Министерство образования РФ
Тольяттинский государственный университет
автомеханический институт
Кафедра: «Резание, станки и инструмент»
Расчетно-пояснительная записка к курсовому проекту по дисциплине:
“Расчет и конструирование станков”
06.С.03.15.00.000 ПЗ
Студент: Цуркан А.В.
Группа: МСКв - 501
Преподаватель: Гомельский М.В.
Тольятти, 2006.
Содержание
1. Расчет-обоснование технической характеристики станка
2. Кинематический расчет передач проектируемого привода
3. Прочностные расчеты передач, валов, шпиндельного узла
4. Краткое описание станка в целом и подробное описание конструкции привода подач
1. Расчет-обоснование технической характеристики станка
Расчет выполнен по [1].
Определяем наименьший диаметр сверления:
D
min
= (0,25…0,3)D
max
;
где,
D
max
-наибольший диаметр сверления.
D
min
= (0,25…0,3)D
max
=(0,25…0,3)30=7,5мм.
Определяем минимальную подачу при сверлении D
min
:
При обработке самого мягкого (из заданных) материала по табл. 2.2.1:
=0,14-0,18мм, при сверлении стали <600 МПа.
Определяем максимальную подачу при сверлении D
max
:
При обработке самого мягкого (из заданных) материала по табл. 2.2.1:
=0,45-0,55мм, при сверлении стали <600 МПа.
Определяем минимальную подачу при сверлении D
min
:
При обработке самого твердого (из заданных) материала по табл. 2.2.1:
=0,13-0,15мм, при сверлении стали =800…1000 МПа.
Определяем максимальную подачу при сверлении D
max
:
При обработке самого твердого (из заданных) материала по табл. 2.2.1:
=0,32-0,4мм, при сверлении стали =800…1000 МПа.
Определяем минимальную подачу при развертывании D
min
по табл. 2.2.2:
S
minp
=0,8мм, при материале режущей части инструмента из быстрорежущей стали.
Определяем максимальную подачу при развертывании D
max
по табл. 2.2.2:
S
maxp
=1,2мм, при материале режущей части инструмента из быстрорежущей стали.
В качестве S
min
принимаем подачу, меньшую из , ,S
minp
.
Следовательно, S
min
=0,13мм.
В качестве S
max
принимаем подачу, большую из , ,S
maxp
.
Следовательно,
S
max
=1,2мм.
Определяем максимальную скорость резания при сверлении при обработке самого мягкого материала:
;
где,
СV
, ZV
, yV
, m- коэффициенты и показатели степени;
Т
- среднее значение периода стойкости сверл;
- минимальная подача при сверлении D
min
при обработке самого мягкого материала;
D
min
- наименьший диаметр сверления;
К
V
- поправочный коэффициент.
Определяем период стойкости сверла по табл. 2.2.4:
Т=
25мин, для углеродистых сталей.
Определяем коэффициенты и показатели степени, зависящие от материала изделия и инструмента по табл. 2.2.3:
СV
=7;
ZV
=0,4;
yV
=0,7;
m=0,2.
Определяем поправочный коэффициент:
К
V
= К
MV
КИ
V
;
где,
К
MV
- коэффициент, учитывающий механические свойства обрабатываемого материала.
КИ
V
- коэффициент, учитывающий материал инструмента.
.Определяем коэффициент, учитывающий механические свойства обрабатываемого материала:
К
MV
=1,25, для самого мягкого материала.
Определяем коэффициент, учитывающий материал инструмента:
КИ
V
=1, для инструментальных сталей.
К
V
= К
MV
КИ
V
=1.25*1=1.25.
м/мин;
Определяем скорость резания при максимальной мощности резания:
;
где,
D
max
- наибольший диаметр сверления;
- максимальная подача при сверлении D
max
при обработке самого мягкого материала.
Т=
50мин, СV
=9,8,ZV
=0,4,yV
=0,5,m=0,2, К
MV
=1,25, КИ
V
=1;
К
V
= К
MV
КИ
V
=1.25*1=1.25.
м/мин.
Определяем минимальную скорость резания при сверлении при обработке самого твердого материала:
;
где,
- максимальная подача при сверлении D
max
при обработке самого твердого материала.
Т=
50мин, СV
=9,8,ZV
=0,4,yV
=0,5,m=0,2, К
MV
=0,9, КИ
V
=1;
К
V
= К
MV
КИ
V
=0.9*1=0.9;
м/мин.
Определяем минимальную скорость при развертывании:
Vminp
=Vp
kp
;
где,
Vp
- скорости резания, для наибольшей подачи при диаметре развертки Dmax
;
kp
- поправочный коэффициент.
Vp
=9,9м/мин, при Dmax
=30мм и S
maxp
=1,2мм.
Определяем поправочный коэффициент:
kp
=0,78, для углеродистых сталей.
Vminp
=Vp
kp
=9,9*0,78=7,72м/мин.
В качестве V
min
принимаем скорость, меньшую из Vmin
с
и Vminp
.
Следовательно, V
min
=7,72м/мин.
Определяем максимальную частоту вращения шпинделя:
об/мин.
Определяем минимальную частоту вращения шпинделя:
об/мин.
Определяем максимальный крутящий момент при сверлении самого твердого материала сверлом из быстрорежущей стали:
;
где,
CM
, ZM
, yM
–коэффициенты и показатели степени в зависимости от обрабатываемого материала (по табл.2.2.11);
КМр
– коэффициент, учитывающий влияние механических свойств стали на крутящий момент(по табл.2.2.12).
Определяем коэффициенты и показатели степени, зависящие от материала детали и инструмента:
CM
=0,34;
ZM
=2;
yM
=0,8;
;
Нм.
Определяем крутящий момент при максимальной мощности при сверлении самого мягкого материала:
;
CM
=0,34;
ZM
=2;
yM
=0,8;
;
Нм.
Определяем максимальную эффективную мощность при сверлении:
;
где,
nN
– частота вращения шпинделя при сверлении с максимальной мощностью.
Определяем частоту вращения шпинделя при сверлении с максимальной мощностью:
об/мин;

