Министерство Образования Российской Федерации
Комсомольский-на-Амуре
Государственный Технический Университет
Кафедра Экологии и Безопасности жизнедеятельности
Расчетно-графическое задание по безопасности жизнедеятельности.
(выплавка чугуна)
Студент: Рыков В.С.
Группа: 5ТС-1
Преподаватель: Ермакова О.Н.
Комсомольск-на-Амуре
2007 г.
Содержание
Введение
1. Краткое описание особенностей выполняемой работы
1.1 Выплавка чугуна
1.2 Физико-химические процессы доменной плавки
1.3 Характеристика вредных веществ, выделяющихся при выплавке чугуна
2. Оценка состояний условий труда на рабочих местах
3. Мероприятия по достижению безопасных условий работ
3.1 Колошниковые газы
3.2 Выпуск чугуна
3.3 Охлаждение шлака
4. Техника безопасности
5. Список литературы
Целью данного расчетного задания является анализ производственной среды и установление соответствия состояния рабочего места служащего требованиям нормативных документов. Анализ производственной среды заключается в оценке условий труда и техники безопасности при выполнении определенных видов работ. В процессе работы необходимо:
ознакомиться с основными приемами выполнения конкретного вида работы;
ознакомиться с используемыми в данном технологическом процессе материалами, оборудованием, инструментами;
определить потенциальную опасность, заключенную в орудиях труда и технологических приемах, характерных для исследуемого вида работ;
ознакомиться с рабочими средствами измерения действующих на работающего или служащего факторов производственной среды;
ознакомиться с требованиями нормативных документов по безопасной организации труда и оценке условий труда;
произвести оценку условий труда в соответствии с документами: 'Типовое положение об оценке условий труда на рабочих местах и порядок применения отраслевых перечней работ, на которых могут устанавливаться доплаты рабочим за условия труда N 3877/22-78 от 3.10.86 " и "Гигиеническая классификация труда", утвержденная Министерством здравоохранения СССР 12 08.86 под N 4137-86 /1,2/;
разработать инструкцию по охране труда для работников на основании Постановления Министерства труда РФ от 01.07.94 за N 129 "Об утверждении Положения о порядке разработки и утверждения правил и инструкций по охране труда и Методических указаний по разработке правил и инструкций по охране труда ";
рекомендовать мероприятия по снижению воздействия действующих факторов производственной среды в соответствии с современными достижениями в науке и технике и учетом передового опыта организации производства и труда.
Объём доменного производства чугуна в целом по всему миру составляет 270 млн. т. в год.
Чугун выплавляют в печах шахтного типа - доменных печах. Сущность процесса получения чугуна в доменных печах заключается в восстановлении оксидов железа, входящих в состав руды, оксидом углерода, водородом, выделяющимся при сгорании топлива в печи и твердым углеродом.
Устройство доменной печи и ее работа.
Доменная печь имеет стальной кожух, выложенный внутри огнеупорным шамотным кирпичом. Рабочее пространство печи включает колошник 6,
шахту 5,
распар 4,
заплечики 3,
горн 1,
лещадь 15.
В верхней части колошника находится засыпной аппарат 8,
через который в печь загружают шихту (офлюсованный агломерат и окатыши). Шихту взвешивают, подают в вагонетки 9
подъемника, которые передвигаются по мосту 12
к засыпному аппарату 8
и, опрокидываясь, высыпают шихту в приемную воронку 7
распределителя шихты. При опускании малого конуса 10
засыпного аппарата шихта попадает в чашу 11
, а при опускании большого конуса 13 -
в доменную печь, что предотвращает выход газов из доменной печи в атмосферу. Для равномерного распределения шихты в доменной печи малый конус и приемная воронка после очередной загрузки поворачиваются на угол, кратный 60°.
