Министерство транспорта Российской Федерации
Федеральное агентство железнодорожного транспорта
Самарский Государственный университет путей сообщения
Кафедра «Безопасность перевозок пассажиров и грузов»
Курсовая работа по дисциплине: « Автотормоза»
на тему: Ремонт автоматического регулятора
Разработал:
студент 561 гр. Дзюба О.В.
Проверил:
Киселев Г.Г.
Самара 2010
Реферат
В данном курсовом проекте рассмотрен и описан процесс ремонта и испытания автоматического регулятора ТРП. Он состоит из пояснительной записки и графической части.
В пояснительной записке затронуты такие вопросы, как: характеристика и описание автоматического регулятора, их основные неисправности, АКП, требования охраны и техники безопасности при ремонте тормозного оборудования. В целом пояснительная записка состоит из 29 листов, 1 таблицы, 5 рисунков.
Графическая часть состоит из 3-х листов: формата А1 и А2, на которых изображены карта неисправностей авторегулятора, схема АКП и карта технологического процесса авторегулятора.
В конце данной работы, для более полного и подробного изучения авторегуляторов, представлен список использованных источников.
Содержание
Введение
1. Контрольный пункт автотормозов (АКП) и автоматные цеха
2. Краткое описание конструкции ремонта автоматического регулятора ТРП №574Б, условия работы и ремонта
3. Разработка карты неисправностей
4. Разработка карты технологического процесса
5. Требования техники безопасности и охрана труда
5.1 Общие положения
5.2 Требования к технологическому оборудованию
5.3 Требования к инструментам и приспособлениям
5.4 Требования организации рабочего места
5.5 Требования при ремонте ТРП
5.6 Требования к персоналу и применению средств индивидуальной защиты
Заключение
Библиографический список
ВВЕДЕНИЕ
Исходя из реальных условий эксплуатации тормозных приборов принята планово - предупредительная система их ремонта. Цель этой системы устранить естественные износы трущихся пар, предупредить возможность отказов приборов в работе и обеспечить безотказную их работу в эксплуатации в течение установленного срока.
Установлены следующие виды ремонта и осмотра тормозного оборудования вагонов: заводской, деповской, ревизия и текущий.
Заводской и деповской ремонты тормозов выполняют на вагоноремонтных заводах и в вагонных депо при соответствующих видах ремонта вагонов. При этих видах ремонта снимают с вагона воздухораспределители, электровоздухораспределители, авторежимы, авторегуляторы, концевые и разобщительные краны, краны экстренного торможения, соединительные рукава, выпускные клапаны и направляют в контрольный пункт автотормозов (АКП) или тормозное отделение завода для осмотра, ремонта и испытания. Взамен снятых приборов устанавливают исправные из оборотного запаса.
Тормозные цилиндры, все воздушные резервуары и воздухопровод осматривают, ремонтируют и испытывают при деповском ремонте без снятия с вагонов, а при заводском – со снятием.
Цилиндры разбивают, очищают, их детали осматривают и обмеряют. После устранения неисправностей рабочие поверхности корпуса цилиндра, манжету, войлочное кольцо поршня и сальник смазывают тормозной смазкой, а также производят сборку.
Рычажную тормозную передачу разбирают, все детали тщательно осматривают и обмеряют для определения величины износов и выявления дефектов. Негодные детали ремонтируют или заменяют. Неисправные предохранительные устройства восстанавливают до альбомных размеров. Для повышения эксплуатационной надежности предохранительные скобы ставят на резиновых прокладках, а на длинные тормозные тяги устанавливают ограничители вибрации – дополнительные скобы с резиновыми и деревянными прокладками. Автоматические регуляторы выхода штока тормозного цилиндра ремонтируют с проверкой действия на специальном стенде.
При заводском ремонте запасные и рабочие ревервуары очищают и подвергают гидравлическому испытанию. После выполнения наносят трафарет с указанием даты и ремонтного пункта.
Ревизия тормозного оборудования выполняется через каждые шесть месяцев при отцепочном ремонте вагонов и на пунктах отстоя. При ревизии осматривают и проверяют: тормозные цилиндры, рычажную передачу, предохранительные устройства, прочность крепления тормозных цилиндров, резервуаров, скоб, воздухопровода, соединительных рукавов и их подвесок. Изношенные тормозные колодки заменяют. Воздухораспределители без бирок и с неявными клеммами на бирках заменяют.
1.
КОНТРОЛЬНЫЕ ПУНКТЫ АВТОТОРМОЗОВ И АВТОМАТНЫЕ ЦЕХИ
Ремонт пневматического оборудования тормозов подвижного состава производится в автоматных цехах или отделениях депо, заводов и контрольных пунктах автотормозов (АКП) (рис.1).
АКП организуют в депо, ремонтирующих грузовые и пассажирские вагоны, а также на вагоноремонтных заводах. АКП специализируют на ремонте тормозного оборудования либо грузовых, либо пассажирских вагонов, а отдельных случаях – грузовых и пассажирских вагонов.
Имеющаяся на АКП компрессорная установка (станция), кроме обеспечения своих потребностей, снабжает сжатым воздухом пункты технического обслуживания вагонов, а также других потребителей узла.
В АКП имеются отделения наружной очистки, разборки тормозных приборов, ремонта воздухораспределителей и авторежимов, авторегуляторов, тормозной арматуры и междувагонных соединений, поршневых узлов тормозных цилиндров, механическое отделение, а также кладовая и при необходимости – служебно-бытовые помещения. Суточная программа ремонта для типового АКП (рис.1) составляет около 100 воздухораспределителей.
Тормозное оборудование в АКП ремонтируют в соответствии с типовым технологическим процессом, технологическими картами, техническими нормами и требованиями инструкций.
