СОДЕРЖАНИЕ
Задание на проектирование. Кинематическая схема редуктора
1. Кинематический расчет электромеханического привода
1.1 Выбор электрического двигателя
1.2 Определение кинематических параметров вала
1.3 Определение кинематических параметров всех валов
2. Выбор материала для зубчатых колес и определение допускаемых напряжений
2.1 Выбор материалов
2.2 Определение допускаемых напряжений
3. Проектный расчет конической прямозубой передачи
3.1 Определение модуля
3.2 Геометрические параметры передачи
4. Эскизное проектирование редуктора
4.1 Предварительный расчет валов
5. Проверочный расчет ведомого вала
5.1 Определение реакций в опорах (вертикальная плоскость)
5.2 Суммарный изгибающий момент
5.3 Построение эпюры эквивалентного момента
5.4 Определение суммарных сил реакций в опорах А и В
5.5 Проверочный расчет вала по статическим нагрузкам
5.6 Проверочный расчет вала на усталостную прочность
6. Проверочный расчет подшипников
7. Выбор и расчет шпонок
8. Выбор сорта масла и способа смазки
Заключение
ЗАДАНИЕ НА ПРОЕКТ
СПРОЕКТИРОВАТЬ КОНИЧЕСКИЙ РЕДУКТОР СОГЛАСНО СХЕМЕ И ВАРИАНТУ
Дано:

1. КИНЕМАТИЧЕСКИЙ РАСЧЕТ ЭЛЕКТРОМЕХАНИЧЕСКОГО ПРИВОДА
1.1 Выбор электродвигателя
Расчёт необходимой мощности электродвигателя

где
h
=0,98 к.п.д. муфты
hr
=0,99 .п.д. одной пары подшипников передача
hI
=h
=0,950,97 ... hI
=0,96
hII
=h
=0,950,96 к.п.д. второй ступени hII
=0,96
Значения берём из таблицы 2.1[ ]
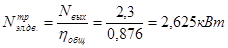
1.1.2 Определение требуемого числа оборотов двигателя

Где Uобщ
=U12
.U23
Из условия и выбираем марку электродвигателя согласно таблице 17.8[2]
Получили:
Nдв
=3кВт, nдв
=1435об/мин
Марка двигателя 100S4/1435
1.2 Определение общего передаточного отношения и расчёт его по ступеням
Определение реального общего передаточного числа
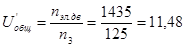
Разбивка общего передаточного отношения по ступеням
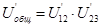
По таблице 2.2.[2 ] задаёмся
, тогда 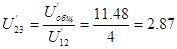
1.3 Определение кинематических параметров всех валов
Определение частоты вращения всех валов
вал I : n1
=nэл.дв
=1435об/мин
вал II : 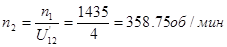
вал III : 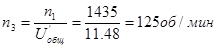
Определение угловой скорости всех валов
вал I :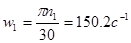
вал II : 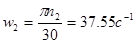
вал III : 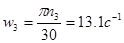
Расчёт мощностей на каждом валу:
вал III : 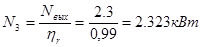
вал II : 
вал I :
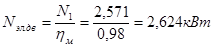
Определение вращающих моментов на каждом валу
вал III : 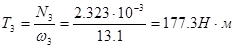
вал II : 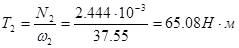
вал I :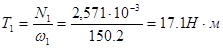

2. ВЫБОР МАТЕРЬЯЛА ДЛЯ ЗУБЧАТЫХ КОЛЁС И ОПРЕДЕЛЕЕИЕ ДОПУСКАЕМЫХ НАПРЯЖЕНИЙ
2.1 Выбор материала для зубчатых колес
Обычно зубчатые колеса изготавливаются из углеродистых и легированных сталей. По твердости все зубчатые колеса делятся на две большие группы:
- Зубчатые колеса с твердостью *
- Зубчатые колеса с твердостью >
Из условия равномерного износа колес материал шестерни должен быть качественнее чем материал зубчатого колеса, то есть HB1
=HB2
+30 .
Исходные данные

