Курсовий проект
По курсу: “Основи проектування дільниць по відновленню деталей”
На тему: ”Проектування дільниці по відновленню кулачків розподільчого валу автомобіля ЗІЛ – 130”
Одеський національний політехнічний університет
Факультет – ІПТДМ
Кафедра – ТКМіМ
Спеціальність – 7,092303 “Технологія і устаткування відновлення та підвищення зносостійкості машин та конструкцій ”
Затверджую:
Зав.каф________
проф. Дерев’янченко О.Г.
_________________________ 2010 р.
Завдання на курсовий проект
студентові: Носенко Віталію Сергійовичу
1.Тема проекту: Проектування дільниці по відновленню кулачків розподільчого валу автомобіля ЗІЛ – 130.
2.Термін здачі студентом закінченого проекту:_________________
3.Зміст розрахунково-пояснювальної записки
1.Аналіз номенклатури деталей, належних відновленню. Вибір деталі
2.Розробка технології відновлення деталі.
3.Вибір основного допоміжного обладнання. Розрахунок числа одиниць устаткування і робочих місць.
4.Компоновка устаткування і робочих місць на ділянці відновлення.
5.Економіка, Екологія. Охорона праці.
4.Планування ділянки по відновленню.
Завдання видав ”__” _____________2010 р. __________________
Завдання отримав ”__” _____________2010 р. __________________
Зміст
Вступ. 4
1. Загальний розділ. 6
1.1 Опис деталі та умов її роботи. 6
1.2 Матеріал деталі 10
1.3 Принцип процессу надзвукового плазмового напилення. 10
2. Спеціальна частина. 13
2.1 Опис базової установки надзвукового плазмового напилення. 13
2.2 Вибір необхідного порошку. 16
2.3 Необхідне обладнання, інструмент, пристрої 17
3. Технологічначастина. 18
3.1 Проектування технологічного процесу відновлення. 18
3.2 Розробка маршрутної технології 18
3.3 Підготовка порошків. 20
3.4 Підготовка поверхні 20
3.5 Механічна обробка деталі 25
3.6 Контроль якості поверхні 27
4. Економічний розділ. 31
4.1 Розрахунок обсягу робіт. 31
4.2 Режим роботи та фонди часу. 31
4.3 Такт виробництва. 32
4.4 Визначення кількості працюючих на кожному робочому місці 33
4.5 Розрахунок кількості робочих постів. 33
4.6 Розрахунок кількості обладнання. 34
4.7 Розрахунок виробничих площ.. 37
4.8 Розробка та обгрунтування схем планування обладнання. 38
4.9 Розрахунок порошкової суміші 38
5. Економічні витрати. 42
5.1 Обгрунтування вибору форми оплати праці та умов преміювання. 42
5.2 Кошторис витрат і калькуляція собівартості 42
5.3 Розрахунок фонду заробітної плати з нарахуваннями в соціальні фонди 42
5.4 Економічний прибуток. 46
5.5 Економічна ефективність. 47
6. Охорона праці 48
6.1 Стан умов праці при роботі по відновленню чавунних розподілвалів. 49
6.2 Аналіз шкідливих і небезпечних факторів шліфувального відділення. 50
6.3 Вимоги нормативно-технічної документації з охорони праці 51
6.4 Заходи щодо захисту робітників від небезпечних і шкідливих факторів 52
6.5 Техніка безпеки. 54
Висновок. 56
Список використаних джерел. 57
Вступ
У задоволенні постійно зростаючих потреб народного господарства нашої країни в перевезеннях пасажирів і вантажів автомобільний транспорт займає провідне місце.
Рішення задач по подальшому розвитку автомобільного транспорту забезпечується постійним збільшенням виробництва автомобілів. Одним з резервів збільшення автомобільного парку країни є ремонт автомобілів, тому його розвитку і вдосконалення в нашій країні приділяється велика увага.
У процесі експлуатації автомобіля його надійність та інші властивості поступово знижуються внаслідок зношування деталей, а також корозії і втоми матеріалу, з якого вони виготовлені. В автомобілі з'являються різні несправності, які усуваються при технічному обслуговуванні та ремонті.
При надходженні автомобілів в капітальний ремонт велика кількість їх деталей в результаті зношування, втоми матеріалу, механічних і корозійних пошкоджень втрачає працездатність.Проте лише деякі з цих деталей, найбільш прості й недорогі у виготовленні, втрачають працездатність повністю і вимагають заміни. Більшість деталей має залишковий ресурс і може бути використане повторно після проведення порівняно невеликого обсягу робіт з їх відновлення.
Відновлення деталей має велике народногосподарське значення. Вартість відновлення деталей значно нижче вартості їх виготовлення. Витрати на відновлення деталей, навіть в умовах сучасних авторемонтних підприємств, становлять залежно від конструктивних особливостей і ступеня зношеності деталей ось 10% до 50% от вартості нових деталей. При цьому, чим складніше деталь і, отже, чим дорожче вона у виготовленні, тим нижче витрати на її відновлення.
Економічна ефективність відновлення деталей у порівнянні з їх виготовленням пояснюється низкою причин. При відновленні деталей значно скорочуються витрати на матеріали і повністю виключаються витрати, пов'язані з одержанням заготовок. За даними досліджень, витрати на одержання заготовок при виготовленні деталей на автобудівельних підприємствах становлять 70-75% от їх собівартості, а при відновленні деталей вони коливаються в межах 1-12% в залежності ось способу відновлення.
При відновленні деталей скорочуються також витрати, пов'язані з обробкою деталей, тому що при цьому обробляються не всі деталі поверхні деталей, а лише те, які мають дефекти.
Відновлення деталей є одним з основних джерел підвищення економічної ефективності авторемонтного виробництва. Відомо, що основною статтею витрат, з яких складається собівартість капітального ремонту автомобілів, є витрати на придбання запасних частин. Ці витрати в даний час складають 40-60% від собівартості капітального ремонту автомобіля.
Їх можна значно скоротити за рахунок розширення відновлення деталей. Значення відновлення деталей полягає також у тому, що воно дозволяє зменшити потреби народного господарства у виробництві нових запасних частин.
1. Загальний розділ
1.1 Опис деталі та умов її роботи
Без процесу газообміну робота двигуна внутрішнього згорання неможлива. Залежно від порядку роботи циліндрів двигуна в строго певні моменти часу повинні відкриватися впускні клапани, пропускаючи всередину циліндрів горючу суміш або повітря, якщо наш мотор - дизель або з безпосереднім уприскуванням бензину.
Далі впускний клапан зобов'язаний закритися, щоб в умовах повної герметичності в циліндрі відбулося згорання. Потім з циліндра необхідно видалити відпрацьовані гази, а для цього знову-таки в певний момент часу потрібно відкрити випускний клапан. Нарешті, коли відпрацьовані гази "вилетіли в трубу", треба повернути випускний клапан в закрите положення. І так по кругу, поки двигун не буде заглушений.
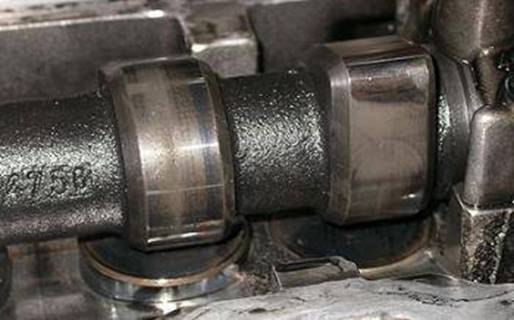
Фази, зони, сектора
Моменти відкриття і закриття клапанів, виражені в градусах кута повороту колінчастого валу, називаються фазами газорозподілу. Однак управляє здійсненням фаз газорозподілу зовсім не колінчастий, а розподільний вал.
При цьому взаємне кутове розташування кулачків на распредвали залежить від порядку роботи циліндрів і загальної діаграми фаз газорозподілу двигуна. А ось виконання фаз газорозподілу кожним окремо взятим клапаном забезпечується геометричним профілем кулачка.Існує також прямий взаємозв'язок між профілем, висотою і швидкістю підйому клапана над сідлом, від яких залежить величина прохідного перерізу відповідного отвори в голівці циліндрів і обсяг потоку свіжого заряду і відпрацьованих газів.
У перерізі кулачок нагадує грушу.Є округлий потилицю і загострена край. Але наука виділяє на профілі кулачка чотири основні зони. Перша - той самий округлий потилицю, який називається сектором відпочинку. Що робить клапан, коли проти його штовхача проходить сектор відпочинку кулачка?Зрозуміло, "відпочиває", а саме: закритий і охолоджується, віддаючи голівці циліндрів тепло через притулену до сідла тарілку. Особливо важлива тривалість відпочинку для випускних клапанів, тарілки яких омиваються розпеченими відпрацьованими газами.
Наступна зона на кулачку - сектор прискорення.Від його профілю залежить, як швидко клапан піднімається. Чим швидше це відбувається, наприклад з впускним клапаном, тим краще для наповнення циліндра свіжим зарядом. Чи означає це ж, що, змінюючи профіль сектора прискорення впускного клапана, можна впливати на показники потужності двигуна показники, ніж, до речі, і користуються при проектуванні так звані спортивні розпредвалів. Однак позичково зі швидкістю підйому клапана на кулачок наростають навантаження від вужчому клапанної пружини. А навантаження ці, треба сказати, чималі - 2000 Н / кв. мм і вище. Тому профіль сектора прискорення - це завжди компроміс між бажанням отримати більше потужності і необхідністю не нашкодити довговічності.
Третя зона називається вершиною. Коли кулачок працює вершиною, клапан відкритий повністю. Ось тільки довго тримати його в такому положенні небажано. Клапан повинен ще встигнути закритися в термін, і необхідно, щоб посадка тарілки клапана в сідло була м'якою. Багаторазово ж повторювані удари ведуть до появи мікротріщин на фаску клапана і сідлі. Та й сили, що діють на кулачок з боку штовхача, в зоні вершини стають максимальними. Тому форма вершини кулачка, втім, як і зони посадки - останньої з чотирьох частин профілю, також є результатом деякого компромісу з довговічністю.
