Реферат
Выполнил студент
Московский государственный институт стали и сплавов
Москва 2007
Введение
Серебро является одним из тех металлов, которые привлекли внимание человека еще в древние времена. История серебра тесно связана с алхимией, поскольку уже в те времена был разработан метод купелирования серебра.
Серебро является редким металлом, его содержание в земной коре равно
10-15 вес.%. В природе серебро встречается как самородное, так и в виде соединений — сульфидов, селенатов, теллуратов или галогенидов в различных минералах.
Серебро встречается также в метеоритах и содержится в морской воде.
В течение последних 15 лет мировое промышленное потребление серебра значительно превышает его добычу, улучшить показатели которой довольно сложно, поскольку три четверти добываемого серебра получается как побочный продукт при разработке месторождений других металлов. Это обязывает нас быть предельно экономными в расходовании металлов и использовать все возможности для максимальной реализации ресурсов этих металлов. В настоящее время потребление золота и серебра не перекрывается их добычей, поэтому возрастает роль вторичной металлургии платино-, золото- и серебросодержащих отходов.
Спецификой вторичной металлургии благородных металлов является многообразие физических форм и химических составов отходов, содержащих благородные металлы.
В большинстве случаев отходы изделий из благородных металлов содержат в себе относительно больше благородных металлов, чем руды, из которых добываются первичные золото, серебро, платина. Поэтому такие отходы выгоднее перерабатывать, чем руды. Но даже при переработке отходов с низким содержанием благородных металлов сбор и использование ценных компонентов из них все же рентабельны вследствие их высокой стоимости.
Переработка вторичного сырья, содержащего
серебро.
Характеристика вторичного серебросодержащего сырья.
Основными поставщиками серебросодержащего сырья являются фото- и кинопромышленность, химическая, электротехническая и радиопромышленности, зеркальное, часовое и ювелирное производства, лечебные учреждения.
Серебросодержащие отходы фото- и кинопромышленности образуются в процессе изготовления, обработки и порчи светочувствительных материалов или износа кинолент и фотоотпечатков.
Забиваем Сайты В ТОП КУВАЛДОЙ - Уникальные возможности от SeoHammer
Каждая ссылка анализируется по трем пакетам оценки: SEO, Трафик и SMM.
SeoHammer делает продвижение сайта прозрачным и простым занятием.
Ссылки, вечные ссылки, статьи, упоминания, пресс-релизы - используйте по максимуму потенциал SeoHammer для продвижения вашего сайта.
Что умеет делать SeoHammer
— Продвижение в один клик, интеллектуальный подбор запросов, покупка самых лучших ссылок с высокой степенью качества у лучших бирж ссылок.
— Регулярная проверка качества ссылок по более чем 100 показателям и ежедневный пересчет показателей качества проекта.
— Все известные форматы ссылок: арендные ссылки, вечные ссылки, публикации (упоминания, мнения, отзывы, статьи, пресс-релизы).
— SeoHammer покажет, где рост или падение, а также запросы, на которые нужно обратить внимание.
SeoHammer еще предоставляет технологию Буст, она ускоряет продвижение в десятки раз,
а первые результаты появляются уже в течение первых 7 дней.
Зарегистрироваться и Начать продвижение
На переработку поступают следующие основные виды сырья, содержащие серебро, %: серебро бромистое 35-66; серебро сернистое 45-65; зола кинопромышленности 45-52; зола фотобумаги 1,2-7; зола фотоотпечатков < 0,5.
Отходы химической промышленности поступают в виде отработанных контактных масс (20-80% Ag); отработанных катализаторов (более 80% Ag); шламов (от 60 до 80% Ag); лома серебряной аппаратуры (20-25% Ag).
Образование серебросодержащих отходов в зеркальной промышленности происходит в процессе серебрения зеркал, елочных украшений и т. д. В зеркальном производстве образуются следующие отходы, в которых присутствует Ag, %: зеркальный бой 0,05-0,2; бой елочных украшений 0,2-0,5; лом серебрильных кувшинов 10-25; сукно серебрильных столов (в золе) 40-50; шлам серебрильных столов 40-60; сернистое серебро, получаемое при осаждении серебра из зеркальных серебрильных растворов 40-60.
В следующих отходах полиграфической промышленности также имеется серебро, %: сернистое серебро 45-64; зола фотобумаги и фотоотпечатков 0,4-4; зола бумажных фильтров 30-60; хлористое серебро - более 50; осадки цементного серебра - более 50. Отходами ювелирных мастерских и заводов, обрабатывающих благородные металлы, являются соры. Их подразделяют на группе условиям образования и количеству присутствующего серебра, %: при плавке благородных металлов 0,5-7 0- при механической обработке 0,05-3,0; при химической и электрохимической обработке серебра 0,05-10.
Часовое производство направляет на переработку следующие виды сырья, содержащего Ag, %: серебряные припои - от 15 до 99; серебряные контакты 20-80; опилки и стружку - от 10 до 70 и др.
От лечебных учреждений на извлечение серебра поступают, %: зола рентгенопленки и фотоотпечатков - от 0,5 до 50; сернистое серебро 45-65.
Большое количество серебросодержащего сырья (до 30-40% Ag) перерабатывается в виде отходов электронной и электротехнической отраслей промышленности: вышедшие из строя серебряно-цинковые и серебряно-кадмиевые аккумуляторы (от 30 до 60%); сплавы-контакты, серебряные припои (от 5 до 99%); металлокерамические композиции 25-50.
Все отходы благородных металлов можно разделить на два вида сырья:
1) металлическое — серебросодержащие соры и золы, оксидные соединения серебра, серебро электролизное, серебросодержащие бракованные изделия и детали, бракованные полуфабрикаты в виде слитков, проката, проволоки, заготовок, порошков или их отходы; крупные серебряно-цинковые аккумуляторы, бракованные или вышедшие из строя; малогабаритные серебряно-цинковые аккумуляторы и др.;
Сервис онлайн-записи на собственном Telegram-боте
Попробуйте сервис онлайн-записи VisitTime на основе вашего собственного Telegram-бота:
— Разгрузит мастера, специалиста или компанию;
— Позволит гибко управлять расписанием и загрузкой;
— Разошлет оповещения о новых услугах или акциях;
— Позволит принять оплату на карту/кошелек/счет;
— Позволит записываться на групповые и персональные посещения;
— Поможет получить от клиента отзывы о визите к вам;
— Включает в себя сервис чаевых.
Для новых пользователей первый месяц бесплатно.
Зарегистрироваться в сервисе
2) неметаллическое - бромистое, сернистое, хлористое серебро; шламы фиксажных растворов и шламы зеркального производства; серебросодержащие соры, шлифы, зола кино-, фото- и рентгенопленки; катализаторы серебряно-пемзовые и др.; серебросодержащие шлаки.
Кроме перечисленных отходов на переработку поступают другие виды сырья, резко различающиеся химическими и физическими свойствами.
Извлечение серебра из электронного лома.
Особенности и состав электронного лома.
В настоящее время для производства вторичного металла все больше используется комплексный металлолом. В связи со сложностью переработки многокомпонентного лома появилась необходимость разработки новых технологий, позволяющих наряду с основным металлом извлекать и другие металлы, содержащиеся в ломе (Al, Fe, Сu, драгоценные металлы, Zn, Mg, нержавеющая сталь и т.д.). Извлечение и обогащение попутных металлов оказались экономически рентабельными - в результате можно получать более чистые металлы и дополнительные доходы. К трудноперерабатываемому лому относятся самолеты и их двигатели, электронно-вычислительная аппаратура, бытовая электроаппаратура, различные изделия электротехнической, электронной, автомобильной и машиностроительной промышленности.
Первичная обработка комплексного лома обычно заключается в его дроблении, обеспечивающем разделение металлов и неметаллических компонентов. Если в составе лома имеются крупногабаритные предметы, необходимо предусмотреть эффективное оборудование для их разрезания на куски, поддающиеся дроблению. Для дробления комплексного лома часто необходимо иметь не одну, а несколько дробилок различных типов, в зависимости от характера обрабатываемого лома.
Как правило, оборудование для переработки металлолома разработано на основе обогатительной техники. Однако при разработке эффективной техники для переработки лома необходимо обладать знаниями о специфических свойствах лома, а также возможностью постоянного совершенствования оборудования на основе опыта его эксплуатации.
Технология комплексной переработки такого лома обычно включает в себя:
- демонтаж оборудования и предварительную сортировку лома;
- измельчение и сепарацию лома;
- получение чистых металлов и других продуктов, товаров народного потребления,
а также использование полученного вторичного сырья в качестве добавки к
первичному сырью.
Лом и отходы производства и потребления продукции радиоэлектронных и электротехнических отраслей промышленности - богатый источник цветных и благородных металлов.
Особая ценность электронного и электротехнического лома состоит в том, что он является источником благородных металлов. Об объемах использования благородных металлов в электронике и электротехнике можно судить по следующим цифрам. во второй половине 80-х годов в капиталистических странах в электронике и электротехнике использовалось около 10% золота (до 1200-1400 г /т), платины - 7% (до 190-200 г/т), палладия и других платиновдов - около 50%, а также значительное количество серебра. Одна из основных целей, преследуемых при переработке многокомпонентного лома, - извлечение из него меди олова свинца, цинка, никеля и благородных металлов.
Важным фактором, свидетельствующим о целесообразности переработки сложных отходов, следует считать их вредное экологическое воздействие на окружающую среду.
Сжигание отходов электронной и электротехнической аппаратуры приводит к загрязнению атмосферы дымовыми газами и вредными химическими веществами, содержащими хлористый и фтористый водород, сернистый газ, соединения свинца и цинка, фенол, этилхлоргидрат, толуол, которые являются токсичными веществами 2-3 класса опасности.
Технологии переработки электронного оборудования с комплексным извлечением всех компонентов.
Перспективными технологическими схемами переработки многокомпонентного лома являются такие технологии, в которых осуществляется первичная обработка лома механическими методами с целью получения концентратов составляющих компонентов этого лома (черные, цветные, благородные металлы, пластмассы, дерево, стекло). Полученные концентраты должны подвергаться электролизу с селективным выделением благородных металлов, свинца и олова в шлам, меди - на катоде, а цинка, никеля и железа в раствор. Дальнейшая переработка шлама позволяет получать находящиеся в нем металлы в виде твердых продуктов. Отработанный электролит утилизируется путем его цементации с получением цементного осадка с высоким содержанием никеля, железа, цинкового купороса, пригодного для переработки, и др.
Основные направления переработки электронного лома.
Ведущими отечественными организациями в области переработке электронного лома являются Минсвязи РФ, НИИГиналмаззолото и некоторые другие.
В Минсвязи разрабатывается технология комплексной переработки лома радиоэлектронной аппаратуры, предусматривающая:
- механические методы измельчения лома и сепарации дробленого лома на компоненты;
- получение вторичного оловянно-свинцового припоя путем нагрева и последующего
центрифугирования лома печатных плат;
- получение чистых металлов электролитическими методами;
- переработку стекла, полимерных и деревянных материалов и производство из них
товаров народного потребления.
Технология, разрабатываемая в НИИГиналмаззолото, ориентирована на получение в основном благородных металлов из элементов и узлов электронного лома, их содержащих. Задач комплексной малоотходной переработки не ставится.
Другой особенностью технологии является широкое использование методов сепарации в жидких средах и некоторых других, характерных для обогащения руд цветных металлов.
ВНИИПвторцветмет специализируется на технологиях переработки отдельных типов лома: печатных плат, электронно-вакуумных приборов, блоков ПТК в телевизорах и др.
По плотности материал платы с большой степенью достоверности делится на две фракции: смесь металлов и неметаллов (+1,25 мм) и неметаллы (-1,25 мм). Такое разделение может быть осуществлено на грохоте. В свою очередь из фракции неметаллов при дополнительной сепарации на гравитационном сепараторе может быть выделена металлическая фракция и тем самым достигнута высокая степень концентрации получаемых материалов.
Часть (80,26%) оставшегося материала +1,25 мм может быть подвергнута повторному дроблению до крупности -1,25 мм с последующим выделением из него металлов и неметаллов.
На извлечение серебра из электронного лома существует достаточно много патентов, некоторые из них с технологией производства описаны ниже.
Способ извлечения благородных металлов (патент Российской Федерации RU2276196). Изобретение может быть использовано на предприятиях по получению цветных, благородных металлов и их сплавов, получаемых при утилизации электронных приборов и деталей. Способ включает дезинтеграцию радиоэлектронного лома, виброобработку с отделением тяжелой фракции, содержащей благородные металлы, сепарацию и выделение металлов, при этом полученный радиоэлектронный лом сортируют и отделяют металлические детали, оставшуюся часть лома подвергают виброобработке с отделением тяжелой фракции и сепарации, тяжелую фракцию после сепарации смешивают с предварительно отделенными металлическими деталями и подвергают смесь окислительному плавлению при подаче воздушного дутья в пределах 0,15-0,25 нм3 на 1 кг смеси, после чего проводят электрорафинирование полученного сплава в сульфатном растворе меди и выделяют из образовавшегося шлама благородные металлы. Благодаря способу обеспечивается высокое извлечение благородных металлов, %: золото - 98,2; серебро - 96,9; палладий - 98,2; платина - 98,5.