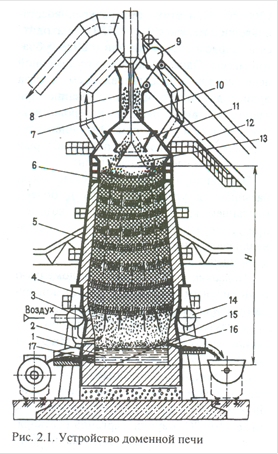
При работе печи шихтовые материалы, проплавляясь, опускаются, а через загрузочное устройство в печь подаются новые порции шихты в таком количестве, чтобы весь полезный объем печи был заполнен. Полезный объем печи - это объем, занимаемый шихтой от лещади до нижней кромки большого конуса засыпного аппарата при его опускании. Современные доменные печи имеют полезный объем 2000...5000 м3
. Полезная высота доменной печи достигает 35 м.
В верхней части горна находятся фурменные устройства 14,
через которые в печь поступает нагретый воздух, необходимый для горения топлива. Воздух нагревают для уменьшения потерь теплоты и снижения расхода кокса. Воздух поступает в доменную печь из воздухонагревателя, внутри которого имеются камера сгорания и насадка. Насадка выложена из огнеупорных кирпичей, так что между ними образуются вертикальные каналы. В камеру сгорания к горелке подается очищенный от пыли доменный газ, который сгорает и образует горячие газы.
Газы, проходя через насадку, нагревают ее и удаляются через дымовую трубу. Затем подача газа к горелке прекращается, и через насадку пропускается воздух, подаваемый турбовоздуходувной машиной. Воздух, проходя через насадку, нагревается до температуры 1000...1200 °С и поступает к фурменному устройству 14,
а оттуда через фурмы 2 -
в рабочее пространство. Доменная печь имеет несколько воздухонагревателей: в то время как в одних насадках нагревается, в других насадка отдает теплоту холодному воздуху, нагревая его. После охлаждения насадки воздухом нагреватели переключаются.
Условно процессы, протекающие в доменной печи, разделяют на горение топлива; разложение компонентов шихты; восстановление железа; науглероживание железа; восстановление марганца, кремния, фосфора, серы; шлакообразование. Все эти процессы проходят в доменной печи одновременно, но с разной интенсивностью, при различных температурах и на разных уровнях.
Горение топлива.
Вблизи фурм углерод кокса, взаимодействуя с кислородом воздуха, сгорает. В результате горения выделяется теплота и образуется газовый поток, содержащий СО, CO2
, N2
, Н2
, СН4
и др. При этом в печи несколько выше уровня фурм развивается температура выше 2000 °С. Горячие газы, поднимаясь, отдают теплоту шихтовым материалам и нагревают их, охлаждаясь до температуры 300...400 °С у колошника.
Восстановление железа в доменной печи.
Шихта (агломерат, кокс) опускается навстречу потоку газов, и при температуре 500...510 °С начинается восстановление оксидов железа.
Разложение компонентов шихты происходит в зависимости от ее состава. Если в доменную печь подается офлюсованный агломерат, то эти процессы протекают при агломерации и в доменной печи почти не идут. При работе на шихте, содержащей флюсы и часть сырой руды, в верхней части доменной печи разрушаются гидраты оксидов железа и алюминия. Известняк флюса диссоциирует по реакции СаСО3
= СаО + СО2
.
В результате взаимодействия оксидов железа с оксидом углерода и твердым углеродом кокса, а также с водородом происходит восстановление железа. Восстановление газами называют косвенным, а восстановление твердым углеродом - прямым. Реакции косвенного восстановления - экзотермические (сопровождаются выделением теплоты), они происходят главным образом в верхних горизонтах печи. Реакции прямого восстановления - эндотермические (сопровождаются поглощением теплоты), они протекают в нижней части доменной печи, где температура более высокая.
Восстановление железа из руды в доменной печи происходит по мере продвижения шихты вниз по шахте печи и повышения температуры в несколько стадий - от высшего оксида к низшему:
Fe2
O3
- > Fe3
O4
- > FeO - > Fe.
Восстановление железа заканчивается при 1100...1200 °С. В доменной печи железо восстанавливается почти полностью. Потери со шлаком составляют не более 1%.
