Федеральное агентство по образованию
Государственное образовательное учреждение высшего профессионального образования
"Ижевский государственный технический университет"
Сарапульский политехнический институт
Кафедра: "Технология машиностроения, металлорежущие станки и инструменты"
Пояснительная записка к курсовому проекту
По дисциплине: Технология машиностроения
На тему: "Модернизация технологического процесса механической обработки детали – лапа долота"
Разработал: студент гр. 812
А.Х. Рахимов
Проверил: доцент, к.т.н.
В.Ю. Кулемин
Сарапул, 2010
Оглавление
Введение
1. Общая часть
1.1 Служебное назначение детали
1.2 Исходные данные для проектирования
1.3 Обоснование типа производства
2. Технологическая часть
2.1 Анализ технологичности детали
2.2 Выбор и обоснование способа получения заготовки
2.3 Разработка технологического процесса механообработки
2.3.1 Анализ существующего технологического процесса
2.3.2 Выбор баз
2.4 Расчет режимов резания
3. Конструкторская часть
3.1 Проектирование станочного приспособления
3.1.1 Описание работы приспособления
3.1.2 Расчет сил зажима детали
3.1.3 Расчет приспособления на точность
4. Проектирование контрольного приспособления
4.1 Расчет на точность контрольного приспособления
Заключение
Список использованных источников
Введение
Человеческое общество постоянно испытывает потребности в новых видах продукции, либо в сокращении затрат труда при производстве освоенной продукции. В обоих случаях эти потребности могут быть удовлетворены только с помощью новых технологических процессов, внедрения новых методов технико-экономического анализа, обеспечивающего решение технических вопросов и экономическую эффективность технологических и конструкторских разработок и новых машин, необходимых для их выполнения. Значение постановки всех этих вопросов при подготовке квалифицированных кадров специалистов производства, полностью инженерными методами проектирования производственных процессов, очевидно. Совокупность методов и приемов изготовления машин, выработанных в течение длительного времени и используемых в определенной области производства, составляет технологию этой области. В связи с этим возникли понятия: технология литья, технология обработки давлением, технология сварки, технология механической обработки, технология сборки машин. Все эти области производства относятся к технологии машиностроения, охватывающей все этапы процесса изготовления машиностроительной продукции. Комплексная механизация и автоматизация технологических процессов в машиностроении является определенным этапом развития техники производства. Комплексную автоматизацию технологических процессов следует рассматривать как высшую форму механизации труда, когда рабочий освобождается от прямого воздействия на продукт труда и за ним остается лишь функция управления сложными автоматическими машинами, осуществляющими технологические процессы. В данной курсовой работе мы пытаемся применить все знания, полученные ранее, для того чтобы спроектировать такой технологический процесс, который бы удовлетворял всем требованиям, предъявляемых к современному производству.
1. Общая часть
1.1 Служебное назначение детали
Деталь – лапа 660,4М-ЦГВУ. С112.040 входит в состав долота 660,4М-ЦГВУ.С112 и изготовлен из стали 20ХН3А-Ш. Лапа каждой секции представляет собой сектор в виде двухгранного угла в 120˚, вследствии чего три соединенные лапы образуют в поперечном сечении круг. Шарошка устанавливается на цапфе лапы через подшипник, образованный двумя наборами цилиндрических роликов и одним набором шариков. Таким образом лапа предназначена для фиксации шарошки и создании корпуса.
Основные сведения об изделии.
Буровое трехшарошечное долото 660,4М-ЦГВУ.С112 является породоразрушающим инструментом и предназначено для бурения скважин.
К основным параметрам бурового трехшарошечного долота, которые ограничены допусками, относят диаметр долота, разновысотность зубков шарошек, радиальное биение диаметрального размера долота относительно резьбы ниппельной части долота и радиальные биения шарошек относительно цапфы лапы.
Под диаметральным размером долота понимается диаметр условной окружности бурового трехшарошечного долота, проведенной через наиболее удаленные калибрующие зубья трех шарошек относительно оси резьбовой поверхности долот.
Разновысотность долота, выраженная как расстояние между крайними точками вершин конусов шарошек.
Основные технические данные:
Диаметр долота, мм 660,4
Высота долота, мм 760
Спинка лапы армирована твердым сплавом - рэлит
Максимально допустимая нагрузка, Кн 400
Масса долота, кг 720
Долото состоит из трех секций, каждая из которых содержит лапу, опорный подшипник, состоящий из двух наборов цилиндрических роликов и набора шариков, насадку гидромониторного канала, замковый палец и шарошку с зубками в количестве зависящем от модели долота. Наборы шариков и роликов образуют соответствующие подшипники.
