ФЕДЕРАЛЬНОЕ АГЕНСТВО ПО ОБРАЗОВАНИЮ РФ ФГУ СПО КРАСНОДАРСКИЙ МЕЖРЕГИОНАЛЬНЫЙ ТЕХНИКУМ
КОНТРОЛЬНАЯ РАБОТА
По ТПМС
Вариант № 2
студента 3 курса группы 3СП
Жидкова Сергея Юрьевича
г.Краснодар 2010 г.
1. Технология изготовления электродов
Складирование материалов электродного покрытия и проволоки:
Материалы покрытия поступают на склад в железнодорожных вагонах или контейнерах 'насыпью в кусках илив виде готовых порошков в мешках или банках.
Разгружают вагоны с помощью механической лопаты, вакуум-трубы или вручную в специальные контейнеры, бункера или траншеи. Затаренные материалы складывают в штабеля.
Материалы должны храниться строго по партиям; разные партии даже одноименного материала смешивать запрещается. Допуск в производство каждой новой партии материала разрешается после получения положительного результата анализа заводской химической лаборатории. Материалы, поступающие с нового месторождения, подвергаются эталонному контролю. До полного расходования партии материала запрещается брать в работу новую партию.
Склад должен обеспечивать сохранность материалов от попадания влаги и загрязнения.
Материалы, годные для производства, отпускаются в цех с обязательным сопроводительным ярлыком, на котором следует указывать наименование материала, дату поступления, номер партии и массу.
Все виды обработки данного материала должны фиксироваться на ярлыке с обязательной отметкой фамилии рабочего. По мере использования материала сопроводительные ярлыки подкалывают к рапорту мастера; таким образом всегда известно, из каких партий материалов изготовлены определенные партии электродов.
Проволоку также следует хранить и расходовать по партиям независимо от того, как она поступает: в бухтах или намотанная на катушках.
Принимают материалы по внешнему виду и сертификату. Для разрешения материала в производство необходимо произвести его химический анализ в заводской лаборатории. Пробы материалов для химического анализа отбирают по ГОСТ 4423—48.
Технологическая схема производства
Производство сварочных электродов заключается в соответствующей обработке каждого материала, входящего в покрытие, дозировке по рецепту, изготовлении однородной сухой и мокрой смеси, нанесении определенного слоя этой смеси на стержни, сушке и прокалке; готовых электродов .
Все материалы покрытия проходят следующую обработку дробление, размол, просев, дозировку, сухое смешивание, смешивание сухой шихты с жидким стеклом, рубку проволоки на стержни, нанесение на стержни покрытия, провяливание, сушку и прокалку электродов, сортировку, взвешивание и упаковку электродов.
Электроды с фтористокальциевым (основным) покрытием очень чувствительны к малейшим нарушениям технологического процесса. Все операции обработки материалов покрытия следует тщательно выполнять, параметры жидкого стекла строго выдерживать, замесы хорошо перемешивать. Величина замесов должна быть но возможности меньшей ввиду того, что такая смесь долго храниться не может. Температурный режим печи следует строго соблюдать, так как такие электроды в большой степени склонны к трещинообразованию и вздутию покрытия во время прокалки.
При изготовлении электродов малых диаметров (1—2,5 мм) требуется более тонкий помол материалов покрытия и длительное перемешивание замесов для усреднения; необходимо также повысить требования к качеству электродных стержней и эксцентричности покрытия.
Дробление и размол ферросплавов
Минералы и ферросплавы, поступающие от поставщиков в крупных кусках, подвергают дроблению до размеров кусков 15—20 мм.
Основная задача, которую преследуют при размоле ферросплавов, заключается в получении необходимой фракции с минимальным содержанием пыли. Кроме того, всегда надо помнить, что ферромарганец и ферроптан взрывоопасны при размоле.
Размол ферросплавов можно производить следующими способами
:
· на мельницах непрерывного действия в среде инертного газа с одновременным просевом;
· путем мокрого помола;
· на мельницах периодического действия с добавкой инертного материала и последующим просевом на механических ситах.
Размол ферросплавов на мельницах непрерывного действия в среде инертного газа с одновременным просевом— процесс достаточно производительный, фракция получается однородной и почти не содержит пыли.
Мокрый помол обеспечивает полную взрывобезопасность, ферросплав получается частично пассивированным, не содержит пылевидной фракции.
Технология размола ферросплавов мокрым путем на мельнице типа 2ШМ-0
. В мельницу загружается 675 кг стальных шаров, в том числе 15% диаметром 50 мм, 45%диаметром 60мм и 50% диаметром 80мм. Раздробленный, таким образом, ферросплав питателем подается в мельницу со скоростью 300 кг/ч, сюда же добавляется хромовокислый калий из расчета 0,2% от массы ферро
сплава. По мере размола ферросплав уносится водой. Поступление воды отрабатывается и регулируется в зависимости от требуемой фракции ферросплава. Пульпа, содержащая размолотый ферросплав, направляется в центрифугу. После фугирования остаточная влага в ферросплаве составляет не более 2%.
Технология размола ферромарганца на мельнице периодического действия типа ШМ-1П. До настоящего времени для размола ферромарганца используют установки периодического действия с последующим просевом на механических ситах.
В мельницу загружают 900 кг стальных шаров (625 кг диаметром 80—85 мм и 275 кг диаметром 60— 65 мм), 350 кг дробленого ферромарганца и 6% инертной добавки. Инертной добавкой может служить любой минерал в виде порошка. Для этой цели лучше использовать молотую слюду, если она входит в состав покрытия электрода изготовляемой марки. Время размола 20—25 мин. После отключения мельницы необходима выдержка 15—20 мин для оседания пыли, затем ферромарганец выгружают через решетку, которую устанавливают на разгрузочный люк для задержания шаров.
Просев размолотого ферромарганца производится через сетку № 04 (331 отв/см2
) по ГОСТ 6613—53.
Оставшуюся на сетке крупную фракцию подвергают повторному размолу по следующей технологии: в мельницу загружают 350 кг ферромарганца, 3% инертной добавки, время размола 20—25 мин. После размола вторичную фракцию можно просеивать через сетку № 05 (198 отв/см2
) по ГОСТ 6613—53. В контейнер готового ферромарганца мельник обязан положить ярлык с указанием даты размола и просева и своей фамилии.