Тормозные приборы очищают и обмывают в специальной машине с использованием моющего раствора, подогретого до температуры 70-800
С, после чего приборы разбирают и комплектно укладывают в специальные поддоны или корзины из проволочной сетки и направляют в машину для вторичной обмывки. Затем тормозные приборы направляют в ремонтное отделение, оборудованное конвейерным транспортером и стойками с оснасткой для ремонта и испытания подкомплектов магистральных и главных частей воздухораспределителей, авторежима. Ремонтные позиции размещены последовательно вдоль потока с расчётом, чтобы с любой из них было удобно брать перемещающиеся по конвейеру узлы. Здесь же установлены специальные станки для притирки и полгонки уплотнительных металлических колец, гидравлические и пневматические прессы, устройство для проверки пружин тормозных приборов, стеллажи и шкафы для инструмента. На рабочих местах вывешивают выписки из действующих правил и технологических процессов ремонта соответствующих узлов.
При поточно-узловом методе ремонта неисправные части заменяются новыми или заранее отремонтированными при строгом соблюдении очередности и максимальной параллельности ремонтных операций.
Все воздухораспределители и авторежимы после ремонта обязательно испытывают на стендах в специально оборудованном отделении, расположенном рядом с отделением ремонта.
Для испытания воздухораспределителей применяют двухпозиционные стенды с электропневматическим управлением, которые обеспечивают быстроту, высокое качество и точность выполнения операций в соответствии с установленными нормами и правилами.
Приёмку тормозных приборов при испытании на стендах производит бригадир или мастер АКП.
На принятом после испытания тормозном приборе ставят пломбу и бирку, на которой ставят клеймо-дату ремонта и условный номер АКП. При этом номер отремонтированного прибора и результаты испытаний записывают в специальный журнал с подписью работников, сдавших и принявших тормозной прибор.
На привалочные фланцы принятых и опломбированных приборов устанавливают предохранительные щитки (резиновые, пластмассовые, картонные) и сдают в кладовую. Авторегуляторы рычажных передач ремонтируют в отделении, находящемся, как правило, рядом с отделением наружной обмывки. После обмывки их разбирают, очищают от грязи внутренние полости и поверхности деталей регулировочного механизма, а затем ремонтируют и испытывают с применением типовой оснастки. На принятом после испытания авторегуляторе, так же как и на тормозном приборе, закрепляют бирку с клеймами.
Концевые, разобщительные краны и краны экстренного торможения ремонтируют в отделении тормозной арматуры. Вдоль поточной линии установлены типовые столы – верстаки с приспособлениями и оснасткой для разборки, ремонта и испытания. На рабочих местах расположены выписки из правил и технологического процесса выполнения операций.
Отделение ремонта соединительных рукавов оснащено приспособлениями для очистки, ремонта и испытания. Неисправный рукав раскомплектовывают, негодные элементы заменяют исправными. Соединительные головки, хомутки, резинотканевые трубки, снятые головки и штуцера очищают, проверяют контрольными шаблонами, ремонтируют и передают для комплектования новых рукавов на специальных стендах. Перед гидравлическим и пневматическим испытаниями скомплектованный рукав выдерживают не менее 24 часов для высыхания резинового клея, которым смазывают наконечники головки и штуцера. После испытания на соединительных рукавах закрепляют бирки с клеймами.
Тормозное оборудование пассажирских вагонов отличается от оборудования грузовых в основном конструкцией воздухораспределителей, а также применением электропневматической системы управления. Пневматическое и электропневматическое оборудование пассажирских вагонов ремонтируют также в АКП.
Все тормозное оборудование, отремонтированное и испытанное в АКП, должно быть зафиксировано в журнале формы ВУ-47.
Хранение отремонтированного и испытанного тормозного оборудования необходимо производить на специальных стеллажах и в кладовой готовой продукции

Экспликация
/ — отделение для наружной очистки; // — отделение для разборки и очистки; /// — место для осмотра и определения объема ремонта; IV
— отделение для ремонта приборов; V
—
отделение для ремонта арматуры; VI
— механическое отделение; VII
— отделение для контроля и испытания приборов; VIII
— кладовая; IX
— гальваническое отделение; X
—
контора мастера; XI
—
котельная; XII
— бытовая комната
2. КРАТКОЕ ОПИСАНИЕ КОНСТРУКЦИИ АВТОРЕГУЛЯТОРА ТРП №574Б, УСЛОВИЯ РАБОТЫ И РЕМОНТА
Все грузовые вагоны, построенные с 1974 г. оборудованы автоматическими регуляторами одностороннего действия № 574Б (рис.2), предназначенными для стягивания рычажной передачи и компенсации износа тормозных колодок. Применение регуляторов позволяет устранить ручную регулировку рычажных передач и поддерживать выход штока ТЦ в установленных пределах. Тем самым обеспечивается правильное взаимное расположение рычагов и тяг, достигается стабильность коэффициента полезного действия рычажной передачи и высокая тормозная эффективность. Наибольшее передаваемое через регулятор усилие составляет 80 кН.
Автоматический регулятор состоит из корпуса 14 с крышкой 16и головкой 3,
защитной трубы 2
с наконечником,
возвращающей пружины 13,
тягового стакана 7 со стопорным кольцом 12и крышкой стакана 4, тягового стержня 17
с ушком 19, регулирующей 8
и вспомогательной 5гаек с упорными подшипниками 9,
пружинами 6 и 11 и втулкой 10, а также регулирующего винта 1
с несамотормозящейся трехзаходной трапециедальной резьбой и предохранительной гайкой 15.
При нормальных зазорах между колодками и колесамив процессе торможения упор 18приближается к корпусу регулятора, но не достигает его или только соприкасается с ним. Усилие от тягового стержня передается на тяговый стакан 7, который входит в сцепление с регулирующей гайкой 8и через нее на регулирующий винт 1 и в рычажную передачу.
Если зазоры между колодками и колесами увеличены, то при торможении упором 18
корпус 14 регулятора перемещается влево по отношению к винту 1,
сжимая возвращающую пружину 13и освобождая из закрепления вспомогательную гайку 5.
Последняя под действием пружины 6 навернется на винт 1,
достигая левым торцом конусной поверхности головки 3.
Если перемещение корпуса 14 по отношению к винту 1
произошло на величину более 8—11 мм, то вспомогательная гайка 5выступом упрется в крышку 4тягового стакана 7, не достигая поверхности головки 3.
Усилие от штока тормозного цилиндра передается в рычажную передачу так же, как и при нормальных зазорах между колодками и колесами.
