СОДЕРЖАНИЕ
Введение
1. Общая часть
1.1 Общие сведения об участке работ
1.2 Геологическая характеристика участка работ
1.2.1 Геологическое строение участка
1.2.2. Стратиграфия
1.2.3 Тектоника
1.2.4 Исходные данные для разработки проекта
2. Проектная часть
2.1 Выбор и обоснование способа бурения
2.2 Проектирование конструкции скважины,
2.2.1 Расчет и обоснование конечного, промежуточного и начального диаметра бурения
2.2.2 Выбор промывочного агента для бурения скважины
2.3 Техника бурения
2.3.1 Определение максимальной массы бурильной колонны
2.3.1.1 Расчёт бурильных труб, УБТ, компоновок бурильной колонны
2.3.1.2 Расчёт обсадных колонн
2.3.2 Буровое оборудование
2.3.2.1 Выбор бурового станка
2.3.2.2 Выбор насосной установки
2.3.2.3 Выбор силовой установки
2.3.2.4 Выбор буровой вышки и талевой системы
2.4 Технология бурения
2.4.1 Выбор породоразрушающего инструмента
2.4.2 Расчет технологического режима бурения
2.4.3 Расчет осевой нагрузки
2.4.4 Расчёт частоты вращения
2.4.5 Расчет производительности насосов для бурения под каждую обсадочную колонну
2.4.6 Расчет количества и качества промывочной жидкости для бурения под каждую обсадочную колонну
2.5 Цементирование скважины
3. Экономический расчет
3.1 Сметный сводный расчет на строительство скважины
4. Безопасность жизнедеятельности
4.1 Мероприятия по обеспечению безопасных и комфортных бытовых условий
4.2 Инженерные мероприятия по обеспечению безопасных и безвредных условий труда на объекте проектирования
4.3 Пожарная безопасность
4.4 Охрана окружающей среды
Заключение
Литература
ВВЕДЕНИЕ
За последние годы, нефтяная промышленность нашей страны, развиваясь бурными темпами, выросла в одну из самых мощных отраслей тяжелой индустрии, оснащенную передовой техникой, располагающую квалифицированными кадрами и сетью специальных научно-исследовательских учреждений.
Нефть и газ – это наиболее дешевое топливо. Из года в год растут потребности страны в моторном, реактивном, дизельном топливе, в смазочных материалах для всевозможных машин и механизмов и в других многочисленных нефтепродуктах. Кроме того, нефть и газ являются сырьём для получения многих ценных химических продуктов, в том числе синтетического каучука, спиртов, эфиров, технических жиров, синтетических тканей и т. д. Поэтому вполне естественно, что в Российской федерации уделяли и уделяют огромное внимание развитию нефтяной и газовой промышленности.
Высокие темпы роста добычи нефти невозможны без значительного прироста разведанных запасов, без вовлечения в промышленную разработку большого числа новых месторождений, без расширения объёма буровых работ, без применения новых систем разработки и, конечно, без соответствующего технического оснащения нефтедобывающей промышленности.
Широкое применение газа в качестве топлива и для технологических нужд открывает перед хозяйством государства неограниченные возможности. Известно, что топливо составляет значительную часть издержек на производство электроэнергии, цемента, металла, стекла, фарфора, ряда строительных материалов и т.д. Использование газа в этих отраслях дает значительный экономический эффект.
Положительные результаты применения природного газа для технологических нужд получены в доменных и мартеновских цехах металлургических заводов страны. Успешно используется газ как технологическое топливо в печах прокатных и трубопрокатных цехов. Рост химической промышленности связан с развитием добычи нефти и газа.
Газовая промышленность Краснодарского края имеет большое значение в топливном балансе страны. Большое количество газоконденсатных месторождений со значительными запасами газа позволило за короткий срок увеличить добычу газа на Кубани.
За последние годы было осуществлено техническое перевооружение в бурении и техники эксплуатации газовых и газоконденсатных скважин Краснодарского края. Используются новые прогрессивные методы и техники разведки, бурения скважин, обустройство промыслов и эксплуатация газовых и газоконденсатных месторождений, разработанных и внедренных на Кубани.
1.ОБЩАЯ ЧАСТЬ
1.1 ОБЩИЕ СВЕДЕНИЯ ОБ УЧАСТКЕ РАБОТ
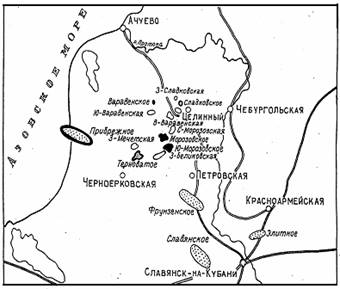
Рис.1.1.Обзорная карта района работ.
По административному делению Северо-Прибрежная площадь расположена на территории Славянского района Краснодарского края, в 130 км в северо-западном направлении от краевого центра, в 4км к северо-западу от станицы Черноерковской (рис. 1.1).
Железнодорожная станция "Протока" (г. Славянск – на – Кубани) находится в 46км к юго-востоку. К станице Черноерковской ведет асфальтированное шоссе через станицу Петровскую, которое выходит на асфальтированное шоссе Славянск-Ачуево. Дорожная сеть в районе, прилегающем к площади, развита слабо. Большинство дорог грунтовые, труднопроходимые в осенне-зимний период.
В орогидрографическом отношении Северо-Прибрежная площадь расположена в пределах низменной равнины, занятой плавнями и лиманами, частью мелиорированной под рисовые чеки, с сетью оросительных каналов. Древесной растительности нет.
Климат района умеренно-континентальный, со среднегодовой температурой +11-12°С. Лето сравнительно сухое, жаркое, со среднемесячной температурой +25°С. Зимой среднемесячная температура - 5°С, однако бывают морозы до -20°С. Безморозный период 195 дней. Среднегодовое количество осадков 550-600мм, большая часть их выпадает в осенне-зимний период в виде дождя.
Промышленность в районе работ практически отсутствует. Население занято в сельском хозяйстве.
Водоснабжение буровых будет осуществляться из артезианских скважин, пробуренных на площадках этих скважин.
1.2 ГЕОЛОГИЧЕСКАЯ ХАРАКТЕРИСТИКА УЧАСТКА РАБОТ
1.2.1 Геологическое строение участка
Газоносный комплекс пород Прибрежных месторождений включает меловые и третичные отложения. Нижний мел представлен главным образом, песчано-глинистыми отложениями, заканчивающимися пачкой темных жирных глин альба с небольшими прослоями рыхлых песчаников. Верхний мел представлен в основном карбонатной толщей – известняками и мергелями.
В разрезе третичных пород, представленных в районе всеми ярусами палеогена и неогена, преобладают песчано-глинистые отложения. Исключение составляют мергели и известняки фораминиферовых отложений, а также прослои известняков в сармате и меотисе.
Наибольший интерес представляют продуктивные, карагано-чокракские слои среднего миоцена, которые являются газоносными на Прибрежных площадях.
Чокракские слои представлены переслаивающимися темными глинами, глинистыми сланцами и рыхлыми кварцевыми песчаниками и песками. На большей части площади в нижнем разрезе чокрака выделяется пачка глин, не содержащих песчаников. Наиболее характерным признаком чокракских отложений является их чрезвычайно резкая фациальная изменчивость по площади и изменение мощностей. Так коэффициент песчанистости их увеличивается с запада на восток от 0,1 до 0,4 милидарси.
Караганские слои по своему литологическому составу сходны с верхней песчано-глинистой частью чокрака и представлены чередованием бурых песчанистых глин, светлых кварцевых песков и песчаников и желтовато-серых мергелей. Основным отличием караганских отложений от чокракских является большая их песчанистость и меньшая фациальная изменчивость. Изменение мощности происходит в том же направлении, что и для чокракских отложений, т.е. мощность уменьшается на северо-запад и юг от 440 до 50-100 метров. Подстилаются чокракские слои однообразной толщей слоистых, темных, битуминозных майкопских глин с тонкими прослоями песчаников и мергелей мощностью до 1500 метров.
В отложениях чокрака по результатам геолого-технологических исследований (механической скорости, исследования шлама, газового каротажа) выделены 7 песчано-алевролитовых пачек.
Песчаники и алевролиты, вскрытые в интервалах 2782 – 2783 метров, 2793 - 2795 метров, 2895 – 2896 метров, и выделяющиеся по ДМК как коллекторы, характеризуются повышенными газопоказаниями и повышенным содержанием маслянистых битумоидов, что свидетельствует о их возможной продуктивности .
Песчаный пласт в интервале 3021 - 3024 метров по ДМК выделяется как коллектор, по результатам геохимических исследований является продуктивным, что позволяет рекомендовать его для опробования.
Песчано-алевролитовые породы, вскрытые в интервалах 2904 - 2906 метров, 2956 – 2958 метров, 2963 – 2964 метров по газовому каротажу характеризуются как водонасыщенные, однако по ЛБА проявляют признаки УВ насыщения. Характер насыщения указанных пластов неясен.
При проходке интервалов 1580-1775 метров, 1910-1980 метров, 2025-2050 метров, 2110-2125 метров, 2280-2520 метров наблюдались осыпи и обвалы стенок скважин,
что подтверждается результатами кавернометрии. Одна из основных причин осыпей и обвалов – несоответствие плотности промывочной жидкости поровым давлениям вскрываемых отложений.
1.2.2 Стратиграфия
Таблица 1.1 Литолого-стратиграфическая и геохимическая характеристика горных пород
Группа |
Система |
Отдел |
Подотдел |
Ярус |
Проектная глубина, м |
Фактич. глубина, м |
Кайнозойская KZ |
Неогеновая N |
Четвертичный +Плиоцен N2
|
Четвертичный +Куяльник Q+ N2
3
kl |
0 – 620 |
0 – 506 |
Плиоцен N2
|
Нижний N2
1
|
Киммерий N2
1
km |
620 – 1020 |
506 –1036 |
Миоцен N1
|
ВерхнийN1
3
|
Понт N1
3
pt |
1020 – 1660 |
1036 – 1659 |
Миоцен N1
|
Верхний N1
3
|
Меотис N1
3
mt |
1660 – 1950 |
1659 - 1964 |
Миоцен N1
|
Верхний N1
3
|
Сарматверхний N1
3
sr3
|
1950 – 2160 |
1964 – 2174 |
Миоцен N1
|
Верхний N1
3
|
Сармат средний N1
3
sr2
|
2160 – 2310 |
2174 - 2392 |
Миоцен N1
|
Средний N1
2
|
Сармат нижний N1
2
sr1
|
2310 – 2490 |
2392 - 2510 |
Миоцен N1
|
Средний N1
2
|
Конка + Караган N1
2
kr +N1
2
kn |
2490 – 2798 |
2510 - 2738 |
Миоцен N1
|
Средний N1
2
|
Чокрак N1
2
ch |
2798 – 3025 |
2738 - 3057 |
Четвертичная система + Куяльницкий ярус Q+
N
2
3
kl
0 – 506 м
Отложения представлены чередованием супесей, суглинков желтовато-коричневых, рыхлых и глин серовато-коричневых, вязких, пластичных, сильно алевритистых, слабоизвестковистых (CaCO3 до 4%). В нижней части переслаивание песка серого, светло - серого, полимиктового, разнозернистого с глинами серыми, голубовато-серыми, мягкими, слабоизвестковистых (CaCO3 до 4%).
В результате проведенных геохимических исследований в отложениях плиоцена отмечаются фоновые газопоказания (от 0.01 до 0.02%). Газ представлен легкой фракцией (метана 100%).
Киммерийский ярус
N
2
1
km
506 – 1036 м
Верхняя часть киммерийского яруса - песчаник светло-серый, серый, кварцевый, разнозернистый, слабосцементированный с прослоями глин серых, голубовато-серых, вязких, пластичных бесструктурных.
Нижняя часть представлена глинами серыми, слабо уплотненными, вязкими, местами сильно алевритистыми, слабоизвестковистыми (CaCO3 3–4 %) с редкими маломощными прослоями песчаника кварцевого, светло-серого, мелкозернистого, слабосцементированного.
В отложениях киммерийского яруса по данным геохимических исследований фоновые газопоказания изменяются от 0 до 0.02%. Газ представлен легкой фракцией (метана 99-100 %). ЛБА 0 баллов.
Понтический ярус N1
3
pt
1036 - 1659 м
Верхняя часть понтического яруса до глубины 1260 м представлена глинами темно-серыми, коричневато-серыми, массивными, слабоуплотненными, вязкими, пластичными, слабоизвестковистыми (CaCO3 до 12%).
Средняя часть разреза до глубины 1556 м представлена чередованием мощных (до 50-90 м) пластов песчаников кварцевых светло-серых, тонкозернистых, слабосцементированных на глинистом цементе и глин серых плотных и слабоуплотненных, слабослюдистых, алевритистых, известковистых и сильноизвестковистых (СаСО3
от 12 до 29%).
Нижняя часть яруса – глины серые и темно-серые, тонкослоистые и неяснослоистые, плотные, алевритистые, слюдистые, слабоизвестковистые (СаСО3
от 4 до 5%).
В результате проведенных геохимических исследований в отложениях понтического яруса отмечаются, в основном, фоновые газопоказания (от 0.03 до 0.06%), с кратковременными, незначительными увеличениями газопоказаний до 0.17%. Газ представлен легкой фракцией (метан 96 - 98%, этан 2 – 4%). По данным люминесцентно - битуминологических исследований, в отложениях отсутствуют концентрации легкого битума (ЛБА 0 баллов). Это говорит о наличии в песчаных пропластках понтического яруса пластовой воды с незначительным количеством растворенного метана.
Меотический ярус N1
3
mt
1659 – 1964 м
Верхняя часть яруса до глубины 1780м - глины серые, темно-серые, массивные, местами тонкослоистые, неравномерно алевритистые, слюдистые, слабоизвестковистые (CaCO3 до 5 %) с прослоями песчаника кварцевого серого и светло-серого, разнозернистого (от мелкозернистого до среднезернистого), слабосцементированного карбонатно-глинистым цементом.
Средняя часть до глубины 1930м представлена переслаиванием мощных до 10 - 25 м песчаников серых и светло - серых, кварцевых, мелкозернистых и среднезернистых, слабосцементированных карбонатно-глинистым цементом с глинами от серого до темно-серого цвета, алевритистыми, слюдистыми, известковистыми (CaCO3 до 8 %), плотными.
Нижняя часть яруса представлена глинами серыми, темно-серыми, плотными, участками тонкослоистыми, алевритистыми, слюдистыми, известковистыми (CaCO3 до 8 %), с редкими маломощными (1-2 м) прослоями кварцевого песчаника.
В отложениях меотического яруса фоновые газопоказания от 0.05 до 0.07 % с незначительными увеличениями до 0.15 %, представленные легкой фракцией: метана 94-100 %, этана 0–6 %. ЛБА 0 баллов. Что указывает на наличие в песчаниках пластовой воды с незначительным количеством растворенного метана.
Сарматский ярус N1
2-3
sr
1964 – 2510 м
Верхний сармат N1
3
sr3
(1964 – 2174м). Глина темно-серая, плотная, массивная и неяснослоистая, алевритистая, слюдистая, известковистая (CaCO3 до 8–10 %) с мощными прослоями (до 50 м) песчаников кварцевых иногда с вкраплениями глауконита, светло-серых, от мелкозернистых до среднезернистых, слабосцементированных карбонатно-глинистым цементом. С глубины 2110м верхний сармат представлен глинами темно-серыми, плотными, массивными и тонкослоистыми, слабослюдистыми, слабоизвестковистыми (CaCO3 до 3.7 %) с маломощными прослоями светло-серого мелкозернистого кварцевого песчаника и коричневато-серого доломитизированного мергеля.
Средний сармат N1
3
sr2
(2174 – 2346 м)Представлен глинами серыми и темно-серыми, слабоалевритистыми, слабослюдистыми, слабоизвестковистыми и известковистыми (СаСО3
от 1.3 до 17 %), вязкая, пластичная с тонкими, редкими прослоями известняка светло-серого цвета, крепкого. С глубины 2300м переслаивание глин серых плотных, слабоалевритистых, слюдистых, известковых (СаСО3
до 20 %), мергеля доломитизированного коричневато-серого, крепкого, алевролита серого и песчаника полимиктового серого, мелкозернистого, слабосцементированного. Нижний сармат N1
2
sr1
(2346–2510 м) Глина темно-серая алевритистая, слюдистая, массивная и тонкослоистая, неизвестковистая и слабоизвестковистая (СаСО3
от 0 до 5%) плотная и вязкая, пластичная с прослоями доломита различной окраски, крепкого и песчаника кварцевого, мелкозернистого и тонкозернистого, слабосцементированного.
