Московская Государственная Академия
Тонкой Химической Технологии
им. М.В. Ломоносова
Кафедра процессов и аппаратов химических технологий
Расчетно-пояснительная записка к курсовому проекту
по расчету ректификационной установки
Студент: гр. ХТ-405
Руководитель:
Москва 2002
ПЛАН
ВВЕДЕНИЕ
Цель и задачи курсового проектирования
Описание технологической схемы
Выбор конструкционного материала
Расчет контактных устройств6
Расчет потоков дистиллята и кубового остатка
РАСЧЕТ ГАБАРИТОВ КОЛОННЫ
Расчет габаритов верха колонны
Расчет габаритов низа колонны
Расчет гидравлического сопротивления колонны
РАСЧЕТ ТЕПЛООБМЕННОЙ АППАРАТУРЫ
Диаметры штуцеров
Расчет кубового испарителя
Расчет конденсатора-дефлегматора
Подогреватель исходной смеси
Водяной холодильник дистиллята
Водяной холодильник кубового остатка
Расчет и выбор конденсатоотводчиков
Расчет емкостных аппаратов
Расчет тепловой изоляции
Расчет центробежного насоса
Расчет толщины обечайки
Список использованной литературы
Введение
Ректификация - один из самых распространенных технологических процессов в химической, нефтеперерабатывающей и, во многих других отраслях промышленности.
Ректификация - это процесс разделения бинарных или многокомпонентных паровых, а также жидких смесей на практически чистые компоненты или их смеси, обогащенные легколетучими или тяжелолетучими компонентами; процесс осуществляется в результате контакта неравновесных потоков пара и жидкости.
Характерной особенностью процесса ректификации являются следующие условия образования неравновесных потоков пара и жидкости, вступающих в контакт: при разделении паровых смесей неравновесный поток жидкости образуется путем полной или частичной конденсации уходящего после контакта потока пара, в то время как при разделении жидких смесей неравновесный паровой поток, образуется путем частичного испарения уходящей после контакта жидкости. Вследствие указанных особенностей проведения процесса неравновесные потоки пара и жидкости, вступающие в контакт, находятся в состоянии насыщения, при этом пар более нагрет, нежели жидкость, и в нем содержится больше тяжелолетучих компонентов, чем в жидкости. После контакта пар обогащается легколетучими, а жидкость - тяжелолетучими компонентами за счет взаимного перераспределения компонентов между фазами.
Цель и задачи курсового проектирования
Курсовой проект базируется не только на теории процессов и аппаратов химической технологии, но и на ряде предшествующих дисциплин (графика, техническая механика, физическая химия). Качество проекта зависит от уровня овладения знаниями по указанным дисциплинам, от умения пользоваться технической литературой и от проявленной при проектировании инициативы.
Целью курсового проектирования является закрепление знаний, приобретенных при изучении перечисленного ряда дисциплин, а также привитие навыков комплексного использования полученных теоретических знаний для решения конкретных задач по аппаратному оформлению технологических процессов.
Курсовой проект состоит из расчетно-пояснительной записки и чертежей проектируемой установки на двух листах стандартного размера - 814х576. На первой листе помещаются общий вид основного аппарата установки с достаточным количеством проекций (продольные и поперечные разрезы) и наиболее важные узлы. На втором листе приводится технологическая схема установки.
Описание технологической схемы
Исходную смесь из емкости Е1 центробежным насосом Н1 подают в теплообменник - подогреватель исходной смеси П, где она нагревается до температуры кипения. Нагретая смесь поступает на разделение в ректификационную колонну КР на тарелку питания, где состав жидкости равен составу исходной смеси х1.
Стекая вниз по колонне, жидкость взаимодействует с поднимающимся вверх паром, образующимся при кипении жидкости в кубовом испарителе К. Начальный состав пара примерно равен составу кубового остатка хо, т.е. обеднен легколетучим компонентом. В результате массообмена с жидкостью пар обогащается легко летучим компонентом. Для более полного обогащения верхнюю часть колонны орошают, в соответствии с заданным флегмовым числом жидкостью (флегмой) состава х2, получаемой в дефлегматоре Д путем конденсации пара, выходящего из колонны. Часть конденсата выводится из дефлегматора в виде готового продукта разделения - дистиллята, который охлаждается в теплообменнике - холодильнике дистиллята Х2 и направляется в емкость Е3.
Из кубовой части колонны насосом непрерывно выводится кубовая жидкость - продукт, обогащенный труднолетучим компонентом, который охлаждается в теплообменнике - холодильнике кубового остатка Х1 и направляется в емкость Е2.
Таким образом, в ректификационной колонне осуществляется непрерывный процесс разделения исходной бинарной смеси на дистиллят (с высоким содержанием легколетучего компонента) и кубовый остаток (обогащенный труднолетучим компонентом).
Выбор конструкционного материала
Материал для изготовления колонн и теплообменной аппаратуры выбирается в соответствии с условиями их эксплуатации (прочность, механическая обработка, свариваемость). Главным же требованием является их коррозийная стойкость. Последняя оценивается в зависимости от скорости коррозии.
Предпочтительны материалы, скорость коррозии которых не превышает 0,1-0,5 мм/год, а по возможности - более стойкие (скорость коррозии 0,01-0,05 мм/год).
Сталь марки ОХ17Т обладает повышенной сопротивляемостью межкристаллической коррозии и устойчива как к ацетону, так и к бензолу. Для трубопроводов выберем марку Х17.
Стали удовлетворительно обрабатываются резанием и обладают удовлетворительной свариваемостью.
Сталь ОХ17Т (ГОСТ 5632-61)
l=25,1 Вт/м·Кr=7700 кг/м3
Сталь Х17 (ГОСТ 5632-61) [6, стр.281, 282]
l=25,1 Вт/м·Кr=7750 кг/м3
Равновесные данные:
Смесь: Ацетон - Бензол.
x
|
y
|
t
|
0
|
0
|
86,1
|
1
|
3,52
|
79,2
|
5
|
14,96
|
76,35
|
10
|
25,31
|
73,6
|
20
|
46,3
|
69,7
|
30
|
51,47
|
66,75
|
40
|
60,3
|
64,5
|
50
|
67,85
|
62,65
|
60
|
74,64
|
61
|
70
|
81
|
59,6
|
80
|
87,37
|
58,35
|
90
|
93,71
|
57,25
|
95
|
96,87
|
56,7
|
99
|
99,37
|
56,27
|
100
|
100
|
56,18
|
1) По равновесным данным необходимо построить диаграммы T(x,y) и (x,y) для смеси ацетон-бензол.
А є Ацетон Ма = 46 кг/кмоль
Б є БензолМб = 78 кг/кмоль
2) Пересчитываем известные концентрации а0, а1 и а2 в x0, x1 и x2:



3) Расчет минимального флегмового числа:
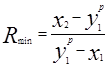
определяем по диаграмме (x,y) по x1:
» 44
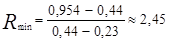
4) Расчет рабочего флегмового числа:
R=sЧRmin=1,2*2,45=2,94
5) Расчет отрезка "b" для построения рабочей линии укрепляющей части колонны:

6) Построение рабочей линии на диаграмме (x,y) и определение числа теоретических тарелок:
nут=5nот=11
Для расчета числа реальных тарелок необходимо найти их КПД.
7) Расчет КПД тарелок:
Расчет ведется для питающей тарелки
х1=0,23 моль/моль
Поскольку смесь подается при температуре кипения, t1 определяется по диаграмме Т(х, у) по х1.
t1»68,8°C
При этой температуре определяется давление насыщенных паров компонентов:
Рa»1100 мм Hg
Рб»31 мм Hg
Необходимо рассчитать коэффициент относительной летучести:
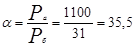
Вязкость жидкой смеси:
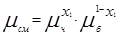
mА и mВ определяются при t1 = 68,8°С:
ma » 0,22 сп
mб » 0,36 сп
aЧmсм=35,5*0,315=11,18
Средний КПД тарелок по диаграмме:
h » 0,25
8) Расчет числа реальных тарелок:
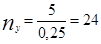 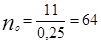
Nобщ=20+44=64
Расчет потоков дистиллята и кубового остатка
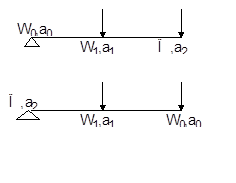
По правилу рычага второго рода:
П(а2-а0) =W1(a1-a0)


