Министерство образования и науки Украины
Одесская государственная академия строительства и архитектуры
Кафедра строительных машин
Курсовая работа
по дисциплине «Строительные машины»
выполнила:
студентка группы ПГС-281
Карпенко М.В.
номер зачётной книжки 05177
проверил:
преподаватель Колин В.М.
Одесса – 2008
Содержание
1. Перспективы развития строительного машиностроения, механизации и автоматизации строительства.
а) Машиностроение Украины
1а) Машиностроительные предприятия Украины и их продукция
б)Перспективы развития механизации и автоматизации строительства
2. Как устроены, работают и где применяются погрузчики?
2а)Вилочные погрузчики
2б) Одноковшовые погрузчики
2в) Погрузчики непрерывного действия
3.Расскажите о перебазировке башенного крана, его устойчивости
3а) Башенные краны
3б) Демонтаж башенных кранов
3в) Устойчивость башенного крана
4. Список использованной литературы
1.Перспективы развития строительного машиностроения, механизации и автоматизации строительства
а) Машиностроение Украины
Отечественная металлургия в настоящее время переживает не лучшие времена. Если раньше она шла по пути интенсивного развития производства, то теперь пора переходить к экстенсивному развитию – заняться энергосберегающими технологиями, использовать внутренние резервы, начинать искать пути повышения эффективности производства, считают эксперты. Украинские рынки сбыта начинает завоёвывать Китай, сделавший колоссальный прорыв, превратившись из страны импортера в экспортера. Не менее важно в этой ситуации и оживление внутреннего рынка. Сегодня 80% отечественной металлопродукции экспортируется, 20%потребляется у себя.
Самая актуальная проблема для украинской металлургии – это нестабильность ситуации с ценой на газ и его поставками. Сейчас предприятия начинают переходить на менее энергоёмкое оборудование, внедряют технологию пылеугольного вдувания и т.д. Однако за это время на традиционных рынках сбыта украинских металлургов могут потеснить крупные игроки – такие как Китай и Индия. В то же время недостаточно развитым остается потребление металла на внутреннем рынке.
Уровень инновационной активности машиностроительных предприятий Украины составляет 19%.Уровень инновационной активности машиностроительных предприятий выше, чем во всей отечественной промышленности.
Забиваем Сайты В ТОП КУВАЛДОЙ - Уникальные возможности от SeoHammer
Каждая ссылка анализируется по трем пакетам оценки: SEO, Трафик и SMM.
SeoHammer делает продвижение сайта прозрачным и простым занятием.
Ссылки, вечные ссылки, статьи, упоминания, пресс-релизы - используйте по максимуму потенциал SeoHammer для продвижения вашего сайта.
Что умеет делать SeoHammer
— Продвижение в один клик, интеллектуальный подбор запросов, покупка самых лучших ссылок с высокой степенью качества у лучших бирж ссылок.
— Регулярная проверка качества ссылок по более чем 100 показателям и ежедневный пересчет показателей качества проекта.
— Все известные форматы ссылок: арендные ссылки, вечные ссылки, публикации (упоминания, мнения, отзывы, статьи, пресс-релизы).
— SeoHammer покажет, где рост или падение, а также запросы, на которые нужно обратить внимание.
SeoHammer еще предоставляет технологию Буст, она ускоряет продвижение в десятки раз,
а первые результаты появляются уже в течение первых 7 дней.
Зарегистрироваться и Начать продвижение
Министром промышленной политики Украины было сказано, что Минпромполитики до 2011года, которой предусмотрено повышение технического уровня отечественного машиностроения в два раза.
Впервые за последние годы в бюджете на 2007 год были предусмотрены средства на инновационную деятельность в размере 1 млрд. грн., в том числе на энергосберегающие технологии – 767,4 млн. грн., финансовую поддержку инвестиционных и инновационных проектах, которые реализуются в технопарках, - 144,5 млн. грн.
Поскольку развитие любой промышленной отрасли неизбежно связано с экономической обстановкой в стране и инвестициями в промышленность, то нельзя не учитывать в перспективах развития проблематику данной отрасли. Проблематика заключается в особенностях функционирования машиностроения в недалёком прошлом. Распад машиностроительного комплекса СССР на отдельные республиканские блоки резко обострил проблемы машиностроения Украины, т.к. одновременно распались внешнеэкономические связи в области торговли машинами и оборудованием, которые отлаживались десятилетиями и, благодаря чему, сложился определённый баланс в насыщении отраслей народного хозяйства. В первой половине 80-х гг рост производства продукции инвестиционного машиностроения полностью прекратился, а во второй половине 80-х начался спад, в начале 90-х – обвальное падение.
Уменьшение спроса в отраслях- потребителях вынудило машиностроение приспосабливаться к условиям использования его продукции, увеличивая выпуск универсальной техники и внедряя примитивные технологии. Это приведет к прекращению выпуска наукоёмкой продукции, к дальнейшему свёртыванию машиностроительного производства и в конечном итоге к затуханию инвестиционного процесса. Особенно снизился объём капиталовложений в производство оборудования для строительства и сельскохозяйственного машиностроения.
Для машиностроения Украины характерно снижение производства наиболее прогрессивной техники, имеющей огромное значение для дальнейшего развития Украины, находится в системном кризисе, обусловленном распадом СССР и изменением структуры народнохозяйственного комплекса Украины. Проведение коренного реформирования отрасли машиностроения поможет выйти на мировой рынок с высокотехнологичной продукцией и занять там достойное место, что послужит базой для стабилизации экономики и подъёма промышленности в целом.
Сервис онлайн-записи на собственном Telegram-боте
Попробуйте сервис онлайн-записи VisitTime на основе вашего собственного Telegram-бота:
— Разгрузит мастера, специалиста или компанию;
— Позволит гибко управлять расписанием и загрузкой;
— Разошлет оповещения о новых услугах или акциях;
— Позволит принять оплату на карту/кошелек/счет;
— Позволит записываться на групповые и персональные посещения;
— Поможет получить от клиента отзывы о визите к вам;
— Включает в себя сервис чаевых.
Для новых пользователей первый месяц бесплатно.
Зарегистрироваться в сервисе
1а) Машиностроительные предприятия Украины и их продукция
Одесский завод «Краян»: самоходные грузоподъёмные автомобильные краны ( «Январец», «Краян», «Кранлод»).
Завод «Азовмаш»: краны козловые, полукозловые, портальные, мостовые.
Славянский завод строительных машин: бетономешательное оборудование.
Прилукский завод «Будмаш»: производство машин строительного назначения ( Цементовозы, подъёмники, смесители, растворомешалки).
б)Перспективы развития механизации и автоматизации строительства
Необходимость насыщения строительных площадок средствами автоматизации и механизации не подлежит сомнению. И все же, техническое содействие процессу строительства посредством машин, механизмов и т. п. оборудования обусловлено конкретной спецификой их применения. Каким бы отвлеченным ни казалось на первый взгляд это сравнение, есть много общего между гражданским строительством и сельским хозяйством. В обоих случаях основанием для роста и фиксации продукции служит земля, где все насаженное и настроенное раньше или позже обновляется. Однако развитие растений происходит «автоматически», достаточно обеспечить и сопровождать их рост внешними источниками питания. К тому же, пищевая потребность напоминает о себе чаще и сильнее, поэтому возможности пахотной и уборочной техники раньше узнали труженики полей, нежели экскаваторы и бульдозеры начали облегчать выемку грунта под фундаменты строений. Что касается «уборочной» техники в строительстве, потребность в ней становится сегодня все более очевидной благодаря актуальности концепции непрерывного развития территорий при наименьшем ущербе для окружающей среды. Несомненно, что преимуществами строительных машин являются их производительность, мобильность и, насколько можно, компактность. Показательна типичная конструкция подъемных кранов, для которых при их мощности и сложности предусмотрена только одна опора. Широкое применение сегодня металлических конструкций в строительстве оказывает огромное влияние на развитие сварочных технологий. Многообразие техники для дорожного строительства объясняется различием технологий прокладки дорог и их предназначением.