В отложения сарматского яруса в интервале 1964 – 2490 м отмечались, в основном, фоновые газопоказания (от 0.03 до 0.05 %). Состав газа: метан 90–100 %, этан 0–10 %. По данным люминесцентно - битуминологических исследований шлама отмечается незначительная концентрация легкого битума " А " до 1 - 2 баллов. Можно сделать вывод о наличии в данных отложениях водонасыщенных коллекторов с незначительным количеством растворенных УВ.
Конкский + Караганский ярус
N
1
2
kr
+
N
1
2
kn
2510 - 2738 м
Отложения представлены глинами темно-серыми алевритистыми, сильно слюдистыми, тонкослоистыми, плотными и глинами тонкослоистыми известковистыми (CaCO3 до 15%), вязкими, пластичными с маломощными прослоями мергеля доломитизированного коричневато-серого, крепкого и песчаника кварцевого серого, тонкозернистого, на карбонатно-глинистом цементе, а также известняка светло-серого и белого. Стяжения пирита, зерна молочно-белого кальцита.
В результате геохимических исследований в отложениях караганского яруса среднего миоцена отмечаются, в основном, фоновые газопоказания (от 0.04 до 0.07%), с кратковременными увеличениями газопоказаний до 0.17%. ЛБА составляет 1 - 2 балла БГ МБ, иногда повышается до 1 – 2 баллов ГЖ МБ.
Такая геохимическая характеристика говорит о присутствии в данных отложениях легких битумоидов в рассеянном состоянии и указывает на наличие пластовой воды с незначительным количеством растворенных УВ.
В интервале 2490 – 2564 м отмечено резкое повышение фоновых газопоказаний до 0.8 – 1.5%, с кратковременным повышением до 2%. Состав газа: СН4
15 - 26%, С2
Н6
0.5 – 2%, С3
Н8
0.5 – 1%, С4
Н10
14 – 20%, С5
Н12
35 – 60%, iС4
Н10
1 – 2%, iС5
Н12
10 – 15%. ЛБА 1 – 2 ГЖ МБ. Это связано с установкой нефтяной ванны при ликвидации аварии. Добавки нефти в промывочную жидкость затрудняют интерпретацию газового каротажа указанного интервала.
Чокракский ярус
N
1
2
ch
2738 – 3057.9 м
Разрез представлен глинистыми породами с прослоями алевролитов, песчаников и доломитизированных мергелей. Многочисленные стяжения пирита и пиритизированные раковины. Зерна прозрачного и молочно-белого кальцита.
Глины коричневато-серые и тёмно-серые, алевритистые, слюдистые, полосчатые, слоистые, карбонатные (CaCO3
до 15 %), плотные и глины серые, вязкие, пластичные, хорошо размокающие в воде, слабо алевритистые, известковистые.
Песчаники кварцевые с зернами глауконита серые и светло-серые, мелкозернистые и тонкозернистые, слабосцементированные, реже плотные на карбонатно-глинистом цементе.
Алевролиты светло-серые и коричневато-серые, кварц-полевошпатовые, плотные.
Мергель доломитизированный коричневато-серый, крепкий.
Фоновые газопоказания в отложениях чокракского горизонта по данным геохимических исследований составляют 0.03-0.06 %. При вскрытии песчаных пачек чокракского горизонта наблюдалось увеличение газопоказаний до 0.6–1 %. В процессе газового каротажа после бурения (СПО, промывок) наблюдались выходы пачек разгазированного глинистого раствора до 2.5–4.7 % и повышенное содержание маслянистых битумоидов при ЛБА (3 балла, цвет – бело-голубой, голубовато-желтый). Это может свидетельствовать о наличии в песчаниках газа либо газоконденсата.
В интервале 2782 – 2783 м наблюдалось повышение газопоказаний до 0.211% при увеличении скорости проходки до 2.99 м/ч. По данным геохимических исследований: ЛБА 2 балла ГЖ МБ, приведенное к объему породы газосодержащие составило 3.4, остаточное углеводородосодержание горных пород по пласту Fг=2.6%, что говорит о возможном газонасыщении.
Повышение газопоказаний до 0.611% с одновременным повышением скорости проходки до 5 м/ч наблюдалось в интервале 2793 – 2795 м. По результатам геохимических исследований: ЛБА 2 балла ГЖ МБ, остаточное углеводородосодержание горных пород по пласту составило Fг=2.02 - 3.3%, что говорит о возможном газонасыщении пласта.
Интервал 2895 – 2896 м характеризуется повышением суммарных газопоказаний до 0,17%, ЛБА 3 балла БГ ЛБ, остаточное углеводородосодержание горных пород составляет Fг=2.2%, что говорит о возможном газонасыщении пласта.
При бурении интервалов 2904 – 2906 м, 2955 – 2958м и 2963 – 2964 м резкого повышения газопоказания над фоновыми не наблюдалось. Однако повышение показаний ЛБА до 2 - 3 баллов ГЖ МБ приурочено к песчано-алевритовым пластам со скоростью проходки до 3.55 – 3.88 м/ч. Данные пласты вероятно водонасыщенные, однако по ЛБА имеют признаки УВ насыщения.
При бурении интервала 3021 – 3024 м наблюдалось повышение суммарных газопоказаний до 1.09 %, по результатам геохимических исследований: ЛБА 3 балла ГЖ МБ, приведенные газопоказания 4.4, остаточное углеводородосодержание горных пород составило Fг=3.3%. По результатам геохимических исследований пласт вероятно газонасыщенный.
1.2.3 Тектоника
Газоконденсатные месторождения Прибрежной площади относятся к одному типу залежей – пластовому и приурочены к сводам антиклинальных поднятий.
Газ месторождений заключен в песчаных пластах различной мощности нижнемелового возраста (альб – апт).
По всему месторождению газосодержащий коллектор представлен песчаниками, переслаивающимися глинами; общее число прослоев иногда достигает 10 и более.
Мощность песчаных слоев невелика, и лишь отдельные пласты достигают 10-15 метров.
Коллектор, как правило, имеет очень неоднородную литологическую характеристику по разрезу, значительную изменчивость физических свойств по вертикали и по площади. Средние значения пористости и проницаемости пластов по месторождению колеблется соответственно от 10 до 19% и от 0,1 до 0,6 дарси. Газонасыщенные песчаники залегают на глубинах 1450-2800 метров. Температура пластов изменяется от 42 до 128ºС.
В период, предшествующий открытию газоконденсатных месторождений на Кубани (1952-1956 гг.), на промысловых площадях наблюдались межколонные проявления, открытое фонтанирование и грифонообразования.
Наибольшее количество межколонных проявлений и грифонообразова-ний произошло в те периоды, когда продуктивные горизонты уже были возбуждены и работали после спуска и крепления колонн.
Анализ имеющихся данных показывает, что 93% осложнений на Кубани произошло на площадях: Ново-Дмитриевской, Калужской, Прибреж-ной и Анастасиевско-Троицкой.
В тектоническом плане эти площади представляют собой антиклинальные складки. Крупные тектонические нарушения здесь отсутствуют, а геологическое строение не отличается от остальных разбуриваемых площадей.
1.2.4 Исходные данные для разработки проекта
Эксплуатационная скважина № 11 расположена в пределах Северо-Прибрежной площади, в 0.35км северо-западнее от разведочной скважины № 15 Прибрежной площади, и заложена с целью эксплуатации газовых залежей в чокракских отложениях.
Геолого-технологические исследования проводились станцией геолого-технологического контроля типа: "Сириус" в интервале 193–3057.9 м с 01.04.05 г по 27.07.05.
Перечень основных геолого-технических параметров скважины приведен в таблице 1.2.
Таблица 1.2 Основные геолого-технические параметры скважины
№п.п. |
Данные по скважине |
Проектные |
Фактические |
1 |
2 |
3 |
4 |
1
2
3
4
5
|
Глубина скважины
Проектный горизонт
Способ бурения
Профиль скважины
Конструкция скважины:
Направление Ø530 мм
Кондуктор Ø324 мм
Тех колонна Ø245/219 мм
Экспл. колонна Ø140 мм
|
3025м
чокрак
роторный
вертикальная
30м
1020м
2600м
3025м
|
3057м
чокрак
роторный
вертикальная
30м
1020м
2600м
3055м
|
Объем выполненных геологических исследований приведен в таблице 1.3.
Таблица 1.3 Объем выполненных геологических исследований
№ п.п. |
Виды исследований |
Количество определений, анализов и пр. |
1 |
2 |
3 |
1
2
3
4
5
6
7
8
9
10
|
Отбор и описание шлама
Литологическое определение пород в интервале
Определение карбонатности пород
Определение градиента порового давления по расчетам параметра буримости "Б"
Проведение люминесцентно - битуминологического анализа пород
Газовый каротаж в интервале
Раздельный анализ газа по стволу скважины
Проведение анализа газа проб бурового раствора
Построение литолого-стратиграфического разреза
Выдача суточных пометровых сводок геолого-технологических параметров.
|
214
193 – 3057 м
214
1020 – 3057 м
214
193 – 3057 м
193 – 3057 м
193 – 3057 м
193 – 3057 м
ежедневно
|
В перспективных участках разреза чокрака проводился отбор проб бурового раствора для определения коэффициента дегазации дегазатора, фактического углеводородосодержания бурового раствора, расчет коэффициента разбавления, определение приведенного к объему породы газосодержания и остаточного углеводородосодержания горных пород Fг.
В процессе бурения проводился непрерывный газовый каротаж в интервале 0 - 3057м с фиксированием суммарных газопоказаний в газовоздушной смеси из бурового раствора, одновременно на ХГ производилось покомпонентное определение состава газа, а также люминесцентно-битуминологический анализ шлама.
2. ПРОЕКТНАЯ ЧАСТЬ
2.1 ВЫБОР И ОБОСНОВАНИЕ СПОСОБА БУРЕНИЯ
Бурить скважины можно механическим, термическим, электроимпульсным и другими способами (несколько десятков). Однако промышленное применение находят только способы механического бурения – ударное и вращательное. Остальные пока не вышли из стадии экспериментальной разработки. Ударный способ более 50 лет не применяется на нефтегазовых промыслах России, следовательно на проектируемой скважине применяем вращательное бурение.
При вращательном бурении разрушение породы происходит в результате одновременного воздействия на долото нагрузки и крутящего момента. Под действием нагрузки долото внедряется в породу, а под влиянием крутящего момента скалывает ее.
Существует две разновидности вращательного бурения – роторный и с забойными двигателями.
При бурении с забойным двигателем долото привинчено к валу, а бурильная колонна – к корпусу двигателя. При работе двигателя вращается его вал с долотом, а бурильная колонна воспринимает реактивный момент вращения корпуса двигателя, который гасится невращающимся ротором (в ротор устанавливают специальную заглушку).
При роторном бурении мощность от двигателей передается через лебедку к ротору - специальному вращательному механизму, установленному над устьем скважины в центре вышки. Ротор вращает бурильную колонну и привинченное к ней долото. Бурильная колонна состоит из ведущей трубы и привинченных к ней с помощью специального переводника бурильных труб.
2.2.ПРОЕКТИРОВАНИЕ КОНСТРУКЦИИ СКВАЖИНЫ, ОБОСНОВАНИЕ И РАСЧЕТ ПРОФИЛЯ ПРОЕКТНОЙ СКВАЖИНЫ
Конструкция газовой или газоконденсатной скважины должна выбираться с учетом конкретных особенностей не только данного месторождения, но и каждой отдельной скважины. Она зависит от геологических условий, глубины залегания и пластового давления эксплуатационного объекта, физико-механических и других свойств горных пород и характера осложнений в процессе бурения. Кроме того, конструкция должна разрабатываться с учетом максимально возможной экономии пластовой энергии и получения больших дебитов газа. Эти два требования определяют выбор диаметра эксплуатационной колонны, которая в свою очередь является основным элементом конструкции скважины, так как от ее диаметра зависят диаметры остальных обсадных колонн[1].
Выбор конструкции скважины зависит также от комплекса неуправляемых и управляемых факторов.
·К неуправляемым факторам следует отнести геологические условия месторождения: глубину залегания продуктивных пластов, их продуктивность и коллекторские свойства; пластовые и поровые давления, а также давления гидроразрыва проходимых пород; физико-механические свойства и состояние пород, вскрываемых скважиной с точки зрения возможных обвалов, осыпей, кавернообразования, передачи на обсадные колонны горного давления и т.д.
·К управляемым факторам можно отнести способ бурения; число продуктивных горизонтов, подлежащих опробованию; способ вскрытия продуктивных горизонтов; материально-техническое обеспечение.
Конструкция скважины считается рациональной, если она обеспечивает минимальную стоимость ее строительства, а также выполнение технических (существующие технические средства и материалы, условия их доставки), технологических (освоенные технологические приемы, организация труда основных и вспомогательных подразделений) и геологических (проявление пластовых флюидов, поглощение буровых и тампонажных растворов, обвалообразование и пластическое течение горных пород) ограничений и требований к надежности и долговечности скважины (обеспечение успешного испытания, освоения и эксплуатации)[8].
2.2.1 Расчет и обоснование конечного, промежуточного и начального диаметров бурения
Строительство скважины состоит из двух последовательно идущих процессов: бурения скважины и ее крепления. Бурение – это разрушение пород и создание ствола скважины. Цель крепления ствола скважины – во-первых, закрепить ее стенки, сделать их устойчивыми против усилий, создаваемых боковым давлением пород, и, во-вторых, изолировать друг от друга разнородные пласты.
Основным элементом при сооружении скважины является ее технический разрез, т.е. конструкция скважины, которая определяется диаметром, глубиной спуска и числом обсадных колонн, толщиной стенок труб, диаметром самой скважины на разных ее глубинах, высотой подъема цемента за трубами.
Для доведения обсадных колонн до намеченных глубин необходимо определить диаметр ствола скважины. Для этого пользуемся данными практики бурения – величинами зазоров просвета и коэффициентов просвета скважины[3].
Величина зазора или просвета скважины определяется по формуле[4]:
β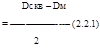
где, β – величина зазора или просвета, мм;
Dскв – диаметр скважины, мм;
Dм – наружный диаметр муфты, мм.
Рекомендуемые значения величин зазоров изменяются в пределах от 15 до 50 мм и зависят от жесткости колонны, степени искривления ствола скважины (таблица 2.1).
Таблица 2.1.Значения величин зазоров
Диаметр обсадных труб, мм |
Зазор между стенками скважины и
Диаметром муфт этих труб не более, мм
|
140
245
324
|
20
30
45
|
Если величину зазора скважины отнести к диаметру скважины, т.е.[4]:
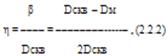
то получим значение коэффициента просвета скважины. Из формулы (2.2) можно получить значение диаметра скважины, выраженное через коэффициент просвета и диаметр муфты[4]:
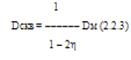
Если величину 1/(1–2η) обозначить через ƒ, то получим[4]:
Dскв = ƒDм (2.2.4)
Из формулы видно, что диаметр скважины можно определить умножением диаметра муфты обсадной колонны, подлежащей спуску в скважину, на расчетный коэффициент ƒ (таблица 2.2).
Таблица 2.2 Диаметры колонны и муфты и значения коэффициентов
Обсадная колонна |
Диаметр
колонны,мм
|
Диаметр
муфты,мм
|
Значение
коэффициентаƒ
|
Кондуктор
Промежуточная колонна
Эксплуатационная колонна
|
324
245
140
|
351
264
160
|
1,14
1,17
1,18-1,35
|
На основании данных таблицы 2.2 находим, что максимальным диаметром долота под 140-мм колонну будет:
Dmin = 1,19 x 160 = 190,5 мм
Чтобы пропустить долото диаметром 190,5 мм через промежуточную колонну обсадных труб, минимальный диаметр последней должен быть:
Dкол = 190,5 + 6 = 200,5 мм
Для промежуточной колонны, исходя из технологических соображений, выбираем трубы диаметром 245 мм и пробурим ствол скважины под данную колонну долотом согласно формуле (2.2.4):
Dскв = 1,17 x 264 = 308,8 мм
Из стандартных типоразмеров выбираем долото диаметром 295,3 мм.
