с откосов автогрейдером (экскаватором-планировщиком UDS-114);
- планировка верха земляного полотна автогрейдером;
- планировка откосов земляного полотна автогрейдером (экскаватором-планировщиком UDS-114);
- окончательное уплотнение земляного полотна катком DYNAPAC СС-422;
- нарезка кюветов, канав.
Технологической картой предусмотрено планировочные работы выполнять автогрейдером ДЗ-180 и/или экскаватором-планировщиком UDS-114.
Перед началом планировки необходимо проверить и восстановить положение оси и бровок земляного полотна в плане на прямых, переходных и основных кривых, а также в продольном профиле.
Планировку верха земляного полотна выполняют автогрейдером ДЗ-180 за четыре прохода по одному следу. Работы организуют по челночной схеме без поворота отвала в конце захватки с задним холостым ходом автогрейдера. Вначале плакировку следует производить короткими проходами для устранения неровностей, видимые на глаз, а затем поверхность выравнивают сквозными проходами по всей длине захватки.
Угол захвата ножа автогрейдера должен быть 35-70°, а угол наклона — в зависимости от проектного поперечного профиля. Перекрытие следов при планировке верха земляного полотна 0,4-0,5 м.
Откосы выемки планируют авто грейдеров ДЗ-180, оборудованным удлинителем, за три прохода. Планировку следует начинать верхней части откоса при движении автогрейдера по бровке выемки; затем планируется нижняя часть.
Кюветы глубиной до 0,7 м нарезают автогрейдером ДЗ-180 за четыре прохода по длине захватки. Глубина кювета— не менее 0,3 м. При большей глубине кюветы и канавы отрывают экскаватором-планировщиком UDS-114. Водоотводные канавы и кюветы укрепляют сразу после их устройства.
Уплотнение верха земляного полотна производится катком на пневмошинах СР-132 (ДУ-16В, DYNAPAC СС-422 за четыре прохода по одному следу по челночной кольцевой) схеме со смещением полос уплотнения от краев полотна к его оси и перекрытием следов на 1/3.
После завершения планировочных работ на откосах насыпи приступают к плакировке.
Работы по возведению земляного полотна выполняет бригада численностью 7 чел.:
Машинист экскаватора 6 разр.............. 1
Машинист бульдозера 6 разр................ 2
Машинист автогрейдера 6 разр........ 1
Машинист экскаватора-планировщика UDS-114 ... 1
Машинист катка 6 разр...................... 1
Тракторист 5 разр................... 1
Качество выполнения работ контролируют согласно табл. 3.3
Таблица 3.3 Контроль выполнения работ.
Операции |
Предмет контроля |
Лицо,осуществляющее контроль |
Вид контроля |
Снятиерастительного слоя грунта |
Границы,толщинаслоя,размещение отвалов грунта |
Мастер |
Инструментальный |
Нарезка уступов, устройство основания |
Положение в плане, размеры, уклоны, качество уплотнения основания |
Мастер, лаборант |
Инструментальный |
Послойная отсыпка и уплотнение земляного полотна |
Качество грунта, ширина и толщина слоев, продольные и поперечные уклоны, качество уплотнения |
Мастер, лаборант |
Инструментальный, лабораторный |
Окончательная планировка верха земляного полотна |
Размеры насыпи, крутизна откосов, положение насыпи в плане, уклоны, ровность поверхности насыпи, степень уплотнения |
Прораб (мастер),лаборант,геодезист |
Инструментальный, лабораторный |
Примечание. Контроль каждой операции осуществляется в процессе производства работ.
При устройстве земляного полотна допускаются следующие отклонения геометрических размеров:
Высотные отметки продольного профиля ..50 мм
Расстояние между осью и бровкой земляного полотна ..10 см
Поперечные уклоны 0,01
Крутизна откосов 10%
Для дорог с капитальными покрытиями разница между показателями плотности верхнего слоя на одном поперечнике не должна превышать 2%.
3.4.2.3 Технико-экономические показатели.
На устройство 1000 м3
земполотна:
Затраты труда............ 2,3 чел.-дня
Потребность в машинах2,3 маш.-смены
Выработка на 1 рабочего200 м3
3.4.2.4 Материально-технические ресурсы.
Потребность комплексной механизированной бригады в машинах, оборудовании и приспособлениях определена из расчета оптимальной их загрузки:
Экскаватор САTERPILLAR (HITACHI) 1
Бульдозер Т-170.............. ... 2
Автогрейдер ДЗ-180.......... .... 1
Экскаватор-планировщик UDS-114 1
Каток полуприцепной на пневмошинах ДУ-29 (DYNAPAC СС-422)....1
Автомобиль-самосвал КАМАЗ-5511
Грузоподъемностью – 13 тн 14
3.4.2.5 Техника безопасности.
При производстве работ по устройству земляного полотна необходимо соблюдать правила техники безопасности, приведенные в соответствующих разделах и «Правил техники безопасности при строительстве, ремонте и содержании автомобильных дорог» и СНиП III-4-80 «Техника безопасности в строительстве».
Постоянно следить за дислокацией дорожных знаков согласно согласованной с ГИБДД схеме.
Общая длина захватки (участка), требующая ограничения движения транспортных средств по существующей дороге, не должна превышать 350 м.
Основные требования техники безопасности изложены в настоящем ППР. Разработки дополнительных мероприятий по обеспечению безопасности труда нетребуется.
3.4.3 Технологическая карта на устройство выемки глубиной до 5 м
экскаватором.
3.4.3.1 Область применения.
Технологическая карта разработана на устройство выемки глубиной до 5 м. В качестве ведущего механизма используется одноковшовый экскаватор Э-10011 А, оборудованный прямой лопатой. Вместимость ковша экскаватора 1 м3
. Сменная производительность — 615 м3
. Можно также использовать экскаваторы с обратной лопатой CATERPILLAR.
В состав работ входят:
- снятие растительного слоя грунта;
- устройство временных проездов;
- снятие существующего дорожного покрытия;
- разработка грунта и погрузка его в транспортные средства;
- планировка верха земляного полотна и откосов;
- нарезка кюветов;
- подкатка верха земляного полотна.
3.4.3.2 Организация и технология производства работ.
До начала производства работ по устройству выемки необходимо:
- восстановить трассу дороги;
- очистить территорию в пределах полосы отвода от леса, пней, кустарников и валунов;
- произвести разбивку земляного полотна;
- выполнить временный проезд для транспортных средств (с учетом образующихся откосов разрабатываемой выемки);
- снять существующее дорожное покрытие.
Устройство экскаватором выемки глубиной до 5 м ведется поэтапно справа и слева от оси дороги. Работы на каждом этапе выполняются поточным методом на трех захватках.
На первой захватке
выполняются следующие работы:
- срезка растительного слоя грунта бульдозером;
- устройство пионерной траншеи бульдозером.
Толщина срезаемого слоя назначается проектом. В карте принята толщина слоя 15 см. Грунт срезают бульдозером Т-170 (ДЗ-8) по поперечно-участковой схеме, перемещают за пределы полосы отвода и обваловывают. В дальнейшем его используют для укрепления откосов.
Перекрытие следов от предыдущих проходов бульдозера и срезке грунта должно составлять 0,25-0,3 м.
Пионерную траншею устраивают бульдозером Т-170 (ДЗ-17, Д-4921А). Ширина ее по низу не менее 4 м, подошва имеет уклон 2% в сторону начала разработки для обеспечения отвода воды. Грунт из пионерной траншеи бульдозер перемещает в близлежащую насыпь (на расстояние до 50 м).
На второй захватке
разрабатывают грунт экскаватором с погрузкой в транспортные средства и последующим его вывозом к месту выгрузки.
В технологической карте принята разработка выемки продольными проходами экскаватора на всю ее длину. Работы начинают с низовой стороны для обеспечения отвода воды.
При первом проходе грунт грузят в транспортные средства (автомобили-самосвалы), движущиеся по пионерной траншее. При последующих проходах экскаватора автомобили-самосвалы перемещаются в пройденных проходках, а также в забое. Под погрузку их устанавливают параллельно оси движения экскаватора.
Для содержания дна забоя в состоянии, обеспечивающем движение транспортных средств,используется бульдозер Т-170 (ДЗ-8).
Грунт в выемке разрабатывают с недобором для предотвращения нарушения структуры грунта в основании. Допускаемый набор грунта при разработке выемки экскаватором Э-10011А—0,2 м.
На третьей захватке
производятся работы по окончательной планировке земляного полотна, нарезке кюветов, планировке откосов выемки и уплотнению земляного полотна.
Планировку верха земляного полотна выполняют автогрейдером ДЗ-180 (ДЗ-31-1) за четыре прохода по одному следу по челночной схема Угол захвата ножа автогрейдера должен быть 35-70°, а угол уклона — в зависимости от проектного поперечного профиля. Перекрытие следов при планировке верха земляного полотна 0,4-0,5 м.
Откосы выемки планируют автогрейдером ДЗ-180 (ДЗ-31-1), оборудованным удлинителем, за три прохода. Планировку следует начинать верхней части откоса при движении автогрейдера по бровке выемки; затем планируется нижняя часть.
Кюветы нарезают автогрейдером ДЗ-180 (ДЗ-31-1) за четыре прохода по длине захватки. Глубина кювета — не менее 0,3 м.
Уплотнение верха земляного полотна производится катком на пневмошинах СР-132 (ДУ-16В) за четыре прохода по одному следу по кольцевой схеме со смещением полос уплотнения от краев полотна к его оси и перекрытием следов на 1/3.
Калькуляция трудовых затрат на разработку 1000 м3
выемки приведена в табл.3.4.
Таблица 3.4 Калькуляция трудовых затрат на разработку 1000 м3
выемки.
Обоснование |
Работа |
Состав звена |
Измеритель |
Объем |
На измеритель |
На объем |
Норма времени чел-ч (Маш-ч) |
Расценка, р-к. |
Трудоемкость, чел-ч (Маш-ч) |
Прямая заработная плата, р-к. |
§ Е2-1-5, п.1а |
Срезка растительного слоя грунта бульдозером ДЗ-8 |
Машинист 6 разр.-1 |
1000 м3
|
0,3 |
0,84 (0,84) |
0-89 |
0,25 (0,25) |
0-27 |
§ Е2-1-22, таб.2, пп.3б+3д |
Устройство пионерной траншеи бульдозером ДЗ-17 с перемещением грунта на расстояние 50 м |
тоже |
100 м3
|
3,0 |
2,58 (2,58) |
2-73,3 |
7,74 (7,74) |
8-20 |
Н.вр.=0,62+0,49*4=2,58
Расц.=(0-65,7)+(0-51,9)*4=2-73,3
|
§ Е2-1-46, п. 1а |
Планировка подъездных путей бульдозером ДЗ-17 |
Машинист 6 разр.-1 |
1000 м3
|
4,0 |
0,6 (0,6) |
0-63,6 |
2,4 (2,4) |
2-55 |
§ Е2-1-8, таб.3,п.6б |
Разработка грунта экскаватором Э-10011 |
Машинист 6 разр.-1
Помощник машиниста 5 разр.-1
|
100 м3
|
10,0 |
2,6 (1,3) |
2-56 |
26 (13) |
25-60 |
§ Е2-1-37, табл.2,п.1б |
Планировка верха земляного полотна автогрейдером ДЗ-31-1 за четыре прохода по одному следу |
Машинист 6разр.-1 |
1000 м3
|
0,42 |
0,68 (0,68) |
0-72 |
0,29 (0,29) |
0-30 |
Н.вр.=0,17*4=0,68
Расц.=(0-18)*6=0-72
|
§ Е2-1-39, п.10б |
Планировка откосов выемки автогрейдером ДЗ-21-1 |
Машинист 6 разр.-1 |
1000 м3
|
0,2 |
0,37 (0,37) |
0-39,2 |
0,08 (0,08) |
0-08 |
§ Е2-1-43 |
Нарезка кюветов автогрейдером ДЗ-31-1 |
Машинист 6разр.-1 |
100 м3
|
0,1 |
2,6 (2,6) |
2-76 |
0,26 (0,26) |
0-28 |
§ Е2-1-29 |
Уплотнение земляного полотна катком ДУ-16В за четыре прохода по одному следу |
Машинист 6разр.-1 |
1000 м3
|
0,1 |
0,92 (0,92) |
0-97,5 |
0,09 (0,09) |
0-10 |
ИТОГО |
37,11 (37,11) |
37-38 |
Примечание: Срезка недобора грунта и его вывоз нормируются в каждом конкретном случае отдельно.
Работы по устройству выемки выполняет бригада численностью 5 чел.:
Машинист экскаватора 6 разр. 1
Помощник машиниста 5 разр. 1
Машинист бульдозера 6 разр. 1
Машинист автогрейдера 6 разр. 1
Машинист катка 6 разр. 1
Качество выполнения работ контролируют согласно табл .3.5.
Таблица 3.5 Контроль качества выполнения работ.
Операция |
Предмет контроля |
Лицо, осуществляющее контроль |
Вид контроля |
Снятие растительного слоя грунта |
Толщина слоя |
Мастер |
Инструментальный |
Разработка грунта выемки |
Отметки подошвы выемки, проектные отметки, уклоны, крутизна откосов |
Мастер (геодезист) |
Инструментальный |
Планировка верха земляного полотна и откосов выемки |
Соответствие профиля рабочим чертежам, ровность поверхности |
Прораб (мастер, геодезист) |
Инструментальный |
Нарезка кюветов |
Положение в плане, уклоны, отметки дна, крутизна откосов |
То же |
Инструментальный |
Уплотнение верха земляного полотна |
Степень уплотнения (коэффициент уплотнения грунта) |
Лаборант |
Лабораторный |
Примечание: Контроль каждой операции осуществляется в процессе работ.
При устройстве земляного полотна допускаются следующие отклонения (±) геометрических размеров:
Высотные отметки продольного профиля50 мм
Расстояние между осью и бровкой земляного полотна10 см
Поперечные уклоны ..................................................... 0,010
Крутизна откосов .... 10%
· Технико-экономические показатели.
На 1000 м3
выемки
Затраты труда 4,7 чел.-дня
Потребность в машинах . . . 3,0 маш.-смены
Выработка на 1 рабочего 200 м3
Прямая заработная плата бригады 37 р. 38 к.
3.4.3.4 Материально-технические ресурсы.
Потребность комплексной механизированной бригады в машинах, оборудовании и приспособлениях определена из расчета оптимальной их загрузки:
Экскаватор-драглайн Э-10011А 1
Бульдозер ДЗ-17 (Д-492А) 2
Бульдозер ДЗ-8 1
Автогрейдер ДЗ-31-1 ......... 1
Каток полуприцепной на пневмошинах ДУ-29 1
Автомобиль-самосвал КАМАЗ-551
грузопд. -13 тн 5
3.4.3.5 Техника безопасности.
При производстве работ по устройству земляного полотна необходимо соблюдать правила техники безопасности, приведенные в соответствующих разделах и «Правил техники безопасности при строительстве, ремонте и содержании автомобильных дорог» и СНиП III-4-80 «Техника безопасности в строительстве».
Ежесменно отслеживать состояние и осадку участка существующей дороги в месте выполнения работ по выторфовке.
Постоянно следить за дислокацией дорожных знаков согласно согласованной с ГИБДД схеме, ограничивая движение тяжелых транспортных средств по полосе дороги у места выполнения работ по выторфовке.
Разработки дополнительных мероприятий по обеспечению безопасности труда не требуется
Проект производства работ по строительству дорожной одежды.
3.5.1 Технологическая карта на устройство двухслойного основания.
3.5.1.1 Область применения.
Технологическая карта составлена на устройство двухслойного основания при Реконструкции участка автомобильной дороги Вологда-Кириллов - Пудож - Медвежьегорск, км 533 км 544. Ширина нижнего слоя основания 9,2 м, толщина в плотном теле - 25 см. Ширина верхнего слоя основания 8,6 м, толщина в плотном теле – 15 см.
3.5.1.2 Указания по технологии производственного процесса.
До устройства основания должны быть полностью закончены работы по возведению земполотна.
При устройстве основания выполняют следующие работы:
- Чистую планировку песчаного подстилающего слоя;
- вывозку и распределение ЩГС для нижнего слоя;
- уплотнение нижнего слоя самоходными катками с поливкой водой;
- вывозку и распределение черного щебня , фр. 20-40 мм, для верхнего слоя;
- уплотнение слоя самоходными катками;
- вывозку и распределение черного щебня, фр.10-20 мм и уплотнение самоходными катками.
3.5.1.3 Устройство нижнего слоя основания.
Разравнивание ЩГС производят автогрейдером за пять-шесть проходов по одному следу, после чего основание профилируют за 8-10 проходов.