При отпуске, когда усилие ТЦ окажется меньше разности между усилием сжатия возвращающей пружины 13и пружины регулирующей гайки (около 1,0 кН), тяговый стержень 17
вместе с тяговым стаканом 7 начнут перемещаться влево по отношению к корпусу 14. Конусные поверхности тягового стакана 7 и регулирующей гайки 8 размыкаются, и последняя за счет пружины 11
навернется на винт 1 до упора в правый торец вспомогательной гайки 5.
После этого все детали регулятора займут исходное положение, а винт 1 будет перемещен внутрь тягового стержня 17
на величину, соответствующую износу колодок, или максимум на 8—11 мм. Если за одно торможение это значение будет превышено, то необходимое сокращение рычажной передачи произойдет за несколько последующих циклов торможения-отпуска. Стягивание рычажной передачи на 8—11 мм соответствует износу колодок грузового вагона в 0,5—0,7 мм. Полный рабочий ход регулятора составляет 550 мм.
При установке регулятора № 574Б на грузовом вагоне используется рычажный привод,
который передает ему при торможении запас энергии, вызывающей сжатие пружин и необходимо для стягивания рычажной передачи. После установки на вагоне всех новых тормозных колодок размер а
(от контрольной риски на стержне г
до конца защитной трубы д)
для регулятора № 574Б должен быть не менее 500 мм. Расстояние А
определяет величину выхода штока ТЦ и ориентировочно должно составлять при композиционных колодках 35—50 мм, а при чугунных колодках — 40—60 мм.
Регулировку размеров а и А
осуществляют вращением корпуса регулятора за выступы головки (один оборот изменяет длину на 30 мм), перестановкой валиков, а также винтом е.
Нарушение работы регулятора при отсутствии видимых повреждений возможно из-за поломки одной из его пружин, завышения расстояния А
или отсутствия запаса рабочего хода регулирующего винта.
Чтобы уменьшить влияние пружины авторегулятора на снижение передаваемого в ТРП усилия, особенно ощутимое при небольших давлениях в ТЦ при порожнем и среднем режимах ВР грузовых вагонов, на них применяют рычажные приводы, а на пассажирских с высоким давлением — стержневые. Они служат для передачи усилия от штока ТЦ к автоматическому регулятору при износе тормозных колодок, которым обеспечивается стягивание рычажной передачи.
3. РАЗРАБОТКА КАРТЫ НЕИСПРАВНОСТЕЙ
Для повышения эффективности контроля целесообразно разработать карту неисправностей. Такая карта представляет собой чертеж, рисунок узла или отдельных деталей, на котором стрелками указаны листы появления неисправностей, сопровождающий каждую стрелку надписи: в верхней строке указывается характер неисправности, а под чертой наиболее характерные признаки, по которым можно определить наличие данной неисправности. Или же делается анализ неисправностей в виде таблицы, где указываются признаки неисправности, причины вызвавшие эту неисправность и способы устранения.
Для обеспечения исправной работы в эксплуатации бескулисные автоматические регуляторы тормозной рычажной передачи осматривают с устранением неисправностей на ПТО, а также при ревизии и периодическом ремонте автотормозов в депо и на ремонтных заводах.
В процессе эксплуатации и при ревизии автотормозов регуляторы осматривают прямо на вагоне. При этом неисправные регуляторы заменяют заранее отремонтированными или новыми. При ремонте подвижного состава в депо или на заводах регуляторы снимают, разбирают, очищают от грязи и промывают, после чего все детали тщательно осматривают, при необходимости ремонтируют или заменяют новыми,
Собранные после осмотра и ремонта регуляторы испытывают на стенде, а затем и на вагоне для определения надежности их действия.
Для того чтобы снять регулятор с вагона, находящегося в эксплуатации, необходимо отключить тормоз от магистрали с помощью разобщительного крана, выпустить воздух из запасного резервуара и рабочей камеры. При наличии рычажного привода отсоединяют регулирующий винт от муфты,
для чёго выдергивают шплинт,
снимают шайбу,
сгоняют муфту с винта иопускают его на предохранительную скобу.
После этого снимают валик , а затем освобождают ушко регулятора из горизонтальных рычагов и рычага-упора привода.
При наличии стержневого привода отсоединение ушка регулятора от горизонтальных рычагов тормозного цилиндра производят после снятия стержня привода, для чего необходимо вывинтить стержень из пальца и упора.
Если стержень изогнут, то сначала следует вытащить шплинт,
отвернуть гайку,
снять шайбу и вывести палец из отверстий горизонтальных рычагов. Затем надо свинтить палец с тяги, предварительно сняв гайку,
и вывернуть тягу из упора.
При составлении карт выбор признаков неисправностей и их рациональной собственности определяется стремлением повышения достоверности контроля и снижению вероятности ошибок первого рода (пропуск дефекта) и второго рода (ложная тревога).
Возможность таких ошибок определяется прежде всего следующими обстоятельствами:
1. Трудность распознания признака
2. Не знание признака конкретной исполнителем
3. Небрежность и невнимание исполнителей
4. Связь одного признака с несколькими неисправностями
Одним из путей повышения эффективности и достоверности контроля является увеличение числа признаков, которые рекомендуются исполнителем для выявления той или иной неисправностей. Поэтому при составлении карты неисправностей оптимальное количество неисправностей 3−4.