Чтобы долото диаметром 293,7 мм пропустить через колонну труб, кондуктор должен иметь диаметр 324 мм. Далее определяем диаметр долота под ствол скважины для спуска кондуктора:
Dскв = 1,14 x 351 = 400 мм
Для бурения скважины под кондуктор выбираем долото диаметром 393,7 мм[5].
Таким образом, предусматривается следующая конструкция скважины №11 Северо-Прибрежной:
·Шахтное направление длиной 30 метров и диаметром 530 мм, спускается для предохранения устья от размыва буровым раствором и для обвязки устья с желобной системой, забивается электровибратором;
·Кондуктор диаметром 324 мм спускается на глубину 1020 метров, цементируется до устья. Предназначен для изоляции и предохранения вод хозяйственно-питьевого назначения, перекрытия неустойчивых отложений и установки противовыбросного оборудования.
·Промежуточная колонна диаметром 245 мм спускается на глубину 2450 метров, цементируется до устья. Предназначена для перекрытия неустойчивых отложений понта, меотиса; верхнего, среднего и большей части нижнего сармата и установки противовыбросного оборудования.
·Эксплуатационная колонна диаметром 140 мм спускается на глубину 3025 метров, цементируется в интервале 3025-1850 метров. Служит для разобщения вскрытых пластов, опробования и эксплуатации продуктивного горизонта[5].
2.2.2 Выбор промывочного агента для бурения скважины
Ствол скважины длительное время находится в необсаженном состоянии при значительном всестороннем давлении, что является причиной обвалов и осыпей, вызывающих посадки, затяжки, прихваты бурильного инструмента, недоходы обсадных колонн до проектных глубин. Проходка ствола скважины в неустойчивых породах также осложняет процесс бурения, так как такие породы способствуют обвалам и вследствие этого прихватам бурильного инструмента. Кроме этого, в некоторых районах, подверженных карстообразованию, ствол скважины иногда попадает в огромные каверны[6].
Идеальный буровой раствор, применяемый при бурении скважин, должен отвечать следующим требованиям:
·способствовать повышению скорости проходки;
·позволять поддерживать низкое содержание твердой фазы, благодаря чему до минимума снижается опасность загрязнения пласта;
·повышать устойчивость ствола, ингибировать склонные к осложнениям породы и обеспечивать сохранение целостности выбуренной породы, благодаря чему облегчается ее удаление;
·обеспечивать поддержание на стабильном уровне статического напряжения сдвига и улучшенную очистку ствола без чрезмерных пульсаций давления в процессе спускоподъемных операций;
·проявлять низкую токсичную и высокую термостабильность;
·давать возможность экономить денежные средства, при этом затраты на контролирование и поддержание необходимых свойств бурового раствора с лихвой окупаются.
Для устранения осложнений скважину бурят с применением высококачественной промывочной жидкости. Непрерывная циркуляция промывочной жидкости в стволе скважины обеспечивает не только очистку забоя от выбуренной породы, но и охлаждение и смазку долота.
Глинистые растворы, применяемые в качестве промывочной жидкости, глинизируют стенки скважины и удерживают во взвешенном состоянии выбуренные частицы породы в покоящейся жидкости, т.е. в период прекращения циркуляции. Они являются одним из наиболее распространенных видов промывочных жидкостей, применяемых при бурении нефтяных и газовых скважин. Обработанные химическими реагентами они образуют устойчивую суспензионно-коллоидную дисперсную систему с небольшой водоотдачей и необходимыми структурно-механическими качествами. При нормальных условиях бурения нетрудно регулировать их параметры[9].
Глинистый раствор – это смесь мелких частиц глины с водой, приготовленная так, что частицы глины находятся во взвешенном состоянии.
Глинистый раствор приготовляется непосредственно на буровой при помощи глиномешалок[8].
Для выбора бурового раствора воспользуемся информацией о горных породах, их проницаемости, пластовых давлениях и номинальных диаметрах скважины представленных в таблицах 1.1 и 2.2. В соответствии с геолого- техническими условиями определяем компонентный состав бурового раствора, одинаковый для всех интервалов: ингибированный полимер-глинистый раствор, в состав которого входят бентонитовый глинопорошок, вода, утяжелитель (барит), ССБ, ФХЛС, нефть, графит, хроматы, эмульгаторы, пеногаситель, КМЦ.
Технологические параметры бурового раствора приведены в таблице 2.3.
Таблица 2.3 Технологические параметры бурового раствора
Интервал |
Параметры раствора |
Реолог. св-ва |
Содержание |
от, м |
до, м |
плот-
ность,
кг/м³
|
услов.
вяз-ть
с
|
водо-
отдача
см³/30´
|
пласт.
вяз-ть
мПа*с
|
динам
напряж
сдв,дПа
|
колоид
фазы
|
песка |
твердой фазы |
всего |
об. % |
вес,% |
0
1020
2010
2232
2312
2391
2489
2581
2697
2803
2907
|
1020
2010
2232
3212
3291
2489
2581
2697
2803
2907
3076
|
1150
1180
1260
1360
1460
1560
1640
1720
1860
1980
2130
|
35-45
35-45
35-45
35-45
40-50
40-50
40-50
40-50
40-50
40-60
40-60
|
4-5
3-3,5
3-3,5
3-3,5
3-3,5
3-3,5
3-3,5
3-3,5
3-3,5
3-3,5
3-3,5
|
20
30
30
30
40
45
45
45
50
50
50
|
70
70
70
70
85
90
90
100
120
140
150
|
3,0
3,0
3,0
3,0
2,9
2,7
2,6
2,5
2,3
2,2
2,0
|
2
1
1
1
1
1
1
1
1
1
1
|
9,4
11,3
16,3
22,5
28,8
35,0
40,0
45,0
53,8
61,3
70,6
|
21,2
24,8
33,5
43,0
51,2
58,3
63,4
68,0
75,1
80,4
86,2
|
2.3ТЕХНИКА БУРЕНИЯ
2.3.1
Определение оптимальной массы бурильной колонны
2.3.1.1 Расчет бурильных труб, УБТ, компоновок бурильной колонны
Бурильная колонна является связующим звеном между долотом, находящимся на забое скважины, и буровым оборудованием, расположенным на поверхности. Она предназначена для подвода энергии (механической, гидравлической, электрической) к долоту, обеспечения подачи бурового раствора к забою, создания осевой нагрузки на долото, восприятия реактивного момента долота и забойного двигателя.
Основные элементы, составляющие бурильную колонну, — ведущая труба (квадратная штанга), бурильные трубы, бурильные замки, муфты, переводники, центраторы бурильной колонны, утяжеленные бурильные трубы (УБТ).
Для передачи вращения БК от ротора или реактивного момента от забойного двигателя к ротору при одновременном осевом перемещении БК и передаче бурового раствора от вертлюга в БК служат ведущие бурильные трубы[6].
При бурении нефтяных и газовых скважин применяют ВБТ сборной конструкции, состоящие из квадратной толстостенной штанги 2 с просверленным каналом, верхнего штангового переводника (ПШВ) 1 с левосторонней резьбой и нижнего штангового переводника (ПШН) 3 с правосторонней резьбой.
Для защиты от износа замковой резьбы ПШН, подвергающейся многократным свинчиваниям и развинчиваниям при наращивании БК и спуско-подъемных работах, на ПШН дополнительно навинчивают предохранительный переводник.
По ТУ 14-3-126 предусматривается выпуск ВБТ с размерами сторон квадратной штанги 112х112, 140х140, 155х155. Размер присоединительной резьбы, соответственно, З-117 (З-121; З-133); З-140 (З-147); З-152 (З-171).
Квадратные штанги для ВБТ изготавливают длиной до 16,5 м из стали групп прочности Д и К (предел текучести 373 и 490 МПа), а переводники ПШН и ПШВ – из стали марки 40ХН (с пределом текучести 735 МПа).
Бурильные трубы составляют основную часть колонны. Они приспособлены к длительному свинчиванию - развинчиванию. Промышленность выпускает бурильные трубы длиной 6 ± 0.6; 8 ± 0.6; 11.5 ± 0.9 м, наружным диаметром 60, 73, 89, 102 мм. Трубы диаметром 114, 127, 140 и 168 мм выпускают длиной 11.5 ± 0.9 м.
В настоящее время в нефтегазовой промышленности широко используются стальные бурильные трубы с приваренными замками
Бурильная труба состоит из трубной заготовки и присоединительных концов (замковой муфты и замкового ниппеля). Последние соединяются с трубной заготовкой либо посредством трубной резьбы (профиль по ГОСТ 631) и представляют собой бурильную трубу сборной конструкции, либо посредством сварки. Для свинчивания в свечи на присоединительных концах нарезается замковая резьба по ГОСТ 5286 (на ниппеле наружная, на муфте внутренняя). Для увеличения прочности соединений концы трубных заготовок "высаживают", т.е. увеличивают толщину стенки[10].
Стальные бурильные трубы с приваренными замками предназначены преимущественно для роторного способа бурения, но также используются и при бурении с забойными гидравлическими двигателями.
ТБП выпускают в соответствие с ГОСТ Р 50278 трех разновидностей:
- ПВ – с внутренней высадкой;
- ПК – с комбинированной высадкой;
- ПН - с наружной высадкой.
Изготовляют трубные заготовки из стали групп прочности Д, Е, Л, М, Р с пределом текучести, соответственно: 373, 530, 637, 735, 882 МПа длиной 12 м. Присоединительные концы – бурильные замки изготовляют по ГОСТ 27834-95 из стали 40 ХН (предел текучести 735 МПа) для труб из стали групп прочности Д, Е. Для труб из стали групп прочности Л, М, Р замки изготовляются из стали 40ХМФА (предел текучести 980 МПа).
При роторном бурении колонна бурильных труб служит для передачи вращения долоту и подачи бурового раствора к забою скважины.
Для увеличения веса и жесткости БК в ее нижней части устанавливают УБТ, позволяющие при относительно небольшой длине создавать частью их веса необходимую нагрузку на долото[3].
В настоящее время наиболее широко используются следующие типы УБТ:
· горячекатанные (УБТ), изготавливаемые по ТУ 14-3-385;
· сбалансированные (УБТС), изготавливаемые по ТУ 51-744.
УБТ этих типов имеют аналогичную беззамковую (отсутствуют отдельные присоединительные концы) толстостенную конструкцию и поставляются в комплекте. Комплект УБТ имеет одну наддолотную трубу с двумя муфтовыми концами, а остальные – промежуточные (верхний конец муфтовая резьба, нижний – ниппельная). Горячекатанные УБТ выполняются гладкими по всей длине. На верхнем конце УБТС выполняется конусная проточка для лучшего захвата клиньями при спуско-подьемных работах.
Горячекатанные УБТ используются преимущественно при бурении с забойными гидравлическими двигателями.
Сбалансированные УБТ используют преимущественно при роторном способе бурения. УБТС изготовляют из сталей марки 38ХН3МФА (предел текучести 735 МПа) и 40ХН2МА (предел текучести 637 МПа). Канал у таких труб просверлен, что обеспечивает его прямолинейность, а наружная поверхность подвергнута механической обработке, что обеспечивает равную толщину стенки и круглое сечение. Обкатка резьбы роликами и ее фосфатирование, термическая обработка концевой (0,8-1,2 м) поверхности труб значительно повышают их прочностные показатели[4].
Диаметр бурильных труб должен составлять 60-65%, а диаметр УБТ -75-85% от диаметра долота. Поэтому при бурении проектируемой скважины будут использоваться бурильные трубы диаметром 127мм (вес1м-31,9 кг), а УБТ -диаметром 178 мм. (вес1м-156 кг)
Определим вес снаряда по формуле:
Q
кр
=
k
*
α
*
q
*
L
*(1-γж
/γст
), (
2.3.1.)
где k - коэффициент, учитывающий силы трения колонны бурильных труб о стенки скважины, а также возможные прихваты ее породой (при подъеме снаряда k = 1,25-1,5; при подъеме обсадных труб k = 1,5-2,0);
α - коэффициент, учитывающий увеличение веса труб за счет соединяющих их элементов ( для муфтово-замковогоα =1,1);
q - вес 1 м труб, кг;
L - длина колонны труб, м;
γж
- удельный вес промывочной жидкости, г/см3
;
γст
- удельный вес материала бурильных труб (для стали 7,85 г/см3
).
Вес инструмента под колонну диаметром 324 мм:
Qкр = 1,25*1,1*31,9*1020*(1-1,18/7,85) = 38028 кг = 38 т.
Вес инструмента под колонну диаметром 245 мм:
Qкр =1,25*1,1*31,9*2450*(1-1,7/7,85)=83821 кг = 83.8 т.
Вес инструмента под колонну диаметром 146 мм:
Qкр = 1,25*1,1*31,9*3025*(1-2,13/7,85)= 96859кг = 96.8т.
Вес инструмента можно также рассчитать по следующей формуле:
Q
кр
= (
P
при
+ Р
перев
+ Р
убт
+ Р
бур.тр
+ Р
вед.тр
+ Р
вертл )
*(1-γж
/γст
), (
2.3.2.)
Для этого необходимо знать длину утяжеленных бурильных труб. Вычислим ее по формуле:
L
убт
=
k
*Р / (
q
*(1-γж
/γст
)),
где Р - осевая нагрузка на породоразрушающий инструмент, Н;
q - вес 1 м УБТ, кг;
k - коэффициент завышения веса УБТ (k = 1,25-1,5).
При бурении под колонну диаметром 324 мм:
Lубт = 1,25*104054/(1560*(1-1,18/7,85)) = 98 м.
Применяем 4 свечей УБТ диаметром 178 мм по 25 м.
При бурении под колонну диаметром 245 мм:
Lубт = 1,25*83271/(1560*(1-1,7/7,85)) = 85.5 м.
Применяем 4 свечей УБТ диаметром 178 мм по 25 м.
При бурении под колонну диаметром 140 мм:
Lубт = 1,25*81207/(1560*(1-2,13/7,85)) = 89 м.
Применяем 4 свечей УБТ диаметром 178 мм по 25 м.
Для создания необходимой нагрузки на долото можно использовать УБТ разного диаметра.
Вычислим вес бурового снаряда при бурении под колонну диаметром 324 мм:
Q
кр
= (
P
при
+ Р
перев
+
L
убт
*
q
убт
+
L
бур.тр
*
q
бур.тр
+
L
вед.тр
*
q
вед.тр
+ Р
вертл
)*(1-γж
/γст
), (2.3.3.)
Qкр = (37,8+15+98*156+922*31,9+16*
124,3+6700)*(1-1,18/7,85) = 45426 кг = 45.4т.
Вычислим вес бурового снаряда при бурении под колонну диаметром 245 мм:
Q
кр
= (
P
при
+ Р
перев
+
L
убт
*
q
убт
+
L
бур.тр
*
q
бур.тр
+
L
вед.тр
*
q
вед.тр
+ Р
вертл
)*(1-γж
/γст
), (2.3.4.)
Qкр = (37,8+15+85.5*156+2364.5*31,9+16*
124,3+6700)*(1-1,7/7,85) = 76056 кг =76т.
Вычислим вес бурового снаряда при бурении под колонну диаметром 140 мм:
Q
кр
= (
P
при
+ Р
перев
+
L
убт
*
q
убт
+
L
бур.тр
*
q
бур.тр
+
L
вед.тр
*
q
вед.тр
+ Р
вертл
)*(1-γж
/γст
), (2.3.5.)
Qкр = (37,8+15+89*156+2936*31,9+16*
124,3+6700)*(1-2,13/7,85) = 84887кг = 84.9т.
Переводники предназначены для соединения элементов БК с резьбами различных типов и размеров. Переводники согласно ГОСТ 7360 разделяются на три типа:
1) Переводники переходные, предназначенные для перехода от резьбы одного размера к резьбе другого. ПП имеющие замковую резьбу одного размера называются предохранительными.
2) Переводники муфтовые для соединения элементов БК, расположенных друг к другу ниппелями.
3) Переводники ниппельные для соединения элементов БК, расположенных друг к другу муфтами.