В процессе бурения скважины долото вращается, совершает поступательное движения, одновременно вращаются и шарошки, разрушая породу.
Обрабатываемые поверхности с точки зрения обеспечения точности и шероховатости не представляют особых технологических трудностей. Но деталь имеет сложную конфигурацию и форму, поэтому обработка детали вызывает небольшие затруднения, требуя специального инструмента, что увеличивает себестоимость обработки детали и самого изделия в целом.
Технологичность – важнейшая техническая основа, обеспечивающая использование конструкторских и технологических резервов для выполнения задания по повышению технико-экономических показателей изготовления и качества изделий.
Проектируемый технологический процесс должен быть с минимальными трудовыми и материальными затратами. Это зависит от правильного выбора технологического процесса, его оснащения, механизации, автоматизации, применения оптимальных режимов обработки и правильной подготовки производства.
1.2 Исходные данные для проектирования
Исходными данными для проектирования, необходимыми для разработки проекта, являются:
- Наименование детали – лапа;
- Материал детали – 20ХН3А-Ш;
- Чистый вес детали – 61 кг.;
- Продолжительность рабочей смены – 8 часов;
- Задание на проектирование – модернизация технологического процесса механической обработки лапы.
Таблица 1 Химический состав стали 20ХН3А-Ш
С |
Cr |
Ni |
Sне более |
Pне более |
0,17-0,22 |
0,60-0,90 |
2,75-3,15 |
0,015 |
0,020 |
Таблица 2 Механические свойства стали 45
σТ
, МПа |
σвр
, МПа |
δ, % |
ψ, % |
ан
, Дж/см2
|
НВ (не более) |
На расстоянии от торца |
не менее |
4,5 |
30 |
882(90) |
610 |
8 |
40 |
88,2 |
37-43 |
22-32 |
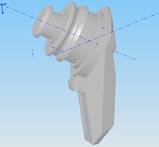
Рис.1 Лапа
Заготовка для изготовления детали - лапа получена методом – поковки горячей ковки на штампованных молотах.
Технологический процесс кузнечно-штамповочного производства характеризуется простотой, высокой экономичностью и производительностью. С помощью разнообразных способов ковки и штамповки получают большое число поковок деталей машин, приборов и т.д.
Трудоемкость кузнечных процессов в значительной степени зависит от серийности и масштаба производства, которые в свою очередь обуславливают специализацию и механизацию, или автоматизацию процессов и техническую культуру производства.
Производственный процесс в кузнечно-штамповочных цехах характеризуется простотой, относительно малой операционностью высокой производительностью, большой металлоемкостью и энергоемкостью.
1.3 Обоснование типа производства
Таблица 3 Проектный вариант технологического процесса
№ опер. |
Операция |
Оборудование |
1 |
Контроль |
Стол контрольный |
2 |
Зачистка |
Пост зачиски |
3 |
Сверлильно-центровальная |
2Н150 |
4 |
Сверлильно-центровальная |
2Н150; 2Н135 |
5 |
Зачистка |
Пост зачиски |
6 |
Токарная |
РТ-467 |
7 |
Токарная |
РТ-467 |
8 |
Токарная |
РТ-467 |
9 |
Токарная |
РТ-467 |
10 |
Фрезерная |
ГФ-1420 |
11 |
Фрезерная |
ГФ-1420 |
12 |
Фрезерная с ЧПУ |
ОЦ22и22"МАЯК-42-2" |
13 |
Фрезерная сЧПУ |
ОЦ22и22"МАЯК-42-2" |
14 |
Фрезерная |
6М13П |
15 |
Фрезерная |
6Т83Г |
16 |
Фрезерная |
6М13П |
17 |
Фрезерная |
6М13П |
18 |
Фрезерная |
6М13П |
19 |
Комплексная на обрабатывающих центрах с ЧПУ |
ОЦ22и22"МАЯК-42-2" |
20 |
Токарная с ЧПУ |
1740 РФЗ |
21 |
Сверлильная |
2М112 |
22 |
Сверлильная |
2Н135 |
22 |
Сверлильная |
2М112 |
23 |
Токарная (вариант) |
РТ 468 |
24 |
Токарная (вариант) |
РТ 468 |
25 |
Слесарная |
Верстак |
26 |
Маркирование |
Верстак |
27 |
Контроль |
Стол контрольный |
28 |