Пассивирование ферросплавов
Свежеразмолотые порошки ферросплавов очень активно вступают в реакцию с щелочами жидкого стекла при изготовлений электродов, поэтому ферросплавы предварительно подвергают пассивированию.
Известны следующие методы пассивирования: 1) мокрая обработка водой или пассивирующими средствами; 2) путем прогрева; 3) путем «остаривания» (окисления с поверхности) на воздухе, с последующим внесением пассивирующих средств в жидкое стекло или в мокрый смеситель при изготовлении замеса.
В качестве пассивирующего средства применяют растворы марганцевокислого или хромовокислого калия.
При мокром пассивировании в противень с молотым ферросплавом наливают 2%-ный водный раствор марганцевокислого калия или 5%-ный раствор хромовокислого калия и периодически, при 24-ч выдержке, перелопачивают. Затем раствор сливают, ферросплав высушивают и просеивают через соответствующую сетку.
Пассивирование путем прогрева — просеянный ферросплав прогревают на механическом сушиле или противне при температуре 160°С в течение 30 мин при периодическом перелопачивании.
Остаривание — выдержку просеянного ферросплава па воздухе в течение 5—6 суток можно ускорить периодическим перелопачиванием.
Если применяют остарепный таким образом ферросплав, при изготовлении мокрого замеса достаточно залить в бегуны насыщенный раствор марганцевокислого калия (6,5%-ный водный раствор) из расчета ЗОО см3
раствора на 100 кг сухой шихты. Если применяют соль хромовокислого калия как пассивирующее средство, ее можно загружать непосредственно в автоклав при варке жидкого стекла. В автоклав загружают хромовокислый калин в пределах 0,1—0,5% от количества загружаемой силикатной глыбы, затем это жидкое стекло применяют при изготовлении мокрых замесов. При использовании остаренных на воздухе ферросплавов достаточно загружать в автоклав 0,1% хромовокислого калия.
С учетом требований эстетики производства, техники безопасности и трудоемкости, лучшим является третий метод пассивирования, по которому требуется лишь создать недельный запас просеянного ферросплава.
Размол рудо-минерального сырья
Размол руд и минералов производят на мельницах непрерывного действия с сепарацией, и пневмотранспортом,
а также на мельницах с одновременным просевом на мельницах периодического действия.
При размоле на мельницах непрерывного действия с сепарацией и пневмотранспортом загрузку дробленого материала в мельницу отрабатывают так, чтобы за единицу времени масса загружаемого материала и масса размолотого годного порошка, уносимого пневмотранспортом, были равны и максимальны.
Материал по мере размола с помощью пневмотранспорта передается в сепаратор, где отделяется крупная фракция от годной, крупный порошок направляется по трубам в мельницу на домол, годная фракция по отдельным трубопроводам поступает в циклоны, где оседает и через «мигалки» передается в бункера дозировочного отделения. Пылевидная фракция воздухом уносится далее на фильтры, где задерживается, очищенный воздух выдается в атмосферу.
Пневмотранспорт создается мощными вентиляторами типа ВВД-8 и др.
Скорость воздуха отрабатывается в каждом отдельном случае экспериментально для каждого материала и зависит также от длины и диаметров трубопроводов пневмотранспорта, заданной величины фракции материала и производительности мельницы.
При загрузке мельницы следует учитывать, что оптимальная норма заполнения объема мельницы шарами составляет 30—40%.
Дозировка материалов и сухое смешивание
В цехах, построенных в последнее время, имеются автоматические линии дозировки материалов и сухого смешивания. Почти везде работают автоматические весы типа ДМС-1-,20 и ДП-20. Сбор взвешенных материалов осуществляется ленточным транспортером или вибротрубой.
Для смешивания шихты применяют барабанные смесители в виде усеченного конуса, валковые смесители или же смешивание производят при помощи сжатого воздуха.
Наиболее эффективным смесителем является барабан в виде усеченного конуса с лопастями на внутренней поверхности.
Весь процесс дозировки материалов и сухого смешивания при полной автоматизации производится нажатием одной кнопки.
Взвешенные материалы поступают в смеситель, где и течение 10—12 мин усредняются до полной однородности. Правильность работы весов и однородность смешивания контролируются систематически.
Хранят шихту по замесам в контейнерах с открывающимся конусным дном или в специальных бункерах, где замесы наслаиваются один на другой. При втором варианте хранения нарушается систематичность контроля качества шихты по замесам, теряется возможность изъятия бракованного замеса. Кроме того, при длительном хранении и ссыпании шихты может произойти расслаивание, отчего нарушается ее однородность. Поэтому хранение шихты по замесам в контейнерах следует считать более технологичным.
Рубка проволоки на стержни
Рубка проволоки на стержни производится на правильно-отрезных станках разных типов. Отличаются станки в основном конструкцией режущего устройства: летучие ножи (ножи укрепляются на вращающихся роликах) и гильотинный нож. Угол среза стержней получается лучше на станках с. гильотинным резом, но эти с ганки менее производительны и сложнее по конструкции.
Перед заправкой проволоки в правильно-отрезной станок рубщик обязан убедиться, что проволока проверена контролером ОТК. Правильная установка технологического инструмента в соответствии с диаметром проволоки и требуемый уход за станками дают возможность одному рубщику обслуживать одновременно три-четыре станка при работе с 1-т катушек.
Нарубленные стержни с помощью специального устройства перегружаются в контейнеры и транспортируются к прессам или с помощью транспортера переносится от станков непосредственно к прессам.
Технология изготовления мокрых замесов
Сухая шихта по замесам или определенная доза сухойшихты переносится в бегунковый смеситель, куда с помощью автоматического дозатора и другого устройства подается заданное количество жидкого стекла требуемой характеристики. Время перемешивания 10— 16 мин. Смесь должна быть однородной, без сухих комков.
Для удобства загрузки мокрого замеса в пресс и равномерной опрессовки изготавливают брикеты. Брикеты готовят непосредственно возле бегункового смесителя и готовые транспортируют к электродообмазочному агрегату, или готовый замес транспортируют к агрегату, где на прессе его брикетируют. Для загрузки мокрой шихты в брикетировочный пресс применяют специальный червячный питатель.