ЩГС уплотняют самоходными катками DYNAPAC с гладкими вальцами массой 10 т. Уплотнение начинают от обочины и постепенно перемещаются к оси дороги с перекрытием предыдущей прикатанной полосы на 1/3 ширины вальца. Первые проходы катка делают со скоростью 1,5-2 км/ч, в конце укатки скорость может быть увеличена до максимальной, но без перегрузки двигателя. Количество проходов три - четыре по одному следу на каждой полосе, по мере приближения к оси дороги уменьшается до' одного. Достигнув середины, каток возвращают к обочине, и уплотнение повторяют в том же порядке.
Для уплотнения ЩГС необходимо 25 проходов катка по одному следу. Окончательное количество проходов устанавливают пробной укаткой.
Поливку ЩГС поливо-моечной машиной начинают после трех проходов катка и производят ее равномерно, периодически, непосредственно перед катком. Норма розлива воды 15-25 л/м2
(большие величины для жаркого времени). Нельзя допускать переувлажнение ЩГС и земполотна. Признаком достаточного увлажнения служит влажное состояние нижних граней щебня, лежащих на поверхности основания.
Уплотнение считается законченным, если перед вальцом катка не образуются волны и не остается следа, а щебень не вдавливается в уплотненный слой.
3.5.1.4 Устройство верхнего слоя основания.
Устройство основания из черного щебня устраивают по принципу последовательного расклинивания крупных фракций щебня менее крупными. Устройство оснований включает доставку черного щебня к месту работ по фракциям; распределение черного щебня фракции 20(25)-40 мм по подготовленному нижнему слою; предварительное уплотнение; распределение черного щебня фракций 10(15)-20(25) мм и заполнение пустот в более крупном щебне; уплотнение второй фракции черного щебня.
Покрытия и основания из горячего щебня устраивают в сухую погоду, если температура воздуха весной и летом не ниже 5 °С, а осенью - не ниже 10 °С.
Покрытия и основания из теплого щебня устраивают в сухую погоду при температуре воздуха до -10 °С и скорости ветра не более 3 м/с и при температуре воздуха до -5 °С, если скорость ветра не более 5 м/с.
Покрытия из холодного щебня устраивают, когда температура воздуха весной не ниже +5 °С, осенью - не ниже +10 °С (за 3-4 недели до начала осенних дождей).
Горячий щебень распределяют сразу после доставки на место работ, теплый щебень можно временно складывать по фракциям в зоне работ и хранить не более 1-2 ч (в зависимости от температуры воздуха); холодный щебень можно складывать и хранить по фракциям в зоне работ без ограничения времени, не допуская его загрязнения.
Рабочая температура горячего, теплого и холодного черного щебня при его распределении должна соответствовать требованиям табл.3.6. Температуру горячего и теплого щебня проверяют в каждом прибывающем на место укладки автомобиле-самосвале.
Таблица 3.6 Температура черного щебня перед укладкой.
#G0
Температура воздуха, °С
|
Температура щебня, °С
|
горячего |
теплого |
холодного |
Более 10
|
120
|
80
|
60
|
10
|
5-10
|
130 |
90 |
70 |
10 |
0-5 |
140
|
100
|
80
|
10
|
0-(-5)
|
150
|
110
|
90
|
-
|
5-(-10)*
|
-
|
120
|
100
|
-
|
_____________
* Текст в соответствии с оригиналом. Примечание "КОДЕКС"
Примечание. В случае применения ПАВ температура горячего щебня при укладке может быть снижена на 20 °С.
Черный щебень фракции 20(25)-40 мм распределяют с помощью щебнеукладчиков слоем, толщина которого на 25-30% более проектной. Допустимо распределение этой фракции щебня автогрейдером.
Черный щебень фракции 20(25)-40 мм уплотняют 4-6 проходами катка по одному следу с таким расчетом, чтобы в нем остались пустоты, заполняемые расклинивающей фракцией при последующей операции.
При распределении второй фракции щебня 10(15)-20(25) мм необходимо обеспечить заполнение поверхностных пустот, образовавшихся в первой фракции щебня, избегая образования самостоятельного слоя; фактический расход черного щебня второй фракция корректируют в процессе распределения (см. табл.17).
Распределив щебнеукладчиком расклинивающую фракцию, пустоты заполняют наметанием щебня механическими щетками.
Расклинивающую фракцию уплотняют 3-4 проходами тяжелого катка по одному следу.
Покрытие (основание) из черного щебня окончательно уплотняют 6-8 проходами тяжелого катка по одному следу. Необходимое количество проходов катка устанавливают пробным уплотнением.
В начальный период эксплуатации покрытия или основания из черного щебня, особенно из холодного, должен быть обеспечен уход, заключающийся в регулировании движения по всей ширине проезжей части и в ликвидации возможных деформаций. Продолжительность окончательного формирования слоя из горячего (теплого) черного щебня зависит от погодных условий и интенсивности движения и находится в пределах от 7 до 15 сут.; период формирования слоя из холодного черного щебня на жидких битумах и дегтях - 20-30 сут.
Покрытие на основании из черного щебня может быть построено через 8-10 сут. после выявления и исправления дефектов основания.
3.5.1.5 Технический контроль при строительстве оснований.
При строительстве покрытий и оснований контролируют: качество каменных и вяжущих материалов; технологию приготовления смесей и черного щебня; технологию устройства покрытий и оснований и их качество.
Качество материалов, применяемых для строительства покрытий и оснований, проверяют методами, установленными соответствующими государственными стандартами (см. п.8.24). Каменные материалы оценивают по зерновому составу, содержанию пылевидных, илистых и глинистых частиц, качество вяжущих - по показателям свойств (глубина проникания, вязкость и др.). Проверяют рабочую температуру вяжущих, подготавливаемых к розливу, сцепление вяжущего и каменного материалов.
Для контроля качества щебня, гравия и песка, поступающих на строительство, отбирают пробы в соответствии с ГОСТ 8269-64 и #M12293 0 1200003348 3271140448 205796632 4294961312 4293091740 2693571757 4294961312 4293091740 5276744ГОСТ 8735-65#S. Пробы каменных материалов, получаемых непосредственно из месторождений, отбирают в карьере или на складах, куда они поступают, а при способе смешения на дороге - непосредственно на дороге.
При использовании каменного материала, полученного в результате киркования старого покрытия, или при устройстве покрытия способом смешения на дороге пробу общей массой 8-10 кг отбирают из валика через каждые 0,5 км.
Для контроля зернового состава минеральных порошков берется одна проба массой 1 кг из каждой партии, а для грунтов пробы по 1 кг отбирают в карьере из трех-четырех разных мест, после чего их смешивают и берут 1 кг.
Для контроля качества поступающего на базу вяжущего из каждой получаемой партии отбирается средняя проба массой 2-3 кг. Проба не должна содержать посторонних примесей.
Качество ПАВ и активаторов следует контролировать в соответствии с Инструкцией ВСН 59-68.
Температуру приготавливаемого и готового вяжущего контролируют не реже, чем через 2 ч.
При использовании ПАВ наряду с проверкой свойств применяемого битума следует дополнительно определять вязкость или глубину проникания смеси битума с ПАВ после окончательного смешения с битумом. Вязкость или глубину проникания битума с добавкой устанавливают путем испытания специально приготовленной смеси из применяемого битума и добавки в принятых соотношениях.
При приготовлении черного щебня контролируют влажность каменных материалов, дозирование материалов, температуру и вязкость вяжущего, продолжительность перемешивания, температуру и качество готового черного щебня.
Влажность каменных материалов проверяют в случае их дозирования в холодном состоянии (до просушки).
При отсутствии автоматизации управления дозировочным оборудованием правильность дозирования контролируют путем проверки работы дозировщиков не менее 3-4 раз в смену.
Температурный режим каменного материала, вяжущего и готового черного щебня непрерывно контролируется. Температуру готового черного щебня проверяют в каждом замесе.
Ровность покрытия и основания, поперечный профиль проверяют в процессе уплотнения трехметровой рейкой, укладываемой на поверхность параллельно оси дороги. Просвет на покрытиях под рейкой не должен превышать 7 мм.
Поперечный профиль проверяют на каждых 100 м покрытия шаблоном; допускается отклонение против норм в пределах ±5%.
Толщина и ширина покрытия и основания проверяются в процессе уплотнения и по его окончании. Толщину покрытия проверяют путем пробных вскрытий - не менее одного на 1 км, если ширина покрытия не более 7 м, и не менее одного на 7000 м при большей ширине. Вырубки и керны следует брать из середины полосы движения.
Отклонение толщины от заданной допускается в пределах 10%, но не более 10 см. Ширину проверяют через каждые 100 м.
Степень уплотнения готовых покрытий и оснований, устраиваемых по способу пропитки и из черного щебня, проверяют пробным проходом тяжелого катка (не менее 15 т); при этом не должно наблюдаться движения смеси, ее смешения или образования волн впереди катка.
3.5.1.6 Технико-экономические показатели.
На 1000 м2
основания
Затраты труда 4,2 чел.-дня
Потребность в машинах . . . 4,0 маш.-смены
3.5.1.7 Материально-технические ресурсы.
Потребность комплексной механизированной бригады в машинах, оборудовании и приспособлениях определена из расчета оптимальной их загрузки:
Автогрейдер ДЗ-31-1 ......... 1
Каток DYNAPACCC-422 1
Автомобиль-самосвал
КАМАЗ-5511, грузопод.-13 тн 7
3.5.2 Технологическая карта устройство асфальтобетонного покрытия
3.5.2.1 Область применения.
В технологической карте предусмотрено устройство однослойного асфальтобетонного покрытия шириной 7 м из плотной асфальтобетонной смеси из каменных материалов изверженных пород:
В технологической карте длины сменных захваток приняты из ;
условия доставки асфальтобетонной смеси с асфальтобетонного завода, имеющего производительность 60 т/ч и последующего ввода второй смесительной установки с производительностью 150 т/ч.
Длинна сменной захватки при работе одного смесителя производительностью 60 т/ч составляет 366 пм/смену, при работе второй установки с производительностью 150 т/ч составляет 914 пм/смену
3.5.2.2 Указания по технологии производственного процесса
* Асфальтобетонное покрытие из горячих смесей укладывают в сухую погоду
при температуре воздуха не ниже -50
С. весной и летом и не ниже -100
С. В осеннее время, асфальтобетонная смесь должна удовлетворять требованиям ГОСТ 9128-84.
3.5.2.3 Подготовка основания.
Основание должно соответствовать -требованиям СНиП 3.06.03-85. Перед устройством асфальтобетонного покрытия основание очищают от пыли и грязи автомобильной щеткой за один - два прохода по одному следу. Если этих мер недостаточно основание проливают поливомоечной машиной и полностью просушивают.
3.5.2.4 Устройство асфальтобетонного слоя
Температура асфальтобетонной смеси приготовленной на битумах БНД 90/130 должна быть не ниже 120 °С.
Температуру смеси проверяют термометром в каждом автомобиле-самосвале.
Укладку асфальтобетонной смеси производят асфальтоукладчиком DYNAPACи ведут последовательно полосами шириной 3,75м. Длину полос устанавливают с таким расчетом, чтобы к моменту укладки смежной полосы смесь на.уложенной и укатанной полосе не успела остыть.
Исходя из среднемесячной температуры воздуха, длину полосы принимаем на защищенных от ветра участках 100-150 м, на открытых участках 50-80 м.
3.5.2.5 Установка копирных струн.
Копирные струны -являются базой для работы автоматических систем обеспечения ровности, Поэтому точность и тщательность выполнения операций по установке копирных струн является одним из важнейших условий обеспечения качества работ.
Установку копирных струн производят перед устройством а/б покрытия. Для установки струн необходимы металлические стойки в комплекте с поперечными штангами и струбцинами. Штанги закрепляются на стойках на требуемой высоте с помощью зажимных винтов и они могут перемещаться по стойке и в горизонтальной плоскости в струбцине. На конце штанги имеется прорезь для установки в нее струны. Струны устанавливают с двух сторон проезжей части. Каждая струна должна быть строго параллельна оси дороги.
Сначала вдоль полотна забивают нивелирные колышки , которые служат отметкой от которой измеряется высота установки струны, а в плане струны устанавливаются точно над колышками. В продольном направлении расстояние между колышками принимаем равным 15-17 м поперечном 5,75-8,75 м. При установке колышков необходимо следить, чтобы линия их верхушек проходила параллельно кромке покрытия. Высоту колышков устанавливают на уровне кромки, устраиваемого покрытия. Для установки колышков в плане в начале и в конце участка разбивают поперечники, на которых забивают начальные и конечные колышки на принятом от оси дороги расстоянии, а затем с помощью теодолита в створе начального и конечного колышков устанавливают промежуточные. При устройстве дороги с двускатным профилем высотные отметки противостоящих друг другу колышков на поперечнике должны быть строго одинаковы, а с односкатным профилем их отметки должны находиться в одной плоскости поверхности будущего покрытия.
Стойки в сборе с поперечными штангами ставят на внешней стороне от линии расположения колышков на расстоянии 30 см. Перемещением струбцины по стойке и поперечной штанге в струбцине добиваются такого положения, чтобы прорезь для струны находилась точно над центром колышка и на 6 мм выше принятой высоты установки струны. Высоту расположения прорезей измеряют линейкой, а совмещение прорезей со створом нивелирных колышков проверяют по теодолиту.
После установки стоек производят натяжение струн перед первой стойкой на расстоянии 10-12 м устанавливают барабан и закрепляют его якорем. В конце участка за последней стойкой устанавливают второй барабан. Барабаны в плане должны находиться точно на линии нивелирных колышков иначе произойдет смещение струны относительно оси дороги. Высота их закрепления должна быть удобной для вращения рукоятей.
Снятую с катушки струну раскладывают вдоль линии натяжения и концы ее закрепляют в барабанах. Струну предварительно натягивают и вставляют в прорези штанг. После окончательной проверки нахождения струны в плане и по высоте за счет перемещения струбцин и поперечных штанг ее окончательно натягивают и закрепляют стопорные винты струбцин. Струна должна быть натянута до такой степени, чтобы ее провисание не было заметно на глаз. Высота установки струны над верхом нивелирного колышка должна составлять не менее 30 см и не более 125 см. Длина участка с установленными струнами берется равной сменной производительности машин. Для того чтобы не производить переналадку машин пристроительстве основания и покрытия на следующем участке установку струн выполняют следующим образом: устанавливают нивелирные колышки и стойки натяжные барабаны закрепляют перед последней стойкой построенного участка и за последней стойкой следующего участка, после предварительного натяжения струну вставляют в про резь., штанги последней стойки построенного участка и выполняют окончательную выправку положения струны. Таким образом обеспечивают установку струны на новом участке на той же высоте.
Работы по установке копирных струн выполняет бригада дорожных рабочих под руководством инженера-геодезиста. В процессе работы комплекта машин операторы машин должны постоянно следить хорошо ли струны держатся в прорезях штанг и туго ли натянуты между стойками. Струны снимают после окончания всего комплекса работ по устройству покрытия.
3.5.2.6 Подготовка асфальтоукладчика к работе.
При подготовке асфальтоукладчика к работе проверяют работоспособность узлов и агрегатов машины, системы автоматизации; исправность контрольно-измерительного оборудования.
Перед началом работы проверяют общее состояние машины, включающее отсутствие повреждений колесного хода, бункера, питателя, шнеков, тяговых брусьев, шаровых соединений, крепежа, панелей и рычагов управления. Проверяют работу приборов освещения, гидромотора трамбующего бруса, гидроцилиндров, питателей и шнеков, давление в гидромагистралях, ход машину.
Асфальтоукладчик готов к работе, если ширина его рабочего органа соответствует ширине укладываемого покрытия, для чего к торцам выглаживающей плиты, имеющей основную ширину 3 м, прикрепляют уширитель, чтобы увеличить ширину до 3,75 м.
3.5.2.7 Правила управления асфальтоукладчиком.
Асфальтоукладчик управляется одним машинистом оператором. На время работы к машине приставляют бригаду вспомогательных рабочих, которые следят за полным использованием а/б смеси и ровностью укладываемого покрытия производя все вспомогательные работы вручную.
Машинист-оператор устанавливает асфальтоукладчик с заданной шириной рабочего органа на исходную позицию, поднимает рабочий орган и подкладывает поднего два бруса толщиной укладываемого слоя. Переводом переключателя подъема рабочего органа в положение «вниз» выглаживающую плиту опускают на бруски и переключатель оставляют в этом положении на все время работы машины. Винтовым регулятором толщины устанавливают угол атаки плиты около 2 °.
Боковые стенки бункера выставляют в вертикальное положение, включают одну из рабочих скоростей, руководствуясь тем, что чем больше толщина укладываемого слоя и чем больше в смеси фракции щебня, тем меньше должка быть скорость укладки.
Устанавливают лыжу и опирают на них щуп датчика под углом 45°. Подключают работающие датчики через разъемы к системе регулирования. Штоки гидроцилиндре в подъема и опускания тяговых брусьев ставят в среднее положение, переключатели на пультах управления - в положении как при настройке каналов стабилизации продольного и поперечного профиля.