Армирование |
29 |
Шлифование |
ХШ1 -06 |
30 |
Шлифование |
ХШ1 -06 |
31 |
Шлифование |
ХШ1 -06 |
32 |
Шлифование |
ХШ1 -06 |
33 |
Контроль |
Стол контрольный |
34 |
Обмазка и сушка |
35 |
Обмазка и сушка |
36 |
Химико-термическая обработка |
37 |
Транспортирование |
Автопогрузчик |
38 |
Слесарная |
Верстак |
39 |
Шлифование |
ХШ1-06 |
40 |
Шлифование |
ХШ1-06 |
41 |
Шлифование |
ХШ1-06 |
42 |
Шлифование |
ХШ1-06 |
43 |
Полировальная |
ХШ1-06 |
44 |
Промывка |
М-216 |
45 |
Контроль |
Стол контрольный |
Определяем программу запуска по формуле:
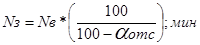
где: Nв - программа выпуска, Nв=3000 шт, αотс
- коэффициент технологического отсева (0,3-0,6), принимаем αотс
=0,5%, тогда:
шт.
Тип производства определяем по коэффициенту серийности:

где: r – такт поточной линии, мин; tшт.ср
– среднештучное время по участку, мин; Такт поточной линии можно определить по формуле:
; мин.
где: Fд.
– эффективный фонд времени работы производственного оборудования, час; для двухсменной работы принимаем: Fд.
=4015 часов, тогда:
мин.
Среднештучное время по участку определяем по формуле:
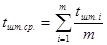
где tшт.
i
– штучное время на i операции, m – количество операций, тогда: tшт.ср.
= мм.
коэффициент серийности:
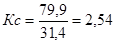
т.к. 1.4 до 5Кс=2,54 то делаем вывод, что производство крупносерийное.
2. Технологическая часть
2.1 Анализ технологичности детали
Деталь-лапа изготовлена из стали 20ХН3А-Ш. Она предназначена для фиксации шарошки и создания корпуса.
Технологичность – важнейшая техническая основа, обеспечивающая использование конструкторских и технологических резервов для выполнения задач по повышению технико-экономических показателей изготовления и качества изделий.
Технологический анализ конструкции детали обеспечивает улучшение технико-экономических показателей разрабатываемого технологического процесса. Поэтому технологический анализ – один из важнейших этапов технологической разработки. Основные задачи, решаемые при анализе технологичности конструкции обрабатываемой детали, сводятся к возможному уменьшению трудоемкости и материалоемкости, возможности обработки детали высокопроизводительными методами. Таким образом, улучшение технологичности конструкции позволяет снизить себестоимость ее изготовления без ущерба для служебного назначения.
В данном курсовом проекте мы совмещаем несколько операций в одну.
Точность размеров и допусков формы и расположения поверхностей заданных конструктором не вызывает существенных трудностей и может быть обеспечено оборудованием нормальной точности.
Деталь в отношении технологичности имеет ряд трудностей, с точки зрения механической обработки, т.к деталь сложна в конструкции. Сложность заключается в базировании заготовки в процесс обработки.
В остальном деталь технологична и допускает применение высокотехнологичных режимов обработки.
2.2 Выбор и обоснование способа получения заготовки
Заготовка лапы являются – поковки горячей ковки на штамповочных молотах. Штамповка заготовки производится на молотах (5 тонн) в закрытых штампах или можно производить на прессах, Технологический процесс кузнечно-штамповочного производства характеризуется простотой, высокой экономичностью и производительностью. С помощью разнообразных способов ковки и штамповки получают большое число поковок деталей машин, приборов и т.д.
При выборе метода получения заготовки учитываем размеры и форму детали, а также тип производства.
Допускается чтобы наружный контур не был оформлен полностью.
