Содержание
Введение
1 Обзор состояния вопроса и постановка задачи на дипломное проектирование
1.2 Горизонтально-расточные станки выпускаемые в РФ и других странах
1.3 Пути и цели модернизации станков
1.4 Постановка задачи на дипломное проектирование
2 Реконструкция горизонтально-расточного станка модели 2А622
2.1 Обоснование реконструкции станка
2.2 Компоновка станка повышенной жесткости
2.3 Обоснование повышенной производительности станка (режимы резания)
2.3.1 Выбор режимов резания
2.3.2 Определить скорость главного движения резания u (м/мин), допускаемую режущими свойствами резца по формуле
2.3.3 Составляющие силы резания
2.3.4 Мощность резания рассчитаем по формуле
2.4 Расчет коробки скоростей
2.4.1 Выбор приводного электродвигателя
2.4.2 Определение общего диапазона регулирования привода
2.4.3 Определение общего числа ступеней скорости
2.4.4 Выбор конструктивных вариантов привода
2.4.5 Определение числа возможных кинематических вариантов
2.4.6 Определение максимальных передаточных отношений по группам передач
2.5 Выбор вариантов структурной формулы
2.5.1 Выбор первого варианта
2.5.2 Выбор второго варианта
2.5.3 Выбор третьего варианта
2.5.4 Выбор четвертого варианта
2.6 Построение структурной сетки
2.7 Построение графика частот вращения
2.8 Определение передаточных отношений в группах передач
2.9 Определение чисел зубьев передач
2.10 Определение крутящих моментов на валах коробки скоростей
2.11 Расчет прямозубой эвольвентной передачи
2.11.1 Определение модуля зубчатой передачи расчетом на контактную выносливость зубьев
2.11.2 Определение модуля зубчатой передачи расчетом на выносливость зубьев при изгибе
2.11.3 Определение стандартного модуля зубчатой передачи
2.12 Расчет и построение свертки коробки скоростей
2.13 Расчет и подбор подшипников
2.14 Расчет сечения сплошного вала
3 Проектирование шпиндельного узла
3.1 Тепловой расчет шпиндельного узла
3.2 Динамический расчет шпиндельного узла
4 Проектирование стойки станка
4.1 Компоновка стойки
4.2 Расчет направляющих
5 Проектирование шпиндельной бабки
5.1 Компоновка шпиндельной бабки
6 Статический и динамический расчет стойки и шпиндельной бабки
6.1 Статический расчет стойки и шпиндельной бабки
6.1.1 Статические характеристики
6.1.2 Динамические характеристики стойки и шпиндельной бабки
5 Расчет экономического эффекта от реконструкции горизонтально-расточного станка мод. 2А622
5.1 Снижение трудоемкости
5.2 Расчет необходимого количества оборудования и его загрузки
5.2.1 Расчетное количество рабочих мест
5.2.2 Принятое количество рабочих мест
5.3 Расчет годовой производительности единицы оборудования и ее изменения
5.3.1 Годовая производительность единицы оборудования
5.3.2 Коэффициент роста производительности оборудования
5.4 Расчет капитальных вложений в оборудование
5.5 Расчет технологической себестоимости годового выпуска изделий
5.5.1 Расчет годовой заработной платы с отчислениями
5.5.2 Расчет годовых затрат на электроэнергию
5.5.3 Расчет годовых амортизационных отчислений для оборудования
5.5.4 Расчет годовых затрат на текущий ремонт оборудования
5.5.5 Расчет годовых затрат на инструмент
5.5.6 Расчет технологической себестоимости годового выпуска изделий
5.6 Штучная технологическая себестоимость
5.7 Экономия от снижения себестоимости
5.8 Расчет приведенных затрат
5.8.1 Годовые приведенные затраты
5.8.2 Удельные приведенные затраты
5.9 Годовой экономический эффект
6 Безопасность труда
6.1 Анализ условий труда
6.2 Мероприятия по улучшению условий труда
6.3 Расчет защитного заземления
6.4 Возможные чрезвычайные ситуации
6.4.1 Расчет времени эвакуации при пожаре
Заключение
Список использованных источников
ПРИЛОЖЕНИЕ А (справочное)
ПРИЛОЖЕНИЕ Б (справочное)
ПРИЛОЖЕНИЕ Г (справочное)
ПРИЛОЖЕНИЕ Д (справочное)
ПРИЛОЖЕНИЕ Е (справочное)
ПРИЛОЖЕНИЕ З (справочное)
ПРИЛОЖЕНИЕ П (справочное)
Важнейшими условиями увеличения роста промышленной продукции является развитие электрификации, комплексной механизации и автоматизации, внедрение новейшего высокопроизводительного оборудования и передовой технологии, широкая замена и модернизация устаревшего оборудования.
Осуществление этих задач в машиностроительной металлообрабатывающей промышленности связанно в первую очередь с повышением производительности основного технологического оборудования - металлорежущих станков.
Работа над созданием и совершенствованием средств автоматизации должна развиваться в двух направлениях: создание средств автоматизации выпускаемого и действующего в настоящее время оборудования с целью повышения его эффективности; создание новых автоматизированных технологических комплексов, где увязаны вопросы повышения производительности, надежности, точности выполнения работ, а также уровня автоматизации операций с необходимой и экономически оправданной гибкостью для быстрой переналадки с целью адаптации к изменяющимся производственным условиям.
Для обеспечения повышения производительности труда в машиностроении большое значение имеет более полное использование действующего парка станков, в первую очередь за счет его модернизации и реконструкции.
Работами, проведенными в промышленности в последние годы, практически доказана возможность значительного повышения эксплуатационных показателей действующих станков путем несложной их переделки.
Однако подавляющая часть работ в области модернизации оборудования проводилась только в направлении повышения быстроходности и мощности. Вопросами механизации и автоматизации рабочего цикла станков уделялось мало внимания. В результате производительность станков повысилась недостаточно, значительно возрос удельный вес затрат времени на выполнение вспомогательных и подготовительно - заключительных работ. Основным направлением модернизации действующего парка станков для обеспечения его наибольшей производительности должно явиться комплексное решение всех факторов, влияющих на производительность, и в первую очередь на повышении уровня автоматизации станков.
1. Обзор состояния вопроса и постановка задачи на дипломное проектирование
Развитие технического прогресса во всех областях науки и техники связано с повышением требований к точности обработки деталей машин при высокой производительности технологического оборудования. Важно не только получить высокую начальную точность станка, но и сохранить её в течении длительного периода эксплуатации. Надёжность станка как технологической системы (технологическая надёжность) становится одной из основных характеристик его качества. Повышение технологической надёжности – одновременное повышение производительности и ресурса работы станков, повышение их эффективности использования в производстве, так как при этом сокращается число подналадок станков, уменьшается объём контрольных измерений деталей, стабилизируется величина припуска, оставляемого на окончательные операции обработки.
С распространением идей кибернетики возник новый взгляд на станки как на машины с неизбежными (естественными) погрешностями функционирования, потому что станок нельзя изолировать от среды, в которой он работает, от влияния вредных процессов, протекающих при его работе (вибраций, силовых и тепловых деформаций, износа, коробления деталей и т.д.). Основным направлением повышения технологической надёжности станков является создание саморегулируемых станков, сохраняющих показатели точности обработки при воздействии окружающей среды и указанных вредных процессов.
Степень воздействия факторов, влияющих на точность обработки, определяется особенностями конструкции станков, технологии и организации производства, используемых при их эксплуатации. Как показывают исследования, погрешности, связанные с тепловыми деформациями, соизмеримы с допусками на изготовление деталей и с требованиями к точности перемещений рабочих узлов станков, а нередко значительно их превышают.
В настоящее время уровень российского станкостроения довольно высок. Российское станкостроение представлено несколькими фирмами. Среди них 4 широко известных станкостроительных завода: Рязанский, Стерлитамакский, Нижегородский и Ивановский, также малоизвестный “Электросистема”, 2 сравнительно недавно созданных фирмы “Пумори” и “Микротехника”. Как правило, наши станки, за исключением некоторых производства Стерлитамакского завода и завода “Электросистема”, не оснащены УЧПУ и большинство из них не имеет индекса СЕ, т.е. не сертифицировано для европейского рынка. Однако это не мешает потенциальным заказчиками, в т.ч. из Европы, активно интересоваться условиями продажи этих станков, несмотря на их довольно непрезентабельный внешний вид.
Фирма “Стерлитамак М.Т.Е.”, демонстрирует широкую номенклатуру своего станочного оборудования, прежде всего многоцелевых станков (но также вертикально- и радиально – сверлильных, хонинговальных, а также прессов).
Обрабатывающий центр модели 630Н предназначен для комлексной 4-х сторонней обработки деталей из различных материалов в условиях мелкосерийного и серийного производства.
Обрабатывающий центр модели 630VH предназначен для комплексной обработки деталей из различных конструкционных материалов с пяти сторон без переустановки в условиях мелкосерийного, серийного и крупносерийного производства.
Обрабатывающий центр модели 800VF6 предназначен для комплексной обработки деталей из различных материалов в 6 координатах управляемых ЧПУ (5 координат управляются одновременно), возможность 5-осевой обработки сложных деталей, постоянная точность обработки, длительный срок эксплуатации, возможность оснащения стандартными и специальными поворотными столами.
Постепенно возрождается Ивановский завод тяжелого станкостроения – когда-то флагман советского станкостроения, один из немногих заводов, успешно экспортировавших свои многоцелевые станки и ГПМ за рубеж. Это возрождение стало очевидным на примере развития его новейших разработок. Если на выставке “Металлообработка – 98” демонстрировался прототип станка мод. “Суперцентр ИС 630”, то спустя 2 года посетители увидели уже серийные образцы этого станка с размерами спутников 630 х 630 мм и аналогичного станка большего типоразмера – “Суперцентр ИС 800”.
Их важнейшие технические характеристики – максимальные скорости перемещения по осям координат – 60 м/мин (ИС630) и 40 м/мин (ИС 800), ускорения (8 м/с2), а также частота вращения шпинделя – 12000 об/мин. Следует также отметить, что “Суперцентр ИС 800” впервые оснащен расточной оправкой длиной 600 мм, что позволяет без переустанова обрабатывать на нем достаточно длинные детали автомобильных двигателей (блоки цилиндров, головки блоков).
Одним из самых наглядных свидетельств продолжения развития станкостроения в России стал разработанный ЛСПО “Свердлов” прототип мехатронного обрабатывающего центра мод. МС 630 ПМФ4. Этот 5- координатный прецизионный (точность линейного позиционирования ± 3мкм, углового ± 2 угл. с) обрабатывающий центр имеет необычную и в то же время рациональную компоновку и предназначен для обработки (с пяти сторон) заготовок размерами до 500 х 500 х 500 мм с поверхностями пространственно сложных форм, в частности сверления и растачивания отверстий, а также измерения этих поверхностей с записью управляющих программ для их обработки. Заготовки устанавливают на поворотном столе диаметром 630 мм и грузоподъемностью 1000 кг. Скорости линейных подач составляют 30 м/мин, угловых – до 18 об/мин, частота вращения шпинделя (от привода мощностью 20 кВт) достигает 24000 об/мин. Инструментальный магазин станка рассчитан на 12 инструментов с конусом ISO 50.
К числу российских предприятий, станки которых отличаются высоким техническим уровнем, безусловно относится и ОАО САВМА - основной поставщик станков для авиакосмической промышленности России. Его фрезерные и многоцелевые станки предназначены для обработки как чугуна и стали, так и труднообрабатываемых материалов, например, титана, а также алюминия.
Рязанский станкостроительный завод и АО “САСТА” специализируются на производстве универсальных токарных станков и станков для обработки труб нефтегазового сортамента.
И конечно же у отечественных станков есть много зарубежных конкурентов. Во главе далеко не малого списка стоят такие страны как Япония, Германия, США, Корея, Швейцария, Италия.
Эти страны по истине являются гигантами станкостроения. Объемы продаж постоянно растут, разрабатываются новые технологии, внедряются новые материалы, выявляются новые тенденции и принципы станкостроения. Каждая страна, и даже каждая фирма, стремится повысить конкурентоспособность свей продукции. Именно поэтому периодически происходит смена лидера, оставляя общее положение без изменений.
Обрабатывающий центр фирмы “CINCINNATI LAMB” идеально подходят для небольших механических цехов и учебных центров, так как сочетают в себе легкость эксплуатации, высокую производительность и низкую стоимость. Высокая точность обработки: точность позиционирования ±5 мкм, воспроизводимость ±1 мкм. Скорость быстрой подачи 20 м/мин и величина разгона - замедления привода 3 м/с2
обеспечивают максимально высокий коэффициент использования шпинделя. Функции, обычно доступные только на дорогостоящих станках, например, предварительное программирование разгона-замедления и функция цилиндрической интерполяции для обеспечения оптимальной скорости контурной обработки и точности. Конвейер шнекового типа для удаления стружки, входящий в базовую комплектацию станка, уменьшает время очистки рабочей зоны.
Вертикальные обрабатывающие центры VMC 40 и VMC 40/8 предназначены для широкого диапазона фрезерных, сверлильных, расточных и прочих операций. Концепция центров основана на продольном перемещении стола, вертикального и поперечного перемещения шпиндельной бабки. Этим обеспечивается высокая стабильность и точность при высокой производительности фрезерования. Сервоприводы соединены с точными ШВП. На станках применены направляющие качения фирмы SCHNEEBERGER. Эта комбинация обеспечивает высокую точность позиционирования наряду с высокими скоростями подач. Широкий диапазон частот вращения шпинделя позволяет обрабатывать все виды материалов.
1.3 Пути и цели модернизации станков
Повышение производительности металлорежущих станков является важной проблемой для заводов машиностроения. Производительность станков может быть повышена проведением ряда мероприятий.
В настоящее время усилия станкостроителей направлены на совершенствование узлов металлорежущих станков.
В частности, предлагаются различные системы и методы смазки подшипников. Недостатки и дороговизну гидростатических и магнитных подшипников пытаются уменьшить путём создания гибридных конструкций. Так, фирма NTN (Япония) предложила комбинацию аэростатического и магнитного подвеса, а фирма Okuma (Япония), используя этот шпиндель, получила высочайшее качество обработанной поверхности.
Повышение жёсткости и точности базирования инструмента достигается путём изменения свойств и конструкции хвостовика. Его дальнейшее совершенствование привело к замене дисковых пружин, подверженных усталости вызывающих нестабильность усилия зажима и разжима, спиральными дисковыми, а также газовым зажимом. В последнем случае механизм зажима укоротился на 50 мм.
Также созданы и применяются ШВП, рассчитанные на скорости перемещения до 200 м/мин.
Создан и стал применяться на станках линейный привод, создающий крутящий момент. К его преимуществам относят: малую нагрузку на систему привода из-за отсутствия взаимодействия между постоянным магнитом и стальным сердечником; простоту получения значительного усилия; высокую стабильность скорости в пределах 0,05 %, т.к. в двигателе отсутствует сердечник, а деформация обмотки во время работы очень мала из-за её значительной жесткости; малое выделение тепла; простоту замены; простоту сборки без регулировки зазора, т.к. эксцентриситет вала по отношению к обмотке ни на что не влияет.
Также усовершенствоваются классические шпиндели, они разрабатываются специально для высоких оборотов и высокой точности. Широкое основание, высокоточные радиально-упорные подшипники. Прямой привод обеспечивает низкий уровень шума, низкие вибрации и высочайшее качество обрабатываемой поверхности.
Развиваются и другие устройства привода подачи. Например, стандартными стали устройства охлаждения винтов ШВП. Предложены устройства, монтируемые с противоположной стороны двигателя, что упрощает монтаж.
Что касается направляющих, то их совершенствование свелось к компромиссу между применением гидростатики, востребованной в наиболее точных многоцелевых, токарных и шлифовальных станках, и сохранением силы трения, препятствующей возникновению колебаний. Чистые направляющие скольжения из-за высокой силы трения не обеспечивают достаточной точности позиционирования и вызывают проблемы при больших подачах. Направляющие качения, хотя и наиболее популярны, но обладают малой демпфирующей способностью и поэтому не гасят колебания. В результате наблюдается рост конструкций гибридного типа, и совершенствуются направляющие качения с целью повысить их демпфирующую способность.
Базовые элементы конструкций станков всё чаще изготавливают из новых материалов. Всё большую популярность завоёвывает полимербетон, обладающий следующими преимуществами в сравнении с чугуном: прекрасными демпфирующими свойствами; превосходной тепловой стабильностью, высокой химической стабильностью, отсутствием необходимости в окраске, коротким циклом производства, сокращением объёмов последующей обработки, возможностью изготовления сложных форм из нескольких простых путём склейки. Необходимость снижения массы подвижных узлов высокоскоростных станков требует применения и других конструкционных материалов. В их числе керамика, алюминиевые сплавы, упрочнение углеродным волокном, пластмасса и др.
Упорная работа ведётся по расширению технологических возможностей станка. Станок приспосабливают для выполнения более широкого круга работ в пределах его основного технологического назначения или для выполнения ранее не свойственных ему работ.
Общие тенденции развития конструкций станков сводятся к созданию многооперационных станков вместо высокоскоростных, т.к. концентрация различных операции вместо простой интенсификации рабочего процесса даёт больший эффект повышения производительности.
К такой категории станков относятся многоцелевые расточные станки. Именно в них сосредоточена наибольшая концентрация различного рода операций и именно такие станки являются базой для создания крупных обрабатывающих центров.
Значение высокоскоростной обработки и в особенности высокоскоростного фрезерования значительно возросло с появлением новых конструкций станков и инструментов, позволяющих снимать большой объем материала, что приводит к снижению времени обработки при одновременном повышении качества поверхности готовых деталей. В статье G. Warnecke , et al. «Динамика высокоскоростной обработки» отмечается, что скорости резания при высокоскоростной обработке в 2 - 3 раза превышают скорости резания при обычной. В связи с ускорением времени контакта между режущими кромками инструмента и заготовкой поведение ее материала при высокой степени деформации, высокой температуре этого материала и инструмента до конца пока неясно и не может быть точно описано обычными законами металловедения. При обычных скоростях резания с их увеличением сила резания уменьшается, а при очень высоких, благодаря силам инерции, увеличивается. Измерение этих сил затруднено вследствие ограничений, налагаемых измерительной системой. Чтобы обеспечить воспроизводимость измерений фактически действующих сил резания, например, при фрезеровании эта система должна обладать очень высокой жесткостью и иметь датчик с достаточно высокими резонансными частотами. Для увеличения диапазона скоростей, при которых могут быть измерены силы резания, можно использовать алгоритмы расчета сигнала, на который не оказывают влияния системы.
Измерение усилий резания неразрывно связано с измерением температуры резания, в частности, температуры поверхности стружки. Наиболее эффективно в настоящее время проведение такого измерения с помощью оптоволоконного двухцветного пирометра.