На 20-т прессах типа АОЭН-1 смесь подается в брикетировочное устройство с помощью стругача.
Прокалка электродов
Влажность покрытия электрода после опрессовки составляет 10—12%. Эта влага должна быть удалена при прокалке почти полностью, при этом электродное покрытие не должно трескаться, склеиваться и проми^ наться. Прокалка должна обеспечить влагостойкость покрытия.
В настоящее время существует целый ряд конструкций камерных и конвейерных печей для: прокалки электродов.
Влажность покрытия электрода после опрессовки свежеопрессованные электроды выдерживают на воздухе в течение 24 ч, при этом теряется около 50% влаги покрытия (так называемое естественное провяливание) затем электроды на рамках загружают в камерные печи для прокалки.
В высокопроизводительных современных цехах электродообмазочный агрегат находится в потоке с прокалочной печью. Свежеопрессованные электроды поступают непосредственно в прокалочную печь. Постепенно повышение температуры по зонам от 50°С до температуры прокалки обеспечивает требуемую технологию прокалки электродов. Заданная температура прокалки указывается в паспортах на электрод каждой марки и колеблется от 200 до 400°С. При этом электроды основного типа прокаливаются при более высокой темпера туре (360—400°С).
Влагостойкость покрытия обеспечивается применением высокомодульного жидкого стекла и соответствующим для каждой марки температурным режимом прокалки. Остаточная влажность прокаленных электродов с кислым покрытием не должна превышать 0,5%, а в электродах с основной обмазкой — ОД %.
Влагостойкость для всех электродов обязательна.
Сортировка, взвешивание и упаковка готовых электродов
При соблюдении технологического процесса по всем операциям и высокой культуры производства электроды но внешнему виду должны полностью удовлетворять требованиям ГОСТ 9466—60. Механические свойства и химический состав металла шва должны соответствовать ГОСТ 9467—60. Малейшее отклонение от технологии производства ухудшает качество электродов и их внешний вид. Поэтому технологический процесс должен строго подвергаться пооперационному контролю, а готовая продукция проверяться в соответствии с требованиями указанных ГОСТов.
Отсортированные по внешнему виду остывшие электроды взвешивают пачками по 5 кг, увязывают, заворачивают в водонепроницаемую бумагу (ГОСТ 8828—61) пли картонные пачки и укладывают в стопки. На каждую пачку наклеивают ярлык.
Ярлык должен содержать следующие сведения об электродах: 1) наименование организации поставщика) марку электродов, тип, номера ГОСТов, которым соответствуют электроды; 3) массу одной пачки; 4) диаметр, номер партии и дату изготовления; 5) рекомендуемые режимы сварочного тока; 6) механические свойства металла шва; 7) технологические параметры при гварке; 8) основные технологические свойства; 9) условное обозначение электродов по ГОСТ 9467—60.
На большинстве современных производств взвешивание механизировано, упаковка в бумагу или в пачки в ящики до сих пор производится вручную. Разработанные автоматы для сортировки, взвешивания и упаковки электродов имеют ряд недостатков.
Упакованную продукцию подвергают проверке. До полной проверки готовую продукцию потребителю не отгружают.
По ГОСТ 9467—60 .предусматривается следующее условное обозначение электродов: например, марка электродов МР-3, тин Э-46, диаметр 5,0 мм, покрыта рутилловое МР-3-Э46-5, ГОСТ 9467—60.
Технология производства электродов на каждом предприятии разрабатывается в соответствии с действующим оборудованием и другими специфическими условиями. Разработанная и утвержденная технология производства является законом для всех работающих.
2. Виды сварочных электродов
Основная роль сварочных электродов
— подача электропитания для нагрева в точку сварки. Кроме того, при помощи электродов можно существенно изменять химический состав сварного шва или производить легирование свариваемого металла в точке сварки. При дуговой сварке обычно используются плавящиеся электроды, к которым относится сварочная проволока (она бывает сплошная и порошковая), присадочные прутки, сварочные ленты и пластины. Если сварочный процесс предусматривает плавление, то при помощи таких электродов вводится присадочный материал. Неплавящимися электродами называют электродные стержни и специальные электроды для контактной сварки.
В зависимости от типа свариваемых материалов и требуемых характеристик сварочного шва, электроды можно разделить на несколько групп:
Электроды для сварки углеродистых и низколегированных конструкционных сталей
К этой группе относятся электроды, предназначенные для сварки углеродистых сталей, содержащих до 0,25% углерода, и низколегированных сталей с временным сопротивлением разрыву до 590 МПа. Основными характеристиками электродов являются механические свойства металла шва и сварного соединения: временное сопротивление разрыву, относительное удлинение, ударная вязкость, угол изгиба. По этим показателям электроды классифицируются на следующие типы (цифры за буквой «Э» соответствуют минимальному временному сопротивлению разрыву металла шва или сварного соединения в кгс/мм2):
Э38, Э42, Э46 и Э50 — для сварки сталей с временным сопротивлением до 490 МПа;
Э42А, Э46А и Э50А — для сварки сталей, когда к металлу шва предъявляются повышенные требования по относительному удлинению и ударной вязкости;
Э55 и Э60 — для сварки сталей с временным сопротивлением разрыву свыше 490 МПа и до 590 Мпа.
В зависимости от типа покрытия электроды для сварки углеродистых и низколегированных сталей характеризуются различным уровнем сварочно-технологических свойств. Типом покрытия в значительной степени определяется возможность ведения сварки во всех пространственных положениях, род сварочного тока, производительность сварочного процесса, склонность к образованию пор, а в некоторых случаях — содержание водорода в наплавленном металле и склонность сварных соединений к образованию трещин.
Различают следующие виды покрытий
:
- Основу кислого покрытия электродов
составляют оксиды железа, марганца и кремния. По механическим свойствам металла шва и сварного соединения электроды относятся к типам Э38 и Э42. Электроды с кислым покрытием не склонны к образованию пор при сварке металла, покрытого окалиной или ржавчиной, а также при удлинении дуги. Сварку можно выполнять постоянным и переменным током. Но при использовании таких электродов металл шва имеет повышенную склонность к образованию горячих трещин.