2.3 Разработка технологического процесса механообработки
2.3.1 Анализ существующего технологического процесса
Таблица 4 Базовый и проектируемый технологические процессы
Базовый тех. процесс |
Проектный тех. процесс |
№ опер |
Наименование операции |
Оборудование |
Наименование операции |
Оборудование |
005 |
Контроль |
Стол контрольный |
Контроль |
Стол контрольный |
010 |
Зачистка |
Пост зачиски |
Зачистка |
Пост зачиски |
015 |
Сверлильно-центровальная |
2Н150 |
Сверлильно-центровальная |
2Н150 |
020 |
Сверлильно-центровальная |
2Н150; 2Н135 |
Сверлильно-центровальная |
2Н150; 2Н135 |
035 |
Зачистка |
Пост зачиски |
Зачистка |
Пост зачиски |
040/1 |
Токарная |
РТ-467 |
Токарная |
РТ-467 |
040/2 |
Токарная |
РТ-467 |
Токарная |
РТ-467 |
040/3 |
Токарная |
РТ-467 |
Токарная |
РТ-467 |
040/4 |
Токарная |
РТ-467 |
Токарная |
РТ-467 |
045 |
Фрезерная |
ГФ-1420 |
Фрезерная |
ГФ-1420 |
050 |
Фрезерная |
ГФ-1420 |
Фрезерная |
ГФ-1420 |
055 |
Фрезерная с ЧПУ |
ОЦ22и22"МАЯК-42-2" |
Фрезерная с ЧПУ |
ОЦ22и22"МАЯК-42-2" |
060 |
Фрезерная сЧПУ |
ОЦ22и22"МАЯК-42-2" |
Фрезерная сЧПУ |
ОЦ22и22"МАЯК-42-2" |
065 |
Фрезерная |
6М13П |
Фрезерная |
6М13П |
070 |
Фрезерная |
6Т83Г |
Фрезерная |
6Т83Г |
075 |
Фрезерная |
6М13П |
Фрезерная |
6М13П |
080 |
Фрезерная |
6М13П |
Фрезерная |
6М13П |
085 |
Фрезерная |
6М13П |
Фрезерная |
6М13П |
090 |
Комплексная на обрабатывающих центрах с ЧПУ |
ОЦ22и22"МАЯК-42-2" |
Комплексная на обрабатывающих центрах с ЧПУ |
ОЦ22и22"МАЯК-42-2" |
095 |
Токарная с ЧПУ |
1740 РФЗ |
Токарная с ЧПУ |
1740 РФЗ |
100 |
Сверлильная |
2М112 |
Сверлильная |
2М112 |
105 |
Сверлильная |
2Н135 |
Сверлильная |
2Н135 |
110 |
Сверлильная |
2М112 |
Сверлильная |
2М112 |
115 |
Токарная (вариант) |
РТ 468 |
Токарная (вариант) |
РТ 468 |
115 |
Токарная (вариант) |
РТ 468 |
Токарная (вариант) |
РТ 468 |
120 |
Слесарная |
Верстак |
Слесарная |
Верстак |
125 |
Маркирование |
Верстак |
Маркирование |
Верстак |
130 |
Контроль |
Стол контрольный |
Контроль |
Стол контрольный |
145-150 |
Армирование |
Армирование |
155 |
Шлифование |
ХШ1 -06 |
Шлифование |
ХШ1 -06 |
160 |
Шлифование |
ХШ1 -06 |
Контроль |
Стол контрольный |
165 |
Шлифование |
ХШ1 -06 |
Обмазка и сушка |
170 |
Шлифование |
ХШ1 -06 |
Обмазка и сушка |
180 |
Контроль |
Стол контрольный |
Химико-термическая обработка |
200 |
Обмазка и сушка |
Транспортирование |
Автопогрузчик |
205 |
Обмазка и сушка |
Слесарная |
Верстак |
250-260 |
Химико-термическая обработка |
Шлифование |
ХШ1-06 |
265 |
Транспортирование |
Автопогрузчик |
Шлифование |
ХШ1-06 |
275 |
Слесарная |
Верстак |
Шлифование |
ХШ1-06 |
280 |
Шлифование |
ХШ1-06 |
Шлифование |
ХШ1-06 |
285 |
Шлифование |
ХШ1-06 |
Полировальная |
ХШ1-06 |
290 |
Шлифование |
ХШ1-06 |
Промывка |
М-216 |
295 |
Шлифование |
ХШ1-06 |
Контроль |
Стол контрольный |
300 |
Полировальная |
ХШ1-06 |
305 |
Промывка |
М-216 |
310 |
Контроль |
Стол контрольный |
В разрабатываемом проекте произошли существенные изменения по сравнению с базовым технологическим процессе. Поменялись операции, то есть вместо трех операций шлифования получаем одну. Сокращаем время обработки и стоимость затраченную на обработку. Это даст существенный экономический эффект и позволяет повысить заработную плату производственных рабочих.