Науглероживание железа.
Восстановление железа начинается в верхней части шахты доменной печи при 500...570 °С и заканчивается в распаре при 1100...1200 °С. При этих температурах восстановленное железо с Тпл
= 1539 °С находится в твердом состоянии или в виде губчатой массы. Однако уже в шахте доменной печи наряду с восстановлением железа происходит и его науглероживание при взаимодействии с оксидом углерода, коксом, сажистым углеродом. Это приводит к образованию жидкого расплава, который каплями начинает стекать в горн.
Эти капли, протекая по кускам кокса, насыщаются углеродом (4% и более), марганцем, кремнием, фосфором, которые при температуре 1000...1200 °С восстанавливаются из руды, а также серой, содержащейся в коксе.
Марганец
в виде оксидов в доменную печь вносится железной, марганцевой рудами или агломератом и восстанавливается в шахте по реакции, аналогичной восстановлению оксидов железа: МnО2
- > Мn2
О3
- > МnО3
- > МnО. Оксид марганца (МnО) восстанавливается только твердым углеродом с образованием карбида марганца (Мn3
С) при температуре не ниже 1100 °С. Карбид марганца растворяется в железе, повышая содержание марганца и углерода в чугуне. Другая часть МnО входит в состав шлака.
Кремний,
содержащийся в руде в виде SiO2
, также частично восстанавливается твердым углеродом и растворяется в железе. Другая часть SiO2
переходит в шлак. Кремний восстанавливается при температурах не ниже 1450 °С.
Фосфор
содержится в руде в виде соединений (FeO3
) *Р2
О5
и (СаОз) *Р2
О5
. При температурах выше 1000 °С фосфат железа восстанавливается оксидом углерода и твердым углеродом с образованием фосфида железа. При температурах выше 1300 °С фосфор восстанавливается из фосфата кальция. Фосфор и фосфид железа Fe3
P полностью растворяются в железе.
Сера
присутствует в коксе и руде в виде органической серы и соединений FeS2
, FeS, CaSO4
. Сера летуча, и поэтому часть ее удаляется с газом при нагреве шихты в печи, а часть в виде серы и FeS растворяется в чугуне. Вследствие реакции:
FeS + СаО => CaS + FeO;
часть серы в виде CaS удаляется в шлак. Фосфор и сера в чугуне являются вредными примесями.
Таким образом, в результате процесса восстановления оксидов железа, части оксидов марганца и кремния, фосфатов и сернистых соединений, растворения в железе С, Mn, Si, P, S в доменной печи образуется чугун.
Образование шлака.
Шлакообразование активно происходит в распаре после окончания процессов восстановления железа путем сплавления флюсов, добавляемых в доменную печь для обеспечения достаточной жидкотекучести при температуре 1400...1450 °С, оксидов пустой породы и золы кокса. Основные составляющие доменного шлака: оксиды кремния (30...45%), оксиды кальция (40...50%), оксид алюминия (10...25%) и другие компоненты. Шлак стекает в горн и скапливается на поверхности жидкого чугуна благодаря меньшей плотности.
Чугун выпускают из печи каждые 3...4 ч, а шлак - через 1...1,5 ч. Чугун выпускают через чугунную летку 16
- отверстие в кладке, расположенное несколько выше лещади, а шлак - через шлаковую летку 17.
Чугунную летку открывают бурильной машиной, после выпуска чугуна ее закрывают огнеупорной массой. Чугун и шлак сливают в чугуновозные ковши и шлаковозные чаши. Чугун транспортируют в кислородно-конвертерные или мартеновские цехи для передела в сталь. Чугун, не используемый в жидком виде, разливают в изложницы разливочной машины, где он затвердевает в виде чушек-слитков массой 45 кг.
Азот и его соединения
- развивается токсический отек легких "синего" или "серого" типа. Сразу после вдыхании появляется небольшой быстро проходящий кашель, отмечаются першение в горле, боли за грудиной, обусловленные раздражением слизистой оболочки дыхательных путей.