Анализ неисправностей
№№ п/п |
Признаки неисправности |
Причины неисправности |
Способы устранения неисправностей |
1 |
Заклинивание, заедание регулирования регулятора |
Трещины, отколы винта, пружины, крышки |
Измеряют при помощи лупы ЛП-1-6 ГОСТ 25706, заменить |
2 |
Невозможность регулирования ТРП |
Износ резьбы винта |
Замер: калибр ПР: кольцо 8211-1101-8g ГОСТ 17763
Непр: кольцо 8211-1101-8g ГОСТ 17764,
ремонт
|
3 |
Заедание регулировки |
Срыв резьбы |
Ремонт |
4 |
Неправильная регулировка ТРП |
Износ конусных поверхностей более чем на 0,6 мм |
Проверка шаблоном 642.003, заменить |
5 |
Невозможность сохранять величину выхода штока поршня ТЦ |
Просадка пружины более чем на 4 мм-возвратная, роспуска -1мм; излом |
При изломе или других видимых дефектах - замена, просадка-ремонт, более допустимого - замена |
6 |
Регулятор не изменяет своей длины при вращении корпуса вручную |
Загрязнение деталей: регулирующего винта, гаек, упорных подшипников |
Сменить авторегулятор |
7 |
При полном торможении ход штока тормозного цилиндра отклоняется от нормы |
Неправильно установлен размер А |
Отренгулировать привод таким образом, чтобы ход штока при полном торможении находился в пределах нормы |
8 |
Изгиб стержня привода |
Допущено чрезмерное сжатие возвращающей пружины (более 110 мм) |
Выправить стержень привода |
9 |
При вращении авторегулятора вручную на стягивание корпус не смещается вдоль тягового стержня |
Авторегулятор полностью укоротил свою длину винт упирается в торец ушка) |
Заменить изношенные колодки или отрегулировать ТРП перестановкой валиков |
Основные неисправности авторегулятора представлены в графической части курсового проекта на листе 2.
4.
РАЗРАБОТКА КАРТЫ ТЕХНОЛОГИЧЕСКОГО ПРОЦЕССА
Снятый с вагона регулятор направляется для очистки, дальнейшей разборки и ремонта в отведенное для этого место отделения автоконтрольного пункта (АКП).
Разборка авторегулятора. Ввиду того что установленная в корпусе регулятора возвратная пружина сжата с силой около 150 кгс, запрещается разбирать и собирать авторегулятор без специального приспособления.
Проектно-конструкторское бюро ПКБ ЦВ МПС разработало технологическую оснастку для разборки, ремонта и сборки бескулисных регуляторов усл. № 536М. В комплект оснастки входят стенд для испытания регуляторов, а также приспособления и инструменты для разборки и сборки регуляторов; весь комплект можно использовать при ремонте регулятора усл. № 574Б.
Комбинированное приспособление для разборки и сборки основных узлов бескулисного авторегулятора (рис. 2) является быстродействующим устройством с пневматическим приводом.

Рисунок 2. Комбинированное устройство для разборки и сборки регулятора № 574 Б
Приспособление смонтировано на опорной раме, которая устанавливается на стол-верстак, имеющий соответствующие вырезы для размещения силового горизонтального цилиндра 20
и вертикального цилиндра, расположенных ниже опорной плиты 21.
Силовой цилиндр 20
предназначен для сжатия возвратной пружины 7 регулятора. На шток 19
цилиндра свободно насажена серьга 18,
которая удерживается двумя гайками 17.
В верхнее отверстие серьги вставлен натяжной винт 15
с маховиком 16.
Конец натяжного винта имеет резьбу, соответствующую резьбе тягового стержня авторегуляторов усл. 536М и 574Б. Горизонтальный цилиндр 20
приварен к ребрам опорной плиты.
Вертикальный цилиндр (на рисунке не показан) служит для перемещения прижима 6,
закрепляющего корпус 4
регулятора на ребрах опорной плиты. Цилиндр 20
имеет двусторонний впуск сжатого воздуха, вертикальный цилиндр — односторонний.
В ряде случаев можно пользоваться более простым приспособлением для сжатия возвратной пружины (рис. 3). Это приспособление состоит из винта 5,
гайки 4
с ленточной двухзаходной резьбой, подшипника 3
и трубы 1
с втулкой 2.
Винт на одном конце имеет такую же нарезку, как и ушко регулятора, а на другом— квадрат для удобства ввинчивания в тяговый стержень регулятора. К гайке 4
приварены рукоятки-стержни.
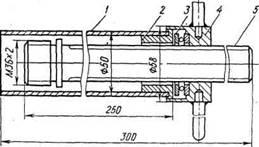
Рисунок 3. Приспособление для сжатия возвратной пружины регулятора
Перед установкой на комбинированное приспособление каждый поступивший в ремонт регулятор должен быть очищен от грязи и проверен на стенде с целью определения предстоящего объема работ.
При разборке корпус авторегулятора устанавливается на У-образных ребрах опорной плиты приспособления таким образом, чтобы его торец упирался во фланец 12
горизонтального цилиндра, как это показано на рис. 2. Затем включают вертикальный силовой цилиндр прижима 6,
и корпус регулятора надежно зажимается в приспособлении.
В начале разборки выбивают заклепку 13,
вывертывают ушко регулятора 14
и снимают упор 11
привода с тягового стержня 10.
Затем регулирующий винт ввертывают в регулятор до тех пор, пока предохранительная гайка 8
не выйдет из тягового стержня 10
со стороны ушка. После этого снимают предохранительную гайку 8,
предварительно выбив штифт 9,
и полностью вывертывают регулирующий винт из регулятора.
Далее с помощью маховика 16
в тяговый стержень 10
регулятора ввертывают натяжной винт 15,
причем нарезанная часть винта должна полностью войти в тяговый стержень во избежание несчастных случаев при последующем сжатии пружины. Из корпуса 4
регулятора вывертывается стопорный болт 3,
соединяющий головку 2
с корпусом.
Поворотом трехходового крана впускают сжатый воздух в левую полость горизонтального цилиндра 20.
В результате этого поршень вместе со штоком 19,
серьгой 18
и винтом 15
перемещается вправо, вытаскивая стержень 10
вместе с узлом стакана 5
и тем самым сжимая возвратную пружину 7. Таким образом, головка 2
регулятора освобождается от нагрузки возвратной пружины 7 и может быть выведена из корпуса 4.
Затем с помощью трехходового крана выпускают сжатый воздух из левой полости горизонтального цилиндра и впускают его в правую полость. Возвратная пружина 7,
постепенно разжимаясь, переместит стакан 5 влево до выхода его из корпуса регулятора, после чего тяговый стержень 10
освобождают от натяжного винта 15
приспособления, а стакан 5 со всеми собранными в нем деталями и возвратную пружину 7 вынимают из корпуса регулятора. После этого начинают разборку стакана.
После чего вывертывают крышку 13,
предварительно вывернув стопорный винт 12
(М6Х8). Вынимают вспомогательную гайку 10
с подшипником 11
и пружиной 9.
