Южного Урала
д-р техн. наук Першин Г. Д., канд. техн. наук Караулов Г. А.,
канд. техн. наук Доможиров Д. В., канд. техн. наук Караулов Н. Г.
Магнитогорский государственный технический университет им. Г.И. Носова
Рассматривается особенность залегания мраморных месторождений с точки зрения многосистемной естественной трещиноватости горного массива. Выбран показатель блочности как критерий товарности добываемых мраморных блоков. Разработана методика определения оптимальных технологических параметров (высота добычного уступа) для максимального выхода блоков.
Мрамор, как строительно-облицовочный материал, используется давно и повсеместно, в силу своих декоративных свойств, прочности и долговечности. Особенно широкое распространение он получил в настоящее время, когда из сферы строительства эффективное его применение расширилось на многие отрасли народного хозяйства.
Особенностью залегания мраморных месторождений является многосистемная естественная трещиноватость горного массива, что формирует в нем природные отдельности разного объема. В процессе добычных работ на естественные трещины массива накладываются пропилы, образующие искусственно созданные отдельности различного объема. При последующей разделке и пассировке этих объемов получают товарные блоки правильной геометрической формы.
Ценность товарных блоков зависит от их объема. Для производства облицовочных и строительно-архитектурных изделий из мрамора применяют в основном блоки объемами свыше 3 м3 (I и II группа ГОСТа 9479-98 «Блоки из природного камня для производства облицовочных изделий»), при которых обеспечивается высокая техническая производительность современных камнеобрабатывающих линий и снижаются удельные технологические потери блочной продукции.
Выход блоков товарной кондиции (свыше 3 м3) зависит от параметров системы разработки месторождения, главными из которых являются высота уступа, ширина заходки и направление фронта добычных работ [1]. Именно эти параметры определяют объемы монолита, отделяемого от массива, и его расположение относительно основной системы природных трещин, влияя на выход блоков из горной массы.
Из блоков I и II групп возможно изготовление слэбов, стоимость которых в 2-3 раза выше стоимости модульной плитки, получаемой из блоков I-III групп (объемом более 0,7 м3).
В разработанных ранее методиках [2], обоснование оптимальной высоты уступа проводилось без учета последующей переработки блоков, а именно, не учитывалась разница в стоимости блоков и эффективности их переработки в зависимости от объема и соответствия группам ГОСТа 9479-98.
Для нахождения оптимального значения высоты уступа (монолита) с учетом минимального объема блока, соответствующего той или иной группе ГОСТа, получено оптимизационное выражение [3]:
, (1)
где оптимальная высота пропила для абсолютно монолитного массива, когда коэффициент выхода блоков из него равен единице ( );
– показатель блочности ( – минимальный объем блока по группе ГОСТа, м3; – коффициент интенсивности трещиноватости горного массива м2/м3).
Таким образом, показатель n зависит от интенсивности трещиноватости массива и мимнимального объема блока, с которого ведется подсчет коэффициента выхода блоков по участку месторождения (рис. 1). Показатель n увеличивается с 0,28 до 0,77 (рис. 2) (параметры трещин и размеры монолита приняты для условий Коелгинского и Редутовского месторождения), если в первом случае учитывать в качестве минимального блока объем Vmin = 0,7 м3, а во втором Vmin = 5,0 м3, т.е для первого варианта расчет выхода продукции вести для I-III категории блочности, согласно ГОСТ 9479-98, а во втором варианте – только для I категории. Минимальный объем добытого блока необходимо выбирать из условия, выгодной реализации дорогостоящей готовой продукции, изготовленной из него.
а
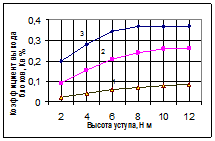
|
б
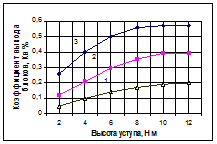
|
Рис. 1. Зависимость коэффициента выхода блоков от высоты уступа (Н) и группы блоков по ГОСТ 9479-98 для Коелгинского месторождения мрамора: 1 – блоки I группы, 2 – блоки I -II группы, 3 – блоки I-III группы (а – интенсивность трещиноватости 0,77 м2/м3,
б – интенсивность трещиноватости 0,44 м2/м3).