Если говорить о профессиональной подготовке специалистов-строителей, то в основном она отвечает задаче повышения объемов строительных работ, производительности труда и получения достаточно качественных результатов. Вместе с тем, обилие в отрасли специалистов ручного и полу-ручного труда ставит под вопрос возможность автоматизации строительства в целом. К счастью, здесь напрасными были бы поиски решений задач автоматизации и механизации в явном виде. Такие задачи во всяком случае оказываются комплексными, поэтому наиболее явно обнаруживаются лишь предпосылки их решения. Будучи искусственными сооружениями, строительные объекты появляются в результате исполнения проектов, создаваемых архитектурными институтами, мастерскими и т. п. организациями. При этом использование знаний по специальности «Системы автоматизированного проектирования» необходимо не только для определения технических возможностей средств автоматизации, но и для комплексного их применения. Так, наряду со средствами разработки прикладных приложений в различных областях строительства (таких, как GraphiCS), технологиями обеспечения разработок в области геодезии и картографии и т. д., применяются средства комплексной автоматизации проектирования и средства управления проектами по разработке технической документации (таких, как TDMS PROJECT DRIVES).
В целом, для автоматизации проектной деятельности имеются благоприятные перспективы развития. Прежде всего, применение автоматизированных технологий существенно повышает оперативность выполнения всех стадий конструирования – проектного задания или эскизного проекта, технического или рабочего проекта. Одновременно повышается вероятность согласования с заказчиком технического задания, каким бы ни было число уточнений в связи с детализацией рабочих чертежей, предусмотренных техническим проектом производства строительных и монтажных работ. Сдерживающим фактором здесь является не столько уменьшение численности проектировщиков за последние 15 лет, сколько умножение организаций, имеющих лицензию на проектирование объектов строительства (10 тысяч организаций в России против 1,8 тысячи проектных институтов в СССР). Правда, в условиях роста заказов на проектирование наблюдается увеличение потребности в системах автоматизации управления проектными организациями, с преобладанием принципа управления в целом организацией и всеми ее подразделениями.
Безусловно, нельзя было бы говорить об автоматизации проектирования, если бы работа проектировщиков не была почти полностью механизированной. В противном случае, конструкторскую деятельность ждал бы неминуемый паралич, в связи с непреодолимыми затруднениями при передаче, обмене и внесении изменений в большие массивы взаимосвязанных данных. С этой точки зрения задача комплексной автоматизации в условиях нынешних российских стройплощадок не может решаться из-за недостатка этой принципиальной важной предпосылки. Подтверждением чему служит то обстоятельство, что подавляющее большинство строительных машин и механизмов классифицируется по признакам рода выполняемой работы, режима работы и степени универсальности. Иначе говоря, речь идет о механизации конкретных трудовых операций (в том числе инструментом, применяемым для разных операций).
Чтобы проиллюстрировать вышеназванные признаки, можно использовать типичный перечень техники для отделочных работ, подразделяющихся на штукатурные, малярные, кровельные, стекольные, изоляционные. Кроме того, индустриальную отделку помещений, а также работы по устройству и отделке полов в помещениях и вспомогательные работы. Машины, применяемые при отделочных работах, разделяются на шесть основных групп (см. таблицу 1).
Таблица 1. Машины и механизмы для отделочных работ.
Группа оборудования |
Наименование машин и механизмов |
для штукатурных работ |
штукатурные станции и агрегаты; растворо-насосы, цемент-пушки, штукатурно-затирочные машины |
для малярных работ |
мелотерки, краскотерки, краскомешалки, эмульсаторы, клееварки, малярные станции, агрегаты для нанесения шпатлевки, окрасочные агрегаты, электрокраскопульты, краскораспылители, агрегаты для окраски фасадов |
для устройства и отделки полов деревянных, мозаично-бетонных и из рулонных материалов |
машины для острожки и шлифования паркетных полов; для затирки, заглаживания и железнения поверхностей; мозаично-шлифовальные машины, для сварки линолеума |
для стекольных работ |
инструмент для нанесения замазки и забивки шпилек |
для кровельных работ |
механизмы для удаления воды и сушки покрытий; машины и установки для подогрева, перемешивания и транспортировки мастик; агрегаты для нанесения битумных мастик, для очистки, раскатки и прикатки рулонных материалов |
вспомогательное оборудование |
компрессоры, трансформаторы, преобразователи тока, механизированные вышки и люльки и др. |
Гипотетически, любая строительная компания может быть автоматизирована, или хотя бы следующие участки и направления своей деятельности: организация строительно-производственного процесса, снабжение и склады, разработка проектной документации и смет, распределение всех ресурсов по объектам, оптимальность работы машин и механизмов, бухгалтерский учет, налоговый учет, расчет заработной платы с учетом тарифных сеток по профессиям, организация бесперебойного финансирования работ. На практике, особенно в условиях ажиотажного спроса на недвижимость, удается в лучшем случае наладить «лоскутную автоматизацию», т. е. автоматизировать отдельные участки деятельности. Автоматизация строительства, по аналогии с ростом растений, подразумевает непрерывность рабочих операций с максимальной производительностью. Судить о «процветании» здесь можно, учитывая одновременно темпы строительства, объемы производства качественных объектов и удельные трудозатраты. Лидирующее положение японских градостроителей сегодня обеспечивается в первую очередь автоматизацией всего процесса строительства, начинаемого с монтажа ступенчатой платформы для перекрытия верхнего этажа. Дальше оснащенные компьютерной системой контроля роботы точно устанавливают все модули, а автоматические сварочные агрегаты сваривают колонны и балки согласно проекту. По завершении установки всех межэтажных перекрытий интегрированные ступенчатые платформы поднимаются гидравликой на следующий уровень, и весь цикл повторяется. Автоматизированная система позволяет на только резко уменьшить сроки круглосуточного строительства, снизить трудозатраты (в среднем, для 20-этажного здания они сокращаются на 30%) и практически исключить травматизм. Точность выполнения сложных технических проектов является гарантией предсказуемого поведения зданий при землетрясениях, сильных аэродинамических нагрузках и т. п. испытаниях прочности и устойчивости.
2. Как устроены, работают и где применяются погрузчики?
ПОГРУЗОЧНЫЕ МАШИНЫ
Погрузочно-разгрузочные работы — один из наиболее тяжелых и трудоемких производственных процессов в большинстве отраслей народного хозяйства и особенно в строительстве. При относительно высоком техническом уровне наших основных производств на погрузочно-разгрузочных работах еще широко применяют ручной труд, число занятых здесь людей велико, а затраты на эти работы в различных отраслях народного хозяйства составляют от 10 до 40% общих издержек производства. Для механизации погрузочно-разгрузочных работ в строительстве кроме кранов, экскаваторов и различных подъемников используют специальные машины. Такие машины предназначены для погрузки в транспортные средства и разгрузки из них сыпучих, кусковых и штучных грузов, а также для доставки их к месту использования в пределах строительной площадки и выполнения различных монтажных и вспомогательных операций. Они бывают специализированные
, используемые на складах предприятий строительной индустрии и пристанционных складах (скребковый разгрузчик - для разгрузки песка, щебня, гравия и т. п. из железнодорожных платформ; разгрузочно-штабелевочная машина - для разгрузки полувагонов), и универсальные самоходные погрузчики. Последние представляют собой чаще всего колесную или гусеничную подъемно-транспортную машину, снабженную одним или (чаще всего) несколькими сменными рабочими органами.
По принципу действия
различают погрузчики цикличного и непрерывного действия. К первым относятся одноковшовые и вилочные погрузчики, а ко вторым — многоковшовые погрузчики.
По назначению
погрузочно-разгрузочные машины разделяют на погрузчики для штучных грузов — вилочные погрузчики и для сыпучих и мелкокусковых материалов — одно- и многоковшовые погрузчики.
По 'способу разгрузки рабочего органа погрузчики бывают: фронтальные (с передней разгрузкой), полуповоротные (с боковой разгрузкой), перекидные (с задней разгрузкой). Наибольшее распространение в строительстве нашли фронтальные и полуповоротные погрузчики, так как они устойчивы и обеспечивают удобную разгрузку, отличаются высокой маневренностью и производительностью.
Для погрузочно-разгрузочных работ в строительном производстве используют погрузчики и разгрузчики. Практика применения экскаваторов в качестве погрузчиков на карьерах и складах нерудных материалов показала, что они менее эффективны, чем погрузчики.
По роду погружаемых грузов погрузчики делят на погрузчики для штучных грузов (подхватывающие или вилочные) и для сыпучих грузов (зачерпывающие). Зачерпывающие погрузчики делят на одноковшовые и многоковшовые непрерывного действия. Одноковшовые погрузчики являются универсальными и могут применяться в различных условиях. Многоковшовые применяются на базисных складах, в дорожном строительстве и там, где рабочий процесс должен быть непрерывным.
В зависимости от ходового оборудования погрузчики могут быть гусеничные и колесные. Погрузчики на гусеничном ходу имеют высокую проходимость и развивают большое напорное усилие. Колесные погрузчики отличаются большей маневренностью и высокими транспортными скоростями, не разрушают поверхности дорог и площадок складов.