Переводники каждого типа изготовляют с замковой резьбой как правого, так и левого направления нарезки. Резьба должна соответствовать ГОСТ 5286-75 для бурильных замков.
ГОСТ 7360 предусматривает изготовление 90 типоразмеров переводников, которые охватывают практически все необходимые случаи их применения.
Пример условного обозначения переводника типа ПП с резьбами муфтовой З-147, ниппельной З-171: П - 147/171 ГОСТ 7360
То же, но с левой резьбой: П - 147/171 –Л ГОСТ 7360
Переводники изготовляются из стали марки 40ХН (предел текучести 735 МПа).
Калибраторы служат для выравнивания стенок скважины и устанавливаются непосредственно над долотом. Используются как лопастные калибраторы с прямыми (К), спиральными (КС) и наклонными лопастями (СТ), так и шарошечные. Диаметры калибратора и долота должны быть равны. Материал вооружения – твердый сплав (К, КС), алмазы (СТ), "Славутич" (КС). При бурении проектной скважины предусматривается использование калибратора лопастного спиралевидного (КЛС).
Центраторы предназначены для обеспечения совмещения оси БК с осью скважины в местах их установки.
Стабилизаторы, имеющие длину в несколько раз большую по сравнению с длиной центраторов, созданы для стабилизации зенитного угла скважины.
2.3.1.2 Расчет обсадных колонн
Обсадные трубы служат для крепления ствола скважины. По ГОСТ 632-80 отечественные обсадные трубы выпускаются следующих диаметров и толщины:
Таблица 2.5 Диаметры и толщина обсадных труб
Æ, мм |
114.3 |
127.0 |
139.7 |
146.1 |
168.3 |
177.8 |
s, мм |
5.2 - 10.2 |
5.6 - 10.2 |
6.2 - 10.5 |
6.5 - 9.5 |
7.3 - 12.2 |
5.9 - 15.0 |
193.7 |
219.1 |
244.5 |
273.1 |
298.5 |
323.9 |
339.7 |
5.2 - 10.2 |
7.6 - 15.1 |
7.9 - 15.9 |
7.1 - 16.5 |
8.5 - 14.8 |
8.5 - 14.0 |
8.4 - 15.4 |
351.0 |
377.0 |
406.4 |
426.0 |
473.3 |
508.0 |
9.0 - 12.0 |
9.0 - 12.0 |
9.5 - 16.7 |
10.0 - 12.0 |
11.1 |
11.1 - 16.1 |
Группа прочности стали "Д", "К", "Е", "Л", "М", "Т". Трубы маркируются клеймением и краской. При спуске в скважину обсадные трубы шаблонируют.
Определим вес обсадной колонны диаметром 324мм по формуле:
Р
обс =
L
обс*
q
обс
,
где (2.3.6.)
Робс. - длина обсадной колонны, м; qобс. - вес 1 м обсадных труб, кг.
Робс
. = 1020*74.7 = 76194 кг = 76,2 т. Робс в р-ре
= Робс
*(1-1,18/7,85) = 64.8т
Определим вес обсадной колонны диаметром 245мм:
Робс
. = 2450*70.8 = 173460 кг = 173,5 т. Робс в р-ре
= Робс
*(1-1,7/7,85) =135.3т
Определим вес обсадной колонны диаметром 140 мм:
Робс
. = 3025*30.7 = 92867 кг = 92,9 т. Робс в р-ре
= Робс
*(1-2,13/7,85) = 67.8т
Сравнив вес обсадных колонн и вес бурового снаряда при бурении под каждую из колонн можно сделать вывод что самой тяжелой является обсадная колонна диаметром 245мм.
Эксплуатационные и промежуточные колонны обсадных труб работают в наиболее тяжелых условиях. Например, в процессе спуска колонн обсадных труб по мере их наращивания увеличивается нагрузка, обусловленная силами собственного веса. После того как колонна доведена до забоя и установлена на забой, трубы частично разгружаются от растягивающих усилий. Силы внешнего давления, действующие на трубы в процессе спуска колонны и определяемые разностью давления столбов жидкости за трубами и внутри их, по своей величине незначительны.
Промежуточная колонна труб работает в несколько иных условиях, нежели эксплуатационная. Промежуточная колонна в основном работает на растяжение от собственного веса, а также от сил, создаваемых внутренним давлением. Наибольшего значения внутреннее давление достигает в момент окончания продавки цемента за колонну, а также при увеличении удельного веса глинистого раствора внутри обсадных труб по отношению к удельному весу раствора, оставшегося в затрубном пространстве.
В эксплуатационной колонне величины осевых усилий и внешнего давления неодинаковы по длине колонны. Осевые усилия достигают наибольшего значения у самой верхней трубы в момент спуска. Наибольшие внешние силы, приводящие к смятию, проявляются у самых нижних труб колонны при снижении уровня жидкости в колонне в процессе эксплуатации скважины. Кроме того, на нижние трубы в фильтровой зоне скважины могут действовать и пластовые давления, которые достигают значительных величин в процессе эксплуатации скважины.
Кроме основных усилий смятия и растяжения, действующих на колонну, в обсадных трубах возникают также дополнительные напряжения. Они возникают тогда, когда приходится расхаживать колонну при ее прихватах, резком торможении во время спуска, изгибе колонны и т.д. Эти напряжения, возникающие в результате указанных явлений, в некоторой степени компенсируются запасом прочности обсадных труб.
При подборе отдельных секций обсадных колонн нужно принимать следующие запасы прочности:
1.в расчетах технических колонн на страгивающую нагрузку – 1,3;
2.при расчете эксплуатационных колонн на страгивающую нагрузку – 1,15-1,20;
3.при расчете эксплуатационных колонн на смятие:
а).запас прочности для интервала высоты подъема цементного раствора – 1,3;
б).запас прочности выше интервала подъема цементного раствора – 1,15.
Запас прочности на страгивающую нагрузку устья скважины составляет[4]:
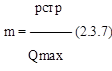
где, pстр – страгивающая нагрузка, кН;
Qmax – вес колонны обсадных труб, кН.
Затрубное сминающее давление, создаваемое столбом глинистого раствора на нижнюю трубу[4]:
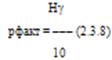
где, Н – глубина, на которую опускается обсадная труба, м;
γ – удельный вес бурового раствора, кг/м³
Кондуктор Ø 324мм рфакт1 = 1020·1150/10 = 11,73МПа
Пром. колонна Ø 245мм рфакт2 = 2450·1460/10 = 35,77МПа
Экс. колонна Ø 140мм рфакт3 = 3025·2130/10 = 64,43МПа
При запасе прочности на сжатие равным m, нужно устанавливать трубы, которые могут выдержать внешнее сминающее давление, равное[4]:
pсм = pфакт m (2.3.9)
Кондуктор Ø 324мм рсм1 = 11,73·1,3 = 15,2МПа
Пром. колонна Ø 245мм рсм2 = 35,77·1,3 = 46,5МПа
Экс. колонна Ø 140мм рсм3 = 64,43·1,15 = 74,1МПа
Результаты вычислений занесем в таблицу 2.6.
Таблица 2.6 Данные диаметров колонн и типы резьб различных марок стали
диаметр
колонны
мм
|
тип резь-
бового
соедин.
|
марка
стали
|
толщина
стенки,
мм
|
Вес, кН |
длина
колонны
|
Давление, МПа |
1 пог. м
трубы
|
общий |
pфакт |
pсм |
324
245
140
|
ОТТМ
ОТТГ
VAМ
|
Д
М
N-80
|
9,5
12,0
10,54
|
0,747
0,708
0,307
|
762
1735
929
|
1020
2450
3025
|
11,73
35,77
64,43
|
15,2
46,5
74,1
|
Фирмой "Валурек" (Франция) разработана высокогерметичное соединение VАМ. Соединение обеспечивает газогерметичность при больших растягивающих и изгибающих усилиях.
2.3.2 Буровое оборудование
2.3.2.1 Выбор бурового станка
Буровые установки – это комплексные системы, включающие все основные и вспомогательные агрегаты и механизмы, которые необходимы для строительства скважин.
Буровую установку выбирают по ее допустимой максимальной грузоподъемности, обуславливающей с некоторым запасом веса в воздухе наиболее тяжелых бурильной и обсадной колонн.
Для принятой по грузоподъемности и условной глубине бурения буровой установки в зависимости от региональных условий, связанных со степенью обустройства (дороги, линии электропередач, водоснабжение и др.) и климатической зоной, выбирают тип привода, схему монтажа и транспортирования, а также учитывают необходимость комплектования отопительными установками, дополнительными агрегатами и оборудованием.
Буровые установки делятся на две категории:
· для бурения глубоких эксплуатационных и разведочных скважин;
· для бурения неглубоких структурных и поисковых скважин.
Каждая категория буровой установки имеет несколько классов, которые обеспечивают наибольшую эффективность бурения скважин определенной глубины и конструкции. Каждой буровой установкой, при определенной мощности ее двигателей, максимально допустимой нагрузке на крюке можно пробурить скважины различной глубины и конструкции. Для сравнительной оценки мощности и класса буровой установки,для глубокого бурения принимают допустимую нагрузку на крюке и номинальную глубину скважины конечного диаметра 190,5мм, которые могут быть достигнуты при использовании бурильной колонны с бурильными трубами диаметром 127мм и массой 1м труб 31,9кг. При работе с бурильными трубами других диаметров и массы глубина бурения этой же буровой установкой может значительно отличаться от ее условной глубины.
Буровые установки для эксплуатационного и глубокого разведочного бурения стандартизованы. ГОСТ 16293—82 (СТ СЭВ 2446—80) предусматривает 11 классов буровых установок для бурения скважин глубиной 1250—12500 м и более.
Вид буровой установки для одного и того же класса определяется рядом факторов:
·условиями бурения (равнина, горы, леса, болота, море, температура окружающего воздуха и ее колебания, сила ветра и др.);
·целью бурения (разведочное или эксплуатационное);
·типом скважины (вертикальная или наклонная);
·способом бурения (роторным или забойным двигателями);
·технологией бурения (гидравлическая мощность на забое, типы и свойства бурового раствора, метод спуска и подъема колонн);
·геологическими условиями бурения (характер буримых пород, возможные осложнения, аномальное пластовое давление, температура на глубине, степень агрессивности подземных вод).
Таблица 2.7 Вес обсадных колонн различного назначения
Наименование
колонны
|
Вес колонны в воздухе, в кН |
кондуктор |
промеж. колонна |
экспл. колонна |
Ø 324 мм |
Ø 245 мм |
Ø 140 мм |
Обсадная колонна
Бурильная колонна (при бурении под данную обсадную)
|
762,0
534
|
1735,0
974
|
929,0
1163
|
В соответствии с п.2.5.6.ПБ НГП (РД-08-624-03) максимальный вес буровой колонны не должен превышать 0,6 и обсадной колонны - 0,9 от грузоподъемности буровой установки.
Максимальный вес обсадной колонны, кН: Gокмакс = 1735.0
Максимальный вес бурильной колонны, кН: Gбк макс = 1163.0
С учетом расчетных значений веса колонн, максимальная нагрузка на крюке должна быть:
– для обсадной колонны, кН Qмин = Gокмакс/0,9 = 1927,8
– для буровой колонны, кН Qмин = Gбкмакс/0,6 = 1938.3
Таким образом, грузоподъемность буровой установки должна быть не менее 1938.3 кН.
В соответствии с ожидаемой максимальной нагрузкой на крюке, экономически выгодным для данного района видом привода и наличием парка буровых установок в филиале "Кубаньбургаз", для строительства скважины принимается буровая установка "БУ3200/200ЭУК-2М"
с допускаемой нагрузкой на крюке 2000 кН при оснастке 5x6, с техническими характеристиками:
Таблица 2.8 Характеристика буровой установки "БУ3200/200ЭУК-2М"
Допустимая нагрузка на крюке, кН |
2000 |
Условная глубина бурения, м |
3200 |
Скорость подъема крюка при расхаживании колонны, м/с |
0,2±0,05 |
Скорость подъема элеватора (без нагрузки), м/с, не менее |
1,5 |
Расч. мощность на входном валу подъемного агрегата, кВт |
670 |
Диаметр отверстия в столе ротора, мм |
700 |
Расчетная мощность привода ротора, кВт |
370 |
Мощность бурового насоса, кВт |
950 |
Вид привода |
Э |
Высота основания (отметка пола буровой), м |
7,2 |
Просвет для установки стволовой части превенторов, м |
5,7 |
2.3.2.2 Выбор насосной установки
В установках глубокого бурения применяются поршневые насосы марок У8-4, У8-5М, Б14-200, БРН-1, УНБ-600А (У8-6МА2) и другие, имеющие подачу 15-50 л/с при давлении нагнетания 10-60 МПа. Подача насоса определяется по формуле[4]:
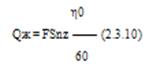
где η0 = 0,85 – 0,95 – объемный к.п.д. насоса, учитывающий утечки жидкости, наличие в ней газа и инерцию срабатывания клапанов,
F – площадь, определяемая по внутреннему диаметру цилиндровой втулки,
S = 2R – ход поршня или плунжера,
R – радиус вращения кривошипа,
n – частота вращения кривошипа,
z – число цилиндров,
f – площадь поперечного сечения штока.
Для регулирования расхода жидкости, нагнетаемой в бурильную колонну, широко применяется метод изменения частоты вращения кривошипа (коренной вал насоса) при помощи коробки передач или путем замены цилиндровых втулок, имеющих разные внутреннии диаметры. Исход жидкости часто регулируется путем сброса части ее на слив в приемный умпф.
Для буровой установки БУ 3200/200 ЭУК-2М в комплект входят два поршневых насоса УНБ-600А (У8-6МА2) (установка насосная блочная), с основными параметрами см. таблцу 2.9 :
Таблица 2.9
Тип
насоса
|
Даметр
втулки
мм
|
Предельное
давление
кгс/см2
|
Идеальная подача (л/с) при частоте двойных ходов, мин-1
|
Допустимое рабочее давление, кг/см2 |
65 |
60 |
50 |
40 |
30 |
20 |
10 |
УНБ-600А |
200 |
100 |
51,9 |
47,9 |
39,9 |
31,9 |
23,9 |
16,0 |
8,0 |
80 |
(У8-6МА2) |
190 |
115 |
45,7 |
42,2 |
35,2 |
27,7 |
21,1 |
14,1 |
7,0 |
92 |
180 |
125 |
42,0 |
38,8 |
32,3 |
25,8 |
19,4 |
12,9 |
6,5 |
100 |
170 |
145 |
36,0 |
33,2 |
27,7 |
22,2 |
16,6 |
11,0 |
5,5 |
116 |
160 |
165 |
31,5 |
29,1 |
24,2 |
19,4 |
14,5 |
9,7 |
4,8 |
132 |
150 |
190 |
27,5 |
25,4 |
21,2 |
16,9 |
12,7 |
8,6 |
4,3 |
152 |
140 |
225 |
23,3 |
21,5 |
17,9 |
14,3 |
10,7 |
7,2 |
3,6 |
180 |
130 |
250 |
19,7 |
18,9 |
15,2 |
12,1 |
9,1 |
6,1 |
3,0 |
200 |
Буровой насос для промывки скважины в конкретных геологических
условиях выбирается по технологически необходимому количеству промывочной жидкости и развиваемому при этом давлению для преодоления потерь напора в элементах циркуляционной системы буровой.
Количество необходимой промывочной жидкости при бурении под эксплуатационную колонну составляет 12 л/с. Определим теперь потери давления в циркуляционной системе, зная которые можно выбрать наиболее рациональную компоновку бурильного инструмента, обоснованно подобрать буровые насосы и полнее использовать их потенциальные возможности.
Потери напора, кГс/см2
, в циркуляционной системе буровой при роторном бурении определяются по формуле:
Р∑
= Рм
+Рб.т
+Ркп
+Р
д
(
2.3.11.)
где Рм
- потери напора при движении бурового раствора в наземных трубопроводах от насосной части до колонны бурильных труб, включая стояк в буровой, буровой шланг, а также вертлюг и ведущую трубу (потери шпора в наружной обвязке буровой - манифольде);
Рб.т — потери напора при движении бурового раствора в бурильных трубах и замковых соединениях (потери давления зависят от глубины скважины);
Ркп
. - потери напора при движении бурового раствора в затрубном кольцевом пространстве скважины (потери давления зависят от глубины скважины);
Рд
- потери напора при движении бурового раствора через промывочные отверстия бурового долота;
Рм
, Рд
- не зависят от глубины скважины, а Рбт
.. и Ркп
. увеличиваются с глубиной скважины.