Водителю самосвала дают команду загрузить бункер а/б смесью. При разгрузке самосвала возможно просыпание смеси на дорогу перед укладчиком, удаление ее с поверхности дороги производят рабочие вспомогательной бригады.
С началом работы при отсутствии раковин и сдвигов на поверхности уложенного покрытия прекращают подогрев выглаживающей плиты. При выборе смеси из середины буккера включают в работу гидроцилиндры поворота стенок бункера, ссыпая остатки смеси на питатели. Рабочие вспомогательные бригады очищают стенки лопатами от остатков смеси. При уменьшении смеси в шнековой камере до уровня, после которого возможно образование дефектов покрытия. Датчики уровня должны передать сигнал на включение в работу питателей и шнеков. В этот момент оператор должен контролировать и в случае отказа в срабатывании датчиков в ручную включить в работу питатель и шнек.
Во время укладки оператор должен следить за направлением движения укладчика так, чтоб один край рабочего органа двигался вдоль заданной проектной линии - края основания дороги или ранее уложенного покрытия. При непрерывном подходе, самосвале в со смесью и цикле разгрузки 3-4 минуты напряженность работы возрастает, оператор должен быть очень внимательным и контролировать работу всех механизмов. В случае появления неисправности оператор должен остановить разгрузку самосвалов, выбрать из бункера всю смесь, а затем приступить к устранению неисправности. При необходимости укладчик от смеси освобождается в ручную с привлечением рабочей вспомогательной бригады.
Рабочие вспомогательной бригады по указанию оператора очищают стенки бункера от остатков смеси после загрузки каждого самосвала, удаляют смесь, просыпавшуюся на дорогу под колеса укладчика, помогают подложить бруски под выглаживающую плиту и регулировать угол атаки ручным регулятором толщены.
В период работы перед каждой остановкой машины оператор должен предварительно выключить из работы трамбующий брус, чтобы он не производил уплотнение в момент стоянки.
3.5.2.8 Укладка асфальтобетонной смеси.
До начала укладки необходимо проверить чистоту укладываемого слоя, его поперечный уклон и ровность. До устранения дефектов основания укладку смеси не производят.
При укладке многощебенистых а/б смесей асфальтоукладчиком толщина укладываемого слоя должна быть на 10-15% больше проектной, а при укладке в ручную на местах недоступных асфальтоукладчика- на 25-30%.
Укладку смеси ведут одним асфальтоукладчиком в две полосы. После установки асфальтоукладчика в исходное положение машинист должен включить на 15 минут устройство для разогрева выглаживающей плиты и установить ее на заданную толщину асфальтобетонного слоя и величину поперечного уклона.
При раскладке смеси в случае избытка ее между шнеками и трамбующим брусом (переполнение шнековой камеры) должна срабатывать система автоматического контроля и выключения питателя. При отсутствии автоматики количество подаваемой смеси регулируется заслонкой. В противном случае произойдет наползание выглаживающей плиты и утолщение покрытия, которое после прохода асфальтоукладчика трудноустранимо (только вручную).
Поперечные сопряжения покрытия должны быть перпендикулярны оси дороги. При перерывах в работе края ранее уложенной полосы обрезают фрезой и обмазывают жидким битумом. Обрезку производят перед началом устройства покрытия.
Продольные швы обрабатывают следующим образом: впереди асфальтоукладчика по уложенной полосе по осевой линии смесь обрезается фрезой, смонтированной на уплотняющем катке так, чтобы получилась ровная линия. Для обеспечения лучшего сцепления в месте стыка ранее уложенного и укладываемого, асфальтобетона шов смазывают нагретым вязким битумом. После прохода асфальтоукладчика уложенную смесь на шве выравнивают, при этом смесь не должна срезаться заподлицо с укатанной соседней полосой, а создается валик из смеси на шве шириной 10-15 см и толщиной 1-2 см (запас на уплотнение).
Отдельные места с недоброкачественной поверхностью или смесью вырубается и заделывается смесью из бункера асфальтоукладчика.
Укладывает смесь машинист асфальтоукладчика б разряда. В процессе' работы машинист управляет машиной, регулирует подачу смеси, следит за тем, чтобы трамбующий брус был в работе и выглаживающая плита при необходимости прогревалась.
Асфальтировщик 3-го разряда находится у приемного бункера и визуально проверяет качество смеси. В конце рабочей смены помогает машинисту асфальтоукладчика в очистке машины.
По одному асфальтобетонщику (5, 4, 3 разрядов) следуют за укладчиком и окончательно обрабатывают поверхность уложенного слоя, кромки и швы, а также заделывают дефекты покрытия.
Асфальтобетонщик 4-го разряда контролирует ровность покрытия и поперечные уклоны .заделывает сопряжение полос.
Асфальтобетонщик 5 разряда является старшим в звене и отвечает за общее качество работ. Он принимает участие в работе по отделке поверхности покрытия и проверяет качество а/б смеси, правильность обработки предшествующего слоя битумом. Он контролирует толщину слоя и регулирует положение выглаживающей плиты асфальтоукладчика, дает указания машинистам катков о режиме укладки. После укладки покрытия он осматривает готовый участок и дает указания на исправление обнаруженных дефектов.
Асфальтобетонщик 3-го разряда дает указания по резке кромки швов в местах сопряжения и выполняет другие вспомогательные работы.
3.5.2.9 Уплотнение асфальтобетонной смеси.
Температурный интервал каждого этапа укладки примерно одинаков и составляет в среднем около 20°С, но по продолжительности времени этапы сильно отличаются друг от друга из-за различной скорости остывания .смеси сразу после ее раскладки в покрытии и в конце укатки.
Таблица 3.7 Температура смеси на этапах уплотнения.
Этап уплотнения смеси в покрытии |
Температура смеси (0
С) тип Б |
Начало предварительного |
135-130 |
Начало основного |
115-110 |
Начало заключительного |
95-90 |
Окончание заключительного |
75-70 |
Температура начала укатки на последующем этапе соответствует окончанию работ на предыдущем участке.
Ориентировочное время остывания смеси от начала до конца ее уплотнения всеми катками можно определить по формуле:
2 Öh3
(То - Т)
t =-------------------------------------------
мин.
(1+0,1Vв).
(Т-Тв)
где: h -толщина слоя смеси в рыхлом состоянии, см;
Т - температура смеси в покрытии сразу после укладчика. °С;
То - температура смеси в момент окончания укатки. °С;
Тв - температура наружного воздуха (основания) при укатке. °С;
Vв - скорость ветра во время уплотнения смеси, м/сек.
На основании таблицы общего времени охлаждения различных слоев смеси от 140-135 С до 65-60 с при определенных погодных условиях в рамках этого времени необходимо выполнить весь объем работ по уплотнению
Толщина слоя покрытия см |
Отводимое по условиям остывания слоя ориентировочное время (мин) на выполнение операции его уплотнение всеми катками при Температуре наружного воздуха |
10-12 |
0..2 °С |
4..5°С |
8..10°С |
13..15°С |
18..20°С |
23. .25 °С |
20-23 |
24-27 |
28-30 |
32-35 |
37-40 |
43-48 |
Указанное время соответствует умеренному ветру (не более 3-5 м/с). При повышении скорости ветра до 8-10 м/с это время уменьшается на треть, а в солнечную безветренную погоду - увеличивается примерно на треть.
Уплотнение смеси следует начинать после ее укладки.
Уплотнение горячей смеси типа Б следует производить виброкатком DYNAPAC СС -222 массой 7,5 т за пять проходов по одному следу и окончательно - DYNAPAC СС -422, 10 т за 7 проходов по одному следу.
Катки должны двигаться от внешнего края укладываемой полосы к оси дороги, а затем от оси к краю перекрывая каждый след на 20-30 см.
Рабочая скорость движения катков должна быть в начале укатки 1,5-2 км/час, а после 5-6 проколов может быть увеличена до 3-5 км/час. Для обеспечения ровности покрытия каток должен трогаться или изменять направление плавно без рывков. Во избежание раскатывания смеси в конце укладываемой полосы следует укладывать упорную доску или рейку. Для предотвращения прилипания 'смеси к вальцам катков их необходимо смачивать водой.
3.5.2.10 Начальное укатывание.
Дорожные катки на слабоуплотненной АБС должны плавно начинать движение, не останавливаться, а также отклонять валец под небольшим углом, когда они останавливаются для включения реверсирования движения. Наибольшая интенсивность уплотнения дорожного покрытия достигается именно в процессе начальной укатки, и поэтому важно, чтобы каток двигался как можно дольше. Когда каток должен остановиться, лучше делать это на холодном дорожном покрытии. Еслиоставить дорожный каток, стоящим на горячем дорожном покрытии, особенно рядом с асфальтоукладчиком, то на свежем асфальтобетоне останется след от вальца катка, который трудно устраняется.
3.5.2.11 Промежуточная укатка.
Промежуточная укатка не всегда обязательна при выполнении проекта. Если достаточная плотность не может быть получена после начальной укатки дорожным катком, промежуточный этап обязателен. Катки для промежуточной укатки использовать на более высоких скоростях, чем в режиме начальной укатки дорожным катком, промежуточный этап обязателен. Катки для промежуточного этапа используются на более высоких скоростях, чем в режиме начальной укатки. Промежуточные дорожные катки должны осуществлять укатку всего покрытия и не сосредотачиваться на его средней части.
3.5.2.12 Технико-экономические показатели.
Производительность звена в смену 914 м
Трудовые затраты на смену 914 чел/см
3.5.2.13 Материально-технические ресурсы.
Состав звена:
Асфальтоукладчик DYNAPAC 1
Каток самоходный вибрационный
7,5 тн DYNAPACCC-222 1
Каток самоходный вибрационный
10 тн DYNAPACCC-422 1
Автомобиль-самосвал
КАМАЗ-5511, грузопод.-13 тн 8
3.5.2.14 Контроль качества.
При выполнении строительно-монтажных работ на объекте: «Реконструкции участка автомобильной дороги Вологда - Кириллов - Пудож - Медвежьегорск, км 533 - км 544» осуществляются следующие виды контроля качества:
Лабораторный контроль - физико-механические испытания дорожностроительных материалов на соответствие требованиям ГОСТ, СНиП, ТУ и др. ( Лаборатория ООО «Трансстрой»)
Геодезический контроль - производится в процессе работ при возведении земляного полотна, искусственных сооружений, проверяется правильность установки плановой и высотной разбивки, оси земляного полотна и искусственных сооружений, соответствие проекту уклонов водоотводных сооружений. Ответственные за производством геодезического контроля на участке - производитель работ, геодезист, инженер-резидент, представитель заказчика.
Входной контроль - проходят конструкции, изделия, материалы, поступающие на объект реконструкции (элементы гофрированных оцинкованных водопропускных труб, конструкции железобетонных труб, битум, рубероид, цемент) поверяется их соответствие паспортам, стандартам, техническим условиям и другим документам, подтверждающих их качество и требованиям рабочих чертежей, а также соблюдается соблюдение правил их разгрузки и хранения, Производитель работ путем внешнего осмотра проверяет соответствие качества поступаемых материалов и изделий на месте монтажа. Ответственный за проведение входного контроля - производитель работ.
Операционный контроль - проходя завершенные производством операции, что позволяет своевременно выявить дефекты, причины их возникновения и принять меры к их своевременному устранению и предупреждению. Проверяется выполнение технологических схем производства работ и соответствие выполняемых работ рабочим чертежам, СНиПам, стандартам, рабочему проекту. Ответственный за проведение операционного контроля -производитель работ, геодезист, инженер-резидент, представитель заказчика, лаборатория.
Приемочный контроль - производится для проверки и оценки качества законченных сооружений или их частей, а также скрытых работ и отдельных ответственных конструкций с составлением актов по формам, установленным СНиП. Ответственный за приемочный контроль - производитель работ, лаборатория, инженер-резидент, представитель заказчика.
Инспекционный контроль - осуществляется согласно должностной инструкции главного инженера.
4 ОРГАНИЗАЦИЯ РАБОТ В ДОРОЖНО-СТРОИТЕЛЬНОМ ОТРЯДЕ
Строительные звенья, бригады, ведущие сооружения автомобильной дороги, объединяют в подразделения, которое называют дорожно-строительный отряд (ДСО).
При организации работ в ДСО следует рассмотреть следующие задачи:
1. Когда должно приступить к работе звено или бригада, в какие сроки будет выполнена порученная им работа, и в какие сроки должно быть начато и завершено строительство дороги в целом;
2. Определить численный состав ДСО и его техническую вооруженность;
3. Определить потребность в топливосмазочных и дорожно-строительных материалах.
Перечисленные задачи решают главным образом путем составления календарного линейного графика. Кроме того выполняют соответствующие расчеты и составляют сводные ведомости.
4.1 Составление линейного календарного графика реконструкции.
При назначении сроков выполнения работ необходимо подсчитать число календарных дней.
При реконструкции принят вахтовый метод ведения работ. Следовательно, коэффициент, учитывающий выходные дни, определяют равным 1.
Календарные дни при строительстве исскуственных сооружений определяют по формуле:
Аиск.с.
=Nиск.с.
/nиск.с.
, (4.1)
где,
Nиск.с.
– затраты труда на строительстве водопропускных сооружений, чел.дн.;
nиск.с.
– количество рабочих в бригаде.
Для строительства земляного полотна и дорожной одежды, число календарных дней определяем по формуле:
А=((L/lзах.
)+tрп
), (4.2)
где,
L – протяженность строящейся дороги, м;
lзах.
– длина захватки, м;
tрп
– время развертывания потока.
Применительно к специализированному потоку период развертывания составляет время с начала работы первого звена первого частного потока на первой захватке, до начала работы на этой захватке последнего звена последнего частного потока.
В расчетах принято:
tрп
=(SПзв
-1), дней, (4.3)
где,
SПзв
– суммарное количество звеньев в частном потоке.
Таким образом, календарные сроки на строительстве работы сгруппированы по их видам и приведены в таблице 4.1.
Таблица 4.1 Календарные сроки работ по реконструкции.
№ п/п |
Наименование работ |
Кален-дарная продол-житель-ность, дни |
Сроки выполнения работ |
начало |
конец |
1 |
Подготовительные работы |
1.1 |
Рубка леса и кустарника |
75 |
1.04 |
14.06 |
1.2 |
Корчевка пней |
74 |
3.04 |
15.06 |
2 |
Искусственные сооружения |
2.1 |
Водопропускные трубы |
42 |
1.05 |
11.06 |
2.2 |
Мост через реку Тамбица |
30 |
1.06 |
30.06 |
2.3 |
Мост через реку Филиппа |
30 |
1.07 |
30.07 |
3 |
Земляное полотно |
3.1 |
Снятие растительного слоя |
70 |
5.04 |
4.07 |
3.2 |
Выторфовывание болот |
72 |
4.04 |
14.06 |
3.3 |
Рыхление откосов существующего земполотна |
83 |
4.04 |
25.06 |
3.4 |
Нарезка уступов |
63 |
4.04 |
5.06 |
3.5 |
Возведение насыпи с уплотнением |
114 |
8.04 |
30.07 |
3.6 |
Разработка выемки |
7 |
6.04 |
15.06 |
3.7 |
Водоотводные канавы |
56 |
15.06 |
9.08 |
3.8 |
Планировка земполотна и откосов насыпи и выемки |
107 |
15.04 |
30.07 |
3.9 |
Укрепление откосов насыпи и выемки засевом трав |
15 |
1.09 |
16.09 |
4 |
Дорожная одежда |
4.1 |
Устройство нижнего слоя основания из ЩПГС |
58 |
2.07 |
28.08 |
4.2 |
Устройство верхнего слоя основания из черного щебня |
72 |
4.07 |
13.09 |
4.3 |
Розлив битума по верхнему слою основания |
25 |
26.08 |
19.09 |
4.4 |
Устройство покрытия из плотной мелкозернистой а/б смеси |
26 |
1.09 |
26.09 |
4.4 |
Устройство обочин ЩПС |
39 |
2.09 |
10.10 |
4.5 |
Укрепление обочин засевом трав |
24 |
5.09 |
14.10 |
5 |
Обустройство дороги |
20 |
25.09 |
15.10 |
Всего:
|
198
|
1.04
|
15.10
|
4.2 Численный состав дорожно-строительного отряда.
Численный состав ДСО определяется по линейному календарному графику. Продолжительность строительного сезона с 01.04 по 15.10 – 198 дней.
Результаты расчетов сведены в таблицу 4.2.
Таблица 4.2 Численный и квалифицированный состав ДСО.