В твердосплавной пластине резца, предназначенного для высокоскоростного точения алюминиевого сплава, было просверлено отверстие, в которой введен световод и установлен на расстоянии 0,4 мм от главной режущей кромки и на расстоянии 1 мм от вспомогательной. Такое минимальное расстояние между световодом и поверхностью сходящей с резца стружки позволяет точно измерить ее температуру при минимальном диаметре измеряемого светового пятна. Функция световода – реагировать на излучение в контактной зоне или вблизи ее. Его положение можно регулировать углом наклона просверливаемого отверстия. Для сравнения экспериментальных и моделируемых результатов была выбрана скорость резания 3000 м/мин, подача 0,25 мм/об и глубина резания 2 мм. При таких режимах на передней поверхности резца наблюдается значительная адгезия. Эта адгезия происходит в зоне отверстия для световода. Этим обеспечивается возможность измерения пирометром температуры непосредственно стружки или, по меньшей мере, температуры тонкой алюминиевой пленки на передней поверхности. Полученные температуры стружки показаны на рис. 2, причем они жестко зависят от скорости резания. Было обнаружено, что максимальное увеличение температур происходит, главным образом, в области обычных скоростей резания (до 1000 м/мин). Их дальнейшее увеличение приводит к непропорциональному увеличению температуры стружки. При очень высоких скоростях резания температуры стружки достигают температур плавления материала заготовки.
В статье Marty A. et al. «Учет вибрации заготовок при числовом моделировании высокоскоростной обработки» рассматривается задача создания модели, использующей все существующие физические и эмпирические сведения о системе «заготовка - инструмент - станок» и на основании этого позволяющей прогнозировать такие результаты обработки как окончательное качество поверхности (круглость, шероховатость и другие геометрические параметры) и виброхарактеристики системы «заготовка - инструмент - станок».
С этой целью для заготовки, станка и инструмента были созданы динамические модели, которые могут быть любого типа, но должны описывать реальное физическое поведение указанных компонентов, и геометрическая модель заготовки, позволяющая в любой момент быть в курсе относительно ее граничной поверхности, причем степень ее вибродеформация выводится из динамической модели. И, наконец, была получена модель взаимодействия инструмента с заготовкой (т.е. процесса резания), учитывающая силу резания в любой момент времени. При таком подходе рассмотрение процесса съема материала значительно упрощается, исключаются его механические детали. Основное допущение базируется на использовании концепции так называемого исчезающего инструмента, приводящей к расчету пересечения двух объемов: объема заготовки и объема стружки, получаемого при воздействии на нее передней поверхности инструмента, в результате чего приходят к объемной модели, учитывающей вибродеформацию заготовки.
Практической борьбе с высокочастотными вибрациями при тонкой расточке посвящена статья E. Edhi et al. «Механизм возникновения высокочастотной вибрации при тонком растачивании и ее предотвращение». Было обнаружено, что у расточной оправки с отношением длины к диаметру менее 1,5 при тонком растачивании сквозного отверстия диаметром 15 мм возникают вибрации с частотой свыше 10000 Гц. В результате анализа механизма возникновения и развития таких вибраций был разработан фрикционный демпфер простой конструкции, особенность которого состоит в том, что демпфирующая масса прикреплена постоянным магнитом к расточной оправке некруглого сечения. В торце этой оправки высверлено отверстие под демпфер диаметром 5 мм.
В статье H. Niemann , et al. «Роль параметров резания и покрытий инструментов при высокоскоростном фрезеровании титановых сплавов концевыми сферическими фрезами» отмечается, что в настоящее время свыше половины используемых в промышленности титановых сплавов - это α- β- сплавы Ti -6 Al -4 V. По ряду известных причин они с трудом поддаются механической обработке, в том числе твердосплавными инструментами как цельными, так и составными. У режущих кромок этих инструментов следует минимизировать абразивное истирание/деформацию. Они должны иметь возможность сопротивления механизмам износа, обусловливающих диффузию/растворение, а также быть достаточно вязкими, чтобы противостоять скалыванию/растрескиванию режущих кромок. Поскольку такими свойствами ни один инструмент в комплексе не обладает, то одним из наиболее эффективных решений является нанесение на твердосплавные инструменты различных покрытий. Следует отметить, что с покрытиями в настоящее время выпускают примерно 75 % твердосплавных инструментов.
В то же время результаты ряда исследований позволяют утверждать, что твердосплавные инструменты с покрытиями по сравнению с инструментами без покрытий не обладают очевидными преимуществами как при точении титановых сплавов, так и при их фрезеровании. При фрезеровании этих сплавов концевыми сферическими фрезами скорость резания достигает 400 м/мин, причем разрушение инструмента происходит обычно путем износа по задней поверхности при сравнительно небольшом кратерном износе. Его стойкость существенно продлевалась при охлаждении, причем охлаждение масляным туманом оказалось значительно эффективнее охлаждения поливом.
Известно, что опоры высокоскоростных шпинделей нередко становятся лимитирующим фактором для улучшения их характеристик. Несмотря на быстрое развитие новых типов опор (магнитные, аэро- и гидростатические и пр.), подшипники качения, теперь уже гибридные (со стальными кольцами и керамическими шариками) продолжают сохранять свое лидирующее значение. Новые разработки в этой области, как отмечено в статье O. Bayer «Современные концепции шпиндельных опор», направлены, прежде всего, на улучшение эксплуатационных характеристик, повышение срока службы, надежности и, соответственно, на снижение стоимости опор.
Гибридные подшипники, изготовленные из стали Cronidur 30, имели при испытаниях примерно в 10 раз больший срок службы, чем изготовленные из обычной подшипниковой стали. В частности, как показано в статье H. Voll «Высокоскоростная обработка алюминия», такие подшипники могут быть установлены на высокоскоростных электрошпинделях германской фирмы WEISS GmbH мощностью 80 кВт и с частотой вращения 40000 мин. С их помощью съем материала при обработке алюминия можно довести до 4000 см3/мин.
Другое решение в области опор для электрошпинделей высокоскоростных станков предложено в обзорной статье R. Fos , et al. «Возможности, пределы и исследования высокоскоростных стандартных шпинделей». Известно, что при доведении частот вращения шпинделей до 60 - 80 тыс. мин-1, подшипники являются одним из важнейших ограничительных факторов. Применение любых подшипников, кроме магнитных, ограничивает в основном угловую скорость и мощность привода. Использование магнитных подшипников снимает эти ограничения, но налагает новые в отношении стоимости вследствие необходимости применения значительно более сложной электронной аппаратуры и установки ряда периферийных компонентов. В статье выполнен также синтез теоретических принципов структур магнитных опор и процессов их контроля. Показано, что магнитные опоры применимы при небольших мощностях приводов, например в насосах для перекачивания крови при использовании плоских роторов, где требования к контролю процесса относительно невысоки. Для снабженных магнитными опорами систем более высокой мощности существуют трудности с управлением процессом при высоких скоростях вращения в переходных процессах, возникающих при взаимодействии между функциями сообщения движения и функцией опоры. В настоящее время исследования сосредоточены на разработке новых конструкций магнитных опор и новых методов управления магнитным потоком и переходными процессами, позволяющих стабильно получать высокие скорости вращения исполнительных узлов (например, шпинделей).
1.4 Постановка задачи на дипломное проектирование
Рассматривая приведенные выше доводы, становится ясно, что вопрос модернизации и реконструкции устаревшего парка металлообрабатывающих станков носит актуальный характер. Учитывая перечисленный объем номенклатуры новейших изделий и отдельных узлов для металлообрабатывающих станков, направления модернизации оборудования могут быть очень разнообразны, и из этого разнообразия владелец самостоятельно определяет, какой вид реконструкции ему нужно провести для повышения производительности и качества обработки оборудования.
Задачей этого дипломного проекта является реконструкция горизонтально-расточного станка повышенной жесткости. За базу выбран горизонтально-расточной станок модели 2А622. Для повышения жесткости предусматривается изменение несущей системы станка. Так же предусматривается изменение обрабатывающих характеристик. В совокупности эти изменения должны повысить производительность и качество обработки изделий данной моделью металлообрабатывающего станка.
2. Реконструкция горизонтально-расточного станка
модели 2А622
2.1 Обоснование реконструкции станка
В настоящее время в российской промышленности имеется большой парк морально и физически устаревших координатно-расточных станков моделей 2А450, 2Д450, 2Е450, 2А620, 2А622 и их модификаций производства нашего завода. Возраст этих станков достигает 30-40 лет, поэтому их конструкционные решения не отвечают современным требованиям, предъявляемым к станкам. Кроме того, высокий износ узлов и потеря точностных параметров вызывают проблемы с их эксплуатацией. Всё это требует обновления станочного оборудования, но большинство предприятий в современной экономической обстановке не имеют для этого достаточных средств. Поэтому в данных условиях экономически целесообразно производить модернизацию имеющегося оборудования, в результате чего потребитель получает современный станок, в конструкции которого воплощён наш многолетний опыт производства станков, соответствующий всем требованиям к точности (для данного станка), оснащённый современными комплектующими и системами управления. При этом заказчик, сдав станок на модернизацию, может не ждать когда пройдёт весь производственный цикл модернизации станка, а получить модернизированный станок данной модели (или станок другой модели) из имеющегося на заводе задела по станкам. При этом из цены приобретенного станка вычитается оценочная стоимость сданного станка.
Основными составляющими модернизации координатно-расточных станков c ручным управлением в общем случае являются:
- установка электронной отсчётно-измерительной системы, включающей в себя фотоэлектрические преобразователи линейных перемещений типа ЛИР и устройство цифровой индикации взамен оптических отсчётных устройств;
- использование программируемого контроллера для построения схемы электроавтоматики станка взамен релейной схемы управления;
- шариковые винтовые пары и регулируемые высокомоментные электродвигатели постоянного тока в приводах перемещений стола и салазок взамен зубчато-реечных передач, простых регулируемых электродвигателей постоянного тока и червячных редукторов;
- установка пневмозажимов стола и салазок вместо электромеханических зажимов;
- механизация перемещения шпиндельной коробки;
- применение конструкции привода перемещения гильзы с регулируемым двигателем постоянного тока.
2.2 Компоновка станка повышенной жесткости
Реконструкция данной модели предусматривает проектирование новой стойки и коробки скоростей. За счет замены этих основных частей происходит повышение жесткости станка и как следствие возможность изменений режимов резания, что в свою очередь ведет к повышает производительности.
2.3 Обоснование повышенной производительности станка (режимы резания)
На производительность станка в большей мере влияют режимы резания. При проведении реконструкции происходит повышение частоты вращения шпинделя с 1250 об/мин (у базовой модели) до 2550 об/мин (у модернизированного станка). Изменение частоты обосновывается возможностью использования наиболее прогрессивных режимов резания при помощи новейшего инструмента. Расчет режимов резания на максимальной частоте производится при наиболее возможных жестких режимах работы станка.
2.3.1 Выбор режимов резания
:
Величину подачи S (мм/об) назначить /7/.
S=0,8÷1,9 мм/об
2.3.2
Определить скорость главного движения резания
u
(м/мин), допускаемую режущими свойствами резца по формуле
:
(1)
Примем скорость равную u = 88 м/мин.
где Т – период стойкости, мин /7/
t – глубина резания, при снятии припуска за один рабочий ход :
(2)
где s – подача, мм/об /7/
C, x, y, z, m – коэффициенты и показатели степени /7/
- поправочный коэффициент, учитывающий влияние физико-механических свойств обрабатываемого материала на скорость резания /7/
- поправочный коэффициент, учитывающий влияние состояния поверхности заготовки на скорость резания /7/;
- поправочный коэффициент, учитывающий влияние инструментального материала на скорость резания /7/;
- поправочные коэффициенты, учитывающие влияние геометрических параметров режущей части инструмента на скорость резания /7/;
2.3.3 Составляющие силы резания
: тангенциальную , осевую , радиальную (Н), рассчитаем по формуле:
(3)
где ,x, y, n – коэффициент и показатели степени /7/;
t – глубина резания, мм /7/;
s – подача, об/мм /7/;
v – скорость резания, м/мин /7/;
- поправочный коэффициент, учитывающий влияние качества обрабатываемого материала на составляющие силы резания /7/;
- поправочные коэффициенты, учитывающие влияние геометрических параметров режущей части инструмента на составляющие силы резания /7/.
2.3.4 Мощность резания рассчитаем по формуле
:
(4)
где - тангенциальная составляющая силы резания /7/;
- скорость резания /7/.
2.4 Расчет коробки скоростей
2.4.1 Выбор приводного электродвигателя
Мощность главного электродвигателя вытекает из расчетов режимов резания. Для обеспечения требуемого диапазона частот вращения выбираем двухступенчатый двигатель 4А160 4/2УЗ со следующими характеристиками: Nэл
=11/14 кВт, nэл
=1460/2940 об/мин.
(5)
где nmax
– наибольшая частота вращения шпинделя, об/мин;
nmin
– наименьшая частота вращения шпинделя, об/мин.
Для геометрического ряда частот вращения число ступеней скорости z
, может быть определено из соотношения:
(6)
Вычисленная по этой формуле величина z округляется до целого числа, что приводит к некоторому изменению действительного диапазона регулирования Rn
При настройке последовательно включенными групповыми передачами число ступеней скорости z
может быть представлено в виде:
(7)
где pk
– число отдельных передач в каждой группе;
m
– число групп передач.
При выбранном числе ступеней частот вращения шпинделя z
количество групп передач, количество передач в каждой группе и порядок расположения групп может быть различным.
Число конструктивных вариантов привода N
кон
состоящего из m
групп передач, определяется по формуле:
, (8)
где q
– число групп с одинаковым числом передач.
Если частоты вращения шпинделя изменяются по геометрическому ряду, то передаточные отношения передач в группах образуют геометрический ряд со знаменателем j
х
, где х
– целое число, называемое характеристикой группы передач. Для последовательного получения частот вращения шпинделя сначала переключают передачи одной группы, затем другой и т. д.
В зависимости от принятого порядка переключений группа может быть:
а) основной, характеристика, которой определяется по формуле:
х0
= 1
, (9)
б) первой переборной группой, для которой характеристика определяется по формуле:
х1
= р1
, (10)
где р1
– число передач в основной группе.
в) второй переборной группой, для которой характеристика определяется по формуле:
х2
= р1
×
р2
, (11)
где р2
– число передач в первой переборной группе.
Основной и различными по номеру переборными группами может быть любая группа передач в приводе. Для определенного конструктивного варианта число кинематических N
кин
будет равно числу перестановок из m
групп передач:
N
кин.
=
m
!
, (12)
2.4.6 Определение максимальных передаточных отношений по руппам передач
Общее максимальное передаточное отношение привода umax
, определяется по формуле:
(13)
Поученное передаточное отношение может быть представлено в виде:
(14)
где Н
– показатель степени, определяющий величину общего передаточного отношения.
Определение максимальных передаточных отношений в группах производится путем разбиения общего передаточного отношения на передаточные отношения групп, для чего вычисляется показатель степени Н
и выражается в виде:
, (15)
где hk
– показатель степени, характеризующий величину максимального передточного отношения k
-той группы передач;
m
– число групп передач.
При этом выбранные значения hk
должны быть целыми числами и должны удовлетворять условию:
hk
£
hk
+1
£
…
£
hm
. (16)
Максимальное передаточное отношение в группе umaxk
, определится по формуле:
. (17)
При этом должно быть обеспечено выполнение следующего условия:
. (18)
Так как показатель степени Н
, как правило, не является целым числом, он не может быть точно представлен суммой целых чисел. Поэтому для сохранения величины общего максимального передаточного отношения вводится дополнительная передача от вала электродвигателя на входной вал, передаточное отношение которой, определится по формуле:
, (19)
. (20)
2
.5.1 Выбор первого варианта
Выбирается конструктивный вариант привода, для которого выполняется условие:
pa
³
pb
³
…
³
pr
, (21)
где ра
– число передач в первой от электродвигателя группе;
pr
– число передач в последней от электродвигателя группе.
Из числа соответствующих ему кинематических вариантов выбирается тот, для которого справедливо условие:
xa
£
xb
£
…
£
xr
, (22)
где ха
– характеристика передач первой от электродвигателя группы;
xr
– характеристика передач последней от электродвигателя группы.
Для выбранного в первом случае конструктивного варианта, выбирается еще один кинематический вариант, для которого диапазон регулирования в каждой группе передач удовлетворяет условию:
, (23)
2.5.3 Выбор третьего варианта
Выбирается конструктивный вариант привода с произвольным расположением групп передач. Из числа соответствующих ему кинематических вариантов, выбирается один для которого справедливы условия (22) и (23).
Выбор данного варианта осуществляется за счет изменения распределения общего максимального передаточного отношения по группам передач в одном из ранее выбранных вариантов. При этом обязательным является выполнение условия (23).
Структурная сетка (рисунок 14) строится в соответствии с выбранной формулой структуры привода. В ней находит отражение относительная связь между передаточными отношениями в группах, поэтому лучи для каждой группы проводятся симметрично, а количество интервалов между их концами численно равно характеристике группы, определяемой в соответствии со структурной формулой.
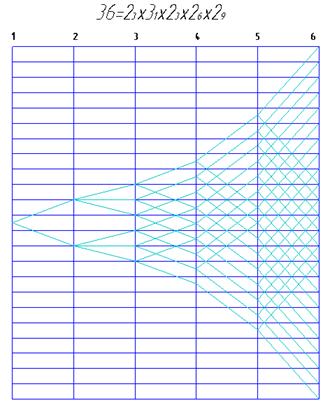
Рисунок 14 – Структурная сетка
График частот вращения (рисунок 15) отражает частоты вращения всех валов привода, включая валы одиночных передач, необходимых для его компоновки. Построение начинают с цепи редукции, обеспечивающей снижение частоты вращения электродвигателя n
эд
.
до nmin
на шпинделе. Для дальнейшего построения используется структурная сетка.
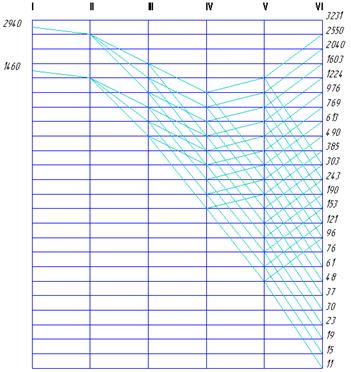
Рисунок 15 – График частот вращения
Для определения передаточных отношений используются построенные графики частот вращения.
Передаточное отношение передачи u
, определяется выражением:
u
=
j
k
, (24)
где k
– число интервалов между горизонталями, перекрытых лучами, соединяющими отметки частот вращения на соседних валах.
При определении чисел зубьев исходят из постоянства межосевого расстояния и числа зубьев, определяют по следующим формулам:
, (25)
, (26)
, (27)
(28)
где z
1
и z
2
– числа зубьев ведущего и ведомого колес;
z
0
– сума чисел зубьев сопряженных колес;
f
– числитель передаточного отношения;
g
– знаменатель передаточного отношения;
K
– наименьшее кратное сумм (f
+
g
);
Е
– целое число;
zmin
= 18 – минимальное число зубьев.
В соответствии с полученными числами зубьев передач, вычерчивается вариант кинематической структуры (рисунок 16).