На этом разборка регулятора заканчивается. Все детали промывают в керосине, протирают насухо и подвергают тщательному осмотру и проверке.
Ремонт основных деталей авторегулятора.Головку авторегулятора осматривают с проверкой основных размеров. При наличии трещин, изломов, а также износа резьбы М95Х2 по шагу и диаметру более чем на 0,4 мм или срыва резьбы общей длиной более 1,5 нитки головка регулятора к дальнейшей эксплуатации не допускается. Заусенцы на гранях резьбы разрешается удалять напильником или шабером, а местные забоины и срывы прорезать на токарно-винторезном станке. Забитую резьбу М8 можно прорезать метчиком.
Если на конусной поверхности появляется местный износ глубиной до 0,6 мм, поверхность следует проточить с сохранением конусности 30°. Мелкие риски на этой поверхности удаляются протиркой с пастой ГОИ.
Регулирующий винт, вспомогательная и регулирующая гайки осматривают, их основные размеры проверяют. При наличии трещин, изломов и изношенной резьбы, когда гайки имеют продольное перемещение более 1 мм, детали бракуют.
Заусенцы, задиры, забоины на резьбе должны быть зачищены. Равномерный износ конусной поверхности регулирующей гайки допускается глубиной не более 0,6 мм; при большем износе разрешается поверхность обточить с сохранением конусности 45°.
Пружины, имеющие излом, трещины и другие поверхностные дефекты, бракуют. Заменяют новыми также пружины, имеющие по сравнению с установленными минимальными допусками просадку: возвратная пружина — более чем на 4 м; пружина роспуска — более чем на 1 мм; пружина регулирующей гайки — более чем на 1,5 мм. Проверка высоты пружин выполняется на специальном приспособлении, показанном на рис. 4. Остальные детали регулятора при ремонте также осматриваются и проверяются специальными шаблонами. Задиры и заусенцы на деталях зачищаются, а их рабочие размеры доводятся до чертежных.
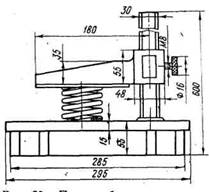
Рисунок 4. Приспособление для измерения высоты пружины
Сборка бескулисного авторегулятора.Сборка регулятора производится по узлам в последовательности, обратной разборке. При сборке все трущиеся поверхности деталей и подшипники смазывают смазкой ЖТКЗ ВТУ ЦТУ № 13-66 или ЦИАТИМ-201 ГОСТ 6267—59.
Вначале в корпус регулятора вставляется возвратная пружина, а затем собирают узел тягового стакана. Корпус стакана зажимают в тисках в вертикальном положении. В него последовательно вставляют пружину 9,
подшипник 11,
вспомогательную гайку 10
и поджимают эти детали крышкой 13,
завертывая ее до совпадения отверстий в ней и в корпус стакана под стопорный винт 12
(М6Х8). Затем ослабляют тиски, переворачивают стакан, вновь закрепляют его в тисках и последовательно вставляют регулирующую гайку 8,
подшипник 2,
пружину 3,
втулку 4,
тяговый стержень 6.
Все эти детали поджимают гильзой 5,
которую завертывают до совпадения отверстий в ней ив корпусе стакана под стопорный винт 7 (М6Х8). После того как собран узел тягового стакана, производят окончательную сборку регулятора на комбинированном приспособлении (см. рис. 2). Корпус 4
регулятора со вставленной в него возвратной пружиной 7 устанавливают на опорную плиту 21
приспособления и закрепляют прижимом 6.
На регулирующий винт навертывают собранные узлы головки и стакана, при этом необходимо убедиться, что они при вертикальном положении винта свободно, без заеданий навинчиваются под собственным весом. Затем комплект этих узлов вставляют в корпус 4,
в отверстие тягового стержня 10
ввертывают натяжной винт 15
приспособления; впуская воздух в силовой цилиндр 20,
сжимают возвратную пружину 7,
ключом ввертывают головку 2
и закрепляют ее болтом М8 х 12.
Далее выпускают воздух из силового цилиндра приспособления, отпуская возвратную пружину, и вывертывают натяжной винт приспособления из тягового стержня 10.
Регулирующий винт ввертывают в головку до выхода его конца из тягового стержня, после, этого на винт навертывают предохранительную гайку 8,
совмещают отверстия в винте и гайке и вставляют штифт 9.
После сборки регулятор снимают с приспособления и устанавливают на стенд для испытания.
Испытание авторегулятора на стенде. Стенд для испытания авторегуляторов (рис. 5) представляет собой сварной каркас, на котором установлен тормозной цилиндр диаметром 14". Шток поршня цилиндра шарнирно соединен с рычагом 2,
верхний конец которого валиком 3
соединяется с ушком 4
регулятора. Специальное упорное устройство 5
предназначено для закрепления упора привода 6.
На стенде имеется механизм, позволяющий имитировать износ тормозных колодок (увеличение или уменьшение зазора между колодкой и колесом). Вращением маховика 18
уменьшается или увеличивается расстояние между упором 16
и колодкой 17,
шарнирно подвешенной на вертикальном рычаге 15.
На верхнем шарнире вертикального рычага установлен поворотный демпфер 14
пружинного типа, имитирующий упругие деформации рычажной передачи. На шток демпфера навинчена тяговая муфта 13
с быстродействующим захватом.
Воздух поступает в тормозной цилиндр по трубе 9
через кран 8
вспомогательного тормоза локомотива усл. № 4ВК. Давление в тормозном цилиндре при испытании контролируется по манометру 7'
,
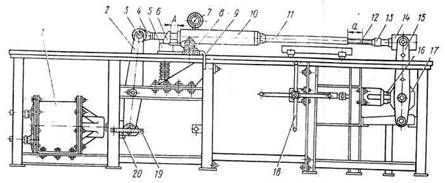
Рисунок 5. Стенд для испытания регуляторов
а величину выхода штока можно определить по указателю 20,
закрепленному на штоке поршня тормозного цилиндра, и масштабной линейке 19,
установленной на: каркасе стенда.
Механизм регулировки зазоров между колодкой и упором и демпферное устройство позволяют проверить работу автоматического регулятора в условиях, близких к эксплуатационным.