№ п/п |
Наименование специалистов |
Подготовительные работы |
Искусственные сооружения |
Строительство земполотна |
Устройство основания |
Устройство покрытия |
Устройство откосов земполотна |
Устройство обочин |
Обустройство дороги |
Всего |
Количество/разряд |
1 |
Машинист |
1/6 |
2/6 |
6/6 |
2/6 |
3/6 |
2/6 |
3/6 |
19 |
2 |
Пом.машиниста |
1/6 |
1/5 |
1/5 |
3 |
3 |
Тракторист |
1/6 |
1/6 |
2 |
4 |
Водитель |
1/2кл |
14/2кл |
7/2кл |
8/2кл |
1/2кл |
1/2кл |
32 |
5 |
Вальщик |
1/6 |
1 |
6 |
Чокеровщик |
1/5 |
1 |
7 |
Рабочий |
2/3,1/5 |
4/2-4 |
4/3-5 |
12 |
Примечание:
1.В таблице учтено совмещение работ на двух машинах в зависимости от коэффициента использования строительной техники;
2.Потребное количество дорожно-строительных рабочих приведено без учета коэффициента сменной.
5 ТЕХНИКО-ЭКОНОМИЧЕСКИЕ ПОКАЗАТЕЛИ ОРГАНИЗАЦИИ РЕКОНСТРУКЦИИ И СМЕТНО-ФИНАНСОВЫЕ РАСЧЕТЫ
Общая стоимость любого строительства складывается из сметной стоимости отдельных объектов, сооружений, зданий, работ и затрат, которые определяются расчетами-сметами по объемам работ и другим данным в соответствии с действующими сметными нормами, ценами, расценками и тарифами. Такой расчет стоимости строительства называется сводной сметой. Это основной документ на весь период строительства.
В состав сметно-финансового расчета входят:
- сводный сметный расчет стоимости строительства;
- объектные и локальные сметы на виды работ;
- расчет прочих затрат, исчисляемых в % от стоимости строительства по действующим нормам;
- калькуляции стоимости материалов;
- каталог единичных расценок.
Сметно-финансовые расчеты выполнены по сборникам ГЭСН-2001, ЕРЕР 1984г.
Накладные расходы определены на основании МДС81-4.99 по виду строительно-монтажных работ в процентах от ФОТ рабочих-строителей и механизаторов.
Сметная прибыль определена на основании МДС 81-25.2001 по виду строительно-монтажных работ в процентах от ФОТ рабочих (строителей и механизаторов).
Затраты на временные здания и сооружения приняты на основании ГСН 81-05-01-2001 (с учетом к=0,8).
В сметный расчет включены дополнительные затраты при производстве работ в зимнее время по нормам ГСН 81-05-02-2001.
Сметная стоимость строительства в ценах 2002 г. составила – 156217,25 тыс.руб.
Сводный сметный расчет по объемам работ приведен в таблице 5.1.
Таблица 5.1 Сводный сметный расчет реконструкции автомобильной дороги «Вологда – Медвежьегорск, км 533 – 544»
№ п/п |
Наименование глав, объектов, работ и затрат |
Сметная стоимость, тыс.руб. |
Общая сметная стоимость, тыс.руб. |
Строительные работы |
Прочие затраты |
Подготовительные работы |
1 |
Отвод участка |
258,70 |
258,70 |
2 |
Разборка существующих искусственных сооружений |
80,22 |
80,22 |
3 |
Рубка леса и корчевка пней по трассе и на карьерах |
4191,97 |
4191,97 |
4 |
Переустройство существующей линии связи |
98,05 |
330,32 |
428,37 |
5 |
Переустройство существующей ВЛ-10 кВ |
0,38 |
35,56 |
35,94 |
Земляное полотно |
6 |
Земляное полотно. Кавальер |
5504,91 |
5504,91 |
7 |
Земляное полотно. Насыпь |
17115,13 |
17115,13 |
8 |
Укрепительные работы |
6489,37 |
6489,37 |
9 |
Рекультивация временных площадок. Технический этап |
15,75 |
15,75 |
10 |
Рекультивация временных площадок. Биологический этап |
437,78 |
437,78 |
11 |
Рекультивация карьеров «69 квартал», «Челмужи». Технический этап |
219,18 |
219,18 |
12 |
Рекультивация карьеров «69 квартал», «Челмужи». Биологический этап |
701,69 |
701,69 |
13 |
Устройство временных подъездов |
2282,75 |
2282,75 |
Искусственные сооружения |
14 |
Удлинение железобетонных труб Д=1,0 м, Д=1,5 м |
1219,36 |
1219,36 |
15 |
Лестничные сходы |
257,83 |
257,83 |
Дорожная одежда |
16 |
Дорожная одежда |
97847,43 |
97847,43 |
Пересечения и примыкания |
17 |
Земляное полотно |
683,16 |
683,16 |
18 |
Дорожная одежда |
2095,12 |
2095,12 |
19 |
Искусственные сооружения |
206,49 |
206,49 |
20 |
Обустройство |
130,52 |
130,52 |
21 |
Железнодорожный переезд |
129,04 |
129,04 |
Обстановка дороги |
22 |
Автобусные остановки |
6141,30 |
6141,30 |
23 |
Обустройство дороги |
3406,87 |
3406,87 |
Всего, общая сметная стоимость |
149878,86 |
Зная затарты труда по основному производству, определяем потребность в чел.-днях на весь комплекс производственных работ.
Апр
=1,4.
Аосн
(5.1)
где,
1,4 – коэффициент, учитывающий:
- работы подсобно-вспомогательного производства – 10%;
- работы на внутри простоечном транспорте – 2%;
- работы дополнительные, в зимний период – 3%;
- работы, реализуемые за счет планируемых расходов – 17%;
- неучтенные работы – 3%.
Апр
=1,4.
23388=32743 чел.-дн.
С учетом затрат на выполнение государственных обязанностей, болезни, а также нахождение рабочих в зимний период в отпуске.
Аспис.
=1,08.
Апр
(5.2)
Аспис
=1,08.
32743=35361 чел.-дн.
Тогда списочная потребность в рабочих определится равной
Рср.спис
=Аспис
/Траб
(5.3)
Рср.спис
=35361/198=179 чел.
Трудоемкость работ на 1 км составит
Ттр
=35361/11,947=2960 чел-дн.
Выработка на одного рабочего составит:
187,10/179=1,05 т./руб. или 187,10/35361=0,005 т./руб.
Уровень механизации труда рабочих определяется отношением
Умех
=100(Амех
/Аспис
) (5.4)
Умех
=100(32743/35361)=93%
Механовооруженность труда рабочих определится по формуле:
Мтр
=Sm
i
=1
Фi
ni
ti
/Рср.спис.
(5.6)
где,
m – количество дорожно-строительных машин, включая автомобили;
Фi
– стоимость одной машины i-й марки;
ni
– количество машин i-й марки в дорожном отряде;
ti
– время нахождения i-й марки на строительстве, т.е. рабочие дни.
Для определения этого показателя необходимо определить стоимость механизмов, участвующих в строительстве. Расчеты представлены в виде таблицы 5.2.
№ п/п |
Наименование механизмов, машин и оборудования |
Кол-во, маш-ч. |
Стоимость единицы, тыс.руб. |
Общая стоимость, тыс.руб. |
Мощность механизмов, кВт |
Общая мощность, кВт |
1 |
Автогрейдеры среднего типа |
2610,08 |
305,50 |
797379 |
99 |
99 |
2 |
Автопогрузчики 5 т |
2122,31 |
113,64 |
241179 |
- |
- |
3 |
Автогудронаторы 3500 л |
192,876 |
234,00 |
45133 |
- |
- |
4 |
Агрегаты сварочные передвижные |
3,05 |
19,41 |
59 |
- |
- |
5 |
Бульдозеры |
1356,42 |
195 |
264502 |
59 |
59 |
6 |
Бульдозеры |
5426069 |
208 |
1128752 |
79 |
79 |
7 |
Бульдозеры |
93,77 |
266,50 |
24990 |
96 |
96 |
8 |
Бульдозеры-рыхлители |
116,412 |
247,00 |
28754 |
79 |
79 |
9 |
Вагонетки неопрокидные вместимостью 1,4 м3
|
4751,06 |
0,72 |
3420,76 |
- |
- |
10 |
Гудронаторы ручные |
566,242 |
0,67 |
379,38 |
- |
- |
11 |
Бороны дисковые мелиоративные (без трактора) |
115,423 |
36,47 |
4209 |
- |
- |
12 |
Дрели электрические |
0,38 |
1,14 |
0,43 |
- |
- |
13 |
Заливщики швов на базе автомобиля |
4,24 |
195,93 |
830 |
- |
- |
14 |
Катки дорожные прицепные на пневмоколесном ходу, 25 т |
4358,15 |
31,51 |
137325 |
- |
- |
15 |
Катки дорожные самоходные гладкие 8 т |
4366,58 |
98,96 |
432117 |
- |
- |
16 |
Катки дорожные самоходные гладкие 13 т |
10354,2 |
146,55 |
1517408 |
- |
- |
17 |
Катки дорожные самоходные на пневмоколесном ходу 30 т |
29,21 |
377 |
11013 |
- |
- |
18 |
Компрессоры передвижные |
73,37 |
169 |
12400 |
- |
- |
19 |
То же |
330,757 |
89,85 |
29719 |
- |
- |
20 |
Корчеватели-собиратели с трактором |
1292,46 |
195,00 |
252030 |
79 |
79 |
21 |
Краны на автомобильном ходу 10, 16, 25 т |
708,66 |
1248 |
170677 |
- |
- |
22 |
Краны на гусеничном ходу 16, 25 т |
209,175 |
520 |
54385 |
- |
- |
23 |
Катки дорожные прицепные гладкие 5 т |
32,70 |
2,45 |
80,13 |
- |
- |
24 |
Лебедки |
252,41 |
3,74 |
215,38 |
- |
- |
25 |
Машины бурильные на тракторе |
12,06 |
787,39 |
2622 |
85 |
85 |
26 |
Машины бурильнокрановые на автомобиле |
11,51 |
363,81 |
2223 |
- |
- |
27 |
Машины шлубинной подготовки полей на тракторе |
931,98 |
167,17 |
155798 |
79 |
79 |
28 |
Машины маркировочные |
50,35 |
110,5 |
5564 |
- |
- |
29 |
Машины поливомоечные |
3583,76 |
273 |
978366 |
- |
- |
30 |
Машины шлифовальные |
4,90 |
1,79 |
8,78 |
- |
- |
31 |
Насосы |
0,25 |
13,68 |
3 |
- |
- |
32 |
Прицепы тракторные |
17,33 |
7,80 |
135,15 |
- |
- |
33 |
Тракторы на гусеничном ходу |
248,18 |
162,5 |
40330 |
59 |
59 |
34 |
То же |
6172,52 |
565,50 |
1102786 |
79 |
79 |
35 |
Тракторы на пневмоколесном ходу |
2,18 |
162,5 |
354 |
59 |
59 |
36 |
Трамбовки пневматические |
48,12 |
1,98 |
95,28 |
- |
- |
37 |
Укладчики асфальтобетона |
1189,93 |
266,5 |
377116 |
- |
- |
38 |
Установки для сварки ручной |
84,27 |
15,41 |
1299 |
- |
- |
39 |
Экскаваторы одноковшовые на гусеничном ходу, 0,5, 0,65 м3
|
5661,37 |
474,5 |
1463953 |
- |
- |
40 |
Котлы битумные передвижные 400 л |
62,25 |
38,17 |
2376 |
- |
- |
41 |
Комплект оборудования для газовой сварки |
7,93 |
15,41 |
122 |
- |
- |
42 |
Подъемники гидравлические |
5,36 |
49,12 |
263 |
- |
- |
43 |
Автогидроподъемники |
2,55 |
111 |
283 |
- |
- |
44 |
Молотки отбойные пневматические |
722,56 |
1,93 |
1394,54 |
- |
- |
45 |
Автомобиль бортовой грузоподъемностью до 8 т |
0,24 |
182 |
43 |
- |
- |
46 |
Сеялка туковая без трактора |
21,77 |
5,10 |
111,04 |
- |
- |
47 |
Бензопила |
3025,02 |
2,84 |
8591,06 |
- |
- |
48 |
Автомобили бортовые групод. до 5 т |
114,98 |
143 |
16443 |
- |
- |
49 |
Автомобили самосвалы грузопд.до 7 т |
258,35 |
156 |
40303 |
- |
- |
50 |
Катки дорожные самоходные вибрационные 8 т |
605,01 |
175,5 |
106180 |
- |
- |
51 |
Распределитель каменной мелочи |
88,20 |
227,5 |
20066 |
- |
- |
52 |
Виброплита |
10,75 |
155,86 |
16,75 |
- |
- |
53 |
Бороны зубовые |
53,11 |
36,47 |
1937 |
- |
- |
54 |
Плуги навесные |
22,87 |
2,45 |
56,02 |
- |
- |
55 |
Разбрасыватели тракторные прицепные |
8,29 |
10,91 |
90 |
- |
- |
Всего |
9462750,18 |
- |
852 |
Механовооруженность труда определится равной:
Мтр
=SСмаш
/Рспис
(5.7)
Мтр
=9462,75/179=52,86 тыс.руб./чел.
Энерговооруженность строительства составит
Эстр
=Sn
i
=1
Ni
/Ссмет
(5.8)
Эстр
=852/149878,86=0,006 кВт/тыс.руб.
Энерговооруженность труда рабочих определится равной:
Эраб
=Sn
i
=1
Ni
/Рр.спис
(5.9)
Эраб
=852/179=4,76 кВт/чел
6 ДЕТАЛЬ ПРОЕКТА
Обновление асфальтобетонных покрытий
6.1 Способы обновления асфальтобетонных покрытий.
При обновлении а/б покрытий используют:
· строительство слоев износа, при которых применяются поверхностная обработка, втопленный щебень и мастика;
· укладка нового а/б покрытия без удаления старого покрытия и с удалением старого покрытия;
· использование старого асфальтобетона.
При использовании старого асфальтобетона применяют холодный и горячий способ.
Горячий способ основан на разогревании и разрыхлении старого асфальтобетона с добавлением новой смеси или разогревании и разрыхлении без добавления новой смеси.
Второй способ основан на холодной регенерации (ХР) конструктивных слоев дорожной одежды и заключается в измельчении покрытия (в некоторых случаях с захватом части основания) преимущественно посредством холодного фрезерования; введении в образовавшийся асфальтобетонный гранулят (АГ) при необходимости нового скелетного материала, вяжущего и, если требуется, других добавок; перемешивании всех компонентов с получением асфальтогранулобетонной смеси (АГБ-смеси); распределении ее в виде конструктивного слоя и уплотнении, после чего АГБ-смесь превращается в асфальтогранулобетон (АГБ).
Все перечисленные технологические операции осуществляют, как правило, на дороге звеном специализированных машин.
Смешение компонентов можно выполнять и в полустационарной установке вблизи дороги. Однако это связано с разрывом технологического процесса и добавления операций погрузки и транспортировки АГ к месту приготовления смеси, его штабелирования, подачи в смесительную установку и транспортировки АГБ-смеси к месту укладки, что приводит к существенному удорожанию работ.
Отличительной особенностью технологии ХР является восстановление монолитности (сплошности) пакета асфальтобетонных слоев дорожной одежды на всю или часть толщины без разогрева асфальтобетона или АГ.
Поверх регенерированного слоя укладывают замыкающий (защитный) слой или асфальтобетонное покрытие.
Устранение трещин в старом покрытии на всю или большую часть глубины в результате его регенерации исключает появление отраженных трещин в вышеукладываемых слоях покрытия (копирования трещин). При традиционном методе усиления дорожной одежды, предусматривающем укладку новых слоев поверх старого покрытия, появление отраженных трещин неизбежно.
6.2 Требования к материалам.
6.2.1 Асфальтобетоны.
Щебень из плотных горных пород и гравий, щебень из шлаков, входящие в состав смесей, должны соответствовать требованиям #M12293 0 1200000314 3271140448 1441418669 247265662 4292033677 3918392535 2960271974 3628676638 4294967268ГОСТ 8267#S и #M12293 1 901704812 3271140448 809731643 247265662 4292033678 557313239 2960271974 3594606034 4293087986ГОСТ 3344#S. Содержание зерен пластинчатой (лещадной) и игловатой формы в щебне и гравии должно быть, % по массе, не более:
15 - для смесей типа А и высокоплотных;
25 - для смесей типов Б, Бх;
35 - для смесей типов В, Вх.
Гравийно-песчаные смеси по зерновому составу должны отвечать требованиям #M12293 2 9052237 3271140448 4009830303 247265662 4292033677 557313239 2960271974 3594606034 4293087986ГОСТ 23735#S, а гравий и песок, входящие в состав этих смесей, - #M12293 3 1200000314 3271140448 1441418669 247265662 4292033677 3918392535 2960271974 3628676638 4294967268ГОСТ 8267#S и ГОСТ 8736 соответственно.
Для приготовления смесей и асфальтобетонов применяют щебень и гравий фракций от 5 до 10 мм, свыше 10 до 20 (15) мм, свыше 20 (15) до 40 мм, а также смеси указанных фракций.
