СОДЕРЖАНИЕ
Введение
1. Теоретические сведения
1.1 Обратные термодинамические циклы
1.2 Циклы тепловых двигателей и установок
1.3 Коэффициент избытка воздуха, степень сжатия
2. Рабочие процессы в поршневых и комбинированных двигателях
2.1 Классификация двигателей внутреннего сгорания
2.2 Топливо для двигателей. Свойства и физико-химические характеристики. Теплота сгорания топлива
2.3 Двухтактные двигатели
3. Параметры, характеризующие поршневые двигатели
3.1Среднее индикаторное давление и индикаторная мощность
3.2 Коэффициенты полезного действия
3.3 Повышение удельной мощности двигателей
4. Дизельные двигатели
4.1 Особенности и применение
4.2 Смесеобразование в дизелях и типы камер сгорания0
4.3 Топливные системы
4.4 Подвод воздуха и отвод выпускных газов
4.5 Устройство двухтактных и четырехтактных двигателей
5. Расчет горения топлива
5.1 Состав топлива и его характеристики
5.2 Процессы горения топлива
6. Устройство двигателя автомобиля марки ВАЗ-2101
6.1 Основные механизмы и системы двигателя
6.2 Силы и моменты, действующие в двигателе
6.3 Кривошипно-шатунный механизм
6.4 Механизм газораспределения
6.5 Системы смазки и охлаждения
Заключение
Список литературы
ВВЕДЕНИЕ
Двигатель внутреннего сгорания (сокращённо ДВС) — это тип двигателя, тепловая машина, в которой химическая энергия топлива (обычно применяется жидкое или газообразное углеводородное топливо), сгорающего в рабочей зоне, преобразуется в механическую работу. На данный момент является одним из самых распространенных типов двигателей. В этой работе будет показаны основы строения ДВС, принцип работы на примере ВАЗ-2101.
Актуальность данной темы заключается в том, что двигатели внутреннего сгорания играют важную роль в жизни человечества.
Применение двигателей внутреннего сгорания чрезвычайно разнообразно: их используют в авиации, теплоходы, автомобили, тракторы и тепловозы также используют ДВС. Более мощные двигатели внутреннего сгорания устанавливают на речных и морских судах. Несмотря на то, что двигатели внутреннего сгорания являются весьма несовершенным типом тепловых машин (низкий КПД, громкий шум, токсичные выбросы, меньший ресурс) благодаря своей автономности (необходимое топливо содержит гораздо больше энергии, чем лучшие электрические аккумуляторы) двигатели внутреннего сгорания очень широко распространены, например на транспорте.
1. ТЕОРЕТИЧЕСКИЕ СВЕДЕНИЯ
1.1 Обратные термодинамические циклы
Обратный термодинамический цикл – это совокупность процессов, в результате которых рабочее тело (пар, газ) возвращается в первоначальное состояние, и при этом за счет затраты работы осуществляется передача теплоты от тел менее нагретых к более нагретым.
Теплота сама по себе не способна переходить от тел, имеющих низкую температуру, к телам более нагретым, что является отражением второго закона термодинамики. Однако при затратах энергии с помощью различного рода холодильников, кондиционеров и тепловых насосов теплота может отниматься от холодных тел и передаваться телам с более высокой температурой. Таким образом, помимо прямых циклов, которые реализуются в целях превращения тепловой энергии в механической энергии в механическую, существует целый класс круговых процессов, назначением которых может являться, в частности перенос теплоты от тел менее нагретых к телам с более высокой температурой. Формально эти циклы отличаются направлением протекания термодинамических процессов – они осуществляются против хода часовой стрелки, а не по ходу, как прямые циклы. Иными словами, по подобным циклам работают различные потребители
энергии.
Обратный термодинамический цикл можно рассмотреть на примере воздушной холодильной установки.
В качестве рабочего тела в холодильной установке может использоваться воздух. В этом случае подвод и отвод теплоты осуществляется – в отличии от цикла Карно – не в изотермных процессах, а в процессах изобарных.
 |
Рис. 1. Схема «воздушной» холодильной установки
Где 1 – холодильная камера, 2 – компрессор, 3 – теплообменник, 4 – расширительный цилиндр
|
|
Нагретый в результате теплообмена с охлаждаемыми предметами воздух поступает из холодильной камеры 1 (рис. 1) в компрессор 2. Вследствие последующего быстрого сжатия температура воздуха поднимается выше температуры окружающей среды и вытесняемый в теплообменник 3 воздух при постоянном давлении отдает теплоту этой среде или охлаждающей жидкости. При этом температура воздуха понижается, оставаясь, однако в процессе теплообмена всегда выше температуры среды или жидкости. Пройдя через трубки теплообменника, воздух через клапаны попадает в расширительный цилиндр 4 (детендер). Здесь он расширяется, совершая «положительную» работу. Поскольку процесс расширения протекает относительно быстро, температура рабочего тела понижается и охлажденный подобным образом воздух в конце расширения через клапана попадает в холодильную камеру 1. Здесь при постоянном давлении он отбирает теплоту у охлаждаемых предметов, после чего вновь поступает в компрессор.
Холодильный коэффициент цикла воздушной холодильной установки определяется как:

Где T1
– исходная температура рабочего тела, T2
, T3
, T4
– температуры компрессора, теплообменника и расширительного цилиндра.
Таким образом, холодильный коэффициент воздушной установки ξk
определяется по той же формуле, как и для обратного цикла Карно. Однако эффективность этих двух циклов оказывается различной. Различие в эффективности цикла воздушной холодильной установки и обратного цикла Карно весьма существенно, и отношение ξ/ξk
, в реальном диапазоне температур, как правило, не превосходит 0,3.
Помимо невысокой эффективности существенным недостатком воздушных холодильных установок являются и их большие габариты. Это предопредило поиск решений, позволяющих при увеличении эффективности уменьшить ее размеры. Достичь этого возможно в приближении к обратному циклу Карно, то есть в случае подвода и отвода теплоты в цикле по изотермам.
1.2 Циклы тепловых двигателей и установок
Круговой цикл (процесс) – это такой процесс, при котором газ (т.е. рабочее тело) после ряда изменений возвращается в исходное состояние.
Круговые процессы осуществляются в тепловых двигателях как процессы, периодически повторяющиеся. В системе p-v координат круговые процессы всегда замкнуты.
Рассмотрим изменение состояния газа в непрерывно работающем тепловом двигателе. Допустим, что газ с начальными параметрами, характеризующимися точкой 1 (рис. 2), вводится в соприкосновение с источником тепла, в результате чего газ расширяется до конечного состояния, характеризуемого точкой 2.
В процессе расширения газ совершает работу, измеряемую площадью 1-1′-2-3-4-1. Если газ сжимать при той же температуре, при которой он расширялся, то работа, затрачиваемая на сжатие, будет равна работе, получаемой при расширении, и в результате такого процесса работа будет равна нулю.


