ДИПЛОМНЫЙ ПРОЕКТ
"Проект совершенствования технического обслуживания и текущего ремонта автомобилей в строительной фирме "Агровод" г. Ижевска Удмуртской республики"
Введение
Автомобильный транспорт играет существенную роль в транспортной системе Российской Федерации. Более 80% грузов перевозится автотранспортом. Основная задача автотранспорта – полное и своевременное удовлетворение потребностей промышленности и население в перевозках, повышение эффективности и качества работы.
Большое значение имеет повышение качества и надежности выпускаемых автомобилей, уровня их технического обслуживания и ремонта, включая организацию и проектирование ремонтно-обслуживающего производства. Однако с ростом стоимости техники существенно увеличиваются и затраты на запасные части и ее ремонт.
По мере роста научно-технического прогресса, способствующего повышению надежности машин, все большее внимание уделяют совершенствованию системы технического обслуживания, которая приобретает характер комбинированной системы, предусматривающей выполнение части операции в обязательном порядке, а другой части по потребности, определяемой техническим осмотром и диагностированием. Это снижает трудоемкость обслуживания, уменьшает потребность в запасных частях и эксплуатационных материалах.
Целью настоящей работы является повышение производительности и качества выполняемой работы машинным парком, при меньших затратах на эксплуатацию за счет улучшения системы технического обслуживания и уменьшения простоев связанных с отказами.
1. Краткая характеристика и анализ производственной деятельности предприятия
1.1 Общая характеристика предприятия
ПК СФ «Агровод» находится в г. Ижевске по адресу ул. Пойма 9. Расстояние до центра города 2,5 км. до ближайшей ж.д. станции 2 км.
Удмуртмелиорация ПМК – 6 была организована в 1953 году и включало в себя помимо Ижевского участка отделения в Воткинске и в Можге. Позднее в 1992 году Ижевский участок реорганизовали в производственный кооператив, строительную фирму «Агровод». Его учредителями являются граждане России, работающие на данном предприятии в количестве 35 человек.
Основным видом деятельности предприятия являются подрядные работы включающие в себя: строительство водопроводов; бурение, ремонт скважин; реконструкция прудов; проектные работы. Кроме того, в состав выручки входят доходы от оказания услуг строительных механизмов; от оптовой торговли прочих строительных материалов; от сдачи внаем собственного нежилого недвижимого имущества. В деятельности предприятия важную роль играет сезонность и погодные условия. В данный момент парк предприятия состоит из 23 единиц строительной техники и 30 автомобилей (прилож. 1).
На предприятии работает 153 человека, из которых 35 человек – аппарат управления, 53 водителя и 65 производственных работника.
1.2 Природно-климатические условия
Климат на территории г. Ижевска умеренно – континентальный с продолжительной холодной и многоснежной зимой. Континентальный арктический воздух нередко врывающийся на территорию Ижевска с севера приносит сильные морозы зимой, а также частые ночные заморозки весной. Лето теплое с хорошо выраженными переходными временами года – весной и осенью. Самый холодный месяц январь со средней месячной температурой -18,9 С°. Максимально холодное время в году – третья декада января -22,6 С°.
Самый теплый месяц в году – июль, средняя месячная температура +20С°. Среднегодовая температура воздуха 3,7 С° тепла. Период со среднесуточной температурой выше 0 С° составляет 200 дней.
Годовое количество осадков выпадает 319 мм, высота снежного покрова – 0,55 – 0,7 м. Преобладающее направление ветров в теплый и холодный периоды северо – западное со средней скоростью 4,3 м/с.
1.3 Специализация предприятия и основные производственные фонды
Одним из принципов рациональной организации производства на предприятиях является углубление специализации и рациональное сочетание отраслей.
Под специализацией предприятия понимается сосредоточение его деятельности на оказание определенного вида услуг или ограниченного их круга. На предприятиях она обычно связана с расширением одного или нескольких направлений при соответствующем сокращении других. Расширение одних направлений за счет сокращения других может осуществляться до тех пор, пока дальнейший их рост уже не приносит экономической выгоды.
Уровень специализации наиболее точно характеризуется удельным весом направлений в структуре оказываемых услуг. Он позволяет выявить те виды услуг, с которыми хозяйство выступает в общественном разделении труда. Структура оказываемых услуг приведена в табл. 1.1
Таблица 1.1 – Структура оказываемых услуг
Вид услуг
|
2004 г. |
2005 г. |
2006 г. |
Выручка
тыс. руб.
|
Уд.вес
%
|
Ранг |
Выручка
тыс. руб.
|
Уд.вес
%
|
Ранг |
Выручка
тыс. руб.
|
Уд.вес
%
|
Ранг |
1. Подрядные работы |
38145 |
77,7 |
1 |
51421 |
80 |
1 |
58786 |
76 |
1 |
2. Субподрядные
работы
|
2938 |
6 |
3 |
7346 |
11,4 |
2 |
11316 |
14,6 |
2 |
3. Услуги
механизмов
|
516 |
1,1 |
5 |
445 |
0,7 |
5 |
534 |
0,7 |
5 |
4. Оптовая
торговля стройматериалами
|
6662 |
13,6 |
2 |
3471 |
5,4 |
3 |
4914 |
6,4 |
3 |
5. Аренда |
827 |
1,6 |
4 |
1613 |
2,5 |
4 |
1787 |
2,3 |
4 |
Итого |
49088 |
100 |
- |
64296 |
100 |
- |
77337 |
100 |
- |
Коэффициент
специализации
|
0,59 |
0,61 |
0,57 |
Рассчитаем коэффициент специализации, Кс
[28]:
Кс
=
,
(1.1)
где УВ – удельный вес услуг, %;
i – порядковый номер удельного веса услуг в ранжированном ряду.
Коэффициент специализации рассчитаем на примере 2006 года. Значение коэффициентов специализации за все три анализируемых года отображаем в табл. 1.1
Кс
=
=0,57
Коэффициенты специализации равные 2004 – 0,59; 2005 – 0,61; 2006 – 0,57 показывают высокий уровень специализации.
Из табл. 1.1 анализируя данные, видим, что основным видом деятельности предприятия являются подрядные работы, включающие в себя: строительство водопроводов, бурение и ремонт скважин, реконструкция прудов и прочее. Коэффициент специализации немного снизился в связи с увеличением процента субподрядных работ, который с 2004 по 2006 год вырос более чем в 2 раза.
Таблица 1.2 – Основные производственные фонды
Показатель |
2004 г. |
2005 г. |
2006 г. |
2006 г. к 2005 г. в% |
1. Среднегодовая стоимость основных производственных фондов, тыс. руб. |
13305 |
12720 |
13498 |
106,1 |
2. Стоимость валовой продукции по себестоимости, тыс. руб. |
47227 |
57384 |
64498 |
112,4 |
3. Выручка от реализации услуг, тыс. руб. |
49088 |
64296 |
77337 |
120,3 |
4. Среднегодовое число работников, чел. |
148 |
149 |
153 |
102,6 |
5. Фондовооруженность, тыс. руб./чел. |
89,9 |
85,4 |
88,2 |
103,3 |
6. Фондоотдача по валовой продукции |
3,55 |
4,51 |
4,78 |
106 |
7. Фондоемкость |
0,28 |
0,22 |
0,21 |
95,5 |
8. Произведено валовой продукции на 1 среднегодового работника, тыс. руб. |
319,1 |
385,1 |
421,6 |
109,5 |
Обобщающими показателями являются: фондоотдача по валовой продукции (ФД), фондоемкость (ФЕ), фондовооруженность (ФВ). Рассчитываем их по следующим формулам:
ФД=ВП/ОПФ, (1.2)
ФЕ=ОПФ/ВП, (1.3)
ФВ=ОПФ/ЧР, (1.4)
где ВП – стоимость валовой продукции, тыс. руб.;
ОПФ – стоимость основных производственных фондов, тыс. руб.;
ЧР – среднегодовая численность работников, чел.
Из приведенных в таблице данных видим, что идет рост производства, т. к. выручка от реализации услуг увеличилась на 20%. Наблюдается незначительная текучесть кадров и, в основном, этот факт сказывается на небольшом провале уровня фондовооруженности в 2006 г. Среднегодовая стоимость основных производственных фондов осталась на уровне 2004 года, это сказалось на увеличении фондоотдачи и на снижении фондоемкости.
1.4 Экономическая характеристика предприятия
ПК СФ «Агровод» осуществляет строительство водохозяйственных сооружений, продажу строительных материалов, а также сдача в аренду собственного нежилого недвижимого имущества и оказание услуг строительной техники. Хранение, техническое обслуживание и ремонт подвижного состава производятся собственными силами на территории фирмы.
Основная цель экономической деятельности получение прибыли и по этому показателю можно оценить результаты работы в целом. Для частной фирмы важна прибыльность т. к. им не приходиться надеяться на государственные дотации, в случае убыточности их ждет банкротство.
Данные о результатах финансовой деятельности работы предприятия приведены в табл. 1.3
Таблица 1.3 – Финансовые результаты работы предприятия
Показатель |
2004 г. |
2005 г. |
2006 г. |
2006 г. к 2005 г. в% |
1. Выручка от реализации услуг, тыс. руб. |
59863,4 |
78409,8 |
94313,4 |
120,3 |
в т.ч. НДС, тыс. руб. |
10775,4 |
14113,8 |
16976,4 |
120,3 |
2. Выручка от реализации услуг (без НДС), тыс. руб. |
49088 |
64296 |
77337 |
120,3 |
3. Себестоимость реализованных услуг, тыс. руб. |
47227 |
57384 |
64498 |
112,4 |
4. Прибыль (убытки) от реализации услуг, тыс. руб. |
1816 |
6912 |
12839 |
185,7 |
Анализируя данные табл. 1.3 прослеживается экономический подъем, по сравнению с 2005 годом прирост составил почти 90%, а по отношению с 2004 годом прибыль увеличилась в 7 раз. Такие результаты достигнуты за счет увеличения выручки при минимальном удорожании себестоимости.
Динамика показателей производства предприятия сведена в табл. 1.4
Таблица 1.4 – Динамика показателей производства
Показатель |
2004 г. |
2005 г. |
2006 г. |
2006 г. к 2005 г. в% |
1. Среднегодовое число работников, чел. |
148 |
149 |
153 |
102,6 |
2. Фонд заработной платы, тыс. руб. |
7472 |
9378 |
15869,5 |
169,2 |
3. Средняя зарплата работников за год, руб. |
50486 |
62940 |
103722 |
164,8 |
4. Себестоимость реализованных услуг, тыс. руб. |
47227 |
57384 |
64498 |
112,4 |
5. Прибыль, тыс. руб. |
1816 |
6912 |
12839 |
185,7 |
6. Рентабельность, % |
3,8 |
12 |
19,9 |
165,8 |
Исходя из данных табл. 1.4 можем сделать вывод, что динамика производства предприятия улучшилась. Увеличилась прибыль, соответственно на аналогичный процент вырос и фонд зарплаты, а в совокупности с незначительным увеличением работников дало рост зарплаты на 65%. Экономическому росту сопутствует повышение уровня рентабельности с 3,8% 2004 году до 19,9% в 2006 году, учитывая динамику «Агровод» можно отнести к быстроразвивающимся фирмам.
1.5 Производственные затраты и себестоимость продукции
Себестоимость продукции один из наиболее важных показателей работы предприятия, показывает денежные затраты на производство продукции и является основополагающим фактором в процессе ценообразования. От уровня себестоимости зависят финансовые результаты деятельности предприятия и как следствие темпы расширения производства. При структурном рассмотрении факторов влияющих на себестоимость можно четко отследить наиболее весомые составляющие, а также пути их снижения. В любом производстве можно найти факторы при помощи снижения затрат на которые уменьшается себестоимость без утраты, а иногда с увеличением качества это называется управление себестоимостью. Основными элементами этого управления являются планирование, нормирование затрат, прогнозирование, анализ и контроль себестоимости. Состав затрат на производство расписан в табл. 1.5
Таблица 1.5 – Состав затрат на производство
Показатель |
2004 г. |
2005 г. |
2006 г. |
2006 г. в % к 2005 г. |
1. Затраты на основное производство, всего, тыс. руб. |
47227 |
57384 |
64498 |
112,4 |
в т.ч. а) Материальные затраты, тыс. руб.:
в т.ч.: сырье и материалы
услуги
топливо
энергия
|
34336
21508
7642
4807
379
|
41720
23827
12150
5242
501
|
42934
22641
14257
5717
319
|
102,9
95
117,3
109,1
64
|
б) Фонд оплаты труда, тыс. руб. |
7472 |
9378 |
15869,5 |
169,2 |
в) Единый соц. налог, тыс. руб. |
3117 |
3787 |
4251 |
112,2 |
г) Амортизация, тыс. руб. |
679 |
562 |
790 |
140,6 |
д) Прочие расходы, тыс. руб. |
1623 |
1937 |
653,5 |
34 |
2. Себестоимость реализованных услуг, тыс. руб. |
47227 |
57384 |
64498 |
112,4 |
Из таблицы видим что основная часть затрат это сырье и материалы в 2006 году снизилась на 5%, но себестоимость увеличилась на 12% и связано это с увеличением фонда зарплаты. Существенно возрос уровень амортизации, вызван этот рост приобретением в 2006 году 3 единиц техники.
1.6 Хранение подвижного состава
Основной сферой деятельности ПК СФ «Агровод» является строительство и часть техники, в основном строительной, хранится на открытых участках в непосредственной близости к объекту строительства. Подвижной состав, ежедневно возвращающийся на территорию, делится по способу хранения на две группы: в отапливаемых боксах и на открытых площадках. В боксах хранится преимущественно легковой транспорт водители этих машин отвечают за чистоту и порядок в гараже, а также за пожарную безопасность.
На открытых площадках хранятся грузовые автомобили и спецтехника. В отдаленных от маршрутов движения по предприятию местах стоит неисправная техника, предназначенная на запчасти. Техника, ожидающая ремонта, стоит на местах своего обычного хранения и в мастерской. Уборку на открытых площадках проводят с помощью трактора. Более подробно территория предприятия представлена на листе ЭМДП.01.009.000Д2
Основные размеры и удельный вес территорий представлены в табл. 1.6
Таблица 1.6 – Размеры территории предприятия
Территория |
Площадь, м2
|
Удельный вес, % |
1. Административно – бытовые корпуса |
1056 |
8,8 |
2. Гаражи и производственные корпуса |
2184 |
18,1 |
3. Крановая площадка |
1184 |
9,8 |
4. Открытые площадки и проезды |
7641 |
63,3 |
5. Общая площадь предприятия |
12065 |
100 |
1.7 Численность работников предприятия
Количество работников зависит от типа и структуры предприятия, его режима работы и спектра оказываемых услуг. При составлении списочного состава работников в него включают все категории работников принятые на постоянную либо сезонную работу.
Каждодневная численность списочного состава, как правило, бывает разнообразной, в связи с выбыванием и приемом новых работников, а также поступлением на прохождение практики, особенно в летние месяцы. В конце года вычисляют среднесписочное количество работников. Среднесписочная численность работников ПК СФ «Агровод» и распределение их по основным категориям приведена в табл. 1.7 на 12 января 2007 г.
Помимо списочного состава на предприятие могут быть привлечены внештатные сотрудники для проведения каких либо не профильных работ, к примеру, строительная бригада, занимающаяся внутренним ремонтом. Объем выполняемых ими работ незначителен.
Таблица 1.7 – Численность работников предприятия
Состав работников |
Количество, чел. |
1. Административно – управленческий персонал |
35 |
2. Водители, всего:
в т.ч. 1 класса
2 класса
3 класса
|
53
20
15
18
|
3. Производственные рабочие, всего:
в т.ч. слесари по ремонту
токари
электрогазосварщики
другие
|
65
4
1
7
53
|
Итого: |
153 |
1.8 Анализ деятельности автопарка
Автомобильный транспорт используется для доставки строительных материалов и техники к местам строительства. Проведем совмещенный анализ работы автопарка по всем группам автомобилей. Результаты анализа работы автопарка приведены в табл. 1.8
Таблица 1.8 – Годовая программа автопарка
Показатель |
2004 г. |
2005 г. |
2006 г. |
2006 г. к
2005 г. в%
|
1. Объем перевозок, тыс. т |
69,3 |
68,5 |
73,7 |
107,6 |
2. Грузооборот, тыс. т×км |
1088 |
1105 |
1315 |
119 |
3. Всего подвижного состава |
26 |
27 |
30 |
111 |
4. Общий пробег, тыс. км |
409 |
428,2 |
457,2 |
106,8 |
5. Среднесуточный пробег, км |
106,2 |
109,3 |
105,8 |
96,8 |
6. Автомобиле – дни на предприятии |
6604 |
6885 |
7470 |
108,5 |
7. Автомобиле – дни в работе |
3853 |
3917 |
4322 |
110,3 |
8. Автомобиле – дни в ремонте |
1376 |
1412 |
1461 |
103,5 |
9. Время пребывания в наряде, тыс. ч |
30,8 |
31,3 |
34,6 |
111 |
10. Коэффициент использования подвижного состава |
0,58 |
0,57 |
0,58 |
102 |
11. Коэффициент технической готовности |
0,79 |
0,795 |
0,804 |
101 |
Анализируя данные из таблицы 1.8, видим довольно высокие показатели, несмотря на то, что это не автотранспортное предприятие и транспорт используется лишь для удовлетворения собственных потребностей. Наметилась хорошая тенденция на обновление автопарка, если в 2005 г. это был 1 автомобиль, то в 2006 их уже 3. На 10% увеличилось количество автомобиле – дней в работе, т.е. повысилась занятость водителей. Незначительно повысились количество дней в ремонте, но существенного влияния на коэффициент использования подвижного состава и коэффициент технической готовности это не оказало.
1.9 Организация обслуживания и ремонта машин
В ПК СФ «Агровод» помимо оказания основных производственных услуг занимается самостоятельным обслуживанием и ремонтом имеющейся в предприятии техники.
Первоначально предприятие организовывалось как механизированная колонна, это подразумевало большое количество техники и ее обслуживание, так как ремонт и обслуживание на стороне привело бы к высокой себестоимости перевозок, что на первоначальном уровне являлось основной деятельностью. Благодаря изначально качественному проекту с расчетом количества ремонтов и полным обеспечением оборудованием, предприятие полноценно укомплектовано, но большая часть из него устарела, список оборудования мастерской (приложение 2) и список подъемно – транспортного оборудования (приложение 3).
В настоящее время комплексная система технического обслуживания и ремонта машин предусматривает три стратегии:
по потребности после отказа – С1;
регламентированная в зависимости от наработки (календарного времени) по сроку и содержанию ремонтно-обслуживающих воздействий – С2;
по состоянию с периодическим или непрерывным контролем (диагностированием) – С3.