Прочность и морозостойкость щебня и гравия для смесей и асфальтобетонов конкретных марок и типов должны соответствовать указанным в таблице 6.1.
(Измененная редакция, #M12293 4 1200029441 2479111094 81 24259 77 373616323 3972405214 3319683020 2038873560Изм. N 2#S).
Таблица 6.1 Прочность и морозостойкость щебня и гравия для смесей асфальтобетонов.
#G0 |
Значение для смесей марки |
I |
II |
II |
Наименование показателя |
горячих типа |
холодных типа |
пористых и высоко- |
горячих типа |
холодных типа |
пористых и высоко- |
горячих типа |
высоко- плотный А
|
Б |
Бх |
Вх |
пористых |
А |
Б |
В |
Бх |
Вх |
пористых |
Б |
В |
Марка, не ниже:
|
по дробимости: |
а) щебня из изверженных и метаморфи-
ческих горных пород
|
1200 |
1200 |
1000 |
800 |
800 |
1000 |
1000 |
800 |
800 |
600 |
600 |
800 |
600 |
б) щебня из осадочных горных пород
|
1200 |
1000 |
800 |
600 |
600 |
1000 |
800 |
600 |
600 |
400 |
400 |
600 |
400 |
в) щебня из металлурги-
ческого шлака
|
-
|
1200 |
1000 |
1000 |
800 |
1200 |
1000 |
800 |
800 |
600 |
600 |
800 |
600 |
г) щебня из гравия
|
- |
1000 |
1000 |
800 |
600 |
1000 |
800 |
600 |
800 |
600 |
400 |
600 |
400 |
д) гравия
|
-
|
-
|
-
|
-
|
-
|
-
|
-
|
600 |
800 |
600 |
400 |
600 |
400 |
по истираемости: |
а) щебня из изверженных и метаморфи-
ческих горных пород
|
И1 |
И1 |
И2 |
И3 |
Не норм. |
И2 |
И2 |
И3 |
И3 |
И4 |
Не норм. |
И3 |
И4 |
б) щебня из осадочных горных пород
|
И1 |
И2 |
И2 |
И3 |
То же |
И1 |
И2 |
И3 |
ИЗ |
И4 |
То же |
И3 |
И4 |
в) щебня из гравия и гравия
|
- |
И1 |
И1 |
И2 |
" |
И1 |
И2 |
И3 |
И2 |
И3 |
" |
И3 |
И4 |
по морозостойкости
|
для всех видов щебня и гравия:
|
а) для дорожно-
климатических зон I, II, III
|
F 50 |
F50 |
F50 |
F50 |
F 25 |
F50 |
F50 |
F25 |
F25 |
F25 |
F15 |
F25 |
F25 |
б) для дорожно-
климатических зон IV, V
|
F 50 |
F50 |
F25 |
F25 |
F 25 |
F50 |
F25 |
F15 |
F15 |
F15 |
F15 |
F15 |
F15 |
Песок природный и из отсевов дробления горных пород должен соответствовать требованиям #M12293 0 901700280 3271140448 236756085 247265662 4292033677 3918392535 2960271974 1052220950 4291804369ГОСТ 8736#S, при этом марка по прочности песка из отсевов дробления и содержание глинистых частиц, определяемых методом набухания, для смесей и асфальтобетонов конкретных марок и типов должны соответствовать указанным в таблице 6.2, а общее содержание зерен менее 0,16 мм (в том числе пылевидных и глинистых частиц) в песке из отсевов дробления не нормируется.
Таблица 6.2 Марка прочности песка для приготовления смесей асфальтобетона.
#G0
|
Значение для смесей и асфальтобетонов марки
|
I
|
II
|
III |
Наименование показателя |
горячих и холодных типа |
пористых и высоко- пористых |
горячих и холодных типа |
пористых и высоко- пористых |
горячих типа |
А, Б, Бх, Вх высоко- плотных |
Г, Гх |
А, Б, Бх, В, Вх |
Г, Д,
Дх
|
Б, В |
Г, Д |
Марка по прочности песка из отсевов дробления горных пород и гравия, не менее
|
800 |
1000 |
600 |
600 |
800 |
400 |
400 |
600 |
Содержание глинистых частиц, определяемое методом набухания, % по массе, не более |
0,5 |
0,5 |
0,5 |
0,5 |
0,5 |
1,0 |
1,0 |
1,0 |
Примечание - Для смесей типа Г марки I необходимо использовать пески из отсевов дробления изверженных горных пород по #M12293 0 901700280 3271140448 236756085 247265662 4292033677 3918392535 2960271974 1052220950 4291804369ГОСТ 8736#S с содержанием зерен менее 0,16 мм не более 5,0 % по массе. |
(Измененная редакция, #M12293 0 1200029441 4120950664 24255 2486450883 3078966168 4164543659 2038873560 1839890747 419630764Изм. N 2#S).
Минеральный порошок, входящий в состав смесей и асфальтобетонов, должен отвечать требованиям #M12293 1 901710667 3271140448 2062469902 247265662 4292033678 557313239 2960271974 3594606034 4293087986ГОСТ 16557#S. Допускается применять в качестве минеральных порошков для пористого и высокопористого асфальтобетона, а также для плотного асфальтобетона II и III марок техногенные отходы промышленного производства (измельченные основные металлургические шлаки, золы-уноса, золошлаковые смеси, пыль-уноса цементных заводов и пр.), показатели свойств которых соответствуют указанным в таблице 6.3.
Таблица 6.3 Свойства минеральных порошков, применяемых для приготовления смесей асфальтобетона.
#G0 |
Значение для |
Наименование показателя |
молотых основных металлургических шлаков
|
зол-уноса и измельченных золошлаковых смесей |
пыли-уноса цементных заводов |
Зерновой состав, % по массе, не менее:
|
мельче 1,25 мм
|
95 |
95 |
95 |
" 0,315 мм
|
80 |
80 |
80 |
" 0,071 мм
|
60 |
60 |
60 |
Пористость, %, не более
|
40 |
45 |
45 |
Водостойкость образцов из смеси порошка с битумом, не менее
|
0,7 |
0,6 |
0,8 |
Показатель битумоемкости, г, не более
|
100 |
100 |
100 |
Потери при прокаливании, % по массе, не более
|
Не нормируется |
20 |
Не нормируется |
Содержание активных СаО+МgО, % по массе, не более
|
3 |
3 |
3 |
Содержание водорастворимых соединений, % по массе, не более
|
6 |
6 |
6 |
Для приготовления смесей применяют битумы нефтяные дорожные вязкие по #M12293 0 1200003410 3271140448 3520591034 247265662 4291541635 557313239 2960271974 3594606034 4293087986ГОСТ 22245#S и жидкие по #M12293 1 1200005335 3271140448 4197226290 247265662 4291541635 557313239 2960271974 3594606034 4293087986ГОСТ 11955#S, а также полимерно-битумные вяжущие и модифицированные битумы по технической документации, согласованной в установленном порядке.
Для холодных смесей марки I следует применять жидкие битумы класса СГ. Допускается применение битумов классов МГ и МГО при условии использования активированных минеральных порошков или предварительной обработки минеральных материалов смесью битума с поверхностно-активными веществами.
Для холодных смесей марки II следует применять жидкие битумы классов СГ, МГ и МГО.
6.2.2 Влажные органоминеральные смеси (ВОМС).
Органоминеральная смесь - искусственная смесь, получаемая смешением на дороге или в смесительных установках щебня, гравия, песка и их смесей, а также минерального порошка (в том числе порошковых отходов промышленного производства) с органическими вяжущими (жидкими или вязкими битумами, битумными эмульсиями) и активными добавками и без них или с органическими вяжущими совместно с минеральными.
Органоминеральные смеси (далее - смеси) и укрепленные грунты должны приготавливаться в соответствии с требованиями настоящего стандарта по технологическому регламенту, утвержденному в установленном порядке строительной организацией.
Смеси и укрепленные грунты в зависимости от наибольшего размера зерен применяемых минеральных материалов приготавливают:
#G0
крупнозернистыми
|
-
|
с зернами размером до 40 мм;
|
мелкозернистыми
|
- |
" " " 20 " |
песчаными |
- |
" " " 5 " |
Зерновой состав минеральной части крупнозернистых и мелкозернистых смесей и укрепленных грунтов должен соответствовать требованиям, приведенным в таблице 6.4.
Таблица 6.4 Зерновой состав минеральной части крупно- и мелкозернистых смесей и укрепленных грунтов и прочность щебня и гравия
#G0
Конструк-
тивный слой
|
Максималь-
ная крупность зерен щебня (гравия), мм
|
Содержание, % по массе
|
Марка по дробимости (прочность), не менее
|
щебня,
не более
|
зерен мельче
0,63 мм,
не менее
|
зерен мельче 0,071 мм,
не менее
|
Покрытие
|
20
20
15
10
|
65
50
35
35
|
24
38
50
50
|
8
10
12
12
|
800
400
300
200
|
Основание
|
40
40
20
15
|
70
55
35
35
|
12
20
30
30
|
Не нормируется
То же
4
4
|
800
400
300
200
|
Зерновой состав минеральной части песчаных смесей и укрепленных грунтов должен содержать зерна размером менее 5 мм не менее 95% по массе, в том числе менее 0,63 мм - от 30 до 70%; менее 0,071 мм - от 10 до 22%.
Физико-механические показатели смесей в зависимости от вида применяемого вяжущего и области применения должны соответствовать указанным в таблицах 6.5 и 6.6.
Таблица 6.5 Физико-механические показатели органоминеральных смесей для покрытий
#G0
|
Значения для смесей |
Наименование показателей |
с жидкими органичес-
кими вяжущими
|
с жидкими органически-
ми вяжущими совместно с минеральными
|
с вязкими, в том числе эмульгиро-
ванными ор-
ганическими вяжущими
|
с эмульгиро-
ванными органическими вяжущими сов-
местно с минеральными
|
Предел прочности на сжатие, МПа, при температурах, °С, не менее:
|
20
|
1,2 |
1,5 |
1,6 |
1,8 |
50
|
0,5 |
0,7 |
0,8 |
0,9 |
Водостойкость, не менее
|
0,55 |
0,7 |
0,75 |
0,8 |
Водостойкость при длительном водонасыщении, не менее
|
0,4
|
0,6
|
0,65
|
0,7
|
Водонасыщение, % по объему
|
от 4,0 до 9,0 |
от 4,0 до 6,0 |
от 2,0 до 6,0 |
от 2,0 до 6,0 |
Набухание, % по объему, не более |
2,5 |
2,0 |
2,0 |
1,5 |
Слеживаемость, число ударов, не более
|
10
|
Не нормируется
|
Примечание - Допускается для смесей с жидкими органическими вяжущими, приготовленных способом смешения на дороге, снижение предела прочности на сжатие при температуре 20°С до 0,8 МПа. Показатель предела прочности на сжатие при температуре 50°С для этих смесей не нормируется.
|
Таблица 6.6 Физико-механические показатели органоминеральных смесей для оснований
#G0
Наименования показателей
|
Значение
|
Предел прочности на сжатие, МПа, при температурах, °С, не менее:
|
20
|
1,4 |
50
|
0,5 |
Водостойкость, не менее
|
0,60 |
Водостойкость при длительном водонасыщении, не менее
|
0,50 |
Водонасыщение, % по объему, не более
|
10 |
Набухание, % по объему, не более |
2,0
|
Смеси и укрепленные грунты в зависимости от значения суммарной удельной эффективной активности естественных радионуклидов в применяемых материалах и грунтах используют для строительства дорог и аэродромов:
без ограничений - при до 740 Бк/кг;
вне населенных пунктов и зон перспективной застройки - при св. 740 до 1500 Бк/кг.
При необходимости в национальных нормах, действующих на территории государства, величина удельной эффективной активности естественных радионуклидов может быть изменена в пределах норм, указанных выше.
Для приготовления смесей и укрепленных грунтов применяют грунты и следующие материалы:
- щебень;
- гравий;
- песок;
- щебеночно-гравийно-песчаные смеси;
- шлаковые щебеночно-песчаные смеси;
- гравийно-песчаные смеси;
- минеральные порошки.
Щебень и гравий из плотных горных пород, щебень из шлаков, шлаковые смеси марок , входящие в состав минеральной части смесей, должны соответствовать требованиям ГОСТ 8267 и ГОСТ 3344 соответственно. Содержание зерен пластинчатой (лещадной) формы в щебне не должно быть более 35% по массе.
Гравийно-песчаные смеси по зерновому составу должны соответствовать требованиям ГОСТ 23735, а гравий и песок, входящие в состав таких смесей, - требованиям ГОСТ 8267 и ГОСТ 8736 соответственно.
Для приготовления смесей применяют щебень и гравий фракций, мм: от 5 до 10, св. 10 до 20, св. 20 до 40, а также смеси фракций - от 5 до 20 и от 5 до 40.
Прочность щебня и гравия должна соответствовать значениям, приведенным в таблице 6.4.
Для приготовления смесей применяют минеральные порошки, соответствующие требованиям ГОСТ 16557, а также порошковые отходы промышленного производства, измельченные основные металлургические шлаки, соответствующие требованиям, приведенным в ГОСТ 9128. Допускается применение фосфорных шлаков с содержанием не более 2% по массе и соответствующих требованиям, приведенным в ГОСТ 9128, по остальным показателям качества. Для смесей, приготавливаемых на дороге, допускается в качестве минерального порошка применять пылеватые грунты с числом пластичности не более 10.
В случае применения материалов и грунтов с показателями качества ниже требований, должно быть проведено их исследование в специализированных лабораториях научно-исследовательских институтов для подтверждения возможности и технико-экономической целесообразности получения смесей и укрепленных грунтов с нормируемыми показателями качества.
В качестве органических вяжущих для приготовления смесей и укрепленных грунтов применяют битумы нефтяные дорожные жидкие по ГОСТ 11955, эмульсии битумные дорожные по ГОСТ 18659.
Допускается применение других органических вяжущих, удовлетворяющих требованиям действующих нормативных документов и обеспечивающих получение смесей и укрепленных грунтов в соответствии с требованиями настоящего стандарта.
Для приготовления смесей применяют также битумы нефтяные дорожные вязкие по ГОСТ 22245.
Для устройства оснований не допускается использование жидких битумов без активных добавок.
В качестве минеральных вяжущих для приготовления смесей и укрепленных грунтов применяют портландцемент и шлакопортландцемент по ГОСТ 10178, золу-унос по ГОСТ 25818.
В качестве активных добавок к применяемым материалам и грунтам используют известь по ГОСТ 9179, а также указанные минеральные вяжущие в количестве не более 4% по массе.
В качестве активных добавок к битуму применяют поверхностно-активные вещества (ПАВ) или продукты, содержащие ПАВ и удовлетворяющие требованиям действующих нормативных документов.
Вода для приготовления смесей и укрепленных грунтов должна соответствовать ГОСТ 23732.
6.2.3 Асфальтогранулобетоны.
В зависимости от вида нового вяжущего, вводимого в АГ при приготовлении АГБ-смесей, их подразделяют на следующие типы:
А – без добавления вяжущего;
Э – с добавлением битумной эмульсии;
В – с добавлением вспененного битума;
Б – с добавлением разогретого битума;
М – с добавлением минерального вяжущего (чаще всего цемента или извести);
К – с добавлением комплексного вяжущего (чаще всего битумной эмульсии и цемента).
АГБ перечисленных типов отличаются своими расчетными характеристиками и скоростью формирования равновесной структуры (структурообразования).
В зависимости от массовой доли щебня или гравия (зерна каменного материала крупнее 5 мм), входящего в состав асфальтобетона, из которого получен АГ, АГБ-смеси подразделяют на щебеночные с содержанием щебня 35% и более, и песчаные – менее 35%.
Показатели физико-механических свойств АГБ, в зависимости от категории автомобильной дороги и типа смеси, должны соответствовать указанным в таблице 6.7.
Таблица 6.7 Физико-механические свойства АГБ в зависимости от категории автомобильной дороги.
Наименование показателя |
Нормы для категории автомобильной дороги |
I-II |
III |
IV |
Для смесей типа |
Э |
М,
К
|
В |
Э |
М,
К
|
В |
Б |
Э |
М,
К
|
В |
Б |
А |
1. Предел прочности при сжатии, не менее, МПа, при температуре 200
С в возрасте:
а) 1 суток
б) 7 суток
|
-
1,4
|
-
2,0
|
1,4
-
|
-
1,4
|
-
2,0
|
1,4
-
|
1,2
-
|
-
1,4
|
-
2,0
|
1,4
-
|
1,2
-
|
0,7
-
|
2. То же, при 500
С в возрасте:
а) 1 суток
б) 7 суток
|
-
0,7
|
-
0,8
|
0,7
-
|
-
0,6
|
-
0,7
|
0,6
-
|
0,5
-
|
-
0,5
|
-
0,7
|
0,6
-
|
0,5
-
|
0,4
-
|
3. Коэффициент водостойкости, не менее |
0,7 |
0,7 |
0,6 |
0,6 |
0,6 |
0,6 |
0,6 |
4. Водонасыщение по объему, %, не более |
10 |
10 |
12 |
12 |
14 |
14 |
16 |
Гранулометрический состав АГБ-смеси должен соответствовать требованиям, установленным в ГОСТ 9128 для пористых и высокопористых щебеночных смесей, за исключением частиц мельче 0,071 мм, содержание которых не нормируется.