Определяем установленную мощность электродвигателя:
;
где,
η-
коэффициент полезного действия привода.
Определяем коэффициент полезного действия привода:
Принимаем предварительно
= 0,75…0,8.

Определяем максимальное осевое усилие при сверлении самого твердого материала сверлом из быстрорежущей стали:
;
где,
Ср
, Zp
, yp
-
значения коэффициентов и показателей степени в формуле окружной силы. Ср
=680, Zp
=1, yp
=0.7.

Определяем тяговую силу, необходимую для осуществления подачи:
;
где,
d- диаметр шлицев на шпинделе.
Определяем диаметр шлицев на шпинделе:
Принимается предварительно d=Dmax
,следовательно, d=30мм.

Определяем коэффициент трения в направляющих пиноли и на шлицах шпинделя:
Принимаем .
2. Кинематический расчет передач проектируемого привода
В данной работе ведется проектирование коробки скоростей вертикально-сверлильного станка.
Диапазон регулирования частот ступенчатой части привода:
,
где:
nmax
= 1683,7 об/мин–максимальная частота вращения шпинделя, (см. п.1.9);
nmin
= 81,95 об/мин–минимальная частота вращения шпинделя, (см. п.1.8).
Таким образом,
.
Определение числа ступеней подач [6]
,
где R
n
= 20,545 – см. п. 2.1;
φ – знаменатель геометрического ряда коробки подач, выбираем φ = 1,41 для вертикально-сверлильного станка;
.
Принимаем полученное значение равным: z = 11(исходя из ряда).
Выбираем значения подач из нормального ряда чисел в станкостроении [3], который соответствует выбранному знаменателю ряда:
63; 90; 125; 180; 250; 355; 500;710;1000;1400;2000 об/мин
.
Построение структурной сетки
Формула структуры привода имеет следующий вид:
.
Структурная сетка привода 
р1
= 2 р2
= 2 р3
= 2
х1
= 2 х2
= 3 х3
= 5
х3
= 5, так как для обеспечения 11 ступеней подач, необходимо одну перекрыть.
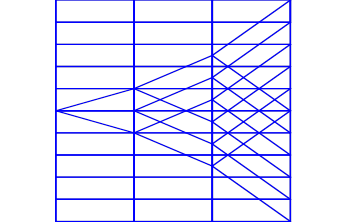
Рисунок 1
Разработка кинематической схемы
За основу разрабатываемой схемы коробки подач возьмем кинематическую схему станка-аналога 2А135 [4].
Кинематическая схема коробки скоростей
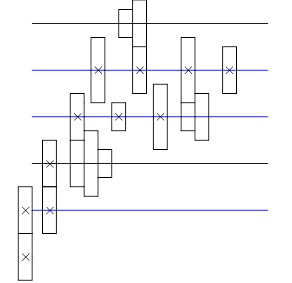
Рисунок 2
Построение графика подач
График подач строится в соответствии с разработанной кинематической схемы станка. Он отражает подачи всех валов привода. Для построения графика используем структурную сетку. Причем понижающие imin
и повышающие imax
передаточные отношения должны соблюдать условия [10]:
; .
Диапазон регулирования групповой передачи должен быть:
.
Исходя из этих условий, назначим минимальные передаточные отношения в коробке подач:
; ; .
Примем передаточные отношения одиночных передач:
; .
График подач
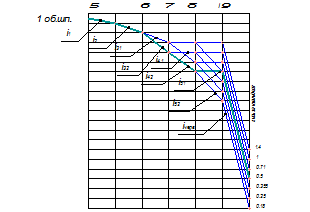
Рисунок 3
Назначение чисел зубьев шестерен
Числа зубьев в групповых передачах назначаем по таблице 3 [8].
Таблица 1 Числа зубьев шестерен групповых передач
S
z
= 75
|
S
z
= 78
|
S
z
= 80
|
|
|
|
1
|
|
1
|

|

|

|

|

|

|
Числа зубьев шестерен одиночных передач:
; .
Определим передаточное отношение i1
:


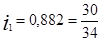
Уравнения кинематического баланса
Поскольку все передаточные отношения получаются с погрешностью, значения подач также получаются неточными. Отклонение значений частот вращения не должно превышать величины:
Δ ≤
±10ּ(φ
– 1) %.
Для знаменателя φ
= 1,41 эта величина составляет Δ = 4,1 %.
1) Значение подачи на графике: S
= 0,18 мм/об
.
Фактическое значение частоты вращения:
.
Отклонение значения подачи:
.
2) Значение подачи на графике: S
= 0,25 мм/об
.
Фактическое значение подачи:
.
Отклонение значения подачи:
.
3) Значение подачи на графике: S
= 0,355 мм/об
.
Фактическое значение подачи:
.
Отклонение значения подачи:
.
4) Значение подачи на графике: S
= 0,5 мм/об
.
Фактическое значение подачи:
.
Отклонение значения подачи:
.
5) Значение подачи на графике: S
= 0,71 мм/об
.
Фактическое значение подачи:
.
Отклонение значения подачи:
.
6) Значение подачи на графике: S
= 1 мм/об
.
Фактическое значение подачи:
.
Отклонение значения подачи:
.
7) Значение подачи на графике: S
= 1,4 мм/об
.
Фактическое значение подачи:
.
Отклонение значения подачи:
.
Отклонения значений частот вращения не выходят за пределы допустимой величины.
3. Прочностные расчеты передач, валов, шпиндельного узла
Расчет передачи колесо-рейка.
Принимаем передачу колесо-рейка, используя станок аналог 2А135.
Определяем контактные напряжения:
,
где,
M
– момент на реечном колесе;
b
– ширина зубчатого колеса; b
=(8…12)m
, принимаем b
=8m
=28мм;
kv
– коэффициент, зависящий от скорости вращения зубчатого колеса. При V
<<1м/с принимаем kv
=1.
m
и z
– модуль и число зубьев зубчатого колеса.

где,
Q
- тяговая сила, необходимая для осуществления подачи, Q
=21256,5Н
(см. п. 1.21.1).


Определяем изгибные напряжения:
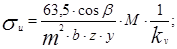
где,
- угол наклона зуба, для прямозубого колеса ;
y
- коэффициент формы зуба, для ориентировочного расчета принимаем
y
=0,1.

Исходя из полученных значений контактных и изгибных напряжений, принимаем Сталь 45, способ термической обработки закалка.
[ ]=1000МПа,
[ ]=250МПа.
Проверочный расчет зубчатых передач на прочность
Расчет проведем для расчетной цепи по [2] с применением специализированного САПР.
Определяем расчетные моменты на валу ведущих колес по формуле:
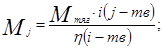
Где Мтяг
– момент на тяговом валу, Нм, Мтяг
=520,8Нм (см. п. 3.1.1);
– коэффициент полезного действия на i-м валу, об/мин.
Расчет моментов начинаем с десятого вала; передаточные отношения на валах берем с графика подач рисунка 3:
1) i10
= 1/47 ;
2) i9
= 1 ;
3) i8
= 40/40 ;
4) i7
= 26/52 ;
5) i6
= 25/50 ;
6) i = 21/30 ;
7) i5
= 30/34 ;
Исходные данные для расчета зубчатых передач занесем в таблицу 2:
Для определения расчетной частоты вращения ведущего колеса и наибольшей частота вращения ведущего колеса в коробке подач возьмем значения частот вращения из структурной схемы коробки скоростей, и умножая эти значения на передаточные отношения расчетной цепи коробки подач получим нужные нам значения.
Значения частот из коробки скоростей следующие:


Определяем значения частот вращения валов в коробке подач по следующим формулам:
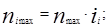
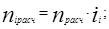
Значения наибольшей и расчетной частот вращения 5-го вала:

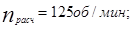
Значения наибольшей и расчетной частот вращения промежуточного вала:


Значения наибольшей и расчетной частот вращения 6-го вала:


Значения наибольшей и расчетной частот вращения 7-го вала:


Значения наибольшей и расчетной частот вращения 8-го вала:


Таблица 2
№
|
Наименование
|
Обозначение
|
Размерность
|
Номер передачи
|
1
|
2
|
3
|
4
|
5
|
1
|
Расчетный момент на валу ведущего колеса
|
М
|
Нм
|
3,89
|
4,21
|
5,72
|
10,86
|
20,65
|
2
|
Вид передачи
|
|
|
цилиндр прямозуб
|
цилиндр прямозуб
|
цилинпрям
|
Цил
прям
|
Цил
прям
|
3
|
Угол наклона зуба
|

|
град
|
0
|
0
|
0
|
0
|
0
|
4
|
Модуль передачи
|
m
|
мм
|
2
|
2
|
2
|
2
|
2
|
5
|
Число зубьев ведущего колеса
|

|
|
30
|
21
|
25
|
26
|
40
|
6
|
Число зубьев ведомого колеса
|

|
|
34
|
30
|
50
|
52
|
40
|
7
|
Ширина зубчатого венца ведущего колеса
|

|
мм
|
12
|
12
|
12
|
12
|
12
|
8
|
Ширина зубчатого венца ведомого колеса
|

|
мм
|
12
|
12
|
12
|
12
|
12
|
9
|
Конструкция (признак переключения) передачи
|
|
|
Не Переключаемая
|
непереключаемая
|
Перек
|
Перек
|
Перек
|
10
|
Расположение зубчатого колеса на валу
|
|
|
посредине
|
На консоли
|
Вблизи
|
Вблизи
|
Вблизи
|
11
|
Расчетная частота вращения ведущего колеса
|

|
об/мин
|
125
|
110
|
77
|
38,5
|
19,25
|
12
|
Наибольшая частота вращения ведущего колеса
|

|
об/мин
|
1000
|
882
|
616
|
308
|
154
|
13
|
Время работы передачи с нагрузкой
|
Т
|
час
|
5000
|
5000
|
5000
|
5000
|
5000
|
14
|
Коэффициент коррекции ведущего колеса
|

|
|
0
|
0
|
0
|
0
|
0
|
15
|
Коэффициент коррекции ведомого колеса
|

|
|
0
|
0
|
0
|
0
|
0
|
16
|
Признак связи колеса с шестерней
|
|
|
Не
паразитное
|
Не
паразитное
|
Не
Паразит.
|
Не
Паразит.
|
Не
Паразит
|
17
|
Режим нагрузки передачи
|
|
|
Средний
|
Средний
|
Средн
|
Сред
|
Сред
|
18
|
Характер процесса резания
|
|
|
Равномерный
|
Равномерный
|
Равн
|
Равн
|
Равн
|
19
|
Вид механической обработки зубьев
|
|
|
шлифован
|
шлифован
|
шлифован
|
шлиф
|
нешлиф
|
20
|
Материал ведущего колеса
|
|
|
40Х-Н
|
40Х-Н
|
40Х-Н
|
40Х-Н
|
40Х-Н
|
21
|
Материал ведомого колеса
|
|
|
40Х-Н
|
40Х-Н
|
40Х-Н
|
40Х-Н
|
40Х-Н
|
Подробный расчет валов. Расчет валов ведем по [3]. Расчет моментов на колесе, приводящем вал в движение: Программа расчета двухопорных валов позволяет работать с валами, на которых расположено только два колеса. Поэтому рассматриваем только колеса входящие в расчетную цепь. Моменты для них уже были рассчитаны в п. 3.2.1. ассчитаем 8-й, 9-й вал на прочность и жесткость. Подготовим исходные данные для расчета обоих валов. Материал для 8-го и 9-го вала принимаем Сталь 45 с пределом текучести σт
=450 МПа, пределом прочности при кручении σ-1
=340 МПа, пределом прочности σв
=750 МПа. Используя чертеж № 06.С.03.15.01.000 ВО – лист 1 и № 06.С.03.15.03.000 ВО – лист 2, составляем расчетные схемы валов. Расчетная схема восьмого вала
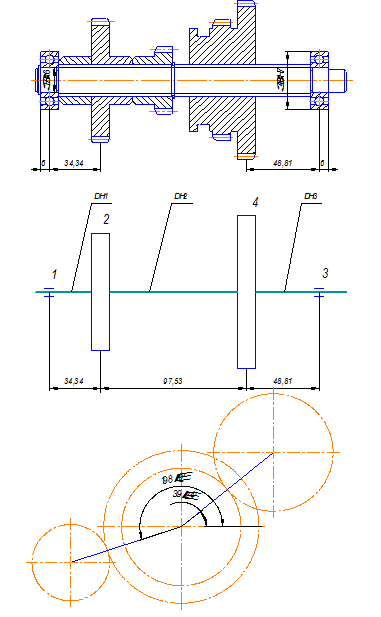
Рисунок 4
Расчетная схема девятого вала
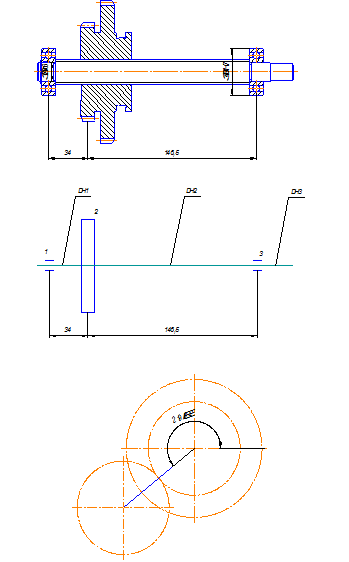
Рисунок 5
Исходные данные для восьмого вала:
1) M – крутящий момент на зубчатом колесе, приводящем вал в движение;
M = 20,65 Н×м (см. п.3.2.1).
2) DHO = m×z – диаметры начальных окружностей зубчатых колес в местах приложения нагрузок.
DHO2
= 2·40 = 80 мм;
DHO4
= 2×52 = 104 мм.
3) - тангенс суммы углов зацепления и трения, при стандартном a = 20° принимаем .

