Министерство образования и науки РФ
Пензенский государственный университет
Проектирование шарообразного резервуара
Пояснительная записка
по курсу ”Организация и производство сварочных работ”
Принял
Кривенков А.О
Выполнил
ст.гр.05.Цф1
Шапилов М.В
Пенза 2007
Курсовой проект
“Проектирование шарообразного резервуара”
Техническое задание
Спроектировать и рассчитать толщину стенок сварного шарообразного резервуара, предназначенного для хранения жидкости с плотностью g=22,9 кН/м3
под давлением P=1,98 МПа; d=12 м. Резервуар изготавливается из стали 15ХСНД. При расчете коррозией пренебречь. Определить толщины стенок, если все швы сварены на флюсовой подушке односторонней многослойной автоматической сваркой под флюсом. Выполнить проверочный расчет сварных соединений. Показать конструкцию стыков с размерами. Дать условное обозначение сварных швов.

Аннотация
Данная курсовая работа содержит листов, рисунков, таблиц.
Целью данной работы является проектирование шарообразного резервуара, выполнение проектировочных и проверочных расчётов сварных соединений, расчёт необходимой толщины стенок резервуара, объёма и площади поверхности сферы, длины сварочных швов, расчёт прочности сварных швов.
На основе проведенных расчётов даётся оценка о работоспособности конструкции резервуара.
Содержание
Техническое задание
Аннотация
Введение
1 Общая характеристика сферического резервуара
2 Технология сборки и сварки сферического резервуара
3 Выбор и характеристики сварочного материала
4 Описание способа сварки
5 Характеристика стыковых многослойных швов
6 Расчет толщины стенки резервуара
7 Расчет объема и площади поверхности сферы
8 Расчет длины кольцевых и меридианных швов
9 Проверочный расчет кольцевых и меридианных швов
10 Конструкция стыка с размерами
11 Определение параметров режима сварки
12 Условное обозначение сварных швов
13.Дифекты образующиеся при сварке
Заключение
Список использованных источников
Введение
Как всем известно, из всех геометрических фигур соотношение площади поверхности к внутреннему объёму у сферы наименьшее. Следовательно, вес шарообразных резервуаров несколько ниже, чем у резервуаров другой формы, так что их применение с экономической точки зрения является эффективным, так как на их сборку расходуется меньшее количество металла, но с другой стороны их изготовление несколько сложнее. Вместо среднеуглеродистых сталей при изготовлении сварных конструкций в машиностроении целесообразно использовать легированные стали, что обеспечивает снижение массы конструкций и позволяет повысить надежность сварных деталей и изделий. Легированные конструкционные стали отличаются повышенной прочностью при комнатной температуре, отсутствием склонности к старению, их можно применять при повышенных (до 500 °С) температурах. Обычно сферические резервуары используют в химической промышленности для хранения жидкостей и газов (в том числе сжиженных).
Сварка – это процесс неразъёмного соединения посредством установления межатомных связей между соединяемыми частями при их нагревании и (или) пластическом деформировании.
Существует огромное количество видов сварки, приведем некоторые классификации. По физическим признакам сварка делится на следующие виды по классам:
Таблица 1 - Классификация сварки по физическим признакам
Класс сварки
|
Вид сварки
|
Термический
|
Дуговая, электрошлаковая, электронно-лучевая, плазменно-лучевая, ионно-лучевая, тлеющим разрядом, световая, индукционная, газовая, термитная, литейная.
|
Термомеханический
|
Контактная, диффузионная, индукционнопрессовая, газопрессовая, термокомпрессионная, дугопрессовая, шлакопрессовая, термитнопрессовая, печная.
|
Механический
|
Холодная, взрывом, ультразвуковая, трением, магнитоимпульсная.
|
По техническим признакам сварка делится на следующие виды:
Таблица 2 - Классификация сварки по техническим признакам
Виды сварки
|
По способу защиты металла в зоне сварки
|
По непрерывности процесса
|
По степени механизации процессов сварки
|
В воздухе
|
В вакууме
|
В защитном газе
|
Под флюсом
|
По флюсу
|
В пене
|
С комбинированой защитой
|
Прерывные
|
непрерывные
|
Ручные
|
Механизированые
|
Автоматизированные
|
Автоматические
|
В данной работе учтем, что сварные швы выполнены на флюсовой подушке односторонней многослойной автоматической сваркой под флюсом.