2а) Вилочные погрузчики
Вилочные погрузчики применяют для погрузочно-разгрузочных У вилочных погрузчиков основным видом рабочего оборудования являются вилы, которые служат для погрузки и разгрузки штучных грузов. Эти погрузчики имеют различное сменное оборудование. При оборудовании ковшами или грейферами они выполняют погрузку и разгрузку сыпучих и мелкокусковых материалов, а при оборудовании стрелами их применяют для подъема грузов на небольшую высоту и иногда для монтажа строительных конструкций. Автопогрузчики изготовляют с использованием узлов серийных автомобилей и оснащают, как и одноковшовые погрузчики, комплектом сменных рабочих органов. Однако основной вид рабочего оборудования - вилочный захват, который можно подвести под штучный груз, установленный на подкладках.
Все органы автопогрузчика (рис. 4.22, а) смонтированы на ходовой раме, которая опирается на передние ведущие двухскатные колеса 2 и задние управляемые односкатные колеса 6. В передней части рамы смонтирован грузоподъемник 3 с рабочим органом, а в задней - противовес 5. Последний обеспечивает собственную и грузовую устойчивость движущегося погрузчика. Грузоподъемник (рис. 4.22, б) включает в себя основную раму 9, которая шарнирно прикреплена к раме машины и может отклоняться от вертикали с помощью двух гидроцилиндров № на угол до 3° вперед и до 12° назад, чем обеспечивается захват грУ34
при загрузке и его устойчивое положение при транспортировании. Внутри основной рамы на катках с помощью гидроцилиндра 11 перемещается выдвижная рама 12, по которой на роликах перемещается грузовая каретка 13 с прикрепленными к ней вилами 1. Каретка подвешена 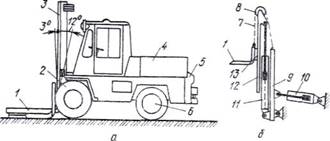
Рис. 4.22. Автопогрузчик:
а — конструктивная схема; 6 — схема грузоподъемника; 1 — вилы; 2,6 — ведущие и управляемые колеса; 3 — грузоподъемник; 4 — двигатель; 5 — противовес; 7 — цепи; 8 — звездочки; 9 — основная рама; 10, 11 — гидроцилиндры; 12 — выдвижная рама; 13 — грузовая каретка
Двух грузовых цепях 7, которые огибают звездочки 8 на выдвижной раме и закрепляются другим концом на основной раме. Такая конструкция образует двухкратный полиспаст для выигрыша в скорости, то есть грузовая каретка движется в 2 раза быстрее, чем шток гидроцилиндра. Такие погрузчики выпускают с грузоподъемностью 2... 10 т и высотой подъема до 4...6 м. Максимальная скорость перемещения автопогрузчика с грузом 6... 15 км/ч, без него - до 45 км/ч.
Техническая производительность (м3
/ч) одноковшовых погрузчиков при работе с сыпучими материалами
ПT
= 3600qКн
/(tц
Kp
) (4.26)
где q- вместимость ковша, м3
; Kн
- коэффициент наполнения ковша; tц
- время цикла, с; Kр
- коэффициент разрыхления материала.
При работе со штучными грузами техническая производительность (т/ч)
Пт
= 3600 GKг
/tц
, (4.27)
где G - грузоподъемность погрузчика, т; Кг
- коэффициент использования по грузоподъемности.
Время цикла включает в себя: время на наполнение ковша, время На
отъезд от забоя; время на подъезд к транспорту или отвалу; время разгрузки и время обратного хода.
Вилочные погрузчики работают на площадках с твердым покрытием покрытием. В соответствии с этим их в основном применяют на складах и в качестве внутризаводского транспорта. Они выполняются на базе автомобилей, поэтому их называют также автопогрузчиками. В качестве привода используют двигатели внутреннего сгорания и электродвигатели, обычно работающие от аккумуляторов. Автопогрузчики выпускают грузонодъемностью 3—5 т, с высотой подъема груза
до 6 м. Скорость подъема груза 3 -=- 50 м/мин, скорость перемещения без груза до 40 км/ч, с грузом — до 20 км/ч.
Рис 1 . Грузоподъёмник вилочного погрузчика
Рабочее оборудование подвешивается на грузоподъемник (рис. 1). Он состоит из основной ( неподвижной ) / и выдвижной (2) рам. К выдвижной раме подвешивается каретка (4), к которой прикрепляется рабочее оборудование. Рама с кареткой поднимается при помощи гидроцилиндра (3) одностороннего действия, установленного на основной раме. При подъеме подвижной рамы одновременно по этой раме перемещается каретка. Это осуществляется благодаря тому, что каретка подвешена на двух цепях (5), один конец которых переброшен через блоки, закрепленные на верхней траверсе подвижной рамы, а второй конец закреплен на основной раме.
Основная рама грузоподъемника смонтирована на раме погрузчика шарнирно и вместе с кареткой может наклоняться в вертикальной плоскости на угол 3—4е
вперед и 12—15и
назад, что осуществляется с помощью двух гидроцилиндров 6.
Вилочные погрузчики выполняют с передним и боковым расположением грузоподъемника. В первом случае погрузчики называются фронтальными, во втором — боковыми. Боковые погрузчики применяют для работ с длинномерными грузами (трубы, сваи).
2б) Одноковшовые погрузчики
Одноковшовый универсальный строительный погрузчик монтируют на базе гусеничных тракторов и колесных тягачей. Он предназначен для механизации погрузочных и строительно-монтажных работ при помощи сменного рабочего оборудования. Главным типом рабочего оборудования является ковш: кроме него погрузчики имеют и другие виды навесного оборудования. На рис. 7.2 показаны основные виды рабочего оборудования
Основной ковш — рабочий орган машины, рассчитанный для работы с различными материалами, объемная масса которых находится пределах 1,4—1,8 т/м3
.
Одноковшовые погрузчики классифицируют по грузоподъемности на легкие — до 2 т, средние—до 4 т, тяжелые — до 10 т и сверхтяжелые — более 10 т. По тину базовой машины погрузчики подразделяют на колесные и гусеничные.
Погрузочное оборудование имеет три модификации: фронтальное, перекидное, полуповоротное. Фронтальным оборудованием можно разгружать материал только со стороны его разработки, полуповоротное обеспечивает и боковую разгрузку. Перекидной тип погрузочного оборудования позволяет вести разгрузку назад.
В настоящее время более распространены строительные фронтальные погрузчики с объемным гидроприводом рабочего оборудования.
Материалы зачерпываются двумя способами: раздельным и совмещенным. При раздельном способе передняя кромка ковша перемещается в глубь штабеля на глубину врезания lпр
, которая больше глубины ковша lк
. Затем ковш поворачивается на угол а3
и поднимается для разгрузки. Совмещенный способ заключается в том, что ковш внедряется в штабель материала на величину, равную приблизительно 0,3 глубины ковша, после чего он поворачивается на угол откоса штабеля; одновременно продолжается перемещение погрузчика и подъем ковша. Движения, сообщаемые ковшу, должны быть такими, чтобы траектория движения режущей кромки была близка к параллельной к откосу штабеля, чтобы сохранялась постоянная толщина снимаемого слоя материала.
При раздельном способе требуются более значительные усилия для внедрения ковша в материал, а также в начальный момент поворота ковша. Коэффициент наполнения k„ в тяжелых материалах обычно составляет 0,4—0,6. Однако при раздельном способе управлять машиной проще, чем при совмещенном, поэтому его можно рекомендовать для погрузки легких сыпучих материалов, в которых можно обеспечить kн
=1,0-1,2.
В гидравлическую схему фронтального погрузчика входит шестеренчатый насос, который подаёт масло через распределитель к гидроцилиндрам. Обычно погрузчик оборудуют гидроцилиндрами опускания и подъёма стрелы и управления рабочим органом.
В современных конструкциях погрузчиков имеются приводы как на передние, так и на задние оси.
Ковш погрузчика подвешивают на специальной рычажной системе, управление которой осуществляется через гидроцилиндры.