Описание изобретения: техническим результатом предлагаемого способа является повышение извлечения благородных металлов. Технический результат достигается тем, что в способе извлечения благородных металлов из узлов и конструкций электронной промышленности при утилизации, включающем дезинтеграцию, вибрацию, сепарацию и выделение благородных металлов, согласно изобретению узлы и конструкции разделяют на элементы из металла, элементы на пластиковой основе и элементы на керамической основе, дезинтеграции, вибрации и сепарации подвергают элементы на пластиковой и керамической основе, - каждую отдельно, с отделением тяжелой фракции, содержащей благородные металлы; смесь тяжелых фракций и элементов из металла подвергают окислительному плавлению при подаче воздушного дутья в пределах 0,15-0,25 нм3 на 1 кг смеси и проводят электрорафинирование полученного сплава в сульфатном растворе меди, а выделение благородных металлов проводят из образовавшегося при электрорафинировании шлама.
Способ поясняется чертежами на фиг.1 и 2.
По способу-прототипу (фиг.1) узлы и конструкции электронной промышленности последовательно подвергают дезинтеграции (1), вибрации (2), магнитной сепарации (3), электросепарации (4), после чего полученные концентраты поступают в вакуумно-термическую печь (5), где их подвергают испарительному разделению с улавливанием металлов в специальных конденсаторах (6, 7).
Предлагаемый способ (фиг.2) осуществляют следующим образом: узлы и конструкции электронной промышленности поступают на разборку до элементов, которые разделяют элементы из металла, элементы на пластиковой основе и элементы на керамической основе. Элементы на керамической и пластиковой основе подвергают (фиг.2) дезинтеграции, вибрации (2), магнитной сепарации (3), электрической сепарации (4), полученные тяжелые фракции смешивают в смесителе (5) с элементами металла, подвергают плавлению с подачей воздушного дутья в пределах 0,15-0,25 нм3 на 1 кг смеси в плавильной печи (6) и проводят электролиз в электрорафинировочной ванне (7) в сульфатном растворе меди с выделением из образовавшегося шлама благородных металлов.Верхний предел воздушного дутья 0,25 нм3 на 1 кг смеси объясняется тем, что увеличение параметра до 0,30 нм 3/1 кг смеси не приводит к увеличению извлечения благородных металлов. Нижний предел воздушного дутья 0,15 нм3 на 1 кг смеси приводит только к незначительному снижению благородных металлов, а снижение более чем до 0,15 нм3 на 1 кг смеси - к недопустимому снижению благородных металлов. Это может быть проиллюстрировано следующими примерами. Сравнительные опыты проводили с однотипными радиоэлектронными платами.
Благодаря предлагаемому способу обеспечивается высокое извлечение благородных металлов (в сравнении с прототипом увеличение извлечения по золоту составляет 3,2%; по серебру 1,1%; по палладию 28,1%; по платине 26,1%) при утилизации электронных деталей и конструкций, что видно из примеров и доказано экспериментально.
Формула изобретения: Способ извлечения благородных металлов из узлов и конструкций электронной промышленности при утилизации, включающий дезинтеграцию, вибрацию, сепарацию и выделение благородных металлов, отличающийся тем, что узлы и конструкции разделяют на элементы из металла, элементы на пластиковой основе и элементы на керамической основе, дезинтеграции, вибрации и сепарации подвергают элементы на пластиковой и керамической основе, каждую отдельно, с отделением тяжелой фракции, содержащей благородные металлы; смесь тяжелых фракций и элементов из металла подвергают окислительному плавлению при подаче воздушного дутья в пределах 0,15-0,25 нм3 на 1 кг смеси и проводят электрорафинирование полученного сплава в сульфатном растворе меди, а выделение благородных металлов проводят из образовавшегося при электрорафинировании шлама.
Способ электролитической регенерации серебра из серебряного покрытия на металлической основе (патент Российской Федерации RU2176290).
Изобретение может быть использовано при электролитическом извлечении серебра из серебряного скрапа электронных и электротехнических изделий. В процессе используют электролит, для анодного растворения серебра, который содержит серную кислоту с концентрацией 80,0-84,5 мас.% и сульфат серебра в количестве 15-40 г/л кислоты. Электролиз ведут при напряжении не более 1,8 В с выделением металлического серебра на катоде. Электролиз предпочтительно вести при 35-50oС c регенерацией серебра из покрытий на основе, содержащей медь, железо или алюминий. Достигаемый результат заключается в осуществлении катодного восстановления серебра из скрапа электронных и электротехнических изделий без разрушения материала их основы. При этом чистота металлического серебра, выделяемого на катоде, составляет не менее 99,9% при его извлечении 99,6-99,8%. В состав электролита входят широко используемые нетоксичные вещества.
Описание изобретения: изобретение может быть использовано при электролитическом извлечении серебра из серебряного скрапа электронных и электротехнических изделий. При регенерации серебра из серебряных покрытий на основе, содержащей медь, железо или алюминий, возникает проблема селективного извлечения серебра без разрушения основы и растворения припоя с одновременным получением высокочистого металлического серебра. При этом важное значение имеет ограничение вредного воздействия используемой технологии или ее компонентов на окружающую среду.
Техническим результатом является селективное электрохимическое извлечение серебра из скрапа, содержащего серебряные покрытия на металлической основе в присутствии припоя, с получением на катоде высокочистого металлического серебра, а также исключение из состава электролита токсичных веществ.
Технический результат достигается тем, что в способе электролитической регенерации серебра из серебряного покрытия на металлической основе, включающем анодное растворение серебра при нагревании в электролите, содержащем серную кислоту и добавку, согласно изобретению электролит содержит серную кислоту с концентрацией 80.0-84.5 мас.%, а в качестве добавки - сульфат серебра в количестве 15-40 г/л кислоты, причем электролиз ведут при напряжении не более 1.8 В с выделением серебра на катоде. Также тем, что электролиз ведут при 35-50oC, и тем, что регенерацию ведут из серебряного покрытия на основе, содержащей медь, железо или алюминий.
Использование для электролиза серной кислоты концентрацией 80.0-84.5 мас. % обеспечивает селективное анодное растворение серебряного покрытия и выделение на катоде порошка высокочистого металлического серебра. При концентрации серной кислоты выше 84.5 мас.% катодное серебро загрязняется примесью сульфида серебра, а при концентрации менее 80.0 мас.% начинается значительное анодное растворение металлической основы и припоя.
Использование сульфата серебра в составе электролита повышает его электропроводность и способствует формированию на катоде кристаллического осадка металлического серебра. При концентрации сульфата серебра менее 15 г/л кислоты на катоде образуется аморфный осадок серебра, а при концентрации более 40 г/л кислоты происходит выпадение сульфата серебра в осадок.
Осуществление электролиза при напряжении не более 1.8 В обеспечивает селективное анодное растворение серебра. При напряжении более 1.8 В происходит образование сульфида серебра на катоде, а также частичное растворение металлической основы и припоя.
Проведение электролиза при 35-50oC способствует поддержанию высокой скорости процесса. При температуре менее 35oC скорость процесса резко падает, а при температуре более 50oC начинается заметное анодное растворение припоя.
Осуществление электролиза в соответствии с вышеуказанными условиями позволяет селективно извлекать металлическое серебро из серебряных покрытий на основе, содержащей медь, железо или алюминий.
Указанные выше особенности и преимущества заявленного изобретения могут быть более наглядно пояснены нижеследующими примерами.
Формула изобретения: способ электролитической регенерации серебра из серебряного покрытия на металлической основе, включающий анодное растворение серебра при нагревании в электролите, содержащем серную кислоту и добавку, отличающийся тем, что, используют серную кислоту с концентрацией 80,0-84,5 мас.%, а в качестве добавки - сульфат серебра в количестве 15-40 г/л кислоты, причем электролиз ведут при напряжении не более 1,8 В с выделением серебра на катоде.
Способы переработки электронного лома за рубежом.
Известны четыре основных способа переработки электронного лома:
1) механический,
2) гидрометаллургический,
3) механический в сочетании с гидрометаллургической переработкой концентрата,
4) обжиг с последующей плавкой.
При этом известны технологии переработки как смешанного лома, так и его отдельных узлов (например, печатных плат) и элементов (например, полупроводниковых приборов).
На практике все фирмы, как правило, используют технологию для переработки смешанного лома. Наиболее широкую известность получили технологии и фирмы стран Западной Европы - Германии, Франции, Швеции, Швейцарии и др.
Анализ данных по технологиям зарубежных фирм показывает что рентабельность всех технологий обеспечивается за счет получения дорогостоящих чистых и благородных металлов.
Для обеспечения стабильности поступления сырья рекомендуется на одном предприятии перерабатывать смешанный промышленный и бытовой, электронный и электротехнический ломы.
Отдельные узлы и элементы радиоэлектронной и электротехнической аппаратуры содержат благородные металлы в количестве, обеспечивающем высокую рентабельность переработки этих узлов и элементов с целью извлечения благородных металлов.
Ниже представлены технологии главным образом зарубежных стран. Это объясняется тем, что отечественные технологии пока сложны и малорентабельны.
В большинстве случаев технологии получения благородных металлов сводятся к механическим методам получения чистых металлов на втором этапе. В СНГ наиболее ярким представителем такого подхода является НИИГиналмаззолото.
Разрабатываемый в Гиналмаззолото технологический процесс включает в себя механическое вскрытие, обогащение электронного лома, содержащего благородные металлы, и гидрометаллургическую переработку.
Обогащение предусматривает три степени дробления и сепарацию полученных продуктов с помощью гидроциклонов и методами флотации. Благородные металлы из обогащенного дробленого лома получают электролитическими методами.
Производительность по переработке электронного лома - до 1,5 т/ч.
Однако известны и другие методы получения благородных металлов, например плавкой обогащенного лома (технология фирмы Galika, Швейцария).
Фирма «Schneck» разработала технологию и оборудование для извлечения цветных и благородных металлов из узлов устаревших компьютеров: панелей, печатных плат, соединительных элементов и т.п.
Лом предварительно измельчают в двухвалковой дробилке и с помощью системы транспортно-погрузочных устройств подают в магнитный сепаратор для выделения железа. Затем обезжелезенный материал направляют в шнек для охлаждения жидким азотом с целью увеличения хрупкости материала и улучшения измельчения в ударно-молотковой дробилке и подают в воздушный сепаратор.
Линия рассчитана на переработку 250 кг/ч лома. Общее потребление мощности 200 кВт, расход азота 0,5-1,522 м3 на 1 кг лома.
Материал в шнековом охладителе с помощью азота охлаждается до -190°С и измельчается в молотковой дробилке до фракции +0 -3 мм, что позволяет очень точно разделить смеси на цветные металлы и пластмассу.
Данную технологию можно использовать при переработке лома кабеля с медной жилой для извлечения меди.
Технология американских фирм включает в себя двукратное измельчение лома в молотковой дробилке, воздушную сепарацию, магнитную сепарацию в слабом поле (выделение железа) и в сильном поле (выделение латуни), грохочение, сепарацию в виде вихревых токов и магнитодинамическую сепарацию. Ферромагнитные металлы выделяются с помощью сепаратора, легкая фракция - с помощью воздушной сепарации, а дальнейшая обработка немагнитной фракции с помощью вихревых токов позволяет выделить неметаллы и металлы.
Продукты передела:
8-10% от всей массы лома - легкая фракция с незначительным количеством меди и
благородных металлов;
12-25% - ферромагнитные материалы с преобладанием железа;
15-25% - концентрат меди и благородных металлов, в котором содержится золота
до 1,3 кг/т, серебра - 15,8 кг/т;
7-20% - тяжелые металлы;
1-5% - концентрат латуни;
1-5% - высокосортный концентрат алюминия.
Процесс переработки электронного скрапа на установке PRV аппаратурно состоит в следующем: молотковая дробилка - 1-я стадия дробления, воздушный классификатор типа «Bauer», магнитный сепаратор «Eriez», грохот (грохочению поддаются раздельно магнитная и немагнитная фракции), валковая дробилка «Exolon» (для измельчения надрешетного продукта немагнитной фракции), виброгрохот, промежуточный магнитный сепаратор для надрешетного продукта и электродинамический сепаратор, работающий на принципе вихревых токов.
В процессе механической переработки электронного скрапа на линии PRV получают следующие фракции: фракцию на основе черных металлов, алюминиевую смешанную металлическую фракции, концентраты с высоким и низким содержанием благородных металлов, легкую и проволочную.
Технология «Valmet» переработки различного электронного и электротехнического оборудования обычно включает три стадии:
- резку лома автоматическими пpecc-ножницами, измельчение и разделение на три
фракции (черные металлы, цветные и благородные металлы, неметаллы);
- разделение цветных и благородных металлов;
- рафинирование благородных металлов, меди, олова и свинца.
Технологическая схема механической переработки лома предусматривает отделение электронных схем и элементов от механических узлов и стальных деталей. Разборка лома осуществляется вручную с использованием пневматических и пневмоэлектрических устройств и приспособлений. Степень разборки определяется исходным сырьем и может быть более или менее полной.
Технологические операции по измельчению электронных схем в виде печатных плат и других материалов осуществляют с помощью модернизированного стандартного оборудования, используемого для нарезки и измельчения кабелей и проводов.
Разделение цветных и благородных металлов осуществляют при последующем применении гидрометаллургических методов и получении продуктов с содержанием благородных металлов > 50%.
Основные операции гидрометаллургического процесса:
- выделение методами электролиза или химического осаждения покрытий из золота
и серебра, что позволяет извлечь до 70% золота и 90% серебра;
-переработка транзисторов, проводников тока с покрытием из благородных
металлов путем выделения меди ее растворением в азотной кислоте без
растворения других металлов с последующим выделением меди из раствора.
Используемое для гидрометаллургического процесса оборудование представляет собой несколько типов химических реакторов с внутренним покрытием из пластмасс, нержавеющей или «остеклованной» стали, обеспечивающих химическую реакцию при температуре 60-80 оС.