Проверка:
П+W0=W1
0,30+1,9=2,2 кг/с
Расчет габаритов колонны
Расчет габаритов верха колонны:
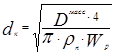
=П(R+1)
Рекомендуемая скорость пара равна:
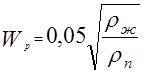
а) Расчет плотности жидкости:
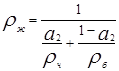
ra и rб определяются при температуре дистиллята tд=t2»68,8 (по диаграмме Т(х, у)):
ra » 719 кг/м3
rб » 805 кг/м3
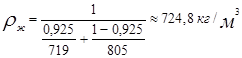
б) Расчет плотности пара:
pu=RT2



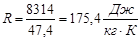
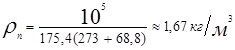
в) Расчет рекомендуемой скорости пара:
»1,04м/с

Расчет габаритов низа колонны.
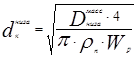
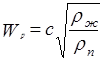
Рекомендуемая скорость пара рассчитывается при температуре t0»77°C (диаграмма T(x,y))
а) Расчет плотности жидкости:
ra»724кг/м3
rб»818кг/м3
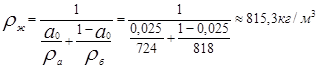
б) Расчет плотности пара:



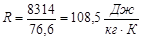

Рекомендуемая скорость пара:
м/с
в) Расчет :

Расчет rкуб производится по принципу аддитивности:
rкуб=raЧa0+ rбЧ(1-a0)
при t0=77°С
rкуб=500*0,025+396Ч(1-0,025) »398,6кДж/кг
Расчет Qкип.
Qкип=W0Чc0Чt0-W1Чc1Чt1+П(RЧrд+iп)
По диаграмме Т(x,y) определяем:
- по х1t1=63,8°C - по х2t2=56,7°C - по х0t0=77°C
Вычисляем теплоемкости смеси при разных температурах:
с0=сaЧa0+сб(1-a0) =0,58*4, 19*0,025+4, 19*0,45*(1-0,025) =1,47кДж/кгК
с1=сaЧa1+сб(1-a1) =0,555·4, 19*0,15+0,444*4, 19*0,85=1,93 кДж/кгЧК
с2=сaЧa2+сб(1-a2) =
0,546·4, 19*0,925+0,43*4, 19*0,075=2,25 кДж/кгЧК
Значения сa и сб взяты из номограммы
При температуре t2=56,7°C удельная теплота парообразования дистиллята:
при t2 = 56,7 °С
rД=raa2+rб(1-a2) =522,4·0,925+410,7·(1-0,925) =595,5 кДж/кг
Энтальпия пара:
iп =c2·t2+rд=2,25·56,7+595,5»654,5 кДж/кг
Qкип=1,9·1,47·77-2,22·1,93·63,8+0,3(2,45·595,5+654,5) =575,7 кВт
Теперь можно рассчитать диаметр колонны:
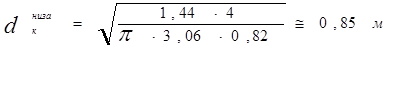
Расчет высоты.
H = h(Nобщ-1) +Zв+Zн = 0,5(64-1) +2+1 = 34,5 м
Габариты колонны.
Н = 34,5 м

d=1000мм
Расчет гидравлического сопротивления тарелочной части колонны.
Общее гидравлическое сопротивление тарелки:
ΔР=ΔРс+ΔРσ+ΔРж, Па.
― Расчет потери напора пара на преодоление местных сопротивлений на сухой (неорошаемой) тарелке
ΔРс=ξ , Па.
Коэффициент сопротивления для клапанной тарелки ξ= 3,6 по [5, стр.25]
Скорость пара в отверстии тарелки: м/с
ΔРс=3,6* Па.
― Расчет сопротивления, вызываемого силами поверхностного натяжения.
ΔРσ= , Па.
dэ=d0=40 мм - эквивалентный диаметр отверстия тарелки.
При ºC
σА=15,9*10-3 Н/м [1, стр.501, табл. XXII]
σб=22,1*10-3 Н/м
σср= Н/м
ΔРσ= Па.
― Расчет статистического сопротивления слоя жидкости на тарелке.
ΔРж=КА*hж*ρж*g, Па
Относительная плотность парожидкостной смеси КА=0,5-0,7
Средняя плотность жидкости
ρж= кг/м3
высота слоя жидкости на тарелке
hж = hw +how
высота перегородки hw=0,03-0,05м
Подпора жидкости на сливной перегородке:
how =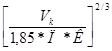
Периметр слива П' =1,12 м