4) KS – эффективный коэффициент концентрации нормальных напряжений в опасных сечениях вала.
;
Используя таблицы [3] определяем: для шлицевого участка вала и материала с sв
= 750 МПа ks
= 1,6; для материала с sв
= 750 МПа и классом шероховатости 6 ks
n
= 1,1.
.
5) KT – эффективный коэффициент концентрации касательных напряжений опасных сечениях вала.
;
Используя таблицы [3] определяем: для шлицевого участка вала и материала с sв
= 750 МПа kt
= 2,45; для материала с sв
= 750 МПа и классом шероховатости 6 kt
n
= 1,1.
.
6) n – частота вращения вала под нагрузкой;
n = 19,25 об/мин
7) L1, L2, L3 – длины участков вала 1, 2, 3 в соответствие с составленной расчетной схемой. Длина L указывается со знаком “минус”, если это – расстояние от опоры до зубчатого колеса, при чем колесо находится между опорами.
L1 = -34,5 мм, L2 = 97,5 мм, L3 = -49 мм.
8) DH1, DH2, DH3 – наружные диаметры вала на участках 1, 2, 3.
,
гдеd – диаметры отдельных ступеней в пределах участка, мм;
l – длины ступеней, мм.
;
;
.
9) DBH1, DBH2, DBH3 – внутренние диаметры вала на участках 1, 2, 3. Если осевого отверстия на участке нет, то задают DBH = 0.
DBH1 = DBH2 = DBH3 = 0.
10) SS, МПа - предел текучести материала вала;
S-150, МПа - предел усталости материала вала.
Эти величины назначают в зависимости от выбранного материала по справочной литературе, для Стали 45 и диаметра заготовки меньше 50 мм.
SS = 450 МПа
SS-150= 300 МПа
11) K – коэффициент податливости опор;
Для опор с высокой жесткостью можно принять К1’=К3’=K1”=K3”=0.
12) B2, B4 – углы наклона зубьев зубчатых колес. Для прямозубых колес B2 = B4 = 0.
13) Ф2, Ф4 – угол между осью OX и линией центров зубчатых пар. Ф2, Ф4 указывается со знаком минус, если угол отсчитывается по часовой стрелки.
Снимаем величины с расчетной схемы: Ф2 = 39°24’, Ф4 = 198°12’.
Исходные данные для девятого вала:
1) M – крутящий момент на зубчатом колесе, приводящем вал в движение;
M = 19,63 Н×м (см. п.3.2.1).
2) DHO = m×z – диаметры начальных окружностей зубчатых колес в местах приложения нагрузок.
DHO2
= 2·40 = 80 мм.
3) - тангенс суммы углов зацепления и трения, при стандартном a = 20° принимаем .