1 Общая характеристика сферического резервуара
В целях экономного использования металла в различных отраслях химической промышленности строят резервуары в виде сфер различных диаметров. Сферические резервуары применяют для хранения сжиженных газов или газов под давлением 2—6 атм (рисунок 1). У нас часто применяются сферические резервуары объемом 600 и 2000 м3
, однако экономически целесообразнее использовать более крупные. За рубежом такие конструкции достигают 30000 м3
и более.

Рисунок 1 – Пример конструкции сферического резервуара
В сферических резервуарах лепестки соединяются встык, их толщина обычно составляет 10-30 мм и, как правило, не превышает 40 мм. Это ограничение толщины диктуется отсутствием термообработки конструкции после сварки.
Напряжения в стенке сферического резервуара определяют по формуле:

где - радиус сферы;
- толщина стенок.
Напряжение в сферическом резервуаре в 2 раза меньше, нежели в цилиндрическом, при одинаковых радиусах и толщинах стенок. Поэтому вес сферических резервуаров меньше цилиндрических, но изготовление сложнее. За рубежом сферическими выполняют конструкции атомных реакторов.
2 Технология сборки и сварки сферического резервуара
В нашей стране сооружают сферические резервуары вместимостью 600 и 2000 м3
на внутреннее давление до 18 кгс/см2
. Тип раскроя оболочек приведен в таблице 4. Сферическую поверхность листовым заготовкам при толщине до 36 мм придают горячей штамповкой (типы раскроя а и в), при толщине до 28 мм — вальцовкой на специальных гибочных вальцах со сферическими валками (раскрой б). В последнем случае плоскую заготовку предварительно сваривают из листов, вырезают газовой резкой по копиру и затем вальцуют.
При раскрое типа а укрупнение блоков и их сварку под флюсом выполняют на шарнирно-качающихся стендах. Блоки собирают в полусферу на стенде (рисунок 2), подварку швов под последующую автоматическую сварку осуществляют вручную. После завершения сборки нижнюю полусферу кантуют и устанавливают на временную опору. На этом же стенде собирают верхнюю полусферу, затем поднимают ее и монтируют на нижнюю. Сборка заканчивается ручной подваркой замыкающего шва.
При раскрое типа б лепестки также предварительно укрупняют в блоки, причем для сферы вместимостью 2000 м3
каждый меридиональный лепесток собирают из двух заводских элементов (большого и малого). Для этого типа раскроя получил применение «вертикальный» способ сборки сферы. На временной опоре 1 (рисунок 3) устанавливают нижнее днище 2, к нему крепят трубчатую монтажную стойку 3 с верхним днищем 4 и монтажной люлькой 5.

Рисунок 2 - Схема сборки полусферы на стенде
Таблица 3 - Типы раскроя оболочек
Вместимость, м3
|
Диаметр сферы, м
|

а) б) в)
Число элементов
|
600
|
10,5
|
28
|
20
|
-
|
2000
|
16
|
-
|
54
|
-
|
Блоки 6 с распорками жесткости 7 поднимают в вертикальное положение и крепят с помощью сборочных планок и клиньев к днищам и друг к другу, а также временными прихватками к опорам 8, устанавливаемым на фундаменте. Затем блоки соединяют пр ихваточным швом, а перед установкой последнего блока удаляют трубы жесткости, монтажную стойку и люльку.
Сварку сферических резервуаров вместимостью 600—2000 м3
выполняют автоматом под флюсом с двух или одной стороны при вращении сферы на специальном манипуляторе, домкратное устройство которого приподнимает сферу над опорами после удаления временных прихваток. При толщине элементов 16 мм разделку кромок не осуществляют. При толщине 25 мм используют V-образную разделку, при толщине 34 мм — Х-образную. Последовательность выполнения швов следующая. Сначала выполняют меридиональные швы со стороны разделки кромок в несколько слоев. С другой (внутренней) стороны подварку корня шва производят без вырубки его за счет глубокого проплавления. Затем сваривают широтные и полюсные соединения.