Рисунок 16 – Кинематическая структура коробки скоростей
Крутящие моменты на валах Т, Н·м, могут быть найдены по формуле:
(29)
где Рэд.
– мощность на валу двигателя, кВт;
h
– КПД участка кинематической цепи от двигателя до рассчитываемого вала;
n
– расчетная частота вращения вала, об/мин.
Кинематический расчет коробки скоростей выполнен с использованием программы «SIRIUS 2». Результаты расчета находятся в приложении А.
Для прямозубой цилиндрической передачи модуль m
н
, мм, определяется по формуле:
(30)
где Kd
– вспомогательный коэффициент; для прямозубых передач Kd
= 770;
z
1
– число зубьев шестерни;
T
1
– вращающий момент на шестерне, Н×м;
u
– передаточное отношение передачи;
s
НР
– допускаемое контактное напряжение, МПа;
KH
b
– коэффициент, учитывающий распределение нагрузки по ширине венца;
(31)
где b
– рабочая ширина венца зубчатой передачи;
d
1
– делительный диаметр шестерни.
Для прямозубой цилиндрической передачи модуль mF
, мм, определяется по формуле:
(32)
где Km
– вспомогательный коэффициент; для прямозубых передач Km
= 14;
KF
b
– коэффициент, учитывающий распределение нагрузки по ширине венца при изгибе;
s
FP
– допускаемое изгибное напряжение, МПа;
YF
1
– коэффициент учитывающий форму зубьев шестерни.
Из полученных расчетных значений mH
и mF
выбирается наибольшее значение и округляется в сторону увеличения до стандартного модуля по ГОСТ 9563– 60. При этом должно выполняться следующее условие:
m
1
£
m
2
£
…
£
mk
, (33)
где m
1
– модуль зубчатых передач группы, расположенной первой от электродвигателя;
mk
– модуль зубчатых передач группы, расположенной последней от электродвигателя.
Для прямозубой цилиндрической передачи межосевое расстояние А
, мм, определяется по формуле:
(34)
где m
– стандартный модуль передачи, мм;
z
2
– число зубьев зубчатого колеса, сопряженного с шестерней.
При определении межосевых расстояний по группам передач должно выполняться следующее условие:
Aw
1
£
Aw
2
£
…
£
Awk
, (35)
где Aw
1
– межосевое расстояние передач группы, расположенной первой от электродвигателя;
Awk
– межосевое расстояние передач группы, расположенной последней от электродвигателя.
Расчет прямозубой эвольвентной передачи выполнен с использованием программы «SIRIUS 2». Результаты расчета находятся в приложении Б.
2.12 Расчет и построение свертки коробки скоростей
Компоновочная схема разрабатывается в следующем порядке:
а) определяются расстояния между осями валов и проводятся осевые линии.
б) на осях располагаются зубчатые колеса, муфты и другие передачи и механизмы в соответствии с кинематической схемой. При этом нужно обеспечить возможность перемещения подвижных зубчатых колес и муфт, размещения механизмов управления, регулирования подшипников, сборки и разборки узла, а также обратить внимание на то, чтобы передвижные блоки зубчатых колес не сцепились одновременно с двумя неподвижными колесами на смежном валу.
в) вдоль оси каждого вала проставляются все соответствующие конструктивные размеры, что позволяет определить его ориентировочную длину.
1. Выбирается положение оси первого вала.
2. Из центра первого вала проводится окружность радиусом, равным расстоянию между осью первого вала и осью соседнего вала. Любая точка на этой окружности может быть центром этого вала и будет удовлетворять условию зацепляемости колес. Центр выбирается с учетом возможности рационального расположения и остальных валов.
3. Таким же путем определяются центры других валов. При расположении валов необходимо обеспечить простую форму корпуса, удобство его обработки, сборки и разборки. Нужно стремиться располагать центры валов на одних и тех же линиях, как по вертикали, так и по горизонтали, что делает корпус более технологичным.
2.12.3 Определение усилий действующих в зубчатых зацеплениях
На основе построенной свертки выполняется расчетная схема (рисунок 17), представляющая собой условное изображение расчетной цепи зубчатых передач. В полюсе зацепления каждой зубчатой пары, по нормали к боковым поверхностям зубьев, действуют силы Fn
, Н, величина которых определяется по формуле:
(36)
где m
и z
– модуль и число зубьев зубчатого колеса;
Т
– вращающий момент приложенный к валу зубчатого колеса, Н×мм.
Рисунок 17 – Свертка коробки скоростей
Сила Р
n
12
, Н, действующая со стороны шестерни на первом валу на зубчатое колесо второго вала:
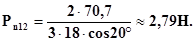
Сила Р
n
23
, Н, действующая со стороны шестерни на втором валу на зубчатое колесо третьего вала:
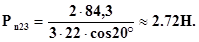
Сила Р
n
34
, Н, действующая со стороны шестерни на третьем валу на зубчатое колесо четвёртого вала:
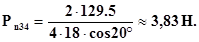
Сила Р
n
45
, Н, действующая со стороны шестерни на четвертом валу на зубчатое колесо пятого вала:
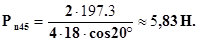
Сила Р
n
56
, Н, действующая со стороны шестерни на пятом валу на зубчатое колесо шестого вала:
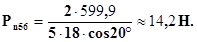
Необходимо определить реакции в каждой опоре с помощью уравнений статики, которые имеют следующий вид:
, , , (37)
где S
Fkx
– сумма всех сил, действующих в плоскости Ozx
;
S
Fky
– сумма всех сил, действующих в плоскости Ozy
;
S
mO
(
Fk
)
– сумма моментов сил относительно выбранной точки плоскости.
Критерием для подшипника служит неравенство:
P
0
£
C
0
,
(38)
где Р0
– эквивалентная статическая нагрузка;
С0
– табличное значение статической грузоподъемности выбранного подшипника.
Величины приведенной статической нагрузки для радиальных подшипников определяются как большие из двух следующих значений:
P0
= X0
Fr
+ Y0
Fa
; P0
= Fr
, (39)
где Х0
– коэффициент радиальной нагрузки;
Y
0
– коэффициент осевой нагрузки;
Fr
– постоянная по величине и направлению радиальная нагрузка, Н;
F
а
– постоянная по величине и направлению осевая нагрузка, Н.
Критерием для выбора подшипника служит неравенство:
Стр.
£ С , (40)
где Cтр.
– требуемая величина динамической грузоподъемности подшипника;
С – табличное значение динамической грузоподъемности выбранного подшипника.
Требуемая динамическая грузоподъемность Стр
, Н, определяется по формуле:
(41)
где Р – эквивалентная динамическая нагрузка, Н;
n – частота вращения вала для которого подбирается подшипник, об/мин;
Lh
– долговечность подшипника, выраженная в часах работы;
a – коэффициент, зависящий от формы кривой контактной усталости.
Эквивалентная динамическая нагрузка Р
, Н, для шариковых радиально-упорных подшипников определяется по формуле:
P = (XVFr
+ YFa
)Kб
Kт
, (41)
где Fr
– радиальная нагрузка, приложенная к подшипнику;
Fa
– осевая нагрузка, приложенная к подшипнику;
V – коэффициент вращения;
Kб
– коэффициент безопасности;
Kт
– температурный коэффициент.
Расчет подшипников качения выполнен с использованием программы
«SIRIUS 2». Результаты расчета находятся в приложении Г.
Под средними участками вала следует понимать участки, на которых расположены шестерни и зубчатые колеса. Определение диаметра производится расчетом на изгиб с кручением.
После завершения расчета, разрабатывается конструкция каждого вала, которая должна обеспечивать возможность сборки коробки скоростей и свободного продвижения зубчатых колес до места посадки.
2.14.2 Расчет валов на усталостную прочность
Расчет сводится к определению расчетных коэффициентов запаса прочности для предположительно опасных сечений валов.
Условие прочности в данном расчете, имеет вид:
(42)
где n – расчетный коэффициент запаса прочности;
[n] = 1,3 ¸1,5 – требуемый коэффициент запаса для обеспечения прочности;
[n] = 2,5 ¸ 4 – требуемый коэффициент запаса для обеспечения жесткости;
ns
– коэффициент запаса прочности по нормальным напряжениям;
nt
– коэффициент запаса прочности по касательным напряжениям.
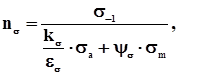 (43)
где s -1
и t -1
– пределы выносливости для материала вала при симметричных циклах изгиба и кручения, МПа;
sа
, tа
и sm
, tm
– амплитуды и средние напряжения циклов нормальных и касательных напряжений, МПа;
ks
и kt
– эффективные коэффициенты концентрации напряжений при изгибе и при кручении;
es
и et
– масштабные факторы для нормальных и касательных напряжений;
ys
и yt
– коэффициенты, учитывающие влияние постоянной составляющей цикла на усталостную прочность.
Можно считать, что нормальные напряжения, возникающие в поперечном сечении вала от изгиба, изменяются по симметричному циклу, тогда:
(44)
где Мизг.
– суммарный изгибающий момент в наиболее нагруженном сечении, Н×мм;
W – момент сопротивления сечения при изгибе, мм3
.
Для круглого сечения вала:
(45)
Для круглого сечения со шпоночной канавкой:
(46)
где b и t – ширина и высота шпоночной канавки, мм.
Для сечения вала со шлицами:
(47)
где x = 1,125 – для шлицев легкой серии;
x = 1,205 – для шлицев средней серии;
x = 1,265 – для шлицев тяжелой серии.
Так как момент, передаваемый валом, изменяется по величине, то при расчете принимают для касательных напряжений наиболее неблагоприятный знакопостоянный цикл – отнулевой:
(48)
где Wк
– момент сопротивления вала при кручении, мм3
.
Для круглого сечения вала:
(49)
Для сечения вала со шпоночной канавкой:
(50)
Для сечения вала со шлицами:
(51)
2.14.3 Расчет на прочность шпонок и шлицевых соединений
Условие прочности по смятию для призматической шпонки имеет вид:
(52)
где z – число шпонок;
sсм
.
– напряжение смятия, МПа;
[s]см.
– допускаемое напряжение при смятии, МПа;
lp
– рабочая длина шпонки, мм;
d – диаметр вала, мм;
h – высота шпонки, мм.
Условие прочности из расчета на срез шпонки:
(53)
где [t]ср.
– допускаемое напряжение при срезе, МПа.
Расчет шлицевых соединений условно производят на смятие втулки в месте ее соприкосновения с боковыми поверхностями зубьев.
(54)
где y = 0,7¸0,8 – коэффициент, учитывающий неравномерность распределения нагрузки по зубьям;
z – число зубьев;
l– рабочая длина зуба вдоль оси вала, мм;
h – рабочая высота контактирующих зубьев в радиальном направлении, мм;
rср.
– средний радиус, мм.
Расчет сечения сплошного вала выполнен с использованием программы «SIRIUS 2». Результаты расчета находятся в приложении Г.
В результате проведенных расчетов можно построить компоновочную схему развертки коробки скоростей.