4) KS – эффективный коэффициент концентрации нормальных напряжений в опасных сечениях вала.
;
Используя таблицы [3] определяем: для шлицевого участка вала и материала с sв
= 750 МПа ks
= 1,6; для материала с sв
= 750 МПа и классом шероховатости 6 ks
n
= 1,1.
.
5) KT – эффективный коэффициент концентрации касательных напряжений опасных сечениях вала.
;
Используя таблицы [3] определяем: для шлицевого участка вала и материала с sв
= 750 МПа kt
= 2,45; для материала с sв
= 750 МПа и классом шероховатости 6 kt
n
= 1,1.
.
6) n – частота вращения вала под нагрузкой;
n = 19,25 об/мин
7) L1, L2 – длины участков вала 1, 2 в соответствие с составленной расчетной схемой. Длина L указывается со знаком “минус”, если это – расстояние от опоры до зубчатого колеса, при чем колесо находится между опорами.
L1 = -34 мм, L2 = -146,5 мм.
8) DH1, DH2, DH3 – наружные диаметры вала на участках 1, 2.
,
гдеd – диаметры отдельных ступеней в пределах участка, мм;
l – длины ступеней, мм.
;
.
9) DBH1, DBH2 – внутренние диаметры вала на участках 1, 2, 3. Если осевого отверстия на участке нет, то задают DBH = 0.
DBH1 = DBH2 = DBH3 = 0.
10) SS, МПа - предел текучести материала вала;
S-150, МПа - предел усталости материала вала.
Эти величины назначают в зависимости от выбранного материала по справочной литературе, для Стали 45 и диаметра заготовки меньше 50 мм.
SS = 450 МПа
SS-150= 300 МПа
11) K – коэффициент податливости опор;
Для опор с высокой жесткостью можно принять К1’=К3’=K1”=K3”=0.
12) B2, B4 – углы наклона зубьев зубчатых колес. Для прямозубых колес B2 = B4 = 0.
13) Ф2, Ф4 – угол между осью OX и линией центров зубчатых пар. Ф2, Ф4 указывается со знаком минус, если угол отсчитывается по часовой стрелки.
Снимаем величины с расчетной схемы: Ф2 = 219°24’.
Анализ полученных результатов.
В первую очередь оценивается суммарный прогиб валов под колесом 2 и 4:
;
.
гдеF2
и F4
– прогиб под колесом, приводящим вал в движение и колесом, передающим движение на следующий вал соответственно;
F2P, F2T, F4P, F4T – составляющие прогибов, получаемые по программе.
Должны удовлетворятся следующие условия:
, 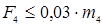
где m2
, m4
– модули зубчатых колес 2, 4.
Далее оцениваем коэффициенты запаса прочности с учетом действия касательных и нормальных напряжений обозначенных N2 и N3. Должно выполнятся условие:
N2 ³1,5…2,5
N3 ³1,5…2,5.
Выполним проверку для шестого вала:
Условия по прогибу следующие:
мм;
мм.
Прогиб под колесом 2:
,
F2P = 0,007254;
F2T = - 0,000025.
мм.
,
F4P = -0,007191;
F4T = 0,000552.
мм.
Таким образом
0,0073 0,06;
0,0072 0,06.
Условие по прогибу выполняется. Сравниваются коэффициенты запаса в опасных сечениях:
,
.
Коэффициенты запаса удовлетворяют требованиям
Выполним проверку для девятого вала:
В первую очередь оценивается суммарный прогиб валов под колесом 2 и 4:
;
.
гдеF2
и F4
– прогиб под колесом, приводящим вал в движение и колесом, передающим движение на следующий вал соответственно;
F2P, F2T– составляющие прогибов, получаемые по программе.
Должны удовлетворятся следующие условия:
, 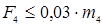
где m2
– модули зубчатых колес 2.
Далее оцениваем коэффициенты запаса прочности с учетом действия касательных и нормальных напряжений обозначенных N2 и N3. Должно выполнятся условие:
N2 ³1,5…2,5
N3 ³1,5…2,5.
Выполним проверку для шестого вала:
Условия по прогибу следующие:
мм.
Прогиб под колесом 2:
,
F2P = 0,007254;
F2T = -0,000025.
мм.
Таким образом
0,0073 0,06.
Условие по прогибу выполняется. Сравниваются коэффициенты запаса в опасных сечениях:
.
Коэффициенты запаса удовлетворяют требованиям
Расчет шпиндельного узла
Определение вылета консоли шпинделя
По технической литературе [9] , исходя из максимального диаметра сверления, по ГОСТ 25557-82 выбираем 4 конус Морзе. По ГОСТ 2848-75 выписываем для данного конуса Морзе основные геометрические размеры конца шпинделя: вылета консоли – а и диаметра переднего конца шпинделя – D1
:
Для 4 конуса Морзе D1
=60мм, а=188.
Определение жесткости шпинделя
По указанию преподавателя принимаем жесткость шпинделя j
шп
=20Н/мкм.
Определение диаметра шпинделя под передней опорой
По номограмме [7] ориентировочно определяем оптимальный диаметр шпинделя d
опт
и коэффициент расстояния между опорами Копт
. При жесткости шпинделя j
ш
= 20 Н/мкм и вылете консоли а = 188 мм, Копт
= 2,5; dопт
= 50 мм.
Расстояние между опорами шпинделя определим из соотношения:
мм.
Выбор подшипников