а — общий вид; б — кинематическая схема; в — гидросхема; / — гидроцилиндр управления ковшом; 2 — стрела: з — кривошнпно-шатунный механизм управления ковшом: 4 — ковш: 5 — гидроцилиндры подъема стрелы; 6 — поворотная рама; 7 — двигатель; 8 — коробка отбора мощности; 9 — гидротрансформатор; 10 — коробка передач; // — главная передача 4 = 2,67; 12 — задний мост; 13 — ступенчатый редуктор i = 5.4; 14 — i ередини мост; 15 — насос: 16 — фильтр; 17 — масляный бак: 18 — гидровыключатель; 19 — распределитель; 20 — цилиндры ковша; 21 — цилиндры для стрелы
Рис..2. Рабочие органы одноковшовых погрузчиков:
а — ковш для погрузки сыпучих материалов: б. в — ковши прямой и обратной лопаты; г — вилы для штучных грузов; д. е — грейферные устройства; ж — грузоподъемный крюк
Время указано для наиболее рациональной установки транспорта, под углом в 45 к подошве забоя и возможно ближе к ней. В этом случае путь отъезда от забоя составляет 6—8 м, а путь подъезда к транспорту 4—5 м. При больших расстояниях
ta
= l/vt
и t0
= l/va
, где
/ _ длина пути от места загрузки до места разгрузки, м; vr
и v„ — скорости движения погрузчика соответственно с грузом в ковше и порожняком, м/с. Одноковшовые погрузчики
применяют для погрузки-разгрузки, перемещения и складирования сыпучих и мелкокусковых материалов, а также для разработки и погрузки в автотранспорт (или отсыпки в отвал) неслежавшихся грунтов I и II категорий и естественного грунта III категории.
Одноковшовые фронтальные погрузчики на пневмоколесном ходу используют также при производстве земляных работ вместо экскаваторов, особенно на открытых горных разработках. Это стало возможным благодаря ряду преимуществ погрузчиков по сравнению с одноковшовыми экскаваторами: большая вместимость ковша при малой собственной массе (в 6...8 раз меньше массы экскаватора при равной вместимости ковша); высокая скорость передвижения, значительно превышаю-"*я скорость перемещения экскаватора; высокая маневренность, позволяющая проводить работы в стесненных условиях, недоступных экскаватору; может транспортировать грунт на небольшие расстояния со скоростью, соответствующей автомобилю-самосвалу.
Колесные погрузчики имеют массу 0,3 ...85 т, вместимость ковша 0,05...35 м3
и более, мощность 6...500 кВт и более. Их производительность в 2,5...3,0 раза выше, чем у одноковшовых экскаваторов такой же массы. У погрузчиков в 2...3 раза меньше высота копания, чем у одноковшовых экскаваторов, и очень маленький радиус действия, требующий подъезда почти вплотную к забою.
Существующие типы одноковшовых погрузчиков отличаются разнообразием конструктивного исполнения и имеют общее для большинства машин — наличие в передней части ковша. Последний поворачивается вокруг своей оси на угол 50° и поднимается на высоту до 4 м. Сочетание этих движений при одновременном движении машины позволяет наполнять ковш, транспортировать груз и выгружать его на заданной высоте.
Главный параметр одноковшовых погрузчиков — грузоподъемность. По этому параметру они разделяются на сверхлегкие (малогабаритные, до 0,5 т), легкие (0,6...2,0 т), средние (2,0...4,0 т), тяжелые (4,0..., 10,0 т) и большегрузные.
По типу ходового устройства они могут быть пневмоколесными и гусеничными. Первые имеют большие транспортные скорости, не разрушают поверхности дорог и площадок складов. Вторые позволяют развивать в 1,2... 1,5 раза большее, чем у колесных, усилие при внедрении в грунт силой тяги, а также обладают большой маневренностью вследствие возможности разворота на месте, что сокращает продолжительность цикла на 8...25 % и повышает производительность на 20...30%. В качестве базовых машин для погрузчиков применяют специальные пневмоколесные шасси, промышленные тракторы погрузочных модификаций или тракторы общего назначения
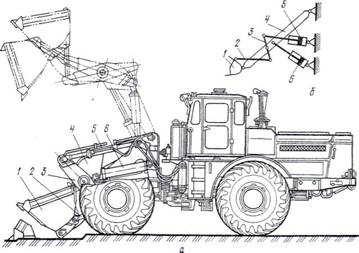
Рис. 4.20. Одноковшовый фронтальный погрузчик (а) и схема его рычажно-гидравлической системы управления (б) :
7 — ковш; 2,3 — рычажные механизмы; 4 — стрела; 5,6 — гидроцилиндры
Фронтальный погрузчик (рис. 4.20) обеспечивает разгрузку ковша со стороны разрабатываемого материала. Он состоит из пневмоколесного трактора с шарнирно сочлененной рамой и ковша 1, укрепленного на стреле 4 и управляемого рычажными механизмами 2,3 с помощью гидроцилиндров 5 двухстороннего действия. Стрелу поднимают и опускают двумя гидроцилиндрами 6. Рычажная система обеспечивает постоянное положение заполненного ковша при его подъеме, что исключает потери загруженного материала.
Цикл работы фронтального погрузчика
, оборудованного ковшом» состоит из следующих операций: перемещение погрузчика к месту
набора материала с одновременным опусканием ковша до требуемой отметки (поверхность дороги, платформы вагона или кузова автомобиля); внедрение ковша в материал; подъем ковша со стрелой; транспортировка материала к месту разгрузки; разгрузка ковша опрокидыванием. Сменное рабочее оборудование расширяет область применения (универсальность) погрузчиков.
Полуповоротные погрузчики (рис. 4.21) в отличие от фронтальных могут обеспечивать разгрузку как впереди, так и сбоку при угле поворота от продольной оси до 90° (рис. 4.21, в). Поворотная платформа 1 с рабочим оборудованием погрузчика опирается на раму 3 машины через опорно-поворотное устройство 2. Вращательное движение поворотной платформы (рис. 4.21,б) осуществляется с помощью двух горизонтально расположенных гидроцилиндров 4, цепи 5 и звездочки 6. Такая конструкция погрузчика позволяет сократить время на развороты и дает возможность применять их в стесненных условиях. Рабочий Цикл полуповоротного погрузчика отличается от рабочего цикла фрон-ального погрузчика тем, что в нем отсутствуют операции на дополнительные развороты машины. Это позволяет сократить продолжительность рабочего цикла на 30...40 %.

Рис. 4.21. Одноковшовый полуповоротный погрузчик:
а — конструктивная схема; б — схема системы поворота; в — зона действия;
1 — поворотная платформа; 2 — опорно-поворотное устройство; 3 — рама;
4 — гидроцилиндр; 5 — цепь; 6 — звездочка
2в) Погрузчики непрерывного действия
Многоковшовые погрузчики
относятся к машинам
непрерывного действия и применяются для погрузки сыпучих и мел-
кокусковых материалов (песок, гравий, щебень, шлак и т. п.) в транспортные средства. Кроме того, их используют для засыпки траншей и фундаментных пазух свеженасыпным грунтом, для обвалования площадок и т. д. Производительность многоковшовых погрузчиков при
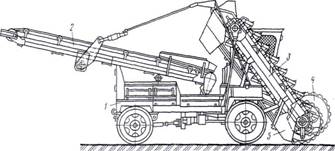
Рис. 4.23. Пневмоколесный погрузчик:
1 — самоходное шасси; 2, 3 — ленточный и многоковшовый конвейеры; 4 -
питатель; 5 — отвал
одной и той же установленной мощности на 40...60% выше, чем одноковшовых, и составляет 40, 80, 160, 250 м3
/ч. Высота разгрузки 2.4... 4,2 м.
Многоковшовые погрузчики различаются по типам ходового устройства, питателя и транспортирующих органов. В качестве ходового устройства используют самоходные гусеничные или пневмоколесные шасси. Для разработки материала и порционной его подачи к конвейеру применяют шнеки, роторы, диски, подгребающие лапы. В первом случае материал разрабатывается и подается с помощью одного или нескольких шнеков, установленных впереди машины. Роторные погрузчики разрабатывают материал шаровыми или ковшовыми фрезами. В дисковых погрузчиках материал подается двумя дисками, вращающимися во встречном направлении. Подгребающие лапы подают материал благодаря специальной кинематике их движения.