Для дорог I-II категорий применяют щебеночные смеси, а для дорог III-IV категорий допускается применение песчаных АГБ-смесей. Если в АГ, используемом для приготовления щебеночных смесей, содержание щебня меньше 35%, при приготовлении АГБ-смеси необходимо добавление недостающей фракции щебня.
Содержание в АГ гранул крупнее 50 мм не должно превышать 5% по массе.
Для приготовления смесей с использованием органического вяжущего применяют вязкие и жидкие нефтяные битумы, отвечающие требованиям соответственно ГОСТ 22245 и ГОСТ 11955.
Марку битума выбирают в зависимости от типа смеси и дорожно-климатической зоны в соответствии с таблицей 6.8.
Таблица 6.8 Марки битума для приготовления АГБ-смесей.
Тип смеси |
Марка битума для дорожно-климатической зоны |
I |
II, III |
IV, V |
Б |
БНД 200/300
СГ, МГ,
МГО 130/200
|
БНД 200/300
СГ, МГ,
МГО 130/200
|
БНД 130/200
СГ, МГ,
МГО 70/130 и 130/200
|
В |
БНД 130/200 |
БНД 90/130
БНД 130/200
|
БНД 60/90
БНД 90/130
|
Э, К |
БНД 90/130
БНД 130/200
|
БНД 60/90
БНД 90/130
|
БНД 60/90
БНД 90/130
|
Для приготовления смесей типов Э и К используют эмульсии, отвечающие требованиям ГОСТ 18659.
В смесях типа Э применяют катионные эмульсии классов ЭБК-2, ЭБК-3 и анионные эмульсии классов ЭБА-2, ЭБА-3. Более предпочтительными являются катионные эмульсии.
В смесях типа К применяют преимущественно катионные эмульсии класса ЭБК-3.
Для приготовления смесей типов М и К в качестве минерального вяжущего чаще всего применяют портландцемент не ниже марки 400, соответствующий требованиям ГОСТ 10178.
При необходимости увеличения содержания в АГБ-смеси щебня к АГ добавляют щебень, отвечающий требованиям ГОСТ 8267.
Для приготовления смесей всех типов, кроме типа Б, в ряде случаев требуется добавление воды. Обычно применят воду, пригодную для питья.
6.3 Конструирование и расчет дорожной одежды.
Большинство существующих дорог, требующих усиления, имеют искаженный поперечный профиль и неудовлетворительную продольную ровность, что отражается на комфорте и безопасности движения и усложняет содержание покрытия, особенно в зимнее время. Поэтому в проекте должны быть предусмотрены мероприятия по выравниванию покрытия.
На стадии сбора исходных данных осуществляют работы, включающие: оценку прочности дорожной одежды в соответствии с нормами ОДН 218.046.01 или Указаниями ВСН-52-89; отбор кернов для определения продольного и поперечного профилей толщин пакета монолитных слоев дорожной одежды и вида асфальтобетона, входящего в эти слои; бурение скважин для определения толщин остальных конструктивных слоев дорожной одежды и оценки состояния составляющих их материалов, в том числе грунта земляного полотна и основания; создание цифровой модели местности.
На дорогах с приведенной расчетной интенсивностью воздействия нагрузки Nр
>2000 ед./сут. регенерированный слой рассматривают в качестве верхнего монолитного слоя основания, на который должно быть уложено двухслойное асфальтобетонное покрытие общей толщиной 9-10 см.
На дорогах с 500£Nр
£2000 ед./сут. на регенерированный слой может быть уложено однослойное покрытие из плотного асфальтобетона толщиной 4-5 см.
На дорогах с Nр
£500 ед./сут. регенерированный слой рассматривают в качестве слоя покрытия, на котором должна быть устроена поверхностная обработка.
Задавшись типом и толщиной покрытия, укладываемого поверх регенерированного слоя, рассчитывают его толщину по допускаемому упругому прогибу в соответствии с ОДН 218.046-01 с учетом требуемого модуля упругости Етр
, рассчитанного общего модуля упругости на поверхности слоя, подстилающего регенерированный, и ориентировочного значения кратковременного модуля упругости регенерирующего слоя при соответствующей расчетной температуре.
Регенерированный слой проверяют на сопротивление растяжению при изгибе при температуре покрытия 00
С.
Ориентировочные расчетные значения кратковременного модуля упругости (Ер
) и среднего сопротивления растяжению при изгибе (Rи
), при времени воздействия нагрузки 0,1 с, для разных типов АГБ-смесей приведены в таблицах 6.6 и 6.7 (в дальнейшем подлежат уточнению).
Таблица 6.9 Расчетные значения кратковременного модуля упругости.
Тип смеси |
Расчетные значения кратковременного модуля упругости Ер
, МПа, при температуре покрытия, 0
С |
+10 |
+20 |
+30 |
+40 |
+50 |
А |
1200 |
700 |
400 |
250 |
210 |
Б |
1600 |
900 |
570 |
420 |
380 |
Э, В |
1800 |
1100 |
700 |
520 |
470 |
К |
2300 |
1400 |
920 |
700 |
630 |
М |
2800 |
1800 |
1200 |
920 |
840 |
Таблица 6.10 Характеристики для расчета на изгиб при температуре покрытия 00
С.
Тип смеси |
Характеристики для расчета на изгиб при температуре покрытия 00
С |
Кратковременный модуль упругости Ер
, МПа |
Среднее сопротивление растяжению при изгибе Rи
, МПа |
А |
1600 |
0,5 |
Б |
2100 |
0,9 |
Э, В |
2500 |
1,1 |
К |
3200 |
1,3 |
М |
3600 |
1,7 |
При расчете по условию сдвига конструктивных слоев дорожной одежды мы рассматриваем его по условию:
С1
+С2
+Р.
tgφ
>0,75Рр
,
где
С1
– коэффициент сцепления а/б на транзитном участке (при движении);
С2
– коэффициент сцепления а/б при воздействии статической и горизонтальной нагрузки (при остановке);
Р – нагрузка на покрытие;
φ
- величина угла внутреннего трения материала проверяемого слоя при действии нагрузки от торможения;
Рр
–
Исходя из условия, находим угол внутреннего трения материала:
Р.
tgφ
³0,75Рр
-С1
.
С2
tgφ
³(0,75-(С1
.
С2
/Рр
.
Р)).
2
при экстренном торможении:
tgφ
³(0,75-(С1
.
С2
/Рр
.
Р)).
4
В зависимости от толщины пакета асфальтобетонных слоев ремонтируемой дорожной одежды (hс
) могут возникнуть следующие случаи:
а) hс
существенно больше, чем толщина регенерированного слоя, полученная по расчету (hс
).
В этом случае старое покрытие целесообразнее всего отфрезеровать с учетом выравнивания его в продольном и поперечном направлениях (выравнивающее фрезерование).
Глубину фрезерования (hв
) по оси проезжей части определяют таким образом, чтобы оставшийся пакет асфальтобетонных слоев был в среднем близок по толщине к hp
, т.е. hв
≈hc
-hp
.
После выравнивающего фрезерования осуществляют регенерационное фрезерование на глубину близкую к hр
.
При построении соответствующей картограммы возможны местами захват части слоя основания или оставление части старого асфальтобетонного слоя с учетом получения регенерируемого слоя требуемой толщины. Пример такой конструкции приведен на рисунке 6.1, а.
Добытый в процессе выравнивающего фрезерования АГ должен быть повторно использован (например, для устройства выравнивающего слоя), что удешевляет производство ремонтных работ.
Если увеличение затрат за счет более глубокого фрезерования, чем это требуется для выравнивания, не компенсируется доходом от повторного использования АГ, можно назначить hв
=0 (рисунок 6.1, б). В этом случае местами требуется устройство выравнивающего слоя.
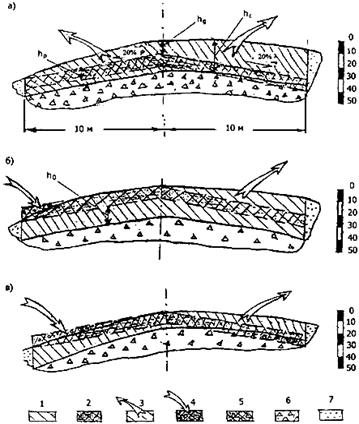
Рисунок 6.1 Примеры конструирования дорожной одежды, включающей регенерированный слой (покрытие, укладываемое поверх регенерированного слоя, не показано):
а) – hс
существенно больше hp
, hв
≈hc
-hр
; б) – то же, при hв
≈0; в) – hс
сопоставима с hр
или меньше ее;
1 – пакет асфальтобетонных слоев старой дорожной одежды; 2 – регенерированный слой; 3 – удаляемая часть старого покрытия после выравнивающего фрезерования; 4 – выравнивающий слой, укладываемый поверх старого покрытия и повторно перерабатываемый совместно с материалом старого покрытия в процессе регенерации; 5- регенерированный слой из АГ с захватом части слоя основания; 6 – слой основания; 7 – обочина.
Оставшийся после регенерации слой нетронутого старого асфальтобетона включают в расчет дорожной одежды, принимая его расчетный модуль упругости Ер
=500 МПа.
Недостатком такого конструктивного решения является то, что в случае превышения средней толщины оставшегося слоя (hо
) общей толщины пакета новых слоев (включая регенерированный) возникает опасность появления отраженных трещин.
б) hс
сопоставима или меньше hр
.
В этом случае предусматривают комплексное выравнивание, сочетающее выравнивающее фрезерование с устройством выравнивающего слоя (рис. 6.1, в), после чего осуществляют регенерацию выровненного покрытия с захватом на всю ширину или часть ширины слоя основания.
Уменьшение толщины слоя основания учитывают при расчете дорожной одежды.
6.4 Подбор состава асфальтогранулобетона.
6.4.1 Отбор пробы.
На основе запроектированной конструкции дорожной одежды и осмотра кернов, отобранных на стадии сбора исходных данных, намечают участки, на которых зерновой состав пакета асфальтобетонных слоев, подлежащих регенерации, находится в пределах одного типа смеси по ГОСТ 9128 (А, Б, В или Д).
Из намеченных участков отбирают пробы АГ путем фрезерования покрытия.
Если выбранная конструкция дорожной одежды предусматривают удаление верхней части асфальтобетонных слоев (см. рис. 6.1, а), которая отличается по типу смеси от нижележащей, пробу отбирают АГ из слоя, подлежащего регенерации.
Масса пробы с одного участка должна быть не менее 30 кг.
6.4.2 Выбор типа АГБ.
В зависимости от имеющегося оборудования и заложенного в проект расчетного модуля упругости намечают для исследования один или несколько типов АГБ-смеси.
Битум, входящий в состав добавок для смесей типов Э, В, Б и К, устраняет излишнюю жесткость состарившегося пленочного битума, окружающего гранулы; экранирует обнажившиеся в результате фрезерования поверхности зеоен минерального материала; обеспечивает сцепление зерен заполнителя, добавляемого для увеличения содержания щебня или корректировки гранулометрического состава АГБ-смеси, между собой и с АГ; заполняет частично межгранулярные пустоты, уменьшая водонасыщение АГБ; снижает межгранулярное трение, способствуя лучшей упаковке гранул при уплотнении АГБ-смеси; способствует залечиванию микродефектов, возникающих в процессе эксплуатации регенерированного слоя.
Цемент, входящий в состав смесей типов М и К, образует в присутствии воды цементный камень, который частично заполняет межгранулярные пустоты; армирует битумную пленку, окружающую гранулу; кристаллически связывается с не обработанными битумом зернами, содержащимися в АГ и заполнителе.
Наиболее технологичны смеси типа Э. Их чаще всего применяют для регенерации слоев, преимущественно состоящих из АГ. К недостаткам следует отнести возможность колееобразования при тяжелом движении.
Смеси типа К более сложны в изготовлении, но АГБ из таких смесей более устойчив к колееобразованию. Применение указанных смесей позволяет снизить толщину регенерированного слоя.
Слой из смесей типа К быстрее формируется, что особенно важно при неблагоприятных погодных условиях.
Смеси типа М чаще всего применяют, когда при регенерации захватывается часть слоя основания из не обработанного битумом материала (более 30% от толщины регенерируемого слоя).
АГБ из такой смеси отличается высокими расчетными характеристиками, однако в регенерированном слое возможно появление усадочных и температурных трещин.
6.4.3 Приготовление смесей.
Из пробы АГ отсеивают крупные гранулы через сито с отверстиями диаметром 40 мм.
Смеси заданного состава готовят при температуре 20±20
С в лабораторной лопастной мешалке или вручную. Перемешивание заканчивают, смесь станет однородной.
Если проектом предусмотрено добавление к АГ щебня или других минеральных заполнителей или при регенерации возможен захват части основания (более 20% по массе), соответствующий материал, просеянный через сито, перемешивают с АГ в требуемой пропорции.
При приготовлении АГБ-смеси АГ должен иметь 2%-ную влажность. Это имитирует его естественное состояние, при котором влажность обычно колеблется в пределах 1-3%. Если проба АГ имеет меньшую влажность, то в него добавляют недостающее количество воды, а если большую влажность, то его подсушивают на воздухе или в сушильном шкафу с принудительной вентиляцией при температуре не выше 400
С до требуемой влажности. Перед приготовлением АГБ-смеси в этом случае необходимо остудить навеску АГ до температуры 20±20
С.
Для упрощения дозирования воды пробу АГ можно заранее высушить до постоянного веса.
При приготовлении АГБ-смеси типа М в АГ с влажностью 2% вводят сначала цемент, а после его равномерного распределения в смеси – дополнительное количество воды.
При приготовлении АГБ-смеси типа К в АГ с влажностью 2% вводят сеачала эмульсию, а после ее равномерного распределения в смеси – цемент.
Если по принятой технологии предполагается введение цемента в виде суспензии, то в лабораторных условиях в АГ вводят цементную суспензию с соотношением В/Ц=0,5 и эмульсию одновременно.
Предварительно определяют совместимость этих двух типов вяжущего путем добавления 150 г суспензии (100 г цемента + 50 г воды) в 100 г эмульсии и непрерывного их перемешивания в стеклянном стакане стеклянной палочкой.
Процесс распада эмульсии должен начаться не ранее, чем через 4 мин. От начала перемешивания.
6.4.4 Изготовление образцов и подготовка их к испытанию.
Физико-механические свойства АГБ определяют на цилиндрических образцах диаметром 71,4 мм (площадью 40 см2
), изготовленных прессованием под давлением 7 МПа, в стандартных формах для изготовления асфальтобетонных образцов (ГОСТ 12801), при температуре 20±20
С. Время выдерживания образца при заданном давлении – 3 мин.
Высота образца должна составлять 71,4±1,5 мм. Ориентировочное количество смеси на образец 610-620 г. Его уточняют при изготовлении пробного образца как для асфальтобетона (ГОСТ 12801).
В процессе прессования излишек воды должен выделятся через зазор между нижним пуансоном и формой. Если зазор недостаточен, на пуансоне необходимо проделать с четырех сторон вертикальные прорези шириной и глубиной 2 мм.
После изготовления образцы хранят в помещении при температуре 20±20
С и влажности воздуха 60-80% до испытания.
Перед испытанием образцы высушивают до постоянного веса на воздухе или в сушильном шкафу с принудительной вентиляцией при температуре не выше 400
С. В последнем случае перед проведением испытанием их следует охладить до комнатной температуры.
6.4.5 Подбор состава АГБ.
Для смесей типов В и Б готовят четыре замеса из АГ с влажностью 2%: с добавлением 1,0, 1,5 и 2,0% битума (сверх 100% АГ по массе) и сравнительный – без добавления битума. На один замес требуется 2 кг АГ.
Из смесей, приготовленных как указано в п.6.4.3, прессуют по три образца (см. п.6.4.4), и через сутки хранения, после подготовки к испытаниям, определяют среднюю плотность образцов.
С целью упрощения испытания, объем образца (V) вычисляют с погрешностью 1 см3
по формуле
, (6.1)
где
– среднее значение высоты образца из четырех замеров штангенциркулем в точках, равностоящих друг от друга по окружности образца, с погрешностью 0,01 см;
S – площадь образца, равная 40 см2
;
6 см3
– ориентировочная разница между объемами, определенными геометрическим и гидростатическим методами.