Рисунок – Развертка коробки скоростей
3. Проектирование шпиндельного узла
Тепловой расчет шпиндельного узла осуществляется на основе решения осесимметричной задачи методом конечных элементов. В качестве типового конечного элемента в данном случае принимается треугольник. Для упрощения формирования расчетной схемы, используется процедура триангуляции четырехугольных элементов, представляющих собой фигуры, полученные при разбиении осевого сечения шпинделя. Под разбиение попадают шпиндель и все элементы установленные на нем за исключением источников тепла, которыми в данном случае являются опоры качения.
Температура аппроксимируется на каждом элементе полиномом, который определяется с помощью узловых значений температуры T
i
.
Вариационная формулировка МКЭ для (22) связана с минимизацией функционала:
- для плоской задачи Э
:
, (55)
- для осесимметричной задачи C
:

(56)
где S1
и S2
—поверхности с заданными граничными условиями второго и третьего родов соответственно.
Расчет выполняется в следующем порядке:
а) назначается количество четырехугольных областей, необязательно правильной формы, в соответствии с условиями однозначности.
б) назначаются граничные условия (конвективный теплообмен и мощности тепловыделения).
в) назначаются исходные данные для расчета мощности тепловыделения и коэффициентов теплоотдачи по теплоотдающим поверхностям.
г) вводятся условия для выполнения теплового расчета (время и номера узлов).
В соответствии с указанными условиями составляется расчетная схема шпинделя (рисунок 19), используемая для последующего расчета на ЭВМ.
Для теплового расчета шпиндельного узла был использован пакет программа «TEMOS».
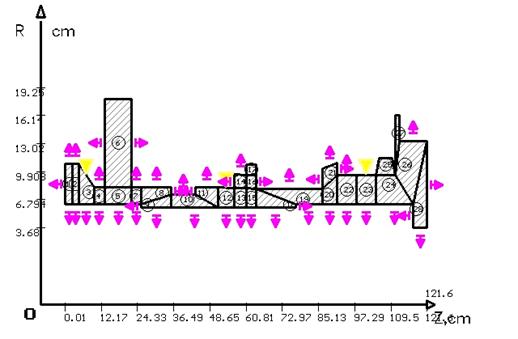
Рисунок 19 – Расчетная схема шпиндельного узла при тепловом расчете
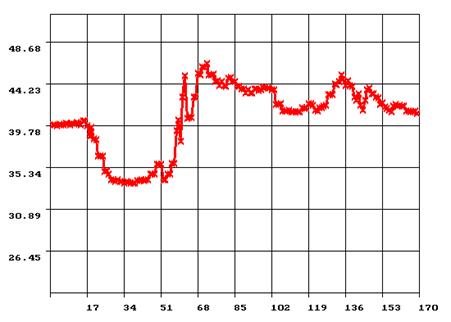
Рисунок 20 – Температурное поле шпиндельного узла
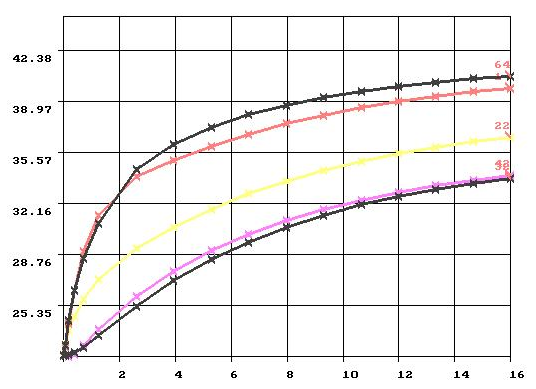
Рисунок 21 – Температурное поле отдельных узлов шпинделя
3.2 Динамический расчет шпиндельного узла
3.2.1 Динамические характеристики шпиндельного узла
На точность работы шпинделя оказывают влияние и динамические характеристики шпиндельного узла, которые являясь показателями динамического качества ШУ, достаточно точно определяют амплитуды колебаний переднего конца шпинделя.
Формы колебаний и их анализ позволяют наглядно представить характер деформирования основных элементов ШУ. Формы колебаний также дают представление о размере колебаний по всей длине шпинделя, что важно для правильного конструирования ШУ.
Низшие собственные частоты колебаний – важные характеристики ШУ, так как практически невозможна работа в резонансной зоне с частотой вращения, близкой к собственной частоте fс
(в интервале ±20%).
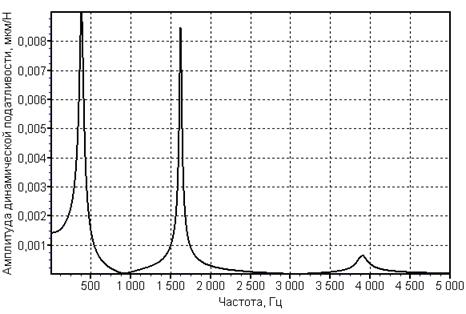
Рисунок 22 – АЧХ шпиндельного узла по координате Х
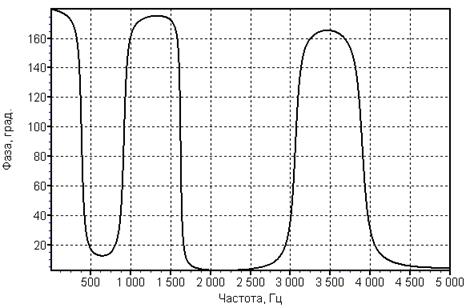
Рисунок 23 – ФЧХ шпиндельного узла по координате Х
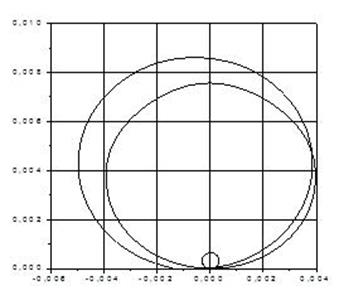
Рисунок 24 – АФЧХ шпиндельного узла по координате Х
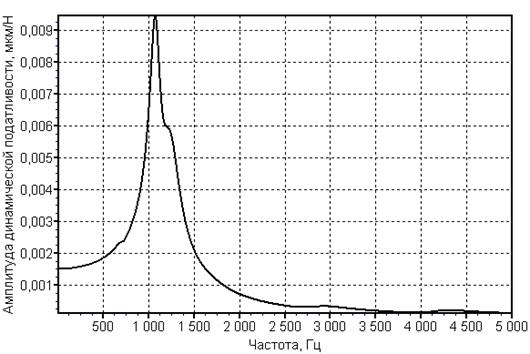
Рисунок 24 - АЧХ шпиндельного узла по координатам Y и Z
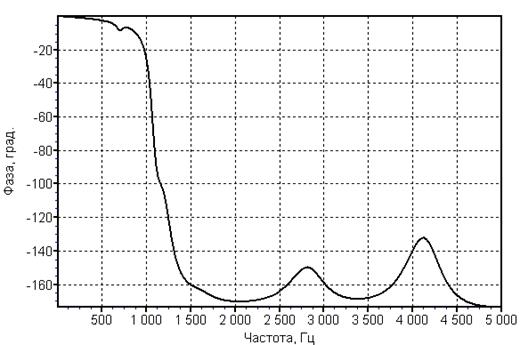
Рисунок 25 – ФЧХ шпиндельного узла по координатам Y и Z
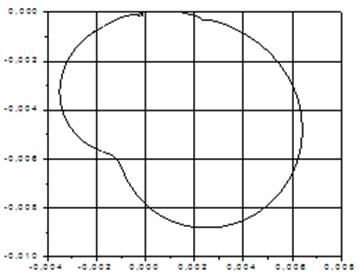
Рисунок 26 – АФЧХ шпиндельного узла по координатам Y и Z
3.2.2 Динамический анализ
Уравнение равновесия для стержневого конечного элемента, без учета гироскопического эффекта и действия центробежных сил, может быть записано в виде:
(57)
где [
Ce
]
– матрица коэффициентов демпфирования;
– вектор узловых скоростей;
При допущении того, что материал стержня не оказывает существенного воздействия на демпфирование колебаний, которое осуществляется, главным образом, посредством упругих демпферов (пружин), расположенных в узлах стержневого элемента, матрица коэффициентов демпфирования принимает вид:
(58)
где
CDOF
– коэффициент демпфирования по соответствующей линейной (угловой) координате, Н×с/м (Н×м×с/рад);
DOF
– индекс, характеризующий степень свободы в рассматриваемом узле;
j
– номер строки;
k
– номер столбца;
– индекс узла
Матрицы [Me
], [Ke
], {u} и {F} идентичны матрицам, используемым при статическом анализе.
По аналогии со статическим анализом уравнение равновесия для модели, состоящей n
элементов, используемое при динамическом анализе, принимает вид:
(59)
где [
Mg
]
– глобальная матрица масс модели;
– глобальный вектор узловых ускорений;
[
Cg
]
– глобальная матрица коэффициентов демпфирования;
– глобальный вектор узловых скоростей.
Глобальная матрица масс [Mg
] формируется путем последовательного суммирования соответствующих коэффициентов в элементных матрицах, то есть:
(60)
Матрицы [Kg
], , и формируются также как и в случае статического анализа модели. Глобальная матрица коэффициентов демпфирования получается аналогично и имеет вид:
(61)
При динамическом анализе шпиндельного узла наибольший интерес представляют его частотные характеристики, определяемые при изменении входной координаты во времени по закону гармонических колебаний. Частота этих колебаний изменяется теоретически от нуля до бесконечности, а практически – в пределах некоторого диапазона частот, который называют рабочим. Для рассматриваемой модели входной координатой является сила или момент силы. Поэтому глобальный вектор узловых нагрузок принимает следующую форму:
(62)
или
(63)
где Fmax
– амплитудное значение силы (момента), Н (Н×м);
е
– основание натуральных логарифмов;
– мнимая единица;
y
– сдвиг силы по фазе, рад;
w
– угловая скорость, рад/с;
t
– время, с;
{
F
1
}
и {
F
2
}
– вещественная и мнимая часть вектора нагрузки,
определяемые по формулам:
(64)
(65)
При изменении входной координаты по гармоническому закону выходная координата (перемещение) также будет изменяться гармонически. Таким образом, глобальный вектор узловых перемещений должен быть представлен в следующем виде:
(66)
или
(67)
где {
umax
}
– амплитудное значение линейного (углового) перемещения, м (рад);
j
– сдвиг перемещения по фазе, рад;
{
u
1
}
и {
u
2
}
– вещественная и мнимая часть вектора перемещений, определяемые по формулам:
(68)
(69)
После подстановки выражений (3.61) и (3.60) в формулу (2.51) уравнение равновесия динамической модели шпиндельного узла принимает вид:
(70)
Решение полученного уравнения относительно неизвестных узловых перемещений имеет следующий вид:
(71)
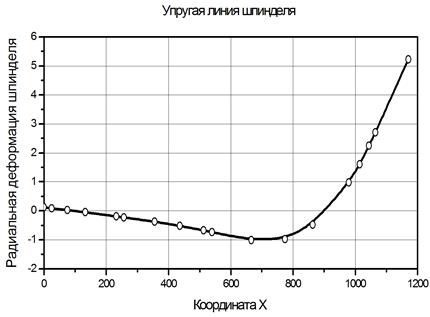
Рисунок 27 – Упругая линия шпинделя
4. Проектирование стойки станка
4.1 Компоновка стойки
В связи с тем, что задачей данного дипломного проекта является реконструкция горизонтально-расточного станка повышенной жесткости, одной из основных задач является проектирование шпиндельной бабки с более высокими динамическими и статическими характеристиками.
Изучив конструкцию базового станка и рассмотрев все возможные варианты ее реконструкции, была рассчитана и спроектирована стойка с улучшенными характеристиками, по сравнению с базовым вариантом.
При проектировании новой стойки были учтены и по возможности использованы все достижения современной науки. В частности внутренняя часть стойки имеет сотовую конструкцию. Такая конструкция позволяет снизить массу примерно на 1\3 часть, но при этом повысить жесткосные и теплодеформационные характеристики стойки.
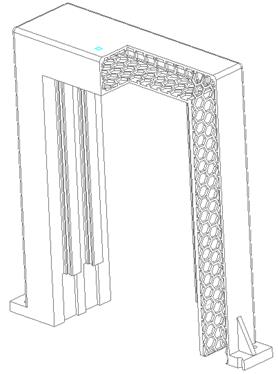
Рисунок 29 – Стойка реконструированного станка с вырезом
Стойка крепится к станине с помощью прямоугольных направляющих, которые могут располагаться горизонтально и вертикально. Также к стойке крепятся направляющие для вертикального перемещения шпиндельной бабки. Стойка также крепится к фундаменту при помощи фундаментных болтов.
4.2 Расчет направляющих
Методика расчета направляющих состоит из следующих этапов:
а) определение суммарных давлений, действующих на каждую грань направляющих;
б) определение среднего удельного давления на каждой из этих граней;
в) определение наибольшего удельного давления на них;
г) сопоставление полученных величин с наибольшими допускаемыми значениями удельных давлений;
Давления на грани направляющих А,Б,С находят из условий равновесия. Также на стойку действуют составляющие Px
, Py
, Pz
силы резания, собственный вес стойки G.
Удельные давления:
; ; ; (72)
где – L – длина направляющих
а, b, c – значения рабочей ширины граней направляющих
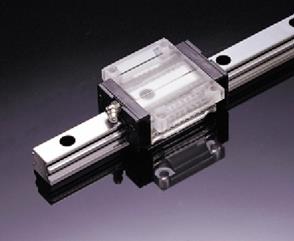
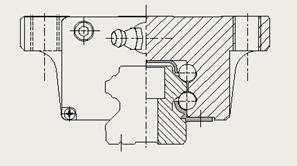
Рисунок– Направляющие качения для шпиндельной бабки
5 Проектирование шпиндельной бабки
5.1 Компоновка шпиндельной бабки
В связи с тем, что бала изменена несущая система и кинематика станка, была спроектирована новая шпиндельная бабка.
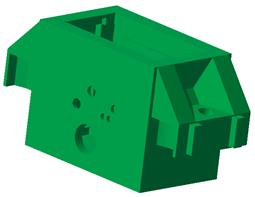
Рисунок 31 – Шпиндельная бабка реконструированного станка модели 2А622
Спроектированная шпиндельная бабка обладает повышенной жесткостью по сравнению со старой. Вертикальное перемещение бабки вдоль стойки происходит по линейным направляющим качения с помощью двух ходовых винтов, что обеспечивает повышенную точность обработки деталей.
6 Статический и динамический расчет стойки и шпиндельной бабки
6.1 Статический расчет стойки и шпиндельной бабки
На точность обработки существенное влияние оказывают статические и динамические характеристики основных органов станка, а именно: статическая и динамическая жесткость, частоты и формы собственных колебаний, амплитудно-частотная характеристика (АЧХ), амплитудно-фазовая частотная характеристика (АФЧХ), коэффициенты демпфирования (или декременты затухания).
6.1.1 Статические характеристики
Статическая рассчитывается по формуле:
(73)
где F
- приложенная сила;
d
- прогиб.
Существенное влияние на жесткость оказывает длина (высота) органа, поэтому при проектировании всегда необходимо стремиться к ее уменьшению.
Жесткость так же зависит от межопорного расстояния b.
6.1.2 Динамические характеристики стойки и шпиндельной бабки
На точность работы станка оказывают влияние и динамические характеристики несущей системы, которые являясь показателями динамического качества, достаточно точно определяют амплитуды колебаний.
Формы колебаний и их анализ позволяют наглядно представить характер деформирования основных элементов несущей системы. Формы колебаний также дают представление о размере колебаний по всей длине (высоте) органа, что важно для правильного конструирования станка.
5. Расчет экономического эффекта от реконструкции горизонтально-расточного станка мод. 2А622
Проведенная реконструкция горизонтально-расточного станка мод. 2А622 позволила повысить его производительность и качество изготовляемых деталей. Рассчитаем годовой экономический эффект от реконструкции выбрав за базу для сравнения горизонтально-расточной станок мод. 2А622. Исходные данные представлены в таблице 5.1.
Таблица 5.1 – Исходные данные для расчета годового экономического эффекта от реконструкции
№ п/п
|
Показатели
|
Усл. обозн.
|
Ед. изм.
|
Базовый вариант (1)
|
Новый вариант
(2)
|
1
|
2
|
3
|
4
|
5
|
6
|
1
|
Годовая программа
|
N год
|
шт/год
|
1600
|
1600
|
2
|
Штучное время
|
t шт
|
мин/шт
|
1,34
|
1,04
|
3
|
Режим работы:
- количество рабочих дней в неделю,
- число смен
- продолжительность смены
|
h дн рабнед
h смен
F смен
|
дни
-
час
|
5
1
8
|
5
1
8
|
4
|
Стоимость единицы оборудования
|
Ц об
|
руб
|
530000
|
600000
|
5
|
Площадь, занимаемая единицей оборудования
|
S об
|
м2
|
3
|
3
|
6
|
Часовая тарифная ставка рабочего
|
С зч
|
руб/час
|
5,90
|
5,90
|
7
|
Коэффициент, учитывающий дополнительную заработную плату
|
К дз
|
-
|
1,2
|
1,2
|
8
|
Коэффициент, учитывающий единый социальный налог
|
К сн
|
-
|
1,262
|
1,262
|
9
|
Районный коэффициент
|
К урал
|
-
|
1,15
|
1,15
|
Продолжение таблицы 5.1
1
|
2
|
3
|
4
|
5
|
6
|
10
|
Мощность электродвигателей
|
N э
|
кВт
|
11
|
11
|
11
|
Стоимость 1 кВт-час электроэнергии
|
Ц э
|
руб/кВт-час
|
1,27
|
1,27
|
12
|
Норма годовых амортизационных отчислений для оборудования
|
Н а об
|
%
|
10
|
10
|
13
|
Норма годовых затрат на ремонт оборудования
|
Н рем
|
%
|
3
|
3
|
14
|
Срок службы инструмента
|
Т сл инстр
|
мин
|
480
|
480
|
15
|
Цена инструмента
|
Ц инстр
|
руб/шт
|
150
|
150
|
16
|
Нормативный коэффициент эффективности капитальных вложений
|
Е н
|

|
0,15
|
0,15
|
5.1 Снижение трудоемкости
Снижение трудоемкости, изм
Тр
,% рассчитывается по формуле:
(74)
где t
шт 1
, t
шт 2
– штучное время при использовании базовой (новой) модели оборудования, мин/шт.
%
5.2 Расчет необходимого количества оборудования и его загрузки
5.2.1 Расчетное количество рабочих мест
Расчетное количество рабочих мест, С расч
рассчитывается по формуле:
(75)
где N
год
– годовая программа, шт/год;
F
дейст
– действительный годовой фонд времени работы оборудования, час/год.
(76)
где K
рн
– коэффициент потерь времени на ремонт и наладку (принимаем Крн
= 0,93
);
F
ном
– номинальный фонд годового времени работы оборудования, час/год;
(77)
где D
кален
– количество календарных дней в году, дней;
D
вых
– количество выходных дней в году, дней;
D
празд
– количество праздничных дней в году, дней;

(78)
где h
смен
– количество смен в день, смен;
F
смен
– количество часов работы в смену, час/смен;
1
– сокращенная продолжительность смен в предпраздничные дни, час;
F
ном дн
– номинальный фонд годового времени работы оборудования, в днях, дн/год.