Поєднання компромісів - кулачок з профілем, що забезпечує найбільшу пропускну здатність клапана при найменших з можливих прискорень його підйому і посадки. Розподільні вали з такими кулачками, званими ненаголошених, використовуються в більшості автомобільних двигунів. Щоправда, в дійсності кулачок працює без ударів, тільки коли його поверхню постійно ковзає, не відриваючись від поверхні штовхача.
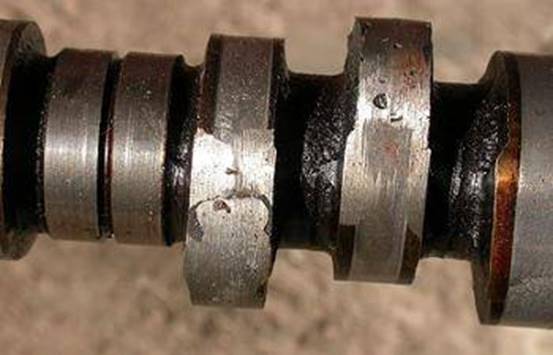
Як зношуються кулачки
Оскільки за умовами роботи чотиритактного двигуна потрібно, щоб за кожні два оберти колінчастого вала клапани тільки один раз відкривалися і закривалися, розподільчий вал кінематично пов'язаний з колінвалом так, що обертається з частотою в два рази меншою, ніж частота обертання колінвала.З точки зору зменшення зношування це добре.
Тим не менше зношування кулачків залишається основною причиною виходу розподілвалів з ладу. Сприяють ж зносу збільшені контактні напруги, які доводиться випробовувати кулачки.Але з якого дива величина контактних напруг може виявитися вище розрахункової?
Згадаймо, що в клапанному механізмі існує так званий теплової зазор. Він покликаний компенсувати подовження стрижня клапана через нагрівання. Якщо тепловий зазор давно не регулювався і тому великий, то між сектором відпочинку кулачка і штовхачем відсутній контакт, через що при подальшому обертанні кулачок не плавно натискає на штовхач, а з силою б'є по ньому боковою поверхнею. Зовнішній прояв таких повторюваних ударів - характерний шум, що виникатиме з-під клапанної кришки. Ділянка переходу сектора відпочинку в сектор прискорення - другий після вершини з найбільш уразливих на кулачку.При збільшеному тепловому зазорі перші мікроразрушенія на кулачку можуть з'явитися в цьому місці, а потім процес прогресує.
Гідрокомпенсатори теплових зазорів, що представляють собою, по суті, два поршенька, розсовуємо тиском масла, вирішують цю проблему, але тільки до тих пір, поки самі залишаються справними. А підклинює гидротолкателі можуть при засміченні системи змащення й наявності в олії сторонніх включень. При заклинюванні гідроштовхачем найбільше дістається вершині кулачки.
1.2 Матеріал деталі
Кулачки розподільчого валу виготовляють із чугуна твердістю 55-62 HRC, шороховатість 8-го класу.
Чавун - сплав заліза з вуглецем (змістом звичайно більш 2,14%), що характеризується евтектічесім перетворенням. Вуглець у чавуні може міститися у вигляді цементиту і графіту. Залежно від форми графіту та кількості цементиту, виділяють: білий, сірий, ковкий і високоміцні чавуни.Чавуни містять постійні домішки (Si, Mn, S, P), а в деяких випадках також легуючі елементи (Cr, Ni, V, Al та ін). Як правило, чавун крихкий.
1.3 Принцип процесу надзвукового плазмового напилення
Зупинимося на деяких характерних рисах плазмового напилювання з використанням надзвукових струменів, оскільки цей метод є найбільш передовим і має ряд істотних переваг. Додавання метану або пропан-бутану до повітря, використання газоповітряної суміші в якості плазмо утворюючого газу, робить високотемпературний ділянку плазмового струменя, в якому відбувається нагрівання й прискорення частинок порошку, більш протяжним, а профіль температур і швидкостей більше заповненим. Це відіграє вирішальну роль у поліпшенні якості покриттів і підвищення продуктивності процесу напилювання. Характер траєкторії часток порошку при бічному вдув в зносячи плазмову струмінь залежить від градієнта швидкості в ній. Висока швидкісна і температурна нерівномірність по перерізу порошкового потоку у плазмовій струмені при подачі під зріз сопла плазматрона обумовлена властивостями плазмового струменя. Траєкторія польоту частинок визначається безліччю факторів. Профіль швидкостей і температур для плазми продуктів згорання характеризується меншою неоднорідністю, тому порошковий потік глибше проникає в струмінь, відбувається більш рівномірний нагрів всіх частинок, незалежно від траєкторії їх польоту. У плазмі продуктів згоряння (незалежно від траєкторії польоту, розмірів і форми частинок) аеродинамічний і теплове вплив на неї більш рівномірно.
Висока тепловіддача до часток порошку і кращі розгінні властивості плазми продуктів згорання в порівнянні з повітряного або азотної вимагають коректування часу перебування частинок порошку в високотемпературної зоні, оптимальний нагрів забезпечується при більш високих швидкостях. Для цього необхідно збільшувати витрату газу або зменшувати діаметр сопла. Підвищена швидкість частинок і рівномірний їх прогрів по всьому перетину забезпечують підвищення щільності і міцності зчеплення покриття з основою.
Профіль швидкостей і температур частинок у поперечному перерізі плями напилювання в момент контакту з основою характеризується меншою неоднорідністю в порівнянні з напилюванням в інертних газах. Тому при відносному переміщенні плазматрона і деталі на поверхню останньої завжди потрапляють частинки з високим енергетичним рівнем. Завдяки цьому периферійні частинки, що беруть участь у формуванні покриття, не так погіршують якість, що сприяє більш сприятливому розподілу міцності зчеплення та пористості покриття по плямі напилювання.
У плазмі продуктів згорання периферійні частинки досягають основи з більш високим енергетичним рівнем. Це особливо важливо при формуванні першого осадження моношару покриття, відповідального за адгезійну міцність зчеплення. Поліпшуються також інтегральні показники якості покриттів.
Вивчено вплив різних факторів (витрат порошку; умов напилювання; зносу електродів) при надзвуковому газоповітряної плазмовому напилюванні порошків із суттєво різними теплофізичними властивостями: алюмінієвого сплаву і оксиду алюмінію - на якість покриттів.
Переваги технології напилювання:
1. Можливість нанесення покриттів на вироби, виготовлені практично з будь-якого матеріалу.
2. Можливість напилювання різних матеріалів за допомогою одного і того ж обладнання.
3. Відсутність обмежень щодо розміру оброблюваних виробів. Покриття можна напилити як на велику площу, так і на обмежені ділянки великих виробів.
4. Можливість застосування для збільшення розмірів деталі (відновлення та ремонт зношених деталей машин).
5.Відносна простота конструкції обладнання для напилювання, його мала маса, нескладність експлуатації обладнання для напилювання, можливість швидко і легко переміщатися.
6. Можливість широкого вибору матеріалів для напилювання.
7. Невелика деформація виробів під впливом напилювання. Багато способи поверхневої обробки виробу вимагають нагрівання до високої температури всього виробу або значної його частини, що часто стає причиною його деформації.
8. Можливість використання напилювання для виготовлення деталей машин різної форми.
9.Простота технологічних операцій напилювання, відносно невелика трудомісткість, висока продуктивність нанесення покриття.
10.Не потрібно спеціальної дорогої обробки (очищення) продуктів, що забруднюють навколишнє середовище, на відміну від засобів очищення і нейтралізації при гальванічних видах обробки виробів.
Напилювання має відмітні особливості, знання яких необхідно для правильного вибору технології нанесення покриттів для кожного конкретного випадку. Для вибору оптимального способу нанесення покриття необхідно враховувати форму і розміри виробів;вимоги, що пред'являються до точності нанесення покриття, його експлуатаційними властивостями; витрати на основне і допоміжне устаткування, наплавочні матеріали і гази, на попередню і остаточну обробку покриттів;умови праці та інші фактори виробничого і соціального характеру.
2. Спеціальна частина
2.1 Опис базової установки надзвукового плазмового напилення
Основні етапи у вдосконаленні апаратури головним чином пов'язані з розробкою і реалізацією нових підходів, а в останні роки з її оснащенням вимірювальними і керуючими цифровими пристроями. НВП ТОПАС розробило і освоїло випуск ряду нових типів наукомісткої плазмової апаратури, реалізувало нові технології. На початку 90-х років Інститутом газу НАН України та Інститут електрозварювання ім. Є.О.Патона НАН України була розроблена і підготовлена до промислової реалізації нова апаратура надзвукового високопродуктивного плазмового напилення потужністю 160 кВт «КИЇВ-С». Великий обсяг випробувань показав, що ця апаратура гарантує найкращу якість газотермічних покриттів, економічна, надійна і доступна для широкого споживача. Однак сьогодні ця передова розробка в нашій країні ще не затребувана.
Представлена робота є спробою авторів зберегти даний напрямок і надати йому нову практичну значимість. Для реалізації цієї ідеї розроблено ряд надзвукових плазмотронів і апаратурних комплектів для напилювання покриттів в плазмі продуктів згоряння вуглеводневого газу з повітрям потужністю 10 ... 40 ... 80 ... 160 кВт. У цих плазмотронах реалізований новий підхід формування дальнього слабо недоросширенного надзвукового плазмового струменя. Зниження розсіювання потужності струменя здійснюється придушенням турбулентності в прикордонному шарі за рахунок використання тонких ефектів динаміки плазми. Як зазначалося вище, основні особливості поведінки плазми молекулярного газу в нерівно важних умовах пов'язані з коливно-поступальною нерівноважністю, яка може досягати декількох тисяч градусів. При цьому можливі умови, коли ефект другої в'язкості звертається (друга чи об'ємна в'язкість стає негативною), що призводить не до загасання звуку, який генерується власної турбулентністю, а до його наростання. Ефективне посилення звуку за рахунок звернення другий в'язкості відбувається на частотах 10-100 кГц. Інтенсивні звукові хвилі, що виникають і посилюються на одній ділянці течії, а поглинають на іншому (нижче по потоку), можуть значно вплинути на гідродинамічні параметри течії та електрофізичні властивості розряду. Генерується при цьому надзвуковий плазмовий струмінь характеризується більше (на 30%) високими розгінної і гріє здібностями. При швидкості частинок близько 600 м / с забезпечується проплавлення всіх тугоплавких матеріалів.