Окись углерода
- хроническая интоксикация характеризуется расстройствами функции центральной нервной системы. Могут отмечаться боли в области сердца, повышение артериального давления.
Пыль
- это твердые частицы, находящиеся во взвешенном состоянии в воздухе. Средний размер этих частиц составляет 11-5 1 мкм. В атмосферу Земли ежегодно поступает около 11 куб. км пылевидных частиц искусственного происхождения. Большое количество пылевых частиц образуется также в ходе производственной деятельности людей. Пыль обладает раздражающим, аллергенным, токсигенным и фиброгенным действием. У рабочих металлургического производства частые жалобы на насморк, чихание, кашель, сухость в горле, головную боль. Аллергические заболевания дыхательных путей встречаются чаще у рабочих с большим стажем (в среднем после 8 лет работы).
Наименование |
Предельно допустимая концентрация максимальная разовая мг/м3
|
Предельно допустимая
концентрация средне
суточная мг/м3
|
Класс
опасности
|
Окислы азота |
0,400 |
0,060 |
3 |
Окись углерода |
5,000 |
3,000 |
4 |
Пыль коксовая и
агломерационная
|
10,000 |
7,500 |
4 |
Сернистый ангидрид |
0,500 |
0,050 |
3 |
Углеводороды |
1,000 |
- |
4 |
Таблица фактического состояния производственной среды.
Фактор условий труда |
Последняя цифра зачетной книжки |
Т |
0 |
Санитарно - гигиенические факторы условий труда |
Превышения ПДК |
1. Вредные химические вещества |
1 - й класс опасности |
1,9 |
1,0 |
2 - й класс опасности |
2,6 |
1,0 |
3, 4 - й класс опасности |
4,2 |
1,0 |
2. Пыль в воздухе рабочей зоны |
3,1 |
1,0 |
Превышения ПДУ |
3. Вибрация, дБ |
2,5 |
0,8 |
4. Шум, дБА |
7,0 |
0,8 |
5. Инфракрасное излучение, Вт/ м2 (
тепловое излучение) |
200 |
1,0 |
6. Неионизирующее излучение радио: ВЧ (высокочастотное), Вт/м2
|
Выше ПДУ |
1,0 |
УВЧ (ультравысокочастотное), Вт/м2
|
Выше ПДУ |
1,0 |
СВЧ (сверхвысокочастотное), мкВт/см2
|
Выше ПДУ |
1,0 |
7. Температура воздуха (эффективная эквивалентная) на рабочем месте в помещении, С, выше максимальных допустимых величин в теплый период или ниже минимально допустимых величин в холодный период года. |
5 |
1 |
Тяжесть ручного физического труда (по методике НИИ труда Госкомтруда СССР) |
8. Физическая перегрузка |
8.1 Статистическая нагрузка за смену при удержании груза, кгс: |
одной рукой |
5,5*104
|
0,6 |
двумя руками |
1,0*104
|
0,6 |
С участием мышц корпуса и ног |
1,4*104
|
0,6 |
8.2 Динамическая нагрузка за смену, кгм: |
При общей нагрузке на мышцы рук, ног, корпуса |
1,1*105
|
0,6 |
При региональной нагрузке на мышцы плечевого пояса |
5*104
|
0,6 |
Карта условий труда.
Факторы условий труда |
1 балл |
2 балла |
3 балла |
1 |
2 |
3 |
4 |
Превышение ПДК |
1. Вредные химические вещества |
3, 4 - й класс опасности |
До 6 раз |
2. Пыль в воздухе рабочей зоны |
До 5 раз |
Превышения ПДУ |
3. Вибрация, дБ |
До 3 раз |
4. Шум, дБА |
До 10 раз |
5. Инфракрасное излучение, Вт/ м2 (
тепловое излучение) |
141-350 |
7. Температура воздуха (эффективная эквивалентная)
на рабочем месте в помещении, С, выше максимальных
допустимых величин в теплый период или ниже минимально
допустимых величин в холодный период года.