Рисунок 3 - Схема сборки сферического резервуара
При выполнении сборочных и сварочных работ над резервуаром целесообразно устраивать общее светопрозрачное пленочное покрытие. В этом случае условия работы лучше, чем под открытым небом, и облегчается сварка в среде защитного газа. За рубежом при сооружении резервуаров больших размеров монтаж осуществляют методом укрупнительной сборки лепестков заводского изготовления в блоки на монтажной площадке и их автоматической сварки под слоем флюса или в среде защитного газа, В проектное положение блоки монтируют последовательным наращиванием, швы между блоками выполняют в основном ручной сваркой покрытыми электродами или автоматами для сварки во всех пространственных положениях проволокой диаметром 1—1,2 мм в смеси аргон — углекислый газ со свободным формированием шва. Очередность установки блоков при монтаже сферы определяется расположением опор. При раскрое типа в монтаж можно начинать с экваториального пояса. К укрупненным блокам лепестков этого пояса приваривают опорные стойки и, устанавливая их на фундамент, монтируют весь экваториальный пояс. Затем на временный постамент укладывают нижнее днище и монтируют блоки нижнего пояса. После установки временной стойки монтируют верхнее днище и верхний пояс.

Рисунок 4 - Положение сферического резервуара при сварке полюсного шва
Положение резервуара на кантователе при сварке полюсного шва показано на рисунке 4. Одна из приводных станций манипулятора выключается, другая работает со скоростью 34 м/ч. При этом скорость сварки полюсного шва составляет около 17 м/ч.
3 Выбор и характеристики сварочного материала
Марка стали 15ХСНД
Назначение:
- Для изготовления специальных фасонных профилей судостроения (полосо-бульбовая несимметричная и симметричная зетовая сталь и др.).
- Для сварных конструкций и аппаратов химической промышленности
- Для изготовления шпуптовых свай корытного профиля 1ЛК-1, ШК-2, зетового ШД-3 и ШД-5 и плоскою П1П-1 и ШП-2
Таблица - Химический состав стали, % (ГОСТ 4543-71)
Марка стали
|
С
|
Si
|
 Мn
|
  Сг
|
 Ni
|
Сu+
|
10ХСНД 15ХСНД 15ГФ
|
<0,12
0.12—0,18 0,12-0.18
|
0.80-1,10 0.40—0.70 0,17-0.37
|
0,50-0.80 0.40—0.70 0.90—1,20
|
0,60-090
0,6-0,9
0,3
|
050-0,8
0,3-0,6
0,3
|
0,4-,-0,65
0,2-0,4
0,3
|

|
Сэ
=C+Mn
/6+Cr
/5+V/5+Mo
/4+Ni
/15+Cu/13+P/2
Сэ
=0,15+0,15/6+1/5+0/5+0/5+0,6/15+1/13+0,035/2=0,15+0,025+0,2+0,04+0,08+0,02=0,51
Сэ
>0,45Þсталь плохо сваривается, необходим предварительный подогрев и последующая термическая обработка
Таблица - Механические свойства стали
Марка стали
|
Толщина проката,мм
|
   Gв Gт
d
%
Кгс/мм2
-40 -70
Не менее
|
15ХСНД
|
4-32
|
   50 35 21 3 3
|
Примечание. Угол загиба для всех марок стали в холодном состоянии 180°.