Каждая их этих стратегий имеет свои преимущества и недостатки. При стратегии по потребности после отказа какой-либо составной части достигается полное использование ресурса машины и составляющих ее элементов. Но при этом снижется надежность (безотказность), увеличиваются простои машин по техническим причинам и связанные с этими простоями потери. При низкой надежности машины применение данной стратегии практически невозможно, так как поток отказов может парализовать работу в самый ответственный период. Сфера этой стратегии – устранение последствий случайных отказов, которые не удалось предотвратить.
Неприемлемо использование стратегии 1 для большинства операций технического обслуживания, носящих обязательный характер: замена масла, фильтрующих элементов, проверка уровня тормозной жидкости и др. Поэтому практически с начала механизации производства, работоспособность техники поддерживается на основе предупредительных стратегий обслуживания и ремонта: по регламенту С2 и по состоянию С3.
В первые годы доминировала планово-предупредительная стратегия назначения работ лишь в последние два-три десятилетия, по мере создания доступных средств диагностирования все большее распространение начала получать система назначения предупредительных ремонтно-обслуживающих работ по результатам оценки технического состояния. В целом система ТО и ремонта машин является планово-предупредительной.
Использование той или иной стратегии обусловливается большим количествам факторов, таких как безотказность машин, их стоимость, насыщенность парка, срочность работы, развитость системы технического сервиса, наличие и стоимость современных средств диагностирования, уровень подготовки кадров механизаторов и слесарей.
Обычно применяются все три стратегии технического обслуживания и ремонта. Например, замена перегоревшей лампочки – первая стратегия, замена моторного масла по достижении установленной наработки – вторая, регулирование клапана в двигателе по результатам заявочного диагностирования – третья.
На предприятии техническое обслуживание организовано по стратегии 2 и это объясняется:
во-первых, ее простотой и универсальностью, легкостью контроля за соблюдением принятых рекомендаций;
во-вторых, эффективностью групповых решений, дающих возможность получать относительно хорошие результаты.
Именно поэтому стратегия 2 оказалась столь привлекательной и используется на практике.
Техническое обслуживание машин выполняется при использовании их по назначению и хранении. Оно имеет целью систематический контроль технического состояния машин и выполнение работ для уменьшения скорости изнашивания элементов, предупреждения отказов и неисправностей, устранения замеченных неисправностей.
В период использования машин предусмотрены следующие виды технического обслуживания: ежесменное (ЕТО), плановые (ТО-1, ТО-2), сезонные (СО), для тракторов (ТО-3).
Проведение плановых ТО регламентировано для автомобилей по пробегу, для тракторов и прочей строительной техники в мото-ч. Ежедневное и первое плановые ТО проводятся непосредственно водителями при необходимости с привлечением слесарей. Второе и третье (для тракторов) проводятся слесарями с применением доступного диагностического оборудования, по части двигателя осмотр и прослушивание осуществляет моторист.
1.10 Организация работы нефтехозяйства
Одно из наиболее пожаро- и взрывоопасных мест в производстве связанным с обслуживанием транспорта является нефтехозяйство. Основные требования предъявляемые к планировочным нормам выполнены: склад построен в отдалении от основного производства с подветренной стороны.
Доставка нефтепродуктов осуществляется автоцистерной с раздаточным шлангом. Водитель по совместительству заправщик ведет учетную ведомость, где отмечает количество топлива полученного на нефтебазе. Жидкие смазки и масла доставляются на бортовых автомобилях и хранятся на территории склада, отработанные смазки и масла сдаются на нефтебазу для утилизации.
На предприятии имеются автомобили, работающие на бензине, но в связи с их малым числом закупать и хранить топливо для них не целесообразно, еще и потому что, организация находиться в черте города и проблем с топливом не испытывает. На этот случай у фирмы заключен договор с предприятием поставщиком о системе талонной оплаты топлива, т.е. водитель получает не живые деньги на заправку, а талоны которые предприятием заранее оплачены и заправляется на ближайшей бензоколонке «Удмуртнефтепродукт».
1.11 Обоснование темы проекта
Технический сервис – это комплекс работ и услуг по эффективному использованию техники, и поддержанию их в исправном состоянии в течение всего периода эксплуатации. Эксплуатация изделия включает в себя: использование по назначению, хранение, техническое обслуживание, ремонт. Целью технической эксплуатации машин является поддержание, сохранение и восстановление исправности, работоспособности и ресурса. Она включает выполнение работ по дозаправке машин топливом и смазочными материалами, очистке, регулированию, замене быстроизнашивающихся элементов машин, восстановлению их, проверке и диагностированию состояния машин и составных частей, определению остаточного ресурса, контролю воздействия на окружающую среду, восстановлению изношенных деталей, модернизация машин, находящихся в эксплуатации.
В условиях недостатка и ограниченного обновления машинно-тракторного парка на предприятиях существенно возрастает значение ремонтно-обслуживающего производства владельцев машин и всей ремонтно-обслуживающей базы. При ограниченном обновлении парка рациональное использование, бережное хранение, своевременные и качественные ремонтно-обслуживающие воздействия способны поддерживать численность и исправность машинно-тракторного парка.
Обеспечение высокой эффективности использования техники предопределяет необходимость своевременного применения комплекса воздействий, поддерживающих или восстанавливающих работоспособность машин. Эти воздействия достигают своей цели, если они осуществляется с применением современных технологий и прогрессивного ремонтно-технологического оборудования.
Целью данного проекта является внедрение диагностических операций для обеспечения углубленной оценки состояния машин и более качественного проведения ремонтов. Диагностика позволяет снизить расходы на ремонт и позволяет не допустить преждевременного выхода машины из строя.
На данном предприятии до сих пор используется система, по которой обслуживание проводиться исходя из наработки, данная система применима для организации ремонта при неизменных условиях, при постоянном качестве обслуживания, запасных частей и расходных материалов, т.е. почти что при идеальных условиях. При внедрении диагностики можно будет учитывать индивидуальные особенности автомобиля и условия его работы, а значит можно будет исключить некоторые ненужные в данном ТО операции тем самым, снизив трудоемкость обслуживания и ремонта. При этом значительно уменьшаться простои автомобилей в ремонте и на ТО.
2 Совершенствование технического обслуживания и ремонта автомобилей
2.1 Виды и периодичность технического обслуживания автомобилей
Знание и закономерность изменения параметров технического состояния узлов, агрегатов и автомобиля в целом позволяет управлять работоспособностью и техническим состоянием в процессе эксплуатации, то есть поддерживать и восстанавливать его работоспособность. Эти работы подразделяются на две большие группы – техническое обслуживание и ремонт. В нашей стране техническое обслуживание (ТО) автомобилей проводится на плановой основе, представляющую собой систему ТО, которая состоит из комплекса взаимосвязанных норм и положений, определяющих порядок работ ТО с целью обеспечения заданных показателей качества автомобилей в процессе эксплуатации.
ТО автомобилей, выполняемое на АТП, по периодичности, перечню и трудоемкости выполняемых работ делят на следующие виды: ежедневное ТО (ЕО); ТО – 1; ТО – 2; сезонное ТО (СТО).
Назначение ЕО: общий контроль, направленный на обеспечение безопасности движения; поддерживание внешнего вида автомобиля.
Назначение ТО-1, ТО-2: снижение интенсивности изменения параметров технического состояния механизмов и агрегатов автомобиля; выявление и предупреждение отказов и неисправностей путем проведения современных контрольно-диагностических, крепежных, регулировочных и других работ.
Целью сезонного технического обслуживания, проводимого два раза в год, является подготовка подвижного состава к эксплуатации при изменении сезона (времени года).
Дорожно-климатические условия влияют на периодичность ТО. Корректирование периодичности ТО автомобилей осуществляют в зависимости от категории условий эксплуатации. Каждая категория характеризуется типом дорожного покрытия или состоянием грунта, рельефом местности и условиями движения.
2.2 Организация технического обслуживания и диагностирования подвижного состава
На АТП ТО осуществляют на рабочих постах. В зависимости от числа ремонтных операций рабочие посты могут быть универсальными или специализированными. На универсальных постах выполняются все виды работ, кроме уборочно-моечных. На одном таком посту работает группа рабочих различных специальностей (слесарей, смазчиков, электриков) или рабочих универсалов. Все работы имеют определенную технологическую последовательность. При проведении ТО на специализированных постах весь объем работ распределяется между несколькими постами. Оборудование на специализированных постах предназначено для выполнения определенных операций. Обслуживаются такие посты рабочими соответствующих специальностей.
В зависимости от объема работ ТО автомобилей выполняют поточным или тупиковым методом. Организация ТО тупиковым методом (на универсальных тупиковых постах) целесообразна при различной продолжительности пребывания автомобиля на каждом посту. К недостаткам этого метода относятся значительные потери времени на установку автомобиля на пост и съезд с него, загрязнение воздуха отработавшими газами при маневрировании и необходимость использования большого числа одинакового оборудования.
Поточный метод организации ТО предусматривает выполнение работ на специализированных рабочих постах в определенной последовательности с заданным временем выполнения работ. Этот метод позволяет сократить потери времени на перемещение автомобилей и переход рабочих с одного поста на другой, а также более экономно использовать площадь производственного помещения. Недостатком поточного метода организации ТО является сложность изменения объема работ на рабочих местах.
Для перемещения автомобиля с поста на пост при поточном методе ТО используют конвейеры непрерывного и периодического действия. На поточных линиях непрерывного действия (автоматическая поточная линия) все работы выполняют на постоянно перемещающихся по рабочим постам автомобиля. Такие линии широко применяют для ЕО, при УМР. На поточных линиях периодического действия автомобили перемещают только с одного поста на другой, а все работы проводят на неподвижных автомобилях.
Операции по обслуживанию автомобилей выполняют в соответствии с постовыми технологическими операционными картами. В них указывают наименование операции, тех. условия и нормы времени на ее выполнение, применяемый инструмент и оборудование, специальность рабочего, пост выполнения операции и число точек обслуживания. Постовые технологические карты предназначены для выполнения работ по контролю регулировке и смазыванию агрегата или узла.
При ТО автомобилей на поточных линиях заполняют карту – схему расстановки рабочих на постах. Карта – схема содержит информацию о числе рабочих, производительности линии обслуживания за смену и данные постовых технологических карт.
Организация производства ТО может быть бригадной или бригадно-участковой. При бригадной форме организации бригады выполняют работы по всем агрегатам машины в пределах данного вида обслуживания. При бригадно-участковой форме организации ТО на отдельных производственных участках выполняются все работы по обслуживанию соответствующих агрегатов. В зависимости от программы работ АТП устанавливают различное число производственных участков разного назначения. При небольшой программе работ АТП возможно обслуживание нескольких видов агрегатов на одном участке.
Во всех АТП участки или бригады можно для удобства управления объединить в производственные комплексы по следующим видам работ: техническому обслуживанию машин и диагностированию их технического состояния; текущему ремонту непосредственно на автомобилях; текущему ремонту агрегатов, узлов и деталей, снятых с автомобилей.
По времени проведения диагностирование бывает периодическое и непрерывное. Периодическое диагностирование осуществляют через определенный пробег автомобиля. Непрерывное проводится водителем постоянно в процессе эксплуатации машины.
В зависимости от решаемых задач диагностирование делят на два вида: Д-1 и Д-2. При диагностировании Д-1, выполняемом, как правило, перед ТО-1 и в процессе его проведения, определяют техническое состояние агрегатов и узлов, обеспечивающих безопасность движения и пригодность автомобиля к эксплуатации.
При диагностировании Д-2, выполняемом, как правило, перед ТО-2, оценивается техническое состояние агрегатов, узлов, систем автомобиля, уточняются объем работ ТО-2 и потребность в ремонте.
2.3 Расчет производственной программы предприятия
На предприятии имеется разного вида техника, и для удобства расчета [2] разбиваем ее на технологически совместимые группы, таковых получается 3:
1. Легковые автомобили;
2. Автомобили марок ГАЗ, ЗИЛ;
3. Автомобили марок МАЗ, КАМАЗ, КрАЗ.
По каждой группе находим исходные данные и обозначаем соответственно номеру группы.
Исходные данные по первой группе:
Количество автомобилей – 9;
Пробег с начала эксплуатации в долях от Lкр
:
менее 0,5 А1
= 44% (4 автомобиля)
0,5 … 0,75 А2
= 22% (2 автомобиля)
0,75 … 1 А3
= 12% (1 автомобиль)
более 1 А4
= 22% (2 автомобиля)
Кол-во автомобилей прошедших капремонт А′′u
= 22% (2 автомобиля).
Среднесуточный пробег lсс
= 58 км.
Исходные данные по второй группе:
Количество автомобилей – 7;
Пробег с начала эксплуатации в долях от Lкр
:
менее 0,5 А1
= 14% (1 автомобиль)
более 1 А4
= 86% (6 автомобилей)
Кол-во автомобилей прошедших капремонт А′′u
= 86% (6 автомобилей).
Среднесуточный пробег lсс
= 46 км.
Исходные данные по третьей группе:
Количество автомобилей – 14;
Пробег с начала эксплуатации в долях от Lкр
:
менее 0,5 А1
= 36% (5 автомобилей)
0,5 … 0,75 А2
= 36% (5 автомобилей)
0,75 … 1 А3
= 14% (2 автомобиля)
более 1 А4
= 14% (2 автомобиля)
Кол-во автомобилей прошедших капремонт А′′u
= 14% (2 автомобиля).
Среднесуточный пробег lсс
= 60 км.
Общие для всего парка данные:
Кол-во рабочих дней в году – 253
Средняя продолжительность смены – 8 часов
Количество смен – 1
2.3.1 Расчет годового пробега парка
Цель корректирования – приведение нормативных величин к конкретным условиям работы автотранспортного предприятия.
Корректирование нормы межремонтного пробега выполняем по формуле:
Lкр
= Lкрн
∙К (2.1)
где Lкр
– скорректированный пробег до капитального ремонта;
Lкрн
– нормативный пробег до капитального ремонта;
К – общий коэффициент корректирования.
Lкрн
в км принимаем по (26, табл. 2.3).
Lкр1
= 100 000×0,54 = 54 000 (км)
При выборе обращаем внимание на то, что нормативный пробег принимается для базовой модели подвижного состава и принимается по автомобилю, а не по агрегатам.
Общий коэффициент корректирования, одинаковый для всех групп, рассчитываем по формуле:
К = К1
∙ К2
∙ К3
(2.2)
где К1
– коэффициент корректирования нормативов в зависимости от категории условий эксплуатации;
К2
– коэффициент корректирования нормативов в зависимости от модификации подвижного состава и способа организации его работы;
К3
– коэффициент корректирования нормативов в зависимости от природно-климатических условий.
К = 0,6×1,0×0,9 = 0,54
К1
выбираем по категории условий эксплуатации в нашем случае это город Ижевск т. к. в нем более 100 000 жителей то категория условий классификации 4, а значение К1
в (26, табл. 2.8), 0,6.
Для выбора К2
воспользуемся (26, табл. 2.9) получаем 1,0.
Для выбора К3
необходимо знать климатический район эксплуатации подвижного состава. Климатическое районирование приведено в (26, прил. 11). После определения климатического района воспользуемся (26, табл. 2.10) для выбора коэффициента К3
= 0,9.
При выборе К3
также обращаем внимание на возможное наличие высокой агрессивности окружающей среды.
Суммарный расчетный коэффициент К должен быть не менее 0,5. Если расчетный получается меньше, то принимается К = 0,5.
Скорректированный пробег до капитального ремонта рассчитываем с точностью до целых сотен километров.
После принятия нормативных величин и приведения примера результаты расчета по остальным группам заносим в таблицу 2.1
Средний пробег до капитального ремонта.
Поскольку все автомобили на АТП имеют различный пробег с начала эксплуатации, то рассчитываем средневзвешенную норму межремонтного пробега по формуле:
Lкрс
= (2.3)
где Lкрс
– средний расчетный пробег до капитального ремонта;
А′u
– число автомобилей не прошедших капитальный ремонт;
А″u
– число автомобилей, прошедших капитальный ремонт.
А′u
и А″u
принимаем по фактическому пробегу в задание
Точность расчета – до целых сотен километров.
Lкрс1
= =
51,6 (тыс. км)
После приведения примера расчета результаты заносим в таблицу 2.1
Корректирование удельного простоя в техническом обслуживании и ремонте выполняем по формуле:
dтор
= dторн
∙ К′4ср
(2.4)
где dтор
– скорректированный удельный простой в ТО и ремонте;
dторн
– нормативный удельный простой в ТО и ремонте;
К′4
c
р
– средний расчетный коэффициент корректирования.
Средний расчетный коэффициент корректирования рассчитываем по формуле:
К′4ср
= (2.5)
где А1
, А2
, Аn
– количество автомобилей в интервале пробега, для которого принимается значение коэффициента К4
′ (см. исходные данные и (26, табл. 2.11));
К′1
4
, К′n
4