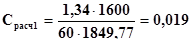
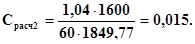
5.2.2 Принятое количество рабочих мест, С прин
Сприн1
= 1
Сприн2
= 1
5.2.3 Загрузка рабочих мест
Загрузка рабочих мест, Кзагр
, % рассчитывается по формуле:
(79)
5.3 Расчет годовой производительности единицы оборудования и ее изменения
5.3.1 Годовая производительность единицы оборудования
Годовая производительность единицы оборудования, ПР
, шт/год рассчитывается по формуле:
(80)
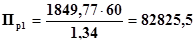
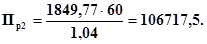
5.3.2 Коэффициент роста производительности оборудования
Коэффициент роста производительности оборудования, Кпр
рассчитывается по формуле:
(81)
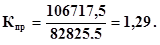
Приводим варианты по оборудованию в сопоставимость:
530000 · 1,29 = 683700 руб.
5.4 Расчет капитальных вложений в оборудование
Капитальные вложения в оборудование, К, руб. рассчитываются по формуле:
(82)
где Цоб
– оптовая цена оборудования, руб;
Ктр
– коэффициент, учитывающий транспортно-заготовительные расходы (принимаем Ктр
= 0,01
);
Кстроит
– коэффициент, учитывающий затраты на строительство и устройство фундамента для оборудования (принимаем Кстроит
= 0,03
);
К осв
– коэффициент, учитывающий затраты на монтаж и освоение оборудования (принимаем К осв
= 0,05
);


5.5 Расчет технологической себестоимости годового выпуска изделий
5.5.1 Расчет годовой заработной платы с отчислениями
Годовая заработная плата с отчислениями, Сзп
, руб/год рассчитывается по формуле:
(83)
где С зн
– часовая тарифная ставка, руб/час;
К дз
– коэффициент, учитывающий дополнительную заработную плату;
К урал
– районный коэффициент;
К сн
– коэффициент, учитывающий единый социальный налог;


5.5.2 Расчет годовых затрат на электроэнергию
Годовые затраты на электроэнергию, Сэл
, руб/год рассчитываются по формуле:
(84)
где Ц э
– стоимость 1 кВт час электроэнергии, руб/кВт-час;
N
эл
– мощность электродвигателей, потребляемая единицей оборудования, кВт;


5.5.3 Расчет годовых амортизационных отчислений для оборудования
Годовые амортизационные отчисления для оборудования, Сам
, руб/год рассчитываются по формуле:
(85)
где Н а
– норма годовых амортизационных отчислений для данного вида оборудования, %
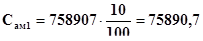
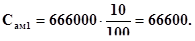
5.5.4 Расчет годовых затрат на текущий ремонт оборудования
Годовые затраты на текущий ремонт оборудования, Срем
, руб/год рассчитываются по формуле:
(86)
где Н рем
– норма годовых затрат на текущий ремонт оборудования, %

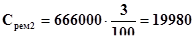
5.5.5 Расчет годовых затрат на инструмент
Годовые затраты на инструмент, Синстр
,руб/год рассчитываются по формуле:
(87)
где Р инстр
– годовой расход инструмента, шт/год;
Т сл инстр
– срок службы инструмента, мин;



где Ц инстр
– цена инструмента, руб/шт;


5.5.6 Расчет технологической себестоимости годового выпуска изделий
Технологическая себестоимость годового выпуска изделий, Ттехн
, руб/год рассчитывается по формуле:
(88)


5.6 Штучная технологическая себестоимость
Штучная технологическая себестоимость, Сшт техн
, руб/шт рассчитывается по формуле:
(89)
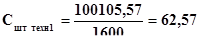
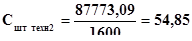
5.7 Экономия от снижения себестоимости
Экономия от снижения себестоимости, изм
С, руб/год рассчитывается по формуле:
(90)

5.8 Расчет приведенных затрат
5.8.1 Годовые приведенные затраты
Годовые приведенные затраты, Зприв год
, руб/год рассчитываются по формуле:
(91)
где Е н
– нормативный коэффициент эффективности капитальных вложений, руб/год/руб;
5.8.2 Удельные приведенные затраты
Удельные приведенные затраты, Зприв уд
, руб/год рассчитываются по формуле:
(92)
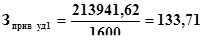
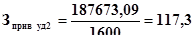
5.9 Годовой экономический эффект
Годовой экономический эффект, Эгод
, руб/год рассчитывается по формуле:
(93)

Результаты расчета приведены в таблице 5.2.
Таблица 5.2 - Технико-экономические показатели проекта
Показатели
|
Базовый
вариант
|
Новый
вариант
|
1 Годовая программа, шт/год
|
1600
|
1600
|
2 Штучное время, мин
|
1,34
|
1,04
|
3 Снижение трудоемкости, %
|
22,39
|
4 Количество оборудования, ед
|
1
|
1
|
5 Годовая производительность оборудования, шт/год
|
82825,5
|
106717,5
|
6 Коэффициент роста производительности оборудования
|
1,29
|
7 Капитальные вложения в оборудование, руб
|
758907
|
666000
|
8 Технологическая себестоимость годового выпуска, руб/год
|
100105,57
|
87773,09
|
9 Экономия от снижения себестоимости, руб/год
|
12332,48
|
10 Годовые приведенные затраты, руб/год
|
213941,62
|
187673,09
|
11 Годовой экономический эффект, руб/год
|
26268,53
|
6. Безопасность труда
6.1 Анализ условий труда
Рабочая зона станка включает в себя опасные зоны – зоны, в которых генерируются вредные и травмирующие воздействия. Незащищенность опасной зоны станка может привести к различным травмам.
При работе станка возникают следующие вредные и опасные факторы: вибрация, шум, пыль, действие электрического тока в сети напряжением 380 В, избыточная температура. Устранение воздействия этих факторов и создание здоровой воздушной среды являются важной задачей, которая должна осуществляться комплексно, одновременно с решением основных вопросов производства.
Метеорологические условия на рабочем месте для категории работ средней тяжести определяются следующими параметрами: относительная влажность оптимальная - 40-60%, допустимая - 75% в холодный период года и 70% в тёплый период года, скорость движения воздуха - 0,2-0,5 м/с в холодный период года и 0,2-1,0 м/с в тёплый период года, температура воздуха оптимальная - 17-20 °С в холодный период года и 20-23 °С в тёплый период года, допустимая 13-24 в холодный период года и 15-29 °С в тёплый период года, температура поверхностей - 9-20 °С (ГОСТ 12.1.005- 88).
Фактические значения параметров микроклимата в помещении цеха следующие:
- в холодный период года: температура воздуха 18 °С; температура поверхностей 9 °С; относительная влажность воздуха 40%; скорость движения воздуха 0,3 м/с;
- в теплый период года : температура воздуха 23 °С; температура поверхностей 20 °С; относительная влажность воздуха 60 %; скорость движения воздуха 0,2 м/с.
Отклонение параметров метеоусловий от санитарных значений согласно ГОСТ 12.1.005-88 может привести в последствии к заболеваниям: простуде, перегреву организма.
Помещение отапливается в холодное время года с целью поддержания заданной температуры воздуха. Система отопления компенсирует потери теплоты через строительные ограждения, а также нагрев проникающего в помещение холодного воздуха, поступающих материалов и транспорта.
От освещения зависят производительность труда и качество выпускаемой продукции. Освещенность на рабочем месте соответствует характеру зрительной работы, обеспечивает достаточно равномерное распределение яркости на рабочей поверхности и в пределах окружающего пространства, на рабочей поверхности должны отсутствовать резкие тени, прямая и отраженная блескость. В дневное время суток используется естественное освещение, которое обеспечивает хорошую освещенность. Естественное освещение помещений осуществляется через световые проемы и выполнено в виде бокового освещения. В темное время суток, а также при недостаточном естественном освещении предусматривается искусственное освещение, как в помещениях, так и на открытых площадках, проездах и т.п. Электрический свет не только заменяет естественное освещение, но и облегчает труд, снижает усталость.
Естественное и искусственное освещение в помещении регламентируется нормами СНиП 23-05-95 в зависимости от характера зрительной работы, системы и вида освещения, фона, контраста объекта с фоном.
Искусственное освещение нормируется количественными (минимальной освещенностью Еmin) и качественными показателями (показателями освещенности и комфорта, коэффициентом пульсации освещенности ).
Естественное освещение характеризуется тем, что создаваемая освещенность изменяется в зависимости от времени суток, года, метеорологических условий. Поэтому в качестве критерия оценки естественного освещения принята относительная величина – коэффициент естественной освещенности КЕО, не зависящий от указанных параметров. КЕО – это отношение освещенности в данной точке внутри помещения к одновременному значению наружной горизонтальной освещенности , создаваемой светом полностью открытого небосвода, выраженное в процентах.
Принято раздельное нормирование КЕО для бокового и верхнего естественного освещения. При боковом освещении нормируют минимальное значение КЕО в пределах рабочей зоны, которое должно быть обеспечено в точках, наиболее отдаленных от окна; в помещениях верхним и комбинированным освещением – по усредненному КЕО в пределах рабочей зоны. Нормированное значение КЕО с учетом характеристики зрительной работы, системы освещения, района расположения зданий на территории страны

(94)
где КЕО
– коэффициент естественной освещенности, определяется по СНиП 23-05-95;
m
– коэффициент светового климата, определяемый в зависимости от района расположения здания на территории страны;
c
– коэффициент солнечного климата, определяемый в зависимости от ориентации здания относительно сторон света; коэффициенты m
и с
определяют по таблицам СНиП 23-05-95.
Согласно СНиП 23-05-95 при работах высокой точности в помещениях с искусственным комбинированным освещением освещенность должна составлять 750 лк, а в помещениях с совмещенным освещением (естественное плюс искусственное) общая освещенность должна быть не менее 200 лк, при показателе ослепленности Р=40 и коэффициенте пульсации =15%.
При работах высокой точности в помещениях с естественным боковым освещением КЕО, , в помещениях с верхним и комбинированным освещением КЕО, (СНиП 23-05-95).
Работа металлообрабатывающего станка сопровождается шумом и вибрацией. Уровень шума достигает 82 дБА, что оказывает вредное влияние на организм человека и в первую очередь на центральную нервную и сердечно-сосудистую системы. Длительное воздействие интенсивного шума может привести к ухудшению слуха, а в отдельных случаях - к глухоте. Шум ослабляет внимание, увеличивает расход энергии при одинаковой физической нагрузке, замедляет скорость психических реакций. В результате снижается производительность и ухудшается качество работы. В данном случае источником шума является двигатель. Допустимый верхний уровень шума на рабочем месте составляет 80 дБА по СН 2.2.4/2.1.8.562-96.
Вредные последствия вибрации возрастают с увеличением быстроходности машин и механизмов, поскольку энергия колебательного процесса возрастает пропорционально квадрату частоты колебаний. При повышении частот колебаний более 0,7 Гц возможны резонансные колебания в органах человека.
Нормирование вибраций производится по ГОСТ 12.1.012-90 «ССБТ. Вибрационная безопасность. Общие требования», Санитарным нормам СН 2.2.4/2.1.8.566-96 «Производственная вибрация, вибрация в помещениях жилых и общественных зданий».
Таблица 6.1 - Нормативные величины вибрации в производственных помещениях предприятий в соответствии с ГОСТ 12.1.012–90
Амплитуда колебаний вибраций, мм
|
Частота вибрации, Гц
|
Скорость колебательных движений, см/с
|
Ускорение колебательных движений, см/с2
|
0,4-0,6
|
До 3
|
0,76-1,12
|
14-22
|
0,15-0,4
|
3-5
|
0,46-0,76
|
14-15
|
0,05-0,15
|
5-8
|
0,25-0,46
|
13-15
|
0,03-0,05
|
8-15
|
0,23-0,28
|
13-27
|
0,009-0,03
|
15-30
|
0,17-0,26
|
27-32
|
0,007-0,009
|
30-50
|
0,16-0,22
|
32-70
|
0,005-0,007
|
50-75
|
0,22-0,23
|
70-112
|
0,003-0,005
|
75-100
|
0,19-0,23
|
112-120
|
1,5-2
|
40-55
|
1,5-2,5
|
25-40
|
Еще одним опасным фактором при работе станка является напряжение в электрической цепи. Станок подключается к цепи напряжением 380 В, значит есть опасность поражения электрическим током. Работа станка связана с использованием различных горючих веществ, таких как керосин (легко воспламеняющаяся жидкость ), масла индустриальные (горючая вязкая жидкость. Плотность – 917 кг/м3
t
всп
.
-181 °С, t
самовоспл
.=
355 °С ), СОЖ (ОСМз - горючее вещество. Плотность 894 кг/м3
, t
всп.
=162 °С, t
самовоспл.
=
178 °С).
Неосторожное обращение с этими веществами, несоблюдение техники безопасности может привести к пожару на территории цеха.
При обработке металлов резанием образуется стружка. Стружка иногда отлетает от места резания на большие расстояния, иногда даже в виде факела, и представляет опасность. Температура стружки может достигать 850 °С.
Кроме стружки в результате резания материалов из чугуна, стали, цветных металлов в воздухе рабочей зоны образуется пыль, которая, попадая в органы дыхания человека, со временем может вызвать различные легочные заболевания. ПДК выделяемой пыли составляет 3-4 мг/м3
по ГОСТ 12.1.005-88. Фактическое значение концентрации пыли в помещении цеха составляет 0,8 мг/м3
, что соответствует указанной норме.
Предприятия машиностроительной промышленности нередко отличаются повышенной пожарной опасностью, так как их характеризует сложность производственных установок, значительное количество легковоспламеняющихся и горючих жидкостей, сжиженных горючих газов, твердых сгораемых материалов и т.д. По отношению к электробезопасности цех относится к помещениям с повышенной опасностью поражения людей электрическим током. С позиции пожарной безопасности цех относится к 3 классу опасности.
Основы противопожарной защиты предприятий определены стандартами (ГОСТ 12.1.004-88). Этими стандартами возможная частота пожаров допускается такой, чтобы вероятность возникновения в течение года не превышала 10-6
.
6.2 Мероприятия по улучшению условий труда
Наличие в цехах большого количества индустриального масла и керосина, а также и других горючих веществ, может привести к пожару на территории предприятия. Для пожарной безопасности предусматривается такое устройство внутризаводских дорог, которое должно обеспечить беспрепятственный проезд пожарных автомобилей к любому зданию. Возникновение пожара в зданиях сопровождается выделением большого количества дыма. Удаление газов и дыма из помещений следует производить через оконные проемы, дымовые люки.
Для защиты от распространения пламени в вентиляционных установках, рекомендуется применять заслонки, отсекатели, водяные завесы. Механический цех, где установлен проектируемый станок, предусматривается оборудовать автоматическими средствами обнаружения пожаров, а также предусмотреть наличие огнетушителей типа ОХВП-10 из расчета один огнетушитель на 50 м² площади цеха и бака для воды из расчета на трехчасовое тушение пожара.
Для хранения промаслянной ветоши предусматривается специальная тара.
Электрооборудование, находящееся в цехе, должно иметь брызгозащитное, закрытое обдуваемое исполнение. Для защиты от поражения электрическим током на проектируемом станке предусматриваем защитное заземление, сопротивление которого 4 Ом. Кнопки на пульте управления защищаем от попадания масла и различной пыли на контакты, что предотвратит короткое замыкание.
Для создания оптимальных или допустимых микроклиматических условий в цехе предусматриваем приточно-вытяжную вентиляцию. В этой системе воздух подается в помещение приточной вентиляцией, а удаляется вытяжной вентиляцией, работающими одновременно.
Для обогрева помещений в холодное время года предусматривается система воздушного и водяного отопления. В цехе рекомендуется поддерживать с помощью кондиционеров оптимальную величину относительной влажности 40 - 60 % и минимальную скорость движения воздуха: в зимнее время 0,2-0,5 м/с, в летнее время 0,2 - 0,1 м/с, а также температуру 19 - 25 ºС.
Для уменьшения шума в станке предлагается применять принудительную смазку трущихся поверхностей, а также балансировку вращающихся элементов станка.
Для уменьшения вибраций, возникающих при работе на станке, во время установки оборудования ставят под станок виброопоры.
В механическом цехе, где установлен станок, рекомендуется общее освещение. Конструкция самого станка предусматривает местное освещение лампами, мощностью 150-200 Вт, которое соответствует нормам освещенности на рабочем месте по СНиП 23-05-95. Естественное освещение осуществляется через фонари в крыше цеха, а искусственное освещение при помощи люминесцентных ламп.
Рабочие в процессе производственной деятельности обеспечиваются специальной одеждой для защиты от общих производственных загрязнений по ГОСТ 12.4.609 - 82 (тип А и тип Б) и полусапогами мужскими по ГОСТ 12.4.164 - 85.
Защитным заземлением называется преднамеренное электрическое соединение с землей или ее эквивалентом металлических нетоковедущих частей, которые могут оказаться под напряжением.
Корпуса электрических машин и другие нетоковедущие части могут оказаться под напряжением при замыкании их токоведущих частей на корпус. Если корпус при этом не имеет контакта с землей, прикосновение к нему также опасно, как и прикосновение к фазе. Если же корпус заземлен, он окажется под напряжением, равным:
U
3
=
I
3
R
3
, (95)
где U
3
-напряжение заземления, В;
I
3
-ток, стекающий в заземление, А;
R
3
-сопротивление стекающего тока, Ом.
Человек, касающийся этого корпуса, попадает под напряжение прикосновения:
U
пр
=
U
3
a
1
a
2
, (96)
где U
пр
- напряжение прикосновения, В;
a
1
- коэффициент напряжения прикосновения;
a
2
- коэффициент напряжения.
Выражение показывает, что чем меньше R
3
и a
1
, тем меньше ток через человека, стоящего на земле и касающегося корпуса оборудования , который находится под напряжением . Таким образом , безопасность обеспечивается путем заземления корпуса заземлителем , имеющем малое сопротивление заземления R
3
и малый коэффициент напряжения прикосновения a
1
.
Защитное заземление может быть эффективно только в том случае, если ток замыкания на землю не увеличивается уменьшением сопротивления заземления . Это возможно в сетях с изолированной нейтрально, где при глухом замыкании на землю или на заземленный корпус ток не зависит от проводимости (или сопротивления) заземления .
Чтобы уменьшить шаговые напряжения за пределами контура, в грунт закладывают специальные шины.
Расчетный ток замыкания на землю – наибольший возможный в данной электроустановке ток замыкания на землю.
В сетях напряжением до 1000 В ток однофазного замыкания на землю не превышает 10 А , так как даже при самом плохом состоянии изоляции и значительной емкости сопротивления фазы относительно земли не бывает менее 100 Ом (½Z
½>100 Ом) . Отсюда ток замыкания на землю в сети напряжением 380 В.
Ih
=
А . (6.4)
В «Правилах безопасной эксплуатации электроустановок» нормируются сопротивления заземления в зависимости от напряжения электроустановки.
В электроустановках напряжением до 1000 В сопротивление заземления должно быть не выше 4 Ом.
Цель расчета заземления – определить число и длину вертикальных элементов, длину горизонтальных элементов (соединительных шин) и разместить заземлители на плане электроустановки, исходя из регламентированных Правилами значений допустимых сопротивлений заземления, напряжения прикосновения и шага, максимального потенциала заземлителя или всех указанных величин.
Расчет простых заземлителей производится в следующем порядке:
-определяется расчетный ток замыкания на землю, принимаем Ih
=11,4 A , что обосновано выше;
-определяется расчетное удельное сопротивление грунта с учетом климатического коэффициента
r
расч
=
r
изм
×
y
, (97)
где - удельное сопротивление крупнообломочного грунта, Ом;
- климатический коэффициент (климатическая зона 1).
Ом
в) сопротивление естественных заземлителей Re
=5,7 Ом;
г) определяется сопротивление искусственного заземлителя, если считать, что искусственные и естественные заземлители соединены параллельно и общее их сопротивление не должно превышать норму RU
, Ом рассчитываемую по формуле:

(98)
Так как к заземляющему устройству присоединяется корпус оборудования напряжением до 1000 В, сопротивление заземляющего устройства должно удовлетворять двум условиям: 10 Ом и 4 Ом. По первому условию:
=10,96 Ом, принимаем 4 Ом как наименьшую.
=13,4 Ом
д) сопротивление одиночного вертикального заземлителя:

(99)
где d
= 0,035 м - эквивалентный диаметр стержней;
I
= 2,5 м - длина стержня;
Н
=1,75 м - расстояние от середины заземлителя до поверхности грунта;
=118,55 Ом
е) предварительно разместив заземлители на плане, определим число вертикальных заземлителей и расстояния между ними, по этим данным определяем коэффициент использования вертикальных стержней .
Длина соединительной полосы (шины) равна периметру прямоугольника 3х1 м , т.е. 8 м. Вертикальные стержни размещаются по периметру прямоугольника, всего 4 стержня, = 0,66
Сопротивление соединительных полос Rn
с учетом коэффициента использования полосы = 0,45:
, (100)
где l
=16 м - длина шины;
b
= 0,1 м - ширина шины;
Н
= 1 м - глубина заложения.
=29,8 Ом.
С учетом коэффициента использования полосы 
=66 Ом.
ж) Требуемое сопротивление растеканию вертикальных стержней:
, (101)
=16,8 Ом.
з) окончательно определяется число вертикальных стержней:
, (102)
где =0,66 – коэффициент использования вертикальных заземлителей
=10,7≈11 шт.
Проведенные расчеты показали, что 11 штук вертикальных стержней обеспечат надежное заземление и предупреждение несчастного случая на участке.
В процессе осуществления трудовой деятельности существует опасность возникновения чрезвычайной ситуации.
Чрезвычайная ситуация (ЧС) – внешне неожиданная, внезапно возникающая обстановка, которая характеризуется резким нарушением установившегося процесса, оказывающая значительное отрицательное влияние на жизнедеятельность людей, функционирование экономики, социальную сферу и окружающую среду.
Под источником чрезвычайной ситуации понимают опасное природное явление, аварию или опасное техногенное происшествие, распространение инфекционных заболеваний и другое, в результате чего произошла или может возникнуть ЧС.
К условиям возникновения чрезвычайной ситуации относят:
- наличие потенциально опасных и вредных производственных факторов при развитии тех или иных процессов;
- действие факторов риска
1)высвобождение энергии в тех или иных процессах;
2)наличие токсичных, биологически активных компонентов в процессах.
Последствиями ЧС могут быть: затопления, разрушения, радиоактивные и химические заражения и т. д.
Одной из ситуаций, которая может возникнуть на рассматриваемом объекте, является пожар. Под пожаром обычно понимают неконтролируемый процесс горения, сопровождающийся уничтожением материальных ценностей и создающий опасность для жизни людей.
Пожары на машиностроительных предприятиях представляют большую опасность для работающих и могут причинить огромный материальный ущерб.
В данном станке используются:
Масло индустриальное 50: горючая, вязкая жидкость. Плотность 917 кг/м3
, температура воспламенения 181 °С, температура самовоспламенения 355 °С. Средством для тушения данного горючего материала является пена или порошок ПБС-3.
Масло индустриальное 50 ГОСТ2487-7.
Смазочно-охлаждающая жидкость МР-5у: горючее вещество с температурой воспламенения 162 °С и температурой самовоспламенения 178 °С. Средством тушения является порошок ПСБ-3, СОЖ МР-5у ГОСТ 2617-70.
Для устранения пожарной опасности на предприятии рекомендуется установить щиты с комплектами пожаротушения в непосредственной близости от рабочего места. В комплект пожаротушения входят: кирки, багры, лопаты, вёдра, огнетушители химические и углекислотные (ОХВП-10, ОУ-8). Также в помещении устанавливают пожарные гидранты центрального водоснабжения и пожарные рукава. В здании, где будут размещаться рабочие места, предусматриваются запасные выходы, на случай пожароопасности и чёткий план эвакуации. Уменьшение вероятности возникновения пожара обеспечат следующие мероприятия. Для предотвращения возгорания кабельных линий рекомендуется использование специальных огнезащитных покрытий, которые препятствуют распространению пожара. Во время ремонта кабельных линий с применением сварки, пайки или открытого огня должны строго соблюдаться правила пожарной безопасности. Необходимо тщательно проверять состояние контактов, так как ослабление контактов в местах присоединения может привести к местному нагреву, а затем к нагреву провода и к нагреву изоляции выше допустимых температур. Надежность работы радио-электронных изделий гарантируется только в определенных интервалах температуры, влажности, тока и напряжения. Из-за возможных отклонений электрических и климатических параметров эти изделия нередко являются источниками открытого пламени и высоких температур. Могут загораться резисторы, выгорать отдельные элементы схемы. Причиной этого являются небрежное исполнение и нарушение правил монтажа.
Для предупреждения возникновения пожара необходимо оборудовать помещение средствами пожарной сигнализации. Наиболее надежной системой пожарной сигнализации является электрическая пожарная сигнализация. Наиболее совершенные виды такой сигнализации дополнительно обеспечивают автоматический ввод в действие предусмотренных на объекте средств пожаротушения.
6.4.1 Расчет времени эвакуации при пожаре
Во время пожара происходит быстрое повышение температуры и увеличение концентрации отравляющих веществ до величин, которые представляют смертельную опасность для организма. По этой причине в случае возгорания должна быть проведена быстрая эвакуация людей из помещения.
Показателем эффективности процесса вынужденной эвакуации является время, в течение которого люди могут при необходимости покинуть отдельные помещения и здание в целом.
Участок располагается на первом этаже здания корпуса. При эвакуации рабочих, количество которых в общем случае составляет двадцать человек, необходимо пройти следующий путь: коридор длиной 35 м и холл длиной 7 м.
Таким образом, полное время эвакуации будет складываться из времени перемещения людей по коридору и холлу:
Тэв.
= tкор.
+ tхолл
, (103)
где Тэв.
– время эвакуации при пожаре, мин;
tкор.
– время прохождения коридора, мин;
tхолл
– время прохождения лестницы, мин.
Время движения людского потока на участке пути определяется по формуле:
, (104)
где L – длина участка пути, м;
v – скорость движения людского потока на данном участке пути, м/мин.
Величина скорости (v) принимается по табличным данным в зависимости от плотности людского потока, определяемого по формуле:
, (105)
где D – плотность людского потока на участке пути, человек/м2
;
N – среднее число людей, находящихся на участке пути (в данном случае N = 20 человек);
b – ширина участка пути (для коридора bкор.
= 2 м, для холла bхолл
= 5 м).
Плотность людского потока в коридоре: ;
в холле: 
При полученных значениях плотности скорость движения людского потока будет равна: в коридоре: vкор.
= 12,5 м/мин; в холле vхолл
= 12,8 м/мин.
С учетом найденных значений скорости время движения людского потока по коридору:
;
в холле: .
Таким образом, время вынужденной эвакуации людей из рассматриваемого помещения составит:
Тэв.
= 2,8+ 0,54 = 3,34 мин
Расчетное время эвакуации при возникновении пожара из корпуса здания составляет 3,34 минут.
Заключение
Результаты реконструкции горизонтально-расточного станка модели 2А622 можно сформулировать в виде следующих выводов:
- спроектирована новая шпиндельная бабка;
- спроектирована новая стойка, что позволило повысить жесткость станка;
- изменена кинематика коробки скоростей, что позволило обеспечить необходимые частоты вращения шпинделя для повышения производительности станка;
- спроектирован новый шпиндельный узел;
Проведенные мероприятия по модернизации станка обеспечили повышение производительности в 1,29 раза, снижение трудоемкости 29,39 %, снижение штучного времени с 1,34 мин до 1,04 мин. Экономия от снижения себестоимости составила 13332 руб./год, годовой экономический эффект 30338,45 руб./год.
Список использованных источников
1. В.Т. Полуянов Технологическая модернизация металлорежущих станков: – Свердловск: Уральский рабочий, 1961, - 370 с.
2. Альбом по проектированию приспособлений: Учеб. Пособие для студентов машиностроительных специальностей вузов / Б.М. Базров, А.И. Сорокин, В.А. Губарь и др. – М.: Машиностроение, 1991.-121 с.
3. Станочные приспособления: Учеб. Пособие / А.Г. Схиртладзе, В.Ю. Новиков, Г.А. Мелетьев, Г.М. Бурков, В.А. Тимирязев, Е.Н. Трембач. – Йошкор-Ола: МарГТУ, 1998. - 170 с.
4. Чернов Н.Н. Металлорежущие станки: Учебник для машиностроительных техникумов.– М.: Машиностроение, 1978. - 389 с.
5. Справочник технолога-машиностроителя. В2-х т. Т.2/ Под ред.А.Г. косиловой и др. – М.: машиностроение, 1985. - 496с.
6. Сборник задач и упражнений по технологии машиностроения / Аверченков В.И. и др. – М.: Машиностроение, 1988.- 192 с.
7. Общемашиностроительные нормативы режимов резания для технического нормирования работ на металлорежущих станках. Часть 1, П.-М.: Машиностроение, 1974. – 456 с.
8. Справочник конструктора-машиностроителя: В 3 т. Т. 1. - 8-е изд., перераб. и доп. / Под ред. И. Н. Жестковой. - М.: Машиностроение, 2001.- 920 с.
9. Абрамов К.Н., Белоновская И.Д., Глинская Н.Ю., Методические указания к курсовому проектрованию по технологии машиностроения. –ГОУ ОГУ: 1993.-25с.
10. Горошкин А.К. приспособления для металлорежущих станков: справочник. – М.: Машиностроение, 1979.- 303 с.
11. Бобровский А.В., Драчев О.И., Николаев С.В., Расторгуев Д.А., Схиртладзе А.Г., Коротков И.А., Шамов Н.П. Расчет и конструирование станочных приспособлений. Учебное пособие.- М.: Славянская школа, 2002.-190с.
12. Проектирование металлорежущих станков и станков и станочных систем: Справочник-учебник Т.2: Расчет и конструирование узлов и элементов станков/Под. ред. А.С. Проникова–М.: МГТУ им. Баумана; Машиностроение, 1995.-320с.
13. Станочные приспособления: Справочник. В 2-х Т. Т.1./Ред. совет: Б.Н. Вардашкин и др.–М.: Машиностроение, 1984.-592с.
14. Обработка резанием, металлорежущий инструмент и станки: Учебник/ В.А. Гапонкин, Л.К. Лукашев, Т.Г. Суворова – М.: Машиностроение, 1990.-448с.
15. Справочник конструктора-машиностроителя: в 3-х т.: Т. 2. - 8-е изд., перераб. и доп. Под ред. И.Н. Жестковой. - М.: Машиностроение, 2001. - 912 с.
16. Антонюк В.Е. Конструктору станочных приспособлений.: Справ. Пособие. – Мн.: Беларусь, 1991. - 400 с.
17. Обработка металлов резанием : Справочник технолога /А.А. Панов, В.В. Аникин, Н.Г. Бойм и др.; Под общей редакцией Панова. –М.: Машиностроение, 1988. – 736 с.
18. Станочные приспособления: Справочник. В 2-х т. /Ред. совет: Б.Н. Вардашкин и др. – М.: Машиностроение , 1984.- Т.2 /Под ред. В.Н. Вардашкина, А.А. Шатилова, 1984.- 656 с.
19. Конструкция шлифовальных станков: Учебник/Т.А. Альперович, К.Н. Константинов, А.Я. Шапиро.-М.: Высш. шк., 1989.-288с.
20. Бабин М.Б., Котов В.Ф. Методические указания к курсовой работе по организации производства. - Оренбург: ОГУ, 1997 - 49 с.
21. Охрана труда в электроустановках: Учебник для вузов / Под ред. Б.А. Князевского. - М.: Энергоатомиздат, 1983. - 287с.
22. Долина П.А. Справочник по технике безопасности. - М.: Энергия, 1993. - 149с.
ПРИЛОЖЕНИЕ А
(справочное)
Кинематический расчет
Исходные данные
Наибольшая частота вращения выходного вала (об/мин)..... 2550
Наименьшая частота вращения выходного вала (об/мин)..... 11.2
Частота вращения вала двигателя привода (об/мин)......…… 1490/2940
Мощность двигателя привода ...........................…………….. 11/14