2.3.2 Выбор баз
При выборе технологических баз руководствуются рядом общих положений. Сначала мы создаем центровые отверстия, которые являются базой для последующих операций. При прочих равных условиях наибольшая точность достигается при использовании на всех операциях одних и тех же баз, то есть при соблюдении принципа единства баз. Желательно совмещать технологические базы с измерительными базами. При совмещении технологических и измерительных баз погрешность базирования равна нулю. Базы используемые на операциях окончательной обработки должны отличатся наибольшей точностью по линейным и угловым размерам, геометрической форме и параметру шероховатости. Выбранные технологические базы совместно с зажимными устройствами должны обеспечить правильное базирование и надежное крепление заготовки, гарантирующее неизменность ее положений во время обработки, а также простую конструкцию приспособления, удобство установки и снятия заготовки. на выполняемом технологическом. При прочих равных условиях наибольшая точность достигается при использовании на всех операциях одних и тех же баз, то есть при соблюдении принципа единства баз. Желательно совмещать технологические базы с измерительными базами. При совмещении технологических и измерительных баз погрешность базирования равна нулю. Базы используемые на операциях окончательной обработки должны отличатся наибольшей точностью по линейным и угловым размерам, геометрической форме и параметру шероховатости. Выбранные технологические базы совместно с зажимными устройствами должны обеспечить правильное базирование и надежное крепление заготовки, гарантирующее неизменность ее положений во время обработки, а также простую конструкцию приспособления, удобство установки и снятия заготовки.
2.4 Расчет режимов резания
Режимы резания, устанавливаемые при обработке деталей, являются одним из главных факторов технологического процесса.
Режимы резания выбираются таким образом, чтобы при наименьшей себестоимости данной технологической операции была достигнута наибольшая производительность труда.
Операция 155 Шлифовальная.
Шлифование роликовых и шариковой беговых дорожек производится блоком абразивных кругов предварительно правленых блоком алмазных роликов. Производится на станке модели ХШ1-06.
Исходные данные: D=87,6мм, B=40,2+0,16
мм; D=169,9 -0,1
мм,B=50-0,33
мм; D=174,9мм B=40,2+0,16 мм.
1) Зернистость шлифовальных кругов 40
2) Скорость круга Vк
=30 м/с
3) Скорость заготовки Vз
=30м/мин.
4) Радиальная подача Sp
=0,005мм/об
5) Определяем эффективную мощность при врезном шлифовании периферией круга: (d- диаметр шлифования, b- ширина шлифования равная длине шлифуемого участка заготовки при круглом врезном шлифовании торцом круга).
Коэффициент и значение показателей формулы для круглого наружного врезного шлифования:
CN
=0,07; r=0,65; x=0,65; y=1; q=0,5; z=1
(кВт)
(кВт)
(кВт)
Общую эффективную мощность развиваемую при врезном шлифовании на периферии кругов всех шлифовальных кругов в блоке находим по формуле:
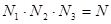
N=1,2+2,08+1,7=4,98 (кВт).
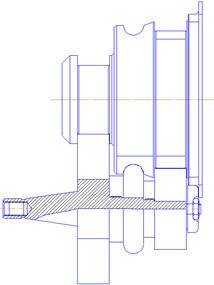
Рис 2. Процесс шлифования
3. Конструкторская часть
3.1 Проектирование станочного приспособления
3.1.1 Описание работы приспособления
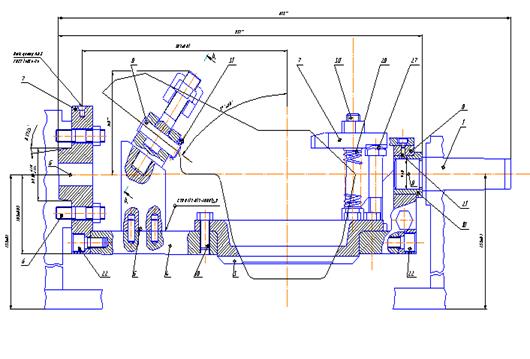
Рис 3. Приспособление станочное
Для операции-центровки и сверления отверстий разработано станочное приспособление, применяемое на станке с 2Н150, 2Н135.