- Основу рутилового покрытия
составляет одноименный концентрат (природный диоксид титана). Металл шва, выполненный такими электродами, соответствует спокойной или полуспокойной стали. Стойкость металла шва против образования трещин у электродов с рутиловым покрытием выше, чем у электродов с кислым покрытием. По механическим свойствам металла шва и сварного соединения большинство марок электродов относятся к электродам типа Э42 и Э46.Рутиловые электроды обладают целым рядом преимуществ по сравнению с другими видами электродов. Они обеспечивают стабильное и мощное горение дуги при сварке переменным током, малые потери металла на разбрызгивание, легкую отделимость шлаковой корки, отличное формирование шва. Рутиловые электроды мало чувствительны к образованию пор при изменении длины дуги, при сварке влажного и ржавого металла и при сварке по окисленной поверхности.
- В состав ильменитового покрытия
электродов в качестве основного компонента входит ильменитовый концентрат (природный концентрат диоксида титана и железа).Такие электроды по свойствам занимают промежуточное положение между электродами с кислым и рутиловым покрытиями.
- В электроды с основным покрытием
входят карбонаты и фтористые соединения. Металл, наплавленный электродами с основным покрытием, по химическому составу соответствует спокойной стали. Благодаря низкому содержанию газов, неметаллических включений и вредных примесей, металл шва отличается высокими показателями пластичности и ударной вязкости при нормальной и пониженной температурах. Кроме того металл шва обладает повышенной стойкостью против образования горячих трещин. По механическим свойствам металла шва и сварных соединений электроды с основным покрытием относятся к электродам типа Э42А, Э46А, Э50А и Э60.Но по технологическим характеристикам электроды с основным покрытием уступают другим видам электродов. Их недостатки — высокая чувствительность к образованию пор при увлажнении покрытия и удлинении дуги. Сварка обычно ведется постоянным током обратной полярности. Перед сваркой электроды с основным покрытием требуют обязательной прокалки при температурах (250-420°С).
- Целлюлозный тип покрытия
содержит большое количество (до 50%) органических составляющих, как правило, целлюлозы. Металл, наплавленный целлюлозными электродами, по химическому составу соответствует полуспокойной или спокойной стали. По механическим свойствам металла шва и сварных соединений электроды с целлюлозным покрытием соответствуют электродам Э42, Э46 и Э50. Для целлюлозных электродов характерно образование равномерного обратного валика шва при односторонней сварке на весу, возможность сварки вертикальных швов способом сверху вниз. Но, в то же время металл шва содержит повышенное количество водорода.
Электроды для сварки легированных конструкционных сталей повышенной и высокой прочности.
В эту группу входят электроды, предназначенные для сварки легированных сталей с временным сопротивлением разрыву свыше 590 МПа. Существует два технологических варианта, по которым производят сварку конструкций из этих сталей: с последующей термической обработкой сварных соединений и без нее.
При сварке с последующей термической обработкой применяют электроды, обеспечивающие получение равнопрочных сварных соединений. По ГОСТ 9467-75 стандартизировано пять типов электродов для сварки конструкционных сталей повышенной и высокой прочности: Э70, Э85, Э100, Э125 и Э150. Стандарт регламентирует содержание в наплавленном металле серы и фосфора, количество которых не должно превышать 0,030% и 0,035% соответственно.
Следует отметить
, что при сварке конструкций, работающих в экстремальных условиях, при выборе конкретной марки электрода необходимо принимать во внимание химический состав свариваемого металла и электрода. Данные по химическому составу приводятся в нормативных документах и, в более общем виде, в условном обозначении электродов.
При сварке конструкций без последующей после сварки термической обработки, особенно, когда равнопрочность сварных соединений не является обязательным условием, используют электроды, обеспечивающие получение металла шва с аустенитной структурой. Получаемые сварные соединения отличаются высокой стойкостью против образования трещин, а металл шва — повышенной пластичностью и вязкостью. Сварка такими электродами производится с учетом особенностей, присущих электродам, предназначенным для сварки высоколегированных сталей. Такие электроды можно использовать и при сварке высоколегированных сталей и разнородных сталей.
Электроды для наплавки
В эту группу входят электроды, предназначенные для дуговой наплавки поверхностных слоев с особыми свойствами (кроме электродов для наплавки слоев из цветных металлов). Электроды изготавливают и поставляют в соответствии с требованиями ГОСТ 9466-75 и ГОСТ 10051-75.
Электроды для наплавки поверхностных слоев по химическому составу наплавленного металла и твердости при нормальной температуре классифицируются на 44 типа, согласно ГОСТ (например, электроды типа Э-16Г2ХМ, Э-110×14В13Ф2, Э-13×16Н8М5С5Г46). Наплавленный металл многих электродов регламентируется техническими условиями предприятий-изготовителей.
В зависимости от принятой системы легирования и условий работы получаемого наплавленного металла электроды для наплавки могут быть условно разделены на шесть групп. Это — электроды, обеспечивающие получение:
- низкоуглеродистого низколегированного наплавленного металла с высокой стойкостью в условиях трения металла о металл и ударных нагрузок;
- среднеуглеродистого низколегированного наплавленного металла с высокой стойкостью в условиях трения металла о металл и ударных нагрузок при нормальной и повышенных температурах (до 600-650°С);
- углеродистого, легированного (или высоколегированного) наплавленного металла с высокой стойкостью в условиях абразивного изнашивания и ударных нагрузок;
- углеродистого высоколегированного наплавленного металла с высокой стойкостью в условиях больших давлений и высоких температур (650-850°С);
- высоколегированного аустенитного наплавленного металла с высокой стойкостью в условиях коррозионно-эрозионного изнашивания и трения металла о металл при повышенных температурах (до 570-600°С);
- дисперсноупрочняемого высоколегированного наплавленного металла с высокой стойкостью в тяжелых температурно-деформационных условиях (910-1100°С).
Необходимо отметить
, что производство наплавочных работ требует применения специальных технологий. В зависимости от химического состава и состояния основного и наплавляемого металлов технологии могут включать обязательное выполнение таких операций, как предварительный и сопутствующий подогрев, термическую обработку и др. — для получения заданных эксплуатационных свойств наплавляемой поверхности.
Электроды для холодной сварки и наплавки чугуна.