При циркуляции очистного агента потери напора, кГс/см2
, различны при прокачке воды и глинистого раствора и зависят от их свойств и расхода.
Рм
= 82,6*λ*
L
э
*γ*
Q
2
/
d
5
, (
2.3.12.)
где λ- безразмерный коэффициент гидравлических сопротивлений при движении в трубах;
Q - расход бурового раствора, л/с;
γ - удельный вес раствора, г/см3
;
d-
внутренний диаметр бурильных труб, см;
Lэ - эквивалентная длина наземных трубопроводов, которая определяется по формуле:
L
э
=
L
н
*(
d
/
d
н
)5
+
L
с
*(
d
/
d
с
)5
+
L
ш
*(
d
/
d
ш
)5
+
L
в
*(
d
/
d
в
)5
+
+
L
в.тр
*(
d
/
d
в.тр)
5
+
L
э.ф
*(
d
/
d
э.ф)
5
(2.3.13.)
где dн, Lн - внутренний диаметр и длина нагнетательной линии, идущей от буровых насосов к стояку;
dс, Lс - внутренний диаметр и длина стояка в буровой;
dш, Lш - внутренний диаметр и длина бурового шланга;
dв, Lв - внутренний диаметр ствола вертлюга и его длина;
dэ.ф, Lэ.ф - диаметр и эквивалентная длина фильтра, устанавливаемого под ведущей трубой;
dв.тр, Lв.тр- внутренний диаметр и длина ведущей трубы.
Lэ=30*(0,107/0,114)5
+15*(0,107/0,114)5
+15*(0,107/0,09)5
+2,5*(0,107/0,09)5
+ +16*(0,107/0,1)5
+2*(0,107/0,114)5
= 96,85 м.
Рм
= 82,6*0,026*96,85*2,13*(12)2
/(10,7)5
= 0.5 кГс/см2
.
Рбт
. = 82,6*λ*γ*Q2
*(1+lэ/l)*Lб
/d5
,
где Lб - длина бурильной колонны, м;
lЭ
- эквивалентная длина замковых соединений, м;
l - расстояние между замковыми соединениями, м.
Рбт
. = 82,6*0,026* 2,13*(12)2
*(1+3,5/11)*3025/(10,7)5
= 18.5 кГс/см2
.
Ркп
= 82,6* λ1*γ*Q2
*L/[(ДС
– dн
)3
*(Дс
+ dн
)2
],
где λ1, - коэффициент гидравлических сопротивлений при движении бурового раствора в кольцевом (затрубном) пространстве;
Дс
- диаметр скважины (долота), см;
dн
- наружный диаметр бурильных труб, см.
Потери давления от замковых соединений в кольцевом пространстве составляют небольшую величину, поэтому ею обычно пренебрегают.
Ркп
= 82,6*0,027* 2,13*122
*3025/[(19.05-12,7)3
*(19.05+12,7)2
]= 8 кГс/см2
.
Потери напора, кГс/см2
, в долоте зависят от конфигурации промывочных отверстий, от количества и площади их сечения, расхода очистного агента (бурового раствора).
Р
д
= С*γ*
Q
2
, ( 2.3.14.)
где С — коэффициент, характеризующий потери напора в промывочных отверстиях долота, который можно вычислить по формуле:
С = 0,51/(μ2
*
f
0
2
)
(2.3.15.)
где μ - коэффициент расхода,
f0 - суммарная площадь сечений промывочных отверстий, см2
.
С = 0,51/(0,652
*13,052
) = 7*10-3
Рд
= 7*10-3
*2,13*122
= 2,15 кГс/см2
.
Вычислим суммарные потери напора при бурении
Р∑
= Рм
+Рб.т
+Ркп
+Р
д
под эксплуатационную колонну:
Р∑
= 0.5+18.5+8+2,15 = 29.15 кГс/см2
.
под техническую колонну:
Р∑
= 127.7кГс/см2
.
под кондуктор:
Р∑
= 120.4 кГс/см2
.
Таким образом, технологически необходимое количество (расход) промывочной жидкости для обеспечения своевременного и бесперебойного выноса шлама из забоя по затрубному пространству и очистки ствола скважины с учетом потерь давления, обеспечит нам насос УНБ-600А.
2.3.2.3 Выбор силовой установки
Под силовым приводом понимается комплексное устройство, осуществляющее преобразование электрической энергии или энергии топлива в механическую и обеспечивающее управление преобразованной механической энергии:
Основными элементами силового привода являются двигатель, передаточные устройства (механизмы) от него к исполнительному механизму и устройства системы управления.
Привод основных исполнительных механизмов буровой установки (лебедки, буровых насосов, ротора) называется главным приводом. В зависимости от вида двигателя и типа передачи он может быть электрическим, дизельным, дизель-гидравлическим, дизель-электрическим и газотурбинным. Наиболее широко применяют в современных буровых установках электрический, дизельный, дизель-гидравлический, дизель-электрический приводы.
Основными преимуществами электрического привода переменного тока являются его относительная простота в монтаже и эксплуатации, высокая надежность, экономичность. В то же время буровые установки с этим типом привода можно использовать лишь в электрифицированных районах.
Дизельный привод применяют в районах, не обеспеченных электроэнергией необходимой мощности. Важными преимуществами двигателей внутреннего сгорания (ДВС) при использовании их в качестве привода являются: высокий к. п. д., небольшой расход топлива и воды и небольшая масса на 1 кВт мощности. Основной недостаток ДВС - отсутствие реверса, поэтому необходимо специальное устройство для получения обратного хода. ДВС типа дизель допускают перегрузку не выше 20%. Для их обслуживания требуется квалифицированный обслуживающий персонал.
Дизель-гидравлический привод состоит из ДВС и турбопередачи. Турбопередача – это промежуточный механизм, встроенный обычно между дизелем и трансмиссией. Применение турбопередачи обеспечивает: плавный подъем груза на крюке; работу двигателя, если нагрузка на крюке больше той, которую сможет преодолеть ДВС, в этом случае двигатель будет работать при пониженных, но вполне устойчивых оборотах; большую долговечность передачи.
Наибольшим преимуществом обладает привод от электродвигателей постоянного тока, в конструкции которого отсутствуют громоздкие коробки перемены передач, сложные соединительные части и т. п. Электрический привод постоянного тока имеет удобное управление, может плавно изменять режим работы лебедки или ротора в широком диапазоне.
Дизель-электрический привод состоит из приводного электродвигателя, связанного с исполнительным механизмом; генератора, питающего этот электродвигатель; дизеля, приводящего во вращение генератор.
Силовые приводы подразделяют на индивидуальный и групповой. Индивидуальным называется такой привод, который приводит в действие один исполнительный механизм или отдельные его части. Групповым называется такой привод, который приводит в действие два и более исполнительных механизма.
Технология бурения нефтяных и газовых скважин имеет свои особенности и предъявляет определенные требования к силовому приводу.
В процессе бурения основная часть мощности потребляется буровыми насосами и ротором, а в процессе спуско-подъемных операций - лебедкой и компрессором. Работа насосов в процессе бурения характеризуется постоянством нагрузки на силовой привод. Во время спуско-подъемных операций привод имеет резко переменную нагрузку - от нулевой (холостого хода двигателей) до максимальной. При подъеме инструмента из скважины необходимо обеспечить в начале подъема каждой свечи плавное включение лебедки и постепенное увеличение скорости подъема, так как резкое включение и мгновенное увеличение скорости могут привести к разрыву талевого каната или поломке оборудования. При ликвидации аварий в скважине привод часто работает с резко переменными нагрузками, превышающими расчетные.
К силовому приводу буровых установок предъявляются следующие требования: соответствие мощности условиям работы и сполнительных механизмов, гибкость характеристики, достаточная надежность и экономичность.
Гибкость характеристики определяется способностью привода автоматически или при участии оператора быстро приспосабливаться в процессе работы к изменениям нагрузок и скоростей работы исполнительных механизмов при условии рационального использования мощности.
Нагрузки и скорости буровой лебедки и ротора в процессе работы могут изменяться в больших пределах (1:4 – 1:10). Двигатели не обладают такой гибкой характеристикой, поэтому в приводах современных буровых установок применяют устройства искусственной приспосабливаемости, т. е. между двигателем и исполнительным механизмом устанавливают промежуточные передачи.
2.3.2.4 Выбор буровой вышки и талевой системы
Буровая вышка предназначена для подъема и спуска бурильной колонны и обсадных труб в скважину, удержания бурильной колонны на весу во время бурения, а также для размещения в ней талевой системы, бурильных труб и части оборудования, необходимого для осуществления процесса бурения.
В настоящее время при бурении на нефть и газ используют металлические вышки башенного и мачтового типов. Из вышек мачтового типа применяются А-образные.
Ее выбор осуществляется по высоте Н, м, и по грузоподъемности Q.
Определим высоту вышки (Н, м) по формуле:
Н =
k
*
L
св
, (
2.3.16.)
где k- коэффициент, предупреждающий затягивание бурового снаряда в кронблок при его переподъеме (обычно k = 1,2-1,5);
Lсв
- длина свечи, зависящая от глубины скважины, м.
Принимаем k = 1,5; Lсв
= 24 м.
Н= 1,5*24 = 40 м.
Таким образом, вышка ВМУ-45*200У, входящая в комплект выбранной буровой установки, вполне подходит для выполнения проектируемых работ.
Талевая (полиспастовая) система буровых установок предназначена для преобразования вращательного движения барабана лебедки в поступательное (вертикальное) перемещение крюка и уменьшения нагрузки на ветви каната.
Через канатные шкивы кронблока и талевого блока в определенном порядке пропускается стальной талевый канат, один конец которого крепится неподвижно, другой конец, называемый ходовым (ведущим), крепится к барабану лебедки.
По грузоподъемности и числу ветвей каната в оснастке талевые системы разделяют на различные типоразмеры. В буровых установках грузоподъемностью 50 – 75т используют талевую систему с числом шкивов 2Х3 и 3Х4; в установках грузоподъемностью 100 - 300т применяют число шкивов 3Х4, 4Х5, 5Х6 и 6Х7. В обозначении системы оснастки первая цифра показывает число канатных шкивов талевого блока, а вторая цифра число канатных шкивов кронблока.
Произведем расчет оснастки и выбор талевого каната.
Вычислим количество рабочих ветвей по формуле:
m
=
Q
кр
/Р
л
*η
m
, (
2.3.17.)
где Qкр - вес бурового снаряда, Н;
Рл
- грузоподъемность лебедки станка, Н;
ηm - КПД талевой системы, равный 0,8 - 0,9.
Так как наибольший вес (173,5 т) будет иметь тех. колонна диаметром 245мм , то производить расчет будем только для этой колонны:
m = 1735000/(200000*0,9) =10 ветвей.
Общее количество ветвей каната при симметричной системе равно:
m0
= m+2
m0
= 10+2=12.
Следовательно, будет применяться оснастка 5x6.
Длина талевого каната в оснастке Lо
c
. зависит от числа струн m в ней и полезной высоты вышки hn
.
L
о
c
=
(
m
+2)*
hn
+
l
3
, (
2.3.18.)
где 13
= 30 м - длина каната, наматываемого на барабан.
Lо
c
= (12+2)*40+30 = 590 м.
Тогда вес каната
G
к
=
L
о
c
*
q
к
,
(2.3.19.)
где qк
- вес 1 м каната.
Gк
= 590*33,8 = 19942 Н = 19,94 кН.
Определим наибольшую статическую нагрузку на подвижные струны каната талевой системы:
Рт с
=
L
*
q
+
l
убт
*
q
убт
+
G
тс
(
2.3.20.)
где L - длина бурильных труб, м;
q - вес 1 м бурильных труб, Н;
lубт
- длина УБТ, м;
qубт
- вес 1 м УБТ, Н;
Gтс
- вес талевого блока, каната и крюка, Н. Рассчитаем Gтс
:
G
тс
=
G
тб
+
G
каната
+
G
крюка
(
2.3.21.)
Gтс
= 67000+19942+35000 = 121942 Н = 121,94 кН.
Для снаряда при бурении под колонну диаметром 324 мм:
L = 922 м, q = 319Н. lубт
= 98м, qубт
= 1.56 кН.
Ртс
= 922*319+ 98*1560+121942 = 568940= 568.94 кН.
Статическая нагрузка на 1 струну:
Р = Ртс
/ m,
где m - число ветвей талевой системы.
Р =568.94/12 = 47.41 кН.
Для снаряда при бурении под колонну диаметром 245 мм:
L = 2364.5, q = 319Н, lубт
= 85.5м, qубт
= 1.56 кН;
Ртс
= 2364.5*319+85.5*1560 + 121942 = 1009608Н = 1009.608 кН.
Статическая нагрузка на 1 струну:
Р = 1009.608 /12 = 84.13 кН.
Для снаряда при бурении под колонну диаметром 140 мм:
L = 2936 м, q = 319 Н, lубт
= 89 м, qубт
= 1,56 кН.
Ртс
= 2936*319+89*1560+ 121942 = 1197366 Н= 1197.366 кН.
Статическая нагрузка на 1 струну:
Р = 1197.366/12 = 99.78 кН.
Для тех. колонны диаметром 245мм:
Lк
= 2450 м, q = 708 Н,
Ртс
= 2450*708+ 121942 = 1856542Н= 1856.542кН.
Статическая нагрузка на 1 струну:
Р = 1856.542/12 = 154.7 кН.
Учитывая вычисленные статические нагрузки, выбираем стальной талевый канат правой крестовой свивки типа ЛК-РО конструкции 6x31+1 м. с. диаметром 32 мм (по ГОСТ 16853-88).
2.4
ТЕХНОЛОГИЯ БУРЕНИЯ
Основу технико-технологических решений при бурении нефтяных и газовых скважин составляет технический проект, содержание которого определяет все основные технические решения, номенклатуру и количество технических средств для реализации выбранной технологии на всех этапах строительства скважин. Эффективность технологических решений определяется степенью научной обоснованности принимаемых решений и достоверностью исходной информации. При этом большую роль играет накопленный в регионах опыт, так как проектирование многих технологических процессов требует постоянного уточнения математических моделей и логических принципов выбора технологических решений в зависимости от конкретизации геолого-геофизических условий бурения.
2.4.1 Выбор породоразрушающего инструмента
Выбор типа породоразрушающего инструмента базируется на информации о физико-механических свойствах пород и литологическом строении разреза пород и, во многом, зависит от конкретных региональных условий.
Долото является рабочим инструментом, разрушающим породу и осуществляющим углубление забоя в процессе бурения скважины.
Эффективность разрушения разнообразных по своим физико-механическим свойствам горных пород может быть достигнута при различном действии на них зубьев долота. Одни породы разрушаются от ударов или в результате дробления, другие – под действием сдвига или резания, третьи – вследствие комбинации этих действий.
Для однородных твердых пород необходимы долота с большим дробящим действием; для мягких однородных пород – долота с большим сдвигающе-скалывающим действием и высокими острыми зубьями, а для твердых пород, перемежающихся мягкими пропластками, следует применять долота не только с дробящим действием, но и сдвигающим.
По назначению буровые долота подразделяются на три вида:
· долота сплошного бурения – для углубления забоя по всей площади;
· колонковые долота – для углубления забоя по кольцу с оставлением в центре нервыбуренного столбика (керна) породы, который в последующем извлекается на поверхность;
· долота специального назначения, используемые для различных вспомогательных работ: разбуривания цементного камня в колонне, забуривания (зарезки) второго наклонного ствола, исправления кривизны скважины, ловильных работ, расширения отдельных интервалов ствола скважины и т.д.
По характеру разрушения породы все буровые долота классифицируются следующим образом.
·долота режуще-скалывающего действия, разрушающие по роду лопастями, наклоненными в сторону вращения долота. Предназначены они для разбуривания мягких пород.