Таблица Прокат стали 15ХСНД
Марка
|
Толщина
|
Механические свойства при растяжении для проката всех категорий поставки
|
Ударная вязкость KCU (а1
), Дж/см2
(кгс·м/см2
), для проката категорий, при температуре, °С
|
Испытание на изгиб в холодном состоянии до параллельности
|
стали
|
проката, мм
|
Временное
|
Предел
|
Относительное
|
1
|
2
|
3
|
1 и 2
|
3
|
сторон для проката
|
сопротивление в
,
|
текучести т
,
|
удлинение 5
, %
|
+20
|
–20
|
категорий
|
Н/мм2
(кгс/мм2
)
|
Н/мм2
(кгс/мм2
)
|
–40
|
–60
|
–70
|
после механического старения
|
1
|
2, 3
|
не менее
|
15ХСНД
|
8-32
|
490-685
(50-70)
|
345 (35)
|
21
|
29
(3,0)
|
29
(3,0)
|
29
(3,0)
|
29
(3,0)
|
29
(3,0)
|
d
|
d
|
|
33-50
|
470-670
(48-68)
|
335 (34)
|
19
|
-
|
29
(3,0)
|
29
(3,0)
|
29
(3,0)
|
29
(3,0)
|
d
|
d
|
Таблица
 Марка стали
|
Размеры, мм
|
Область применения
|
толщина, S
|
ширина, L
|
длина, B
|
15ХСНД
|
4-35
|
150-600
|
3000-12000
|
для сварных металлоконструкций
|
|
Выбор сварочных материалов
Сварочная проволока СВ08ГС
Таблица Механические свойства проволоки
Диаметр, мм
|
Временное сопротивление разрыву, Н/кв.мм
|
Относительное удлинение,%,термически необработанная
|
Термически необработанная
|
Термически обработанная
|
Не менее:
|
Группа I
|
Группа II
|
Без покрытия
|
С покрытием
|
Без покрытия
|
С покрытием
|
0.8 - 1.0
|
690-1270
|
690-1180
|
-
|
-
|
15
|
12
|
1.0 - 1.2
|
590-1270
|
690-1180
|
-
|
-
|
15
|
12
|
1.2 - 2.5
|
590-1180
|
690-980
|
-
|
-
|
15
|
12
|
2.5 - 3.2
|
540-1080
|
640-930
|
-
|
-
|
20
|
18
|
3.2 - 3.6
|
440-930
|
640-930
|
-
|
-
|
20
|
18
|
3.6 - 4.5
|
440-930
|
590-880
|
290-490
|
340-540
|
20
|
18
|
4.5 - 6.0
|
390-830
|
490-780
|
-
|
-
|
20
|
18
|
Таблица[ ] Химический состав , % , сварочной проволоки
Марка проволоки
|
Химический состав, %, не более:
|
Al
|
Mn
|
C
|
Si
|
Cr
|
Ni
|
S
|
P
|
СВ08Г2С
|
0,01
|
1.80-2.10
|
0.05-0.11
|
0.70-0.95
|
0.20
|
0.25
|
0.025
|
0.03
|
4. Описание способа сварки
Сварка под флюсом в большинстве случаев используется как автоматический процесс. Полуавтоматическая сварка под флюсом применяется в значительно меньшем объеме, чем автоматическая. Процесс ведется преимущественно в нижнем положении. Объем работ, выполняемых при помощи сварки под флюсом, из года в год увеличивается. Интенсивное развитие автоматической сварки под флюсом обусловлено высокой производительностью этого способа, стабильным качеством сварки, малым расходом электродного металла и электроэнергии и хорошими условиями труда.
При сварке под флюсом производительность процесса по машинному времени повышается в 6—12 раз, что даже при коэффициенте использования сварочной установки 0,5 в 3—6 раз превосходит производительность ручной сварки покрытыми электродами. При сварке на специальных, так называемых форсированных режимах, применяемых при изготовлении труб большого диаметра и широкополых двутавровых балок, производительность повышается в 15—20 раз. За счет повышения коэффициента использования сварочной установки можно добиться значительного дальнейшего роста производительности сварки под флюсом. Повышение производительности при автоматической сварке под флюсом достигается за счет использования больших токов и повышения плотности тока в электроде.
Резкое повышение абсолютной величины тока и плотности тока в электроде без увеличения потерь на угар и разбрызгивание и без ухудшения формировании шва возможно благодаря наличию плотного слоя флюса вокруг зоны сварки; это предотвращает выдувание жидкого металла шва из сварочной ванны и сводит потери на угар и разбрызгивание до 1—3%.