У такого привода много преимуществ:
1. Значительное сокращение времени на зажим и разжим обрабатываемой заготовки.
2. Постоянство сил зажима заготовки в приспособлении.
3. Возможность регулирования сил зажима заготовки.
4. Простота управления зажимными устройствами приспособления.
Установка в приспособлении производится по определенным поверхностям заготовки, при этом фактическое положение заготовки в рабочей зоне станка, вносят коррекцию в программу обработки, таким образом, в этом случае требования к точности установки заготовки в приспособлении более низкие, чем при установке в приспособление без выверки и установки в приспособление с выверкой положения каждой заготовки по разметочным рискам.
Для ориентации предмета производства (заготовки при изготовлении детали или сборочной единицы при сборке изделия) в приспособлении определенные ее поверхности соединяются с поверхностями детали технологической оснастки. Поверхности, принадлежащие заготовке и используемые при базировании, называются базами. Базы используют для определения положения: детали или сборочной единицы в изделии при изготовлении или ремонте – технологическая база; средств измерения при контроле расположения поверхностей заготовки или элементов изделия – измерительная база.
В данном приспособлении заготовка базируется по поверхности цапфы лапы и для этого плита 4 в сочетании с кольцом 3 создают точный контур заготовки.
С помощью зажимного устройства лапа закрепляется на конце хвостовика. Оно фиксируется к приспособлению с помощью нескольких шпилек, а также с помощью Т-образная сварка.
3.1.2 Расчет сил зажима детали
К зажимным устройствам предъявляются следующие требования:
1. При зажиме не должно нарушаться положение заготовки, достигнутое базированием. Это удовлетворяется рациональным выбором направления и точки приложения точки зажима.
2. Зажим не должен вызывать деформации закрепляемых в приспособлении заготовок или порчи (смятия) их поверхностей.
3. Сила зажима должна быть минимальной необходимой, но достаточной для обеспечения надежного положения заготовки относительно установочных элементов приспособлений в процессе обработки.
4. Зажим и открепление заготовки необходимо производить с минимальной затратой сил и времени рабочего.
5. Силы резания не должны, по возможности, воспринимать зажимные устройства.
6. Зажимной механизм должен быть простым по конструкции, максимально удобным и безопасным в работе.
Потребная сила зажима заготовки определяется из условия равновесия заготовки с учетом коэффициента запаса k.
W=P*k;
Р - сила резания при фрезеровании;
Коэффициент запаса k является произведением семи первичных коэффициентов:

где k0
- гарантированный коэффициент запаса, k0
=1,5; k1
- коэффициент, учитывающий возрастание сил обработки при затуплении инструмента, k1
=1,0; k2
- коэффициент, учитывающий неравномерность сил резания из-за непостоянства снимаемого при обработке припуска, k2
=1,2; k3
- коэффициент, учитывающий изменение сил обработки при прерывистом резании, k3
=1,0; k4
- коэффициент, учитывающий непостоянство развиваемых приводами сил зажима, k4
=1,0; k5
- коэффициент, учитывающий непостоянство развиваемых сил зажимных устройств с ручным приводом, k5
=1,0; k6
- коэффициент, учитывающий неопределенность положения мест контакта заготовки с установочными элементами, k6
=1,0;
3.1.3 Расчет приспособления на точность
Требуемое положение заготовки в рабочей зоне станка достигается в процессе её установки. Процесс установки включает базирование и закрепление.
Базирование – придание заготовке или изделию требуемого положения относительно выбранной системе координат.
Закрепление – приложение сил и пар сил к изделию для обеспечения постоянства и неизменности его положения, достигнутого при базировании. Фактическое положение заготовки отличается от требуемого.
Отклонение в положении заготовки, возникающее при базировании, называют погрешностью базирования Δεб
=0[7, стр.80]; при закреплении – погрешностью закрепления Δεз
=0,01; при установке – погрешностью установки Δεу
=0,055мм, причем Δεу
=f(Δεб
, Δεз
).
Общая погрешность находится по следующей формуле:
;
.
При закреплении заготовок в призме имеют место контактные деформации, вызывающие смещение оси заготовки. Величину смещения (осадку) заготовок в мкм в плоскости симметрии призмы с углом 90۫ можно определить по эмпирической формуле:
4. Проектирование контрольного приспособления
Контрольные приспособления применяют для проверки заготовок, деталей и узлов машин. Приспособления для проверки деталей применяют на промежуточных этапах обработки (межоперационный контроль) и для окончательной их приемки. При помощи этих приспособлений проверяют точность размеров и взаимного положения поверхностей, а также правильность их геометрической формы.