К этой группе относятся электроды, предназначенные для устранения дефектов в чугунных отливках, а также электроды, используемые при ремонте вышедшего из строя оборудования и восстановления изношенных деталей. В ряде случаев электроды могут быть применены при изготовлении сварно-литых конструкций.
Технология холодной сварки и наплавки чугуна ведется без предварительного подогрева, с минимальным тепловложением короткими валиками протяженностью 25-60 мм с охлаждением каждого наложенного валика на воздухе до температуры не более 60°С. Электроды позволяют получать металл шва с заданными свойствами в виде стали, сплавов на основе меди, никеля, железноникелевого сплава и др.
Электроды для сварки высоколегированных сталей и сплавов
Различают две группы электродов, предназначенных для сварки высоколегированных сталей и сплавов на железоникелевой и никелевой основах:
- электроды для сварки коррозионно-стойких материалов,
- электроды для сварки жаростойких и жаропрочных материалов.
Согласно действующей классификации к высоколегированным сталям относят сплавы, содержание железа в которых более 45%, а суммарное содержание легирующих элементов не менее 10%. К сплавам на никелевой основе относят сплавы с содержанием никеля не менее 55%. Промежуточное положение занимают сплавы на железоникелевой основе.
В соответствии с ГОСТ 10052-75 электроды для сварки высоколегированных коррозионно-стойких, жаростойких и жаропрочных сталей и сплавов по химическому составу наплавленного металла и механическим свойствам металла шва и наплавленного металла классифицируются на 49 типов. Наплавленный металл значительной части электродов, регламентируется техническими условиями предприятий-изготовителей.
Химический состав и структура наплавленного металла электродов для сварки высоколегированных сталей и сплавов отличается — и иногда весьма существенно — от состава и структуры свариваемых материалов.
Основными показателями, решающими вопрос выбора таких электродов, является обеспечение основных эксплуатационных характеристик сварных соединений (механических свойств, коррозионной стойкости, жаростойкости, жаропрочности), стойкости металла шва против образования трещин, требуемого комплекса сварочно-технологических свойств.
Электроды для сварки высоколегированных сталей и сплавов имеют покрытие основного, рутилового и рутилово-основного видов. Скорость плавления, а следовательно и коэффициент наплавки электродов со стержнями из высоколегированных сталей и сплавов существенно выше, чем у электродов для сварки углеродистых, низколегированных и легированных сталей. Это свойство электродов обусловлено их низкой теплопроводностью и высоким электрическим сопротивлением.
Однако эти свойства обуславливают необходимость применения при сварке пониженных значений тока и уменьшения длины самих электродов. Сварка, как правило, производится постоянным током обратной полярности.
Электроды для сварки теплоустойчивых сталей
К группе электродов для сварки теплоустойчивых сталей (марок ЦУ-5, ЦЛ-17, ОЗС-11, ТМЛ-1У, ТМЛ-3У, ЦЛ-39, АНЖР-2 и др.) относятся электроды, предназначенные для сварки низколегированных и легированных теплоустойчивых сталей. (Теплоустойчивыми называются стали, работающие при повышенных температурах — до 550-600°С).
Основными характеристиками электродов являются
химический состав наплавленного металла и механические свойства металла шва при нормальной температуре. При выборе электродов учитывают также максимальную рабочую температуру, при которой регламентированы показатели длительной прочности металла шва.
Согласно ГОСТ 9467-75 электроды для сварки теплоустойчивых сталей по показателям химического состава и механических свойств наплавленного металла и металла шва классифицированы на девять типов: Э-09М, Э-09МХ, Э-09×1М, Э-05×2М, Э-09×2М1, Э-09×1М1НФБ, Э-10×3М1БФ, Э-10×5МФ. Электроды могут иметь рутиловое и основное покрытие.
Вместе с тем, при сварке теплоустойчивых сталей применяют электроды, не регламентированные ГОСТ 9467-75, основным назначением которых является сварка других классов стали (например, электроды АНЖР-1, предназначенные, главным образом, для сварки разнородных сталей).
Сварку теплоустойчивых сталей в большинстве случаев выполняют с предварительным подогревом и последующей термообработкой.
3. Оборудование для обработки материалов
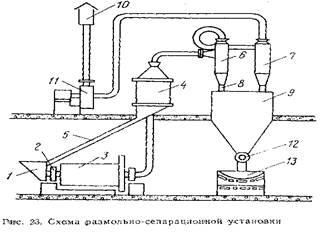
Для размола и классификации рудо-минералов широко применяют хорошо механизированные или автоматические линии размольно-селарационных установок. Работая под разрежением, они почти полностью устраняют пылевыделение в агрегатах и соединениях трубопроводов. Хорошая работа размольно-сепарационых установок требует точной регулировки всех агрегатов потоков воздуха, как по скорости, так и по количеству. Почти все установки индивидуальны, так как на каждом заводе вносятся в схему и конструкцию этих установок дополнения и усовершенствования. На рис. приведена принципиальная схема размольно-сепарационной установки.
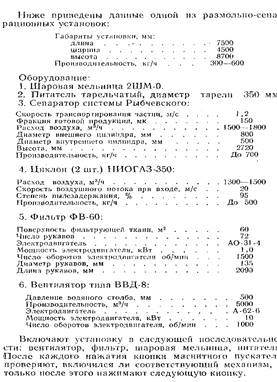
Подлежащий размолу материал после дробления и утки поступает с помощью питателя 1,через полую цапфу 2 в шаровую мельницу 3. Измельченный продукт через вторую полую цапфу подается воздушным потоком в классификатор 4, где происходит разделение на крупную и мелкую фракцию. Крупная фракция возвращается в мельницу по трубе 5, а мелкая улавливается циклонами 6 я 7, установленными последовательно, откуда через мигалку 8 попадает в бункер готового материала 9. Поток воздуха с пылевидной фракцией дополнительно очищается в многорукавном фильтре 10, после чего выбрасывается в атмосферу. Воздушный поток создается центробежным пылевым вентилятором высокого давления 11, установленным в конце технологической линии, что обеспечивает работу всех агрегатов и соединений установки под разрежением. Готовый материал через весовой дозатор 12 попадает на транспортер 13 и направляется в смеситель.