Показатель n, являясь критерием товарности добываемых блоков, определяет и оптимальную высоту добычного уступа по выражению (1) через минимальный объем блока и степень трещиноватости горного массива (см. рис. 2). Если за минимальный блок товарной кондиции принять объем Vmin = 3 м3, то согласно рис. 2, оптимальная высота добычного уступа составит для участков месторождения: со степенью трещиноватости 0,77 м2/м3 – Ноп = 8 м; со степенью трещиноватости 0,44 м2/м3 – м.
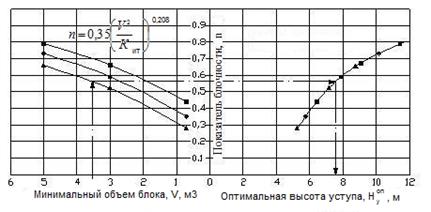
Рис. 2. Номограмма по определению оптимальной высоты уступа от показателя блочности и минимального объема товарного блока, м3; с интенсивностью трещиноватости (Кит) 0,44 (■); 0,77 (●); 1,12 (▲) м2/м3 .
Однако для принятия окончательного проектного решения по выбору рациональной высоты добычного уступа следует учитывать и суммарную выручку от реализации всего блочного сырья, получаемого из горной массы.
Так, для степени трещиноватости горного массива 0,77 м2/м3 показателем товарности блоков n1 = 0,59 (Vmin =3,0 м3) и n2 = 0,73 (Vmin = 5,0 м3) соответствуют следующие расчетные высоты уступов: м и м, для которых суммарная выручка от реализации блочной продукции изменяется всего лишь на 3 % (рис. 3). При этом с увеличением высоты уступа увеличиваются удельные эксплуатационные затраты, поэтому согласно экономическому критерию в данном случае за рациональную высоту уступа следует принимать оптимальное расчетное значение м. Анализ более блочного участка месторождения со степенью трещиноватости 0,44 м2/м3 показывает, что увеличение высоты уступа с величины 9 м до 11 м ведет к повышению суммарной выручки на 20 %. Поэтому для рассматриваемого варианта имеет смысл за рациональное значение высоты уступа принять интервал H = 10-11 м.
а
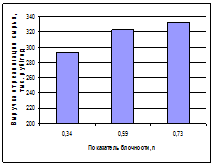
|
б
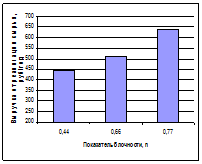
|
Рис. 3. Выручки от реализации сырья в зависимости от показателя блочности (а – интенсивность трещиноватости 0,77 м2/м3,
б – интенсивность трещиноватости 0,44 м2/м3) при производительности карьера по мрамору 90 тыс. м3 .
Работа системы «карьер – камнеобрабатывающее производство» должна быть всегда направлена на выпуск более дорогостоящей продукции, например слэбов, что обосновывает нижний предел товарности (ценности) блоков объемом не ниже 3 м3.
Заключение. Применение разработанной методики определения высоты добычного уступа для максимального выхода комерческих блоков I и II групп ГОСТа 9479-98 обеспечит максимальную прибыль от реализации добываемого сырья.
Список литературы
6 Труды молодых ученых № 4, 2007 |
|
Косолапов А.И., Невежин А.Ю. Исследование зависимости параметров технологии от пространственной изменчивости выхода блоков при комбинированной разработке месторождений мрамора. Сб. научных трудов. Магнитогорск, 2007. С. 89-96.Першин Г.Д., Караулов Г.А., Караулов Н.Г. Добыча блоков мрамора алмазно-канатными пилами. Учеб. пособие. Магнитогорск: МГТУ, 2003.
3 Першин Г.Д., Караулов Г.А., Караулов Н.Г., Караулов А.Г. Обоснование способов комплексного использования мраморного сырья. Вестник МГТУ. 2007.№1 (17). С. 31-35.
|