·долота дробяще-скалывающего действия, разрушающие по роду зубьями или штырями, расположенными на шарошках, которые вращаются вокруг своей оси и вокруг оси долота. При вращении долота наряду с дробящим действием зубья (штыри) шарошек, проскальзывая по забою скважины, скалывают (срезают) породу, за счет чего повышается эффективность разрушения пород. Следует отметить, что выпускаются буровые долота и бурильные головки только дробящего действия. При работе этими долотами породы разрушаются в результате динамического воздействия (ударов) зубьев шарошек по забою скважины. Перечисленные долота и бурильные головки предназначены для разбуривания неабразивных и абразивных средней твердости, твердых, крепких и очень крепких пород.
·долота истирающе-режущего действия, разрушающие породу алмазными зернами или твердосплавными штырями, располагающиеся в торцовой части долота или в кромках лопастей долота. Долота с алмазными зернами и твердосплавными штырями в торцевой части применяются для бурения неабразивных пород средней твердости и твердых; долота лопастные армированные алмазными зернами или твердосплавными штырями — для разбуривания перемежающихся по твердости абразивных и неабразивных пород.
Долота для сплошного бурения и бурильные головки для колонкового бурения предназначены для углубления скважины. Выпускаются они различных типов, что позволяет подбирать нужное долото.
Наибольшее распространение в практике бурения нефтяных и газовых скважин получили шарошечные долота дробяще-скалывающего действия с твердосплавным или стальным вооружением.
Три лапы сваривают между собой. На верхнем конце конструкции нарезана замковая присоединительная резьба. Каждая лапа в нижней части завершается цапфой, на которой проточены беговые дорожки под шарики и ролики. На цапфе через систему подшипников устанавливается шарошка с беговыми дорожками. Тело шарошки оснащено фрезерованными стальными зубьями, размещенными по венцам. На торце со стороны присоединительной резьбы выбиваются шифр долота, его порядковый номер, год изготовления.
Шарошечные долота изготавливают как с центральной, так и с боковой системой промывки. На лапах долота с боковой гидромониторной системой промывки выполнены специальные утолщения – приливы с промывочными каналами и гнездами для установки гидромониторных насадок
При центральной промывке забоя лучше очищаются от шлама центр забоя и вершины шарошек, шлам беспрепятственно выносится в наддолотную зону. Однако при высокой скорости углубки забоя трудно подвести к долоту необходимую гидравлическую мощность, требуемую для качественной очистки забоя (перепад давления на долотах с центральной промывкой не превышает 0,5-1,5 МПа). Боковая гидромониторная промывка обеспечивает лучшую очистку наиболее зашламованной периферийной части забоя, позволяет подвести к долоту большую гидравлическую мощность (перепад давления на долотах с гидромониторной промывкой достигает 5-15 МПа). Однако мощные струи бурового раствора, выходящие из гидромониторных насадок экранируют транспортирование шлама через проемы между секциями долота, поэтому часть шлама циркулирует некоторое время в зоне действия шарошек и переизмельчается, а часть – транспортируется в зазорах между стенкой скважины и спинками лап. Поэтому зачастую переходят на ассиметричную систему промывки, заглушая одну или две гидромониторные насадки для повышения пропускной способности основных транспортных каналов долота.
По ГОСТ 20692 "Долота шарошечные" предусматривается выпуск долот диаметром 76-508мм трех разновидностей: одно- двух- и трех-шарошечных. Наибольший объем бурения нефтяных и газовых скважин приходится на трехшарошечные долота диаметрами 190,5; 215,9; 269,9; 295,3 мм.
По материалу вооружения шарошечные долота делятся на два класса:
1 класс – долота с фрезерованным стальным вооружением для бурения малоабразивных пород (М, МС, С, СТ, Т, ТК);
2 класс – долота со вставным твердосплавным вооружением для бурения абразивных пород (МЗ, МСЗ, СЗ, ТЗ, ТКЗ, К, ОК)
Условное обозначение (шифр) долота:
III – 215,9 С-ГНУ 2354, где III – трехшарошечное ;
215,9 – номинальный диаметр долота, мм;
С – тип долота (для бурения пород средней твердости);
Г – боковая гидромониторная промывка;
Н – опора для низкооборотного бурения на одном подшипнике скольжения;
У – опора маслонаполненная с уплотнительной манжетой;
2354 – заводской номер долота.
Типы и область применения шарошечных долот приведены в табл. 2.10.
Таблица 2.10 Типы и область применения шарошечных долот
Тип долота |
Рекомендуемые области применения долот |
М |
Самые мягкие, несцементированные, пластичные (наносы, мягкие и вязкие глины, сланцы, мягкие известняки) |
МЗ |
Мягкие, слабосцементированные, абразивные (песчаники, мергели) |
МС |
Мягкие, неабразивные, с пропластками пород средней твердости (мел с пропластками слабосцементированных песчаников, каменная соль с пропластками ангидритов, глинистые сланцы) |
МСЗ |
Мягкие, слабосцементированные, абразивные, с пропластками пород средней твердости (песчаноглинистые сланцы, плотные глины с пропластками песчаников) |
С |
Пластичные и хрупкопластичные неабразивные, средней твердости (плотные глины, глинистые сланцы, известняки средней твердости) |
СЗ |
Абразивные, средней твердости (песчаники, песчанистые сланцы) |
СТ |
Хрупкопластичные, средней твердости, с пропластками твердых пород (песчаники с пропластками гипса, известняки с пропластками гипса, ангидриты) |
Т |
Твердые, неабразивные (твердые известняки, доломиты, доломитизированные известняки) |
ТЗ |
Твердые, абразивные (окварцованные известняки и доломиты) |
ТК |
Твердые, с пропластками крепких (твердые известняки с пропластками мелкокристаллических известняков и доломитов) |
ТКЗ |
Абразивные, твердые, с пропластками крепких (окремнелые аргиллиты, твердые известняки и доломиты, мелкозернистые сильносцементированные песчаники) |
К |
Крепкие, абразивные (окремнелые мелкокристаллические известняки, доломиты, кварциты) |
ОК |
Очень крепкие, абразивные (граниты, квациты, диабазы) |
Геологический разрез Северо-Прибрежной площади в основном представлен следующими породами: песчаник, глины, доломиты, алевролиты.
После изучения залегания пород Северо-Прибрежной площади выбираем под бурение каждой колонны свой тип долота:
·под кондуктор Ø 324мм ІІІ 393,7 М-ГВ
·под промежуточную колонну Ø 245мм ІІІ 295,3 RХ+С
·под эксплуатационную колонну Ø 140мм ІІІ 190,5 МС-ГАУ
2.4.2Расчет технологического режима бурения
Способ бурения скважины выбирается с учетом ряда факторов, основными из которых являются геологические условия бурения; глубины и диаметры скважины; назначение скважины; рельеф местности, условия транспортировки грузов, удаленность точки бурения от производственной базы, а также масштабы буровых работ и степень их концентрации. Наиболее сложным и ответственным разделом технологии проводки скважины является режим бурения, который определяется в зависимости от гидрогеологических условий, физико-механических свойств проходимых пород и типа применяемого оборудования и инструмента.
При проектировании технологического процесса проводки скважины для отдельных интервалов бурения устанавливается соответствующий режим.
Под режимом бурения понимается совокупность основных факторов, определяющих скоростные и качественные показатели, оказывающие непосредственное влияние на эффективность разрушения породы. К таким факторам относятся тип долота, осевая нагрузка на долото, скорость вращения ротора, количество и качество подаваемой в скважину промывочной жидкости. Правильное сочетание элементов режима бурения определяется в зависимости от крепости проходимых пород, профиля зубьев и характера их расположения у шарошечных долот, диаметра долота и бурильного инструмента, глубины скважины, а также типа, количества и состояния бурового оборудования.
Под оптимальным или рациональном режимом бурения понимается совокупность параметров, обеспечивающих наилучшие технико-экономические показатели как качественные, так и количественные. К качественным показателям следует относить величину отклонения ствола пробуренной скважины от вертикали, степень глинизации коллектора; к количественным – скорость проходки, величину долбления долота и др.
Существующие в настоящее время режимы бурения для скважины установлены практически; поинтервально для каждого горизонта пород режимы бурения указаны в геологическом наряде.
2.4.3Расчет осевой нагрузки
Осевую нагрузку на долото следует устанавливать, изменяя скорость движения, т.е. подачи на забой бурильного инструмента. Нагрузка на долото должна создаваться весом бурильных и утяжеленных труб. Увеличение осевой нагрузки способствует росту скорости проходки, которая может изменяться в зависимости от крепости и других характеристик проходимых пород.
На буровом станке установлен гидравлический индикатор веса (ГИВ-6-2М1), который показывает вес свободно подвешенного инструмента; нагрузка определяется как разность первоначального веса инструмента и веса инструмента, частично поставленного на забой. По диаграмме индикатора веса можно проанализировать время, затраченное на бурение и другие вспомогательные операции.
Осевая нагрузка на долото создается за счет применения утяжеленных бурильных труб. Длина утяжеленных бурильных труб (УБТ) подсчитывается таким образом, чтобы 75% их общего веса создавали нагрузку на долото, а 25% их веса создавали силу, растягивающую колонну бурильных труб. Эта закономерность приемлема при соотношении диаметров бурильных труб и долота 1:2. . Осевую нагрузку на долото с учетом показателей механических свойств горных пород и конструктивных данных о площади контакта рабочих элементов долота с забоем определим по формуле[4]:
РД
= aрFk
(2.4.1)
где, a - эмпирический коэффициент, учитывающий влияние забойных условий на изменение твердости (a = 0,3-1,59);
р – твердость породы, определяемая по методике Л.А.Шрейнера, Па;
Fk
– площадь контакта зубьев долота с забоем в мм2
, определяемая по формуле В.С.Федо рова
Fk
= *hd (2.4.2)
где, Д – диаметр долота, мм,
h =0,95 - коэффициент перекрытия,
d =1мм - притупление зубьев долота.
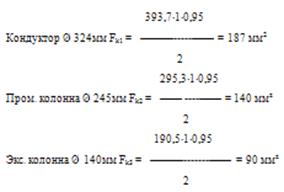
Отсюда находим максимальную осевую нагрузку на долото под каждую колонну:
Кондуктор Ø 324мм РД1 = 104,05 кН
Пром. колонна Ø 245мм РД2 = 83.27 кН
Экс. колонна Ø 140мм РД3 = 81.21 кН
По существующим нормам максимальная допустимая нагрузка на трехшарошечное долото находится в рекомендуемых пределах.
2.4.4 Расчет частоты вращения
Скважины можно бурить при двух режимах:
1. большой скорости вращения ротора и малой осевой нагрузки на долото;
2. небольшой скорости вращения ротора и повышенной осевой нагрузкой.
Скорость вращения ротора и осевая нагрузка на долото прямо пропорциональны механической скорости проходки, однако это положение справедливо только для пород средней твердости. При бурении в твердых породах осевую нагрузку на долото нужно увеличивать, а скорость вращения ротора снижать.
Скорость вращения ротора снижается при увеличении диаметра долота, уменьшении диаметра бурильных труб, увеличении абразивности проходимых пород, при переходе из пласта меньшей твердости в пласт большей твердости, а также при бурении чередующихся пластов небольшой мощности. В связи с тем, что большая скорость вращения ротора вызывает значительные инерционные напряжения, для каждого диаметра бурильного инструмента на основании расчета устанавливается допустимая скорость вращения ротора, которая определяется по формуле[4]:
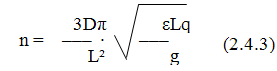
где D – диаметр бурильных труб, мм;
n – допустимая скорость вращения ротора;
L – длина вращающихся бурильных труб, м;
ε = 2,1·10 кг/см² – модуль упругости;
g = 9,8 м/сек² – ускорение силы тяжести;
q – вес 1 м бурильных труб, кг.
Находим скорость вращения ротора при бурении под каждую колонну (диаметр бурильных труб – 127мм, вес 1м бурильных труб – 31.9кг, длина L1 = 1020м L2 = 2450м L3 = 3025м):
Кондуктор Ø 324мм n1 = 80об/мин II – скорость вращения
Пром. колонна Ø 245мм n2 = 100об/мин III – скорость вращения
Экс. колонна Ø 140мм n3 = 90об/мин III – скорость вращения
2.4.5 Расчет производительности насосов для бурения под каждую обсадную колонну
Производительность насосов определяем по формуле[4]:
Q = 0,785(D²сквк - d²бт)V
где D – диаметр скважины;
к = 1,1-1,12 – коэффициент кавернозности;
d – диаметр бурильной трубы;
V = 0,5-0,8м/с – скорость восходящего потока.
Отсюда для бурения под каждую колонну получаем:
Кондуктор Ø 324 Q = 0,785(0,155∙1,1 – 0,02)0,5 = 0,059м³/с = 59 л/с
Пром. колонна Ø 245 Q = 0,785(0,087∙1,1 – 0,02)0,6 = 0,036м³/с = 36 л/с
Экс. колонна Ø 140 Q = 0,785(0,036∙1,12 – 0,02)0,8 = 0,012м³/с =12 л/с
Исходя из вычисленных значений производительности выбираем необходимое количество насосов, диаметр втулок и количество двойных ходов:
Кондуктор Ø 324 Q = 59 л/с (2 насоса, Двт = 160мм, 65 х/мин)
Пром. колонна Ø 245 Q = 36 л/с (2 насоса, Двт = 130мм, 65 х/мин)
Экс. колонна Ø 140 Q = 12 л/с (1насос, Двт = 130мм, 50 х/мин)
2.4.6 Расчет количества и качества промывочной жидкости для бурения под каждую обсадную колонну
При бурении вращательным способом в скважине постоянно циркулирует поток жидкости, которая ранее рассматривалась только как средство для удаления продуктов разрушения (шлама). В настоящее время она воспринимается, как один из главных факторов обеспечивающих эффективность всего процесса бурения.
При проведении буровых работ циркулирующую в скважине жидкость принято называть - буровым раствором
или промывочной жидкостью.
Буровой раствор кроме удаления шлама должен выполнять другие, в равной степени важные функции, направленные на эффективное
, экономичное
, и безопасное
выполнение и завершение процесса бурения. По этой причине, состав буровых растворов и оценка его свойств становился темой большого объема научно-практических исследований и анализа.
В настоящее время в мировой практике наблюдается тенденция роста глубин бурения скважин, а как следствие, и увеличение опасности возникновения при этом различных осложнений. Кроме того, постоянно ужесточаются требования более полной и эффективной эксплуатации продуктивных пород. В этой связи буровой раствор должен иметь состав и свойства, которые обеспечивали бы возможность борьбы с большинством из возможных осложнений и не оказывали негативного воздействия на коллекторские свойства продуктивных горизонтов.
Выбор типа бурового раствора до настоящего времени не имеет формализованных правил и поэтому производится на основании анализа практики бурения и опыта инженеров по буровым растворам.
Основа выбора допустимых типов буровых растворов – соответствие их составов разбуриваемым породам на всем интервале бурения до спуска обсадной колонны.
Процедура выбора типа бурового раствора состоит из следующих операций: получение от геологической службы информации о разрезе скважины; идентификацию пород разреза; установление типов буровых растворов, которые могут быть использованы при разбуривании пород данного класса; определение оптимальной последовательности применения буровых растворов.
Разрез скважины разбивают на интервалы, для каждого из которых выбирают допустимые типы буровых растворов, причем на каждом интервале ими могут быть только растворы, применимые на всех вышележащих интервалах в пределах не обсаженной части скважины. Затем рассчитывают стоимость 1 м3
каждого раствора, допустимого на данном интервале.
На следующем этапе определяют объемы растворов, необходимые для бурения каждого интервала. На последнем этапе рассчитывают количество материалов и химических реагентов, необходимых для реализации выбранной последовательности буровых растворов с учетом затрат материалов на поддержание свойств раствора.
В результате по всем интервалам бурения должна быть получена следующая информация: наименование и компонентный состав бурового раствора, его необходимый объем и стоимость, расход материалов на поддержание свойств бурового раствора, степень его очистки.
Определяем количество бентонитовой глины и воды для приготовления 1м3
раствора по формуле[4]:
Gг
=rг
(rгр
-rв)
/ rг
-rв
(2.4.4)
где, rг
– плотность глины, т/м3
(rг
= 2¸2,7 т/м3
)
rв
– плотность воды, т/м3
Gг
= = 0,455 т/м3
Объем глины в 1м3
раствора составит[4]:
Vг
=Gг
/rг
(2.4.5)
Vг= 0,455/2,6 = 0,175 м3
/м3
Объем воды будет равен[4]:
Vв
= 1 – Vг
(2.4.6)
Vв = 1 – 0175 = 0,825 м3
/м3
Количество глины, потребной для приготовления 1м3
раствора с учетом влажности глины, определяем по формуле[4]:
Gг
= rг
(rгр
- rв
) / rг
- rв
(1-n + nrг
) (2.4.7)
где, n – влажность глины, доли единицы. Для практи ческих расчетов принимают n=0.05-0.1
Gг
= = 0,505 т/м3
Объем глины в 1м3
раствора составит
Vг
=0,505/2,6 = 0,194 м3
/м3
.