Таблица 11 - Сила и плотность тока в электроде при сварке покрытыми электродами и под флюсом
Диаметр электродного стержня или проволоки, мм
|
Сварка покрытыми электродами вручную
|
Автоматическая сварка под флюсом
|
Сила тока, А
|
Плотность тока, А/мм2
|
Сила тока, А
|
Плотность тока, А/мм2
|
5
4
3
2
|
190-350
125-200
80-130
50-65
|
10-18
10-16
11-18
16-20
|
700-1000
500-800
350-600
200-400
|
35-50
40-63
50-85
63-125
|
Увеличение силы тока позволяет сваривать металл значительной толщины без разделки кромок с одной или двух сторон (производительность сварки для этого случая определяется в основном глубиной проплавления основного металла) и увеличивать количество наплавляем
ого в единицу времени металла. Коэффициент наплавки при сварке под флюсом составляет 14—18 г/А·ч против 8—12 г/А·ч при сварке покрытыми электродами. Повышение силы тока, увеличение глубины провара и коэффициента наплавки позволяют повысить производительность и при сварке многослойных швов. Отсутствие брызг — также серьезное преимущество сварки под флюсом, так как отпадает надобность в трудоемкой операции очистки от них поверхности свариваемых деталей.
При сварке под флюсом обеспечивается высокое и стабильное качество сварки. Это достигается за счет надежной защиты металла шва от воздействия кислорода и азота воздуха, однородности металла шва по химическому составу, улучшения формы шва и сохранения постоянства его размеров. В результате обеспечивается меньшая вероятность образования непроваров, подрезов и других дефектов формирования шва и отсутствие перерывов в процессе сварки, вызванных необходимостью смены электродов. За счет уменьшения доли электродного металла в металле шва в среднем с 70% при сварке покрытыми электродами до 35% при сварке под флюсом и уменьшения потерь на угар, разбрызгивание и огарки снижается расход электродного металла и электроэнергии. Отпадает необходимость в защите глаз и лица рабочего и несколько уменьшается количество выделяемых в процессе сварки вредных газов, что улучшает условия труда. Для приобретения квалификации автосварщика необходимо затратить значительно меньше времени и средств, чем для овладения специальностью сварщика, работающего вручную.
Автоматическую и полуавтоматическую сварку под флюсом применяют в заводских и монтажных условиях для выполнения швов, расположенных в нижнем положении, обычно при толщине металла 2—100 мм. Сваривают стали различного состава, медь, титан, алюминий и сплавы на их основе. Сварку алюминия ведут не под флюсом, а по флюсу. Под флюсом сваривают и горизонтальные швы, расположенные на вертикальной плоскости. В отечественной промышленности этот способ из-за трудности удаления шлаковой корки и удержания флюса не находит практического применения. Сварку под флюсом широко используют и при наплавочных работах. Автоматическую сварку под флюсом ведут сварочной проволокой сплошного сечения диаметром 1—6 мм при силе тока 150—2000А и напряжении дуги 22—55 В, полуавтоматическую — сварочной проволокой диаметром 0,8—2 мм при силе тока 100—500 А и напряжении дуги 22—38 В. В обоих случаях возможно применение активированной и порошковой проволок.
Основным методом автоматической и полуавтоматической сварки под флюсом является сварка одной дугой. С целью повышения производительности труда при сварке многослойных швов одной дугой в разделку вводят металлические наполнители в виде порошка, проволоки, окатышей и других материалов. В некоторых случаях наполнители вводят не только для увеличения производительности, но и для улучшения качества шва. Для повышения коэффициента расплавления электрода можно применять автоматическую и полуавтоматическую сварку под флюсом с увеличенным вылетом электрода. При этом достигается предварительный нагрев электродной проволоки па участке вылета.
Повысить производительность процесса и качество сварного соединения можно путем автоматической сварки под флюсом двумя и более электродами. Различают многоэлектродную и многодуговую сварку. При многоэлектродной сварке все электроды присоединены к одному полюсу источника питания. При многодуговой сварке каждый из электродов подсоединен к отдельному источнику питания и они электрически изолированы друг от друга.