|
До 8 |
Тяжесть ручного физического труда (по методике НИИ труда Госкомтруда СССР) |
8. Физическая перегрузка |
8.1 Статистическая нагрузка за смену при удержании груза, кгс: |
одной рукой |
44000-97000 |
двумя руками |
97000 - 208000 |
С участием мышц корпуса и ног |
131000-260000 |
8.2 Динамическая нагрузка за смену, кгм: |
При общей нагрузке на мышцы рук, ног, корпуса |
44000-97000 |
При региональной нагрузке на мышцы плечевого пояса |
Более 85.000 |
Баллы, установленные по степеням вредности факторов тяжести работ, корректируются по формуле: X = Xст*Т, где Xст - степень вредности фактора, определённая по критериальной таблице, баллы. Т = (Тфакт/ Тсмены) - отношение фактического времени действия фактора (Тфакт) к продолжительности смены (Тсмены), определяемое из таблицы задания параметров.
Карта условий труда на рабочем месте № 1
Предприятие: ОАО "Амурсталь".
Выплавка чугуна и стали. Цех: 23.
Участок: 2. Профессия: Металлург.
Количество аналогичных рабочих мест: 19.
Численность рабочих: 97.
Факторы производственной среды |
Норматив ПДК, ПДУ |
Фактическое состояние факторов |
Xст, балл |
Т |
X, балл |
1. Вредные химические
вещества, мг/м3
:
|
Окислы азота |
0,06 |
0,252 |
2 |
1 |
2 |
Окись углерода |
3,0 |
12,6 |
2 |
1 |
Сернистый ангидрид |
0,05 |
0,21 |
2 |
1 |
Углеводороды |
1 |
4,2 |
2 |
1 |
2. Пыль, мг/м3
|
7,5 |
23,25 |
2 |
1 |
2 |
3. Вибрация, дБ |
96 |
98,5 |
1 |
0,8 |
0,8 |
4. Шум, дБА |
85 |
92 |
1 |
0,8 |
0,8 |
5. Инфракрасное излучение, Вт/м2
|
200 |
1 |
1 |
1 |
6. Температура воздуха
на рабочем месте
(в помещении), С
|
24 - 28 |
29 - 33 |
2 |
1 |
2 |
7. Тяжесть труда, кгс |
90 000 |
140 000 |
1,2 |
0,6 |
0,72 |
Сумма значений факторов производственной среды (Х), балл: 10,32
Размер доплаты за условия труда, %: 24%
Подпись ответственного за заполнение карты:
Подпись начальника цеха (участка):
Дата заполнения: 16.12.2007 г.
Колошниковые газы, имеющие высокую теплоту сгорания, используют в качестве топлива в самих же доменных печах, в коксовых печах, в нагревателях, в котельных и т.д.
Чтобы минимизировать проблемы, связанные с эксплуатацией сжигающих устройств, в повседневной практике используют высокоэффективную газовую очистку.
Более старые печи обычно работают при давлениях, изменяющихся от 0,025 до 0,05 МПа, а более современные печи могут работать при давлениях до 0,3 МПа. В печах, в которых используют невысокие давления, чаще применяют мокрые электрофильтры, за которыми следует скруббер Вентури, чтобы можно было получить желаемую чистоту газа. При использовании скруббера Вентури можно достичь содержания аэрозолей на выходе до 5 мг/м3
при перепаде давлений, характерных для печей с высоким давлением.
Основная трудность, которая связана с отсосом аэрозолей, возникающих в процессе плавки металла, состоит в большой длине литникового хода, над которым и образуются выбросы плавильного производства; особенно это касается печей большой емкости. В современных печах часто используют наклонные литниковые ходы, что позволяет сократить его длину вдвое, при этом сокращается и площадь, с которой происходит испарение. Современная система захвата аэрозолей показана на рисунке.