Объем количества бурового раствора для бурения под каждую колонну определяем по формуле[4]:
Vбр = LS
где L – длина ствола;
S – поперечное сечение ствола.
Кондуктор Ø 324мм Vбр1 = 1020 · 0,12 = 124м³
Пром. колнна Ø 245мм Vбр2 =(1020 · 0.08)+ 1430 · 0,07 = 180м³
Экс. колонна Ø 140мм Vбр3 = (2450 · 0,045) +575 · 0,03= 128м³
Химическая обработка растворов.
Химическую обработку глинистого раствора производят для снижения водоотдачи и уменьшения толщины глинистой корки, получения минимального значения статистического напряжения сдвига, понижения вязкости, лучшего закрепления неустойчивых пород.
Химическая обработка глинистого раствора обеспечивает получение растворов определенных качеств согласно геолого техническому наряду. Для обработки растворов применяются следующие химические реагенты: каустическая сода, кальцинированная сода, углещелочной реагент (УЩР), торфощелочной реагент (ТЩР), жидкое стекло, нефть, костный и кератиновый клей и др. Для утяжеления глинистых растворов применяют тонкомолотые минералы: гематит, магнетит, барит.
2.5
ЦЕМЕНТИРОВАНИЕ СКВАЖИНЫ
Разобщение пластов при существующей технологии крепления скважин - завершающий и наиболее ответственный этап, от качества выполнения которого в значительной степени зависит успешное строительство скважины. Под разобщением пластов понимается комплекс процессов и операций, проводимых для закачки тампонажного раствора в затрубное пространство (т.е. в пространство за обсадной колонной) с целью создания там надежной изоляции в виде плотного материала, образующегося со временем в результате отвердения тампонажного раствора. Поскольку в качестве тампонажного наиболее широко применяется цементный раствор, то и для обозначения работ по разобщению используется термин "цементирование".
Цементный камень за обсадной колонной должен быть достаточно прочным и непроницаемым, иметь хорошее сцепление (адгезию) с поверхностью обсадных труб и со стенками ствола скважины. Высокие требования к цементному камню обусловливаются многообразием его функций: плотное заполнение пространства между обсадной колонной и стенками ствола скважины; изоляция и разобщение продуктивных нефтегазоносных горизонтов и проницаемых пластов; предупреждение распространения нефти или газа в затрубном пространстве под влиянием высокого пластового давления; заякоривание обсадной колонны в массиве горных пород; защита обсадной колонны от коррозионного воздействия пластовых вод и некоторая разгрузка от внешнего давления.
Следует отметить, что роль и значение цементного камня остаются неизменными на протяжении всего срока использования скважины, поэтому к нему предъявляются требования высокой устойчивости против воздействия отрицательных факторов.
Существует несколько способов цементирования. Они различаются схемой подачи тампонажного раствора в затрубное пространство и особенностями используемых приспособлений. Возможны два варианта подачи тампонажного раствора в затрубное пространство:
·раствор, закачанный внутрь цементируемой обсадной колонны, проходит по ней до башмака и затем поступает в затрубное пространство, распространяясь снизу вверх (по аналогии с промывкой называется цементированием по прямой схеме);
·тампонажный раствор с поверхности подают в затрубное пространство, по которому он перемещается вниз (цементирование по обратной схеме).
В промышленных масштабах применяют способы цементирования по прямой схеме. Если через башмак обсадной колонны в затрубное пространство продавливают весь тампонажный раствор, способ называется одноступенчатым (одноцикловым) цементированием. Если обсадная колонна на разных уровнях оснащена дополнительными приспособлениями (заливочными муфтами), позволяющими подавать тампонажный раствор в затрубное пространство поинтервально на разной глубине, способ цементирования называется многоступенчатым (многоцикловым). Простейший и наиболее распространенный способ - цементирование в две ступени (двухступенчатое). Иногда возникает необходимость не допустить проникновения тампонажного раствора в нижнюю часть обсадной колонны, расположенную в интервале продуктивного пласта, тогда этот интервал в затрубном пространстве изолируется манжетой, установленной на обсадной колонне, и сам способ цементирования называется манжетным. Выделяются также способы цементирования потайных колонн и секций, поскольку тампонажный раствор в этом случае закачивают по бурильной колонне, на которой спускают секцию или потайную колонну.
Расчеты при цементировании скважины – важная часть проектирования заключительного этапа строительства скважины. Применительно к конкретным местным условиям проводится метод сплошного одноступенчатого цементирования обсадной колонны. Расчет этого цементирования включает:
·определение объема цементного раствора;
·установление количества сухого цемента (или смеси цемента с наполнителями), выбор типа цемента;
·определение необходимого количества воды и реагентов для затворения, определение объема продавочной жидкости;
·установление допустимого времени цементирования скважины;
·определение числа агрегатов и цементно-смесительных машин;
·определение возможного максимального давления в конце процесса цементирования.
Объем скважины соответствует объему цементного раствора[5]:
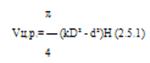
где k – коэффициент кавернозности;
H – высота подъема цементного раствора;
D – диаметр скважины;
d – диаметр обсадной колонны.
Коэффициент кавернозности составляет 1,10 – 1,12.
Кондуктор Ø 324мм: Vцр1 = (3,14/4)(1,1·0,394² – 0,324²)1020 = 52,6м³
Пром. колонна Ø 245мм: Vцр2 = (3,14/4)(1,1·0,2903² – 0,245²)2450 = 63м³
Экс. колонна Ø 140мм: Vцр3 = (3,14/4)(1,1·0,1905² – 0,140²)1175 = 23,5м³
Для приготовления 1м² цементного раствора требуется цемента[5]:
q = ρцρв/(ρв+mρц) (2.5.2)
где ρц – плотность цемента;
ρв – плотность воды;
m – водоцементное отношение.
Кондуктор Ø 324мм: q1 = 2900·1000/(1000+0,5·2900) = 1184кг
Пром. колонна Ø 245мм: q2 = 3015·1000/(1000+0,48·3015) = 1232кг
Экс. колонна Ø 140мм: q3 = 3500·1000/(1000+0,34·3500) = 1598кг
отсюда плотность цементного раствора будет[5]:
ρц.р. = q(1+m) (2.5.3)
Практически плотность цементного раствора определяется ареометром.
Общее количество цемента[5]:
G = kцqVц.р. (2.5.4)
где kц = 1,03-1,05 – коэффициент, учитывающий потери цемента при погрузочно-разгрузочны работах.
Кондуктор Ø 324мм: G1 = 1,04·1184·52,6 = 64,8т
Пром. колонна Ø 245мм: G2 = 1,04·1232·63 = 80,7т
Экс.колонна Ø 140мм: G3 = 1,04·1596·23,5 = 39т
Число цементно-смесительных машин принимается с учетом расчетного объема цемента при условии, что на каждую из них можно загрузить примерно 20 т материала (n1 = 3, n2 = 4, n3 = 2).
Общий объем воды при этом составляет[5]:
Vв = Gц/(kцkвρв) (2.5.5)
где kв = 1,01-1,05 – коэффициент, учитывающий потери воды.
Объем продавочной жидкости для транспортирования цементного раствора в затрубное пространство можно определить по формуле[5]:
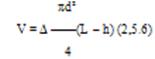
где Δ = 1,03-1,05 – коэффициент сжимаемости продавочной жидкости.
Кондуктор Ø 324мм: V1 = 1,04·0,785·0,324²(1020 – 10) = 86,6м³
Пром.колонна Ø 245мм: V2 = 1,04·0,785·0,245²(2450 – 10) = 119,6м³
Экс. колонна Ø 140мм: V3 = 1,04·0,785·0,14²(3025 – 10) = 48,2м³
Величина максимального давления в конце продавки вычисляется по формуле[5]:
p = p1 + p2 (2.5.7)
где p1 – давление, обусловленное разностью удельных весов в трубах и затрубном пространстве;
p2 – гидравлические потери давления.
Давление, обусловленное разностью весов в трубах и затрубном пространстве, находим по формуле[5]:
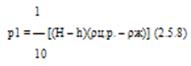
Гидравлические потери давления точно рассчитать пока невозможно. Для приблизительных расчетов используем ориентировочные формулы Р.И.Шищенко:
а) для скважин глубиной до 1000м – р2 = 0,001L + 0,8, МПа;
б) для скважин глубиной более 1000м – р2 = 0,001L + 1,6, МПа.
Время цементирования колонны[5]:
Тцем = tц + tпц + 10 (2.5.9)
где tц – время закачки цементного раствора;
tпц – время продавки цементного раствора;
10 – время, необходимое для выполнения операции по закладыванию в заливочную головку пробки.
Время закачки цементного раствора и время продавки цементного раствора находим по формулам[5]:
tц = Vц.р/qср (2.5.10)
tпц = Vж/qср (2.5.11)
где qср = 0,020м³/с – средняя производительность насосов цементировочных агрегатов.
Кондуктор Ø 324мм: tц1 = 52,6/0,02 = 44мин
Пром. колонна Ø 245мм: tц2 = 63/0,02 = 53мин
Экс. колонна Ø 140мм: tц3 = 23,5/0,02 = 20мин
Кондуктор Ø 324мм: tпц1 = 86,6/0,02 = 72мин
Пром. колонна Ø 245мм: tпц2 = 119,6/0,02 = 100мин
Экс. колонна Ø 140мм: tпц3 = 48,2/0,02 = 40мин
Потребное количество цементировочных агрегатов определяем по следующей формуле[5]:
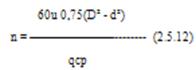
где u = 1,5м/сек – средняя скорость восходящего потока цементного раствора.
Вычисленные значения заносим в таблицы.
Таблица 2.11 Общие сведения о цементировании обсадных колонн.
Наим.колонны |
Диаметр,мм |
Коэф.
кавер-
нознос.
|
Характеристика секций |
Интервал
цементирования
|
Плотн.
цем.р.,
кг/м³
|
колон-
ны
|
сква-
жины
|
ин-вал уст.,м |
кол-во
ступен.
|
от |
до |
от |
до |
Кондуктор
Пром. колонна
Экс.колонна
|
324
245
140
|
394
295,3
190,5
|
1,10
1,10
1,12
|
1020
2450
3025
|
0
0
0
|
1
1
1
|
1020
2450
3025
|
0
0
1850
|
1780
1820
2150
|
Таблица 2.12 Данные к расчету цементирования колонн
Наим.
колонны
|
Диам.
колонн
|
Плотность,кг/м³ |
В/С
отнош.
|
Мас.там.
матер.
|
Объем,м³ |
Давление,МПа |
сух.мат. |
раств. |
цем.рас. |
буф.ж. |
в труб. |
в затр. |
Кондуктор
Пром. колонна
Экс.колонна
|
324
245
140
|
2900
3015
3500
|
1780
1820
2150
|
0,50
0,48
0,34
|
1,184
1,232
1,598
|
52,6
63,0
23,5
|
6,0
6,0
6,0
|
6,8
4,3
6,5
|
18,4
45,8
68,5
|
Таблица 2.13 Потребное количество материалов и цементировочной техники
Наименование работ или затрат |
Единица
измерения
|
Потребное кол-во на колонну |
кондуктор |
пром.кол. |
экс.кол. |
Цемент
Вода техническая: для буфера
для затворения
УНБ 160/40
АН-400
2СМН-20
БМ-700
СКЦ-2М
Осреднитель
|
тонн
м³
м³
шт
шт
шт
шт
шт
шт
|
64,8
6,6
32,4
2
3
3
1
1
2
|
80,7
6,6
38,8
2
3
4
1
1
2
|
39
1,1
14
1
4
5
1
1
1
|
3. ЭКОНОМИЧЕСКИЙ РАСЧЕТ
СМЕТА
К РАБОЧЕМУ ПРОЕКТУ
на строительство эксплуатационной скважины
№11 на площади СЕВЕРО-ПРИБРЕЖНАЯ.
Цель работ эксплуатация
Способ бурения роторный
Вид бурения вертикальный
Местоположение суша
Вид энергии электричество
Буровая установка 4Э-76
Глубина скважины 3025
Скорость бурения 612 м/ст.мес.
Продолжительность цикла
строительства скважины, сут 229,1
·строительно-монтажные работы 67
·подготовительные работы к бурению 4
·бурение и крепление 150,3
·испытание 7,8
Конструкция скважины
·направление 530мм×30м
·кондуктор 324мм×1020м
·промежуточная колонна 245мм
×2450м
·эксплуатационная колонна 140мм×3025м
3.1 СМЕТНЫЙ СВОДНЫЙ РАСЧЕТ НА СТРОИТЕЛЬСТВО СКВАЖИНЫ
Таблица 4.1 Сводный расчет на строительство скважины
Наименование работ и затрат |
Стоимость, всего |
В ценах 1991 года |
В текущих ценах,руб |
Прямые затраты, руб |
В т.ч. осн з/плата рабочих |
1 |
2 |
3 |
4 |
Глава 1. Подготовительные раб. к строительству
Разборка К=0,1
Итого
Транспорт 9,8%
Итого по гл. 1
Глава 2. Строительство и разборка вышки, привышеечн. сооруж., монтаж и демонт. БУ
Строительство и монтаж
Разборка и демонт. К=0,2
Итого
Транспорт 9,8%
Итого по гл. 2
Глава 3. Бурение и крепление скважины
Бурение скважины
Крепление скважины
Итого
Транспорт 9,8%
Итого по гл. 3
Глава 4. Испытание скв. на продуктивность
Обвязка устья скважины
Испытание скв. на продуктивность
Итого
Транспорт 9,8%
Итого по гл. 4
Глава 5. Дополнительные затраты при строительстве в зимнее время 0,8%
Итого по гл. 1-5
Глава 6. Накладные расходы 26,0%
Глава 7. Плановые накопления 20,0%
Итого по гл. 1-7
Глава 8. Прочие работы и затраты
Платежи по страховым взносам 3,0%
Выплата премий 2,2%
Полевое довольствие 2,3%
Лабораторные работы 0,15%
|
73713
7371
81084
7946
89030
31004
6201
37205
3646
40851
528619
418929
947548
92860
1040407
3968
32737
36705
3597
40302
1039
1211630
315024
305331
1831984
54960
40304
42136
1621
|
1745
1745
2712
2712
26444
8774
35217
292
2876
3168
36
42879
42879
|
2288079,72
1049859,97
26738468,23
1035766,77
26703,52
8096108,34
7846997,31
1412459,52
1035803,64
1082885,63
41661,35
|
Охрана окружающей среды
Рекультивация
Итого по гл. 8
Итого по гл. 1-8
Глава 9. Авторский надзор 0,2%
Глава 10. Резерв на непредвиденные работы5,0%
Итого по гл. 1-10
(в ценах 91 г)
Индекс удорожания к ценам 91г. К=25,7
Итого по гл. 1-10
(текущих ценах)
Глава 11.Доп. затраты в текущих ценах
Пуско-наладочные работы
Пуско-наладочные работы электричес-
кой части установки "KEM-TRON"
Пробег _К. Лаборатории на 170 км
Подвоз воды автоцистернами на 10 км
Промыслово-геофизические работы
Инженерные изыскания
Радиационный контроль
Дежурство инженеров СКВО
Платежи за выбросы в атмосферу
Плата за размещение отходов
Содержание шламохранилища
Проектные работы в т.ч. согласование и
экспертиза проекта
Ущерб ЧНВХ
Аренда земли
Оформление земли
Регистрация
Потери сельхоз производства
Ущерб госохотзаказнику
Изготовление Технического паспорта
Технологическая дорога и площадка
под скважину
Площадка для скважины №11 Северо-
Прибрежного месторождения
Подъездная технологическая дорога
Инженерное сопровожд. (супервайзер)
Программа по растворам
Сервисные услуги "Эколог Кубани"
Геоэкологический мониторинг
Итого по гл. 11
Итого по гл. 1-11
НДС
18,0%
Всего по сметному расчету
|
39076
4928
183024
2015008
4030
100952
2119990
1225792350
3345782032
602240766
3948022798
|
27
27
42906
42906
1102687
1102687
1102687
|
1004261,31
126644,56
4703716,00
103571,40
2594463,56
54483734,82
369341,48
25426,86
4471,00
13072,72
2627913,00
152542,37
50847,46
84745,76
366,07
275010,77
593220,34
1059642,30
1271186,44
338983,05
42372,88
55084,75
84745,76
211864,41
50847,46
6924912,03
8583309,00
1330693,00
1702210,17
5170054,33
300000,00
180000,00
31502863,39
85986598,22
15447587,68
101464185,9
|
Стоимость оборудования, приобретаемого заказчиком:
·устройство замера устьевых параметров 278588 руб.