– коэффициент корректирования, учитывающий пробег с начала эксплуатации.
К′4
принимаем по (26, табл. 2.11)
dторн
принимаем по (26, табл. 2.6).
К′4ср1
= =
0,99
dтор1
= 0,35 × 0,99 = 0,35 (дн/1000 км)
После приведения расчета, результаты расчета сводим в таблицу 2.1
Расчет коэффициента технической готовности выполняем по формуле:
αт
= Дэ
/(Дэ
+ Дтор
+ Дкр
) (2.6)
где αт
– расчетный коэффициент технической готовности;
Дэ
– дни эксплуатации в цикле;
Дтор
– дни простоя за цикл в ТО и ремонте;
Дкт
– дни отсутствия авто на АТП по причине кап. ремонта.
Дни эксплуатации в цикле рассчитываем по формуле:
Дэ
= Lкрс
/1сс
(2.7)
где 1сс
– среднесуточный пробег.
Дэ1
= 51600/58 = 890 (дней)
Обращаем внимание на размерность подставляемых величин, она должна быть однозначной.
Дни простоя в ТО и ремонте рассчитываем по формуле:
Дтор
= dтор
∙ Lкр
/1000 (2.8)
Размерность величин в формуле: [dтор
] = дн/1000 км, Lкр
км.
Дтор1
= 0,35∙ 54000/1000 = 19 (дней)
Расчетные значения дней эксплуатации и дней простоя в ТО и ремонте должны иметь целое значение.
Дни отсутствия автомобилей на АТП по причине нахождения на капитальном ремонте:
Дкр
= dкр
+ dтран
(2.9)
где dкр
– дни нахождения авто на капитальном ремонте на спец. АРЗ;
dтран
– дни транспортировки авто на кап. ремонте.
dтран
= (0,15…0,20) · dкр
(2.10)
dкр
принимаем по (26, табл. 2.6)
Дкр1
= 18+ 0,2×18 = 27
αт1
= 890/(890 + 27 + 19) = 0,95
После расчета по одной группе, результаты сводим в таблицу 2.1
Коэффициент выпуска автомобилей рассчитывается по формуле:
αи
= Дрг
· αт
· Ки
/365 (2.11)
где αи
– коэффициент выпуска автомобилей;
Дрг
– дни работы в году авто на линии;
Ки
– коэффициент внеэксплуатационного простоя.
Коэффициент внеэксплуатационного простоя характеризует организацию работы подвижного состава и учитывает простой по причине отсутствия водителей, отсутствия работы, простоя без топлива, по причине бездорожья и т.д.
Принимаем Ки
= 0,95
Дрг
– 253 дней
αи1
= 253 × 0,95 × 0,95 /365 = 0,626
Коэффициенты рассчитываем с точностью до тысячных.
По остальным группам расчет ведется аналогично, результаты оформляем в таблицу 2.1
Расчет годового пробега по марке подвижного состава производится по формуле:
Lг
= 365 ∙ Аи
· 1сс
· αи
(2.12)
где Аи
– списочное число подвижного состава.
Lг1
= 365 × 9 × 58 × 0,626 = 119300 (км)
Расчет годового пробега ведем с точностью до целых сотен километров.
По остальным группам расчет аналогичный, результаты в таблице 2.1
Таблица 2.1 – Расчет и корректирование годового пробега автопарка
Показатели |
1 группа |
2 группа |
3 группа |
Lкрн
, тыс. км. |
100 |
150 |
300 |
Lкр
, тыс. км. |
54 |
81 |
162 |
А′u
|
7 |
1 |
12 |
А″u
|
2 |
6 |
2 |
Lкрс
, тыс. км. |
51,6 |
67,1 |
157,4 |
А1
|
К′4
|
4 |
0,7 |
1 |
0,7 |
5 |
0,7 |
А2
|
К′4
2
|
2 |
1 |
0 |
1 |
5 |
1 |
А3
|
К′4
3
|
1 |
1,3 |
0 |
1,2 |
2 |
1,2 |
А4
|
К′4
4
|
2 |
1,4 |
6 |
1,3 |
2 |
1,3 |
К′4ср
|
0,99 |
1,21 |
0,96 |
dторн
, дн/1000 км. |
0,35 |
0,45 |
0,5 |
dтор
, дн/1000 км. |
0,35 |
0,54 |
0,48 |
1сс
, км. |
58 |
46 |
60 |
Дэ
, дн. |
890 |
1459 |
2623 |
Дтор
, дн. |
19 |
44 |
78 |
Дкр
, дн. |
27 |
23 |
33 |
dтран
, дн. |
9 |
8 |
11 |
dкр
, дн. |
18 |
15 |
22 |
αт
|
0,95 |
0,96 |
0,96 |
αи
|
0,626 |
0,632 |
0,632 |
Lг
, тыс. км. |
119,3 |
74,3 |
193,8 |
2.3.2 Расчет производственной программы по техническому обслуживанию
Цель раздела – рассчитать производственную программу для объекта проектирования по техническому обслуживанию, диагностике и определить количество обслуживаний для расчета трудоемкости работ.
Расчет количества уборочно-моечных работ.
Количество ежедневных обслуживаний рассчитывается по автомобилям.
Nео
= Lг
/1сс
(2.13)
где Nео
– годовое количество ежедневных обслуживаний.
Nео1
= 119300/58 = 2057
Годовое количество уборочно-моечных работ не совпадет с годовым количеством ежедневных обслуживаний.
Количество УМР за год следует рассчитать по формулам (2.14, 2.15):
– для легковых автомобилей
Nумр
= (1,10– : – 1,15) ∙ Neo
(2.14)
где Nумр
– годовое количество уборочно-моечных работ.
Nумр1
= 1,1 ∙ 2057 = 2263
– для грузовых автомобилей
Nумр
= (0,75– : – 0,80) · Nео
, (2.15)
Nумр2
= 0,8 · 1615 = 1292
Сменная программа уборочно-моечных работ, для ее расчета воспользуемся формулой:
Nумс
= Nумр
/(Дргу
· Ссм
) (2.16)
где Nумс
– сменная программа уборочно-моечных работ.
Дргу
– количество дней работы в году зоны УМР. (Задаемся с учетом дней работы в году авто на линии).
Ссм
– число смен работы за сутки зоны уборочно-моечных работ, в нашем случае 1.
Nумс1
= 2263/(253· 1) = 9
После приведения примера, результаты расчета сводим в таблицу 2.2
Корректирование периодичности технического обслуживания.
Корректирование периодичности ТО-1 выполняем по формуле:
L1
= L1н
· К1
· К3
(2.17)
где L1
– скорректированная периодичность ТО-1.
L1н
– нормативная периодичность ТО-1, принимаем по (26, табл. 2.1)
L11
= 4000 · 0,6 · 0,9 = 2160
Корректирование периодичности ТО-1 по кратности к среднесуточному пробегу.
n1
= L1
/lcc
(2.18)
где n1
– коэффициент кратности периодичности ТО-1 к среднесуточному пробегу.
n11
= 2160/58 = 37,24 ≈ 37
Коэффициент кратности рассчитывается с точностью до сотых, с последующим округлением до целого значения.
Расчетная периодичность ТО-1
L1
p
= 1cc
· n1
(2.19)
где L1
p
– расчетная периодичность ТО-1.
Расчетная периодичность ТО-1 округляется до целых сотен километров.
L1
p
1
= 58 · 37 = 2146 ≈ 2200
Результаты расчета оформляем в таблицу 2.3
Корректирование периодичности ТО-2.
Корректирование выполняем по формуле:
L2
= L2н
· K1
· K3
(2.20)
где L2
– скорректированная периодичность ТО-2.
L2н
– нормативная периодичность ТО-2, принимаем по (26, табл. 2.1)
L21
= 16000 · 0,6 · 0,9 = 8640
Корректирование периодичности ТО-2 по кратности к периодичности ТО-1.
n2
= L2
/L1р
(2.21)
где n2
– коэффициент кратности периодичности ТО-2 к периодичности ТО-1.
n21
= 8640/2200 = 3,93 ≈ 4
Расчетная периодичность ТО-2.
L2р
= L1р
· n2
(2.22)
где L2р
– расчетная периодичность ТО-2.
Расчетная периодичность ТО-2 округляется до целых сотен километров
L2р1
= 2200 · 4 = 8800
Результаты расчета оформляем в таблицу 2.3
Расчет производственной программы по техническому обслуживанию.
Годовое количество ТО-2 рассчитывается по формуле:
N2
= Lг
/L2р
(2.23)
где N2
– годовое количество ТО-2.
N21
= 119300/8800 = 13,6 ≈ 14
Годовое количество ТО-1 рассчитываем по формуле:
N1
= Lг
/L1р
– N2
(2.24)
где N1
– годовое количество ТО-1.
N11
= 119300/2200 – 14 = 40,2 ≈ 40
Рассчитываем сменную программу.
Техническое обслуживание №1
N1с
= N1
/(Дрт
· Сст
) (2.25)
где N1с
– сменная программа по ТО-1.
Дрт
и Сст
задаемся исходя из дней работы в году авто на линии, авторемонтной мастерской и обеспечения выполнения работ в межсменное время.
В нашем случае режим работы 253 дня в году и 1 смена в сутки.
N1с1
= 40/(253· 1) = 0,16
Техническое обслуживание №2.
N2с
= N2
/(Дрт
· Сст
) (2.26)
где N2с
– сменная программа по ТО-2.
В зоне ТО-2 режим работы 253 дня в году и 1 смена.
N2с1
= 14/(253 · 1) = 0,06
На основании сменной программы по ТО необходимо определиться со способом организации выполнения работ.
В нашем случае при сменной программе технических обслуживаний №1 не превышающих 1 обслуживания в 2 дня по автопарку не целесообразно использовать поточную линию, в случае с ТО №2 обслуживаний еще меньше, и это значит, что поточную линию использовать не стоит. На предприятии лучше всего применять метод универсальных постов, это связано с разномарочностью подвижного состава и небольшой производственной программы.
Результаты расчета производственной программы по техническому обслуживанию сводим в таблицу 2.3
Расчет годового количества сезонных обслуживаний выполняем по формуле:
Nсо
= 2 · Аи
(2.27)
где Nсо
– годовое количество сезонных обслуживаний.
Nсо1
= 2 · 9 = 18
Расчет программы работ на постах поэлементной диагностики.
Nд2
= 1,2 · N2
(2.28)
где Nд2
– годовая программа по Д-2.
Число обслуживаний рассчитывается по автомобилям.
Nд21
= 1,2 · 14 = 16,8
Сменная программа на постах Д-2
Nд2с
= Nд2
/(Дрд
·Ссд
) (2.29)
где Nд2с
– сменная программа работ по Д-2.
Дрд
– число дней работы в году постов Д-2, 253 дня.
Ссд
– число смен работы в сутки постов Д-2, 1 смена.
Nд2с1
= 16,8/(253 ·1) = 0,07
После приведения примера, результаты сводим в таблицу 2.4
Расчёт программы работ на постах общей диагностики.
Годовое количество обслуживаний на постах Д-1.
Nд1
= 1.1 · N1
+ N2
(2.30)
где Nд1
– годовая программа по Д-1.
Nд11
= 1.1 · 40+ 14 = 58
Сменная программа на постах Д-1
Nд1с
= Nд1
/(Дрд
· Ссд
) (2.31)
где Nд1с
– сменная программа работ по Д-1
Дрд
– число дней работы в году постов Д-1.
Ссд
– число смен работы в сутки постов Д-1.
На нашем предприятии принимаем число дней работы 253, и количество смен 1.
Nд1с1
= 58/(253 · 1) = 0,23
Результаты расчетов по остальным группам, приводим в таблице 2.4
2.3.3 Корректирование трудоёмкости технического обслуживания
Корректирование трудоемкости ежедневного обслуживания.
tео
= tеон
· К2
· К5
(2.32)
где tео
– скорректированная трудоемкость ЕО.
tеон
– нормативная трудоемкость ЕО.
К5
– коэффициент учитывающий размеры АТП и число технологически совместимых групп п/состава.
tеон
принимаем по (26, табл. 2.2)
К5
принимаем по (26, табл. 2.12)
tео1
= 0,35· 1,0· 1,05 = 0,37
Результаты корректирования оформляем в таблицу 2.2
Расчет трудоемкости уборочно-моечных работ.
Трудоемкость работ ежедневного обслуживания включает в себя уборочные, моечные и обтирочные работы, на данном предприятии выполняемые вручную 100% без применения механизации.
Трудоемкость работ при использовании механизации рассчитывается по формуле:
tумр
= tео
· Пр (2.33)
где tумр
– трудоемкость уборочно-моечных работ.
Пр – процент работ выполняемых вручную.
Как видим из формулы при 100% ручном выполнении уборочно-моечных работ, их трудоемкость численно равна трудоемкости ежедневного обслуживания.
Для распределения рабочих в организационной части проекта необходимо знать процент работ каждого вида выполняемых ручным способом.
Результаты расчета трудоемкости и примерное распределение ручных работ приведены в таблице 2.2
Корректирование трудоемкости технического обслуживания №1 выполняем по формуле:
t1
= t1н
· К2
· К5
(2.34)
где t1
– скорректированная трудоемкость ТО-1.
t1н
– нормативная трудоемкость ТО-1.
К5
– коэффициент, учитывающий размеры АТП и количества технологически совместимых групп п/состава.
t1н
принимаем по (26, табл. 2.2)
t11
= 2,5 · 1 · 1,05 = 2,63
После приведения примеров корректирования результаты расчета сводим в таблицу 2.3
Корректирование трудоемкости технического обслуживания №2 выполняем по формуле:
t2
= t2н
· К2
· К5
(2.35)
где t2
– скорректированная трудоемкость ТО-2.
t2н
– нормативная трудоемкость ТО-2, (26, табл. 2.2).
t21
= 10,5 · 1· 1,05 = 11,03
Результаты расчета оформим в таблицу 2.3
Трудоемкость дополнительных работ сезонного обслуживания рассчитываем по формуле:
tco
= Cco
· t2
(2.36)
где tсо
– трудоемкость дополнительных работ сезонного обслуживания.
Ссо
– процент дополнительных работ по сезонному обслуживанию от трудоемкости ТО-2, (26, п. 2.11.2).
Нормативы трудоемкости СО составляют от трудоемкости ТО-2: 30% для холодного и жаркого сухого районов (26, п. 2.11.2)
tco
1
= 0,2 · 11,03 = 2,21
Результаты расчета вносим в таблицу 2.3
Корректирование трудоемкости общей диагностики выполняем по формуле:
tд1
= tд1н
· К2
· К5
(2.37)
где tд1
– скорректированная трудоемкость Д-1.
tд1н
– нормативная трудоемкость Д-1. (2, прил. 3)
tд11
= 0,32 · 1 · 1,05 = 0,34
Результаты корректирования приведены в таблице 2.4
Корректирование трудоемкости поэлементной диагностики выполняем по формуле:
tд2
= tд2н
· К2
· К5
(2.38)
где tд2
– скорректированная трудоемкость Д-2.
tд2н
– нормативная трудоемкость Д-2. (2, прил. 4).
tд21
= 1,72 · 1 · 1,05 = 1,81
После корректирования результаты расчета оформлены в таблицу 2.4
2.3.4 Расчет годовой трудоемкости работ
Ежедневное обслуживание.
Годовую трудоемкость уборочно-моечных работ рассчитываем по формуле:
Тумр
= tумр
· Nумр
(2.39)
где Тумр
– годовая трудоемкость уборочно-моечных работ.
Тумр1
= 0,37 · 2263 = 837,3
По остальным группам расчет аналогичный, результаты в таблице 2.2
Общая диагностика.
Годовую трудоемкость общей диагностики рассчитываем по формуле:
Тд1
= tд1
· Nд1
(2.40)
где Тд1
– годовая трудоемкость общей диагностики.
Тд1
= 0,34· 58 = 19,7
По остальным группам расчет аналогичный, результаты в таблице 2.4
Поэлементная диагностика.
Годовую трудоемкость поэлементной диагностики рассчитываем по формуле:
Тд2
= tд2
· Nд2
(2.41)
где Тд2
– годовая трудоемкость поэлементной диагностики.
Тд21
= 1,81· 16,8 = 30,4
После приведения примера расчета, результаты по остальным группам сводим в таблицу 2.4
Годовая трудоемкость ТО-1
Годовую трудоемкость ТО-1 рассчитываем по формуле:
Т1
= t1
· N1
(2.42)
где Т1
– годовая трудоемкость ТО-1.
Т11
= 2,63· 40 = 105,2
Результаты по остальным группам п/состава вычисляются аналогично, результаты в таблице 2.3
Годовая трудоемкость ТО-2 и сезонного обслуживания.
Годовую трудоемкость ТО-2 рассчитываем по формуле:
Т2
= t2
· N2
(2.43)
где Т2
– годовая трудоемкость ТО-2.
Т21
= 11,03 · 14 = 154,4
Годовую трудоемкость сезонного обслуживания рассчитываем по формуле:
Тсо
= tco
· Nco
(2.44)
где Тсо
– годовая трудоемкость дополнительных работ по сезонному обслуживанию.
Тсо
= 2,21 · 18 = 39,8
После приведения примеров расчета результаты по остальным группам п/состава сводим в таблицу 2.3
2.3.5 Расчет годовой трудоемкости работ зон ТО-1 и ТО-2
Зона технического обслуживания №1.
Трудоемкость работ в зоне ТО-1 рассчитываем по формуле:
Т13
= с · Т1
– Тд1
+ Тco
п1
(2.45)
где Т1
– годовая трудоемкость работ в зоне ТО-1.
с – коэффициент, учитывающий способ организации выполнения работ в зоне ТО-1.
Тсоп1
– трудоемкость сопутствующего текущего ремонта, выполняемого в зоне ТО-1.
с = 1 при организации производства ТО-1 без применения поточной линии.
Тсоп1
= 0,20 · Т1
(2.46)
Т131
= 1 · 105,2 – 19,7 + 0,2 · 105,2 = 106,5
Приводим пример расчета, и результаты оформляем в таблицу 2.3
Зона технического обслуживания №2.
Трудоемкость работ в зоне ТО-2 рассчитывается по формуле:
Т23
= с · (Т2
+ Тсо
) – Тд2
+ Тсоп2
(2.47)
где Т2
– годовая трудоемкость работ в зоне ТО-2.
с – коэффициент, учитывающий способ организации выполнения работ в зоне ТО-2.
Тсоп2
– трудоемкость сопутствующего текущего ремонта, выполняемого в зоне ТО-2.
с = 1 при организации производства ТО-2 без применения поточной линии.
Тсоп2
= 0,20 · (Т2
+ Тсо
) (2.48)
Т231
= 1 · (154,4 + 39,8) – 30,4 + 0,2 · (154,4 + 39,8) = 202,6
Остальные группы рассчитываются аналогично, результаты сведены в таблицу 2.3
Таблица 2.2 – Расчет программы УМР
Показатели |
1 группа |
2 группа |
3 группа |
Всего за год |
Nео
|
2057 |
1615 |
3230 |
6902 |
Nумр
|
2263 |
1292 |
2584 |
6139 |
Nумс
|
9 |
5 |
10 |
- |
tеон
, чел. ч |
0,35 |
0,45 |
0,4 |
- |
tео
, чел. ч |
0,37 |
0,47 |
0,42 |
- |
% ручных работ в т.ч. |
100 |
100 |
100 |
- |
уборочные |
30 |
23 |
23 |
- |
моечные |
55 |
65 |
65 |
- |
обтирочные |
15 |
12 |
12 |
- |
tумр
, чел. ч |
0,37 |
0,47 |
0,42 |
- |
Tумр
, чел. ч |
837,3 |
607,2 |
1085,3 |
2529,8 |
Таблица 2.3 – Расчет программы технического обслуживания
Показатели |
1 группа |
2 группа |
3 группа |
Всего за год |
L1н
, км. |
4000 |
3000 |
3000 |
- |
n1
|
37 |
35 |
27 |
- |
L1р
, км. |
2200 |
1600 |
1600 |
- |
N1
|
40 |
34 |
91 |
165 |
N1с
|
0,16 |
0,13 |
0,36 |
- |
t1н
, чел. ч |
2,5 |
2,7 |
3,2 |
- |
t1
, чел. ч |
2,63 |
2,84 |
3,36 |
- |
T1
, чел. ч |
105,2 |
96,6 |
305,8 |
507,6 |
Tсоп1
, чел. ч |
21 |
19,3 |
61,2 |
- |
T13
, чел. ч |
106,5 |
76,9 |
238,2 |
421,6 |
L2н
, км. |
16000 |
12000 |
12000 |
- |
n2
|
4 |
4 |
4 |
- |
L2р
, км. |
8800 |
6400 |
6400 |
- |
N2
|
14 |
12 |
30 |
56 |
N2с
|
0,06 |
0,05 |
0,12 |
- |
t2н
, чел. ч |
10,5 |
10,8 |
12 |
- |
t2
, чел. ч |
11,03 |
11,34 |
12,6 |
- |
T2
, чел. ч |
154,4 |
136,1 |
378 |
668,5 |
Tсоп2
, чел. ч |
38,8 |
33,6 |
89,7 |
- |
T23
, чел. ч |
202,6 |
163,3 |
458,4 |
824,3 |
Nсо
|
18 |
14 |
28 |
60 |
tсо
, чел. ч |
2,21 |
2,27 |
2,52 |
- |
Tсо
, чел. ч |
39,8 |
31,8 |
70,6 |
142,2 |
Таблица 2.4 – Расчет программы диагностики
Показатели |
1 группа |
2 группа |
3 группа |
Всего за год |
Nд1
|
58 |
49,4 |
130,1 |
237,5 |
Nд1с
|
0,23 |
0,2 |
0,51 |
- |
tд1н
, чел. ч |
0,32 |
0,75 |
0,95 |
- |
tд1
, чел. ч |
0,34 |
0,79 |
0,99 |
- |
Tд1
, чел. ч |
19,7 |
39 |
128,8 |
187,5 |
Nд2
|
16,8 |
14,4 |
36 |
67,2 |
Nд2с
|
0,07 |
0,06 |
0,14 |
- |
tд2н
, чел. ч |
1,72 |
2,52 |
2,11 |
- |
tд2
, чел. ч |
1,81 |
2,65 |
2,22 |
- |
Tд2
, чел. ч |
30,4 |
38,2 |
79,9 |
148,5 |
2.3.6 Расчет годовой трудоемкости текущего ремонта
Корректирование удельной трудоемкости текущего ремонта.
Корректирование выполняем по формуле:
tтр
= tтрн
· К1
· К2
· К3
· К4ср
· К5
(2.49)
где tтр
– скорректированная удельная трудоемкость ТР.
tтрн
– нормативная удельная трудоемкость ТР.
К1-5
– коэффициенты корректирования.
Принимаем значения нормативных величин по:
tтрн
(26, табл. 2.2)
К1
, К2
, К3
, К5
соответственно в (26, табл. 2.8, 2.9, 2.10, 2.12) и получаем, 0,6; 1; 0,9; 1,05.
К4ср
рассчитывается аналогично К′4ср
.
tтр
= 3 · 0,6 · 1 · 0,9 · 0,99 · 1,05 = 1,7
Результаты корректирования приведены в таблице 2.5
Годовую трудоемкость работ по текущему ремонту рассчитываем по формуле:
Ттр
= tтр
· Lг
/1000 (2.50)
где Ттр
– годовая трудоемкость работ текущего ремонта.
Ттр1
= 1,7 · 1193000/1000 = 202,8
Расчеты по другим группам аналогичны, результаты в таблице 2.5
Годовую трудоемкость работ в зоне ТР рассчитываем по формуле:
Ттр3
= Сз
· Ттр
– Тсоп1
– Тсоп2
(2.51)
где Ттр
– годовая трудоемкость работ в зоне ТР.
Сз
– процент работ ТР, выполняемых в зоне ТР.
Принимаем по [2] равный 60%.
Ттр3
= 0,6 · 202,8 – 21– 38,8 = 61,9
Пример расчета и результаты по остальным группам в таблице 2.5
Таблица 2.5 – Расчет программы текущего ремонта