При испытании авторегулятора на стенде проверяется его работа на стабильность действия и стягивание рычажной передачи при различной величине износа тормозных колодок.
Устанавливая регулятор 10
на стенд, его ушко 4
соединяют с вертикальным рычагом 2
при помощи валика 3
со шплинтом. С противоположной стороны регулирующий винт 12-
соединяют муфтой 13
с поворотным демпфером 14.
Проверка работы автоматического регулятора на стабильность позволяет определить способность регулятора при нормальных зазорах между колодками и колесами сохранять постоянную величину выхода штока поршня тормозного цилиндра. Для этого вращением маховика 18
против часовой стрелки устанавливают зазор между упором 16
и колодкой 17
вертикального рычага, обеспечивающий определенную величину хода штока, тормозного цилиндра, например 100 мм при полном служебном торможении. Затем поворотом ручки крана 8
производят полное служебное торможение. Исправный авторегулятор должен установить выход штока в пределах 100 мм. Далее, поворачивая ручку крана 8,
выпускают воздух из цилиндра, рычажная передача стенда возвращается в исходное положение, а между упором 16
и колодкой 17.
образуется зазор.
Чтобы проверить стабильность работы регулятора, наносят продольную и поперечную меловые риски на конец защитной трубы 11 я
регулирующий винт 12
и производят одно-два регулировочных торможения с последующим отпуском. У исправного авторегулятора меловые риски не должны сместиться. Если же они сместились, значит, регулятор неисправен и его необходимо вернуть в ремонтное отделение АКП.
Во время эксплуатации регулятор должен надежно стягивать рычажную передачу в зависимости от увеличения выхода штока поршня тормозного цилиндра, поддерживая постоянные зазоры между колодками и колесами.
Проверяя на стенде действие регулятора на стягивание рычажной, передачи, необходимо маховик 18
повернуть по часовой стрелке на один-два оборота, чтобы между упором 16
и колодкой 17
образовался зазор 8—16 мм. Затем производят при помощи крана 8
полное служебное торможение с последующим отпуском, в результате чего регулятор должен сократиться по длине на величину до 8—10 мм и стянуть рычажную передачу. Проверку величины стягивания (также и роспуска) производят замером рабочего хода регулирующего винта. Операцию стягивания следует повторить еще 1—2 раза.
На исправный регулятор после испытания устанавливают металлическую бирку, на которой выбивается клеймо, присвоенное ремонтному пункту, и дата проведения испытания. Бирку закрепляют болтом, стопорящим головку на корпусе регулятора. Результаты испытания записывают в отдельный журнал.
Нерабочие поверхности отремонтированного и испытанного авторегулятора окрашивают битумным лаком и устанавливают регулятор в вертикальном положении ушком вниз на стеллаж готовой продукции.
Монтаж авторегулятора на вагоне ипроверка его действия.
Перед установкой на вагон регулирующий винт авторегулятора должен быть вывернут таким образом, чтобы расстояние от конца защитной трубы 8
до риски на регулирующем винте было в пределах а = 500 мм. При постановке на вагон, оборудованный рычажным приводом, авторегулятор нужно положить на предохранительную скобу 3,
ушко 2
пропустить между планками рычага-упора 10
и установить между горизонтальными рычагами 11.
Затем вставить в отверстие валик , надеть на него шайбу и закрепить шплинтом.
После этого навертывают на регулирующий винт 4
муфту 6,
ставят квадратную шайбу 5 и шплинт 7. Регулировка размера А
производится перемещением гаек 9
с последующей проверкой величины выхода штока тормозного цилиндра (производится полное служебное торможение).
При постановке авторегулятора на вагон, оборудованный стержневым приводом, операции по креплению ушка регулятора и конца регулирующего винта такие же, как при постановке на вагон с рычажным приводом. После закрепления регулятора стержень 13
привода одним концом ввертывают в упор 12,
а другим — в палец 14
с постановкой контргаек 15.
Величину размера А
при стержневом приводе регулируют перемещением гаек 15
и вращением стержня 13
с обязательной последующей проверкой выхода штока поршня тормозного цилиндра при полном служебном торможении.
После установки регулятора на вагон проверяется стабильность его действия, а также действие на стягивание тормозной рычажной передачи вагона.
Для проверки на стабильность действия на конец защитной трубы 8
и поверхность регулирующего винта 4
наносят мелом продольную и поперечную риски. Затем производят 2 раза торможение при давлении в тормозном цилиндре 1 —1,2 кгс/см2
. Если при этом риски не смещаются, значит, регулятор работает нормально и поддерживает постоянный выход штока поршня тормозного цилиндра.
Во время проверки действия авторегулятора на стягивание рычажной передачи корпус его поворачивают на 1—2 оборота против часовой стрелки, затем производят полное служебное торможение и отпуск. После этого регулятор должен сократить первоначальную величину а
рабочего хода винта на 8—10 мм.
В случае неправильного действия регулятора при любой из проверок он должен быть заменен и направлен в АКП для повторного ремонта.
Карта технологического процесса представлена в графической части курсового проекта на листе 3.
5. ТРЕБОВАНИЯ ТЕХНИКИ БЕЗОПАСНОСТИ И ОХРАНЫ ТРУДА
5.1 Общие положения
При ремонте тормозного оборудования в АКП должны соблюдаться требования, предусмотренные Правилами техники безопасности и производственной санитарии при техническом обслуживании и ремонте вагонов № ПОТ РО32-ЦВ-400-96., Правил пожарной безопасности на железнодорожном транспорте, требований техники безопасности, изложенных в местных инструкциях и указаниях МПС РФ и управления дороги.
За организацию в соответствии с требованиями техники безопасности и состояние охраны труда в цехе несут ответственность мастер АКП и бригадиры цеха.
Мастер АКП организует обучение и проверку знаний по охране труда в соответствии с Положением по организации обучения и проверки знаний по охране труда на железнодорожном транспорте №ЦСР-325-85.
Каждый работник цеха обязан знать и строго выполнять требования Правил, Инструкций по техники безопасности и производственной санитарии, пользоваться спецодеждой и предохранительными устройствами и приспособлениями, содержать в чистоте и порядке свое рабочее место, соблюдать чистоту в цехе. Рабочая одежда должна соответствовать требованиям ГОСТ 12.4.103-83.