Обычно берут такую зависимость:
HB1
=HB2
+(25÷35)
HB1
-твёрдость шестерни
HB2
-твёрдость зубчатого колеса
HB2
=N2
ּ100=2.5 ּ100=255
HB1
= HB2
+25=255+30=280
В данном проекте был выбран материал для зубчатых колес из таб.2.1[2] и 5.1[2] марка стали 45 .Сталь подверглась двум термическим обработкам: в результате нормализации HB2
=255 - для колеса;
В результате улучшения HB1
=280 - для шестерни.
2.2 Определение допускаемых напряжений
Определение допускаемых контактных напряжений
,
где допускаемое напряжение при нулевом цикле:
=2 .
280+70=630
=2 .
255+70=580
коэффициент нагрузки при 
hH
=1,2 - коэффициент безопасности
=630ּ1/1,2=525
=580ּ1/1,2=483 ,
Определение допускаемых напряжений на усталостную прочность
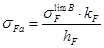
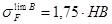
-допускаемое напряжение на усталостную рочность при нулевом цикле
kF
=1 коэффициент нагрузки
- коэффициент безопасности
sF1
limB1
=1,75 .
HB1
=1,75 .
280=490 Н/мм2
=1,75 .
255=446
sFa1
=sF
limB1
.
kh
/ hH
=490 ּ1/ 1,75=280 Н/мм2
sF2
=sF
limB2
.
kh
/hH
=446ּ1/ 1,75=255 Н/мм2
3. ПРОЕКТНЫЙ РАСЧЕТ КОНИЧЕСКОЙ ПРЯМОЗУБОЙ ПЕРЕДАЧИ
Проектный расчет конического редуктора состоит в определении одного из геометрических размеров редуктора (de
2
, mt
) из условия прочности зубьев, из контактных напряжений на усталость.
Проектный расчёт определяется из условия прочности по контактным напряжениям.
3.1 Определяем диаметр внешнего делительного конуса de
2
По формуле 2.33[1] имеем:

где - коэффициент концентрации нагрузки стр.20[1]
U =4 – передаточное отношение для конической передачи
Т2
= 65.08 Н/м – крутящий момент на тихоходном валу редуктора
- допускаемое контактное напряжение
vH
=0,85 - стр.20[1]
3.2 Геометрические параметры передачи
Уголы делительных конусов, конусное расстояние ширина колёс 2.34[1]
, где
U=2,5
– передаточное отношение для конической передачи



Конусное расстояние 2.35[2]
, где
- диаметр внешней делительной окружности колеса
- угол делительных конусов
Ширина венца 2.36[1]:
, где
Re
– конусное расстояние
Вычисление модуля передачи 2.37[1]
, где
kF
=1,0 – коэффициент для прямозубых колёс стр.52 [1]
Т2
= 65.08 Н/м – крутящий момент на тихоходном валу редуктора
vF
=0,85 - коэффициент для прямозубых колёс стр.52 [1]
- диаметр внешней делительной окружности колеса
b=28мм – ширина колёс
- допускаемое напряжение

примем модуль равный me
=1
Число зубьев колёс
, где
- диаметр внешней делительной окружности колеса
me
(mte
)=1 - модуль передачи
зубьев
Число зубьев шестерни 2.39[1]:
, где
z1
=180 – число зубьев колеса
=4 – передаточное отношение для конической передачи
зубьев
Фактическое передаточное число
,где
z2
=180– число зубьев колеса
z1
=45– число зубьев шестерни

отклонение от заданного передаточного числа:

=76˚ 
Делительные диаметры колес 2.41[1]:


Коэффициенты смещения 2.42[1]:


Внешний диаметр колес 2.43[1]:


Определим длину образующей внешнего делительного конуса :
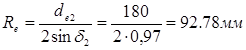
Определим среднюю длину образующей внешнего делительного конуса :

Высота ножки зуба: hc
=2,4∙me
=2,4∙1=2,4 мм
Высота головки зуба: hae
=1∙me
=1∙1=1 мм
Силы в зацеплении
Окружная сила:
N
где dm
2
=0,857∙de
2
=0,857∙ 180=154.2 мм