Высокая точность современных машин обусловливает необходимость применения в контрольных приспособлениях измерителей высокой чувствительности, а также правильного выбора принципиальной схемы и конструкции приспособления.
Погрешность измерения, под которой понимают разность между показанием контрольного приспособления и фактическим значением измеряемой величины, должна быть по возможности малой. Однако чрезмерное повышение точности измерения может привести к усложнению и удорожанию приспособления и снижению его производительности.
Контрольное приспособление предназначено для проверки соосности беговых дорожек относительно центровых отверстий.
Для измерения диаметра беговых дорожек в лапах долот и устанавливает методы и средства их проверки.
В процессе контроля необходимо закрепить заготовку с помощью неподвижного центра в одно центровое отверстие и с помощью подвижного центра с другое центровое отверстие. Необходимо их надежное закрепление.
Перемещение измерительной ножки, а также стрелки индикатора должно производится плавно.
Пределы измерения нутрометра – приспособления контрольного должны соответствовать техническим требованиям на приспособление контрольное.
Размах показаний определяют как разность наибольшего и наименьшего показаний нутрометра при десятикратном измерении диаметра одного и того же кольца. Размах показаний должен быть не более 0,005 мм.
Контрольное приспособление состоит из установочных, зажимных, измерительных и вспомогательных элементов, установленных в корпусе приспособления. Проверяемую деталь поджимается с одной стороны неподвижным центром, а с другой стороны подвижным центром. Индикатор крепится в корпусе и все это закрепляется на стойке. Все элементы приспособления устанавливаются на плите.
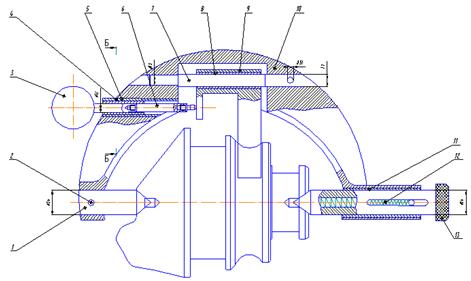
Рис.4 Приспособление контрольное
4.1 Расчет на точность контрольного приспособления
Погрешностью измерений называется разность между полученным при измерении размером и его истинным значением.
Погрешность измерения является следствием ряда факторов, проявляющихся в процессе измерения. К ним относятся погрешность приспособления, температурные деформации, отклонения элементов для настройки приспособления, ошибки оператора другие погрешности. Количество факторов, влияющих на погрешность измерения и степень влияния каждого фактора на общую погрешность измерения, зависит от метода измерения.
В данном контрольном приспособлении используется индикатор с ценой деления 0,001 мм и пределами измерения 1 мм.
1. Назначение приспособления – определить биение детали.
Измерение производится после установки детали в приспособлении и выведения стрелки индикатора на ноль, при этом измерительный наконечник должен касаться передней грани детали. Вращая деталь, на индикаторе отражается какое биение дает деталь.
2. Основные ошибки узлов:
Установка детали в центрах и закрепление ее на ней. Погрешность установки зависит от силы зажима, которая была приложена при закреплении детали в центрах. Погрешность закрепления равна 0,001 мм.
3. Исходным звеном измерительной размерной цепи является расстояние контактной точки измерительного наконечника от поверхности детали при нулевом положении стрелки индикатора.
Составляющие погрешности:
-погрешность установки;
-погрешность настройки (отклонение установочной меры);
-погрешность образцовых перемещений;
-погрешность измерительных перемещений;
-погрешность отсчета;
4. Условия измерения:
Отклонения от нормальной температуры в цехе 5ْ
Измерительное усилие 1Н. Средний темп сбоя 0,01-0,03 мкм на одно измерение. Использование образцовой детали и установочной меры позволяет исключить влияние температуры и измерительного усилия и значительно уменьшить влияние нарушения первичной настройки.
5. Допускается погрешность измерения для деталей средней точности, согласно табл.1 [л.5], составляет 25% от Тизд
или 25 мкм. Указанная погрешность дает m=3,75; n=5,4 и С=0,17. Т. к.приспособление стоит на участке заточки, ошибочно забракованные детали (в количестве n%) могут быть исправлены. ВС СЭВ 303-76 принято нормировать погрешность измерения δ (согласно определению погрешности) половиной размаха кривой рассеивания и истинным значениями размеров может быть больше и меньше нуля, т. е. размах погрешности измерения составит 25*2=50 мкм (±25 мкм).