Фирма «Inter Recycling» разработала и изготовила и апробирует экспериментальную установку по дроблению и сепарации компьютерного лома. Утилизируемые компьютеры предварительно разбираются вручную (с применением электрических дрелей, другого инструмента). Отделяются корпус, другие пластмассовые детали, монитор, печатные платы.
Печатные платы с навесными элементами дробятся в роторном измельчителе, затем дробленый продукт проходит магнитную, воздушную и другие виды сепарации. Из лома выделяются медь, никель, алюминий. Вместе с медью выделяются благородные металлы: золото, платина, палладий. Для увеличения производительности ванн применяется постоянная рециркуляция электролита. Пилотная установка компактна, высокомеханизирована, проста в управлении. Производительность установки составляет
5 т в смену.
Фирма также организовала производство по переработке электронного и другого лома общего назначения и содержащего благородные металлы.
Предприятие для переработки такого лома представляет собой трехэтажное здание общей площадью около 10 тыс.кв.м. На первом этаже размещено дробильное оборудование, магнитные сепараторы, плавильные печи, другие машины, в том числе подъемно-транспортные; на втором этаже размещено оборудование для электролиза металлов; на третьем этаже - оборудование для аспирации процессов, научно-исследовательские службы, административно-управленческий аппарат. На предприятии работает всего 20 человек.
Программой фирмы предусмотрено ежегодно перерабатывать порядка 40 тыс. т лома, в том числе: 3 тыс. т компьютерного электронного лома, 1 тыс. т гальванических элементов питания, 2 тыс. т катализаторов, 5 тыс. т прецезионных сплавов, 20 тыс. т шламов гальванического производства и др.
Следует отметить, что электронный лом, перерабатываемой фирмой «Inter Recycling» , по составу существенно отличается от отечественного радиоэлектронного лома. Так, в 1 т западного компьютерного лома содержится более 700 г золота, а в 1 т лома отечественных телевизоров и другой БРЭА содержится около 30 г золота и более 300 г серебра.
Фирма «Tekony Sanso», специализируясь на технологии переработки малогабаритных двигателей, компьютеров, радиоэлектронного скрапа и пр., большое внимание уделяет процессу дробления, как определяющему эффективность и качество технологии.
Технологический процесс состоит из следующих основных этапов: сортировки, полуручного демонтажа с помощью пневматического инструмента на транспорте, прессования, трехстадийного низкотемпературного дробления (дробление +5 -25 мм, измельчение +0,3 -5 мм, микроизмельчение не более 50 мкм), магнитной и пневмовибросепарации. Фирма также располагает оборудованием для получения чистых материалов из концентратов первичной переработки лома (металл, пластмасса, резина) на основе процесса высокой очистки с повторным циклом. Производительность оборудования 150 кг/ч.
Фирма W.Hunter and Assiates LTD предлагает технологический процесс восстановления благородных металлов из электронного скрапа (производительность линии 1 т/сут), который можно разделить на три основные стадии.
1. Предварительное отделение деталей, содержащих благородные металлы. Эту операцию осуществляют вручную с помощью ножниц гильотинного типа.
2. Сухое отделение и обогащение содержащей благородный металл фракции. Эта стадия процесса полностью автоматизирована и включает серию отдельных операций, направленных на уменьшение размера частиц перерабатываемого материала до -2 мм. Для обогащения фракции, содержащей благородный металл, применяют магнитную сепарацию, воздушную классификацию и вибрационный стенд.
3. Мокрое обогащение на концентрационных столах, направленное на еще большее обогащение фракции, содержащей благородный металл.
После этого используют электрохимические процессы с целью восстановления золота из металлических материалов. Мокрый осадок, возникающий в результате проведения указанного процесса, фильтруют, расплавляют и отливают в слитки. Эти слитки впоследствии поступают на плавильный завод, на котором осуществляется восстановление благородных металлов. Степень восстановления 85-90%.
Фирма «VEB» осуществляет переработку печатных плат измельчением их в шаровой мельнице до крупности ±1 мм, классификацию полученных фракций по слоям в вибропитателе и разделение металлов и неметаллов, электростатическую сепарацию.
Другая технология позволяет получать вторичные благородные металлы без разрушения керамических, стеклянных или других подложек микросхем.
Предлагается также раздельная регенерация печатных плат, проводников и сопротивлений. При этом платы микросхем с покрытием подвергают комбинированным процессам растворения, промывки, сушки и прокаливания, во время которых открытый металл дорожки проводника отделяют кислотами, а подложку промывают водным раствором, после чего погружают в раствор фторида аммония. Затем материал сушат и дополнительно прокаливают на воздухе. Технология может быть использована для всех толстослойных переключающих схем и их элементов.
Если лом представляет собой термосные колбы или сосуды Дьюара, используют водный раствор соли, дающий кислую реакцию. Серебро отделяется от стекла в виде хлопьев и выделяется затем из раствора методами сепарации.
По технологии исходное сырье, содержащее благородные металлы, переводят в разлагающуюся форму путем сжигания или криогенного охлаждения, после чего его дробят и классифицируют на ситах в диапазоне крупностей 0,2-5,0 мм.
Из подрешетного продукта методом гравитационной сепарации выделяют тяжелую фракцию, содержащую благородные металлы, а надрешетный продукт подвергают магнитной сепарации. Из магнитной фракции продукта механическим способом выделяют концентрат благородных металлов. Из немагнитной фракции и тяжелой фракции, полученной при гравитационной сепарации, также получают некоторое количество благородных металлов путем их химической обработки и удаления цветных металлов и примесей.
Для получения высококачественного концентрата с содержанием благородных металлов не ниже 95% дополнительно проводят выщелачивание концентратов в неорганической кислоте.
По технологии фирмы «Galika» лом, например телевизоров, дробят в молотковой дробилке на фракции до 100 мм. Дробильная установка проста по конструкции и может быть установлена на грузовике. Из дробленого продукта выделяется железо с помощью магнитного барабанного сепаратора, а узлы электронных схем и большие куски алюминия отбирают вручную с ленточного транспортера, поставляющего лом в плавильную печь. Плавку осуществляют во вращающейся барабанной печи.
Перед плавкой дно печи заполняют старым стеклом. В результате в процессе плавки расплавленное стекло создает защитный слой над расплавленным металлом, что препятствует испарению благородных металлов.
В процессе плавки содержание меди в печи должно быть определенным, так как медь хорошо связывает благородные металлы. Поэтому необходимо добавлять медьсодержащие отходы, в том числе и провода с изоляцией.
Вследствие того, что в магнитном сепараторе удаляется не все железо, оставшуюся его часть выжигают с использованием жидкого кислорода в процессе плавки. Для этого на 15 т расплавленной плиты требуется 150 кг жидкого кислорода.
В качестве горючего для печи могут использоваться любое, в том числе отработанное, машинное масло и деревянные корпуса телевизоров. Газоочистка осуществляется с применением катализаторов. Отработанная тепловая энергия может использоваться повторно, например для отопления квартир.
Выплавленный металл состоит в основном из меди с примесями благородных металлов. В последующем из него электролитическими методами выделяют сначала медь, затем золото, серебро, платину и палладий.
Шлаки, оставшиеся после плавки, состоят в основном из стекла. Эти шлаки после измельчения могут повторно использоваться в плавке или во вторичной стройиндустрии.
По технологии американских компаний исходное сырье может содержать скрап в виде электродвигателей, генераторов, силовых щитов, реле и других электронных и электротехнических устройств, в которых кроме меди имеются алюминий, органические изоляционные материалы, железосодержащие материалы и в небольших количествах другие металлы, в том числе благородные.
Технология предусматривает криогенное охлаждение, несколько циклов измельчения, воздушной и магнитной сепарации. В качестве измельчителей в начальных стадиях используют молотковые дробилки, а в последующих стадиях для измельчения ковких материалов - роторные измельчители-грануляторы. Для сепарации практически всех видов получаемых продуктов (металлов и неметаллов) применяют виброгрохоты с воздушным псевдосжижением и концентрационные столы, также в режиме воздушного псевдосжижения.
Технология энергоемкая из-за большой степени дробления (до 100 и более раз) и решения сложной проблемы полной сепарации многокомпонентного лома.
По технологии фирмы «Lindemann» гидравлическим грейдером лом загружают в наклонно расположенный загрузочный желоб и направляют в дробилку (цердиратор-160). Вторая кромка отбойной плиты цердиратора служит для дополнительного дробления крупных кусков лома до размеров, обеспечивающих их прохождение через колосниковую решетку. Недробимые куски лома разгружаются посредством разгрузочного клапана гидравлического действия в обход колосниковой решетки.
Дробленый материал виброконвейером подается на ленточный конвейер, с помощью которого направляется к воздушному сепаратору, где металлы очищаются от неметаллических материалов, после чего поток металлов поступает на барабан электромагнитного сепаратора. Здесь магнитная фракция отделяется в контейнер, а немагнитная попадает на сортировочный конвейер, где раскрытые цветные металлы сортируют вручную, после чего поток цветных металлов направляют на измельчение и ЭДС-сепарацию для разделения по видам металлов. Чистота получаемых металлов 85-90%.
Проблема пылеулавливания технологической линии решена по так называемому принципу двухступенчатого отделения. Во время 1-й ступени отсасываемый воздух, содержащий пыль, предварительно очищается от крупной пыли и отходов в циклоне (методом центробежного отделения). Во время 2-й ступени часть потока предварительно очищенного воздуха проходит в мокрый скруббер Вентури.
Технология предназначена для выделения цветных металлов из лома в гидроциклонах и включает в себя подготовительные операции дробления, магнитной сепарации, грохочения и гидроциклонирования.
Измельченный материал до крупности -0,7 см, из которого отделены ферромагнитные металлы, подается на батарею последовательно соединенных гидроциклонов, в которых материал разделяется по плотности с использованием только одной разделяющей среды.
Технология экологически чистая. Технологическая жидкость очищается от мелких твердых частиц в специальных концентраторах циклонного типа. При этом полученный концентрат также может рассматриваться как источник многокомпонентных отходов.
Извлечение серебра из фотоматериалов.
Отходы фотографических материалов.
Все фотографические материалы состоят из светочувствительных эмульсионных и вспомогательных слоев и подложки. В качестве последней применяются высокополимерные пленки, стекло и бумага. Фотографические эмульсионные слои содержат галогениды серебра в виде дисперсных кристаллов, равномерно распределенных в желатине. Фотоэмульсионные слои в обычных высушенных светочувствительных материалах содержат 40-60% галогенидов серебра (обычно AgBr), 30-50% желатина и 6-10% воды. Содержание галогенидов серебра в фотографических слоях изменяется в очень широких пределах в зависимости от характера, назначения и типа фотоматериалов.
При изготовлении эмульсий исходными являются водножелатнновый раствор галогенидов (бромистого калия КВг, бромистого аммония NH4Br, йодистого калия KI, хлористого натрия NaCl и др.) и раствор азотнокислого серебра AgNО3 Для аммиачных эмульсий применяют водно-аммиачный раствор AgN03, получаемый при добавлении к водному раствору AgNО3 25%-нoro раствора аммиака по суммарной реакции:
AgNO3 + 2NH4OH = [Ag(NH3)2]NО3 + 2H2О
При смешении исходных растворов протекают следующие реакции:
AgNO3 + Ме Hal = Ag Hal + MeNO3
или
[Ag(NO3)2]NО3 + Ме Hal = Ag Hal + MeNO3 + 2NH3,
где Me-K, Na или NH4; Hal - Br, I или CI.
Галогенид серебра выделяется из раствора в виде микрокристаллов, равномерно заполняющих желатиновую среду. В 1 см3 эмульсии в зависимости от условий синтеза может присутствовать от 109 до 1014 микрокристаллов.
Полученную эмульсию, точней суспензию, выстаивают, удаляют из нее промывкой или другими способами нитрат того или иного металла, остаточный аммиак и избыточную соль галогена и подвергают второму выстаиванию при 40-50 °С, при котором в кристаллах галогенидов возникают центры светочувствительности. Затем эмульсию охлаждают до превращения в твердый студень. При изготовлении фотографических материалов этот студень расплавляют, фильтруют эмульсию, наносят ее на подложку в поливных машинах и подвергают нанесенные эмульсионные слои студенению и сушке.
В фотоэмульсию помимо основных реагентов вводят: стабилизаторы, сохраняющие свойства эмульсии длительное время, пластификаторы, придающие гибкость и пластичность желатиновому слою, дубители, повышающие точку плавления и прочность желатинового слоя, антисептики, предохраняющие эмульсию от воздействия бактерий.
При экспонировании фотографического слоя в освещенных его местах происходит фотохимическая реакция, при которой в кристаллической решетке галогенида (бромида) серебра электроны переходят от ионов галоида (брома) к иону серебра: Ag+Br- + hy = Ag + Br, где hy — энергия кванта.
Образовавшийся по этой реакции бром, покидая микрокристалл, поглощается желатиной эмульсионного слоя. Выделяющееся серебро служит для образования скрытого фотографического изображения.
Проявление заключается в обработке пленки медленно действующим органическим восстановителем (гидрохиноном, метолом или другими соединениями), избирательно восстанавливающим серебро в тех зернах AgBr, которые уже содержали его в виде зародышей скрытого изображения.
На примере гидрохинона процесс протекает по схеме:
  ОН ОН + 2AgBr ↔ O= =O + 2HBr + 2Ag
В результате скрытое изображение усиливается и становится видимым серебряным изображением. Это изображение является обратным - негативом, на котором светлым областям оригинала соответствуют темные пятна и наоборот.