Объемный расход жидкости
R=2,94
K/моль см
м3/с
how = м
hж=0,04+0,02=0,06 м
ΔРж=0,5*0,06*770*9,81=226,6 Па
И так ΔР=514+1,9+226,6=642,5 Па
Проверим, соблюдается ли при расстоянии между тарелками 0,5 м необходимые для нормальной работы тарелок условие:
h >1,8*
0,4 >1,8* 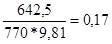
0,4 > 0,17 => условия выполняются
Полное сопротивление тарельчатой колонны определяется числом тарелок
nΣ =64 в колонне.
ΔРполное =ΔР* nΣ =642,5*64=31120 Па.
Расчет диаметров штуцеров.
1) Штуцер для ввода исходной смеси.
d= , или
исходные данные: =2,22 кг/с
=0,23 
t1= 63,8 ºC
ρA=640,1 кг/ м3
ρВ=829,2 кг/ м3
ω1=0,9м/с
ρ1=Х1*ρА+(1-Х1) *ρВ=0,23*640,1+(1-0,23) *829,2=785,7 кг/ м3
d= =0,06м =60мм
Принимаю
Dу=50мм,dн=55мм, S=3,5мм, Н=120мм
2) Штуцер для вывода пара из колонны.
d = , мм
Исходные данные: =1,3 кг/с
=10-20 м/с
=1,67 кг/м3
d= =0,35м =350 мм
Принимаю
Dу=350 мм, dн=358 мм, S=4 мм, Н=235 мм
3) Штуцер для ввода флегмы.
d= , мм
Исходные данные: =0,882 кг/с
=724,8 кг/м3
=0,5-1,0 м/с
d= =0,045 м =45 мм
Принимаю
Dу=50 мм, dн=55 мм, S=3,5 мм, Н=120 мм
4) Штуцер для вывода кубового остатка.
d= , мм
Исходные данные: =1,7 кг/с
=0,5-1,0 м/с [7, стр.41]
=815,3кг/м3
d= =0,06 м =60 мм
Принимаю
Dу=50 мм, dн=55 мм, S=3,5 мм, Н=120 мм
5) Штуцер для ввода парожидкостной смеси.
d= , или
f=0,25*fтр
fтр= 0,176 м2
d= =0,237 м =237 мм
Принимаю
Dу=250 мм, dн=260 мм, S=5 мм, Н=175 мм
6) Штуцер для вывода жидкости.
d= , мм
Исходные данные: =1,9 кг/с
=0,5-1,0 м/с
=815,3кг/м3
d= =0,06 м =60 мм
Принимаю
Dу=50 мм, dн=55 мм, S=3,5 мм, Н=120 мм
Тепловой баланс ректификационной установки
1) Расход тепла в кипятильнике:
(рассчитан выше)
2) Расход греющего пара в кипятильнике:

По (3, стр.525, табл. LVII) через давление греющего пара P =0,4 MПа=4 ат находим удельную энтальпию пара:
=4ат rкон=2744 
кг/с
3) Расход тепла дефлегматора:
Qg=Dм* rдис
Qg = 1,3*595,5=774 кВт
4) Расход охлаждающей воды в дефлегматоре при нагреве её на 20ºC:

В интервале температур 9-20 ºC вода имеет теплоемкость Cв = 4, 19
кг/с
5) Расход тепла в подогревателе:
Qn= ω1 * C1 * t1=2,22*1,93*63,8=273,4 
6) Расход греющего пара в подогревателе:
кг/с
7) Общий расход греющего пара:
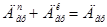
0, 20+0,09=0,29 кг/с
8) Расход тепла холодильника:
- дистиллята:
= П * t2 * C2 =0,3 *56,7 * 2,25=38,3 кВт
- кубового остатка:
= ω0 * t0 * C0 =1,9* 77 * 1,47=215 кВт
9) Расход охлаждающей воды при нагреве её на 20 ºC в холодильнике:
- дистиллата:
кг/с
- кубового остатка:
кг/с
10) Общий расход охлаждающей воды:
кг/с
Расчет кубового кипятильника
1) Расход тепла в кипятильнике:
Qкип = 575,7 кВт
2) Расход гр. Пара в кипятильнике:

3) Подготовка к расчету коэффициента теплопередачи:
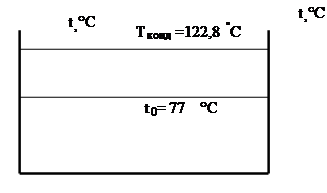 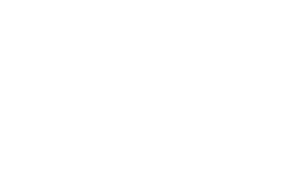
В трубах смесь, в межтрубном пространстве - теплоноситель (конденсированный пар)
Движущая сила процесса:
Dt = T-t = 45,8°С
Коэффициент теплопередачи от конденсирующегося пара к жидкости:
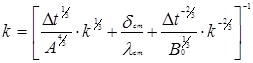
А) Для водяного пара:
, где x - высота труб
с = 0,943 - для вертикальных теплообменников
А0 = 12,92·103 [7, c.149]
kор = 600 Вт/м2·К.
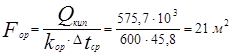
Выбираем теплообменник по каталогу:
Одноходовой теплообменник типа ТН и ТЛ:
F = 21 м2
l = 1500 мм-длина трубы
dнґs = 38ґ2 [мм]
nтруб=121
fтр =0,11 м2-трубное пространство
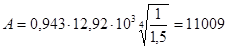
Б) Характеристика стенки:
Выбор материала из которого изготавливать трубки:
Стальl=46,5 [3, c.529, табл. XXVIII]
По каталогу [4, с.414] выбираем толщину стенки:
d=2мм
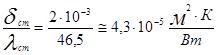
В) Для кипящего бензола:
В0 = 40·р0,3·j3 [7]
(коэффициент, включающий различные теплофизические константы)
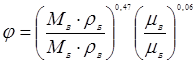
Бензол: Вода:
r = 815 кг/м3r = 972 кг/м3 [3, c.512, табл. IV]
m = 0,316·10-3 Па·сm = 0,357 10-3 Па·с [3, c.516, табл. IX]
М = 78 г/мольМ = 18 г/моль [3, c.541, табл. XLIV]
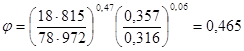
p = рверха + Dрполн = 1,3 бар
В0 = 40·1,30,3·0,4653 = 4,8
4) Расчет коэффициента теплопередачи:
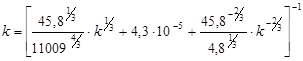
kрасч = 1902 Вт/м2·К.
5) Расчет поверхности теплообмена:
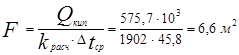
Одноходовой теплообменник типа ТН и ТЛ:
F = 7 м2
H = 1500 мм-высота трубы
dнґs = 25ґ2 [мм]
nтруб=61
fтр =0,021м2-трубное пространство
Dнар = 325 мм
Расчёт дефлегматора
1) Расход тепла:
Qд=774 кВт
2) Расход охлаждающей воды:
Gвдеф=9,23 кг/с
3) Расчет движущей силы теплообменного процесса:
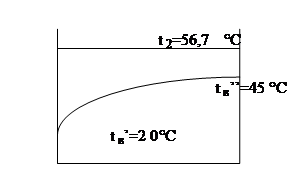 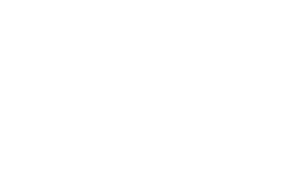
°C
4) Расчет термического сопротивления:
Материал трубок:
Стальl=46,5 [3, c.529, табл. XXVIII]
толщина стенки:
d=2мм(dґS: 25ґ2)
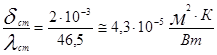
5) Предварительный выбор теплообменного устройства:
Задаемся ориентировочным коэффициентом теплопередачи кор = 500 Вт/(м2·К) (при вынужденном движении, при передаче тепла от конденсирующегося пара к воде, границы задания ориентировочных значений к=300ё800)
[3, c.172, табл.4.8]
Ориентировочная поверхность теплообмена:
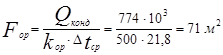
Для одноходового теплообменника ближайшей является F=71м2.
l = 5000 мм-длина трубы
dнґs = 38ґ2 [мм]
nтруб=121
fтр =0,11 м2-трубное пространство
Расчет скорости воды:
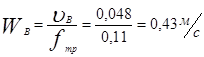
Оценка режима течения:

nводы = 0,66 м2/с
- это развитый турб. режим (Re > 104)
6) Расчет a2:
Расчет значения критерия Нуссельта по формуле:
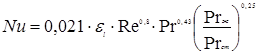
el=1(т. к. l/d > 50)