Существуют две разновидности многодуговой сварки: сварка в общую ванну, когда расплавляемый всеми дугами металл образует единую ванну, кристаллизующуюся как одно целое (рисунок 5, а); сварка в раздельные ванны, или, как ее называют, сварка раздвинутыми дугами, в этом случае каждая дуга образует свою ванну и последующая дуга расплавляет уже закристаллизовавшийся слой, сваренный предыдущей дугой (рисунок 5, б). Многоэлектродная сварка ведется только в общую ванну.
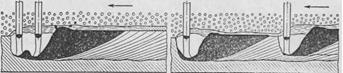
а) б)
Рисунок 5 - Сварка двумя дугами (стрелкой показано направление сварки):
а) - в общую ванну;
б) – в раздельные ванны.
5. Характеристика стыковых многослойных швов
Если проплавляющая способность источника теплоты не обеспечивает возможности провара основного металла с одной или двух сторон на всю толщину, то производят специальную подготовку свариваемых кромок. В этом случае между соединяемыми элементами оставляют пространство, позволяющее приблизить источник теплоты к самой отдаленной от поверхности точке основного металла. Достигается это за счет скоса кромок с оставлением небольшого нескошенного участка - притупления, которое проплавляется в процессе сварки (рисунок 6, а—г).

Рисунок 6 - Форма разделки кромок, применяемая при дуговой сварке многослойных швов:
а) – V-образная;
б) – рюмкообразная;
в) – Х-образная;
г) – двойная рюмкообразная.
К многослойной сварке со скосом кромок даже для толщин, которые могут быть сварены в один слой, прибегают и в тех случаях, когда отсутствуют источники питания достаточной мощности, необходимо уменьшить долю основного металла в металле шва (например, при сварке среднеуглеродистых, среднелегированных и других марок стали), создать благоприятный термический цикл или снизить вероятность образования дефектов и пр. Очевидно, что такое решение вопроса менее целесообразно, чем сварка без разделки кромок, так как в этом случае искусственно удаляется часть основного металла, а образовавшаяся полость заполняется другим, более дорогим, электродным или присадочным металлом. При этом металл шва на 60—80% состоит из электродного и только на 20—40% из основного металла. Производительность сварки существенно снижается.

Рисунок 7 - Размещение шва при различной подготовке кромок:
а) – без скоса кромок;
б) – с малым углом скоса кромок;
в) – с оптимальным углом скоса кромок.
Условия, благодаря которым осуществляется провар корня шва при многослойной сварке, ясны из схем, приведенных на рисунке 7. При сварке без разделки кромок при данной мощности источника нагрева шов будет формироваться так, как показано на рисунке 7,а. Если раздвинуть кромки на расстояние, превосходящее ширину шва, то при той же мощности источника нагрева шов погрузится в разделку до такого положения, при котором ширина его совпадет с шириной разделки (рисунок 7,б).
При увеличении угла раскрытия кромок произойдет дальнейшее понижение уровня сварочной ванны и при той же мощности источника нагрева и форме шва будет достигнут провар соединяемых деталей в корне шва (рисунок 7,в). При малом угле разделки кромок трудно обеспечить провар и при многослойном шве.
Кромки под сварку разделывают путем удаления части металла по плоскости, расположенной под некоторым углом к вертикальной оси (V-образная разделка кромок, рисунок 6,а), или же по специально подобранной криволинейной поверхности (рюмкообразная разделка кромок, рисунок 6,б). Характер подготовки кромок под сварку при V-образной разделке определяется углом раскрытия кромок или углом скоса кромок , величиной притупления и расстоянием (зазором) между свариваемыми деталями а (рисунок 6, а).
Угол раскрытия кромок выбирают с таким расчетом, чтобы были обеспечены провар вершины угла притупления и оптимальный коэффициент формы провара. При малом угле раскрытия возможны непровар вершины угла (рисунок 7,б) и возникновение кристаллизационных трещин. Последнее связано с тем, что для достижения провара при этих условиях слой должен иметь малый коэффициент формы. Угол раскрытия кромок практически не зависит от толщины свариваемого металла и мало зависит от способа сварки. При любой толщине необходимо создать условия для качественного выполнения первого слоя.