По стандарту норм точности и жесткости [9] определяем радиальное биение шпинделя: Δ = 6 мкм
.
мкм.
Схема биения шпинделя (векторы биения опор направлены в разные стороны)
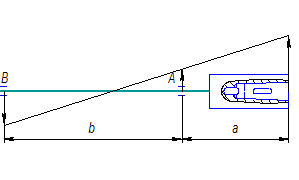
Рисунок 6
Допускаемое радиальное биение подшипников передней опоры можно определить по формуле:
,
Где Δ – допускаемое радиальное биение переднего конца шпинделя, Δ = 6 мкм;
а
– вылет консоли шпинделя, а
= 188 мм
;
b
– расстояние между опорами шпинделя, b
= 470 мм
;
мкм.
Допускаемое радиальное биение подшипников задней опоры:
,
.
По радиальному биению дорожки качения внутреннего кольца подшипника [15] подбираем класс точности подшипников:
– для передней опоры – класс точности 2, δА
= 2,5 мкм
;
– для задней опоры – класс точности 4, δВ
= 5 мкм
.
Поскольку точность подшипника в передней опоре меньше требуемой, необходимо применить специальную сборку. Для этого измеряется биение всех подшипников шпинделя, в месте максимального биения ставится отметка на торце кольца. Шпиндель собирают так, чтобы векторы биения в опорах были направлены в одну и ту же сторону.
Схема биения шпинделя (векторы биения опор направлены в одну сторону)
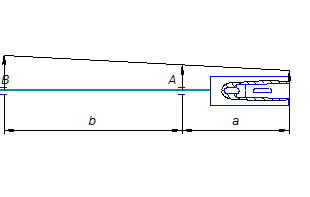
Рисунок 7
В этом случае биение можно определить по формуле:
,
гдеδА
– радиальное биение подшипников передней опоры, δА
= 2,5 мкм;
δВ
– радиальное биение подшипников задней опоры, δВ
= 5 мкм;
mА
– число подшипников в передней опоре, mА
= 3;
mВ
– число подшипников в задней опоре, mВ
= 2;
а
– вылет консоли шпинделя, а
= 188 мм;
b
– расстояние между опорами шпинделя, b
= 470 мм;
мкм.
Полученное биение не превышает допустимой погрешности опор.
4. Краткое описание станка в целом и подробное описание конструкции привода подач
Вертикально-сверлильный станок предназначен для выполнения операций сверления, рассверливания, зенкерования, зенкования, развёртывания отверстий в различных деталях, а также для торцевания и нарезания резьб машинными метчиками в условиях индивидуального и серийного производства. На станке обрабатываются детали сравнительно небольших размеров и веса.
Технические характеристики станка
|
Наибольший диаметр сверления
|
35 мм
|
Пределы частот вращения шпинделя в минуту
|
63 –1000
|
Пределы величин продольных подач
|
0,18-1,4
|
Мощность главного движения электродвигателя
|
5 кВт
|
Несущей системой станка является колонна. Колонна расположена на основании станины. В верхней части колонны расположен главный электродвигатель с коробкой скоростей. На колонне расположены направляющие, по которым перемещается шпиндельная бабка с коробкой подач и подъемным механизмом. На основании станины установлен стол, на который устанавливается обрабатываемая деталь и закрепляется в машинных тисках или в специальных приспособлениях. Режущий инструмент в зависимости от формы его хвостовика закрепляется в шпинделе станка при помощи патрона или переходных втулок. Наличие электрореверса, управляемого как автоматически, так и вручную, обеспечивает возможность нарезания резьбы при ручном подводе и отводе метчика.
Коробка подач вертикально-сверлильного станка изображена на чертеже 06.С.03.15.01.000.ВО. Она позволяет сообщить шпинделю 7 различных подач.
Движение подачи заимствуется от шпинделя V.
Движение передается через шестерни 30-34 и 21-30 на вал V
I
,
коробку подач с передвижными блоками, предохранительную муфту, вал Х,
червячную передачу 1-47, вал Х
I
и реечную передачу гильзе шпинделя.
От вала V
I
две скорости вращения сообщаются валу V
II
,
на котором жестко закреплены шестерни 45, 50, 39 и 26. От вала V
II
четыре скорости вращения передаются валу V
III
,
на котором расположен переключаемый двойной блок и жестко закреплены шестерни 40 и 21.
От вала V
III
восемь скоростей вращения передается валу IX
.
Теоретически коробка подач обеспечивает 8 скоростей вращения, однако, как видно из рисунка 1, одна из них повторяющаяся, поэтому станок имеет только 7 различных величин подач.
От вала IX
через кулачковую муфту движение сообщается валу X
, на котором закреплен червяк. Червячное колесо 47 расположено на одном валу с реечной шестерней 14, находящейся в зацеплении с рейкой, нарезанной на гильзе шпинделя. Муфта служит для предохранения механизма подач от поломок при перегрузках, а также для автоматического выключения подачи при работе по упорам.
Валы V
I
– IX
снабжены шлицами. Закрепление неподвижных зубчатых колес на валах V
I
I
, VII
I