Размол материалов
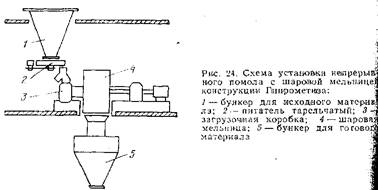
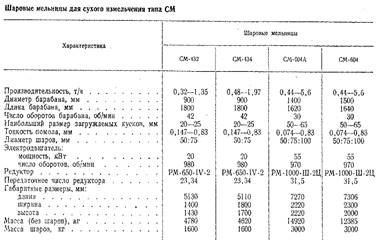
В качестве размольных механизмов используют главным образом шаровые мельницы промышленного изготовления. Они бывают различной конструкции и производительности. В табл. 11приводятся данные шаровых мельниц, наиболее часто применяемых в электродных цехах.
Установка непрерывного помола с шаровой мельницей конструкции Гипрометиза показана на рис. 24
Мельница предназначена для обработки руд, минера лов и ферросплавов.
При размоле ферромарганца в мельницу необходим! подавать инертный газ из расчета 1
м3
/ч.
Материал из бункера с помощью питателя через цагфу попадает в шестигранный барабан. Внутри барабан! установлены броневые плиты, в которых имеются щеля. На пяти гранях из шести установлены сетки. Мелки! материал, прошедший через сетки, поступает в бункер готовой продукции, а непрошедший возвращается в размольный барабан:
Производительность, кг/ч. 300
Электродвигатель. А-52
Мощность электродвигателя, кВт. 4,5
Число оборотов электродвигателя, об/мин 950
Питатель тарельчатый. АО-31
Мощность электродвигателя, кВт 0,6
Число оборотов электродвигателя, об/мин 1410
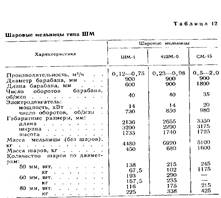
В табл. приведена техническая характеристика шаровых мельниц типа ШМ.
Вибрационные сита (грохоты электромагнитные вибрационные)
Характеристика |
Вибрационные сита |
Гипрохим |
С-265 |
С-265а |
СМ-402 |
Размер сита, мм ... .
Число сит
Число колебаний в минуту
Амплитуда колебаний, мм.
Мощность электродвигателя, кВт
Масса грохота, кг ... .
|
385x1470 3
3000 До 3
1,2 700
|
700x1000 1
3000 До 3
0,9 182
|
700X1000 2
3000 До 3
0,9 246
|
600x1000
1
3000 0,5—1,0
0,9
530
|
Вибрационные сита:
Завод |
Славянский |
Характеристика |
Куйбышевгид- |
завод |
ростроя |
200—400 |
200—400 |
0,5 |
0,6 |
2800 |
3000 |
Мощность электродвигателя, кВт . . . |
0,4 |
0,5 |
Габаритные размеры, мм: |
1400 |
1810 |
730 |
775 |
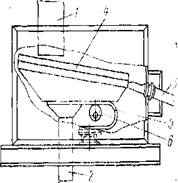
Схема вибрационного сита завода Куйбышевгидростроя: 1 - труба для питания сита; 2 — труба для выхода готового материала; 3 — труба для возврата отсевов; 4 — короб сита с сеткой №40; 5 —рессорная опора; 6 — электровибратор с мотором.
Установка для обработки ферросплавов мокрым способом
На некоторых предприятиях применяется мокрый способ обработки ферросплавов. В установку для обработки ферросплавов мокрым способом входит следующее оборудование (рис. 27).
1.Шаровая мельница 2ШМ-0.
2.Питатель ПЛ-1.
3.Центрифуга фильтрующая типа ТН-800Н:**
Диаметр ротора, мм. 800
Высота ротора, мм 400
Емкость ротора, м3
0,09
Число оборотов ротора, об/мин 1250
Масса загрузки, кг 180
Электродвигатель АОП-42-4
Мощность электродвигателя, кВт . 2,8
Габариты, мм:
Длина 1600
Ширина 1245
Высота 1020
Масса, кг 910
Оборудование для изготовления стержней
Для изготовления стержней электродов применяют правильно-отрезные станки, которые делятся на две группы: с «летучими» ножами и гильотинными.
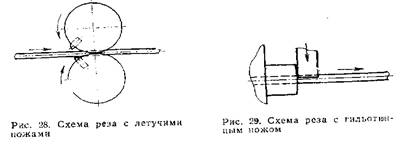
Правильно-отрезные станки имеют: мотовило (с постоянным барабаном или регулируемым и наклонным), правящий барабан (рис. 30) с пятью или семью твердосплавными (ВК-б или чугун перлитный) сухарями с числом оборотов 3000-7000 в минуту и режущим устройством, которое не определяет группу станка.

Рис. Схема правильного барабана: / — сухари
Правильно-отрезные станки с летучими ножами проще, обычно более производительны, но на них трудно получить чистый перпендикулярный рез и строго постоянную длину стержня. Они рассчитаны для правки и рубки малоуглеродистой стали.
Правильно-отрезные станки с гильотинным ножом обычно предназначены для рубки и правки стержней из любой стали — малоуглеродистой, высоколегированной и из цветных металлов, практически любой длины.
Техническая характеристика станков
Станки |
Характеристика |
ПОС-1 |
ОСЗ-МД |
ОСЗ |
ИО-3213 |
Диаметр проволоки, мм . , . |
3—6 |
2—3 |
4—6 |
2—6 |
Длина стержня, мм .... |
225—450 |
250 и 350 |
450 |
450 |
Производительность, м/мип |
58—100 |
56 |
81 |
58—100 |
Число оборотов правильного |
барабана, об/мин |
4680 |
4800 |
5000 |
4700 |
Мощность двух электродвига |
телей, кВт |
8,5 |
1,6 |
6,2 |
9,0 |
Габаритные размеры, мм; |
длина |
1600 |
1920 |
1200 |
1740 |
ширина |
660 |
600 |
845 |
772 |
высота |
1200 |
1150 |
1170 |
1305 |
Рез стержней чистый, длина одинаковая (в пределах 2 мм). Значительные преимущества правильно-отрезных станков с гильотинным резом способствуют их широкому применению.