Следовательно, процесс сжатия необходимо вести при меньшей температуре, чем процесс расширения, т.е. при сжатии газ следует охлаждать.
Работа, затраченная на сжатие, изображается площадью 2-2′-1-4-3-2. в результате кругового процесса получается полезная работа, равная разности работ расширения и сжатия, которая изображается площадью 1-1′-1-4-3-2, ограниченной замкнутой кривой обоих процессов.
Для осуществления кругового процесса (цикла) и получения полезной работы необходимо к газу в процессе расширения подвести тепло , а в процессе сжатия отвести от него тепло .
Так как в круговом процессе конечное и начальное состояния газа совпадают, то изменение внутренней энергии газа за цикл равно нулю, т.е. .
На совершение полезной работы в круговом процессе затрачивается количество тепла q=q1
-q2
, где q1
и q2
- количество подведенного и отведенного тепла соответственно.
Процесс на рисунке 2 называют прямым, и он направлен по часовой стрелке. Прямые циклы имеют место в тепловых двигателях.
Экономичность цикла оценивается термическим коэффициентом полезного действия (к.п.д.), обозначаемым и равным отношению тепла, превращенного в полезную работу, к подведенному теплу, т.е.
.
где q1
и q2
- количество подведенного и отведенного тепла соответственно. Данное уравнение показывает, что к.п.д. не может быть больше или равен единице, т.к. ни q2
ни q1
не могут быть равны нулю.
1.3 Коэффициент избытка воздуха, степень сжатия
В зависимости от организации рабочего процесса двигателя соотношение между количествами воздуха и топлива может изменяться. При теоретических расчетах получают необходимое для горения количество воздуха, но на практике подводят большее количество. Отношение действительного количества воздуха ( ), подводимого в процессе горения, к теоретически необходимому ( ), называется коэффициентом избытка воздуха
.
Он характеризует качество горючей смеси. При увеличении α смесь делается более бедной. Полным сгоранием топлива называется такое сгорание, при котором все горючие части топлива превращаются в конечные продукты окисления.
Число, показывающее, во сколько раз полный объем цилиндра больше объема камеры сгорания называют степенью сжатия. Степень сжатия можно найти через отношение полного объема цилиндра к объему камеры сгорания и обозначают :
,
где - полный объем цилиндра, - объем камеры сгорания, - рабочий объем.
2. РАБОЧИЕ ПРОЦЕССЫ В ПОРШНЕВЫХ И КОМБИНИРОВАННЫХ ДВИГАТЕЛЯХ
2.1 Классификация двигателей внутреннего сгорания
Двигателем внутреннего сгорания называют поршневой тепловой двигатель, в котором процессы сгорания топлива, выделение теплоты и превращение ее в механическую работу происходят непосредственно в цилиндре двигателя.
ДВС можно разделить на:
· газовые турбины;
· поршневые двигатели;
· реактивные двигатели.
В газовых турбинах сжигание топлива производится в специальной камере сгорания. Газовые турбины, имеющие только вращающиеся детали, могут работать с высоким числом оборотом. Основным недостатком газовых турбин являются невысокая экономичность и работа лопаток в среде газа с высокой температурой.
В поршневом двигателе топливо и воздух, необходимые для сгорания, вводятся в объем цилиндра двигателя. Образующиеся при сгорании газы имеют высокую температуру и создают давление на поршень, перемещая его в цилиндре. Поступательное движение поршня через шатун передается коленчатому валу, установленному в картере, и преобразуется во вращательное движение вала.
В реактивных двигателях мощность увеличивается с повышением скорости движения. Поэтому они распространены в авиации. Недостаток таких двигателей в высокой стоимости.
Наиболее экономичными являются ДВС поршневого типа. Но наличие кривошипно-шатунного механизма, который усложняет конструкцию и ограничивает возможность повышения числа оборотов, является их недостатком.
Двигатели внутреннего сгорания классифицируются по следующим основным признакам:
1. по способу смесеобразования:
а) двигатели с внешним смесеобразованием, когда горючая смесь образуется вне цилиндра. Примером таких двигателей служат газовые и карбюраторные.
б) двигатели с внутренним смесеобразованием, когда горючая смесь образуется непосредственно внутри цилиндра. Например, двигатели на дизеле и двигатели с впрыском легкого топлива в цилиндр.
2. по виду применяемого топлива:
а) двигатели, работающие на легком жидком топливе (бензине, лигроине и керосине);
б) двигатели, работающие на тяжелом жидком топливе (соляровом масле и дизельном топливе);
в) двигатели, работающие на газовом топливе (сжатом и сжиженном газах).
3. по способу воспламенения горючей смеси:
а) двигатели с воспламенением горючей смеси от электрической искры (карбюраторные, газовые и с впрыском легкого топлива);
б) двигатели с воспламенением топлива от сжатия (дизели).
4. по способу осуществления рабочего цикла:
а) четырехтактные. У этих двигателей рабочий цикл совершается за 4 хода поршня или за 2 оборота коленчатого вала;
б) двухтактные. У этих двигателей рабочий цикл в каждом цилиндре совершается за два хода поршня или за один оборот коленчатого вала.
5. по числу и расположению цилиндров:
а) двигатели одно- и многоцилиндровые (двух-, четырех-, шести-, восьмицилиндровые и т.д.)
б) двигатели однорядные (вертикальные и горизонтальные);
в) двигатели двухрядные (V-образные и с противолежащими цилиндрами).
6. по способу охлаждения:
а) двигатели с жидкостным охлаждением;
б) двигатели с воздушным охлаждением.
7. по назначению:
а) двигатели транспортные, устанавливаемые на автомобилях, тракторах, строительных машинах и других транспортных машинах;
б) двигатели стационарные;
в) двигатели специального назначения.
2.2 Топливо для двигателей. Свойства и физико-химические характеристики. Теплота сгорания топлива
Действительный рабочий цикл ДВС осуществляется в результате выделения теплоты при химических реакциях сгорания топлива непосредственно в цилиндре двигателя.
В качестве топлива для двигателей используют жидкие нефтепродукты (бензин, дизтоплива, тяжелое дизельное топливо) и горючие газы, основную часть которых составляют углеводороды.
Топливо и воздух на горение в зависимости от физических свойств топлива вводится в цилиндр двигателя совместно или раздельно.
При проектировании нового двигателя обязательно указывается вид топлива. Для характеристики конструктивных особенностей двигатели часто называют по роду используемого топлива (газообразные, бензиновые).
В зависимости от физического состояния и метода получения газообразного топлива различают сжиженный газ (смеси углеводородов, которые при 20 С и давлении 760 мм рт.ст. газообразны, а при понижении температуры или повышении давления превращаются в жидкость), сжатый газ, генераторный газ и т.п. Выбор газа в качестве топлива для ДВС определяется его способностью к воспламенению и скоростью распространения пламени в газо-воздешной смеси.
Жидкое топливо получается в основном в результате переработки нефти. Нефтяное жидкое топливо состоит в основном из углерода 85-87%, водорода 12-15%, кислорода 0-0,5%. Жидкие топлива делят на топлива для карбюраторных двигателей и для двигателей с воспламенением от сжатия (дизеля).
Бензин
— основной вид топлива для карбюраторных двигателей. Сырьем для получения бензина служит нефть, нефтяные газы, бурый и каменный уголь, горючие сланцы.
Октановое число́ — показатель, характеризующий детонационную стойкость топлива (способность топлива противостоять самовоспламенению при сжатии) для двигателей внутреннего сгорания. Число равно содержанию (в процентах по объёму) изооктана(2,2,4-триметилпентана) в его смеси с н
-гептаном, при котором эта смесь эквивалентна по детонационной стойкости исследуемому топливу в стандартных условиях испытаний.
Бензин как топливо должен обладать хорошей испаряемостью, стойкостью против детонации, высокой стабильностью (т. е. способностью сохранять первоначальные свойства при длительном хранении), не содержать соединений, вызывающих коррозию металла, и не содержать смолистых отложений, а также воды и механических примесей.
Об испаряемости бензина судят по его фракционному составу.
Фракционный состав характеризуется температурой выкипания 10%; 50%; 90 % топлива и температурой конца выкипания.
Температура выкипания 10% топлива характеризует его пусковые качества: чем ниже эта температура, тем легче можно пустить двигатель.
Температура выкипания 50% топлива характеризует способность его обеспечивать быстрый прогрев двигателя, устойчивость его работы на малой частоте вращения коленчатого вала и приемистость двигателя.
Температура выкипания 90 % топлива и конца выкипания характеризует полноту его испарения.
Температура начала кипения бензина должна быть не ниже 30 °С, для того, чтобы в жаркое время года не образовывались "паровые" пробки в топливопроводах и фильтрах.
Стойкость бензина против детонации оценивается октановым числом, которое присутствует в каждой марке бензина. Так, например, в марке бензина АИ-92 буква А означает, что бензин предназначен для автомобилей, буква И — что октановое число данного бензина определяют по исследовательскому методу, а цифра 92 — октановое число. В марке А-76, где нет буквы И — октановое число 76 определено по моторному методу.
На слух детонация проявляется в звонких металлических стуках при работе двигателя. Кроме того, при детонации в отработавших газах периодически появляется черный дым, двигатель перегревается и его мощность падает.
Чем выше октановое число, тем меньше склонность бензина к детонации, поэтому для повышения октанового числа к бензинам добавляют антидетонатор — этиловую жидкость. Бензин, в который добавлена этиловая жидкость, называют этилированным. Этиловая жидкость ядовита, поэтому этилированные бензины тоже ядовиты и применение их требует строгого соблюдения правил техники безопасности. Присутствие в бензине кислот и сернистых соединений вызывает коррозию металлов, поэтому содержание их строго ограничивается.
Вода и механические примеси в бензине не допускаются. Вода способствует коррозии топливных баков и тары, а также ускоряет осмоление бензина.
В соответствии с рекомендациями заводов-изготовителей автомобилей применяют марки бензинов:
Дизельные топлива.
Это топливо применяется для дизелей.
Основными свойствами дизельного топлива являются температура самовоспламенения, температура застывания и вязкость.
Цетановое число — характеристика воспламеняемости дизельных топлив, определяющая период задержки воспламенения смеси (промежуток времени от впрыска топлива в цилиндр до начала его горения). Чем выше цетановое число, тем меньше задержка и тем более спокойно и плавно горит топливная смесь.
Температурой самовоспламенения называется температура, до которой необходимо нагреть смесь дизельного топлива с воздухом, чтобы начался процесс ее горения. Эта температура равна примерно 300—350 °С. Самовоспламеняемость дизельного топлива определяют по цетановому числу. Чтобы определить цетановое число, дизельное топливо сравнивают с эталонными топливами, цетановое число которых заранее известно. Цетановое число находится в пределах 40—45 единиц.
Температура застывания дизельного топлива оказывает влияние на работу дизеля: чем она ниже, тем надежнее работает дизель, так как при застывании топливо превращается в желеобразную массу и подача его из топливных баков в цилиндры двигателя становится невозможной. Температура застывания дизельного топлива должна быть на 10—15°С ниже температуры окружающего воздуха в районе его эксплуатации.
Выпускают следующие марки дизельного топлива: Л — летнее, 3 — зимнее, А — арктическое.
Газовое топливо
, используемое в газобаллонных автомобилях, может быть как естественного, так и искусственного происхождения и применяться в сжатом или сжиженном виде. К сжатым газам относят природный газ (метан) и промышленные газы. Сжиженными называют такие газы, которые переходят из газообразного в жидкое состояние при нормальной температуре и давлении до 1,6 МПа. К ним относят углеводороды, получаемые при переработке нефти.
Газ как топливо имеет ряд преимуществ: обеспечивает лучшее смесеобразование, позволяет использовать бедные горючие смеси. К недостаткам газового топлива относят меньшую теплоту сгорания горючей смеси. В результате этого мощность двигателя уменьшается на 7...20%.
К физико-химическим характеристикам топлива относят:
- испаряемость – способность переходить в парообразное состояние, характеризуется фракционным составом;
- вязкость влияет на процессы распыливания и топливоподачи;
- детонационная стойкость влияет на нормальное распределение пламени при сгорании. Работа двигателя на детонационном режиме недопустима вследствие перегрева двигателя, падения мощности, прогорания поршней, клапанов. Детонационная стойкость бензина характеризуется октановым числом, т.е. процентным по объему содержанием изооктана в такой смеси с нормальным гептаном, которая по детонационной стойкости равноценна данному топливу. Так, если исследуемое топливо детонирует так же, как смесь, содержащая 70% изооктана и 30% нормального гептана, то октановое число такого топлива = 70;
- склонность к воспламенению. Воспламеняемость дизельных топлив зависит от группового химического состава;
- примеси. Топливо не должно содержать механические примеси, воду, корродирующие вещества;
- температуру кристаллизации.
Одной из наиболее важных технических характеристик топлива является теплота сгорания.
Теплотой сгорания называют количество тепла, которое выделяется при полном сгорании 1 нм3
газообразного топлива. На практике теплоту сгорания топлива определяют методом калориметрирования. В закрытом сосуде сжигают определенное количество топлива. Теплота сгоревшего топлива через стенки сосуда передается воде. Зная это количество воды, окружающей сосуд, теплоемкость сосуда и разность температур воды до и после опыта, определяют теплоту сгорания топлива.
Различают высшую и низшую теплоту сгорания топлива. Теплота сгорания высшая больше, чем теплота сгорания низшая на количество теплоты, которое затрачивается на испарение влаги рабочей массы топлива и влаги, получаемой при сгорании водорода, входящего в состав топлива.
Высшая теплота сгорания определяется по формуле Менлелеева
Qs
af
=81С + 300Н − 26(О-S),
где С, Н, О, S — массовая доля элементов в веществе ТГИ, %
Низшая теплота сгорания определяется по формулам (кДж/кг или ккал/кг):
(для твердого вещества)
или
(для жидкого вещества), где:
• 2514 — теплота парообразования при температуре 0 °C и атмосферном давлении, кДж/кг;
• HP
и WP
— содержание водорода и водяных паров в рабочем топливе, %;
• 9 — коэффициент, показывающий, что при сгорании 1 кг водорода в соединении с кислородом образуется 9 кг воды.
Соотношение между теплотой сгорания высшей и низшей в кДж/кг

Для удобства расчетов и сравнения теплоты сгорания различных видов топлива пользуются понятием условное топливо. Теплота сгорания условного топлива составляет 29,3 МДж/кг (7000 ккал/кг).
Для пересчета расходов натурального топлива на условное служит тепловой эквивалент топлива
,
где Ву
и Вр
— расходы соответственно условного и рабочего (натурального) топлива; Э
— тепловой эквивалент топлива,
,
Или

Газообразное топливо представляет собой смесь различных газов. Природные газы содержат от 80 до 98% метана. Попутные газы, выходящие на поверхность из нефтяных скважин одновременно с добываемой нефтью, состоят из метана (40—60%) и тяжелых углеводородов (этана, пропана, бутана). Теплота сгорания природного газа , попутного .
Из искусственных газов наибольшее распространение получили генераторный газ , коксовой с и доменный с .
2.3 Двухтактные двигатели
ДВС, в которых рабочий цикл совершается за два хода поршня (один оборот коленчатого вала), называется двухтактными.
В двухтактном двигателе отсутствуют клапаны. Впуск горючей смеси и выпуск отработавших газов двигателей происходят через окна в цилиндре, которые своевременно открываются и закрываются движущимся поршнем.
Первый такт. При движении вверх поршень 2 (рис. 3.а) перекрывает выпускные окна 3 в цилиндре, в результате чего рабочая смесь над поршнем сжимается. Одновременно под поршнем создается разряжение, и из карбюратора 4 через выпускные окна 5 цилиндра горючая смесь засасывается в кривошипную камеру 6.
При подходе поршня к верхней мертвой точке (в.м.т.) в искровой свече зажигания 1 (рис. 3.б) образуется электрическая искра и рабочая смесь в цилиндре воспламеняется. На этом заканчивается первый такт.
Второй такт. Под давлением образовавшихся от сгорания рабочей смеси газов поршень перемещается вниз, совершая рабочий ход, который происходит до тех пор, пока не откроются выпускные клапана и начнется выпуск отработавших газов через выпускную трубу наружу. При движении поршня вниз горючая смесь в кривошипной камере сжимается. В конце второго такта поршень открывает окна продувочного канала 7 и горючая смесь нагнетается из кривошипной камеры в цилиндр, вытесняя из него отработавшие газы (рис. 3.в). происходят продувка и одновременно наполнение цилиндра свежей горючей смесью. При этом горючая смесь частично выходит вместе с отработавшими газами.

Рис.3. Схема работы двухтактного двигателя: а - первый такт; б – конец первого и начало второго такта; в – конец второго такта; 1 – искровая свеча зажигания; 2 – поршень; 3 и 5 – выпускное и впускное окна цилиндра; 4 – карбюратор; 6 – кривошипная камера; 7 – продувочный канал; 8 – цилиндр; 9 – выпускная труба; 10 – картер.
Таким образом, за два хода поршня (два такта) совершается полный рабочий цикл. Однако двухтактные двигатели менее экономичны, чем четырехтактные. При продувке через выпускные окна теряется 30% горючей смеси. Поэтому на тракторах их используют при кратковременной работе для пуска двигателя.
3. ПАРАМЕТРЫ, ХАРАКТЕРИЗУЮЩИЕ ПОРШНЕВЫЕ ДВИГАТЕЛИ
3.1 Среднее индикаторное давление и индикаторная мощность
Индикаторная мощность двигателя, полезная работа, совершаемая газами в цилиндре поршневого двигателя в единицу времени; определяется путём обработки индикаторных диаграмм, полученных при испытании двигателя. Индикаторная мощность данного двигателя различна на разных режимах его работы. Зависимость Индикаторная мощность от частоты вращения называется скоростной характеристикой. Чтобы построить скоростную характеристику Индикаторная мощность, снимают индикаторные диаграммы на различных частотах вращения. Путём планиметрирования площадей полученных диаграмм определяют Индикаторная мощность на данной частоте вращения. Индикаторная мощность частично расходуется на преодоление сил трения внутри двигателя и на приведение в действие вспомогательных механизмов. Индикаторная мощность может быть определена как сумма мощности, получаемой на коленчатом валу (эффективная мощность), и мощности, расходуемой на потери (мощность трения).
Под средним индикаторным давлением понимают такое условное постоянное давление, которое, действуя на поршень в течение одного рабочего хода, совершает работу, равную индикаторной работе газов в цилиндре за рабочий цикл.
Согласно определению среднее индикаторное давление находится как отношение индикаторной работы газов за цикл к единице рабочего объема цилиндра , т.е.
.
При наличии индикаторной диаграммы, снятой в двигателе (рис. 4), среднее индикаторное давление можно определить по высоте прямоугольника, построенного на основании , площадь которого равна полезной площади индикаторной диаграммы, представляющей собой в некотором масштабе индикаторную работу .
Определив с помощью планиметра полезную площадь индикаторной диаграммы в и длину индикаторной диаграммы в , соответствующую рабочему объему цилиндра, находят значение среднего индикаторного давления