4. ЭСКИЗНОЕ ПРОЕКТИРОВАНИЕ РЕДУКТОРА
4.1 Предварительный расчет валов
Ведущий вал:
Поскольку валы нагружены как крутящим, так и изгибающим моментом, то размеры вала должны учитывать это. Однако в данной работе только первый участок вала проектируется из условия прочности при кручении.
Диаметр входного участка вала:
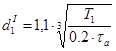 , 
где : - коэффициент, учитывающий ослабление вала шпоночным пазом
τa
=15÷ 25 H/мм2
стр.117(1)




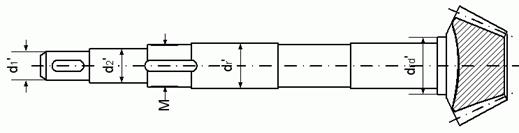
Рис.2.Эскиз ведущего вала
Ведомый вал
=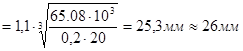




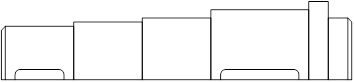
Рис.3. Эскиз ведомого вала
По значениям d3
из табл. 19.24[1] выбираем подшипники конические роликовые ГОСТ 333.75
№ вала
|
Серия
|
Т
|
В
|
С
|
r1
|
r2
|
Cr
|
Co
|
e
|
Ύ
|
d
|
D
|
1
|
7206
|
17,25
|
16
|
143
|
1,5
|
0,5
|
31
|
22
|
0,36
|
1,64
|
30
|
62
|
2
|
7206
|
17,25
|
16
|
143
|
1,5
|
0,5
|
31
|
22
|
0,36
|
1,64
|
30
|
62
|
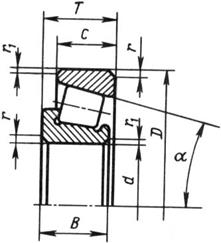
Рис.4. Параметры подшипника
Конструктивные размеры колеса конического стр.69 [2]
δо
=2,5me
+2= 2,5∙1+2=4,5≈5мм
S=0,6∙b=0,6∙28=16,8≈16 мм
C=0,3∙b=0,3∙28=8,4≈8,0 мм
dc
1
=1,55∙d=1,55∙34≈53 мм
lc
т
=(1÷1,5)d=1÷1,5)∙34=34÷51мм или lc
т
= lм
+5мм \\
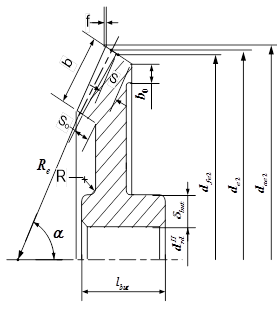
Рис.5. Эскиз зубчатого колеса
Конструктивные размеры крышек подшипников.
По стр.130 [1] находим δ, d,z ….. с= d δ1
=1,2 δ
dф
= d+d4
Размеры крышек записываем в таблицу:
№ вала
|
d
|
δ
|
δ1
|
δ2
|
d
|
c
|
z
|
d ф
|
1
|
62
|
5
|
6
|
5
|
6
|
6
|
4
|
86
|
2
|
62
|
5
|
6
|
5
|
6
|
6
|
4
|
86
|
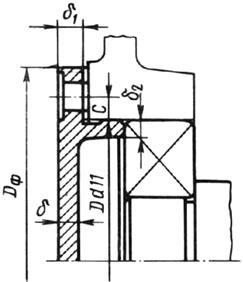
Рис.6 Крышка подшипниа
Конструктивные размеры корпуса и крышки редуктора
По стр. 179(1) толщина стенки корпуса:
≥6 мм Примем δ=6 мм
Толщина стенки крышки:
δ1
=0,9·δ=0,9·6=5,4 6 мм
Толщина фундаментных лап:
h=1,5·dф
= 1,5 ·12=18, где
dф
=1,25·d= 1,25·10=12,5мм. Примем 12 мм
– диаметр болтов "корпус – крышка"
к=3d=3·10=30 мм табл.17.1[3]
С=0,5· К=0,5· 30=15 мм
h=1,5·δ=1,5·6=9 ≈ 10 мм
h1
=1,5·δ=1,5·6=9 ≈ 10 мм
h2
=0,5·δ=0,5·6=3 мм
С=(2 ÷3) мм=3