Показатели |
1 группа |
2 группа |
3 группа |
Всего за год |
tтрн
, чел. ч/1000 км. |
3 |
4 |
5,8 |
- |
tтр
, чел. ч/1000 км. |
1,7 |
2,7 |
3,2 |
- |
Tтр
, чел. ч |
202,8 |
200,6 |
620,2 |
1023,6 |
Tтр3
, чел. ч |
61,9 |
67,5 |
221,2 |
350,6 |
2.3.7 Расчет численности производственных рабочих
При расчете численности производственного персонала различают явочное или технологически необходимое – Рт
и Рш
число исполнителей.
Явочное число рабочих (число рабочих мест).
Рт
= Тдт
/Фрм
(2.52)
где Рт
– число рабочих мест;
Тдт
– годовой объем работ ТО и диагностики (трудоемкость);
Фрм
– годовой фонд времени рабочего места.
Т1
принимается по предыдущим расчетом для зоны поэлементной диагностики Д2
.
При пятидневной рабочей неделе
Фрм
= Тсм
· (Дкг
– Дв
– Дп
) (2.53)
где Тсм
– продолжительность рабочей смены, при пятидневной Тсм
= 8 ч.
Дкг
– число календарных дней в году;
Дв
– число выходных дней в году;
Дп
– число праздничных дней в году;
Фрм
= 8 · (365 – 105 – 7) = 2024
Рт
= 1724,1/2024 = 0,85
Штатное число исполнителей.
Рш
= Тдт
/Фэр
(2.54)
где Рш
– численность штатных рабочих;
Тдт
– годовой объем работ ТО и диагностики (трудоемкость);
Фэр
– эффективный годовой фонд времени штатного рабочего.
Фэр
принимаем согласно рекомендации (2, стр. 30)
Рш
= 1724,1/1840 = 0,94
По расчетам получилось, что при таком маленьком автопарке на проведение всех операций диагностики и технического обслуживания необходим один слесарь, но мы принимаем 2 человека, т. к. большинство операций невозможно производить в одиночку. Один из слесарей должен знать приемы производства диагностических операций.
2.3.8 Расчет количества постов в зонах технического обслуживания
Расчет числа постов зоны технического обслуживания.
Расчет основного числа постов выполняем по формуле:
Nто
= τп
/R (2.55)
где Nто
– расчетное число основных постов зоны ТО;
τп
– такт поста;
R – ритм производства.
Такт поста, т.е. время обслуживания авто на посту, рассчитывается по формуле:
τп
= + tп
(2.56)
где Тi
– годовой объем работ в зоне ТО
Ni
– годовая программа работ в зоне ТО
Рп
– среднее число исполнителей одновременно работающих на посту.
tп
– время установки и снятия автомобиля на пост.
Среднее число исполнителей на посту рекомендуется принять для зон ТО Рп
= 2 исполнителя.
Время на установку и перемещение авто по постам принимается tп
= 2 мин.
Ритм производства, т.е. время полного обслуживания авто, рассчитывается по формуле:
R = (2.57)
где Тсм
– продолжительность работы зоны ТО в смену, час;
Ссм
– число смен работы зоны ТО в смену;
Ni
см
– сменная программа по соответствующему виду обслуживания.
Количество постов в зоне ТО – 1 рассчитываем с учетом операции связанных с диагностикой в зоне ТО – 1.
τп1
= + 2 = 53,8
R1
= = 302
Nто-1
= 53,8/302 = 0,18
Количество постов в зоне ТО – 2 рассчитываем с учетом операции связанных с диагностикой в зоне ТО – 2.
τп2
= + 2 = 201
R2
= = 960
Nто-2
= 201/960 = 0,21
Число постов подпора для зон техобслуживания принимаем[2]:
15% сменной программы ТО-1
40% сменной программы ТО-2.
Общее число постов зоны ТО определяется суммированием основного числа постов и постов подпора.
Nто-1
= 0,18+1,59×0,15 = 0,42
Nто-2
= 0,21+0,5×0,4 = 0,41
Целесообразнее всего обслуживания и диагностики проводить на совмещенном посту для полной занятости рабочих. В имеющейся планировке лучше всего последовательно расположить два поста: совмещенный пост ТО-1 и сопутствующей диагностики; совмещенный пост ТО-2 и сопутствующей диагностики. На этих постах будет занято 2 человека, один из которых мастер – диагност, другой слесарь по техническому обслуживанию.
2.3.9 Расчет производственной площади совмещенного участка технического обслуживания и диагностики
Предварительная площадь производственных помещений зон ТО и постов диагностики рассчитывается по площади в плане наибольшего автомобиля по формуле:
F = Fa
· N · Kп
, (2.58)
где: F – расчетная площадь зоны (ТО и Д), м2
.
Fa
– площадь наибольшего авто в плане.
N – количество постов в зоне, принимаем 2.
Кп
– коэффициент плотности расстановки постов.
При одностороннем расположении постов [2] Кп
= 6,5;
F = 7,9×2,5×2×6,5 = 256,75
Окончательные размеры ширины и длины зоны уточняем по шагу колонн и пролетам помещения. Ширина помещения 9 м, необходимо определить длину участка.
L = F/B = 256,75 / 9 = 28,53
Принимаем ширину участка кратную 6 в нашем случае 30 м, тогда окончательная площадь участка равна
F = 9×30 = 270 (м2
)
2.3.10 Подбор технологического оборудования
В большинстве случаев оборудование, оснастку, необходимую для выполнения работ на постах ТО и диагностики, подбирают по технологической необходимости, так как они используются периодически. Поэтому никакого расчета в подборе оборудования нет.
При выборе оборудования руководствуемся следующими принципами:
– обеспечение выполнения работ по диагностике и ТО в полном объеме;
– обеспечение всех исполнителей рабочими местами и объемом работ.
Другими словами, необходимо оборудование подобрать так, чтобы выполнить любые работы по ТО и диагностике для заданного парка подвижного состава и в тоже время обеспечить всех исполнителей работой.
Число единиц, подъемно-транспортного оборудования определяется числом постов ТО и диагностики, а также предусмотренным в проекте уровнем механизации производственных процессов.
Количество производственного инвентаря (верстаков, стеллажей и т.п.), который используется в течение всей рабочей смены, определяют по числу работающих в наиболее загруженной смене.
На предприятии имеется мастерская с оборудованием, предлагаю дополнить ее по части ТО и диагностики.
3. Конструкторская разработка
3.1 Цель разработки
Техническая диагностика – отрасль знаний, изучающая закономерности изменения технического состояния машин и разрабатывающая методы и средства его определения. Многообразие условий и режимов эксплуатации приводит к значительному рассеиванию ресурса составных частей. Поэтому важно иметь методы и средства для оценки их технического состояния с целью контроля работоспособности для прогнозирования остаточного ресурса и с целью поиска дефектов и выявления причин отказа.
Техническое диагностирование – это процесс определения технического состояния изделия с определенной точностью. Результатом диагностирования является заключение о техническом состоянии изделия с указанием места, вида и причины дефекта.
Методы и средства диагностирования должны быть удобны для применения, должны обеспечивать контроль изделия без разборки или с минимальной разборкой и быть экономически целесообразными. Данная разработка предназначена для комплексной оценки состояния топливной аппаратуры высокого давления без снятия агрегатов с машин.
3.2 Оценка существующих конструкций для диагностирования дизельной топливной аппаратуры
В настоящий момент существует довольно много приборов и приспособлений, предназначенных для диагностирования топливной аппаратуры высокого давления. Рассмотрим наиболее близкие по концепции и конструкции приспособления с оценкой их отрицательных сторон, часть из которых решена в данной разработке. Общий вид всех аналогов приведен в листе ЭМДП.01.009.000.Д4
Приспособление КИ – 16301А
Состояние плунжерных пар проверяют приспособлением КИ – 16301А, а нагнетательных клапанов – этим же приспособление и секундомером.
Приспособление представляет собой насос высокого давления и состоит из манометра, подключенного к нагнетательной полости корпуса, плунжерной пары и нагнетательного клапана, находящихся внутри корпуса рукоятки резервуара и привода плунжера, представляющего собой рычаг, один конец которого шарнирно закреплен на корпусе, и толкатель.
Проверку выполняют в следующем порядке. Отсоединяют топливопровод высокого давления от проверяемой секции топливного насоса и присоединяют к секции приспособление. Ослабляют затяжку накидных гаек топливопроводов высокого давления на остальных секциях топливного насоса.
Проверяют износ плунжерной пары по давлению, развиваемому ею при пусковой частоте вращения коленчатого вала. Для этого включают подачу топлива и, прокручивая коленчатый вал пусковым устройством, наблюдают за положением стрелки манометра. При возникновении колебаний стрелки выключают подачу и, плавно включая ее, повышают давление до 30 МПа, если давление окажется меньше, плунжерные пары заменяют.
Проверяют плотность прилегания нагнетательного клапана к седлу. Для этого прекращают прокручивать коленчатый вал, выключают подачу топлива и, наблюдая за перемещением стрелки манометра, измеряют время падения давления от 15 до 10 МПа. Если время падения менее 10 с, нагнетательный клапан заменяют.
Проверяют форсунку, давление начала подъема иглы распылителя определяют по максимальному отклонению стрелки манометра, делая 35 – 40 качков рычага в минуту. При достижении максимального отклонения стрелки манометра проверяют герметичность распылителя по скорости падения давления после его снижения на 2 МПа от максимальной величины. Если за 20 с давление снизится более чем на 1,5 МПа, форсунки снимают, разбирают, очищают распылитель от нагара и проверяют работоспособность форсунки. При необходимости заменяют распылитель.
Недостатки:
– по ходу проведении проверки нет возможности регулировок, т. к. у оператора заняты обе руки;
– материалоемкость;
– возможность попадания в нагнетательную полость воздуха из – за горизонтального расположения бачка с испытательной жидкостью;
– нежесткое соединение устройства с входным элементом затрудняет обеспечение повторяемости.
Прибор КИ – 562 для испытания и регулировки форсунок.
Предназначен для измерения и регулировки давления впрыска и определения качества распыливания топлива форсункой, снятой с двигателя.
Состоит из корпуса, внутри которого помещен насосный элемент, механизма привода насосного элемента с рычагом ручной подкачки, присоединительного штуцера с маховичком, распределителя с запорным вентилем, манометра, топливного бачка с фланелевым фильтром и глушителя. Топливо в испытуемую форсунку и манометр нагнетают рычагом ручной подкачки. Запорный вентиль служит для отключения полости манометра при проверке качества распыливания топлива.
Недостатки:
– возможность проверки только форсунок;
– необходимость снимать форсунки с двигателя.
Устройство КИ – 4802 для проверки прецизионных пар топливных насосов.
Предназначено для определения износа плунжерных пар и герметичности нагнетательных клапанов топливных насосов.
Состоит из тройника, корпуса, манометра, предохранительного клапана и топливопровода высокого давления с накидными гайками.
Для определения технического состояния прецизионных пар устройство при помощи топливопровода и накидной гайки присоединяют к проверяемой секции топливного насоса. Прокручивают коленчатый вал двигателя пусковым устройством и определяют величину давления, развиваемого плунжерной парой. По времени падения давления с 15 до 10 МПа определяют состояние нагнетательного клапана.
Недостатки:
– нет возможности проверки форсунок.
Приспособление КИ – 9917 для проверки форсунок
Предназначено для проверки давления и качества распыливания топлива форсункой без снятия ее с двигателя. Приспособление можно использовать для проверки износа прецизионных пар топливного насоса и развиваемого им давления при прокручивании коленчатого вала двигателя с помощью пускового устройства.
Приспособление представляет собой ручной насос высокого давления, содержащий контрольный манометр, корпус с плунжерной парой, рычаг – привод плунжерной пары и резервуар для топлива, расположенный в неподвижной ручке. Топливо в резервуаре находится под давлением подпружиненного поршня.
При диагностировании приспособление соединяют с испытуемой форсункой через топливопровод высокого давления, нагнетают топливо в форсунку и по манометру определяют давление ее срабатывания. Качество распыливания топлива определяют по характерному щелчку иглы распылителя в момент впрыска топлива: если щелчок четкий и звонкий, то качество распыливания удовлетворительное.
Износное состояние плунжерной пары определяют по величине создаваемого ею давления. Состояние нагнетательного клапана оценивают по продолжительности падения давления.
Недостатки:
– по ходу проведении проверки нет возможности регулировок, т. к. у оператора заняты обе руки;
– материалоемкость;
3.3 Описание и принцип действия разработки
Основной задачей настоящего изобретения является создание устройства для бесстендового диагностирования ТАВД, которое имело бы меньшую материалоемкость и обеспечило бы снижение трудоемкости диагностирования, а также приемлемую точность и достоверность результатов диагностики путем получения достаточной повторяемости тестового воздействия на диагностируемый орган.
Дополнительные задачи настоящего изобретения заключаются в повышении безопасности работ при проверке плунжерных пар и расширении функциональных возможностей устройства путем обеспечения, в частности, возможности экспресс – оценки производительности плунжерной пары.
Заявленное устройство содержит корпус 2 с резьбовым наконечником 6, в котором выполнен канал высокого давления для подачи испытательной жидкости, в качестве которой используют, как правило, дизельное топливо, к диагностируемому органу. Внутри корпуса 1 расположен плунжерный насос с плунжером 8 для подачи топлива в канал наконечника 6. Привод насоса 8 выполнен в виде рычага 3, который для обеспечения возможности воздействия на плунжер шарнирно соединен с корпусом 2, для чего к последнему жестко прикреплен промежуточный кронштейн, с которым посредством шарнирного соединения соединен рычаг 3. Воздействие рычага 3 на плунжер обеспечено через шарнирное соединение с толкателем 4 и воздействия на него. Толкатель 4 установлен с возможностью осевого перемещения в корпусе 2 в контакте с хвостовиком плунжера, обратный ход которого обеспечен пружиной 11, воздействующей на тарелку 14, которая контактирует с хвостовиком плунжера со стороны, противоположной толкателю 4.
Резервуар для топлива установлен в рычаге 3 и имеет отвинчивающуюся крышку 7. Полость резервуара подключена к кольцевой полости питания насоса 8 посредством гибкого трубопровода 15.
В корпусе 2 между надплунжерным пространством и каналом высокого давления установлен также нагнетательный клапан 5 для создания высокого давления испытательной жидкости в канале. Манометр 19 установлен на корпусе 2 и подключен к каналу через полость, в которой расположена возвратная пружина 12 клапана 5.
В качестве плунжера в заявленном устройстве использован плунжер серийной конструкции, применяемой в существующих ТНВД. На цилиндрической поверхности плунжера такой конструкции имеется винтовая канавка, сообщенная с Г-образным каналом, выходящим на торец плунжера, где установлена заглушка.
В зоне полости питания в корпусе 2 выполнено сообщенное с этой полостью резьбовое отверстие, в которое ввернута резьбовая пробка 10, выполненная с каналом, один конец которого выходит на поверхность внутреннего торца пробки 10, а другой – на ее резьбовую поверхность, на участке, смежном с головкой пробки.
Для фиксации рычага 3 с резервуаром относительно корпуса 2 в целях транспортировки предусмотрен элемент крепления, выполненный, например, в виде шплинта 20, вставляемого в соответствующие отверстия кронштейна и рычага 3.
Устройство работает следующим образом.
Вывернув крышку 7, в резервуар заливают топливо. Крышку 7 вворачивают обратно не полностью. Для удаления воздуха из полости питания и гибкого трубопровода 15 частично откручивают пробку 10 на некоторое время до истечения топлива без пузырьков. Заполняют полость питания топливом, произведя несколько перемещений рычага 3 до наступления полнопоточного истечения топлива из наконечника 6 и штуцера. Полностью закручивают пробку 10 и рукояткой 13 закрывают вентиль дросселя 1.
Для проверки форсунки или плунжерной пары ТНВД двигателя устройство подключают к штуцеру форсунки или ТНВД соответственно, для чего используют переходник 9, наворачиваемый одновременно (за счет противоположных направлений навивки ее резьбовых участков) на наконечник 6 и на штуцер диагностируемого органа. При этом конец наконечника 6 плотно сопрягается с отверстием штуцера. Если штуцер диагностируемого органа расположен в неудобном или труднодоступном месте, используют необходимые переходники и удлинители.
Диагностику проводят, создавая в диагностируемом органе заданное давление топлива путем плавных качательных перемещений рычага 3, дросселируя при необходимости рукояткой 13 выход топлива. Создаваемое давление топлива контролируют манометром 19. При этом топливо самотеком поступает из резервуара по трубопроводу 15 в полость питания, откуда плунжер, преодолевая сопротивление пружины 12 клапана 5, подает топливо в полость, сообщенную с каналом высокого давления. Из этого канала топливо поступает в диагностируемый орган. Вытекающее из дросселя 1 через штуцер топливо может быть аккуратно собрано в отдельную емкость.
3.4 Расчет конструкторской разработки
Рассчитываем на прочность наиболее нагруженные части и соединения, для определения надежности и работоспособности конструкции в целом. Расчет производим при максимальном давлении 40 МПа.
3.4.1 Расчет объема бачка
Для проведения испытаний используется дизельное топливо, которое заливаем в бачок, объем которого находим по формуле:
V = πR2
H(3.1)
где R – внутренний радиус, мм2
;
Н – высота цилиндра которая заполняется испытательной жидкостью.
V = 3,14×152
×196,5 = 138827 (мм2
) = 0,14 (л.)
Этого объема достаточно для проведения испытаний.
3.4.2 Расчет усилия на рукоятке
Рассчитываем усилие [15] необходимое для создания заявленного давления в рабочей полости, в размере 40 МПа, которое действует на клапан диаметром 6 мм. Для этого рассмотрим рукоятку как нагруженный стержень.