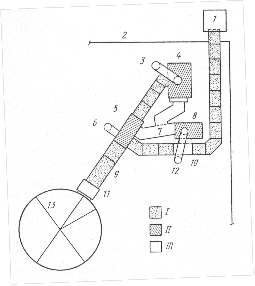
Схема крытого литникового хода и мест размещения вытяжных устройств в литейном цехе у доменной печи, где расположена система улавливания дыма: 1 - шлаковая траншея; 2 -
стена литейного цеха; 3 - соединение с трубопроводом, расположенным под полом; 4 - вытяжка над наклонным литниковым ходом; 5 - вытяжка над ванной с расплавленным металлом; 6 - соединение с трубопроводом, расположенным под полом; 7 - открытый запасной литниковый ход; 8 - вытяжка над черпаком для отбора шлака; 9 - сменяемое покрытие; 10 - шлаковый порог; 11 - вытяжной колпак над леткой; 12 - соединение с трубопроводом, расположенным под полом; 13 - летка чугуна; I - укрытые площади на уровне пола; II - защитный покров с вытяжкой отработанных газов; III - открытые площади она состоит из воздухоочистительных устройств над леткой, над отсекателем, над подпором и над наклонным литниковым ходом с трубопроводом, установленным под полом, чтобы не мешать передвижениям крана. Хорошо герметизированное покрытие над литниковым ходом мешает подводу кислорода и ограничивает образование аэрозольных загрязнений из продуктов испарения. Для ограничения поступления кислорода можно обдувать поверхность металла паром или горячими газами. Проектная производительность прокачки воздуха (тыс. м3
/ч) вытяжных устройств улавливания отработанных газов (укрытие литникового хода в литейном цехе доменного производства) приведена ниже:
Вытяжка над леткой 250
Укрытие литникового хода от летки 190
Шлакоотделитель 184
Наклонный литниковый ход чугуна 310
На предприятии "Кобе Стил" в Японии на крыше литейного цеха установили мокрый электрофильтр. Продукты испарения через электрофильтр выносит естественная тяга. Это позволяет отказаться от применения газоходов и вентиляторов.
Поскольку температура газа, который улавливается местными вытяжными устройствами, как правило, не превышает 90°, вполне подходящими устройствами для очистки газов от загрязнений могут быть рукавные фильтры и электрофильтры.
Как уже упоминалось, использование воды для охлаждения шлака приводит в результате к выбросам H2
S. Может быть достигнуто 50% -ное сокращение выброса H2
S, если в воду, предназначенную для охлаждения, добавить 100 млн-1
КМпО4
. Было получено 88% -ное сокращение выброса H2
S после трехдневного охлаждения на воздухе с последующим добавлением в охлаждающую воду КМп04
концентрацией 100 млн. - 1
1. ОБЩИЕ ТРЕБОВАНИЯ БЕЗОПАСНОСТИ.
1.1 К самостоятельному выполнению работ допускаются лица не моложе 18 лет, прошедшие медицинское освидетельствование, специальное обучение, аттестацию с выдачей удостоверения.
1.2 Повторная проверка знаний правил охраны труда и пожарной безопасности проводится один раз в год. Проверка знаний технический эксплуатации - один раз в два года.
1.3 Хорошо изучите и строго соблюдайте требования охраны труда при выполнении порученной работы - этим предохраните себя и окружающих от несчастного случая.
1.4 Строго выполняйте правила внутреннего распорядка, установленного на предприятии:
приступайте к порученной работе при условии, что безопасные способы выполнения её вам известны. В сомнительных случаях обращайтесь к мастеру за разъяснениями;
содержите свое рабочее место, оборудование, инструмент, приспособления, спец. одежду в чистом и исправном состоянии:
соблюдайте правила жетонной системы при получении и хранении аппаратуры, инструмента, приспособлений;
курите только в отведенном для этого месте;
1.5 Рабочие, участвующие в выплавке чугуна, обеспечиваются:
хлопчатобумажными костюмами с огнестойкой пропиткой;
кожаными ботинками по ГОСТ 12.4 032-77;
брезентовыми рукавицами по ГОСТ 535-75;
защитными касками по ГОСТ 12.4 087-84;
защитными очками типа ЗН8-72 по ГОСТ 12.4 013-97;
респираторами ЩБ-1 типа "Лепесток" по ГОСТ 12.4 028-76 или шланговыми дыхательными аппаратами типа РПГ-67 по ГОСТ 12.4 004-74.