,
где - масштаб давления индикаторной диаграммы, .
Среднее индикаторное давление при полной нагрузке у четырехтактных карбюраторных двигателей , у четырехтактных дизелей , а у двухтактных дизелей - .
Индикаторная работа, совершаемая газами в одном цилиндре за один цикл ,
.
где pi
- среднее индикаторное давление газов, н/м2
;
V – объем поршня, м2
.
Так как число рабочих циклов, совершаемых двигателем в секунду, равно 2 , то индикаторная мощность одного цилиндра
,
где - число оборотов коленчатого вала в секунду; - тактность двигателя – число тактов за цикл.
Индикаторная мощность многоцилиндрового двигателя при числе цилиндров :
.
3.2 Коэффициенты полезного действия
Экономичность действительного рабочего цикла двигателя определяется индикаторным к.п.д.
и удельным индикаторным расходом топлива . Экономичность работы двигателя в целом оценивается эффективным к.п.д.
и удельным расходом топлива .
Индикаторный к.п.д. оценивает степень использования теплоты в действительном цикле с учетом всех тепловых потерь и представляет собой отношение теплоты , эквивалентной полезной индикаторной работе, ко всей затраченной теплоте , т.е.
.
Теплота, затраченная на работу двигателя в течение 1 :
,
где - расход топлива, ; - низшая теплота сгорания топлива, .
Подставляя значения и в равенство (а), получим
.
Эффективный к.п.д. оценивает степень использования теплоты топлива с учетом всех видов потерь как тепловых, так и механических и представляет собой отношение теплоты , эквивалентной полезной эффективной работе, ко всей затраченной теплоте ,т.е.
.
Удельный эффективный расход топлива представляет собой отношение секундного расхода топлива к эффективной мощности , т.е.
или
.
Коэффициент полезного действия (КПД) теплового двигателя может быть определён как отношение полезной механической работы к затрачиваемому количеству теплоты, содержащейся в топливе. Остальная часть энергии выделяется в окружающую среду в виде тепла. КПД тепловой машины равен
,
Где Wтм
— механическая работа, Дж;
Qз
— затраченное количество теплоты, Дж.
Тепловой двигатель не может иметь КПД больший, чем у цикла Карно, в котором количество теплоты передается от нагревателя с высокой температурой к холодильнику с низкой температурой. КПД идеальной тепловой машины Карно зависит исключительно от разности температур, причём в расчётах используется абсолютная термодинамическая температура. Следовательно, для паровых двигателей необходимы максимально высокая температура T1
в начале цикла (достигаемая, например, с помощью пароперегрева) и как можно более низкая температура T2
в конце цикла (например, с помощью конденсатора):

Так как механический к.п.д.
равен отношению к , то получим
откуда
,
где - механический к.п.д.
3.3 Повышение удельной мощности двигателей
Увеличение быстроходности (повышение) пропорционально увеличивает удельную мощность до тех пор, пока не снижаются. Дальнейший прирост мощности при повышении частоты вращения идет до такого уровня, пока увеличивается произведение , несмотря на снижение коэффициента наполнения и механического КПД. Проблем, ограничивающих быстроходность современных карбюраторных двигателей из-за увеличения скорости горения, практически нет. При достижении некоторого, специфичного для каждого двигателя, режима (точки перегиба) максимальная мощность начинает снижаться, т. е. повышение числа оборотов не успевает компенсировать рост сопротивлений и ухудшение наполнения цилиндра. Как уже отмечалось, все конструктивные мероприятия, направленные на улучшение теплоиспользования, снижение механических и насосных потерь, увеличение наполнения цилиндра способствуют повышению скоростного режима двигателя, отодвигают точку перегиба внешней скоростной характеристики в сторону высоких чисел оборотов, что позволяет получить более высокие удельные мощности. Увеличению быстроходности двигателя препятствуют факторы предельно допустимой средней скорости и ускорений поршня, обеспечения надежности работы шатунных подшипников, поршневых колец и др. Максимальная частота вращения коленчатых валов современных гоночных двигателей находится в пределах 8000—20 000 об/мин. Однако средняя скорость поршня не превышает 22 м/с. Это достигается за счет уменьшения размерностей отдельного цилиндра и создания многоцилиндровых двигателей. Высокие ускорения поршня нередко вызывают вибрацию поршневых колец, прорыв газов под ними и даже их поломку. Для повышения надежности на гоночных двигателях применяют узкие стальные поршневые кольца. Хорошо подготовленный мотор должен выдерживать работу на скоростном режиме, соответствующем максимальной мощности, в течение нескольких часов без каких-либо повреждений. Диапазон рабочих частот вращения обычно является критерием для оценки внешней скоростной характеристики двтгателя. Границы этого диапазона определяют скорость вращения коленчатого вала при максимальной мощности (n точка перегиба) и минимальная угловая скорость n min, при которой двигатель еще устойчиво работает на полностью открытом дросселе. Рабочий диапазон оборотов коленчатого вала двигателя можно оценить коэффициентом диапазона d: Для большинства современных гоночных двигателей коэффициент диапазона находится в пределах 0,35—0,40. У некоторых высокофорсированных двигателей этот коэффициент снижается до 0,1 , и они по своим качествам приближаются к однорежимным моторам. Многие форсированные ДВС имеют внешние характеристики с крутым перегибом Nm и резким спадом мощности после точки перегиба, кроме того, работают в этом режиме с очень высокими механическими и тепловыми перегрузками. Такие двигатели отличаются малыми моторесурсом и надежностью в эксплуатации. Если кривая мощностной характеристики имеет плавный перегиб и постепенное снижение мощности после точки перегиба, то в определенных случаях целесообразно эксплуатировать двигатель именно в этом диапазоне частот вращения.
Способность продолжительно работать на высоком числе оборотов за перегибом характеристики является важным качеством двигателя в водно-моторном спорте. В режиме движения судна с полным отрывом корпуса от воды действует экранный эффект. Сопротивление выступающих частей и полное сопротивление движению резко снижается. В этом случае дальнейший прирост скорости судна возможен благодаря увеличению частоты вращения коленчатого вала даже при снижении мощности двигателя и уменьшении тяги гребного винта. Одним из трудных вопросов при повышении быстроходности двухтактного двигателя является обеспечение надежной работы нижнего шатунного подшипника, воспринимающего большее перегрузки от давления и центробежных сил, которые нельзя компенсировать облегчением поршня и шатуна. В отличие от четырехтактных ДВС здесь не удается осуществить достаточное охлаждение и смазку прокачкой большого количества масла. Охлаждение и смазка этого напряженного узла производится проходящей через картер топливной смесью. Поэтому шатунные подрипники надежно работают на обогащенных смесях с высокой скрытой теплотой испарения и повышенным содержанием смазочного масла.
5) Форсирование двигателя внутреннего сгорания путем применения топлив с высокой теплотворной способностью (повышение ) практически неосуществимо. Несмотря на большое разнообразие углеводородных топлив с теплотворной способностью, их объемная теплопроизводительность почти одинакова (820—840 ккал/м3 при). Объясняется это тем, что для полного окисления топлива с малой теплотворной способностью требуется меньшее количество воздуха. Как известно, мощность двигателя определяется количеством топливовоздушной смеси, сжигаемой в цилиндрах за единицу времени, и степенью теплоиспользования. Для топлив гоночных двигателей важнейшими качествами являются: а) антидетонационная стойкость; б) испаряемость (летучесть); в) скрытая теплота испарения. При выборе антидетонационных качеств топливной смеси следует учитывать, что необходимое октановое число топлива для любого двигателя — величина непостоянная. При увеличении частоты вращения коэффициент наполнения и давление конца сжатия снижаются, требуемая антидетонационная стойкость уменьшается. Именно поэтому у быстроходных гоночных Характеристика моторных топлив двигателей не очень высокая требовательность к октановому числу топлива, несмотря на высокие степени сжатия. При обогащении рабочей смеси углеводородные топлива в различной степень повышают свое октановое число. Высокая испаряемость ускоряет процесс смесеобразования, т. е. перемешивание топлива с воздухом, облегчает пуск двигателя, обеспечивает полноту сгорания циклового заряда. Если нет ограничений Правилами или Положением о соревнованиях, в гонках на короткие дистанции (5—15 миль) следует отдать предпочтение спиртовым топливам. Их высокая скрытая теплота парообразования и повышенная масса циклового заряда обеспечивают эффективное охлаждающее действие наиболее нагретых деталей: дна поршня, клапанов и шатунных подшипников, а также снижает температуру горючей смеси в конце хода сжатия перед воспламенением. Охлаждающий эффект можно усилить конструктивно — максимальным приближением распылителя к впускному окну (клапану). Тогда процесс испарения почти полностью протекает в кривошипно-шатунной камере и цилиндре, отбирая тепло от внутренних наиболее горячих деталей. Отсутствие испарения во впускном патрубке позволяет пропустить дополнительную порцию воздуха, заполняющую объем неиспаренной части топлива. Повышение коэффициента наполнения и плотности заряда при использовании спиртовых топлив называют компрессорным эффектом. Лабораторными исследованиями определено, что без каких-либо конструктивных изменений при переходе с бензина на спиртовое топливо прирост мощности составляет 5-8%. Еще одним достоинством спирта является его способность надежно воспламеняться от электрической искры в широком диапазоне изменений состава топливной смеси. Пределы воспламеняемости спиртовых топлив составляют против для бензина, причем скорость горения спиртовых смесей почти не снижается во всем диапазоне воспламеняемости. Для повышения надежности воспламенения иногда применяют следующий прием. Карбюраторы регулируют на обогащенную смесь. При этом двигатель может устойчиво работать, разбивая обороты, близкие к максимальным. Не полностью сгоревшая часть топлива выбрасывается с отработавшими газами. Такой режим работы обеспечивает значительное снижение тепловой напряженности двигателя, существенное повышение надежности, улучшение антидетонационной стойкости без увеличения октанового числа топлива. Подобная настройка двигателя на бензине невозможна из-за обильного нагарообразования и малой скорости горения богатой бензовоздушной топливной смеси. Таким образом, применение спиртовых топлив несколько усложняет пуск, но повышает максимальную мощность и надежность работы гоночных двигателей. Небольшие добавки бензина и ацетона к спиртовым топливным смесям служат для улучшения пуска двигателя. Современные гоночные моторы оснащаются мощными, надежными, чаще всего электронными, системами зажигания, что позволяет использовать спирты (метанол и этанол) без улучшающих пуск присадок. Значительное увеличение удельной мощности интенсификацией рабочего процесса можно получить, включая в состав топлива азотистые соединения, например нитрометан и нитробензол. Форсирующий эффект этих топлив состоит в том, что появляется возможность окислить дополнительное количество топлива за счет кислорода молекулы NO. Добавляя азотистые присадки к топливу, следует всегда помнить, что сгорание таких смесей идет при повышенных температуре и давлении, а это существенно снижает надежность и моторесурс. Малейший просчет в регулировке может оказаться причиной неудачи. Обеднение смеси вызывает прогар поршней. Избыток нитросоединений может привести к обгоранию клапанов и электродов запальных свечей, поломкам деталей кривошипно-шатунного механизма. После работы на топливе, содержащем нитроприсадки, двигатель требует незамедлительной промывки. В качестве смазок гоночных двигателей внутреннего сгорания наибольшее применение имеют касторовое масло и комбинированные смазки на его основе. Такие масла обладают очень высокими смазывающими качествами, проникают в малейшие зазоры, выдерживают большие давления и температуры, имеют минимальную склонность к нагарообразованию (практически беззольные).
4. ДИЗЕЛЬНЫЕ ДВИГАТЕЛИ
4.1 Особенности и применение
Двигателям, работающим по циклу с подводом теплоты при Р=const, соответствуют стационарные и судовые компрессорные дизельные двигатели с распыливанием жидкого топлива в цилиндре двигателя при помощи сжатого в специальном компрессоре воздуха, которые имеют значения 
Автомобиль с дизельным типом двигателя является более экономичным по 2 причинам: дизельное топливо более дешево, чем бензин; у дизельного автомобиля степень сжатия больше степени сжатия бензинового двигателя почти в два раза.
У дизельных двигателей также более высокий КПД (около 40%). Для сравнения КПД бензинового двигателя всего лишь около 30%.
Регулирование рабочей смеси в дизельном ДВС более качественное, чем в бензиновом. Подаваемое в цилиндры количество воздуха не зависит от частоты вращения коленвала и нагрузки.
Расход топлива в первую очередь зависит от сопротивления воздухоочистителя, которое влияет на наполнение цилиндров воздухом, давления начала подъема иглы форсунки, качества распыла топлива форсунками, угла опережения впрыска топлива, от характера подачи топлива топливным насосом высокого давления. Стабильности регулировочных параметров системы подачи топлива, у дизельных двигателей выше, чем у бензиновых.
Дизельный двигатель выдает высокий крутящий момент в широком диапазоне оборотов, что делает автомобиль с дизельным двигателем более «гибким» в движении, чем такой же автомобиль с бензиновым двигателем. Высокий крутящий момент при низких оборотах делает более легким эффективное использование мощности двигателя, это преимущество используется в джипах и грузовых автомобилях.
У дизельных двигателей также имеются недостатки - это большая масса, меньшая литровая мощность, повышенный шум.
Но помимо положительных черт дизельного двигателя он имеет и недостатки: сравнительно большая масса, высокий шуми меньшую литровую мощность, чем в бензиновых ДВС.
Дизельные двигатели применяют:
· стационарные силовые установки;
· в качестве главных и вспомогательных двигателей в судостроении
· на рельсовых (тепловозы, дизелевозы) и безрельсовых (автомобили, автобусы, грузовые автомобили) транспортных средствах;
· самоходных машинах и механизмах.
4.2 Смесеобразование в дизелях и типы камер сгорания
Смесеобразование – процесс приготовления горючей смеси из топлива и воздуха. Топливо через форсунку впрыскивается в цилиндр под высоким давлением, вследствие чего образуется горячая смесь.
На качество смесеобразования влияет не только качество распыливания топлива, но и способ смесеобразования и тип камеры сгорания. Различают дизели с непосредственным впрыском топлива (или дизели с неразделенной камерой сгорания) и дизели с разделенной камерой сгорания.
По типам камер сгорания дизельные ДВС делят на:
1. дизели с неразделенной камерой сгорания (или с непосредственным впрыском топлива);
2. дизели с разделенной камерой сгорания.
Рассмотрим некоторые типичные схемы неразделенных камер сгорания (рис. 1.5). Камеры этого типа получили наиболее широкое применение. Процесс смесеобразования здесь идет в едином объеме,, поэтому к качеству распыливания предъявляют очень высокие требования. Для более полного распыливания топлива применяют только многодырчатые форсунки 4. Хорошее распыливание обеспечивается при высоком давлении впрыска (200-2000 кГ/см2).

