Аннотация
Морозов А.М. «Реконструкция котла-утилизатора КСТ-80 с целью установки конденсационной турбины на ОАО «Урал Сталь». Дипломный проект. – Орск: ОГУ - 2007 г. - 118 стр., 13 рис., 40 табл., 22 источника литературы, 7 форматов А1.
В проекте рассмотрена возможность увеличения производства электрической энергии за счет использования тепла газов отходящих от УСТК.
Анализ энергетической системы ОАО «Урал Сталь» показал, что отходящие от УСТК газы используются в котлах-утилизаторах неэффективно.
Высокий абразивный износ предвключенных испарительных поверхностей приводит к снижению надежности работы котлоагрегата, а неэффективная работа поверхностного пароохладителя приводит к уменьшению КПД котлоагрегата.
Кроме того, на ОАО «Урал Сталь» в летний период нет потребности в перегретом паре.
В данном проекте предлагается реконструкция котлов утилизаторов КСТ-80 и преобразование котельной УСТК в энергоутилизационную мини-ТЭЦ, с установкой 2-х конденсационных паровых турбин суммарной электрической мощностью 6 МВт.
Приведены тепловой, гидравлический, конструктивный расчеты оборудования.
Кроме того, рассмотрены вопросы автоматизации, защиты окружающей среды, численности рабочих.
Проведена оценка ожидаемых технического и экономического эффектов.
Ожидаемый срок окупаемости мероприятия менее 4 лет.
Полученные результаты могут быть использованы для реконструкции существующих и вновь проектируемых УСТК.
Содержание
Введение
1 Анализ энергетического хозяйства цеха теплогазоснабжения ОАО «Урал Сталь»
1.1 Общая характеристика ЦТГС
1.2 Описание энергетического оборудования участка УСТК
1.3 Описание подсистем энергоносителей участка УСТК
1.4 Тепловой расчет котла КСТ-80 №1 УСТК
1.5 Баланс энергоносителей на участке
1.6 Анализ современного развития аналогичных производств в России и за рубежом
1.7 Постановка задачи дипломного проектирования
2 Реконструкция котла-утилизатора КСТ-80 с целью установки конденсационной турбины
2.1 Краткое описание мероприятий предлагаемых в дипломном проекте
2.2 Тепловой расчет реконструированного котла КСТ-80
2.3 Расчет впрыскивающего пароохладителя
2.4 Гидравлический расчет
2.5 Тепловой расчет паропровода
2.6 Расчет схемы электроснабжения
2.7 Энергоутилизационная мини-ТЭЦ
3 Автоматизация и механизация производственных процессов
4 Безопасность и экологичность
4.1 Анализ опасностей и вредностей на проектируемом объекте
4.2 Обеспечение безопасности труда
4.3 Предупреждение и ликвидация чрезвычайных ситуаций
5 Анализ технико-экономических показателей и обоснование экономической целесообразности принятых в проекте решений
5.1 Расчет себестоимости
5.2 Расчет объема инвестиций
5.3 Исходные данные для расчета экономических показателей
5.4 Расчет основных технико-экономических показателей
5.5 Сводный отчет об ожидаемых технико-экономических показателях проекта
Список используемой литературы
Введение
Рациональное использование топливно-энергетических ресурсов - важнейшая задача, значимость которой все возрастает. Основными направлениями экономического развития России предусмотрена программа развития топливно-энергетического комплекса и экономии энергоресурсов. В частности, планируется переход на энергосберегающие технологии производств, сокращение всех видов энергетических потерь и повышение уровня использования вторичных энергоресурсов (ВЭР).
Значительная экономия топливно-энергетических ресурсов может быть достигнута при более широком вовлечении в топливно-энергетический баланс страны вторичных энергоресурсов, имеющихся практически во всех отраслях промышленности, где применяются теплотехнические процессы, в первую очередь высокотемпературные. Коэффициент полезного теплоиспользования для многих процессов не превышает 15-35%.
Использованию ВЭР в последние годы уделяется значительное внимание.
В соответствии с принятыми методическими положениями по выявлению и направлениям использования ВЭР на промышленных предприятиях под вторичными энергоресурсами подразумевают энергетический потенциал продукции, отходов, побочных и промежуточных продуктов, образующихся в технологических агрегатах, который не используется в самом агрегате, но может быть частично или полностью использован для энергоснабжения других агрегатов. Под энергетическим потенциалом понимается наличие в указанных продуктах определенного запаса энергии (химически связанной теплоты, физической теплоты, потенциальной энергии избыточного давления).
ВЭР можно использовать в качестве топлива либо непосредственно (без изменения вида энергоносителя), либо за счет выработки теплоты, электрической энергии, холода, механической работы в утилизационных установках.
ВЭР разделяют на три основные группы:
1) горючие - побочные газы плавильных печей (доменный, колошниковый, газ шахтных печей и вагранок, конверторный и др.);
2) тепловые - физическое тепло отходящих газов технологических агрегатов; физическое тепло основной и побочной продукции; тепло рабочих тел систем принудительного охлаждения технологических агрегатов и установок; тепло шлаков, золы; тепло горячей воды и пара отработавших технологических силовых установок;
3) избыточного давления - потенциальная энергия газов, жидкостей покидающих технологические агрегаты с избыточным давлением, которое необходимо снижать перед последующей ступенью использования этих жидкостей или при выбросе их в атмосферу, водоемы, емкости и другие приемники.
Использование горючих ВЭР особых затруднений не вызывает, и они используются на промышленных предприятиях с достаточной полнотой (90-95%) и эффективностью. Использование тепловых ВЭР еще недостаточно и составляет в среднем 30-40%. Основное значение в структуре тепловых ВЭР имеет физическая теплота отходящих газов теплотехнических установок, доля которой в общем балансе возможного использования тепловых ВЭР составляет 75%.
Вторичными энергоресурсами располагают практически все отрасли промышленности, в которых имеются теплотехнические установки.
Таблица 1 - Использование ВЭР в промышленности /1, 43/
Отрасль
|
Виды ВЭР
|
Использование (%)
|
Черная
металлургия
|
Горючие
Тепловые
|
74,3
25,7
|
Цветная
металлургия
|
Горючие
Тепловые
|
6,1
93,9
|
Химическая
промышленность
|
Горючие
Тепловые
|
17,4
82,6
|
Газовая
промышленность
|
Горючие
Тепловые
|
19,3
80,7
|
Нефтеперерабатывающая и нефтехимическая промышленность
|
Горючие
Тепловые
|
53,0
47,0
|
Таким образом, из таблицы 1 видно, что в черной металлургии доля использования тепловых ВЭР чрезвычайно мала.
Из графика на рисунке 1, видно, что черная металлургия является крупнейшим потребителем ВЭР. Основным оборудованием для использования тепловых ВЭР, а также избыточного давления являются: котлы-утилизаторы (КУ), системы испарительного охлаждения (СИО), охладители конвертерных газов (ОКГ), установки сухого тушения кокса (УСТК), газовые утилизационные бескомпрессорные турбины (ГУБТ), адсорбционные холодильные машины.
Котлы-утилизаторы в установках сухого тушения кокса
Котлы-утилизаторы в коксохимическом производстве в комплексе с тушильным устройством предназначены для использования физической теплоты раскаленного кокса и его сухого тушения. В тепловом балансе коксовой батареи теплота, уносимая раскаленным коксом, достигает 45-50% количества теплоты, поступающей на обогрев печи.
На каждый миллион тонн произведенного кокса при мокром тушении теряется примерно 50 тыс. тонн условного топлива. Поэтому использование физической теплоты раскаленного кокса имеет большое значение. Одним из таких способов является сухое тушение кокса, которое дает возможность не только использовать физическую теплоту раскаленного кокса для получения пара энергетических параметров, значительно повысить качество кокса, технико-экономические показатели доменного процесса, но также улучшить условия труда в коксовых цехах, уменьшить загрязнение окружающего воздушного бассейна.
Опыт эксплуатации доменных печей показывает, что при использовании кокса сухого тушения удельный расход его снижается примерно на 10% по сравнению с удельным расходом при применении кокса мокрого тушения. Таким образом, общая экономия условного топлива от использования физической теплоты раскаленного кокса и улучшении эффективности доменного процесса (в результате использования кокса сухого тушения) составляет 110×103
тонн на каждый миллион тонн произведенного чугуна.
На больших газовых заводах и коксохимических производствах металлургических заводов, выпускающих тысячи тонн кокса в сутки, вопрос о наиболее выгодном способе использования тепла раскаленного кокса зависит от потребности в том или ином виде энергии и от стоимости энергии, получаемой со стороны. От правильного выбора способа использования уловленного тепла кокса зависят прежде всего сроки окупаемости капитальных затрат на сооружение установок сухого тушения и рентабельность последних.
Тепло УСТК используется для получения пара, расходуемого на технологические нужды производства. Это объясняется тем, что производительность большинства установок небольшая, а пар, вырабатываемый в таких УСТК, может быть полностью использован на месте.
При крупных бункерных установках целесообразно комбинировать выработку электрической энергии и тепловой в виде пара для технологических нужд. В таких комбинированных установках водяной пар энергетических параметров, получаемой в котлах УСТК, можно направлять в конденсационные турбины с промышленными и теплофикационными отборами или в турбины с противодавлением (в зависимости от энергетического баланса данного предприятия). В обоих случаях паровые турбины служат приводами электрических генераторов /1, 56/.
Разработка мер по использованию пара за счет ВЭР на технологические нужды, производство электроэнергии, теплоснабжение в комбинированных схемах требует детального изучения тепловых балансов производства и создания типовых решений с учетом технико-экономического обоснования по использованию пара от котлов. Параметры пара также зависят от стабильности работы (технологического режима) основного теплотехнического устройства. Технико-экономическое обоснование должно производиться при выборе типа котла для каждого конкретного случая.
Установка сухого тушения кокса состоит из двух основных частей (рисунок 2) - тушильной камеры (1) и парового котла (2). Раскаленный кокс скиповым подъемником загружается в тушильную камеру. Через щели в конической нижней части тушильной камеры, заполненной коксом, в нее поступают инертные газы, двигаясь навстречу коксу, охлаждают его от 1300 до 500 К, и сами нагреваются от 425-440 до 1000-1100 К. Нагретые инертные газы выходят через окна, расположенные в верхней части камеры, проходят через пылеуловительный бункер и поступают в котел, после котла газы проходят пылеуловительные циклоны (4) и поступают на всас мельничного вентилятора (3). В котле газы последовательно омывают пароперегреватель, секции испарительных поверхностей нагрева и экономайзер.
1 Анализ энергетического хозяйства цеха теплогазоснабжения (ЦТГС) ОАО «Уральская Сталь»
1.1 Общая характеристика ЦТГС
1.1.1 Общая характеристика энергохозяйства
Высокий температурный уровень основных технологических процессов металлургического производства и низкий коэффициент использования тепла топлива технологическим агрегатом предопределяет большой выход вторичных энергоресурсов. При большом объеме металлургического производства рациональное использование вторичного тепла является важной производственной задачей, так как экономия топлива идентична увеличению на ту же величину его добычи, а капитальные вложения на сооружение соответствующих теплоутилизационных установок намного меньше, чем на добычу топлива и теплогенераторные установки на топливе.
Перспективным является комплексное использование тепла отходящих газов и тепла испарительного охлаждения печи. При этом котел-утилизатор и охлаждаемые элементы печи объединяются общей циркуляционной системой.
Получение пара за счет тепла отходящих газов мартеновских, методических печей, установок сухого тушения кокса в общем случае экономичнее, т.к. обычно пар используется круглогодично для технологических нужд и при теплофикации ценность его тепла выше, чем тепла сетевой воды.
Цех теплогазоснабжения включает в себя:
1) Участок котлов-утилизаторов (КУ) проката.
За группой нагревательных методических печей стана 950/800 и стана 2800 применены комплексные утилизационные установки, представляющие собой для каждой печи котлы-утилизаторы КУ-100 и КУ-80 соответственно, с многократной принудительной циркуляцией, и систему испарительного охлаждения печи, совмещенные в единую установку, в которой охлаждаемые элементы печи включены в циркуляционную систему котла параллельно его испарительной системе. В здании первого листопрокатного цеха (ЛПЦ-1) расположена питательная установка, являющаяся общей для всего комплекса утилизационных установок прокатного цеха. Каждый из котлов КУ-100 при среднем режиме работы нагревательных печей вырабатывает с учетом испарительного охлаждения печи 33,9 т/ч перегретого пара с параметрами Р=1,2 МПа и температурой Т=360 ºС. Пар, вырабатываемый котлами-утилизаторами, направляется в общезаводскую сеть паропроводов, а часть пара редуцируется и используется на нужды питательной установки.
2) Установка сухого тушения кокса совместно с котлами КСТ-80.
Котельная установка сухого тушения кокса батарей №№5, 6 предназначена для выработки пара за счет использования тепла инертных газов сухого тушения кокса. Соответственно количеству кокса поступающего на тушение, в котельной вырабатывается 63 т/ч перегретого пара следующих параметров: давление Р=1,8 МПа и температура перегрева до 450 ºС. Полученный пар используется на технологические нужды Общества.
3) Котельные за мартеновскими печами.
Котлы-утилизаторы КУ-80/120 предназначены для охлаждения уходящих дымовых газов мартеновских печей и получения перегретого пара с давлением Р=1,6-1,8 МПа, с температурой до 375 ºС. Температура уходящих газов после котлов-утилизаторов 180-250 ºС. Для удаления плавильной пыли с конвективных поверхностей нагрева предусмотрена импульсная очистка.
4) Газоочистка за мартеновскими печами.
За мартеновскими печами №№3, 4, 6, 7 установлены электрофильтры. Перед электрофильтром установлена эжекционная система кондиционирования. За двухванными сталеплавильными агрегатами ДСПА-1 и ДСПА-9 установлены газоочистки с регулируемой трубой Вентури.
5) Мазутное хозяйство (снабжение мартеновских печей мазутом, хранение мазута).
6) Участок тепловых сетей (обслуживание магистральных трубопроводов пара и горячей воды).
7) Электрослужба (обслуживание и ремонт электрооборудования ЦТГС).
8) Участок подготовки ремонтов.
9) Газовый участок.
1.1.2 Этапы развития ЦТГС
Ниже приводится таблица, показывающая этапы развития ЦТГС по годам, начиная с 1960 года.
Таблица 2 - Этапы развития ЦТГС
Год
|
Мероприятие
|
1960-1961
|
пущены в работу 4 КУ стана «2800»
|
1961-1965
|
оснащены КУ все мартеновские печи
|
1960
|
перевод методических печей ЛПЦ-1 на СИО
|
1958-1967
|
перевод мартеновских печей на СИО
|
1969
|
пущены в работу 3 КУ на СПЦ
|
1969
|
перевод мартеновских печей на СИО
|
1968-1970
|
пуск 4 КУ КСТ-80 на УСТК
|
1980
|
пуск 4-го КУ на СПЦ
|
1980
|
демонтаж КУ за мартеновской печью №9
|
1996-1998
|
демонтаж КУ за мартеновскими печами №№1, 5, 8
|
2005
|
объединение газового и теплосилового цехов, образование ЦТГС
|
Цех теплогазоснабжения является крупным структурным подразделением ОАО «Урал Сталь», обеспечивающим паром энергетических параметров другие структурные подразделения комбината. Кроме того, на балансе цеха теплогазоснабжения находятся тепловые сети, обеспечивающие сетевой водой на нужды отопления и вентиляции не только комбинат, но и город Новотроицк.
1.2 Описание энергетического оборудования участка УСТК
1.2.1 Устройство, техническая характеристика и принцип работы котла- утилизатора КСТ-80
Котел-утилизатор КСТ-80 конструкции «Укрэнергочермета» установки сухого тушения кокса - однобарабанный, змеевикового типа с многократной принудительной циркуляцией. Поверхности нагрева расположены в вертикальной шахте. Направление потока греющих газов сверху вниз (нисходящий поток). Скорость газового потока не должна быть выше 7 м/сек, во избежание истирания металла трубок поверхностей нагрева котла мелкой фракцией кокса, уносимой потоком циркуляционного газа из тушильной камеры. Газоход котла выполнен из металлических листов, сваренных между собой для создания газоплотности, во избежание присосов воздуха, повышения содержания кислорода в газах, влекущего за собой усиление горения кокса в камере тушения. В зонах высоких температур (пылеосадительный бункер, газоход котла в районе пароперегревателя и испарительной поверхности) металлический кожух газохода изнутри выложен огнеупорным кирпичом.
Котел состоит из следующих частей:
1) барабана (диаметр 1 600 мм, длина 5 500 мм), в барабане расположены устройства: для ввода реагентов для внутрикотловой обработки воды, отвода воды непрерывной и периодической продувок, испарительные устройства, состоящие из двух приемных отсеков, в которых установлены отбойные щиты, паросборного коллектора, защитного устройства водоотводящих труб.
2) двух блоков (четырех пакетов), последовательно соединенных, водяного экономайзера. Входной блок экономайзера состоит из пакетов, над которыми расположены два пакета выходного блока экономайзера, блоки расположены последовательно по ходу газов. Каждый пакет состоит из 26 параллельно включенных змеевиков из трубы диаметром 25×3 мм. Входные и выходные коллектора экономайзера расположены в газоходе котла, входные камеры в зоне температур около 160°С, а выходные в зоне температур порядка 300 °С.
3) двух блоков (четырех пакетов), последовательно соединенных, испарительной поверхности. Входные коллектора испарительной секции расположены в газоходе котла, в зоне температур газов около 300 °С.
4) двух последовательно соединенных пакетов пароперегревателя, со встроенным пароохладителем. Пакеты расположены первыми по ходу газов горизонтально в вертикальной шахте, за поворотной камерой.
5) котлы №№1, 2, 3 имеют экранные испарительные пучки труб (солому). Верхняя часть экранной поверхности образует двухтрубный шахматный пучок труб над пароперегревателем, который переходит затем в настенные, двухсветные экраны в области поворотного газохода. Экранные поверхности состоят из труб диаметром 166×2, параллельно включенных змеевиков из трубы диаметром 25×3 мм. Выходные участки труб проходят через обмуровку потолочного перекрытия и привариваются непосредственно к штуцерам барабана котла. На котле №4 произведена реконструкция испарительной поверхности, и экранная часть отсутствует, котловая вода после верхней испарительной секции собирается в коллекторах и по восьми трубам подается в барабан котла.
6) трубопроводы в пределах котла:
а) подводящие трубопроводы питательной воды;
б) отводящие трубопроводы испарительного контура;
в) трубопроводы насыщенного и перегретого пара;
г) трубы периодической и непрерывной продувок, линия фосфатирования
7) запорная, регулирующая, предохранительная и защитная арматура.
К вспомогательному оборудованию котла относятся:
а) циркуляционные насосы типа НКУ-250 (по два на каждом котле);
б) мельничный дутьевой вентилятор типа ВМ-160/850;
в) резервный дымосос типа ДН-12 (работает только при аварийном отключении мельничного вентилятора).
Специальная щитовая обмуровка и металлическая обшивка котла отвечают требованиям повышенной плотности. В зоне высоких температур (выше 450 °С) обмуровка трехслойная (огнеупорный бетон, термоизоляционный бетон, совелитовые плиты). В ходе проведения ремонтов огнеупорные бетоны в районе коллекторов пароперегревателя и стен, вдоль испарительных поверхностей нагрева, обращенных внутрь котельной, заменены на огнеупорный кирпич - шамотный и динасовый. Металлические щиты обшивки котла имеют наружную тепловую изоляцию в виде минераловатных прошивных матов покрытых сверху металлическим (алюминиевым) покровным слоем.
1.2.2 Тепловая характеристика котла-утилизатора КСТ-80
Ниже приводится таблица, отражающая краткие тепловые характеристики котлов-утилизаторов КСТ-80 №№1, 2, 3, 4. Таблица составлена на основе технологической инструкции.
Таблица 3 - Тепловая характеристика котлов-утилизаторов КСТ-80
Наименование параметра
|
Единицы измерения
|
Показатель
|
КУ №1, 2, 3
|
КУ №4
|
1
|
2
|
3
|
4
|
Рабочее давление в барабане котла
|
кгс/см2
|
18; 18; 25
|
25
|
Паропроизводительность
|
т/ч
|
25
|
25
|
Допустимая температура перегретого пара в промежуточной камере
|
°С
|
450
|
450
|
Температура пара в промежуточной камере
|
°С
|
370
|
370
|
Количество греющих продуктов сгорания (расчетная)
|
м3
/ч
|
82100
|
82100
|
Продолжение таблицы 3
|
1
|
2
|
3
|
4
|
Температура греющих продуктов сгорания перед котлом
|
°С
|
800
|
750
|
Температура греющих продуктов сгорания перед испарительной поверхностью
|
°С
|
650
|
600
|
Температура греющих продуктов сгорания перед экономайзером
|
°С
|
до 300
|
до 300
|
Температура греющих продуктов после экономайзера
|
°С
|
160-220
|
160-220
|
Температура воды на входе в
экономайзер
|
°С
|
74-104
|
74-100
|
КПД котлоагрегата
|
%
|
80,8
|
81,5
|
Потери тепла:
с уходящими газами
в окружающую среду
|
%
%
|
до 20
до 0,6
|
до 20
до 0,6
|
Гидравлическое сопротивление
котла
|
кгс/см2
|
3,5
|
3
|
Гидравлическое сопротивление
пароперегревателя
|
кгс/см2
|
2-2,5
|
2-2,5
|
Аэродинамическое сопротивление котла
|
мм.вод.ст
|
80-100
|
80-100
|
Паровой объём котла
|
м3
|
7,3
|
7,3
|
Водяной объём котла
|
м3
|
12,8
|
12,5
|
Количество циркуляционной
воды, до
|
т/ч
|
250
|
250
|
1.2.3 Технологическая схема УСТК
Установка сухого тушения кокса представляет собой сложный единый технологический агрегат, условно состоящий из двух основных частей:
1) тушильной камеры;
2) парового котла-утилизатора со вспомогательным оборудованием для очистки циркуляционных газов от угольной пыли (пылеосадительный бункер для очистки от крупных частиц, циклонов для очистки от мелких частиц), соединительных газоходов и вспомогательных тягодутьевых устройств (основного и вспомогательного дымососов).
Всего УСТК ОАО «Уральская Сталь» оснащено четырьмя агрегатами сухого тушения кокса.