В качестве транспортирующего органа, как правило, используют ковшовые, скребковые и ленточные конвейеры. Наибольшее распространение в строительстве получили пневмоколесный погрузчик с питателем шнекового типа и ковшовым конвейером (рис. 4.23). Он состоит из пневмоколесного самоходного шасси 1, на котором смонтирован наклонный многоковшовый конвейер 3 с питателем 4 шнекового типа, и поворотного в плане и в вертикальной плоскости ленточного разгрузочного конвейера 2. Для лучшей подачи материала к питателю на раме ковшового конвейера установлен отвал 5. Технологический процесс осуществляется следующим образом: материал захватывается шнековым питателем, сгребается к оси машины и подается в ковш непрерывно движущегося конвейера, а далее через приемное устройство и ленточный конвейер в транспорт или отвал. Питатель выполнен в виде двух соосных шнеков с правым и левым направлением спирали, что обеспечивает подгребание материала к центру машины. По мере забора материала погрузчик передвигается в сторону штабеля, а при малом его сечении движется все время на него. Привод всех механизмов, кроме ковшового конвейера, гидрофицирован.
Техническая производительность многоковшовых погрузчиков зависит от производительностей шнекового питателя и ковшового конвейера.
Основные направления развития строительных погрузчиков: улучшение технико-экономических и экологических показателей; повышение энергонасыщенности, тягово-сцепных качеств и напорных усилий, маневренности, -надежности, расширение номенклатуры сменных рабочих органов; увеличение параметров рабочего оборудования; дальнейшее совершенствование систем гидропривода.
Производительность многоковшовых погрузчиков при одной и той же установленной мощности на 40—60% выше, чем одноковшовых.
Их целесообразно применять на кирпичных заводах, заводах строительных деталей, железнодорожных станциях с большими объемами разгрузки и погрузки сыпучих материалов. Кроме того, их используют для разделения сыпучих материалов на фракции, для чего па них монтируют специальные виброгрохоты.
Рис. 7.6. Погрузчик непрерывного действия:
о общий вид; б — кинематическая схема
Многоковшовые погрузчики можно эффективно использовать для разгрузки железнодорожных платформ, при этом погрузчик, двигаясь на самой платформе, сбрасывает материал на сторону. Эти
"погрузчики можно применять в технологических линиях (на заводах строительных деталей) или при строительстве дорог. В последнем случае погрузчики загружают песок и гравий в сушильные барабаны и в смесители.
Общий вид многоковшового погрузчика показан на рис. 7.6, а. Рабочим органом является шнековый питатель, который состоит из двух шпеков с правым и левым направлением спирали. Шнеки расположены по обеим сторонам ковшового элеватора. При вращении питателя погружаемый материал подается к ковшам, что способствует лучшему загребанию материала ковшами. Внизу под шнековым питателем прикреплен скребок. Обычно материалы с элеватора разгружаются на ленточные конвейеры, которые подают его в транспортные средства.
У некоторых погрузчиков материал разгружается в транспортные средства через бункера или лотки.
На,рис. 7.6, б показана кинематическая схема погрузчика. Двигатель / через зубчатые колеса 2 приводит в движение конические передачи 4. Одна из них сообщает движение через цепную передачу ковшовому элеватору 7 и шнековому питателю 8, а другая коническая пара через цепную передачу приводит во вращение барабан 3 ленточного конвейера. Двигатель / через коробку передач 9 и карданные валы 6 передает вращение заднему и переднему мостам 5 и 10.
В строительстве помимо многоковшовых применяют роторные погрузчики. Их изготовляют с обычным ротором и с ротором в виде шаровой головки.
Производительность многоковшовых погрузчиков (техническая) зависит от производительности шнекового питателя и производительности ковшового элеватора, которые определяются как для машин непрерывного действия.
Производигельность шнекового питателя
Пт
= 60(πD2
/4)tnϕ, м3
/ч, (7.6)
где D—диаметр шнека, м; / — шаг винта, м; п—частота вращения» об/мин; ф — коэффициент заполнения, равный 0,6—0,9. Производительность ковшового элеватора
Пт
= 3,6(qv/t)ϕ1
, м3
/ч, (7.7)
где q— емкость ковша элеватора, л; v— скорость ковшовой цепи, м/с; t — шаг расположения ковшей, м; ϕ, — коэффициент заполнения ковшей, равный 0,7—1,1. Последнее значение принимается для рыхлых сыпучих материалов без крупных кусков, заполняющих ковши с шапкой».

3.Расскажите о перебазировке башенного крана, его устойчивости
3а) Башенные краны
Башенные краны перемешают грузы по сложным пространственным траекториям. Благодаря стреле, закрепленной в верхней части башни, они имеют большое подстрелковое пространство, в котором размещается возводимое здание или сооружение. В связи с этим их широко используют в строительстве.
По мобильности башенные краны бывают стационарные, передвижные и самоподъемные. Передвижные краны оснащают, как правило, рельсово-колесным ходовым устройством, что повышает безопасность их использования. На башенных кранах обычно применяют многомоторный электропровод.
Система индексации отечественных башенных кранов имеет следующую структуру.
Помимо букв КБ (кран башенный) в обозначение крана могут входить четыре цифровых значения и два буквенных. Цифра, стоящая на первом месте, означает размерную группу крана и характеризует его грузовой момент, две последующие цифры - порядковый номер модели, четвертая цифра, стоящая после точки, - номер модели крана, характеризующий отличия в длине стрелы, высоте подъема и других параметрах. Первое буквенное обозначение указывает номер модернизации, которой подвергался кран. Если модернизация не проводилась, это обозначение отсутствует. Последнее буквенное обозначение указывает на климатическое исполнение крана: ХЛ — северное, Т и ТВ — соответственно для сухих и влажных тропиков. Если кран будет эксплуатироваться в умеренном климате, буквенное обозначение не проставляется. Например, индекс КБ-674.3А обозначает: кран башенный, шестой размерной группы, то есть грузовой момент - 300...550 т • м. с неповоротной башней, третье исполнение после первой модернизации, предназначен Для работы в умеренном климате.
Наибольшее распространение получили краны нескольких конструктивных схем. Краны выпускают с поворотной башней и нижним расположением опорно-поворотного устройства и с неповоротной баш-Неи
и верхним расположением опорно-поворотного устройства. Изменение вылета стрелы обеспечивается наклоном стрелы и передвижением Слежки на стреле. Сочетание указанных конструктивных признаков может быть любым. На рисунке 5.10 показаны схема башенного крана с
поворотной башней и изменением вылета стрелы путем ее наклона "основные его параметры (ГОСТ 13555-79):
Q(т) - грузоподъемность, то есть максимальная масса груза, который может поднять кран, причем обычно кран может поднять наибольший груз при минимальном вылете;
L(м) - вылет стрелы, то есть расстояние от центра массы груза вращения крана;
М (т • м) — грузовой момент, М = QL.
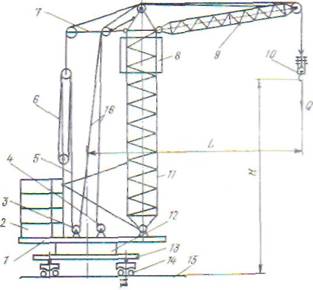
Рис. 5.10. Схема башенного крана с поворотной башней:
1 - поворотная платформа; 2 - противовес; 3.4 — стреловая и грузовая лебедки; 5, 6 — стреловые канат и полиспаст; 7 — консоль; 8 — кабина управления; 9 — стрела; 10 - крюковая подвеска; 11 — башня; 12 — опорно-поворотное устройство и механизм поворота; 13 - рама ходового устройства; 14 - ходовые тележки; 15 — крановые пути; 16 - грузовой канат
Для башенных кранов грузовой момент — главный параметр. К основным их параметрам относят высоту подъема, скорость всех рабочих перемещений, базу, колею, габариты, установленную мощность механизмов, массу.