Нормы выдачи спец. одежды должны соответствовать "Отраслевым нормам бесплатной выдачи спец. одежды, спец. обуви и других средств индивидуальной защиты рабочим и служащим".
1.6 В случае получения травмы, даже незначительной, прекратите работу, немедленно сообщите о случившемся мастеру и обратитесь к врачу.
1.7 Работайте чистыми, без следов масла руками и в чистой спец. одежде.
1.8 Не применяйте кислород для очистки одежды от пыли и грязи, так как кислород способствует интенсивному возгоранию ее при попадании искр или наличия следов масла.
1.9 Соблюдайте чистоту и порядок на своем рабочем месте и в шкафу для инструмента.
1.12. За нарушение требований настоящей инструкции виновные привлекаются к ответственности в установленном законом порядке.
2. ПРАВИЛА БЕЗОПАСНОСТИ ПЕРЕД НАЧАЛОМ РАБОТЫ
2.1 Получив от мастера производственное задание и свой жетон, возьмите по нему из кладовой хранения закрепленную за вами исправную аппаратуру, а жетон отдайте наладчику.
2.2 Проверьте исправность и доброкачественность спец. одежды, предохранительных средств (очки, респиратор, страховочный пояс и др.).
2.3 Приведите в порядок свою спец. одежду: куртку и брюки наденьте на выпуск, карманы закройте клапанами, ботинки зашнуруйте, застегните или подвяжите обшлага рукавов, при потенциальной опасности травмирования головы наденьте защитную каску.
2.4 Осмотрите свое рабочее место, освободите от лишних, мешающих работе предметов и легковоспламеняющихся и токсичных материалов.
2.5 Проверьте наличие противопожарных средств: огнетушителя, асбестового полотна, ведра с водой, пожарного ящика, рукава с рожком.
2.6 Применяйте резиновые рукава по ГОСТ 9356-75 класс 1 - для подачи горючих газов; класс 2 - для подачи жидкого топлива; класс 3 - для подачи кислорода. Запрещается рукава для горючих газов использовать для подачи кислорода.
2.7 Убедитесь в исправности вентиляции и интенсивности воздухообмена.
2.8 Проверьте готовность конструкции к выполнению работ, уберите мешающие работе ненужные предметы, освободите проходы, убедитесь в безопасности проведения работ.
2.9 В работе необходимо руководствоваться "Правилами пожарной безопасности ППБ 01-03" от 30.06.2003г.
3. ПРАВИЛА БЕЗОПАСНОСТИ ВО ВРЕМЯ РАБОТЫ.
3.1 Работы выполняйте в строгом соответствии с требованиями технологической документацией.
3.2 Выполняйте работу в спец. одежде с применением индивидуальных средств защиты органов дыхания и слуха; применяйте исправный инструмент и приспособления.
3.3 Баллоны с кислородом перемещайте на специальных передвижных тележках, носилках или перевозите на рессорных транспортных средствах, применяя в качестве смягчающих прокладок резиновые или веревочные кольца толщиной нее 25 мм по два на каждый баллон.
3.4 При многорядной перевозке баллонов применяйте деревянные прокладки между рядами, при этом высота перевозимых баллонов не должна превышать высоты кузова транспортного средства.
3.5 В исключительных случаях, при совместной перевозке баллонов с кислородом, выполняйте следующие требования:
одновременно перевозите суммарно не более 10 баллонов, уложенных в 1 ряд;
очистите баллоны от следов масел и грязи;
проверьте герметичность вентилей, наличие и надежность закрепления предохранительных колпаков;
укладывайте баллоны поперек кузова транспортного средства предохранительными колпаками в одну сторону и при необходимости раскрепите их.