По номограмме [3, c.564, рис. ХIII] определяется значение критерия Прандтля: Pr = 3,4


7) Расчет интенсивности теплообмена:

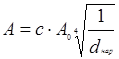
c=0,72 - для горизонтальных труб
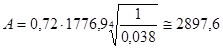
8) Расчет коэффициента теплопередачи:
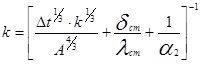
kop=500 Вт/(м2·К)
k=397,9 Вт/(м2·К)
9) Выбор теплообменника по каталогу [4, c.417]:
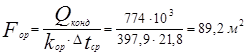
Одноходовой теплообменный аппарат типа ТН или ТЛ:
F = 97 м2
fтр = 0,176 м2
nтруб=511
Подогреватель исходной смеси
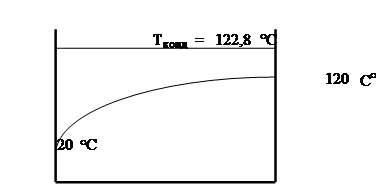 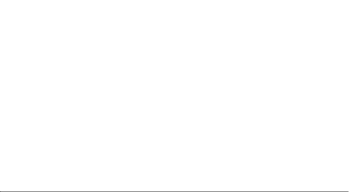

где 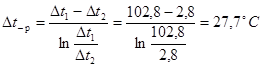
По каталогу [4, c.416] выбираем одноходовой теплообменник со следующими характеристиками:
F = 28 м2
l = 2000 мм-высота трубы
dнґs = 38ґ2 [мм]
fтр =0,11 м2-трубное пространство
Dнар = 600 мм
Водяной холодильник дистиллята
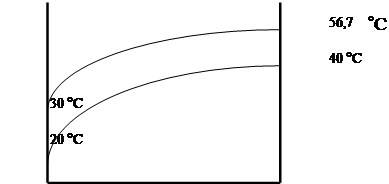 

где 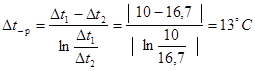
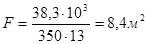
F = 9 м2
l = 1000 мм-высота трубы
dнґs = 25ґ2 [мм]
fтр =0,0042 м2-трубное пространство
Dнар = 400 мм
Водяной холодильник кубового остатка.
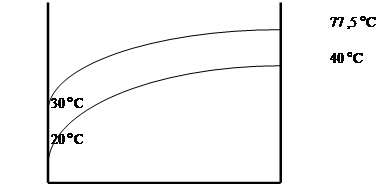 