а=10 мм
l >2a1
l 2
= l2
-стр.115(3)
мм
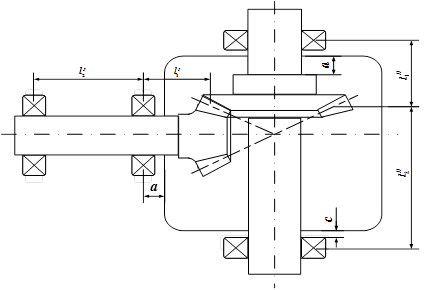
Рис.7 Схема редуктора
5. ПРОВЕРОЧНЫЙ РАСЧЕТ ВЕДОМОГО ВАЛА
Исходные данные:
5.1 Нахождение реакций в опорах и построение изгибающих моментов
Определение реакций в опорах (вертикальная плоскость)
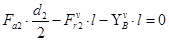

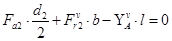

Построение эпюр изгибающих моментов
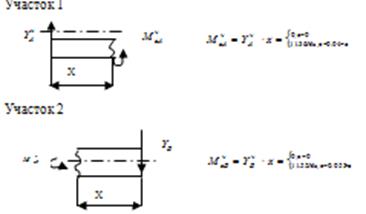
Определение реакций в вертикальной плоскости
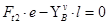
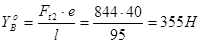
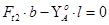
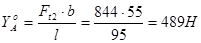
Построение
эпюр изгибающих моментов горизонтальной плоскости
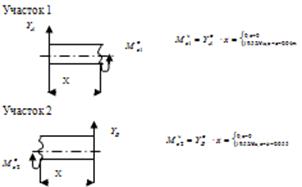
5.2 Суммарный изгибающий момент
Суммарный изгибающий момент в любой точке вала определяется по формуле



5.3 Построение эпюры эквивалентного момента
По определению второй вал подвергается как кручению, так и изгибу. Поэтому для проверочного расчета необходимо построение одной эпюры так называемого эквивалентного момента- это чисто изгибающий момент, который по воздействию на вал равен сумме воздействий крутящего и изгибающего моментов. Эквивалентный момент определяется по формуле


Из эпюры определяется опасное сечение- сечение, в котором равно максимальному значению 60,76 мм.
5.4 Определение суммарных сил реакции в опорах А и В
H
H
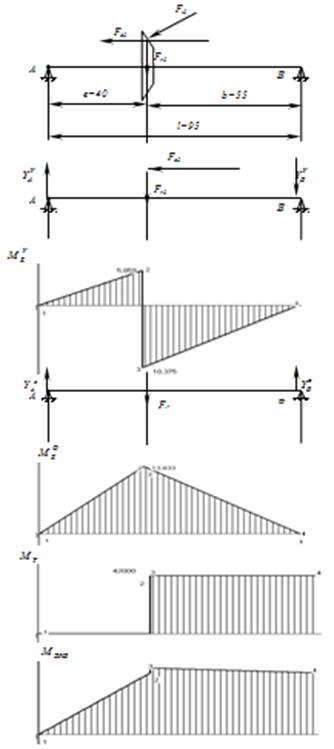
Рис.8 Построение эпюр для ведомого вала
5.5 Проверочный расчет вала по статическим нагрузкам
Данный расчет заключается в определении диаметра вала в опасном сечении из условия прочности на изгиб
Диаметр вала:
< (см. п.4.1.2)
где - допускаемое напряжение для материала вала выбирается из табл. 9.4 [2] стр.125 
5.6 Проверочный расчет вала на усталостную прочность
Данный расчет заключается в определении коэффициента запаса прочности S и его сравнении с допустимым.
Материал вала -сталь 45 (табл.12.7(1); d2
=34 мм
Коэффициент запаса прочности определяется по формуле 9.10 [1]
, =1,5÷ 2,1
где - коэффициент запаса прочности по нормальным напряжениям, Кd
=0,88 (табл. 12.12 (1)
- коэффициент запаса прочности по касательным напряжениям
где - эффективные коэффициенты концентраторов напряжений. Для выбранного материала из табл. 12.7 [1] выбирается

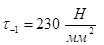
-допускаемые напряжения на усталость и на кручение
- коэффициент, учитывающий абсолютный диаметр и шероховатость вала, выбирается из табл. 12.16 [1] 
- коэффициенты, учитывающие отклонения циклов от симметричного. Для углеродистых сталей