Рис. 1. Функціональна схема плазмової установки: ПУ – пульт керування, ПР – плазмовий розпилювач.
Основними елементами всіх плазмових установок є: плазмотрон (плазмовий розпилювач), джерело живлення дуги, система газоживлення, дозатор-живильник і вся система подачі розпалюваного матеріалу, система охолодження і пульт управління. Крім цих основних елементів до кожної установки надають пристрої, які приводять в рух деталь, гасять шуми, система вентиляції.

Рис. 2. Блок-схема установки до плазмового напилення: 1 - система газопостачання; 2 - механізм подачі напилювального матеріалу; 3 - механізм пересування плазмотрона; 4 - розпилювач; 5 - виріб, на поверхню якого наносять покриття, і система його руху; 6 - пульт керування; 7 - джерело живлення дуги.
Для газо термічного напилення в виробничих умовах необхідно здійснювати взаємне переміщення пальника і деталі. Параметри цього переміщення – швидкість, дистанція напилення (відстань від пальника до деталі), кут зустрічі напилювального потоку з поверхнею, яку обробляємо – повинні витримуватися у процесі напилення і точно відтворюватися від деталі до деталі. Для забезпечення цих вимог використовують спеціальну технологічну оснастку.
ТОПАС-40
Установка плазмового напилення потужністю 40 кВт комплектується плазматрона в ручному і машинному виконаннях. Плазматрона виконані з одиночною МЕВ і рекуперативним охолодженням, можуть працювати на до-і надзвуковому режимах. Призначена для напилювання покриттів на зовнішні і внутрішні поверхні. Можуть використовуватися порошкові і дротяні матеріали.
Плазмообразуючий газ - повітря+метан
Напруга мережі, В - 3х380 (180)
Робоча напруга, В - 140-180
Робочий струм, А - 100-250
Витрата суміші, м3/год - 3-10
ККД плазматрон - 90
Продуктивність напилювання, кг / год:
метали - 10
кераміка (Аl2О3) - 5
2.2 Вибір необхідного порошку
У більшості випадків напилювані матеріали можуть поставлятися у вигляді порошків. При напилюванні порошку можна отримати покриття навіть у разі неповного проплавлення нагрівається порошку. Напилювання дроту або прутка неможливо без повного розплавлення напилюваного матеріалу. Тому в порівнянні з порошковим напилюванням при пруткової або дротовому напилюванні утворюються частинки на початковому етапі руху мають більш високу температуру і швидкість, що забезпечує і більш високу енергію зіткнення частинок з поверхнею і підвищує міцність зчеплення покриття з основою. Однак при дротовому або прутковому напилюванні утворюються розплавлені частинки швидко охолоджуються. При порошковому ж напилюванні високотемпературна область полум'я в порівнянні з дротяним має велику протяжність, що дозволяє ефективно використовувати цю область для нагрівання що летять частинок.
Основною перевагою порошкового напилювання є низька вартість і проста технологія отримання порошків металів, сплавів і хімічних сполук, з яких неможливо виготовити дріт або пруток звичайними методами з огляду на їх високої твердості та крихкості.
Частинки порошків повинні мати сферичну або комкоподібну форму. Такі порошки мають гарну сипучості, що дозволяє досить просто регулювати і підтримувати витрата напилюваного матеріалу.
Для напилювання в основному використовують порошок з розміром частинок 40-100 мкм. При зберіганні і використанні необхідно звертати увагу на те, щоб порошки були сухими.
Напилювання покриттів з самофлюсуючих сплавів і подальше їх проплавлення дозволяє одержувати покриття без пористосі. Самофлюсуючі сплави являють собою сплави на основі нікелю, нікелю та хрому або кобальту, що містять добавки бору та кремнію.
Назва напилюваного порошку СНГН-55. Хімічний склад порошку: Ni - основа, B - 3.2-4.0, C - 0.7-1.0, Si - 3.8-4.5, Cr - 14-17, Fe ≤ 3, Mn - 1.0.Твердість одержуваного покриття 53-58 HRC. Діаметр порошинки d - 20-50 мкм.
Для відновлення кулачка розподільного валу автомобіля ЗІЛ-130 я вибрав цей порошок так він дає можливість отримати покриття, що володіє зносостійкістю, ерозійної стійкістю, корозійною стійкістю, стійкістю до окислення при високих температурах і т.д.
2.3 Необхідне обладнання, інструмент, пристрої
Установки для плазмового напилення включають такі основні елементи: інструмент для плазмового напилення (плазмотрон); джерело енергопостачання; систему газопостачання; систему водяного охолодження, систему регулювання параметрів робочого режиму, систему подачі напилюваного матеріалу (порошку чи дроту), мийна мишина, сушильний шкаф, абразивна установка, копіювально-шліфувальний станок. Крім того, вони можуть включати робочу камеру з системою вентиляції і пиловловлення, засоби механізації переміщення плазмотрона і деталі.
3. Технологічначастина
3.1 Проектування технологічного процесу відновлення
Використовуємо операції, пов'язані тільки з відновленням кулачків, тобто часткове відновлення кулачків розподільного валу ЗІЛ-130.
3.2 Розробка маршрутної технології
1.Очисна.
2.Контрольно-дефекточна.
3.Термічна.
4.Абразивно-шліфовальна.
5.Напилювальна.
6.Копіювально-шліфовальна.
7.Контрольна
1. Очисна.
Очистити вал і промити його в розчині миючого засобу МС-8 концентрації 20 г / л і температурою 75-80 0 С.
Наявність смолистих відкладень, забруднення і мастила на поверхні вала не допускаються.
Машина для очищення: SIMPLEX 120.
Розряд роботи-2. Трудомісткість-5 хв.
2. Контрольно-дефекточна.
Провести ретельний візуальний огляд. Визначити геометричні параметри валу - виміряти інструментом.
Визначити тріщини магнітним дефектоскопом МД-50.
Режими: ток намагнічування 1500 А, метод намагнічування - циркулярний, характер струму - миттєвий.
Умови: тріщини більше 5 мм не допускаються.
Розряд роботи - 4. Трудомісткість- 8,5 хв.
3.Термічна.
Помістити вал в піч при температурі 400-4500 С і витримувати протягом 30 хвилин.
Електропіч шахтна СШО 10.10/10.
Розряд роботи-1
4.Абразивно-шліфовальна.
Шліфовати під напилювання в закритій абразивній установці, забезпечивши шороховатість поверхні Ra 2 мкм.
Обладняння: абразивна установка HSP-20.
Розряд роботи - 4. Трудомісткість - 20 хв.
5.Напилювальна.
Закріпити розподілвал в спеціальний валотримач, який забезпече потрібну форму положення при напилюванні, а обертаючись – може швидко перевести плазматрон на слідуючий кулачок. Напилювати профіль кулачка.
Обладняння: напилювальна установка Топас – 40.
Розряд роботи - 3. Трудомісткість – 25 хв.
6.Копіювально-шліфовальна.
Помістити вал в копіювально-шліфувальний верстат і на протязі 18 хв. він автоматично прошліфує профілі кулачків.
Обладняння: копіювально-шліфовальний верстат ХШ3-33н.
Розряд роботи – 1.
7.Контрольна.
Провести контроль згідно технічним вимогам на видачу розподільчого валу з відновлення.
Розряд роботи - 4. Трудомісткість - 8 хв.
3.3 Підготовка порошків
Для визначення розмірів частинок часто використовують ситовий аналіз (ГОСТ 3584-73). Набір сит з розміром у світлі 0,05; 0,063; 0,1 і 0,125 мм дозволяє простим способом оцінити гранулометричний склад порошку. Існують й інші способи визначення гранулометричного складу порошків, особливо дрібнодисперсних з розміром частинок менше 40мкм.
Обов'язковою операцією при підготовці є сушка або прожарювання порошку, при цьому поліпшується його сипучість, зменшується кількість пов'язаної або адсорбованому вологи, органічних забруднень. Для сушіння порошку температура становить 120-1500 С .При більш високих температурах спостерігається інтенсивне окислення порошку. Для сушіння металевих порошків і прожарювання використовують металеві дроту з товщиною засипки 5-10 мм. Час обробки вибирають в межах 2-5 годин. Сушку та прожарювання порошків здійснюють у печах або шафах.
Готуючи порошки для напилювання, корисно перевірити їх сипкість. Для цього використовують методи, прийняті в порошковій металургії.
3.4 Підготовка поверхні
Якісна обробка поверхні виробу перед напилюванням багато в чому гарантує високу, адгезійну міцність покриттів. Поверхня виробу, що надходить на напилювання, звичайно містить різні види забруднень:
1. фізичні чи механічні забруднення. До них відносяться пил, ворсинки, абразивні частинки та ін. Забруднення хімічно не пов’язані з поверхнею.
2. органічні забруднення у вигляді адсорбованих тонких і товстих плівок - різноманітні мастила, віск, парафін.
3. забруднення, розчинені у воді: солі, кислоти, луги та ін.
4. хімічно пов’язані забруднення. До них відносять: оксидні, нітридні, сульфідні та інші сполуки.
5. газоподібні забруднення, адсорбовані поверхнею. Попередні оцінки показують існування на поверхні виробу біля 3 -5мкг/мм2 органічних забруднень, і товщина оксидної плівки 3 -З0нм.
Особливо погано впливають органічні забруднення. Суттєвий їх вплив проявляється вже при вмісті 1мкг/мм2 .