Рис. 5. Неразделенные камеры сгорания:
а - днище сложной формы с выступающей центральной частью, б - днище поршня с выступающим краем, в - днище с полусферической выемкой, г - камера в поршне с объемно-пленочным смесеобразованием; / - поршень, 2 - днище поршня, 3 - головка цилиндра, 4 - форсунка
В неразделенных камерах с объемным смесеобразованием стремятся все топливо равномерно распределить в воздушном заряде камеры. Камера сгорания должна иметь такую конфигурацию, чтобы каждая частица топлива успела загореться раньше, чем достигнет стенок цилиндра. У некоторых дизелей для более полного перемешивания топлива используют принудительное завихрение воздуха. У четырехтактных дизелей применяют впускные клапаны со специальным козырьком для завихрения, а у двухтактных - тангенциально направленные продувочные окна. Наиболее часто применяют форму камеры, показанную на рис. 5, а, которая напоминает горящие факелы топлива. Реже используют сковородообразную форму (рис. 5, б) и полусферическую (рис. 5, в). Главные достоинства объемного смесеобразования- простая и симметричная форма камеры, небольшие тепловые потери и хорошие пусковые качества.
В неразделенных камерах с пленочным смесеобразованием камера имеет шарообразную форму и располагается в поршне. Форсунка установлена под очень малым углом к внутренней сферической поверхности камеры и примерно 95% топлива под давлением около 150 кГ/см2 подается в виде тонкой пленки на эту поверхность. Поджигание топлива, испарившегося с поверхности камеры, осуществляется вследствие воспламенения 5% топлива, направленного в центральную часть воздушного заряда. Дизели с пленочным смесеобразованием являются многотопливными, т. е. могут работать на дизельном топливе, газойле-и др.
На рис. 5, г показана неразделенная камера со смешанным (объемно-пленочным) смесеобразованием. Здесь количество топлива, направляемого на стенки, зависит от формы камеры сгорания, расположения форсунок и др. Камеры с объемно-пленочным смесеобразованием характеризуются невысоким давлением сгорания, плавной и мягкой работой.
Разделенную камеру сгорания имеют предкамерные дизели. У этих дизелей камера сгорания состоит из основной камеры и предкамеры, сообщающееся с основной камерой одним или несколькими каналами. Предкамера чаще всего имеет цилиндрическую форму, а форсунка располагается по оси камеры и имеет однодырчатый распылитель. Процесс смесеобразования происходит следующим образом. При ходе сжатия давление в цилиндре возрастает и воздух с большой скоростью через соединительные каналы входит в предкамеру, где. происходит интенсивное вихреобразование. Благодаря этому топливо, впрыскиваемое за 10-20° до в.м.т. в предкамеру, хорошо перемешивается с воздухом и воспламеняется.
В предкамере топливо сгорает частично из-за недостатка кислорода. Остальная часть топлива в связи с резким повышением давления при сгорании выбрасывается с большой скоростью через соединительные каналы в главную камеру. При этом основная часть топлива также распыливается, перемешивается с воздухом, находящимся в главной камере, и догорает.
Неразделенные камеры
(рис. 6) ограничены днищем поршня 1 и поверхностями стенок и головки 5 цилиндра 2. В этот объем форсункой 4 впрыскивается топливо, чаще всего в виде нескольких струй, через отверстия достаточно малого диаметра (0,2—0,4 мм). Форму камеры приспосабливают в известной мере к форме струи топлива, чтобы лучше использовать воздушный заряд в цилиндре.
В большинстве дизелей с неразделенными камерами сгорания конструкция впускной системы обеспечивает создание вращательного движения воздуха в цилиндре, которое в некоторой степени сохраняется до конца сжатия, способствуя качественному смесеобразованию и сгоранию. В рассматриваемых дизелях скорость движения воздуха у стенки камеры не превышает 30—35 м/с.

Рис. 6. Неразделенная камера сгорания дизеля:
1 — поршень, 2 — цилиндр, 3 — камера сгорания, 4 — форсунка, 5 — головка цилиндра
Недостаток дизелей с неразделенными камерами — необходимость в высоком давлении впрыска — до 20 МПа, что предъявляет повышенные требования к топливной аппаратуре. Кроме того, дизель весьма чувствителен к сорту топлива: использование тяжелого топлива оказывается невозможным. Качество смесеобразования ухудшается при понижении нагрузок и частоты вращения коленчатого вала двигателя.
Разделенные камеры
сгорания состоят из двух частей: основной камеры, расположенной над поршнем, и дополнительной, помещенной чаще всего в головке цилиндра. Основная и дополнительная камеры соединены между собой одним или несколькими каналами. Наибольшее распространение получили следующие два типа разделенных камер сгорания: вихревые камеры и предкамеры.


При форкамерном процессе топливо впрыскивается в специальную предварительную камеру, связанную с цилиндром несколькими небольшими каналами или отверстиями, ударяется об ее стенки и перемешивается с воздухом. Воспламенившись, смесь поступает в основную камеру сгорания, где и сгорает полностью. Сечение каналов подбирается так, чтобы при ходе поршня вверх (сжатие) и вниз (расширение) между цилиндром и форкамерой возникал большой перепад давления, вызывающий течение газов через отверстия с большой скоростью.
Во время вихрекамерного процесса сгорание также начинается в специальной отдельной камере, только выполненной в виде полого шара. В период такта сжатия воздух по соединительному каналу поступает в предкамеру и интенсивно закручивается (образует вихрь) в ней. Впрыснутое в определенный момент топливо хорошо перемешивается с воздухом.
Таким образом, при разделенной камере сгорания происходит как бы двухступенчатое сгорание топлива. Это снижает нагрузку на поршневую группу, а также делает звук работы двигателя более мягким. Недостатком дизельных двигателей с разделенной камерой сгорания являются: увеличение расхода топлива вследствие потерь из-за увеличенной поверхности камеры сгорания, больших потерь на перетекание воздушного заряда в дополнительную камеру и горящей смеси обратно в цилиндр. Кроме того, ухудшаются пусковые качества.
Дизельные двигатели с неразделенной камерой называют также дизелями с непосредственным впрыском. Топливо впрыскивается непосредственно в цилиндр, камера сгорания выполнена в днище поршня. До недавнего времени непосредственный впрыск использовался на низкооборотистых дизелях большого объема (проще говоря, на грузовиках). Хотя такие двигатели экономичнее моторов с разделенными камерами сгорания, их применение на небольших дизелях сдерживалось трудностями организации процесса сгорания, а также повышенными шумом и вибрацией, особенно в режиме разгона.
Сейчас благодаря повсеместному внедрению электронного управления процессом дозирования топлива удалось оптимизировать процесс сгорания топливной смеси в дизеле с неразделенной камерой сгорания и существенно снизить шумность. Новые дизельные двигатели разрабатываются только с непосредственным впрыском.
4.3 Топливные системы
Система питания дизелей топливом включает топливный бак, фильтры, топливоподкачивающий насос, насос высокого давления, форсунки, трубопроводы и соединительную арматуру.
Топливные фильтры являются ответственным элементом системы питания дизелей, так как качество очистки топлива оказывает большое влияние на надежность работы топливного насоса и форсунок. Зазоры в прецизионных парах топливной аппаратуры находятся в пределах 15—25-1СН. Поэтому и размеры механических примесей в топливе после очистки не должны превышать указанных значений. Очистку топлива производят в фильтрах грубой и тонкой очистки. В двигателе А-01Л применяют трехступенчатую очистку, являющуюся контрольной очисткой в фильтре ТФ-3.
Топливоподкачивающий насос может быть поршневым, шестеренчатым и коловратным. Поршневые насосы получили наибольшее распространение, так как могут создавать разрежение, обеспечивающее подсос топлива из емкости, расположенной на 1,5—2 м ниже насоса. Поршень движется вверх под действием роликового толкателя, приводимого в движение от кулачка, вниз —под действием сжатых пружин. Топливоподкачивающий насос создает давление в топливопроводе низкого давления в пределах 0,15—0,2 МПа и должен иметь производительность, примерно в 5 раз превышающую максимальную потребность двигателя в топливе. Объясняется такой большой резерв производительности тем, что для выделения пузырьков воздуха из топлива оно должно непрерывно циркулировать во впускной полости насоса высокого давления.
Топливный насос высокого давления подает топливо через трубопровод и форсунки в камеры сгорания двигателя. На автотракторных дизелях применяются насосы плунжерного типа, в которых имеются секции для каждого цилиндра. Плунжер (рис. 8, а) получает движение от кулачкового вала через роликовый толкатель. Гильза имеет впускное окно. Подъем плунжера под действием кулачка сопровождается сжатием пружины 8, под действием которой плунжер опускается.
Характерные положения плунжера показаны на рис. 8, б.
Верхняя часть плунжера имеет продольную канавку (см. рис. 8, б), кольцевую выточку с винтовой (отсечной) кромкой. Такое устройство плунжера необходимо для регулирования количества подаваемого топлива за один цикл работы насоса поворотом плунжера. С этой целью на его хвостовик насажен зубчатый сектор (см. рис. 7, а), находящийся в постоянном зацеплении с зубчатой рейкой, которая системой тяг и рычагов связана с центробежным регулятором двигателя и с ручным управлением. При повороте плунжера, вызываемом движением зубчатой рейки, изменяется расстояние по вертикали h (см. рис. 7, б) между винтовой кромкой плунжера и нижней кромкой впускного отверстия.