Башенные краны монтируют на крановых путях 15 (см. рис. 5.1О), которые должны соответствовать "Инструкции по устройству, эксплуатации и перевозке рельсовых путей для строительных башенных кранов" СН 78 — 73 и "Правилам устройства и безопасной эксплуатации грузоподъемных кранов". По рельсам крановых путей перемешаются ходовые тележки 14, две из них обычно приводные, а две неприводные. Механизм перемещения приводных тележек содержит электродвигатель, нормально замкнутый двухколодочный тормоз с электромагнитным или электрогидравлическим управлением, редуктор и открытую зубчатую передачу. Ходовые тележки устанавливают на вертикальных осях с возможностью поворота для прохождения закруглений рельсового пути
На раме ходового устройства 13 установлено опорно-поворотное устройство и механизм поворота 12. Опорно-поворотное устройство кранов с поворотной башней представляет собой специально выполненный шариковый или роликовый подшипник качения диаметром около 2 м. Этот подшипник воспринимает не только осевые и радиальные нагрузки, но и нагрузки в виде опрокидывающего момента. На опорно-поворотном устройстве установлена поворотная платформа. На последней смонтирован противовес 2, стреловая 3 и грузовая 4 лебедки и башня 11. В верхней части башни установлена кабина управления 8 и шарнирно закреплена стрела 9. С противоположной стреле стороны башни закреплена несущая обводные блоки консоль 7. Стреловой канат 5, сбегая с барабана лебедки, проходит через блоки стрелового полиспаста 6, второй конец каната 5 закреплен неподвижно. При наматывании стрелового каната 5 на барабан полиспаст 6 укорачивается, подвижные блоки полиспаста опускаются и при помощи дополнительных расчальных канатов, на которых они подвешены, поднимают стрелу. Так осуществляют изменение вылета. Грузовой канат 16, наматываясь на барабан лебедки 4, огибает обводные блоки, блоки на конце стрелы и крюковой подвеске 10 и поднимает груз. Второй конец грузового каната огибает обводные блоки и закрепляется на стреловом барабане лебедки 3. Сделано это для того, чтобы при изменении вылета (подъеме и опускании стрелы) высота подвеса груза не изменялась. Тем не менее на практике небольшие изменения высоты подвеса груза происходят. На рисунке 5.11 показана схема башенного крана с неповоротной башней и изменением вылета стрелы при помощи грузовой тележки. Такие краны в основном изготавливают без ходового устройства и устанавливают на фундаменте /. Их часто используют при высотном строительстве, при этом, чтобы повысить устойчивость башни, ее крепят к строящемуся зданию. В верхней части башни 2 закреплена кабина управления 3. На башне установлен наголовник 9, он соединен с башней при помощи центральной цапфы и расположенных по окружности катков, Которые (цапфа и катки) и образуют опорно-поворотное устройство. К наголовнику шарнирно прикреплена стрела 10, а с противоположной бороны — консоль 5. На последней смонтированы противовес 6, стреловая 8 и грузовая 7 лебедки и механизм поворота 4. По стреле может перемещаться грузовая тележка 13. Стреловая лебедка 8 служит для удержания стрелы. Существуют конструкции, в которых стрела удерживается при помощи жестких тяг. Применяют краны, у которых стреловая лебедка может наклонять стрелу, что повышает высоту подъема груза. При этом грузовая тележка либо крепится на конце стрелы, либо перемещается по наклонной стреле. Грузовой канат 11 сбегает с барана лебедки 7, огибает обводные блоки, установленные на конце стрелы, на грузовой тележке, на крюковой подвеске 12. Конец каната закреплен неподвижно у основания стрелы. Блоки грузовой тележки и Раковой лебедки, огибаемые канатом, образуют грузовой полиспаст.
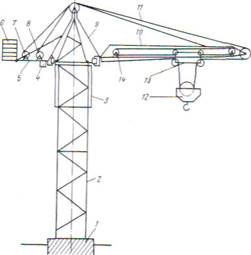
Рис. 5.11. Схема башенного крана с неповоротной башней:
' — фундамент; 2 — башня; 3 -кабина управления; 4 — механизм поворота; 5 — консоль; 6 — противовес; 7,8 — грузовая и стреловая лебедки; 9 — наголовник; 10 — стрела; 11 — грузовой канат; 12 — крюковая подвеска; 13 — грузовая тележка; 14 — лебедка перемещения грузовой тележки
При подъеме груза канат 11 наматывается на барабан лебедки 7, выли стрелы при этом не изменяется.
Механизм поворота 4 содержит электродвигатель, нормально замкнутый тормоз, редуктор и открытую зубчатую передачу. При повороте шестерня этой передачи катится по неподвижному зубчатому колесу, закрепленному на башне, приводя во вращение наголовник с закрепленными на нем элементами конструкции. Вылет стрелы изменяют путем перемещения грузовой тележки 13 при помощи лебедки 14, с барабана которой сбегают обе ветви каната. Концы каната крепят к грузовой тележке. При изменении вылета (и горизонтальной стреле) высота подвеса груза остается постоянной.
Самоподъемные краны используют при строительстве высотных зданий (150 м и выше), имеющих металлический или мощный железобетонный монолитный каркас. Кран крепят на строящемся здании и мере его возведения при помощи дополнительных механизмов по. мают по этому зданию.
Краны с изменением вылета путем наклона стрелы (с
подъемной стрелой) при тех же параметрах (вылете, высоте подъема, грузоподъемности) на 15...20% легче кранов с изменением вылета при помощи грузовой тележки (с балочной стрелой). Подъемная стрела позволяет увеличить высоту подъема груза при уменьшении ее вылета, обеспечивает хорошую маневренность в стесненных условиях строительной площадки. Краны с подъемной стрелой более технологичны в изготовлении, удобнее в монтаже и перевозке. Однако подъемные стрелы имеют и некоторые недостатки по сравнению с балочными стрелами: отсутствие строго горизонтального перемещения груза при изменении вылета, что повышает мощность двигателя стреловой лебедки; незначительная и неравномерная горизонтальная скорость перемещения при изменении вылета; уменьшение зоны обслуживания с одной стоянки, так как груз нельзя подвести близко к башне крана.
Применение кранов с поворотной башней также способствует снижению их веса, так как вес механизмов не нагружает башню. Однако при большой высоте башни, чтобы уменьшить ее гибкость, башню приходится крепить к строящемуся зданию. В этом случае целесообразнее использовать краны с неповоротной башней.
Подъемные стрелы получили наибольшее распространение в мобильных кранах с поворотной башней. Балочные стрелы применяют в основном в кранах со значительной высотой подъема и неповоротной башней. Обычно краны монтируют на объекте при минимальной высоте башни, а в процессе возведения здания или сооружения высоту башни увеличивают у кранов с поворотной башней чаще подращиванием снизу, а у кранов с неповоротной башней - наращиванием сверху.
Приставные краны (рис. 5.22, б) выпускают грузоподъемностью 6,3; 8; 10; 12,5 т с вылетом стрелы до 45 м и высотой подъема до 150 м; скоростью подъема груза 0,33 -¥■ 1,5 м/с; скоростью изменения вылета 0,5 м/с; частотой вращения поворотной части 0,5 -г- 0,7 об/мин.
Наиболее часто применяют краны с поворотной башней. У них центр тяжести находится ниже, чем у кранов с поворотным оголовком, так как большинство узлов расположено у основания крана. Благодаря этой особенности масса кранов с поворотной башней меньше, чем с неповоротной. Эти краны проще монтировать, демонтировать, транспортировать; башня при нагрузке меньше деформируется, что приводит к меньшей раскачке груза.
Кран с поворотной башней (рис. 5.22, г) состоит из трубчатой или решетчатой башни /, закрепленной на упорно-поворотном устройстве 2, на котором установлен противовес 3. В верхней части башни монтируется распорка 4 для направляющих роликов и оголовок 5. На башне закреплена стрела 6. На кране с балочной стрелой противовес размещается на консоли 7 (см. рис. 5.22, д).
Опорно-поворотное устройство устанавливают на опорной раме 8 (рис. 5.22, з) с четырьмя поворотными кронштейнами 9, которые опираются на балансирные тележки 10 с противоугонными захватами //. Поворотные кронштейны позволяют перемещаться крану на криволинейных участках рельсового пути при малых радиусах закругления в 7—8 м по внутреннему рельсу.
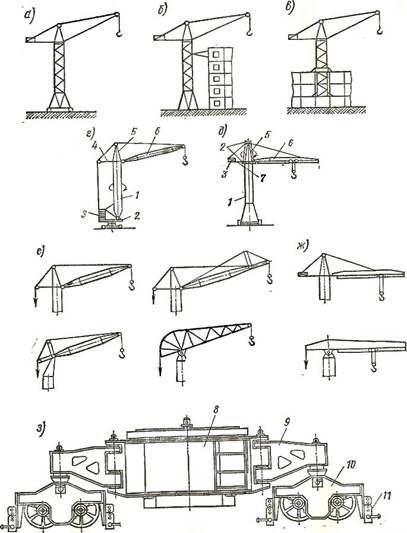
Рис. 5.22. Башенные краны
Простота монтажа и демонтажа, возможность демонтировать и монтировать эти краны без разборки на отдельные узлы делает их особенно эффективными.
Краны с подъемной стрелой, у которых вылет стрелы осуществляется ее наклоном, более просты по конструкции, но к недостаткам этих кранов надо отнести то, что у них нельзя полностью использовать подкрановое пространство. Наименьший вылет стрелы у них составляет 30% от наибольшего. При таком креплении стрелы трудно достигнуть точной наводки элементов конструкции, так как при подъеме или опускании стрелы груз перемещается как в вертикальном, так и в горизонтальном направлении.