Стійкі оксидні плівки товщиною менш 0,5мк суттєво не впливають на контактну температуру. Разом з тим енергія активації оксидних плівок вища за енергію активації відповідних металів. На адгезійну міцність покриття впливають плівки товщиною більше 10 -15нм.
Підготування поверхні перед напилюванням має слідуючу мету: видалення жирових та інших видів забруднень; видалення оксидних плівок при підготовці металевих, металідних або металоїдних поверхонь.
Поряд з цим необхідно активувати напилювану поверхню, тобто вивести її зі стану термодинамічної рівноваги. Для цього необхідне розірвати зв'язки між поверхневими і сторонніми атомами твердого тіла, підвищити енергію поверхневих атомів до різня забезпечення їхньої хімічної взаємодії з напилюваними частинками. При напилюванні покриттів на активовану поверхню необхідно враховувати можливість швидкої втрати придбаних властивостей. Хімічна адсорбція атмосферних газів відновлює звільнені міжатомні зв'язки.
Активація напилюваної поверхні значно підсилюється при утворенні в поверхневому шарі структурних дефектів. При цьому не тільки зростає енергія атомів, але і збільшується швидкість їхньої дифузії в процесі хімічної взаємодії.
Підготовку поверхні треба проводити з таким розрахунки, щоб поряд з очищенням здійснювався і процес її активації. Вибір способу підготовки залежить від матеріалу напилюваного виробу і його конструкції Необхідно враховувати у виробі наявність тонкостінних елементів, У цьому випадку активні зрушені деформації в поверхневих шарах приведуть до викривлення геометрії виробу.
Знежирення напилюваних виробів
Знежирення має на меті видалення різного роду жирових забруднень. Разом з попереднім і наступним промиваннями видаляється більшість різних забруднень, хімічно не зв'язаних з поверхнею виробу. Знежиренню піддають практично всі напилюванні вироби. Обробку ведуть у ваннах чи застосовують місцеве знежирення, за допомогою протирання дрантям чи бавовняними серветками.
Рекомендуються багато складів ванн і режимів обробки. Зокрема:
1)35 -40г/л тринатрійфосфату;
2) 40 -45г/л кальцинованої соди.
Температура ванни 75 -85°С; час знежирення 20 -25хв. Потім промивають гарячою І холодною проточною водою з наступним сушінням стисненим повітрям, підігрітим до температури 50°С.
Широке поширення одержало знежирення у ваннах з органічними розчинниками, наприклад, "Ломбид - 315" та ін. Для місцевого знежирення застосовують більш сильні розчинники: бензин, уайт - спірит, ацетон тощо.
Очищення напилюваних поверхонь від хімічних сполук
Застосовують різні способи очищення: абразивне - струминне; травлення; впливом ультразвуку; тліючими і дуговими розрядами; НВЧ- полем та
1) Абразивно - струминне очищення. Належить до найбільш розповсюдженого методу підготовки поверхні при газотермічних способах напилення. Обробку поверхні проводять струменем стиснутого повітря з абразивними частинками в захисних камерах. Процес здійснюють як виучку, так і механізовано. Як абразивні частинки використовують електрокорунд, карбід кремнію, дріб чавуну (ДЧК) і сталеву (ДСК) та ін. Стиснене повітря має бути добре очищене. Розмір абразивних частинок складає 0,3 -1,5мм. Тиск повітря вибирають у межах 0,4 -0,7МІІа; дистанцію обробки - у межах 0,08 –0,15м; кут зустрічі 60 -90°; витрата абразивних частинок 300 —500кг/год. Контроль поверхні здійснюють по еталонних зразках. На адгезійну міцність особливо впливає марка дробу і розмір частинок.
Вилежування після обробки має бути мінімальним. Час релаксації для кожного матеріалу різний. Тому в ряді виробничих інструкцій термін вилежування складає не більм 2 -5год.
Абразивно -струменева обробка вносить істотні зміни в поверхневі шари напилюваної деталі. Відбувається насичення їх структурними дефектами. Поверхня набуває аномальних фізико - хімічних властивостей. При цьому різко зростає швидкість дифузії поверхневих атомів і їхня енергія.
2) Травлення, хімічне й електричне полірування. При цих способах підготовки розкриваються енергетичне стабільні елементи поверхні у вигляді терас, граней та ін. Додаткові порушення кристалічних ґраток незначні чи взагалі відсутні. Усе це не сприяє активації поверхні при її очищенні.
Склади ванн і режими вибирають виходячи з властивостей матеріалу напилюваного виробу, Ці способи в основному застосовують при підготовці виробів малого розміру та наявності тонкостінних елементів.
3) Очищення поверхні електричними газовими розрядами. Особливо широко таке очищення застосовують при вакуумних конденсаційних методах напилення. У більшості установок цього типу передбачені пристрої для попереднього очищення поверхні напилювання тліючим високовольтним розрядом.
В останній час отримують велике розповсюдження способи плазмового напилювання з герметичних камерах при нормальному і зниженому тиску плазмоутворюючого газу. Завдяки цьому з'являється можливість остаточного очищення поверхні виробів газовими електричними розрядами. Очищення тліючим розрядом проводять при невисокому розрідженні (100 - 0,1 Па) із застосуванням важких бомбардуючих іонів аргону. Прискорені іони здатні зміщати атоми в кристалічних ґратках чи вибивати їх. Для цього потрібна енергія іонів, що перевищує граничні значення. Величина її залежить від теплофізичних властивостей матеріалу виробу, що очищується:
ЕПа>Н,
де ЕП -порогова енергія бомбардуючих іонів; а -коефіцієнт, що визначає максимальну енергію, яку іон може передати атому; Н -теплота возгонки матеріалу.
Для більшості матеріалів Н=1,4 -1,8еВ/атом.Доля енергії, що передається електронами ядру визначається із виразу
∆Е=(4Еm)/M, де
Е -кінетична енергія електронів; m, М -маси електронів і атомного ядра.
Обробка поверхні прискореними іонами не тільки очищуй поверхню, але й значною мірою її активує. У поверхневих шарах з'являються вакансії і дислокації. Для очищення тліючими розрядами використовують режими процесу: Ір=30 -60мА; Up=l,5 -3,ОкВ; час очищення 5 -25с. Поряд із тліючими для очищення поверхні можуть бути використані і дугові розряди. І в цьому випадку на поверхні спостерігаються ерозійні процеси. Дослідження і практика показують, що для очищення поверхні найбільш доцільно використовувати дуговий розряд в імпульсному режимі горіння. Цим значною мірою попереджується перегрів оброблюваного виробу і поліпшується якість підготовки. Орієнтовно режими дугового очищення імпульсними розрядами складають: Ір=10 –З0А; Up=15 -20B; t=10 -15с.
Піскострумна обробкa
Поверхню напилюваного виробу піддають піскоструминній обробці. Така підготовка:
-по-перше, очищує поверхню і виводить її зі стану термодинамічної рівноваги із середовищем, звільнюючи міжатомні зв'язки поверхневих атомів, тобто хімічно активує підкладку, але активність підкладки швидко падає через хімічну адсорбцію газів з атмосфери й окислювання.
-по-друге, піскоструминна обробка робить поверхню підкладки шорсткуватою, що збільшує контактну температуру під напилюваними частинками на виступах шорсткості і відповідно підвищує сумарну площу ділянок приварювання.
-по-третє, шорсткувата поверхня має велику площу порівняно з гладкою, що також сприяє збільшенню міцності зчеплення.
Для підвищення абразивної міцності покриття напилювану поверхню піддають абразивне-струминній обробці. При нанесенні покриття на робочі поверхні шипів хрестовини карданного валу, що підвертається корозії, в якості абразиву можна використати крошку білого чавуну Д4К1 або Д4К1,5, також можна рекомендувати електрокорунд зерністю З0 -100мкм ТУ=036-297-76 абразивну обробку треба проводити не раніше ніж за 4 години до напилення. Також можна застосувати піскоструминну обробку для даного виробу.
3.5 Механічна обробка деталі
Напилені покриття мають підвищену шорсткість поверхні і деяку нерівномірність по товщині. Тому більшість виробів з напиленими покриттями піддають остаточній механічній обробці. При цьому мають на меті таке: придання виробу остаточних розмірів і доведення поверхні покриття до необхідного класу чистоти. Механічна обробка напилених покриттів є відповідальною і важкою операцією, оскільки внаслідок неправильного її проведення покриття може прийти в непридатність. Тому при виборі методу напилення, матеріалу покриття і технології необхідно враховувати характер подальшої механічної обробки. Висота нерівностей напиленої поверхні в основному визначається зернистістю напилюваного порошку: дрібний порошок дає менш шорсткувату поверхню, великий -більш грубу.
Основними видами механічної обробки напилених покриттів є різання, шліфування, фрезерування і полірування.
Обробку різанням можна проводити для металевих покриттів, що мають високу міцність зчеплення і достатню товщину. Це можуть бути як м'які, так і тверді покриття. Обробку таких матеріалів можна вести різцями з швидкорізальної сталі, твердосплавними, а також мінералокерамічними і з надтвердих матеріалів (ельбор, гексаніт, алмаз). Однак при точінні тонких покриттів (приблизно 0,3 -0,5мм) може статися їхнє розтріскування, відшаровування і руйнування. Швидкість різання вибирають експериментальне для різних покриттів, і вона становить 15 - 100м/хв при подачі 0,05 -0,15мм/об.
Тверді і зносостійкі напилені покриття, в тому числі композиційні, звичайне обробляють шліфуванням. Можна проводити як мокре, так і сухе шліфування напилених виробів.
Отримане покриття на випускному клапані будемо обробляти на шліфувальному верстаті.
При шліфуванні покриття використовуватимемо охолоджування (мокре шліфування). Для того, щоб після шліфування отримати хорошу поверхню, виключити утворення тріщин і викришувань, необхідно правильно вибрати круг і режим шліфування,
Після закінчення шліфування поверхня покриття, отриманого газополуменевим напилюванням, повинна мати матовий блиск і містити дрібні пори. Дужі блискуча поверхня, на якій відсутні пори, вказує на неправильне шліфування та ймовірне її засалювання.