Рис. 8. Принципиальная схема топливного насоса высокого давления: а — схема устройства: 1 — кулачковый вал; 2 — роликовый толкатель; 3 — плунжер; 4 — гильза; 5 — впускное окно; 6 — нагнетательный клапан; 7 —пружина; 8 — пружина обратного хода плунжера; б — характерные положения плунжера: /— ход плунжера без подачи топлива; // —начало подачи; /// — конец подачи (отсечка); 1 — плунжер; 2 — гильза; 3 — седло обратного клапана; 4 — обратный клапан; 5 —пружина клапана; 6 — цилиндрический (разгрузочный) поясок клапана; 7— впускное отверстие
Размер h показывает величину рабочего (не полного!) хода плунжера, который определяет количество подаваемого топлива.
Форсунки осуществляют впрыск топлива в камеру сгорания, подводимого к ним под высоким давлением.
Качество впрыска определяется: тонкостью и однородностью распыливания топлива; равномерным распределением частиц распыленного топлива, в камере сгорания; своевременным началом и окончанием впрыска; поддержанием требуемого давления впрыска при различных режимах работы двигателя.
Форсунки бывают двух типов — открытые, не разобщающие камеру сгорания с форсункой после впрыска, и закрытые, имеющие запорную иглу, открывающую сопловое отверстие форсунки на период впрыска топлива. Закрытые форсунки конструктивно сложнее, по они обеспечивают впрыск топлива на всех режимах работы двигателя под постоянным давлением и поэтому более распространены.
4.4 Подвод воздуха и отвод выпускных газов
Для нормальной работы дизеля необходимо обеспечивать подачу воздуха в его цилиндры и выпуск из них отработавших газов. Наполнение цилиндров воздухом может осуществляться как за счет разрежения, создаваемого движущимися в цилиндрах поршнями, так и за счет подачи воздуха в цилиндры под давлением, превышающим атмосферное. Во втором случае, т. е. с применением наддува, масса воздуха, заполняющего цилиндр, значительно больше, что позволяет сжигать больше топлива за каждый цикл и повышать мощность дизеля при сохранении его габаритов.
Для нагнетания воздуха в цилиндры дизеля используется специальное оборудование, различающееся между собой по приводу и принципу действия. Сжатие воздуха всегда сопровождается повышением температуры, что приводит к снижению его плотности. Это нежелательно, так как одновременно уменьшается масса воздуха в цилиндрах дизеля (воздушный заряд). Охлаждение сжатого воздуха можно производить в промежуточных теплообменниках, расположенных между нагнетателем и воздушным коллектором..
Отработавшие в цилиндрах газы выбрасываются в атмосферу, но перед выбросом они отдают часть своей энергии на привод ротора турбонагнетателя. Отвод газов от цилиндров дизеля осуществляется через цилиндровые крышки и два выпускных коллектора, имеющих надежную теплоизоляцию.
Турбонагнетатель (рис. 9, а) предназначен для подачи воздуха под давлением в цилиндры дизеля. На номинальном режиме работы давление наддувочного воздуха достигает 0,06 МПа (0,6 кгс/см2), а подача — 6550 м /ч (при частоте вращения ротора турбонагнетателя 18 800 об/мин).
Неподвижная часть турбонагнетателя (статор) состоит из трех корпусов: входного 6, турбинного 9 и воздушного 16, соединенных цилиндрическими фланцами.
Входной корпус 6 соединен с двумя выпускными коллекторами и имеет каналы для прохода выпускных газов к турбине, расположенной в среднем (турбинном) корпусе 9.
Входной 6 и турбинный 9 корпусы, соприкасающиеся с горячими выпускными газами, отлиты из чугуна и имеют водяные полости для охлаждения водой, циркулирующей в основном контуре. Подвод воды из напорного коллектора осуществляется через нижние, а отвод — через верхние штуцера корпусов, причем из турбинного корпуса вода выходит через два верхних штуцера. Охладившая турбонагнетатель вода отводится по трубопроводу в коллектор горячей воды.
К торцу входного корпуса, обращенному к турбинному, крепят тремя болтами 7 с лепестковыми шайбами сопловой аппарат 8, представляющий собой стальное лопастное колесо. Газы, проходящие через сопловой аппарат, перед тем как попасть на лопатки турбинного колеса приобретают нужное направление и большую скорость за счет специальной формы неподвижных лопастей аппарата.
Из турбинного корпуса 9 газы отводятся через глушитель в выпускную трубу. В верхней части корпуса имеется прямоугольное отверстие, заканчивающееся обработанным фланцем для крепления глушителя. Снизу к турбинному корпусу крепят болтами 28 две лапы 27 для установки турбонагнетателя на кронштейн, прикрепленный восемью шпильками к заднему торцу блока цилиндров. Турбонагнетатель закрепляют на кронштейне восемью болтами.
Чтобы ограничить передачу тепла от выпускных газов к нагнетаемому воздуху, между турбинным 9 и воздушным 16 корпусами имеется теплоизоляция. Она состоит из стекловаты 26, заключенной в металлический кожух 12, который прикреплен болтами к воздушному корпусу. Кожух 12 одновременно охватывает вал ротора, уменьшая возможность его нагрева и передачи тепла по валу к рабочему колесу нагнетателя.
Лопаточный диффузор 24 служит для направления воздуха, отбрасываемого лопастями рабочего колеса, в расширяющийся канал улиткообразного корпуса. За счет формы лопаток диффузора уменьшается скорость нагнетаемого воздуха и одновременно увеличивается его давление.
Ротор турбонагнетателя (рис. 9, б) состоит из вала 11 и двух колес: турбинного 10 и рабочего 14. Диск турбины приварен к валу, причем плавный переход (галтель) от вала к диску обеспечивает достаточную прочность турбины. В диске сделано 45 елочных пазов для крепления лопаток, изготовленных из жаропрочной стали и имеющих елочные хвостовики. Все лопатки для прочности скреплены бандажной проволокой.
Рабочее колесо нагнетателя состоит из двух частей, отлитых из алюминиевого сплава. Одна часть колеса — заборник 23 — имеет спиральные лопасти, а другая (рабочая) — прямые радиальные, причем переход от спиральных лопастей к радиальным выполнен плавным. Колесо с помощью шпонки 13 напрессовано на вал до упора в выступ и закреплено кольцом 22, которое насаживается на вал в горячем состоянии.
Смазывание подшипников осуществляется дизельным маслом, заливаемым в камеры через специальные горловины, которые закрыты пробками 4. Для контроля за уровнем масла в камерах крышки 2 оснащены круглыми стеклами 3. При неработающем дизеле уровень масла должен быть выше центра стекла на 4 мм. Для смазывания подшипников применены центробежные диски 5, укрепленные на валу ротора. Вращающиеся диски захватывают масло и забрасывают его в корпуса подшипников, после чего масло вновь стекает в камеру.
4.5 Устройство двухтактных и четырехтактных двигателей
Четырехтактные дизели (Рис.10). 1 такт – впуск. При движении поршня от ВМТ к НМТ вследствие образующегося разряжения из воздухоочистителя в полость цилиндра через открытый впускной клапан поступает атмосферный воздух. Давление воздуха в цилиндре составляет 0.08 - 0.095 МПа, а температура 40 - 60 С.
2 такт – сжатие. Поршень движется от НМТ к ВМТ; впускной и выпускной клапаны закрыты, вследствие этого перемещающийся вверх поршень сжимает поступивший воздух. Для воспламенения топлива необходимо, чтобы температура сжатого воздуха была выше температуры самовоспламенения топлива. При ходе поршня к ВМТ цилиндр через форсунку впрыскивается дизельное топливо, подаваемое топливным насосом.
3 такт – расширение или рабочий ход. Впрыснутое в конце такта сжатия топливо, перемешиваясь с нагретым воздухом, воспламеняется, и начинается процесс сгорания, характеризующийся быстрым повышением температуры и давления. При этом максимальное давление газов достигает 6-9МПа, а температура 1800-2000С. Под действием давления газов поршень 2 перемещается от ВМТ в НМТ – происходит рабочий ход. Около НМТ давление снижается до 0.3-0.5МПа, а температура до700-900С.

а) 1 такт б) 2 такт в) 3 такт г) 4 такт
(впуск воздуха) (сжатие воздуха) (рабочий ход) (выпуск)
Ри2с.10. Схема работы четырехтактного дизеля:
1 — топливный насос, 2 — поршень, 3 — форсунка, 4, 5 — впускной и выпускной клапаны, 6 — цилиндр 4 такт – выпуск.
Поршень перемещается от НМТ в ВМТ и через открытый выпускной клапан 6отработавшие газы выталкиваются из цилиндра. Давление газов снижается до 0.11-0.12МПа, а температура до 500-700С. После окончания такта выпуска при дальнейшем вращении коленчатого вала рабочий цикл повторяется в той же последовательности.
Двигатель внутреннего сгорания, в котором рабочий цикл совершается за один оборот коленчатого вала, т. е. наполнение цилиндра горючей смесью (или воздухом), сжатие и сгорание, а также расширение и выпуск газов происходят за два хода поршня (рис. 10).
Часть свежего заряда, поступившего в цилиндр, неизбежно теряется через выпускные органы во время процесса продувки, что снижает экономичность двух2тактного двигателя. Недостатками Д. д. являются высокая термическая нагруженность поршневой группы, снижающая надёжность двигателя, и сложность осуществления продувки.
5. РАСЧЕТ ГОРЕНИЯ ТОПЛИВА
5.1 Состав топлива и его характеристики
Топливо — это горючие вещества, основной составной частью которых является углерод, применяемые с целью получения при их сжигании тепловой энергии.
Топливо состоит из сложных химических соединений, углерода (C), водорода (Н), кислорода (О), азота (N) и серы (S). Также топливо включает в себя минеральные примеси А, воду W.
Элементарный состав топлива может задаваться органической, рабочей, горючей или сухой массами. Эти массы могут быть представлены следующими равенствами:
Органическая
Со
+Но
+Оо
+Nо
= 100%
Рабочая масса
Ср
+Нр
+Ор
+Nр
+Sр
+Aр
+Wр
= 100%;
Сухая
Сс
+Нс
+Ос
+Nс
+Sс
л
+Aс
= 100%;
Горючая
Сг
+Нг
+Ог
+Nг
+Sг
л
= 100%;
Где Со
, Ср
, Сс
, Сс
– содержание углерода, входящего в состав соответственно рабочей, сухой, горючей и органической массе топлива; Hр
, Hс
, Hr
, Hо
– содержание водорода; Оо
, Ор
, Ос
, Ог
— содержание кислорода; Nо
, Nр
, Nс
, Nг
— содержание азота; Sр
, Sc
л,
Sг
л
— содержание серы; Аp
, Аc
,Wp
— содержание золы и влаги.
При этом
,
где Sр
, Sр
л
, Sр
м
— это суммарное содержание в топливе соответственно серы, летучей серы, минеральной серы.
Химический состав газообразного топлива можно хадать в процентах по объему. Все расчеты, связанные с определением состава газообразного топлива, производятся для сухого газа при нормальных условиях. Содержание водяных паров и других примесей (пыли и смол) задается в сухого газа.
Одной из важных составляющих частей является углерод. При полном сгорании углерода выделяется 34 100 кДж тепла. Чем выше содержание углерода в топливе, тем больше тепла выделится при его сжигании. При химической переработке топлива углерод входит в состав образующихся при этом органических соединений. Другой основной составной частью топлива является водород. Кислород и азот относятся к негорючей массе топлива (к балласту). Сера содержится в топливе в виде колчедановой серы ( и сернистых органических соединений) и в виде сульфатов (сернокислых соединений кальция, магния и натрия). Количество горючей серы определяется как разность между общим содержанием серы в топливе и количеством сульфатной серы. Твердый негорючий продукт полного окисления и разложения всех минеральных примесей топлива называют золой. Качество золы в продуктах сгорания и ее количество учитываются при использовании топлива. Зола после разложения и плавления превращается в сплавленную массу, которая называется шлаком.
Важным показателем качества топлива является выход летучих веществ и характеристика кокса. В состав летучих веществ, которые выделяются из топлива при нагревании, входят газы — окись углерода, водород, углеводороды, азот, кислород, углекислый газ и др.
Выход летучих веществ определяют в процентах к безводной и беззольной (горючей) массам топлива:

Где — соответственно выход летучих веществ, содержание золы и влаги в топливе на аналитическую пробу в процентах.
Чем больше выход летучих веществ, тем легче загорается топливо. Выход летучих веществ положен в основу классификации твердого топлива.
5.2 Процессы горения топлива
Горение топлива - химический процесс соединения горючих веществ топлива с кислородом воздуха, который сопровождается интенсивным выделением теплоты.
Процессы горения могут быть гомогенными и гетерогенными. Если топливо и окислитель (кислород) находятся в газообразном состоянии и образуют гомогенную смесь, то горение протекает в объеме и называется гомогенным. При гетерогенном горении топливо и окислитель находятся в различных агрегатных состояниях, реакции протекают на поверхности раздела фаз: твердой, жидкой и газообразной. Процесс горения топлива условно можно разделить на две стадии: воспламенение и последующее горение. При нагревании топлива происходит повышение температуры. При достижении определенной для каждого топлива температуры (температуры воспламенения) топливо воспламеняется, после чего начинается процесс устойчивого горения.
Расход воздуха. Теоретическое количество воздуха, необходимое для сгорания топлива, определяется по формулам горения составных элементов топлива. Так, для сгорания 1 кг
углерода необходимо 32/12 = 8/3 = 2,67 кг
кислорода, так как реакция горения углерода протекает следующим образом:

Для сгорания 1 кг водорода требуется 8 кг кислорода:
;
для сгорания 1 кг серы — 1 кг кислорода:
.
Если учесть, что массовая доля содержания кислорода в воздухе равна 0,232, то теоретически необходимое количество воздуха для сгорания 1 кг твердого и жидкого топлива при нормальных условиях (в кг воздуха на кг топлива)
.
Так как при нормальных условиях плотность воздуха , то объемный расход воздуха для сгорания 1 кг топлива

или

где — элементарный состав топлива на рабочую массу, %.
В выражении коэффициенты m
и n
принимаются равными значениям индексов тех газов, перед которыми стоят эти коэффициенты.
Практически при горении часть кислорода воздуха не участвует в химических реакциях, поэтому для полного сгорания топлива подводят воздуха больше, чем необходимо теоретически. Отношение действительного количества воздуха ( ), подводимого в процессе горения, к теоретически необходимому ( ), называется коэффициентом избытка воздуха