Инструмент, применяемый для правильно-отрезных станков:
1.Тянущие ролики (сталь СтЗ с наплавкой рабоч. поверхности электродами Т-540 или Ш-7; сталь ШХ15
3) при прогибе стержня—чрезмерный прижим роликов, повышенная упругость проволоки, неправильная установка сухарей;
4) при волнистости стержня — неправильная установка сухарей, плохая шлифовка' сухарей, недостаточное число оборотов правильного барабана.
4. Изготовление сварочной проволоки
Для производства электродов применяют стальную сварочную проволоку углеродистую, легированную и высоколегированную по ГОСТ 2246—60.
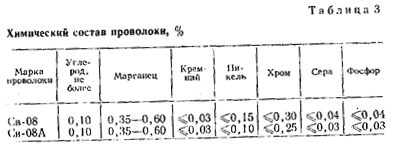
В зависимости от области применения электродов в паспорте указывается марка проволоки. Наибольшее распространение получила углеродистая проволока марок Св-08 и Св-08А, химический анализ проволоки этих марок указан в табл. 3.
Допускаемые отклонения по диаметру для проволоки диаметром от 4 до 6 мм составляют минус 0,16 мм. Овальность для указанных диаметров 'проволоки допускается в размере 0,08 мм. Проволока поступает в электродные цехи намотанная на катушки массой до 1 т или в бухтах по 80-100кг.
Технология изготовления жидкого стекла
Сырьем для изготовления жидкого стекла является силикатная глыба. При соблюдении технологии разварки силикатной глыбы модуль ее сохраняется для жидкого стекла.
Для ускорения процесса разварку глыбы производят и автоклавах с применением острого или глухого пара давлением до 500 кН/м2
(5 ат). Автоклавы используются горизонтальные вращающиеся или стационарные вертикальные. Наиболее производительными являются горизонтальные вращающиеся автоклавы.
В малопроизводительных старых цехах разварка силикатной глыбы производится в баках с нижней топкой, где подвешиваются специальные корзины из полосового листового железа для загрузки глыбы. Вода заливается в баки. Это малоэффективный длительный метод изготовления жидкого стекла, кроме того, глыба полностью не разваривается и модуль глыбы не сохраняется и жидком стекле.
При разварке глыбы во вращающихся горизонтальных автоклавах объемом 1,5 м3
загружают единовременно 500 кг силикатной глыбы, 400—450 л горячей воды по водомеру и 0,5 кг хромовокислого калия. В случае, если для шихты используется неостаренный или малоостаренный ферромарганец, необходимо расходовать на каждую варку жидкого стекла до 2,5 кг хромовокислого калия. Время разварки 1—1,5ч при использовании перегретого острого пара давлением 350-400кН/м2
(3,5-4 атмосферы).
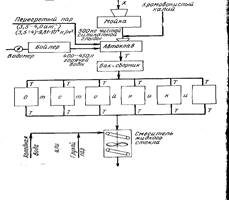
Технологическая схема варки жидкого стекла {X — химический анализ силикатной глыбы по партиям, Т — технологическая проба; плотность, температура, вязкость)
Готовность жидкого стекла определяют по ареометр, в горячем виде. Следует иметь в виду, что при охлаждении жидкого стекла плотность его увеличивается на 0,04 кг/см3
. Готовое жидкое стекло необходимо осветлить в отстойниках с выдержкой до 10 сут.
Вязкость жидкого стекла при необходимости снижают менее вязким жидким стеклом, но ни в коем случае не водой. Для усреднения вязкости или плотно" жидких стекол пользуются механизированным смесителем.
Для транспортировки жидкого стекла лучше использовать сжатый воздух, чем насосы, так как жидкое стекло имеет свойство засыхать, отчего насосы работают неудовлетворительно.
Вязкость жидкого стекла можно повысить путем добавления хлористых солей натрия или калия, кальцинированной или пищевой соды. Упаренное жидкое стекло имеет более высокую вязкость, чем свежеразваренное в автоклаве той же плотности. Разбавленное водой жидкое стекло резко теряет вязкость. Замерзшее жидкое стекло при отогреве также теряет вязкость. Хранить жидкое стекло можно при температуре не ниже +5°С.
Плотность жидкого стекла и вязкость, необходимые дли производства электродов определенной марки, различные и зависят от особенностей и пластичности покрытия. Эта характеристика жидкого стекла оговаривается в паспорте на электроды.
5.
Агрегаты для опрессовки электродов
(Питатель, пресс гидравлический, зачистная машина)
На рис. показан агрегат для опрессовки электродов, в табл. дана техническая характеристика агрегатов различных марок.
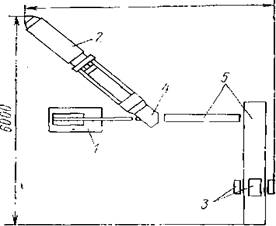
Рис. Схема агрегата типа ОСЗ-3 для опрессовки электродов: 1 — питатель стержней; 2—пресс гидравлической; 3 — зачистная машина; 4—головка пресса; В—транспортеры
В табл. 22 и 23 приведена техническая характеристика оборудования для изготовления электродов.
Агрегат непрерывного действия МАОЭ-1 предназначен для электродных стержней диаметром 4—-10 мм и длиной 450 мм. Агрегат работает с периодической за грузкой пресса массой по автоматическому и неавтоматическому циклу работ.
Время перезарядки опрессовочной части пресса 0,5 мин. Время опрессовки электродов ОММ-5 диаметром 5 мм и толщиной покрытия 1,25 мм из одного цилиндра составляет 3,5 мин плюс 0,5 мин перезарядки. Итого время цикла 4 мим или 15 циклов в час. Это составляет коэффициент полезной работы пресса 87,5%.
Пресс имеет четыре вертикальных обмазочных цилиндра. В то время как из одного цилиндра выпрессовывается масса, второй цилиндр промывается, в третий загружается обмазочная масса и уплотняется, у четвертого зачищается нижняя часть. Масса подается к прессу по транспортерной ленте от смесителя и попадает в приемный бункер над цилиндром. При помощи «стругана» масса заполняет приемный цилиндр в количестве, определяемом специальным весовым дозатором. Затем масса опускается в рабочий цилиндр и уплотняется поршнем.