Форма подготовки кромок при рюмкообразной разделке определяется величиной притупления и величиной зазора а, назначаемыми из тех же соображений, что и для V-образной разделки, радиусом , изменяемым в пределах 5—8 мм, и углом скоса кромок , равным 10—14°. По условиям формирования металла первого слоя и по сечению разделки предпочтительна рюмкообразная подготовка кромок. Однако в этом случае увеличивается сложность подготовки под сварку и требуется более точное направление электрода по оси соединения для обеспечения провара кромок.
Параметры различных видов разделки и выбор способов подготовки кромок для различных методов дуговой сварки регламентированы ГОСТ 8713-70, 14771-69 и 5264-69.
6. Расчёт толщины стенки резервуара
При изготовлении сферического резервуара применяют сталь 15ХСНД:
Её предел прочности sв
=520мПа, предел тякучести sт
=350 мПа.
Допустимое напряжение можно определить:
[s]р
= sт
/n , где n-коэффициент запаса=1,5
[s]р
=350/1,5=233,3 мПа
Толщина стенки сферического резервуара определяется по формуле:
S0
= PR0
/2s ,
где
P- давление жидкости в резервуаре=1,98 мПа
R0
- радиус сферы=6м
s- напряжение в стенке резервуара, мПа
Из условия s£[s]р
примем что s= [s]р
=233,3 мПа
Подставив исходные данные P,R0
,s в формулу получим:
S0
=1,98´6´103
/233,3=23,5 (мм)
Примем толщину стенки S0
=24мм
7. Расчёт объёма и площади поверхности сферы
Объём сферы определяется по формуле: V=4R0
3
/3=4´4.13´63
/3= 904.8 (м3
) , примем V=905(м3
)
Площадь поверхности сферы определяется по формуле:
S= pD2
,
где D-диаметр сферы=12 м
S= pD2
=3.14´(12´103
)2
=452.2´103
(мм)
Для расчёта объёма резервуара наиболее предпочтительной является конструкция показанная в таблице на рисунке . При диаметре сферы d=12м и объёме резервуара V=905м3
число элементов(лепеcтков)nл
составляет 24штуки.
8. Расчёт длины кольцевых и меридианных швов
Примем высоту шарового сегмента h0
=1м, тогда h=d-2h0
, где
h0
=высота шарового сегмента
  dсег
=2a
Радиус шарового сегмента находится по формуле
a=Öh0
´(2R0
-h) =1(12-1)=3.32м
Длина кольцевого шва равна: Lk
=p dсег
, где
dсег
=диаметр сегмента=2a
Lk
=3.14´6.64=20.8 (м)
Длина меридионального шва определяется по формуле
Lм
=l=2pR0
a/360 , где
a=центральный угол=1250
, который был найден графическим путём, из построения графического резервуара в масштабе 1:100
Lм
=l=2´3.14´6´125/360=13,09(м)
Ширина одного лепестка в зоне соединения со сферическим днищем составляет:
9. Проверочный расчёт кольцевого и меридианного швов
Давление распределяется равномерно по внутренней поверхности сферического резервуара. На сварные швы действует усилие N, которое стремится разорвать изделие: N=P×S , где S площадь днища (Sд) и сферической части без днищ (Sсф). Площадь днища определяется по формуле :
Площадь двух лепестков (Sсф2) сферической части резервуара без днищ определяется по формуле :

Напряжение, возникающее в кольцевом шве равно:
Напряжение, возникающее в меридиональном шве, между двумя лепестками сферической части резервуара рано:
Так как напряжения в кольцевом и меридиональном меньше допустимого sр


10. Конструкция стыка с размерами
Условное обозначение сварного соединения – С18.

Рисунок - Конструктивные элементы подготовленных кромок свариваемых деталей:
1), 2) – соединяемые детали;
3) – флюсовая подушка.

Рисунок - Конструктивные элементы сварного шва (швы №1 и №2, рисунок
1), 2) – соединяемые детали;
3) – сварной шов – трехслойный (выполнен за три прохода).