Состав продуктов сгорания
. Условно считают, что продукты сгорания топлива (в м3
/кг)

где — сухие газы; — водяные пары.
Объем сухих газов

где .
При = 1 объем сухих газов минимальный, т.е. . Если > 1, то

где 0,79 — объем азота в теоретически необходимом количестве воздуха; 0,0187 — объем трехатомных газов
.
Объем продуктов сгорания газообразного топлива определяется по той же формуле, что и для твердого или жидкого. При этом
.
При = 1

где — влагосодержание газообразного топлива. При > 1

Объем сухих газов при > 1
.
При атмосферном давлении с учетом температуры газов объем продуктов сгорания
.
Состав продуктов сгорания определяется с помощью газоанализаторов.
Энтальпия продуктов сгорания
. Энтальпия (теплосодержание) продуктов сгорания топлива определяется суммированием теплосодержаний отдельных составляющих дымовых газов и зависит от вида топлива (твердое, жидкое или газообразное). Энтальпия имеет размерность кДж/кг или кДж/м3
и равна

Энтальпия теоретического объема газов ( = 1) при температуре 
 
Энтальпия продуктов сгорания при > 1 больше чем (т. е. при = 1)
 
Где — энтальпия теоретически необходимого воздуха
кДж/кг или кДж/м3
; — энтальпия дополнительного объема водяных паров
кДж/кг или кДж/м3
;
— энтальпия золы
кДж/кг,
где — доля золы топлива, уносимая газами из топки; — соответственно теплоемкости при постоянном давлении трехатомных газов, азота, водяных паров, воздуха и золы при температуре .
Рабочий состав доменного газа, %:
;
;
;
;
.
Таблица 1. Состав рабочего доменного газа.
Газ
|
СН4
|
СО2
|
H2
|
CO
|
N2
|
H2
O
|
∑
|
Доменный
|
0,285
|
12,039
|
1,337
|
25,596
|
55,553
|
5,19
|
100
|
Определение теплоты сгорания газов
.
Природного газа:
.
Доменного газа:
.
Расчет состава смеси природного и доменного газов.
Принимаем долю доменного газа в природно-доменной смеси (ПДС) за x, тогда доля природного газа будет равна y = (1-x). Составляем уравнение:
,
где – исходная теплота сгорания смеси газов, МДж/м3
.
Находим, что
Мдж/м3
.
у = (1-х) = 1-0,747 = 0,253.
Состав смешанного газа, %.
;









6. УСТРОЙСТВО ДВИГАТЕЛЯ АВТОМОБИЛЯ МАРКИ ВАЗ-2101
6.1 Основные механизмы и системы двигателя
Для нормальной работы двигателя в цилиндры должны подаваться горючая смесь в определенной пропорции. Для уменьшения затрат работы на преодоление трения, отвода теплоты, предотвращения задиров и быстрого износа трущиеся детали смазывают маслом. В целях создания нормального теплового режима в цилиндрах двигатель должен охлаждаться. Двигатель, устанавливаемый на автомобиль ВАЗ-2101, состоит из следующих механизмов и систем.
Система зажигания
служит для воспламенения рабочей смеси в цилиндрах двигателя в определенный момент.
Механизм газораспределения
управляет работой клапанов, что позволяет в определенных положениях поршня впускать воздух или горючую смесь в цилиндры, сжимать их до определенного давления и удалять оттуда отработавшие газы.
Кривошипно-шатунный механизм
преобразует прямолинейное движение поршней во вращательное движение коленчатого вала.
Система питания
двигателя предназначена для приготовления горючей смеси в карбюраторе и подачи ее в цилиндры двигателя, а также для отвода продуктов сгорания из цилиндров.
Смазочная система
необходима для непрерывной подачи масла к трущимся деталям и отвода теплоты от них.
Система охлаждения
предохраняет стенки камеры сгорания от перегрева и поддерживает в цилиндрах нормальный тепловой режим.
6.2 Силы и моменты, действующие в двигателе
Рассмотрим силы, действующие в кривошипно-шатунном механизме. Суммарная сила определяется из следующей формулы - , где - силы инерции от возвратно-поступательно движущихся масс. Определяются они на основании выражения , т.е. произведения массы на ускорение J. К этой массе относят: массу поршневого комплекта и часть массы шатуна ( ), отнесенной к массе, совершающей возвратно-поступательное движение (для этого осуществляют приведение действительных масс элементов КШМ к динамически эквивалентным см. рис. 11).

Рис. 11. Силы инерции
и массы кривошипно-шатунного механизма, создающие их
Так же как и ускорение
J = =
Газовая сила задается свернутой индикаторной диаграммой или развернутой индикаторной диаграммой по углу поворота коленчатого вала (ПКВ). Суммируя затем ее с получают - основную нагрузку на элементы КШМ.
При испытаниях можно получить и развернутую индикаторную диаграмму по углу ПКВ, использую пневмоэлектрический датчик и специализированную аппаратуру, получив таким образом действующие газовые силы. Затем ее можно свернуть в координаты для определения индикаторных показателей двигателя.
Давление газов в цилиндре двигателя создает усилие на головке двигателя и на поршне , которое, передаваясь через подвижные элементы КШМ, выходит на коренные опоры, но не передается на опоры двигателя и не требует уравновешивания. Она уравновешивается внутри двигателя за счет упругой деформации элементов формирующих внутрицилиндровое пространство.
В КШМ действует и еще одна значительная по величине сила инерции – центробежная сила инерции , создаваемая массами вращающихся элементов: - массой колена и частью массы шатуна, совершающей вращательное движение, и полученной в результате приведения масс
В результате получаем систему масс создающих силы инерции и . Они выходят на опоры двигателя и требуют уравновешивания.
Вектор силы прикладывается к оси поршневого и раскладывается на две составляющие: N и S.