Принцип работы установки сухого тушения кокса заключается в следующем:
1) через щель в нижней конической части сушильной камеры, заполненной горячим коксом, с помощью мельничного вентилятора ВМ-160/850 нагнетается инертный газ, смешанный с продуктами горения кокса (далее циркуляционный газ);
2) циркуляционный газ имеет следующие усредненные значения составных компонентов (данные из технологической инструкции):
азот N2
|
– от 65 до 75 %
|
окись углерода СО
|
– от 8 до 12%
|
водород Н2
|
– от 3 до 5 %
|
двуокись углерода СО2
|
– от 7 до 14 %
|
кислород О2
|
– до 2%
|
метан СН4
|
– от 0,5 до 4 %
|
3) газы, двигаясь на встречу загруженному сверху коксу, нагревается, одновременно его охлаждая;
4) нагретые газы выходят через верхние окна тушильной камеры и поступают в пылеосадительный бункер. За счет резкого изменения, объёма в бункере происходит выпадение крупных частиц кокса;
5) из пылеосадительного бункера циркуляционный газ поступает в котёл- утилизатор, где последовательно омывает поверхности нагрева котла (на котлах №1, 2, 3 - экранные испарительные трубки), пароперегреватель, испарительные секции, водяной экономайзер, проходя через которые охлаждается, передавая тепло воде, проходящей внутри труб поверхностей нагрева;
6) после котла-утилизатора циркуляционный газ проходит через газораспределительный короб, распределяется на два потока и по восходящим газоходам поступает на циклоны;
7) проходя через циклоны газ, очищенный от более мелких частиц угольной пыли, поступает в общий газоход и подводится на всас мельничного вентилятора;
8) за счет центробежной силы, создаваемой вентилятором, циркуляционный газ приобретает дополнительную энергию напора и вновь под давлением подаётся в нижнюю часть тушильной камеры;
9) для поддержания заданного количества инертного газа, недопущения подсосов кислорода из воздуха и восполнения утечек инертного газа через неплотности, свечи и др., на всас дутьевого вентилятора производится подача азота - из магистрального азотопровода;
10) осажденные в бункере и циклонах частицы коксовой пыли через систему мигалок сбрасываются в трубопровод гидрозолоудаления.
Здание котельной делится помещением щитов управления КИПиА и подстанцией на две части, в каждой из которой размещаются два котлоагрегата.
В служебном отделении УСТК располагается всё вспомогательное оборудование котельной: на первом этаже - питательные насосы, установка фосфатирования, щит управления питательной установкой; на втором этаже - расположены трубопроводы подвода химочищенной воды, теплообменник; на третьем этаже расположены деаэраторы, трубопроводы пара и воды, сепараторы непрерывной продувки.
1.2.4 Устройство и принцип работы циркуляционного насоса
Циркуляционный насос предназначен для принудительной циркуляции воды в водяном контуре котла-утилизатора.
Насос состоит из приводной и проточной частей. Приводная часть состоит из опорного кронштейна, в котором на подшипниках установлен вал насоса. Подшипники закрыты крышками. Проточная часть состоит из спирального корпуса, который крепится к фланцу опорного кронштейна, рабочего колеса, насаженного на конец вала, и всасывающего патрубка, присоединенного к спиральному корпусу.
Спиральный корпус служит для преобразования кинетической энергии жидкости после рабочего колеса в энергию давления. Насосы поставляются с напорным патрубком, направленным вертикально вверх.
Рабочее колесо служит для передачи механической энергии двигателя потоку жидкости. Оно выполнено из двух дисков соединенных лопатками; передний диск, с входным отверстием. Рабочее колесо имеет уплотняющий поясок, который в паре с уплотнительным кольцом, запрессованным во всасывающем патрубке, образует уплотнение, служащее для уменьшения перетока жидкости из области высокого давления в область низкого давления.
Всасывающий патрубок служит для подвода перекачиваемой жидкости к рабочему колесу. Он крепится к спиральному корпусу и является его причиной. На фланце патрубка имеется резьбовое отверстие для присоединения манометра, заглушаемое при поставке пробкой.
Сальниковое уплотнение насоса служит для уплотнения вала в месте выхода из корпуса и состоит из отдельных колец, установленных с относительным смещением разрезов по 120 градусов.
1.2.5 Технические параметры насоса НКУ-250
Основные технические параметры циркуляционных насосов приведены в таблице 4, данные приводятся на основе технологической инструкции, паспорта агрегата.
Таблица 4 - Техническая характеристика насоса НКУ-250
Наименование показателя
|
Единицы
измерения
|
Показатель
|
1
|
2
|
3
|
Производительность
|
м3
/ч
|
250
|
Создаваемый напор
|
м.вод.ст
|
32
|
Частота вращения
|
об/мин
|
1450
|
Мощность электропривода
|
кВт
|
45
|
Допустимая температура перекачиваемой воды
|
°С
|
255
|
Характеристика качества перекачиваемой воды:
значение РН
содержание механических примесей при размере не более 0,1 мм
|
-
%
|
8-9
до 0,1 по массе
|
1.2.6 Технологическая схема работы деаэрационно-питательной установки (ДПУ) участка котлов-утилизаторов за УСТК
В ДПУ участка входят:
1) два деаэратора атмосферного типа с трубопроводами обвязки химочищенной воды, пара, сброса дренажных вод, устройств защиты (гидрозатворов) и охладителей выпара, включенных в тепловую схему деаэратора;
2) группа питательных насосов котлов-утилизаторов из четырех штук;
3) водоводяной кожухотрубчатый теплообменник;
4) сепараторы непрерывной продувки в количестве двух штук;
5) узлы ввода и разводки трубопроводов обвязки химочищенной, деаэрированной питательной воды, 7-ми и 16-ти атмосферного паропровода;
6) первичные приборы измерения и контроля, системы автоматического регулирования и управления технологическим процессом, и щитов управления КИПиА;
7) установка ввода дозирования корректирующих реагентов (фосфата) в питательную воду.
Химочищенная вода с химводоочистки №1 теплоэлектроцентрали, по двум трубопроводам поступает на ДПУ участка котлов-утилизаторов за УСТК, откуда через узел ввода через теплообменник, по двум ниткам подается на верхние сита деаэрационной колонки. Проходя деаэрационную колонку, деаэрированная вода накапливается в баке-аккумуляторе. Далее деаэрированная вода по сборным трубопроводам подаётся на кожухотрубчатый теплообменник, где происходит снижение её температуры до 70 ºС и далее по всасывающим трубопроводам подаётся на общий сборный коллектор деаэрированной воды и далее на всас питательных насосов. Группа питательных насосов обеспечивает подачу деаэрированной питательной воды по двум напорным трубопроводам с давлением 56-66 кгс/см2
. Для поддержания требуемого давления в напорных трубопроводах, регулирование может осуществляться за счет включения дополнительного насоса, переходя с насоса большей производительности на насос с меньшей производительностью, а также за счет перепуска воды из напорных трубопроводов в безнапорную часть бака-аккумулятора деаэрационной установки по линии рециркуляции.
Для обеспечения процесса термической деаэрации (обескислороживания) в ДПУ подведены трубопроводы 7-ми, 16-ти атмосферного пара и сепарационного пара от сепараторов непрерывной продувки котлов. Основной подвод пара на деаэрацию осуществляется из магистрального паропровода 7-ми атмосферного пара. В качестве резервного, на ДПУ имеется подвод 16-ти атмосферного пара, взятый из паропровода котельной от котлов-утилизаторов за УСТК.
Загрязнённый кислородом пар (выпар) проходя через охладители выпара отдаёт тепло химочищенной воде, конденсируется и сбрасывается в канализацию. Для обеспечения режима пуска и остановки деаэраторов, а также для сброса выпара в случае необходимости отключения охладителя выпара или в случае его неисправности, предусмотрен прямой отвод выпара в атмосферу.
1.2.7 Устройство и принцип действия деаэратора
Деаэратор состоит из бака-аккумулятора, деаэрационной колонки, устройств защиты деаэратора от превышения давления пара и уровня воды.
В деаэрационной колонке применена двухступенчатая система деаэрации: первая ступень - струйная, вторая ступень - барботажная. Потоки воды, подлежащие деаэрации, подаются на верхнюю перфорированную тарелку. С неё вода стекает на расположенную ниже перепускную тарелку, откуда узким пучком струй увеличенного диаметра сливается на начальный участок непровального, барботажного листа. Затем вода проходит по барботажному листу в слое, обеспечиваемом переливным порогом, и через трубу самотеком сливается под уровень воды в бак-аккумулятор, после выдержки в котором отводится из деаэратора по трубе на питательные насосы.
В деаэратор предусмотрено три подвода пара:
1) через один пар поступает в верхнюю часть бака-аккумулятора, вентилирует паровой объём бака и попадает под барботажный лист. При увеличении тепловой нагрузки деаэратора срабатывает гидрозатвор пароперепускного устройства, через который избыточный пар перепускается в струйный отсек барботажного устройства третьей тарелки деаэрационной колонки;
2) часть пара подаётся по перфорированной трубе в деаэрационную колонку на дополнительное барботажное устройство, после которого пар также попадает в барботажный отсек;
3) подвод пара на барботажный подогрев в нижнюю часть бака-аккумулятора предназначен для прогрева деаэратора на предпусковых режимах работы, а также для догрева воды до необходимых параметров в баке-аккумуляторе;
4) парогазовая смесь отводится из деаэратора через патрубок отвода. В струях осуществляется подогрев воды до температуры близкой к температуре насыщения, удаления основной массы газов и конденсации большей части пара, подводимого в деаэратор, частичное выделение газов из воды в виде мелких пузырьков идет на тарелках. На барботажном листе осуществляется догрев воды до температуры насыщения с незначительной конденсацией пара и удаление микроскопических газов. Процесс дегазации завершается в деаэраторном баке, где происходит выделение из воды мелких пузырьков газов за счет отстоя.
1.2.8 Техническая характеристика деаэратора ДА-200
Техническая характеристика деаэраторов установленных на участке УСТК приведена в таблице 5, данные приводятся на основе технологической инструкции, паспорта агрегата.
Таблица 5 - Техническая характеристика деаэратора ДА-200
Наименование показателей
|
Единицы измерения
|
Значение
|
1
|
2
|
3
|
Производительность
|
т/час
|
200
|
Абсолютное давление
|
МПа (атм)
|
0,12 (1,2)
|
Продолжение таблицы 5
|
1
|
2
|
3
|
Температура деаэрированной воды
|
°С
|
104,2
|
Остаточная массовая доля кислорода в
деаэрированной воде
|
мкг/кг
|
20
|
Остаточная массовая доля свободной
углекислоты в деаэрированной воде
|
мкг/кг
|
отсутствует
|
Номинальный удельный расход выпара
|
кг/т.д.в.
|
1,2-0,3
|
Максимальный и минимальный подогрев воды, требуемый качеством воды
|
°С
|
64-104
|
Диапазон изменения производительности, в пределах которого гарантируется устойчивая работа и требуемое качество
деаэрированной воды
|
%
|
30-120
|
Ёмкость бака-аккумулятора
|
м3
|
35
|
Диапазон изменения начальной массовой доли кислорода в исходной воде, в пределах которого обеспечивается требуемое качество воды
|
мг/кг
|
0,02-15
|
Диапазон изменения начальной массовой доли свободной углекислоты в исходной воде, в пределах которого обеспечивается требуемое качество воды
|
мг/кг
|
0,5-10
|
Диапазон изменения бикарбонатной щелочности, в пределах которой гарантируется остаточная массовая доля свободной углекислоты в деаэрированной воде
|
мгэкв/кг
|
0,4-0,7
|
1.2.9 Устройство и принцип действия питательного насоса типа ПЭ
Выбор производительности и создаваемого напора насоса производится из расчета, номинальной потребности котлов-утилизаторов в питательной воде с запасом прочности не менее 10%, обеспечения требуемого давления на преодоление гидравлического сопротивления в трубопроводах и элементах, подъёма воды на высоту и преодоления избыточного давления в барабанах. Ротор насоса приводится в действие электродвигателем через упругую втулочно-пальцевую полумуфту.
Принцип действия питательного насоса типа ПЭ основан на действии центробежных сил. Вращаясь, рабочее колесо, сообщает круговое движение жидкости, находящейся между лопатками рабочего колеса. Вследствие возникающей при этом центробежной силы, жидкость от центра рабочего колеса перемещается к внешнему выходу, а освобождающееся пространство вновь заполняется жидкостью, поступающей из всасывающего трубопровода под действием атмосферного давления или подпора. Выйдя из рабочего колеса, жидкость поступает в каналы направляющего аппарата, а затем во второе рабочее колесо с давлением, созданным в первой ступени, оттуда жидкость поступает на третье колесо и т.д. Вышедшая из последнего рабочего колеса жидкость проходит через направляющий аппарат и поступает в напорный трубопровод.
Питательные насосы служат для подачи химически очищенной воды через экономайзер в барабан котла.
1.2.10 Техническая характеристика питательного насоса
Техническая характеристика питательных насосов ПЭ-100-53 и ПЭ-100-56 приведена в таблице 6, данные приводятся на основе технологической инструкции, паспорта агрегата.
Таблица 6 - Техническая характеристика питательных насосов
Наименование показателя
|
Единицы измерения
|
ПЭ-100-53
|
ПЭ-100-56
|
1
|
2
|
3
|
4
|
Количество
|
шт.
|
2
|
2
|
Подача
|
м3
/ч
|
100
|
100
|
Напор
|
м.вод.ст.
|
530
|
560
|
Частота вращения
|
об/мин
|
2 980
|
2 980
|
Допустимый ковитационный запас
|
м.вод.ст.
|
не более 4
|
до 4
|
Мощность насоса
|
кВт
|
210
|
240
|
КПД не менее
|
%
|
69
|
69
|
Температура перекачиваемой воды
|
К (°С)
|
438 (165)
|
433 (160)
|
Расход воды на охлаждение подшипников и сальников насоса
|
м3
/с (м3
/ч)
|
0,0014 (5)
|
0,0014 (5)
|
Мощность электродвигателя
|
кВт
|
315
|
320
|
Напряжение на электродвигатель
|
В
|
3 000
|
3 000
|
1.2.11 Устройство и принцип действия сепаратора непрерывной продувки
Для использования тепла продувочных вод на деаэрацию в ДПУ участка котлов-утилизаторов за УСТК установлены сепараторы непрерывной продувки с котлов-утилизаторов №1-4.
Сепаратор состоит из корпуса, улитки, пластинчатого каплеулавливателя, регулятора выхода продувочной воды, выхода отсепарированного пара, отвода к предохранительному клапану, водомерного стекла, трубопроводов отвода дренажей.
Принцип действия сепаратора основан на выделении пара и конденсата из продувочной эмульсии, удаляемой из котлов-утилизаторов с непрерывной продувкой, за счет резкого изменения (увеличения) объёма в расширителе (корпусе сепаратора) и соответственно падения давления подаваемой продувочной среды до давления в расширителе.
Продувочная вода с давлением равным давлению пара в барабане котла-утилизатора по общему коллектору продувочной воды поступает на вход продувочной воды в сепаратор. За счёт тангенциального расположения входа продувочной воды поток приобретает вращательное движение, за счёт чего происходит интенсивное разделение пароводяной эмульсии на пар и воду, имеющие различные значения плотности, у противоположных стенок улитки сепаратора. Проходя через щель в улитке, поток попадает во внутреннее пространство корпуса сепаратора (расширитель). За счет резкого изменения объёма, давление подаваемой воды падает и происходит вскипание перегретой воды.
Пар, отсепарированный в улитке, и пар выделившийся при вскипании жидкости поступает в верхнюю паровую часть сепаратора, проходят каплеуловитель, где освобождается от частичек воды захваченных потоком пара и далее по трубопроводу поступает на деаэрационную колонку. Вода поступает в нижнюю часть сепаратора, где с помощью поплавкового регулятора поддерживается нормальный уровень воды (нормальным считается уровень, колеблющийся в средней части водоуказательного стекла). Излишняя вода удаляется в канализацию.
В случае необходимости (при неисправности регулятора уровня, увеличения уровня воды в сепараторе выше допустимого и т. д.) вода может удаляться через дренаж в нижней части сепаратора.
1.3 Описание подсистем энергоносителей участка УСТК
1.3.1 Потребляемые энергоносители
Участок ЦТГС на УСТК потребляет:
1) Химически очищенную воду, которая поступает с ТЭЦ ОАО «Уральская Сталь» по двум трубопроводам диаметром 219 мм, один из которых резервный. Температура химически очищенной воды порядка 30-40 °С. Количество химически очищенной воды полученной участком УСТК с ТЭЦ за 2006 год равно 503 364 тонны, что составляет 23,2% от всей химически очищенной воды полученной ЦТГС от ТЭЦ. Химически очищенная вода поступает в деаэраторы, а затем на питание котлов.
2) Азот для восполнения инертного теплоносителя используемого для сухого тушения кокса. Азот поступает с кислородно-компрессорного цеха ОАО «Уральская Сталь» по трубопроводу диаметром 76 мм.
3) Кислород и сжатый воздух. Диаметр кислородопровода 25 мм, диаметр воздухопровода 57 мм. Назначение этих энергоносителей - применение при проведении аварийно-восстановительных работ и планово-предупредительных ремонтов на участке.
4) Техническую воду. Вода поступает из системы оборотного водоснабжения ОАО «Уральская Сталь», и применяется для охлаждения подшипников и сальников питательных и циркуляционных насосов.
5) Питьевую воду.
1.3.2 Вырабатываемые энергоносители
Котлы-утилизаторы участка УСТК вырабатывают тепловую энергию в виде перегретого пара. Пар поступает на собственные нужды ОАО «Уральская Сталь». Перегретый пар по двум трубопроводам диаметром 159 мм поступает в общекомбинатовский 16-ти атмосферный паровой коллектор диаметром 219 мм.
Для примера приведены параметры пара, выработанного котлом-утилизатором №1 10 марта 2007 года:
1) Средняя температура перегретого пара 380 °С.
2) Среднее давление перегретого пара 12 атм (1,2 МПа).
3) Среднечасовая выработка перегретого пара 27,2 тонны.
Далее приводится ведомость выработки (Таблица 7) перегретого пара котлами-утилизаторами участка УСТК и всем ЦТГС (включая пар СИО) за 2006 год.
Таблица 7 - Ведомость выработки пара
Месяц
|
Объект
|
Выработка (тонн)
|
1
|
2
|
3
|
Январь
|
Участок УСТК
ЦТГС
|
42160
137192
|
Февраль
|
Участок УСТК
ЦТГС
|
41162
135642
|
Март
|
Участок УСТК
ЦТГС
|
43647
149324
|
Апрель
|
Участок УСТК
ЦТГС
|
42767
149590
|
Май
|
Участок УСТК
ЦТГС
|
41333
149008
|
Июнь
|
Участок УСТК
ЦТГС
|
34866
143052
|
Июль
|
Участок УСТК
ЦТГС
|
41152
139302
|
Август
|
Участок УСТК
ЦТГС
|
39953
147903
|
Сентябрь
|
Участок УСТК
ЦТГС
|
29350
155831
|
Октябрь
|
Участок УСТК
ЦТГС
|
30837
144968
|
Ноябрь
|
Участок УСТК
ЦТГС
|
36045
174303
|
Декабрь
|
Участок УСТК
ЦТГС
|
51028
174688
|
1.4 Тепловой расчет котла КСТ-80 №1 УСТК
Котел-утилизатор КСТ-80 изначально рассчитан на параметры: паропроизводительность D=26,5 т/час, давление перегретого пара Р=4 МПа, температура перегретого пара Т=440 °С. Работа КУ КСТ-80 в данном режиме недопустима в связи с износом испарительных поверхностей нагрева, барабана-сепаратора, пароперегревателя. В связи с этим Ростехнадзором РФ максимальные разрешенные параметры перегретого пара ограничены: Р=1,8 МПа, Т=420 °С.
Далее приводится тепловой баланс котла КСТ-80 №1. Данные по температуре и давлению перегретого пара, температуре и количестве дымовых газов взяты по показаниям контрольно-измерительных приборов за 10 марта 2007 года. Данные по площадям поверхностей нагрева взяты из характеристики оборудования.
Исходные данные
1 Температура инертных газов поступающих в котел: °С.
2 Состав инертных газов (в % по объему):
Таблица 8 - Химических состав теплоносителя (инертного газа)
СО2
|
О2
|
СО
|
N2
|
H2
O
|
17
|
1,6
|
0,3
|
78,6
|
2,5
|
3 Давление в барабане котла Pб
=0,85 МПа.
4 Температура перегретого пара Тпп
=378 °С.
5 Температура питательной воды Тпв
=100 °С.
6 Расход газов Vг
=82100 нм3
/час.
7 Присосы воздуха – отсутствуют.
Теплосодержание инертных газов.
Объем газов
1 нм3
/нм3
.
2 нм3
/нм3
.
3 нм3
/нм3
.
Таблица 9 - Сводная таблица зависимости теплосодержания дымовых газов от температуры
Наимено-вание величины
|
Размер-ность
|
900
ºС
|
800
ºС
|
700
ºС
|
600
ºС
|
500
ºС
|
400
ºС
|
300
ºС
|
200
ºС
|
100
ºС
|
I
|
кДж/м3
|
1368
|
1202
|
1037
|
879
|
723
|
570
|
422
|
277
|
137
|
Согласно методическим указаниям /4/ по проведению теплового расчета котельных агрегатов расчет сведен в таблицы.
Тепловой расчет котельного агрегата может иметь двоякое назначение, а именно:
1 при проектировании нового котельного агрегата по заданным параметрам его работы (паропроизводительность, температуры перегретого пара, питательной воды и другим) определяют величины всех поверхностей нагрева его;
2 при наличии готового котельного агрегата проверяют соответствие величин всех поверхностей нагрева его заданным параметрам его работы.
Первый вид расчета называется конструкторским, второй - поверочным.
Элементы котельного агрегата рассчитывают последовательно, переходя от поверхностей нагрева с более высокими температурами дымовых газов (пароперегреватель) к поверхностям нагрева с более низкими температурами дымовых газов (испарительные поверхности нагрева, водяной экономайзер). Предварительно выполняют ряд вспомогательных расчетов, а именно: определяют количество дымовых газов по газоходам котельного агрегата и их энтальпию, составляют тепловой баланс котельного агрегата.
При конструкторском расчете поверхностей нагрева по известным значениям температуры дымовых газов перед поверхностью нагрева и после нее определяют величину поверхности нагрева. При поверочном расчете по заданной величине поверхности нагрева и известной температуре дымовых газов перед ней определяют температуру дымовых газов за поверхностью нагрева.
Все поверхности нагрева рассчитывают по двум основным уравнениям, а именно по уравнению теплового баланса рассчитываемой поверхности нагрева и уравнению теплопередачи в ней. В зависимости от того, производится расчет поверочный или конструкторский, неизвестными в уравнениях теплового баланса и теплопередачи оказываются различные величины. Однако в обоих случаях расчета в этих уравнениях известна температура дымовых газов перед поверхностью нагрева, которая становится исходной величиной для расчета
Таблица 10 - Тепловой баланс котельного агрегата и паропроизводительности
Наименование
|
Обозначение
|
Размерность
|
Формула
|
Расчет
|
1
|
2
|
3
|
4
|
5
|
1 Объем продуктов сгорания перед котлом
|