в осевом направлении осуществляется с помощью пружинных упорных колец и втулок. В опорах валов применены шариковые радиальные однорядные подшипники. Колесо 30 на валу V
I
установлено консольно и закреплено на нем с помощью шпонки. Каждый из валов коробки подач имеет одну фиксированную и одну плавающую опору. Подшипник фиксированной опоры выполнен со стопорной канавкой под упорное кольцо, препятствующее осевым перемещениям и удерживаются круглой гайкой с отверстиями на торце под ключ, которая стопорится стопорной многолапчатой шайбой. Подшипник плавающей опоры не закреплен наружным кольцом в осевом направлении и допускает перемещение вала при тепловом расширении.
Для переключения передач используется однорукояточный механизм, изменение величины подачи происходит при помощи передвижения рукоятки в двух направлениях. Вращением рукоятки, которая закреплена на валу, свободно перемещающегося внутри полого вала, движение передается через зубчатое колесо 48 на зубчатый диск 48. Диск имеет два торцовых криволинейных паза, которые расположены по разные стороны диска. В криволинейные пазы диска входят ролики, установленные на качающихся рычагах. Эти рычаги при вращении диска поворачиваются на определенный угол относительно своих осей в зависимости от кривизны пазов. Сухари, смонтированные на концах рычагов, входят в пазы вилок. Вилки сидят на направляющих скалках и входят в кольцевые выточки блоков шестерен и перемещают их в требуемое положение для данной величины подачи. При продольном перемещении рукоятки, рейка на конце вала зацепляется с колесом, затем через зубчатое колесо и рейку движение передается на вилку, которая перемещает двойной блок.
Втулка имеет по периферии 8 V-образных канавок, в которые входит фиксатор, подпираемый пружиной. Натяжение пружины регулируется резьбовой пробкой. На валу рукоятки также имеется одна V-образная канавка, регулирующая величину хода в продольном направлении. На передней части втулки нанесены цифры величин подач. Стрелка на втулке указывает величину подачи.
Передаточные отношения при вращении вала рукоятки, 1:1, следовательно, одному обороту рукоятки соответствует один полный оборот диска.
Передний конец шпинделя выполнен по ГОСТ 2848-75 – конец шпинделя сверлильных станков. В передней опоре шпинделя установлены три подшипника: два подшипника серии 110 ГОСТ 8338-75 шариковые радиально однорядные и шариковый упорный одинарный подшипник серии 8210 ГОСТ 6874-75. Передняя опора, как и задняя, выполнена фиксированной.
Задняя опора шпинделя состоит из подшипника серии 110 ГОСТ 8338-75 шарикового радиально однорядного и шарикового упорного одинарного подшипника серии 8210 ГОСТ 6874-75. Регулировка задней опоры осуществляется с помощью круглой гайки с отверстиями на торце под ключ. Через втулку гайка воздействует на кольцо шарикового упорного одинарного подшипника. Кольцо смещается по шейке, деформируясь в осевом направлении, и выбирает зазор между дорожкой и телами качения. Величина максимального натяга устанавливается упорной втулкой.
Поскольку точность подшипников в передней опоре меньше требуемой, шпиндель необходимо собирать так, чтобы векторы биения в опорах были направлены в одну и ту же сторону.
Список литературы
1. Расчет технической характеристики металлорежущих станков. Методические указания к курсовому и дипломному проектированию. Составитель Гомельский М. В. 1992.
2. Проверочный расчет на прочность зубчатых передач на ПЭВМ. Методические указания к курсовому и дипломному проектированию. Составитель Гомельский М. В. 2000.
3. Расчет двухопорных валов на ПЭВМ с учетом деформации опор. Методические указания к курсовому и дипломному проектированию. Составитель Гомельский М. В. 2000.
4. Кучер А. М., Металлорежущие станки. Изд. 2-е. “Высшая школа”, – М.: Машиностроение, Ленинград 1972.
5.Перель Л. Я., Филатов А. А. Подшипники качения: Расчет, проектирование и обслуживание опор: Справочник. –2-е изд., перераб. и доп. – М.: Машиностроение, 1992. – 608 с.: ил.
6.Расчет и конструирование станков. Курсовое и дипломное проектирование: Учеб. Пособие / Н.С. Ачеркан, В.Э. Пуш. – Машгиз, 1952.
7.Альбом иллюстраций к лекционному курсу по дисциплине “РиКС”. / Под ред. М.В. Гомельского, 2003, стр. 16.
8.ГОСТ 2848 – 75. Станки металлорежущие. Концы шпинделей сверлильных и фрезерных станков. Основные и присоединительные размеры.
9.Анурьев В.И. Справочник конструктора-машиностроителя: В 3-х т. – 5-е изд., перераб. и доп. – М.: Машиностроение, 1980. – 557 с., ил.
|