В кранах с балочной стрелой перемещение груза требует меньшей энергии, но маневренность таких кранов ниже, чем у кранов с подъемной стрелой.
Стационарные (приставные) башенные краны устанавливают на фундаменте и обслуживают площадку с одной стоянки.
Самоподъемные башенные краны применяют главным образом при ргроительстве многоэтажных и высотных зданий.
На рис. 5.23, с показана кинематическая схема отдельных механизмов башенного крана с подъемной стрелой и схема запасовки канатов. Стрела поднимается лебедкой и стреловым полиспастом на подвижной обойме (траверсе) 2, несущей два блока. Полиспаст подъема стрелы четырехкратный. Три блока полиспаста находятся на неподвижной обойме 6, жестко прикрепленной к поворотной платформе 7. Один конец каната подъема стрелы жестко закреплен на той же не-
141 подвижной обойме и перекинут через неподвижный блок /, другой конец каната закреплен на стреловой лебедке.
Механизм подъема стрелы одновременно служит и механизмом опускания груза в процессе подъема стрелы, что обеспечивает движение груза по горизонтали во время ее подъема. Для этой цели один из концов подъемного каната закреплен на барабане лебедки подъема стрелы так, что во время наматывания каната подъема стрелы на барабан канат подъема груза сматывается с барабана. Груз и стрела поднимаются при помощи крановых лебедок.
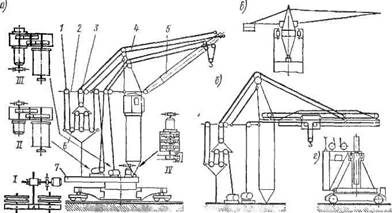
Рис. 5.23. Кинематические схемы башенных кранов:
/__ механизм привода передвижения крана; // — то же. лебедкн подъема груза; /// — то же, лебедки подъема стрелы; IV— механизм поворота башни со стрелой или только стрелы
Лебедки состоят из кранового фланцевого электродвигателя, двухступенчатого редуктора, тормоза, барабана, выносной опоры и двух сферических опор редуктора. Для плавной посадки груза лебедка снабжена тормозным генератором, обеспечивающим снижение скорости в 5—6 раз, и двух колодочным тормозом с гидротолкателем.
Механизм поворота включает фланцевый вертикально расположенный электродвигатель и планетарный зубчатый редуктор с вертикальными валами. На ведомом валу редуктора снизу располагается шестерня, сцепляющаяся с зубчатым венцом опорно-поворотного круга. Тормоз располагается на втором конце вала электродвигателя в горизонтальном положении. Смазка шестерен и подшипников редуктора принудительная. Редуктор имеет две проушины, которыми он крепится к поворотной платформе.
Кран опирается на четыре двухколесные балансирные тележки. Две тележки являются ведомыми (неприводными), две — ведущими. Привод тележки осуществляется от фланцевого двигателя через червячный редуктор. Тележки снабжены центральным захватом для закрепления крана за рельсы в нерабочем состоянии.
Для восприятия грузового момента и вертикальных нагрузок поворотная часть крана соединяется двухрядным шариковым опорно-поворотным кругом с неповоротной частью. На внутреннем кольце круга предусмотрен зубчатый венец, с которым связана ведущая шестерня механизма поворота. На рис. 5.23, б показана схема крана с балочной стрелой. Горизонтальное перемещение груза производится грузовой кареткой, движущейся вдоль стрелы, но может также осуществляться поворотом стрелы или передвижением всего крана. Стрела удерживается на кране канатами и полиспастным устройством, подобным тому, каким оборудованы краны с подъемной стрелой.
Поворотный оголовок (рис. 5.23, в) устанавливается на подпятнике и роликах. Поворотная башня (рис. 5.23, г) устанавливается на поворотной платформе.
3б) Демонтаж башенных кранов
Монтаж и демонтаж башенных кранов с поворотной башней могут осуществляться без их разборки на отдельные сборочные единицы. Для монтажа и демонтажа используются механизмы крана.
Демонтаж крана показан на рис. 5.24. Стрелу крана опускают в крайнее нижнее положение, после чего разъединяют среднюю и крайнюю секции стрелы. Эти секции прикрепляют к башне (положение III). Затем ее разъединяют с основанием и опускают в горизонтальное положение. Башню со стрелой укладывают на домкрат (положение IV), поворачивают тележку (положение V) и под тележку крана подводят ось 2 с автомобильными колесами, после чего под передвижную часть крана подводят тягач 3 и опускают домкрат. В таком виде кран транспортируют. '
Монтаж осуществляется в обратном порядке.
Эксплуатация башенных кранов допускается только после их освидетельствования, включающего осмотр, статические и динамические испытания. Согласно правилам Госгортехнадзора СССР статические испытания проводятся под нагрузкой, на 25% превышающей максимальную грузоподъемность крана. Во время испытания стрелу устанавливают относительно неповоротной части в положение, соответствующее наименьшей устойчивости, при этом груз поднимается на высоту 100—200 мм и выдерживается 10 мин. Динамические испытания проводятся грузом, на 10% превышающем грузоподъемность крана. При этом выполняются все рабочие движения и проверяется действие механизмов и их тормозов.
Устойчивость крана проверяют для следующих условий: 1) при действии рабочего груза — грузовая устойчивость; 2) при отсутствии груза — собственная устойчивость определяется для двух случаев — при возможности и невозможности свободного вращения крана; 3) при внезапном снятии нагрузки на крюке; 4) при монтаже (демонтаже) крана.
Расчет грузовой устойчивости крана должен производиться для условий действия опасной комбинации нагрузок относительно ребра опрокидывания, когда кран по устойчивости максимально приближается к предельному состоянию. Расчет на устойчивость производится для свободно стоящих кранов без учета действия рельсовых захватов и свободно подвешенных стрел.


Рис. 5.24. Демонтаж башенного крана с поворотной башней
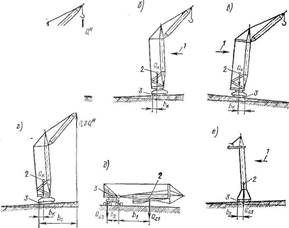
Рис. 5.25. Схемы для расчета устойчивости. / — направление ветра; 2 — центр тяжести; 3 — ребро опрокидывания
Кран с поворотной башней и подъемной стрелой обычно демонтируют в такой последовательности (рис. 5.12). Высоту башни уменьшают до минимальной. Стрелу опускают вертикально вниз. При необходимости, чтобы уменьшить длину стрелы, последнюю складывают. Башню вместе со стрелой переводят в горизонтальное положение и закрепляют на седельном устройстве автомобиля-тягача. Демонтируют и отдельно перевозят противовес. Домкратом или самоходным краном приподнимают раму ходового оборудования и к ней снизу крепят инвентарную пневмоколесную ось. С объекта на объект кран перемещают как автопоезд. Для монтажа крана на новом объекте необходимо заранее Установить одну секцию крановых путей. Монтируют кран в обратной последовательности. Монтаж и демонтаж башенных кранов проводят при помощи их механизмов и одного- двух стреловых самоходных Кранов.
С целью повышения безопасности работы башенные краны оборудуют автоматическими приборами безопасности. К ним относят ограничители перемещений (передвижения крана, угла наклона стрелы, высоты подъема крюковой подвески, передвижения грузовой тележки, поворота крана и т. д.) и грузоподъемности. Первые отключают механизмы, крана до достижения предельного положения его элементов. Вторые отключают механизмы крана в случае превышения номинальной его грузоподъемности. Все механизмы крана оснащаются нормально-замкнутыми тормозами, нулевой и концевой электрозащитой. На башенных кранах устанавливают анемометры, дающие звуковые и световые сигналы при опасной скорости ветра. Кроме того, краны оборудуют рельсовыми захватами, указателями вылета и соответствующей ему грузоподъемности.
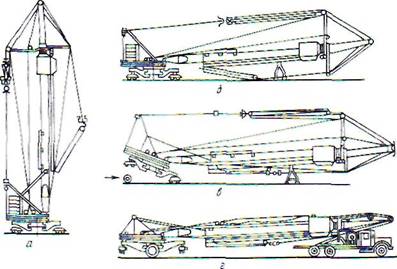
Рис. 5.12. Схема демонтажа крана:
а, б — опускание стрелы и башни; в - установка пневмоколесной оси; г -транспортное положение
3в) Устойчивость башенного крана
На свободно стоящий кран действуют различные нагрузки, создающие опрокидывающий момент относительно ребра опорного контура. Опорный контур башенных кранов ограничивается линией, образующей прямоугольник со сторонами, проходящими по рельсам подкранового пути и осям ходовых колес или балансирных тележек.