·фонтанная арматура АФ6-63x70 1120000 руб.
·колонная головка ОКК2-70-140x245x324 650000 руб.
·НКТ (3025 м) Ø73x5,51 1200000 руб.
Итого: 3248588 руб.
НДС: 18,0% 584746 руб.
ВСЕГО: 3833334 руб.
Итого, затраты на скважину с учетом оборудования, приобретаемого заказчиком составляет 105297519,74 руб.
Содержание службы заказчика 2421842,95 руб.
ВСЕГО затрат на скважину: 107719363 руб.
4.БЕЗОПАСТНОСТЬ ЖИЗНЕДЕЯТЕЛЬНОСТИ
4.1 МЕРОПРИЯТИЯ ПО ОБЕСПЕЧЕНИЮ БЕЗОПАСНЫХ И КОМФОРТНЫХ БЫТОВЫХ УСЛОВИЙ
В связи с тем, что на нефтегазодобывающих предприятиях основная часть работы протекает под открытым небом, законодательством предусмотрены помещения для обогревания и отдыха рабочих.
Помещения бывают стационарными и передвижными. Они устанавливаются у каждой буровой установки, установки капитального ремонта скважин и у других производственных объектов.
Расстояние между помещениями и спуско-подъемным сооружением должно превышать высоту этих сооружений на 10 метров.
В помещении имеется бачок с питьевой водой, аптечка с полным набором медикаментов первой помощи, носилки и мебель. Помещение необходимо содержать в чистоте и периодически дезинфицировать, в нем расположены: гардеробные, душевые, помещения для сушки, обеспыливания и обезвреживания рабочей одежды, умывальные, курительные, прачечные.
В гардеробных
рабочей одежды предусмотрены отдельные кладовые для хранения чистой и грязной одежды. В гардеробных одежда может храниться открытым способом (на вешалках или в открытых шкафах), закрытым (в закрытых шкафах) и смешанным, при котором один вид одежды хранится открытым, а другой – закрытым способом.
Головные уборы, обувь и белье должны храниться в гнездах и ящиках закрытых шкафов.
Душевые
размещаются в помещениях, смежных с гардеробными. Расположение помещений душевых у стен здания не допускается. Число душевых сеток зависит от числа человек на одну душевую сетку, работающих в наиболее многочисленной смене. При душевых имеются помещения для переодевания. Рекомендуется применение шарнирных душевых сеток, позволяющих регулировать направление и распыление водяной струи.
Помещения для сушки, обеспыливания и обезвреживания рабочей одежды
оборудованы отопительными и вентиляционными установками, которые рассчитаны на высушивание рабочей одежды в течение времени не более продолжительности рабочей смены.
Помещения для обезвреживания рабочей одежды обособленны. Требования к ним определяются в зависимости от способа обезвреживания, который должен быть согласован с органами Государственного санитарного надзора.
Помещения для обеспыливания рабочей одежды также обособленны и располагаются рядом с гардеробными.
Умывальные
размещаются в отдельных помещениях, смежных с гардеробными, или в гардеробных.
Число кранов в умывальных определяется в зависимости от производственного процесса: по числу человек на один кран, работающих в наиболее многочисленной смене.
Курительные
следует размещать смежно с туалетами или с помещениями для обогревания работающих.
Прачечные
для стирки и обезвреживания спецодежды должны быть механизированные и иметь помещение для ремонта этой одежды.
Гардеробные, дущевые и другие санитарно-бытовые помещения и устройства должны периодически дезинфицироваться.
4.2 ИНЖЕНЕРНЫЕ МЕРОПРИЯТИЯ ПО ОБЕСПЕЧЕНИЮ БЕЗОПАСНЫХ И БЕЗВРЕДНЫХ УСЛОВИЙ ТРУДА НА ОБЪЕКТЕ ПРОЕКТИРОВАНИЯ
Создание и обеспечение безопасных и безвредных условий труда на объекте проектирования являются основными задачами администрации и инженерно-технических работников в охране труда. Для выполнения их необходимо:
·Планировать организационно-технические мероприятия по улучшению условий труда и обеспечивать их выполнение;
·Вводить в эксплуатацию новые и реконструированные объекты только после приемки их комиссией с участием работника службы техники безопасности, представителей профсоюзной организации и органов государственного надзора;
·Обеспечивать строгое выполнение требований правил, норм, стандартов, инструкций по охране труда и пожарной безопасности;
·Осуществлять технологические процессы, организацию труда и рабочих мест в соответствии с требованиями охраны труда, техники безопасности и современных достижений науки и техники;
·Обеспечивать исправное состояние оборудования и инструмента, санитарное состояние рабочих мест, производственных, вспомогательных, санитарно-бытовых помещений;
·Организовать обучение и повышение квалификации инженерно-технических работников по вопросам охраны труда;
·Обеспечивать правильное и своевременное расследование, регистрацию и учет несчастных случаев, профессиональных заболеваний, профессиональных отравлений на производстве с разработкой мероприятий по предотвращению аналогичных случаев;
·Обеспечивать оборудование защитными и оградительными приспособлениями, представлять рабочим индивидуальные защитные средства, спецодежду, принимать меры к оснащению производственных объектов приспособлениями и устройствами по технике безопасности;
·Организовать контроль за соблюдением трудового законодательства, а также выполнением предписаний органов государственного надзора и технических инспекторов профсоюза по устранению нарушений правил и норм по охране труда.
Заместитель руководителя предприятия организовывает своевременное снабжение материалами и оборудованием для проведения мероприятий по оздоровлению условий труда, своевременное составление заявок и обеспечение работников спецодеждой, спецобувью и средствами индивидуальной защиты (очками, респираторами, диэлектрическими перчатками и т.д.) в соответствии с типовыми отраслевыми нормами, а также молоком, мазями, пастами, моющими средствами и мылом; обеспечивает надлежащее состояние санитарно-бытовых помещений.
Соответствующие специалисты цехов отвечают за исправное состояние и безопасную эксплуатацию вверенного им оборудования и технологических установок.
Большое место в организации производства принадлежит инженерно-технологическим службам. Они несут ответственность за правильное ведение технологических процессов в соответствии с требованиями охраны труда и производственной санитарии, обеспечивают выполнение в установленные сроки предписаний и требований органов государственного надзора, технических инспекторов профсоюза, работников службы техники безопасности; осуществляют систематический контроль за своевременным и качественным проведением мастерами инструктажа по технике безопасности на рабочем месте.
В вопросах обеспечения на производстве безопасных условий труда особая роль принадлежит непосредственным руководителям работ (мастер, старший мастер, производитель работ, начальник смены, начальник установки и др.). От них зависит соответствующая организация работы, надлежащее обучение рабочих безопасным методам труда, соблюдение требований правил и инструкций по технике безопасности и производственной санитарии, установленных режимов труда и отдыха, трудовой и производственной дисциплины.
На предприятии для организации работы по охране труда, технике безопасности и производственной санитарии предусмотрена служба техники безопасности. Основными задачами службы техники безопасности являются организация работы по созданию безопасных и безвредных условий труда, осуществление контроля за работой производственных подразделений по улучшению условий труда, разработка и осуществление, с учетом современных достижений науки и техники, организационно-технических санитарно-гигиенических мероприятий по предупреждению производственного травматизма, профессиональных заболеваний и отравлений. Служба техники безопасности осуществляет свою деятельность под непосредственным руководством главного инженера, в методическом отношении подчиняется службе охраны труда и техники безопасности вышестоящей организации.
4.3
ПОЖАРНАЯ БЕЗОПАСНОСТЬ
Пожарная безопасность – состояние объекта, при котором с установленной вероятностью исключается возможность возникновения и развития пожара и воздействия на людей опасных факторов пожара, а также обеспечивается защита материальных ценностей.
Пожарная безопасность объекта должна быть обеспечена в рабочем состоянии объекта и при возникновении аварийной обстановки.
Вся территория производственных объектов бурения и капитального ремонта скважин, а также добычи нефти и газа, в том числе площадки, на которых расположены скважины должны постоянно содержаться в чистоте и порядке. Не допускается замазучивание территории вокруг скважины, загрязнение легковоспламеняющимися и горючими жидкостями, мусором и отходами производства. Сгораемые отходы производства, мусор, сухая трава и др. должны убираться, а места розлива легковоспламеняющихся и горючих жидкостей должны тщательно убираться и засыпаться сухим песком или грунтом. Разбирать устьевую арматуру следует после глушения скважины и снижения в ней давления до атмосферного.
При длительных перерывах в работе по подъему и спуску труб устье скважины должно быть надежно герметизировано.
Выхлопные трубы передвижных насосных агрегатов, автоцистерны должны быть снабжены глушителями с искрогасителями.
Курение на территории выполнения работ допускается в специально отведенном месте, оборудованным урной для окурков и емкостью с водой. В этом месте должна быть вывешена надпись "Место для курения".
4.4
ОХРАНА ОКРУЖАЮЩЕЙ СРЕДЫ
Охрана недр.
Конструкция скважин должна обеспечивать защиту недр от загрязнения промывочной жидкостью и пластовым флюидом. Как правило, кондукторы скважин цементированы на всю длину до устья с целью перекрытия насыщенного грунтовыми водами почвенного слоя и укрепления устья скважины, перекрытия водоносных горизонтов, предупреждения обвалов стенок скважины и установки противовыбросового оборудования.
Эксплутационные колонны также цементированы до устья высокопрочным цементом с целью разобщения продуктивных горизонтов с вышележащими непродуктивными пластами.
Качество цементного кольца и надежность разобщения водоносных горизонтов проверяется путем опрессовки цементного кольца, которая производится после разбуривания цементного стакана и элементов оборудования низа колонны. При бурении скважин давление бурового раствора должно быть не менее пластового давления с целью исключения выбросов пластовых флюидов на поверхность и не более давления гидроразрыва пласта с целью недопущения загрязнения водоносных пластов технологическими жидкостями. Обвязка устья скважины должна обеспечивать надежность противовыбросового оборудования.
Рекультивация нарушенных земель.
Территория горного отвода одной скважины в среднем составляет 0,36га, в том числе территория устьевого оборудования 0,02-0,06га.
После окончания бурения проводятся работы по разборке временных бетонных стяжек и септиков, по демонтажу и перебазированию плит покрытия и уборке территории, по технической рекультивации, включающие засыпку амбара, приямков, разборку обваловок, планировку площадки, перемещение и укладку плодородного слоя на площадке буровой
Мероприятия по охране почв.
Для уменьшения опасности загрязнения почвы в аварийных ситуациях на площадке проектом предусматривается:
1.Откачка жидкости из технологических аппаратов в аварийные емкости и возврат продуктов в технологический процесс;
2.Сброс нефти и газа с предохранительных клапанов аппаратов, работающих под давлением, в дренажные емкости;
3.Откачка жидкости из всех дренажных емкостей в нефтесборные сети;
4.Аварийная сигнализация предельных значений регулируемых параметров (уровня, давления, температуры).
Для локализации загрязнения непосредственно на месте образования в проекте предусмотрены следующие мероприятия:
1.Устройство земляного вала по периметру площадки бурения;
2.Устройство площадок с бордюрным ограждением и дождеприемником под сепарационными установками и прочими агрегатами, работающими под давлением, для сбора разливаемых дождевых вод, загрязненные нефтью;
3.Устройство площадок с бордюрами, ограждением для хранения химреагентов, применяемых в технологическом процессе.
Охрана растительного покрова, лесов и насаждений.
При выполнении подготовительных работ, бурения и испытаний не допускается:
1.Нарушение древостоев, растительного покрова и почв за пределами участка бурения;
2.Перекрытие естественных путей стока поверхностных вод;
3.Захламление участков и прилегающих территорий строительным мусором и токсичными веществами;
4.Вылив и утечки ГСМ, неочищенных промышленных стоков, минерализованных вод, буровых растворов и пр. в поверхностные водоемы и гидрографическую сеть;
5.Выбросы в атмосферу и утечки по поверхности продукции скважин;
6.Проезд транспорта по произвольным маршрутам;
7.Уничтожение межевых знаков.
Охрана животного мира.
При проведении работ, связанных с бурением скважин, проектом предусматриваются и осуществляются мероприятия по сохранению среды обитания и условий размножения животных:
1.Обеспечивается неприкосновенность участков, представляющих особую ценность в качестве среды обитания животных;
2.Не допускается уничтожение древесно-кустарниковой растительности в местах обитания животных вблизи выбранных объектов вторых стволов;
3.Принимаются меры по предупреждению разливов нефти и вызываемой ими гибели рыб, водо-обитающих животных, водоплавающих и других птиц.
Технология бурения скважины месторождения Северо-Прибрежная, при выполнении комплекса вышеизложенных рекомендаций по обеспечению экологической безопасности, оказывает слабое техногенное воздействие на окружающую среду, без заметного влияния на здоровье персонала, а также на растительный и животный мир.
ЗАКЛЮЧЕНИЕ
В данной работе запроектировано бурение и крепление эксплуатационной скважины на нефтегазоконденсат глубинной 3025 м на Северо-Прибрежной площади Краснодарского края.
В общей части даны географическое положение, обзор ранее проведенных геолого-геофизических исследований и геологическая характеристика района работ. Описаны: стратиграфия, тектоника и нефтегазоносность данного района.
Проходка проектной скважины будет осуществляться буровой установкой БУ3200/200ЭУК-2М в четыре интервала бурения: под направление диаметром 530 мм, под кондуктор диаметром 324 мм, под тех колонну диаметром 245 мм и под эксплуатационную колонну диаметром 140 мм, с применением полимерно-глинистого раствора. Контроль процесса бурения обеспечит станция ГТИ. Цементирование скважины будет осуществляться с применением 4 цементосмесительных машин 2СМН-20, 5 цементировочных агрегатов и осреднительной емкости. Контроль процесса обеспечит станция контроля цементирования СКЦ-2М.
В работе предусмотрены все необходимые меры безопасности жизнедеятельности, Рассмотрены мероприятия по предупреждению аварий и осложнений, охране недр и окружающей среды.
Сроки выполнения работ: начало - 1 ноября 2007 г., окончание - 20 июня 2008 г.
Предполагаемая стоимость работ 107719363руб.
ЛИТЕРАТУРА
1. Методические указания по выбору конструкции нефтяных и газовых скважин. – М.: Миннефтепром, 1973 г.
2. Середа Н.Г., Сахаров В.А., Тимашев А.Н. "Спутник нефтяника и газовика". М., Недра, 1986.
3. Иночкин П.Т., Прокшиц В.А. "Справочник бурового мастера". М., Гостоптехиздат, 1958
4. Вадецкий Ю.В. "Бурение нефтяных и газовых скважин". М., Недра, 1973.
5. Булатов А.И. "Технология цементирования нефтяных и газовых скважин".М., Недра, 1983.
6. Правила безопасности в нефтяной и газовой промышленности. М.: Госгортехнадзор России, 1998 г.
7. Сулейманов М.М., Газарян Г.С., Манвелян Э.Г., Тимошук А.Б. "Охрана труда в нефтяной промышленности". М., Недра, 1980.
8. "Правила пожарной безопасности в нефтяной промышленности ППБО-85". М., Недра, 1987.
9. Хоботько В.И., Эстрин Р.Я., Сулейманов М.М. "Противопожарная безопасность и защита на предприятиях нефтяной промышленности". М., Недра, 1982.
10. В.И.Мищевич, Н.А.Сидоров "Справочник инженера по бурению", М, "Недра", 1973г.
|