где 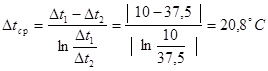
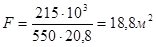
По каталогу [4, c.413] выбираем одноходовой теплообменник со следующими характеристиками:
F = 19 м2
l = 4000 мм-высота трубы
dнґs = 25ґ2 [мм]
fтр =0,0021 м2-трубное пространство
Dнар = 325 мм
Подбор и расчет конденсатоотводчиков.
При давлении на входе не менее 0,1 МПа и противодавлении не более 50% давления на входе устойчиво работают термодинамические конденсатоотводчики. Они применяются для отвода переохлажденного конденсата.
Расчетное количество конденсата после теплопотребляющего аппарата:
кг/с =0,86 т/ч
кг/с =0,36 т/ч
Давление греющего пара перед конденсатоотводчиком:
P1=0,95*Pгр=0,95*4=3,8 ат
Давление после конденсатоотводчика при свободном сливе конденсата:
Р2=0,1 ат.
Условная пропускная способость:
КVу= , где
ΔР = Р2 - Р1 - перепад давления на конденсатоотводчике, ат.
А - коэффициент, учитывающий температуру конденсата и перепад давлений на конденсатоотводчике (определяется по графику).
т/с
мм
Подбираем конденсатоотводчик для кипятильника:
Dу=50 мм; L=200 мм; L1=24 мм; Hмакс=103 мм; H1=60 мм; D0=115 мм
т/с
мм
Подбираем конденсатоотводчик для подогревателя:
Dу=20 мм; L=100 мм; L1=16 мм; Hмакс=63 мм; H1=22,5 мм; D0=67 мм
В данном проекте используют термодинамические конденсатоотводчики 45Ч12ИЖ для автоматического отвода из пароприемника конденсата водяного пара рабочей температуры до 200 ºC.
Расчет и выбор вспомогательного оборудования
Расчет емкостей.
Для приема исходной смеси (Е1), кубового остатка (Е2) и дистиллата (Е3) должны быть предусмотрены резервуары. Размеры последних рассчитываются, исходя из условий обеспечения непрерывности работы установки в течение 6 часов (τ) и заполнении их на 0,8 емкости (К3).
Расчет резервуара для хранения исходной смеси.
Исходные данные: a1=0,15 масс дол.
W1 =2,22 кг/с;
τ=6ч =21600 с; ρА=791,0 кг/м3
К3=0,8; ρВ=879,0кг/м3 при 20 ºC
кг/м3
м3
Подбираю емкость ГЭЭ1-1-100-0,6.
Dвн=3200 мм L(H) =16700 мм
Расчет резервуара для хранения дистиллата.
Исходные данные: d2=0,925 масс дол.
П =0,55 кг/с;
τ=21600 с; ρА=791,0 кг/м3
К3=0,8; ρВ=879,0кг/м3 при 20 ºC
кг/м3
м3
Подбираю емкость ГЭЭ1-2-125-0,6.
Dвн=2400 мм L(H) =4500 мм
Расчет резервуара для хранения кубового остатка.
Исходные данные: a0=0,025 масс дол.
W0 =1,9 кг/с;
τ=21600 с; ρА=791,0 кг/м3
К3=0,8; ρВ=879,0кг/м3 при 20 ºC
кг/м3
м3
Подбираю емкость ГЭЭ1-1-100-0,6.
Dвн=3200 мм L(H) =16700 мм
Расчет толщины тепловой изоляции ректификационной установки.
Расчет толщины тепловой изоляции проводится по формуле:
, где
αВ =9,3+0,058* - коэффициент теплоотдачи от внешней поверхности изоляционного материала в окружающую среду, Вт/м2 *К.
- температура изоляции со стороны окружающей среды.
=20 0С
- температура изоляции со стороны колонны. Ввиду незначительного термического сопротивления стенки аппарата по сравнению с термическим сопротивлением слоя изоляции:
≈ При Ргр =4ат. → =142,9 0С
- температура окружающей среды (воздуха). Температура воздуха в г. Ярославле зимой - 20 0С.
λu - коэффициент теплопроводности изоляционного материала в качестве материала для тепловой изоляции выбираю совелит (85% магнезии и 15% асбеста). По (1, стр.504, табл. XXVIII) для совелита λu =0,09
αВ =9,3+0,058 * 40 =11,6
м
Принимаю толщину тепловой изоляции 0,23м и для других аппаратов.
Список использованной литературы
1) Коган В.Б., Фридман В.М., Кафаров В.В. Равновесие между жидкостью и паром, М.: Наука, 1966.
2) Захаров М.К., Солопенков К.Н., Варфоломеев Б.Г. Методические указания к курсовому проектированию ректификационных установок непрерывного действия, М.: Полинор-М, 1995.
3) Павлов К.Ф., Романков П.Г., Носков А.А. Примеры и задачи по курсу процессов и аппаратов химической технологии, Л.: Химия, 1987.
4) Лащинский А.А., Толчинский А.Р. Основы конструирования и расчета химической аппаратуры: Приложение к справочнику, М.: Машиностроение, 1970.
5) Колонные аппараты: Каталог, М.: Цинтихимнефтемаш, 1978.
6) Лащинский А.А., Толчинский А.Р. Основы конструирования и расчета химической аппаратуры: Справочник, М.: Машиностроение, 1970.
Мясоединков В.М. / Под ред. Б.Г. Варфоломеева Подбор и расчет конденсатоотводчиков, М.: МИТХТ, 1989.
Борисов Г.С., Брыков В.П., Дытнерский Ю.И. и др. Основные процессы и аппараты химической технологии: Пособие по проектированию, М.: Химия, 1991.
Сварное емкостное оборудование. Каталог ЦИНТИХИМНЕФТЕМАН, "Москва", 1987 г.
|