Силами, создающими опрокидывающий момент Мот являются: основная нагрузка — вес поднимаемого груза и грузозахватных устройств;
дополнительные нагрузки — инерционные, возникающие в период пуска, торможения и изменения скоростей механизмов (подъема, передвижения и изменения вылета стрелы), центробежные силы, возникающие при вращении поворотной части крана и изменении наклона стрелы, ветровое давление на наветренную часть крана и груза, а также атмосферные осадки в виде снега или наледи (116).
Противодействие опрокидыванию свободно стоящего крана оказывает только собственная сила тяжести, если центр тяжести лежит внутри опорного контура. (Сила ветра и уклон пути всегда рассматриваются как факторы неблагоприятные.)
Произведение силы тяжести крана (вместе с пригрузом) на расстояние от центра тяжести до ребра опрокидывания создает удерживающий момент, который должен быть всегда больше опрокидывающего момента.
Согласно правилам Госгортехнадзора, коэффициент запаса устойчивости определяют для двух случаев: от опрокидывания крана в сторону груза (грузовая устойчивость) и от опрокидывания в сторону противовеса при нерабочем состоянии крана (собственная устойчивость). При воздействии на кран основной нагрузки без учета дополнительных нагрузок и влияния уклона пути (опорной поверхности) коэффициент запаса устойчивости будет равен отношению удерживающего момента крана, установленного на горизонтальной плоскости, к опрокидывающему моменту от основной нагрузки и должен быть не менее 1,4.
При воздействии на кран как основной, так и дополнительных нагрузок учитываются влияния наклона пути и момента от ветровой нагрузки, совпадающего по направлению с моментом от основной нагрузки. В этом случае коэффициент запаса устойчивости рассчитывается как отношение удерживающего момента крана, стоящего на наклонной плоскости, за вычетом суммы моментов от дополнительных нагрузок к опрокидывающему моменту от основной нагрузки и должен быть не менее 1,15
Устойчивость крана в нерабочем состоянии (собственная устойчивость) определяется при наименьшем вылете стрелы, ветровой нагрузке, направленной в сторону противовеса, и с учетом уклона пути (опорной поверхности). Коэффициент запаса собственной устойчивости рассчитывается как отношение удерживающего момента крана, стоящего на наклонной поверхности, к опрокидывающему моменту от ветровой нагрузки и также должен быть не менее 1,15
При расчете устойчивости угол наклона а опорной поверхности (пути) принимается для кранов на железнодорожном, пневмоколесном и гусеничном ходу при установке без выносных опор —3°, при установке на выносные опоры —1,5°.
Для железнодорожных кранов, работающих без выносных опор, необходимо учитывать превышение наружного рельса на криволинейных участках пути.
Для строительных башенных кранов учитывают возможность превышения одного рельса над другим на 100 мм независимо от размера колеи.
|
Устойчивость крана проверяют для следующих условий: 1) при действии рабочего груза — грузовая устойчивость; 2) при отсутствии груза — собственная устойчивость определяется для двух случаев — при возможности и невозможности свободного вращения крана; 3) при внезапном снятии нагрузки на крюке; 4) при монтаже (демонтаже) крана.
Расчет грузовой устойчивости крана должен производиться для условий действия опасной комбинации нагрузок относительно ребра опрокидывания, когда кран по устойчивости максимально приближается к предельному состоянию. Расчет на устойчивость производится для свободно стоящих кранов без учета действия рельсовых захватов и свободно подвешенных стрел.
Для обеспечения надежной и безопасной работы кран должен обладать устойчивостью против опрокидывания, т. е. способностью противодействовать опрокидывающим кран нагрузкам. Обязательным условием сохранения устойчивости крана является превышение или равенство удерживающего момента сумме опрокидывающих.
Когда кран находится на строительной площадке, на него действуют моменты от сил, стремящихся опрокинуть кран (от массы груза, ветровые нагрузки, силы инерции движущихся частей, нагрузки от уклона), и силы, удерживающей кран от опрокидывания, которая зависит от собственной массы крана G0. Эти силы с учетом плеча их действия относительно ребра опрокидывания крана Р создают соответственно опрокидывающий и удерживающий моменты.
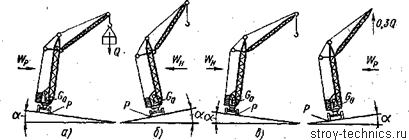
Рис. 5. Схема определения устойчивости крана:
а — в рабочем состоянии (грузовая устойчивость), б, в — в нерабочем (собственная устойчивость), е — при внезапном снятии нагрузки; Р — ребро опрокидывания
Расчет устойчивости производится для следующих случаев: при работе крана с,грузом (грузовая устойчивость, рис. 5, а), нерабочего состояния (собственная устойчивость, рис. 5, б, в), внезапного снятия нагрузки с крюка (обрыв груза, рис. 5, г), монтажа (демонтажа) крана.
Устойчивость крана определяют для наиболее неблагоприятных условий его работы. Так, при расчете грузовой устойчивости крана предполагают, что кран поднимает груз Q, равный грузоподъемности крана на данном вылете, при этом груз имеет максимально возможную площадь; ветровые нагрузки рабочего состояния Wp действуют со стороны противовеса, кран стоит на уклоне а (в сторону груза). При проверке собственной устойчивости крана считают, что на кран действуют ветровые нагрузки нерабочего состояния в сторону противовеса W„, кран стоит на уклоне а (в сторону опрокидывания) без груза. Если кран в нерабочем состоянии имеет возможность свободного вращения под действием ветровых нагрузок, при проверке собственной устойчивости считают, что ветер направлен со стороны противовеса. Для проверки устойчивости при внезапном снятии нагрузки считают, что кран располагается на уклоне в сторону опрокидывания, нагрузка на крюке принимается направленной вверх, а ветровая нагрузка рабочего состояния Wp направлена со стороны стрелы.
Устойчивость при монтаже (демонтаже) рассчитывают для различных этапов монтажа (демонтажа): при положении монтируемой (демонтируемой) башни у земли, при отсутствии стрелы, при выдвижении башни и в другие моменты, зависящие от конструкции крана и способа монтажа.
В соответствии с ГОСТ 13994—75 «Краны башенные строительные. Нормы расчета» устойчивость проверяют по следующим формулам: грузовая устойчивость ксМ0 + М% + Мл – 0,95Му, собственная устойчивость Мн ^ 0,95Л1У, при внезапном снятии нагрузки 0,ЗМо + МР <; 0,95Му, при монтаже (демонтаже) крана кМп – 0,95Л1Н,
где Л10, Мд, Мр, MUH —опрокидывающие моменты относительно ребра опрокидывания соответственно от силы тяжести груза, динамических нагрузок и от ветровой нагрузки в рабочем.и нерабочем состоянии крана: кг — коэффициент, учитывающий режим работы, грузоподъемность и условия работы крана; Му — удерживающий момент относительно ребра опрокидывания от силы тяжести крана; к — коэффициент перегрузки; Мп, Мн — соответственно опрокидывающий момент от поднимаемых частей крана и удерживающий от неподвижных частей крана.
Грузовую устойчивость крана проверяют как для максимального, так и для минимального вылетов. Собственную устойчивость кранов с маневровым изменением вылета контролируют при положении стрелы на максимальном вылете. Устойчивость кранов с установочным изменением вылета устанавливают для положения, когда стрела поднята до минимального вылета.
Правилами Госгортехнадзора предписывается по окончании работы закреплять краны противоугонными захватами за рельсы. При этом усилия от закрепления за рельсы, создающие дополнительный удерживающий момент, при расчете собственной устойчивости не учитываются. Они идут в запас устойчивости кран
Список использованной литературы:
1. И.И. Гальперин, Н.Г. Домбровский «Строительные машины», Москва, «Высшая школа», 1980г
2. С.С. Добронравов, В.П. Сергеев «Строительные машины»
3. Мачульский И.И. Погрузочно-разгрузочные машины. М.: Желдориздат, 2000
4.Невзоров Л.А., Подзельский Г.Н., Романюха В.А. Строительные башенные краны. М.: Высш. шк., 1986.
5.Добронравов С.С., Дронов В.Г. Строительные машины и основы автоматизации. М.: Высш. шк, 2001.
6. Также использовались Интернет-ресурсы о перспективах развития машиностроения
|