Знаменатель ряда......................................……………………. 1.26
Код типа коробки передач [коробка скоростей ---> 4 ] …… 4
[ коробка подач ---> 5 ]
Результаты расчета 1
Рекомендуемый конструктивный вариант:
3.0000, 2.0000, 2.0000, 2.0000,
Рекомендуемый кинематический вариант:
1.0000, 3.0000, 6.0000, 9.0000,
Результаты распределения характеристики всей цепи
по группам передач:
Характеристика всей цепи 20.8917
Характеристика 0 0.8917
Характеристика 1 4.0000
Характеристика 2 5.0000
Характеристика 3 5.0000
Характеристика 4 6.0000
Матрица передаточных чисел:
0 0.8138
1 0.3968 0.4999 0.6299
2 0.3149 0.6299
3 0.3149 1.2600
4 0.2499 2.0004
Матрица чисел зубьев:
0 22.00 18.00
1 56.00 22.00 52.00 26.00 48.00 30.00
2 57.00 18.00 46.00 29.00
3 57.00 18.00 33.00 42.00
4 72.00 18.00 30.00 60.00
Матрица частот вращения валов(об/мин):
Частота вращения входного вала коробки передач 1220.6528
Частота вращения второго вала коробки передач
479.5422 610.3264 762.9080
Частота вращения третьего вала коробки передач
151.4344 192.7347 240.9183
302.3201 384.7710 480.9637
Частота вращения четвертого вала коробки передач
47.8214 60.8636 76.0795
95.4695 121.5066 151.8833
192.7347 245.2986 306.6233
384.7710 489.7085 612.1357
Частота вращения пятого вала коробки передач
11.9553 15.2159 19.0199
23.8674 30.3767 37.9708
48.1837 61.3247 76.6558
96.1927 122.4271 153.0339
95.6428 121.7271 152.1589
190.9390 243.0133 303.7666
385.4693 490.5973 613.2466
769.5420 979.4171 1224.2713
Расчетная кинематическая цепь (об/мин)
1500.0000 1220.6528 762.9080 480.9637 151.8833 37.9708
Расчетные моменты на валах (Н/м)
70.7124 84.2881 129.5070 197.2696 599.8869 2304.2855
Ориентировочные диаметры валов (мм)
19.3633 20.5306 23.6907 27.2584 39.4915 61.8480
Результаты расчета 2
Рекомендуемый конструктивный вариант:
3.0000, 2.0000, 2.0000, 2.0000,
Рекомендуемый кинематический вариант:
1.0000, 3.0000, 6.0000, 9.0000,
Результаты распределения характеристики всей цепи по группам передач:
Характеристика всей цепи 20.7151
Характеристика 0 0.7151
Характеристика 1 4.0000
Характеристика 2 5.0000
Характеристика 3 5.0000
Характеристика 4 6.0000
Матрица передаточных чисел:
0 0.8477
1 0.3968 0.4999 0.6299
2 0.3149 0.6299
3 0.3149 1.2600
4 0.2499 2.0004
Матрица чисел зубьев:
0 21.00 18.00
1 56.00 22.00 52.00 26.00 48.00 30.00
2 57.00 18.00 46.00 29.00
3 57.00 18.00 33.00 42.00
4 72.00 18.00 30.00 60.00
Матрица частот вращения валов(об/мин):
Частота вращения входного вала коробки передач 2543.0266
Частота вращения второго вала коробки передач
999.0462 1271.5133 1589.3917
Частота вращения третьего вала коробки передач
315.4883 401.5305 501.9132
629.8335 801.6062 1002.0078
Частота вращения четвертого вала коробки передач
99.6279 126.7991 158.4989
198.8948 253.1388 316.4235
401.5305 511.0388 638.7986
801.6062 1020.2261 1275.2826
Частота вращения пятого вала коробки передач
24.9070 31.6998 39.6247
49.7237 63.2847 79.1059
100.3826 127.7597 159.6996
200.4016 255.0565 318.8207
199.2557 253.5982 316.9978
397.7896 506.2776 632.8470
803.0610 1022.0777 1277.5971
1603.2125 2040.4522 2550.5653
Расчетная кинематическая цепь (об/мин)
3000.0000 2543.0266 1589.3917 1002.0078 316.4235 79.1059
Расчетные моменты на валах (Н/м)
35.3562 40.4583 62.1634 94.6894 287.9457 1106.0571
Ориентировочные диаметры валов (мм)
15.3686 16.0749 18.5492 21.3426 30.9208 48.4254
ПРИЛОЖЕНИЕ Б
(справочное)
Расчет прямозубой эвольвентной передачи
ИСХОДНЫЕ ДАННЫЕ
Крутящий момент на шестерне = 84,28 Н*М
Частота вращения шестерни = 1220 об/мин
Допустимое контактное напряжение = 1100 Мпа
Допустимое изгибное напряжение = 300 Мпа
Отношение ширины венца к нач. диаметру шестерни = 0,4
Число зубъев шестерни = 18
Число зубъев колеса = 22
Степень точности передачи = 7
Расположение передачи - между опор
РЕЗУЛЬТАТЫ РАСЧЕТА
Расчетный модуль по контактным напряжениям = 2,9
Расчетный модуль по изгибным напряжениям = 3,1
Стандартный модуль по ГОСТ 9563-60 = 3,00
Межосевое расстояние = 60 мм
Ширина шестерни = 21,6 мм
Окружная скорость зубъев передачи = 3,45 м/с
ИСХОДНЫЕ ДАННЫЕ
Крутящий момент на шестерне = 129,51 Н*М
Частота вращения шестерни = 762,91 об/мин
Допустимое контактное напряжение = 650 Мпа
Допустимое изгибное напряжение = 220 Мпа
Отношение ширины венца к нач. диаметру шестерни = 0,3
Число зубъев шестерни = 30
Число зубъев колеса = 48
Степень точности передачи = 7
Расположение передачи - между опор
РЕЗУЛЬТАТЫ РАСЧЕТА
Расчетный модуль по контактным напряжениям = 2,94
Расчетный модуль по изгибным напряжениям = 2,97
Стандартный модуль по ГОСТ 9563-60 = 3,00
Межосевое расстояние = 117 мм
Ширина шестерни = 27 мм
Окружная скорость зубъев передачи = 3,6 м/с
ИСХОДНЫЕ ДАННЫЕ
Крутящий момент на шестерне = 197,27 Н*М
Частота вращения шестерни = 480,96 об/мин
Допустимое контактное напряжение = 650 Мпа
Допустимое изгибное напряжение = 220 Мпа
Отношение ширины венца к нач. диаметру шестерни = 0,3
Число зубъев шестерни = 29
Число зубъев колеса = 46
Степень точности передачи = 7
Расположение передачи - между опор
РЕЗУЛЬТАТЫ РАСЧЕТА
Расчетный модуль по контактным напряжениям = 3,5
Расчетный модуль по изгибным напряжениям = 3,5
Стандартный модуль по ГОСТ 9563-60 = 4,00
Межосевое расстояние = 150 мм
Ширина шестерни = 34,8 мм
Окружная скорость зубъев передачи = 2,92 м/с
ИСХОДНЫЕ ДАННЫЕ
Крутящий момент на шестерне = 599,89 Н*М
Частота вращения шестерни = 151,88 об/мин
Допустимое контактное напряжение = 650 Мпа
Допустимое изгибное напряжение = 220 Мпа
Отношение ширины венца к нач. диаметру шестерни = 0,3
Число зубъев шестерни = 42
Число зубъев колеса = 33
Степень точности передачи = 7
Расположение передачи - между опор
РЕЗУЛЬТАТЫ РАСЧЕТА
Расчетный модуль по контактным напряжениям = 3,92
Расчетный модуль по изгибным напряжениям = 3,92
Стандартный модуль по ГОСТ 9563-60 = 4,00
Межосевое расстояние = 150 мм
Ширина шестерни = 50,4 мм
Окружная скорость зубъев передачи = 1,34 м/с
ИСХОДНЫЕ ДАННЫЕ
Крутящий момент на шестерне = 2304,29 Н*М
Частота вращения шестерни = 37,97 об/мин
Допустимое контактное напряжение = 650 Мпа
Допустимое изгибное напряжение = 220 Мпа
Отношение ширины венца к нач. диаметру шестерни = 0,3
Число зубъев шестерни = 60
Число зубъев колеса = 30
Степень точности передачи = 7
Расположение передачи - между опор
РЕЗУЛЬТАТЫ РАСЧЕТА
Расчетный модуль по контактным напряжениям = 4,8
Расчетный модуль по изгибным напряжениям = 4,81
Стандартный модуль по ГОСТ 9563-60 = 5,00
Межосевое расстояние = 225 мм
Ширина шестерни = 90 м
ПРИЛОЖЕНИЕ Г
(справочное)
Расчет реакций, грузоподъемности подшипников и валов
Входной вал
ИСХОДНЫЕ ДАННЫЕ
Расстояние от левой опоры до силы Р = 34 мм
Расстояние от левой опоры до силы Q = 34 мм
Расстояние между опорами = 1 мм
Сила Р действующая на вал = 2,79 H
Сила Q действующая на вал = 0,01 H
Угол между плоскостями действия сил = 0,01 Град
Частота вращения вала = 1450 Об/мин
РЕЗУЛЬТАТЫ РАСЧЕТА
Реакции в опорах
R = 92,40 H
S = 95,20 H
Статическая грузоподъемность подшипников
С01 = 92,40 H
С02 = 95,20 H
Динамическая грузоподъемность подшипников
С1 = 1058,49 H
С2 = 1090,57 H
Изгибающие моменты на валу(X от левого конца)
X1 = 1,00 H
M1 = 0,09 H*м
X2 = 34,00 H
M2 = 0,00 H*м
Выбираем шарикоподшипник радиально-упорный 36204 (одна опора)
Вал 2
ИСХОДНЫЕ ДАННЫЕ
Расстояние от левой опоры до силы Р = 34 мм
Расстояние от левой опоры до силы Q = 205 мм
Расстояние между опорами = 405 мм
Сила Р действующая на вал = 2,79 H
Сила Q действующая на вал = 2,72 H
Угол между плоскостями действия сил = 48 Град
Частота вращения вала = 479,54 Об/мин
РЕЗУЛЬТАТЫ РАСЧЕТА
Реакции в опорах
R = 3,60 H
S = 1,54 H
Статическая грузоподъемность подшипников
С01 = 3,60 H
С02 = 1,54 H
Динамическая грузоподъемность подшипников
С1 = 28,48 H
С2 = 12,22 H
Изгибающие моменты на валу(X от левого конца)
X1 = 34,00 H
M1 = 0,12 H*м
X2 = 205,00 H
M2 = 0,31 H*м
Выбираем шарикоподшипники радиально-упорные 36204 - 2 штуки
Вал 3
ИСХОДНЫЕ ДАННЫЕ
Расстояние от левой опоры до силы Р = 205 мм
Расстояние от левой опоры до силы Q = 595 мм
Расстояние между опорами = 430 мм
Сила Р действующая на вал = 2,72 H
Сила Q действующая на вал = 3,83 H
Угол между плоскостями действия сил = 66 Град
Частота вращения вала = 151,43 Об/мин
РЕЗУЛЬТАТЫ РАСЧЕТА
Реакции в опорах
R = 1,58 H
S = 5,95 H
Статическая грузоподъемность подшипников
С01 = 1,58 H
С02 = 5,95 H
Динамическая грузоподъемность подшипников
С1 = 8,50 H
С2 = 32,07 H
Изгибающие моменты на валу(X от левого конца)
X1 = 205,00 H
M1 = 0,32 H*м
X2 = 595,00 H
M2 = -0,98 H*м
Выбираем шарикоподшипники радиально-упорные 36206 и 36205
Вал 4
ИСХОДНЫЕ ДАННЫЕ
Расстояние от левой опоры до силы Р = 181 мм
Расстояние от левой опоры до силы Q = 327 мм
Расстояние между опорами = 570 мм
Сила Р действующая на вал = 3,83 H
Сила Q действующая на вал = 5,83 H
Угол между плоскостями действия сил = 24 Град
Частота вращения вала = 47,8 Об/мин
РЕЗУЛЬТАТЫ РАСЧЕТА
Реакции в опорах
R = 4,99 H
S = 4,48 H
Статическая грузоподъемность подшипников
С01 = 4,99 H
С02 = 4,48 H
Динамическая грузоподъемность подшипников
С1 = 18,31 H
С2 = 16,46 H
Изгибающие моменты на валу(X от левого конца)
X1 = 181,00 H
M1 = 0,90 H*м
X2 = 327,00 H
M2 = 1,09 H*м
Выбираем шарикоподшипники радиально-упорные 36207 и 36206
Выходной вал
ИСХОДНЫЕ ДАННЫЕ
Расстояние от левой опоры до силы Р = 395 мм
Расстояние от левой опоры до силы Q = 740 мм
Расстояние между опорами = 980 мм
Сила Р действующая на вал = 5,83 H
Сила Q действующая на вал = 14,2 H
Угол между плоскостями действия сил = 108 Град
Частота вращения вала = 12 Об/мин
РЕЗУЛЬТАТЫ РАСЧЕТА
Реакции в опорах
R = 4,09 H
S = 10,24 H
Статическая грузоподъемность подшипников
С01 = 4,09 H
С02 = 10,24 H
Динамическая грузоподъемность подшипников
С1 = 9,47 H
С2 = 23,72 H
Изгибающие моменты на валу(X от левого конца)
X1 = 395,00 H
M1 = 1,62 H*м
X2 = 740,00 H
M2 = 2,46 H*м
Выбираем шарикоподшипники радиально-упорные 36208 и 36207
ПРИЛОЖЕНИЕ Д
(справочное)
Расчет теплового баланса опор качения
Входной вал
Исходные данные:
Количество групп подшипников в опоре…1
Длина опоры, MM.............................…... 15.00
Диаметр или высота опоры, MM……......52.00
N группы Мощность трения
подшипников группы подшипников
1 3.6717
Результаты расчета:
Избыточная температура опоры, Град. - 7.8279... 18.2650
Требуемое количество жидкой смазки, Л/МИН. - 0.0071 ... 0.0166
Первый промежуточный вал
Исходные данные:
Количество групп подшипников в опоре…1
Длина опоры, MM.....................……….….16.00
Диаметр или высота опоры, MM...............62.00
N группы Мощность трения
подшипников группы подшипников
1 2.0188
Результаты расчета:
Избыточная температура опоры, Град. - 4.6660... 10.8874
Требуемое количество жидкой смазки, Л/МИН. - 0.0097... 0.0227
Второй промежуточный вал
Исходные данные:
Количество групп подшипников в опоре… 1
Длина опоры, MM.....................………..... 16.00
Диаметр или высота опоры, MM............. 62.00
N группы Мощность трения
подшипников группы подшипников
1 2.9966
Результаты расчета:
Избыточная температура опоры, Град. - 4.6660... 10.8874
Требуемое количество жидкой смазки, Л/МИН. - 0.0097... 0.0227
Вал 5
Исходные данные:
Количество групп подшипников в опоре… 1
Длина опоры, MM.....................………..... 45.00
Диаметр или высота опоры, MM............. 85.00
N группы Мощность трения
подшипников группы подшипников
1 0.8112
Результаты расчета:
Избыточная температура опоры, Град. - 0.6959... 1.6238
Требуемое количество жидкой смазки, Л/МИН. - 0.0174... 0.0407
ПРИЛОЖЕНИЕ Е
(справочное)
Расчет сечения сплошного вала на статическую прочность и выносливость