|
м3
/с
|
по показаниям КИП
|
22,8
|
2 Температура продуктов сгорания перед котлом
|

|
ºС
|
по показаниям КИП
|
830
|
3 Энтальпия продуктов сгорания перед котлом
|

|
кДж/м3
|
по таблице 9
|
1253,6
|
4 Температура продуктов сгорания за котлом
|

|
ºС
|
по показаниям КИП
|
210
|
5 Энтальпия продуктов сгорания за котлом
|

|
кДж/м3
|
по таблице 9
|
291,8
|
6 Потери тепла с уходящими газами
|

|
Вт
|
, /4, 33/
|
22,8×291 800=6 653 000
|
7 Общее количество тепла, вносимое в котел газами
|

|
Вт
|
, /4, 33/
|
22,8×1 253 600=28 582 000
|
8 Потери тепла с уходящими газами
|

|
%
|
, /4, 34/
|
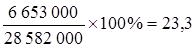
|
9 Потери тепла в окружающую среду
|

|
%
|
нормативный
метод, /4, 55/
|
2
|
Продолжение таблицы 10
|
1
|
2
|
3
|
4
|
5
|
10 Потери тепла в окружающую среду
|

|
Вт
|
, /4, 34/
|
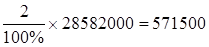
|
11 Коэффициент сохранения тепла
|

|
-
|
, /4, 35/
|
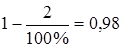
|
12 Сумма тепловых потерь
|

|
%
|
, /4, 35/
|
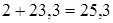
|
13 КПД котла
|

|
%
|
, /4, 35/
|

|
14 Паропроизводительность КА
|
D
|
кг/с
|
, /4, 36/
|
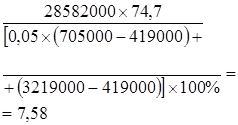
|
Таблица 11 - Тепловой расчет пароперегревателя
Наименование
|
Обозначение
|
Размерность
|
Формула
|
Расчет
|
1
|
2
|
3
|
4
|
5
|
1 Температура газов на входе
|

|
ºС
|
принято
|

|
2 Энтальпия газов на входе
|

|
кДж/м3
|
по таблице 9
|

|
3 Температура насыщенного пара
|

|
ºС
|
по таблице воды и водяного пара, /5, 410/
|

|
Продолжение таблицы 11
|
1
|
2
|
3
|
4
|
5
|
4 Энтальпия насыщенного пара
|

|
кДж/кг
|
по таблице воды и водяного пара, /5, 410/
|

|
5 Температура перегретого пара
|

|
ºС
|
по показаниям КИП
|

|
6 Энтальпия перегретого пара
|

|
кДж/кг
|
по таблице воды и водяного пара, /5, 411/
|

|
7 Тепловосприятие по балансу
|

|
Дж/м3
|
, /4, 37/
|
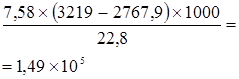
|
8 Энтальпия газов на выходе
|

|
кДж/м3
|
, /4, 37/
|
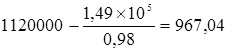
|
9 Температура газов на выходе
|

|
ºС
|
по таблице 9
|

|
10 Средняя температура газов
|

|
ºС
|
, /4, 38/
|
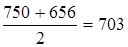
|
11 Средняя температура пара
|

|
ºС
|
, /4, 38/
|

|
12 Скорость газов
|

|
м/с
|
, /4, 40/
|
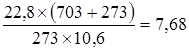
|
13 Коэффициент теплоотдачи конвекцией
|

|
Вт/м2
׺С
|
по номограмме, /4, 157/
|

|
14 Средний удельный объем пара
|

|
м3
/кг
|
, /4, 40/
|
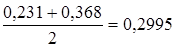
|
Продолжение таблицы 11
|
1
|
2
|
3
|
4
|
5
|
15 Скорость пара
|
Wг
|
м/с
|
, /4, 40/
|
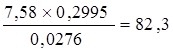
|
16 Эффективная толщина излучающего слоя
|
Sэф
|
м
|
, /4, 41/
|
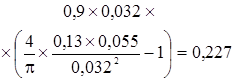
|
17 Объемная доля 3-х атомных газов
|
Кр
S
|
-
|
, /4, 41/
|

|
18 Поглощательная способность 3-х атомных газов
|
Pн
S
|
м×МПа
|
, /4, 41/
|
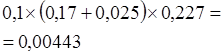
|
19 Коэффициент ослабления лучей 3-х атомными газами
|
Kг
|
-
|
по номограмме, /4, 159/
|

|
20 Сила поглощения запыленного потока
|
A
|
-
|
по номограмме, /4, 161/
|

|
21 Степень черноты потока
|
A
|
-
|
, /4, 45/
|
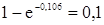
|
22 Коэффициент загрязнения
|
|
м2
׺С/Вт
|
принят по
литературе, /4, 45/
|

|
23 Коэффициент теплоотдачи от стенки к пару
|
|
Вт/м2
׺С
|
принят по
литературе, /4, 45/
|

|
Продолжение таблицы 11
|
1
|
2
|
3
|
4
|
5
|
24 Температура загрязненной стенки
|
Tз
|
ºС
|
, /4, 47/
|
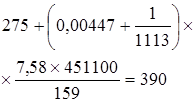
|
25 Коэффициент теплоотдачи излучением
|
|
Вт/м2
׺С
|
/4, 47/
|
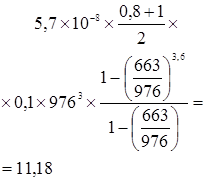
|
26 Коэффициент теплоотдачи от газов к стенке
|
|
Вт/м2
׺С
|
, /4, 47/
|

|
27 Температурный напор
|
|
ºС
|
, /4, 47/
|
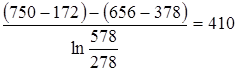
|
28 Коэффициент теплопередачи
|
K
|
Вт/м2
׺С
|
, /4, 48/
|
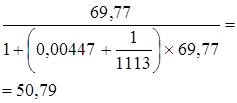
|
Продолжение таблицы 11
|
1
|
2
|
3
|
4
|
5
|
29 Тепловосприятие по уравнению теплопередачи
|
|
Дж/м3
|
, /4, 50/
|
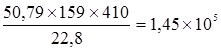
|
%
|
, /4, 50/
|
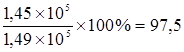
|
Таблица 12 - Тепловой расчет испарительной поверхности
Наименование
|
Обозначение
|
Размерность
|
Формула
|
Расчет
|
1
|
2
|
3
|
4
|
5
|
1 Температура газов на входе
|

|
ºС
|
таблица 11
п. 9
|

|
2 Энтальпия газов на входе
|

|
кДж/м3
|
по таблице 9
|

|
3 Температура среды на входе в поверхность
|

|
ºС
|
по таблице воды и водяного пара, /5, 410/
|

|
4 Энтальпия среды на входе
|

|
кДж/кг
|
по таблице воды и водяного пара. /5, 410/
|

|
5 Температура газов на выходе
|

|
ºС
|
принято
|

|
6 Энтальпия газов на выходе
|

|
кДж/м3
|
по таблице 9
|

|
7 Тепловосприятие по балансу
|

|
Дж/м3
|
, /4, 51/
|
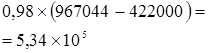
|
8 Средняя температура газов
|

|
ºС
|
, /4, 51/
|
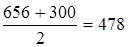
|
Продолжение таблицы 12
|
1
|
2
|
3
|
4
|
5
|
9 Энтальпия среды на выходе
|

|
кДж/кг
|
, /4, 51/
|

|
10 Условная температура среды на выходе
|

|
ºС
|
, /4, 51/
|
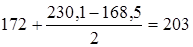
|
11 Средняя температура среды
|

|
ºС
|
, /4, 51/
|
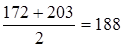
|
12 Скорость газов
|
|
м/с
|
, /4, 51/
|
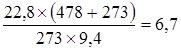
|
13 Коэффициент теплоотдачи конвекцией
|
|
Вт/м2
׺С
|
по номограмме, /4, 157/
|

|
14 Температура загрязненной стенки
|

|
ºС
|
, /4, 51/
|
 
|
15 Эффективная толщина излучающего слоя
|
Sэф
|
м
|
, /4, 51/
|

|
16 Поглощательная способность 3-х атомных газов
|
Pн
S
|
м×МПа
|
, /4, 52/
|

|
Продолжение таблицы 12
|
1
|
2
|
3
|
4
|
5
|
17 Коэффициент ослабления лучей 3-х атомными газами
|
Kг
|
-
|
по номограмме, /4, 159/
|

|
18 Оптическая толщина излучающего слоя
|
Kр
S
|
м
|
, /4, 41/
|

|
19 Степень черноты потока
|
а
|
-
|
, /4, 52/
|

|
20 Коэффициент теплоотдачи излучением
|
|
Вт/м2
׺С
|
, /4, 53/
|
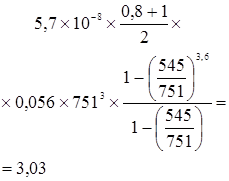
|
21 Коэффициент теплоотдачи от газов к стенке
|
|
Вт/м2
׺С
|
, /4, 53/
|

|
22 Коэффициент теплопередачи
|
K
|
Вт/м2
׺С
|
, /4, 54/
|
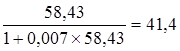
|
23 Температурный напор
|
|
ºС
|
, /4, 54/
|
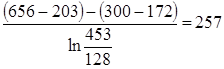
|
Продолжение таблицы 12
|
1
|
2
|
3
|
4
|
5
|
24 Тепловосприятие по уравнению теплопередачи
|
|
Дж/м3
|
, /4, 54/
|
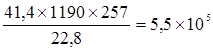
|
%
|
, /4, 50/
|
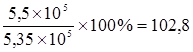
|
Таблица 13 - Тепловой расчет экономайзера
Наименование
|
Обозначение
|
Размерность
|
Формула
|
Расчет
|
1
|
2
|
3
|
4
|
5
|
1 Температура питательной воды
|

|
ºС
|
по показаниям КИП
|

|
2 Энтальпия питательной воды
|

|
кДж/кг
|
по таблице воды и водяного пара, /5, 410/
|

|
3 Температура газов на входе
|

|
ºС
|
таблица 12
|

|
4 Энтальпия газов на входе
|

|
кДж/м3
|
таблица 12
|

|
5 Температура уходящих газов
|

|
ºС
|
по показаниям КИП
|

|
6 Энтальпия уходящих газов
|

|
кДж/м3
|
по таблице 9
|

|
7 Тепловосприятие по балансу
|

|
Дж/м3
|
, /4, 51/
|
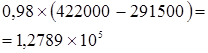
|
Продолжение таблицы 13
|
1
|
2
|
3
|
4
|
5
|
8 Энтальпия воды на выходе
|

|
кДж/кг
|
, /4, 51/
|
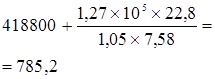
|
9 Температура воды на выходе
|

|
ºС
|
по таблице воды
и водяного пара, /5, 410/
|

|
10 Средняя температура газов
|

|
ºС
|
, /4, 51/
|
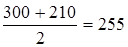
|
11 Средняя температура воды
|

|
ºС
|
, /4, 51/
|
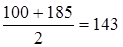
|
12 Скорость газов
|

|
м/с
|
, /4, 51/
|
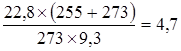
|
13 Коэффициент теплоотдачи конвекцией
|

|
Вт/м2
׺С
|
по номограмме, /4, 157/
|

|
14 Эффективная толщина излучающего слоя
|
Sэф
|
м
|
, /4, 51/
|
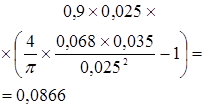
|
15 Поглощательная способность 3-х атомных газов
|
Pн
S
|
м×МПа
|
, /4, 52/
|

|
16 Коэффициент ослабления лучей 3-х атомными газами
|
Kг
|
-
|
по номограмме, /4, 159/
|

|
Продолжение таблицы 13
|
1
|
2
|
3
|
4
|
5
|
17 Оптическая толщина излучающего слоя
|
Kр
S
|
м
|
, /4, 41/
|

|
18 Степень черноты запыленного потока
|
А
|
-
|
, /4, 52/
|

|
19 Температура загрязненной стенки
|

|
ºС
|
, /4, 87/
|

|
20 Коэффициент теплоотдачи излучением
|
|
Вт/м2
׺С
|
/4, 53/
|
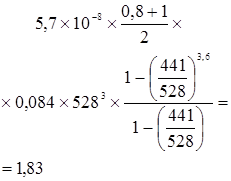
|
21 Коэффициент теплоотдачи от газов к стенке
|
|
Вт/м2
׺С
|
 , /4, 53/
|

|
22 Коэффициент теплопередачи
|
K
|
Вт/м2
׺С
|
, /4, 54/
|
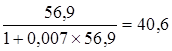
|
23 Температурный напор
|
|
ºС
|
, /4, 54/
|
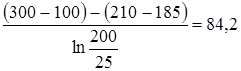
|
Продолжение таблицы 13
|
1
|
2
|
3
|
4
|
5
|
24 Тепловосприятие по уравнению теплопередачи
|
|
Дж/м3
|
, /4, 54/
|
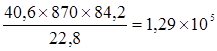
|
%
|
, /4, 50/
|
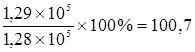
|
Таблица 14 - Тепловой расчет предвключенной испарительной поверхности
Наименование
|
Обозначение
|
Размерность
|
Формула
|
Расчет
|
1
|
2
|
3
|
4
|
5
|
1 Температура газов на входе
|

|
ºС
|
по показаниям КИП
|

|
2 Энтальпия газов на входе
|

|
кДж/м3
|
по таблице 9
|

|
3 Температура среды на входе в поверхность
|

|
ºС
|
таблица 12
|

|
4 Энтальпия среды на входе
|

|
кДж/кг
|
таблица 12
|

|
5 Температура газов на выходе
|

|
ºС
|
таблица 11
|

|
6 Энтальпия газов на выходе
|

|
кДж/м3
|
таблица 11
|

|
7 Тепловосприятие по балансу
|

|
Дж/м3
|
, /4, 51/
|
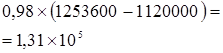
|
8 Средняя температура газов
|

|
ºС
|
, /4, 51/
|
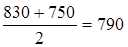
|
Продолжение таблицы 14
|
1
|
2
|
3
|
4
|
5
|
9 Энтальпия среды на выходе
|

|
кДж/кг
|
, /4, 51/
|
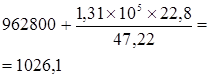
|
10 Условная температура среды на выходе
|

|
ºС
|
, /4, 51/
|
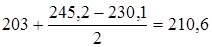
|
11 Средняя температура среды
|

|
ºС
|
, /4, 51/
|
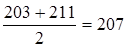
|
12 Скорость газов
|

|
м/с
|
, /4, 51/
|

|
13 Коэффициент теплоотдачи конвекцией
|

|
Вт/м2
׺С
|
по номограмме, /4, 157/
|

|
14 Температура загрязненной стенки
|

|
ºС
|
, /4, 87/
|
 
|
15 Эффективная толщина излучающего слоя
|
Sэф
|
м
|
, /4, 51/
|

|
16 Поглощательная способность 3-х атомных газов
|
Pн
S
|
м×МПа
|
, /4, 52/
|

|
Продолжение таблицы 14
|
1
|
2
|
3
|
4
|
5
|
17 Коэффициент ослабления лучей 3-х атомными газами
|
Kг
|
-
|
по номограмме
|

|
18 Оптическая толщина излучающего слоя
|
Kр
S
|
м
|
, /4, 159/
|

|
19 Степень черноты запыленного потока
|
а
|
-
|
, /4, 52/
|

|
20 Коэффициент теплоотдачи излучением
|
|
Вт/м2
׺С
|
, /4, 53/
|
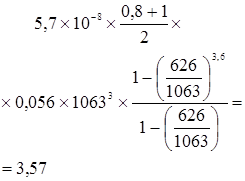
|
21 Коэффициент теплоотдачи от газов к стенке
|
|
Вт/м2
׺С
|
, /4, 53/
|

|
22 Коэффициент теплопередачи
|
K
|
Вт/м2
׺С
|
, /4, 54/
|
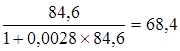
|
23 Температурный напор
|
|
ºС
|
, /4, 54/
|

|
Продолжение таблицы 14
|
1
|
2
|
3
|
4
|
5
|
24 Тепловосприятие по уравнению теплопередачи
|
|
Дж/м3
|
, /4, 54/
|