,
для симметричного цикла 
По табл.12.11(1) определяем Wz
=3330 ; Wp
=7190


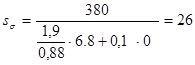
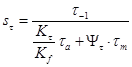 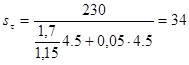
Общий коэффициент запаса:
> =1,5÷ 2,1
6. ПРОВЕРОЧНЫЙ РАСЧЕТ ПОДШИПНИКОВ
В связи с наличием осевых сил примем конические подшипники
Вал 2
Подшипник 7206 
Осевые составляющие RS
:


Осевые силы:

Отношение:
< l, то х=1,0; Υ=0
> l, то х=0,4; Υ=1,64
Эквивалентная динамическая нагрузка:


где v=1 - коэффициент кольца
х - коэффициент осевой нагрузки
КБ
=1,3 коэффициент безопасности
Кт
=1 температурный коэффициент
Долговечность подшипников Lh
> (h)=20000
где - динамическая грузоподъемность подшипника
7. ВЫБОР И РАСЧЕТ ШПОНКИ
Принимаем призматические шпонки
Вал 1 d1
=22 мм
Шпонка b x h=6x6
t1
= 3,5 мм
t2
= 2,8 мм
Рабочая длина шпонки
где c
м
= 110÷190 МПа (стр.91(1)- допускаемое напряжение смятия
Полная длина шпонки:
l= lр
+ b= 5,6+6=11,6 мм
Берем l= 25 мм.
Вал 2 d=34 мм
Шпонка b x h=10x8
t1
= 5,0 мм
t2
= 3,3 мм
Рабочая длина шпонки

Полная длина шпонки:
l= lр
+ b= 11,6+10=21,6 мм
Берем l2
=28 мм.
d'2
=24 мм
Шпонка b x h=8x7
t1
= 4,0 мм
t2
= 3,3 мм
Рабочая длина шпонки
= 12 мм
Полная длина шпонки:
l= lр
+ b= 16,4+8=22,4 мм ≈25мм
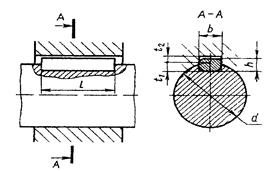
Рис.7. Схема шпоночного соединения
8. ВЫБОР СОРТА МАСЛА И СПОСОБА СМАЗКИ
Для уменьшения потерь мощности на трение и снижения интенсивности изнашивания трущихся поверхностей, а также для предохранения их от заедания, задиров, коррозии и для лучшего отвода теплоты трущиеся поверхности деталей должны иметь надежное смазывание.
Выбор смазочного материала основан на опыте эксплуатации машин. Принцип назначения сорта масла следующий: чем выше контактные давления в зубьях, тем большей вязкостью должно обладать масло, чем выше окружная скорость колеса, тем меньше должна быть вязкость масла.
При скорости колеса V=0,3÷12,5 м/c смазка колес производится окунанием колес в масляную ванну (стр.134 (1)

По табл.8.1(1) примем сорт масла И-Г-А-46.
Подшипники смазываются разбрызгиванием при работе редуктора.
Глубина погружения колес в масло (hм):
2м<hм<0,25d2
hм=2·1=2 мм; hм=0,25d2
=0,25·180=45мм
Примем hм=h2
=10 мм
Объем масла:
V=0,5·P1
=0,5·2,57=1,3 литр
Примем V=1,5 л.
ЗАКЛЮЧЕНИЕ
В данной работе был спроектирован конический редуктор, исходя из заданных выходной мощности, количества оборотов и передаточного числа. На базе данной работы были систематизированы теоретические знания. В данной работе представлена конструкция некоторых деталей и соединения, были даны условия, в которых находится редуктор, был сделан кинематический расчет сил, действующих на опору.
ЛИТЕРАТУРА
1. П.Ф.Дунаев "Детали машин", г.Москва, 1990 г.
2. И.Бостан ВРМ 2000, г.Кишинев, 2000 г.
3. А.Е.Шейнблит "Курсовое проектирование деталей машин" г.Москва, 1990 г.
|