11. Определение параметров режима сварки
Таблица - Определение параметров режима сварки
№ слоя
|
Поляр. тока
|
dпп
|
Iсв
(А)
|
U (В)
|
Vпп
м/ч
|
V сварки(м/ч)
|
1
|
обратная
|
2
|
150-200
|
30-34
|
90-120
|
15-25
|
2
|
обратная
|
2
|
200-400
|
32-34
|
90-120
|
25-35
|
3
|
прямая
|
5
|
350-600
|
36-40
|
90-120
|
25-40
|
4
|
прямая
|
5
|
500-800
|
38-40
|
90-120
|
30-40
|
5
|
прямая
|
5
|
700-1000
|
40-44
|
90-120
|
30-40
|
12. Условное обозначение сварных швов
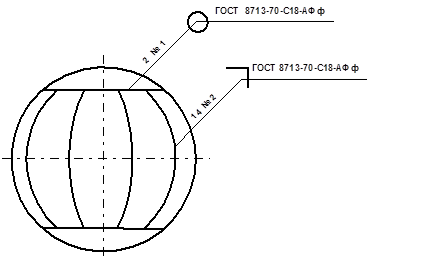
Рисунок - Обозначение сварных соединений
13. Дефеткы образующиеся при сварке
Остаточные сварочные напряжения и деформация.
Дефекты в соединениях бывают двух типов: внешние и внутренние. В сварных соединениях к внешним дефектам относят наплывы подрезы, наружные непровары и несплавления, поверхностные трещины и поры. К внутренним – скрытые трещины и поры, внутренние непровары и несплавления, шлаковые включения и др. В паяных соединениях внешними дефектами являются наплывы и натеки припоя, неполное заполнение шва припоем; внутренними – поры, вкючения флюса, трещины и др.
Качество сварных и паяных соединений обеспечивают предварительным контролем материалов и заготовок, текущим контролем за процессом сварки и пайки и приемочным контролем готовых сварных или паяных соединений. В зависимости от нарушения целостности сварного соединения при контроле различают разрушающие и неразрушающие методы контроля.
Заключение
В данной курсовой работе мной был спроектирован шарообразный резервуар предназначенный для хранения жидкости. Произведен выбор типа раскроя оболочки, типа и размеров проката, сварочной проволоки, флюса, формы разделки кромок и были определены параметры режима сварки. Из расчетов углеродного эквивалента следует, что сталь нужно сваривать только с предварительной термообработкой, подогревом в процессе сварки и последующей термообработкой. Показаны конструкции стыков с размерами и условные обозначения сварных швов. Были проведены расчеты по допустимым напряжениям и по предельным состояниям. Были рассчитаны толщина стенки шарообразного резервуара, объём сферы и площадь поверхности, длины меридианного и кольцевого швов. По проверочным расчетам кольцевого и меридианного швов был сделан вывод о работоспособности конструкции
Список использованных источников
1 Николаев Г.А., Курнин С.А., Винокуров В.А. Расчёт проектирование и изготовление сварных конструкций: учебное пособие для вузов. - М.: Высш.шк., 1971.
2 Сварка в машиностроении: Справочник в 4-х т. / Под ред. В.А. Винокурова - М.: Машиностроение, 1979-т.3.
3 Технология электрической сваркой металлов и сплавов плавленим / Под ред. Акад. Б.Е. Патона - М.: Машиностроение, 1974.
4 Николаев Г.А., Курнин С.А., Винокуров В.А. Автоматизация проектирования сварных конструкций: Учеб. пособие - М.: Высш. шк., 1983.
5 Сварка в машиностроении: Справочник / Под ред. Н. А. Ольшанского.-М.: Машиностроение, 1978-т.1.
6 Марочник сталей и сплавов / В.Г. Сорокин, А.В. Волосникова, С.А. Вяткин. Под общей ред. В.Г. Сорокина. – М.: Машиностроение, 1989.
6 ГОСТ 8713-79. Сварка под флюсом. Соединения сварные. Основные типы, конструктивные элементы и размеры.
7 ГОСТ 9087-81. Флюсы сварочные плавленые. Техническая документация.
8 ГОСТ 19903-74. Прокат листовой горячекатаный. Сортамент.
9 ГОСТ 19521-74. Сварка металлов. Классификация.
|