Коллективные и индивидуальные средства защиты работающих должны отвечать требованиям ГОСТ 12.4.011-75.
В случае повреждения механизмов, приспособлений, оборудования или получения травмы, нарушения техники безопасности работник должен немедленно сообщить об этом мастеру цеха.
5.2 Требования к технологическому оборудованию
Все производственное оборудование должно отвечать требованиям ГОСТ 12.1.003-83, ГОСТ 12.2.003-91, ГОСТ 12.2.022-80.
Все узлы и детали тормозного оборудования, при поступлении в ремонт, должны тщательно очищаться и обмываться в моечной машине. Запрещается подача в ремонт неочищенные тормозные приборы и арматура.
Для обеспечения безопасных условий труда электродвигатели, пусковая аппаратура и все другие части оборудования и моечной машины, которые могут находиться под напряжением, надежно заземляются и перед началом работы проверяются работниками цеха.
Для работы на моечной машине допускаются лица, обученные с устройством, эксплуатацией и технике безопасности обслуживания машин и прошедшие инструктаж на рабочем месте. Перед началом работы моечной машины работнику необходимо включить вентиляцию и перед машиной уложить деревянные решетки. Люк моечной машины должен надежно закрываться, и после обмывки приборов при включенной вентиляции открывать не ранее 5 минут. Состояние воздушной среды на производственных участках должно соответствовать требованиям ГОСТ 12.1.005-88.
На производственных участках применяют сигнальные цвета и знаки безопасности в соответствии с требованиями ГОСТ 12.4.026-76.
Конструкции предохранительных устройств на станках и испытательных стендах должны быть прочными и надежно закрепленными. Внутренние поверхности защитных ограждений окрашиваются в ярко-красный цвет, сигнализирующий об опасности в случае открытия их.
Новое или установленное после ремонта испытательное оборудование должно пройти метрологическую аттестацию и быть принятым комиссией в соответствии с Инструктивными указаниями №255-83 ПКБ ЦВ.
Оборудование, предназначенное для ремонта и испытания тормозного оборудования, должно содержаться в исправном состоянии, размещаться в предусмотренных технологическим процессом местах и не мешать свободному проходу.
Проходы и транспортные проезды должны быть свободными и иметь габаритные полосы безопасности.
Электрооборудование стендов и механизированных приспособлений для ремонта тормозного оборудования потребляющих при работе электрический ток, должно эксплуатироваться по нормам и требованиям действующих Правил технической эксплуатации электроустановок потребителей, Правил техники безопасности при эксплуатации электроустановок потребителей, Правил пользования и испытания защитных средств, применяемых в электроустановках.
Стенды и механизированные приспособления для ремонта тормозного оборудования, потребляющие при работе электрический ток, должны иметь надежное защитное заземление в соответствии с ГОСТ 12.1.030, предупредительные знаки, надписи и предохранители. Сопротивление заземления должно быть не более 4,0Ом.
Сопротивление изоляции стендов и механизированных приспособлений для ремонта тормозного оборудования, потребляющих при работе электрический ток, должно соответствовать требованиям ГОСТ 1516.1 и быть не менее 0,5 Ом.
По способу защиты от поражения электрическим током стенды и механизированные приспособления для ремонта тормозного оборудования, потребляющие при работе электрический ток, должны удовлетворять классу 01 ГОСТ 12.2.007.0.
Все провода должны прокладываться в металлических трубах или гибких металлорукавах, защищенных асбестовой тканью. Степень защиты, обеспечиваемая оболочкой, должна соответствовать 1Р ГОСТ 14254. Наращивать провода пайкой запрещается.
На изоляции проводов и кабелей не допускаются задиры, надрезы, трещины и другие механические повреждения.
Исходящие трубопроводы напорной магистрали должны иметь возможность свободного температурного удлинения, не приводящего к деформации и нарушению плотности, герметичности и целостности соединений.
Способ соединения трубопроводов должен обеспечивать плотность и исключать возможность повреждения трубопроводов. Перед началом работы на приспособлении для отсоединения концевого крана от соединительного рукава необходимо проверить техническое состояние узлов, пусковой кнопки и заземления. При отсоединении концевого крана запрещается касаться рукой корпуса концевого крана.
Перед проведением комплектовки рукавов проверить плавность передвижения узлов, механизмов, приспособлений и состояние пусковых кнопок. При комплектовке рукавов запрещается отвлекаться на посторонние работы и разговоры.
Перед началом испытания концевых и разобщительных кранов и соединительных рукавов необходимо убедиться в целостности подводящих трубок, соединений, плавность передвижения узлов и деталей приспособлений, исправности манометров и правильности установки кранов и рукавов на приспособлении.
Грузовые лифты, предназначенные для подачи узлов и деталей тормозного оборудования на ремонт и из ремонта, грузоподъемностью 200 кг, должен иметь четко проставленные предельные нагрузки крупными буквами и цифрами и трафарет о дате следующего испытания и проверки работоспособности.
5.3. Требования к инструменту и приспособлениям.
Перед началом работы работник должен проверить состояние инструмента, находящегося на рабочем месте или получаемого из инструментальной и кладовой.
Инструмент и приспособления должны отвечать требованиям стандартов и технических условий.
Места обработки деталей зубилом или другим подобным инструментом ограждают ширмами или щитками из сетки, а исполнители работ обеспечиваются защитными очками.
Мастер и бригадиры должны ежедневно проверять исправность инструмента, а исполнители перед началом работы.
Работа неисправным инструментом, неочищенным от грязи и масла и без защитных средств запрещается.
При ремонте тормозного оборудования разрешается применять переносные лампы напряжением не свыше 36В. Штепсельные соединения, применяемые на напряжение до 36В, должны отличаться от штепсельных соединений, предназначенных для напряжения свыше 36В, и иметь различную окраску.
5.4. Требования к организации рабочих мест.
Производственные помещения и рабочие места должны соответствовать требованиям Правил пожарной безопасности на железнодорожном транспорте ЦУО/112, санитарным нормам и ГОСТ 12.1.004-85, ГОСТ 12.1.010-76.