РАСЧЕТ СЕЧЕНИЯ ВХОДНОГО ВАЛА
ИСХОДНЫЕ ДАННЫЕ
Изгибающий момент в сечении = 121,23 Н*м
Крутящий момент в сечении = 70,71 Н*м
Предел прочности материала вала = 900 МПа
Максимальный диаметр сечения вала = 22 мм
Минимальный диаметр сечения вала = 22 мм
Ширина шлица или шпонки = 4 мм
Высота шпонки шпонки = 4 мм
Радиус галтели,выточки или признак = 1 мм
Код марки стали = 35
Признак концентратора напряжений = 4
Число шлицев или шпонок в сечении вала = 1
РЕЗУЛЬТАТЫ РАСЧЕТА
Шпонка (торцевая фреза) Х=4, R=1, B=4 мм T=4 мм Z=1
K1=1,706
Запас статической прочности при изгибе = 5,122
Запас статической прочности при кручении = 13,042
Сумарный запас статической прочности = 4,767
Запас усталостной прочности при изгибе = 1,468
Запас усталостной прочности при кручении = 9,479
Сумарный запас усталостной прочности = 1,451
РАСЧЕТ СЕЧЕНИЯ ВАЛА 2
ИСХОДНЫЕ ДАННЫЕ
Изгибающий момент в сечении = 140,54 Н*м
Крутящий момент в сечении = 84,28 Н*м
Предел прочности материала вала = 900 МПа
Максимальный диаметр сечения вала = 22 мм
Минимальный диаметр сечения вала = 22 мм
Ширина шлица или шпонки = 4 мм
Высота шпонки шпонки = 4 мм
Радиус галтели,выточки или признак = 1 мм
Код марки стали = 35
Признак концентратора напряжений = 4
Число шлицев или шпонок в сечении вала = 1
РЕЗУЛЬТАТЫ РАСЧЕТА
Шпонка (торцевая фреза) Х=4, R=1, B=4 мм T=4 мм Z=1
K1=1,706
Запас статической прочности при изгибе = 4,418
Запас статической прочности при кручении = 10,942
Сумарный запас статической прочности = 4,097
Запас усталостной прочности при изгибе = 1,266
Запас усталостной прочности при кручении = 7,953
Сумарный запас усталостной прочности = 1,250
РАСЧЕТ СЕЧЕНИЯ ВАЛА 3
ИСХОДНЫЕ ДАННЫЕ
Изгибающий момент в сечении = 136,79 Н*м
Крутящий момент в сечении = 129,5 Н*м
Предел прочности материала вала = 900 МПа
Максимальный диаметр сечения вала = 28 мм
Минимальный диаметр сечения вала = 24 мм
Ширина шлица или шпонки = 6 мм
Высота шпонки шпонки = 6 мм
Радиус галтели,выточки или признак = 1 мм
Код марки стали = 35
Признак концентратора напряжений = 4
Число шлицев или шпонок в сечении вала = 1
РЕЗУЛЬТАТЫ РАСЧЕТА
Шпонка (торцевая фреза) Х=4, R=1, B=6 мм T=6 мм Z=1
K1=1,706
Запас статической прочности при изгибе = 5,562
Запас статической прочности при кручении = 8,995
Сумарный запас статической прочности = 4,731
Запас усталостной прочности при изгибе = 1,583
Запас усталостной прочности при кручении = 6,481
Сумарный запас усталостной прочности = 1,538
РАСЧЕТ СЕЧЕНИЯ ВАЛА 4
ИСХОДНЫЕ ДАННЫЕ
Изгибающий момент в сечении = 109,36 Н*м
Крутящий момент в сечении = 197,3 Н*м
Предел прочности материала вала = 900 МПа
Максимальный диаметр сечения вала = 36 мм
Минимальный диаметр сечения вала = 28 мм
Ширина шлица или шпонки = 6 мм
Высота шпонки шпонки = 6 мм
Радиус галтели,выточки или признак = 1 мм
Код марки стали = 35
Признак концентратора напряжений = 4
Число шлицев или шпонок в сечении вала = 1
РЕЗУЛЬТАТЫ РАСЧЕТА
Шпонка (торцевая фреза) Х=4, R=1, B=6 мм T=6 мм Z=1
K1=1,706
Запас статической прочности при изгибе = 11,408
Запас статической прочности при кручении = 9,518
Сумарный запас статической прочности = 7,308
Запас усталостной прочности при изгибе = 3,201
Запас усталостной прочности при кручении = 6,739
Сумарный запас усталостной прочности = 2,892
РАСЧЕТ СЕЧЕНИЯ ВАЛА 5
ИСХОДНЫЕ ДАННЫЕ
Изгибающий момент в сечении = 109,36 Н*м
Крутящий момент в сечении = 599,9 Н*м
Предел прочности материала вала = 900 МПа
Максимальный диаметр сечения вала = 40 мм
Минимальный диаметр сечения вала = 36 мм
Ширина шлица или шпонки = 6 мм
Высота шпонки шпонки = 6 мм
Радиус галтели,выточки или признак = 1 мм
Код марки стали = 35
Признак концентратора напряжений = 4
Число шлицев или шпонок в сечении вала = 1
РЕЗУЛЬТАТЫ РАСЧЕТА
Шпонка (торцевая фреза) Х=4, R=1, B=6 мм T=6 мм Z=1
K1=1,706
Запас статической прочности при изгибе = 25,149
Запас статической прочности при кручении = 6,771
Сумарный запас статической прочности = 6,538
Запас усталостной прочности при изгибе = 6,858
Запас усталостной прочности при кручении = 4,627
Сумарный запас усталостной прочности = 3,835
РАСЧЕТ СЕЧЕНИЯ ВЫХОДНОГО ВАЛА
ИСХОДНЫЕ ДАННЫЕ
Изгибающий момент в сечении = 34,14 Н*м
Крутящий момент в сечении = 2304,3 Н*м
Предел прочности материала вала = 900 МПа
Максимальный диаметр сечения вала = 160 мм
Минимальный диаметр сечения вала = 110 мм
Ширина шлица или шпонки = 8 мм
Высота шпонки шпонки = 8 мм
Радиус галтели,выточки или признак = 1 мм
Код марки стали = 35
Признак концентратора напряжений = 4
Число шлицев или шпонок в сечении вала = 1
РЕЗУЛЬТАТЫ РАСЧЕТА
Шпонка (торцевая фреза) Х=4, R=1, B=8 мм T=8 мм Z=1
K1=1,706
Запас статической прочности при изгибе = 2412,839
Запас статической прочности при кручении = 51,505
Сумарный запас статической прочности = 51,493
Запас усталостной прочности при изгибе = 480,720
Запас усталостной прочности при кручении = 24,186
Сумарный запас усталостной прочности = 24,156
ПРИЛОЖЕНИЕ З
(справочное)
Температурный расчет шпиндельного узла
┌───────────────────────────────────────────────────────────────┐
│ КОЭФФИЦИЕНТЫ ТЕПЛООТДАЧИ BT/M**2*K │
├───────┬─────────────┬─────────────┬─────────────┬─────────────┤
│ноmeр │ для нижнeй │ для вeрхнeй │ для лeвой │ для прaвой │
│облaсти│ грaни │ грaни │ грaни │ грaни │
├───────┼─────────────┼─────────────┼─────────────┼─────────────┤
│ │ 1 │ 2 │ 3 │ 4 │
├───────┼─────────────┼─────────────┼─────────────┼─────────────┤
│ 1 │ 46.0360│ 53.0211│ 82.9249│ 0.0000│
│ 2 │ 46.0360│ 53.0211│ 0.0000│ 0.0000│
│ 3 │ 46.0360│ 0.0000│ 0.0000│ 0.0000│
│ 4 │ 46.0360│ 49.1161│ 0.0000│ 0.0000│
│ 5 │ 46.0360│ 0.0000│ 0.0000│ 0.0000│
│ 6 │ 0.0000│ 0.0000│ 98.2592│ 98.2592│
│ 7 │ 46.0360│ 49.1161│ 0.0000│ 0.0000│
│ 8 │ 0.0000│ 49.1161│ 0.0000│ 80.4622│
│ 9 │ 45.4008│ 0.0000│ 71.6354│ 0.0000│
│ 10 │ 45.4008│ 47.8148│ 0.0000│ 0.0000│
│ 11 │ 0.0000│ 49.1161│ 80.7387│ 0.0000│
│ 12 │ 45.4008│ 0.0000│ 0.0000│ 0.0000│
│ 13 │ 45.4008│ 0.0000│ 0.0000│ 0.0000│
│ 14 │ 0.0000│ 50.8863│ 84.0238│ 0.0000│
│ 15 │ 45.4008│ 0.0000│ 0.0000│ 0.0000│
│ 16 │ 0.0000│ 0.0000│ 0.0000│ 83.8143│
│ 17 │ 0.0000│ 0.0000│ 0.0000│ 0.0000│
│ 18 │ 45.4008│ 0.0000│ 0.0000│ 71.0641│
│ 19 │ 46.0360│ 48.8809│ 0.0000│ 0.0000│
│ 20 │ 46.0360│ 0.0000│ 0.0000│ 0.0000│
│ 21 │ 0.0000│ 52.5265│ 83.4643│ 90.4745│
│ 22 │ 46.0360│ 50.8775│ 0.0000│ 0.0000│
│ 23 │ 46.0360│ 0.0000│ 0.0000│ 0.0000│
│ 24 │ 46.0360│ 0.0000│ 0.0000│ 0.0000│
│ 25 │ 0.0000│ 0.0000│ 0.0000│ 0.0000│
│ 26 │ 0.0000│ 56.7825│ 0.0000│ 0.0000│
│ 27 │ 0.0000│ 0.0000│ 0.0000│ 0.0000│
│ 28 │ 40.2621│ 0.0000│ 61.0465│ 88.5833│
└───────┴─────────────┴─────────────┴─────────────┴─────────────┘
ПРИЛОЖЕНИЕ П
(справочное)
┌─────────────────────────────────────────────────────────────┐
│ ПОСТОЯННЫЕ ВРЕМЕНИ СИСТЕМЫ │
├──────┬───────────────────────┬──────┬───────────────────────┤
│NN п/п│ [ мин ] │NN п/п│ [ мин ] │
├──────┼───────────────────────┼──────┼───────────────────────┤
│ 1 │ 231.36824/ 0.004322│ 86 │ 0.03012/ 33.199963│
│ 2 │ 201.32951/ 0.004967│ 87 │ 0.02961/ 33.775009│
│ 3 │ 52.47458/ 0.019057│ 88 │ 0.02866/ 34.894947│
│ 4 │ 19.60326/ 0.051012│ 89 │ 0.02774/ 36.050003│
│ 5 │ 18.54321/ 0.053928│ 90 │ 0.02746/ 36.421028│
│ 6 │ 10.01857/ 0.099815│ 91 │ 0.02585/ 38.683289│
│ 7 │ 4.73847/ 0.211039│ 92 │ 0.02558/ 39.087833│
│ 8 │ 3.93896/ 0.253874│ 93 │ 0.02451/ 40.796440│
│ 9 │ 2.41037/ 0.414874│ 94 │ 0.02342/ 42.704559│
│ 10 │ 1.74574/ 0.572824│ 95 │ 0.02330/ 42.914650│
│ 11 │ 1.58405/ 0.631294│ 96 │ 0.02283/ 43.807236│
│ 12 │ 1.37668/ 0.726384│ 97 │ 0.02251/ 44.417358│
│ 13 │ 1.26167/ 0.792602│ 98 │ 0.02182/ 45.838917│
│ 14 │ 0.93778/ 1.066353│ 99 │ 0.02087/ 47.926167│
│ 15 │ 0.82861/ 1.206841│ 100 │ 0.02033/ 49.192287│
│ 16 │ 0.80185/ 1.247120│ 101 │ 0.01937/ 51.615135│
│ 17 │ 0.70294/ 1.422591│ 102 │ 0.01930/ 51.820023│
│ 18 │ 0.62880/ 1.590333│ 103 │ 0.01925/ 51.939262│
│ 19 │ 0.51886/ 1.927295│ 104 │ 0.01867/ 53.549881│
│ 20 │ 0.47652/ 2.098568│ 105 │ 0.01859/ 53.781609│
│ 21 │ 0.42450/ 2.355696│ 106 │ 0.01821/ 54.919216│
│ 22 │ 0.39998/ 2.500134│ 107 │ 0.01811/ 55.213421│
│ 23 │ 0.34442/ 2.903433│ 108 │ 0.01659/ 60.274029│
│ 24 │ 0.30928/ 3.233325│ 109 │ 0.01644/ 60.815220│
│ 25 │ 0.30224/ 3.308675│ 110 │ 0.01593/ 62.785473│
│ 26 │ 0.29223/ 3.421985│ 111 │ 0.01500/ 66.679344│
│ 27 │ 0.26913/ 3.715658│ 112 │ 0.01479/ 67.594452│
│ 28 │ 0.25458/ 3.928036│ 113 │ 0.01479/ 67.622131│
│ 29 │ 0.22055/ 4.534057│ 114 │ 0.01389/ 72.008652│
│ 30 │ 0.20191/ 4.952746│ 115 │ 0.01374/ 72.778152│
│ 31 │ 0.19802/ 5.049895│ 116 │ 0.01319/ 75.820854│
│ 32 │ 0.19120/ 5.230112│ 117 │ 0.01310/ 76.322144│
│ 33 │ 0.18748/ 5.333882│ 118 │ 0.01290/ 77.503433│
│ 34 │ 0.18422/ 5.428304│ 119 │ 0.01268/ 78.846512│
│ 35 │ 0.17158/ 5.828164│ 120 │ 0.01244/ 80.398315│
│ 36 │ 0.16091/ 6.214795│ 121 │ 0.01231/ 81.218842│
│ 37 │ 0.15536/ 6.436527│ 122 │ 0.01231/ 81.241058│
│ 38 │ 0.15329/ 6.523651│ 123 │ 0.01193/ 83.808113│
│ 39 │ 0.14182/ 7.050992│ 124 │ 0.01154/ 86.618660│
│ 40 │ 0.13574/ 7.367010│ 125 │ 0.01141/ 87.639412│
│ 41 │ 0.11794/ 8.478667│ 126 │ 0.01079/ 92.663620│
│ 42 │ 0.11597/ 8.622961│ 127 │ 0.01068/ 93.621895│
│ 43 │ 0.10912/ 9.164243│ 128 │ 0.01051/ 95.169365│
│ 44 │ 0.10737/ 9.313998│ 129 │ 0.01035/ 96.571976│
│ 45 │ 0.10084/ 9.916328│ 130 │ 0.01006/ 99.442635│
│ 46 │ 0.10037/ 9.963492│ 131 │ 0.00994/ 100.566551│
│ 47 │ 0.09300/ 10.752790│ 132 │ 0.00928/ 107.756332│
│ 48 │ 0.09232/ 10.832183│ 133 │ 0.00921/ 108.589531│
│ 49 │ 0.08685/ 11.514173│ 134 │ 0.00888/ 112.566383│
│ 50 │ 0.08354/ 11.970201│ 135 │ 0.00888/ 112.653755│
│ 51 │ 0.08011/ 12.482639│ 136 │ 0.00878/ 113.912804│
│ 52 │ 0.07980/ 12.530700│ 137 │ 0.00867/ 115.325356│
│ 53 │ 0.07882/ 12.687247│ 138 │ 0.00795/ 125.820915│
│ 54 │ 0.07328/ 13.646398│ 139 │ 0.00782/ 127.913834│
│ 55 │ 0.07244/ 13.805387│ 140 │ 0.00776/ 128.806549│
│ 56 │ 0.07133/ 14.020028│ 141 │ 0.00758/ 131.892426│
│ 57 │ 0.06939/ 14.411319│ 142 │ 0.00741/ 134.883057│
│ 58 │ 0.06267/ 15.957355│ 143 │ 0.00718/ 139.350479│
│ 59 │ 0.06246/ 16.010237│ 144 │ 0.00711/ 140.619904│
│ 60 │ 0.05971/ 16.746704│ 145 │ 0.00663/ 150.799011│
│ 61 │ 0.05723/ 17.474869│ 146 │ 0.00643/ 155.605362│
│ 62 │ 0.05691/ 17.572847│ 147 │ 0.00589/ 169.690079│
│ 63 │ 0.05587/ 17.898434│ 148 │ 0.00560/ 178.672913│
│ 64 │ 0.05384/ 18.573925│ 149 │ 0.00559/ 178.939728│
│ 65 │ 0.05152/ 19.409784│ 150 │ 0.00554/ 180.638748│
│ 66 │ 0.04984/ 20.063517│ 151 │ 0.00551/ 181.354660│
│ 67 │ 0.04947/ 20.214706│ 152 │ 0.00503/ 198.785599│
│ 68 │ 0.04593/ 21.774050│ 153 │ 0.00486/ 205.864029│
│ 69 │ 0.04576/ 21.855066│ 154 │ 0.00476/ 210.095581│
│ 70 │ 0.04499/ 22.225391│ 155 │ 0.00455/ 219.858902│
│ 71 │ 0.04353/ 22.974771│ 156 │ 0.00442/ 226.346848│
│ 72 │ 0.04059/ 24.638704│ 157 │ 0.00439/ 227.684555│
│ 73 │ 0.03972/ 25.176624│ 158 │ 0.00388/ 257.789185│
│ 74 │ 0.03922/ 25.499952│ 159 │ 0.00342/ 292.476196│
│ 75 │ 0.03921/ 25.503365│ 160 │ 0.00301/ 332.115143│
│ 76 │ 0.03673/ 27.223289│ 161 │ 0.00278/ 359.698120│
│ 77 │ 0.03652/ 27.382963│ 162 │ 0.00278/ 360.277344│
│ 78 │ 0.03598/ 27.791597│ 163 │ 0.00273/ 365.766327│
│ 79 │ 0.03500/ 28.575209│ 164 │ 0.00259/ 385.876404│
│ 80 │ 0.03469/ 28.823397│ 165 │ 0.00218/ 458.046967│
│ 81 │ 0.03322/ 30.104521│ 166 │ 0.00191/ 524.208862│
│ 82 │ 0.03316/ 30.158560│ 167 │ 0.00187/ 534.188843│
│ 83 │ 0.03234/ 30.922937│ 168 │ 0.00098/1025.395874│
│ 84 │ 0.03228/ 30.983370│ 169 │ 0.00076/1312.600952│
│ 85 │ 0.03122/ 32.030903│ 170 │ 0.00000/ 0.000000│
└──────┴───────────────────────┴──────┴───────────────────────┘
|