Техническая характеристика питателей для электродных стержней
Характеристика |
ОСЗ-3 |
OC3-4 |
АОЭ-2 |
АОЭ-З |
Длина стержня, мм . . . |
250—450 |
250-450 |
350—450 |
450 |
Диаметр стержня, мм . . |
2—10 |
2—10 |
3—10 |
4—8 |
Окружная скорость тяну- |
щих роликов, м/мин. |
45—180 |
70-330 |
63—250 |
69,6—297 |
Пределы регулировки вида- |
чи стержней при диаметре |
5 мм и длине 450 мм, |
шт/мин |
100—400 |
155-600 |
125—380 |
155—660 |
Мощность электродвигате- |
2,8 |
6,5 |
3,8 |
6,5 |
Габаритные размеры, мм: |
-длина |
1400 |
1650 |
1570 |
1750 |
ширина |
820 |
860 |
620 |
860 |
высота |
1570 |
1656 |
1590 |
1650 |
Смена цилиндров производится одновременно и автоматически. Одновременно включаются (и выключаются) механизм, подающий стержни, транспортерные ленты пресса, зачистная машина и транспортерные ленты конвейерной печи:
Усилие, т:
прижима цилиндра 80
уплотнения массы 114
па шток пресса 180—200
Скорость подачи стержней, шт/мин До 650
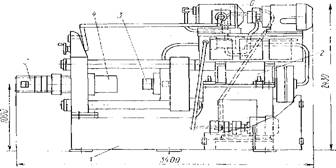
Часовая производительность агрегата по электродам ОММ-5 диаметром 5 мм и толщиной покрытий 1,25 мм составляет 3 т, за 8-ч смену — 24 т.
Это не представляет большого труда приспособить агрегат. Для опрессовки электродов диаметром 3 мм. Скорость подачи стержней увеличится до 840 шт/мин. Пресс позволяет наносить покрытие с хорошей концентричностью, что очень важно для тонких электродов. Коэффициент полезной работы пресса при изготовлении электродов диаметром 3 мм значительно повышается:
Техническая характеристика агрегата МАОЭ-1:
Производительность, шт/мин До 650
Диаметр стержней, мм 4—10
Длина стержней, мм 450
Усилие на штоке пресса, т 180—200
- Максимальное давление
в головке пресса, МН/м2
(ат) 5,78 (578)
Максимальное давление в масляном цилиндре,
МН/м2
(ат)2 (200)
Максимальное количество массы, подаваемое
прессом, л/мин12
Ход поршня, мм:
полный885
рабочий800
Диаметр поршня цилиндра, мм:
масляного360
обмазочного200
Емкость обмазочного цилиндра, л .... .25
Скорость хода поршня, мм/мин:
рабочего максимального490
холостого вперед2450
холостого назадч
3050
Общая мощность электродвигателей, кВт . .94—100
Габаритные размеры, мм:
длинаЮ800
ширина 5200
высота5600
Общая масса, т32—40
Технологический процесс нанесения покрытия на стержень.
Нанесение электродного покрытия на стержень вручную в настоящее время не применяют. На современных электродных производствах используют в основном агрегаты типа АОЗ-2 со средней производительностью 6 т электродов в смену, типа ОЗС-2 со средней производительностью 10 т электродов в смену и четырехцилиндровые агрегаты типа АОЭН-1 со средней производительностью 20 т электродов в смену.
На всех агрегатах, за исключением АОЭН-il, брикеты вручную загружают в цилиндр пресса. Смачивать водой брикеты не рекомендуется, так как это может вызвать трещинообразование на электродном покрытии при прокалке. Стержни, загружаемые в подающий станок, предварительно проверяются контролером ОТК и должны отвечать всем требованиям по внешней характеристике.
Прессовщик проверяет вхолостую работу гидравлической системы пресса, правильность установки технологического инструмента, а также соответствие инструмента выпускаемому диаметру электрода. Далее он проверяет подачу стержней без поступления покрытия, после чего производит пробную опрессовку электродов при отладке установки калибрующей втулки в головке пресса, чтобы обеспечить концентричность нанесения покрытия на стержень.
Допуск по эксцентричности покрытия по ГОСТМ66—60 следующий:
Диаметр, мм 4 5 6 и более
Допуск, мм 0,20 0,25 0,30
Однако опыт показывает, что электроды с указанными отклонениями по эксцентричности невозможно применять при сварке швов в переменных пространственных положениях, что зачастую требуется в машиностроении и при монтаже конструкций. При опрессовке электродов прессовщик также следит за толщиной покрытия, так как выпуск электродов диаметром, меньшим указанного в паспорте, повлечет за собой снижение перехода легирующих элементов в шов, уменьшение газовой и шлаковой защиты, а следовательно, снижение механических свойств и ухудшение химического состава металла шва, что приведет к перерасходу проволоки. Электроды с превышенной толщиной покрытия могут потрескаться в печи; кроме того такое превышение ведет к перерасходу материалов покрытия. Допускаемая толщина покрытия указывается в паспорте на электроды и определяется калибрующей втулкой и давлением обмазочной массы в головке пресса.
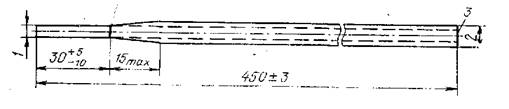
Рис. Сварочный электрод (ГОСТ 946660):
1 —
диаметр стержня; 2—диаметр электрода; 3 —торец без покрытия
Толщину покрытия характеризует коэффициент покрытия, пределы которого также ограничиваются в паспорте на электроды.
Важное значение имеет также правильность зачистки торцов электродов.
Диаметр электрода указывается в паспорте. Стержень электрода из проволоки марки Св-08 или Св-08А должен отвечать требованиям ГОСТ 2246—60.
По ГОСТ 9466—60 длина стержня без покрытия с одного конца электрода для держателя должна составлять 30 мм (допуск от +5до —10 мм) при плавномПереходе От стержня к покрытой части; Длина стержня без покрытия на другом конце электрода при диаметре' стержня до 6 мм не должна быть больше половины диаметра, а при диаметре стержня свыше 6 мм — не более/ 3 мм.
Список используемой литературы
1) Л.А. Колчанов «Сварочное производство».
2) И.И. Гарник, Г.М. Пиолунковский «Производство металлических электродов».
|