Рис. 3.1 – Схема действия сил, эпюры моментов и усилий
Найдем усилие действующее в точке А по формуле:
РА
= (3.2)
где Р – давление, Па;
d – диаметр клапана, м.
РА
= = 1130 (Н)
Для нахождении усилия руки РС
составляем уравнение моментов относительно точки В.
Σ МВ
= 0 (3.3)
РС
(l1
+l2
) – PA
l2
= 0 (3.4)
РС
= РА
l2
/(l1
+l2
) (3.5)
где l1
– расстояние между точками А и С, м;
l2
– расстояние между точками А и В, м.
РС
= 1130×0,032/0,244 = 148,2 (Н)
По результатам расчета видим, что усилие на рукоятке составляет приблизительно 15 кг, это в пределах допустимой нормы от 15 до 20 кг.
3.4.3 Расчет на прочность сварных швов
В первом случае рассчитываем, сварной шов [15] между корпусом и кронштейном, он испытывает растягивающее усилие и при этом работает на срез.

Для определения прочности нам необходимо знать реакцию в точке В, которую мы находим по выше приведенной схеме на рис. 3.1. Составим уравнение моментов относительно точки А.
РС
l1
– RB
l2
= 0 (3.6)
RB
= РС
l1
/l2
(3.7)
где RВ
– реакция в точке В, Н.
RB
= 148,2×0,212/0,032 = 981,8 (Н)
Условие прочности на срез имеет вид:
(3.8)
где Fшва
– площадь шва, м;
τ – касательное напряжение, которое материал способен выдерживать длительное время, МПа.
Касательное напряжение находим по формуле:
(3.9)
где σ – допустимое нормальное напряжение, МПа.
Находим допустимое нормальное напряжение по формуле:
(3.10)
где σТ
– предел текучести материала, МПа, для стали 45 σТ
= 340 МПа;
n – коэффициент запаса, принимаем 2,125
σ= 340/2,125 = 160 (МПа)
τ = 160/2 = 80 (МПа)
Площадь сварного шва находим по следующей формуле:
Fшва
= 2×a×β×hшва
+ 2×b×β×hшва
(3.11)
где а – ширина провариваемого элемента, м;
b – длина провариваемого элемента, м;
β – коэффициент зависящий от способа сварки, для ручной однопроходной сварки β = 0,8;
hшва
– высота катета углового шва, м.
Fшва
= 2×10-4
×0,8×4×10-3
+ 2×37×10-3
×0,8×4×10-3
= 300,8×10-6
Проводим проверку на прочность
τср
= 981,8/ 0,0003 = 3,27 ≤ 80 (МПа)
Условие прочности выполняется, значит, данный шов выдержит нагрузки.
Расчет шва толкателя на разрыв производим, прибегнув к некоторым упрощения, будем считать, что толкатель жестко закреплен и на него действует сила РА
.