Среднюю плотность образца γа
или γаг
определяют с погрешностью 0,01 г/см3
по формуле
γ=g0
/V (6.2)
где
g0
– масса образца, взвешенного с погрешностью 1 г на воздухе.
За среднюю плотность для каждой серии образцов принимают среднее арифметическое результатов определений плотности трех образцов. Расхождение между результатами параллельных определений не должно превышать 0,03 г/см3
.
Вычисляют коэффициенты упаковки гранул (Кг
) для каждой серии образцов из АГБ с разным содержанием битума.
После определения средней плотности образцы испытывают на сжатие при 200
С.
Оптимальным является содержание битума, при котором образцы показывают максимальное значение показателя предела прочности АГБ при сжатии при 200
С (R20
). Как правило, у образцов из такой серии максимальным оказывается и значение показателя Кг
.
Если средний показатель R20
для двух смежных серий отличается меньше чем на 0,1 МПа, предпочтение следует отдать АГБ с более высоким значением показателя Кг
.
В зависимости от тенденции изменения показателей Кг
и R20
с изменением содержания битума может потребоваться изготовление дополнительных замесов с другим содержанием битума: менее 1,0% или более 2,0%.
Если показатель R20
для серии с оптимальным содержанием битума не отвечает требованиям табл.6.7 следует попытаться откорректировать гранулометрический состав АГБ-смеси или перейти на смеси типов К или М.
Для смесей типа Э процедура подбора оптимального состава АГБ аналогична описанной выше.
Основные замесы готовят с добавлением 2,0, 3,0 и 4,0% эмульсии.
В смесях этого типа содержания воды, как правило, оказывается избыточным и лишняя вода отжимается при прессовании образцов.
Определение средней плотности образцов упрощенным способом и испытание на сжатие при 200
С осуществляют через 7 сут. после их изготовления, так как АГБ на эмульсии требует времени для формирования битумной пленки.
Для смесей типа М основные замесы готовят с добавлением 2,0, 3,0 и 4,0% цемента и добавлением в последние две смеси 1,0 и 2,0% воды (сверх 100% АГ по массе) соответственно (помимо 2% воды, содержащейся в АГ).
Если какая-либо из этих смесей плохо перемешивается, следует увеличить содержание воды на 0,5%.
В остальном процедура подбора оптимального состава АГБ аналогична описанной выше.
Оптимальным является содержание цемента, при котором у образцов достигается максимальное значение показателя Кг
. Значение же показателя R20
должно соответствовать требованиям табл.6.7. В противном случае следует попытаться откорректировать гранулометрический состав АГБ-смеси или увеличить содержание цемента, но не более, чем до 5%.
Для смесей типа К назначают содержание: цемента 3%, а эмульсии – 2,0, 3,0 и 4,0% (сверх 100% АГ по массе). Если обеспечена 2%-ная влажность АГ, воду в смеси не добавляют.
В остальном процедура подбора оптимального состава АГБ аналогична предыдущим процедурам.
Оптимальным является содержание эмульсии, при котором у образцов наблюдается максимальное значение показателя Кг
.
С увеличением в смеси содержания цемента растет и кратковременный модуль упругости (Ер
). Например, при одном и том же содержании эмульсии 3% и содержаниях цемента 2,0, 3,0 и 4,0% соответствующие значения Ер
регенерированного слоя в 28-дневном возрасте при 100
С могут достигать 1700, 2950 и 4250 МПа.
Эмульсия снижает кратковременный модуль упругости регенерированного слоя из смесей типа К примерно на 20%, по сравнению со смесями типа М.
Оптимальное соотношение между содержанием цемента и эмульсии в смеси – 50:50, но допускаются вариации от 60:40 до 40:60.
Если показатель R20
находится на пределе или ниже требований табл.6.7, а корректировка гранулометрического состава АГБ-смеси нежелательна из экономических соображений, можно увеличить содержание цемента (но не более 5%) и повторить процедуру подбора оптимального содержания эмульсии.
Подобрав состав, изготавливают соответствующую смесь для проверки остальных физико-механических свойств АГБ. На замес требуется 4 кг АГ.
Прессуют шесть образцов и через сутки или 7 суток ( в зависимости от типа АГБ-смеси) определяют их среднюю плотность. После этого делят образцы на две группы по три образца так, чтобы средние арифметические результатов определения плотности в каждой из групп были максимально близки.
Для трех образцов одной из групп определяют водонасыщение, а также показатели предела прочности АГБ в водонасыщенном состоянии (Rв
) и коэффициента водостойкости АГБ (Кв
). Это делается сразу после определения средней плотности. При вычислении водонасыщения используют значения массы образцов, взвешенных на воздухе, полученные при определении их средней плотности.
Перед определением показателя предела прочности АГБ при сжатии при 500
С (R50
) образцы из второй серии высушивают (после определения средней плотности) до постоянного веса.
Если показатель водонасыщения АГБ (W) или Кв
не отвечают требованиям табл. 6.7, следует или откорректировать гранулометрический состав АГБ-смеси, или увеличить содержание вяжущего в смесях типа Б, В и Э, или перейти на смеси типов К или М, для которых, как правило, не возникает проблем с этими показателями.
Если показатель R50
не отвечает требованиям табл.6.7, что иногда имеет место для смесей типов Б, В и Э, следует перейти на смеси типов К или М, для которых всегда может быть обеспечено требуемое значение этого показателя путем увеличения содержания цемента.
6.5 Технологические схемы производства работ.
Выбор технологической схемы производства работ зависит от цели ремонта, категории автомобильной дороги, конструкции дорожной одежды, ее состояния.
Технологическую схему разрабатывает подрядчик на основе проекта, имеющегося у него в наличии оборудования и выбранного типа АГБ-смеси.
На рисунке 6.2 приведены схемы работ, в которых операция фрезерования отделена от остальных операций.

Рисунок 6.2 Технологические схемы холодной регенерации с использованием в качестве ведущей машины смесителя-укладчика:
1 – каток; 2 – смеситель-укладчик; 3 – фреза; 4 – подборщик; 5 – валик АГ; 6 – автомобиль-самосвал; 7 – склад АГ.
После выравнивания покрытия с помощью дорожной фрезерной машины (далее фрезы) осуществляют регенерационное фрезерование пакета асфальтобетонных слоев на проектную глубину. Образующийся АГ, по транспортеру, имеющемуся на фрезе, поступает в приемный бункер смесителя-укладчика. Оттуда он попадает в двухвальную мешалку горизонтального типа, где перемешивается с органическим вяжущим. Готовую смесь укладывают и уплотняют.
Согласно схеме (рис.6.2, а), фреза работает в сцепе со смесителем-укладчиком, который является ведущей машиной. Производительность смесителя-укладчика – 80-150 т/ч, что соответствует рабочей скорости 2-3 м/мин. Толщина укладываемого слоя – до 12 см. Так как рабочая скорость фрезы составляет 7-10 м/мин, очевидно, что ее производительность искусственно будет занижена минимум в три раза.
Смеситель-укладчик имеет два скользящих уширителя, что позволяет варьировать ширину укладки от 2,4 до 4,2 м. Отсюда следует, что минимальная ширина фрезерования должна составлять 2,4 м.
Недостатком этой схемы является то, что при неисправности или техническом обслуживании одной из машин останавливается весь поток.
По схеме (рис.6.2, б) фреза оставляет АГ на проезжей части в виде призмы. Ее подбирает прицепной или самоходный подборщик, работающий в сцепе со смесителем-укладчиком, и направляет в приемный бункер последнего. Здесь производительность фрезы не зависит от производительности ведущей машины.
Регенерационное фрезерование может быть совмещено с выравнивающим (рис.6.2, в). В этом случае фреза работает в одном звене с автомобилями-самосвалами, которые доставляют основной объем АГ к смесителю-укладчику, а избыток АГ - на другой объект или склад.
Возможен также вариант, при котором работу фрезы не увязывают с работой смесителя-укладчика. АГ складируют на притрассовых складах, откуда отгружают погрузчиком в автомобили-самосвалы и направляют к смесителю-укладчику.
Наиболее дешевым и технологичным является второй вариант.
Смеситель-укладчик приспособлен в первую очередь для работы со смесями типа Э. Он имеет емкость для хранения 10 т эмульсии и дозирующее устройство.
При необходимости увеличения содержания щебня в АГБ-смеси или корректировки ее гранулометрического состава новый материал распределяют ровным слоем требуемой толщины по покрытию перед регенерационным фрезерованием или после него.
На рис.6.3 приведена технологическая схема с использованием в качестве смесителя-укладчика ремиксера, освобожденного от газового оборудования для разогрева покрытия. Здесь операция регенерационного фрезерования также отделена от остальных операций.
После проходов фрезы автогрейдер профилирует призмы АГ ровным слоем по всей ширине регенерируемой полосы.
Смеситель-укладчик (далее - регенератор) позволяет готовить смеси типов Э, М и К. В комплекте с ним работает специальная машина, оборудованная силосными банками для хранения эмульсии, цемента и воды (рис.6.3, а). Материал для корректировки гранулометрического состава АГБ-смеси можно выгружать непосредственно в приемный бункер регенератора.
Для подачи АГ в смеситель не требуется подборщик. Эту операцию выполняют специальные шнеки.
Ширину укладки можно изменять в пределах от 3,5 до 4,5 м, что, как и в случае смесителя-укладчика, облегчает выполнение кратного числа проходов по ширине покрытия.
Толщина укладываемого слоя - до 30 см; рабочая скорость - до 16 м/мин; производительность - около 300 т/ч.
На регенераторе имеются емкости для хранения эмульсии, цемента и воды, которые пополняются из автомашины с силосными банками.
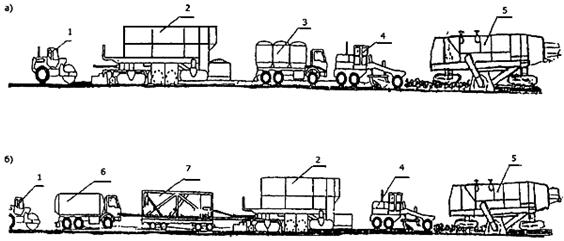
Рисунок 6.3. Технологические схемы ХР с использованием в качестве ведущей машины регенератора:
1 - каток; 2 - регенератор; 3 - машина с силосными банками для основных компонентов смеси;
4 - автогрейдер; 5 - фреза; 6 - эмульсиовоз; 7 - суспензатор
Дозировкой компонентов управляют микропроцессоры.
В последнее время все большее распространение получает технология, предусматривающая добавку цемента и воды в смесях типов М и К в виде цементного теста (суспензии). Для его приготовления на регенераторе имеется соответствующее устройство. Применяется и специальная машина - суспензатор. На рис.6.3, б показана схема ХР с приготовлением смеси типа К с добавлением суспензии.
Была также создана машина, совмещающая операции регенерационного фрезерования с приготовлением и укладкой АГБ-смеси. Эта машина работает в комплекте со специальной дозировочной машиной, оборудованной силосными банками для эмульсии, цемента и воды. Она также позволяет готовить смеси типов Э, М и К.
Позднее было признано более целесообразным отделить функцию фрезерования, предоставив ее фрезе, и облегчить тем самым основную машину.
Технологическая схема, предусматривающая совмещение всех основных операций одной машиной, представлена на рис.6.4.
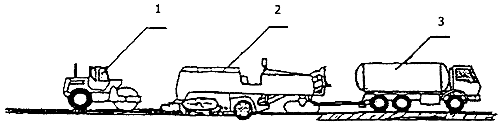
Рисунок 6.4. Технологическая схема ХР с использованием в качестве ведущей машины фрезы-регенератора и изготовлением смеси типа Э:
1 - каток; 2 - фреза-регенератор; 3 - эмульсиовоз
Здесь в качестве ведущей машины использована фреза-регенератор гусеничного типа.
Перемешивание АГ с добавками осуществляется под кожухом фрезерного барабана, а для укладки АГБ-смеси имеется навесное оборудование, аналогичное установленному на обычных асфальтоукладчиках.
В комплекте с этой машиной работают эмульсиовоз - автоцистерна для транспортировки, хранения и подачи эмульсии (когда готовят смесь типа Э) и (или) суспензатор (когда готовят смеси типов К или М).
Ранее цемент распределяли по покрытию перед фрезерованием специальным цементовозом-распределителем, но эта операция оказалась нетехнологичной из-за пылимости цемента. Применение цементного теста устранило отмеченный недостаток.
Добавление нового минерального материала (если это необходимо) осуществляют, как указано выше.
Ширина фрезеруемой полосы 2 м, но в специальном варианте она может быть увеличена до 2,5 м. Глубина фрезерования достигает 30 см.
Рабочая скорость машины существенно зависит от глубины фрезерования и в среднем составляет 5-7 м/мин.
На регенераторе имеются дозаторы для воды и эмульсии. Специальное прижимное устройство предотвращает образование крупных кусков асфальтобетона в процессе фрезерования. Вибротрамбующий рабочий орган позволяет достичь высокой степени предварительного уплотнения смеси.
Качество перемешивания смеси этой машиной ниже, чем при использовании машин, описанных выше, так как последние оборудованы специальными двухвальными смесителями, а здесь перемешивание осуществляется фрезерным рабочим органом без гомогенизации смеси в поперечном направлении.
На рис.6.5 показаны технологические схемы с использованием в качестве ведущей машины фрезы-грунтосмесителя (далее - стабилизер) на колесном ходу. Эта машина значительно проще упомянутых выше, хотя и совмещает основные операции.
Как правило, стабилизер работает по двухпроходной схеме. Сначала он фрезерует дорожную одежду на заданную глубину, а автогрейдер разравнивает призмы АГ (рис.6.5, а). Затем им же осуществляется перемешивание АГ с добавками при повторном проходе.
Дозировка битума, эмульсии и воды осуществляется насосами, управляемыми микропроцессорами, а цементного теста - насосом суспензатора. Перемешивание АГ с добавками происходит под кожухом фрезерного барабана. Регулируемый по высоте зачистной отвал, расположенный за фрезерным барабаном, улучшает качество перемешивания.
Ширина фрезеруемой полосы - 2,44 м, а глубина фрезерования достигает 50 см. Средняя рабочая скорость при фрезеровании (первый проход) - 7-15 м/мин, а при смешении (второй проход) - 10-20 м/мин.
В зависимости от типа АГБ-смеси стабилизер работает в комплекте со вспомогательными машинами (рис.6.5, б-д).
В отличие от фрезы-регенератора, данная машина не имеет специального оборудования для распределения, выглаживания и предварительного уплотнения смеси. Смесь разравнивает автогрейдер. Отсюда ровность слоя и соответствие заданному поперечному профилю будет ниже, чем по предыдущим схемам.
Стабилизер в качестве ведущей машины используют для ХР обычно на второстепенных дорогах.
Все вышеперечисленные технологические схемы объединяет то, что АГБ-смесь готовят непосредственно на дороге в процессе перемещения строительного потока. Однако возможна схема, при которой АГ, полученный в процессе фрезерования, складируют вблизи дороги. Там же, на полустационарной смесительной установке, готовят смесь, которую транспортируют к месту укладки.
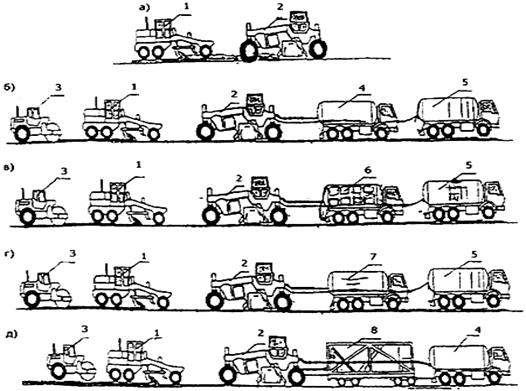
Рисунок 6.5. Технологические схемы ХР с использованием в качестве ведущей машины стабилизера:
а - предварительное фрезерование покрытия; б, в, г, д - изготовление смесей типов: Э, М, В, К соответственно;
1 - автогрейдер; 2 - стабилизер; 3 - каток; 4 - эмульсиовоз; 5 - водовоз; 6 - цементовоз-распределитель;
7 - битумовоз; 8 - суспензатор
6.6 Фрезерование.
Для фрезерования покрытия различные зарубежные фирмы предлагают большое число фрез, отличающихся по ширине фрезерного барабана, мощности двигателя, глубине фрезерования и другим параметрам. Многие из них оснащены устройствами для сбора АГ и погрузки его в автомобили-самосвалы.
Чаще всего используют фрезы с шириной обрабатываемой полосы - 2,0-2,5 м.
Для выравнивающего фрезерования, включающего и выравнивание покрытия в продольном направлении, фреза должна быть оснащена автоматикой, позволяющей работать по струне или с нивелировочной балкой (на колесиках) длиной 5-7 м (ее поставляют фирмы по отдельному заказу).