- боковая сила, прижимающая направляющую часть поршня к зеркалу цилиндра и вызывающая их взаимный износ.
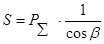
направлена по оси шатуна; сжимает или растягивает шатун.
Перенесем силу S по линии ее действия и приложим к оси шатунной шейки (обозначим ). Силу разложим на две составляющие:
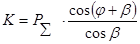
нормальная сила; направлена по радиусу кривошипа; сжимает и растягивает щеку кривошипа; нагружает шатунную и коренную шейки.
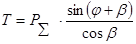
тангенциальная сила; вектор ее перпендикулярен радиусу кривошипа.
Силу К перенесем по линии ее действия и приложим к оси коренной шейки ( ). Одновременно к оси коленчатого вала приложим две противоположные по направлению, но равные по величине силы . Это соответствует параллельному переносу силы Т к оси коленчатого вала (метод Пуансо). При этом . Пара сил на плече r создает крутящий момент , направленный в сторону вращения коленчатого вала. Свободная сила суммируется с силой . В результате получим силу . Силы равны. Сила , в свою очередь, раскладывается на две составляющие и силу . Пара сил на плече h создает опрокидывающий момент равный по величине, но противоположный по направлению моменту .
6.3 Кривошипно-шатунный механизм
На двигателе установлен полноопорный, отлитый из чугуна, коленчатый вал с пятью коренными опорами и четырьмя шатунными шейками, Коренные и шатунные шейки вала не должны иметь трещин и задиров, Появившиеся на шейках вала глубокие риски или овальности более 0,05 мм шлифуют и шейки доводят до ремонтного размера, после чего тщательно промывают. Для повышения их износостойкости коренные и шатунные шейки коленчатого вала подвергаются закалке токами высокой частоты на глубину 2—3 мм. Наиболее допустимые овальность и конусность шатунных и коренных шеек после шлифования по 0,007 мм. Допустимое биение коренных шеек 0,02 мм, а отклонение осей шатунных шеек относительно коренных ±0,25 мм. Номинальные размеры шатунных шеек коленчатого вала составляют 47,814 и 47,834 мм, а коренных 50,775 и 50,795 мм. Причем преимущественно применяются номинальные размеры 47,834—0,020 и 50,795—0,020 мм. Допустимое уменьшение их толщины для различных ремонтных размеров составляет 0,25; 0,50; 0,75 и 1,0 мм.
Коренные и шатунные шейки соединяются между собой щеками с противовесами. Для подачи масла от коренных подшипников к шатунным в шейках и щеках просверлены каналы, выходные технологические отверстия которых закрыты заглушками.
Для очистки каналов удаляются заглушки, каналы промывают бензином и продувают сжатым воздухом, а при необходимости отверстия развертывают, после чего запрессовывают и крепят новые заглушки.
В торце задней коренной шейки коленчатого вала расточено отверстие Ø 34,992—34,960 мм под установку переднего шарикового подшипника ведущего вала коробки передач.
Коленчатый вал подвергают балансировке. Его равномерное вращение в коренных подшипниках обеспечивается отлитым из чугуна маховиком 18, который после раскручивания вала способствует преодолению сопротивления сжатию в цилиндрах двигателя, а также преодолению двигателем кратковременных перегрузок при трогании с места, торможении двигателем и т. д.
Крепление маховика к торцу фланца задней коренной шейки коленчатого вала осуществляется шестью болтами с общей стопорной шайбой, причем точная установка механизма сцепления на маховике обеспечивается двумя центровочными штифтами. Болты крепления маховика затягиваются приложением момента 7,2—8,9 кгс·м. Максимально допустимое отклонение поверхности опорного фланца маховика 18 относительно оси коленчатого вала на радиусе 34 мм — 0,025 мм. Допустимая непараллельность опорной поверхности ведомого диска сцепления относительно поверхности крепления к фланцу коленчатого вала и проверяется индикатором и должна быть не более 0,1 мм.
Стельной зубчатый обод маховика имеет 129 зубьев, поверхность которых закаляется токами высокой частоты, Перед напрессовкой обод нагревают в масле до температуры + 80о
С.
Проверка балансировки коленчатого вала производится на двух призмах на поверочной плите. Вал устанавливается вместе с маховиком и сцеплением.
Для обеспечения удлинения коленчатого вала при его нагреве и достаточной жесткости его крепления, а также сохранения герметичности сальников, которые располагаются на обоих концах коленчатого вала, на задней коренной шейке устанавливают упорные шайбы коренного подшипника.
Длина задней коренной шейки между упорными поверхностями шайб 16 должна быть в пределах 23,140—23,200 мм, а полная ширина задней коренной шейки составляет 27,975—28,025 мм. Толщина упорных шайб нормального размера 2,310—2,360 мм, а увеличенного (ремонтного) — 2,437—2,487 мм. При этом проверенный индикатором монтажный осевой зазор вала должен быть в пределах 0,055—0,265 мм, а предельный износ упорных шайб, характеризуемый осевым зазором вала,— 0,35 мм.
Коленчатый вал соединяется с четырьмя поршнями коваными стальными шатунами. Шатун передает усилие от поршня и является ответственной деталью кривошипно-шатунного механизма, преобразующего возвратно-поступательное движение поршня во вращательное движение коленчатого вала.
Нижняя головка шатуна, соединяемая с шатунной шейкой коленчатого вала, разъемная. Верхняя головка шатуна, соединяемая при помощи поршневого пальца с поршнем, неразъемная, цельная. В верхней части нижней головки шатуна имеется отверстие, через которое подается масло на зеркало цилиндра. Это происходит в момент совпадения отверстия с радиальным сверлением в шатунной шейке коленчатого вала.
Чтобы уменьшить потери на трение и износ шатунных шеек, применены тонкостенные вкладыши шатунного подшипника, стальная лента которых залита антифрикционным слоем из оловянисто-алюминиевого сплава (20% олова и 80% алюминия). Толщина вкладышей шатунных подшипников номинального размера 1,723—1,730 мм, причем преимущественно применяется размер 1,730—0,007 мм. Допустимое увеличение толщины вкладышей до ремонтных размеров составляет 0,25; 0,50; 0,75 и 1,0 мм. Диаметр расточки нижней головки шатуна под вкладыши 51,330 — 51,346 мм. Во избежание повреждения антифрикционного слоя вкладыши нельзя подвергать обработке, они не должны иметь рисок, задиров, отслоения заливки и повышенного износа. Монтажный зазор между шатунным подшипником и шейкой вала находится в пределах 0,036 — 0,086 мм, а предельный по износу — 0,10 мм. На нижней головке шатуна и его крышке выбивается номер цилиндра, по которому они подобраны в комплект с поршнем и поршневым пальцем.
Поршневой палец запрессовывают в верхнюю головку шатуна с прессовой посадкой при натяге 0,010—0,042 мм, а в бобышки поршня — со скользящей посадкой. Для этого- шатун нагревают до 240°С.
Диаметр расточки верхней головки шатуна 21,940—21,960 мм. Пальцы по диаметру и отверстия в бобышках поршней под пальцы сортируют на три категории. Диаметры поршневого пальца номинального размера находятся в пределах для 1-й категории 21,970—21,974 мм; 2-й категории 21,974—21,978 мм .и 3-й категории 21,978—21,982 мм. Для того чтобы при сборке различать пальцы по категориям, их торцы окрашивают соответственно в синий, зеленый или красный цвет. Ремонтные размеры поршневых пальцев увеличиваются на 0,2—0,5 мм. Диаметры отверстий в бобышках поршней номинального размера 1-й категории 21,982 — 21,986 мм; 2-й категории 21,986 — 21,990 мм и 3-й категории 21,990 — 21,994 мм.
При сборке поршня и пальца они соответственно подбираются по группам одной категории.
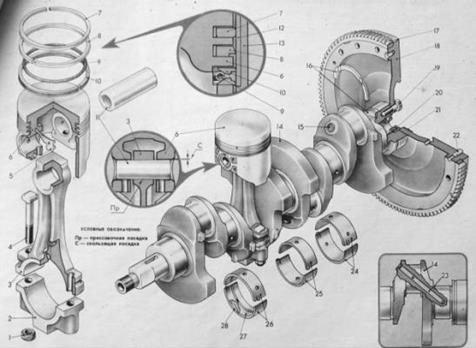
Рис. 12. Детали кривошипно-шатунного механизма
1 — гайка крепления крышки шатуна, 2 — крышка шатуна, 3 — шатун, 4 — шатунный болт, 5 — терморегулирующая пластина поршня, 6 — поршень, 7 — верхнее компрессионное поршневое кольцо, 8 — нижнее компрессионное поршневое кольцо, 9 — пружина маслосъемного кольца, 10 — маслосъемное поршневое кольцо,11 — поршневой палец, 12 — гильза цилиндра, 13 — цилиндр двигателя, 14 — пятиопорный коленчатый вал, 15 — заглушка масляного канала, 16 — упорные шайбы заднего коренного подшипника, 17 — зубчатый обод маховика (шестерня с прямым зубом— 129 зубьев), 18 — махойик коленчатого вала, 19 — болт крепления маховика, 20 — передний подшипник ведущего вала коробки передач, 21 — шайба маховика, 22 — центровочный штифт установки механизма сцепления, 23 — канал подачи смазки от коренного подшипника коленчатого вала к шатунному, 24 — вкладыши третьего центрального (среднего) коренного подшипника, 25 — вкладыши шатунного подшипника, 26 — вкладыши коренного подшипника, 27 — антифрикционный слой (сплав 20% олова и 80% алюминия), 28 — стальная лента; Пр — прессовая посадка, С — скользящая посадка
6.4 Механизм газораспределения
В двигателях ВАЗ выпуск отработавших газов из цилиндров и впуск свежей горючей смеси осуществляется механизмом газораспределения с верхним расположением впускных и выпускных клапанов и цепным приводом распределительного вала от коленчатого вала двигателя.
Чугунный литой пятиопорный вал установлен на головке цилиндров в алюминиевом литом корпусе подшипников. Он имеет пять опорных шеек и восемь кулачков для открытия клапанов. Высота впускных и выпускных кулачков должна быть 36,36 мм. Опорные шейки и кулачки распределительного вала закалены токами высокой частоты, а наружная поверхность вала фосфатирована. Корпус подшипников отлит из алюминиевого сплава и имеет закрытую сверху корытообразную форму с пятью перемычками, что обеспечивает повышение его жесткости. Корпус крепится к головке цилиндров девятью шпильками. Гайки шпилек затягиваются приложением момента 1,9—2,3 кгс·с. Причем затяжка осуществляется в последовательности от середины корпуса к его краям. В перемычках корпуса расточено пять отверстий, которые являются подшипниками под опорные шейки вала.
Фиксация распределительного вала от осевых перемещений осуществляется упорным фланцем, который крепится к корпусу подшипников и помещен в проточке передней опорной шейки вала. Смазка к опорным шейкам и кулачкам передается по каналу в центральной опоре, проточке в средней шейке и по осевому каналу в распределительном валу .
Привод распределительного вала от коленчатого вала осуществляется двухрядной роликовой цепью, которая имеет 114 звеньев с шагом 9,525 мм. Установленная на коленчатом валу ведущая звездочка имеет 19 зубьев, а на распределительном валу ведомая звездочка привода—38 зубьев. Кроме того, цепь осуществляет через звездочку (38 зубьев) привод топливного и масляного насосов и прерывателя-распределителя зажигания. Для предохранения цепи от вибраций и последующего соскакивания с зубьев звездочек и предотвращения повышенных износов на ее противоположной ветви установлен успокоитель с привулканизированной резиновой профильной накладкой. Покрытие башмака и успокоителя обладает высокой износостойкостью и низким коэффициентом трения, оно снижает шум работы цепного привода. Болт крепления башмака натяжателя цепи, одновременно являющийся осью поворота, затягивается приложением момента 3,8—4,7 кгс·м.
Натяжение цепи регулирует фиксирующая гайка натяжного устройства. Для регулировки ослабляют гайку натяжного устройства и проворачивают коленчатый вал на 1/2—3/4 оборота. При этом зажимной сухарь стержня разгружается и пружина, нажимая через шайбу на внутренний упор плунжера и заплечик стержня, автоматически устанавливает необходимое натяжение цепи. В случае появления шума и стуков в цепном приводе необходимо повторно отрегулировать натяжение цепи или устранить поломку башмака натяжного устройства, заедание штока плунжера или чрезмерный износ цепи, в связи с чем требуется ее замена.
Во время работы цепь должна вытягиваться не более чем на 4 мм. Цепь проверяют на приспособлении, имеющем два ролика диаметром по 31,72 + 0,01 мм, растягивая сначала с усилием 30 кгс, а потом 15 кгс. При этом замеряют расстояние между осями роликов. Для новой цепи двигателей ВАЗ-2101 и ВАЗ-21011 это расстояние должно быть равным 485,776—485,780 мм. Если цепь вытянулась до 489,9 мм, ее следует заменить.
Клапаны двигателя работают в тяжелых условиях. Впускные и выпускные клапаны имеют верхнее расположение и монтируются на головке цилиндров в один ряд. Впускной клапан изготовлен из хромоникельмолибденовой стали. Базовый диаметр головки клапана 36 мм, угол фаски головки клапана 45°30 ±5 . Наружный диаметр головки клапана 37±0,15 мм.
Диаметры стержней клапанов 8,000—7,985 мм и их высота 111±0,1 мм. Торцы стержней клапанов закалены, глубина слоя закалки 1, —3 мм. Оба клапана азотированы. Направляющие втулки 25 клапанов чугунные, имеют маслоотражательный колпачок 26 из маслостойкой резины с металлическим каркасом. Допустимый зазор между впускными и выпускными клапанами и их втулками находится соответственно в пределах 0,022—0,055 мм и 0,029—0,062 мм, а максимальный зазор должен быть не более 0,15 мм.
Каждый клапан устанавливается на двух пружинах — наружной и внутренней, которые соответственно имеют по шесть и шесть с половиной витков с внутренними диаметрами 25,5 и 17,6 мм при диаметрах проволоки 3,6 и 2,7 мм. Длина наружной пружины в свободном состоянии 50 мм, а внутренней — 39,2 мм.
Открытие клапана осуществляется стальным кованым рычагом. Пятка рычага опирается на шаровую головку регулировочного болта, который установлен в резьбовой втулке головки цилиндров. Рычаг прижимается к болту при помощи пружины. которая крепится к пластине. Пружина рычага имеет внутренний диаметр 20 мм, ее длина под нагрузкой 5,6—0,6 кгс составляет 43 мм.
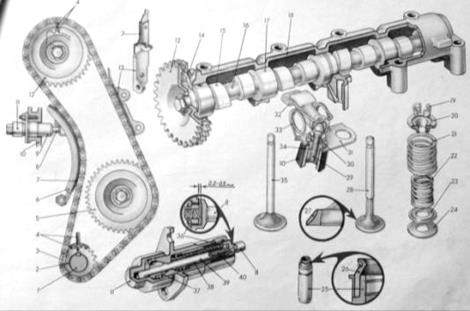
Рис. 13. Детали механизма газораспределения
1 — коленчатый вал, 2 — ведущая звездочка коленчатого вала, 3 — роликовая цепь привода, 4 — установочные метки, 5 — звездочка валика привода, 6 — башмак натяжного устройства, 7 — вулканизированная резиновая накладка, 8 — плунжер, 9 — корпус натяжного устройства, 10 — головка цилиндров, 11 — фиксирующая гайка, 12— ведомая звездочка распределительного вала, 13—успокоитель цепи, 14 — упорный фланец, 15 — кулачок распределительного вала, 16 — распределительный вал, 17 — опорная шейка вала, 18 — корпус подшипников распределительного вала, 19 — сухарь клапана, 20 — тарелка пружины клапана, 21 — наружная пружина клапана, 22 — внутренняя пружина клапана, 23 — опорная шайба внутренней пружины клапана, 24 — опорная шайба наружной пружины клапана, 25 — направляющая втулка клапана, 26 — маслоотражательный колпачок, 27 — жаростойкая наплавка, 28 — выпускной клапан, 29—регулировочный болт,30 — контргайка, 31 — пластина крепления пружины, 32 — рычаг привода клапана, 33 — пружина рычага, 34 — резьбовая втулка, 35 — впускной клапан, 36 — шайба пружины, 37 — зажимной сухарь стержня, 38 — пружина стержня, 39 — стержень натяжного устройства, 40 — пружина плунжера
6.5 Системы смазки и охлаждения
Масло в двигателе работает в разнообразных и сложных условиях. В камере сгорания масло подвергается воздействию высоких температур (до +2000°С), вследствие чего на деталях отлагается нагар, а часть масла сгорает, образуя золу и кокс. Вследствие отложения нагара двигатель перегревается, что приводит к самовоспламенению смеси, детонации, повышенным износам и прогоранию деталей.
В сопряжениях поршень—цилиндр тонкий слой масла нагревается до 200—300°С, вследствие чего на поршнях и кольцах образуются лаковые отложения. Отложение лаковых углеродистых веществ усиливается при износе колец и прорыве газов в картер. Для уменьшения лаковых отложений в масла добавляют моющие присадки.