Используем формулы (3.8) и (3.11), но при этом вместо RB
подставляем РА
и получаем:
Fшва
= 2×11,5×10-3
×0,8×4×10-3
+ 2×10×10-3
×0,8×4×10-3
= 137,6×10-6
τср
= 1130/ 0,0001378 = 8,21 ≤ 80 (МПа)
Условие прочности выполняется.
Расчет сварных швов рычага выполняем по той же методике, но для этого необходимо найти реакцию в точке сварки К.

Находим значение реакции по пропорции:
RK
= RA
l1
/ l3
(3.12)
где l3
– расстояние от точки В до точки К, м.
RK
= 1130×0,032/0,044 = 822 (Н)
Fшва
= 2×18×10-3
×0,8×3×10-3
+ 2×5×10-3
×0,8×3×10-3
= 110,4×10-6
В условие прочности подставляем удвоенную площадь шва, т. к. на рычаг приварены две пластины, нагрузка между которыми поделена поровну.
τср
= 822/ 0,00022 = 3,7 ≤ 80 (МПа)
Условие прочности выполняется с большим запасом, что гарантирует надежность и работоспособность разработки.
3.4.4 Расчет оси шарнира на срез
Ось шарнира, крепящая рычаг к корпусу имеет две перерезывающие плоскости. Необходимо выполнение условия прочности на срез:
(3.13)
где F1
– площадь перерезывающей плоскости, м2
.
Площадь находим по формуле:
(3.14)
где d – диаметр перерезывающей плоскости, м2
.
F1
= 3,14×82
×10-3
/4 = 10-4
Проверяем по условию прочности (3.13):