|
%
|
, /4, 50/
|
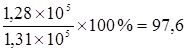
|
1.5 Баланс энергоносителей на участке УСТК
Все данные в энергетическом балансе приведены за 2006 год.
1) Химически очищенная вода, полученная с ТЭЦ-ПВС ОАО «Урал Сталь» и выработанный перегретый пар (по месяцам).
Таблица 15 - Баланс энергоносителей
Месяц
|
Количество выработанного перегретого
пара (тонн)
|
Количество химически очищенной воды полученной с ТЭЦ (тонн)
|
1
|
2
|
3
|
Январь
|
42 160
|
44 600
|
Февраль
|
41 162
|
42 554
|
Март
|
43 647
|
47 227
|
Апрель
|
42 767
|
48 016
|
Май
|
41 333
|
47 639
|
Июнь
|
34 866
|
39 985
|
Июль
|
41 152
|
44 268
|
Август
|
39 953
|
40 448
|
Сентябрь
|
29 350
|
29 823
|
Октябрь
|
30 837
|
29 170
|
Ноябрь
|
36 045
|
37 392
|
Декабрь
|
51 028
|
52 847
|
Всего
|
474 300
|
503 969
|
Таким образом, участком УСТК расходуется на собственные нужды, или теряется в виде утечек и продувок, 29 669 тонн химически очищенной воды в год, что составляет 6,89% от общего потребления химически очищенной воды участком.
2) Получаемый азот из ККЦ ОАО «Урал Сталь» используется полностью.
3) Кислород и сжатый воздух - используются полностью.
4) Техническая вода возвращается в оборотную систему комбината в том же количестве, за исключением незначительных утечек.
1.6 Анализ современного развития аналогичных производств в России и за рубежом
В настоящее время в России и за рубежом используется как сухое тушение кокса, так и мокрое (примерное соотношение 1:1). В Японии, например, весь получаемый кокс тушат в УСТК. В России распространению УСТК, прежде всего, препятствует тяжелое финансовое положение металлургических предприятий (все УСТК в России уже выработали свой ресурс, и дальнейшая их реконструкция не проводится).
Вместе с тем в мировой науке выработано несколько направлений по использованию тепла раскаленного кокса.
1.6.1 Котлы-утилизаторы в схеме УСТК
Развитие данного направления производства в России ограничивается модернизацией (усовершенствованием) котла-утилизатора, а не всей УСТК. Как альтернатива устаревшему КСТ-80 разработан более совершенный котел КСТК 25/39-С-1 который вырабатывает пар энергетических параметров /5, 113/, который затем направляется в паровой турбогенератор.
В Германии и Японии также имеются свои котлы-утилизаторы, вырабатывающие пар иных параметров, но принцип действия всех этих котлов одинаков.
1.6.2 Газовая турбина в схеме УСТК
Представляет интерес схема УСТК в сочетании с газовой турбиной /6, 99/. В схемах с газовой турбиной тепло раскаленного кокса, уловленное в установке сухого тушения, может быть использовано для нагрева компонентов горения при поступлении их в камеру сгорания турбины.
В зависимости от того, какое топливо применено для сжигания в турбине, в цикле УСТК может нагреваться воздух и топливо, или только воздух или воздух и рабочая смесь.
На рисунке 4 приведена схема комбинированной установки сухого тушения кокса с газовой турбиной. Горячие циркулирующие газы после бункера тушения поступают в воздухонагреватель, в котором нагревается воздух, поступающий в камеру сгорания. Затем газы проходят паровой котел и вентилятором вновь нагнетаются в бункер тушения. Воздух, сжатый в воздушном компрессоре газотурбинной установки, нагнетается в камеру сгорания, предварительно он последовательно проходит теплообменник, нагреваемый выхлопными газами турбины, и воздухонагреватель. Газовый компрессор нагнетает горючий газ в камеру смешения, расположенную перед камерой сгорания. Смесь нагретого воздуха и газа сгорает в камере сгорания турбины, продукты сгорания поступают в газовую турбину, где, расширяясь, совершают работу. Выхлопные газы перед выбросом в атмосферу пропускают через газовоздушный теплообменник и через специальный отсек парового котла для нагрева питательной воды.
1.6.3 Коксо-энергетический комплекс в США /6, 102/
Промышленный коксо-энергетический комплекс, включающий 4 коксовые батареи (268 печей) без улавливания химических продуктов коксования мощностью 1,107 млн. тонн в год сортированного кокса и энергоутилизационную установку с электрогенератором мощностью 94 МВт, работает на полную мощность с июня 1998 года на заводе Индиана Харбор в Ист Чикаго фирмы «Indiana Harbor Coke Co».
Энергетическое оборудование комплекса получает от коксовых печей дымовые газы с температурой 870-1200 ºС. Эти газы проходят через 16 котлов-утилизаторов отходящего тепла (по 4 на каждую батарею), где температура газов снижается до 175-180 ºС. Генерируемый пар с параметрами: T=400 ºС, P=5,3 МПа собирается в общем коллекторе и направляется в паровую турбину, где энергия пара превращается в электроэнергию. Использованные газы отводят из котла-утилизатора в коллектор холодного газа, а затем в безнасадочные циклонные мокрые скрубберы для десульфурации. Через вращающийся распылитель в верхней части скруббера внутрь подается гашеная известь, эффективность десульфурации газа 68-98%. Затем двумя вентиляторами газ отсасывается в батарею тканевых фильтров и сбрасывается в дымовую трубу. Таким образом, на энергоутилизационной установке теплота сгорания летучих процессов коксования угля превращается в электроэнергию и технологический пар, который поступает в доменный цех фирмы-потребителя.
Пар из котлов-утилизаторов со средним расходом 2 050 тонн в час поступает в паровую конденсационную турбину мощностью 94 МВт с автоматическим отбором пара. Технологический пар для использования потребителем отбирается из турбины с расходом 45-227 тонн в час. Паровая турбина снабжена байпасной линией. Конденсатор турбины способен принять весь объем сброшенного пара в случае нарушения нормальной работы оборудования. Электрогенератор имеет установленную мощность 94 МВт при напряжении 13,8 кВ.
Основная задача энергосистемы комплекса состоит в переработке всего объема дымовых газов из коксовых печей и поддержании величин атмосферного выброса в пределах, установленных экологическими нормативами.
Процесс производства кокса без улавливания газообразных продуктов в сочетании с энергетическим оборудованием не только представляет конкурентную альтернативу традиционному коксохимическому производству, но и предлагает путь к решению экологических проблем.
1.7 Постановка задачи дипломного проектирования
Проведя анализ результатов энергоаудита ОАО «Урал Сталь» можно сделать следующие выводы:
1) На ОАО «Урал Сталь» низкий уровень использования вторичных энергетических ресурсов.
2) Нет потребности в перегретом паре 16-ти атмосфер.
3) На ОАО «Урал Сталь» недостаточна выработка электрической энергии собственными генераторами. Выработка электрической энергии генераторами ТЭЦ составляет 60-62% от потребления электрической энергии комбинатом. Недостающие 38-40% электрической энергии покупается у ОАО «Межрайонные электрические сети».
4) На ОАО «Урал Сталь» нет дополнительных генераторов электрической энергии кроме комбинатовской ТЭЦ-ПВС.
5) В котельной УСТК на котлах утилизаторах имеются проблемы с работой котлов, в части быстрого износа предвключенных испарительных поверхностей.
На сегодняшний день, в эпоху жестких тарифов на топливо и энергоносители, необходимым условием для нормального функционирования промышленного предприятия и его рентабельности является развитие собственных энергетических мощностей, а также рациональное использование и грамотная утилизация вторичных энергоресурсов.
Задачей дипломного проектирования является установка турбогенератора за котлами-утилизаторами КСТ-80 участка УСТК цеха теплогазоснабжения, с целью выработки дополнительной электрической энергии за счет вторичных энергоресурсов (в частности физической теплоты раскаленного кокса). Выработанная за счет ВЭР электрическая энергия более дешевая, так как в ее себестоимости отсутствует топливная составляющая, которая составляет порядка 75-85% себестоимости электрической энергии получаемой на ТЭС или КЭС.
В дипломном проекте предлагается установить конденсационную паровую турбину для привода синхронного электрического генератора. Для этого потребуется реконструировать котлы-утилизаторы: исключить из работы третью предвключенную испарительную секцию; заменить поверхностный пароохладитель на впрыскивающий с подачей питательной воды, рассмотреть вопросы по установке турбогенераторов, расчету трубопроводов, изменению схемы электронсабжения.
2. Реконструкция котла-утилизатора КСТ-80 с целью установки конденсационной турбины
2.1. Краткое описание мероприятий предлагаемых в дипломном проекте
В данном дипломном проекте предлагаются следующие мероприятия:
1) В связи с высоким абразивным износом третьей предвключенной испарительной поверхности нагрева предлагается произвести ее демонтаж;
2) В связи с неэффективной работой поверхностного пароохладителя, предлагается заменить его на впрыскивающий, с подачей питательной воды;
После проведения данных мероприятий котлы-утилизаторы КСТ-80 станут вырабатывать перегретый пар с параметрами: Р=1,1 МПа и Т=280 ºС, который предлагается использовать в 2-х конденсационных турбогенераторах ТГ-3/6,3-С-1, с суммарной электрической мощностью 6 МВт, их установка позволит поднять выработку электрической энергии на собственных мощностях до 188 МВт, т.е. повысить выработку на 2%.
2.2 Тепловой расчет реконструированного котла КСТ-80
Исходные данные:
1 Температура инертных газов поступающих в котел: ºС.
2 Состав инертных газов (в % по объему):
Таблица 16.
СО2
|
О2
|
СО
|
N2
|
H2
O
|
17
|
1,6
|
0,3
|
78,6
|
2,5
|
3 Давление в барабане котла Pб
=1,1 МПа.
4 Температура перегретого пара Тпп
=380 ºС.
5 Температура питательной воды Тпв
=100 ºС.
6 Расход газов Vг
=82 100 нм3
/час.
7 Присосы воздуха - отсутствуют.
Теплосодержание инертных газов.
Объем газов
1 нм3
/нм3
.
2 нм3
/нм3
.
3 нм3
/нм3
.
Таблица 17 - Сводная таблица зависимости теплосодержания газов от температуры
Наименование величины
|
Размер-ность
|
900
°С
|
800
°С
|
700
°С
|
600
°С
|
500
°С
|
400
°С
|
300
°С
|
200
°С
|
100
°С
|
I
|
кДж/м3
|
1368
|
1202
|
1037
|
879
|
723
|
570
|
422
|
277
|
137
|
3) Просчитать трубопровод охлаждающей воды конденсаторов турбин от градирен КХП, которые в настоящее время загружены на 50%. Это позволит наиболее полно задействовать потенциал градирен на нужды ОАО «Урал Сталь».
4) Произвести электрический, тепловой, гидравлический расчеты.
Тепловой расчет выполнен для котла-утилизатора с демонтированной предвключенной испарительной поверхностью. Конечные и исходные данные приняты на основе данных полученных в разделе 1.6 общей части пояснительной записки, технической характеристики котлов-утилизаторов КСТ-80, а также исходя из параметров пара необходимых для выбранного турбогенератора. Температура перегретого пара принята 380 ºС, дальнейшее снижение температуры перегретого пара нецелесообразно, так как это как следствие повышает температуру уходящих газов и снижает коэффициент полезного действия котельного агрегата (понижает эффективность тушения кокса). Снижение температуры перегретого пара с 380 ºС до необходимых 280 ºС осуществляется во впрыскивающем пароохладителе, который вынесен за пределы котельного агрегата
В настоящее время, установленная мощность электрического оборудования Общества составляет порядка 280 МВт, мощность ТЭЦ - 182 МВт, таким образом, установка турбогенераторов позволит поднять выработку электрической энергии на собственных мощностях до 188 МВт, т.е. повысить выработку на 2%.
Таблица 18 - Тепловой баланс котельного агрегата и паропроизводительности
Наименование
|
Обозначение
|
Размерность
|
Формула
|
Расчет
|
1
|
2
|
3
|
4
|
5
|
1 Объем продуктов сгорания перед котлом
|

|
м3
/с
|
по показаниям КИП
|

|
2 Температура продуктов сгорания перед котлом
|

|
ºС
|
по показаниям КИП
|

|
3 Энтальпия продуктов сгорания перед котлом
|

|
кДж/м3
|
по таблице 17
|

|
4 Температура продуктов сгорания за котлом
|

|
ºС
|
по показаниям КИП
|

|
5 Энтальпия продуктов сгорания за котлом
|

|
кДж/м3
|
по таблице 17
|

|
6 Потери тепла с уходящими газами
|

|
Вт
|
, /4, 33/
|

|
7 Общее количество тепла, вносимое в котел газами
|

|
Вт
|
, /4, 33/
|

|
8 Потери тепла с уходящими газами
|

|
%
|
, /4, 34/
|

|
9 Потери тепла в окружающую среду
|

|
%
|
нормативный
метод, /4, 55/
|

|
Продолжение таблицы 18
|
1
|
2
|
3
|
4
|
5
|
10 Потери тепла в окружающую среду
|

|
Вт
|
, /4, 34/
|
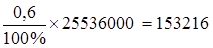
|
11 Коэффициент сохранения тепла
|

|
-
|
, /4, 35/
|
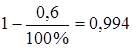
|
12 Сумма тепловых потерь
|

|
%
|
, /4, 35/
|

|
13 КПД котла
|

|
%
|
, /4, 35/
|

|
14 Паропроизводительность КА
|
D
|
кг/с
|
, /4, 36/
|
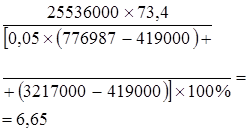
|
Таблица 19 - Тепловой расчет пароперегревателя
Наименование
|
Обозначение
|
Размерность
|
Формула
|
Расчет
|
1
|
2
|
3
|
4
|
5
|
1 Температура газов на входе
|

|
ºС
|
принято
|

|
2 Энтальпия газов на входе
|

|
кДж/м3
|
по таблице 17
|

|
3 Температура насыщенного пара
|

|
ºС
|
по таблице воды и водяного пара, /5, 410/
|

|
Продолжение таблицы 19
|
1
|
2
|
3
|
4
|
5
|
4 Энтальпия насыщенного пара
|

|
кДж/кг
|
по таблице воды и водяного пара, /5, 410/
|

|
5 Температура перегретого пара
|

|
ºС
|
по показаниям КИП
|

|
6 Энтальпия перегретого пара
|

|
кДж/кг
|
по таблице воды и водяного пара, /5, 411/
|

|
7 Тепловосприятие по балансу
|

|
Дж/м3
|
, /4, 37/
|
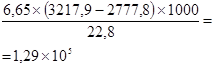
|
8 Энтальпия газов на выходе
|

|
кДж/м3
|
, /4, 37/
|

|
9 Температура газов на выходе
|

|
ºС
|
по таблице 17
|

|
10 Средняя температура газов
|

|
ºС
|
, /4, 38/
|

|
11 Средняя температура пара
|

|
ºС
|
, /4, 38/
|
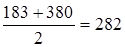
|
12 Скорость газов
|

|
м/с
|
, /4, 40/
|
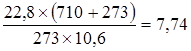
|
13 Коэффициент теплоотдачи конвекцией
|

|
Вт/м2
׺С
|
по номограмме, /4, 157/
|

|
14 Средний удельный объем пара
|

|
м3
/кг
|
, /4, 40/
|
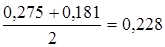
|
Продолжение таблицы 19
|
1
|
2
|
3
|
4
|
5
|
15 Скорость пара
|
Wг
|
м/с
|
, /4, 40/
|

|
16 Эффективная толщина излучающего слоя
|
Sэф
|
м
|
, /4, 41/
|
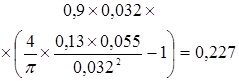
|
17 Объемная доля 3-х атомных газов
|
Кр
S
|
-
|
, /4, 41/
|

|
18 Поглощательная способность 3-х атомных газов
|
Pн
S
|
м×МПа
|
, /4, 41/
|
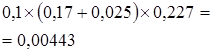
|
19 Коэффициент ослабления лучей 3-х атомными газами
|
Kг
|
-
|
по номограмме, /4, 159/
|

|
20 Сила поглощения запыленного потока
|
A
|
-
|
по номограмме, /4, 161/
|

|
21 Степень черноты потока
|
A
|
-
|
, /4, 45/
|
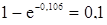
|
22 Коэффициент загрязнения
|
|
м2
׺С/Вт
|
принят по
литературе, /4, 45/
|

|
23 Коэффициент теплоотдачи от стенки к пару
|
|
Вт/м2
׺С
|
принят по
литературе, /4, 45/
|

|
Продолжение таблицы 19
|
1
|
2
|
3
|
4
|
5
|
24 Температура загрязненной стенки
|
Tз
|
ºС
|
, /4, 47/
|
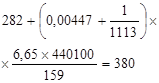
|
25 Коэффициент теплоотдачи излучением
|
|
Вт/м2
׺С
|
/4, 47/
|
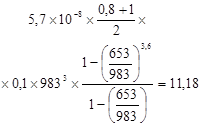
|
26 Коэффициент теплоотдачи от газов к стенке
|
|
Вт/м2
׺С
|
, /4, 47/
|

|
27 Температурный напор
|
|
ºС
|
, /4, 47/
|
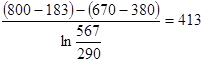
|
28 Коэффициент теплопередачи
|
K
|
Вт/м2
׺С
|
/4, 48/
|
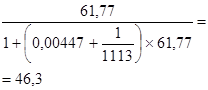
|
Продолжение таблицы 19
|
1
|
2
|
3
|
4
|
5
|
29 Тепловосприятие по уравнению теплопередачи
|
|
Дж/м3
|
, /4, 50/
|
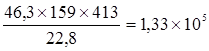
|
%
|
, /4, 50/
|
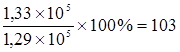
|
Таблица 20 - Тепловой расчет испарительной поверхности
Наименование
|
Обозначение
|
Размерность
|
Формула
|
Расчет
|
1
|
2
|
3
|
4
|
5
|
1 Температура газов на входе
|

|
ºС
|
таблица 19
|

|
2 Энтальпия газов на входе
|

|
кДж/м3
|
по таблице 17
|

|
3 Температура среды на входе в поверхность
|

|
ºС
|
по таблице воды и водяного пара, /5, 410/
|

|
4 Энтальпия среды на входе
|

|
кДж/кг
|
по таблице воды и водяного пара. /5, 410/
|

|
5 Температура газов на выходе
|

|
ºС
|
принято
|

|
6 Энтальпия газов на выходе
|

|
кДж/м3
|
по таблице 17
|

|
7 Тепловосприятие по балансу
|

|
Дж/м3
|
, /4, 51/
|
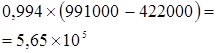
|
Продолжение таблицы 20
|
1
|
2
|
3
|
4
|
5
|
8 Средняя температура газов
|

|
ºС
|
, /4, 51/
|
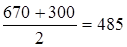
|
9 Энтальпия среды на выходе
|

|
кДж/кг
|
, /4, 51/
|
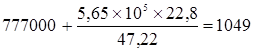
|
10 Условная температура среды на выходе
|

|
ºС
|
, /4, 51/
|
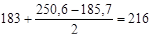
|
11 Средняя температура среды
|

|
ºС
|
, /4, 51/
|
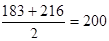
|
12 Скорость газов
|
|
м/с
|
, /4, 51/
|
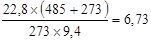
|
13 Коэффициент теплоотдачи конвекцией
|
|
Вт/м2
׺С
|
по номограмме, /4, 157/
|

|
14 Температура загрязненной стенки
|

|
ºС
|
, /4, 51/
|
 
|
15 Эффективная толщина излучающего слоя
|
Sэф
|
м
|
, /4, 51/
|
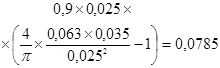
|
Продолжение таблицы 20
|
1
|
2
|
3
|
4
|
5
|
16 Поглощательная способность 3-х атомных газов
|
Pн
S
|
м×МПа
|
, /4, 52/
|

|
17 Коэффициент ослабления лучей 3-х атомными газами
|
Kг
|
-
|
по номограмме, /4, 159/
|

|
18 Оптическая толщина излучающего слоя
|
Kр
S
|
м
|
, /4, 41/
|

|
19 Степень черноты потока
|
а
|
-
|
, /4, 52/
|

|
20 Коэффициент теплоотдачи излучением
|
|
Вт/м2
׺С
|
, /4, 53/
|
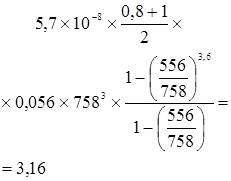
|
21 Коэффициент теплоотдачи от газов к стенке
|
|
Вт/м2
׺С
|
, /4, 53/
|

|
22 Коэффициент теплопередачи
|
K
|
Вт/м2
׺С
|
, /4, 54/
|
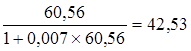
|
Продолжение таблицы 20
|
1
|
2
|
3
|
4
|
5
|
23 Температурный напор
|
|
ºС
|
, /4, 54/
|
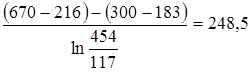
|
24 Тепловосприятие по уравнению теплопередачи
|
|
Дж/м3
|
, /4, 54/
|
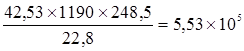
|
%
|
, /4, 50/
|
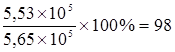
|
Таблица 21 - Тепловой расчет экономайзера
Наименование
|
Обозначение
|
Размерность
|
Формула
|
Расчет
|
1
|
2
|
3
|
4
|
5
|
1 Температура питательной воды
|

|
ºС
|
по показаниям КИП
|

|
2 Энтальпия питательной воды
|

|
кДж/кг
|
по таблице воды и водяного пара, /5, 410/
|

|
3 Температура газов на входе
|

|
ºС
|
таблица 20
|

|
4 Энтальпия газов на входе
|

|
кДж/м3
|
таблица 20
|

|
5 Температура уходящих газов
|

|
ºС
|
по показаниям КИП
|

|
2.3 Расчет впрыскивающего пароохладителя
Впрыскивающий пароохладитель представляет собой участок паропровода перегретого пара, в котором расположена перфорированная труба с отверстиями диаметром 3-5 мм, через которые в пар подается распыленная вода. Для предотвращения попадания на стенку паропровода относительно холодных струй воды в месте установки распылителя в паропроводе имеется разгруженная от давления защитная рубашка с зазором между ней и паропроводом 6-10 мм. Длина защитной рубашки не менее 0,5 метра.
2.3.1 Тепловой расчет
Тепловой расчет выполнен в соответствии с указаниями /7, 113/
В данном дипломном проекте предлагается заменить поверхностный пароохладитель, который в настоящее время работает неэффективно, на впрыскивающий, с целью понижения температуры перегретого пара с 380 ºС до необходимых 280 ºС.
Количество пара Gп
, кг/час, после впрыскивающего пароохладителя увеличивается, и находится по формуле:
, (1)
где - количество пара до пароохладителя, кг/час;
- количество воды поступающей в пароохладитель, кг/час.
Общее количество воды , кг/час, поступающей в поверхностный пароохладитель определяется по формуле:
, (2)
где и - энтальпии перегретого пара и впрыскиваемой воды, поступающих в пароохладитель, кДж/кг;
- снижение энтальпии пара в пароохладителе, кДж/кг.
Впрыскивать в пароохладителе предполагается питательную воду с температурой ºС.
Таким образом, исходя из данных полученных в результате теплового расчета котла-утилизатора КСТ-80, имеем:
Количество пара до пароохладителя =23 940 кг/час.
Энтальпия перегретого пара до пароохладителя =3 218 кДж/кг.
Энтальпия питательной воды =419 кДж/кг.
Снижение энтальпии перегретого пара в пароохладителе при снижении его температуры с 380 ºС до 280 ºС составляет =214 кДж/кг.
Тогда общее количество питательной воды поступающей на впрыск согласно формуле (2) будет равно:
, кг/час.
Количество пара с температурой 280 ºС после впрыскивающего пароохладителя согласно формуле (1) будет равно:
, кг/час.
Таким образом, паропроизводительность котельного агрегата увеличится на 5,88%. При оснащении впрыскивающими пароохладителями всех котлов-утилизаторов КСТ-80 и, учитывая, что постоянно в работе находится 3 котла, суммарная паропроизводительность будет равна 76,05 тонн в час. Из этих 76,05 тонн в час 50,04 тонн в час будет направляться в конденсационные турбины, а 26,01 тонн в час - на нужды ОАО «Урал Сталь».
2.3.2 Конструктивный расчет
Выбор числа отверстий производится из условия, что при максимальном расходе воды на впрыск скорость воды в отверстии должна составлять 10-12 метров в секунду. Скорость воды в отверстии , м/сек, определяется по следующей формуле:
, (3)
где - расход воды на впрыск, кг/сек;
- удельный объем впрыскиваемой воды, м3
/кг;
- площадь отверстия, м2
;
- число отверстий.
Площадь сечения отверстия F, м2
, определяется по формуле:
, (4)
где - диаметр отверстия, м.
Принимаем, согласно рекомендациям в литературе /8, 224/ диаметр отверстия 0,003 метра и скорость воды в отверстии 12 м/сек. Тогда число отверстий n, будет равно:
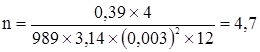
Принимаем число отверстий n=5.
Надежность работы впрыскивающего пароохладителя зависит от выбора длины защитной рубашки. Длина защитной рубашки определяется для максимальной производительности узла впрыска в зависимости от массовой скорости пара в месте впрыска, при минимальной расчетной нагрузке парогенератора, давления пара и разности температур между паром и каплями влаги в начале и конце участка испарения.
Для определения длины защитной рубашки определяет значения , ºС,:
, (5)
где - температура пара на входе в пароохладитель, ºС;
- температура насыщения при давлении в пароохладителе, ºС.
ºС.
, (6)
где - температура пара на выходе из пароохладителя, ºС;
ºС.
Определяем длину защитной рубашки по номограммам /8, 226/ на основании значений разностей температур и .
Пароохладитель выполнен из трубы с внутренним диаметром 169 мм ( ).
Длину защитной рубашки принимаем: метра.
Защитная рубашка выполнена из трубы с наружным диаметром 159 мм.
2.4 Гидравлический расчет
Задачами гидравлических расчётов трубопроводов могут являться:
1) расчёт перепадов давления при обычных режимах, т.е. расходах меньших критических;
2) определение максимально возможного (критического) расхода пара в паропроводе;
3) определение перепадов давления (и соответственно параметров потока) в паропроводе при продувках в атмосферу.
Для выполнения гидравлических расчётов трубопроводов необходимо располагать параметрами пара на выходе, компоновочными и конструктивными данными по всем элементам трассы трубопроводов.
Компоновочные и конструктивные данные трассы трубопроводов должны содержать: схему трубопроводов, включающую в себя все элементы в последовательности, соответствующей движению потока, геометрические размеры каждого элемента, характеристики всех местных сопротивлений, в том числе арматуры.
В данном дипломном проекте проводится расчёт перепадов давления при обычном режиме.
Ниже приводится принципиальная схема проектируемого паропровода.
На схеме обозначены:
1) КУ№1-котел-утилизатор КСТ-80 №1
2) КУ№2-котел-утилизатор КСТ-80 №2
3) КУ№3-котел-утилизатор КСТ-80 №3
4) КУ№4-котел-утилизатор КСТ-80 №4
5) ТГ №1-турбогенератор ТГ-3/6,3-С-1
6) ТГ №2-турбогенератор ТГ-3/6,3-С-1
2.4.1 Гидравлический расчет паропровода
Паропроводы на температуру перегретого пара до 450 ºС и давление не более 4 МПа конструируются из труб, стали 20.
Рекомендуемое значение скорости свежего пара докритических параметров 50-70 м/сек.
Потеря давления в трубопроводе , Па, определяется по формуле:
, (7)
где - линейная потеря давления, Па;
- потеря давления в местных сопротивлениях, Па.
Линейная потеря давления , Па равна:
, (8)
где - удельная линейная потеря давления, Па/м;
- длина трубопровода, м.
Подавляющее большинство трубопроводов работает в области квадратичного закона сопротивлений, для них (для определения удельной линейной потери давления , Па/м) справедлива следующая формула:
, (9)
где - коэффициент, определяется по литературе /9, 98/ с учетом абсолютной эквивалентной шероховатости внутренней стенки труб трубопровода, м0,25
;
- расход теплоносителя, кг/сек;
- средняя плотность пара, кг/м3
;
- внутренний диаметр участка трубопровода, м.
Внутренний диаметр участка трубопровода , м, определяют по рекомендуемой скорости движения среды, исходя из максимально-возможного в эксплуатации ее расхода:
, (10)
где - скорость движения среды, м/с.
Потеря давления в местных сопротивлениях , Па равна:
, (11)
где - сумма коэффициентов местных сопротивлений. Значения этих коэффициентов выбираются по таблицам, приведенным в /9, 99/
Позиции 1, 2, 3, 4 - места врезки паропроводов от соответствующих котлов-утилизаторов КСТ-80.
В связи с тем, что постоянно в работе находится 3 котла из 4-х, для достижения наиболее точного результата гидравлического расчета принимаем, что не работает котел №1 (позиция 1 на рисунке 9).
G - расход пара на участке, кг/сек;
L - длина участка, м;
- скорость движения пара, м/сек;
P1
- давление пара в начале участка, МПа;
dвн
- внутренний диаметр участка трубопровода, мм;
Rл
- удельная линейная потеря давления, Па/м;
- потеря давления на участке, Па;
P2
– давление пара в конце участка, МПа.
Ниже приводится сводная таблица результатов гидравлического расчета выполненного согласно формул (7)-(11)
Таблица 22 - Сводная таблица расчета участка А-В
№ участка
|
G
|
L
|

|
P1
|
dвн
|
Rл
|

|
P2
|
4-3
|
7,04
|
12
|
21,8
|
1,1
|
351
|
38,35
|
460
|
1,0995
|
3-2
|
14,08
|
24
|
44
|
1,0995
|
351
|
153,4
|
4316
|
1,095
|
2-1
|
21,12
|
12
|
65,4
|
1,095
|
351
|
345,1
|
6211
|
1,089
|
1-5
|
21,12
|
6
|
Участок 4-3.
Принимаем скорость движения пара - 50 м/сек. Тогда согласно формуле (10) внутренний диаметр трубопровода будет равен:
м
Согласно сортаменту труб для паропроводов принимаем к прокладке трубу с внутренним диаметром 351 мм. Тогда скорость движения пара из выражения (10) определится:
м/сек.
Удельная линейная потеря давления на участке составит:
Па/м.
Линейная потеря давления на участке:
Па.
Местных сопротивлений на участке нет, следовательно, потеря давления на участке будет равна:

Па.
Давление пара P2
, Па, в конце участка 4-3 будет равно:
, (12)
Па.
Участок 3-2.
Принимаем скорость движения пара - 70 м/сек. Тогда согласно формуле (10) внутренний диаметр трубопровода будет равен:
м.
Согласно сортаменту труб для паропроводов принимаем к прокладке трубу с внутренним диаметром 351 мм. Тогда скорость движения пара из выражения (10) определится:
м/сек.
Удельная линейная потеря давления на участке составит:
Па/м.
Линейная потеря давления на участке:
Па.
Из местных сопротивлений на участке есть сальниковый компенсатор ( ), следовательно, потеря давления в местном сопротивлении согласно формулы (11) составит:
Па.
Полное падение давления на участке по формуле (7) составит:
Па.
Давление пара в конце участка 3-2, согласно формуле (12) будет равно:
Па.
Участки 2-1 и 1-5.
Принимаем скорость движения пара - 70 м/сек. Тогда согласно формуле (10) внутренний диаметр трубопровода будет равен:
м
Согласно сортаменту труб для паропроводов принимаем к прокладке трубу с внутренним диаметром 351 мм. Тогда скорость движения пара из выражения (10) определится:
м/сек.
Удельная линейная потеря давления на участке составит:
Па/м.
Линейная потеря давления на участке:
Па.
Местных сопротивлений на участке нет, следовательно, потеря давления на участке будет равна:

Па.
Давление пара в конце участка 5-1 согласно формуле (10) будет равно:
Па.
Расчет падения давления при переходе с участка A-B на B-C, с B-C на C-D, c C-D на D-E (см. рисунок 8).
При переходе используется колено под углом 90º, гладкое R=2d, коэффициент местного сопротивления , количество колен 3.
Тогда падение давления пара при переходе через местное сопротивление согласно формуле (9) будет равно:
Па.
Расчет падения давления на участке B-C-D-DI
(см. рисунок 7).
Согласно формуле (9) удельная линейная потеря давления будет равна:
Па/м.
Линейное падение давления:
, Па.
Расчет падения давления на участке DI
-E. Расход пара на турбогенераторы составляет: 13,9 кг/сек. Принимаем скорость движения пара - 70 м/сек. Тогда согласно формуле (10) внутренний диаметр трубопровода определится:
м.
Согласно сортаменту труб для паропроводов принимаем к прокладке трубу с внутренним диаметром 299 мм. Тогда скорость движения пара из выражения (10) определится:
м/сек.
Удельная линейная потеря давления:
Па/м.
Линейное падение давления:
Па.
Расчет падения давления при переходе с участка D-E на E-F, с E-F на F-G, c F-G на G-H (см. рисунок 7).
При переходе используется колено под углом 90º, гладкое R=2d, коэффициент местного сопротивления , количество колен 3.
Тогда падение давления пара при переходе через местное сопротивление согласно формуле (11) будет равно:
Па.
Расчет падения давления на участке E-F (см. рисунок 7).
Согласно формуле (9) удельная линейная потеря давления будет равна:
Па/м.
Линейное падение давления:
Па.
На данном участке расположены: измерительная диафрагма и нормальная задвижка. Коэффициент местного сопротивления измерительной диафрагмы , задвижки нормальной .
Па.
Полное падение давления на участке:
Па.
Расчет линейного падения давления на участке F-G-H.
Согласно формуле (9) удельная линейная потеря давления будет равна:
Па/м.
Линейное падение давления:
Па.
Суммируя линейные и местные потери давления по всем участкам и вычитая их из давления в начальной точке получаем давление в точке H:
Па. (13)
Таким образом, у потребителей - паровых турбин гарантируется давление свежего пара не ниже 1,034 МПа.
2.4.2 Гидравлический расчет водовода технической воды
В данном подразделе приводится гидравлический расчет водопровода технической воды. Техническая вода поступает на охлаждение конденсаторов турбин из градирен КХП. Градирни вентиляторные №№3, 4, брызгально-капельные производительностью по 2 000 м3
/час. На охлаждение обоих конденсаторов требуется 1 800 м3
/час. В настоящее время градирни работают не на полную мощность (по охлаждаемой воде), и загрузка их еще на 1 800 м3
/час позволит использовать мощность на 100%.
Водопровод спроектирован от насосной №15 оборотного водоснабжения КХП до котельной УСТК. Прокладка водовода воздушная на опорах, общая длина 666 метров. На прямолинейных участках длиной более 50 метров устанавливается двусторонний сальниковый компенсатор. Количество компенсаторов 8. Температурные деформации будут также компенсироваться за счет естественных поворотов трассы.
Исходные данные
Скорость движения воды: принимаем 3 м/сек, длина трассы 666 метров, количество воды 500 кг/сек, эквивалентная шероховатость стенок трубопровода 0,5 мм. Сумма коэффициентов местных сопротивлений определена по литературе /9, 116/ и составляет . Требуется определить падение давления в паропроводе.
Решение:
Согласно формуле (10) определяем внутренний диаметр трубопровода:
м.
Согласно сортаменту труб для паропроводов принимаем к прокладке трубу с внутренним диаметром 466 мм. Тогда скорость движения пара из выражения (10) определится:
м/сек.
Коэффициент гидравлического трения по формуле Б.Л.Шифринсона:
, (14)
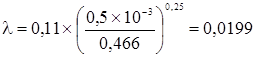
Эквивалентная длина , м, местных сопротивлений равна:
, (15)
м.
Приведенная длина , м, трубопровода равна:
, (16)
, м.
Удельное линейное падение , Па, давления:
, (17)
, Па.
Полное падение давления согласно формуле (8) определится:
, Па.
По каталогу выбираем три насоса (два в работе параллельно подключенных и один в резерве) 1Д1250-63а.
Насосы устанавливаются в здании существующей насосной станции №15, на месте демонтированных в настоящее время агрегатов.
Параметры насоса 1Д1250-63а:
Мощность электропривода - 250 кВт
Создаваемый напор - 52,5 м
Производительность - 1100 м3
/час
2.5 Тепловой расчет паропровода
Для уменьшения потерь теплоты в окружающую среду и обеспечения безопасности труда персонала все трубопроводы, имеющие температуру теплоносителя выше 50 ºС внутри помещений и выше 60 ºС вне помещений, должны иметь тепловую изоляцию. Температура поверхности изоляции должна быть не выше 45 ºС внутри помещений и не более 60 ºС на открытом воздухе.
Потерю теплоты , Вт/м, через изоляцию на 1 метр длины трубопровода определяют по формуле:
(18)
где - температура среды в трубопроводе, ºС;
- температура окружающего воздуха, ºС;
- суммарное термическое сопротивление, м׺С/Вт.
(19)
где , - термическое сопротивление внутренней и наружной поверхностей изолированного трубопровода, м׺С/Вт;
, - термическое сопротивление стенки трубы и слоя изоляции, м׺С/Вт;
(20)
где - внутренний диаметр трубы, м;
- коэффициент теплоотдачи от теплоносителя к стенке трубы, Вт/м2
׺С.
(21)
где - наружный диаметр трубы, м;
- коэффициент теплоотдачи от стенки трубы к изоляции, Вт/м2
׺С.
(22)
где - теплопроводность стенки трубы, Вт/м׺С;
(23)
где - теплопроводность тепловой изоляции, Вт/м׺С;
- диаметр тепловой изоляции, м.
Величина , связана уравнением теплоотдачи с заданной температурой наружной поверхности изоляции:
(24)
где - температура наружной поверхности изоляции.
Необходимое значение диаметра тепловой изоляции определяется из совместного решения уравнений (18) и (24).
2.5.1 Тепловой расчет наружного участка паропровода
Принимаем следующие исходные данные:
внутренний диаметр трубы - 351 мм;
наружный диаметр трубы - 377 мм;
коэффициент теплоотдачи от пара к стенке - 10 000 Вт/м2
׺С;
коэффициент теплоотдачи от наружной поверхности изоляции к окружающему воздуху - 20 Вт/м2
׺С;
теплопроводность стенки стальной трубы - 58 Вт/м׺С.
в качестве изоляционного материала выбираем минеральную вату с коэффициентом теплопроводности - 0,08 Вт/м2
׺С
температура пара - 280 ºС;
средняя температура наружного воздуха зимнего периода - -8 ºС
температура поверхности изоляции - 30 0
ºС.
Определяем необходимую толщину тепловой изоляции.
По формулам (19)-(23) определяем термическое сопротивление изолированного трубопровода:
м׺С/Вт;
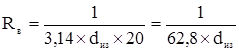
, м׺С/Вт;
, м׺С/Вт;
Суммарное термическое сопротивление трубопровода:
;
; (25)
Для нахождения диаметра тепловой изоляции решаем совместно уравнения (18) и (24):
;
м. Тогда толщина изоляции 77 мм.
Для эффективной работы тепловой изоляции необходимо, чтобы соблюдалось условие:
(26)
(27)
м.
Условие (26) соблюдается.
Тогда термическое сопротивление паропровода согласно формуле (25) будет равно:
м׺С/Вт.
Определяем падение температуры пара по длине наружного участка.
Коэффициент местных потерь теплоты .
Расход пара кг/сек.
Длина паропровода м.
Теплоемкость пара кДж/кг׺С.
Температура в конце участка будет равна:
(28)
ºС.
Падение температуры незначительное ºС.
2.5.2 Тепловой расчет внутреннего участка паропровода
Принимаем следующие исходные данные:
внутренний диаметр трубы - 351 мм;
наружный диаметр трубы - 377 мм;
коэффициент теплоотдачи от пара к стенке - 10000 Вт/м2
׺С;
коэффициент теплоотдачи от наружной поверхности изоляции к окружающему воздуху - 20 Вт/м2
׺С;
теплопроводность стенки стальной трубы - 58 Вт/м׺С.
в качестве изоляционного материала выбираем минеральную вату с коэффициентом теплопроводности - 0,08 Вт/м2
׺С
температура пара - 280 ºС;
средняя температура воздуха в помещении котельной - 30 ºС;
температура поверхности изоляции - 45 ºС.
Определяем необходимую толщину тепловой изоляции.
По формулам (19)-(23) определяем термическое сопротивление изолированного трубопровода:
м×ºС /Вт;
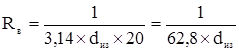
м×ºС /Вт;
м×ºС /Вт;
Суммарное термическое сопротивление трубопровода:
;
.
Для нахождения диаметра тепловой изоляции решаем совместно уравнения (18) и (24):
;
м. Тогда толщина изоляции 153 мм.
Термическое сопротивление паропровода согласно формуле (25) будет равно:
м׺С/Вт.
Определяем падение температуры пара по длине внутреннего участка.
Коэффициент местных потерь теплоты .
Расход пара кг/сек.
Длина паропровода м.
Теплоемкость пара кДж/кг׺С.
Температура в конце участка будет равна:
ºС.
Падение температуры незначительное ºС.
Таким образом, гарантируется температура перегретого пара у потребителя - 279 ºС.
2.6 Расчет схемы электроснабжения
Электроснабжение оборудования котельной УСТК на сегодняшний день осуществляется от подстанции №20 «Т». При вводе в эксплуатацию электрогенераторов турбин, а также трансформаторов устанавливаемых на участке, питание электроприемников котельной УСТК, относящихся ко II-ой категории надежности электроснабжения, будет осуществляться независимо от комбинатовской системы электроснабжения, которая в настоящий момент осуществляется от ТЭЦ и ГПП-2. Кроме того, после внедрения мероприятий, предлагаемых в дипломном проекте, ввод от подстанции №20 «Т» выведется в резерв, что увеличит надежность электроснабжения участка.
2.6.1 Выбор и обоснование схемы электроснабжения участка котельной УСТК
Схемы электрических сетей должны обеспечивать надежное питание потребителей электроэнергии, быть удобными в эксплуатации. Поэтому, для решения электроснабжения участка котельной УСТК с вводом двух генераторов предлагается радиальная схема, характеризующаяся тем, что от источника питания (трансформаторной подстанции) отходят линии, питающие групповые распределительные пункты, от которых в свою очередь, отходят самостоятельные линии, питающие прочие электроприемники малой мощности. Данная схема, несмотря на высокую стоимость, обладает существенными достоинствами: простота в эксплуатации, высокая надежность (так, выход из строя одного из питающих кабелей, повлечет остановку лишь 1-го из котлов участка, которых на участке 4, что было бы невозможно при использовании ШМА или ШРА).
2.6.2 Расчет электрических нагрузок котельной УСТК
Расчет электрических нагрузок ведем методом упорядоченных диаграмм, с применением коэффициента расчетной нагрузки. Результаты расчет сведены в таблицу 23.
Порядок заполнения таблицы:
1. В первую графу записываем наименование групп электроприемников;
2. Во вторую графу записываем количество электроприемников и узлов питания;
3. В третью графу заносим минимальную и максимальную мощность электроприемников для групп и узлов питания. Паспортную мощность оборудования с повторно-кратковременным режимом работы, приводим к длительному режиму работы ПВ-100%:
- для кранов ;
- для сварочных трансформаторов ;
4. В четвертую графу заносим суммарную номинальную мощность электроприемника для групп и узла питания;
5. В пятую графу для узла питания заносим значение модуля сборки m, рассчитываемого по формуле:
m = Рн
max1
/Рн
min1
, (29)
где Рн max1
- максимальная мощность одного электроприемника, кВт;
Рн min1
- минимальная мощность одного электроприемника, кВт.
Коэффициент использования определяется для группы электроприемников по /10, 144/
6. В шестую графу заносим значение коэффициента использования Ки
;
7. В седьмую графу для групп электроприемников записываем значения и вычисляем значения ;
8. В графы 8 и 9 записываем значения средней активной и реактивной мощностей для групп электроприемников:
Рассчитываются средние мощности для группы электроприемников, Pсм
, кВт:
Рсм
= Ки
×ΣРн
, (30)
где Ки
- коэффициент использования;
ΣРн
- сумма номинальных мощностей для узла питания, кВт.
Реактивная средняя мощность Qсм
, квар, для групп электропиемников равна:
Qсм
= Рсм
×tgφ, (31)
где tgφ – определяется по /10, с.159/;
В итоговой строке определяем суммы этих величин;
9. Затем определяются средневзвешенные значения коэффициентов использования и tgφ:
Ки ср. вз.
= ΣРсм
/ΣРн
, (32)
tgφср. вз.
= ΣQсм
/Рсм
, (33)
10. В графу 10 для узла питания записываем эффективное число электроприемников, nЭ
:
, (34)
11. В графу 11 узла питания заносим значение коэффициента расчетной нагрузки KР
в зависимости от КИ
средневзвешенного и nЭ
.
12. В графы 12, 13, 14 заносим для зла питания расчетную нагрузку
Расчетная нагрузка определяется по выражениям:
Расчетная активная нагрузка, Рр
, кВт:
Рр
= Кр
×ΣРсм
, (35)
Расчетная реактивная нагрузка, Qр
, квар:
Qр
= 1,1×ΣQсм
, (36)
Расчетная полная нагрузка, Sр
, кВ×А:

, (37)
13. В графу 15 записываем расчетный ток IР
, А:
, (38)
2.6.3 Выбор марки и сечения проводов и кабелей
Условие выбора сечения по нагреву:
Iр
Iдл.доп.
×Кп
×Кt
, (39)
где Кп
- поправочный коэффициент на количество прокладываемых кабелей в одной траншее; по /11, 28/ Кп
= 0,95;
Кt
- поправочный коэффициент на температуру окружающей среды; при нормальных условиях Кt
= 1;
Iдл.доп.
- длительно допустимый ток с учетом прокладки, А.
, (40)
Выбранное сечение проверяем по допустимой потере напряжения:
ΔUдоп
≥ ΔUp
, (41)
где - допустимая потеря напряжения в сети;
, (42)
где r0
, x0
- удельное активное и реактивное сопротивление провода;
Iр
- расчетный ток, А;
l - длина провода (кабеля) км.
После выбора автоматического выключателя или предохранителя, производим проверку выбранного сечения по току защитного аппарата:
Iдл.доп.
Кзащ
×Iзащ
, (43)
где Кзащ
- коэффициент защиты, зависит от среды и конструктивного выполнения токоведущих частей;
Iзащ
- ток защитного аппарата, А.
Таблица 23 - Расчет электрических нагрузок котельной УСТК
Группа
электро-
приемников
|
n
|
Pmin
-Pmax
|
ΣPн
|
m
|
Ки
|
cosφ/tgφ
|
Pсм
|
Qсм
|
nэ
|
Кр
|
Рр
|
Qр
|
Sр
|
Iр
|
1
|
2
|
3
|
4
|
5
|
6
|
7
|
8
|
9
|
10
|
11
|
12
|
13
|
14
|
15
|
Мостовой
кран
|
1
|
13,3
|
13,3
|
0,3
|
0,82/0,7
|
3,99
|
2,79
|
Конденсат-
ный насос КС
|
2
|
18,5
|
37
|
0,8
|
0,86/0,59
|
29,6
|
17,46
|
Итого по
РП-1
|
3
|
13,3-18,5
|
50,3
|
<3
|
0,55
|
0,84/0,65
|
33,59
|
20,25
|
9
|
1,46
|
49,04
|
22,28
|
53,86
|
81,83
|
Циркуля-
ционный
насос НКУ
|
4
|
45
|
180
|
0,8
|
0,86/0,59
|
144
|
85
|
Сварочный трансфор-матор
|
1
|
24,7
|
24,7
|
0,35
|
0,65/1,17
|
16,05
|
18,78
|
Итого по РП-2
|
5
|
24,7-45
|
204,7
|
<3
|
0,57
|
0,76/0,88
|
160,05
|
103,78
|
1
|
1,48
|
236,87
|
114,16
|
262,94
|
399,49
|
Дымосос
|
2
|
75
|
150
|
0,8
|
0,86/0,59
|
120
|
70,8
|
Итого по РП-3
|
2
|
150
|
<3
|
0,8
|
0,86/0,59
|
120
|
70,8
|
1
|
1
|
120
|
77,88
|
143,06
|
217,36
|
Циркуля-
ционный
насос НКУ
|
4
|
45
|
180
|
0,8
|
0,86/0,59
|
144
|
85
|
Сварочный трансфор-матор
|
1
|
24,7
|
24,7
|
0,35
|
0,65/1,17
|
16,05
|
18,78
|
Продолжение таблицы 23
|
1
|
2
|
3
|
4
|
5
|
6
|
7
|
8
|
9
|
10
|
11
|
12
|
13
|
14
|
15
|
Итого по РП-4
|
5
|
24,7-45
|
13,3
|
<3
|
0,57
|
0,76/0,88
|
160,05
|
103,78
|
1
|
1,48
|
236,87
|
114,16
|
262,94
|
399,49
|
Дымосос
|
2
|
75
|
150
|
0,8
|
0,86/0,59
|
120
|
70,8
|
Итого по
РП-5
|
2
|
150
|
<3
|
0,8
|
0,86/0,59
|
120
|
70,8
|
1
|
1
|
120
|
77,88
|
143,06
|
217,36
|
Итого по
0,4 кВ
|
17
|
759,7
|
<3
|
0,66
|
0,82/0,72
|
593,69
|
369,41
|
4
|
1,08
|
641,18
|
406,35
|
759,1
|
1153,3
|
Таблица 24 - Расчет токоведущих частей напряжением до 1000 В (0,4 кВ)
Наименование линии
|
РР
, кВт
|
cosφ/tgφ
|
sinφ
|
Iр
, А
|
Iдл.доп
, А
|
Марка и сечение проводника
|
Ro
,
Ом
|
xo
,
Ом
|
l, м
|
ΔU, В
|
Kз
×Iз
|
Принятое сечение
|
1
|
2
|
3
|
4
|
5
|
6
|
7
|
8
|
9
|
10
|
11
|
12
|
13
|
ТП-РП-1
|
49,04
|
0,84/0,65
|
0,54
|
81,83
|
87,4
|
АПВ3(1×35)
|
0,894
|
0,088
|
12
|
1,36
|
105
|
РП-1-11
|
18,5
|
0,86/0,59
|
0,51
|
24,17
|
28
|
АПВ3(1×4)
|
7,81
|
0,107
|
6
|
1,7
|
13,2
|
12
|
РП-1-12
|
18,5
|
0,86/0,59
|
0,51
|
24,17
|
25,76
|
АПВ3(1×4)
|
7,81
|
0,107
|
4
|
1,13
|
13,2
|
12
|
РП-1-кран
|
13,3
|
0,82/0,7
|
0,57
|
24,64
|
25,76
|
АПВ3(1×4)
|
7,81
|
0,107
|
16
|
4,41
|
22
|
12
|
ТП-РП-2
|
236,87
|
0,76/0,88
|
0,65
|
399,49
|
400,4
|
ВВГ3(1×150)
|
0,12
|
0,074
|
24
|
2,31
|
450
|
РП-2-21
|
45
|
0,86/0,59
|
0,51
|
79,5
|
87,4
|
АПВ3(1×35)
|
0,894
|
0,088
|
12
|
1,34
|
44
|
105
|
РП-2-22
|
45
|
0,86/0,59
|
0,51
|
79,5
|
87,4
|
АПВ3(1×35)
|
0,894
|
0,088
|
8
|
0,9
|
44
|
105
|
РП-2-23
|
45
|
0,86/0,59
|
0,51
|
79,5
|
87,4
|
АПВ3(1×35)
|
0,894
|
0,088
|
8
|
0,9
|
44
|
105
|
РП-2-24
|
45
|
0,86/0,59
|
0,51
|
79,5
|
87,4
|
АПВ3(1×35)
|
0,894
|
0,088
|
12
|
1,34
|
44
|
105
|
РП-2-41
|
24,7
|
065/1,17
|
0,76
|
57,73
|
60
|
АПВ3(1×16)
|
1,95
|
0,095
|
15
|
1,16
|
13,2
|
48
|
ТП-РП-3
|
120
|
0,86/0,59
|
0,51
|
217,36
|
220
|
АПВ3(1×120)
|
0,245
|
0,076
|
30
|
2,82
|
360
|
РП-3-31
|
75
|
0,86/0,59
|
0,51
|
132,5
|
165
|
АПВ3(1×70)
|
0,42
|
0,08
|
10
|
0,92
|
77
|
210
|
РП-3-32
|
75
|
0,86/0,59
|
0,51
|
132,5
|
165
|
АПВ3(1×70)
|
0,42
|
0,08
|
10
|
0,92
|
77
|
210
|
Продолжение таблицы 24
|
1
|
2
|
3
|
4
|
5
|
6
|
7
|
8
|
9
|
10
|
11
|
12
|
13
|
ТП-РП-4
|
236,87
|
0,76/0,88
|
0,65
|
399,49
|
400,4
|
ВВГ3(1×150)
|
0,12
|
0,074
|
24
|
2,31
|
450
|
РП-4-25
|
45
|
0,86/0,59
|
0,51
|
79,5
|
87,4
|
АПВ3(1×35)
|
0,894
|
0,088
|
12
|
1,34
|
44
|
105
|
РП-4-26
|
45
|
0,86/0,59
|
0,51
|
79,5
|
87,4
|
АПВ3(1×35)
|
0,894
|
0,088
|
8
|
0,9
|
44
|
105
|
РП-4-27
|
45
|
0,86/0,59
|
0,51
|
79,5
|
87,4
|
АПВ3(1×35)
|
0,894
|
0,088
|
8
|
0,9
|
44
|
105
|
РП-4-28
|
45
|
0,86/0,59
|
0,51
|
79,5
|
87,4
|
АПВ3(1×35)
|
0,894
|
0,088
|
12
|
1,34
|
44
|
105
|
РП-4-42
|
24,7
|
065/1,17
|
0,76
|
57,73
|
60
|
АПВ3(1×16)
|
1,95
|
0,095
|
15
|
1,16
|
13,2
|
48
|
ТП-РП-5
|
120
|
0,86/0,59
|
0,51
|
217,36
|
220
|
АПВ3(1×120)
|
0,245
|
0,076
|
30
|
2,82
|
360
|
РП-5-33
|
75
|
0,86/0,59
|
0,51
|
132,5
|
165
|
АПВ3(1×70)
|
0,42
|
0,08
|
10
|
0,92
|
77
|
210
|
РП-5-34
|
75
|
0,86/0,59
|
0,51
|
132,5
|
165
|
АПВ3(1×70)
|
0,42
|
0,08
|
10
|
0,92
|
77
|
210
|
Таблица 25 - Выбор предохранителей
|
Наименование линии
|
РРН
, кВт
|
Iдоп
, А
|
Iр
, А
|
Kз
×Iз
|
Iпуск
, А
|
Iпл.вст
, А
|
Тип предохранителя
|
1
|
2
|
3
|
4
|
5
|
6
|
7
|
8
|
РП-1-11
|
18,5
|
28
|
24,17
|
13,2
|
113,6
|
60
|
ПР-2-60
|
РП-1-12
|
18,5
|
25,76
|
24,17
|
13,2
|
113,6
|
60
|
ПР-2-60
|
РП-1-кран
|
13,3
|
25,76
|
24,64
|
22
|
115,81
|
80
|
ПР-2-100
|
РП-2-21
|
45
|
87,4
|
79,5
|
44
|
397,5
|
160
|
ПР-2-200
|
РП-2-22
|
45
|
87,4
|
79,5
|
44
|
397,5
|
160
|
ПР-2-200
|
РП-2-23
|
45
|
87,4
|
79,5
|
44
|
397,5
|
160
|
ПР-2-200
|
РП-2-24
|
45
|
87,4
|
79,5
|
44
|
397,5
|
160
|
ПР-2-200
|
РП-2-41
|
24,7
|
60
|
57,73
|
13,2
|
282,88
|
45
|
ПР-2-60
|
РП-3-31
|
75
|
165
|
132,5
|
77
|
728,75
|
300
|
ПР-2-350
|
РП-3-32
|
75
|
165
|
132,5
|
77
|
728,75
|
300
|
ПР-2-350
|
РП-4-25
|
45
|
87,4
|
79,5
|
44
|
397,5
|
160
|
ПР-2-200
|
РП-4-26
|
45
|
87,4
|
79,5
|
44
|
397,5
|
160
|
ПР-2-200
|
РП-4-27
|
45
|
87,4
|
79,5
|
44
|
397,5
|
160
|
ПР-2-200
|
Продолжение таблицы 25
|
1
|
2
|
3
|
4
|
5
|
6
|
7
|
8
|
РП-4-28
|
45
|
87,4
|
79,5
|
44
|
397,5
|
160
|
ПР-2-200
|
РП-4-42
|
24,7
|
60
|
57,73
|
13,2
|
282,88
|
45
|
ПР-2-60
|
РП-5-33
|
75
|
165
|
132,5
|
77
|
728,75
|
300
|
ПР-2-350
|
РП-5-34
|
75
|
165
|
132,5
|
77
|
728,75
|
300
|
ПР-2-350
|
Таблица 26
|
Наименование линии
|
РРН
, кВт
|
Iдоп
, А
|
Iр
, А
|
Kз
×Iз
|
Iпуск
, А
|
Iср.тепл.расц
, А
|
Iср.эл.магн.расц
, А
|
Тип выключателя
|
1
|
2
|
3
|
4
|
5
|
6
|
7
|
8
|
9
|
ТП-РП-1
|
49,04
|
87,4
|
81,83
|
23
|
113,6
|
135
|
100
|
ВА-5131
|
ТП-РП-2
|
236,87
|
400,4
|
399,49
|
138,6
|
397,5
|
787,5
|
630
|
ВА-5139
|
ТП-РП-3
|
120
|
220
|
217,36
|
55
|
728,75
|
312,5
|
250
|
ВА-5135
|
ТП-РП-4
|
236,87
|
400,4
|
399,49
|
138,6
|
397,5
|
787,5
|
630
|
ВА-5139
|
ТП-РП-5
|
120
|
220
|
217,36
|
55
|
728,75
|
312,5
|
250
|
ВА-5135
|
2.6.4 Выбор предохранителей
Для выбора плавких вставок предохранителей ответвлений, ведущих к одиночному электродвигателю с легким пуском ток вставки Iпл.вст
, А, определится:
Iпл.вст
≥ Iпуск
/2,5 - для насосов и вентиляторов;
Iпл.вст
≥ 1,2×Iсв
× - для сварочного аппарата;
Iпл.вст
≥ Iпуск
/1,6 - для кранов.
Результаты расчета сведены в таблицу 25.
2.6.5 Выбор автоматических выключателей
Условия выбора автоматических выключателей следующие:
Iном.автомата.
≥ Iр
Iср.тепл.расц.
≥ Iном.двиг
Iср.эл.маг.расц.
≥ 1,25×Iпуск
Результаты расчета сведены в таблицу 26.
2.6.6 Выбор мощности трансформаторов цеховой подстанции
Ориентировочная мощность трансформатора Sор.т.
, кВА, определяется:
, (44)
где Sр.ц
- расчетная мощность цеха, кВА;
N - число трансформаторов на подстанции;
kз
- коэффициент загрузки трансформатора.
кВА
Выбираем для установки на цеховой подстанции трансформаторы типа ТСЗ-630, 2 шт.
Определяем минимальное число цеховых трансформаторов, Nmin
, одинаковой мощности, предназначенных для питания технологически связанных нагрузок:
, (45)
где Pр.ц
- расчетная нагрузка цеха, кВт;
- коэффициент загрузки трансформаторов в нормальном режиме;
- добавка до ближайшего целого числа.
шт.
Определяем экономически оптимальное число Nопт
трансформаторов в цехе:
Nопт
= Nmin
+m=2+0=2 шт. (46)
где m - дополнительное число трансформаторов.
2.6.7 Компенсация реактивной мощности
При выборе числа и мощности цеховых трансформаторов одновременно должен решаться вопрос об экономически целесообразной величине реактивной мощности, передаваемой через трансформаторы в сеть напряжением до 1 кВ.
Согласно норм технологического проектирования систем электроснабжения, мощность компенсирующих устройств выбирается по 2-м этапам:
1 Исходя из возможной передачи реактивной мощности через трансформаторы из сети 6-10 кВ.
2 Выбор дополнительной мощности компенсирующих устройств из условий оптимизации потерь мощности в трансформаторах и сети 6-10 кВ.
Тогда суммарная мощность низковольтных компенсирующих устройств Qнк
, квар, составит:
Qнк
= Qнк1
+Qнк2
, (47)
где Qнк1
, Qнк2
- суммарные мощности низковольтных компенсирующих устройств, определенные на 2-х указанных этапах расчета.
Определим возможную наибольшую реактивную мощность, Q1р
, квар, которая может быть передана через трансформаторы в сеть 0,4 кВ:
, (48)
квар.
Суммарная мощность конденсаторных батарей Qнк1
квар, на стороне 0,4 кВ составит:
Qнк1
= Qрн
+Q1р
=641,18-777,8=-136,62, квар.
Так как в расчетах оказалось, что Qнк1
меньше нуля, то установка низковольтных компенсирующих устройств на первом этапе расчета не требуется.
Дополнительная мощность, Qнк2
квар, НБК для данной группы трансформаторов определяется:
Qнк2
= Qрц
+Qнк1
- ×Nопт
×Sнт
,
где - коэффициент, зависящий от расчетных параметров Кр1
, Кр2
(Кр1
=12, Кр2
=2, тогда =0,55).
Qнк2
= 641,18+0-0,55×2 ×630=-51,82,
Так как Qнк2
меньше нуля, то принимаем Qнк2
=0 и, следовательно, установка НБК в цехе не требуется.
2.6.8 Расчет питающей линии 10 кВ
Определяем сечение по экономической плотности тока Fэ
, мм2
:
Fэ
= Ip
/jэ
, (49)
где Iр
- расчетный ток линии в нормальном режиме, А;
, (50)
где Sp
- расчетная нагрузка секции подстанции;
n - количество кабельных линий;
jэ
- экономическая плотность тока.
А
Fэ
= 21,9/1,4 = 15,6 мм2
По справочнику /9, 45/ принимаем кабель ААБ с бумажной изоляцией и алюминиевыми жилами сечением F=16 мм2
(Iдл.ток.
=75 А)
Определяем расчетный ток Iрк
, А одного кабеля
Iрк
=Ip
/n, (51)
где n - число запараллеленных кабелей в одной линии;
Iрк
=21,9/2 = 10,95 А;
Проверяем выполнение условия по нагреву в нормальном режиме
I'дл.доп.
≥ Iрк
, (52)
Определяем длительно допустимый ток I'дл.доп.
, А, кабеля
I'дл.доп.
= Iдл.ток
×Кл
×Кt
, (53)
где Кл
- поправочный коэффициент на количество прокладываемых кабелей в одной траншее; по /11, 28/ Кп
= 0,9;
Кt
- поправочный коэффициент на температуру окружающей среды; при нормальных условиях Кt
= 1.
I'дл.доп.
= 75×0,9×1 = 67,5 А
Отсюда видно, что условие (52) выполняется, следовательно, кабель по нагреву проходит.
Определим ток одного кабеля IАВ
, А, в послеаварийном режиме:
IАВ
=2× Iрк
(54)
IАВ
=2×21,9=43,8 А.
Проверим выбранный кабель по условию нагрева в послеаварийном режиме:
- рассчитаем допустимый ток кабеля I'АВ
, А в послеаварийном режиме:
I'АВ
= I'дл.доп
×КАВ
, (55)
где КАВ
- коэффициент аварийной перегрузки;
I'АВ
=67,5×1,25=84,37 А.
- проверим выполнение условий по нагреву в послеаварийном режиме:
I'АВ
≥ IАВ
84,37≥43,8
Проверка выбранного сечения по допустимой потере напряжения
ΔUдоп
≥ ΔUp
, (56)
где ΔUp
= ,
здесь n - число кабелей в линии;
P, Q - расчетные нагрузки в кабельной линии;
r=1,95 , x=0,113 - сопротивления одного кабеля Ом/км;
l=0,012 км
ΔUp
= %
Проверка кабеля на термическую стойкость производится по условию:
, (57)
где - установившийся ток короткого замыкания линии, А;
С - коэффициент, учитывающий изменение температуры до и после короткого замыкания; по /11, с. 53/ С = 95;
tпр
= tз
+ tв
= 1+ 0,075=1,075 с; (58)
Для вычисления токов короткого замыкания, составим расчетную схему и схему замещения. Расчет производится в относительных единицах, точным методом.
Рисунок 11. Расчетная схема
Рисунок 12. Схема замещения
Задаемся базисными условиями.
Принимаем базисную мощность Sб
= 6 МВА (6000кВА)
Базисные напряжения Uб
=10,5 кВ
Определим сопротивления элементов схемы, приведенные к базисным условиям.
1) ЭДС генератора Ег:
(59)
2) Сопротивление кабельных линий:
(60)
3) Сопротивление генератора:
(61)
Определим результирующее сопротивление в точке К1:
(62)
Определим базисный ток Iб
, кА
(63)
Определим установившийся ток, Iк
, кА:
(64)
Определим термически стойкое сечение Fт
, мм2
:
(65)
Окончательно принимаем сечение кабеля 10 кВ, Fк
=16 мм2
- ААБ-10-2 (3×16).
2.6.9 Конструктивное выполнение сети 0,4 кВ
От подстанции до РП сеть 0,4 кВ выполнена проводами АПВ и кабелем ВВГ, проложенными открытым способом по стене на скобах, вбитых в стену.
Провода от РП к электроприемникам проложены скрытым способом, в пластмассовых трубах под полом на глубине 100 мм, при котором обеспечивается высокая надежность и хорошая механическая защита проводов.
2.7 Энергоутилизационная мини-ТЭЦ
После проведенных обследований и расчетов приходим к выводу, что реализовав ряд мероприятий, имеется возможность преобразовать котельную УСТК в энерго-утилизационную мини-ТЭЦ, с установкой двух конденсационных турбогенераторов.
Таблица 27 - Характеристика устанавливаемых блочных турбогенераторов
Параметр
|
Значение
|
Тип блочного турбогенератора
|
ТГ-3/6,3-С-1
|
Номинальная мощность, кВт
|
3 000
|
Частота вращения, об/мин:
|
ротора турбины
|
3 000
|
ротора генератора
|
3 000
|
Параметры 3-х фазного электрического тока:
|
напряжение, В
|
6 300 (10 000)*
|
частота, Гц
|
50
|
Номинальные параметры сухого
насыщенного пара (рабочий диапазон):
|
абсолютное давление, МПа
|
1,4 (1,0 – 1,8)
|
температура, °С
|
280 - 380
|
Номинальный расход пара, т/ч
|
25,02
|
Номинальные параметры охлаждающей воды:
|
температура, °С
|
30
|
расход, м3
/ч
|
900
|
Масса турбогенератора, т
|
27
|
Масса поставляемого оборудования, т
|
29,7
|
Габариты турбогенератора, м:
|
длина
|
5,8
|
ширина
|
3,4
|
высота
|
2,8
|
Тип генератора*
|
ТК-4
|
* Напряжение и тип электрогенератора оговариваются при заказе.
Охлаждение конденсаторов турбин будет обеспечиваться оборотной технической водой с насосной станции №15, для этого планируется демонтировать два устаревших насоса и на их место поставить новые.
Отдельно устанавливаются: эжектор пароструйный, блок откачки конденсата (регулятор уровня конденсата, два конденсатных электронасоса), аварийный маслобак или аварийный масляный насос, щит КИП.
Турбогенераторы планируется разместить в помещении электромастерской (в настоящий момент используется как склад) непосредственно примыкающей к основному корпусу котельной УСТК
Турбогенераторы состоят из турбины в сборе, синхронного генератора и вспомогательного оборудования, размещенного на общей раме, со встроенными масляным баком и конденсатором
Выводы по специальной части
Произведенные расчеты показывают техническую возможность преобразования котельной УСТК цеха теплогазоснабжения в энергоутилизационную мини-ТЭЦ, что отвечает требованиям современного развития промышленной энергетики. В данном дипломе предусматривается установка 2-х турбогенераторов типа ТГ-3/6,3-С-1, с суммарной электрической мощностью 6 МВт, краткие параметры турбогенераторов представлены в таблице 24.
Таблица 28 - Характеристика блочного турбогенератора
Наименование параметров
|
Значение параметров
|
Номинальная электрическая мощность, кВт
Параметры свежего пара
абсолютное давление, МПа
температура, ºС
Расход охлаждающей воды, м3
/час
Номинальный расход пара, т/час
|
3 000
1,4 (1,0- 1,8)
280- 380
900
25,02
|
Установка турбин позволит повысить выработку собственной электроэнергии ОАО «Урал Сталь» на 2%.
Демонтаж третьей предвключенной поверхности нагрева позволяет увеличить межремонтный период работы котлов и уменьшить затраты на ремонт. Надежность работы повышается.
3 Автоматизация и механизация производственных процессов
Правильный выбор схемы регулирования и её параметров имеет весьма важное, практически определяющее значение. Этот выбор зависит от тщательного учета требований, которые ставятся условиями регулирования данного агрегата. Так как практически никогда нельзя в полной мере удовлетворить всем требованиям, необходимо особенно тщательно отобрать главные и на их выполнении сосредоточить основное внимание при разработке системы регулирования.
При проектировании системы регулирования необходимо соблюдать условие, при котором всякий выход из строя узла или линии связи должен приводить к остановке агрегата или снижению нагрузки на него. Если этому требованию не удовлетворяет работа какого-либо элемента системы регулирования, то необходимо обеспечить максимальную надёжность этого элемента в любых условиях эксплуатации. Недостаточная надёжность какого-либо узла в системе регулирования может практически сделать нецелесообразным применение автоматического регулирования. Отказ в работе системы или её ложное срабатывание могут привести к более тяжелым последствиям, чем отсутствие регулирования, а уход за ненадежными системами зачастую требует более квалифицированного персонала, чем обслуживание регулируемого агрегата.
Для всякой силовой установки, казалось бы, автоматическое регулирование должно приводить в соответствие производимую и потребляемую мощность. В действительности при такой постановке задачи не выполняется требование о поддержании определенного качества энергии. Для установок переменного тока качество энергии определяется постоянством частоты тока и его напряжения. Поэтому соответствие между потребляемой и производимой мощностью должно обеспечиваться при одновременном поддержании заданного уровня частоты и напряжения переменного тока. Единственный параметр, однозначно определяющий баланс потребления и производства энергии, - частота сети. Любое изменение нагрузки системы обязательно вызывает изменение частоты сети. Поэтому только измерение и поддержание этого параметра на неизменном уровне позволяют выбранным способом не только поддерживать баланс энергий, но и сохранять высокое качество переменного тока. С другой стороны, измерение частоты может производиться в любой точке системы.
В современных условиях экономически нецелесообразно все изменения частоты полностью воспринимать всеми агрегатами энергетической системы. В последнем случае все агрегаты должны быть настолько недогруженными, чтобы у них сохранялась способность воспринять дополнительную нагрузку полностью. Эта недогрузка должна выбираться с большим запасом с учётом недостаточной приемистости блоков. Но недогрузка мощных блоков должна покрываться увеличением нагрузки менее экономичных агрегатов, существующих во всех энергетических системах. Поэтому более целесообразно мощные агрегаты недогружать лишь настолько, чтобы они воспринимали начальное отклонение частоты. Одновременно на наименее экономичных электростанциях следует устанавливать прецизионные регуляторы частоты, которые передавали бы регулируемым агрегатам соответственно увеличенную команду, что приведет к более быстрому изменению их нагрузки и частота системы восстановится раньше, чем мощные агрегаты воспримут все её изменения. Станционный регулятор частоты выполняет так называемое вторичное регулирование. Соответственно этому изменяются условия работы систем регулирования.
В аварийных ситуациях необходимо значительно большее быстродействие, чем это было раньше, поскольку системы регулирования выполняют функции не только поддержания частоты, но одновременно и защиты.
Автоматизация технологических процессов является одним из решающих факторов повышения производительности, обеспечения оптимальных режимов работы оборудования, повышения надежности систем и безопасности работы персонала.
Система контроля позволяет осуществить измерение параметров работы котла по щитовым и местным приборам и своевременно выявлять нарушения важнейших параметров с помощью звуковой и световой сигнализации. Система предназначена для обеспечения экономичной, безопасной эксплуатации и оперативного управления работой котла и его оборудования.
Система защит (блокировок) предусматривает оперативное предотвращение повреждений оборудования при достижении предельных параметров работы котла.
Применяемые в котлах-утилизаторах средства автоматического управления представляют собой комплекс, включающий элементы:
- технологический контроль;
- сигнализацию (предупредительную, аварийную и контрольную);
- технологическую защиту котла-утилизатора от нарушения рабочего процесса;
- автоматическое регулирование (стабилизацию заданного значения регулируемого параметра);
- дистанционное управление запорными и регулирующими органами, операциями пуска и останова механизмов, узлов, агрегатов;
- запорно-регулирующую и аварийную блокировку;
Автоматическое регулирование - важнейший элемент средств автоматического управления, служащий для поддержания заданного значения регулируемого параметра.
Автоматическое регулирование независимо от свойств регулируемого параметра состоит из характерных элементов:
- объекта регулирования;
- автоматического регулятора.
4 Безопасность жизнедеятельности и экологичность
4.1 Анализ опасностей и вредностей на проектируемом объекте
К работе по обслуживанию котлов-утилизаторов допускаются лица не моложе 18 лет, прошедшие медицинское освидетельствование, обученные по профессии аттестованные на знание инструкции по охране труда и имеющие удостоверение на право обслуживания выше указанных объектов, заверенное государственным инспектором Ростехнадзора. Допуск осуществляется после прохождения стажировки по эксплуатации на объектах цеха теплогазоснабжения распоряжением по цеху.
В процессе работы на оператора (машиниста-кочегара) котлов-утилизаторов могут воздействовать опасные производственные факторы, основными из которых являются:
1) воздействие движущихся и вращающихся частей механизмов - при проникновении в опасную зону во время работы механизма (насосы - НКУ-250, ПЭ-100-53 (56), дымососы - ДН-12, мельничные вентиляторы - ВМ-160/850);
2) термические ожоги при прикосновении к неизолированным частям технологических агрегатов, трубопроводов, а также при не использовании средств индивидуальной защиты (СИЗ) или при повреждении тепловой изоляции на поверхности оборудования, трубопроводов (температура неизолированных паропроводов - до 380 °С, трубопроводов питательной воды - до 105 °С);
3) поражение электрическим током при прикосновении с токоведущими частями механизмов, находящихся под напряжением, при отсутствии или неисправности заземления (напряжение: циркуляционные насосы - 0,4 кВ, питательные насосы - 3 кВ, при силе тока до 83 А);
4) разрушение конструкций, трубопроводов и элементов котла (избыточное давление: паропроводы до 1,6 МПа, трубопроводы питательной воды - до 5,6 МПа, барабан котла - 1,8 МПа). В связи с высокими рабочими параметрами котлов-утилизаторов КСТ-80, данное оборудование зарегистрировано в Ростехнадзоре.
5) высота при неисправности перильных ограждений обслуживающих и переходных площадок (максимальная отметка обслуживаемого оборудования 15,5 м);
6) повышенный шум в рабочей зоне при неиспользовании СИЗ (в районе работающих мельничных вентиляторов - 136,5 дБ, насосов - 123 дБ);
7) химические ожоги при проведении щелочения, кислотной либо реагентной промывке оборудования при неиспользовании СИЗ или неосторожном обращении с хим.растворами (NaOH)
Микроклимат рабочего места.
Установленные нормы оптимального микроклимата в рабочей зоне в зависимости от сезона года и тяжести работы приведены в таблице 29.
Таблица 29 - Нормы оптимального микроклимата в рабочей зоне; относительная влажность 60-40%
Сезон года, температура наружного воздуха
|
Категория работ
|
Температура в рабочей зоне,
ºС
|
Скорость движения воздуха,
м/с
|
Холодный и переходной; менее +10 ºС
|
Легкая I
Средней тяжести II а
Средней тяжести II б
Тяжелая III
|
20 - 23
18 - 20
17 - 19
16 - 18
|
0,2
0,2
0,3
0,3
|
Теплый; +10 ºС и более
|
Легкая I
Средней тяжести II а
Средней тяжести II б
Тяжелая III
|
22 - 25
21 - 23
20 - 22
18 - 20
|
0,2
0,3
0,4
0,5
|
На участке УСТК микроклимат в рабочей зоне соответствует требованиям категории работ средней тяжести (II б).
Допустимая область влажности воздуха 40-75%. При влажности более 75% затрудняется испарение пота, менее 40% - наступает пересыхание слизистой оболочки.
Допустимая область подвижности воздуха 0,2-1 м/с. Застойный воздух затрудняет конвекцию; слишком подвижный вызывает сквозняк.
Человеку необходим чистый естественный воздух без примесей пыли, вредных аэрозолей, газов, паров. При наличии в воздухе частиц ядовитых веществ возможно отравление, вредной пыли - заболевание легких (пневмокониоз), угольной пыли (что характерно для участка котельной УСТК) - антрокоз легких.