Целью последующей за проявлением операции фиксирования является полное удаление из эмульсионного слоя невосстановленного при проявлении галогенида серебра. Для его растворения используют вещества, образующие с серебром растворимые комплексные соединения. Наиболее широкое применение для фиксирования приобрел тиосульфат натрия, кристаллогидрат которого именуется гипосульфитом. Кроме тиосульфата натрия в качестве фиксирующего вещества используют тиосульфат аммония.
Растворимости галоидных солей серебра в воде очень малы. Произведение растворимости бромистого серебра:
[Ag+]lBr] = 5,3*10-3,
т.е. при растворении AgBr в чистой воде насыщение наступает при концентрации серебра ~8-10-5г/л. Концентрацию насыщения при данном значении произведения растворимости можно увеличить, уменьшая диссоциацию серебряной соли в растворе. Это достигается растворением бромистого серебра в растворителях, дающих с серебром комплексные соединения. Если комплексный ион, содержащий серебро, диссоциирует в растворе по уравнению AgМ- - Ag+ + М2, то константа диссоциации 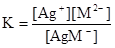
Чем меньше константа диссоциации комплексного иона серебра, тем больше в растворе должна быть общая концентрация серебра, т.е. тем более растворим галогенид серебра, в данном случае AgBr.
В литературе приводятся различные формулы комплексных соединений серебра, которые в общем виде могут быть представлены формулой Me2n-l[AgS2О3)n].
Константы диссоциации комплексных ионов:
[AgS2О3]- -Ag+ * S2O32- K1= 1,5 * 10-9;
[Ag(S2O3)2]3- - Ag+ + 2SO32- К2= 3,5 * 10-14;
[Ag(S203)3]5- -Ag+ + 3S2O32- Kз= 7,1 * 10-15
При избытке тиосульфата (в реальных растворах для обеспечения надлежащего качества фотографий при фиксировании применяют примерно 10-кратное количество тиосульфата по сравнению со стехиометрически необходимым) в растворе присутствуют одновременно все три комплексных иона, причем преобладают ионы [Ag (S2О3)3]5-.
По Блюмбергу, с поправкой на указанный выше состав комплексного иона в фиксажном растворе, существует следующая система равновесий:
AgBr + 3Na2S2O3 NaBr + Na5[Ag(S2O3)3]
5Na+ + [Ag(S2O3)3]5-
Na+ + Br- + Ag+ + 3S2O32-
При увеличении количества растворенного серебра растет концентрация соли Na5[Ag(S2O3)3]5- концентрация комплексного иона [Ag(S2О3)3]5-, следовательно, концентрация Ag+. Когда последняя увеличивается настолько, что будет достигнуто произведение растворимости AgBr, раствор будет насыщен бромистым серебром. Применение избытка тиосульфата обеспечивает полный переход бромистого серебра в раствор. Обычно исходные фиксажные растворы содержат 250-400 г/л пятиводного тиосульфата натрия.
Содержание серебра в черно-белом изображении зависит от сюжета объекта съемки и других факторов. На построение изображения расходуется меньшая часть серебра из эмульсионного слоя, большая же его часть переходит в фиксажный раствор. В среднем в фиксажный раствор переходит 50-60% серебра от нанесенного на светочувствительные материалы. В случае фиксирования фотопластинок и фотобумаги этот показатель может достигать 75%, при фиксировании же цветных пленок, фотопластинок со снимками спектральных линий, пленок с осциллограммами, промышленных и медицинских рентгеновских снимков — 80-90%.
Отработанные фиксажные растворы, образующиеся у мелких потребителей светочувствительных материалов, обычно содержат 2-7 г/л, редко 14-15 г/л и лишь в исключительных случаях 20 г/л серебра.
В этих растворах всегда имеется большой избыток свободного тиосульфата натрия (или, реже, аммония) и бромистый натрий. В них могут присутствовать добавляемые в процессе фиксирования метабисульфит калия, уксусная кислота, хлористый аммоний, алюминиевые или хромовые квасцы, примеси солей железа, меди и свинца, а также неотмытые компоненты проявителя и продукты его разложения.
Отработанные фиксажные растворы, поступающие на извлечение серебра, весьма неоднородны по составу. Они часто загрязнены посторонними веществами, попадающими в них при транспортировке и в результате смешивания с другими растворами, применяемыми в фотографии, например, при отбеливании, вирировании и т.п.
Первые (непроточные) промывные воды от промывки фотоматериалов после фиксирования содержат 1-2 г/л серебра.
В состав отходов пленки и фотобумаги входят изношенные («битые») кино-фотопленки, потерявшие свое значение негативные и позитивные фотоснимки и рентгеновские снимки, различные обрезки кинофотопленки и фотобумаги, бракованные, засвеченные или потерявшие чувствительность из-за долгого хранения фотоматериалы.
Основными сдатчиками этих отходов являются сеть кинопроката (срок службы демонстрируемого фильма, как правило, не превышает двух лет), рентгеновские кабинеты, фотоателье, лаборатории научных учреждений. Битая пленка образуется также у фотолюбителей, в организациях, занимающихся аэрофотосъемкой и т.п.
Цветографическая пленка является многослойной. Она содержит три эмульсионных слоя, в которых помимо веществ, применяемых для черно-белого изображения, содержатся компоненты, которые при появлении дадут цветное изображение (красители). В зависимости от состава красителя получается желтое, пурпурное и голубое окрашивание снимка. В результате цветного проявления в отдельных слоях материала образуются однокрасочные и серебряные изображения. Кроме того, в одном из слоев (фильтровом) остается коллоидное серебро. Так как серебряные изображения и фильтровый слой закрывают цветное изображение, серебро следует удалить из материала. Эту операцию производят в две стадии — отбеливанием красной кровяной солью и фиксированием с помощью тиосульфата.
Битая цветная кино-фотопленка содержит очень малое количество серебра, а в ряде случаев вообще не содержит его. Вполне очевидно, что нельзя объединить для переработки все поступающие отходы кино-фотоматериалов.
С другой стороны, перерабатывать отдельно фотоотходы от каждого сдатчика физически невозможно и нерентабельно, так как встречаются партии отходов массой менее 5 кг, а количество сдатчиков измеряется тысячами. В практике выработана следующая номенклатура перерабатываемых фотоотходов:
1) рентгеновская пленка медицинская;
2) рентгеновская пленка техническая;
3) фотопленка;
4) кинопленка;
5) фототехническая пленка;
6) флюорографическая пленка;
7) аэрофотопленка;
8) осциллографная бумага;
9) фотобумага.
Порядок сбора и хранения серебросодержащих отходов от использования фотоматериалов.
При использовании фотоматериалов, содержащих серебро, на предприятиях (в типографиях, издательствах, фотоателье, кино- и фотолабораториях, фото- и рентгенокабинетах и т.п.) обязательному сбору подлежат: отработанные фиксажные растворы, первая промывная вода после промывки отфиксированных отпечатков, отработанные отбеливающе-фиксирующие растворы, обрезки фотобумаги, пробные или забракованные фотоотпечатки, бой фотопластинок, использованные или бракованные негативы, заправочные и защитные концы кинопленки, остатки сухой или жидкой эмульсии, обтирочные и фильтровальные материалы, используемые при фотоработах и переработке серебросодержащих отходов. Сбору также подлежат архивные материалы и неэкспонированные фотоматериалы, срок хранения которых истек, а также пришедшие в негодность из-за нарушения правил их хранения.
Отходы в виде водных растворов собирают в тару (канистры, бутыли и т.д.), изготовленную из материала, не являющегося восстановителем серебра (полиэтиленовую, пластмассовую и т.д.). При этом отработанные фиксажные растворы и первая непроточная промывная вода сливаются в одну емкость, а отбеливающие отходы - в отдельную тару. Категорически запрещается собирать и хранить фиксажные и отбеливающие растворы, первые промывные непроточные воды в стеклянных, а также металлических емкостях без антикоррозийных покрытий.
Твердые отходы (пробные, забракованные фотоотпечатки, обрезки фотобумаги и т.д.), изготовленные на ацетатной негорючей основе, хранят в деревянных ящиках, корзинах, тканевых и бумажных мешках. Отходы фотоматериалов, изготовленные на легковоспламеняющейся нитрооснове, хранят в плотно закрывающихся железных ящиках или другой таре из негорючего материала, обеспечивающего противопожарные требования. При этом сбор и сдача экспонированных отходов производится раздельно от неэкспонированных по видам используемых фотоматериалов - рентгенопленки, кинопленки, аэрофотопленки и т.д.
Методы предварительной обработки серебросодержащих отходов.
Перед отправкой отходы для приведения их в транспортабельное состояние и с целью сокращения потерь от расплескивания, утечки или распыления подлежат первичной обработке.
Уничтожение таких отходов до извлечения на них серебра не допускается.
Описание рекомендуемых различных способов первичной обработки применительно к отдельным видам отходов фотоматериалов приводится ниже.
Извлечение серебра из отработанных фиксирующих растворов.
На построение фотографического изображения расходуется лишь часть серебра, содержащегося в светочувствительном слое фотоматериала. Большая же часть серебра переходит в фиксаж. Вот некоторые цифры: фотографическая бумага содержит от 1 до 3,7 г/м2, фотопластинки содержат серебра от 4 до (!) 510 г/м2, фотопленка - 2,5-9,5 г/м2, рентгеновская пленка - 10-50 г/м2.
Способы извлечения серебра из отработанных фиксирующих растворов делятся на химические и электролитические: К химическому способу осаждения серебра относятся способы восстановления серебра порошком или опилками (стружками) цинка и железа, гидросульфитом, гидразинборатом и проявителем, а также сульфидная регенерация-осаждение серебра в виде сульфида серебра при введении в фиксаж раствора сернистого натрия.
Для промышленного применения наиболее целесообразным является использование способа электролитической регенерации серебра, при котором серебро выделяется в наиболее чистом виде, что облегчает его дальнейшее рафинирование (очистку). Электролитическая регенерация серебра основана на восстановлении ионов серебра электрическим током.
Наиболее распространенными способами извлечения серебра являются следующие:
1. К 1 л использованного фиксирующего раствора добавляют 5-6 г гидросульфита натрия и 5-6 г безводной соды. Через 10-20 ч образовавшееся в виде черного мелкого порошка металлическое серебро фильтруют, а обессеребренный фиксирующий раствор подкисляют бисульфитом натрия и вновь используют для работы.
2. Отработанный фиксирующий раствор подкисляют серной кислотой и вводят в него цинковые опилки или стружки цинковой, жести, энергично перемешивают до тех пор, пока раствор не станет прозрачным. Затем раствор осторожно сливают. Осадок, состоящий из серебра, цинка и его соединений, серы и остатков желатины, промывают и высушивают.
3. К 1 л отработанного фиксирующего раствора приливают 20 мл 20%-ного раствора сернистого натрия. После отстоя раствора в течение суток осадок, представляющий собой сернистое серебро, отфильтровывают и высушивают. Осаждение ведут вне помещения или при усиленной вентиляции, для уменьшения выделения сероводорода отработанный фиксирующий раствор предварительно подщелачивают.
4. Метод, исключающий малоэффективную транспортировку растворов с малым содержанием в них серебра, основан на способности некоторых ионообменных смол сорбировать ионы серебра из растворов. Он пригоден для регенерации серебра непосредственно в кинофотолабораториях и фотоателье, не требует никакого специального оборудования и практически может осуществляться в процессе повседневной работы.
В отработанный фиксирующий раствор или первую промывную воду добавляют гранулы ионообменной смолы марки КУ-1 или АН-21 из расчёта 5 г на 1 л раствора. Для более полного прохождения ионообмена раствор достаточно взбалтывать 2-3 раза за 5-8 часов. Процесс протекает 10-12 ч. По истечении этого времени раствор фильтруют, полученный шлам высушивают. Этим способом из растворов извлекается 80-90% серебра.
5. Осаждение труднорастворимой соли сульфида серебра производят после предварительного подщелачивания раствора фиксажа едкой щелочью с целью последующей нейтрализации сероводорода H2S, который выделяется при осаждении серебра сульфидом натрия. К щелочному раствору фиксажа постепенно приливают при постоянном помешивании 20%-ный раствор сульфида натрия. Сульфид натрия, реагируя с комплексной солью серебра, образует труднорастворимую соль серебра Ag2S, которая выпадает в осадок. В общем виде реакция сульфидного способа осаждения серебра протекает по уравнению:
Na4[Ag2(S2O3)3] + Na2S = Ag2S + 3Na2S2O3
Через сутки после отстаивания на дне сосуда осаждается сульфид серебра. Осадок содержит около 87% серебра. Осветлённую жидкость сливают с осадка, который высушивают любым способом.
6. Восстановление серебра до металлического производят с помощью активного восстановителя - дитионита натрия. Раствор кислого фиксажа предварительно подщелачивают содой до pH = 7 - 8, после чего в него добавляют дитионит натрия. Для прохождения реакции раствор необходимо подогреть. Выпавший осадок почти на 100% состоит из металлического серебра. На 1 л отработанного фиксажа добавляют не менее 20 г безводной соды и 20 г дитионита натрия Na2S2O4 * 2H2O.
Реакция восстановления серебра из щелочного раствора отработанного фиксажа протекает по следующей схеме:
Na4[Ag2(S2O3)3] + Na2S2O4 + 2NaOH = 2Ag + 2NaHSO3 + 3Na2S2O3
Как видно из приведенных уравнений, при извлечении серебра из фиксирующих растворов они одновременно регенерируются. Таким восстановленным фиксажем можно повторно пользоваться, если в него добавить 15-20% тиосульфата натрия.