3.6. Не допускайте при погрузке и разгрузке баллонов их сбрасывания и ударов друг о друга, а также разгрузку вниз вентилями.
3.7. Во избежание случайных падений баллоны на рабочем месте закрепите в специальной стойке или на тележке.
3.8. Исключите любую возможность попадания жиров и масел на кислородную аппаратуру.
3.9. При работе возле печи закрывайте баллоны экраном из асботкани или брезента, не допускайте нагрева выше 35°С.
3.10. Устанавливайте баллоны не ближе 15 м от печей и других источников тепла с открытым огнем.
3.11 При эксплуатации баллонов с кислородом:
следите за плотностью закрытия вентилей;
перед использованием баллона продуйте вентиль, плавно приоткрывая его на короткое время (1-2 сек), при этом находитесь в стороне от печи;
расходуйте кислород до остаточного давления - 0,5 кгс/см2
.
3.12. Колпаки с баллонов снимайте только специальным ключом. Не применяйте различные средства, могущие вызвать искрообразование.
3.13. При понижении уровня воды в барабанах-сепараторах ниже допустимого подпитка их запрещается.
3.14. Состояние систем охлаждения доменных печей и вспомогательных устройств должно ежесменно проверяться.
3.15. Пользоваться открытым огнем при ремонте и осмотре барабанов-сепараторов без предварительного анализа газов в них запрещается.
3.16. При прожигании летки кислородом рабочие должны пользоваться индивидуальными защитными средствами.
3.17. Прожигать летки при длине кислородной трубки менее 4 м запрещается.
3.18. Заделка летки производится с помощью электропушки.
4. ТРЕБОВАНИЯ БЕЗОПАСНОСТИ В АВАРИЙНЫХ СИТУАЦИЯХ.
4.1 При наличии в системе течи, угрожающей жизни обслуживающего персонала, необходимо немедленно перевести систему испарительного охлаждения на охлаждение технической водой.
4.2 При аварийном выходе из строя водоводов питательной воды необходимо:
снять давление системы испарительного охлаждения шиберов воздухонагревателей и печей;
закрыть задвижки на двух вводах питательной воды в галереи;
открыть задвижки от водовода технической воды;
закрыть дренажные вентили.
4.2 При небольших по площади ожогах первой и второй степени наложите осторожно на обожженный участок стерильную повязку. Если на человеке загорелась одежда, набросьте быстро на него пальто, куртку, любую плотную ткань или сбейте пламя водой. При необходимости, прилипшую к обожженному участку тела одежду или обувь не срывайте, а разрежьте ножницами и осторожно снимите, не повреждая кожу, а затем наложите стерильную повязку и отправьте пострадавшего в лечебное учреждение. При тяжелых и обширных ожогах заверните пострадавшего в чистую простынь или ткань, не раздевая его, укройте потеплее, напоите теплым чаем и создайте покой до прибытия врача.
5. ТРЕБОВАНИЯ БЕЗОПАСНОСТИ ПО ОКОНЧАНИИ РАБОТЫ.
5.1. Приведите в порядок рабочее место, уберите с оборудования инструмент, приспособление в отведенное для них место.
5.2. Уходя с рабочего места, убедитесь в отсутствии.
5.3. При сдаче смены сообщите мастеру и своему сменщику о замеченных вами неполадках оборудования, аппаратуры, средств вентиляции и освещения.
5.4. Соблюдайте правила личной гигиены: вымойте руки теплой водой с мылом, при необходимости примите душ. Не мойте руки и другие части тела растворителями (бензином, ацетоном и т.д.)
5.5. Об уходе домой сообщите мастеру.
1. "Технология конструкционных материалов" А.М. Дальский / Москва "Машиностроение" 2004 г.;
2. Справочник "Промышленное загрязнение окружающей среды", том 2;
3. "Предприятие - источник загрязнения окружающей среды" / Методические указания к расчётному заданию по курсу "Промышленная экология" курса "Экология".
|