Для шліфування покриття, отриманого напилюванням порошкової суміші СНГН-55 з послідуючим оплавленням, можна використати круги з карбіду кремнію зеленого (64С) на бакелітовій або керамічній зв'язці (наприклад, 64С25СМ16К). Допустимо шліфування абразивними кругами з сілого (24А) І хромистого (34А) електрокорундів. Швидкість шліфувального круга вибирають в межах 15 -40м/с при глибині різання до 0,015 -С,030мм.
Необхідно також враховувати, що при шліфуванні напилених покриттів цими кругами вони швидко засалюються, тому їх необхідно частіше правити.
Шліфування повинно проводитися з подачею охолоджувальної рідини. Найкращим варіантом охолоджувача є вода з добавкою 5% емульсора Э -2 при витраті 0,6 -0,85м/хв.
Іноді з метою підвищення економічності процесу, використовують комбіновану технологію, при якій чорнове шліфування проводять алмазними кругами, а чистове - кругами з карбіду кремнію.
3.6 Контроль якості поверхні
Контроль якості продукції є необхідним елементом технології, що забезпечує її надійність в умовах промислового виробництва. При виробництві напилених виробів проводять контроль параметрів процесу та кінцевий контроль покриттів.
Правильно обрані параметри процесу і підтримка їх стабільними при повному циклі напилювання виробу в значній мірі гарантують отримання заданих властивостей. У зв'язку з цим головну увагу при напилюванні виробів потрібно уділяти контролю параметрів режиму напилювання.
Остаточний контроль напилених виробів складається з наступних операцій: визначення товщини покриття; зовнішній огляд напиленого виробу; вияв прихованих дефектів; оцінка адгезійної міцності.
Існуючі методи контролю якості плазмових покриттів розподіляються на не руйнуючі та руйнуючі.
До числа не руйнуючих відносяться контроль зовнішнього виду; вимір товщини; шорсткості поверхні покриття; визначення зносостійкості методом дряпання, скрізної пористості на основі з залізних, мідних, або нікелевих сплавів, а також деякі засоби оцінки міцності зчеплення.
Визначення пористості покриттів
Однією з важливих характеристик напилених покриттів є пористість. З одного боку, це - непрямий показник умов напилювання, пористість також може служити параметром оптимізації процесу напилювання, а з Іншого боку - зона безпосередньо впливає на ефективність захисних властивостей покриття, його теплопровідність, механічні та інші характеристики.
Загальноприйнятою методикою визначення пористості є методика гідростатичного зважування (ГОСТ 18898-73). Знизити помилку цієї методики можна, використовуючи модифікований метод гідростатичного зважування. Метод дозволяє виявити загальну пористість у відділених від підкладки покриттях. Відкриту пористість визначають вимірюванням проникності покриттів, відділених від підкладки. Проникність характери- зується швидкістю проходження газу через шар відповідного розміру при певній різниці тиску на сторонах зразка. Застосовується також метод просочення водою зразків - свідків у вакуумі.
Пористість напилених покриттів можна також визначати металографічним методом, тобто шляховим виготовленням і розгляду мікро шліфів під мікроскопом.
Визначення товщини покриття
Товщину покриття визначають вимірювальними інструментами, ваговими засобами, спеціальними товщиномірами та іншими прийомами.
При вимірюванні товщини покриття вимірювальними інструментами необхідне знання початкових розмірів напилюваного виробу. Зазвичай товщину покриття на деталях простої форми і невеликих розмірів вимірюють штангенциркулями. Після механічної обробки, як правило, для визначення товщини покриттів використовують мікроміри. При вимірюванні товщини покриттів на складних поверхнях невеликих виробів використовують вагові методи. Для цього повинна бути відома початкова маса виробу і розміри напилюваної поверхні. Ваговий метод дозволяє визначати середню товщину покриття. Найбільш простим є визначення товщини покриттів спеціальними приладами—товщиномірами. Як правило, такі прилади настроюють на один або декілька видів матеріалів покриттів. Товщиноміри не використовують у випадках, коли потрібна висока точність вимірювання. Погрішність вимірювання цих приладів складає в середньому 10%. Для точних вимірювань необхідно використати штангенциркулі і мікроміри.
Зовнішній огляд покриття
При зовнішньому огляді покриття контролюється загальний стан поверхні напилення, порівнюється з еталоном наявність зовнішніх дефектів: тріщин, сколювань, спучувань і т.д. Для більш ретельного огляду застосовують лупи із збільшенням до 10 і більше разів.
Мікро тріщини, локальні відшаровування, макро- і мікронесуцільності з великими труднощами або зовсім не піддаються не руйнуючому контролю. У ряді випадків деякі дефекти вдається виявити, застосовуючи ультразвукове опромінення. До числа руйнувальних методів виявлення дефектів можна віднести виготовлення мікро шліфів.
Оцінка адгезійної міцності
Одним з основних показників якості покриттів є міцність зчеплення їх з підкладкою.
Для визначення міцності зчеплення на зразках - свідках у багатьох випадках застосовують методику іспитів на відрив покриття від підкладки. Найбільш розповсюджені іспити міцності клейового сполучення і складової підкладки. Основними недоліками цієї методики є граничність верхньої межі вимірювань міцністю клейового сполучення, а також у проникливості клею у пори покриття та зміні з результаті цього міцністних характеристик.
При використанні штифтової методики матеріал покриття при розтяганні штифта підкоряється дії як відривних, так і зрізуючих навантажень. У випадку застосування штифта з торцем у вигляді кола діаметром dш відношення міцності на відрив до міцності на зріз повинно бути менш ніж 4∆/dш . З практики відомо, що ∆/d ≥ 0,091 — 0,096.
Адгезійна міцність характеризується зв'язком між покриттям і основою і визначається сукупною дією сил фізичної, хімічної і механічної взаємодії матеріалу покриття з матеріалом підкладки. Міцність зчеплення покриттів з підкладкою може коливатися в широких межах залежно від способу підготовки поверхні підкладки, товщини шару, температури підкладки і ряду інших чинників.
4. Економічний розділ
4.1 Розрахунок обсягу робіт
Вибір програми відновлення розподільчого валу двигуна ЗІЛ-130: на період 2010 р. підприємством заплановано провести відновлення 2144 шт. розподільних валів двигуна ЗІЛ - 130. З урахуванням того, що парк машин у нашому регіоні зростає, та ремонт на інших підприємствах скорочується, можна зупиниться на програмі відновлення колінчастих валів - 178 шт. на місяць.
4.2 Режим роботи та фонди часу
Режим роботи ділянки планується в одну зміну. Робочий тиждень встановлюється п'ятиденний, тривалість робочої зміни - 8 годин.
Планований період роботи ділянки з відновлення розподіличих валів двигуна ЗІЛ -130 становить один рік. Решту часу ділянку спеціалізується на відновленні розподільчих валів різних марок автомобілів, в тому числі й іноземного виробництва.
Фонди часу підрозділяють на номінальні та дійсні. Номінальним фондом називається час, який може бути відпрацьований за планований період на робочому місці без урахування будь б то не було втрат, тобто календарно.
Фн = (Дк-Дсв-Дв)·tc·у,
де
Дк, Дсв, Дв – кількість днів календарних, святкових, вихідних відповідно.
Дк = 365, Дсв = 10, Дв = 104;
tc = 8 год – час зміни;
у = 1 – кількість змін.
Фн = (365 – 104 -10)·8·1 = 2008 год.
Дійсний фонд робочого часу роботи обладнання:
Фдо = Фн· зо,
де
зо – коефіцієнт, що враховує простій устаткування (0,95)
Фдо = 2008·0,95 = 1908 год.
4.3 Такт виробництва
Для ритмічної роботи дільниці потрібно узгодити роботу на всіх робочих місцях в часі. Для цього встановлюється єдиний для всіх робочих місць такт виробництва:
ф=Фдо/N=1908ч./2144 р.в.=0,9 ч/р.в.
№ п/п |
Назва операції |
Т/ємк. визгот. дет. – предст. (н/год) |
1. |
Очисна |
0,075 |
2. |
Контрольно-дефекточна |
0,14 |
3. |
Термічна |
0,5 |
4. |
Абразивно-шліфовальна |
0,33 |
5. |
Напилювальна |
0,41 |
6. |
Копіювально-шліфовальна |
0,3 |
7. |
Контрольна |
0,13 |
Підсумок |
1,69 |
4.4 Визначення кількості працюючих на кожному робочому місці
Кількість основних технологічних робітників з кожної технологічної операції:
Mp=Уh/ф люд.
де
Уh – трудомісткість, люд/год,
ф = 0,9 – такт виробництва.
1.Очисна.
Mp=0,075/0,9 =0,08 люд.
2. Контрольно-дефекточна.
Mp=0,14/0,9 =0,16 люд.
3.Термічна.
Mp=0,5/0,9 =0,56 люд.
4.Абразивно-шліфовальна.
Mp=0,33/0,9 =0,37 люд.
5.Напилювальна.
Mp=0,41/0,9 =0,46 люд.
6.Копіювально-шліфовальна.
Mp=0,3/0,9 =0,33 люд.
7.Контрольна.
Mp=0,13/0,9 =0,14 люд.
4.5 Розрахунок кількості робочих постів
Відсоток завантаження поста допускається у межах 95 ... 120% і розраховують за формулою:
Зр= Уh/ф ·100%,
де
Уh – сумарна трудомісткість всіх робіт, включених в пост повинна бути однаковою.
Пост №1. Включає в себе операції 1,3,5 по формулі знаходим:
Уh=0,08+0,56+0,46=1,1 люд-г.
Зр=1,1/0,9 х 100=120%
Пост №2.Включає в себе операції 2,4,6,7 по формулі знаходим:
Уh=0,16+0,37+0,33+0,14=1 люд-г.