7. Осаждение серебра отработанным гидрохиновым проявителем заключается в том, что равные объемы отработанного фиксирующего раствора и отработанного проявителя смешивают и на 1 л фиксажного раствора добавляют 3-4 г едкого натра или каустической соды. Раствор хорошо перемешивают и дают отстояться в течение суток, а затем фильтруют. Оставшийся на фильтре серебросодержащий осадок собирают и высушивают. Для наиболее полного выделения серебра в раствор, пропущенный через фильтр, добавляют ещё некоторое количество отработанного проявителя и процесс повторяют.
Химические процессы, происходящие при указанном методе регенерации серебра, можно выразить следующей схемой:
1. Na4[Ag2(S2O3)3] + C6H4(OH)2 = 2Ag + 2Na2S2O3 + H2S2O3 + C6H4O2
2. H2S2O3 + Na3CO3 = Na2S2O3 + CO2 + H2O
8. Восстановление серебра формалином осуществляется путём добавления к отработанному фиксирующему раствору 40%-ного водного раствора формальдегида из расчёта 4 мл на 1 г осаждаемого раствора. Процесс ведут при кипячении в фарфоровой или эмалированной посуде в течение суток.
Преимуществом метода является высокое содержание серебра в осадке, а недостатком - большой энергетический расход и сильный запах.
9. Восстановление серебра металлами основано на том, что серебро вытесняется из растворов его солей подавляющим большинством других металлов. Наибольшее применение для этой цели получили железо, алюминий и цинк, причём металлы используются в виде стружки, что значительно удешевляет процесс, так как могут использоваться отходы производства, или пыли. С увеличением поверхности соприкосновения металла с раствором скорость процесса возрастает. Перед применением стружку обезжиривают в 3%-ном растворе щелочи. Длительность осаждения серебра и расход металлов-восстановителей приведены ниже.
Используемый материал |
Расход реагента на 1 гр серебра (гр) |
Время осаждения (сутки) |
Железная стружка или опилки |
2-5 |
3-6 |
Алюминиевая пыль, фольга или стружка |
1,5-2 |
2-3 |
Цинковая пыль |
1,5-2 |
1-2 |
Преимущества процесса - дешевизна и высокое содержание серебра в осадке; недостатки - длительность, необходимость переодического перемешивания, наличие больших сосудов для хранения растворов.
10. Небольшая заметка из журнала "Юный техник" (№ 11 за 1959 г.) "Серебряные рудники" - в отходах.
Отработанный фиксажный раствор имеет следующую химическую формулу: Na2[Ag(S2О3)3]. Если смешать равные количества фиксажа и раствора сернистого натрия (5-6 г Na2S на 1 л воды), произойдет реакция, в результате которой в осадок выпадет сернистое серебро. Смешайте высушенный осадок с железными опилками и кальцинированной содой. Расплавьте смесь в тигле - получите черновое металлическое серебро".
11. К отработанному фиксажу добавляется отработанный гидрохиноновый, метилгидрохиноновый или фенидонгидрохиноновый проявитель в пропорции 1:1, затем все интенсивно перемешивают. Отстаивают в течение суток и сливают раствор с осадка.
Концентрация серебра в отходах |
Расход гидразинборана,
г/л
|
исходная, г/л |
конечная, мг/л |
0,56 |
0,4 |
0,056 |
0,87 |
0,6 |
0,095 |
1,2 |
0,5 |
0,13 |
1,34 |
0,6 |
0,145 |
1,58 |
0,6 |
0,175 |
1,94 |
0,7 |
0,215 |
2,06 |
0,65 |
0,225 |
2,60 |
0,5 |
0,285 |
3,09 |
0,4 |
0,34 |
3,27 |
0,6 |
0,365 |
12. Осаждение серебра гидразинбораном. В отработанный фиксажный раствор добавляется едкая щелочь для повышения рН раствора до 11-12. На 1 г серебра в растворе расходуется 0,11 г гидразинборана, остаточная концентрация не превышает 0,7 мг/л (см.табл.). Продолжительность регенерации - 2-3 ч, а полное осаждение металлического серебра происходит в течение 20-24 ч при комнатной температуре. В ходе регенерации необходимо равномерно перемешивать раствор. В полученном осадке содержится 70-80% серебра. Незагрязненные фиксирующие растворы после регенерации серебра с помощью гидразинборана можно повторно использовать в процессе химико-фотографической обработки фото- и кинопленки. При регенерации серебра из отбеливающе-фиксирующих растворов содержание серебра в шламе не превышает 20%.
13. Восстановление серебра дитионитом натрия.
Раствор кислого фиксажа предварительно подщелачивают содой до рН 7-8, после добавляют активный восстановитель - дитионит натрия, раствор подогревают. На 1 л отработанного фиксажа добавляют не менее 20 г соды и 20 г дитионита натрия. Выпавший осадок, содержащий до 100% металлического серебра, высушивают.
14. Выпаривание отработанных фиксажных растворов.
В тех местах, где образуется незначительное количество фиксажных растворов и отсутствуют условия для осаждения серебра указанными выше методами, фиксажные растворы подвергают полному выпариванию в металлических или керамических сосудах до образования сухих солей, которые растирают в той же посуде и опробуют.
Полученную соль в упакованном виде отправляют на перерабатывающее предприятие.
Способ извлечения серебра из отработанных фоторастворов, промывных и сточных
вод (патент Российской Федерации RU2165468)
Изобретение может быть применимо к отработанным растворам и промывным водам, образующимся при обработке светочувствительных серебросодержащих, в том числе цветных, материалов, а также для извлечения серебра из других содержащих его растворов. Способ извлечения серебра из отработанных фоторастворов промывных и сточных вод, включает сорбцию серебра, отделение насыщенного серебром сорбента от раствора, сушку, обжиг насыщенного сорбента и выплавку металлического серебра из концентрата; в качестве сорбента используют бис-(диметилтиокарбамил) дисульфид. Сорбцию серебра проводят в статическом режиме с расходом 1,5-1,6 г сорбента на 1 г находящегося в растворе серебра; в динамическом режиме с использованием указанного сорбента, нанесенного на пористый носитель с развитой поверхностью, например на активированный уголь с размером частиц 0,1-1,5 мм. Использование бис-(диметилтиокарбамил) дисульфида в качестве сорбента позволяет извлекать серебро в широком диапазоне концентраций и рН среды из фиксажных растворов черно-белой и цветной фотопленки и других промывных и сточных вод с высокой эффективностью за счет более высокой сорбционной емкости, при этом сокращается время сорбции. Предлагаемый способ извлечения серебра сравнительно прост и может быть использован в производстве в самых широких масштабах.
Описание изобретения: изобретение относится к гидрометаллургии благородных металлов и может быть применимо к отработанным растворам и промывным водам, образующимся при обработке светочувствительных серебросодержащих, в том числе цветных, материалов, а также для извлечения серебра из других содержащих его растворов (вторичное серебро).
Задачей настоящего изобретения является повышение эффективности извлечения серебра из серебросодержащих растворов.
Поставленная задача достигается за счет способа извлечения серебра из отработанных фоторастворов промывных и сточных вод, который включает сорбцию серебра, отделение насыщенного серебром сорбента от раствора, сушку, обжиг насыщенного сорбента и выплавку металлического серебра из концентрата, в качестве сорбента используют бис-(диметилтиокарбамил) дисульфид, практически нерастворимый в тиосульфатном растворе.
Сорбцию серебра проводят в статическом режиме с расходом 1,5-1,6 г сорбента на 1 г находящегося в растворе серебра или в динамическом режиме.
При извлечении серебра из промывных и сточных вод в динамическом режиме указанный сорбент наносят на пористый носитель с развитой поверхностью, например на активированный уголь с размером частиц 0,5-1,5 мм.
Нами предлагается в качестве сорбента серебра из отработанных фоторастворов и других растворов использовать бис-(диметилтиокарбамил) дисульфид. Сорбционная емкость при извлечении серебра из различных отработанных фоторастворов и промывных вод на предлагаемом сорбенте выше, чем у известных, причем процесс сорбции практически завершается в течение трех часов. Степень извлечения серебра из растворов более 99,0%, сорбция может проводиться в статических или динамических условиях.
Насыщенный серебром сорбент отделяют от раствора, высушивают и обжигают с получением концентрата, из которого выплавляют металлическое серебро чистотой 99,5-99,8%.
В качестве сорбента используют активированный уголь с достаточно широкими порами (например, марки БАУ), на который наносят 10-15 мас.% бис-(диметилтиокарбамил) дисульфида.
Эффективность сорбента зависит от размера частиц носителя.
Таким образом, использование бис-(диметилтиокарбамил) дисульфида в качестве сорбента позволяет извлекать серебро в широком диапазоне концентраций и pH среды из фиксажных растворов черно-белой и цветной фотопленки и других промывных и сточных вод с высокой эффективностью за счет более высокой сорбционной емкости, при этом сокращается время сорбции. Предлагаемый способ извлечения серебра сравнительно прост и может быть использован в производстве в самых широких масштабах.
Формула изобретения: Способ извлечения серебра из отработанных фоторастворов промывных и сточных вод, включающий сорбцию серебра, отделение насыщенного серебром сорбента от раствора, сушку, обжиг насыщенного сорбента и выплавку металлического серебра из концентрата, отличающийся тем, что в качестве сорбента используют бис-(диометилтиокарбамил)дисульфид.
Методы извлечения серебра из отходов.
1. Со стеклянных фотопластинок снимается эмульсионный слой в горячем содовом растворе, прочие фотоматериалы сжигаются в фарфоровой посуде. Правда, при сжигании часть серебра будет улетучиваться с дымом. Для уменьшения потерь фотоматериалы лучше всего сжигать тлеющим огнем или же извлечь серебро гипосульфитом натрия.
2. Зеркальный бой и елочные игрушки также содержат большое количество серебра: зеркала - от 3 до 7 г/м2, игрушки - от 0,2 до 0,5% от массы осколков. Для снятия серебросодержащего слоя с зеркального боя его помещают в кислотоустойчивую емкость, заливают горячим раствором соляной кислоты и подвергают механической обработке: проще говоря, ворошат до полного отделения серебросодержащего слоя от стекла. В промышленности для этой цели применяют вращающийся барабан.
3. Для восстановления серебра из золы фотоматериалов вам понадобится муфельная печь и термостойкие тигли, способные выдержать тысячеградусную температуру. Зола тщательно перемешивается с содой и битым стеклом в следующих соотношениях: 30% золы, 65% двууглекислого натрия и 5% битого стекла. Составленная таким образом шихта спекается при температуре 1200°С. Расплав выливают в чугунную изложницу, смазанную порошком окиси железа. Можно остудить расплав и в тигле, но потом его придется разбивать, а на дне у вас окажется слиток чистого серебра.
4. А вот методика выделения серебра из серебряно-медного сплава, описанная в 20-м томе "Технической энциклопедии", изданной в 1935 году: изделие растворяют в азотной кислоте, добавляют соляную кислоту, осажденное хлористое серебро промывают водой и восстанавливают из него металлическое серебро через взаимодействие с цинком и разбавленной серной или соляной кислотой.
5. Другой метод очень подробно был описан в журнале "Сделай сам" (№ 4 за 1990г.). Он состоит в следующем: Серебросодержащее изделие тщательно очищается от окислов и отмывается сначала теплым щелочным раствором, а затем - обычной водой. После этого изделие заливают 10%-й азотной кислотой до полного его растворения. В растворе, таким образом, находится смесь солей серебра и меди. Раствор выпаривают, а полученный порошок прокаливают в фарфоровой чашке, в результате чего нитрат меди переходит в нерастворимую окись меди. Завершение этого процесса определяется по прекращению выделения с поверхности расплава пузырьков весьма едкого газа. Теперь расплав остужают и растворяют в 2-х частях дистиллированной воды; прозрачный раствор, содержащий чистый нитрат серебра, снимают с осадка,- ну, а как восстановить из солей металлическое серебро, мы с вами уже обсуждали. В описанном процессе встречаются некоторые сложности, как-то: манипуляции с азотной кислотой, ядовитыми летучими соединениями и выпаривание больших объемов растворов. Впрочем, такие проблемы легко разрешаются в лабораторных условиях.
6. Серебряные покрытия (в том числе и наносимые химическим путем) и сплавы серебра на основах из меди, нейзильбера, латуни, томпака, мельхиора и стали снимают в смеси концентрированных серной и азотной кислот с соотношением объемов 19:1 при температуре 40-60°С. Раствор предохраняют от разбавления и регулярно корректируют его азотной кислотой, которая используется в процессе растворения покрытия.
Серебро с поверхности меди и ее сплавов удаляют и анодной обработкой в растворе состава, %:
Серная кислота H2SO4 (плотность 1,84 г/см3) – 91, Натрий азотнокислый (нитрат натрия) NaNO2 – 3 при температуре 20-50"С и напряжении источника постоянного тока 2-3 В. В качестве катодов применяют свинец.
Снятие серебра с деталей малой толщины покрытия обычно проводят при температуре 40-50°С в растворе состава, г/л: Йодистый калий KI – 250, Йод металлический I2 – 7, Сплав серебра и сурьмы с таких же деталей удаляют в растворе состава, г/л: Йодистый калий KI – 250, Йод металлический I2 - 7,5, Кислота азотная HNO2 (плотность 1,41 г/см3) - 150 мл/л,
Извлечение серебра из отходов кино-, фото- и рентгенопленки, фотопластинок и фотобумаги.
Озоление пленки и фотобумаги.