Производственные и вспомогательные помещения должны иметь искусственное и естественное освещение согласно требований СНиП П-4-79.
Во всех производственных и вспомогательных помещениях системы вентиляции и отопления должны обеспечивать выполнение требований ГОСТ 12.1.005-88, ГОСТ 12.4.021-75,СниП 2.04.05-86 и содержаться в исправном состоянии, обеспечивающем эффективное их использование.
В производственных и вспомогательных помещениях независимо от наличия вредных выделений и вентиляционных устройств должны предусматриваться открывающиеся фрамуги и другие открывающиеся устройства в окнах площадью не менее 20% общей площади световых проемов.
Окраска оборудования и приспособлений должны производиться в соответствии с требованиями Руководства по рациональному цветовому оформлению и Альбома по окраске производственных и вспомогательных помещений, оборудования, транспортных средств, коммуникаций, сооружений и инвентаря и ГОСТ 14202.
Расположение и планировка оборудования и инвентаря на рабочем месте должна обеспечивать минимальные движения рабочего в процессе выполнения заданий на данном рабочем месте.
Виды и количество технологической оснастки, находящейся на рабочем месте, должны соответствовать характеру выполняемых на нем технологических процессов и обеспечивать бесперебойную и безопасную работу в течении всего рабочего времени.
Освещенность цеха при люминесцентных лампах на уровне 0,8 м от пола должна быть не менее 200 лк, при этом может применяться также местное освещение рабочего места. (СниП 11-4-79).
Вентиляционная система цеха должна обеспечивать в любое время года такую кратность или величину объема воздуха, при которой в рабочей зоне постоянно поддерживается нормальная температура, и воздух не имеет вредных примесей выше допустимых по нормам. Рабочей зоной считается пространство высотой до 2 м над уровнем пола.
В производственных помещениях должна находиться аптечка с набором медикаментов для оказания первой до врачебной помощи.
5.5. Требования при ремонте тормозного оборудования
Отвертывание заглушек тормозных приборов и резервуаров при нахождении их под давлением не допускается.
Разборка приборов, обстукивание их молотком при нахождении их под давлением не допускается.
При обдувке деталей и их узлов сжатым воздухом после их обмывки пользоваться защитными очками.
При испытании соединительных рукавов сжатым воздухом рукав должен быть надежно закреплен и огражден предохранительным щитком.
Запрещается отвертывать заглушки тормозных приборов, находящихся под давлением.
При техническом обслуживании и ремонте электрической части электропневматического тормоза пассажирских вагонов следует руководствоваться требованиями техники безопасности, изложенными в типовом технологическом процессе ремонта тормозного оборудования вагонов.
5.6.Требования к персоналу и применению средств индивидуальной защиты
Персонал, выполняющий ремонт тормозного оборудования должен быть обучен и испытан в знаниях техники безопасности и производственной санитарии в соответствии с № ЦСР-325-85.
Все работники, связанные с ремонтом, проходят медицинское освидетельствование согласно действующих указаний МПС и приказа Минздрава РФ.
Все работники цеха обеспечиваются спецодеждой согласно приказу МПС от 18.09.90г. № 25Ц. Спецодежда, спецобувь и предохранительные приспособления должны соответствовать требованиям ГОСТов и технических условий. Сроки носки спецодежды и спецобуви и пользование предохранительными средствами исчисляются со дня фактической выдачи их рабочим. Стирка, ремонт и хранение организуется предприятием.
За счет средств депо спецодежда и спецобувь рабочих ремонтируется или заменяется в случае непригодности до истечения срока носки по причинам, не зависящим от рабочего.
Замена спецодежды и спецобуви осуществляется на основании соответствующего акта, составленного администрацией с представителем профкома.
Во время работы рабочие должны пользоваться выданной им спецодеждой, спецобувью и не допускаться к работе без них.
Рабочие получающие предохранительные приспособления, проходят специальный инструктаж по правилам пользования и способами проверки исправности этих приспособлений.
Дежурные спецодежда, спецобувь и предохранительные приспособления выдаются только на время выполнения работ, для которых они предусмотрены.
Рабочие и служащие цеха обеспечиваются мылом в соответствии с Положением о снабжении рабочих и служащих железнодорожного транспорта.
ЗАКЛЮЧЕНИЕ
Совершенствование тормозной техники в нашей стране, как правило, происходило вследствие изменения условий эксплуатации подвижного состава, что вызывало определенную временную паузу, отделявшую их от создания необходимых по характеристикам тормозных приборов. В силу этого в течение нескольких лет приходилось пользоваться устаревшими тормозными устройствами, что снижало безопасность движения поездов.
В данном курсовом проекте мы рассмотрели контрольный пункт автотормозов, с кратким описанием конструкции и ремонта автоматического регулятора. Разработали карту неисправностей и карту технологического процесса.
Поэтому наряду с авторегулятором 574Б в последнее время используется более совершенный РТРП-675 с аналогичным принципом действия. Он обеспечивает передачу усилия в 90 кН (вместо 80 кН для 574Б), имеет рабочий диапазон по стягиванию ТРП 675 мм (против 550 мм), а за один цикл торможение-отпуск максимально сокращает ее на 20 мм (ранее на 12 мм).
Кроме рассмотренных на локомотивах и моторных вагонах электропоездов используются винтовые (ЧС7), реечные (ЧС2) и пневматические автоматические регуляторы ТРП.
Библиографический список
1. Задание и методические указания по дисциплине «Автоматические тормоза вагонов» к выполнению курсового проекта студентами специальности 190302 «Вагоны» очной и заочной форм обучения / составитель: Г.Г. Киселев. – Самара: СамГАПС, 2006. – 15 с.
2. Асадченко В.Р. Автоматические тормоза подвижного состава: Учебное пособие для вузов ж.- д. транспорта. –М.: Маршрут, 2006. – 392 с.
3. Иноземцев В.Г., Абашкин И.В. Тормозное и пневматическое оборудование подвижного состава: Учебник для ПТУ.−2-е изд., перераб. и доп. –М.: Транспорт, 1984. −342 с., ил., табл.
|