При выравнивании по струне ее натягивают на металлические штыри, установленные на некотором расстоянии (в зависимости от конструкции следящего устройства) от осевой линии (реже - кромки покрытия) с шагом 10-20 м.
Первый проход фрезы выполняют по струне, установив (с осевой стороны) требуемые глубину фрезерования и уклон фрезерного барабана, а последующие - используя копир, скользящий по выровненной поверхности нижележащего слоя.
Перед выравнивающим фрезерованием целесообразно произвести выравнивающую подсыпку покрытия в местах, где это предусмотрено проектом, используя АГ или асфальтобетонную смесь. Выравнивающую смесь прикатывают.
. Направление вращения фрезерного барабана зависит от глубины фрезерования или и толщины пакета асфальтобетонных слоев (рис.6.6):
- при выравнивающем фрезеровании, когда , и регенерационном фрезеровании, когда не захватывается слой несвязного основания ( ), вращение фрезерного барабана осуществляется "сверху-вниз" по отношению к направлению движения потока;
- в случаях, когда или , т.е. граница фрезерования проходит между асфальтобетонным и несвязным слоями или ниже с захватом материала последнего, вращение фрезерного барабана осуществляется "снизу-вверх".
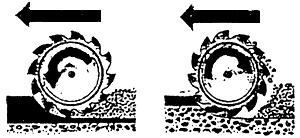
Рисунок 6.6. Направление вращения фрезерного барабана в зависимости от глубины фрезерования и толщины пакета асфальтобетонных слоев
Крупность АГ зависит от конструкции фрезерного органа, скорости вращения фрезерного барабана, рабочей скорости движения фрезы, глубины фрезерования, типа асфальтобетона и других факторов.
Чем уже задняя щель под кожухом фрезерного барабана, тем дольше задерживается АГ внутри кожуха и сильнее измельчается. Максимальный размер АГ не может быть мельче максимального размера щебня, входящего в состав АГ.
Чем выше скорость вращения фрезерного барабана, тем мельче АГ по гранулометрии. Обычно при фрезеровании толстых покрытий (более 15 см) используют первую скорость; покрытий средней толщины (8-15 см) - вторую скорость; тонких покрытий (менее 8 см) - третью скорость.
Чем прочнее покрытие, тем более низкая скорость вращения фрезерного барабана требуется для измельчения асфальтобетона.
Третий контролируемый фактор - рабочая скорость фрезы. Чем она меньше, тем мельче получается АГ.
. В процессе фрезерования покрытия зубья фрезерного барабана изнашиваются. Их замена является наиболее дорогостоящей операцией и фактором, снижающим производительность. На износ зубьев влияют твердость асфальтобетона, глубина фрезерования, температура покрытия и другие факторы. Наиболее благоприятная температура для работы зубьев 10-30 °С. В среднем через каждые 10 тыс.м покрытия требуется замена всех зубьев.
Самопроизвольное снижение рабочей скорости фрезы указывает на сильный износ зубьев. Работа с изношенными зубьями может привести к повреждению держателей зуба, что потребует сварочных работ, а следовательно, и к задержке потока.
Зубья необходимо проверять регулярно через каждые 2 ч или в конце захватки.
Во время инспектирования заменяют наиболее изношенные или разрушенные зубья. Обычно причиной разрушения является попадание зуба на захороненные в покрытие металлические предметы или крупные камни.
Зубья требуют замены в случаях, изображенных на рис.6.7 (2-5). Их извлекают из держателя или вставляют в него при помощи специального съемника, входящего в состав инструмента. Два человека могут заменить все зубья за час.
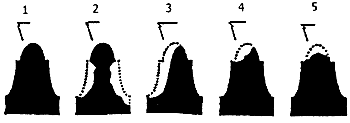
Рисунок 6.7 Виды износа и разрушения фрезерных зубьев:
1 - новый зуб; 2 - зуб со стертой средней частью; 3 - зуб со стертой стороной;
4 - зуб с частично разрушенным наконечником; 5 - зуб со стертым наконечником
Некоторые из снятых зубьев, подходящих по длине, могут быть использованы для замены разрушенных.
Производительность фрезы точно указать трудно из-за большого числа влияющих факторов. Обычно ее определяют на опытной секции или с учетом имеющегося опыта работы в подобных условиях. Если рабочая скорость в данных условиях определена, то производительность определяется просто.
Например, при ширине обрабатываемой полосы 2,42 м, рабочей скорости 10 м/мин и коэффициенте использования рабочего времени 80% часовая производительность составит:
м .
7 ОХРАНА ОКРУЖАЮЩЕЙ СРЕДЫ
7.1 Оценка природных условий
Оценка воздействия поверхностного стока с автомобильной дороги на водную среду.
Загрязнение водотоков поверхностными водами с автомобильной дороги и мостов составляет незначительный удельный вес от загрязнения водной среды отходами промышленного и химического производства. Оседающие на покрытие автомобильной дороги пыль, продукты износа покрытия, шин и тормозных колодок, выбросы от работы двигателей автомобилей, материалы, используемые для борьбы с гололедом, пылеподавления и т.д. при смыве дождевыми и талыми водами приводит к насыщению вод поверхностного стока различными загрязняющими веществами, в числе которых взвешенные вещества, нефтепродукты (бензин, дизельное топливо, масло, мазут и др.), которые затем могут попадать в водотоки.
При решении вопроса необходимости очистки поверхностных сточных вод и расчете предельно допустимого сброса загрязняющих веществ в водный объект руководствовались Санитарными правилами и нормами (СанПиН 2.1.5-980-00) Водоотведение населенных мест. Санитарная охрана водных объектов. Гигиенические требования к охране поверхностных вод.
В связи с тем, что проектируемая дорога проходит вне пределов водо-охранных зон, и далее 500 метров от близлежащих пунктов водопользования сбор дождевых и талых вод с поверхности автомобильной дороги производится кюветами, со сбросом на рельеф или к перепускным искусственным сооружениям без очистки. Эрозии почв не наблюдается, так как дорога проходит по залесенной местности, откосы насыпи земляного полотна укрепляются засевом трав. На водоперепускных сооружениях, трубах и мостах тип укрепления принят в соответствии с расчетом допускаемых для них скоростями течений. Действующие водотоки не являются зоной промышленного рыболовства.
Оценка загрязнения атмосферного воздуха и придорожных территорий пылью, продуктами загрязнения и износа покрытия. Запретные мероприятия.
Почти все технологические процессы по реконструкции автомобильной дороги вызывают выделение пыли, загрязняющей атмосферный воздух и придорожную полосу. Выделение пыли происходит при разработке грунта и его транспортировке; при погрузочно-разгрузочных работах и транспортировке сыпучих материалов; движении транспортных средств; при укладке, разравнивании и уплотнении каменных и других материалов.
Пылеобразование на дороге происходит в результате износа покрытия, внесения колесами автомобиля на проезжую часть грязи и пыли, а также износа автопокрышек. На интенсивность пылеобразования влияют физико-механические свойства материалов и состояния покрытия, скорость движения автотранспорта и типы движущихся по дороге автомобилей, погодно-климатические условия в районе проложения трассы.
Для предотвращения пылеобразования проектом предусматривается поливка грунта водой в сухой период лета при отсыпке земляного полотна с доведением его до оптимальной влажности. Поливка водой для обеспыливания также предусматривается при устройстве песчаных и щебеночных оснований.
Во избежании заноса грязи на покрытие дороги длина устройства дорожной одежды на пересечениях и примыканиях принята в соответствии с требованиями СНиП 2.05.02-85 и 5.5.
Перевозка пылящих материалов (цемент, известь и др.) производится в специальных машинах
Оценка уровня шумового воздействия транспорта. Средства защиты от шума.
Оценка воздействия на окружающую среду транспортного шума не производится, так как в зону влияния дороги не попадают селитебнопромышленные территории населенных пунктов, санитарно-курортные зоны, территории сельскохозяйственного назначения, заповедники, заказники.
Оценка уровня вибрационного воздействия транспорта. Специальные методы защиты.
Движение автомобиля по дороге сопровождается процессом вибрации, которая воздействует через механическую систему на человека, пользующегося автомобилем, и через дорожную конструкцию на здания и сооружения, находящиеся в зоне воздействия.
Интенсивность вибрации, передающейся зданиям и сооружениям в придорожной зоне, зависит от количества тяжелых грузовых автомобилей, их скорости, ровности дорожного покрытия, конструкции дорожной одежды, типа подстилающего грунта.
Ровность покрытия обеспечивается устройством покрытия из асфальтобетона, а в конструкцию дорожного основания замещены слои из зернистых несвязных материалов (щебень, песок). Грунты по трассе не водонасыщены. Здания и сооружения вдоль реконструируемого участка отсутствуют.
Учитывая, что все вышеназванные принятые мероприятия позволяют снизить вибрационное ускорение, устройство вибрационного экрана не требуется.
6.2 Воздействие на животный и растительный мир
Реконструируемый участок проходит по залесенной территории, пересекая небольшие заболоченные места. Основной состав леса: сосна, ель, береза, осина.
В пределах изучаемого участка из представителей фауны встречаются лось, медведь, рысь, лиса, заяц. Пернатый мир представлен глухарем, тетеревом, рябчиком и др. птицами.
Проложение трассы автомобильной дороги произведено с максимальным использованием существующей полосы отвода и минимальным дополнительным отводом.
Рубка в придорожной полосе должна быть выполнена в установленном порядке.
Не допускается складирование и сжигание срезанного кустарника и выкорчеванных пней у границ леса и полосы отвода, что влечет создание благоприятных условий для развития и распределения болезней лесов, повреждения огнем деревьев и кустарниковой растительности, а также загрязнения атмосферного воздуха продуктами сгорания. Проектом предусматривается вывозка порубочных остатков, корней деревьев и кустарника в специально отведенные для этого места с последующей засыпкой вскрышными породами.
Учитывая, что радиус распространения корневой системы от ствола дерева, как правило, на 1 метр больше кроны, необходимы следующие мероприятия:
· не допускать переуплотнения грунтов в зоне распространения корневой системы деревьев при проезде дорожно-строительных и транспортных машин.
· Засыпка зон распространения корневой системы не должна превышать толщину более 0,5 м.
· Запрещается слив и заправка горюче-смазочных материалов, складирование активных химических веществ (солей, ядохимикатов), разведение костров, которые могут вызвать повреждения деревьев и их корневой системы.
· Для защиты стволов деревьев от механических повреждений, возможных при строительстве, рекомендуется применять специальные ограждения из старых шин, которые не должны соприкасаться со стволами деревьев.
Следует отметить, что прохождение автодороги через лесные массивы создает проблемы возможности заболачивания и осушения. Проектом предусмотрены отверстия водопропускных труб и уклоны с таким расчетом, чтобы обеспечить беспрепятственный сток воды, тем самым исключить подтопление и заболачивание.
Планировка территории, исключение мест застоя воды, своевременная уборка и захоронение порубочных остатков не дает условий для размножения комаров и клещей.
В целях предотвращения лесных пожаров, борьбы с ними необходимо соблюдать Лесной кодекс. Обслуживающим организациям данного участка дороги – Пудожскому ДРСУ, Медвежьегорскому ДРСУ в месте с администрацией районов ежегодно предусматривать мероприятия и составлять оперативные планы по борьбе с лесными пожарами.
Все вышеперечисленные мероприятия позволяет сохранить и не нарушить сложившиеся условия произрастания растений и обитания животных в данной местности.
6.3 Мониторинг в процессе эксплуатации автомобильной дороги
Для обеспечения надлежащего мониторинга необходимо подготовить развернутый план трассы с указанием пунктов и участков подлежащих регулярному, периодическому и эпизодическому контролю:
Регулярному контролю подвергается:
· Санитарное состояние дороги и придорожной полосы.
· Состояние проезжей части обочин откосов и обстановки дороги.
· В зимнее время участки дороги подвержены снегозаносам.
· Изношенные шины автомобилей и других механизмов вывозятся на регенерацию и переработку.
· В случае аварии на дороге необходим контроль направления потока горюче-смазочных материалов и других вредных жидкостей, в целях недопущения их на прилегающие к автодороге территории.
Периодическому наблюдению подвергаются:
· Подъем паводковых вод на мостовых переходах и железобетонных трубах.
· Подъем грунтовых вод на равнинных участках лесных угодий.
· Состояние древесных и кустарниковых культур в лесных массивах прилегающих к трассе автомобильной дороги.
Эпизодическому контролю подвергаются:
· Водопропускные трубы, заложенные под дорогой – чтобы гарантировать пропуск талых и дождевых вод. Состояние укрепления дна и откосов у входящих и выходящих отверстий труб.
· Развитие травянистой растительности в свободных зонах.
· Сбор грибов, ягод в защитных лесных полосах с предупреждением населения об их загрязненности металлами и бензанирином.
ЗАКЛЮЧЕНИЕ
В данном проекте рассмотрено производство и организация работ при реконструкции автомобильной дороги. В проекте рассчитано: дорожная одежда, технологические карты, произведен сметный расчет реконструкции.
В качестве научно-исследовательского раздела рассмотрено обновление асфальтобетонных покрытий, преимущественно способом холодной регенерации. При этом выделены разделы по подбору смесей, рассмотрены технологические процессы регенерации покрытий.
Все данные, использованные и рассчитанные в данном проекте могут реально использоваться в строительстве автомобильных дорог.
СПИСОК ИСПОЛЬЗОВАННЫХ ИСТОЧНИКОВ
1. СНиП 2.02.01-82 Строительная климатология и геофизика. – М.: ЦИТП Госстроя СССР, 1983 – 136 с.
2. СНиП 2.05.02-85 Автомобильные дороги. – М.: Госстроя СССР, 1986 – 51 с.
3. СНиП 2.01.14-83 Автомобильные дороги. – М.: Госстроя ССР, 1984 – 109 с.
4. СНиП 1.02.07-87 Инженерно-геологические изыскания. – М.: Госстроя СССР, 1988 – 78 с.
5. СНиП III-8-76, п.3.68 Автомобильные дороги. – М.: Госстроя СССР, 1977 - 115 с.
6. «Автомобильные дороги», март 1997 год, «Издательство дороги», 64 с.
7. ОДН 218.046-01 Проектирование нежестких дорожных одежд. Юмашев В.М., Казарновский В.Д. и др. – М.: Информавтодор, 2001 – 145 с.
8. ГОСТ 9128-97 Смеси асфальтобетонные дорожные, аэродромные и асфальтобетон. Технические условия. – М.: Издательство стандартов, 1997 – 45 с.
9. СНиП 3.01.01-85 Нормы продолжительности строительства и задела в строительстве предприятий, зданий, сооружений и дорог. – М.: ЦИТП Госстроя СССР, 1986 – 528 с.
10. СНиП 4.02.01-85 Инструкция о составе, порядке разработке, согласования и утверждения проектно-сметной документации на строительство предприятий, зданий, сооружений и дорог. – М.: ЦИТП Госстроя СССР, 1991 – 258 с.
11. СНиП 1.04.03-85 Нормы продолжительности строительства и задела в строительстве предприятий, зданий и сооружений. – М.: ЦИТП Госстроя СССР, 1991 – 523 с.
12. СНиП 3.06.03-85 Автомобильные дороги. – М.: Госстроя СССР, 1986 – 111 с.
13. СНиП 3.06.07-86 Автомобильные дороги, мосты и трубы. – М.: Госстроя СССР, 1986 – 98 с.
14. ВСН 5-81 Инструкция по разбивочным работам при строительстве, реконструкции и капитальном ремонте автомобильных дорог и искусственных сооружений. – М.: Транспорт, 1981 – 96 с.
15. ЕНиР Сборник Е 2 Земляные работы. Выпуск 1. Механизированные и ручные работы. – М.: Госстроя СССР, 1986 – 155 с.
16. ЕНиР Сборник Е 17 Строительство автомобильных дорог. – М.: Стройиздат, 1967 – 46 с.
17. СНиП III-4-80 Техника безопасности в строительстве. – М.: ЦИТП Госстроя СССР, 1982 – 163 с.
18. СН 202-81 Методические указания по выполнению раздела дипломного проекта «Календарное планирование. Технико-экономические показатели организации строительства» (Воронеж. Гос. арх.-строит. акад.; составители: Растегаева Г.А. – Воронеж, 1997 – 15 с.)
19. Автомобильные дороги (охрана труда в строительстве). Учебник для вузов. – М.: Транспорт, 1985 – 207 с.
20. Методические рекомендации по восстановлению асфальтобетонных покрытий и оснований автомобильных дорог способами холодной регенерации. – М.: ГП «Информавтодор», 2002 – 26 с.
21. ВСН 14-95 Инструкция по строительству дорожных асфальтобетонных покрытий. – М.: , 1995 – 31 с.
22. ГОСТ 30491-97 Смеси органоминеральные и грунты, укрепленные органическими вяжущими, для дорожного и аэродромного строительства. – М.: ГУП ЦПП, 1997 – 20 с.
|