Озоление пленки и фотобумаги с последующей металлургической переработкой золы на специализированных заводах не может быть признано принципиально правильным методом извлечения серебра, так как при этом уничтожается основа пленки и фотобумаги. Это противоречит принципу комплексного использования сырья, обеспечивающему максимальный экономический эффект. Однако часто возникают ситуации, когда регенерированная основа пленки и фотобумаги по технологическим причинам не имеет сбыта; в частности, это происходит при переработке смешанной битой пленки. Смешанную регенерированную основу пленки использовать в этом же производстве нецелесообразно, а сортировка ее практически невозможна или обходится очень дорого. В этих случаях некоторые предприятия, как в СНГ так и за рубежом, практикуют способ сжигания пленки и фотобумаги. Однако при реализации этого способа необходимо обеспечить минимальные потери серебра в золе с отходящими газами путем регулирования режима сжигания и надлежащей организации газоочистки.
На заводе фирмы «Eastman Kodak» в США сжигание смешанной пленки и фотобумаги производят в специальной печи производительностью 50 т/сут, оборудованной автоматической системой загрузки сырья, колосниковой решеткой с возвратно-поступательным движением для выгрузки золы и вибрационным транспортером, подающим золу непосредственно в бункера. В камере сжигания температуру поддерживают на уровне 760°С путем регулирования скорости загрузки сырья, подачи первичного воздуха и охлаждающей воды, поступающей в камеру через специальные распылительные форсунки. Горячие газы дожигаются вторичным воздухом в камере дожигания. Отходящие газы орошаются водой в охладительной камере и при 315 °С поступают в электрофильтр, улавливающий 99% пыли. Отмечается, что стоимость сжигательной печи и электрофильтра составила около 1 млн долл., а стоимость извлеченного за год серебра в несколько раз превышает эту цифру.
Однако не все установки для сжигания пленки и фотобумаги характеризуются таким техническим совершенством. В ряде случаев пленку и фотобумагу сжигают в примитивных условиях, теряя часть золы и отравляя окружающую среду. В настоящее время ведутся исследовательские работы по созданию новых конструкций сжигательных печей, обеспечивающих минимальные потери золы.
Исследования, проведенные в печах Рижского цеха МЗВДМ, показали, что оптимальный выход золы составляет при сжигании всех видов пленки ~10% и при сжигании фотобумаги 18-20%. Для фотобумаги он выше, поскольку на нее перед поливом наносят баритовый подслой.
Эти исследования показали также, что при снижении выхода золы из пленки и фотобумаги (за счет увеличения продолжительности цикла сжигания) содержание серебра в золе не возрастает. Очевидно, это происходит из-за улетучивания серебра при длительном нагреве.
При сжигании пленки в печи в описанных условиях не наблюдают так называемого пережога (вкраплений в золе металлических корольков). Эти вкрапления обнаруживаются только в огнеупорных выломках из печи при ее ремонте, которые направляют на специализированный завод для извлечения серебра.
При внепечном сжигании пленки зола часто содержит металлические вкрапления, а общий выход серебра по сравнению сжиганием в печах, существенно ниже.
В последнее время появились разработки, предусматривающие пиролиз основы пленки и фотобумаги вместо сжигания. При этом, естественно, также как и при сжигании, уничтожается основа пленки, но потери серебра могут быть существенно снижены.
На фирме «Van Slyke» через вертикальную реторту, вмещающую отходы пленки и фотобумаги, пропускают восстановительный газ, вызывающий пиролиз материалов. При этом выделяются горячие газы, и образуется смесь золы с углеродом. Через эту смесь пропускают нагретую до 700 °С смесь воздуха и водяного пара. При этом образуется зола, содержащая восстановленное серебро (которое извлекают из нее известными методами), и горючий газ, содержащий водород, используемый для пиролиза пленки и бумаги.
На фирме «Cameron» предусмотрен нагрев серебросодержащих отходов фотоматериалов перегретым паром до температуры выше 350 °С. После возгонки органических веществ остается зола, из которой серебро можно извлечь плавкой или флотацией.
Извлечение серебра из фотоотходов смывом эмульсионного слоя с помощью
химических реагентов.
С неэкспонированной пленки, содержащей серебро в виде бромида, эмульсионный слой можно снять кипящей водой. Нарезанную на мелкие куски пленку загружают в бетонные или цементированные баки с водой, нагреваемой острым паром. При этом желатина расплавляется, и эмульсия сползает с пленки. Однако желатина удерживает бромистое серебро в суспензии. Для разрушения желатины, после которого бромистое серебро может быть отделено от раствора отстаиванием, эмульсию обрабатывают в бетонных или цементированных баках в течение 3-4 мин кипящим 6%-ным раствором серной кислоты.
С экспонированной пленки эмульсионный слой сползает с большим трудом. Ее обрабатывают не водой, а горячим раствором каустической соды. При этом кислотная обработка отпадает. Некоторые из предложенных щелочных растворов содержат добавки цианидов, поташа, карбонатной соли и хлористого натрия.
С поверхности фотопластинок — отходов производства и утративших свое значение негативов — эмульсионный слой смывают, погружая их в кипящий (подогреваемый острым паром) разбавленный раствор каустической соды. Длительность обработки 6-8 мин.
В других баках, также при обогреве острым паром, ведут отстаивание, добавляя в качестве коагулянта сульфат алюминия. Отстаивание длится 1,5-2 ч, после чего осветленную жидкость декантируют с помощью поплавкового устройства: шлам извлекают из баков по мере накопления. Высушенный в полочных сушильных шкафах шлам содержит до 50% серебра.
Разработано много вариантов кислотных (с применением соляной, азотной и уксусной кислот) и щелочных способов смыва эмульсионного слоя с фотоотходов. Их общие недостатки: значительный расход химических реагентов, токсичность передела, необходимость оборудования местной вентиляции, необходимость применения флокулянтов для ускорения отстаивания осадка.
В настоящее время чисто химические способы смыва эмульсионного слоя уступают место способам смыва с участием ферментов.
Эмульсионный слой с поверхности фотобумаги смывают раствором хлорной извести. Обычно для этой цели применяют реакторы из нержавеющей стали вместимостью около 800 л. В реакторе приготовляют ~500 л 1,5-2,0%-ного раствора хлорной извести, загружают в него 120-160 кг отходов фотобумаги и перемешивают механической мешалкой в течение 10-20 мин. При полном удалении эмульсионного слоя глянцевая сторона бумаги становится матовой. Пульпу перекачивают в отстойник из нержавеющей стали. Отстаивание производят в течение 2-4 ч, декантированный раствор фильтруют на нутч-фильтре и сбрасывают в канализацию. Осадок сушат на противнях в полочном электрическом сушильном шкафу при температуре 110-120°С в течение 24-40 ч, затем охлаждают и упаковывают в металлические ящики.
Отработанную бумагу промывают чистой водой до полного удаления белого хлопьевидного осадка. Промывные воды направляют на отстаивание.
Смыв эмульсионного слоя при участии ферментов.
Способ разрушения желатины эмульсионного слоя с помощью ферментов наиболее перспективен. Ферменты — это специфические белковые вещества (с молекулярной массой от десятков тысяч до миллиона и более), служащие биологическими катализаторами. Они способствуют различным превращениям белков, жиров и углеводов, расщеплению или построению их. Как всякие катализаторы, ферменты снижают энергию активации, необходимую для осуществления данной химической реакции, направляя ее обходным путем — через промежуточные реакции, требующие значительно меньшей энергии активации. Активность ферментов очень велика. Они способствуют превращениям такой большой массы вещества, которая во много раз превышает количество самого фермента.
В настоящее время известны более тысячи различных ферментов. Практическое использование в технике, медицине, сельском хозяйстве и других областях находят главным образом различные гидролазы-ферменты, катализирующие гидролиз, т.е. расщепление при участии воды различных сложных органических соединений на более простые. Производство ферментных препаратов состоит из двух главных этапов.
1. Получение ферментного сырья, т.е. выращивание микроорганизмов (или получение культуральной жидкости), богатых данным ферментом или содержащих фермент специального качества.
Реже используют сырье растительного или животного происхождения.
2. Выделение из полученного ферментного сырья необходимых ферментных белков либо в виде комплекса, либо отдельных, в той или иной степени очищенных, т.е. выделение ферментов из биомассы микроорганизмов или из соответствующих культуральных жидкостей.
Первый этап является преимущественно задачей микробиологов, второй — биохимиков и химиков белка.
На Шосткинском химическом заводе были начаты исследования по удалению с триацетатной кинопленки фотографической эмульсии и желатины подслоя с помощью бактериальных протеолитических ферментов, содержащихся в культуральной жидкости Bacillus Subtilis-mesentericus. Эта жидкость была получена на полупроизводственной микробиологической установке, построенной на заводе. Измельченную на резательной машине пленку обрабатывали в реакторе при перемешивании раствором фермента при 45 °С. Этот способ обеспечивал регенерацию триацетатной пленки и был внедрен в производство. Количество регенерированной пленки составляло в среднем 250-300% от неразбавленной культуральной жидкости НБ-8.
Однако активность ферментного раствора была относительно невысокой, что не позволяло достаточно глубоко расщепить желатину. Для получения серебросодержащего шлама пришлось ввести дополнительную операцию кислотного гидролиза эмульсионных смывов.
В институте биохимии АН Украины был разработан способ регенерации серебра и основы триацетатной пленки с помощью препарата Протеназа-1, представляющего собой комплекс протеолитических ферментов, продуцируемый актиномецитом Streptomyces griseus. Этот комплекс, наиболее мощный из всех известиях, расщепляет желатину более глубоко, т.е. до наиболее низкомолекулярных фрагментов. Эксперименты показали, что Протеназа-1 интенсивно гидролизует желатину фотоэмульсий, осаждая одновременно с этим шлам, содержащий 45% серебра (по сравнению с 35% по старой технологии). Смыв эмульсионного слоя производится при 45°С. При рН=6-7,8 гидролиз протекает почти одинаково, что позволяет использовать водные растворы ферментного препарата. Средняя молекулярная масса желатины под действием препарата Str. griseus после 1 ч гидролиза снижалась почти в 20 раз и составляла около 3000, тогда как для молекул исходного белка она равна 60000. За это же время количество серебра в растворе фотоэмульсии падает до нуля. Глубокий гидролиз желатины позволяет смывать с различных видов основы не только эмульсионный слой, но и подслой.
Препарат Протеназа-1 представляет собой сухой порошок, хорошо сохраняющийся и транспортируемый, достаточно стабильный по активности и составу. Применение такого препарата позволило бы легко регулировать активность и действие ферментного раствора, а также организовать смыв эмульсионного слоя с битой кино-, фото- и рентгеновской пленки непосредственно в местах ее накопления.
На заводе вторичных драгоценных металлов для снятия эмульсионного слоя с пленки предложено применять ферментный препарат Протосубтилин ГЗх-1, выращенный из культуральной жидкости продуцента Bac.Subtilis. Этот отечественный порошкообразный препарат используется в кожевенной промышленности для мягчения кожсырья и в животноводстве — в качестве добавки к кормам и комбикормам.
Применение ферментов для смыва с пленки эмульсионного слоя практикуется и в зарубежной практике. Так, фирма «Sramec» рекомендует использовать для этой цели панкреатин (трипсин) — протеолитический фермент животного происхождения — и приводит следующий режим смыва эмульсионного слоя с пленки:
1) обработка пленки щелочным (рН=8-9) раствором, содержащим до 0,2% панкреатина при температуре 40°С. Расход панкреатина - 1 г/кг рентгеновской пленки;
2) разбавление пульпы промывными водами от промывки регенерированной основы пленки;
3) подкисление раствора 20%-ной серной кислотой до рН=2-3, отстаивание, декантация осветленного раствора и сушка серебросодержащего шлама.
Удаление серебра из эмульсионного слоя без разрушения основы и желатины.
Наибольшее распространение получил способ отбеливания пленок и фотобумаги раствором медного купороса и поваренной соли по реакции:
2Ag + CuSО4 + 2NaCl = 2AgCl + Cu2SО4 + 2Na2SО4.
Окислительный потенциал системы Cu2+/Cu+ недостаточен для окисления серебра с получением раствора соли серебра ощутимой концентрации. В присутствии NaCl ионы серебра связываются в нерастворимый AgCl, что смещает реакцию вправо. Хлорид серебра откладывается в желатиновом слое пленки. Для его растворения используются фиксажные растворы, часто — сбросные, из которых предварительно электролизом удалено серебро.
Достоинства этого способа — дешевизна и доступность реактивов и вполне приемлемая скорость процесса отбеливания. К недостаткам его относятся многостадийность (отбеливание, обработка фиксажным раствором, извлечение серебра из раствора) и токсичность солей меди.
Этот способ используют также при переработке отходов фотобумаги. Представляет интерес обработка битой (проявленной и отфиксированной) пленки реагентами, окисляющими серебро с образованием его растворимых солей. К таким реагентам относятся персульфат аммония, применяемый в фотографии в качестве ослабителя, сульфат трехвалентного железа и бихромат калия. Наиболее быстро окисляет серебро последний реагент в смеси с серной кислотой (в свежеприготовленном растворе изображение на пленке исчезает в течение 1 мин). Реакция протекает по уравнению:
6Ag + K2Cr2O7 + 7H2SO4 = 3Ag2SO4 + Cr2(SO4)3 + K2SO4 + 7H2O.
Серебро из раствора осаждают с помощью НС1 и NaCl. Средний фактический расход бихромата калия составляет 2,15 г на 1 г извлеченного серебра или 1 кг на 100 кг обработанной пленки. Стоимость реактивов, расходуемых на обработку битой пленки бихроматным раствором, ниже, чем в случае применения медного купороса. Экономичность процесса еще возрастает при использовании отработанных бихроматных растворов из фотоавтоматов.
Для обработки пленки применяется бихроматный раствор, подкисленный азотной кислотой, взятый с избытком против стехиометрического количества; промывку пленки ведут раствором азотной кислоты при рН=1,2-1,3. Эти условия обеспечивают получение хорошо растворимого азотнокислого серебра и препятствуют выделению нерастворимого хромата серебра. Серебро из раствора осаждают в виде хлорида насыщенным раствором поваренной соли.