В картере двигателя масло нагревается до 50—100°С. С повышением температуры масло окисляется, что усиливает его коррозионное действие, термический распад и сгорание.
При понижении температуры масла до +35°С в нем образуются осадки, представляющие собой липкую мазеобразную массу, которая отлагается на деталях двигателя. Осадкообразование увеличивается при попадании воды в масло, а также вследствие работы неподогретого двигателя.
Система смазки двигателя обеспечивает подачу масла к трущимся поверхностям деталей для уменьшения трения между ними. Масло также охлаждает детали и удаляет с их поверхности продукты износа. Кроме того, слой масла, образующийся у кромок поршневых колец, увеличивает герметичность между поршнем и зеркалом цилиндра.
В двигателе принята комбинированная система смазки: под давлением и разбрызгиванием.
Систему смазки двигателя составляют: масляный картер для запаса масла, шестеренчатый масляный насос с маслозаборным патрубком, полнопоточный фильтр тонкой очистки масла с фильтрующим элементом, масляные каналы в блоке цилиндров, головке цилиндров и в деталях двигателя, а также устройства и приспособления для контроля давления масла во время работы двигателя, сигнализации об аварийном падении давления масла, для проверки уровня масла, заправки и выпуска масла и вентиляции картера.
Масляный картер отштампован из листовой стали. Его устанавливают на уплотнительной прокладке, изготовленной из пробковой крошки на резиновой связке, толщиной 3 мм, крепят к блоку двенадцатью болтами, которые затягиваются с приложением момента в 0,52—0,84 кгс·м. Чтобы предотвратить расплескивание масла при движении по плохим дорогам, на крутых подъемах, при спуске и резком торможении, в картере 3 установлена перегородка. Для выпуска отработавшего масла к нижней части картера приварен фланец, в котором установлена резьбовая сливная пробка.
Масляный насос — шестеренчатый, с редукционным клапаном. Привод ведущего валика насоса осуществляется от коленчатого вала двигателя через цепную передачу, валик привода, звездочку валика привода и шестерню с винтовыми зубьями, изготовленную как одно целое с валиком. Осевое перемещение валика в блоке ограничивается установкой упорного фланца. В случае чрезмерного износа упорный фланец заменяют. Валик установлен и вращается в сталеалюминевых втулках, запрессованных в блок цилиндров двигателя.
Масло по каналам в блоке к деталям двигателя подается от насоса через фильтр по магистральному масляному каналу и подканалам к коренным подшипникам коленчатого вала.
Таким образом, в двигателе под давлением смазываются: подшипники коренных и шатунных шеек коленчатого вала, опоры и кулачки распределительного вала, опоры валика привода и втулка шестерни привода масляного насоса и прерывателя-распределителя. Цилиндры, поршни и поршневые кольца, поршневые пальцы, втулки и пружины клапанов, цепной привод распределительного вала, шестерня привода масляного насоса и прерывателя-распределителя, кулачок привода топливного насоса смазываются масляным туманом, который образовался в результате разбрызгивания масла.
Давление масла в двигателе контролируется при помощи электрического датчика. В прогретом двигателе при 5600 об/мин коленчатого вала и температуре 85°С нормальное давление масла должно быть в пределах 3,5...4,5 кгс/см2
. В случае падения давления масла до 0,4—0,8 кгс/см2
контрольная лампа с красным светофильтром, расположенная на щитке (комбинации) приборов, загорается и сигнализирует об аварийном падении давления масла.
Допускается временное загорание контрольной лампы падения давления масла в режиме холостого хода, а при увеличении частоты вращения оборотов коленчатого вала лампа должна гаснуть. В случае загорания лампы в рабочих режимах двигателя следует прекратить работу двигателя, так как давление масла недостаточно.
В связи с тем, что масляный манометр на двигателях ВАЗ-2101 не устанавливается, периодически следует проверять давление масла по контрольному манометру, штуцер которого завертывается в отверстие блока цилиндров вместо вывернутого датчика.
Емкость системы смазки (картера двигателя и масляного фильтра) — 3,75 л или 3,5 кг масла. Общая емкость картера, масляного фильтра, каналов и трубок составляет 4,2 л. Для периодической замены масла достаточно 3,75 л. Масло заливают через маслозаливную горловину, герметически закрытую пробкой. Эта пробка уплотняется резиновой прокладкой и удерживается плоской пружиной. Работа двигателя без пробки маслозаливной горловины недопустима, так как при этом в систему попадает значительное количество пыли и влаги, что повышает износ двигателя и при этом возрастает угар масла.
Уровень масла контролируется указателем (маслоизмерительным стержнем), на котором нанесены метки «МIN» и «МАХ».
Метка «МАХ» находится на расстоянии 61 мм от конца указателя. Расстояние между метками «МIN» и «МАХ» 16 мм.
Работа жидкостной, двухконтурной системы охлаждения двигателей ВАЗ закрытого типа с принудительной циркуляцией обеспечивается установкой водяного насоса, трубчатого радиатора, полнопоточного термостата с байпасным обводом, герметичной пробки и расширительного (конденсационного) бачка.
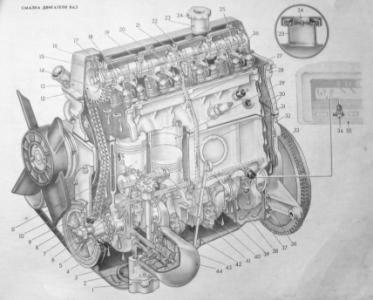
Рис. 14. Система смазки двигателя ВАЗ-2101
1 — шестеренчатый масляный насос, 2 — маслозаборный патрубок, 3 — масляный картер двигателя, 4 — ведущий валик масляного насоса, 5 — ведущая звездочка коленчатого вала, 6 — шестерня привода масляного насоса и прерывателя-распределителя, 7 — канал для подачи масла к подшипникам и кулачкам валика привода, 8 — передняя полость блока для стока избыточного масла и вентиляции картера, 9—валик привода прерывателя-распределителя зажигания, масляного и топливного насосов, 10—роликовая цепь привода, 11 — поршень, 12 — ведомая звездочка распределительного вала, 13 — крышка головки цилиндров, 14 — пружины клапана, 15 — упорный фланец распределительного вала,1 6 — отверстие в звездочке для смазки цепи, 17 — распределительный вал, 18 — масляный канал распределительного вала, 19 — канал для смазки опорной шейки распределительного вала, 20 — канал в стойке корпуса подшипников для подачи смазки к распределительному механизму, 21 — канавка для подачи масла в масляный канал распределительного вала, 22 — корпус подшипников распределительного вала, 23 — маслозаливная горловина двигателя, 24 — пробка маслозаливной горловины двигателя, 25 — канал для смазки кулачка, 26 — рычаг привода клапана, 27 — канал в головке цилиндров для подачи масла к распределительному механизму, 28 — головка цилиндров, 29 — цилиндр двигателя, 30 — задняя полость головки и блока цилиндров для стока избыточного масла и вентиляции картера, 31 —канал в блоке для подачи масла к распределительному механизму, 32 — блок цилиндров, 33 — пятиопорный коленчатый вал, 34 — контрольная лампа (с красным светофильтром) падения давления масла в двигателе до 0,4— 0,8 кгс/см2
, 35 — щиток (комбинация) приборов, 36 — датчик давления масла, 37 — канал для смазки коренного подшипника коленчатого вала, 38 — магистральный масляный канал, 39 — маслосъемное поршневое кольцо, 40 — масляный канал в валике привода, 41 — указатель для измерения уровня масла в картере двигателя, 42 — перегородка масляного картера, 43 — фильтрующий элемент, 44 — корпус полнопоточного фильтра тонкой очистки масла
Горение рабочей смеси в камерах сгорания цилиндров двигателя является сложным физико-химическим процессом, который сопровождается значительным выделением избыточного тепла. Тепловые процессы в двигателях ВАЗ усложняются с увеличением степени сжатия и числа оборотов коленчатого вала, причем эти двигатели имеют высокую литровую мощность. Перегрев двигателя приводит к самовоспламенению смеси в цилиндрах, заклиниванию поршней, выплавлению подшипников и поломкам деталей.
Таким образом, система охлаждения должна поддерживать постоянный оптимальный тепловой режим двигателя вне зависимости от условий эксплуатации.
В связи с тем, что байпасный клапан термостата закрыт и над термостатом остается небольшое количество воздуха, необходимо залить в расширительный бачок через горловину, закрываемую пробкой 6, дополнительное количество жидкости в 100—150 см3
сверх нормального уровня, который обычно находится на 3—4 см выше метки «МИН».
При горячем двигателе охлаждающая жидкость в системе охлаждения двигателя циркулирует по большому контуру — от нижнего бачка радиатора по шлангу она подается в корпус термостата и через канал, открытый основным клапаном, в корпус водяного насоса. Под действием крыльчатки водяного насоса, которая приводится в действие ременной передачей от шкива коленчатого вала, жидкость поступает в рубашку охлаждения блока цилиндров и рубашку охлаждения головки цилиндров, охлаждая цилиндры и камеры сгорания двигателя. Затем через выпускной патрубок и подводящий шланг жидкость поступает в верхний бачок радиатора.
При холодном двигателе основной клапан, термостата закрыт и байпасный (перепускной) клапан открыт. При этом охлаждающая жидкость циркулирует по малому контуру — от водяного насоса подается в рубашку охлаждения блока и головки цилиндров.
Термочувствительный элемент термостата состоит из стакана, внутри которого завальцована резиновая вставка и находится твердый наполнитель. В резиновой вставке размещен полированный стальной поршень, посаженный на резьбе в держателе и стопорящийся регулировочной гайкой. На стакане установлен основной клапан термостата, на который воздействует пружина, прижимая его к седлу держателя. При закрытом клапане перекрывается доступ жидкости от нижнего бачка 1 радиатора и входного патрубка. Сверху стакана в обойме установлен байпасный клапан, на который воздействует пружина.
Основной клапан находится в закрытом положении, пока температура охлаждающей жидкости ниже 80°С.
При дальнейшем повышении температуры жидкости твердый наполнитель расширяется, сжимает резиновую вставку и вытесняет поршень.
Таким образом, некоторое время при температуре в пределах 80—94°С циркуляция идет одновременно по двум контурам, а при нагреве жидкости до 94—96°С байпасный клапан полностью закроется и будет продолжаться циркуляция охлаждающей жидкости только по большому контуру. Под температурой, соответствующей началу открытия клапана, понимается такая температура, при которой ход основного клапана составит 0,1 мм. Эта температура должна находиться в пределах 80—83°С. Полный ход клапана при нагреве жидкости до 94—96°С должен быть не менее 8 мм. Регулировка термостата осуществляется перемещением поршня в резьбовом отверстии держателя, причем положение поршня фиксируется гайкой.
Для контроля нагрева охлаждающей жидкости в рубашке охлаждения головки цилиндров установлен электрический датчик, соединенный с указателем температуры охлаждающей жидкости, который находится на щитке приборов.
На шкале указателя имеются две контрольные риски, и красная зона. Положение стрелки у первой черной риски соответствует температуре нагрева жидкости до 30°С, у второй риски 21 — до 60°С. Если стрелка входит в красную зону шкалы, это свидетельствует о повышении температуры до 108°С. Расположение стрелки указателя в красной зоне сигнализирует о перегреве двигателя. Поэтому двигатель необходимо немедленно остановить.
При понижении температуры жидкости в верхнем бачке радиатора уменьшается ее объем и образуется разрежение. При этом открывается впускной (вентиляционный) клапан пробки и жидкость из расширительного бачка по шлангу поступает в верхний бачок радиатора. Чтобы слить охлаждающую жидкость, необходимо систему разгерметизировать. Для этого открывают пробку радиатора и выпускают жидкость через сливной кран нижнего бачка радиатора и сливной кран из рубашки охлаждения блока цилиндров.
В процессе эксплуатации может произойти перегрев двигателя, который возникает в результате следующих причин:
· утечки жидкости вследствие ослабления хомутов крепления шлангов, повреждения шлангов и патрубков, ослабления креплений и повреждения прокладок (особенно прокладки головки цилиндров), повреждения трубок и бачков радиатора и сливных кранов;
· засорения трубок радиатора, отложения накипи в системе охлаждения и загрязнения системы охлаждения;
· нарушения режима термостата и герметичности системы;
· понижения уровня жидкости.
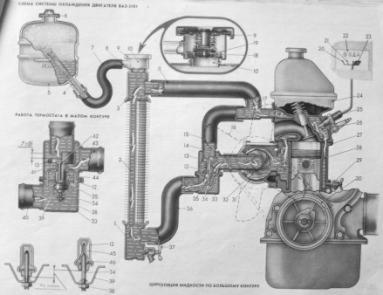
Рис. 15. Система охлаждения двигателя ВАЗ-2101
1 — нижний бачок радиатора, 2 — трубка радиатора, 3 — верхний бачок радиатора, 4 — трубка подачи кипящей жидкости (пара) в расширительный бачок, 5 — расширительный (конденсационный) бачок, 6 — пробка бачка, 7 — шланг подачи подогретой жидкости из радиатора к бачку, 8 — пароотводный патрубок, 9 — пробка радиатора, 10—заливная горловина радиатора, 11 — подводящий шланг радиатора, 11 — стакан, 13 — байпасный клапан, 14 — входной патрубок термостата, 15 — перепускной шланг термостата, 16 — вентилятор, 17 — выпускной патрубок системы охлаждения, 18 — выпускной (паровой) клапан пробки, 19 — впускной (вентиляционный) клапан пробки, 20 — контрольная риска нагрева жидкости до 30°С, 21 — контрольная риска нагрева жидкости до 60°С, 22 — указатель температуры охлаждающей жидкости в двигателе, 23 — красная зона перегрева двигателя (температура жидкости превышает 108°С), 24 — головка цилиндров, 25 — датчик температуры охлаждающей жидкости, 26 — рубашка охлаждения головки цилиндров, 27 — блок цилиндров, 28 — рубашка охлаждения блока цилиндров, 29 — сливной кран рубашки блока, 30 — шкив коленчатого вала для ременного привода вентилятора, водяного насоса и генератора, 31 —корпус водяного насоса, 32 — крыльчатка водяного насоса, 33 — корпус термостата, 34 — поршень, 35 — основной клапан термостата, 36 — отводящий шланг радиатора, 37 — сливной кран радиатора, 38 — регулировочная фиксирующая гайка термостата, 39 — держатель, 40 — входной патрубок, 41 — пружина байпасного клапана, 42 — обойма, 43 — выходной патрубок термостата, 44 — пружина основного клапана, 45 — наполнитель, 46 — резиновая вставка
ЗАКЛЮЧЕНИЕ
Эта работа была сделана с целью проведения анализа ДВС. Этот анализ был проведен, и в результате в работе было показано следующее:
· теоретические сведения об обратных термодинамических циклах, циклах тепловых двигателей и коэффициенте избытка воздуха;
· Степень сжатия – безразмерная величина, которая показывает, во сколько раз уменьшается объем рабочей смеси или воздуха, находящихся в цилиндре.
· Коэффициент избытка воздуха – это отношение действительного количества воздуха, подводимого в процессе горения, к теоретически необходимому.
· была проведена характеристика ДВС по различным признакам;
· ДВС состоят из механизмов и систем. Основными частями двигателей являются: кривошипно-шатунный и газораспределительный механизмы, а также системы питания, смазочная система и системы охлаждения и зажигания.
· характеристика поршневых двигателей;
· Индикаторная мощность двигателя, полезная работа, совершаемая газами в цилиндре поршневого двигателя в единицу времени; определяется путём обработки индикаторных диаграмм, полученных при испытании двигателя.
· дизельные двигатели;
· проведен расчет горения топлива;
· было показано устройство автомобиля ВАЗ-2101.
|