Условие прочности выполняется.
3.4.5 Расчет усилия затяжки
Наиболее ответственные резьбовые соединения необходимо рассчитывать. Для нахождения момента затяжки [27] необходимо найти силу затяжки.
Расчет момента затяжки резьбового наконечника.
Усилие затяжки находим по формуле:
Fзат
= ν (1 – χ) Fвн
(3.15)
где ν – коэффициент затяжки, для герметичных соединений с мягкими прокладками [27], принимаем ν = 1,9;
χ – коэффициент внешней нагрузки [27], принимаем χ = 0,25;
Fвн
– внешняя нагрузка, в нашем случае таковой является давление жидкости.
Переводим давление в силу:
F = (3.16)
где Р – давление, Па;
d – диаметр на который оказывается давление, м.
F = = 4522 (Н)
Находим усилие затяжки:
Fзат
= 1,9×(1 – 0,25)×4522 = 6014 (Н)
Для нахождения момента необходимо знать радиус затягиваемой детали и подставить в формулу:
Мзат
= Fзат
×R(3.17)
где R – радиус затягиваемой детали, в нашем случае 0,018 м.
Мзат
= 6014×0,018 = 108 (Нм)
Расчет момента затяжки манометра производим по аналогичной технологии с применением формул (3.15), (3.16), (3.17).
F = = 502,4 (Н)
Fзат
= 1,9×(1 – 0,25)×502,4 = 716 (Н)
Мзат
= 716×0,007 = 5 (Нм)
3.5 Технико-экономическая оценка конструкторской разработки
Масса конструкции [8] определяется по формуле
G = (Gk
+ Gг
)×К, (3.18)
где Gk
– масса сконструированных деталей, кг;
Gг
– масса готовых деталей, узлов и агрегатов, кг;
К – коэффициент, учитывающий массу расходуемых на изготовление монтажных материалов, К = 1,1.
Массу сконструированных деталей определяем в форме таблицы 3.1.
Таблица 3.1 – Расчет массы сконструированных деталей
Наименование детали |
Объем
детали,
см3
|
Удельный вес,
кг/см3
|
Масса
детали,
кг
|
Кол-во
деталей,
шт.
|
Общая масса,
кг
|
Дроссель |
40 |
0,002 |
0,08 |
1 |
0,08 |
Корпус |
150 |
0,002 |
0,3 |
1 |
0,3 |
Рычаг |
175 |
0,002 |
0,35 |
1 |
0,35 |
Наконечник резьбовой |
65 |
0,002 |
0,13 |
1 |
0,13 |
Крышка |
30 |
0,002 |
0,06 |
1 |
0,06 |
Переходник |
10 |
0,002 |
0,02 |
1 |
0,02 |
Пробка |
5 |
0,002 |
0,01 |
1 |
0,01 |
Тарелка |
7,5 |
0,002 |
0,015 |
1 |
0,015 |
Трубопровод |
10,7 |
0,0014 |
0,015 |
1 |
0,015 |
Итого |
- |
- |
0,98 |
9 |
0,98 |
Масса конструкции
G = (0,98 + 0,55)×1,1 = 1,68 ≈ 1,7 (кг)
Стоимость разработки определим по формуле:
СБ1
= СБ0
× G1
× Jц
× R/G0
,(3.19)
где СБ0
– балансовая стоимость базовой конструкции, руб.;
G1
и G0
– масса новой и базовой конструкции, кг;
Jц
– коэффициент, учитывающий изменение цен в изучаемом периоде;
R – коэффициент, учитывающий удорожание или удешевление новой конструкции в зависимости от сложности изготовления (R = 1,05).
СБ1
= 1300 × 1,7 × 1,08 × 1,05/2,3 = 1090 (руб.)
3.5.2 Расчет технико-экономических показателей
Для дальнейшего расчета составим табл. 3.2. В качестве базовой модели для сравнения бралось приспособление для проверки форсунок и прецизионных пар топливного насоса КИ – 16301А.
Таблица 3.2 – Исходные данные для расчета технико-экономических показателей
Наименование
|
Вариант |
Базовый |
Проектируемый |
1. Масса конструкции, кг. |
2,3 |
1,7 |
2. Балансовая стоимость, руб. |
1300 |
1090 |
3. Потребляемая мощность, кВт. |
– |
– |
4. Количество обслуживающего персонала, чел. |
1 |
1 |
5. Разряд работы |
3 |
3 |
6. Тарифная ставка, руб./чел.-ч. |
36 |
36 |
7. Норма амортизации, %. |
14,2 |
14,2 |
8. Норма затрат на ремонт и обслуживание, %. |
7,1 |
7,1 |
9. Годовая загрузка конструкции, ч. |
23 |
38 |
Расчет ведем для проектируемого приспособления. Часовая производительность определяется:
(3.20)
где t – коэффициент использования рабочего времени смены (0,6…0,9)
ТЦ
– время одного рабочего цикла, мин.
(шт./ч)
Металлоемкость процесса:
(3.21)
где Gi – масса машины, кг;
Тгод – годовая загрузка машины, ч;
Тсл – срок службы машины, лет.
Ме = 1,7 / (2,5×38×5) = 0,004 кг/шт.
Фондоемкость процесса:
(3.22)
где Сб
– балансовая стоимость приспособления, руб.
FЕ
= 1090 / (2,5×38) = 11,47 руб./шт.
Трудоемкость процесса:
(3.23)
Nобсл
– количество обслуживающего персонала, чел.
ТЕ
= 1 / 2,5 = 0,4 чел.-ч/шт.
Себестоимость работы, выполняемой с помощью спроектированной конструкции, находят из выражения:
Sэксп = Сзп + Сэ + Сро + А + Пр, (3.24)
где Сзп – затраты на оплату труда с единым соц. налогом, руб./шт.;
Здесь:
Сзп = Z × Те × Ксоц, (3.25)
где Z – часовая тарифная ставка рабочих, руб./шт.;
Ксоц – коэффициент учитывающий единый социальный налог, 1,26.
Сзп = 36×0,4×1,26 = 18,14 руб./шт.
Сэ – затраты на электроэнергию, руб./шт. (отсутствуют);
Сро – затраты на ремонт и обслуживание, руб./шт.;
Здесь:
Сро = (Сб×Нрто) / (100×Wч×Тгод), (3.26)
где Нро – норма затрат на ремонт и обслуживание, %.
Сро = (1090×7,1) / (100×2,5×38) = 0,81 руб./шт.
А – затраты на амортизационные отчисления, руб./шт.;
Здесь:
А = (Сб×На) / (100×Wч×Тгод), (3.27)
где На – норма затрат на амортизационные отчисления, %.
А = (1090×14,2) / (100×2,5×38) = 1,62 руб./шт.
Пр – прочие затраты, (5–10% от суммы предыдущих элементов).
Здесь:
Пр = (А + Сро)×0,1, (3.28)
Пр = (1,62 + 0,81)×0,1 = 0,24 руб./шт.
Sэксп = 18,14 + 0,81 + 1,62 + 0,24 = 23,68 руб./шт.
Уровень приведенных затрат на работу конструкции определяется по формуле:
Спр = Sэксп + Ен×Куд, (3.29)
где Куд – удельные капитальные вложения или фондоемкость процесса, руб./шт.;
Ен – нормативный коэффициент эффективности капитальных вложений, Ен = 0,25
Спр = 20,81 + 0,25×11,47 = 23,68 руб.
Годовая экономия составляет:
Эгод = (S0
– S1
) × Wч × Тгод, (3.30)
где Тгод – годовая загрузка машины, ч.
Эгод = (32,11 – 23,68) × 2,5 × 38 = 800,85 руб.
Годовой экономический эффект:
Егод = Эгод – Ен × Кдоп, (3.31)
где Кдоп – капитальные дополнительные вложения равные балансовой стоимости конструкции, руб.
Егод = 800,85 – 0,25 × 1090 = 528,35 руб.
Срок окупаемости капитальных дополнительных вложений:
Ток = Сб / Эгод, (3.32)
Сб – балансовая стоимость подъемника, руб.
Ток = 1090 / 800,85 = 1,4 ≈ 1,5 года.
По результатам расчетов заполним табл. 3.3.
Таблица 3.3 – Технико-экономические показатели
Наименование |
Базовый |
Проектируемый |
Проектируемый к базовому в% |
1. Часовая производительность машины, ед/ч. |
2,25 |
2,5 |
111 |
2. Металлоемкость процесса, кг/шт. |
0,009 |
0,004 |
44 |
3. Фондоемкость, руб./шт. |
25,12 |
11,47 |
46 |
4. Трудоемкость, чел.-ч/шт. |
0,44 |
0,4 |
91 |
5. Себестоимость работы, руб./шт. |
25,83 |
20,81 |
81 |
6. Уровень приведенных затрат, руб./шт. |
32,11 |
23,68 |
74 |
7. Годовая экономия, руб. |
800,85 |
8. Годовой экономический эффект, руб. |
528,35 |
9. Срок окупаемости, лет. |
1,5 |
10. Коэффициент эффективности. |
0,67 |
Фактический коэффициент эффективности капитальных вложений.
Еэф = 1 / Ток, (3.33)
Еэф = 1 / 1,5 = 0,67
Приспособление для диагностирования дизельной топливной аппаратуры высокого давления экономически и технологически эффективнее, т. к. срок окупаемости 1,5 года и фактический коэффициент эффективности капитальных вложений более 0,25. Данная разработка подходит для внедрения в производство.
4. Безопасность жизнедеятельности на производстве
4.1 Организация работы по созданию здоровых и безопасных условий труда
Общее руководство и ответственность за организацию и проведение работ по охране труда и пожарной безопасности возложена на руководителя предприятия. В целях организации технического контроля и безопасной эксплуатации машин и технологического оборудования, директором предприятия в начале каждого года издается приказ о назначении лиц, ответственных за состояние охраны труда в каждом подразделении, на каждом производственном участке. В приказе утверждается комиссия по приемке технических минимумов рабочих, а также эта комиссия проверяет правильность оформления нормативных документов.
Хорошо организована пропаганда безопасных приемов труда: на рабочих местах имеются плакаты с указанием правильных приемов труда, предупреждающие надписи. Кабинет по безопасности дорожного движения отсутствует, но инженер по охране труда периодически проводит занятия и рассказывает о нововведениях и дополнениях, у него в наличии есть необходимая литература. При несчастном случае на производстве производится расследование с составлением акта по форме Н-1 в двух экземплярах. Ежегодно составляется отчетность по форме 7-Т.
Составляется соглашение по охране труда между профсоюзом коллектива и администрацией предприятия. Ежегодно составляется план работ по охране труда с обязательной отчетностью при подведении итогов работы коллектива.
Женщины и молодежь работают в соответствии с требованиями трудового законодательства.
Все работающие обеспечиваются спецодеждой, спецобувью, спецпитанием, моющими средствами, за это ответственный директор по общим вопросам. При поступлении на работу проводятся обязательный медицинский осмотр. Затем не реже одного раза в год проводятся медицинские осмотры.
Организацию пожарной безопасности на предприятии осуществляют администрация предприятия, непосредственные руководители на местах. Производственные участки, автомобили, подсобные помещения полностью обеспечены средствами пожаротушения.
Ответственность и своевременность проведения освидетельствования и испытания грузоподъемных устройств закреплена приказом по предприятию за определенными лицами. Освидетельствование и испытание грузоподъемных машин проводится качественно и в срок.
Санитарно-бытовые помещения находятся непосредственно в производственных помещениях, имеются умывальники, туалеты.
4.2 Анализ условий труда и производственного травматизма
Для предотвращения травматизма и заболевания в производственных предприятиях необходимы разносторонние знания по охране труда, умение выявлять и устранять потенциальные опасности и вредности, учитывая влияние меняющихся внешних условий на безопасность труда. Огромное значение в эффективности мероприятий по предупреждению травматизма играет анализ условий труда и производственного травматизма. Рассматривая же условия труда в ПК СФ «Агровод» можно отметить, что они на большинстве рабочих мест не соответствует санитарным требованиям.
Подавляющее большинство рабочих мест не оборудованы шумоизолирующими и виброгасящими устройствами. Запыленность и загазованность превышает установленные нормы. Вентиляционные системы в производственных помещениях давно не чистились, а в бытовых помещениях их и вовсе нет, поэтому эффективность их работы не соответствует требованиям.
На многих опасных объектах и зонах отсутствуют или находятся в не пригодном для использования состоянии предупреждающие и сигнальные устройства. Санитарно-бытовые помещения в большинстве своем находятся в неудовлетворительном состоянии. Душевых нет вместо них умывальники с теплой водой.
Обобщение и выводы о состоянии травматизма в хозяйстве можно сделать на основании годовых отчетов и актов, которые дают возможность получить показатели, характеризующие уровень травматизма.
Динамика производственного травматизма приведена в таблице 4.1.
Таблица 4.1 – Динамика производственного травматизма
Наименование показателей |
Год |
2004 г. |
2005 г. |
2006 г. |
1 Среднесписочная численность работников, чел |
148 |
149 |
153 |
2 Число пострадавших с утратой трудоспособности на 1 рабочий день и более |
1 |
5 |
2 |
3 Число чел.-дней нетрудоспособности у пострадавших |
11 |
110 |
16 |
4 Коэффициент частоты, Кч
|
6,8 |
33,5 |
13,1 |
5 Коэффициент тяжести, Кт
|
11 |
22 |
8 |
6 Коэффициент потерь, Кп
|
74,3 |
738,3 |
104,6 |
7 Израсходовано средств, тыс. руб. |
175,8 |
265,3 |
652,5 |
8 Израсходовано средств на одного работающего, руб./чел. |
1187,8 |
1780,5 |
4264,7 |
Производственный травматизм – сложное явление современной жизни. Причины его чрезвычайно многообразны, а точная оценка затруднена. Существует несколько показателей, характеризующих состояние травматизма на производстве. Определим эти показатели [22] и сведем в таблицу 4.1.
Анализируя табличные данные можно сделать вывод, что в ПК СФ «Агровод» довольно невысокие показатели травматизма, кроме 2005 г. где травматизм самый высокий за анализируемый период.
В 2006 г. по отношению к 2005 г. произошли существенные изменения в плане безопасности труда. Коэффициент частоты уменьшился в 2,5 раза, но это говорит лишь о том, что 2005 г. был очень травмоносным, необходимо стремится уменьшить показатель до значения 2004 г., а в лучшем случае свести к нулевому значению. Рассматривая коэффициент тяжести, видим, что в 2006 г. было два случая, но по тяжести они легче, чем единичный случай в 2004 г. и имеет наименьшее значение за анализируемый период. Потеря рабочего времени в 2006 г. лишь на немного больше базового 2004 г. и связано это с более легким травматизмом. Средств на мероприятия по охране труда выделяется достаточно. В 2006 г. на обеспечение рабочих спецодеждой было потрачено на 25% больше, чем запланировано. В целом по предприятию наметилась благоприятная тенденция на снижение травматизма.
Для более тщательного анализа производственного травматизма в хозяйстве необходимо рассмотреть распределение несчастных случаев по отраслям производства (таблица 4.2), и причины несчастных случаев (таблица 4.3).
Таблица 4.2 – Распределение несчастных случаев по отраслям производства
Производства |
2004 г. |
2005 г. |
2006 г. |
Кол-во работающих |
Кол-во пострадавших |
Кч
|
Кол-во работающих |
Кол-во пострадавших |
Кч
|
Кол-во работающих |
Кол-во пострадавших |
Кч
|
Ремонтная мастерская |
64 |
1 |
15,6 |
65 |
4 |
61,5 |
65 |
1 |
15,4 |
Строительная площадка |
49 |
- |
- |
49 |
1 |
20,4 |
53 |
1 |
18,9 |
Большинство несчастных случаев в хозяйстве в рассматриваемые три года приходятся на ремонтные работы в механических мастерских. Ниже в таблице 4.3 приведены причины произошедших несчастных случаев.
Таблица 4.3 – Причины несчастных случаев
Причины |
2004 г. |
2005 г. |
2006 г. |
1 Неудовлетворительное содержание территории и рабочих мест |
- |
1 |
1 |
2 Нарушение правил техники безопасности |
1 |
4 |
1 |
Анализ причин травматизма показывает, что большая часть несчастных случаев связано с несоблюдением элементарных правил техники безопасности трудовой дисциплины, в частности не серьезное отношение и невнимательность к соблюдению инструкций.
Для снижения и предупреждения травматизма в хозяйстве необходимо предусмотреть следующие организационно-технические мероприятия:
– повысить требования к проверке уровня знаний правил и инструкций по охране труда;
– усилить надзор со стороны руководителей работ за их проведением в течение рабочего дня, не допускать к работе лиц в состоянии алкогольного опьянения и отстранять таких лиц от работы в течение рабочего дня с применением мер дисциплинарного и административного наказания;
– улучшить контроль за техническим состоянием инструмента, машин и оборудования, надежности средств индивидуальной защиты;
– привести в порядок в соответствии с санитарными требованиями, содержание территорий и рабочих мест;
– поощрять дисциплинированных рабочих материально;
– улучшить по возможности параметры микроклимата, освещенности, зашумленности, загазованности рабочих зон в соответствии с нормами производственной санитарии;
– привлекать к дисциплинарной ответственности лиц, нарушающих технику безопасности.
Эти мероприятия необходимо включить в план мероприятий по улучшению охраны труда по хозяйству, прилагаемого к коллективному договору.
4.3 Инструкция по охране труда для слесаря по ремонту и диагностике топливной аппаратуры
4.3.1 Общие требования охраны труда
1.1 К работе допускаются лица, не моложе 16 лет прошедший вводный инструктаж, первичный инструктаж на рабочем месте, а также овладевшие практическими навыками безопасного выполнения работ, прошедшее проверку полученных знаний и навыков с регистрацией в журнале и медицинский осмотр;
1.2 Рабочий обязан соблюдать правила внутреннего распорядка, режимы труда и отдыха, правил Т.Б. и пожарной безопасности, исключать опоздания на рабочее место в начале смены и после отдыха; запрещается уходить с рабочего места в рабочее время по неуважительной причине;
1.3 При выполнении работ на рабочего могут оказать влияние и вредные производственные факторы: воздействие пыли, пары ТСМ, оказывающие влияние на органы дыхания, пищеварения и зрения, и наличие масла, при попадании которого на кожу или слизистые может произойти раздражение или аллергия, а также опасные производственные факторы: открытые вращающиеся и движущиеся части машин, скользкие поверхности, захламленность рабочего места, использование инструмента не по назначению или в неисправном состоянии, что может привести к частичной или полной утрате работоспособности;
1.4 Грузы, массой более 20 кг разрешается поднимать только подъемными механизмами с применением специальных захватов, подъем грузов должен производиться только вертикально;
1.5 Рабочий обязан получить спецодежду, спецобувь и, при необходимости, защитные приспособления и рукавицы;
1.6 Рабочий должен соблюдать все требования по обеспечению пожаробезопасности и взрывобезопасности: курить разрешается только в специально отведенных местах, запрещается разводить очаги открытого пламени. Он должен уметь пользоваться первичными средствами пожаротушения;
1.7 В случаях травмирования рабочего и в случаях неисправности оборудования и приспособлении рабочий обязан немедленно сообщить мастеру;
1.8 В случаях травмирования работника рабочий обязан знать приемы до врачебной помощи, до прибытия врачей должен оказать, первую медицинскую помощь и сообщить мастеру;
1.9 Рабочий обязан содержать в чистоте и порядке рабочее место, не загромождать переходы и проезды, при выполнении работ использовать по прямому назначению средства индивидуальной защиты, рабочая одежда и спецодежда должны храниться отдельно от личной одежды, запрещается выносить спецодежду за пределы территории предприятия;
1.10 Участок должен быть оснащен противопожарным оборудованием и инвентарем согласно пожарной безопасности; лица, работающие на этом участке, должны знать это оборудование и умело пользоваться им в случаях необходимости. К тому же кроме технологических карт, на стенах должны быть вывешены красочные плакаты по правилам охраны труда, противопожарной безопасности и безопасным приемам труда;
1.11 Здесь же необходимо предусмотреть место для медицинской аптечки, укомплектованной медикаментами для оказания первой помощи;
1.12 При нарушении требовании инструкции рабочий привлекается к дисциплинарной ответственности.
4.3.2 Требования охраны труда перед началом работы
2.1 Убедиться в исправности и надеть специальную одежду, застегнуть ее на все пуговицы, волосы убрать под головной убор.
2.2 Проверить не загромождены ли проходы и рабочее место посторонними предметами. Убедиться в том, что рабочее место достаточно освещено и свет не будет слепить глаза. Напряжение местного освещения не должно превышать 42В, а переносных электроламп 12В.
2.3 Поверхность верстака должна быть гладкой, обитой листовой сталью. На верстаке должны быть установлены предохранительные сетки или щиты высотой не менее 1 метра.
2.4 Проверить необходимый для работы инструмент и приспособления и убедиться в их исправности. Неисправный инструмент и приспособления с рабочего места убрать. Переносить рабочий инструмент следует в специальной сумке или ящике.
2.5 Проверить наличие противопожарного инвентаря в цехе.
2.6 Приступить к ремонту топливной аппаратуры только после освобождения бензобаков и бензопроводов от остатков бензина.
2.7 Ознакомиться с предстоящей работой, продумать порядок ее выполнения.
4.3.3 Требования охраны труда во время работы
3.1 Принять меры, исключающие проливание топлива из топливного бака, топливопроводов и приборов системы питания.
3.2 При ремонте топливной аппаратуры на автомобиле снять клеммы с аккумулятора или отключить его выключателем массы.
3.3 Надежно закрепить топливные насосы и узлы при разборке, сборке в кондукторах или на специальных стендах.
3.4 Применять для выпрессовки отдельных деталей съемники или прессы, при их отсутствии пользуйтесь выколотками с медными наконечниками и молотками с медными бойками
3.5 Разборку и проверку карбюраторов, бензонасосов производить в местах с механической вытяжкой.
3.6 Следите за показаниями установленных на стендах приборов.
3.7 Не допускается разлив масла и топлива на пол
3.8 Грузозахватные приспособления применять только по назначению.
3.9 Регулировку приборов системы питания двигателя производить при выключенном зажигании.
3.10 Следить за исправностью шлангов на стендах, имеющих гидравлические и пневматические устройства.
3.11 Не находитесь в плоскости вращения вентилятора при работающем двигателе.
3.12 Не производите регулировку движущихся и вращающихся механизмов двигателя.
3.13 Не кладите детали системы питания на верстаки для разборки и сборки с оставшимся в них топливом.
3.14 Не применять проволоку для крепления шлангов на штуцерах.
3.15 Не касайтесь руками вращающихся частей стендов, не тормозите их, не прикасайтесь к элементам электрооборудования.
3.16 Направлять струю воздуха при продувке деталей в сторону от стоящих людей.
3.17 Не подставлять руки к распылителю при проверке работы форсунок и топливных насосов высокого давления.
3.18 Применять устройства, обеспечивающие невозможность внезапного действия пружин при сборке механизмов и узлов топливной аппаратуры.
3.19 Прочно закрепляйте на испытательных стендах топливные насосы, форсунки и другие элементы системы питания.
3.20 Регулировать величину подачи топлива отдельными секциями насоса при отключенном стенде.
3.21 Не оставляйте работающий стенд без присмотра.
3.22 Удаляйте из магистралей топливо перед снятием топливной аппаратуры с испытательного стенда.
3.23 Не удаляйте топливо с испытуемой аппаратуры на стенде сжатым воздухом.
3.24 Не используйте спецодежду, пропитанную нефтепродуктами.
3.25 Не мойте детали в этилированном бензине.
3.26 Для предотвращения возникновения пожара в помещении не пользуйтесь открытым огнем.
3.27 При проведении работ применяйте инструмент, изготовленный из материала, не дающего искрообразования (медь, латунь)
3.28 При ремонте или техническом обслуживании автомобиля вывесить на рулевое колесо табличку: «Двигатель не пускать! Работают люди!»
3.29 При ремонте поставить автомобиль на козелки и убедиться, что они надежно установлены. При работе под автомобилем вне осмотровой канавы, эстакады или подъемника использовать лежаки.
3.30 Сливать масло и воду из агрегатов автомобиля можно только в специальную тару
4.3.4 Требования охраны труда в аварийных ситуациях
4.1 При потере устойчивости узлов и агрегатов автотранспорта во время ремонтных работ их следует прекратить и сообщить о случившемся бригадиру или руководителю работ. После этого слесари должны принять участие в предотвращении произвольного перемещения частей машин.
4.2 В случае возникновения загорания необходимо работу прекратить, принять участие в тушении пожара (огнетушителями, асбестовыми покрывалами, песком или сильной струей воды), а при невозможности ликвидации загорания следует вызвать пожарную охрану по телефону 01 и поставить в известность руководство.
4.3 В случае повышения содержания вредных паров нефтепродуктов выше предельно допустимых норм или обнаружения взрывоопасных концентраций работу немедленно прекратить и удалиться из помещения.
4.4 При несчастных случаях с людьми окажите доврачебную медицинскую помощь, поставьте в известность руководителя, при необходимости вызвать скорую мед. помощь.
4.5 При поражении электрическим током как можно быстрее освободить пострадавшего от действия электрического тока, для этого отключить рубильник, или освободить пользуясь сухой веревкой, доской, любым другим сухим предметом, при этом желательно пользоваться одной рукой.
4.6 При попадании на кожу дизельного топлива необходимо промыть пораженное место горячей водой с мылом.
4.3.5 Требования охраны труда по окончании работы
5.1 Привести в порядок рабочее место. Инструмент и приспособления протереть и сложить в отведенное для них место.
5.2 Сложить в специально отведенном помещении ремонтный фонд топливной аппаратуры.
5.3 Использованные обтирочные материалы убрать в металлические ящики с крышками или в безопасное в пожарном отношении место.
5.4 Сообщить бригадиру или мастеру о выполненной работе, замеченных недостатках, которые были выявлены в процессе работы.
5.5 Снять и убрать специальную одежду в шкаф, вымыть руки и лицо с мылом, принять душ. Применять для мытья химические вещества запрещается.
4.4 Пожарная безопасность
Эффективное тушение и своевременное предупреждение пожаров достигается в результате выполнения всех требований пожарной безопасности.
На предприятии пожарной безопасности уделяется достаточное внимание. Весь инженерно-технический персонал ежегодно обучается по программе пожарно-технического минимума. С рабочими предприятия ежеквартально проводится инструктаж о мерах пожарной безопасности, в которых отражены все вопросы действующих правил пожарной безопасности.
Все помещения, участки оборудованы первичными средствами пожаротушения, установлены оборудованные пожарные щиты. Разработан и утвержден всеми инстанциями план эвакуации в случае аварии и пожара. На путях эвакуации установлены информационные знаки.
Допускается использовать только исправное оборудование, не допускается подтекание масла и горючих жидкостей. По окончании работы тщательно убирать рабочие места, промасленную ветошь убирать только в специальные металлические ящики.
Все электрические приборы использовать только согласно ПУЭ, не допускать перегрузок электрических сетей. Не использовать самодельные электронагревательные приборы. Проводить своевременную ревизию всего электрооборудования.
Допускается хранить машины на открытых площадках небольшими группами. Расставляют машины так, чтобы была возможность эвакуировать их в случае пожара. Площадки для открытого хранения техники располагают на расстоянии 15…20 м от зданий в зависимости от степени их огнестойкости.
Средства пожаротушения размещают в доступных местах.
Потребное число огнетушителей для производственных помещений определим из соотношения: 1 огнетушитель на 100 м2
площади.
Потребное число огнетушителей для участка определим по формуле:
(4.1)
где m0
– нормированное число огнетушителей на 1 м2
, (m0
= 0,01);
S – площадь участка ТО и диагностики, м2
.