Зр=1/0,9 х 100=111%
Чисельність основних виробничих робітників становить 2 осіб. Чисельність допоміжних робітників від 5 до 12% від числа основних виробничих робітників (не приймаємо).
Чисельність ІТР не більше 10-12% від загального числа робочих (не приймаємо). Разом весь штат ділянки становитиме 2 людини.
4.6 Розрахунок кількості обладнання
Число мийних машин розраховується за формулою :
Nm=УQ/Фд.о.·q·Кз.м, де
УQ=0,075 ·2144=160,8 т,
q=0,6-2,7 т/г. часова продуктивність,
Кз.м.=0,65-0,75 степень загрузки.
По формулі знаходим: Nm=160,8/1908 ·0,6 ·0,65=0,22 шт.
Приймаємо одну машину.
Число контрольно-випробувальних стендів:
Nc=УWk·tk/Фд.о.·Кс,
де
УWk=2144,
tk=0,14 – тривалість контролю однієї деталі,
Кс=0,75…0,8 – коефіцієнт, що враховує використання стенду в часі.
Nс=(2144 ·0,14)/(1908 ·0,75)=0,2 шт.
Приймаємо один контрольно-випробувальний стенд.
Число одиниць напилювального обладнання:
Nн= УТн/Фд.о. ·Кн,
де
УТн = 0,41 ·2144=879 – сумарна трудомісткість напилювальних робіт.
Кс=0,8 – коефіцієнт, що враховує використання напилювального устаткування в часі.
Nн=879/1908 ·0,8=0,37 шт.
Приймаємо одну напилювальну установку.
Число абразивних установок:
Nш= УТш/Фд.о. ·Кн,
де
УТш=0,33·2144=708 люд-г.
Nш=708/1908 ·0,8=0,3 шт.
Приймаємо одну абразивну установку.
Число копіювально-шліфовальних верстатів:
Nш= УТш/Фд.о. ·Кн,
де
УТш=0,3·2144=643 люд-г.
Nш=643/1908 ·0,8=0,26 шт
Приймаємо одну абразивно-шліфовальну установку.
Сумарна кількість годин витрачені одою одиницею обладнання на відновлення одного розподілвала на рік.
Визначимо сумарний час роботи мийної ванни:
T м= T · N · q,
де
Т – витрачений час на очищення однієї деталі, н/час
N – кількість відновлюваних розподілвалів, шт
q – коефіцієнт "розігріву" устаткування, приймаємо 1,1
T м= 0,075 · 2144 · 1,1 = 177 год.
Визначимо сумарний час роботи сушильного шкафа:
T сш= T · N · q,
де
Т – витрачений час на прогріву однієї деталі, н/час
N – кількість відновлюваних розподілвалів, шт
q – коефіцієнт "розігріву" устаткування, приймаємо 1,2
T сш= 0,5 · 2144 · 1,2 = 1287 год.
Визначимо сумарний час роботи піскострумного апарата :
T п= T · N · q,
де
Т – витрачений час на шліфовку одной деталі, н/год
N – кількість відновлюваних розподілвалів, шт
q – коефіцієнт "розігріву" устаткування, приймаємо 1,01
T п= 0,33 · 2144 · 1,01 = 715 год.
Визначимо сумарний час роботи напилювального обладнання :
T н= T · N · q,
де
Т – витрачений час на напилювання одної деталі, н/год
q – коефіцієнт "розігріву" устаткування, приймаємо 1,01
T н= 0,41 · 2144 · 1,01 = 887 год.
Визначимо сумарний час роботи кіювального верстата :
T к= T · N · q,
де
Т – витрачений час на шліфовку одної деталі, н/год
q – коефіцієнт "розігріву" устаткування, приймаємо 1
T к= 0,3 · 2144 · 1= 643 год.
4.7 Розрахунок виробничих площ
Розрахунок площ ділянки відновлення чавунних розплдільчих валів проведений за нормами технологічного проектування підприємств машинобудування.
,
де - загальна площа, займана устаткуванням;
к – коефіцієнт розстановки обладнання. Приймаємо = 4,5.
Fуч= 14,38 · 4,5 = 64,71 м2
4.8 Розробка та обгрунтування схем планування обладнання
Ширина прольоту ділянки прийнята В = 12 м.
Довжина займана ділянкою:
,
м;
Довжину проектованого цеху приймаємо число, кратне 6, але більше 5,39 - приймаємо 6м. Висота - 4,8 м.
Норми ширини проїзду прийняті на підставі типових проектів організації робочих місць і вимог ГОСТ 12.3.020 - 80.
Ширина проїзду - 3 м;
Відстань від верстата до проїзду - 2 м;
Відстань між верстатами:
* між тильними сторонами - 1м;
*між бічними сторонами - 1,3 м;
*між фронтом - 2,6 м;
Відстань від стін і колон до:
* фронту - 1,6 м;
* тильної сторони - 1,5 м;
* бічної сторони - 0,9 м;
4.9 Розрахунок порошкової суміші
Для відновлення кулачка застосовуємо порошкову суміш: Ni – 70%, B – 4%, C – 1%, Si – 4%, Cr – 17%, Fe – 3%, Mn – 1% (СНГН-55).
Наплавлений шар характеризується високою стійкістю проти зношу- вання тертям, стійкістю проти абразивного зношування та окислення при нормальних і збільшених до 700 ° С температурах.
Товщина покриття, що рекомендуєтся - до 2 мм.
Покриття обробляється шліфуванням.
Твердість наплавленої кулі 53-58 HRC.
Для розрахунку необхідно вирахувати площу поверхні кулачка:
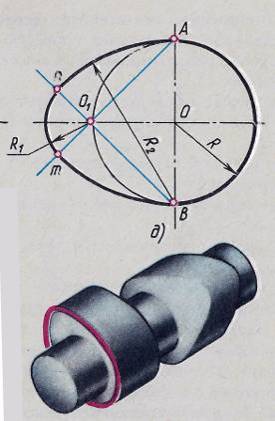
Кулачок має складну форму. Довжина лінії профілю буде:
L=l1+l2+2l3;
R=18,8 мм ;
R1=8,0 мм;
R2=26,0 мм;
l1=рR; (дуга AB)=3,14•18,8=46,472мм.
l2=ЅрR1; (дуга nm)=4,71мм.
l3=јрR2; (дуга nA або mB)=17,27мм.
L=l1+l2+2l3=46,472мм+4,71мм+17,27мм=68,452мм.
Площа поверхні кулачка:
h=11,9 мм.
s=L•h=68,452мм•11,9 мм=814,5788мм2.
Знаходимо товщину покриття:
d=1мм. на шліфування - 0,5мм. d=1,5 мм.
V=S•d=814,5788мм2•1,5мм=1221,8682мм3≈1,222см3;
Маса порошку: щільність елементів, що входять в порошок:
rпор = 0,70*rNi + 0,17*rCr + 0,04*rB + 0,04*rSi + 0,03*rFe + 0,01*rMn + 0,01*rC =0,7*8,902 + 0,17*7,18 + 0,04*2,34 + 0,04*2,33 + 0,03*7,874 + 0,01*7,21 + 0,01*2,25 = 7,97 г/см3.
mтеор. = спорошку· V = 7,97 г/см3 • 1,222см3 = 9,74 г.
Mпракт.1 = = 9,74 г ч 0,6=16,23 г.
Так як автомобіль ЗІЛ-130 має 8-ми циліндровий V-подібний двигун, то на розподільчому валу розміщено 16 кулачків. Для повного відновлювання всіх кулачків на розподільчому валу необхідно:
Mпракт.= Mпракт.1 • 16=16,23 • 16 = 259,68 г
5. Економічні витрати
5.1 Обгрунтування вибору форми оплати праці та умов преміювання
Для оплати праці робітників відновного ділянки вибирається почасово-преміальна система оплати праці. Почасово-преміальна система оплати праці є різновидом погодинної оплати праці.При вибраної нами системі заробітна плата розраховується множенням встановленої годинної тарифної ставки робітника даного розряду на відпрацьований ним час з урахуванням премій. Преміювання може здійснюватися за стабільну якість роботи в розмірі - 10%, за зниження витрат на ремонт - 5%, за виконання і перевиконання завдання по коефіцієнту випуску рухомого складу на лінію - 15%.
5.2 Кошторис витрат і калькуляція собівартості
При калькуляції собівартості всі витрати у залежності від їхнього характеру і цільового призначення розподіляються за статтями.Кошторис витрат при виконанні технічного обслуговування включає в себе основну та додаткову заробітну плату виробничих робітників з нарахуваннями в соціальні фонди, витрати на запасні частини і цехові витрати.
5.3 Розрахунок фонду заробітної плати з нарахуваннями в соціальні фонди
Погодинний фонд заробітної плати визначають за основним даними про планову чисельності робітників підрозділу, плановому фонді робочого часу одного робітника та середньої годинної тарифної ставки, встановленої для робітників даного підрозділу.
ФЗПпов= Y чс*Фр*No,
де, Y чс – середня годинна трифна ставка робітника, грн.
Фр – річний фонд робочого часу, год,
No – кількість робітників, люд.
ФЗПпов=12,6*1908*2=48081,6 грн.,
У відповідності до встановлених показниками преміювання робітників розмір премії нараховується наступним чином:
Пр фзп=П%*ФЗПпов,
де, П% - відсоток премій,%
Приймаємо:
П% = 20%
Пр фзп=20*48081,6/100=9616,32 грн
ƩФЗПпов=9616,32+48081,6=57698 грн
Розраховуємо грошові витрати на електроенергію..
Грошовий річна витрата електроенергії на освітлення становитиме:
Сос = N * W х Тос * Y ве
де, N – кількість ламп, шт.
W – потужність однієї лампи, кВт,
Тос- число годин штучного освітлення при однозмінний режим роботи, рік.
Y ве – вартість однієї кВт електроенегргії, грн / кВт
Сос = 24 * 0,08 * 800 * 0,76 =1167 грн/рік
Денежный годовой расход электроэнергии на вентиляцию помещения составит:
Свен= N * W х Fдо * Y ве
де, N – кількість моторів, шт.