Дальнейший расчет погрешностей составляющих звеньев будем вести, исходя из абсолютной величины погрешности измерения, т. е. выявлять значения предельных величин погрешностей составляющих звеньев также без учета знака.
6. Переход от погрешностей к их предельным допустимым значениям (допускам) производится обычно заменой символа Δ на δ.
Допустимая погрешность измерения δизм
равна:
;
где δ1
*ζ1
– зазор между деталью и центрами;δ1
*ζ1
=0,004 мм;δ2
*ζ2
=0,0001 мм; δ3
*ζ3
=0,0001 мм; δ4
*ζ4
= 0,001 мм;

Величина контактных деформаций (измерительный наконечник из искусственного корунда, деталь из стали)
;
гдеР – сила, Н; r – радиус сферы, м.
мкм;
Погрешность контрольного приспособления:

где d1
– погрешность настройки, d1
=0,01; d2
– погрешность установки вала в центрах, 0; d3
– погрешность закрепления индикатора, а т. к. перед измерением производится установка индикатора на ноль, то d4
=0;d4
– погрешность индикатора, d5
=0,001 мм.

Заключение
В данном курсовом проекте был модернизирован базовый технологический процесс. Так как базовый технологический процесс содержал много недостатков: применялось старое оборудование, на котором качество обработки было не самым лучшим, режимы резания, ухудшающие качество поверхностного слоя и др.
В модернизированном технологическом процессе был изменен порядок обработки, то есть нарезание резьбы производится перед операцией фрезерования пазов и сверления отверстий. Эти операции были соединены в одну, что позволило улучшить производительность труда и сократить время обработки.
Для повышения производительности обработки было разработано быстродействующее зажимное станочное приспособление. За счет этого приспособления уменьшилось подготовительно-заключительное время на операцию, так как упрощается управление зажимными устройствами приспособления. Такое приспособление работает бесперебойно при изменениях температуры воздуха в окружающей среде.
Для контроля биения детали было разработано контрольное приспособление. Оно просто в управлении и дает маленькую погрешность измерения.
В целом, при разработке технологического процесса, быстродействующих зажимных приспособлений и выбора оборудования учитывались реальные возможности и потребности производства с целью возможного внедрения курсового проекта на предприятии.
Список использованных источников
1. Андреев Г.Н. Проектирование технологической оснастки машиностроительного производства. М. "Высшая школа", 1999.
2. Анурьев В.И. Справочник конструктора-машиностроителя: В 3т. Т.1 – 8-е изд., перераб. и доп. Под ред. И.Н. Жестоковой - М.: Машиностроение, 2001. – 920 с. ил.
3. Базров Б.М. Основы технологии машиностроения: Учебник для вузов. М.: Машиностроение, 2005. – 736с. ил.
4. Иванов М.И. Детали машин. – М.: "Высшая школа" 7-е издание, перераб. и доп. 2002.
5. Колесов И.М. Основы технологии машиностроения; Учебник для машиностроительных специальных вузов – 2-е изд., испр. – М.: Высшая школа., 1999 – 591с. ил.
6. Справочник технолога - машиностроителя. В 2-х т. Т.1/Под ред. А.М. Дальского, А.Г. Косиловой, Р.К. Мещерякова, А. Г. Суслова. – 5-е изд., исправл.. – М.: Машиностроение-1, 2003г. 912с., ил.
7. Справочник технолога - машиностроителя. В 2-х т. Т.2/Под ред. А.М. Дальского, А.Г. Косиловой, Р.К. Мещерякова, А.Г. Суслова. – 5-е изд., исправл.. – М.: Машиностроение-1, 2003г. 944с., ил.
8. Схиртладзе А.Г. Новиков В.Ю. "Станочные приспособления". Учеб. пособие для вузов: Высш. шк., 2001. – 110с.:ил.
9. Технология машиностроения: В 2кн. Кн.1. Основы технологии машиностроения: Учеб. пособие для вузов/ Э.Л. Жуков, И.И. Козарь, С.Л. Мурашкин и др.; Под ред. С.Л. Мурашкина – М.: Высш. шк., 2003 – 278с.: ил.
|