Принимаем 3 огнетушителя марки ОХП-10.
Участок ТО и диагностики относят к категории В и 1 классу по степени пожаро- и взрывоопасности.
Расчетный расход воды на наружное пожаротушение здания принимаем 10 л/с.
Расход воды (м /ч) на наружное и внутреннее пожаротушение рассчитаем по формуле:
(4.2)
где Д – удельный расход воды на внутренне и наружное пожаротушение, л/с;
ТП
– время пожара, (ТП
= 3 ч);
ПП
– число одновременных пожаров, (ПП
= 1… 3).

Участок технического обслуживания и диагностики площадью 270 м2
имеет пожарный щит с тремя огнетушителями и ящик с песком.
Приказом по предприятию назначаются ответственные за пожарную безопасность.
5. Охрана окружающей среды
В последнее время в России стало уделяться больше внимания окружающей среде. Это связано с последствиями халатного отношения к природе. В районах с большой концентрацией предприятий наблюдается повышенная токсичность воздуха, уровень радиации превышает допустимые концентрации. В связи с этим увеличился рост заболеваемости, в том числе онкологических. Очень сильно беспокоит людей утилизация и хранение отходов производства и жизнедеятельности.
В ПК СФ «Агровод» ответственный за охрану окружающей среды заместитель директора по общим вопросам. В его обязанности входит осуществление периодического контроля, совместно с СЭС берутся пробы воздуха, воды, почвы. Вредные участки на предприятии (сварочный участок, кузница) снабжены вентиляцией с фильтрами, отработанные материалы утилизируют. Отработанные масла и прочие технические жидкости отправляют на утилизацию в специализированное предприятие.
На предприятии большой проблемой в плане экологии является мойка, от которой не организован сток грязной воды в отстойники, наиболее эффективным решением данной проблемы была бы организация рециркуляционной системы водоснабжения.
Территория за пределами предприятия достаточно озеленена, на самом предприятии Ко=0,01, на территории не предусмотрено достаточно места для озеленения.
Водонапорные башни ограждены.
В целом можно сделать вывод, что руководство старается заботится об охране природы, при наличии свободных денежных средств не отказывает в их использовании на охрану природы.
Стоимость капитальных дополнительных вложений находится из выражения [8]:
(6.1)
где С1ОПФ
– стоимость имеющихся производственных фондов на предприятии, тыс. руб.;
КДОП
– капитальные дополнительные вложения, тыс. руб.
Капитальные дополнительные вложения определяются по формуле [8]:
(6.2)
где СРЕК.ЗД.
- затраты на реконструкцию здания, тыс. руб.;
СОБ.ПИ.
- стоимость дополнительного оборудования, приспособлений,
инструмента, тыс. руб.;
Стоимость новых помещений и пристройки здания равна нулю т. к. внедряется лишь новое оборудование без модернизации сооружения.
Стоимость дополнительного оборудования, приспособлений, инструмента [8]:
(6.3)
где Ц – оптовая цена оборудования, приспособлений, инструмента, тыс. руб.;
КНЦ
- коэффициент дополнительных затрат включающий торговую наценку, установку и обкатку оборудования, принимаем 1,32.



Расчет себестоимости ремонтно-технических работ, тыс. руб.:
(6.4)
где СЗП
– затраты на оплату труда производственных рабочих, тыс. руб.;
СЗЧ
– затраты на запасные части, тыс. руб.;
СРМ
– затраты на ремонтные материалы, тыс. руб.;
СОП
– затраты на общепроизводственные расходы, тыс. руб.;
NРТО
– количество обслуживаний в условном исчислении, усл. обсл.
Затраты на оплату труда [8]:
(6.5)
где СПР
- тарифный фонд оплаты труда, руб.;
СДОП
- дополнительная оплата труда, руб.;
КСОЦ
- коэффициент, учитывающий единый социальный налог.
Тарифный фонд оплаты труда [8]:
(6.6)
где ZЧ
– часовая тарифная ставка по среднему разряду, руб./ чел.-ч.;
Т – общая трудоемкость работ по ТО и Д, чел. – ч.;
КТ
– коэффициент, учитывающий доплату к основной зарплате за
сверхурочные и другие работы, равный 1,05…1,1.

Часовая тарифная ставка по среднему разряду, руб./чел.-ч.
(6.7)
где ZЧ
i
– часовая тарифная ставка по 3 разряду, руб.;
NP
i
– количество рабочих определенного разряда, чел.;
NP
– общая численность рабочих, чел.
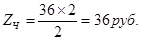
Дополнительная оплата труда [8]:
(6.8)
где УДОП
- дополнительная оплата в процентах к тарифному годовому фонду, составляющая 55…80%.


Затраты на запасные части определяются по формуле [8]:
(6.9)
где УЗЧО,
УЗПО
– фактические затраты на запасные части и оплату труда в общей сумме их в техническом производстве хозяйства в среднем за 2…3 года.

Затраты на ремонтные материалы, руб.;
, (6.10)
где УРМ
– затраты на ремонтные материалы в% к затратам на запасные части, равной 5…6%.


Фондоемкость [8]:
(6.11)
где СОПФ
– балансовая стоимость основных производственных фондов, руб.

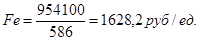
Производительность труда [8]:
, (6.12)
где NР
– кол – во работников ремонтно-технического производства, чел.
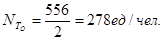
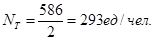
Уровень приведенных затрат, руб./ед:
(6.13)
гдеЕН
– нормативный коэффициент эффективности капитальных вложений, равный 0,25;
КУД
– капитальные удельные вложения или фондоемкость, руб./ед. рто.


Годовая экономия, руб.:
(6.14)
где S0
, S1
– себестоимости РТО, сложившаяся в хозяйстве за 2…3 года и по проекту, руб./ед. рто.;
NРТО
- программа РТО, ед.

Годовой экономический эффект [8]:
(6.15)
где КДОП
– сумма капитальных дополнительных вложений по дипломному проекту, руб.

Срок окупаемости капитальных дополнительных вложений [8]:
(6.16)
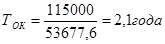
Коэффициент эффективности капитальных дополнительных вложений[8]:
(6.17)
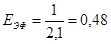
В нашем случае величина ЕЭФ
больше установленного норматива ЕН
, который равен 0,25, значит рассматриваемый вариант капитальных вложений эффективен. Срок окупаемости составляет 2,1 года, при затратах 115 тыс. руб. Результаты расчетов заносим в таблицу 6.1, (лист ЭМДП.01.009.000Д5).
Таблица 6.1. Сравнительные показатели экономической эффективности проекта
Наименование показателя
|
В среднем за 2004–2006 г. |
Проект |
Проект
к базовому, %.
|
1. Фондоемкость, руб./РТО
2. Производительность труда, ед./чел.
3. Себестоимость, руб./РТО
4. Приведенные затраты, руб./РТО
|
1509,2
278
641,6
1018,9
|
1628,2
293
550
957,1
|
107,8
105,4
85,7
94
|
5. Годовая экономия, тыс. руб.
6. Годовой экономический эффект, тыс. руб.
7. Срок окупаемости капитальных дополнительных вложений, лет.
8. Коэффициент эффективности капитальных дополнительных вложений.
|
53,8
24,9
2,1
0,48
|
Заключение
1. Проведен краткий анализ: производственной деятельности ПК СФ «Агровод» г. Ижевска; метода организации работ по поддержанию машин в работоспособном состоянии; работы нефтехозяйства.
2. Рассчитана годовая программа технических обслуживаний и диагностики, а также текущего ремонта. Подобрано технологическое оборудование, количество рабочих, приведена схема мастерской.
3. В конструкторской разработке рассчитано приспособление для диагностирования топливной аппаратуры высокого давления на дизельных двигателях. Данное приспособление значительно уменьшает трудоёмкость работ, повышает качество и удобство проведения диагностирования, дает возможность регулировки во время проведения диагностирования, снижает металлоемкость процесса, отвечает современным требованиям к переносному оборудованию.
4. Рассмотрен вопрос состояния охраны труда на производстве. Проанализирован уровень и причины травматизма, предложены организационно – технологические мероприятия, направленные на снижение и предотвращение несчастных случаев. Разработана инструкция по охране труда для слесаря по ремонту и диагностике топливной аппаратуры.
5. Проанализировано состояние охраны окружающей среды.
6. Рассчитан годовой экономический эффект от внедрения совмещенного поста технического обслуживания и диагностирования, также рассчитаны экономические показатели от использования приспособления для диагностики.
Список использованной литературы
1. С.М. Бабусенко. Проектирование ремонтно-обслуживающих предприятий. – М.: Агропромиздат, 1990.
2. Ю.Г. Корепанов. Техническая эксплуатация автотранспортных средств в сельском хозяйстве. Учебно – методическое пособие – Ижевск: ФГОУ ВПО ИжГСХА, 2005.
3. И.С. Серый. Взаимозаменяемость, стандартизация и технические измерения – 2-ое изд., перераб. – М.: Агропромиздат, 1987.
4. В.И. Черноиванов, В.В. Бледных, А.Э. Северный. Техническое обслуживание и ремонт машин в сельском хозяйстве – М.: ГОСНИТИ, 2003.
5. С.А. Иофинов, Г.П. Лышко. Эксплуатация машинно-тракторного парка –2-ое изд., перераб. и доп. – М.: Колос, 1984.
6. Дипломное проектирование: уч. – метод./сост. В.Ф. Первушин и др., ФГОУ ВПО Ижевская ГСХА – Ижевск: ИжГСХА, 2006.
7. М.И. Юдин, Н.И. Стукопин, О.Г. Ширай. Организация ремонтно-обслуживающего производства в сельском хозяйстве. – Краснодар, 2002.
8. И.Л. Иванов, В.Л. Редников. Методические указания по экономическому обоснованию дипломных проектов – Ижевск: ИжГСХА, 2002.
9. В.М. Грибков, П.А. Карпекин. Справочник по оборудованию для технического обслуживания и текущего ремонта автомобилей. – М.: Россельхозиздат, 1984.
10. А.А. Зангиев, Г.П. Лышко, А.Н. Скороходов. Производственная эксплуатация машинно-тракторного парка – М.: Колос, 1996.
11. В.И. Анурьев. Справочник конструктора машиностроителя: в 3-х томах – М.: Машиностроение, 1978.
12. Г.Ф. Фастовцев. Автотехобслуживание. – М.: Машиностроение, 1985.
13. Б.Н. Суханов. Техническое обслуживание и ремонт автомобилей. Пособие по дипломному проектированию. – М.: Транспорт, 1991.
14. Г.Н. Попова. Справочник по машиностроительному черчению – Л.: Машиностроение, 1986.
15. А.В. Александров. Сопротивление материалов – М.: Высш.шк., 2004.
16. Программа ЭВМ «Компас-График – 5.1» – С.-П.: Аскон, 2001.
17. Годовые отчёты ПК СФ «Агровод» – Ижевск, 2004–2006 г.
18. Д.Ф. Гуревич, А.А. Цырин. Ремонтные мастерские совхозов и колхозов – М.: Агропромиздат, 1988.
19. А.И. Олянич, А.И. Пантюхин, А.В. Пыталев, А.В. Колгин, Л.А. Буренко. Сборник типовых отраслевых инструкций по охране труда при ремонте и техническом обслуживании машин и оборудования в хоз-ве – ВНИИОТ, 1988.
20. Е.С. Кузнецова. Техническая эксплуатация автомобилей – М.: Транспорт, 1991.
21. Технологическое оборудование, оснастка, приборы, инструмент для ремонта машин и оборудования. Каталог – М.: АгроНИИТЭИИТО, 1990.
22. С.М. Чурин. Безопасность жизнедеятельности на производстве: Метод. указания – Ижевск: ИжГСХА, 2004.
23. Б.П. Кашуба. Каталог деталей и сборочных единиц трактора Т-74 – Харьков: 1978.
24. Б.А. Улитовский. Диагностирование с/х техники – М.: Агропромиздат, 1985.
25. В.И. Бельских. Справочник по техническому обслуживанию и диагностированию тракторов – М.: Россельхозиздат, 1986.
26. Положение о техническом обслуживании и ремонте подвижного состава автомобильного транспорта – М.: Транспорт, 1986.
27. В.Н. Кудрявцев. Детали машин – Л. Машиностроение, 1980.
28. И.Л. Иванов. Анализ хозяйственной деятельности и использования МТП в сельскохозяйственных предприятиях. Методические указания по выполнению курсовой работы для студентов по специальности 311300 – Механизация сельского хозяйства – 2-е изд., доп. – Ижевск: ИжГСХА, 2003.
|