W – потужність одного мотора, Вт,
Fдо - дійсний фонд робочого часу роботи обладнання, год.
Y ве – вартість однієї кВт електроенегргіі, грн / кВт
Сос = 1 * 0,18 * 1908 * 0,76 =261 грн/рік
Грошовий річна витрата електроенергії на експлуатацію електрообладнання складе:
Сео = ƩW х Y ве
де, ƩW – сумарна електроспоживання електрообладнання на рік, кВт
Y ве – вартість однієї кВт електроенегргіі, грн / кВт
ƩW =T н * Wн + Тсш * Wсш + Тм * Wм + Тп * Wп + Тк * Wк
ƩW = 177 * 2 + 1287 * 80 + 715 * 2 + 887 * 40 + 643 * 5.5 = 143760 кВт/рік
Сео = 0,76 * 143760 = 109 тис. грн
Знайдемо загальну суму витрат на електрику:
Се = Сос + Свен + Сео
Се = 1167 + 261 + 109000 = 110428 грн
Грошовий річна витрата води складає:
Св = Свв * Qм ,
де, Y вв – вартість одного літра води, грн / л
Qм – річна витрата води, л
Св = 7,22 * 197 = 1422 грн
Грошовий річна витрата природного газу на опалення складе:
Вартість 1000 м3. газа – 1888 грн.
Вартість 1 кВт*час - 0,2 грн.
Розрахуємо кількість грошових коштів, щоб обігріти цех:
Соп= Y пг * Рот * Tот
де, Y пг – вартість 1 кВт * год природного газу, грн,
Рот – теплова потужність обігріву, кВт,
Tот – опалювальний сезон (в Одесі він становить в середньому 155 дн, або 3720 год), год
Соп= 0,2 * 13 * 3720 = 9672 грн
Розрахуємо кількість коштів на напилювання:
Спор= Y вп * Mпракт. * N
де, Y вп – вартість 1 грама порошку для відновлення, грн
Mпракт. – вага порошку, щоб відновити один розподілвал, гр
N – кількість деталей, шт
Спор = 0,176 * 259,68 * 2144 = 98000 грн
Розрахуємо кількість коштів на оренду цеху:
Со = Y * S пприм * 12
де, Y – орендна вартість м2, грн / міс
S пприм - площа приміщення, м2
12 – кількість місяців
Со = 40 * 72 * 12 = 34560 грн
Визначимо витрати на відшкодування зносу малоцінних і швидкозношуваних предметів,пристосувань за формулою:
Сзн = Соб * qизн/100
де, Соб - вартість обладнання, грн.,
qзн – відсоток відшкодування зносу малоцінних, швидкозношуваних предметів і пристосувань, %
Приймаємо:
Соб = 279100 грн.
Сзн = 279100 * 2/100 = 5582 грн.
Всі розрахунки вводимо в таблицю.
Статті видатків |
Умовні позначення |
Сума витрат, грн. |
Витрати на з/п |
ФЗПпов |
57698 |
Витрата на купівлю обладнання |
Соб |
279100 |
Витрати на порошок для напилювання |
Спор |
98000 |
Витрати на знос обладнання |
Сзн |
5582 |
Витрати на електроенергію |
Се |
110428 |
Витрати на опалення |
Соп |
9672 |
Витрати на воду |
Св |
1422 |
Оренда цеха |
Со |
34560 |
Всього |
ƩСвитр |
596462 |
5.4 Економічний прибуток
Вартість нового розподільного валу ЗІЛ-130 = 780 грн. У нашому цеху ми проводимо відновлення цих частин двигуна, за ціною - 440 грн / шт., в половину ціни нової деталі.
Визначимо економічний прибуток:
ƩСприб = Yвр * N
де, Yвр - вартість відновленого розподільчого вала, грн
N – запланована кількість відновлених розподілвалів, шт
ƩСприб = 440 * 2144 = 943360 грн/рік
5.5 Економічна ефективність
Сеф = ƩСприб – ƩСвитр
Сеф = 943360 – 596462 = 346900 грн
6. Охорона праці
Охорона праці ставить своєю метою зниження травматизму та захворюваності працюючих шляхом створення здорових та безпечних умов праці.
Охорона праці - система збереження життя і здоров'я працівників у процесі трудової діяльності, яка включає правові, соціально - економічні, організаційно - технічні, санітарно - гігієнічні, лікувально - профілактичні, реабілітаційні та інші заходи. Вивчення і рішення проблем, пов'язаних із забезпеченням здорових та безпечних умов, в яких протікає праця людини - одна з найбільш важливих завдань у розробці нових технологій і систем виробництва. Вивчення і виявлення можливих причин виробничих нещасних випадків, професійних захворювань, аварій, вибухів, пожеж, і розробка заходів та вимог, спрямованих на усунення цих причин дозволяють створити безпечні і сприятливі умови для праці людини. Комфортні та безпечні умови праці - один з основних факторів, що впливають на продуктивність і безпеку праці, здоров'я працівників. Метою даної роботи є огляд всіх основних питань що стосуються охорони праці: поняття охорони праці; джерел норм що регулюють питання охорони праці;прав і обов'язків суб'єктів трудового права, що стосуються охорони праці; відповідальності за порушення законодавства про працю і правил охорони праці; прав окремих категорій працівників (жінок, неповнолітніх, осіб зі зниженою працездатністю).
Вимоги охорони праці обов'язкові для виконання юридичними і фізичними особами при здійсненні ними будь-яких видів діяльності, у тому числі при проектуванні, будівництві (реконструкції) та експлуатації об'єктів, конструюванні машин, механізмів та іншого обладнання,розробці технологічних процесів,промисловості і трудових організацій.
6.1
Стан умов праці при роботі по відновленню чавунних розподілвалів
Технологічний процес відновлення чавунних розподільчих валів включає в себе ряд несприятливих, для виконавців робіт, чинників. Небезпеки, що мають місце на робочих місцях, підрозділяються на імпульсні і акумулятивні.
Джерелами імпульсних небезпек є рухливі маси, потоки повітря, газів і рідин, незаземлене джерела електричної енергії, неправильне розміщення устаткування на робочому місці.Імпульсна небезпека, що призводить до травми, миттєво реалізується у випадкові моменти часу і може бути представлена дискретної,випадкової функцією виробничого процесу.
Джерелами акумулятивних небезпек є: підвищений шум, вібрація,забрудненість повітряного середовища газами і парами.В результаті дії цих факторів організм людини перевтомлюватися, порушується координація рухів, притупляється реакція організму на зовнішні подразники.Акумулятивна небезпека реалізується протягом всього виробничого процесу, представляючи його безперервну функцію, і призводить до підвищеного стомлення і захворювань.
На робочих місцях зварювання і наплавлення присутні такі шкідливі фактори як ультрафіолетове випромінювання, виділення шкідливих речовин процесу згоряння, надлишкове виділення теплоти.
На робочому місці шліфувальника присутній підвищений вміст абразивної суспензії в повітрі, шум при обробці виробів.
На робочому місці токаря і слюсаря присутній підвищений шум, є небезпека отримати травму від обертових частин обладнання. До травмі може призвести так само попадання стружки в очі.
На робочому місці мийника робочим тілом є вода, температура якої досягає 90 градусів.Існує можливість отримання опіків.
У зв'язку з тим, що технологічний процес відновлення чавунних розподільчих валів призначений для невеликих ділянок ремонтних підрозділів МПС в основному розташовуються в старих приміщеннях, що часто мають не достатня кількість освітлення, а також у зв'язку з тим,що однією з найбільш об'ємної роботою з відновлення чавунних колінчастих валів є операції шліфування,зроблений розрахунок штучного освітлення на робочому місці шліфувальника.
6.2 Аналіз шкідливих і небезпечних факторів шліфувального відділення
Робоче місце |
Небезпечні і шкідливі фактори |
Характеристика небезпечних та шкідливих факторів |
Абразив-но – шлі-фувальна установка |
Шум |
Шум як фізіологічне явище являє собою несприятливий фактор зовнішнього середовища і визначається як звуковий процес, несприятливий для сприйняття і заважає роботі та відпочинку. За фізичну природу шум, створювати устаткування, обумовлений процесами механічної дії деталей. |
Освітлення |
Світло є природним умовою життєдіяльності людини і грає велику роль у збереженні здоров'я і високої працездатності.Недостатня освітленість вимагає не тільки постійної напруги очей, що призводить до перевтоми і зниження працездатності, але також може призвести до того, що будуть незамічена деякі похибки у виготовленні. |
Небезпека травмування обертовими частинами. |
При роботі верстата обертається його частиною є шліфувальний круг і оброблювана деталь, тому існує небезпека травмування обертовими частинами при роботі. |
Пожежонебезпека |
На робочому місці шліфувальника є мастильні матеріали, які можуть бути розлиті і при недбалому ставленні до заходів пожежної безпеки може виникнути пожежа. |
Небезпека ураження електричним |
У своєму пристрої шліфувальний верстат має електрообладнання, необхідне для його функціонування,тому наявність електрообладнання та струмоведучих частин при неправильній експлуатації та недотримання правил техніки безпеки електроустановок може призвести до ураження обслуговуючого персоналу електричним струмом. |
6.3
Вимоги нормативно-технічної документації з охорони праці
Вимоги |
Нормативний
документ
|
Робоче місце, його обладнання та оснащення, що застосовуються відповідно до характеру роботи, повинні забезпечувати безпеку, охорону здоров'я і працездатність працюючих. |
ГОСТ 12.2.061-81.
Обладнання.
|
Шум на робочому місці не повинен перевищувати 80 дБА. |
ГОСТ 12.1.003-83.