При всех описанных способах обработка пленки производится при комнатной температуре, что исключает необходимость подвода в промышленных условиях пара и электроэнергии и дополнительной вентиляции производственного помещения. Кроме того, работа с горячими растворами ограничивает выбор пластических материалов для изготовления рабочих емкостей. В горячих растворах возможен полный смыв эмульсионного слоя, при котором окисление серебра теряет смысл.
Извлечение серебра из промпродуктов, содержащих хлорид серебра (патент Российской Федерации RU2170277).
Изобретение относится к металлургии благородных металлов, в частности к аффинажу серебра. Способ получения серебра из промпродуктов, содержащих хлорид серебра, включает растворение в сульфитном растворе и нагревание. При этом восстановление серебра из сульфитного раствора ведут при добавлении щелочи и с применением восстановителя - параформальдегида при его расходе 0,27-0,35 г на 1 г серебра. Способ позволяет снизить остаточную массовую концентрацию серебра в растворе и повысить его извлечение.
Описание изобретения: В процессе переработки золотосеребряного сырья практически по любой технологии аффинажа серебро концентрируется в промпродуктах в виде хлорида серебра с разным содержанием золота. Данные промпродукты перерабатываются гидрометаллургическими или пирометаллургическими способами. Основой данных промпродуктов является хлорид серебра. В качестве растворителя хлорида серебра можно использовать сульфитный раствор щелочного металла, например сульфита натрия [1], в результате чего образуется комплекс сульфитной соли серебра состава Na5[Ag(SO3)3] [2].Задачей изобретения является повышение эффективности процесса, а именно повышение степени извлечения серебра из раствора. Поставленная задача решается за счет достижения технического результата, который заключается в снижении остаточной массовой концентрации серебра в растворе. Указанный технический результат достигается тем, что в известном способе получения серебра из промпродуктов, содержащих хлорид серебра, включающем растворение в сульфитном растворе и нагревание с получением металлического серебра, согласно изобретению в раствор добавляют щелочь и параформальдегид в качестве восстановителя при его расходе 0.27 - 0.35 г на 1 г серебра. Физико-химическая сущность заявляемого способа основывается на восстановлении серебра из сульфитного комплекса по следующей реакции: 2Na[Ag(SO3)3] + 2CN2O + 4NaOH - 2Ag↓ + H2↑ + 2HCOONa + 6Na2SO3 + 2H2O
Применение данного восстановителя для осаждения серебра из сульфитного комплекса позволяет повысить эффективность процесса восстановления серебра из раствора за счет снижения его остаточной массовой концентрации в растворе. Сопоставительный анализ заявляемого способа с прототипом показывает, что заявляемый способ отличается от известного тем, что в сульфитный раствор добавляют щелочь и параформальдегид в качестве восстановителя. Таким образом, заявляемое техническое решение соответствует критерию "новизна".
Для доказательства соответствия заявляемого изобретения критерию "изобретательский уровень" проводилось сравнение с другими техническими решениями, известными из источников, включенных в уровень техники.
Заявляемый способ получения серебра из промпродуктов, содержащих хлорид серебра соответствует требованию "изобретательского уровня", так как использование в качестве восстановителя параформальдегида в присутствии щелочи обеспечивает повышение извлечения серебра в конечный продукт, что не следует явным образом из известного уровня техники.
Для доказательства критерия "промышленное применение" достаточно сказать, что прорабатывается вопрос об его использовании на Колымском аффинажном заводе.
Для экспериментальной проверки использовали хлорид серебра. Масса навески составляла 10 г. Выщелачивание проводили раствором сульфита натрия при Ж: Т= 18: 1 и СNa2SO3=300 г/л. Хлорид серебра растворялся без остатка полностью в течение 30 минут. Концентрация серебра в растворе после растворения составляла 41 г/л.
Полученный сульфитный раствор подвергали термической выдержке при температурах 90 и 100oC в течение двух часов. Отмечено, что осаждение серебра начинается при температуре не менее 80oC. Остаточная концентрация серебра в растворе составила 7430 мг/л при 90oC, и 6940 мг/л при 100oC.
Таким образом, сравнивая полученные данные заявляемого способа и способа прототипа, следует отметить, что в способе прототипе остаточная массовая концентрация серебра составляет 7430 мг/л и 6940 мг/л, а в заявляемом - 3,5 мг/л. Отсюда видно, что применение в качестве восстановителя серебра из сульфитных растворов параформальдегида способствует повышению эффективности процесса получения серебра, а именно повышению степени извлечения серебра.
Пример использования заявленного способа: Для экспериментальной проверки использовали хлорид серебра. Масса навески составляла 10 г. Выщелачивание проводили раствором сульфита натрия при Ж: Т= 18:1 и СNa2SO3=300 г/л. Хлорид серебра растворялся без остатка полностью в течение 30 минут. Концентрация серебра в растворе после растворения составляла 41 г/л.
Опыты по осаждению серебра из раствора проводили в зависимости от температуры и расхода реагентов. Время выдержки составляло 2 часа. Полученные экспериментальные данные представлены в таблице.
Результаты экспериментовзаявляемого способа |
Номер
опыта
|
Температура, °С |
Расход на 1 г серебра, г |
Остаточное содержание Ag в растворе, г/л |
NaOH |
CH2O |
1 |
20 |
0.62 |
0.18 |
6.0000 |
2 |
60 |
0.62 |
0.18 |
2.2000 |
3 |
20 |
0.80 |
0.18 |
1.8000 |
4 |
60 |
0.80 |
0.18 |
0.4300 |
5 |
20 |
0.80 |
0.27 |
0.0100 |
6 |
60 |
0.80 |
0.27 |
0.0035 |
7 |
60 |
0.80 |
0.35 |
0.0030 |
Оптимальными условиями являются выдержка в течение 2 часов при температуре 60oC и загрузке реагентов на 1 г получаемого серебра в количестве 0,80 г NaOH и 0,27 г параформальдегида, поскольку с повышением температуры относительно комнатной и при данном расходе реагентов достигается минимальная остаточная концентрация серебра в растворе, которая составляет 3,5 мг/л. Извлечение при этом серебра в осадок составляет 99,991%.
Пример использования способа-прототипа: Для сравнения показателей заявляемого способа и способа-прототипа провели опыты по осаждению серебра из сульфитного раствора в соответствии с операциями и режимами способа по прототипу.
Формула изобретения: Способ получения серебра из промпродуктов, содержащих хлорид серебра, включающий растворение в сульфитном растворе и нагревание с получением металлического серебра, отличающийся тем, что при нагревании в раствор добавляют щелочь и параформальдегид в качестве восстановителя при его расходе 0,27 - 0,35 г на 1 г серебра.
Способ перколяционного извлечения серебра и золота из руд и отвалов (патент Российской Федерации RU2081193).
Использование: касается способов извлечения серебра и золота из сульфидных, окисленных руд, концентратов и материалов хвостохранилищ. Сущность: обработку исходных веществ ведут выщелачиванием водными растворами, содержащими ионы тиоцианата и трехвалентного железа, а выделяют серебро и золото пропусканием раствора после очередного цикла выщелачивания через слой железного скрапа или алюминиевых стружек и возврата этого раствора после корректировки на новый цикл.
Описание изобретения: Задачей изобретения является создание технологии, обеспечивающей возможность извлечения серебра и золота из руд и отвалов с таким низким содержанием этих металлов, при котором другие способы могут быть экономически неоправданы, многооборотное использование выщелачивающего раствора, затруднение регенерации выщелачивающего раствора, одновременно обеспечивается уровень экологической безопасности более высокий, чем при цианидной технологии, и не ниже, чем при использовании тиомочевины.
Технический результат достигается тем, что обеспечивается высокая степень извлечения золота и серебра при низком расходе реагентов за счет многократного использования раствора в замкнутом цикле. Повышение экологической безопасности связано с применением малотоксичных реагентов и малым объемом используемых растворов за счет замкнутого цикла их обращения.
Способ перколяционного извлечения серебра и золота из руд и отвалов, содержащих также свинец, цинк, железо, кальций, магний, кремний и серу, заключающийся в том, что измельченный материал орошают раствором, содержащим 10-50 г/дм3 тиоцианат-ионов, 0,1-5,0 г/дм3 трехвалентного железа при pH 0,5-7,0, проводя процесс выщелачивания. Заданную концентрацию трехвалентного железа обеспечивают добавлением в раствор сульфата или нитрата железа (III) или за счет растворения его из выщелачиваемого материала. Выделение серебра и золота ведут пропусканием раствора после выщелачивания через слой железного скрапа или алюминиевых стружек. После улавливания золота и серебра из раствора и коррекции его состава раствор возвращают на повторное орошение. Описанный цикл повторяется многократно.
Выщелачивание проводят при температуре окружающей среды (от 0,1 до 50oC) от 2 недель до достижения максимальной степени выщелачивания. Каждый цикл орошения в зависимости от толщины слоя материала продолжается от 1 до нескольких суток. При этом в раствор переходит серебро и золото. После каждого цикла раствор протекает через слой железного скрапа или алюминиевых стружек. Затем раствор при необходимости подкрепляют добавлением тиоцианата и серной кислоты, аэрируют для окисления железа (II) до железа (III) и подают на новый цикл выщелачивания.
Степень извлечения серебра составляет 82,1% а золота 69,4% за 15-дневный период обработки выщелачиваемого материала.
Предлагаемый способ позволяет извлечь серебро и золото из материалов, обработка которых другими методами оказывается экономически не оправданной, а также обеспечивает более высокий уровень экологической безопасности, чем ранее известные.
Проведение процесса выщелачивания в сильнокислой среде (pH<0,5) приводит к окислению тиоцианата, pH среды выше 7,0 приводит к падению окисляющей способности применяемого раствора.
Концентрация ионов железа (III) 0,5 г/дм3 достаточна для протекания процесса выщелачивания с заметной скоростью, а превышение ее более 5 г/дм3 приводит к замедлению перехода золота в раствор.
При содержании тиоцианат-ионов в растворе менее 10 г/дм3 серебро и золото практически не выщелачивается, а поддержание их концентрации на уровне, превышающем 50 г/дм3, связано с неоправданными затратами без увеличения эффективности выщелачивания путем орошения материала.
Температурные пределы соответствуют условиям извлечения геотехнологическими методами без применения нагревания при отрицательной температуре возможно замерзание раствора, а предел 50oC практически не превышается в условиях естественного нагревания верхних слоев выщелачиваемой массы солнечными лучами.
Заявляемые параметры являются оптимальными для перколяционного извлечения серебра и золота из руд и отвалов и обеспечивают высокую эффективность процесса при максимальной экологической безопасности.
Как видно из описания способа и чертежа, по сравнению с прототипом состав выщелачивающего раствора и использование его в замкнутом цикле являются новым.
Результаты опытов по применению способы перколяционного извлечения серебра и золотаиз руд и отвалов
Опыт |
Содержание NSC-, г/дм3 |
Содержание Fe3+, г/дм3 |
pH |
Т°C |
Степень извлечения Ag, % |
Cтепень извлечения Au, % |
1 |
40 |
1 |
3 |
20 |
82.1 |
69.4 |
2 |
10 |
0.1 |
0.5 |
10 |
41.6 |
26.8 |
3 |
50 |
5 |
7 |
50 |
46.7 |
32.0 |
4 |
5 |
0.05 |
0.3 |
10 |
9.2 |
5.5 |
5 |
55 |
- |
8 |
55 |
7.4 |
4.6 |
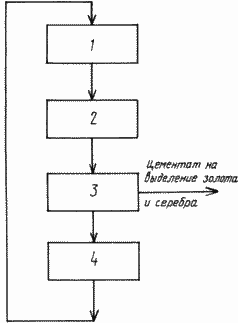
Преимущества данного способа станут понятны из технологической схемы, приведенной на фиг. 1 где 1 напорная емкость, 2 перколятор, 3 лоток (цементатор), 4 приемная емкость, снабженная аэролифтом. Пример: В качестве материала, содержащего драгоценные металлы, взята проба отвалов, содержащих серебра 125 г/т, золота 78 г/т, свинца 0,3% цинка 0,5% железа 4,2% кобальта 1,1% магния 1,1% серы 0,4% SiO2 60,6% крупностью 2 мм. В перколятор 2 объемом 1 дм3 загружали 1,5 кг выщелачиваемого материала и смачивали его водой перед выщелачиванием. Из напорной емкости 1 попадали на орошение материала в перколяторе 0,2 дм3 выщелачивающего раствора (NCS- 40 г/дм3, Fe3+ 1 г/дм3, pH=3). Для получения ионов NCS- использовали тиоцианат калия, а Fe3+ - сульфат железа (III). Один цикл выщелачивания составлял 10 ч (плотность орошения 0,3 м3/т сут.). Раствор после перколятора протекал через лоток цементатор 3, заполненный 20 г обожженных и промытых серной кислотой (1:3) железных опилок, после чего попадал в приемную емкость 4, откуда периодически включаемым аэролифтом раствор подавали в емкость 1, где проводили корректировку состава выщелачивающего раствора. Все опыты проводили при продолжительности выщелачивания 15 суток. По окончании опыта железные стружки растворяли в азотной кислоте. Из раствора после фильтрации осаждали хлорид серебра, а из осадка на фильтре выделяли золото. Как видно из таблицыизвлечение серебра и золота в пределах параметров, оговоренных формулой изобретения (опыты 1, 2 и 3) обеспечивают степень извлечения серебра не ниже 41,6% а золота 26,8. Условия за нижними пределами оговоренных параметров (опыт 4) и за верхним (опыт 5) не обеспечивают достаточное извлечение серебра и золота. Простота и экономичность предложенного способа позволяет широко использовать его для извлечения золота и серебра там, где остальные способы непригодны:
1) из-за малых концентраций этих драгоценных металлов в исходных соединениях;
2) требуется экологическая безопасность процесса. Предлагаемый способ позволяет извлекать серебро со степенью извлечения - 82,1 а золото 69,4% всего за 15-дневный период обработки выщелачиваемого материала.