Избыточная теплота.
Нагретые поверхности котлов, паропроводов, турбин излучают тепловую энергию инфракрасного спектра мощностью в несколько тысяч Вт/м2
, в то время как допустимое облучение тела человека в этом диапазоне спектра - не более 350 Вт/м2
. Применяют следующие способы защиты от избыточной теплоты: теплоизоляцию горячих поверхностей; экранирование источников излучения поглощающими и отражающими теплоту экранами; воздушные души и вентиляцию; защитную одежду; ограничение длительности работы при больших тепловых нагрузках.
Согласно санитарным нормам температура наружных поверхностей оболочек теплоизоляции не должна превышать 45 ºС. Поэтому излучающие поверхности покрывают тепловой изоляцией: шамотом, изделиями из диатомового кирпича, шлаковой ватой, асбестом со слюдой, минеральной ватой, асбестом, стеклополотном, торкретмассой.
Освещенность рабочих мест и производственных помещений.
Для обеспечения нормальных условий работы все производственные, вспомогательные и бытовые помещения, а также проходы, проезды и определенные участки предприятия должны освещаться. Особенно благоприятен естественный свет, вследствие большого рассеяния, оптимального спектра излучения, наличия ультрафиолетового излучения,
необходимого для жизни человека (длина волны 297 нм) и обеззараживания воздуха (максимальный эффект обеззараживания при длине волны 254 нм).
В производственных помещениях УСТК в данное время применяется естественное освещение, а в вечернее и ночное время - искусственное. Естественное освещение осуществляется тремя способами: боковое через окна; верхнее через световые фонари и комбинированное. Естественная освещенность на рабочем месте в помещении характеризуется коэффициентом естественной освещенности - КЕО. Значения КЕО для производственных зданий расположенных между 45 и 60 ° северной широты, приведены в таблице 30.
Коэффициент естественной освещенности
Искусственное освещение осуществляется комбинацией общего освещения с местным освещением рабочих мест. Выбор системы освещения регламентируется строительными нормами и правилами и зависит от требований технологического процесса, размеров объектов различения и характера зрительных работ.
Таблица 30 - Значения КЕО
Разряд работы
|
Характер работ, выполняемых в помещениях
|
Размер
объекта различения, мм
|
Коэффициент естественной
освещенности
|
при комбинированном освещении
|
при боковом освещении
|
I
II
III
IV
V
VI
|
Особо точные
Высокой точности
Точные
Малой точности
Грубые
Работы, требующие общего наблюдения за ходом производственного процесса
|
0,1 и менее
0,1-0,3
0,3-1,0
1-10
Более 10
-
|
10
7
5
3
2
1
|
3,5
2
1,5
1,5
0,5
0,25
|
Таблица 31 - Нормы освещенности некоторых помещений теплоэнергетических установок
Рабочие места
|
Освещенность, лк,
не менее
|
Пульты управления, измерительные приборы, указатели уровня воды на котлах
Машинный зал
Фронт котлов, подвал машинных залов, помещения дымососов, вентиляторов топливоподачи, электропомещения
Зольное помещение, площадки обслуживания, проходы за котлами
Лестницы оборудования
|
300
200
100
50
10
|
По результатам мониторинга микроклимата рабочих мест, предоставленным управлением промышленной безопасности Общества, нормы освещенности и КЕО на участке УСТК соответствуют нормам.
Производственный шум и вибрация.
Работа некоторого оборудования промышленных установок сопровождается значительным шумом, вибрацией и сотрясением. К такому оборудованию относятся дробилки, мельницы, компрессоры, двигатели, вентиляторы, пневматический инструмент и др. Шум, вибрации и сотрясения отрицательно влияют на организм человека и при длительном воздействии могут вызвать профессиональные заболевания.
Основными характеристиками шума являются частотный спектр интенсивности звука и звуковое давление.
Органы слуха человека воспринимают частоты от 20 Гц до 20000 Гц и звуковое давление от до 20 Па. Уровень звукового давления, достигающий болевого порога, составляет 130 дБ при частоте 1000 Гц.
Санитарными нормами установлены допустимые уровни звукового давления. Они приведены в таблице 32.
Таблица 32 - Предельно допустимые уровни звукового давления шума, действующие более 4 часов
Рабочие места, помещения
|
Уровни звукового давления, дБ, в октавных полосах со среднегеометрическими частотами, Гц
|
63
|
125
|
250
|
500
|
1000
|
2000
|
4000
|
8000
|
Котельный участок - щит котлов
Турбинный участок - щит управления
|
95
83
|
87
74
|
82
68
|
78
63
|
75
60
|
73
57
|
71
55
|
69
54
|
Вибрация оборудования, передаваемая через конструкции и пол организму человека, вызывает заболевания с потерей трудоспособности. Предельно допустимые вибрации на рабочем месте в зависимости от частоты колебаний, амплитуды, скорости и ускорения колебательных движений приведены в таблице 33.
Таблица 33 - Предельно допустимые вибрации на рабочем месте
Частота колебаний, Гц
|
Амплитуда колебаний, мм
|
Скорость колебательных движений, см/с
|
Ускорение колебательных движений, см/с2
|
До 3
3-5
5-8
8-15
15-30
30-50
50-75
75-100
|
0,6-0,4
0,4-0,15
0,15-0,05
0,05-0,03
0,03-0,009
0,009-0,007
0,007-0,005
0,005-0,003
|
1,12-0,76
0,76-0,46
0,46-0,28
0,28-0,25
0,25-0,23
0,23-0,22
0,22-0,19
0,19-0,17
|
12-14
14-15
15-18
18-27
27-32
32-70
70-112
112-120
|
Для ослабления вибраций под основание оборудования устанавливают виброгасители в виде эластичных прокладок, пружины или пневматические демпферы. Для исключения вибраций и сотрясений от работы машин несущие конструкции здания и площадки не должны соприкасаться с фундаментами машин.
Опасность поражения электрическим током.
Проектирование электроустановок должно осуществляться в соответствии с Правилами устройства электрических установок.
Поражение человека электрическим током может быть в следующих случаях:
прикосновения к токоведущим частям - к одной фазе (полюсу) при нахождении ног на земле или токопроводящем полу;
прикосновение к нетоковедущим, конструктивным частям электроустановки, случайно оказавшимся под напряжением вследствие повреждения изоляции;
разряда через человека, конденсатор или кабель, отключенный от источников питания, но заряженный в соответствии с их его электрической емкостью;
ожогов тела электрической дугой;
воздействия электромагнитного поля.
Степень поражения человека электрическим током зависит от характера помещения, в котором произошло включение человека в цепь тока.
Рекомендуемые номинальные напряжения для электроустановок приведены в таблице 30.
Таблица 34 - Номинальные напряжения для электроустановок и область их применения
Напряжение, В
|
Область применения
|
12
36
65
200
220, 380, 660
Выше 1000
|
Для ручных светильников в помещениях особо опасных
Для ручного инструмента
Для ручной сварки
Для стационарных осветительных установок
Для электропривода
Для технических целей, кроме освещения, ручных электроприборов
|
Взрыво- и пожароопасность.
Помещение котельной УСТК относится к категории пожароопасности В. Для локализации возникших пожаров, опасными факторами при которых являются: открытый огонь, повышенная температура воздуха и предметов, дым, недостаток кислорода в воздухе, предусмотрены укомплектованные по правилам пожарной безопасности пожарные щиты, в комплект которых входит: багор, топор, лом, ведра, огнетушители (ОУ-2 – 2 шт, ОУ-5 – 2 шт, ОУ-10 – 2 шт, ОУ-20 – 2 шт.), ящики с песком.
4.2 Обеспечение безопасности труда
В дополнение к существующим инструкциям по охране труда для операторов котельной УСТК, после проведения мероприятий предлагаемых в данном дипломном проекте, необходимо разработать инструкцию по охране труда для машинистов турбинных установок, в которой в обязательном порядке должны быть рассмотрены:
а) режим пуска и нагружения турбоагрегата по отдельным операциям;
б) условия, при которых эксплуатация турбины запрещается - предельные давление и температура пара- перед турбиной, давление в контрольной ступени, давление отработавшего пара, температура пара в выхлопном патрубке турбины, давление масла в маслопроводе к подшипникам и на регулирование, температура масла после маслоохладителей и в подшипниках;
в) предельный пропуск пара через цилиндры (части);
г) аварийные случаи, при которых турбина должна быть немедленно остановлена.
Пуск турбины должен производиться под руководством начальника смены или машиниста цеха (старшего машиниста), а после выхода из ремонта самой турбины - под руководством начальника цеха или его заместителя.
Для турбин, не имеющих валоповоротного устройства, в местной инструкции должен быть предусмотрен режим пуска в зависимости от времени простоя турбины, а также установлен промежуток времени после останова турбины, в течение которого повторный пуск ее не допускается.
Пуск турбины в эксплуатацию запрещается при следующих дефектах регулирования:
а) если регулирование турбины не удерживает холостого хода и при мгновенном сбросе нагрузки скорость вращения ротора превышает 110% номинальной величины или величины, указанной заводом-изготовителем турбины для настройки автомата безопасности;
б) при неисправности стопорного клапана, автомата безопасности, электромагнитного выключателя турбины, масляных насосов и устройств их автоматического включения, а также при заедании органов регулирования.
При неисправности обратного клапана отбора работа турбины с соответствующим отбором не разрешается.
Подача пара на уплотнения и прогрев ротора в неподвижном состоянии запрещается, если на этот счет нет специальных указаний завода - изготовителя турбины.
Система регулирования турбины должна удовлетворять следующим требованиям:
а) устойчиво удерживать турбину на холостом ходу при полностью открытых запорных задвижках;
б) обеспечивать при изменении нагрузки плавное, (без толчков) перемещение регулирующих клапанов;
в) удерживать скорость вращения ротора, не вызывающую срабатывания автомата безопасности при мгновенном сбросе нагрузки - от полной до нуля;
г) обеспечивать плотное закрытие стопорных клапанов; у турбин давлением 9,0 МПа и выше плотность закрытия клапанов может быть признана удовлетворительной, если при полном их закрытии установившаяся скорость вращения ротора не превышает 50% от номинального значения;
д) неравномерность регулирования турбины должна быть 4,0±1,0%, а степень нечувствительности - не более 0,5 %.
Состояние стопорного клапана должно проверяться ежедневно путем перемещения шпинделя на некоторую часть хода, если это допускает конструкция.
Автомат безопасности должен быть отрегулирован на срабатывание при повышении скорости вращения ротора турбины на 10-12% сверх номинальной или до величины, указанной заводом - изготовителем.
Проверка автомата безопасности должна производиться после разборки системы защиты и регулирования, длительной стоянки (более 1 мес.) и через каждые 4 месяца работы турбины. При этом после разборки системы регулирования автомат безопасности проверяется посредством повышения числа оборотов; в остальных случаях допускается проверка без повышения числа оборотов.
Аксиальное положение ротора должно проверяться при холостом ходе и наборе нагрузки, при резких изменениях режима работы и при приемке смены.
Для контроля за проточной частью турбин и заносом ее солями должна производиться проверка величины давлений и перепадов давлений по ступеням, а также проверка степени открытия паровпускных клапанов при различных режимах работы.
Для каждой турбины должны быть установлены предельные величины давления в контрольных ступенях.
Масляный пусковой насос, вспомогательные масляные насосы смазки и устройства их автоматического, включения должны проверяться в работе 1 раз в неделю и перед каждым остановом турбины.
Основные паровые эжекторы при наличии резервных групп должны чередоваться в работе каждый месяц.
Маховики задвижек и вентилей, установленных на маслопроводах перед маслоохладителями, должны быть запломбированы.
Вибрация подшипников турбины, турбогенератора и возбудителя должна проверяться:
а) при вводе в эксплуатацию после монтажа;
б) 1 раз в 3 мес.;
в) перед выводом агрегата в капитальный ремонт и при вводе его в работу после капитального ремонта;
г) при заметном повышении вибрации подшипников;
Сетки фильтров охлаждающей воды, у масло- и воздухоохладителей, фильтров в масляном баке и на паропроводах к основным эжекторам должны осматриваться и очищаться по графику, учитывающему местные условия.
Для достижения максимальной экономичности при эксплуатации турбинной установки должны обеспечиваться:
а) нормальные параметры пара, экономический вакуум и отсутствие переохлаждения конденсата;
б) частота проточной части турбины и теплообменных поверхностей, конденсаторов, подогревателей и испарителей;
в) подогрев конденсата и питательной воды в регенеративной установке в соответствии с давлением греющего пара;
г) открытие регулирующих клапанов в соответствии с тепловой и электрической нагрузкой турбины.
Турбина должна быть немедленно отключена воздействием на автомат безопасности и генератор отключен от сети (при отсутствии или отказе в работе соответствующих защит) в случаях:
а) возникновения внезапной сильной вибраций;
б) гидравлического удара;
в) воспламенения масла на турбине и невозможности быстро потушить огонь;
г) появления дыма из подшипников или из генератора;
д) отказа в работе автомата безопасности при повышении скорости вращения ротора турбины до величины, на которую настроек автомат безопасности;
е) понижения уровня масла в баке за нижний предельный уровень;
ж) появления металлического шума в турбине;
з) осевого сдвига ротора, превышающего установленную предельную величину;
и) понижения вакуума до аварийной величины;
к) отклонения параметров свежего пара против установленных верхних и нижних предельных величин;
При заедании стопорных и регулирующих клапанов и невозможности устранения его на ходу турбина должна быть разгружена открытием главных запорных задвижек, а затем остановлена воздействием на автомат безопасности.
Для каждой турбины должна быть определена длительность выбега, соответствующая останову турбоагрегата при нормальном вакууме. В эксплуатации длительность выбега проверяется при всех остановах турбины и записывается в сменный журнал. При отклонении выбега от нормального должна быть выявлена причина отклонения и приняты меры по устранению.
После останова турбины должны быть открыты вентили обеспаривания, а также все дренажи цилиндров (частей) и паровых коробок клапанов.
Насосы конденсатные, циркуляционные, дренажные, грязевые и технической воды имеющие резервные агрегаты, должны чередоваться в работе. Простой каждого из этих насосов в резерве не должен превышать 1 месяц.
При эксплуатации конденсационной установки должны производиться:
а) периодическая проверки воздушной плотности конденсатора с устранением всех неплотностей;
б) проверка водяной плотности конденсатора путем химического контроля качества конденсата с устранением всех неплотностей;
в) профилактические мероприятия; по предотвращению загрязнений конденсатора; если по местным условиям проведение этих мероприятий затруднено, допускается в качестве временной меры периодическая очистка конденсаторов механическим или химическим способом; необходимость применения химических промывов конденсаторов устанавливается в каждом отдельном случае главным инженером электростанции.
Испытания турбины в процессе эксплуатации должны производиться после внесения изменений в ее проточную часть или в тепловую схему установки. Объем и программа испытаний утверждаются главным инженером электростанции. В объеме испытаний должны включаться испытания конденсационной установки и системы регулирования.
Для ремонта турбоагрегатов машинный зал должен быть оборудован одним или двумя подъемными кранами грузоподъемностью, соответствующей весу статора генератора, или самой тяжелой части турбины, поднимаемой при ремонте, если монтаж статора генератора производится специальным приспособлением. Кроме того, цех должен иметь набор такелажных и ремонтных приспособлений и инструмента.
Детали турбин должны быть маркированы, и иметь контрольные шпильки для облегчения и ускорения сборки. Детали оборудования весом более 0,5 т должны иметь на видном месте клеймо с указанием веса.
Капитальный ремонт турбоагрегата должен производиться через год после ввода в эксплуатацию и в дальнейшем 1 раз в 2 года. С разрешения главного инженера энергосистемы допускается в случае необходимости производство капитального ремонта турбоагрегата ежегодно, а также удлинение периода работы между капитальными ремонтами до 3 лет и более, если турбоагрегат работает нормально и по своему состоянию может обеспечить надежную работу в дальнейшем.
Текущий ремонт турбинной установки производится по мере необходимости.
При капитальном ремонте производиться проверка и наладка работы системы регулирования и защитных устройств и определяться статическая характеристика регулирования. Статическая характеристика регулирования определяется также после изменения схемы регулирования.
Зазоры в проточной части турбины, подшипниках, уплотнениях и прочих элементах, установленные заводом-изготовителем, должны строго выдерживаться. При ремонтах должно производиться тщательное измерение этих зазоров с внесением результатов измерения в формуляр турбины. Измерение зазоров в проточной части должно производиться при полном охлаждении турбины.
Подшипники и масляная система всего турбоагрегата находятся в ведении турбинного участка. Проверка и балансировка турбоагрегата выполняются турбинным участком. Ремонт электрической части генератора, включая выемку и обратную установку ротора, а также системы охлаждения генератора выполняется электроцехом.
4.3 Предупреждение и ликвидация чрезвычайных ситуаций
Чрезвычайные ситуации (ЧС) - это нарушение нормальных условий жизни и деятельности работника ОАО «Урал Сталь» и членов их семей, вызванное аварией, катастрофой, стихийным или экологическим бедствием, применением боевых средств поражения и приведшее или могущее привести к людским и материальным потерям.
О возникновении ЧС вас известят длительные гудки электросирен, автомобилей или речевое сообщение по громкоговорящей связи диспетчера ОАО «Урал Сталь».
Наиболее опасные ЧС встречающие на ОАО «Урал Сталь»:
1) авария с выливом (взрывом) или пожаром бензола на складе КХП, железнодорожных цистернах УЖДТ, при транспортировке.
5) газовые аварии с природным, доменным и коксовым газами.
6) пожары ГСМ, маслоподвалов прокатных цехов, кабельных тоннелей ЦСП, природного и коксового газов и т. д.
К ЧС которые потенциально могут произойти в районе котельной УСТК, относятся ситуации под пунктами 1, 5 и 6.
Газовые аварии с природным, доменным и коксовым газами
Поражающие факторы: Сильнодействующие ядовитые, агрессивные жидкости. Зона заражения может накрыть весь комбинат и город. Угарный газ, СО, из состава доменного газа, вытесняет кислород из гемоглобина крови. Утечка газов может сопровождается взрывами, большой разрушительной силы. Характеристика некоторых газов приведена в таблице 35.
Таблица 35 - Характеристика горючих газов
Газы
|
ПДК
|
Смертельные концентрации
мг/л
|
Предел взрываемости
|
%
|
мг/л
|
природный
|
2,28 г/м3
|
-
|
5-15
|
28,5-85,5
|
доменный
|
20 мг/м3
|
3,4-5,7
за 20 - 30 мин
|
46-68
|
598-884
|
коксовый
|
20 мг/м3
|
5-30
|
25-150
|
Способы и средства защиты: Срочная эвакуация кратчайшим путем. Вызывать газоспасателей. Немедленное прекращение огневых работ, устранение источников огня, искр, соблюдение мер пожарной безопасности. Избегать низких, непроветриваемых мест. Держаться наветренной стороны.
Защита: изолирующие противогазы, респираторы, защиту от доменного газа (по угарному газу СО) обеспечивают промышленные противогазы марки: СО, СОХ
, М.
Меры первой помощи пострадавшим: быстро вынести в лежачем положение на свежий воздух, освободить стесняющую дыхание одежду. При отсутствии дыхания - сделать искусственное дыхание, дать понюхать нашатырный спирт. При необходимости - дать кислород. Провентилировать помещение. Госпитализировать в ЛПУ МСЧ ОАО «Урал Сталь».
Необходимые действия по ликвидации ЧС: изолировать районы аварии. Провести разведку. В зоне аварии входить в изолирующем противогазе, кислородном респираторе после определения взрывобезопасных концентраций. Соблюдать правила взрыво-пожаробезопасности. Работы выполнять с обязательной страховкой. Главные усилия направлять на перекрытие подачи газа. Перевести цех на аварийный режим работы.
Пожары ГСМ, маслоподвалов прокатных цехов, кабельных тоннелей ЦСП, природного и коксового газов
Поражающие факторы: Быстрое распространение огня, создание зон опасного задымления, выделение угарного газа СО, высокотоксичных веществ может охватить до 25% цехов, а зона задымления накроет весь комбинат и город. Под воздействием угарного газа СО появляется оцепенелость, слабость, безучастность и смерть.
ПДК СО - 20 мг/м3
Опасная концентрация СО - 1 мг/л.
Смертельная доза СО - 25 мг/л.
Пожары, как правило, сопровождаются взрывами емкостей, газов, жидкостей с большим материальным ущербом.
Способы и средства защиты: принять меры по ликвидации очага загораний или локализации огня. Немедленная эвакуация из зоны огня и опасного задымления в сторону противоположную направлению распространения пожара.
Защита: спецодежда, подручные материалы, вода, изолирующие противогазы, кислородные респираторы. Защиту по угарному газу обеспечивают промышленные противогазы: СО, СОХ
.
Меры первой помощи пострадавшим: ликвидировать воздействие на тело человека огня, горячих поверхностей, газа или пара. Промыть пораженные участки тела струей холодной воды или обложить снегом на 15¸20 минут. Вынести из зоны огня, сильного задымления. При первых признаках шока необходимо дать выпить 20 капель валерьяны. При ожогах глаз – холодные примочки из раствора борной кислоты (0,5 чайной ложки на стакан воды). Нельзя касаться руками обожженных участков, вскрывать пузыри. Нельзя срывать обувь и одежду - их надо разрезать и осторожно снять.
При тяжелых обширных ожогах - завернуть в простыню, укрыть потеплее, дать 1-2 таблетки анальгина или амидопирина, напоить теплым чаем. Госпитализировать в ЛПУ МСЧ ОАО «Урал Сталь».
Необходимые действия по ликвидации ЧС: Вызвать ОВПО-3, добровольные пожарные дружины, ВВО. Изолировать район пожара. Взводу особого риска обеспечить тушение пожара в условиях СДЯВ, газов.
Действовать в соответствии с планом пожарной защиты. Усилия направить в соответствии с планом взаимодействия. Тушение электропроводок, газопроводов, кабельных тоннелей осуществлять после отключения, прекращения подачи. Постоянно вести химическую разведку очага пожара, контроль взрывоопасных концентраций. Основные усилия направить на локализацию очага пожара с последующей ликвидацией. Перевести цех на аварийный режим работы.
Авария с выливом (взрывом) или пожаром бензола на складе КХП, железнодорожных цистернах УЖДТ, при транспортировке.
Поражающие факторы: Сильнодействующее ядовитое, вещество. Зона заражения может накрыть весь комбинат и город. Пары бензола нарушают функции нервной системы, печени, проникают через кожу, накапливаются и отравляют организм человека.
ПДК - рабочей зоны - 5мг/м3
. ПДК - вне зоны - 1,5 мг/м3
.
Смертельные концентрации: 65 мг/л за 5-10 мин.
Опасные концентрации: 25 мг/л за 0,5 часа.
Способы защиты: Срочная эвакуация. Избегать низких и непроветриваемых мест.
Защита: промышленный противогаз марки: А, М, БКФ или гражданский противогаз ГП-5(7) на непродолжительное время. Держаться наветренной стороны, соблюдать меры пожарной безопасности.
5. Анализ технико-экономических показателей и обоснование экономической целесообразности принятых в проекте решений
В связи с резким повышение цен на топливо и энергоресурсы, развитием рыночной экономики одной из первоочередных задач энергетики является внедрение энергосберегающих технологий, рациональное использование ТЭР. Эти факторы приводят к внедрению новых эффективных технологий.
С переходом предприятия на самоокупаемость и самофинансирование, объем внедрения оборудования будет определяться его экономической эффективностью.
Для оценки денежных потоков, которые будут генерировать применяемое техническое решение, необходимо определить объём средств, требуемых для реализации технической части проекта (объём инвестиций) и разницу между доходными и расходными статьями (калькуляция себестоимости).
Ниже рассмотрены механизмы расчёта объёма инвестиций, анализ калькуляции себестоимости до и после реконструкции, построение на основе этого анализа 3-х отчётов: отчёт о себестоимости, отчёт о наращении прибыли, отчёт о движении денежных средств и рассчитаны показатели экономической эффективности (NPV, PI, IRR, PP).
5.1 Метод ЮНИДО в оценке коммерческой эффективности инвестиционного проекта
Для коммерческой оценки эффективности инвестиционного проекта в его развитии применяют специальный метод ЮНИДО, разработанный институтом развития и организации - ООН.
Оценка коммерческой эффективности инвестиционного проекта
|