Шум. Загальні вимоги безпеки.
|
Виробниче обладнання повинно мати вбудований пристрій для видалення виділяються в процесі роботи шкідливих речовин безпосередньо від місця їх утворення і скупчення. |
ГОСТ 12.2.003-74. |
Штучне освітлення у виробничих приміщеннях повинен устоювати з лампами розжарювання або люмінесцентними лампами у вигляді загального освітлення з рівномірним або локалізованим розміщенням світильників і комбінованого (загального і місцевого). Застосування одного місцевого освітлення не допускається.Норма освітленості робочого місця повинна становити при загальному освітленні 300 лк. |
СНіП II-4-79 |
Приводні частини обладнання, а також передачі, до яких можливий доступ людей, повинні бути огороджені. |
ГОСТ 12.2.002-80.
Огородження. Загальні вимоги.
|
Рухомі і обертові елементи устаткування, до яких можливий доступ обслуговуючого персоналу, повинні бути огороджені з усіх боків і по всій довжині, незалежно від висоти розташування і швидкості руху. |
ГОСТ 12.2.027-80.
Устаткування гаражне й авторемонтного.
|
Органи управління, пов'язані з певною послідовністю їх застосування, повинні групуватися таким чином, щоб дії працюючого здійснювалися зліва направо і зверху вниз. |
ГОСТ 12.2.064-81.
Органи управління виробничим устаткуванням.
|
У конструкціях органів управління, призначених для включення обладнання, повинні бути передбачені засоби захисту від випадкового включення. |
ГОСТ 12.2.027-80. |
Електрична схема обладнання повинна виключати можливість його мимовільне включення / вимикання. |
ГОСТ 12.2.007-75.
Вироби електротехнічні. Загальні вимоги.
|
6.4 Заходи щодо захисту робітників від небезпечних і шкідливих факторів
На людину в процесі його трудової діяльності можуть впливати небезпечні (що викликають травми) і шкідливі (викликають захворювання) виробничі фактори. Небезпечні та шкідливі виробничі фактори (ГОСТ 12.0.003-74) поділяються на чотири групи: фізичні, хімічні, біологічні та психофізіологічні.
До небезпечних фізичних чинників відносяться: рухомі машини і механізми; різні підйомно-транспортні пристрої та переміщувані вантажі;незахищені рухливі елементи виробничого устаткування (приводні та передавальні механізми, ріжучі інструменти, що обертаються і переміщаються пристосування тощо);рикошетом частинки оброблюваного матеріалу та інструменту, електричний струм, підвищена температура поверхонь устаткування і оброблюваних матеріалів і т.д.
Шкідливими для здоров'я фізичними факторами є: підвищена або знижена температура повітря робочої зони;високі вологість і швидкість руху повітря; підвищені рівні шуму, вібрації, ультразвуку та різних випромінювань - теплових, іонізуючих, електромагнітних, інфрачервоних і ін До шкідливих фізичних чинників відносяться також запиленість і загазованість повітря робочої зони;недостатня освітленість робочих місць, проходів та проїздів; підвищена яскравість світла й пульсація світлового потоку.
Хімічні небезпечні та шкідливі виробничі фактори за характером дії на організм людини підрозділяються на наступні підгрупи: загальнотоксичну, дратівливі, сенсибілізуючі (що викликають алергічні захворювання), канцерогенні (викликають розвиток пухлин),мутогенние (діючі на статеві клітки організму).У цю групу входять численні пари й гази: пари бензолу й толуолу, окис вуглецю, сірчистий ангідрид, оксиди азоту, аерозолі свинцю й ін, токсичні пилу, що утворюються, наприклад, при обробці різанням берилію, свінцовістих бронз і латуней і деяких пластмас з шкідливими наповнювачами.До цієї групи відносяться агресивні рідини (кислоти, луги), які можуть заподіяти хімічні опіки шкірного покриву при зіткненні з ними.
До біологічних небезпечним і шкідливим виробничим факторам ставляться мікроорганізми (бактерії, віруси та ін) І макроорганізму (рослини і тварини), вплив яких на працюючих викликає травми або захворювання.
До психофізіологічних небезпечним і шкідливим виробничим факторам відносяться фізичні перевантаження (статичні та динамічні) і нервово-психічні перевантаження (розумове перенапруження, перенапруження аналізаторів слуху, зору та ін.)
Тим шкідливими і небезпечними виробничими чинниками спостерігається певний взаємозв'язок. У багатьох випадках наявність шкідливих факторів сприяє прояву травмонебезпечних факторів.Наприклад, надмірна вологість у виробничому приміщенні та наявність струмопровідного пилу (шкідливі фактори) підвищують небезпеку ураження людини електричним струмом (небезпечний чинник).
Рівні впливу на працюючих шкідливих виробничих факторів нормовані гранично-допустимими рівнями, значення яких зазначені у відповідних стандартах системи стандартів безпеки праці та санітарно-гігієнічних правилах.
Гранично допустиме значення шкiдливого впливу (згідно з ГОСТ 12.0.002-80) - це конкретне значення величини шкідливого виробничого фактора, вплив якого при щоденній регламентованій тривалості протягом усього трудового стажу не призводить до зниження працездатностi i захворювання в період трудової діяльності,так і до захворювання в наступний період життя,а також не робить несприятливого впливу на здоров'я потомства.
6.5 Техніка безпеки
Загальні вимоги.
Верстат має бути заземлений.
Не допускаються до керування верстата особи, які не пройшли навчання та не атестовані з професії шліфувальник, а також особи, молодші 18 років.
Забороняється робота на несправному обладнанням, при несправному захисному кожусі.
При роботі на верстаті обов'язково користуватися захисним екраном.
Вимоги перед початком роботи.
Перед початком роботи робітник зобов'язаний оглянути і перевірити технічний стан вузлів і деталей верстата і переконатися в їх справності.
Перевірці на справність і надійність підлягають:
- Огорожі та захисні кожухи обертових вузлів верстата, а також їх кріплення;
- Заземлення верстата, (візуально);
- Освітлення робочого місця;
- Система управління стендом.
Працювати на верстаті, що має несправності, забороняється.Необхідно переконатися в наявності на робочому місці засобів індивідуального захисту, засобів пожежогасіння та засобів надання першої медичної допомоги.
Вимоги під час роботи.
При появі під час роботи верстата сторонніх шумів, стукотів і т.д.верстат необхідно відключити і перевірити, звідки виходять дані ознаки несправності.
Під час роботи забороняється:
- Відволікатися від виконання прямих обов'язків;
- Виходити з приміщення при працюючому обладнанні;
- Передавати керування верстатом особам, які не мають на це дозвіл.
При припиненні подачі електроенергії робітник повинен відключити верстат від мережі.
Вимоги після закінчення робіт.
Після закінчення робіт робочий зобов'язаний:
- Вимкнути верстат і провести його збирання;
- Зробити необхідні записи в журналі прийому та здачі зміни.
Вимоги в аварійній ситуації.
При виникненні аварійної ситуації робочий зобов'язаний відключити стенд від мережі і повідомити про це своєму безпосередньому керівникові.
Висновок
Дипломний проект присвячений актуальній проблемі відновлення чавунних розподільчих валів двигунів автомобіля ЗІЛ-130. За основу взято автором спосіб відновлення напилюванням зношених кулачків. Технологічний процес за складом операцій, прийняття устаткування та за технологічною оснащенні можна віднести до категорії легко реалізуються, тому ця робота може бути впроваджена в ремонтних дорожніх майстерень. Технологічний процес відпрацьований досить глибоко, прийняті рішення обгрунтовані розрахунками.
На підставі виконаної роботи можна зробити слудуючі висновки: плазмова технологія напилювання високоміцного чавуну під флюсом по оболонці дозволяє значною мірою підвищити працездатність відновлених розподыльчих валів за рахунок усунення в наплавленому металі дефектів (пір і тріщин) і підвищення втомної міцності.
Технологічний процес складається з 6 етапів відновлення:
- Наплавочні операції;
- Механічна обробка кулачків вала під номінальні розміри.
Технологія відновлення містить:
- Розрахунок і вибір устаткування;
- Технологічне нормування операцій;
- Розрахунок виробничої ділянки.
- Вибір технологічного оснащення;
Що до економічного показника, то ми досить вдало теоретично реалізували методику ремонту напилюванням розподільчого валу, наш цех зумів заробити 346 900 грн.
Список використаних джерел
1. Сіньковський А.С., Раддац О.В. Інструкція по одержанню композитних плакованих порошків. – Одеса, 2001
2. Борисов Ю.С., Борисова А.Л. Плазменные порошковые покрытия. – К., 1986.
3. Газотермические покрытия из порошкових материалов: Справ очник/ Ю.С. Борисов и др. – К. Наукова думка, 1987.
4. Петров С.В., Саков А.Г. Плазма продуктов сгорания в инженерии поверхности. – К., 2000.
5. Кудинов В.В., Іванов В.М. Нанесение плазмой тугоплавких покрытий. – М.: Машиностроение, 1981.
6. Кудинов В.В., Іванов В.М. Эффективность использования энергии плазменной струи при нанесении покритий порошком // Порошковая металургия. – 1972.-№12.-с.79-83.
7. Пащенко В.М. Обладнання для газотермічного нанесення покриттів: Навч. Посіб. – К.: Політехніка, 2001.
8. Сидоров А.И. Восстановление деталей машин напылением и наплавкой. – М.: Машиностроение, 1987.
9. Карп И. Н., Петров С. В. Новое оборудование для плазменного упрочнения // Энергетик. – 1990, № 8
10. Под. ред. Митина Б. С. Порошковая металлургия и напыление порошков. Москва, 1987.
11. Хасуй А. Техника напыления. Перевод с японского. Москва: Машиностроение, 1985, 288 с.
12. Линник В. А., Пешков П. Ю. Современная техника нанесений покрытий. Москва: Машиностроение, 1985, 128 с.
13. Антошин Е. В. Газотермическое нанесение покрытий. М.: Машиностроение, 1974, 97 с.
14. Гуляев А. П. Металознавство. М., 1966.
15. Сборник типовых инструкций по технике безопасности. М., 1994. 432 с.
16. Безопасность производственных процессов// Справ очник: С.В.Белов, В.Н.Брынза, 1985.
17. Жидецкий В.И. Основы охраны труда: Ученик, 2000.
|