Формула изобретения: Способ перколяционного извлечения серебра и золота из руд и отвалов, включающий выщелачивание водным раствором, содержащим ионы тиоцианата и трехвалентного железа, отличающийся тем, что выщелачивание ведут в режиме орошения при 0,1-50oС, рН 0,5-7,0 при содержании в растворе тиоцианат-ионов 10-50 г/дм3 и трехвалентного железа 0,1-5,0 г/дм3 с выделением золота и серебра из полученного раствора путем пропускания раствора через слой железного скрапа или алюминиевых стружек с последующим корректированием раствора по значению рН, содержанию тиоцианат-ионов и трехвалентного железа и возвратом полученного раствора на выщелачивание.
Способ извлечения серебра из отработанных сорбентов, содержащих йод-129 (патент Российской Федерации RU2277599)
Изобретение относится к области переработки и утилизации твердых радиоактивных отходов радиохимических предприятий атомной промышленности, в частности к способу иммобилизации йода-129 и извлечению серебра из отработанных сорбентов, которое может быть использовано для изготовления йодного поглотителя. Серебросодержащий сорбент обрабатывают нагретым до 75-80°С щелочным раствором гидразин-нитрата с концентрацией по щелочи от 30 до 100 г/л и по гидразину - от 15 до 50 г/л. Раствор выдерживают не менее 60 минут и сливают в отдельную емкость для концентрирования из него йода-129. Промывку сорбента осуществляют водой. Затем сорбент обрабатывают азотной кислотой с концентрацией от 3 до 10 моль/л, нагретой до 80°С, в течение 30 минут. Техническим результатом является повторное использование серебра из отработанного сорбента и увеличение срока эксплуатации узла йодной очистки при переработке облученного ядерного топлива с минимальными затратами.
Описание изобретения: Изобретение относится к области переработки и утилизации твердых радиоактивных отходов радиохимических предприятий атомной промышленности, а именно к способу иммобилизации йода-129 и извлечению серебра из отработанных сорбентов, которое может быть использовано для изготовления йодного поглотителя.
Технологические процессы производств по переработке облученного ядерного топлива (ОЯТ) энергетических реакторов и транспортных установок неразрывно связаны с очисткой газоаэрозольных отходов от долгоживущего йода-129 (T1/2=1,57·107 лет). В качестве сорбента для его улавливания используется, например, активная гамма-окись алюминия, импрегнированная азотнокислым серебром. В процессе эксплуатации серебро связывается с йодом и частично с хлором и фтором. Так, в отработанном промышленном сорбенте до 70% серебра связано с йодом (йод-127, 129). Оставшаяся часть серебра находится в основном в виде хлорида и фторида, а также в азотнокислой форме.
После нескольких циклов регенерации сорбент разрушается и значительная его часть превращается в пылевидную фракцию, что исключает дальнейшее его использование в технологии очистки газоаэрозольных отходов [И.А.Истомин. Разработка и внедрение технологии обращения с йодом-129 в процессе переработки облученного ядерного топлива энергетических реакторов. Диссертация на соискание ученой степени кандидата технических наук. - Озерск, ФГУП "ПО "Маяк". - 2003 г. С. - 105].
Учитывая то обстоятельство, что серебро является остродефицитным и дорогостоящим реагентом, существует необходимость разработки методов извлечения серебра из отработанных "серебряных" фильтров, содержащих йод-129, с целью использования его для приготовления нового фильтрующего материала.
Известен метод регенерации твердотельного йодного фильтра, содержащего йодид серебра, йодат серебра и сорбированный физическим путем молекулярный йод [GB 2390219 А (МПК G 21 F 9/30, опубл. 31.12.2003)], в котором представлен способ извлечения серебра из отработанных сорбентов, содержащих йод-129. Сущность метода заключается в приведении твердотельного фильтра в контакт с водным раствором восстановителя, выбранным из гидроксиламина, гидроксиламиновых солей, аскорбиновой кислоты, солей аскорбиновой кислоты, аскорбил-эфиров, борогидрида натрия, гипофосфита натрия, формальдегида, мочевины, муравьиной кислоты и их солей для десорбции йода с фильтра и растворении его в водном растворе. Извлечение серебра осуществляется путем погружения фильтра, содержащего восстановленное серебро в раствор азотной кислоты с концентрацией от двух до шести моль на литр.
Отличительными признаками изобретения по сравнению с ближайшим аналогом являются следующие.
1. Использование в процессе удаления из отработанного сорбента радиоактивного йода в качестве восстановителя щелочного раствора гидразин-нитрата.
2. Расширение диапазона концентрации азотной кислоты до 10 моль/л в процессе извлечения серебра из отработанного сорбента.
Техническим результатом изобретения является упрощение и оптимизация эксплуатации йодного сорбента за счет повторного использования технического серебра, полученного в виде раствора азотнокислого серебра, пригодного для изготовления нового сорбента.
Технический результат достигается способом извлечения серебра из отработанных сорбентов, содержащих йод-129, включающим восстановление серебра с переводом его в металлическое состояние обработкой щелочным раствором реагента, промывку сорбента водой и обработку сорбента, содержащего металлическое серебро, азотной кислотой, в котором согласно изобретению, восстановление серебра ведут щелочным раствором гидразин-нитрата с концентрацией гидразина 15-50 г/л и щелочи 30-100 г/л в течение не менее 60 минут при температуре 75-80°С, обработку сорбента, содержащего металлическое серебро, осуществляют азотной кислотой с концентрацией 3-10 моль/л, нагретой до 80°С, в течение 30 минут.
Осуществление предлагаемого способа делится на следующие этапы
1. Отработанный сорбент, содержащий йод-129, обрабатывается щелочным раствором гидразин-нитрата с концентрацией по щелочи от 30 до 100 г/л и по гидразину - от 15 до 50 г/л при температуре от 75 до 80°С и продолжительности процесса не менее 60 минут для перевода всего серебра в металлическое состояние.
2. Сорбент промывается водой до полного устранения следов щелочи и гидразина.
3. В аппарат, содержащий промытый сорбент, заливается предварительно нагретая до 80°С азотная кислота с концентрацией от 3 до 10 моль/л. Система выдерживается в течение 30 минут, после чего раствор сливается в отдельную емкость. Основа сорбента промывается водой для устранения остатков серебра. Растворы объединяются и используются для изготовления сорбента за счет пропитки новой основы.
Пример 1: Несколько порций сорбента, содержащего металлическое серебро, были обработаны раствором азотной кислоты с концентраций от 0,1 до 7,0 моль/л при температуре 80°С в течение 30 минут. Степень извлечения серебра определяли как по остаточному содержанию его в сорбенте, так и по его концентрации в растворе. Зависимость степени извлечения серебра из сорбента от концентрации азотной кислоты приведена на чертеже. Как видно из чертежа максимальная эффективность извлечения ионов серебра в раствор наблюдается в диапазоне концентраций азотной кислоты от 3 моль/л и выше.
Пример 2: Несколько порций серебросодержащего сорбента (гранулы в виде цилиндров d = от 3 до 5 мм и h = от 10 до 15 мм) на основе окиси алюминия, содержащего труднорастворимые соединения серебра (AgI, AgCl, AgF) обрабатывали, предварительно нагретым до 80°С щелочным раствором гидразин-нитрата с концентрацией по щелочи 30 г/л и по гидразину 15 г/л в течение не менее 60 минут. После проведения процесса извлечения йода сорбент промывали дистиллированной водой до достижения нейтральной реакции в промывных растворах, сушили и взвешивали. Растворы, образующиеся в процессе регенерации (регенераты и промывка), анализировались на содержание в них йода. Результаты извлечения йода из сорбента приведены в таблице извлечение йода из отработанного сорбента.
Извлечение йода из отработанного сорбента |
Номер опыта |
Масса сорбента, мг |
Масса йода в растворе, мг |
Эффективность извлечения йода, % |
до извлечения йода |
после извлечения йода |
1 |
4952 |
4642 |
310 |
98,1 |
2 |
4926 |
4628 |
298 |
98,7 |
3 |
4946 |
4649 |
294 |
98,9 |
4 |
5047 |
4762 |
312 |
99,1 |
5 |
4960 |
4667 |
299 |
97,4 |
6 |
4993 |
4697 |
315 |
96,9 |
7 |
5030 |
4735 |
321 |
97,3 |
8 |
4985 |
4698 |
309 |
97,2 |
9 |
4953 |
4674 |
307 |
99,4 |
10 |
5000 |
4711 |
305 |
97,1 |
Среднее |
4979,2±27,5 |
4б87,2±29,5 |
292,0±4,8 |
98,0±0,7 |
Далее было проведено извлечение серебра из сорбента. Пробы сорбента обрабатывались азотной кислотой с концентрацией 5 моль/л в течение 30 минут при температуре 80°С. После проведения процесса маточные и промывные растворы анализировались на содержание в них серебра. Результаты экспериментов представлены в таблице извлечение серебра из сорбента.
Извлечение серебра из сорбента |
Номер опыта |
Масса сорбента, мг |
Масса серебра в растворе, мг |
Эффективность извлечения серебра, % |
До извлечения Ag |
После извлечения Ag |
1 |
4642 |
4322 |
321 |
98,8 |
2 |
4628 |
4310 |
318 |
98,2 |
3 |
4649 |
4334 |
316 |
97,1 |
4 |
4762 |
4440 |
321 |
96,3 |
5 |
4667 |
4343 |
322 |
98,5 |
6 |
4697 |
4377 |
318 |
96,7 |
7 |
4735 |
4410 |
320 |
96,5 |
8 |
4698 |
4382 |
317 |
96,4 |
9 |
4674 |
4360 |
324 |
99,0 |
10 |
4711 |
4391 |
322 |
97,6 |
Среднее |
97,4±0,6 |
Таким образом, эффективность извлечения серебра из всех порций сорбента составила (97,4±0,6)%. Достоинством предложенного способа является комплексный подход к вопросу утилизации сорбента, насыщенного йодом-129, при котором возможно после завершения использования сорбента извлечь из него радиоактивный йод для последующей его утилизации с последующим извлечением из него серебра для дальнейшего его использования (изготовления нового сорбента). Применение одного химического реагента (азотной кислоты) для извлечения серебра, а также снижение концентрации азотной кислоты позволяет получить раствор азотнокислого серебра, пригодного для повторного его использования в технологии переработки облученного ядерного топлива.
Формула изобретения: Способ извлечения серебра из отработанных сорбентов, содержащих йод-129, включающий восстановление серебра с переводом его в металлическое состояние обработкой щелочным раствором реагента, промывку сорбента водой и обработку сорбента, содержащего металлическое серебро, азотной кислотой, отличающийся тем, что восстановление серебра ведут щелочным раствором гидразин-нитрата с концентрацией гидразина 15-50 г/л и щелочи 30-100 г/л в течение не менее 60 мин при температуре 75-80°С, обработку сорбента, содержащего металлическое серебро, осуществляют азотной кислотой с концентрацией 3-10 моль/л, нагретой до 80°С, в течение 30 мин.
Список литературы
1. Барченков В.В. Основы сорбционной технологии извлечения золота и серебра из руд. – М.: Металлургия. – 1982. – 128 с.
2. Даймонд Р.М., Уитней Д.К. Селективность ионитов в разбавленных и концентрированных водных растворах. Ионный обмен: Пер. с англ./ Под ред. Я. Маринского. – М.: Мир.- 1968. – (С.187-212).
3. Каковский И.А., Поташников Ю.М. Кинетика процессов растворения. – М.: Металлургия. – 1975. – 224 с.
4. Меретуков М.А., Орлов А.М. Металлургия благородных металлов. Зарубежный опыт. - М.: Металлургия. – 1991. – 451 с.
5. Меретуков М.А., Стрижко Л.С. Современное состояние производства золота за рубежом. – М.: Цветметинформация. – 1985. – 59 с.
6. Металлургия благородных металлов / Под общей ред. Л.В. Чугаева
7. Плаксин И.Н. Гидрометаллургия. Избранные труды. – М.: Наука. – 1972. – 278 с.
8. Плаксин И.Н., Тэтару С.А. Гидрометаллургия с применение ионитов. – М.: Металлургия. – 1964. – 282 с.
9. Пунишко А.А. Современное состояние и перспективы применения сорбционных процессов в гидрометаллургии золота. – М.: Цветметинформация. – 1971. – (С. 21-24)
10. Техника и технология извлечения золота из руд за рубежом / Под ред. Лодейщикова В.В. – М.: Металлургия. – 1973. – 288 с.
11. Журнал «Юный техник» (№11 за 1959 г.) «Серебряные рудники» - в отходах
12. Журнал «Сделай сам» (№4 за 1990 г.)
13. Энциклопедия Брокгауза Ф.А. и Ефрона И.А. (1890 - 1916гг.)
14. Патент Российской Федерации RU2165468
15. Патент Российской Федерации RU2276196
16. Патент Российской Федерации RU2176290
17. Патент Российской Федерации RU2170277
18. Патент Российской Федерации RU2081193
19. Патент Российской Федерации RU2277599
20. www.ntpo.com
21. cepebpo.narod.ru
|