 - отчёт о себестоимости; - простые методы;
- отчёт о прибылях и убытках; - чистая текущая стоимость
- отчёт о движении денежных средств; (NPV);
- прогнозный балансовый отчёт - индекс рентабельности (PI);
(финансовые коэффициенты). - внутренняя норма
доходности (IRR);
- период окупаемости (PP).
Экономическая оценка инвестиций показывает, каков экономический эффект, выраженный в рублях, приносит данный проект за весь период экономической жизни, с учётом удовлетворения требований инвестора.
Чистая текущая стоимость (NPV): этот показатель рассчитывается на основе сравнения доходов и расходов по инвестиционному проекту за весь период экономической жизни:
NPV=I+PV, (68)
где: I – инвестиции, руб.
PV – сумма доходов, руб.
Для определения будущей стоимости FV, руб, сегодняшних денег в финансовой математики используют метод наращения:
FV=P×(1+R)n
, (69)
где: P – денежный поток, руб.
R – ставка дисконтирования, %
n – период планирования, лет.
Стоимость будущих денег сегодня PV, руб:
PV=FV/(1+R)n
, (70)
Тогда окончательно чистая текущая стоимость NPV, руб, будет равна:
, (71)
Уравнение (71) может иметь 3-и решения:
если I>PV NPV<0, то проект не окупается;
если I=PV NPV=0, то проект только окупается и не приносит доход;
если I<PV NPV>0, то проект окупается и приносит доход, проект принимается.
Индекс рентабельности (PI): этот показатель показывает, сколько денежных единиц суммарной текущей стоимости доходов по проекту приходится на одну денежную единицу вложенных инвестиций в этот проект.
, (72)
Уравнение (33) может иметь 3-и решения:
если PV<I PI<1 и NPV<0, то проект не окупается;
если PV=I PI=1 и NPV=0, то проект только окупается и не приносит доход;
если PV>I PI>1 и NPV>0, то проект окупается и приносит доход, проект принимается.
Внутренняя норма доходности (IRR): этот показатель отвечает на вопрос, какая величина прибыли достигается при реализации проекта.
, % (73)
Уравнение (34) может иметь 3-и решения:
если IRR<R NPV<0, то проект не окупается;
если IRR=R NPV=0, то проект только окупается и не приносит доход;
если IRR>R NPV>0, то проект окупается и приносит доход, проект принимается.
5.2 Расчет себестоимости
1) затраты на химически очищенную воду (ХОВ).
Суммарная производительность котлов - 82 т/ч,
цена 1 м3
ХОВ с ТЭЦ - 8,34 руб.,
утечки составляют 10%, тогда годовые затраты на ХОВ Ззп
, руб/год, котельной УСТК составляют:
, руб/год
2) затраты на заработанную плату.
Количество рабочих на участке УСТК - 44 человека:
котельное отделение - 4 смены по 3 человека;
турбинное отделение - 4 смены по 2 человека;
лаборатория - 4 смены по 2 человека;
деаэраторы - 4 смены по 2 человека;
рабочая бригада слесарей - 8 человек.
Средняя заработанная плата с учетом роста 10 000 руб./чел. в месяц, начисления на зарплату - 26%, тогда затраты на зарплату Ззп
, руб/год составляют:
, руб/год
3) затраты на ремонт и содержание основных фондов.
По калькуляции за 2006 год по участку УСТК затраты на ремонт составляют 4 919 333 руб. (с учетом капитальных ремонтов). Поскольку турбины устанавливаются новые, то расход только на их содержание по калькуляции 1%, тогда затраты на ремонт и содержание основных фондов Зсоф
, руб/год составляют:
, руб/год
4) затраты на общецеховые расходы.
По калькуляции за 2006 год затраты составляют 3 352 590 руб., а с вводом турбогенераторов увеличится на 20%, тогда затраты на общецеховые расходы Зор
, руб/год составляют:
, руб/год
Годовые затраты З, руб/год:
руб/год
За год вырабатывается электроэнергии, N, МВт×ч/год:
МВт×ч/год
Себестоимость электроэнергии, Ц, руб/кВт×ч:
руб/кВт×ч
5.3 Расчет объема инвестиций
По данным, приводимым в литературе и интернет-информации стоимость 1 кВт установленной электрической мощности (турбина+электрогенератор) составляет порядка $200. Предлагаемый в данной работе проект предусматривает установку 6 МВт электрической мощности.
Принимаем курс доллара США - 26 руб.
Общие затраты N, руб, составят:
руб.
Воспользовавшись, методическими указаниями к дипломному проекту оцениваем полные капиталовложения.
Таблица 36 - Укрупненная структура сметы капитальных затрат на строительство ТЭС
Наименование главы сметы
|
Удельный вес, %
|
Затраты,
тыс. руб
|
1
|
2
|
3
|
Глава 1. Подготовка территории строительства
|
0,5
|
223
|
Глава 2. Основные объекты строительства
|
70
|
31 200
|
Глава 3. Объекты подсобного назначения
|
4
|
1 782
|
Глава 4. Объекты транспорта и связи
|
5
|
2 229
|
Глава 5. Наружные сети водоснабжения и канализации
|
2
|
891
|
Глава 6. Благоустройство и озеленение территории
|
1
|
446
|
Глава 7. Временные здания и сооружения
|
4
|
1 782
|
Глава 8. Прочие работы и затраты
|
5
|
2 229
|
Главы 9, 10. Содержание дирекции и подготовка эксплуатационных кадров
|
0,5
|
223
|
Глава 11. Проектно-изыскательские работы
|
5
|
2 229
|
Непредвиденные работы и затраты
|
3
|
1 338
|
Всего капитальные затраты
|
100
|
44 572
|
Таким образом, общие капиталовложения составят 44 млн. 572 тыс. рублей.
5.4 Расчет основных экономических показателей
Рассматривается инвестиционный проект стоимостью 44,572 млн. руб. Себестоимость выработки электроэнергии составляет 529 руб./МВт×ч. Цена покупной электроэнергии 1 084 руб./МВт
×
ч.
Учитываем, что рентабельность активов предприятия составляет R=14,39%, а период экономической жизни проекта 10 лет. Установленная электрическая мощность Nуст
=6 МВт, время генерации электроэнергии 7 000 часов в год. Амортизация 10% от инвестиций.
За базовый год вырабатывается 42 000 МВт×ч электроэнергии при себестоимости 529 руб./МВт×ч. Годовые затраты составляют 22 234 302 руб/год.
При покупке такого же количества электроэнергии (42 000 МВт×ч) у ОАО «Межрайонные электрические сети» годовые затраты составят: 45 528 000 руб/год.
Экономия на издержках составляет: 23 293 698 руб/год.
Показатели
|
Интервалы планирования, год
|
0
|
1
|
2
|
3
|
4
|
5
|
6
|
7
|
8
|
9
|
10
|
Приток:
|
Приток инвестиций,
тыс. руб.
|
-44 572
|
Экономия на издержках, тыс. руб.
|
23 293
|
23 293
|
23 293
|
23 293
|
23 293
|
23 293
|
23 293
|
23 293
|
23 293
|
23 293
|
Амортизация,
тыс. руб.
|
4 457
|
4 457
|
4 457
|
4 457
|
4 457
|
4 457
|
4 457
|
4 457
|
4 457
|
4 457
|
Итого, тыс. руб:
|
27 750
|
27 750
|
27 750
|
27 750
|
27 750
|
27 750
|
27 750
|
27 750
|
27 750
|
27 750
|
Отток:
|
Налог на прибыль (24%), тыс. руб.
|
5 590
|
5 590
|
5 590
|
5 590
|
5 590
|
5 590
|
5 590
|
5 590
|
5 590
|
5 590
|
Налог на имущество, тыс. руб.
|
595
|
535
|
476
|
416
|
357
|
297
|
238
|
178
|
119
|
59
|
Дивиденды, (14,39%), тыс. руб.
|
3 352
|
3 352
|
3 352
|
3 352
|
3 352
|
3 352
|
3 352
|
3 352
|
3 352
|
3 352
|
Итого, тыс. руб:
|
9 537
|
9 478
|
9 418
|
9 359
|
9 299
|
9 240
|
9 180
|
9 121
|
9 061
|
9 002
|
Сальдо денежных средств, тыс. руб.
|
18 213
|
18 273
|
18 332
|
18 392
|
18 451
|
18 511
|
18 570
|
18 630
|
18 689
|
18 749
|
Таблица 37 - Отчет о движении денежных средств
Таблица 38 - Отчет о приращении прибыли
Показатели
|
Интервалы планирования, год
|
1
|
2
|
3
|
4
|
5
|
6
|
7
|
8
|
9
|
10
|
Итого
|
Экономия на издержках, тыс. руб.
|
23293
|
23293
|
23293
|
23293
|
23293
|
23293
|
23293
|
23293
|
23293
|
23293
|
232930
|
Налог на
имущество,
тыс. руб.
|
595
|
535
|
476
|
416
|
357
|
297
|
238
|
178
|
119
|
59
|
3272
|
Налог на прибыль 24%, тыс. руб.
|
5590
|
5590
|
5590
|
5590
|
5590
|
5590
|
5590
|
5590
|
5590
|
5590
|
55903
|
Наращение прибыли, тыс. руб.
|
17108
|
17167
|
17227
|
17286
|
17346
|
17405
|
17465
|
17524
|
17584
|
17643
|
173755
|
Дивиденды, 14,39%, тыс. руб.
|
3352
|
3352
|
3352
|
3352
|
3352
|
3352
|
3352
|
3352
|
3352
|
3352
|
33519
|
Нераспределенная прибыль, тыс. руб.
|
13756
|
13815
|
13875
|
13934
|
13994
|
14053
|
14113
|
14172
|
14232
|
14291
|
140236
|
Таблица 39 - Показатели финансовой оценки инвестиционного проекта
n
|
Инвестиции, I
тыс. руб
|
Денежный поток Pi
тыс. руб
|
(1+R)n
|
Текущая стоимость
PV=Pi
/(1+R)n
, тыс. руб
|
Чистая текущая стоимость
NPV=I+PV
тыс. руб
|
0
|
-44 572
|
1
|
18 213
|
1,14
|
15 922
|
-28 650
|
2
|
18 273
|
1,31
|
13 964
|
-14 686
|
3
|
18 332
|
1,50
|
12 248
|
-2 438
|
4
|
18 392
|
1,71
|
10 742
|
8 303
|
5
|
18 451
|
1,96
|
9 421
|
17 724
|
6
|
18 511
|
2,24
|
8 262
|
25 986
|
7
|
18 570
|
2,56
|
7 246
|
33 232
|
8
|
18 630
|
2,93
|
6 355
|
39 587
|
9
|
18 689
|
3,35
|
5 573
|
45 160
|
10
|
18 749
|
3,84
|
4 888
|
50 048
|
Итого
|
184 808
|
94 620
|
В результате расчётов с использованием экономико-математической модели получено значение NPV проекта равное 50 048 000 руб.
Результаты расчёта внутренней нормы прибыли проекта также приводится в таблице 39. Осуществляя этот расчёт методом итерации, остановились на значении ставки R равном 0,4768. При таком значении ставки R величина внутренней нормы прибыли проекта NPV близка к нулю. Следовательно, внутренняя норма прибыли проекта IRR составляет около 0,397 (≈39,7 %).
Применяя формулу (72) определяем индекс рентабельности инвестиций:
руб/руб
Так как PI > 1, то проект принимается.
Срок окупаемости инвестиций равен:
года
Анализ полученных результатов показывает, что капиталовложения полностью покрываются дисконтированными доходами проекта на 2-ом интервале планирования от начала эксплуатации проекта. Следовательно, период окупаемости капиталовложений составляет 3 года 83 дня.
Список используемых источников
1. Л.Н. Сидельковский. Котлы-утилизаторы и энерготехнологические агрегаты: учебник / А.П.Воинов, В.А.Зайцев, Л.И. Куперман, Л.Н. Сидельковский - М.: Энергоатомиздат, 2003.- 272 с.- ISBN 5-283-00264-0
2. В.А.Григорьев, В.М.Зорин. Промышленная теплоэнергетика и теплотехника: справочник / А.М. Бакластов, В.М. Бродянский, Б.П.Голубев, В.А. Григорьев, В.М. Зорин: - М.: Энергоатомиздат, 1983.-552 с.
3. Ю.М. Липов Компоновка и тепловой расчет парогенератора: учебное пособие для вузов / Ю.М. Липов.- М.: Энергия, 1975.- 176 с.
4. Справочное пособие по наладке котельных установок промышленных предприятий. С: Уралэнергочермет, 1986.- 332 с.
5. Н.Б. Варгафтик Справочник по теплофизическим свойствам газов и жидкостей. М.: Физматгиз, 1963.-708 с.
6. М.Г. Теплитский, И.З.Гордон, Н.А .Кудрявая, М.С. Кручинин, Ю.М. Волович Сухое тушение кокса.-М.: Металлургия, 1971.- 264 с.
7. Л.Н Сидельковский., В.Н. Юренев. Котельные установки промышленных предприятий: учебник / Л.Н. Сидельковский., В.Н. Юренев - М.: Энергоатом - издат, 1988.- 528 с.-ISBN 5-283-00571-2
8. В.А. Локшин. Гидравлический расчет котельных агрегатов: нормативный метод / О.М. Балдина., В.А. Локшин, Д.Ф. Петерсон.- М.:Энергия,1978.-256с.
9. Ю.Г. Барыгин. Справочник по проектированию электроснабжения. М.: Энергоатомиздат, 2005.- 456 с.- ISBN 5-283-00653-0
10. Б.Н. Неклепаев, И.П. Крючков. Электрическая часть станций и подстанций: справочное пособие для курсового и дипломного проектирования / Неклепаев Б.Н., Крючков И.П. - М.: Энергоатомиздат,1989. - 384 с.- ISBN 5-283-00298-2
11. А.А. Федоров., Л.Е Старкова. Учебное пособие для курсового и дипломного проектирования по электроснабжению промышленных предприятий. – М.: Энергоатомиздат, 1987.- 462с .- ISBN 5-283-00653-0
12. Правила устройства электроустановок. М.: Энергоатомсервис, 2005.-286с.-ISBN 5-543-00123-0
13. А.П. Сафонов Сборник задач по теплофикации и тепловым сетям: учебное пособие для вузов. – М.: Энергоатомиздат, 1985.- 232 с.- ISBN 5-283-00653-0
14. В.А. Григорьева, В.М. Зорина Тепловые и атомные электрические станции: справочник В.А.Григорьев, В.М.Зорин: - М.: Энергоатомиздат, 1982.- 624 с
15. Н.И. Кошкин., М.Г. Ширкевич Справочник по элементарной физике.- М: Наука, 1974.- 256 с.
16. П.Н. Шляхин, М.А. Бершадский. Краткий справочник по паротурбинным установкам.- М.: Энергия, 2003.- 216 с. - ISBN 5-125-00345-0
17. Ю.П. Соловьев., А.И. Михельсон Вспомогательное оборудование ТЭЦ, центральных котельных и его авоматизация.- М.: Энергия, 1972.- 256 с.
18. В.А. Кириллин. Техническая термодинамика: учебник / В.А. Кириллин, В.В.Сычев, А.Е. Шейндлин.-М.: Энергоатомиздат,1983.-416с.
19. А.А. Гухман. Термодинамика: учебник/ Жуковский В.С., А.А. Гухман.- М.: Энергоатомиздат, 1983.-304с.
20. С.И. Мочан. Аэродинамический расчет котельных установок: нормативный метод/ С.И. Мочан. - С-Пб., Энергия, 2004, 256 с.- ISBN 5-94087-721-4
21. www.ktz.kaluga.ru
22. www.sciteclibrary.ru
|